Structure-controlled porous films of nanoparticulate Rh-doped SrTiO3 photocatalyst toward efficient H2 evolution under visible light irradiation†‡
Received
30th June 2015
, Accepted 3rd August 2015
First published on 7th August 2015
Abstract
Porous films of Rh-doped SrTiO3 (SrTiO3:Rh) were prepared on glass substrates as a visible light-responsive photocatalyst panel that can generate H2 efficiently under visible light irradiation. The films were prepared by simple screen-printing using the pastes of the fine particles (ca. 50 nm) of SrTiO3:Rh (WH-particles), which were prepared via a facile water-based process, followed by calcination at 500 °C. The use of WH-particles having relatively narrow size distribution allowed us to prepare homogeneous films with controlled thickness ranging from 1 to 10 μm, along with enough mechanical strength. On the other hand, the use of SrTiO3:Rh particles (SS-particles, ca. 300 nm) prepared by a conventional solid state reaction method resulted in inhomogeneous surfaces and exposure of the glass substrates when the thickness was below 3 μm. The SrTiO3:Rh films (WH-films) consisting of the fine particles exhibited much higher efficiency for H2 evolution from methanol aqueous solution under visible light than those prepared from the SS-particles (SS-films) at each thickness. The H2 evolution rate on WH-films increased to reach maximum value at 10 μm (3.2 μmol h−1) while those on SS-films saturated at a thinner thickness of 5 μm (0.7 μmol h−1), and was confirmed to be higher than those on the suspended system with the same amounts of WH-particles. Furthermore, the addition (10–20 wt%) of the large particles to the WH-films further increased the H2 evolution rate, probably due to the light scattering with large SS-particles, by which the neighboring small WH-particles in the films can effectively absorb the scattered light and generate more H2.
Introduction
Photocatalytic water splitting using semiconductors has attracted much attention as a technique that can produce hydrogen (H2) directly from water by harvesting abundant solar light.1 The design of photocatalytic systems that enable efficient utilization of a wide range of the solar light spectrum, especially in the visible region has become one of the cutting-edge research areas for achieving practically sufficient efficiency in solar hydrogen production, as well as in the development of semiconductor materials employed.2–4 So far, two types of semiconductor-based systems have been extensively studied for photo-induced water splitting: one is a heterogeneous system5–8 with suspended semiconductor particles and the other is a photoelectrochemical system8–10 with semiconductor photoelectrodes. The former suspended system has, however, some disadvantages in large-scale applications.11 Such heterogeneous systems undoubtedly require energy for keeping the semiconductor particles suspended in the solution, by means of mechanical stirring or gas-bubbling, and also required separation of particles for the recycling or replacing the used photocatalysts. Although these problems can be solved in the latter photoelectrochemical systems, in which semiconductor materials are generally fixed on substrates, other cost disadvantages come up to the surface, i.e., the costs for the conductive substrates (such as conductive glass or metals) and for the external circuit including power source. Photocatalyst panels, wherein semiconductor particles are fixed on an inexpensive substrate such as glass, will become candidates for a cost-effective and efficient water-splitting system, if they exhibit comparable (or higher) efficiency to those in conventional systems.11,12 Recently, Domen et al. demonstrated simultaneous evolution of H2 and O2 under UV-vis irradiation using photocatalyst panels of GaN–ZnO solid solution semiconductor prepared via a drop-casting or squeegee method.11 However, there are only a few reports on water splitting using such kinds of photocatalyst panels.11–13 Thus, detailed and systematic studies on photocatalyst panels are highly desired to evaluate their feasibility by examining the influences of various factors such as the types of semiconductors and the structure of films on the performance. It is expected that high-performance photocatalyst panels should have both the controlled structures for efficient light absorption and the controlled pores allowing efficient reaction and transportation of substances. However, such well-designed panels are generally difficult to be fabricated by using the semiconductor particles prepared via conventional synthesis processes such as the solid-state (SS) reaction, in which large and inhomogeneous particles are generally produced.14 The use of semiconductor particles having well-controlled particle sizes, specifically in nano to submicron regions, is highly desirable for fabricating such well-designed photocatalyst panels; the use of such fine particles will be also beneficial to ensure the mechanical strength of the panels by forming good adhesion.15
We have recently reported a facile synthesis of the fine particles of Rh-doped SrTiO3 (SrTiO3:Rh) semiconductor, which is well known as one of the promising materials of visible light-responsive photocatalyst for H2 production,16–26via a newly-developed water-based hetero-chelate method using a stable aqueous titania sol27 as a precursor with other metal salts.28 The prepared SrTiO3:Rh particles possessed a homogeneous and small particle size (ca. 50 nm) and exhibited significantly high efficiency for H2 evolution from aqueous methanol solution under visible light irradiation (ca. 13.3% of quantum efficiency at 420 nm).28 These findings have motivated us to apply the SrTiO3:Rh fine particles as a model photocatalyst to the fabrication of photocatalyst panels that can efficiently generate H2 under visible light. In this paper, we attempted to prepare the porous SrTiO3:Rh films having both the controlled thickness and pores from the nanoparticulate SrTiO3:Rh by means of simple screen-printing, and applied them for photocatalytic H2 production under visible light.
Experimental
Materials
Titanium(IV) tetraisopropoxide (TIPT) (95.0%), acetylacetone (acac) (99.0%), acetic acid (AcOH) (99.7%), strontium acetate hemihydrate (Sr(OAc)2·0.5H2O), rhodium(III) chloride trihydrate (RhCl3·3H2O), lactic acid (85.5–94.5%), Rh2O3, α-terpineol, 2-(2-butoxyethoxy)ethanol and poly(vinyl butyral) were purchased from Wako Pure Chemical Industries, Ltd., Osaka, Japan. Acrylic emulsion (VONCOAT (EC-905EF), particle size: 100–150 nm) was purchased from DIC Corporation. TiO2 (99.9%) was purchased from Soekawa Chemical. SrCO3 (99.9%) was purchased from Kanto Chemical. All reagents were used as received, and all the experiments were carried out under ambient conditions without eliminating the moisture from the atmosphere.
Preparation of SrTiO3:Rh films
The particles of SrTiO3:Rh(2%) were prepared via the water-based hetero-chelate method (WH-method), which was recently developed by our group,28 using a stable titania sol27 as a precursor. The aqueous titania sol (AA-sol) was prepared by mixing TIPT, an aqueous solution of acac, and an aqueous solution of AcOH.27 The AA-sol was mixed with an aqueous solution containing both Sr(OAc)2 (1.08 mol L−1) and lactic acid (2.16 mol L−1) and an aqueous solution of RhCl3 (0.24 mol L−1) at a ratio of Sr
:
Ti
:
Rh = 1.02
:
0.98
:
0.02, and stirred for 1 hour at room temperature, yielding an orange transparent sol. To the sol was added an acrylic emulsion and it was stirred for 15 minutes at room temperature, then dried at 80 °C for 3 hours, and finally calcined at 1000 °C for 10 hours, yielding SrTiO3:Rh (Rh: 2%) powdered samples (these samples are denoted as WH-particles). For comparison, SrTiO3:Rh(2%) particles were also prepared via the solid state reaction method (SS-method) using TiO2, SrCO3 and Rh2O3 as raw materials, and calcination at 1000 °C for 10 hours (these samples will be denoted by SS-particles) followed. Although some reports have suggested that the addition of excess Sr in the preparation of SrTiO3-based particles via the SS-method is effective to obtain more active photocatalyst samples, we confirmed that the SrTiO3:Rh particles prepared via the SS-method with excess amount of Sr (Sr/(Ti + Rh) = 1.03, for example) showed almost same rate of H2 evolution as that on the sample prepared with the stoichiometric ratio.28 Thus, in the present study, the SrTiO3:Rh particles prepared via the SS-method with stoichiometric ratio (Sr:(Ti + Rh) = 1) was employed as the almost best SS-sample for fabricating SrTiO3:Rh films for comparison. As an effective cocatalyst for water reduction, small amount (0.5 wt%) of platinum particles were loaded on all the samples by means of in situ photodeposition method.16,17,28
The SrTiO3:Rh(2%) films were prepared via a conventional screen printing method as follows. The WH- or SS-particles were first dispersed in a methanol solution and then dried at 80 °C for 5 min. After the dispersion process, the particles were mixed with organic compounds (α-terpineol: 2-(2-butoxyethoxy)ethanol: poly(vinyl butyral) = 60
:
15
:
25) as vehicles, yielding the paste of WH- or SS-particles (ca. 20 wt%) having an appropriate viscosity for screen-printing. The films were then prepared by screen-printing using the prepared pastes, followed by calcination in air at 500 °C for 30 min. To control the thickness, the screen-printing procedure was repeated (1–10 times) before calcination; the obtained films are denoted as WH- or SS-x where x (x = 1–10) indicates the number of print repetition. To obtain a thicker film having the same thickness as the WH-10 and SS-10 without repeating the printing process, another setup of screen-printing with a thicker screen was used. The obtained films are named WH-10′ and SS-10′.
Characterization of SrTiO3:Rh films
The obtained SrTiO3:Rh films were characterized by means of a scanning electron microscope (SEM, HITACHI, S-4100), and an X-ray diffraction instrument (XRD, PANalytical, X'Pert Pro, rotating anode diffractometer, 45 kV, 40 mA, Cu Kλ radiation). The photocatalytic activity of SrTiO3:Rh(2%) films was evaluated for H2 evolution from aqueous methanol solution under visible light irradiation, using a gas-closed circulation system equipped with a top-irradiation type reaction cell (Pyrex-made), in which the photocatalyst film was fixed horizontally in the solution. The light irradiation was carried out from the top of the reactor by a 300 W Xe-arc lamp (Perkin–Elmer, Cermax PE300BF) attached with a cut-off filter (Hoya; L42) to eliminate the UV light. The amounts of gas produced were analyzed and quantified by means of on-line gas chromatography (GL Science; GC-3200, TCD, Ar carrier, MS-5A column).
Results and discussion
Characterizations of SrTiO3:Rh films prepared via a screen-printing method
Fig. 1 and 2 show the SEM images of the films that were prepared via screen-printing with the pastes of SrTiO3:Rh(2%) particles followed by calcination at 500 °C for 30 min. The thickness of the films was controlled by changing the number of repetitions of screen-printing before calcination or by using another setup. The SEM images of WH-x films (“x” represents the number of repeats) revealed that the film thickness increased by ca. 1 μm with the increasing number of screen-printing repetition (see Fig. 1 and S1†). For example, the film thickness of WH-1, 3, 5 and 10′ were about 1, 3, 5 and 10 μm, respectively. In addition, all the WH-films exhibit flat surfaces.
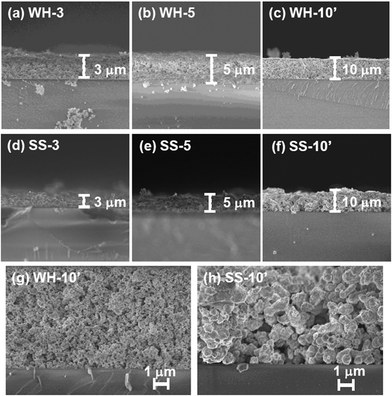 |
| Fig. 1 Cross-sectional SEM images of SrTiO3:Rh films (WH- and SS-films) with different thickness. | |
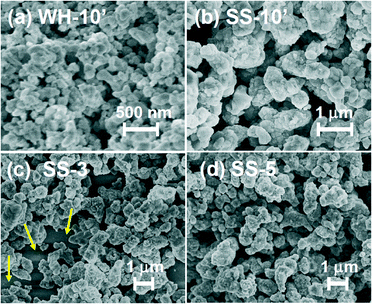 |
| Fig. 2 Surface SEM images of SrTiO3:Rh films (WH- and SS-films) with different thickness. Yellow arrowed lines show the uncovered parts of the substrate. | |
It was also confirmed that the WH-10′ film, which was prepared by using a thicker screen, possessed almost the same thickness (ca. 10 μm) as to that of WH-10 (see Fig. S1(e)†), indicating the availability of such thicker screen for fabricating thicker films without repetition of screen printing. The flat surface morphology and uniform increment in thickness are certainly due to the homogeneous and small size of WH-particles (ca. 50 nm, see Fig. S1†), which were prepared via a newly developed water-based procedure. On the other hand, the surfaces of SS-films, especially in the case of the thinner ones (SS-1, SS-3), were not smooth as seen in Fig. S2(d)† and Fig. 1(d), while the thickness actually increased roughly in proportion with the increasing number of the screen-printing. The inhomogeneous and large size of SS-particles (ca. 200–500 nm, see Fig. S3†) is undoubtedly one of the causes for the rough surfaces of SS-films. The magnified views of the cross-section revealed that both the WH-10′ and SS-10′ films have densely-packed porous structures (Fig. 1(g) and (h)). Fig. 2 shows the top-view SEM images of WH- and SS-films (x = 3, 5, 10′). All the WH-films exhibit smooth surfaces without exposing the glass substrates, even in the case of the thinner one (see Fig. S2(a)–(c)†). On the other hand, the uncovered parts of the substrate were clearly observed for the thinner SS-3 sample (see Fig. 2(c)), while the repeated printing improved the homogeneity to some extent (see SS-5, 10′ in Fig. 2(b) and (d)). These findings indicated the difficulty in preparing thin films with well-controlled structures from the SS-particles.
As clearly seen in the SEM images, the WH- and SS-films were composed of the SrTiO3:Rh particles whose primary particle sizes were almost the same as those of WH- or SS-particles (see Fig. S3†). The XRD patterns of WH- and SS-films showed a single phase of SrTiO3; no appreciable peaks attributed to an impurity phase were observed (Fig. 3). The diffuse reflectance spectra of WH- and SS-films (Fig. 4) were similar to those reported for SrTiO3:Rh particles.28 Two absorption bands were observed at around 420 nm and 580 nm, which are attributed to the transitions from the donor levels formed by the Rh3+ species to the conduction band (2.3 eV), and from the valence band to the acceptor levels formed by the Rh4+ species (1.7 eV), respectively. These results indicated that the particles contained in WH- and SS-films retained the physicochemical properties of the original WH- and SS-particles, even after the preparation process which was accompanied by final calcinations at 500 °C. As demonstrated above, the screen printing of the appropriate pastes of WH-particles which possess uniformly small size (ca. 50 nm), was proven as an effective way for fabricating porous films of SrTiO3:Rh with homogenous and controllable thickness ranging from 1 to 10 μm.
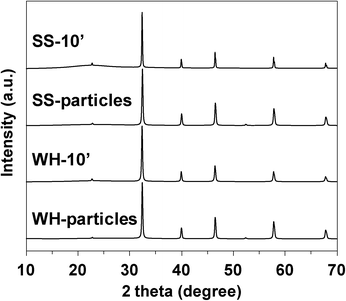 |
| Fig. 3 XRD patterns of SrTiO3:Rh films (WH- and SS-films) and particles (WH- and SS-particles). | |
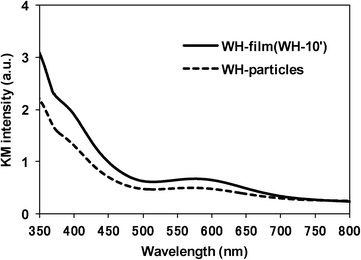 |
| Fig. 4 UV-vis spectra of SrTiO3:Rh films (WH-10′) and SrTiO3:Rh particles (WH-particles). | |
Photocatalytic H2 evolution from aqueous methanol solution under visible light on SrTiO3:Rh films
The photocatalytic activity of these SrTiO3:Rh(2%) films was evaluated for the H2 evolution from aqueous methanol solution under visible light irradiation (λ > 410 nm). As an effective co-catalyst for water reduction, 0.5 wt% of platinum particles were loaded on the WH-1000 or SS-1000 samples by means of an in situ photodeposition method28 prior to the preparation of the paste. All the WH- and SS-films showed photocatalytic activity for H2 evolution from aqueous methanol solution under visible light irradiation (λ > 410 nm) with almost steady rates. The time courses of H2 evolution on WH-10′ and SS-10′ are shown in Fig. 5; for example, the H2 evolution rate on WH-film was about 4 times higher than that on SS-film. During the reaction, the color of WH-film changed from gray to pale yellow (see Fig. S5†), indicating the photocatalytic reduction of Rh4+ species to Rh3+ by photo-excited electrons, as previously reported for SrTiO3:Rh particles.16,28 No appreciable release of particles from the substrate was observed for WH-10′ film after the reaction. On the other hand, the fraction of exposed surface of the substrate was appreciably increased in the SS-10′ film after the reaction, indicating that a part of the particles was detached from the substrate during the H2 evolution reaction (see Fig. S6†). Even the stirring of the solution in the dark resulted in a particle release from the SS-10′ film (not shown). These results indicated that the WH-films were mechanically more robust than the SS-films. The small particle sizes of WH-particles certainly allowed the sufficient contact among the particles in WH-film as well as the sufficient adhesion between the particles and the substrate.
 |
| Fig. 5 H2 evolution from an aqueous methanol solution under visible light irradiation over a SrTiO3:Rh film ((a) WH-10′ or (b) SS-10′). Conditions: 3 × 3 cm film; reactant solution, 100 mL of 10 vol% aqueous methanol solution; light source, 300 W Xe lamp with cut-off filters (λ > 410 nm). | |
Fig. 6 shows the dependence of film thickness on the H2 evolution rates. The rates of H2 evolution on the WH-films increased linearly with increasing thickness up to 5 μm and gradually increased to reach maximum value at 10 μm (3.2 μmol h−1). The rates of H2 evolution on SS-films increased with increasing film thickness, but saturated at a thinner thickness of 5 μm. Up to 5 μm, each WH-film showed nearly 4 times higher H2 evolution rates than the corresponding SS-films with the same thickness. As we recently reported, SrTiO3:Rh particles prepared by the present WH-method showed higher photocatalytic activity for H2 evolution than the SrTiO3:Rh particles prepared by the SS-method. Indeed, the present WH-particles, which were prepared at 1000 °C, showed ca. 4 times higher H2 evolution rates than SS-particles prepared at the same temperature.28 This finding strongly suggested that the higher photocatalytic activity of WH-particles dominantly contributed to the higher performance of WH-films for H2 production. It should also be noted that the H2 evolution rates of WH-films increased as the film thickness increased up to 10 μm, while those of SS-films saturated as the film thickness reached 5 μm. In the case of SS-film, large SS-particles (>300 nm) existing in the upper side certainly scattered back the incident photons partially, as well as absorbed, and consequently inhibited light penetration into the bottom part, resulting in the saturated rate of H2 evolution in the thicker films. In other words, a part of the particles in SS-films, especially those in the bottom side, is unable to absorb the incident photons. On the other hand, in the case of WH-films which consist of small WH-particles (ca. 50 nm), most of the particles effectively absorbed the light and functioned as photocatalyst due to the much less scattering of the incident light, and consequently afforded the enhanced H2 evolution with increasing thickness up to 10 μm, while further increase in thickness resulted in saturation because nearly all of the incident photons were absorbed within the films.
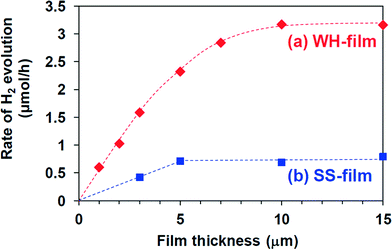 |
| Fig. 6 Rate of H2 evolution from an aqueous methanol solution under visible light irradiation over a SrTiO3:Rh film ((a) WH-film, (b) SS-film) having different thickness. Conditions: 3 × 3 cm film; reactant solution, 100 mL of 10 vol% aqueous methanol solution; light source, 300 W Xe lamp with cut-off filters (λ > 410 nm). | |
Influence of immobilization on the photocatalytic performance
To evaluate the influence of immobilization on the performance, we compared the H2 evolution rates on the films with those on the suspended particles. For example, the immobilization of the particles on substrates may lower the diffusion of the substances (e.g., water) and/or the products (e.g., H2 gas) inside the pores of the film and therefore may decrease the H2 evolution rate. The rates of H2 evolution using suspended WH- or SS-particles or fixed WH- or SS-T (T = 5, 10′) films are summarized in Fig. 7. The amounts of particles loaded on each film with a thickness of 5 and 10 μm were measured to be ca. 8 mg and 16 mg, respectively, regardless of the kind of particles (WH or SS). Thus, the same amounts of particles were used in the suspended system for comparison. Except for SS-10′, the films showed activity higher than the corresponding suspended systems employing the same amounts of photocatalyst particles. These results indicated that the SrTiO3:Rh particles immobilized on the films, especially in the case of WH-films, could absorb the light more efficiently than the suspended particles. The higher efficiency in the films were probably due to the more effective absorption of the photons by the neighboring particles in the densely packed film even if a part of the incident photons was scattered on the surface of the particles. On the other hand, in the suspended systems, a portion of the photons is scattered on the surface of the particles and then uselessly passed through the diluted suspension, resulting in efficiency lower than in the film systems. As for SS-10′, the light can be used only on the upper side because of significant light scattering due to the large particle size, resulting in the similar rate of H2 evolution with that on the suspension system. The higher H2 evolution rates in other films also implied that the diffusion of substances was not significantly lowered in the pores in the WH- and SS-films. However, the rates of gas evolution on the present SrTiO3:Rh films were still lower than those on general suspension systems for water splitting under visible light. The low evolution rates make it difficult to evaluate objectively the efficiency in the diffusion of substances and/or products in the present porous films. Thus, we prepared non-doped-SrTiO3 porous films (10 μm) that are expected to evolve H2 at rates much higher than the Rh-doped one, while the former required the irradiation of UV light. The non-doped-SrTiO3 particles were prepared via the same preparation procedure with that for Rh-doped-SrTiO3 (WH-) particles, except for the absence of Rh-salt, producing the non-doped-SrTiO3 having the same particles size (ca. 50 nm) with that of the Rh-doped one. As shown in Fig. S7,† the H2 evolution rate on the SrTiO3 porous film showed a rate (78 μmol h−1) much higher than that on the Rh-doped one (3.2 μmol h−1, under visible light). The H2 evolution rate on the SrTiO3 porous film was almost the same with that on the corresponding suspended particles, strongly suggesting that the diffusion of substances and/or products was not significantly lowered in the pores of the present SrTiO3 film systems, including the Rh-doped one, prepared via screen-printing.
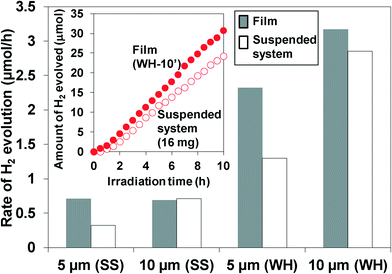 |
| Fig. 7 Rate of H2 evolution from an aqueous methanol solution under visible light irradiation on a WH/SS-x film (x = 5 or 10′) and from a SrTiO3:Rh-suspended system containing SrTiO3:Rh particles with the same amount as the film contains. Conditions: 3 × 3 cm film, 8 mg (5 μm) or 16 mg (10 μm) of particles; reactant solution, 100 mL of 10 vol% aqueous methanol solution; light source, 300 W Xe lamp with cut-off filters (λ > 410 nm). | |
Effect of adding the light scattering centers on the photocatalytic performance
As shown above, the combination of the screen-printing method with SrTiO3:Rh particles prepared via the WH-method enables the fabrication of porous SrTiO3:Rh film which possesses the capability of evolving H2 efficiently from aqueous methanol solution under visible light irradiation, in which the use of small WH-particle probably minimize the light scattering and enable the most of SrTiO3:Rh particles to absorb the incident light. However, very low scattering may result in the transmittance of a part of incident light without absorption in the WH-film. To solve the discrepancy between the light absorbance and scattering in the WH-film, we attempted to add a small amount of SS-particles of larger diameters which significantly scatter the light, into WH-particles, and this shows higher activity of H2 evolution. For example, for the improvement of the photon-to-current efficiency in the dye-sensitized solar cell (DSSC), small amounts of large TiO2 particles (>200 nm) that scatter the visible light are often added into the nanosized TiO2 particles which absorb large amount of dye molecules and conduct electricity efficiently.29–33 Thus, we expect that a part of the incident visible light is scattered by the large SS-particles and subsequently absorbed by small WH-particles, resulting in more efficient utilization of the incident light. We prepared films by screen-printing using the paste composed of WH- and SS-particles of various ratios. The fractions of SS-particles, X, were 0, 10, 20, and 30 wt%. The resulting films are denoted as (WH + X-SS) hereafter. As shown in the SEM image of (WH + 20-SS), for example, SS-particles were dispersed in the film homogeneously (see Fig. S8†). Fig. 8 shows the relationship between the ratios of SS-particles added and the H2-evolution rate on the films with different thickness. The rate of H2 evolution in every thickness increased with increasing amounts of SS-particles up to 20 wt%, but decreased with further addition. If the WH- and SS-particles act independently as photocatalysts, the H2 evolution rates should be a simple sum of each contribution of WH- and SS-particles, as shown in Fig. 8 as dotted lines. However, the H2 evolution rates on the composite films were higher than the estimated values and also higher than those on pure WH-films. We also prepared the composite films (10 μm) in which SS-particles (10 wt%) exist only at the bottom side, for comparison. The H2 evolution rate on this film was higher than the estimated value (see Fig 8, open triangle), but lower than that on the composite film in which the SS-particles were dispersed homogeneously. These results strongly suggested that the composite films could use incident light more efficiently due to the light scattering by large SS-particles added into the films. The large SS-particles might also improve the diffusion of the substrates by forming larger pores in the film, as suggested in the previous report on the photocatalyst panel of GaN-ZnO particles added with large SiO2 particles (a few μm size).11
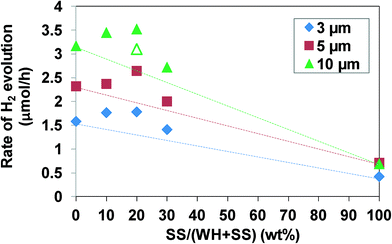 |
| Fig. 8 Plots of the H2 evolution rate from an aqueous methanol solution on films prepared with a mixture of WH- and SS-particles under visible light irradiation against the ratio of SS particles over the sum of WH- and SS-particles (weight%). Filled triangle, filled square, and filled diamond show films with 3, 5, and 10 μm-thickness. Open triangle shows a layered film consisted of WH-particles (80 wt%) over SS-film (20 wt%). The dashed lines indicate the expected rate based on the rates with pure WH- and SS-films. Conditions: 3 × 3 cm film; reactant solution, 100 mL of 10 vol% aqueous methanol solution; light source, 300 W Xe lamp with cut-off filters (λ > 410 nm). | |
Conclusion
In the present study, we attempt to fabricate photocatalyst panels which can efficiently generate H2 under visible light by employing highly active SrTiO3:Rh fine particles prepared via a water-based hetero-chelate method. The combination of the fine particles and the screen-printing method enabled us to precisely control the thickness (1 to 10 μm) of the porous films with enough mechanical strength after calcination (500 °C) in air, whereas the use of large particles prepared via a conventional solid state reaction method resulted in inhomogeneous and uncontrollable thickness. The porous SrTiO3:Rh films prepared with fine particles exhibited an almost linear increase in H2 evolution rate with increasing film thickness up to 5 μm and gradually increased to reach maximum value at 10 μm; the H2 evolution rates on the films (5 and 10 μm) were higher than those on the suspended system using the same amounts of photocatalyst particles. These results indicate that the present photocatalyst panels, as assembled in a 2-D structure, can effectively utilize the incident light comparable to the conventional suspension systems. Efficient H2 production on these panels also suggested that the transfer of substance and products was not significantly inhibited within the porous films. Moreover, the improvement of H2 evolution rate by adding light scattering media (large SrTiO3:Rh particles) provides an effective strategy for achieving highly efficient photocatalysis in the fixed panels. Our concept of constructing highly active porous structure with fine photocatalyst particles via a simple screen-printing method provides the possibility of large-scale application of photocatalyst panels for practical splitting of water under solar light.
Notes and references
- A. Fujishima and K. Honda, Nature, 1972, 238, 37–38 CrossRef CAS PubMed.
- K. Maeda and K. Domen, J. Phys. Chem. C, 2007, 111, 7851 CAS.
- A. Kudo and Y. Miseki, Chem. Soc. Rev., 2009, 38, 253–278 RSC.
- F. E. Osterloh, Chem. Mater., 2008, 20, 35–54 CrossRef CAS.
- A. Kudo, Mater. Res. Bull., 2011, 36, 32–38 CrossRef CAS.
- R. Abe, Bull. Chem. Soc. Jpn., 2011, 84, 1000–1030 CrossRef CAS.
- K. Maeda, ACS Catal., 2013, 3, 1486–1503 CrossRef CAS.
- R. Abe, J. Photochem. Photobiol., C, 2010, 11, 179–209 CrossRef CAS.
- T. Hisatomi, J. Kubota and K. Domen, Chem. Soc. Rev., 2014, 43, 7520 RSC.
- F. E. Osterloh, Chem. Soc. Rev., 2013, 42, 2294 RSC.
- A. Xiong, G. Ma, K. Maeda, T. Takata, T. Hisatomi, T. Setoyama, J. Kubota and K. Domen, Catal. Sci. Technol., 2014, 4, 325–328 CAS.
- B. Pinaud, J. Benck, L. Seitz, A. Forman, Z. Chen, T. Deutsch, B. James, K. Baum, G. Baum, S. Ardo, H. Wang, E. Miller and T. Jaramillo, Energy Environ. Sci., 2013, 6, 1983 CAS.
- Q. Wang, Y. Li, T. Hisatomi, M. Nakabayashi, N. Shibata, J. Kubota and K. Domen, J. Catal., 2015, 328, 308–315 CrossRef.
- K. Takanabe and K. Domen, ChemCatChem, 2012, 4, 1485 CrossRef CAS.
- C. Agrafiotis and A. Tsetsekou, J. Eur. Ceram. Soc., 2000, 20, 815–824 CrossRef CAS.
- R. Konta, T. Ishii, H. Kato and A. Kudo, J. Phys. Chem. B, 2004, 108, 8992–8995 CrossRef CAS.
- H. Kato, M. Hori, R. Konta, Y. Shimodaira and A. Kudo, Chem. Lett., 2004, 33, 1348–1349 CrossRef.
- H. Kato, Y. Sasaki, A. Iwase and A. Kudo, Bull. Chem. Soc. Jpn., 2007, 80, 2457–2464 CrossRef CAS.
- Y. Sasaki, A. Iwase, H. Kato and A. Kudo, J. Catal., 2008, 259, 133–137 CrossRef CAS.
- Y. Sasaki, H. Nemoto, K. Saito and A. Kudo, J. Phys. Chem. C, 2009, 113, 17536–17542 CAS.
- A. Iwase, Y. H. Ng, Y. Ishiguro, A. Kudo and R. Amal, J. Am. Chem. Soc., 2011, 133, 11054–11057 CrossRef CAS PubMed.
- H. Kato, Y. Sasaki, N. Shirakura and A. Kudo, J. Mater. Chem. A, 2013, 1, 12327–12333 CAS.
- Y. Sasaki, H. Kato and A. Kudo, J. Am. Chem. Soc., 2013, 135, 5441 CrossRef CAS PubMed.
- S. S. K. Ma, K. Maeda, T. Hisatomi, M. Tabata, A. Kudo and K. Domen, Chem. – Eur. J., 2013, 19, 7480–7486 CrossRef CAS PubMed.
- Q. Jia, A. Iwase and A. Kudo, Chem. Sci., 2014, 5, 1513–1519 RSC.
- Q. Wang, T. Hisatomi, S. S. K. Ma, Y. Li and K. Domen, Chem. Mater., 2014, 26, 4144–4150 CrossRef CAS.
- S. Okunaka, H. Tokudome, Y. Hitomi and R. Abe, J. Mater. Chem. A, 2015, 3, 1688–1695 CAS.
- S. Okunaka, H. Tokudome, Y. Hitomi and R. Abe, J. Mater. Chem. A, 2015, 3, 14794–14800 CAS.
- C. J. Barbè, F. Arendse, P. Comte, M. Jirousek, F. Lenzmann, V. Shkolver and M. Grätzel, J. Am. Ceram. Soc., 1997, 80(12), 3157–3171 CrossRef.
- T. G. Deepak, G. S. Anjusree, S. Thomas, T. A. Arun, S. V. Nair and A. S. Nair, RSC Adv., 2014, 4, 17615–17638 RSC.
- A. Usami, Chem. Phys. Lett., 1997, 277, 105 CrossRef CAS.
- S. Hore, C. Vatter, R. Kern, H. Smit and A. Hinsch, Sol. Energy Mater. Sol. Cells, 2006, 90, 1176 CrossRef CAS.
- J.-K. Lee, B.-H. Jeong, S. J. Y.-G. Kim, Y.-W. Jang, S.-B. Lee and M.-R. Lim, J. Ind. Eng. Chem., 2009, 15, 724 CrossRef CAS.
Footnotes |
† Electronic supplementary information (ESI) available: UV-vis spectrum, SEM images, photocatalytic H2 evolving reaction data. See DOI: 10.1039/c5cy00979k |
‡ The authors have a patent application (international application number: WO2014203996A) on a part of this work. |
|
This journal is © The Royal Society of Chemistry 2016 |
Click here to see how this site uses Cookies. View our privacy policy here.