DOI:
10.1039/C5RA15363H
(Paper)
RSC Adv., 2015,
5, 102633-102642
Spray-coated epoxy barrier films containing high aspect ratio functionalized graphene nanosheets†
Received
1st August 2015
, Accepted 24th November 2015
First published on 25th November 2015
Abstract
Epoxy nanocomposite spray-coatings containing large aspect ratio modified graphene (MG) were successfully prepared in a facile manner. The individually exfoliated MG nanosheets form liquid crystalline mesophases in the epoxy precursor at low loadings. The epoxy/MG nanocomposite films exhibit significantly improved gas barrier properties even in humid conditions. The spray-coating method allows for the preparation of high MG content nanocomposites in large scale without compromising processability. Implication of the present finding for fabrication of high-performance graphene-based packaging films with multi-functionality is discussed.
1. Introduction
Because of their relatively low cost, light weight, flexibility, versatility and effectiveness, polymer nanocomposites have long been recognized to be ideal for barrier and protective coating and film applications, such as in food, beverages, pharmaceuticals, and electronics.1–4 The long-term effectiveness of barrier coatings and films in preventing product degradation is directly dependent upon a variety of factors, including their impermeability to corrosive gases, opacity to high-energy light, thermal stability, mechanical integrity, and electrical conductivity, particularly in prevention of electrostatic charge build-up. Various strategies have been developed to fabricate high-performance, multi-functional polymer nanocomposite barrier films, such as microlayer coextrusion,5 the Langmuir–Blodgett method,6,7 spin-coating,8 and layer-by-layer (LbL) assembly.9,10 However, most of the above approaches require time-consuming sequential deposition processes or extensive energy consumption, both of which severely limit their commercial attractiveness for large-scale production.
Nanoparticles with a 2-dimensional sheet-like geometry, such as natural montmorillonite (MMT) clay and other natural and synthetic analogs with layered structure, like LAPONITE®, goethite, and α-zirconium phosphate (ZrP), have been widely studied as potential fillers to improve the barrier properties of various polymer matrices by forming a “tortuous pathway” to hinder transportation of gas molecules through the polymer.9,11,12 However, there is still significant challenge to be able to exfoliate and uniformly disperse high concentrations of clay particles a polymer matrix.13–15 Graphene and its derivatives have recently garnered significant attention due to their excellent material characteristics, such as large aspect ratio, impermeability to gases, high electrical and thermal conductivity, good thermal stability with respect to most polymers, and availability for diverse chemical modification approaches.16–21 Several approaches have been developed to prepare polymer/graphene nanocomposites, and in many cases were found to exhibit not only greatly enhanced gas-barrier properties compared to polymers containing inorganic clays but also improved electrical and thermal conductivity when properly dispersed in a polymer matrix.22,23 In addition to gas barrier applications, graphene-based materials could potentially be used as molecular gas filters,24 metal protection layers to prevent corrosion,25,26 effective surface lubricants,27,28 and solvated ion separation membranes.29
In general, large-scale graphene-based polymer nanocomposites used for barrier properties maybe prepared by two approaches. The first is the direct transfer of a few layers of large-size graphene or its derivatives onto a polymeric substrate. A major challenge with this route is to minimize structural defects during the transfer process.30,31 The second approach is to disperse the graphene-based filler into a polymer matrix. This approach is simpler and better suited for large-scale industrial applications, but it suffers from limitations in pre-processing steps to effectively exfoliate graphene without compromising intrinsic properties or reduction in size and aspect ratio during preparation. One penalty associated with achieving a high level of exfoliation and good dispersion of nanofillers in a polymer matrix is that there may be an associated increase in viscosity that will hinder processability, particularly at high nanofiller concentrations. Here, we adopt a simple spray coating approach to prepare high-quality, flexible epoxy barrier films based on modified graphene (MG) in epoxy.32 This method allows for the preparation of nanocomposites containing a large volume fraction of MG without compromising processability. The high aspect ratio MG nanosheets were individually exfoliated and showed liquid-crystalline order when dispersed in an epoxy pre-polymer at high concentrations. After curing, the epoxy/MG nanocomposite films show significantly improved gas barrier properties, along with good electrical conductivity and thermal stability. Implication of the present findings on the fabrication of high-performance barrier films with multifunctionality is discussed.
2. Experimental
2.1 Materials
Hydrogen peroxide (H2O2), potassium permanganate (KMnO4), barium sulfate (BaSO4), and sodium nitrate (NaNO3) were purchased from Aldrich. Bisphenol-F epoxy (EPON 862) and aromatic diamine curing agent (Epikure W) were purchased from Momentive. Graphite (SP-1) was donated by Bay Carbon Inc. Graphene and its derivatives may be an irritant to eyes, skin or causes respiratory reaction. H2SO4, KMnO4, and H2O2 could cause severe burn from direct contact. Protection against inhalation and skin contact can be achieved by wearing protective clothes and face protecting mask during exposure to chemicals.
2.2 Synthesis of graphene oxide
Graphene oxide (GO) was synthesized from purified natural graphite using the modified Hummers' method. First, 0.5 g graphite was added into a 250 mL flask with 50 mL of concentrated H2SO4 and 0.5 g NaNO3. After stirring for 20 min, the flask was submerged in an ice bath and KMnO4 (0.3 g) was slowly added while continuously stirring. After 3 h, 23 mL DI water heated to 70 °C was slowly added into the mixture. After 30 min, the reaction was further diluted with 70 mL of 70 °C DI water, followed by an addition of 10 mL H2O2 to react with the excess KMnO4. The mixture was subsequently washed with DI water and a 5% HCl aqueous solution several times to remove any remaining metal species.
2.3 Synthesis of MG
The GO prepared above was treated with sodium dodecyl benzene sulfonate (SDBS) surfactant by gently stirring 70 mg GO in 140 mL aqueous solution containing 1 wt% SDBS for 4 h. Chemical reduction was carried out by adding 70 μL of hydrazine. The reaction mixture was heated to 80 °C for 12 h with mechanical stirring to obtain reduced GO (rGO). Separately, 3 g of nitroaniline was dissolved in 140 mL acetonitrile solvent to achieve a homogenous solution, following by an addition of 140 mL rGO aqueous solution (0.5 mg mL−1). Additionally, 3 mL isoamyl nitrite was added dropwise under nitrogen atmosphere. The reaction mixture was heated with stirring to 70 °C for 12 h. Afterwards, the mixture was filtered and washed with DI water and acetone several times. The resulting nitrobenzene functionalized graphene, designated as modified graphene (MG), was redispersed in acetone to reach a concentration of 0.5 mg mL−1.
2.4 Preparation of epoxy/MG barrier film
2.4 g bisphenol-F epoxy (EPON 862, Momentive) was dissolved in 5 mL acetone to form a clear solution. The epoxy solution was added dropwise to the MG dispersion (0.5 mg mL−1), followed by stirring for 6 h. Then, 0.634 g of diethyltoluenediamine (Epikure W, Momentive) was added to the solution and homogenized by stirring. The solution of epoxy/MG in acetone was loaded into a spray-gun (Master Airbrush G444-SETand Royal Mini Air Compressor) and deposited onto a polyimide (PI) film (Apical, Kaneka). The PI substrate was sprayed multiple times to achieve desired final thickness of the barrier film. The spray-coated film was cured in an oven at 40 °C for 1 h, 80 °C for 1 h, 120 °C for 2 h, and 180 °C for 4 h.
2.5 Characterization
Transmission electron microscopy (TEM) was performed using a JEOL 2010 high-resolution transmission electron microscope with accelerating voltage of 200 kV. X-ray diffraction (XRD) patterns were obtained using a Bruker D8 Advanced Power X-ray diffractometer with Cu-Kα incident radiation (λ = 1.5418 Å). Fourier transform infrared spectroscopy under attenuated total reflectance mode (FTIR-ATR) was performed using a Nicolet Avatar 360. Optical micrographs (OM) were collected using an Olympus BX60 microscope. Tapping-mode atomic force microscopy (AFM) was carried out with a Digital Instruments Nanoscope AFM system. Thermogravimetric analysis (TGA) was carried out using a Q500-TGA from TA instruments. Grazing-incidence small-angle X-ray scattering (GISAXS) experiments were performed using a Rigaku S-Max 3000 unit at the University of Houston. Data were collected with a grazing incidence angle of 0.05°. The dynamic mechanical behavior was measured using an ARES-G2 (TA Instruments). The oxygen transmission rate (OTR) of the films was evaluated using a MOCON OX-TRAN 2/21 in accordance to ASTM D3985 at Dow Chemical. Small-angle X-ray scattering (SAXS) experiments were performed at the Japan Synchrotron Radiation Research Institute (JASRI) SPring-8 facility located in Hyogo, Japan. The scattering intensity is reported as a function of a scattering vector, q, which is defined as q = (4π/λ)sin
θ, where λ = 0.07 nm is the wavelength of the X-ray and 2θ is the angle between the incident X-ray beam and the scattered X-rays.
3. Results and discussion
3.1 Preparation and characterization of epoxy/MG barrier films
Direct deposition of large-scale, defect-free sheets of graphene on desirable polymeric substrates for greatly improved barrier properties remains a major challenge. One strategy for fabricating high-performance graphene-based barrier films is to utilize high-quality graphene derivatives, such as GO, rGO, and MG, which are easier to be exfoliated and dispersed in organic solvents and in polymer matrices. In this work, exfoliated epoxy/MG films were prepared via a simple and efficient spray-coating method (Fig. 1). MG was prepared by chemically modifying GO precursors with nitroaniline. GO sheets were individually dispersed in aqueous suspension with a thickness of 0.9 nm (Fig. 2a), and showed excellent stability at a concentration of 5 mg mL−1 (Fig. 2b). Lyotropic liquid crystalline behavior was observed by cross-polarized OM for GO suspensions at 10 mg mL−1 (Fig. 2c and d), which indicates the presence of an ordered mesophase. SAXS measurements carried out on aqueous dispersions of GO at 1.3 wt% showed first and second order peaks corresponding to smectic order with inter-layer d-spacing of ∼80 nm (Fig. 2e). We previously used this approach as an efficient method to disperse multi-walled carbon nanotubes (MWCNT) in organic solvents and epoxy without causing significant physical damage to the MWCNT.32 The MG was well dispersed in acetone at 0.7 mg mL−1 without any visual evidence of aggregation or precipitation after 2 days of storage (Fig. 3a). AFM measurements show that MG flakes are individually exfoliated and have an average thickness and diameter of ∼1.1 nm (Fig. 3b and c) and 1.7 μm (Fig. 3d), respectively. The diameter of an irregular sheet was defined as a circular diameter with an area equivalent to the area of an irregular MG. More AFM of MG sheets are shown in ESI Fig. S1.† The aspect ratio of MG, defined as the length to thickness ratio, is about 1500.
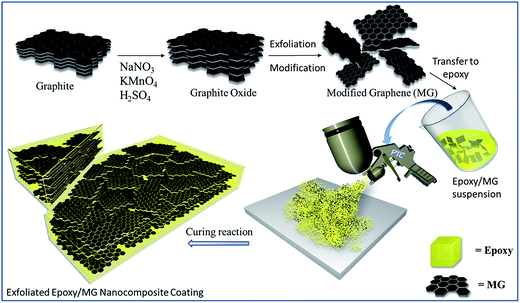 |
| Fig. 1 Schematic of epoxy/MG nanocomposite film preparation. | |
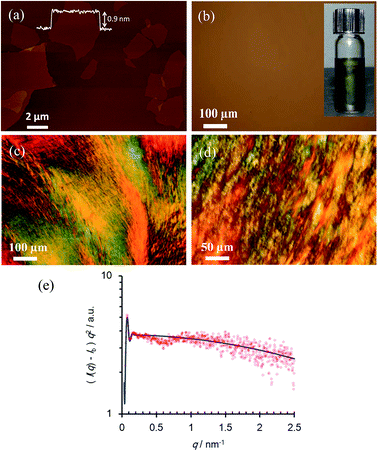 |
| Fig. 2 Images of GO viewed using (a) AFM, (b) OM, (c and d) cross-polarized light OM, and (e) SAXS of GO aqueous dispersion. Profiles of scattering intensity (I(q)−Ib)q2 as a function of scattering vector q (q = 4π sin θ/λ = 2π/d) for 1.32 wt% GO dispersion including measured data (red line) and calculated profile (blue line) based on the 1D paracrystal model. Inset in (b) is photograph of GO aqueous suspension. | |
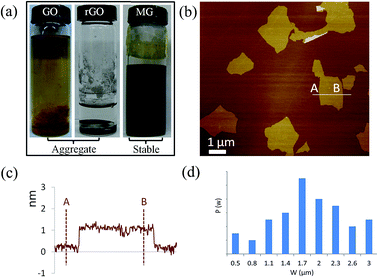 |
| Fig. 3 (a) Photograph of GO, rGO and MG in acetone having a concentration of 0.7 mg mL−1. (b) Tapping-mode AFM image, (c) height profile, and (d) size distribution of MG. | |
The chemical composition of MG was characterized by FTIR-ATR and TGA (Fig. 4). The FTIR-ATR measurements of the GO show characteristic peaks at 3500 cm−1, 1220 cm−1, and 1720 cm−1, which are assigned to stretching of O–H, C–O, and C
O functionalities, respectively, and indicate that the presence of oxygen-functional groups attached to surface. The MG shows C–N stretching at 852 cm−1, and NO2 asymmetric and symmetric stretching at 1520 cm−1 and 1285 cm−1, respectively, which are consistent with the presence of nitrobenzene groups.32 The XRD pattern of the GO exhibits a diffraction peak at 2θ = 10.8°, which correspond to an interlayer spacing of 0.82 nm (ESI Fig. S2†). After chemical reduction treatment, the interlayer distance of the rGO decreases to 0.35 nm (2θ = 25.6°) indicating that a significant amount of the oxygen species on GO were removed after chemical reduction. The XRD pattern of the MG shifts to 2θ = 8.4° corresponding to a d-spacing of 1.1 nm, suggesting that the nitrobenzene functional groups are tethered on the MG surfaces. The degree of functionalization was estimated using TGA (Fig. 4b). GO shows a mass loss of ∼27.1 wt% at around 220 °C, which is attributed to the decomposition of oxidized species. There is no obvious weight loss after hydrazine reduction up to 220 °C. The final weight loss values of GO, rGO and MG at 700 °C were 57.8 wt%, 20.3 wt% and 38.2 wt%, respectively. The weight fraction of nitrobenzene functional groups in MG is 17.9%, which is equal to the difference between 38.2% and 20.3%. It is estimated that there is approximately 1 nitrobenzene functional group for every 47 carbon atoms in graphene.
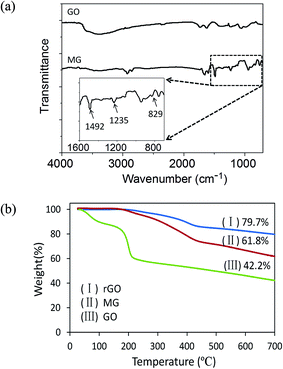 |
| Fig. 4 (a) FTIR-ATR spectra of GO and MG; inset shows the details of wavenumber region from 1600 to 700 cm−1. (b) TGA results of GO, rGO and MG. | |
A high degree of exfoliation is necessary to be benefitted from the high aspect ratio nanofillers in polymer nanocomposites, particularly for barrier properties applications. The degree of exfoliation in epoxy/MG was evaluated using XRD (Fig. 5a). The pristine graphite exhibits a diffraction peak at 2θ = 26.5°, which corresponds to a basal layer d-spacing of 0.34 nm. Epoxy/MG nanocomposites were prepared with concentration from 0.6 to 7.5 vol%. For systems containing up to 3.6 vol% of MG, the XRD patterns show no new peaks. Only a broad hump centered at 2θ = 19° is observed due to the amorphous epoxy structure, which indicates the MG remains well exfoliated in the cured epoxy matrix. TEM micrographs confirm that for concentrations as high as 3.6 vol%, the MG remains exfoliated and well dispersed (Fig. 5c and ESI S3†). However, when the MG content was increased to 7.5 vol%, there is a weak diffraction peak at 2θ = 7.9°, which corresponds to an interlayer d-spacing of 1.12 nm, suggesting some re-stacking of the dispersed MG sheets.
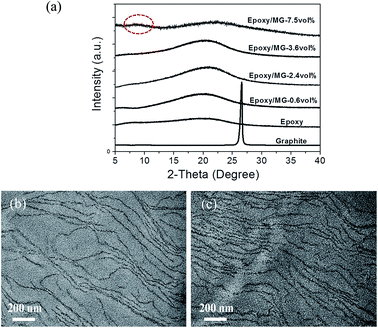 |
| Fig. 5 (a) XRD results of cured neat epoxy, graphite, and epoxy/MG films at various MG concentrations. TEM of cross-sectional epoxy/MG films at different MG loading: (b) 2.4 vol%, (c) 3.6 vol%. | |
High-quality epoxy/MG nanocomposite films were prepared by spray-coating and show good mechanical flexibility after curing (Fig. 7a). The dynamic mechanical behavior (ESI Fig. S4†) shows that the storage moduli at 25 °C of neat epoxy and epoxy/MG (1 vol%) bulk samples are 1.1 and 1. 3 GPa, respectively. Incorporation of MG appears to lower the Tg of the neat epoxy which may be attributed to the side reactions between the MG surface-tethered carboxylic groups and the epoxy monomers. The surface quality of the films are of significant importance to gas barrier properties, and was analyzed using OM. Films prepared with up to 3.6 vol% MG show uniform surface morphology (Fig. 7b–d and ESI S5†). At higher MG loadings, void and air bubble formation within the films become inevitable (Fig. 7d and e), which are likely caused by high viscosity of epoxy/MG and incomplete removal of solvent before curing. The epoxy/MG nanocomposite films at 7.5 vol% still exhibit good mechanical flexibility (ESI Fig. S6†). The evaporation of solvent initially takes place on the surface of the coating precursor, thus a concentration gradient will exist within the coating. Since cross-linking reactions of the coatings can drive up the viscosity significantly, it is possible for the coating experiences a rapid increase in viscosity and potentially to act as barrier for solvent to evaporate. Solvent evaporation rate and kinetics of curing reactions are believed to be among the key factors responsible for the rough surface morphology.46
High aspect ratio nanoplatelets have a tendency to form a long-range liquid crystalline mesophase at relatively low concentrations,13 but the order is seldom preserved after curing in thermosetting materials. We recently used a similar spray-coating approach to deposit monoamine oligomer-modified ZrP nanoplatelets in epoxy, and observed a long-range smectic order after curing.11 A number of key properties, particularly barrier performance and processability, are benefitted from this type of highly aligned structure.33,34 The microstructure of MG sheets in epoxy was characterized using OM and GISAXS. Prior to curing, the epoxy/MG (3.6 vol%) suspension shows a strong birefringence (Fig. 6), which indicates the presence of mesoscale liquid crystalline order. The nature of long-range organization was probed at different concentrations using GISAXS (ESI Fig. S7†). The GISAXS measurements did not show Bragg peaks corresponding to mesoscale lamellar organization, which indicates that the MG sheets were assembled in a nematic order.
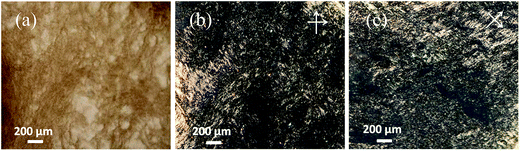 |
| Fig. 6 (a) OM and (b and c) cross-polarized light OM of epoxy/MG precursor (3.6 vol%) before curing reaction. | |
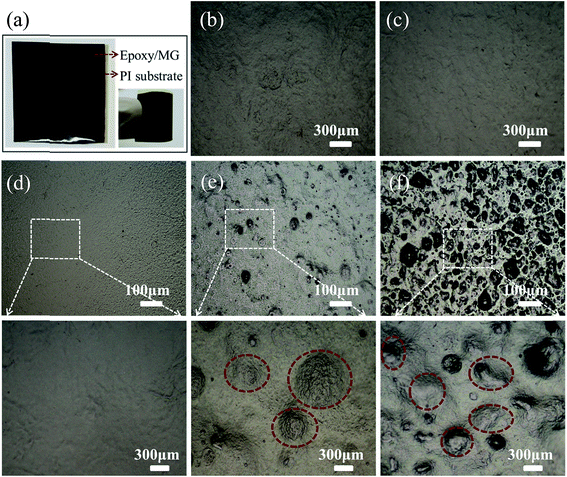 |
| Fig. 7 (a) Photograph of epoxy/MG (3.6 vol%) film on PI substrate. OM images of epoxy/MG film surface at various MG concentrations: (b) 0.6 vol%, (c) 2.4 vol%, (d) 3.6 vol%, (e) 5.5 vol%, and (f) 7.5 vol%. | |
3.2 Rheological behavior
The rheological behavior of the uncured suspension was characterized to provide insight into the influence of the long-range organization and inter-particle interaction on bulk response. The linear viscoelastic response was strongly dependent on shearing history shown in Fig. 8a and b, which is in contrast to our previous investigations of oligomer-modified nanoplatelets with smectic order in epoxy.35 After loading the sample and allowing the normal force to equilibrate, the storage modulus, G′, which is a measure of solid-like response, shows a low-frequency plateau that generally indicates a mechanically percolated network. This type of response is typical of high aspect ratio nanoparticles at moderate and high concentrations. The loss modulus, G′′, which describes the dissipative component of response, similarly appears consistent with an inter-connected particle network, but shows a minima and weak increase in the limit of low frequency. This type of behavior suggests a meta-stable microstructure and suggests that, based on the geometry of the filler used here, there is either an increased number of inter-connections with time, or a gradual mis-alignment of the MG sheets on long time scales. We previously modified MWCNTs with nitrobenzene functionalities,32 and found a transition in relaxation behavior that was attributed to a significant suppression in inter-particle attraction. After steady shear, the magnitude of G′ and G′′ were significantly reduced. However, when the suspensions were subjected to large-amplitude oscillatory deformation, both G′ and G′′ increased, suggesting either greater connectivity between aligned sheets or alignment of the director out of the flow direction. Changes in alignment behavior dependent on the size of graphene sheet have been previously reported by Wallace.50 They demonstrated that large graphene sheets tend to give rise to entropic rearrangement of sheets to form long range liquid crystalline order. The transition from isotropic to nematic phase is due to increased translational entropy. The MG sheets used here have high aspect ratio and any change in orientation must involve a domain-level transition, which suggests a highly cooperative behavior.
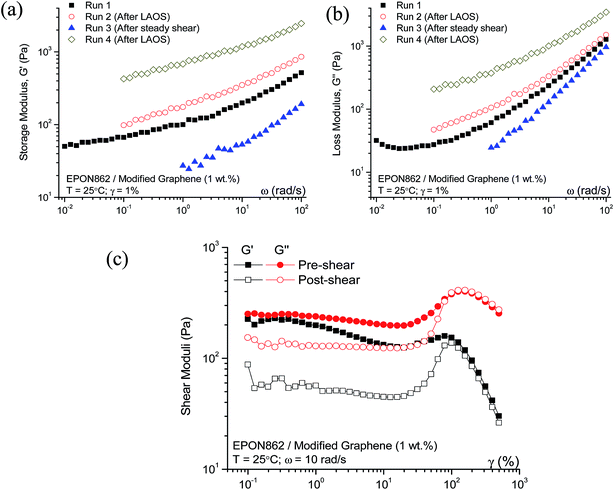 |
| Fig. 8 The response of the epoxy/MG suspension to (a and b) linear viscoelastic response, and (c) large amplitude oscillatory deformation. | |
The response of the suspension to large amplitude oscillatory deformation is shown in Fig. 8c. Prior to shear, there is no clearly defined linear region in G′, but G′′ does show a broad region of linear response. At large strain amplitude, γ ≈ 30%, there is a minima in both G′ and G′′, and at larger strains, both components of shear moduli show strain-hardening behavior and reach a maxima. This type of non-linear viscoelastic response is unusual and rarely reported.35,36 Hyun et al.37 proposed a network model to account for various modes of non-linear viscoelastic behavior, and suggested that similar LAOS curves were associated with the presence of both attractive and destructive processes that are enhanced by straining. The remarkable feature of the LAOS response here is that despite the substantial decrease in both G′ and G′′ after shearing, which is consistent with the SAOS results, their magnitude and position are nearly identical at large strain amplitudes. This suggests that there is a unique microstructural state introduced by large amplitude deformation, and that it is reversible. The reversible nature of the microstructure is supported by steady shear measurements. More detailed work is still necessary to explicitly identify the mechanisms responsible for the unique behavior observed here, particularly to separate local interaction between MG sheets from longer-range changes in orientation. We modified MWCNTs using nitrobenzene functionalities with similar degree of functionalization compared to the MG used here. The rheological results suggest that despite the observed excellent exfoliation and dispersion, there remains significant interaction between MG nanoplatelets, which stands in contrast with our prior reports on exfoliated MWCNTs with similar surface treatment.32 The difference in rheological response is more likely a consequence of particle geometry rather than surface chemistry. Both steric interaction between oligomer modified nanoparticles and entropic effects to drive particle orientation significantly depend on nanoparticle geometry.47
3.3 Gas barrier properties
The oxygen permeability of epoxy/MG nanocomposite films spray-coated on PI substrates was characterized in accordance to ASTM D3985 (Fig. 9). Compared to the neat epoxy, the epoxy/MG (3.6 vol%) nanocomposite films, which are only 21 μm thick, show nearly an order of magnitude decrease in oxygen permeability. At a higher concentration, the barrier performance is reduced, which is likely due to the presence of void defects resulting from incomplete removal of solvent or trapped air bubbles before curing.
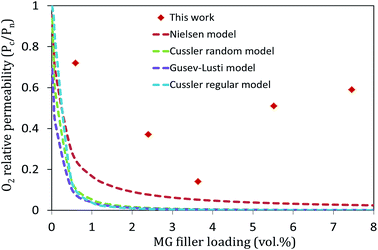 |
| Fig. 9 Oxygen relative permeability plots of epoxy/MG (PC) at various MG loadings compared to the pristine epoxy (Pn). Predicted values from various models are also included for comparison. | |
The barrier performance may be compared with existing models to provide some idea on the influence of alignment and aggregation on permeability. Several models used to predict barrier properties, such as those proposed by Neilson, Gusev–Lusti and Cussler, are included in Fig. 9. The details of various barrier models are summarized in ESI Table S1.† More detailed information can be found in reviews by Picard13 and Takahashi38 et al. Most of the models assume that the nanoplatelets are aligned perfectly parallel to the barrier film surface, which is not a realistic assumption for most nanocomposite materials, except for films prepared by sequential layer-by-layer deposition. The gas permeability of the epoxy/MG nanocomposites presented here is below the performance expected for individual, perfectly aligned sheets with aspect ratio ≈1500. The difference in performance is likely due to non-uniform alignment and dispersion of the MG, and possibly also because of the wrinkled morphology of the MG nanosheets (Fig. 5c).
The oxygen barrier properties at different humidity levels were also evaluated and are shown in Fig. 10. Both the OTR and oxygen permeability of the epoxy/MG films (3.6 vol%) show good stability under high humidity conditions (Fig. 10). Variability in permeability at low and high humidity levels is attributed to water molecules occupying Langmuir sites, which results in a competition in diffusion between water and oxygen molecules, thereby reducing permeation of oxygen.39 This behavior is in contrast to gas barrier films made by sequential deposition methods, which typically involves hydrophilic polyelectrolytes and show reduced barrier performance in humid environments due to swelling.
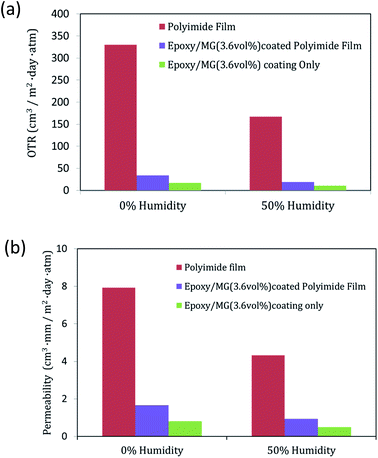 |
| Fig. 10 (a) Oxygen transmission rate (OTR) and (b) permeability of pure polyimide film, epoxy/MG (3.6 vol%) coating on polyimide substrate, and epoxy/MG (3.6 vol%) coating alone at different humidity conditions. | |
The barrier performance may be quantified by considering the “tortuosity” of the diffusion pathway for penetrant molecules caused by the impermeable nanoplatelets. The relative permeability can be expressed as:13,38
where
PR is relative permeability,
P and
P0 are the permeability coefficients of the polymer nanocomposite and neat polymer, respectively,
ϕ is the nanoplatelet volume fraction, and
τ is the tortuosity factor. The tortuosity factor is conceptually defined as the ratio of actual distance to shortest distance that a penetrant molecule needs to travel to penetrate a surface. In other words, it is the magnitude of perturbation in the pathway followed by a diffusing molecule from the ideal path. The aspect ratio of the nanoplatelets is regarded as one of the most important factors influencing tortuosity. One of the advantages of the MG filler presented here is its high aspect ratio, ∼1500, which effectively extends the tortuous pathway of diffusing gas molecules in the nanocomposites. The effect of aspect ratio on the gas permeability is shown in
Fig. 11a. The Bharadwaj model, which developed based on a uniform dispersion state, was used to estimate the “effective” aspect ratio of MG in epoxy. The details about the Bharadwaj model are given in ESI Table S1.
† The effective aspect ratio of MG is estimated to be about 600 (
Fig. 11a). The difference in the expected aspect ratio from that observed experimentally is attributed both to the wrinkled morphology and imperfect alignment of the MG in the polymer matrix. Prior reports have shown that large aspect ratio nanoplatelets, including ZrP
15 and MMT clay,
40 tend to curl up when imbedded in polymer matrices, which was attributed partially to the residual stress build-up during curing and partially to the presence of defects within the nanosheet structure. The curling of nanoplatelets reduces the effective aspect ratio, thereby reducing the resulting tortuous path experienced by the penetrant molecules. The curling of nanoplatelets obviously complicates the structure–property relationships in polymer nanocomposites.
41
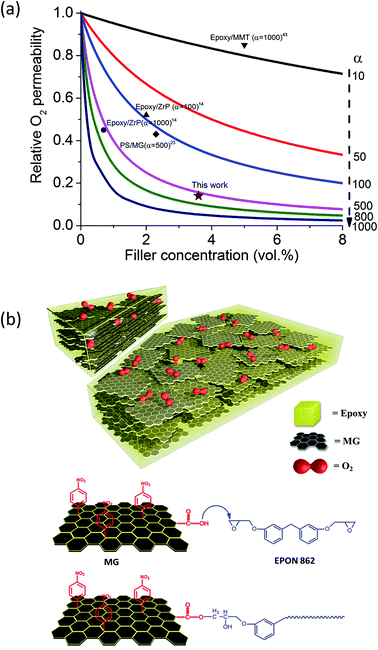 |
| Fig. 11 (a) Experimental data and Bharadwaj barrier model predictions as a function of nanoplate aspect ratio. (b) Schematic of oxygen barrier mechanism of epoxy/MG nanocomposites. | |
An additional consideration is the nature of the polymer/nanofiller interface, which is not considered in the available barrier models for rigid 2D fillers. A poor interfacial contact between the nanoplatelets and the matrix will generally diminish barrier properties.42,43 Compton et al.23 reported that crumpled graphene sheets can exhibit enhanced interaction with the polymer matrix because the sheets may be more fully “wetted” by the polymer chains. The wrinkled MG sheets in epoxy might favor this interaction more than otherwise. Moreover, the polar functional groups on MG surfaces will likely enhance the compatibility with the epoxy matrix. Haddon et al.45 reported the chemical reaction mechanism between carboxylic acid-functionalized carbon nanotubes and the epoxide groups of bisphenol-F epoxy resin. The formation of covalent bonds leads to a highly cross-linked structure, which efficiently improves load transfer between epoxy and CNTs. As shown in Fig. 11b, the carboxylic groups on MG surfaces can covalently bond with epoxide groups during epoxy curing.44,45 FTIR results shown in ESI Fig. S8† give direct evidence of the esterification reaction at interface after heat treatment. Such a reaction would suppress the formation of interstitial cavities between the MG sheets and the epoxy matrix, which help maintain oxygen barrier properties in epoxy/MG nanocomposites.
The shelf life of perishable goods depends on the permeability of gas molecules into products through its outer polymeric packaging materials, along with many other properties. High-energy lighting may degrade light-sensitive food products, vitamins, wines, and electronic devices. The light transmittance of the epoxy/MG films was characterized using UV-vis spectroscopy (ESI Fig. S9†), and is significantly reduced compared to that of neat epoxy. The reduction in transmittance is likely due to the good exfoliation of MG within polymer matrix along with its high specific surface area. The MG also improves the thermal stability of epoxy, as shown by the TGA results in Fig. 12. The decomposition temperature of the epoxy/MG nanocomposites is increased compared to the neat epoxy (Table 1). The epoxy/MG nanocomposites with multifunctional properties may offer alternatives to ever-increasing demands for performance in the packaging field.
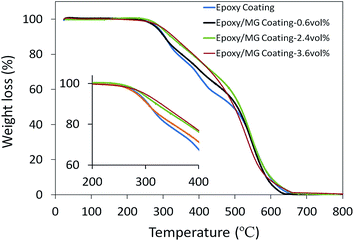 |
| Fig. 12 TGA results of epoxy/MG coatings at various MG concentrations. | |
Table 1 Thermal degradation temperature of pure epoxy and epoxy/MG filmsa
|
T10% (°C) |
T30% (°C) |
T10% and T30%: decomposition temperature of at 10% and 30% mass loss. |
Pure epoxy |
302 |
388 |
Epoxy/MG-0.6 vol% |
300 |
403 |
Epoxy/MG-2.4 vol% |
321 |
432 |
Epoxy/MG-3.6 vol% |
330 |
429 |
Two-dimensional graphene nanosheets and their derivatives have become a versatile building block for fabrication of attractive polymer nanocomposites for structural and functional applications. The gas barrier performance of epoxy/MG nanocomposites is closely related to the MG nanoscale organization and interfacial interaction with the epoxy matrix. In the present work, good-quality epoxy/MG barrier films suitable for large-scale applications were prepared using a simple spray coating method without compromising processability. Entropy-driven nematic phase formation of exfoliated MG nanosheets in epoxy precursor was observed here for the first time. The isotropic–nematic phase transition is originated from a net gain in entropy as the loss of orientational entropy is compensated by the increased translational entropy. Above the critical volume fraction, large aspect ratio MG nanosheets orientate parallel to each other in order to minimize the excluded volume, thus maximizing the entropy and favoring the nematic order. According to the Onsager' theory, as the aspect ratio increases, the critical volume fraction for mesophase transition decreases.48 Colloidal self-assembly of nanosheets to form liquid crystalline phase in solvents has been extensively studied.49,50 However, fundamental understanding of the same phenomena in polymer matrices is still lacking. Large-scale self-assembly of graphene-based nanosheets in a polymer to form thermodynamically favorable order is challenging. Additional work is currently underway to explore conditions from which liquid crystalline order of MG can be retained and manipulated upon epoxy curing for optimized barrier properties in epoxy/MG nanocomposites.
4. Conclusion
Exfoliated epoxy nanocomposites containing large-aspect-ratio MG were prepared via a facile spray coating approach. The MG sheets are individually exfoliated and form liquid crystalline mesophases in epoxy precursor at a low concentration. The spray-coating process allows for the preparation of high MG content nanocomposites without compromising processability, which is suitable for large-scale industrial practices. The epoxy/MG nanocomposite films exhibit significantly improved gas barrier properties at different humidity levels. These highly desirable packaging properties make graphene-based epoxy nanocomposites attractive for high performance multifunctional packaging applications.
Acknowledgements
Financial support of this research is provided by the Kaneka Corporation and is greatly appreciated. The authors acknowledge Chun-An Chen for his help with the schematic art and the use of NSF funded proposal (DMR 1040446) for providing GISAXS at the University of Houston.
References
- I.-H. Tseng, M.-H. Tsai and C.-W. Chung, ACS Appl. Mater. Interfaces, 2014, 6, 13098–13105 CAS.
- B. M. Yoo, H. J. Shin, H. W. Yoon and H. B. Park, J. Appl. Polym. Sci., 2014, 131, 39628–39639 CrossRef.
- T. Duncan, J. Colloid Interface Sci., 2011, 363, 1–14 CrossRef CAS PubMed.
- W. K. Chee, H. N. Lim, H. N. Ming and I. Harrison, RSC Adv., 2015, 5, 68014–68051 RSC.
- M. Gupta, Y. Lin, T. Deans, E. Baer, A. Hiltner and D. A. Schiraldi, Macromolecules, 2010, 43, 4230–4239 CrossRef CAS.
- L. J. Cote, F. Kim and J. Huang, J. Am. Chem. Soc., 2009, 131, 1043–1049 CrossRef CAS PubMed.
- X. Li, G. Zhang, X. Bai, X. Sun, X. Wang, E. Wang and H. Dai, Nat. Nanotechnol., 2008, 3, 538–542 CrossRef CAS PubMed.
- J. T. Robinson, M. Zalalutdinov, J. W. Baldwin, E. S. Snow, Z. Wei, P. Sheehan and B. H. Houston, Nano Lett., 2008, 8, 3441–3445 CrossRef CAS PubMed.
- M. A. Priolo, D. Gamboa, K. M. Holder and J. C. Grunlan, Nano Lett., 2010, 10, 4970–4974 CrossRef CAS PubMed.
- K. Apaydin, T. Fouquet, M. Jimenez, S. Bourbigot and D. Ruch, RSC Adv., 2014, 4, 43326–43334 RSC.
- M. Wong, R. Ishige, K. L. White, P. Li, R. Krishnamoorti, R. Gunther, T. Higuchi, H. Jinnai, A. Takahara, R. Nishimura and H. J. Sue, Nat. Commun., 2014, 5, 3589–3598 Search PubMed.
- E. L. Cussler, S. E. Hughes and W. J. Ward, J. Membr. Sci., 1988, 38, 161–174 CrossRef CAS.
- E. Picard, J.-F. Gérardc and E. Espuchea, J. Membr. Sci., 2007, 292, 133–144 CrossRef CAS.
- L. Sun, W. J. Boo, A. Clearfield, H. Q. Pham and H.-J. Sue, J. Membr. Sci., 2008, 318, 129–136 CrossRef CAS.
- L. Y. Sun, W. J. Boo, D. Z. Sun, A. Clearfield and H. J. Sue, Chem. Mater., 2007, 19, 1749–1754 CrossRef CAS.
- M.-H. Tsai, H. Tseng, J.-C. Chiang and J.-J. Li, ACS Appl. Mater. Interfaces, 2014, 6, 8639–8645 CAS.
- P. Li, M. Wong, X. Zhang, H. Yao, R. Ishige, A. Takahar, M. Miyamoto, R. Nishimura and H.-J. Sue, ACS Photonics, 2014, 1, 79–86 CrossRef CAS.
- A. A. Balandin, S. Ghosh, W. Bao, I. Calizo, D. Teweldebrhan, F. Miao and C. N. Lau, Nano Lett., 2008, 8, 902–907 CrossRef CAS PubMed.
- J. Jiang, J. Wang and B. Li, Phys. Rev. B: Condens. Matter Mater. Phys., 2009, 80, 113405–113409 CrossRef.
- L. Chen, M. Feng and H. Zhan, RSC Adv., 2014, 4, 30689–30696 RSC.
- Y. Y. Zhang, Q. X. Pei, M. Hucd and Z. Zonge, RSC Adv., 2015, 5, 65221–65226 RSC.
- S. H. Song, K. H. Park, B. H. Kim, Y. W. Choi, G. H. Jun, D. J. Lee, B.-S. Kong, K.-W. Paik and S. Jeon, Adv. Mater., 2012, 25, 732–737 CrossRef PubMed.
- O. C. Compton, S. Kim, C. Pierre, J. M. Torkelson and S. T. Nguyen, Adv. Mater., 2010, 22, 4759–4763 CrossRef CAS PubMed.
- D. Jiang, V. R. Cooper and S. Dai, Nano Lett., 2009, 9, 4019–4024 CrossRef CAS PubMed.
- C.-H. Chang, T.-C. Huang, C.-W. Peng, T.-C. Yeh, W.-I. Hung, C.-J. Weng, T.-I. Yang, J.-M. Yeh and H.-I. Lu, Carbon, 2012, 50, 5044–5051 CrossRef CAS.
- Y.-H. Yu, Y.-Y. Lin, C.-H. Lin, C.-C. Chan and Y.-C. Huang, Polym. Chem., 2013, 5, 535–550 RSC.
- J. C. Spear, B. W. Ewers and J. D. Batteas, Nano Today, 2015, 10, 301–314 CrossRef CAS.
- J. C. Spear, J. P. Custer and J. D. Batteas, Nanoscale, 2015, 7, 10021–10029 RSC.
- K. Sint, B. Wang and P. Král, J. Am. Chem. Soc., 2008, 130, 16448–16449 CrossRef CAS PubMed.
- P. Huang, C. Ruiz-Varga, A. V. D. Zande, W. S. Whitney and D. A. Muller, Nature, 2011, 469, 389–392 CrossRef CAS PubMed.
- Y. Lee, S. Bae, H. Jang, S. Jang, S.-E. Zhu, S. H. Sim, Y. I. Song, B. H. Hong and J.-H. Ahn, Nano Lett., 2010, 10, 490–493 CrossRef CAS PubMed.
- K. White, P. Li, Y. Sumi and H.-J. Sue, J. Phys. Chem. B, 2014, 118, 362–371 CrossRef CAS PubMed.
- M. Wong, R. Ishige, T. Hoshino, S. Hawkins, P. Li, A. Takahara and H. J. Sue, Chem. Mater., 2014, 26, 1528–1537 CrossRef CAS.
- P. Li, K. L. White, C. Lin, D. Kim, A. Muliana, R. Krishnamoort, R. Nishimura and H.-J. Sue, ACS Appl. Mater. Interfaces, 2014, 6, 10188–10195 CAS.
- K. White, M. Wong, P. Li, M. Miyamoto, Y. Higaki, A. Takahara and H. J. Sue, Soft Mater., 2014, 11, 954–971 RSC.
- K. L. White, P. Li, H. Yao, R. Nishimura and H.-J. Sue, Rheol. Acta, 2014, 7, 571–583 CrossRef.
- K. Hyun, S. H. Kim, K. H. Ahn and S. J. Lee, J. Non-Newtonian Fluid Mech., 2002, 107, 51–65 CrossRef CAS.
- S. Takahashi, H. A. Goldbergb, C. A. Feeneyb, D. P. Karimb, M. Farrellb, K. O'Learya and D. R. Paula, Polymer, 2006, 47, 3083–3093 CrossRef CAS.
- F. Piroux, E. Espuche and R. Mercier, J. Membr. Sci., 2004, 232, 115–122 CrossRef CAS.
- H. J. Sue, K. T. Gam, N. Bestaoui, N. Spurr and A. Clearfield, Chem. Mater., 2004, 16, 242–249 CrossRef CAS.
- J. Biceranoa, J. F. Douglasb and D. A. Brunea, J. Macromol. Sci., Part A: Pure Appl.Chem., 1999, 39, 561–642 CrossRef.
- D. J. Chaiko and A. A. Leyva, Chem. Mater., 2005, 17, 13–19 CrossRef CAS.
- M. A. Osman, V. Mittal, M. Morbidelli and U. W. Suter, Macromolecules, 2004, 37, 7250–7257 CrossRef CAS.
- A. Yu, P. Ramesh, X. Sun, E. Bekyarova, M. E. Itkis and R. C. Haddon, Adv. Mater., 2008, 20, 4740–4744 CrossRef CAS.
- E. Bekyarova, T. Chou, E. T. Thostenson, R. C. Haddon, A. Yu, M. E. Itkis and D. Fakhrutdinov, J. Phys. Chem. C, 2007, 111, 17865–17871 CAS.
- D. Haas, J. Quijada, S. Picone and D. Birnie, Proc. SPIE, 2000, 3943, 280–284 CrossRef CAS.
- K. Bishp, C. Wilmer, S. Soh and B. Grzybowski, Small, 2009, 14, 1600–1630 CrossRef PubMed.
- L. Onsager, Ann. N. Y. Acad. Sci., 1949, 51, 627–659 CrossRef CAS.
- Z. Xu and C. Gao, ACS Nano, 2011, 4, 2908–2915 CrossRef PubMed.
- R. Jalili, S. Aboutalebi, D. Esrafilzadeh and G. Wallace, Mater. Horiz., 2014, 1, 87–94 RSC.
Footnote |
† Electronic supplementary information (ESI) available. See DOI: 10.1039/c5ra15363h |
|
This journal is © The Royal Society of Chemistry 2015 |
Click here to see how this site uses Cookies. View our privacy policy here.