DOI:
10.1039/C5RA21016J
(Paper)
RSC Adv., 2015,
5, 92947-92953
A facile dip-coating approach to stable superhydrophobic SiO2/epoxy resin membrane preparation for micro-water separation in transformer oil liquids†
Received
29th August 2015
, Accepted 14th October 2015
First published on 26th October 2015
Abstract
In this study, a facile one-step dip-coating approach was reported for superhydrophobic membrane fabrication, in which only epoxy resin and silica nanoparticles were needed. In addition, the surface microstructure and wettability of the membrane were closely related to the content of silica nanoparticles. When the content of silica nanoparticles was 4 wt%, the membrane exhibited optimum surface roughness and superhydrophobicity, by which water was blocked, while oil was allowed to permeate. Through the application of water contact angle, scanning electron microscopy, energy dispersive spectroscopy, thermal gravimetric analysis and Karl Fischer moisture titrator measurements, the membrane examination indicated that the micro/nanostructures enhanced the water repellency, which was similar to the lotus leaf effect. Furthermore, this method is suitable for large-scale production and employed for micro-water separation in transformer oil. This is possible because environmentally friendly and inexpensive materials are adopted and harsh operations, sophisticated equipment and a special atmosphere are avoided.
1. Introduction
In recent years, superhydrophobic materials have attracted more and more attention due to their various applications, such as self-cleaning,1,2 anti-fogging,3 delayed frosting,4 anti-corrosion,5,6 and oil–water separation.7,8 Since a lot of oily wastewater is produced in daily life and many industrial processes, numerous researchers have focused on the development of materials with superhydrophobic properties for oil/water separation.9–11 Superhydrophobic materials were focused on to efficiently separate the common layered mixture of oil/water or emulsified oil/water.12,13 To the best of our knowledge, it's the first time that superhydrophobic films have been employed to separate ppm levels of micro-water in oil liquids. The ppm level of micro-water is dissolved in transformer oil and the distribution of water is very uniform and stable. As a result, the separation is much more difficult than the deposition of water and emulsified water.
After a long time running, power transformers oil tends to mix with a small amount of water. Therefore, it is necessary and urgent to reduce the water content in transformer oil, so as to protect the transformer from aging and corrosion.14 To date, conventional technologies have been employed to separate oil/water mixtures, such as air flotation, gravity separation, centrifugation, oil-absorbing materials and biological treatment.15–18 However, there are usually some limitations in these technologies, which can hardly separate dissolved water in oil. In order to separate micro-water, the vacuum oil filter is commonly adopted in industry. However, a lot of energy is required. In consideration of superior chemical and mechanical stability, high separation efficiency, low cost and relatively simple operational process, membrane technology is considered as the most efficient method.19–21 In this paper, a superhydrophobic membrane has been prepared and successfully used for micro-water separation in oil liquids.
By studying the natural superhydrophobicity of lotus leaves, rice leaves and water strider legs,22 researchers have been found out that in combination with the low surface energy, micro/nanostructures on the materials surface generate superhydrophobic properties.23–25 In addition, various techniques have been employed to fabricate superhydrophobic surfaces, such as plasma etching, template/hydrothermal method, self-assembly, phase separation, chemical vapor deposition, sol–gel and electrodeposition.26–29 In this paper, a facile and inexpensive method is used to fabricate a robust superhydrophobic membrane, in which only epoxy resin and silica nanoparticles need to be mixed, coated and dried. As one of the most important thermo-setting polymers, epoxy resin is widely used as coating and composite materials, as well as structural adhesives due to its great versatility and outstanding properties. Furthermore, the introduction of inorganic silica nanoparticles provide a straightforward and effective way to improve the surface roughness and mechanical properties of the membrane. In consideration of the small filtration resistance and low cost, a double-sided composite filter paper material was selected as the membrane substrate. Through the combination of the advantages of organic materials and inorganic materials, a solution of epoxy resin loaded with silica (SiO2) nanoparticles was conglutinated on the surface subsequently, which led to a water contact angle (WCA) of 161° upon hydrophobization. By simply dip-coating with the nano-SiO2/epoxy resin solution, a robust and durable superhydrophobic membrane was presented, which possessed good mechanical properties and environmental durability.
2. Experimental
2.1 Materials
Bisphenol epoxy resin (E-44) was purchased from Yueyang petrochemical plant, China. Ancamine® 2771 (a commercial-grade modified aliphatic amine curing agent) was purchased from Air Products and Chemicals, Inc. PDMS–SiO2 (hydrophobic fumed silica after treated with polydimethylsiloxane, AEROSIL® R 202, having an average particle size of 14 nm) was purchased from Evonik Inc. Double-sided composite filter paper was supplied from Chongqing Paper Industry Research and Design Institute, China. Transformer oil was taken from Hanchuan Power Plant, China. Absolute ethanol (99.5%) was purchased from Sinopharm Chemical Reagent Co., Ltd. All chemicals were used as received without any further treatment.
2.2 Preparation of superhydrophobic membrane
As shown in Fig. 1, the process to prepare superhydrophobic membrane is described. First of all, 2 g of epoxy resin and 1 g of Ancamine 2771 curing agent were added into 50 g of ethanol and stirred for 10 minutes. In the next step, PDMS–SiO2 nanoparticles with different weight fractions (wt%) (respectively containing 0, 1, 2, 3, 4, and 5 wt% PDMS–SiO2) were added and stirred for 30 minutes until the mixture became a uniform solution. And then, with a diameter of 80 mm, the double-sided composite filter paper was dipped into the solution for 10 minutes and pulled out with the help of narrow-nosed tweezers, so as to reduce the contact with the surface. Next, the coating was solidified for 2 h at 90 °C. Finally, stable superhydrophobic membrane was yielded.
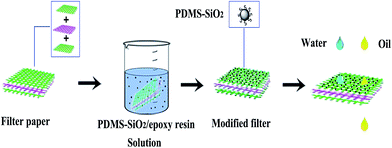 |
| Fig. 1 The process to prepare superhydrophobic membrane, double-sided composite filter paper was dipped into the PDMS–SiO2/epoxy resin solution and then solidified for 2 h at 90 °C. | |
2.3 Separation process of micro-water in oil liquids
As shown in Fig. 2, the oil–water separation apparatus, the as-prepared superhydrophobic membrane was placed in the ultrafiltration cup. And then, the transformer oil sample was poured into the ultrafiltration cup and nitrogen was added to guarantee a pressure of 5 kPa. After the filtrate flowed out of the ultrafiltration cup stably, a 1 mL sampler was used to sample the filtrate in the silicone tube, so as to ensure that the filtrate was not exposed to air. Moisture in the air that causes the experiment deviation was excluded. In addition, Karl Fischer moisture titrator was adopted to measure water content of the original oil sample and the filtrate. Sampling and measurement were performed for three times and the average was taken.
 |
| Fig. 2 Oil–water separation apparatus, in which the membrane was put at the bottom of the ultrafiltration cup. When the transformer oil was passed through the membrane, the water was retained above the membrane. | |
2.4 Characterization
Through the application of a contact angle detector (DSA100, Germany), the water contact angle (WCA) was measured at room temperature, during which 5 μL of distilled water was used as an indicator. By employing electron microscopy (FEI Quanta 200, Holland) equipped with energy dispersion spectroscopy (EDS) unit, morphologies of the as-prepared samples and EDS were investigated. With the help of a thermal analysis system (Setaram Instrumentation, France), thermal gravimetric analysis (TGA) was performed. Furthermore, at a heating rate of 10 °C min−1, the samples were heated from room temperature to 600 °C under nitrogen atmosphere with a gas flow rate of 20 mL min−1. Karl Fischer moisture titrator (SFY-101, China) was used to analyze the water content in oil. All the tests were carried out in triplicate and the average values were presented.
3. Results and discussion
3.1 Wetting behavior
By adding different weight fractions of PDMS–SiO2 nanoparticles in the impregnating solution ranging from 0 to 5 wt%, six membrane samples were prepared, including A-0, A-1, A-2, A-3, A-4, and A-5. The WCAs of the membrane samples are shown in Fig. 3. Wetting involving such a heterogeneous surface is best described by the Cassie–Baxter model and reduced to the Wenzel mode in areas that no air trapping occurs.30 From 125° on the surface coated with epoxy resin only up to the maximum WCA of 161° for 5 wt% of PDMS–SiO2, the WCAs of the coated surface increased as the concentration of PDMS–SiO2 increased.
 |
| Fig. 3 Contact angle of the membrane samples with different silica nanoparticles concentration, photographs of water droplets on the membrane samples. | |
3.2 Surface morphology and chemical composition
By making use of SEM, surface morphology of the six membrane samples was investigated (Fig. 4 and S1 in ESI†). For A-0 (without PDMS–SiO2 in the membrane), a smooth surface of filter paper was clearly observed with a diameter of about 20–500 μm. In contrast, after being treated by PDMS–SiO2, a comparative rough surface of the membrane was observed from A-1 to A-5. It was found that with the increase of PDMS–SiO2 content in the dispersions, in which the filter paper was immersed, more PDMS–SiO2 nanoparticles adhered to the fiber columns via epoxy resin and this roughened the surface of the membranes significantly. Due to poor adhesion to the substrates, a small number of nanoparticles would fall off as nanoparticles further increased to 5 wt% in the membranes. Besides, the fiber columns of the membranes were almost blocked by PDMS–SiO2/epoxy resin. On account of the resistance increase when filtering, these membranes were not conducive to oil/water separation. In addition, it has been found that prepared with 4 wt% PDMS–SiO2 nanoparticles incorporating epoxy resin, the membranes provided the best coating adhesion correlating best with high water contact angle and the optimum surface roughness. Our observation was well consistent with the study of D. K. Sarkar et al.,31 in which similar tendency on the roughness and the water contact angle was found on the surface prepared with ZnO nanoparticles incorporating epoxy resin.
 |
| Fig. 4 SEM of the membrane samples: (a) A-0; (b) A-4; (c) A-5. | |
In order to determine the elements content on the surface of the filter paper, EDS analysis of the large area on the membranes were carried out and the results were shown in Fig. 5 and S2 in ESI.† In A-1 to A-5, C, O and Si were found to be present, which indicated the presence of PDMS–SiO2. For A-0, the mass ratio of C
:
O was 75.65
:
24.35, while for A-1 to A-5, the mass ratio of C
:
O
:
Si were respectively 69.71
:
29.19
:
1.10, 71.12
:
26.16
:
2.71, 69.30
:
24.41
:
6.30, 63.36
:
26.04
:
10.59, 63.66
:
22.90
:
13.44. Upon treatment with SiO2/epoxy resin, a decrease in the carbon and oxygen content and an increase in the silicon content were observed in samples, which indicated a successful functionalization of the filter paper. In conclusion, a micro/nanostructure and low-surface-energy element was treated on the filter paper surface, such as silicon.
 |
| Fig. 5 EDS of the membrane samples: (a) A-0; (b) A-4. | |
3.3 Thermal stability of the membranes
In Fig. 6, TGA profiles of the six membrane samples were presented, which revealed that the thermal stability increased with the concentration increase of PDMS–SiO2 and once the thermal decomposition temperature was respectively 331 °C and 360 °C, SiO2 content was 0% and 5% of the membranes in weightlessness 5%. Furthermore, all the samples occurred in weightlessness above 300 °C and this suggested that the membranes had excellent thermal stability, which could completely satisfy the use environment of transformer oil/water separation.
 |
| Fig. 6 TGA of the membrane samples: A-0 to A-5. | |
3.4 Separation efficiency of micro-water in oil liquids
Owing to the WCA and SEM of these superhydrophobic membrane, 4% SiO2/epoxy resin modified superhydrophobic filter paper could be chosen for optimized oil–water separation. Oil–water separation apparatus was shown in Fig. 2. By combined pressure and gravity, oil passed through the superhydrophobic membrane and flowed into the filtrate flask during the separation process, while water was blocked by superhydrophobic membrane. Transformer oils with an initial water content of 59.5 ppm, 71.6 ppm, 89.3 ppm and 126.3 ppm were filtered, a certain mass of filtrate was respectively filtered out and the water content was measured. In addition, the weight and water content of both filtrate and retentate were measured at least three times on average. As shown in Fig. 7 and S3 in ESI,† the first point corresponds to the initial water content of transformer oil and the remaining points correspond to the water content versus different filtrate weights. By resorting to Fig. 7, S3† and Table 1, it was illustrated that the separation efficiency increased as initial water content in transformer oil increased. When the initial water content was 59.5 ppm, the oil–water separation efficiency is only about 23.0%. However, when the initial water content was 126.3 ppm, the separation efficiency could reach 54.2%. In Table 2, we have tried three times of filtration on membrane separation efficiency, and thereafter, the water content of transformer oil reduced from 132.9 ppm to 22.3 ppm. The separation efficiency was 83.2% and the flux of transformer oil was about 130 mL min−1 in the separation process. According to the Chinese Electric Power Standard GB/T 7595-2008 (Table 3), the water content of the running transformer oil must be ≤35 ppm for the voltage level of transformers ≤110 kV, so as to operate the machine safely. After three times of filtration through the superhydrophobic membrane, transformer oil could be used in transformers directly and the problem of the transformer oil water content exceeding standard was solved. Moreover, comparison between the membrane and vacuum oil filters was made. After three times of filtration with vacuum oil filters, the water content of transformer oil was reduced to 15.6 ppm. Nevertheless, the micro-water vaporization under high vacuum was needed in vacuum oil filters, which would consume a lot of energy and a long time. In industrial application, the membrane has a great value and numerous advantages.
 |
| Fig. 7 The weight and water content of the filtrate: initial water content 59.5 ppm, temperature 27.9 °C, humidity 68%. | |
Table 1 The oil/water separation efficiency of the membranes
Samples |
Initial water content/ppm |
Filtrate water content/ppm |
Retentate water content/ppm |
Separation efficiency/% |
1 |
59.5 |
45.8 |
87.5 |
23.0% |
2 |
71.6 |
46.0 |
116.3 |
35.8% |
3 |
89.3 |
53.3 |
158.9 |
40.3% |
4 |
126.3 |
57.9 |
249.1 |
54.2% |
Table 2 Three times of filtration on membrane separation efficiency
Filter times |
The water content/ppm |
The average water content/ppm |
Before the filter |
131.8 |
128.1 |
138.7 |
132.9 |
The first filter |
60.3 |
61.5 |
57.8 |
59.9 |
The second filter |
46.0 |
36.5 |
42.7 |
41.7 |
The third filter |
19.2 |
26.1 |
21.7 |
22.3 |
Table 3 Transformer oil quality standards
Items |
Equipment voltage grade kV |
Quality index |
Test methods |
New oil |
Running oil |
The water content mg L−1 |
330–1000 |
≤10 |
≤15 |
GB/T 7600 or GB/T 7601 |
220 |
≤15 |
≤25 |
≤110 |
≤20 |
≤35 |
3.5 Resistance against oil scouring
The stability and durability of A-4 membrane samples have been characterized by an oil scouring test (Fig. 8), in which the samples were scoured by oil current using a constant flow pump. The samples were taken out every two hours, washed with hexane three times and dried in an oven at 60 °C after each cycle, the WCA was measured. In Fig. 8, the changes of WCAs of the surface versus the scouring time were displayed. At 10 h of the test, a little decrease was presented in the WCA, which was reduced from 155° to 151°. The reason might be that a few loose particles were washed off the surface by the oil, during which a slightly reduced roughness of the surface was produced.32 The WCAs only exhibited a very little decrease as the scouring time increased, which suggested a good durability of the superhydrophobic property against the oil scouring. After 10 h of the oil scouring test, the membrane was adopted to separate micro-water in transformer oil liquids. After three times of filtration, the separation efficiency was 80.6%. This excellent stability was attributed to the remarkable mechanical strength of epoxy adhesive that was associated with the strong interaction between epoxy adhesive and SiO2 and the cross-linked structure. Besides, the structure of double-sided composite filter paper also led to the maintenance of superhydrophobicity and oil/water separation ability.
 |
| Fig. 8 The variation of the water contact angle versus the scouring time. | |
4. Conclusions
Superhydrophobic membranes with micro/nanostructures have been successfully prepared by making use of SiO2/epoxy resin coated filter paper. Due to the hydroxyl groups formed in the epoxy, the adhesion between inorganic particles and epoxy was strong. The membranes were characterized by water contact angle, scanning electron microscope, energy dispersion spectroscopy, thermal gravimetric analysis, and Karl Fischer moisture titrator measurement. As a result, the water contact angle of these membranes was found to be increased from 125° to 161° and the super-oleophilicity with the oil contact angle of 0° was observed. Besides, 4 wt% SiO2/epoxy resin membrane was selected for optimized oil–water separation. In addition, even after an extremely harsh oil scouring test, the membranes could maintain the required superhydrophobicity. This is the first reported technique for the application of superhydrophobic membrane in micro-water separation in transformer oil. Furthermore, this method is very simple, environmentally friendly and low-cost in superhydrophobic membrane preparation, which makes it available for large-scale production and applied in oil/water separation.
Acknowledgements
The authors are most grateful for the support of this research project by Yunnan power grid Co., Ltd, “study of superhydrophobic modified epoxy copolymer membrane in micro-water separation of transformer oil”.
References
- S. Nishimoto and B. Bhushan, RSC Adv., 2013, 3, 671–690 RSC.
- Y. Lu, S. Sathasivam, J. L. Song, C. R. Crick, C. J. Carmalt and I. P. Parkin, Science, 2015, 347, 1132–1135 CrossRef CAS PubMed.
- Z. Q. Sun, T. Liao, K. S. Liu, L. Jiang, J. H. Kim and S. X. Dou, Small, 2014, 10, 3001–3006 CrossRef CAS PubMed.
- Q. Xu, J. Li, J. Tian, J. Zhu and X. F. Gao, ACS Appl. Mater. Interfaces, 2014, 6, 8976–8980 CAS.
- Y. J. Cho, H. Jang, K. S. Lee and D. R. Kim, Appl. Surf. Sci., 2015, 340, 96–101 CrossRef CAS.
- H. Q. Liu, S. Szunerits, W. G. Xu and R. Boukherroub, ACS Appl. Mater. Interfaces, 2009, 1, 1150–1153 CAS.
- W. B. Zhang, Z. Shi, F. Zhang, X. Liu, J. Jin and L. Jiang, Adv. Mater., 2013, 25, 2071–2076 CrossRef CAS PubMed.
- L. Peng, H. Li, Y. Zhang, J. Su, P. Yu and Y. B. Luo, RSC Adv., 2014, 4, 46470–46475 RSC.
- X. Y. Zhang, Z. Li, K. S. Liu and L. Jiang, Adv. Funct. Mater., 2013, 23, 2881–2886 CrossRef CAS.
- W. X. Liang and Z. G. Guo, RSC Adv., 2013, 3, 16469–16474 RSC.
- Z. X. Xue, Z. X. Sun, Y. Z. Cao, Y. N. Chen, L. Tao, K. Li, L. Feng, Q. Fu and Y. Wei, RSC Adv., 2013, 3, 23432–23437 RSC.
- B. Wang, W. X. Liang, Z. G. Guo and W. M. Liu, Chem. Soc. Rev., 2015, 44, 336–361 RSC.
- Y. Z. Zhu, D. Wang, L. Jiang and J. Jin, NPG Asia Mater., 2014, 6, e101 CrossRef CAS.
- J. H. R. Rodríguez, F. M. Piñón, J. A. A. Chávez, D. J. Vigueras and E. G. R. Pimentel, Meas. Sci. Technol., 2011, 22, 11 CrossRef.
- B. Wang, J. Li, G. Y. Wang, W. X. Liang, Y. B. Zhang, L. Shi, Z. G. Guo and W. M. Liu, ACS Appl. Mater. Interfaces, 2013, 5, 1827–1839 CAS.
- Z. X. Xue, Y. Z. Cao, N. Liu, L. Feng and L. Jiang, J. Mater. Chem. A, 2014, 2, 2445–2460 CAS.
- L. Peng, S. Yuan, G. Yan, P. Yu and Y. B. Luo, J. Appl. Polym. Sci., 2014, 131, 40886 Search PubMed.
- Y. Liu, J. Zhou, E. W. Zhu, J. Tang, X. H. Liu and W. H. Tang, Carbon, 2015, 82, 264–272 CrossRef CAS.
- Y. Z. Zhu, W. Xie, J. Y. Li, T. L. Xing and J. Jin, J. Membr. Sci., 2015, 477, 131–138 CrossRef CAS.
- B. X. Jing, H. T. Wang, K. Y. Lin, P. J. McGinn, C. Z. Na and Y. X. Zhu, Polymer, 2013, 54, 5771–5778 CrossRef CAS.
- M. Zhang, C. Y. Wang, S. L. Wang, Y. L. Shi and J. Li, Appl. Surf. Sci., 2012, 261, 764–769 CrossRef CAS.
- T. Darmanin and F. Guittard, J. Mater. Chem. A, 2014, 2, 16319–16359 CAS.
- Z. Qian, Z. C. Zhang, L. Y. Song and H. R. Liu, J. Mater. Chem., 2009, 19, 1297–1304 RSC.
- K. S. Liu and L. Jiang, Nano Today, 2011, 6, 155–175 CrossRef CAS.
- G. D. Bixler and B. Bhushan, Nanoscale, 2014, 6, 76–96 RSC.
- E. Celia, T. Darmanin, E. T. D. Givenchy, S. Amigoni and F. Guittard, J. Colloid Interface Sci., 2013, 402, 1–18 CrossRef CAS PubMed.
- X. X. Zhang, F. Zheng, L. Q. Ye, P. Xiong, L. H. Yan, W. B. Yang and B. Jiang, RSC Adv., 2014, 4, 9838–9841 RSC.
- C. H. Lee, N. Johnson, J. Drelich and Y. K. Yap, Carbon, 2011, 49, 669–676 CrossRef CAS.
- T. Darmanin, M. Nicolas and F. Guittard, Phys. Chem. Chem. Phys., 2008, 10, 4322–4326 RSC.
- Z. X. Xue, M. J. Liu and L. Jiang, J. Polym. Sci., Part B: Polym. Phys., 2012, 50, 1209–1224 CrossRef CAS.
- J. D. Brassard, D. K. Sarkar and J. Perron, Appl. Surf. Sci., 2015, 324, 525–531 CrossRef CAS.
- Z. Cui, Q. J. Wang, Y. Xiao, C. H. Su and Q. M. Chen, Appl. Surf. Sci., 2008, 254, 2911–2916 CrossRef CAS.
Footnote |
† Electronic supplementary information (ESI) available. See DOI: 10.1039/c5ra21016j |
|
This journal is © The Royal Society of Chemistry 2015 |
Click here to see how this site uses Cookies. View our privacy policy here.