DOI:
10.1039/C5NJ02491A
(Paper)
New J. Chem., 2016,
40, 538-544
Rod-in-tube nanostructure of MgFe2O4: electrospinning synthesis and photocatalytic activities of tetracycline
Received
(in Montpellier, France)
16th September 2015
, Accepted 4th November 2015
First published on 10th November 2015
Abstract
Magnesium ferrite (MgFe2O4) nanofibers were synthesized by direct annealing of electrospun precursor fibers using an appropriate heat treatment process. The crystal structure, morphology and surface area of the as-synthesized MgFe2O4 nanofibers were investigated by X-ray diffraction, scanning electron microscopy, and transmission electron microscopy, respectively. The optical properties of the as-synthesized products were studied through ultraviolet-visible and photoluminescence spectroscopy. Due to its potential application in photocatalysis, the photocatalytic degradation of tetracycline (TC) was conducted, and the result indicated that MgFe2O4 showed a better photocatalytic degradation ratio (1.5 times and 2 times) of TC than the others under visible-light irradiation, which may be due to the unique rod-in-tube structure, and larger specific area and the larger specific surface area could absorb more catalyst and provide more active sites.
1 Introduction
Environmental problems have undoubtedly become one of the greatest problems and have attracted worldwide attention in the modern society.1,2 Tetracycline (TC), a widely used antibiotic, is usually released into the water environment3 and directly affects the environment by disrupting the ecosystem equilibrium.4 Natural bacteria exposed to residual antibiotics, such as TC, could modify their genetic information, develop higher antibiotic resistance and result in multi-resistant strains of micro-organisms.5 Fortunately, semiconductor-based photocatalysts provide a good tool for the degradation of antibiotics, and much effort has been focused on the degradation of TC by photocatalysis.6–8 Conventional photocatalysts such as TiO2, CdS, and ZnO have been reported recently,9–12 but due to their disadvantages (inability to respond to visible light, poor stability, and poor ability to degrade), their practical application is restricted. Therefore, new-type visible light driven photocatalysts with excellent stability and high efficiency for TC degradation are still desired.
Multi-metal oxides are of particular interest due to their remarkable magnetic, electrical, and optical properties. Among them, MgFe2O4, a member of spinel family, is found to be a promising visible light photocatalyst due to its narrow band gap (2.0 eV) and corrosion resistance.13 In the past few decades, there have been a variety of reports on synthesis of MgFe2O4 using methods such as hydrothermal, solvothermal, solid synthesis, sol–gel, and microwave-assisted methods.14–18 However, these conventional synthesis methods could not effectively control the morphology and size, therefore, searching a new method for the controllable synthesis of MgFe2O4 is urgent.
Among these fabrication methods, the electrospinning technique has been extensively exploited as a simple and versatile controllable synthesis method for generating 1D nanostructures of various different materials.19 The electrospinning method has demonstrated its capability to prepare a range of interesting structures, such as porous nanofibers,20,21 nanotubes,22 nanobelts,23 core–shell,24 tube-in-tube,25 side-by-side,26 hollow tubes,27 and triaxial structures.28
Herein, we report the synthesis of MgFe2O4 by electrospinning and subsequent direct annealing processes. Compared with the above-mentioned methods, only simple electrospinning and calcination are required, without a coating procedure and a special spinner. In our experiments, a mixed ethanol and water solution was used as a solvent instead of the use of toxic solvents such as DMF,29,30 avoiding the pollution of the environment. The unique rod-in-tube structure nanofiber morphology and larger specific surface area of MgFe2O4 endow it better photocatalytic properties.
2 Experimental
2.1. Materials
Polyvinylpyrrolidone (PVP, K-90, Mw = 1
300
000) was purchased from tianjin tiantai Fine Chemical Co., Ltd. Fe(NO3)3·9H2O (purchased from Beijing Chemical Reagent Co., Ltd), Mg(NO3)2·3H2O (purchased from Shanghai Shanpu Chemical Co., Ltd) and ethanol (C2H5OH, 99.7%, purchased from tianjin Rionlon BoHua Medical Chemistry Co., Ltd) were used as received. Other reagents were commercially available and were of analytical reagent grade.
2.2. Preparation of MgFe2O4 nanofibers
4.04 g of Fe(NO3)3·9H2O and 1.28 g of Mg(NO3)2·3H2O were added into a mixture of 2.5 mL of ethanol and 7.5 mL of water, and then 1.3 g of PVP was added into the above solution to increase viscidity. Then the mixture was magnetically stirred for several hours at room temperature (RT) to form a homogeneous precursor solution. In the subsequent electrospinning process, the spinnable precursor sol was loaded into a glass syringe equipped with a stainless steel needle. A high voltage of 25 kV was supplied by a direct-current power supply. The distance between the tip of the needle and the collector was 15 cm. The humidity is about 40–50% and temperature is room temperature (25–30 °C). For the following thermolysis process, the as-spun fibers were placed in a muffle furnace and calcined at a temperature of 500 °C for 2 h to remove PVP and obtain MgFe2O4 samples under different conditions of heating treatment.
2.3. Characterization
To analyze the crystal structures of the samples, the X-ray diffraction (XRD) measurements were conducted on an X-ray diffractometer using Cu-Kα radiation (XRD, Panalytical X'Pert Pro) from 10 to 80°. The morphology and microstructures of the as-spun fibers and calcined samples were analyzed using a field emission scanning electron microscope (FESEM, Hitachi S-4800) and a transmission electron microscope (TEM, Hitachi JEM-2010). The BET surface area was calculated from N2 adsorption–desorption measurements by using a Beesd instrument technology (Beijing) Co., Ltd 3H-2000PM2 Surface Area & Pore Size analyzer. In addition, UV-vis absorption spectra were recorded on a Shimadzu UV-2450 spectrometer. Photoluminescence spectra were recorded on a QuantaMaster & TimeMaster Spectrofluorometer. The room-temperature photoluminescence spectrum (PL) was collected using a Hitachi F-4500 spectrofluorometer with an excitement wavelength of 440 nm.
2.4. Photocatalytic activity measurement
The photodegradative reaction for TC was carried out at room temperature under visible light. The photochemical reactor contained 10 mg of the sample and 50 mL of TC solution (10 mg L−1). To determine the initial absorbency of samples, the reactor was kept in darkness for 60 min to reach absorption equilibrium. The photochemical reactor was irradiated with a 150 W Xenon lamp which was located with a distance of 8 cm at one side of the containing solution. UV light with wavelengths less than 420 nm was removed using a UV-cutoff filter. The sampling analysis was conducted at 15 min intervals. The photocatalytic degradation ratio (DR) was calculated by the following formula:
A0 is the initial absorbency of TC that reached absorption equilibrium, while Ai is the absorbency after the sampling analysis. The TC concentration was measured using a UV-vis spectrophotometer with the maximum absorption wavelength at 357 nm.
3 Result and discussion
3.1. Morphology and structure
The phase of the synthesized MgFe2O4 nanofibers is identified by XRD characterization. Fig. 1 shows the XRD patterns of precursor fibers after annealing at different heating rates. As shown in Fig. 1, all diffraction peaks of the three samples can be indexed to spinel MgFe2O4. When the heating rate increases, the diffraction peaks gradually enhance, which indicates the enhanced crystallinity and the growth of MgFe2O4 nanocrystals. No other crystalline impurities are detected, which indicates that all the products are in correspondence with pure MgFe2O4 (JCPDS 36-0398).
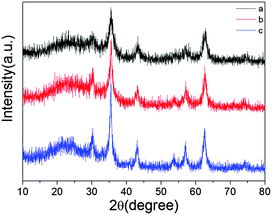 |
| Fig. 1 Typical XRD pattern of the prepared MgFe2O4 nanofibers: (a) at the heating rate of 1 °C min−1 to 500 °C, (b) at the heating rate of 1 °C min−1 to 400 °C and 5 °C min−1 to 500 °C, and (c) at the heating rate of 5 °C min−1 to 500 °C. | |
The morphology and microstructure of the samples were obtained by scanning electron microscopy (SEM) and transmission electron microscopy (TEM), Fig. 2 shows the SEM and TEM images of the prepared samples. Uniform nanofibers and nanobelts, which are ca. 400 nm in diameter and from several to ten of micrometers in length, are shown in Fig. 2a. Fig. 2b shows that the rough nanofibers are rod-in-tube nanostructures and there exists nanorod in them. The formation of a rough surface is attributed to the growth of MgFe2O4 nanocrystals at the higher heating rate in the second step. The average length is up to tens of micrometers with the average diameter of ca. 450 nm. In Fig. 2c, a nanobelt is coating onto the nanofibers, and several other nanofibers are smooth without any nanobelt. The TEM images in Fig. 2d–f further revealed the internal structure of the obtained products. Fig. 2d shows a solid nanofiber structure. As shown in Fig. 2e and f, in the intensive contrast between the dark center and the dark edges, there exists light space, which demonstrates that the obtained fibers are rod-in-tube nanostructures, which is consistent with the SEM results. Moreover, it is clear that the wall of the rod-in-tube structure is assembled by irregular nanoparticles.
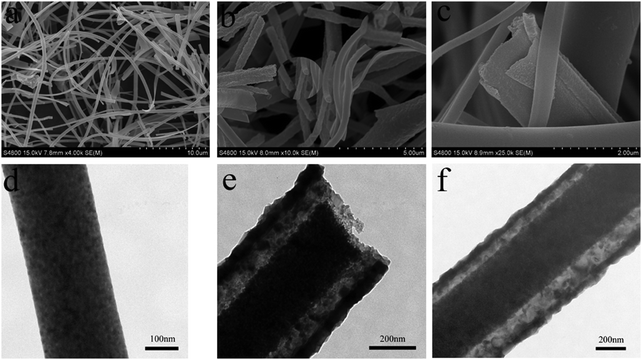 |
| Fig. 2 SEM and TEM images of the prepared MgFe2O4 nanofibers: (a) and (d) at the heating rate of 1 °C min−1 to 500 °C, (b) and (e) at the heating rate of 1 °C min−1 to 400 °C and 5 °C min−1 to 500 °C, and (c) and (f) at the heating rate of 5 °C min−1 to 500 °C. | |
Based on the experiment data and analyses above, a possible formation mechanism of the MgFe2O4 rod-in-tube produced in this study is proposed, whose schematic diagrams are shown in Scheme 1. Initially, a sol–gel composed of PVP, ethanol/deionized water, iron nitrate, and magnesium nitrate was prepared for electrospinning. After the electrospinning process, nanorods and nanobelts were formed when the nanofibers were collected on the collector. At the heating rate of 1 °C min−1, due to the slow heating rate, the morphology remained unchanged, and nanofibers and nanobelts were smooth on the surface (entry a in Fig. 2). When the heating rate increased to 5 °C min−1, the nanobelts gradually coated on the surface of the nanofibers and in the meantime the nanoparticles which formed the nanobelts gradually became large so the surface of the rod-in-tube nanostructure is rough (entry b in Fig. 2). In the end, the unique rod-in-tube structure was formed. If the heating rate was 5 °C min−1 from initial, a large number of nanobelts will reunite to form a rod-like structure, so the nanobelts disappeared, which was not conducive to the formation of a rod-in-tube structure, and therefore the structure of rod-in-tube decreased (entry c in Fig. 2).
 |
| Scheme 1 Schematic diagram illustrating the possible formation and growth mechanism of the unique MgFe2O4 rod-in-tube structure. | |
3.2. UV-vis diffuse reflectance spectra
The optical absorption properties of the photocatalysts are one of the most important parameters in the field of photocatalysis. The diffuse reflectance spectrum (DRS) of the as-prepared MgFe2O4 nanofiber samples is shown in Fig. 3. The absorbance in the 400–600 nm range is observed. From Fig. 3, it is obvious that MgFe2O4 samples respond to visible light, which is due to their narrow band (2.0 eV). They all share the similar UV-vis curves, and sample b has superior absorption spectroscopy compared to the others, which may be attributed to its unique structure. Besides they also exhibit the magnetic properties. These two properties (absorption in the visible range and magnetism) exhibited by MgFe2O4 make this material attractive for magnetically separable and recyclable photocatalyst materials.31
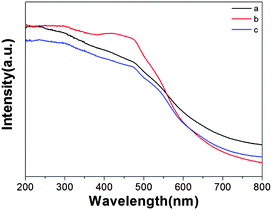 |
| Fig. 3 UV-vis absorption spectra of MgFe2O4 nanofibers: (a) at the heating rate of 1 °C min−1 to 500 °C, (b) at the heating rate of 1 °C min−1 to 400 °C and 5 °C min−1 to 500 °C, and (c) at the heating rate of 5 °C min−1 to 500 °C. | |
3.3. Photocatalytic properties
Antibiotics are widely used in human life. It was usually released into the water environment and directly affects the environment by disrupting the ecosystem equilibrium. TC, a popular broad-spectrum antibacterial agent, has been widely applied in bacterial infection treatment. Therefore, there are serious threats to the ecosystem and human health if TC is released into the environment. So, the degradation of TC has been established to be one of the most promising technologies for environmental remediation.32
Based on the interesting absorption spectra and unique structure, the photocatalytic activity of MgFe2O4 was studied on degradation of TC in an aqueous solution (10 mg L−1). During the process of photo-degradation, the major absorbance (ca. 357 nm) from TC in the solution gradually decreased under visible light (λ > 420 nm) for 2 h, which suggested the significant photodegradation of TC by MgFe2O4.
The photocatalytic activities of the as-prepared samples were evaluated by the degradation of the antibiotic under visible light irradiation. TC was chosen as a representative hazardous antibiotic to evaluate the photocatalytic performance. Fig. 4 shows the photocatalytic performance of the synthesized MgFe2O4 under different conditions of heating treatment under visible light (λ > 420 nm). As shown in Fig. 4, sample b exhibits an excellent photocatalytic degradation ratio of TC (64.4%) after irradiation for 2 h under visible light, which is 50% more than the others under the same conditions. This may be ascribed to the special rod-in-tube nanostructure, which has superior absorption spectroscopy. In order to check the stability of the catalyst, we have made an error bar analysis. Fig. 4 indicates that the error range is small, which confirms that it is relatively stable.
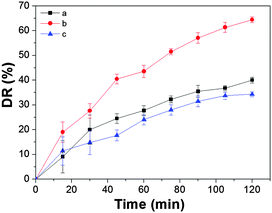 |
| Fig. 4 Photocatalytic degradation ratios (detection wavelength is 357 nm) of MgFe2O4 under visible light: (a) at the heating rate of 1 °C min−1 to 500 °C, (b) at the heating rate of 1 °C min−1 to 400 °C and 5 °C min−1 to 500 °C, and (c) at the heating rate of 5 °C min−1 to 500 °C. | |
3.4. BET and PL properties of the MgFe2O4 samples
Fig. 5 shows the N2 absorption–desorption isotherms and pore size distribution. The materials exhibit absorption–desorption isotherms which can be attributed to type IV according to the classification of IUPAC33 with a small hysteresis loop (type H3) due to the capillary condensation process in the mesopores.34 The specific surface area of each sample is estimated according to the BET method. The pore size distributions are obtained from the Barrett–Joyner–Halenda (BJH) method. According to the calculation, the results are summarized in Table 1. From Table 1 we could see that the specific surface areas, total pore volume and average pore width of all the samples are nearly the same. From the data above, we could see that the special structure cannot alter the specific surface areas much, but the slightly changed specific surface areas do affect the photocatalytic performance and the larger specific area do enhance its photocatalytic activity.
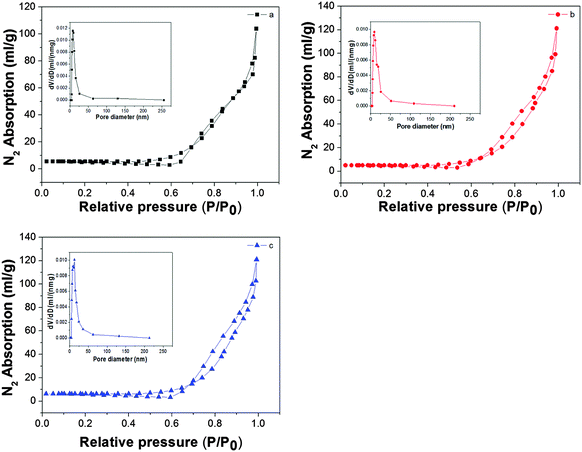 |
| Fig. 5 Nitrogen adsorption–desorption isotherms and pore size distribution (a) at the heating rate of 1 °C min−1 to 500 °C, (b) at the heating rate of 1 °C min−1 to 400 °C and 5 °C min−1 to 500 °C, and (c) at the heating rate of 5 °C min−1 to 500 °C. | |
Table 1 Specific surface area (SBET), total pore volume (Vpore) and average pore width (dpore) of the as-prepared products
Sample |
S
BET (m2 g−1) |
V
pore (cm3 g−1) |
d
pore (nm) |
a |
15.0933 |
0.2115 |
17.38 |
b |
19.0752 |
0.2093 |
17.61 |
c |
16.3916 |
0.1839 |
15.30 |
To further understand the higher photocatalytic activity of sample b for the degradation of TC than the other two, we probe into a possible reason on the basis of experimental analysis. Fig. 6 shows photoluminescence (PL) spectra of the samples. The fluorescence intensity is directly proportional to the electron hole recombination probability,35 and the lower PL intensity indicates the decrease in the recombination rate. The results shown in Fig. 6 indicate that sample b shares the lowest fluorescence intensity when compared with the others, which may be due to the unique rod-in-tube structure, leading to the enhancement of electron and hole separation and improving the photocatalytic performance.
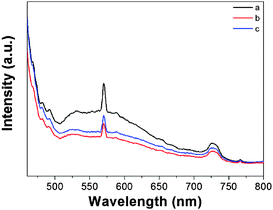 |
| Fig. 6 Photoluminescence (PL) spectra of the photocatalysts (excitation wavelength = 440 nm) (a) at the heating rate of 1 °C min−1 to 500 °C, (b) at the heating rate of 1 °C min−1 to 400 °C and 5 °C min−1 to 500 °C, and (c) at the heating rate of 5 °C min−1 to 500 °C. | |
For further understanding the role of photogenerated radical species and the underlying reaction mechanism for the degradation of TC under visible light irradiation, a series of controlled experiments were conducted. Fig. 7 shows the results of adding different radical scavengers over the MgFe2O4 photocatalyst reaction system under visible light irradiation. When the radical scavenger, isopropanol, for hydroxyl is added into the reaction system, the degradation rate of TC is inhibited (entry c in Fig. 7). A significant inhibition phenomenon for the photocatalytic reaction is observed when the triethanolamine scavenger for holes is added (entry d in Fig. 7), while when the AgNO3 scavenger for electrons is added into the reaction system, it almost remains the same but rises a little (entry b in Fig. 7), which may be due to the fact that part of electrons are captured by AgNO3 and therefore inhibit the recombination of electron and hole pairs and increase the numbers of holes. These results clearly suggest that the photocatalytic degradation of TC over MgFe2O4 is primarily driven by photogenerated holes and hydroxyl.
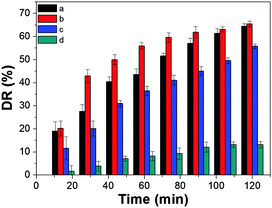 |
| Fig. 7 Controlled experiments using different radical scavengers for the photocatalytic degradation of TC; (a) reaction in the absence of radical scavengers, (b) reaction with AgNO3 as a radical scavenger for photogenerated electrons, (c) reaction with isopropanol as a radical for hydroxyl scavengers, and (d) reaction with triethanolamine as a scavenger for photogenerated holes under visible light irradiation for 2 h. | |
On the basis of the experimental results, we have proposed a possible mechanistic pathway. As depicted in Fig. 8, when the visible light irradiates onto the catalyst, e− changes from the ground state to the excited state, and transfers from the valence band to the conduction band, which is the separation of electron hole pairs. The excited e− which is transferred to the conduction band reacts with O2 and produces ˙OH radicals. The as-produced ˙OH radicals can then degrade the TC molecules into CO2 and H2O. Meanwhile h+ in the valence band can directly degrade the TC molecules into CO2 and H2O and a small amount of h+ produces ˙OH to degrade TC.36–39 From the analyses above, it can be concluded that h+ and ˙OH are the main active species of MgFe2O4 in aqueous solution under visible light irradiation.
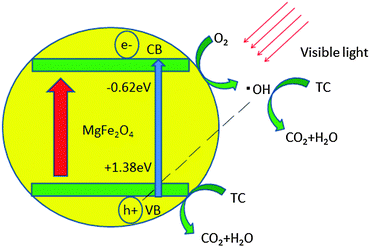 |
| Fig. 8 Illustration of the proposed possible reaction mechanism for the photocatalytic degradation of TC over MgFe2O4 under visible light irradiation. | |
4 Conclusions
In summary, MgFe2O4 nanofibers have been successfully fabricated by direct annealing of electrospun precursor fibers. Compared with other methods for preparing nanofibers by electrospinning, no toxic substance such as DMF is used and only environmentally friendly ethanol and deionized water are required, which provide a potential application in synthesis. The photocatalytic degradation of tetracycline under visible light is conducted. The as-obtained products which have a unique rod-in-tube nanostructure exhibited a better photocatalytic degradation ratio (64.4%) of tetracycline than the others under visible light irradiation, which may be due to the unique rod-in-tube structure, small diameter in size and large specific area. Furthermore, we study the degradation process of the as-obtained products and propose possible reaction mechanisms. The results show that holes and hydroxyl are the main active species of MgFe2O4 in the process of degradation TC under visible light irradiation. Our work provides a potential application in fabricating special structure nanomaterials in a facial and environmentally friendly way.
Acknowledgements
The authors would like to acknowledge the National Natural Science Foundation of China (11174092, 11474111, 21477050 and 21522603), the Chinese-German Cooperation Research Project (GZ1091), the Excellent Youth Foundation of Jiangsu Scientific Committee (BK20140011), the Program for New Century Excellent Talents in University (NCET-13-0835), the Jiangsu Province Postdoctoral Foundation (1501027A), the Henry Fok Education Foundation (141068) and Six Talents Peak Project in Jiangsu Province (XCL-025).
References
- P. M. Martins, V. Gomez, A. C. Lopes, C. J. Tavares, G. Botelho, S. Irusta and S. Lanceros-Mendez, J. Phys. Chem. C, 2014, 118, 27944 CAS.
- J. G. Yu, S. H. Wang, J. X. Low and W. Xiao, Phys. Chem. Chem. Phys., 2013, 15, 16883 RSC.
- F. Baquero, J. L. Martinez and R. Canton, Curr. Opin. Biotechnol., 2008, 19, 260 CrossRef CAS PubMed.
- C. Tixier, H. P. Singer, S. Oellers and S. R. Müller, Environ. Sci. Technol., 2003, 37, 1061 CrossRef CAS PubMed.
- D. M. Bila and M. Dezotti, Quím. Nova, 2003, 26, 523 CrossRef CAS.
- A. Fujishima and K. Honda, Nature, 1972, 238, 37 CrossRef CAS PubMed.
- R. Hao, X. Xiao, X. X. Zuo, J. M. Nan and W. D. Zhang, J. Hazard. Mater., 2012, 209, 137 CrossRef PubMed.
- M. Brigante and P. C. Schulz, J. Hazard. Mater., 2011, 192, 1597 CrossRef CAS PubMed.
- X. D. Zhu, Y. J. Wang, R. J. Sun and D. M. Zhou, Chemosphere, 2013, 92, 925 CrossRef CAS PubMed.
- B. Sun, A. V. Vorontsov and P. G. Smirniotis, J. Hazard. Mater., 2011, 186, 1147 CrossRef CAS PubMed.
- Y. B. Liu, X. J. Gan, B. X. Zhou, B. T. Xiong, J. H. Li, C. P. Dong, J. Bai and W. M. Cai, J. Hazard. Mater., 2009, 171, 678 CrossRef CAS PubMed.
- R. A. Palominos, M. A. Mondaca, A. Giraldo, G. Peñuela, M. Pérez-Moya and H. D. Mansilla, Catal. Today, 2009, 144, 100 CrossRef CAS.
- H. G. Kim, P. H. Borse, J. S. Jang, E. D. Jeong, O. S. Jung, Y. J. Suh and J. S. Lee, Chem. Commun., 2009, 5889 RSC.
- Y. H. Yin, B. Zhang, X. T. Zhang, J. J. Xu and S. T. Yang, J. Sol-Gel Sci. Technol., 2013, 66, 540 CrossRef CAS.
- M. G. Naseri, M. H. M. Ara, E. B. Saion and A. S. Halim, J. Magn. Magn. Mater., 2014, 350, 141 CrossRef.
- M. R. Barati, C. Selomulya and K. Suzuki, J. Appl. Phys., 2014, 115, 17 Search PubMed.
- H. W. Liu and H. F. Liu, J. Electron. Mater., 2014, 43, 2553 CrossRef CAS.
- S. Ilhan, S. G. Izotova and A. A. Komlev, Ceram. Interfaces, 2015, 41, 577 CrossRef CAS.
- D. Li and Y. N. Xia, Adv. Mater., 2004, 16, 1151 CrossRef CAS.
- Y. Z. Zhang, Y. Feng, Z. M. Huang, S. Ramakrishna and C. T. Lim, Nanotechnology, 2006, 17, 901 CrossRef CAS.
- X. Zhang, V. Thavasi, S. G. Mhaisalkar and S. Ramakrishna, Nanoscale, 2012, 4, 1707 RSC.
- W. Wang, J. Y. Zhou, S. S. Zhang, J. Song, H. G. Duan, M. Zhou, C. S. Gong, Z. Bao, B. A. Lu, X. D. Li, W. Lan and E. Q. Xie, J. Mater. Chem., 2010, 20, 9068 RSC.
- Y. Wang, Y. R. Su, L. Qiao, L. X. Liu, Q. Su, C. Q. Zhu and X. Q. Liu, Nanotechnology, 2011, 22, 225702 CrossRef CAS PubMed.
- Z. Sun, E. Zussman, A. L. Yarin, J. H. Wendorff and A. Greiner, Adv. Mater., 2003, 15, 1929 CrossRef CAS.
- L. Lang, D. Wu and Z. Xu, Chem. – Eur. J., 2012, 18, 10661 CrossRef CAS PubMed.
- S. Jiang, Q. Jin and S. Agarwal, Macromol. Mater. Eng., 2014, 299, 1298 CrossRef CAS.
- D. Li and Y. Xia, Nano Lett., 2004, 4, 933 CrossRef CAS.
- S. Jiang, G. Duan, E. Zussman, A. Greiner and S. Agarwal, ACS Appl. Mater. Interfaces, 2014, 6, 5918 CAS.
- S. Maensiri, M. Sangmanee and A. Wiengmoon, Nanoscale Res. Lett, 2009, 4, 221 CrossRef CAS PubMed.
- R. Dom, R. Subasri, K. Radha and P. H. Borse, Solid State Commun., 2011, 151, 470 CrossRef CAS.
- S. Muhammad, J. L. Liu, A. Zahid, S. Imran, F. W. Muhammad, P. Riffat and N. Muhammad, Mater. Chem. Phys., 2013, 139, 566 CrossRef.
- X. Xiao, R. P. Hu, C. Liu, C. L. Xing, X. X. Zuo, J. M. Nan and L. S. Wang, Chem. Eng. J., 2013, 225, 790 CrossRef CAS.
- S. Lowell, J. E. Shields, M. A. Thomas and M. Thommes, J. Am. Chem. Soc., 2005, 127, 14117 Search PubMed.
- L. V. C. Lima, M. Rodriguez, V. A. A. Freitas, T. E. Souza, A. E. H. Machado, A. O. T. Patrocinio, J. D. Fabris, L. C. A. Oliveira and M. C. Pereira, Appl. Catal., B, 2015, 165, 579 CrossRef CAS.
- E. C. Su, B. S. Huang, C. C. Liu and M. Y. Wey, Renew. Energy, 2015, 75, 266 CrossRef CAS.
- S. Q. Liu, N. Zhang, Z. R. Tang and Y. J. Xu, ACS Appl. Mater. Interfaces, 2012, 4, 6378 CAS.
- G. H. Zhang, W. S. Guan, H. Shen, X. Zhang, W. Q. Fan, C. Y. Lu, H. Y. Bai, L. S. Xiao, W. Gu and W. D. Shi, Ind. Eng. Chem. Res., 2014, 53, 5443 CrossRef CAS.
- P. Li, C. B. Liu, G. L. Wu, Y. Heng, S. Lin, A. Ren, K. H. Lv, L. S. Xiao and W. D. Shi, RSC Adv., 2014, 4, 47615 RSC.
- M. Q. Yang, N. Zhang and Y. J. Xu, ACS Appl. Mater. Interfaces, 2013, 5, 1156 CAS.
|
This journal is © The Royal Society of Chemistry and the Centre National de la Recherche Scientifique 2016 |
Click here to see how this site uses Cookies. View our privacy policy here.