DOI:
10.1039/C5RA13847G
(Paper)
RSC Adv., 2015,
5, 79852-79859
A facile preparation of superhydrophobic and oleophilic precipitated calcium carbonate sorbent powder for oil spill clean-ups from water and land surfaces†
Received
14th July 2015
, Accepted 14th September 2015
First published on 14th September 2015
Abstract
Fabrication of superhydrophobic and oleophilic materials has attracted environment scientists due their application in oil spill clean-up. Herein, we report the preparation of superhydrophobic and oleophilic precipitated calcium carbonate sorbent via a simple and economical one-step synthetic approach using precipitated calcium carbonate as the substrate and palmitic acid as the surface modifying agent. The material is tested for its selectivity and effectiveness in the removal of spilled oil from both water and land surfaces. Test confirms the superhydrophobic character of the material with a static water contact angle of 166 ± 1°, whereas the oleophilic nature was validated from various oil uptake studies. In addition to being superhydrophobic and oleophilic, the sorbent material was found to be reusable for more than five times. Interestingly, the sorbent has high oil sorption selectivity, suitable buoyancy to float on water and possesses high oil sorption efficiencies (>99%).
1. Introduction
Removal of petroleum hydrocarbons from the water surface, resulting from an oil spill, is a thrust area of research among the different scientific groups for environment protection and related socio-economic issues. In this context, fabrication of superhydrophobic and oleophilic sorbents had drawn huge attention owing to their ease of fabrication and handy utilization at the affected site. Oil spills not only impact the aquatic ecosystem, but also affects tourism and fishing1 in addition to the loss of precious oil. The spillage of oil commonly arises from the accidental release of oil during the transportation and exploitation operations,2 which can occur on both land surfaces as well as on water bodies. Although, the land oil spill seems to be less harmful, but the oil that is washed away by the running water during rainy seasons ultimately reaches water body, after which it floats on the water surface and adversely affects the surroundings. Hence, the remediation of the ill-effects of oil spills by employing selectively oil capturing sorbents having easily recoverable property is highly warranted.
Oil sorbents are solid material that can efficiently collect the spilled oil from the affected sites leaving behind oil-free surfaces. Hence, in addition to being superhydrophobic and oleophilic, an ideal oil-sorbent should be non-toxic, buoyant, recoverable for reuse, and exhibit high selectivity as well as rate of uptake.3 These sorbents are commonly used in the form of bulk sorbent, sorbent pillow, sorbent sheets, sorbent pads, sorbent rolls, sorbent booms, etc. Among these various forms, sorbent booms by virtue of their elongated shapes are commonly used to prevent the oil from further spreading by forming an enclosed boundary around the spillage-oil on water surface, after which the bulk sorbent, sorbent pillows, sheets, rolls, etc. are applied in the enclosed area to sorb the oil. These sorbent booms, pillows, and pads usually comprise of a porous fabric bag containing hydrophobic as well as oleophilic materials as fillers. Till date, various sorbent materials have been reported in the literature for oil spill clean-ups using natural products, synthetic polymers, and inorganic materials.4 However, these materials possess their own merits and demerits. For instance, sorbents fabricated from natural products such as cotton,5–9 wool,10,11 bagasse,12 etc. are biodegradable but they have very low selectivity. On the other hand, synthetic polymers such as polypropylene,13 butyl rubber,14 etc. show excellent selectivity, however, they exhibits slow biodegradation as well as high cost. Among the inorganic materials, sorbents prepared with zeolite,15,16 graphite,17 and perlite,18,19 etc. have exhibited good biodegradability as well as selectivity, whereas they involves multiple-stage synthetic approaches. Hence, the fabrication of a superhydrophobic and oleophilic sorbent material by a facile and economical synthetic approach for selective and efficient removal of oil is urgently warranted for oil spill clean-up application. In this context, the present work attempts the fabrication of a superhydrophobic and oleophilic precipitated calcium carbonate sorbent powder with improved characteristics via a simple one-step synthetic approach, using precipitated calcium carbonate as the starting precursor and palmitic acid as the surface modifying agent. Precipitated calcium carbonate (PCC), obtained by the carbonation of hydrated lime, is a cheap non-toxic material, and commercially used in various products such as paper, plastics, paints, adhesives, sealants, and cosmetics, whereas palmitic acid (hexadecanoic acid, CH3(CH2)14CO2H) is the most common fatty acid in living organisms and widely used to produce cosmetics, soaps, and release agents. Although, superhydrophobic surfaces of PCC possessing a maximum water contact angle of 164° and 152.8° was reported by Hu et al.20 and Zhang et al.21 respectively for preparing self-cleaning surfaces, but these materials have not been studied for oil spill removal applications. Moreover, the usage of these surfaces requires the collection of polluted water for filtration through them which is difficult in dynamic water bodies. Wang et al.22 prepared hydrophobic calcium carbonate particles via a carbonation route, but the particles possess a maximum water contact angle of 96° which is not sufficient for selective oil sorption from water surface. In another approach, Arbatan and co-workers23 prepared superhydrophobic and oleophilic calcium carbonate powder with a water contact angle of 152° to selectively separate the oil from an oil–water mixture. However, the applicability of the powder for land oil spill clean-ups as well as the oil recovery and reusability of the material was not discussed. Therefore, a facile approach was put forward to prepare a superhydrophobic and oleophilic material possessing a much higher water contact angle (i.e. superior wettable character) for selective and efficient removal of oil from surfaces of both land (dry or wetlands such as swamps, marshland, etc.) as well as water bodies. The prepared sorbent powder was characterized in detail, while its wettability was confirmed through contact angle measurements as well as various laboratory experiments. The reusability of the prepared sorbent material was also investigated.
2. Experimental
2.1 Chemicals and materials
Precipitated calcium carbonate (PCC) was purchased from Merck (India), while palmitic acid, silicon oil, paraffin oil, rhodamine B, methylene blue, methyl orange and congo red were purchased from Loba Chemie (India). Sodium chloride (NaCl) was procured from RFCL (India). Crude oil was kindly provided by M/S Haldia Refinery, Haldia (India). Diesel oil, engine oil, and kerosene oil were bought from Indian Oil Fuel Station in Kharagpur (W.B., India). All the chemicals were used as received without any purifications or modifications.
2.2 Preparation of superhydrophobic and oleophilic precipitated calcium carbonate
The superhydrophobic and oleophilic precipitated calcium carbonate sorbent powder was prepared by the surface modification of PCC with palmitic acid under ambient condition (25 °C). For the preparation, initially palmitic acid (3.5 g) was dissolved in hot water (25 mL) which was then added to an aqueous dispersion of PCC (8 g in 50 mL) kept at 70 °C. The mixture was stirred at 70 °C for 90 min. Finally, the mixture was placed at 60 °C for 12 h to evaporate the water. The dried product was gently crushed to obtain the powder of superhydrophobic precipitated calcium carbonate and designated as SHPCC in the text.
2.3 Characterization techniques
X-ray diffraction (XRD) analysis of the samples were performed using Cu-Kα radiation over 2θ range of 10°–90° at a scan rate of 3° min−1 and a sampling interval of 0.05 at 40 mA and 40 kV using Bruker AXS Diffractometer D8 Powder XRD. The Fourier transform infrared (FT-IR) spectroscopic analyses were performed using Thermo Scientific Nicolet 6700 FT-IR instrument within the scan range 4000–400 cm−1. Raman spectra were collected using a micro-Raman spectrometer (MODEL T64000, Jobin Yvon Horiba, France) equipped with an optical microscope (Model BX 41, Olympus, Japan), argon–krypton mixed ion gas laser (MODEL 2018 RM, Spectra Physics, USA), and a thermoelectric cooled CCD (MODEL SynpseTM, Jobin Yvon Horiba, France) detector. Scanning electron microscopic (SEM) analyses were performed using SUPRA 40 Field Emission Scanning Electron Microscope (Carl Zeiss SMT AG, Germany) at two magnifications (viz. 36.81 k× and 150 k×) and acceleration voltage of 5 kV. Atomic force microscopic (AFM) analyses were performed using Agilent Technologies USA: AFM 5500. BET surface area measurements were performed with a Quantachrome Nova 2000e surface area and pore size analyzer. For the measurement, the samples were degassed at 338 K for 6 h. The thermal analyses [thermogravimetric analysis (TGA) and differential thermal analysis (DTA)] were performed using Netzsch STA 409 PC Luxx (Germany). The wettability tests were done by contact angle measurements with water (pH = 6.2) using Ramé-Hart Automated Goniometer, model 290-G using the sessile drop method. For the measurements, the powder was pressed on a glass slide to make a uniform and smooth thin layer.
2.4 Oil sorption capacity studies
The oil sorption capacity (OSC) of the SHPCC sorbent powder was performed quantitatively to determine its maximum oil sorption ability towards different oil samples. Two different studies were performed using six different oils viz. crude oil (viscosity, η = 4.3 cP), engine oil (η = 239.2 cP), diesel oil (η = 3.17 cP), kerosene oil (η = 2.71 cP), paraffin oil (η = 34.6 cP), and silicon oil (η = 13.8 cP). In the first study, the effect of NaCl concentration, pH and temperature on the OSC of SHPCC was determined using oil–water mixtures (oil–water ratio being 1
:
20 (w/w)), where oil was added to water and shaked for 10 min at 120 rpm. For studying the effect of NaCl concentration on OSC of SHPCC at 25 °C, NaCl was added to the water with concentrations varying from 0.0 to 0.5 M, while the amount of sorbent powder was kept constant (1 g). On the other hand, the effect of pH (in the pH range of 5.0 to 9.0 at 25 °C) and temperature (over the range of 10 to 50 °C) were studied using fresh water (having no NaCl) in the oil–water mixture and 1 g of SHPCC. For all the studies, the sorbent powder was added to the oil–water mixture, mixed and left for 10 min for complete sorption of the oil. After sorption of oil, the floating oil-sorbed powder was collected by scooping technique and weighed. The oil sorption capacity (q, in g g−1) was calculated using the following eqn (1).24,25where, WT is the total weight of oil sorbed SHPCC (in g) and WS is the initial weight of SHPCC (in g). All the experiments were performed in triplicate and the errors in the values of q were estimated as ±0.001–0.002 g g−1.
The second study was performed in pure oil medium, where 1 g of the SHPCC sorbent powder was added to excess amount of the six oil samples in six different beakers at 25 °C and stirred for 10 minutes for complete sorption of the oil by the powder. The mixture was then filtered through a pre-weighed whatman filter paper (previously soaked in the oil) and the excess oil was allowed to drain off completely. Finally, the filter paper containing the oil sorbed powder was weighed. The amount of oil sorbed by the powder was calculated by subtracting the weight of the oiled filter paper and SHPCC powder (1 g) from the total weight of the filter paper containing the oil sorbed powder. The amount of oil sorbed by PCC was similarly determined in oil medium by following the same procedure. Both the experiments were performed in triplicate and the error values in results are in the range of ± 0.002–0.004 g g−1.
2.5 Oil sorption efficiency study
The efficiency of the SHPCC sorbent powder to selectively sorb oil from oil–water mixture at 25 °C was investigated by following an earlier reported procedure.23 For the study, oil–water mixtures of varying ratios using fresh water (zero NaCl) and six different oil samples (viz. crude oil, engine oil, diesel oil, kerosene oil, paraffin oil, and silicon oil) were prepared to which the SHPCC sorbent powder was added for selective sorption of the oil. For all the oil samples, the oil–water ratio was varied from 0.005 to 0.025 (w/w), maintaining a total volume of 50 mL and the weight of the powder was equal to the weight of the oil in the oil–water mixture. After the sorption of oil by the SHPCC powder, the solid lump was removed from the water surface and the remaining water is weighed. The oil sorption efficiency (OSE) was determined using eqn (2). |
OSE = (WWR/WWI) × 100
| (2) |
where, WWR is the weight of recovered water and WWI is the initial weight of water. The experiments were performed in triplicate and the errors in the values were ±0.2%.
2.6 Reusability tests
Reusability tests of the SHPCC sorbent powder was performed in pure crude oil medium, where the sorbent powder was regenerated for further use by simply washing the crude oil sorbed powder with tetrahydrofuran (THF).24 In brief, the crude oil sorbed powder was collected and washed three times with THF, followed by drying at 50 °C for 5 h. The dried powder was again added to crude oil to test its usability. The tests were performed for five consecutive cycles of the sorption process. The applicability of the regenerated powder, after each sorption cycle, for usage in oil spill clean-up application was determined by water contact angle measurements. The crude oil and THF was separated from the crude oil–THF mixture (obtained after the washing process) by solvent evaporation technique (using rotary evaporator). The amount of recovered oil after each sorption cycle was calculated using eqn (3). |
Oil recovery = (WOR/WOI) × 100
| (3) |
where, WOR is the weight of recovered oil and WOI is the initial weight of sorbed oil.
3. Results and discussion
3.1 Characterization of SHPCC
The crystalline phase and purity of SHPCC as well as the as-received PCC powder was determined from the XRD analysis and the patterns are shown in Fig. 1. The XRD pattern of PCC (Fig. 1a) was found to be consistent with JCPDS file no. 72-1652, corresponding to the calcite phase of calcium carbonate.26 The diffraction peaks observed at 2θ values of 23.05, 29.43, 35.88, 39.33, 43.08, 47.51, and 48.49° can be assigned to the (012), (104), (110), (113), (202), (018), and (116) crystal planes of calcite respectively. On the other hand, the XRD pattern for SHPCC (Fig. 1b) was observed to be similar to that of PCC without any peaks attributing to the palmitic acid molecules. This similarity in the XRD pattern suggests the proper coating of PCC with palmitic acid without leaving any residues of the surface modifying agent. Consequently, SHPCC retains the crystalline phase of PCC even after the treatment with palmitic acid.
 |
| Fig. 1 XRD patterns of PCC (a) and SHPCC (b). | |
The functional group analyses of SHPCC as well as PCC powder was performed from their respective FT-IR spectra which are shown in Fig. 2. The FT-IR spectra of both the samples (PCC and SHPCC) shows peak at 1460 cm−1 which corresponds to the asymmetric stretching (υ3) of the carbonate C–O bond, while the peak observed at 873 cm−1 corresponds to the out-of-plane bending vibration (υ2) of carbonate. The in-plane bending vibration (υ4) was observed at 712 cm−1 in both the samples. The peaks at 2513 and 1796 cm−1 are the combination band of (υ1 + υ3) and (υ1 + υ4), respectively.27 In addition to the peaks corresponding to the carbonate group, the FT-IR spectrum of PCC (Fig. 2a) shows a broad peak at around 3446 cm−1 corresponding to O–H stretching present in the adsorbed water molecules. However, in the FT-IR spectrum of SHPCC powder (Fig. 2b), the intensity of the peak at 3434 cm−1 corresponding to O–H stretching is much lowered which might be due to the hydrophobic character of the powder attained after the surface modification with palmitic acid. Apart from the characteristic peaks corresponding to the carbonate group, the FT-IR spectrum of SHPCC shows two extra peaks at 2917 and 2851 cm−1 that can be assigned to the stretching mode of C–H bond. Another peak at 1081 cm−1 in SHPCC can be attributed to stretching mode of C–O bond present in palmitic acid, validating the presence of the fatty acid on the surface of SHPCC. Further, a peak starts appearing below 440 cm−1 in SHPCC (inset of Fig. 2) which can be assigned to Ca–O bond28 present in calcium palmitate, indicating the presence of palmitic acid in its salt form rather than in its free form. In the Raman spectrum of palmitic acid, the peaks at 1439, 1296, 1063, and 893 cm−1 corresponding to CH2, C–C–H, C–O, and C–H vibrations respectively are observed to be shifted to 1442, 1295, 1064, and 890 cm−1 respectively in SHPCC (Fig. S1†). These shifts in the vibrational frequency further validate the presence of palmitic acid in its salt form (i.e. calcium palmitate) in SHPCC.
 |
| Fig. 2 FT-IR spectra of PCC (a) and SHPCC (b) (inset: spectrum of SHPCC from 400–550 cm−1). | |
The surface morphology of SHPCC and PCC was analyzed from their respective SEM images. The SEM images (shown in Fig. 3) indicate that most of the particles are elongated with needle-shaped morphology in both the samples. The surface of PCC was observed to be smooth (Fig. 3c), whereas SHPCC possesses rough surface (Fig. 3d). The rough surface of SHPCC can be attributed to the presence of insoluble calcium palmitate on their surface, after the treatment with palmitic acid. A similar effect was observed by Arbatan et al.23 on treatment of PCC with stearic acid. The AFM images (phase contrast) of the samples show that PCC exhibits a surface roughness (root mean square height, sq) value of 0.85 nm, while SHPCC exhibits a surface roughness value of 2.18 nm (Fig. S2†). This variation in surface roughness of the samples can again be attributed to the presence of calcium palmitate on the surface of SHPCC.
 |
| Fig. 3 SEM images of PCC (a and c) and SHPCC (b and d). | |
The presence of palmitic acid in SHPCC was further confirmed from the thermal behavior of PCC and SHPCC which was determined from their respective TGA-DTA curves represented in Fig. 4. For measurements, the samples were heated in alumina crucibles from 45 to 700 °C at a heating rate of 20 °C min−1 under nitrogen atmosphere. The TGA curve of PCC (Fig. 4a) shows two regions of significant weight loss. The first weight loss of ∼3.4% from 45 to ∼425 °C, which is accompanied by a broad endothermic peak centered at 103 °C in the DTA curve (Fig. 4b), can be assigned to the loss of water molecules from the sample. The second weight loss from ∼608 °C in the TGA curve can be assigned to the decomposition of calcium carbonate to calcium oxide and carbon dioxide which is again accompanied by an endothermic peak starting at ∼608 °C in the DTA curve. On the other hand, the TGA curve of SHPCC (Fig. 4a) shows a three-stage pattern for weight loss in the temperature ranges of 45–357, 357–516, and 608–700 °C. The first and third weight loss can be assigned to the dehydration and decomposition of calcium carbonate respectively reflected by endothermic peaks in the DTA curve (Fig. 4b) at the corresponding temperature regions. The second weight loss of ∼4.5% in the TGA curve which is accompanied by an exothermic peak centered at 497 °C in the DTA curve can be attributed to the combustion of palmitic acid molecules, thereby confirming the presence of palmitic acid in SHPCC.
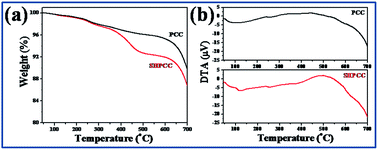 |
| Fig. 4 TGA (a) and DTA (b) curves of PCC and SHPCC. | |
The BET surface area of PCC and SHPCC were determined from their nitrogen adsorption–desorption isotherms at 77 K (Fig. S3 and S4†). The surface area of the samples, calculated using the Brunauer–Emmett–Teller (BET) method, was observed to be 6.852 and 15.890 m2 g−1 for PCC and SHPCC respectively. The higher surface area in SHPCC compared to PCC might be due to the surface roughness generated on SHPCC after its surface modification with palmitic acid. Since sorption is a surface area dependent process, the higher surface area of SHPCC is expected to enhance the sorption process thereby encouraging its suitability for usage as a sorbent material.
3.2 Wettability tests
The wettability test of the SHPCC powder reveals a static water contact angle value of 166 ± 1°, thereby confirming its superhydrophobic character (Fig. 5a). The observed static water contact angle value for SHPCC was found to be much higher as compared to the previously prepared hydrophobic materials using PCC as the precursor. For instance, the sorbent material prepared by Arbatan et al.23 using PCC and stearic acid was found to possess a water contact angle of 152°, while Wang et al.22 produced hydrophobic calcium carbonate particles with a water contact angle of 96°. The optical image, shown in Fig. 5b, further substantiates the non-wettable behaviour of SHPCC towards water. Interestingly, the water drop (dyed with methylene blue, pH = 7) remains static and un-absorbed by the powder for more than 12 h at ambient condition (25 °C), while the oil samples (crude oil, diesel oil and engine oil) readily spreads/penetrates into the powder within 30 s, depicting its significant oleophilic character. The rapid oil uptake by the SHPCC powder is presented in Fig. S5,† where it was found that 10 μL crude oil was sorbed by SHPCC within 2.5 s.
 |
| Fig. 5 Water contact angle measurement on SHPCC (a); optical image of water (dyed with methylene blue), crude oil, diesel oil, and engine oil droplets on SHPCC (b). | |
The superhydrophobic character of the SHPCC powder can be attributed to presence of palmitic acid on the surface of PCC with their long hydrophobic tail (i.e. the alkyl chain) pointing outwards, as represented in the schematic diagram in Fig. 6, thereby generating a non-wettable behavior towards water. The superhydrophobic character can also be attributed to the surface roughness of SHPCC after modification with palmitic acid.
 |
| Fig. 6 Schematic representation for the SHPCC formation from PCC. | |
3.3 Buoyancy and selectivity studies
The buoyancy and selectivity of the SHPCC powder was determined qualitatively and the results are demonstrated in Fig. 7. The study was performed in oil–water mixture (oil–water ratio being 1
:
60 w/w) using distilled water (60 g) and three different oil samples (viz. crude oil (brown colored), diesel oil (light yellow colored) and kerosene oil (light blue colored); each 1 g). It was observed that on adding the SHPCC sorbent powder (1 g) to the oil–water mixture, the powder selectively sorbs the oil forming a semi-solid mass and floats on the water surface (Fig. 7b and c), depicting its buoyant as well as selective nature. These behaviours of the SHPCC powder can be attributed to its superhydrophobic as well as oleophilic character rendering it to selectively sorb the oil and float on the water surface. After complete sorption of the oil, the semi-solid can be easily removed by scooping technique leaving behind oil-free water (Fig. 7e).
 |
| Fig. 7 Qualitative demonstration showing the buoyancy and selectivity of the SHPCC powder: oil–water mixtures (a); after adding SHPCC to the mixtures: front view (b), top view (c); oil-sorbed SHPCC powder (d); clear water after the removal of oil-sorbed SHPCC powder (e). | |
3.4 Oil sorption capacity studies
The maximum oil sorption ability of the SHPCC sorbent powder was determined through the quantitative oil sorption capacity (OSC) studies, where two different studies were performed. The first study (performed with oil–water mixtures) was done to verify the OSC of the sorbent powder in water bodies, while the second study (performed with only oil) was done to verify the OSC of the sorbent on land surfaces. From the first study, the maximum OSC of SHPCC for crude oil, engine oil, diesel oil, kerosene oil, paraffin oil, and silicon oil, calculated from the plot of OSC versus varying sorbent weight using eqn (1) at 25 °C (Fig. 8a), was found to be 1.12, 1.85, 1.09, 1.05, 1.43, and 1.24 g g−1 respectively. This variation in the OSC of SHPCC towards different oil samples can be correlated with their viscosity. The oil with the highest viscosity will adhere strongly with SHPCC via intermolecular hydrophobic interaction resulting in higher OSC value.29
 |
| Fig. 8 Oil sorption capacity of SHPCC under variation of sorbent weight (a) and NaCl concentration (b) for different oil samples in oil–water mixture. | |
Among the six oil samples used in the present study, engine oil (viscosity, η = 239.2 cP) possesses the highest viscosity and hence adheres strongly with SHPCC resulting in the highest OSC value, while kerosene oil (possessing the lowest viscosity, η = 2.71 cP) adheres weakly resulting in the poor OSC values. The study of variation in OSC of SHPCC with NaCl concentration towards various oil samples, shown in Fig. 8b, illustrates that the concentration of NaCl has no remarkable effect on the OSC values for all the oil samples. This could be due to the superhydrophobic character as well as sufficient buoyancy of the material, which in turn prevent the material from interaction with the electrolyte in water (Fig. 7). The concentration of NaCl in the aqueous medium also can increase density of water by which it enhances the buoyancy of materials.30
Since, SHPCC retains sufficient buoyancy even after completely sorbing the oil, the concentration of NaCl doesn't affect its OSC values indicating the suitability of the sorbent to work in both fresh water (without any NaCl) as well as salt water bodies.
The oil sorption capacity of SHPCC is varied under different temperature (in Fig. 9a), which indicates the optimum temperature for selective and efficient sorption of oil by the sorbent powder in the range of 20–30 °C for all the oil samples, thereby indicating the presence of adsorption phenomenon in the oil removal process as adsorption is a temperature-dependent process. On the other hand, the study of variation in OSC of SHPCC in the pH values of 5, 7, and 9 (Fig. 9b) shows no remarkable change in the OSC values for all the oil samples, indicating that pH of the aqueous medium doesn't affect the wettability of SHPCC powder and hence the sorbent can be applied for selective oil removal in a wide range of corrosive liquids from acidic to basic aqueous solutions.
 |
| Fig. 9 OSC of SHPCC at different temperature (a) and pH (b) for different oil samples in oil–water mixture. Optical image of water drops at different pH on SHPCC: pH 3 (water dyed with rhodamine B), pH 5 (water dyed with methyl orange), pH 7 (pure water), pH 9 (water dyed with congo red), pH 11 (water dyed with methylene blue). | |
Table 1 presents a comparison of the oil sorption capacity of SHPCC with those of some typical sorbents reported in the literature. Although the OSC of SHPCC for crude oil is slightly lower than that reported by Sayed et al.31 but SHPCC exhibits excellent superhydrophobic character (water contact angle 166 ± 1°), which is crucial for selective removal of oil from the affected area. Apart from that the sorbent should be reusable for multiple usages, and hence, recycling studies were carried out on the material after recovery from oil sorption experiments.
Table 1 The oil sorption capacity values of some sorbents reported in the literature
Sorbent |
Oil |
Oil sorption capacity (g g−1) |
Water contact angle (°) |
Literature |
Zeolitic fly ash powders |
ParaLux 701 paraffinic process oil |
1.10, 1.02, 0.86, and 1.15 |
147 |
16 |
Treated CaCO3 |
Crude oil |
1.25 |
— |
31 |
CaCO3 |
Crude oil |
0.201 |
— |
32 |
Aswanly clay and CaCO3 mixture |
Crude oil |
0.112 |
— |
32 |
Precipitated calcium carbonate |
Diesel oil and crude oil |
— |
152 |
23 |
Hydrophobic CaCO3 particles |
— |
— |
96 |
22 |
Precipitated calcium carbonate |
Crude oil, engine oil, diesel oil, kerosene oil, paraffin oil, and silicon oil |
1.12, 1.85, 1.09, 1.05, 1.43, and 1.24 |
166 ± 1 |
Present work |
The second study (performed with only oil to determine the OSC of the sorbent on land surfaces) shows that SHPCC exhibits slightly higher OSC values compared to PCC for all the oil samples (Fig. 10a). This slight enhancement in the OSC value of SHPCC can be attributed to its higher surface area (observed in the BET measurements) that provides a larger surface for the sorption of oil. The OSC values of SHPCC were found to be equal as the maximum OSC values observed in oil–water mixture (Fig. 8a), indicating its similar oleophilic behavior in both the situations. Further, the OSC values of both the materials (PCC and SHPCC) for the six oil samples was observed to follow similar trend as observed in the first study, performed in oil–water mixture, where the OSC is highest for engine oil (most viscous) followed by paraffin oil, silicon oil, crude oil, diesel oil and finally kerosene oil (least viscous). The qualitative demonstration, shown in Fig. 10b–d, substantiates the applicability of SHPCC for land oil spill clean-ups, where 1 g of the sorbent powder was observe to sorb 1 g of crude oil completely from a dry petri dish.
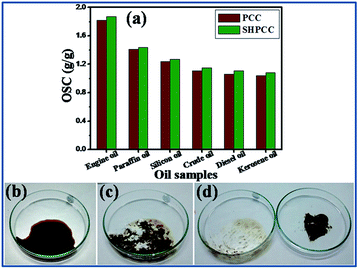 |
| Fig. 10 OSC of SHPCC and PCC in pure oil samples (a); qualitative demonstration showing the usage of SHPCC for land oil spill clean-ups (b–d). | |
3.5 Oil sorption efficiency study
The efficiency of the prepared SHPCC sorbent powder for selective sorption of the oil slick formed on the water surface after an oil spill was determined from the oil sorption efficiency study performed with oil–water mixture and the results are shown in Fig. 11. It was observed that the SHPCC sorbent power is efficient in sorbing the oil slick by more than 99% for all the oil samples and for all the oil–water mixtures (oil–water ratio varying from 0.005 to 0.025 (w/w)). The superior efficiency of the sorbent powder to selectively sorb the oil slick from the water surface can be attributed to its superhydrophobic and oleophilic character which enable it to repel the water and selectively sorb the oil from the mixtures. The very slight loss of water (<1%) might be due the sticking of water molecules to the oil-sorbed powder (or the oil) during the scooping process. Further, separate studies would be required to know the interaction of water with different oil samples or their components.
 |
| Fig. 11 Oil sorption efficiency of SHPCC from oil–water mixtures of different ratios. | |
3.6 Reusability tests
The reusability of the prepared SHPCC sorbent powder for repeated usage in oil spill removal application was tested through the reusability test and the results are shown in Fig. 12. The wettability test performed through contact angle measurements using water reveals a static water contact angle of 157.6°, 157.1°, 156.8°, 155.7°, and 150.2° for the first (Fig. 12a), second (Fig. 12b), third (Fig. 12c), fourth (Fig. 12d), and fifth (Fig. 12e) sorption cycle respectively indicating the retention of superhydrophobic character by the regenerated powder. The wettability tests confirm that the prepared SHPCC sorbent powder is reusable for more than five times with a very slight decrease in its superhydrophobic character. The optical image (Fig. 12) shows the water droplets on the surface of the regenerated sorbent powder, which further substantiate their superhydrophobic nature and encourages their repeatable usage in oil spill clean-up application. The oil recovered from the crude oil-THF mixture via the solvent evaporation technique (using rotary evaporator) was observed to be >98% for each of the regenerated sorbent powder (Table S1†).
 |
| Fig. 12 Water contact angle and optical image of water drops on the regenerated SHPCC powder: first cycle (a), second cycle (b), third cycle (c), fourth cycle (d), fifth cycle (e). | |
4. Conclusions
In summary, a superhydrophobic and oleophilic sorbent powder was fabricated successfully by a simple and inexpensive methodology involving the surface coating of palmitic acid on precipitated calcium carbonate. The prepared sorbent powder has significant selectivity and efficiency for the removal of wide variety of oil samples from land surfaces and water bodies. Contact angle measurement shows an interesting value of 166 ± 1° (static water contact angle value), which confirms the excellent non-wettable behavior of the sorbent towards water. The prepared sorbent also exhibits remarkable buoyancy.
The superhydrophobicity, oleophilicity, excellent selectivity, more than five times reusability, excellent oil sorption efficiency (>99%), and applicability in a wide range of corrosive liquids prove the material as an ideal sorbent for the removal of various kinds of oils. We believe that the prepared sorbent powder could be a potential candidate for removal of spilled oil from both water and land surfaces (both dry and wetlands). Moreover, we hope the preparation methodology of sorbent could be scaled up to the commercial need like either used as fillers in sorbent booms, pillows and pads for selectively sorption of the spilled oil from the land and water surface, or directly sprinkled on the spilled oil.
Acknowledgements
This work is financially supported by MoES, New Delhi. Authors are grateful to Prof. S. Dasgupta, Department of Chemical Engineering, IIT Kharagpur for helping us in recording the contact angle measurements.
Notes and references
- M. D. Garza-Gil, A. Prada-Blanco and M. X. Vazquez-Rodriguez, Ecol. Econ., 2006, 58, 842–849 CrossRef PubMed.
- X. C. Gui, H. B. Li, K. L. Wang, J. Q. Wei, Y. Jia, Z. Li, L. L. Fan, A. Y. Cao, H. W. Zhu and D. H. Wu, Acta Mater., 2011, 59, 4798–4804 CrossRef CAS PubMed.
- J. Y. Lin, Y. W. Shang, B. Ding, J. M. Yang, J. Y. Yu and S. S. Al-Deyab, Mar. Pollut. Bull., 2012, 64, 347–352 CrossRef CAS PubMed.
- C. Teas, S. Kalligeros, F. Zanikos, S. Stournas, E. Lois and G. Anastopoulos, Desalination, 2001, 140, 259–264 CrossRef CAS.
- H. C. Bi, Z. Y. Yin, X. H. Cao, X. Xie, C. L. Tan, X. Huang, B. Chen, F. T. Chen, Q. L. Yang, X. Y. Bu, X. H. Lu, L. T. Sun and H. Zhang, Adv. Mater., 2013, 25, 5916–5921 CrossRef CAS PubMed.
- G. Deschamps, H. Caruel, M. E. Borredon, C. Bonnin and C. Vignoles, Environ. Sci. Technol., 2003, 37, 1013–1015 CrossRef CAS.
- H. M. Choi, J. Environ. Sci. Health, Part A: Environ. Sci. Eng. Toxic Hazard. Subst. Control, 1996, 31, 1441–1457 CrossRef PubMed.
- S. Suni, A. L. Kosunen, M. Hautala, A. Pasila and M. Romantschuk, Mar. Pollut. Bull., 2004, 49, 916–921 CrossRef CAS PubMed.
- B. Wang, R. Karthikeyan, X. Y. Lu, J. Xuan and M. K. H. Leung, Ind. Eng. Chem. Res., 2013, 52, 18251–18261 CrossRef CAS.
- M. M. Radetic, D. M. Jocic, P. M. Iovantic, Z. L. Petrovic and H. F. Thomas, Environ. Sci. Technol., 2003, 37, 1008–1012 CrossRef CAS.
- V. Rajakovic, G. Aleksic, M. Radetic and L. Rajakovic, J. Hazard. Mater., 2007, 143, 494–499 CrossRef CAS PubMed.
- M. Hussein, A. A. Amer and I. I. Sawsan, J. Anal. Appl. Pyrolysis, 2008, 82, 205–211 CrossRef CAS PubMed.
- E. L. Schrader, Environ. Geol. Water Sci., 1991, 17, 157–166 CrossRef CAS.
- D. Ceylan, S. Dogu, B. Karacik, S. D. Yakan, O. S. Okay and O. Okay, Environ. Sci. Technol., 2009, 43, 3846–3852 CrossRef CAS.
- Q. Wen, J. C. Di, L. Jiang, J. H. Yu and R. R. Xu, Chem. Sci., 2013, 4, 591–595 RSC.
- T. Sakthivel, D. L. Reid, I. Goldstein, L. Hench and S. Seal, Environ. Sci. Technol., 2013, 47, 5843–5850 CrossRef CAS PubMed.
- M. Toyoda and M. Inagaki, Spill Sci. Technol. Bull., 2003, 8, 467–474 CrossRef CAS.
- D. Bastani, A. A. Safekordi, A. Alihosseini and V. Taghikhani, Sep. Purif. Technol., 2006, 52, 295–300 CrossRef CAS PubMed.
- M. Roulia, K. Chassapis, C. Fotinopoulos, T. Savvidis and D. Katakis, Spill Sci. Technol. Bull., 2003, 8, 425–431 CrossRef CAS.
- Z. S. Hu and Y. L. Deng, Ind. Eng. Chem. Res., 2010, 49, 5625–5630 CrossRef CAS.
- H. Zhang, X. F. Zeng, Y. F. Gao, F. Shi, P. Y. Zhang and J. F. Chen, Ind. Eng. Chem. Res., 2011, 50, 3089–3094 CrossRef CAS.
- C. Y. Wang, C. Piao, X. L. Zhai, F. N. Hickman and J. Li, Powder Technol., 2010, 198, 131–134 CrossRef CAS PubMed.
- T. Arbatan, X. Y. Fang and W. Shen, Chem. Eng. J., 2011, 166, 787–791 CrossRef CAS PubMed.
- M. Patowary, R. Ananthakrishnan and K. Pathak, Appl. Surf. Sci., 2014, 320, 294–300 CrossRef CAS PubMed.
- N. Kannan and A. Rajakumar, Indian J. Environ. Prot., 2009, 29, 533–538 CAS.
- C. L. Yao, A. J. Xie, Y. H. Shen, J. M. Zhu and T. J. Li, J. Chil. Chem. Soc., 2013, 58, 2235–2238 CrossRef CAS.
- B. Xu and K. M. Poduska, Phys. Chem. Chem. Phys., 2014, 16, 17634–17639 RSC.
- M. Sadeghi and M. H. Husseini, J. Appl. Chem. Res., 2013, 7, 39–49 Search PubMed.
- D. Ceylan, S. Dogu, B. Karacik, S. D. Yakan, O. S. Okay and O. Okay, Environ. Sci. Technol., 2009, 43, 3846–3852 CrossRef CAS.
- S. A. Sayed and A. M. Zayed, Desalination, 2006, 194, 90–100 CrossRef CAS PubMed.
- S. A. Sayed, A. S. El Sayed and A. M. Zayed, J. Appl. Sci. Environ. Manage., 2004, 8, 71–80 CAS.
- S. A. Sayed, A. S. El Sayed, S. M. El Kareish and A. M. Zayed, J. Appl. Sci. Environ. Manage., 2003, 7, 25–35 CAS.
Footnote |
† Electronic supplementary information (ESI) available: Raman spectra, AFM images, nitrogen adsorption–desorption isotherms and images showing the rate of up-take of crude oil by SHPCC. Data for the oil-recovery experiment is also presented. See DOI: 10.1039/c5ra13847g |
|
This journal is © The Royal Society of Chemistry 2015 |
Click here to see how this site uses Cookies. View our privacy policy here.