DOI:
10.1039/C5NJ02399H
(Paper)
New J. Chem., 2016,
40, 679-686
V2O5/SBA-15 nanocatalysts for the selective synthesis of 2,3,5-trimethyl-1,4-benzoquinone at room temperature
Received
(in Nottingham, UK)
7th September 2015
, Accepted 12th November 2015
First published on 16th November 2015
Abstract
A series of four V2O5/SBA-15 catalysts with the loadings of 5, 7.5, 10 and 12.5% (by weight) V2O5 have been prepared by the molecular designed dispersion (MDD) method and are characterized by N2-physisorption, low-angle and wide-angle XRD, transmission electron microscopy (TEM), Fourier Transform-Raman spectroscopy (FT-Raman), Ultraviolet-visible diffuse reflectance spectroscopy (UV-Vis, DRS), temperature programmed reduction (TPR) and inductively coupled plasma-optical emission spectrometry (ICP-OES) techniques. Among V2O5/SBA-15 catalysts, the 10%V2O5/SBA-15 catalyst exhibited 99% 2,3,5-trimethylphenol (TMP) conversion with 95% 2,3,5-trimethyl-1,4-benzoquinone (TMBQ) yield when H2O2 (30% aqueous solution) and ethanol were used as green oxidant and green solvent respectively at room temperature. The remarkable activity of the 10%V2O5/SBA-15 catalyst is due to the isolated distribution of uniform sized nanovanadium species on the pore surfaces of the hexagonally ordered mesoporous SBA-15 silica support.
Introduction
Vitamins are essential food components which are either not synthesized in the human beings or animals or not formed in sufficient amounts. The selective oxidation of phenols to quinones constitutes an essential biological process1 and is of significant interest to the chemical industry.2 Quinones serve as electron acceptors in electron transport chains in photosynthesis and aerobic respiration.3 Among the industrially relevant quinones, TMBQ represents a crucial intermediate for the industrial synthesis of α-tocopherol that is the most active component of vitamin E,4 which is of particular economical relevance and industrial interest, and is extensively used as an antioxidant in food, medical treatments and cosmetics.5
Notably, TMBQ shows anti-aging properties and functions as anti-free radical thus preventing apoplexy, heart disease, cardiovascular vessel disease and cancer.6 Adequately, it shows biological properties such as antigerminative, antibacterial, antitumor, and antiprotozoan activities. In general, the main route for TMBQ production is p-sulphonation of TMP followed by stoichiometric oxidation with MnO2.7 Industrially, for the production of TMBQ, copper halides and other copper salts/O2 systems have been employed.8 Catalytic systems such as cobalt(II) salen complexes, ruthenium salts and heteropolyacid systems using O2 or H2O2 are reported.9–11 However, the main drawback of the above mentioned systems is the use of homogeneous catalysts which leads to the problems of catalyst separation, recycling and product purification.
Evidently, there has been a rising demand for economic and environmentally friendly processes, which requires the development of clean oxidation methods. Nowadays, green chemistry has become the central issue in both academia and industry as a sustainable approach for fine chemical synthesis.12 Aqueous H2O2 is an ideal, inexpensive, very attractive, and waste-avoiding oxidant for liquid phase reactions13 which gained particular interest from the point of “green” chemistry, with the generation of H2O as the only co-product.
To date, titanium silicates TS-1 and TS-2 have been effective catalysts for H2O2 based heterogeneous oxidation14 and have undergone continuous development. However, the use of these catalysts is limited to compounds with a kinetic diameter less than 6 Å and inefficient for the selective oxidation of bulky reactants due to slow diffusion of reactants and/or products and deactivation caused by substance blockage in micropores. It is therefore reasonable to research the elaboration of new environmentally friendly catalysts with greater porosity and to host the larger molecules.
Oxovanadium species have been found to have particular catalytic activity especially in oxidation reactions.15 The presence of V+5 dimers or small oligomers with adjacent V atoms is required to ensure fast oxidation. The synthesis of supported and unsupported nanovanadium catalysts has been described and the structural features have been discussed.16–22 Herein, V2O5/SBA-15 nanovanadium catalysts have been prepared by the MDD method and the superior performance of these nanocatalysts in the oxidation of 2,3,5-trimethylphenol to 2,3,5-trimethyl-1,4-benzoquinone has been described.
Experimental
Catalyst preparation
The siliceous SBA-15 was synthesized in accordance with the procedures mentioned in the literature.23,24 A solution of EO20PO70EO20
:
2 M HCl
:
TEOS
:
H2O = 2
:
60
:
4.25
:
15 (mass ratio) was prepared, stirred for 12 h at 40 °C and then hydrothermally treated at 100 °C under static conditions for 12 h, and subsequently filtered, dried at 100 °C and calcined at 550 °C for 8 h. The resultant white powder is mesoporous silica SBA-15, which is used as a support, and it is also known as a parent SBA-15. To prepare mesoporous SBA-15 supported nanovanadium catalysts (V2O5/SBA-15), the deposition of VO(acac)2 metal complexes onto the SBA-15 surface was performed by the liquid phase MDD method.22 With a slight modification of the MDD method, the V2O5/SBA-15 catalysts were prepared, wherein, requisite amount of VO(acac)2 was dissolved in 100 ml of dry dichloromethane solution with the simultaneous addition of the vacuum dried SBA-15 support (120 °C for 6 h) followed by stirring for 1 h at room temperature. The resultant slurry was filtered off, washed thoroughly with toluene and dried at 100 °C for 12 h. The acac ligands were removed by calcination, which was performed in a programmable oven at 450 °C for 5 h in air and represented as xV2O5/SBA-15 catalysts where the prefixed x indicates the loading of V2O5 (by wt%).
Catalyst characterization
X-ray diffraction (XRD) patterns were recorded at room temperature using an X-ray diffractometer (Multiflex, M/s. Rigaku, Japan) with nickel filtered CuKα radiation. N2 adsorption–desorption isotherms were recorded on a N2 adsorption unit at −196 °C (Quadrasorb-SI V 5.06, M/s. Quantachrome Instruments Corporation, USA). The samples were out-gassed at 200 °C for 4 h prior to the measurement. The FT-Raman spectra were recorded on a Nicolet Nexus FT-Raman spectrometer with a Ge detector. All samples were measured at room temperature in 180° reflective sampling configuration, with 1064 nm Nd:YAG excitation laser. For each spectrum, 2.0 scans were averaged and the laser power was set between 1 and 2 W. TEM images were taken on a Philips Technai G2 FEI F12 instrument at an accelerating voltage of 80–100 kV. The samples were crushed in A.R. grade ethanol and the resulting suspension was allowed to dry on a carbon film supported on copper grids. UV-Vis DRS was performed at room temperature using a UV-2000 spectrophotometer (M/s Shimadzu, Japan) equipped with a diffuse reflectance attachment with an integrating sphere containing BaSO4 as a reference. The spectra were recorded in the range of 200–800 nm with a sampling interval of 0.5 nm and slit width of 2 nm. The TPR profiles of the catalysts were obtained from a homemade apparatus consisting of TCD equipped GC and a quartz microreactor. In a typical TPR experiment, the fixed bed quartz microreactor was loaded with 50 mg of catalyst and the temperature was raised in the flow of 5% H2 in Argon (v/v) with a heating rate of 10 °C min−1 from room temperature to 800 °C and maintained at this temperature for 30 min to ensure the complete reduction. The elemental composition was characterized by ICP-OES analysis (iCAP6500 series, M/s. Thermo Scientific, Germany).
Liquid phase oxidation of 2,3,5-trimethylphenol
In a typical experiment, 50 mg of V2O5/SBA-15 nanocatalyst was dispersed in 2 ml of ethanol (EtOH) in a 10 ml capacity round bottomed flask, which was open to air. Subsequently, 1 mmol of 2,3,5-trimethylphenol and 3 mmol of H2O2 (30% aqueous solution) were added and the reaction was conducted at room temperature under constant stirring for 1 h. After completion of the reaction, the catalyst was separated from the product mixture by simple filtration, dried over anhydrous MgSO4 to remove water and analyzed by a gas chromatograph (GC-17A, M/s. Shimadzu Instruments, Japan) using an Equity-5 capillary column (0.53 mm × 30 m). The products were confirmed by GC-MS (QP-5050 model, M/s. Shimadzu Instruments, Japan) equipped with a DB-5 capillary column (0.32 mm dia. and 25 m long, M/s. J & W Scientific, USA).
Results and discussion
ICP-OES
To confirm the loading of vanadium, all the four V2O5/SBA-15 catalysts were analyzed by ICP-OES and the data are displayed in the parenthesis against each catalyst viz., 5V2O5/SBA-15 (4.9 wt%), 7.5V2O5/SBA-15 (8.5 wt%), 10V2O5/SBA-15 (10.7 wt%) and 12.5V2O5/SBA-15 (12.8 wt%).
X-Ray diffraction
To assess the mesoporous nature of V2O5/SBA-15 catalysts including SBA-15, low angle XRD analysis was carried out and the obtained patterns are shown in Fig. 1. The parent SBA-15 exhibited three well-resolved peaks at 2θ = 0.96, 1.65 and 1.90° indexed as (100), (110) and (200) reflections, characteristic of two-dimensional (2D) hexagonal mesostructures with the p6mm space group. Similar to SBA-15, V2O5/SBA-15 catalysts also exhibited three diffraction peaks positioned at 0.91–0.96°, 1.57–1.69°, and 1.81–1.95°, revealing the retention of the well ordered mesoporous nature of SBA-15 in all the prepared V2O5/SBA-15 catalysts.
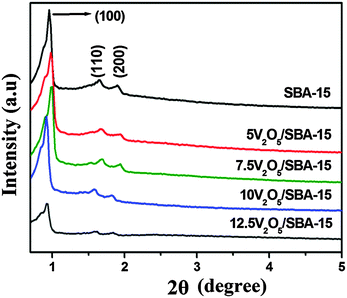 |
| Fig. 1 Low-angle XRD patterns of SBA-15 and V2O5/SBA-15 catalysts. | |
To evaluate the crystalline behaviour of the vanadium oxide species dispersed on the surface of the SBA-15 support, the V2O5/SBA-15 catalysts were characterized by wide-angle XRD in the 2θ range of 10–80° (Fig. 2). A broad peak that appears in all the patterns at 2θ ≈ 22° is responsible for the SiO2 phase of SBA-15. The absence of the characteristic V2O5 XRD peaks at all the loadings of V2O5/SBA-15 catalysts may be due to higher dispersion of nanovanadium oxide with crystallite size less than 5 nm (XRD detection limit) or its presence on SBA-15 as the amorphous phase.
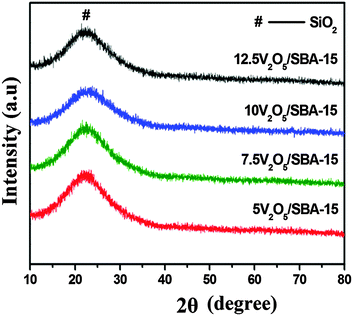 |
| Fig. 2 Wide-angle XRD patterns of various V2O5/SBA-15 catalysts. | |
N2-physisorption studies
Fig. 3 shows the V2O5/SBA-15 catalysts together with the parent SBA-15 and are characterized by N2 adsorption–desorption measurements. The isotherms obtained for the parent SBA-15 and V2O5/SBA-15 catalysts are of type IV in nature with H1 hysteresis loop and the well defined step due to capillary condensation in the range of 0.6–0.8 p/p0 in accordance with the IUPAC classification is the typical nature of ordered mesoporous materials with cylindrical pores in a narrow pore size distribution. All V2O5/SBA-15 catalysts show hysteresis loops similar to that of the parent SBA-15, implying the retention of the mesophase structure.
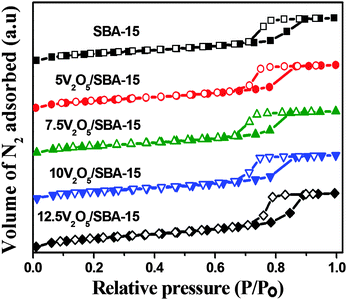 |
| Fig. 3 N2 adsorption–desorption isotherms of SBA-15 and various V2O5/SBA-15 catalysts. | |
The structural and textural parameters are summarized in Table 1. The specific surface area and total pore volume of parent SBA-15 decreased as the loading of the active V2O5 component increased, which is ascertained from the partial blockage of pore mouths. The marginal increment in the surface area in the case of higher loading catalysts such as 10V2O5 and 12.5V2O5 catalysts may be due to the segregation of certain particulates of the V2O5 phase.25Fig. 4 shows the pore size distribution curves of V2O5/SBA-15 catalysts, which reveal that most of the pores are distributed in the range of 6–10 nm.
Table 1 Textural and structural parameters of V2O5/SBA-15 catalysts from N2 sorption data and low angle XRD analysis
Catalyst |
S
BET
(m2 g−1) |
V
t
(cm3 g−1) |
D
(nm) |
d
100
(nm) |
a
0
(nm) |
t
(nm) |
BET surface area.
Total pore volume.
BJH average pore diameter.
Periodicity of the (100) plane.
Unit cell length (a0 = 2d(100)/√3).
Pore wall thickness (t = a0 − DBJH).
|
SBA-15 |
762 |
1.19 |
8.14 |
9.18 |
10.6 |
2.4 |
5V2O5/SBA-15 |
538 |
0.84 |
7.95 |
9.01 |
10.4 |
2.4 |
7.5V2O5/SBA-15 |
511 |
0.80 |
7.10 |
8.95 |
10.3 |
3.2 |
10V2O5/SBA-15 |
546 |
0.85 |
7.91 |
9.65 |
11.1 |
3.2 |
12.5V2O5/SBA-15 |
625 |
1.04 |
7.99 |
9.46 |
10.9 |
2.9 |
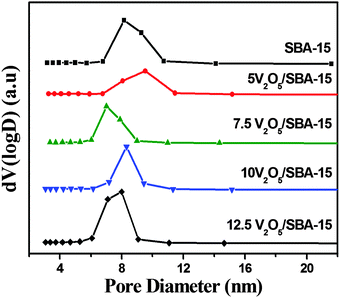 |
| Fig. 4 Pore size distribution curves of various V2O5/SBA-15 catalysts. | |
FT-Raman spectroscopy
Raman spectroscopy is a very interesting characterization tool as it is very sensitive to the presence of crystals; even if in XRD, V2O5 crystallites are not seen, FT-Raman would give typical bands of these crystals. Fig. 5 shows the laser Raman spectra ranging from 1200 cm−1 to 200 cm−1 of all the samples. A clear band at 1036 cm−1 is attributed to the symmetric V
O stretching vibrations of the isolated distorted vanadium tetrahedron (VO4) species26 in a well dispersed way. The absence of a typical band at 995 cm−1 in spectra a–c implies that no crystalline V2O5 was observed in all the samples, which indicates that V2O5 is highly dispersed in the mesoporous silica-based SBA-15 catalyst and is well supported by wide-angle XRD results. However, a shoulder peak at 995 cm−1 in the spectra of sample d indicates the formation of V2O5 species of crystalline and/or microcrystalline nature that may result in the decrease in catalytic activity. The increase in the intensity of the weak band at 915 cm−1 with an increase in vanadium loading is characteristic of Si(–O−)2 functionalities corresponding to the perturbation in silica vibrations indicating the formation of V–O–Si bands. The bands at 702, 523 and 271 cm−1 are assigned to VOx clusters.26d The bands at 462 cm−1 can be assigned to the cyclic tetrasiloxane rings of the silica support, and the weaker bands appeared at 640 and 826 cm−1 are attributed to the cyclic trisiloxane rings and the symmetrical Si–O–Si stretching mode, respectively.27
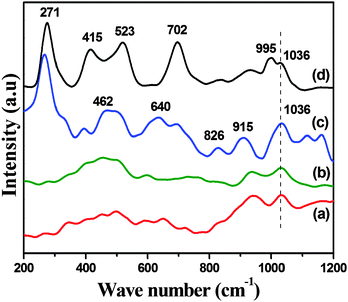 |
| Fig. 5 Raman spectra of (a) 5V2O5/SBA-15, (b) 7.5V2O5/SBA-15, (c) 10V2O5/SBA-15 and (d) 12.5V2O5/SBA-15 catalysts. | |
TEM analysis
The TEM image (Fig. 6) of the 10V2O5/SBA-15 catalyst gives direct observation about the structural investigations of V2O5 nanoparticles, which are highly and uniformly dispersed inside the pore channels of SBA-15. The particle size distribution (PSD) bar graph as inset reveals that the V2O5 particles are of around 5.5 nm size of peak maxima.
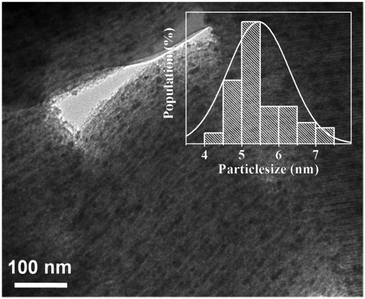 |
| Fig. 6 TEM image of the 10V2O5/SBA-15 catalyst and particle size distribution as inset. | |
UV-Vis-DR spectra
The room temperature UV-Vis-DR spectra of pure V2O5 and calcined V2O5/SBA-15 samples, additionally dried at 200 °C directly before the measurement, are presented in Fig. 7. The wide band between 240 and 300 nm observed for the 5V2O5/SBA-15, 7.5V2O5/SBA-15, 10V2O5/SBA-15 and 12.5V2O5/SBA-15 samples could be assigned to the V5+ species in four fold coordination state of highly dispersed V2O5 species on the support surface, which were also detected by FT-Raman measurements. The additional peak in the range of 350–400 nm confirms the V5+ species in six fold coordination state and corresponds to the low polymerized V chains or/and domains with the V5+ species in square pyramidal configuration. The relative intensity of the band at 380 nm increased due to hydration of the V5+ species in tetrahedral coordination. However, even at the highest 12.5V2O5/SBA-15 loading, the absorption above 470 nm was not observed as in the case of pure V2O5, and therefore the absence of the microcrystalline V2O5 species in the studied catalysts was concluded.
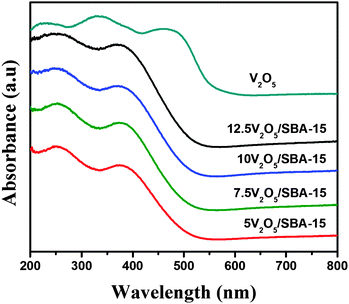 |
| Fig. 7 UV-Vis-DR spectra of V2O5 and various V2O5/SBA-15 catalysts. | |
Temperature programmed reduction
Temperature programmed reduction reveals the reducibility and stability of the metal/metal oxide supported catalysts and even the surface distribution of different loadings of metal species. The comparative TPR profiles of all the V2O5/SBA-15 samples between 100 and 800 °C with increasing vanadium loadings are shown in Fig. 8. For SBA-15 supported samples with V loadings from 5.0 to 10.0 wt%, the reduction temperature maximum in between 450 and 500 °C is attributed to the reduction of highly dispersed tetrahedral monomeric V2O5 species. An additional reduction temperature maximum in 10V2O5/SBA-15 at 600 °C corresponds to the partially occluded tetrahedral V2O5 species by surface silica. In the case of 12.5V2O5/SBA-15 with high V content, the main peak becomes broader, shifted around 450 °C and the reduction temperature maximum shifted to a higher temperature 658 °C, suggesting that the polymeric vanadium species are deposited on the high-surface area SBA-15 support that might be more difficult to reduce than the isolated vanadium species under the TPR conditions. However, the smaller integral peak area of 10V2O5/SBA-15 than 12.5V2O5/SBA-15 and the progressive shift of the maximum of the H2 consumption peak to high temperature with the V loading suggest a progressive formation of less reducible high polymeric vanadium species which is also confirmed by a shoulder peak around 995 cm−1 in Raman spectra.
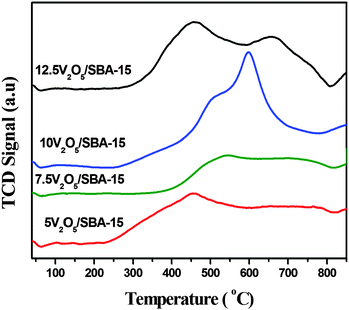 |
| Fig. 8 H2-TPR profiles of various V2O5/SBA-15 catalysts. | |
SEM-EDX spectrum
The morphology of the 10V2O5/SBA-15 catalyst was confirmed by SEM analysis (the inset of Fig. 9) and EDX elemental mapping confirms the presence of nanovanadium species (Fig. 9).
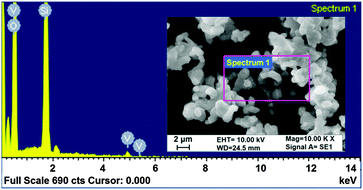 |
| Fig. 9 SEM image of the 10V2O5/SBA-15 catalyst as inset in its EDX spectrum. | |
Reaction scheme
Despite the formation of several products such as 2,3,5-trimethylhydroquinone (TMHQ), 2-hydroxy-3,5,6-trimethyl-1,4-benzoquinone (HTMBQ) and 2,3,6-trimethyl-4-(2,3,5-trimethylphenoxy)phenol in the TMP oxidation (shown in Scheme 1), selective formation of TMBQ is the present challenging task. To complete the task successfully, reaction parameters are systematically investigated.
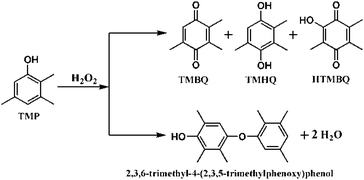 |
| Scheme 1 Possibility of products in 2,3,5,-trimethylphenol oxidation. | |
Catalytic activity results
In our initial experiments, the influence of V2O5 loading on SBA-15 has been investigated using 50 mg of catalyst, 3 mmol of H2O2 (30% aqueous solution) and 1 mmol of TMP in EtOH (2 ml) at room temperature for 1 h. A gradual increment in the conversion of TMP and selectivity of TMBQ with an increase in V2O5 loading on SBA-15 was observed, which can be seen in Table 2. It seems that the formation of uniform sized particles of V2O5 and their isolated distribution on the high surface area SBA-15 are responsible for the gradual increment in activity with increase in V2O5 loading. Among the different V2O5 loading catalysts, the 10V2O5/SBA-15 catalyst achieved good TMP conversion (63%) and TMBQ yield (49%), which seems to be the optimum loading catalyst. The catalytic activity of bulk V2O5 was evaluated (Table 2) and it was found to be inferior compared to present V2O5/SBA-15 nanocatalysts (Table 2).
Table 2 Effect of various wt% loadings of V2O5 over SBA-15 supported catalysts in the oxidation of TMP
Loading (wt%) |
TMP conv. (%) |
TMBQ yield (%) |
TMHQ yield (%) |
Bulk V2O5 |
15 |
11 |
04 |
5V2O5/SBA-15 |
22 |
15 |
07 |
7.5V2O5/SBA-15 |
50 |
34 |
16 |
10V2O5/SBA-15 |
63 |
49 |
14 |
12.5V2O5SBA-15 |
66 |
47 |
19 |
Other reaction parameters are optimized using the 10V2O5/SBA-15 catalyst. With increase in the 30% H2O2 to TMP molar ratio, from 2 to 3, the TMP conversion and TMBQ yield were increased from 54 to 63% and 41 to 49% that might be due to higher availability of oxidant molecules. A high TMP conversion of 75% with the TMBQ yield of 64% was achieved at an oxidant to reactant mole ratio of 4. However, with a further increase in the amount of 30% H2O2, i.e., 4 to 5 mmol, no significant changes in the activity have been noticed. Hence, the optimum oxidant to substrate mole ratio is 4.
The influence of solvents was investigated, using different solvents and the results are shown in Table 3, which, reveals that EtOH is the best solvent compared to others.
Table 3 Effect of solvents in the oxidation of TMP over 10V2O5/SBA-15
Solvent |
TMP conv. (%) |
TMBQ yield (%) |
TMHQ yield (%) |
Toluene |
05 |
03 |
02 |
Chloroform |
10 |
07 |
03 |
Dichloromethane |
13 |
05 |
08 |
Neat |
19 |
11 |
08 |
Acetonitrile |
62 |
48 |
14 |
Ethanol |
75 |
64 |
11 |
The effect of the amount of 10V2O5/SBA-15 catalyst on the oxidation of TMP was studied using different amounts of the catalyst viz., 25, 50, 75 and 100 mg. With the increase in the amount of catalyst from 25 to 50 mg, augmentation in the TMP conversion from 68 to 75% and the TMBQ yield from 55 to 64% was observed. When 75 mg catalyst was used, the TMP conversion was raised to 87% with the TMBQ yield 78%. No significant changes either in the conversion or in the selectivity were observed beyond 75 mg of catalyst. Hence, the optimum amount of catalyst is 75 mg.
To understand the nature of 10V2O5/SBA-15 towards the oxidation of TMP with reaction time, four different experiments were conducted and the results are displayed in Table 4. In the first half-an-hour experiment, the TMP conversion is 72% with the yield of TMBQ and TMHQ of 62 and 10%. In the 1 h experiment, the TMP conversion has been increased to 87% and TMBQ yield increased to 78%. A similar hike in activity has been observed in the 1.5 h experiment, wherein the TMP conversion has been increased to 94% and the TMBQ yield is increased to 89%. Notably, there was a decrease in the TMHQ yield from 09 to 05% with 1 to 1.5 h, which indicates the transformation of initially formed TMHQ to TMBQ product. Furthermore, in the 2 h experiment, we obtained the maximum TMP conversion of 99% and TMBQ yield of 95%.
Table 4 Effect of time in the oxidation of TMP over 10V2O5/SBA-15 catalyst
Time (h) |
TMP conv. (%) |
TMBQ yield (%) |
TMHQ yield (%) |
0.5 |
72 |
62 |
10 |
1.0 |
87 |
78 |
09 |
1.5 |
94 |
89 |
05 |
2.0 |
99 |
95 |
04 |
To test the heterogeneity of the catalyst, the TMP oxidation reaction was conducted using 10V2O5/SBA-15 as a catalyst and 30% H2O2 as an oxidant at room temperature for 1 h, and then the reaction was stopped, the catalyst was separated from the reactant/product mixture and the reaction was continued further for 1, 2 and 3 h. No progress in the reaction after removing the catalyst was observed, revealing the absence of catalyst leaching, and proving that the reaction is in the heterogeneous mode.
To evaluate the reusability of the catalyst, a series of recycling experiments were conducted under optimised conditions and the results are depicted in Fig. 10, which reveals that there is no significant loss of catalytic activity on TMP oxidation up to 4 repeated cycles.
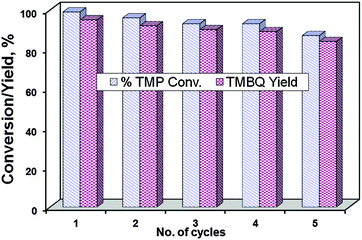 |
| Fig. 10 Recyclability of the 10V2O5/SBA-15 catalyst. | |
The present catalytic system, V2O5/SBA-15 prepared by the MDD method, is found to be a good catalyst for the oxidation of TMP to TMBQ at room temperature with 95% yield of TMBQ in the presence of green 30% H2O2 oxidant with eco-friendly ethanol solvent in 2 h. A similar high activity catalyst has also been reported, but at a higher temperature. Kholdeeva and his co-workers contributed a lot for the oxidation of TMP to TMBQ over different catalysts such as mesostructured Ti-MMM28 and TiO2–SiO2 aerogels.29 The yield of TMBQ is 82% on both of these catalysts and the hydrolytic instability of these catalysts is observed. In the subsequent studies, the same group improved the thermal stability as well as the catalytic activity up to 95% yield (at 80 °C in acetonitrile solvent).30–33 Very few reports are available on TMP oxidation at room temperature.34 Unfortunately, the above systems involve the usage of environmentally undesirable solvents and operation at elevated temperatures which are the drawbacks compared to the present study. In the present research contribution, the use of hazardous chemical waste, stoichiometric amounts of oxidants and catalysts, harmful solvents, high temperature operations linked to heating devices and electric power are avoided, which are the cutting-edge features of the present piece of work.
Conclusions
The molecular designed dispersion method yielded 4–7.5 nm sized V2O5/SBA-15 nanocatalysts, which are highly effective in the selective oxidation of trimethylphenol to trimethylbenzoquinone at room temperature and atmospheric pressure with green oxidant (30% H2O2) and eco-friendly ethanol solvent. The 10%V2O5/SBA-15 catalyst selectively oxidized trimethylphenol into trimethylbenzoquinone with 95% yield. The higher catalytic activities of V2O5/SBA-15 nanocatalysts are attributed to (i) uniform sized V2O5 nanoparticles and (ii) their isolated distribution on the mesopore surfaces of hexagonally ordered porous catalysts, which are effective in providing an intimate contact to the reactant molecules and a diffusion-free environment to the products.
Acknowledgements
Chinna Krishna Prasad acknowledges the Council of Scientific and Industrial Research (CSIR-UGC), New Delhi, for awarding research fellowship. The authors thank Dr R Nageswara Rao, Head Analytical Division, IICT, India, for their kind help with the ICP-OES analysis.
Notes and references
-
(a)
K. U. Baldenius, L. V. D. Bussche-Hnunefeld, E. Hilgemann, P. Hoppe and R. Sturmer, Ullmann's Encylopedia of Industrial Chemistry, VCH, Weinheim, 1996 Search PubMed;
(b) T. Dunlap, R. E. P. Chandrasena, Z. Wang, V. Sinha, Z. Wang and G. R. J. Thatcher, Chem. Res. Toxicol., 2007, 20, 1903 CrossRef CAS PubMed;
(c) T. Netscher, Vitam. Horm., 2007, 76, 155 CAS;
(d) T. Netscher, F. Mazzini and R. Jestin, Eur. J. Org. Chem., 2007, 1176 CrossRef CAS.
-
(a) H. Dau and I. Zaharieva, Acc. Chem. Res., 2009, 42, 1861 CrossRef CAS PubMed;
(b) C. Rein, P. Demel, R. A. Outten, T. Netscher and B. Breit, Angew. Chem., Int. Ed., 2007, 46, 8670 CrossRef CAS PubMed;
(c) A. Wildermann, Y. Foricher, T. Netscher and W. Bonrath, Pure Appl. Chem., 2007, 79, 1839 CrossRef CAS;
(d) W. Bonrath, M. Eggersdorfer and T. Netscher, Catal. Today, 2007, 121, 45 CrossRef CAS.
-
(a)
P. Schudel, H. Mayer and O. Isler, in The Vitamins, ed. W. H. Sebrell and R. S. Harris, Academic, New York, 1972, vol. 5, pp. 168–317 Search PubMed;
(b) W. Bonrath and T. Netscher, Appl. Catal., A, 2005, 280, 55 CrossRef CAS;
(c) O. A. Kholdeeva, O. V. Zalomaeva, A. B. Sorokin, I. D. Ivanchikova, C. Della Pina and M. Rossi, Catal. Today, 2007, 121, 58 CrossRef CAS;
(d) M. Eggersdorfer, D. Laudert, U. Letinois, T. McClymont, J. Medlock, T. Netscher and W. Bonrath, Angew. Chem., Int. Ed., 2012, 51, 12960 CrossRef CAS PubMed.
-
(a) H. Sun, K. Harms and J. Sundermeyer, J. Am. Chem. Soc., 2004, 126, 9550 CrossRef CAS PubMed;
(b) H. Sun, X. Li and J. Sundermeyer, J. Mol. Catal. A: Chem., 2005, 240, 119 CAS;
(c) K. Moller, G. Wienhofer, F. Westerhaus, K. Junge and M. Beller, Catal. Today, 2011, 173, 68 CrossRef.
-
(a) L. F. Tietze, K. M. Sommer, J. Zinngrebe and F. Stecker, Angew. Chem., Int. Ed., 2005, 44, 257 CrossRef CAS PubMed;
(b) G. Malaise, W. Bonrath, M. Breuninger and T. Netscher, Helv. Chim. Acta, 2006, 89, 797–812 CrossRef CAS;
(c) S. Bell, B. Wustenberg, S. Kaiser, F. Menges, T. Netscher and A. Pfaltz, Science, 2006, 311, 642 CrossRef CAS PubMed.
- H. Verhagen, B. Buijsse, E. Jansen and B. Bueno-de-Mesquita, Nutr. Today, 2006, 41, 244 CrossRef.
- V. A. Bushmilyev, T. A. Kondratyeva, M. A. Lipkin and A. V. Kondratyev, Khim.-Farm. Zh., 1991, 5, 65 Search PubMed , in Russian.
-
(a)
R. A. Sheldon and J. K. Kochi, ‘Metal Catalyzed Oxidations of Organic Compounds’, Academic Press, New York, 1981, p. 369 Search PubMed;
(b)
T. Isshiki, T. Yui, H. Uno and M. Abe, Eur. Pat., 0127888, 1984 Search PubMed;
(c)
R. Maasen, S. Krill and K. Huthmacher, Eur. Pat., 1132367, 2001 Search PubMed;
(d) K. Takehira, M. Shimizu, Y. Watanabe, H. Orita and T. Hayakawa, J. Chem. Soc., Chem. Commun., 1989, 1705 RSC.
-
L. Schuster and H. Pommer, DE, 1793183, 1968 Search PubMed.
-
(a) S. Ito, K. Aihara and M. Matsumoto, Tetrahedron Lett., 1983, 24, 5249 CrossRef CAS;
(b) F. Shi, M. K. Tse and M. Beller, Adv. Synth. Catal., 2007, 349, 303 CrossRef CAS;
(c) G. Wienhofer, K. Schroder, K. Moller, K. Junge and M. Beller, Adv. Synth. Catal., 2010, 352, 1615 CrossRef.
-
(a)
M. Shimizu, K. Takehira, T. Hayakawa and H. Orita, US. Pat., 5245059, 1993 Search PubMed;
(b)
M. Vandewalle, WO Pat., 18746, 1998 Search PubMed.
-
(a)
P. T. Anastas and J. C. Warner, Green Chemistry, Theory and Practice, Oxford University Press, Oxford, 1998 Search PubMed;
(b)
Green Chemistry, Frontiers in Benign Chemical Syntheses and Processes, ed. P. T. Anastas and T. C. Williamson, Oxford University Press, Oxford, 1998 Search PubMed;
(c)
J. Clark and D. Macquarrie, Handbook of Green Chemistry & Technology, Blackwell, MA, 2002 Search PubMed.
-
(a)
C. W. Jones, Applications of Hydrogen Peroxide and Derivatives, Royal Society of Chemistry, Cambridge, 1999 Search PubMed;
(b)
G. Strukul, Catalytic Oxidations with Hydrogen Peroxide as Oxidant, Kluwer Academic, Dordrecht, The Netherlands, 1992 Search PubMed.
-
(a) P. T. Tanev, M. Chibwe and T. J. Pinnavaia, Nature, 1994, 368, 321 CrossRef CAS PubMed;
(b)
M. Taramasso, G. Perego and B. Notari, U. S. Pat., 4 410 501, 1983 Search PubMed;
(c) B. Notari, Adv. Catal., 1996, 41, 253 CAS;
(d) S. Gontier and A. Tuel, Appl. Catal., A, 1994, 118, 173 CrossRef CAS.
- T. Hirao, Chem. Rev., 1997, 97, 2707 CrossRef CAS PubMed.
- P. R. Makgwane and S. S. Ray, Appl. Catal., A, 2015, 492, 10 CrossRef CAS.
- P. S. Sonawane, S. S. Haram, P. R. Lawate, L. P. Kale, A. A. Patil and P. S. Lokhande, Int. J. Nanomater. Chem., 2015, 1, 1 Search PubMed.
- R. Abazari, S. Sanati and L. A. Saghatforoush, Chem. Eng. J., 2014, 236, 82 CrossRef CAS.
- A. L. Ahmad, B. Koohestani, S. Bhatia and S. B. Ooi, Int. J. Appl. Ceram. Technol., 2012, 9, 588 CrossRef CAS.
- E. T. Drew, Y. Yang, J. A. Russo, M. L. Campbell, S. A. Rackley, J. Hudson, P. Schmuki and D. C. Whitehead, Catal. Sci. Technol., 2013, 3, 2610 CAS.
- D. P. Nair, T. Sakthivel, R. Nivea, J. S. Eshow and V. Gunasekaran, J. Nanosci. Nanotechnol., 2015, 15, 4392 CrossRef CAS PubMed.
-
(a) Y. Segura, P. Cool, P. Van Der Voort, F. Mees, V. Meynen and E. F. Vansant, J. Phys. Chem. B, 2004, 108, 3794 CrossRef CAS;
(b) S. Van Doorslaer, Y. Segura and P. Cool, J. Phys. Chem. B, 2004, 108, 19404 CrossRef CAS.
- D. Zhao, J. Feng, Q. Huo, N. Melosh, G. H. Fredrickson, B. F. Chmelka and G. D. Stucky, Science, 1998, 279, 548 CrossRef CAS PubMed.
-
(a) C. K. P. Neeli, S. Ganji, V. S. P. Ganjala, R. R. S. Kamaraju and D. R. Burri, RSC Adv., 2014, 4, 14128 RSC;
(b) C. K. P. Neeli, A. Narani, R. K. Marella, K. S. Rama Rao and D. R. Burri, Catal. Commun., 2013, 39, 5 CrossRef CAS;
(c) A. Narani, K. H. P. Reddy, S. Vinukonda, K. S. Rama Rao and D. R. Burri, Microporous Mesoporous Mater., 2011, 143, 132 CrossRef;
(d) S. Ganji, S. Mutyala, C. K. P. Neeli, K. S. Rama Rao and D. R. Burri, RSC Adv., 2013, 3, 11533 RSC.
- J. E. Herrera, J. H. Kwak, J. Z. Hu, Y. Wang and C. H. F. Peden, Top. Catal., 2006, 39, 245 CrossRef CAS.
-
(a) X. Gao, S. R. Bare, B. Meckhuysen and I. E. Wachs, J. Phys. Chem. B, 1998, 102, 10842 CrossRef CAS;
(b) G. T. Went, S. T. Oyama and A. T. Bell, J. Phys. Chem., 1990, 94, 4240 CrossRef CAS;
(c) S. T. Oyama, G. T. Went, K. B. Lewis, A. T. Bell and G. A. Somorijai, J. Phys. Chem., 1989, 93, 6786 CrossRef CAS;
(d) Y. Segura, P. Cool, P. Kustrowski, L. Chmielarz, R. Dziembaj and E. F. Vansant, J. Phys. Chem. B, 2005, 109, 12071 CrossRef CAS PubMed.
-
(a) C. Hess, J. D. Hoefelmeyer and T. Don Tilley, J. Phys. Chem., 2004, 108, 9703 CrossRef CAS;
(b) C. Hess, M. H. Looi, S. B. A. Hamid and R. Schlogl, Chem. Commun., 2006, 451 RSC;
(c) C. J. Brinker, R. Kirkpatrick, D. R. Tallant, B. C. Bunker and B. Montez, J. Non-Cryst. Solids, 1988, 99, 418 CrossRef CAS.
- N. N. Trukhan, V. N. Romannikov, E. A. Paukshtis, A. N. Shmakov and O. A. Kholdeeva, J. Catal., 2001, 202, 110 CrossRef CAS.
- O. A. Kholdeeva, I. D. Ivanchikova, M. Guidotti, N. Ravasio, M. Sgobba and M. V. Barmatova, Catal. Today, 2009, 141, 330 CrossRef CAS.
- O. A. Kholdeeva, M. S. Melgunov, A. N. Shmakov, N. N. Trukhan, V. V. Kriventsov, V. I. Zaikovskii, M. E. Malyshev and V. N. Romannikov, Catal. Today, 2004, 91–92, 205 CrossRef CAS.
- O. A. Kholdeeva, I. D. Ivanchikova, M. Guidotti and N. Ravasio, Green Chem., 2007, 9, 731 RSC.
- O. A. Kholdeeva, I. D. Ivanchikova, M. Guidotti, C. Pirovano, N. Ravasio, M. V. Barmatova and Y. A. Chesalov, Adv. Synth. Catal., 2009, 351, 1877 CrossRef CAS.
- I. D. Ivanchikova, M. K. Kovalev, M. S. Melgunov, A. N. Shmakov and O. A. Kholdeeva, Catal. Sci. Technol., 2014, 4, 200 CAS.
- I. D. Ivanchikova, N. V. Maksimchuk, R. I. Maksimovskaya, G. M. Maksimov and O. A. Kholdeeva, ACS Catal., 2014, 4, 2706 CrossRef CAS.
|
This journal is © The Royal Society of Chemistry and the Centre National de la Recherche Scientifique 2016 |
Click here to see how this site uses Cookies. View our privacy policy here.