DOI:
10.1039/C5RA15310G
(Paper)
RSC Adv., 2015,
5, 77019-77026
RAFT-synthesized polymers based on new ferrocenyl methacrylates and electrochemical properties†
Received
31st July 2015
, Accepted 4th September 2015
First published on 4th September 2015
Abstract
Herein are reported the synthesis and the full characterization of three new ferrocenyl monomers, namely 2-(ferrocenylmethoxy)ethyl methacrylate (FMOEMA), 3-(ferrocenylmethoxy)propyl methacrylate (FMOPMA) and 4-(ferrocenylmethoxy)butyl methacrylate (FMOBMA), synthesized from ferrocenemethanol. Homopolymers were prepared by reversible addition–fragmentation chain transfer (RAFT) polymerization in toluene at 70 °C using 2-cyanoprop-2-yl-dithiobenzoate (CPDB) as a chain transfer agent. Polymerization kinetics were compared to those of the well-known 1-ferrocenylmethyl methacrylate (FMMA). The ferrocenyl containing monomers with alkoxy linkers were found to be as reactive as FMMA in RAFT polymerization. Polymers with controlled molar masses with dispersities lower than 1.5 were obtained. The chemical structures of the monomers and polymers were fully characterized by NMR and size exclusion chromatography. Glass transition temperatures of these methacrylic polymers ranged from 36 °C to 2 °C when controlling the length of the alkoxy linker between the ferrocene unit and the backbone. The electrochemical properties of the monomers and the homopolymers were demonstrated using cyclic voltammetry.
Introduction
The incorporation of metallic redox centers into macromolecules has led to materials that combine the catalytic, magnetic, and electronic properties of metals with the desirable mechanical and processing properties of polymers. The research interest in this area has increased over the last three decades, affording a so-called class of organometallic polymers which have been used as active materials for a variety of applications such as sensing, catalysis and/or media storage.1–4 Recent advances in polymerization techniques have provided ample new opportunities to prepare polymers with tunable chemistry and composition, associated with predetermined molar masses and low dispersity values (ĐM). Furthermore, well-defined polymers with distinct microstructures including gradient, graft, and block copolymers are easy and readily prepared.5–7
Among the main applications, there is a great demand on the elaboration of smart surfaces or coatings for a wide range of applications from material science to biological and environmental concerns. For instance, biofilms could easily grow on medical equipments, biosensors, food manufacturing, water cooling systems or on marine submerged structures. Indeed, the accumulation of microorganisms (bacteria) and macroorganisms (algae, invertebrates) on surfaces causes adverse effects such as the biocontamination of medical equipments or the increase of the fuel consumption for ships. Several solutions are currently developed to prevent biofilm formation onto surfaces.8,9 For instance, although not widely reported, electrochemical polymerization or electrodeposition of polymers can be used as alternatives for making smart surfaces.10 In addition, the use of ferrocene units was reported to considerably reduce fouling on an electrode surface under electrical potential.11,12
As the ferrocene oxidation/reduction cycles could switch the surface wettability from hydrophobic to hydrophilic surfaces,13,14 we turned out our attention to the use of ferrocenyl-based polymers to prevent the adhesion of bacteria on surfaces by applying a potential. Vinylferrocene and acrylic ferrocene are known since decades and useful applications in the recent past have shown that homopolymers and block copolymers could be prepared in a controlled manner via anionic polymerization,15–19 ring-opening metathesis polymerization (ROMP)20,21 and reversible deactivation radical polymerizations22 including atom transfer radical polymerization (ATRP)14,23 and reversible addition–fragmentation chain transfer polymerization (RAFT).19,24
Herfurth et al. successfully polymerized alkyl-ferrocene methacrylic monomers in solution by conventional radical polymerization as well as by the RAFT process.25 The authors demonstrated for the first time that the ferrocene moiety is compatible with the sulfur functionalities typically used in the RAFT process.
Herein, we report the synthesis of a series of new ferrocene-containing methacrylates and their controlled homopolymerization by the RAFT process. Different alkoxy linkers were placed between the ferrocene unit and the methacrylic group, considering that these linkers could alter significantly the glass transition temperature of the resulting polymers in comparison with the well-known poly(1-ferrocenylmethyl methacrylate) (pFMMA). Kinetics studies were carried out to characterize the controlled behaviour of the polymerization process. The thermal properties of polymers were studied using differential scanning calorimetry (DSC). The electrochemical properties of these homopolymers were investigated and will be discussed.
Experimental section
Materials
Anhydrous tetrahydrofuran (THF), basic alumina, and crown ether were used as received from Acros. Cyclohexane and ethyl acetate were used as received from VWR. Methacryloyl chloride, 2-cyanoprop-2-yl-dithiobenzoate (CPDB), tetra-n-butylammonium hexafluorophosphate (n-Bu4NPF6), anhydrous dichloromethane (DCM), allyl bromide, ferrocenecarboxaldehyde, sodium hydride (NaH 60% dispersion in mineral oil), (2-bromoethoxy)-tert-butyldimethylsilane, ammonium chloride, magnesium sulfate (MgSO4), hexane, toluene, tetrabutylammonium fluoride solution (TBAF, 1 M in THF), hydrogen peroxide (H2O2), sodium hydroxide (NaOH), ethyl acetate, triethylamine (Et3N), methacryloyl chloride, potassium carbonate (K2CO3), toluene-d8, tert-butyl(4-iodobutoxy)dimethylsilane, and borane (BH3, THF complex solution, 1 M) were used as received from Aldrich. 2,2-Azobis(isobutyronitrile) (AIBN, Aldrich) was recrystallized from methanol prior to use.
Characterizations
1H-(400 MHz) and 13C-(100.6 MHz) NMR spectra were recorded on a Bruker Avance NMR spectrometer. Mass spectrometry was conducted on a Waters Micromass Q-Tof mass spectrometer, and the ionization source was a positive ion electrospray. The number average-molar mass (Mn) and dispersity (ĐM) of polymers were determined by triple detection size exclusion chromatography (TD-SEC). Analyses were performed on a Viscotek apparatus, composed of a GPC max (comprising a degasser, a pump and an autosampler) with a TDA-302 (refractive index detector, right and low angle light scattering detector at 670 nm and viscometer) and a UV detector (λ = 303 nm). The following columns were used: a Viscotek HHR-H precolumn and two Viscotek ViscoGel GMHHR-H columns. THF was used as the eluent with a flow rate of 1 mL min−1 at 30 °C. For each precipitated polymer, the refractive index increment (dn/dc) was determined using the OmniSec software, from a solution of known concentration (ca. 10 mg mL−1) filtered through a 0.2 μm PTFE filter.
Differential scanning calorimetry (DSC)
The glass transition temperatures (Tg) of the homopolymers were measured with a Q100 differential scanning calorimeter (TA Instruments). The samples were cooled down to −100 °C and then scanned at a heating rate of 20 °C min−1 from 100 to 165 °C. The Tg values were determined as the midpoint between the onset and the end of a step transition on the second heating run using the TA Instruments Universal Analysis 2000 software.
Cyclic voltammetry (CV)
Cyclic voltammograms were acquired using a BioLogic VSP300 potentiostat and the EC-Lab® software. A three-electrode system based on a platinum working electrode (diameter 1.6 mm), a platinum counter electrode and a saturated calomel reference electrode were used. n-Bu4NPF6 was used as the supporting electrolyte (0.1 M). Electrochemical reduction/oxidation potential values vs. SCE were determined from the cyclic voltammograms at a concentration of 1 × 10−3 M for monomers and 1 × 10−4 M for homopolymers with a scan rate of 10 mV s−1.
Monomers synthesis
Ferrocenemethanol (FcMeOH, 1). Ferrocenemethanol 1 was prepared by reduction of a commercially available ferrocenylcarboxaldehyde following a published synthetic procedure.17,26 Mp: 78–80 °C. 1H-NMR (400 MHz, CDCl3) δ (ppm): 1.60 (s, 1H, O
); 4.19 (s, 7H, C5
5 + C5
4); 4.25 (s, 2H, C5
4); 4.31 (s, 2H, –C
2OH). 13C-NMR (100.6 MHz, CDCl3) δ (ppm): 60.9 (–![[C with combining low line]](https://www.rsc.org/images/entities/char_0043_0332.gif)
2OH); 68.1 (
5H4); 68.5 (
5H5 +
5H4); 88.7 (
5H4).
Ferrocenyl methylmethacrylate (FMMA, 2). Under an argon atmosphere, 1.80 g of compound 1 (8.33 mmol, 1 eq.) and 15 mL of Et3N (104.70 mmol, 12.6 eq.) were dissolved in 100 mL of anhydrous DCM. To the ice-cooled solution (0 °C) 1.80 mL of methacryloyl chloride (17.65 mmol, 2.12 eq.) were added dropwise over a period of 30 min. The reaction was kept at 0 °C for 2 h then warmed up to room temperature overnight. The organic phase was washed twice with 150 mL of a saturated K2CO3 aqueous solution then with water. The combined organic phases were dried over MgSO4, filtered and the solvent was removed under reduced pressure. The obtained residue was flashed over a pad of basic alumina affording the titled compound 2 as a yellow solid (2.15 g, 87% yield). Mp: 74–75 °C. 1H-NMR (400 MHz, CDCl3) δ (ppm): 1.94 (s, 3H, ![[C with combining low line]](https://www.rsc.org/images/entities/char_0043_0332.gif)
3); 4.17 (m, 7H, Fc); 4.28 (s, 2H, Fc); 4.96 (s, 2H, ![[C with combining low line]](https://www.rsc.org/images/entities/char_0043_0332.gif)
2–Fc); 5.54 (s, 1H, ![[double bond, length as m-dash]](https://www.rsc.org/images/entities/char_e001.gif)
![[C with combining low line]](https://www.rsc.org/images/entities/char_0043_0332.gif)
2); 6.10 (s, 1H, ![[double bond, length as m-dash]](https://www.rsc.org/images/entities/char_e001.gif)
![[C with combining low line]](https://www.rsc.org/images/entities/char_0043_0332.gif)
2).23
tert-Butyl(2-(ferrocenylmethoxy)ethoxy) dimethylsilane (FMOETBDMS, 3). To a suspension of NaH (0.31 g, 7.87 mmol, 1.7 eq.) in dry THF (100 mL) was added a solution of crown ether (380 mg, 0.144 mmol) and FcMeOH (1) (1 g, 4.62 mmol, 1 eq.) in dry THF (50 mL). The reaction was stirred at room temperature for 2 h under an inert atmosphere. (2-Bromoethoxy)-tert-butyldimethylsilane (1.7 mL, 7.87 mmol, 1.7 eq.) was added dropwise. The resulting suspension was stirred overnight at room temperature. The solvent was partially removed under reduced pressure, and saturated ammonium chloride solution was added. The aqueous phase was extracted with ethyl acetate (3 × 100 mL) and the combined organic extracts were dried (MgSO4) and concentrated under vacuum. The crude product was purified by flash column chromatography over SiO2 using cyclohexane/ethyl acetate as eluent (8/2 v
:
v) leading compound 3 as an orange oil (1 g, 58% yield). 1H-NMR (400 MHz, CDCl3) δ (ppm): 0.07 (s, 6H, –OSi(CH3)2); 0.91 (s, 9H, –OSi–C(CH3)3); 3.39 (t, 2H, –![[C with combining low line]](https://www.rsc.org/images/entities/char_0043_0332.gif)
2–OSi–C(CH3)3, 3J = 6.4 Hz), 3.89 (t, 2H, Fc–CH2–O–![[C with combining low line]](https://www.rsc.org/images/entities/char_0043_0332.gif)
2–CH2–OSi–C(CH3)3, 3J = 6.4 Hz); 4.13 (m, 7H, C5H5 + C5H4), 4.20 (s, 2H, C5H4); 4.43 (s, 2H, –![[C with combining low line]](https://www.rsc.org/images/entities/char_0043_0332.gif)
2–Fc).
2-(Ferrocenylmethoxy)ethanol (FMOE, 4). To a solution of compound 3 (1 g, 2.67 mmol, 1 eq.) in dry THF was carefully added TBAF at 0 °C under a N2 atmosphere (1 M in THF, 2.93 mmol, 2.93 mL), then warmed up to room temperature for 2 h. The solvent was partially removed in vacuum. The combined organic extracts were washed with water then dried over MgSO4 and concentrated under reduced pressure. The product was purified by flash column chromatography over SiO2 using cyclohexane/ethyl acetate (7/3 v
:
v) affording compound 4 as an orange solid (0.60 g, 86% yield). Mp: 41 °C. 1H-NMR (400 MHz, CDCl3) δ (ppm): 1.97 (s, 1H, OH); 3.53 (t, 2H, Fc–CH2O–![[C with combining low line]](https://www.rsc.org/images/entities/char_0043_0332.gif)
2–, 3J = 4.4 Hz); 3.68 (q, 2H, –![[C with combining low line]](https://www.rsc.org/images/entities/char_0043_0332.gif)
2–OH, 3J = 4.8 Hz); 4.14 (m, 7H, C5H5 + C5H4); 4.24 (s, 2H, C5H4); 4.32 (s, 2H, Fc–![[C with combining low line]](https://www.rsc.org/images/entities/char_0043_0332.gif)
2–O–). 13C-NMR (100.6 MHz, CDCl3) δ (ppm): 61.8 (Fc–![[C with combining low line]](https://www.rsc.org/images/entities/char_0043_0332.gif)
2
–![[C with combining low line]](https://www.rsc.org/images/entities/char_0043_0332.gif)
2–CH2O–); 68.6 (C5H5); 69.5 (C5H4); 70.8 (C5H4); 83.1 (C5H4).
2-(Ferrocenylmethoxy)ethyl methacrylate (FMOEMA, 5). This compound was prepared like compound 2 from compound 4 (0.36 g, 1.38 mmol, 1 eq.), anhydrous DCM, Et3N (2.34 mL, 17.35 mmol, 12.6 eq.), methacryloyl chloride (0.29 mL, 2.93 mmol, 2.12 eq.) following a similar procedure used for FMMA (2) giving compound 5 as an orange oil (0.40 g, 89% yield). 1H-NMR (400 MHz, CDCl3) δ (ppm): 1.87 (s, 3H, CH3); 3.66 (t, 2H, Fc–CH2O–![[C with combining low line]](https://www.rsc.org/images/entities/char_0043_0332.gif)
2–CH2–, 3J = 4.8 Hz); 4.02 (m, 7H, C5H5 + C5H4); 4.11 (s, 2H, C5H4); 4.13 (s, 2H, –O![[C with combining low line]](https://www.rsc.org/images/entities/char_0043_0332.gif)
2–Fc); 4.18 (t, 2H, Fc–CH2O–CH2–![[C with combining low line]](https://www.rsc.org/images/entities/char_0043_0332.gif)
2O–C
O, 3J = 5.2 Hz); 5.29 (s, 1H); 6.14 (s, 1H). 13C-NMR (100.6 MHz, CDCl3) δ (ppm): 18.2 (–CH3); 63.8 (–
H2–O–
H2–
H2–O–); 67.3 (C5H5); 68.4 (C5H4); 69.3 (C5H4); 83.0 (C5H4); 125.7 (–![[C with combining low line]](https://www.rsc.org/images/entities/char_0043_0332.gif)
2
C–); 136.0 (–![[C with combining low line]](https://www.rsc.org/images/entities/char_0043_0332.gif)
CH2–); 167.3 (–![[C with combining low line]](https://www.rsc.org/images/entities/char_0043_0332.gif)
O). MS (EI), m/z calcd for C17H20FeO3 328.08; found 328 [M]+.
1-(Allyloxymethyl)ferrocene (AMF, 6). This compound was prepared from FcMeOH (1) (1 g, 4.63 mmol, 1 eq.) with anhydrous THF, allyl bromide and NaH (200 mg, 50.90 mmol, 1.1 eq.) following a similar procedure used for compound 6 to give an orange oil (1.09 g, 92% yield). 1H-NMR (400 MHz, CDCl3) δ (ppm): 4.00 (d, 2H, –OCH2–CH–, 3J = 4.8 Hz); 4.15 (s, 7H, C5H5 + C5H4); 4.26 (s, 2H, C5H4); 4.3 (s, 2H, –OCH2–Fc); 5.19 (d, 1H, CH2
CH–, 2J = 10.4 Hz trans); 5.29 (d, 1H, CH2
CH–, 2J = 17.2 Hz cis); 5.92 (m, 1H, –CH
CH2). 13C-NMR (100.6 MHz, CDCl3) δ (ppm): 68.2 (Fc–CH2O–CH2–); 68.3 (C5H5); 69.3 (C5H4); 70.6 (C5H4); 83.3 (C5H4); 116.7 (CH2
CH–); 134.8 (–CH
CH2).
3-(Ferrocenylmethoxy)propanol (FMOP-1-ol, 7). To a solution of compound 6 (1 g, 3.90 mmol, 1 eq.) in dry THF (35 mL) was added dropwise 4 mL of BH3 (1 M solution in THF) at 0 °C over a period of 1 h. After 1 h at room temperature, ice pellets were added to hydrolyse the excess of borane. The reaction mixture was cooled with an ice-bath before the addition of 0.9 mL of NaOH (3 M) followed by 0.5 mL of 30% H2O2, over a period of 1 h. After stirring 1 h at room temperature, the combined organic phases were dried over MgSO4. The crude product was purified by column chromatography over SiO2 with cyclohexane/ethyl acetate (8/2 v
:
v) affording compound 7 (0.53 g, 47% yield) as orange solids. Mp: 32 °C, 1H-NMR (400 MHz, CDCl3) δ (ppm): 1.81 (q, 2H, –OCH2–![[C with combining low line]](https://www.rsc.org/images/entities/char_0043_0332.gif)
2–CH2OH, 3J = 5.6 Hz); 2.41 (s, 1H, OH); 3.63 (t, 2H, O![[C with combining low line]](https://www.rsc.org/images/entities/char_0043_0332.gif)
2–CH2–, 3J = 6 Hz); 3.74 (q, 2H, –![[C with combining low line]](https://www.rsc.org/images/entities/char_0043_0332.gif)
2OH, 3J = 4.8 Hz); 4.13 (m, 7H, C5H5 + C5H4); 4.21 (s, 2H, C5H4); 4.28 (s, 2H, Fc–![[C with combining low line]](https://www.rsc.org/images/entities/char_0043_0332.gif)
2–O–). 13C-NMR (100.6 MHz, CDCl3) δ (ppm): 31.9 (HO–CH2–![[C with combining low line]](https://www.rsc.org/images/entities/char_0043_0332.gif)
2–CH2O–CH2–Fc); 61.8 (–CH2–![[C with combining low line]](https://www.rsc.org/images/entities/char_0043_0332.gif)
2–OH); 68.4 (Fc–![[C with combining low line]](https://www.rsc.org/images/entities/char_0043_0332.gif)
2–O–![[C with combining low line]](https://www.rsc.org/images/entities/char_0043_0332.gif)
2–); 69.0 (C5H5); 69.1 (C5H4); 69.3 (C5H4); 83.2 (C5H4). MS (EI), m/z calcd for C14H18FeO2 274.07, found 274 [M]+.
3-(Ferrocenylmethoxy)propyl methacrylate (FMOPMA, 8). The compound 8 was obtained as an orange oil after purification from the reaction of compound 7 (0.35 g, 1 eq.), Et3N (1.63 g, 12.6 eq.), and methacryloyl chloride (0.28 g, 2.12 eq.) in dry DCM (15 mL) (0.38 g, 88% yield). 1H-NMR (400 MHz, CDCl3) δ (ppm): 1.92 (m, 5H, –OCH2–![[C with combining low line]](https://www.rsc.org/images/entities/char_0043_0332.gif)
2–CH2O– and –![[C with combining low line]](https://www.rsc.org/images/entities/char_0043_0332.gif)
3); 3.51 (t, 2H, 3J = 6.4 Hz, Fc–CH2O–![[C with combining low line]](https://www.rsc.org/images/entities/char_0043_0332.gif)
2–); 4.12 (m, 7H, C5H5 + C5H4); 4.21 (m, 4H, –O![[C with combining low line]](https://www.rsc.org/images/entities/char_0043_0332.gif)
2–Fc and –O![[C with combining low line]](https://www.rsc.org/images/entities/char_0043_0332.gif)
2–CH2–); 4.26 (s, 2H, C5H4); 5.53 (s, 1H); 6.07 (s, 1H). 13C-NMR (100.6 MHz, CDCl3) δ (ppm): 18.2 (–![[C with combining low line]](https://www.rsc.org/images/entities/char_0043_0332.gif)
3); 28.9 (–OCH2–![[C with combining low line]](https://www.rsc.org/images/entities/char_0043_0332.gif)
2–CH2–O–); 61.7 (–![[C with combining low line]](https://www.rsc.org/images/entities/char_0043_0332.gif)
2O–C
O); 66.1 (Fc–![[C with combining low line]](https://www.rsc.org/images/entities/char_0043_0332.gif)
2O–![[C with combining low line]](https://www.rsc.org/images/entities/char_0043_0332.gif)
2–); 68.3 (C5H5); 69.0 (C5H4); 69.2 (C5H4); 83.4 (C5H4); 125.1 (![[C with combining low line]](https://www.rsc.org/images/entities/char_0043_0332.gif)
2
CH–); 136.2 (–![[C with combining low line]](https://www.rsc.org/images/entities/char_0043_0332.gif)
CH2); 167.1 (–C
O). MS (EI), m/z calcd for C18H22FeO3 342.09; found 342 [M]+.
tert-Butyl(4-(ferrocenylmethoxy)butoxy)dimethylsilane (FMOBTBDMS, 9). The compound 9 was prepared from compound 1 (6 g, 1 eq.), tert-butyl(4-iodobutoxy)dimethylsilane (9.6 g, 1.1 eq.), NaH (60% in mineral oil) (1.22 g, 1.1 eq.), crown ether (70 mg, 0.01 eq.) in dry THF (250 mL) following a similar procedure used for compound 3, affording 9 as an orange oil (3.90 g, 35% yield). 1H-NMR (400 MHz, CDCl3) δ (ppm): 0.06 (s, 6H, –OSi(CH3)2); 0.91 (s, 9H, –OSi–C(CH3)3); 1.59 (m, 4H, –CH2–![[C with combining low line]](https://www.rsc.org/images/entities/char_0043_0332.gif)
2–![[C with combining low line]](https://www.rsc.org/images/entities/char_0043_0332.gif)
2–CH2–); 3.44 (t, 2H, 3J = 6.4 Hz, –![[C with combining low line]](https://www.rsc.org/images/entities/char_0043_0332.gif)
2–OSi–); 3.62 (t, 2H, 3J = 6.4 Hz, Fc–CH2O–![[C with combining low line]](https://www.rsc.org/images/entities/char_0043_0332.gif)
2–); 4.14 (m, 7H, C5H5 + C5H4); 4.24 (s, 2H, C5H4); 4.27 (s, 2H, Fc–![[C with combining low line]](https://www.rsc.org/images/entities/char_0043_0332.gif)
2–O–).
4-(Ferrocenyl methoxy)butane-1-ol (FMOB, 10). This compound was prepared from compound 9 (3.9 g, 1 eq.) and TBAF (21 mL, 2.1 eq.) solution in dry THF following a similar procedure used for compound 4 leading to 10 as an orange oil (1.80 g, 65% yield). 1H-NMR (400 MHz, CDCl3) δ (ppm): 1.62 (m, 4H, –CH2–CH2–); 2.03 (s, 1H, OH); 3.45 (t, 2H, 3J = 5.6 Hz, Fc–CH2O–![[C with combining low line]](https://www.rsc.org/images/entities/char_0043_0332.gif)
2–); 3.58 (t, 2H, 3J = 5.6 Hz, –![[C with combining low line]](https://www.rsc.org/images/entities/char_0043_0332.gif)
2OH); 4.12 (m, 7H, C5H5 + C5H4); 4.21 (s, 2H, C5H4); 4.27 (s, 2H, C5H4). 13C-NMR (100.6 MHz, CDCl3) δ (ppm): 26.8 (–![[C with combining low line]](https://www.rsc.org/images/entities/char_0043_0332.gif)
2–CH2–CH2–OH); 30.2 (–![[C with combining low line]](https://www.rsc.org/images/entities/char_0043_0332.gif)
2–CH2–OH); 62.5 (–CH2–OH); 68.5 (Fc–CH2O–CH2–, 2C); 69.1 (C5H5); 69.4 (C5H4, 1C); 69.9 (C5H4, 1C); 83.2 (C5H4). MS (EI), m/z calcd for C15H20FeO2 288.08; found 288 [M]+.
4-(Ferrocenylmethoxy)butyl methacrylate (FMOBMA, 11). This compound was prepared from compound 10 (1.7 g, 1 eq.), Et3N (7.5 g, 12.60 eq.), and methacryloyl chloride (1.3 g, 2.12 eq.) in dry DCM (100 mL) following a similar procedure used for compound 2 giving compound 11 as an orange oil (1.80 g, 86% yield). 1H-NMR (400 MHz, CDCl3) δ (ppm): 1.62 (q, 2H, –O–CH2–![[C with combining low line]](https://www.rsc.org/images/entities/char_0043_0332.gif)
2–CH2–CH2–O–, 3J = 7.2 Hz); 1.67 (q, 2H, –O–CH2–CH2–![[C with combining low line]](https://www.rsc.org/images/entities/char_0043_0332.gif)
2–CH2–O–, J = 6.4 Hz); 1.91 (s, 3H, –CH3); 3.42 (t, 2H, –O![[C with combining low line]](https://www.rsc.org/images/entities/char_0043_0332.gif)
2–C
O, 3J = 6.4 Hz); 4.10 (m, 9H, C5H5 + C5H4); 4.20 (s, 2H, Fc–![[C with combining low line]](https://www.rsc.org/images/entities/char_0043_0332.gif)
2–O–); 4.24 (s, 2H, –![[C with combining low line]](https://www.rsc.org/images/entities/char_0043_0332.gif)
2–OC
O); 5.52 (s, 1H); 6.07 (s, 1H). 13C-NMR (100.6 MHz, CDCl3) δ (ppm): 18.1 (–CH3); 25.3 (Fc–CH2O–CH2–![[C with combining low line]](https://www.rsc.org/images/entities/char_0043_0332.gif)
2–); 26.1 (–![[C with combining low line]](https://www.rsc.org/images/entities/char_0043_0332.gif)
2–CH2–O–C
O); 64.3 (–![[C with combining low line]](https://www.rsc.org/images/entities/char_0043_0332.gif)
2–O–CO); 68.3 (Fc–![[C with combining low line]](https://www.rsc.org/images/entities/char_0043_0332.gif)
2O–![[C with combining low line]](https://www.rsc.org/images/entities/char_0043_0332.gif)
2–, 2C); 68.9 (C5H5); 69.1 (C5H4); 69.2 (C5H4); 83.4 (C5H4); 125.1 (![[C with combining low line]](https://www.rsc.org/images/entities/char_0043_0332.gif)
2
C–); 136.2 (–![[C with combining low line]](https://www.rsc.org/images/entities/char_0043_0332.gif)
CH2); 167.2 (–![[C with combining low line]](https://www.rsc.org/images/entities/char_0043_0332.gif)
O). MS (EI), m/z calcd for C19H24FeO3 356.10; found 356 [M]+.
Polymers synthesis
In situ 1H-NMR RAFT polymerizations were carried out in toluene-d8 at 70 °C using CPDB as chain transfer agent (CTA) and AIBN as initiator at a molar ratio [CPDB]/[AIBN] = 5. The concentration of CPDB was adjusted to the targeted number-average molar mass (Mtgn), taking into account a full conversion of monomers and the theoretical number-average molar mass Mthn, calculated with eqn (1): |
 | (1) |
where [M]0 and [CTA]0 are the initial concentrations of monomer and CTA respectively, Mmon and MCTA the molar mass of monomer and CTA respectively, conv. the monomer conversion, d the average number of chains that are formed in a termination reaction, f the initiator efficiency, kd the constant of initiator decomposition, t the half-live of the initiator and [A]0 the initiator concentration. Considering that each polymer chain contains one CTA, a simplified version of eqn (1) was used: |
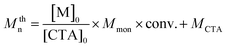 | (2) |
In a typical experiment, 160 mg of monomer 11 (FMOBMA) (0.45 mmol), 3.62 mg of CPDB (0.0164 mmol) and 0.54 mg of AIBN (0.00328 mmol) were dissolved in 0.3 mL of dry toluene-d8 in a high pressure/vacuum Wilmad NMR tube, then degassed by three cycles of freeze–pump–thaw. The polymerization occurred into the NMR apparatus, heated at 70 °C during 15 h, and followed by 1H-NMR analysis at regular times. After cooling down to room temperature, the reaction mixture was precipitated in hexane. The obtained precipitate was redissolved in toluene and reprecipitated into hexane twice. The obtained purified polymer was vacuum-dried for 24 h (30 mg, 19% yield).
Polymers from monomers 2, 5, and 8 were prepared following a similar procedure as for monomer 11 with yield values after precipitation of 20%, 20% and 23%, respectively.
The conversion of FMOBMA 11 is determined from in situ 1H-NMR analysis of the reaction mixture by comparing the integration area of peaks at 5.0 (one vinylic protons of monomer) and the peak between 3.6 at 3.0 ppm corresponding to the methylene protons (–C(O)–O–CH2–) of both monomer and polymer. The conversion of FMOBMA 11 and MNMRn were determined using eqn (3) and (4), respectively:
|
 | (3) |
|
MNMRn = XNMRn × Mmon + MCTA
| (4) |
where
MNMRn is the number of repeating unit, determined from
1H-NMR spectra by integrating the two aromatic protons of CPDB (in ortho position) that are shifted from 7.9 to 8.1 ppm when inserted at the end of the polymer chains (
eqn (5)).
|
 | (5) |
The conversion, MNMRn, and MNMRn of all the monomers 2, 5, and 8 were determined using similar equations as eqn (3)–(5).
Results and discussion
Synthesis of monomers
The synthesis of monomers 2, 5, 8 and 11 is outlined in Scheme 1. All monomers were readily obtained from ferrocenemethanol 1. Subsequent reaction of 1 with methacryloyl chloride in dry DCM in presence of Et3N affords FMMA 2 in 87% yield. Monomer 5 was prepared in three steps from 1 as follows: compound 1 was first reacted with ethyl(2-bromoethoxy-tert-butyl)dimethylsilane in dry THF in the presence of NaH affording 3 in 58% yield, followed by deprotection with TBAF in dry THF at room temperature (4, 71%) and subsequent condensation with methacryloyl chloride to give monomer 5 in 88% yield. Compound 1 was further reacted with bromoallyl in anhydrous THF in the presence of NaH affording the intermediate 6 in 92% yield. Hydroboration of the later with BH3 in THF led to the alcohol 7 in 50% yield, after column chromatography purification. Reaction between 7 and methacryloyl chloride in dry DCM in the presence of Et3N led to monomer 8 in 89% yield. The corresponding monomers structurally differ from each other by the length of the linker between the ferrocenyl moiety and the methacrylate end-group. FMOBMA 11 has the longest linker and FMOEMA 5 the shortest one.
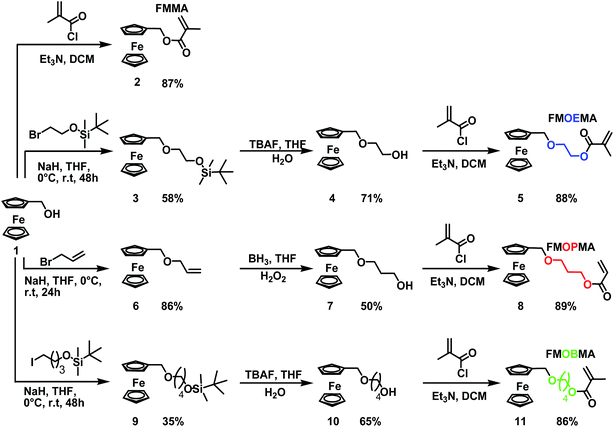 |
| Scheme 1 Synthetic pathways for ferrocenyl-methacrylate monomers. | |
RAFT polymerization of ferrocenyl methacrylate monomers
We wanted to explore the use of the RAFT process for the controlled radical polymerization of these new ferrocenyl monomers. The RAFT process is a reversible deactivation radical polymerization, which is arguably the most robust, tolerates the largest variety of monomers, and is less demanding in terms of experimental set-up, compared to other controlled polymerization processes. The key difference from a conventional free radical polymerization is the addition of a chain transfer agent (CTA) to control the polymerization.27–29 Importantly, the reactivity of the CTA must be adjusted to the reactivity of the monomer to obtain a good control over the polymerization while maintaining an ideally unaltered rate of polymerization. Consequently, CTAs best suited for the polymerization of methacrylates bear different R and Z groups30,31 from CTAs used for the polymerization of acrylates.32 2-Cyanoprop-2-yl-dithiobenzoate (CPDB) and 2,2-azobis(isobutyronitrile) were used as CTA and initiator, respectively (Scheme 2). The homopolymerizations were carried out in toluene-d8 with a molar ratio [CPDB]/[AIBN] of 5/1 at 70 °C.
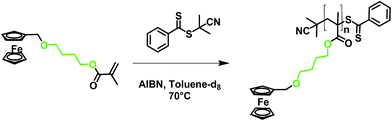 |
| Scheme 2 Synthesis of p(FMOBMA) by the RAFT process. | |
To demonstrate that the RAFT polymerization of these ferrocenyl monomers follows a controlled process, kinetics were investigated. The polymerization conditions were kept constant for all monomers in order to compare the monomers reactivities. The targeted molar mass was 10
000 g mol−1. The disappearance of the vinyl protons from the methacrylate group, around 5.6 and 5.0 ppm, and the appearance of broad peaks assigned to the main chain around 2.0 ppm (–CH2–) and 0.8–1.2 ppm (–CH3) and to the –OCH2– directly linked to the ferrocene group around 3.5 ppm except for FMMA (4.3 ppm) suggested the successful polymerization for all monomers (Fig. 1).
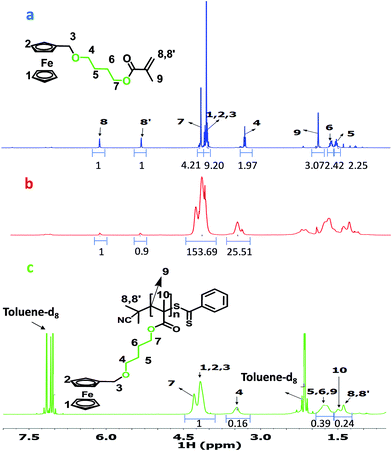 |
| Fig. 1 1H-NMR spectra of (a) FMOBMA 11, (b) the polymerization media after 15 h of reaction in toluene-d8 at 70 °C, and (c) the purified pFMOBMA homopolymer. | |
The semilogarithmic plots are shown in Fig. 2. Each polymerization showed a linear kinetic plot, indicating the control of the growth of the polymer chains with time, up to ca. 77% of monomer conversion.
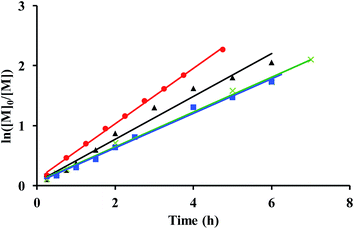 |
| Fig. 2 ln([M]0/[M]) vs. time during the RAFT polymerization of FMMA ( , 2), FMOEMA ( , 5), FMOPMA ( , 8), and FMOBMA ( , 11). [M] = 1.5 mol L−1, CTA/initiator = 5/1. | |
All ferrocenyl monomers including FMMA were found to be highly reactive in RAFT polymerization, leading to monomer conversion values up to at least 90% (ESI†). These results were reported for monomers with longer spacer groups ((4-ferrocenylbutyl methacrylate) with 4 atoms between the polymerizable and the ferrocene moiety) which polymerized under standard conditions (AIBN, 60 °C) using dodecyl-4-cyanovaleric acid trithiocarbonate (DoCVAT) as CTA.25 Fig. 2 shows that the length of the alkoxy linker affects the polymerization rate of monomers. The global polymerization constant value (kg) is ranging from 7 to 13 mol−1/2 L1/2 s−1 (Table 1).
Table 1 The global polymerization constant kg of monomers
Polymers |
kg (10−4 mol−1/2 L1/2 s−1) |
pFMMA |
13 |
pFMOEMA |
8 |
pFMOPMA |
13 |
pFMOBMA |
7 |
A linear molar mass growth with monomer conversion and low dispersities (less than 1.4) were obtained for all the polymers (Fig. 3, Table 2, and ESI†), indicating the control of the RAFT polymerization of FMMA 2, and the three new ferrocenyl monomers FMOEMA 5, FMOPMA 8, and FMOBMA 11.
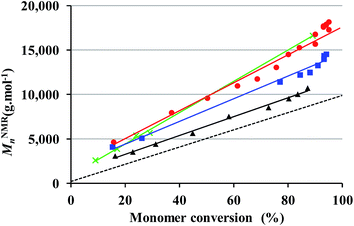 |
| Fig. 3 Evolution of MNMRn vs. monomer conversion during the RAFT polymerization of FMMA ( , 2), FMOEMA ( , 5), FMOPMA ( , 8), and FMOBMA ( , 11). [M] = 1.5 mol L−1, CTA/initiator = 5/1. Mtgn = 10 000 g mol−1. Solid lines are linear fits to the data. The dashed line is corresponding to the theoretical line. | |
Table 2 Characteristics of ferrocenyl methacrylic homopolymers prepared by the RAFT process
Polymers |
Conv.a (%) |
Mnb (g mol−1) |
MNMRnc (g mol−1) |
MTD-SECnd (g mol−1) |
ĐMd |
Calculated from eqn (3). Calculated from eqn (2). Calculated from eqn (4). Determined by TD-SEC. Additional peaks corresponding to some uncontrolled chains observed on TD-SEC chromatogram. |
pFMMA |
97 |
9600 |
15 000 |
20 400 |
1.3 |
pFMOEMA |
99 |
9900 |
14 400 |
19 400 |
1.2 |
pFMOPMAe |
99 |
9900 |
18 000 |
13 800 |
1.2 |
pFMOBMA |
89 |
8900 |
16 800 |
15 700 |
1.4 |
Thermal properties
The thermal properties of the homopolymers were characterized by DSC. Thermal behaviours of these homopolymers exhibited a strong relationship with the alkoxy linkers. As shown in ESI,† pFMOBMA, which contains the longest alkoxy linker, showed the lowest Tg around 2 °C, whereas pFMOPMA and pFMOEMA with shorter alkoxy linkers exhibited Tg at 6 and 36 °C, respectively. The Tg of pFMMA, which contains no alkoxy linker was at 106 °C. Clearly, the Tg of the polymers decreases with increasing the length of the linker between the bulky ferrocene unit and the polymer backbone. This is in agreement with variations encountered for methacrylate polymers having alkylester side chains.33
Compared to alkyl-ferrocene methacrylic polymers with butyl linker, namely the poly(4-ferrocenylbutyl methacrylate), which exhibited Tg at 40 °C,25 pFMOPMA and pFMOBMA exhibited expected and noticeable lower Tgs due to the alkoxy group. In addition, pFMOBMA and pFMOPMA exhibited a lower Tg than the poly(4-(acryloyloxy)butyl ferrocenecarboxylate)23 (Tg at 20 °C). The ether linkage is known to strongly decrease the Tg of ferrocenyl homopolymers when localized in the main chain such as poly(ferrocenyl glycidyl ether) homopolymers with a Tg value of −8 °C.34 The presence of the ether linkage in lateral groups decreases the Tg of methacrylic homopolymers to a level close to acrylic polymers and suitable for forming coatings with good film properties.
Electrochemical properties
Cyclic voltammetry (CV) of the ferrocenyl methacrylate monomers and of their corresponding homopolymers was carried out in DCM and n-Bu4NPF6 as supporting electrolyte. As expected for all monomers a reversible redox behaviour attributed to the ferrocene/ferricenium (Fc/Fc+) couple appears within the range of 448–525 mV vs. SCE (Fig. 4, Table 3 and ESI†).
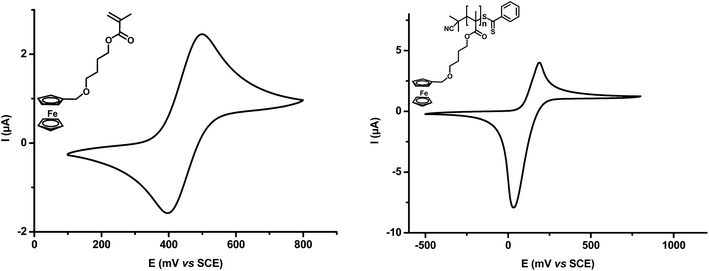 |
| Fig. 4 Cyclic voltammograms of (left) FMOBMA 11 at 1 × 10−3 M and (right) pFMOBMA at 1 × 10−4 M in 0.1 M n-Bu4NPF6/CH2Cl2 in both cases. Scan rate: 10 mV s−1, Pt working electrode, SCE reference. | |
Table 3 Anodic and cathodic potentials for monomers and homopolymers recorded in n-Bu4NPF6/CH2Cl2 at 1 × 10−3 M and 1 × 10−4 M respectively
|
Monomer (mV vs. SCE) |
Homopolymer (mV vs. SCE) |
Epa |
Epc |
E1/2 |
Epa |
Epc |
E1/2 |
FMMA |
593 |
456 |
525 |
576 |
327 |
452 |
FMOEMA |
540 |
399 |
470 |
504 |
346 |
425 |
FMOPMA |
523 |
396 |
460 |
485 |
361 |
423 |
FMOBMA |
499 |
397 |
448 |
191 |
33 |
112 |
All E1/2 redox potentials of monomers were slightly higher than the corresponding value of ferrocene (440 mV vs. SCE) in the same conditions of electrolyte and solvent (Table 3). It is in good agreement with the electron-withdrawing effect of the methacrylate group.35 The direct link of the ferrocenyl group to the ester function of methacrylate in FMMA leads to a significant increase of E1/2. The increase of the length of the alkoxy linker between the cyclopentadienyle ring and the methacrylate group leads to a negative shift of E1/2 potential in comparison with FMMA. This last result is in good correlation with a decrease of electron-withdrawing effect of the methacrylate group, coming back to the E1/2 potential of the ferrocene. As for monomers, cyclic voltammetry of homopolymers revealed a negative shift of E1/2 with the increase of the linker length between the cyclopentadienyle ring and the ester function. For all homopolymers, the peak current ratios, Ipa/Ipc were less than one which indicates an adsorption of the oxidized species followed by cathodic desorption from the electrode surface (Fig. 4 (right), Table 3 and ESI†).36,37
The number of electrons transferred during the oxidation of the polymers (ne) can be determined with the Bard–Anson electrochemical method35 using the empirical eqn (6) where Id, M, and C are the CV wave intensities of the diffusion current, molar mass, and concentration of the monomer (Id,mon, Mmon, Cmon) and polymer (Id,pol, Mpol, Cpol), respectively:
|
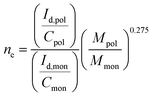 | (6) |
By assuming that the oxidation process of ferrocene is the same for monomers alone and for monomer units in the polymer, the total number of electrons transferred during the oxidation of polymers can be compared with the polymerization degree Xn obtained from TD-SEC to evaluate the oxidation ability of the ferrocenyl groups in the polymers. As shown in Table 4, the estimated values of electrons (ne) and Xn are in good agreement for all the polymers except for pFMOPMA for which small proportions of uncontrolled polymer chains are present as indicated in Table 2. The good correlation between ne and Xn values demonstrates the electroactivity of all ferrocenyl groups in homopolymers, i.e. all the ferrocenyl groups present in the homopolymers can be oxidized.
Table 4 Comparison of the number of transferred electrons ne and the polymerization degree Xn for the ferrocenyl homopolymers
Polymers |
Id,mona (μA) |
Id,pola (μA) |
neb |
XTD-SECnc |
Determined by cyclic voltammetry. Calculated with eqn (6). Determined by TD-SEC. |
pFMMA |
2.66 |
6.84 |
79.5 |
71.8 |
pFMOEMA |
2.23 |
4.64 |
58.6 |
59.1 |
pFMOPMA |
2.37 |
7.07 |
82.2 |
40.4 |
pFMOBMA |
2.42 |
4.00 |
46.1 |
44.1 |
Conclusions
In this paper, a series of new electroactive monomers based on ferrocenyl unit was synthesized with several alkoxy linkers between the ferrocene and the methacrylate groups. These new monomers were well characterized by conventional techniques (NMR, MS, etc.). The polymerization of these ferrocenyl methacrylate monomers was successfully carried out by the RAFT process. Homopolymers with controlled molar masses and low molar mass dispersities values were obtained. Electrochemical investigations on monomers and homopolymers by cyclic voltammetry showed that all ferrocenyl groups present in polymers can be oxidized. DSC investigations showed that the ether linkage reduced the Tg values to a level suitable for further forming well-ordered microphase separated nanostructures in block copolymers. Further electrochemical investigations on polymers, and potential marine bacterial anti-adhesion properties upon redox control are now under progress.
Acknowledgements
R. W. Nguema Edzang thanks the Ministère de l’Enseignement Supérieur et de la Recherche du Gabon for his PhD financial support.
Notes and references
- F. Jäkle, Chem. Rev., 2010, 110(7), 3985–4022 CrossRef PubMed.
- A. S. Abd-El-Aziz and I. Manners, Frontiers in transition metal-containing polymers; John Wiley & Sons, 2007 Search PubMed.
- A. S. Abd-El-Aziz and E. A. Strohm, Polymer, 2012, 53(22), 4879–4921 CrossRef CAS PubMed.
- X. Wang, K. Cao, Y. Liu, B. Tsang and S. Liew, J. Am. Chem. Soc., 2013, 135(9), 3399–3402 CrossRef CAS PubMed.
- N. Hadjichristidis, M. Pitsikalis, S. Pispas and H. Iatrou, Chem. Rev., 2001, 101(12), 3747–3792 CrossRef CAS PubMed.
- W. A. Braunecker and K. Matyjaszewski, Prog. Polym. Sci., 2007, 32(1), 93–146 CrossRef CAS PubMed.
- J. Nicolas, Y. Guillaneuf, C. Lefay, D. Bertin, D. Gigmes and B. Charleux, Prog. Polym. Sci., 2013, 38(1), 63–235 CrossRef CAS PubMed.
- M. Lejars, A. Margaillan and C. Bressy, Chem. Rev., 2012, 112(8), 4347–4390 CrossRef CAS PubMed.
- I. Banerjee, R. C. Pangule and R. S. Kane, Adv. Mater., 2011, 23(6), 690–718 CrossRef CAS PubMed.
- R. B. Pernites, C. M. Santos, M. Maldonado, R. R. Ponnapati, D. F. Rodrigues and R. C. Advincula, Chem. Mater., 2011, 24(5), 870–880 CrossRef.
- Y. Sun, K. Ren, J. Wang, G. Chang and J. Ji, ACS Appl. Mater. Interfaces, 2013, 5(11), 4597–4602 CAS.
- M. Okochi and T. Matsunaga, Electrochim. Acta, 1997, 42(20–22), 3247–3250 CrossRef CAS.
- J. Elbert, M. Gallei, C. Rüttiger, A. Brunsen, H. Didzoleit, B. Stühn and M. Rehahn, Organometallics, 2013, 32(20), 5873–5878 CrossRef CAS.
- J. Elbert, F. Krohm, C. Rüttiger, S. Kienle, H. Didzoleit, B. N. Balzer, T. Hugel, B. Stühn, M. Gallei and A. Brunsen, Adv. Funct. Mater., 2014, 24(11), 1591–1601 CrossRef CAS PubMed.
- A. Alkan, L. Thomi, T. Gleede and F. R. Wurm, Polym. Chem., 2015, 6, 3617–3624 RSC.
- O. Nuyken, V. Burkhardt and C. Hübsch, Macromol. Chem. Phys., 1997, 198(11), 3353–3363 CrossRef CAS PubMed.
- M. Gallei, B. V. K. J. Schmidt, R. Klein and M. Rehahn, Macromol. Rapid Commun., 2009, 30(17), 1463–1469 CrossRef CAS PubMed.
- R. H. Staff, M. Gallei, M. Mazurowski, M. Rehahn, R. Berger, K. Landfester and D. Crespy, ACS Nano, 2012, 6(10), 9042–9049 CrossRef CAS PubMed.
- B. V. K. J. Schmidt, J. Elbert, C. Barner-Kowollik and M. Gallei, Macromol. Rapid Commun., 2014, 35(7), 708–714 CrossRef CAS PubMed.
- H. Gu, A. Rapakousiou, P. Castel, N. Guidolin, N. Pinaud, J. Ruiz and D. Astruc, Organometallics, 2014, 33(16), 4323–4335 CrossRef CAS.
- J. Elbert, J. Mersini, N. Vilbrandt, C. Lederle, M. Kraska, M. Gallei, B. Stühn, H. Plenio and M. Rehahn, Macromolecules, 2013, 46(11), 4255–4267 CrossRef CAS.
- M. Kamigaito, T. Ando and M. Sawamoto, Chem. Rev., 2001, 101(12), 3689–3746 CrossRef CAS PubMed.
- C. G. Hardy, L. Ren, T. C. Tamboue and C. Tang, J. Polym. Sci., Part A: Polym. Chem., 2011, 49(6), 1409–1420 CrossRef CAS PubMed.
- J. Zhang, L. Ren, C. G. Hardy and C. Tang, Macromolecules, 2012, 45(17), 6857–6863 CrossRef CAS.
- C. Herfurth, D. Voll, J. Buller, J. Weiss, C. Barner-Kowollik and A. Laschewsky, J. Polym. Sci., Part A: Polym. Chem., 2012, 50, 108–118 CrossRef CAS PubMed.
- P. J. Graham, R. V. Lindsey, G. W. Parshall, M. L. Peterson and G. M. Whitman, J. Am. Chem. Soc., 1957, 79(13), 3416–3420 CrossRef CAS.
- J. Chiefari, Y. K. Chong, F. Ercole, J. Krstina, J. Jeffery, T. P. Le, R. T. Mayadunne, G. F. Meijs, C. L. Moad and G. Moad, Macromolecules, 1998, 31(16), 5559–5562 CrossRef CAS.
- C. Barner-Kowollik, in Handbook of RAFT Polymerization, ed. C. Barner-Kowollik, Wiley-VCH Verlag GmbH & Co. KGaA, 2008, pp. 1–4 Search PubMed.
- G. Moad, E. Rizzardo and S. H. Thang, Aust. J. Chem., 2009, 62(11), 1402–1472 CrossRef CAS.
- M. Benaglia, E. Rizzardo, A. Alberti and M. Guerra, Macromolecules, 2005, 38(8), 3129–3140 CrossRef CAS.
- C. Barner-Kowollik, J. F. Quinn, T. U. Nguyen, J. P. Heuts and T. P. Davis, Macromolecules, 2001, 34(22), 7849–7857 CrossRef CAS.
- E. Chernikova, A. Morozov, E. Leonova, E. Garina, V. Golubev, C. Bui and B. Charleux, Macromolecules, 2004, 37(17), 6329–6339 CrossRef CAS.
- E. Hempel, M. Beiner, H. Huth and E. Donth, Thermochim. Acta, 2002, 391(1–2), 219–225 CrossRef CAS.
- A. Alkan, A. Natalello, M. Wagner, H. Frey and F. R. Wurm, Macromolecules, 2014, 47(7), 2242–2249 CrossRef CAS.
- D. Astruc, C. Ornelas and J. Ruiz, Chem.–Eur. J., 2009, 15(36), 8936–8944 CrossRef CAS PubMed.
- A. F. Bard and L. R. Faulkner, Electrochemical Methods; Fundamentals and Applications, Wiley, New York, 1982 Search PubMed.
- C. M. A. Brett and A. M. Oliveira Brett, Electrochemistry, Principles, Methods and Applications, Oxford University Press, Oxford, Great Britain, 1992 Search PubMed.
Footnote |
† Electronic supplementary information (ESI) available. See DOI: 10.1039/c5ra15310g |
|
This journal is © The Royal Society of Chemistry 2015 |
Click here to see how this site uses Cookies. View our privacy policy here.