DOI:
10.1039/C5RA12859E
(Paper)
RSC Adv., 2015,
5, 70856-70867
From a bio-based phosphorus-containing epoxy monomer to fully bio-based flame-retardant thermosets†
Received
2nd July 2015
, Accepted 5th August 2015
First published on 5th August 2015
Abstract
In this work, phloroglucinol was used as a renewable resource to prepare an epoxy monomer and phosphorus containing reactive flame retardant (FR). These building blocks were reacted with diamines to obtain partly or fully bio-based flame retardant epoxy resins. It was highlighted that the glass transition temperature of the materials was tightly related to the functionality of the reactive monomers and the resulting crosslink density. Thermal stability and char yield of the thermosets seems to be mainly governed by the aromaticity of the monomers, the linking rate of the aromatic ring and the phosphorus content. Phosphorus FR are more efficient in intrinsically poorly charring matrices. It was evidenced that the flammability of bio-based epoxies can be monitored by two strategies: (i) choosing bio-based monomers with high charring ability and low combustion energy, (ii) incorporating bio-based phosphorus-containing reactive FR in the polymer network.
Introduction
During the last fifteen years, there has been a huge interest in the development of polymers from renewable resources. These research efforts intend to find alternatives to oil-based polymers and to limit the environmental impact of polymer production. Among polymeric materials, epoxy resins are an important class of thermosets widely used for their intrinsic characteristics, such as excellent mechanical properties, adhesion or thermal resistance. They have many applications such as in adhesives, coatings, electronic components and materials for energy. Numerous studies have been carried out to obtain epoxies from bio-based molecules. A good overview of these attempts can be found in the review of Auvergne et al.1 Various fractions of the biomass are likely to be utilized to prepare epoxy monomers or hardeners: the carbohydrate fraction (starch,2 sugar3), the lipid fraction (vegetable oils,4 terpene5), or the phenolic fraction (polyphenol, tannins,6 vanillin7). Recently, Chang et al. synthesized the first fully bio-based epoxy resin from isosorbide diglycidyl ether cured by bio-based curing agent.8
Concomitantly to bio-based polymers, the development of green additives for polymers has become a great challenge in the recent period. Among additives, flame retardants (FR) represent a significant group whose use is crucial in many sectors where fire safety is a major issue (building, transportation, electronics…). The most actual trends of green solutions for flame retardancy have been gathered in a recent book.9 One promising way consists in preparing FR from renewable resources.10 Once again, various fractions of the biomass have been considered in the literature to promote bio-based FR. (i) Carbohydrate fraction: Réti et al. used starch as charring agent in intumescent system for fire proofing of polylactic acid.11 Hu et al. modified chitosan with phosphorus pentoxide and urea to obtain bio-based FR for polyvinyl alcohol.12 (ii) Oil fraction: the team of Cádiz13,14 reported new routes to obtained phosphorus-containing triglycerides or fatty acids to decrease flammability of thermosets. (iii) Protein fraction: Alongi et al. investigated caseins and hydrophobins as green FR for cotton fabrics.15 (iv) Phenolic fraction: several studies mentioned the use of lignin to improve fire properties of thermoplastic polymers.16,17 In some cases, lignin was modified by phosphorus compound to emphasize its action as FR.18,19 Eugenol was also used to prepare benzoxazine monomers that were further polymerized leading to copolymers with performant fire behavior.20
Up to now, there have been only a limited number of papers reporting bio-based solutions for epoxy flame retardancy. Howell et al. used isosorbide and 10-undecenoic acid to synthesize a phosphorus ester flame retardant that was later incorporated in a DGEBA epoxy resin.21 In a recent paper,22 our team reported the synthesis of several bio-based phosphorus-containing additive flame retardants by grafting phosphate functions onto hydroxyl groups of phloroglucinol, a bio-based phenolic molecule found in the bark of fruit trees. This study highlighted the potential of these compounds to improve the flame retardancy of epoxy thermosets. However, it also showed that the difference of chemical structure between the additive FR and the flame-retardant matrix can reduce their compatibility, leading to phase segregation and opacity of the material. A plasticizing effect of the thermoset network is also often observed, leading to a decrease of its mechanical properties. Moreover, because of their additive character these low molecular weight FR are likely to move in the thermoset network, leading to their migration to the material surface and forward to a decrease of the fire performance.
Migration or leaching of flame retardants exposed to high temperature or humid atmosphere may be reduced by moving from the additive to the reactive approach.23,24 In this latter case, flame retardant species are covalently bonded to the polymer chain what inhibits their mobility within the polymer network and maintains their efficiency over the time. In a previous paper,25 we compared both reactive and additive approaches in the case of phosphorus and sulfur-containing FR of similar structure incorporated in a DGEBA epoxy resin. It was highlighted that the reactive approach avoids phase segregation. As regards fire performance, at equivalent phosphorus content, the reactive approach was shown to promote a higher char yield and a stronger reduction of the heat release.
No bio-based reactive phosphorous flame retardants for epoxy resin are commercially available so far. Recently, some studies related the synthesis of bio-based epoxy monomers and cross-linkers containing phosphorus moieties for epoxy thermosets. Lligadas et al. prepared a phosphorous epoxy monomer from a fatty acid derivative.26 10-Undecenoyl chloride was first reacted with DOPO before glycidylation to obtain a di-functional epoxy monomer. The final material was only partially bio-based since crosslinking was achieved with oil-based diamines. In another study, Ma et al. followed a strategy similar to that of Lligadas using itaconic acid as bio-based raw matter and DOPO as phosphorus source.27 A di-functional phosphorous epoxy was also obtained. Gu et al. synthesized a phosphorus-and-nitrogen containing diol from vanillin functionalized with 9,10-dihydro-9-oxy-10-phosphaphenanthrene-10-oxide (DOPO) that can be used as co-curing agent in epoxy resin.28 It should be noted that phosphorus moieties and aromaticity, which favor charring and help maintaining a good thermal stability respectively, are systematically brought by DOPO, i.e. a petro-based compound.
The aim of this study is to prepare the first bio-based flame retardant epoxy resin. For that purpose, phloroglucinol will be chosen as bio-based raw matter because this phenolic compound exhibits a symmetrical structure with three hydroxyl groups having the same reactivity. Phloroglucinol will be functionalized by glycidylation and/or phosphorylation in order to obtain building blocks that can be further used either as epoxy monomer or as phosphorus reactive flame retardant. Furthermore bio-based diamine hardeners will be used to achieve network crosslinking. Partially or fully bio-based polymers will be compared to a standard DGEBA/IPDA epoxy resin. In a first step, FR-free polymers will be characterized with the objective to identify the influence of the chemical structure of monomers and hardeners on the thermal and fire properties of the thermosets. In a second step, the FR epoxies will be compared in order to determine their overall thermal and fire behavior and identify the specific modes-of-action of phosphorus moieties in relation with the structure of the monomers.
Results and discussions
Synthesis and formulation of epoxy materials
One part of this study aims at assessing the influence of the bio-based monomers chemical structure on the fire behavior of epoxy thermoset. To do that, a bio-based epoxy monomer, i.e. the triglycidyl phloroglucinol and two bio-based curing agents (one aliphatic, i.e. the decane-1,10-diamine (DA10) and one aromatic, i.e. the difurfurylamine (DIFFA)) were formulated without any P-FR (white lines of Table 1). In the second part of the study, the thermosets prepared with the monomers described above are then flame-retarded with the reactive synthesized diglycidyl monophosphonated phloroglucinol noted P-FR P2EP1P (grey lines of the Table 1). The thermal behavior and flammability of the P-FR-free and P-FR-containing thermosets are then investigated.
Table 1 Compositions of the formulated epoxy thermosets with their respective theoretical crosslink density and theoretical EHC (effective heat of combustion) value
Epoxy monomer used (w%) |
Curing agent used (w%) |
Reactive P-FR (w%) |
Phosphorus content (w% P/thermoset) |
Average fepoxy |
Theoretical crosslink density (mol of crosslink per 200 g) |
Theoretical EHC values (kJ g−1) |
DGEBA (80.0) |
IPDA (20.0) |
None |
0 |
2 |
0.47 |
32.3 |
DGEBA (68.6) |
IPDA (18.9) |
P2EP1P (12.5) |
1 |
1.92 |
0.44 |
31.1 |
DGEBA (45.8) |
IPDA (16.6) |
P2EP1P (37.6) |
3 |
1.77 |
0.39 |
28.8 |
P3EP (72.8) |
IPDA (27.2) |
None |
0 |
2.60 |
1.14 |
27.6 |
P3EP (62.9) |
IPDA (24.5) |
P2EP1P (12.6) |
1 |
2.46 |
1.01 |
27.0 |
P3EP (42.0) |
IPDA (20.4) |
P2EP1P (37.6) |
3 |
2.16 |
0.77 |
26.0 |
P3EP (72.5) |
DA10 (27.5) |
None |
0 |
2.60 |
1.13 |
27.8 |
P3EP (61.9) |
DA10 (25.2) |
P2EP1P (12.9) |
1 |
2.46 |
1.01 |
27.3 |
P3EP (41.6) |
DA10 (20.7) |
P2EP1P (37.7) |
3 |
2.16 |
0.76 |
26.3 |
P3EP (65.9) |
DIFFA (34.1) |
None |
0 |
2.60 |
1.03 |
25.6 |
P3EP (56.3) |
DIFFA (31.2) |
P2EP1P (12.5) |
1 |
2.45 |
0.91 |
25.3 |
P3EP (37.1) |
DIFFA (25.8) |
P2EP1P (37.1) |
3 |
2.13 |
0.69 |
24.6 |
Concerning the reactive P-FR synthesis, our strategy (Scheme 1) consists in functionalizing a bio-based phenolic compound with epichlorohydrin to graft epoxy functions and bring reactivity to the future P-FR. In a second step, oxirane cycles of the glycidylated biophenol are partially functionalized by ring-opening with a phosphorus-containing precursor: triethyl phosphite. The reactive P-FR obtained has been then formulated in epoxy matrix according to the reactive approach to obtain a bio-based phosphorus-containing epoxy thermoset.
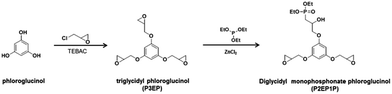 |
| Scheme 1 Synthesis of the reactive flame retardant: diglycidyl monophosphonated phloroglucinol (P2EP1P). | |
Thus, bio-based epoxy monomers, curing agents and reactive P-FR are finally used in combination, leading to the first fully bio-based epoxy thermosets flame-retarded by reactive approach.
Synthesis of triglycidyl phloroglucinol (P3EP). To bring reactivity to phloroglucinol, we used the method developed by Nouailhas et al.33 which consists in solubilizing the biophenol in a large excess of epichlorohydrin by preparing its phenolate ammonium salt in presence of an ammonium phase transfer catalyst. The phenolate is then able to react with epichlorohydrin, forming chlorinated intermediates. The crude mixture is treated with a sodium hydroxide solution to form the oxirane rings from the chlorinated intermediates.The 1H-NMR spectrum of the final product (ESI 1†) allows determining its epoxy functionality, by comparing the integration of the signal of the aromatic protons at 6.19 ppm to the integration of the signal of the proton carried by the tertiary carbon of the glycidyl group at 3.30 ppm. The final epoxy functionality of P3EP was found to be 2.6 epoxy functions per aromatic ring. This epoxy functionality was also assessed from DSC analyses by reacting P3EP with IPDA (knowing its amine functionality), considering different P3EP functionalities (i.e. from 2.4 to 2.7).
We assume that the product synthesized is a mixture between a phloroglucinol diepoxy and triepoxy. The P3EP is totally functionalized by epichlorohydrin, but some side reactions, as the partial oligomerization or the presence of residual opened epoxy functions, which are not detailed in this paper reduce the final epoxy functionality of the P3EP compound.
Synthesis of diglycidyl mono-phosphonated phloroglucinol (P2EP1P). Different synthesis pathways allow the grafting of a phosphonate group by oxirane ring opening. In 1979, Baboulene et al.34 were the first ones to use the reactivity of phosphite with oxirane cycle in basic medium to synthesize β-hydroxy phosphonate compounds. Other teams used lithium diethylphosphite,35,36 or trialkyl phosphite with triflate as catalysts.37 However these methods suffer from some drawbacks, such as difficult workup, or the use of strong bases, such as butyl lithium. In 2007, Sardarian et al.38 developed a simple and attractive one-pot reaction to prepare β-hydroxy phosphonate in relatively mild conditions using a trialkyl phosphite, catalyzed by zinc chloride. This method has been used by Catel et al.39 to synthesize different methacrylate monomers bearing phosphonic groups at room temperature. It is assumed that the presence of water in the medium allows the creation of a hydrogenophosphonate intermediate, which is able to attack the terminal carbon of the oxirane ring. We used this synthesis pathway to prepare a bio-based reactive P-FR. Thus this reaction was performed onto P3EP, aiming at functionalizing only one epoxy group.The 1H-NMR analysis of the P2EP1P compound (Fig. 1) allows determining its epoxy functionality by integrating the H3 signal at 3.30 ppm, equal to 1.4 epoxy function/aromatic ring. The reaction is also followed by 31P-NMR: the complete conversion of the triethyl phosphite is observed by the modification of the δ 31P from 138 ppm to 28.9 ppm. The final δ 31P corresponds to the δ 31P of the β-hydroxy phosphonate, as reported in the literature.5 These NMR analyses confirm the partial conversion of the epoxy functions into β-hydroxy phosphonate. The phosphorus content of the P2EP1P is found to be 8.0 w% P.
 |
| Fig. 1 1H-NMR (A) and 31P-NMR (B) spectra of the diglycidyl monophosphonated phloroglucinol (P2EP1P). | |
Synthesis of difurfurylamine (DIFFA). In search for renewable alternatives for oil-based compounds, bio-based diamine became a topic of great interest. Difurfuryl amines have attracted interest. These compounds are derived from furfural, which is potentially available in large quantities from agricultural waste materials and byproducts of solvent wood-pulping operations. Difurfuryl amines have already been used as curing agents for epoxy thermosets and the authors40 reported a very effective epoxy curing agent with the ability to cure DGEBA at rates similar to that of standard aliphatic curing agents. Holfinger et al.41 reported a single-step synthesis of the difurfuryl amine from furfuryl amine. This process is then used to synthesize a bio-based curing agent.
Incorporation in epoxy matrix. Fig. 2 represents the chemical structures of the epoxy monomers and diamine curing agents used for the thermosets preparation. It is important to note that only DGEBA and IPDA are oil-based compounds, unlike the bio-based compounds P3EP, P2EP1P, DA10 and DIFFA.
 |
| Fig. 2 Epoxy monomers/reactive P-FR and curing agents used for thermosets formulations. | |
To assess its efficiency, the synthesized reactive P-FR P2EP1P was firstly formulated in a conventional epoxy matrix, i.e. DGEBA, cured by isophorone diamine (IPDA). DGEBA exhibits an aromatic structure leading to rigid network with excellent mechanical properties and good chemical inertness. That is why DGEBA is widely used, especially in the production of coatings or high performance composites.42,43 IPDA is a cycloaliphatic cross-linking agent and provides a good balance between reactivity and network rigidity. In order to balance the loss of epoxy functionality due to the incorporation of the reactive flame retardant (fepoxy < 2), triglycidyl phloroglucinol (P3EP) used as intermediate in the synthesis of the reactive P-FR P2EP1P, was also used as epoxy monomer (fepoxy > 2) in combination with IPDA, increasing the bio-based part of the thermoset. Two bio-based diamines of different structures (DA10 and DIFFA) were also used in combination with P3EP to perform fully bio-based thermosets flame retarded by a reactive approach. To obtain high cross-linking rate, the epoxy/amine ratio was kept constant and equal to 2 in all the formulations. Different thermosets were prepared with various P-FR contents and thus phosphorus contents. The curing conditions were determined in a previous study.25
A possible incompatibility between the matrix and the FR could lead to partial phase segregation.22 During early stages of curing, viscosity of the system decreases and may allow sedimentation or creaming of segregated phases. The homogeneity of the cured thermosets was studied by scanning electron microscopy with Energy Dispersive X-ray technology (EDX). Results exhibited the good compatibility of the reactive P-FR in all the formulations, avoiding phase segregation and leading to homogeneous thermosets.
Characterization of the thermosets properties
In each following part, the P-FR-free thermosets are firstly discussed, and then the effect of the reactive P-FR P2EP1P on these thermosets behavior is described.
Differential scanning calorimetry (DSC) analyses of crosslinked thermosets. Physical properties of thermosets can be assessed by measuring their glass transition temperature (Tg) from DSC (Table 2 and Fig. 3). Usually, high Tg are targeted for the epoxy thermosets to reach both high thermal and mechanical properties. DSC analyses were performed on cross-linked thermosets.
Table 2 Tg values obtained by DSC at 20 °C min−1; T10 and w% char obtained by TGA under nitrogen flow at 10 °C min−1; pHRR (peak of heat released rate), THR and EHC obtained by PCFC analyses at 1 °C s−1
Thermosets |
DSC/TGA |
PCFC |
Tg (°C) |
T10 (°C) |
w% char at 700 °C |
pHRR (W g−1) |
THR (kJ g−1) |
EHCexp (kJ g−1) |
EHCtheo (kJ g−1) |
DGEBA–IPDA |
157 |
369 |
8.6 |
664 |
34.2 |
37.4 |
32.3 |
1% P(DGEBA–IPDA–P2EP1P) |
146 |
289 |
19.7 |
445 |
31.3 |
39 |
31.1 |
3% P(DGEBA–IPDA–P2EP1P) |
139 |
256 |
31.5 |
332 |
25.4 |
37 |
28.8 |
P3EP–IDPA |
177 |
306 |
24.1 |
395 |
18.3 |
24.1 |
27.6 |
1% P(P3EP–IPDA–P2EP1P) |
168 |
292 |
25.3 |
263 |
19.3 |
25.8 |
27.0 |
3% P(P3EP–IPDA–P2EP1P) |
155 |
276 |
30.3 |
166 |
17.3 |
24.8 |
26.0 |
P3EP–DA10 |
137 |
300 |
24.5 |
185 |
19.4 |
25.8 |
27.8 |
1% P(P3EP–DA10–P2EP1P) |
114 |
299 |
25.7 |
154 |
17.8 |
24.0 |
27.3 |
3% P(P3EP–DA10–P2EP1P) |
87 |
281 |
27.6 |
145 |
18.2 |
25.1 |
26.3 |
P3EP–DIFFA |
134 |
290 |
38.1 |
119 |
11.4 |
18.4 |
25.6 |
1% P(P3EP–DIFFA–P2EP1P) |
128 |
288 |
42.2 |
85 |
9.3 |
15.6 |
25.3 |
3% P(P3EP–DIFFA–P2EP1P) |
124 |
267 |
43.5 |
78 |
8.7 |
15.4 |
24.6 |
 |
| Fig. 3 Glass transition temperatures versus theoretical crosslink density of all the prepared thermosets determined by DSC at 20 °C min−1. | |
Study of the P-FR free thermosets. Considering first the P-FR-free thermosets, P3EP–IPDA thermoset presents a Tg value of 177 °C, compared to 157 °C for the DGEBA–IPDA thermoset. Since these two materials were cured by the same curing agent, the difference in Tg values is due to the structure of the epoxy monomer. More precisely, this result can be related to its epoxy functionality. P3EP has an epoxy functionality of 2.6 compared to 2.0 for the DGEBA, which leads to a higher crosslink density of the P3EP–IPDA thermoset. Indeed, the theoretical crosslink density of the DGEBA–IPDA and the P3EP–IPDA are 0.47 and 1.14 mol of crosslink per 200 g of thermoset, respectively. When P3EP reacts with DA10, the Tg value was lowered to reach 137 °C. In this case the difference observed is due to the structure of the curing agent, i.e. DA10 shows a linear aliphatic structure compared to a cycloaliphatic structure of IPDA. The cyclic configuration considerably reduces the mobility of the curing agent segment and increases the rigidity of the network. This effect was also expected between P3EP–DA10 and P3EP–DIFFA thermosets because DIFFA shows an aromatic structure. However, in this case the two materials present equivalent Tg values. It means that the two curing agent structures provide the same rigidity to the network. Thus, the aromaticity of the DIFFA is balanced by the lower crosslink density of the P3EP–DIFFA thermoset (1.03 mol of crosslink per 200 g of thermoset) compared to the P3EP–DA10 (1.13 mol of crosslink per 200 g of thermoset). Moreover, the aliphatic links between the furanic cycles and the amine functions of the DIFFA allow free rotations of the system and may provide some mobility to balance the rigidity brought by the aromaticity of the furanic cycles.It is likely to note that P3EP–DA10 and P3EP–DIFFA thermosets, which are fully bio-based exhibit high performance epoxy thermoset Tg values around 135 °C.
Study of the P2EP1P-containing thermosets. Fig. 3 plots the Tg values of the prepared thermosets versus theoretical crosslink densities. The DSC curves are given in ESI 2.† The Tg values of the phosphorus-containing thermosets are lower than the Tg values of the corresponding FR-free matrices. This effect increases with the FR content, i.e. with the phosphorus content. This result can be related to the low epoxy functionality of the reactive P-FR P2EP1P, equal to 1.4. This low P-FR epoxy functionality induces a decrease of the average epoxy functionality of the system (Table 1). Indeed, the theoretical crosslink densities of the 3 w% P-containing thermosets are between 10 and 30% lower than that of the corresponding P-FR-free matrices, leading to a partial termination of the growing network and finally to a lower Tg value. We can note that the crosslink density is reduced by the incorporation of P2EP1P and also that in the thermosets series, the higher the crosslink density, the higher the Tg value. It may be assumed that the phosphonate segment may also plasticize the network, participating to the Tg values reduction.The incorporation of the reactive P-FR P2EP1P leads to lower Tg values, which is not suitable for the thermal and mechanical properties of the epoxy thermosets. To preserve a high Tg value of fire-retardant materials, it is possible to introduce a monomer with an epoxy functionality higher than 2 (for instance P3EP: fepoxy = 2.6) to increase the average epoxy functionality of the system. For instance, the phosphorus-containing material 3% P(P3EP–IPDA–P2EP1P) presents a Tg value equal to 155 °C, which is equivalent to the Tg value of the P-FR-free DGEBA–IPDA thermoset (157 °C) (Fig. 3).
Thermal behavior and flammability of the epoxy thermosets. The flammability of the different thermosets was assessed according to parameters such as high temperature char amounts, the peak of heat release rates (pHRR) or total heat released (THR) during decomposition. Thermosets were thus characterized by thermogravimetric analyses (TGA) and pyrolysis combustion flow calorimetry analyses (PCFC) to highlight the effects of the different monomers of and of the reactive P-FR on the thermal properties and flammability.
Thermogravimetric analyses (TGA) of flame retardant thermosets. TGA analyses were firstly performed to assess the influence of the monomer structure and then of the reactive FRs on thermal stability and charring of the thermosets. T10 represents the temperature at which the material loses 10% of its initial mass.
Study of the P-FR free thermosets. Concerning the P-FR-free matrices (Fig. 4), significant differences were observed. P3EP based thermosets all exhibit lower thermal stabilities than the DGEBA–IPDA thermoset. Indeed, the T10 of the P3EP-containing thermosets ranged between 290 and 300 °C, compared to 368 °C for the DGEBA-containing thermoset. The P3EP epoxy monomer reduces the thermal stability of the thermoset compared to DGEBA. It is assumed that different parameters could be responsible for this reduced thermal stability; such as the higher aromaticity of the DGEBA compared to the P3EP which could stabilize more the system and the nature and the number of groups linked to the aromatic ring. Indeed, it has already been observed that the environment of the aromatic ring influences directly its thermal stability, Vothi et al.44 showed this phenomenon with a phloroglucinol triphosphate which is thermally less stable than a resorcinol diphosphate. The thermal stability of an epoxy thermoset has also already been described as a function of the hydroxyl group concentration.45,46 Indeed, epoxy thermoset decomposition starts by the dehydration of the secondary alcohol. The P3EP-containing thermosets possess a higher hydroxyl group concentration than the DGEBA-containing one, thus, their thermal stability is lower than the DGEBA-containing one. In another way, the structure of the curing agent does not seem influencing the thermal stability. For instance, the three P3EP-containing thermosets cured with different diamines, present similar thermal stabilities around 295 °C.
 |
| Fig. 4 Thermograms of the FR-free thermosets at 10 °C min−1 under nitrogen flow. | |
It was observed that the char yield depends on the structure of the epoxy monomer and the curing agent. Thermosets P3EP–DA10, P3EP–IPDA and P3EP–DIFFA exhibit higher char content than that of the DGEBA–IPDA thermoset. Indeed, the P3EP–IPDA produces 24.1 w% of char compared to 8.6 w% for the DGEBA–IPDA thermoset. The P3EP epoxy monomer favors the charring of the material during its thermal decomposition. It may be due to the higher linking rate of the aromatic rings, which favors the charring. Furthermore, by using DIFFA instead of IPDA, the char content reaches 38 w%. The aliphatic curing agents (DA10 and IPDA) containing thermosets present lower char contents than the aromatic-containing one (DIFFA). Thus, the conjugated five-membered heterocycle of the curing agent promotes the charring during the thermal degradation. Indeed, this conjugated structure favors the Diels Alder reactions during the charring. However, the P3EP–IPDA and P3EP–DA10 present similar char content around 24–25 w%. It means that the cyclic structure of the IPDA does not promote more the charring than the aliphatic one of the DA10. Concerning the P3EP–DA10 thermoset, a two-step degradation is observed; the first one around 300 °C is common to the other P3EP-containing thermosets and is assigned to the degradation of the P3EP segment but the second one which occurs around 400 °C is assigned to the decomposition of the aliphatic segment of the DA10.
It is worth noting that P3EP–DIFFA, showing both high thermal stability and high char yield is a fully bio-based thermoset without any P-FR. It proves the intrinsic potential of the used bio-based monomers (P3EP and DIFFA) to favor charring of an epoxy thermoset during thermal degradation.
Study of the P2EP1P-containing thermosets. Table 2 presents the T10 values and the char contents of all the prepared thermosets. Fig. 5 shows the thermograms of the DGEBA–IPDA thermosets series. It is noted that P2EP1P containing-thermosets showed lower thermal stability than that of corresponding P-FR-free matrices (Fig. 5). Indeed, T10 is reduced from 369 °C for the DGEBA–IPDA thermoset to 289 °C for the 1% P(DGEBA–IPDA–P2EP1P) and to 256 °C for the 3% P(DGEBA–IPDA–P2EP1P) thermoset. These lower degradation temperatures may be assigned to the reduced crosslink density but mostly to the early stage of decomposition for phosphorus-containing groups. Price et al.47 described the phosphonic-ester decomposition ranging between 300 and 340 °C by alkyl chain loss. It may be assumed that phosphonic-ester decomposition generates radical species which initiate the matrix decomposition. Indeed the loss of thermal stability was systematically observed by using phosphorus-containing flame retardants.22,25 This loss of thermal stability appears to be a function of the phosphorus content. Moreover, the higher the intrinsic thermal stability of the matrix, the higher the decrease of the T10 caused by the incorporation of the reactive P-FR. It shows that the thermal stability of a phosphorus-containing thermoset is mainly guided by the early degradation of the phosphonate moieties around 250–280 °C.
 |
| Fig. 5 Thermograms of the DGEBA–IPDA series thermosets at 10 °C min−1 under nitrogen flow. | |
Concerning the char content, the reactive P-FR improves the charring of the matrix during thermal decomposition. Table 2 gives the char content of all the thermosets. The charring promotion is more obvious in the DGEBA–IPDA matrix. We observe that the char content increases with the phosphorus content, from 8.6 w% for the P-FR-free matrix to 19.7 w% with 1 w% P and to 31.5 w% with 3 w% P. Fig. 6A–D represent the TGA curves of the four matrices compared to their respective 3 w% P-containing counterpart. The same trend is observed for the three other matrices. However, we can note that the lower the intrinsic char content of the matrix, the higher the increase of char content brought by phosphorus content. For instance, in the DGEBA–IPDA matrix, 3 w% P allows to increase the char content of 22.9 w%, while in the P3EP–DIFFA matrix it only increases the char content of 5.4 w%. These results indicate that P2EP1P might be a good flame retardant as it promotes a significant charring of the epoxy thermosets.
 |
| Fig. 6 Thermograms of the P-FR-free matrix and the 3 w% P-containing thermosets in DGEBA–IPDA (A); P3EP–IPDA (B); P3EP–DA10 (C) and P3EP–DIFFA (D) under nitrogen flow at 10 °C min−1. | |
Pyrolysis combustion flow calorimetry (PCFC) of the prepared thermosets.
Study of the P-FR free thermosets. To assess the flame retardant properties of all the thermosets studied, thermosets were characterized by pyrolysis/combustion flow calorimetry. Concerning the FR-free matrices (Fig. 7), significant differences are observed, showing the influence of the chemical structure on the flammability of the thermosets. The loss of thermal stability observed by TGA on P3EP-containing thermosets is reflected by the emission of fuel gases at a lower temperature compared to the DGEBA-containing thermoset. The DGEBA–IPDA has high pHRR and THR, respectively 664 W g−1 and 34.2 kJ g−1; these parameters were significantly reduced by replacing the DGEBA by the P3EP. Indeed P3EP–IPDA has lower pHRR and THR, respectively 395 W g−1 and 18.3 kJ g−1. The lower THR of P3EP-containing epoxy is partly assigned to its higher char yield but also partly related to its lower EHC (effective heat of combustion) as revealed in Table 2 and Fig. 9. The lower EHC of P3EP segment compared to DGEBA segment is consistent with expected values calculated from thermochemistry according to the elemental composition of each monomer.
 |
| Fig. 7 PCFC curves of the FR-free thermosets. | |
The three P3EP-containing thermosets present the same first emission of fuels around 280 °C. However, a second emission occurs around 440 °C for the DA10-containing one. Remind that the same phenomenon was observed by TGA.
Table 2 also shows the EHC values, highlighting a significant decrease of the calorific power of the decomposition gas from the DGEBA-containing to the fully bio-based P3EP–DIFFA thermosets. By comparing these results with that of the TGA, we observe that the higher the char content obtained by TGA, the lower the THR by PCFC (Fig. 6B). Indeed, the amount of carbon stored in the char does not feed the combustion. The lower theoretical EHC of the bio-based thermosets (Table 3) also explain the lower THR. Thus, the higher char content and the lower calorific power of the fuels released allow the bio-based thermosets to present lower THR.
Table 3 Theoretical EHC values of the thermoset components from elemental composition according to the Lyons' method
Thermoset components |
Theoretical EHC value (kJ g−1) |
DGEBA |
30.8 |
P3EP |
23.5 |
P2EP1P |
22.3 |
IPDA |
38.2 |
DA10 |
39.0 |
DIFFA |
29.6 |
While P3EP–DIFFA exhibits higher char content and lower EHC, its THR is the lowest among the four thermosets studied. On the contrary, DGEBA–IPDA exhibits lower char content and higher EHC and then this thermoset releases the highest amount of energy. P3EP–DA10 and P3EP–IPDA exhibit similar char content and EHC and then similar THR. This result may be explained by the equal amount of aliphatic carbon brought by the DA10 or the IPDA.
It is worth noting that the fully bio-based thermosets prepared P3EP–DA10 and P3EP–DIFFA possess intrinsically both lower pHRR and THR than the oil-based one: they release less energy at lower release rate.
Study of the P2EP1P-containing thermosets. Concerning the P-FR-containing thermosets, the effects of the reactive flame retardant are more marked into the intrinsically more flammable matrices: DGEBA–IPDA and P3EP–IPDA. The phosphorus-containing fully bio-based thermosets present flammability similar to the P-free counterparts which already have an excellent thermal behavior (Fig. 8A–D).
 |
| Fig. 8 PCFC curves of the DGEBA–IPDA series (A), P3EP–IPDA series (B), P3EP–DA10 series (C) and P3EP–DIFFA series (D) at 1 °C s−1. | |
The loss of thermal stability observed by TGA leads to fuel release at lower temperature. For instance, the fuels release starts around 320 °C for the DGEBA–IPDA thermoset, 250 °C for the 1% P(DGEBA–IPDA–P2EP1P) thermoset and below 250 °C for the 3% P(DGEBA–IPDA–P2EP1P) thermoset. The loss of thermal stability increases with the increasing phosphorus content. The same trend is observed in the other matrices. It may be assumed that the early stage of decomposition for phosphorus-containing groups leads to fuel emission at lower temperature.
The pHRR and THR are also reduced by the reactive P-FR. In the DGEBA–IPDA matrix: pHRR is reduced from 664 W g−1 for the phosphorus-free matrix to 332 W g−1 for the 3% P(DGEBA–IPDA–P2EP1P) thermoset. Similarly, THR is reduced from 35.2 to 25.4 kJ g−1. The pHRR is also significantly reduced in the P3EP–IPDA matrix. In the P3EP–DA10 and P3EP–DIFFA matrices, the pHRR and THR of the P-FR-containing thermosets are only slightly lower than the corresponding P-FR-free matrices.
The incorporation of phosphorus does not modify significantly the effective heat of combustion, i.e. the nature of the pyrolysis gases. Phosphorus promotes charring but this effect is more significant for highly flammable thermosets (i.e. DGEBA–IPDA). As a consequence, THR decreases when incorporating phosphorus and this decrease is only assigned to char promotion. THR is reduced from 34.2 kJ g−1 for the DGEBA–IPDA to 25.4 kJ g−1 for the 3% P(DGEBA–IPDA–P2EP1P) thermoset. The phosphorus-containing fully bio-based thermosets present EHC similar to the P-FR-free matrices which already have an excellent thermal behavior.
Fig. 9 plots the THR and char content of all thermosets with and without P-FR and provides an overview of all results. For a thermoset series, the slope of the curve “THR versus char content” gives the mean EHC of the series. As said above, the lower THR values of the bio-based thermosets are due to two phenomena: the lower EHC value of the thermoset, from elemental composition and the higher charring of these bio-based thermosets. This representation (Fig. 9) allows quantifying each phenomenon independently. For instance: the THR gap between 3% P(DGEBA–IPDA–P2EP1P) and 3% P(P3EP–DIFFA–P2EP1P), (32.4–11.4) = 16.7 kJ g−1 can be divided in two part as shown in Fig. 9. The part attributed to the lower EHC of the bio-based thermoset is measured as the difference of THR between the two thermosets, considering similar char yield (12.7 kJ g−1). The part attributed to the higher charring corresponds to the difference 16.7 − 12.7 = 4 kJ g−1. It is important to note that the lower THR values of the bio-based thermosets are mainly due to their lower EHC. For instance, the difference between the THR of the 3% P(DGEBA–IPDA–P2EP1P) and the 3% P(P3EP–DIFFA–P2EP1P) is due at 76% to the lower EHC and at 24% to the charring.
 |
| Fig. 9 THR values versus the char content. | |
A last remark concerns the DIFFA containing-thermoset series. This series exhibits experimental EHC values (in the range of 15–18 kJ g−1) significantly lower than the theoretical ones which are in the range of 25–27 kJ g−1. This result means that the char produced with this thermoset series is highly carbon concentrated and that a significant amount of energy is still stored in the char.
Conclusions
In this study, two bio-based building blocks (an epoxy monomer and a phosphorus reactive FR) were successfully synthesized using phloroglucinol as raw matter. These molecules were then reacted with oil-based or bio-based diamines to prepare FR-free and FR, partly or fully bio-based epoxy resins. These resins have been compared to a conventional DGEBA–IPDA control.
As regards FR-free epoxy resins, it was highlighted that the chemical structure of the reactants plays a leading role that affects directly the thermoset properties. The functionality of the epoxy monomer as well as its aromaticity directly influences the glass transition temperature and the thermal stability of the materials. Moreover the presence of aromatic structure in the epoxy monomer and/or in the curing agent seems to favor the charring process during thermal decomposition. It was also shown that the chemical composition is an important parameter that governs the flammability of the final materials by modifying their effective heat of combustion (EHC). Thus the fully bio-based P3EP–DIFFA resin exhibits a good thermal stability and produces a high char content (38 w%) as well as a low EHC (18.4 kJ g−1) without any phosphorus addition. It presents intrinsically a better fire behavior than the oil-based DGEBA–IPDA, evidencing the potential of these aromatic monomers coming from bio-based raw materials to improve the fire behavior of epoxy resins.
Concerning FR resins, the incorporation of the bio-based phosphorus reactive FR (P2EP1P) into the polymer network was shown to induce a decrease of the glass transition temperature of epoxies. This was assigned on one hand to a plasticizing effect of the phosphonate chain and on the other hand to a decrease of the thermoset crosslink density because of the low epoxy functionality of P2EP1P. The loss of crosslink density can be balanced by using the phloroglucinol epoxy monomer whose functionality is higher than 2. The presence of the phosphorus reactive FR was shown to decrease the thermal stability of the epoxy network but it results in an increase of the char yield at elevated temperature. It was evidenced that the ability of P2EP1P to promote charring was much more efficient in a matrix which is intrinsically highly flammable. On the contrary, its action was limited in the high charring P3EP–DIFFA epoxy matrix.
Hence the fire behavior of epoxy resins can be improved both by (i) a judicious choice of monomers having low combustibility and high charring propensity and (ii) by the incorporation of phosphorus species into the polymer network. The main drawback of the synthesized reactive P-FR (P2EP1P) is linked to its low epoxy functionality. Our forthcoming study will try to challenge this issue by synthesizing a reactive P-FR with epoxy functionality higher than two. The combination of the two above-described reactive approaches leads to the first fully bio-based flame retardant epoxy thermosets, such as the P3EP–DIFFA–P2EP1P series.
Experimental
Reagents
Phloroglucinol, epichlorohydrin, benzyltriethylammonium chloride (TEBAC), zinc chloride, diethylallyl phosphonate, thioacetic acid, furfurylamine and triethylamine were purchased from Sigma-Aldrich. Triethyl phosphite, potassium cyanide and benzophenone were purchased from Alfa Aesar. For epoxy resins components, diglycidylether of bisphenol A (DGEBA) resin and isophorone diamine (IPDA) as curing agent were purchased from Sigma-Aldrich. Decane-1,10-diamine (DA10) was provided from Arkema. All reactants were used without any further purification.
Characterizations
Chemical structures of the prepared compounds were determined by 31P-NMR and 1H-NMR spectroscopy in a Bruker Avance 400 MHz spectrometer at room temperature in (CD3)2CO solutions. External references were trimethylsilane (TMS) for 1H-NMR and phosphoric acid (H3PO4) for 31P-NMR. Shifts are given in ppm. Samples were observed using a FEI Quanta 200 scanning electron microscope with the Energy Dispersive X-ray spectroscopy (EDX) using Oxford INCA Energy 300 system and a detector of 133 eV (at Mn). Samples were characterized after metallization in high vacuum sputtering metallizer Bal-Tec CED 030 Blatzer.
Differential Scanning Calorimetry (DSC) analyses were carried out using a Netzsch DSC200F3 calorimeter. Constant calibration was performed using indium, n-octadecane and n-octane standards. Nitrogen was used as the purge gas. The thermal properties were analyzed at 15 °C min−1 between 20 and 200 °C to observe the glass transition temperature determined as the inflexion value in the heat capacity jump. Thermogravimetric analyses were performed using a Perkin Elmer Pyris 1 TGA at a heating rate of 10 °C min−1 under nitrogen atmosphere. Flammability was assessed using a pyrolysis-combustion flow calorimeter from Fire Testing Technology (FTT UK). About 3 mg was placed in the pyrolyzer, undergoing an increase of temperature from 20 °C to 750 °C at 1 °C s−1 under a nitrogen flow. Decomposition gases were sent to a combustor heated at 900 °C under air flow (N2/O2 = 80/20). At this temperature and with 20% of oxygen, combustion was considered to be complete. Heat release rate was determined by oxygen depletion according to Huggett principle29 (1 kg of consumed oxygen corresponds to 13.1 MJ of heat released). PCFC analyses correspond to anaerobic thermoset pyrolysis followed by the high temperature oxidation of decomposition products (complete combustion).30 pHRR is the maximal value of the heat release rate. The total heat released (THR) was obtained by integration of PCFC curves. The effective heat of combustion (EHC) represents the released heat by loss mass. It is calculated as the ratio between THR and mass loss measured in TGA according to the eqn (1):
|
THR = EHC × ((1 − w% char))/100
| (1) |
Table 2 summarizes all these parameters.
Synthesis and formulation
Synthesis of triglycidyl phloroglucinol (P3EP). Phloroglucinol (3 g, 23.8 mmol) is solubilized in epichlorohydrin (44 g, 0.47 mol) with benzyltriethylammonium chloride (0.27 g, 1.19 mmol) in a round bottom flask equipped with a magnetic stirrer and a condenser. The system is heated at 80 °C during 5 h under vigorous stirring. After reaction the excess of epichlorohydrin is distilled at 50 °C under high vacuum. The mixture is then solubilized in 80 ml of ethyl acetate. 100 ml of sodium hydroxide (10 w%) is then added and the biphasic system is stirred at room temperature during 30 minutes. After demixing, the organic phase is washed with brine and then with water, dried on sodium sulfate, filtered and then concentrated under vacuum to obtain a yellow resin. Yield: 68%.
1H-NMR (400 MHz, DMSO-d6, ppm) δ = 6.19 (3H, H1); 3.77 and 4.28 (6H, H2); 3.30 (3H, H3); 2.69 and 2.84 (6H, H4).
Synthesis of diglycidyl monophosphonated phloroglucinol (P2EP1P). A solution of triglycidyl phloroglucinol (10 g, 34 mmol) in 100 ml of THF is introduced in a 250 ml two-necked round bottom flask equipped with a condenser and a magnetic stirrer. Zinc chloride (1.78 g, 13.1 mmol) is added to the solution. Then, triethylphosphite (2.17 g, 13.1 mmol) is slowly added to the mixture with a syringe under vigorous stirring. The mixture is stirred at room temperature during 10 h. After reaction, 250 ml of ethyl acetate is added and the solution is washed with a saturated solution of ammonium chloride and then with deionized water. The organic phase is dried with sodium sulfate and then distilled under vacuum. Yield: 73%.
31P-NMR (400 MHz, DMSO-d6, ppm): 28.9.
1H-NMR (400 MHz, DMSO-d6, ppm): δ = 2.68 and 2.83 (4H, H4); 3.30 (2H, H3); 3.76 and 4.35 (4H, H2); 6.20 (3H, H1); 4.11 and 4.20 (2H, H5); 3.80 (1H, H6), 1.55 and 1.80 (2H, H7); 4.12 (4H, H8); 1.30 (6H, H9).
Synthesis of difurfurylamine (DIFFA). Furfurylamine (2.1 eq.) is introduced in a two-necked round-bottom flask equipped with a reflux condenser and cooled down to 0 °C with an ice bath. A 18 w% aqueous solution of HCl (5 eq.) is then added dropwise to furfurylamine. Once this addition is completed, the temperature is risen to 25 °C and the mixture is stirred for 15 min. Acetone (1.0 eq.) is then added to the mixture. The temperature is risen to 40 °C. In such a case, an additional aliquot of acetone (0.4 eq.) is added to the mixture. The reaction is completed after 7 days and 2 additional aliquots of acetone were necessary to attain the complete conversion of furfurylamine. The mixture is then cooled down to 25 °C and 150 ml of deionized water are added. The pH is adjusted to 10 with a 15 w% aqueous solution of NaOH. The mixture is extracted thrice with ethyl acetate. The organic fractions are collected, washed with brine, dried on anhydrous MgSO4 and ethyl acetate is removed under vacuum to obtain a yellow to brown oil. Yield = 90%.
1H-NMR (400 MHz, DMSO-d6, ppm): δ = (1.76, 4H, H1); (3.59, 4H, H2); (6.06, 2H, H3); (5.97, 2H, H4); (1.54, 6H, H5).
Thermosets preparation. Different thermosets were prepared with the different bio-based epoxy monomers/curing agents and with/without the synthesized reactive P-FR. A series of P-FR-free thermosets was prepared by using only the P-free monomers: DGEBA, P3EP, IPDA, DA10, and DIFFA. Then, each thermoset prepared was flame-retarded by the reactive P-FR synthesized. The P-FR was solubilized in epoxy monomer under stirring at 80 °C for 10 minutes. The mixture was cooled at 50 °C to avoid any crosslinking upon mixing with the hardener. A stoichiometric epoxy/amine ratio (2/1) was used. The system was stirred manually for 5 minutes. Lastly the mixture was crosslinked in a circular rubber mold according to the following temperature program: 4 h at 80 °C and 10 h at 150 °C. Thermosets were named according to their phosphorus content followed by the used monomers: “x% P(epoxy monomer–curing agent–FR)”. Table 2 summarizes the weight composition of the prepared thermosets. P3EP–DIFFA and P3EP–DA10 thermoset series are fully bio-based materials. The theoretical crosslink densities are calculated by counting the crosslink, i.e. the nitrogen atoms from the curing agent and the aromatic ring of the P3EP. Thermosets theoretical EHC values are calculated from the theoretical EHC values of each component of the system given in Table 3. Theoretical EHC of each component is calculated according to the method described by Lyons' et al.31 in which it is assumed that the pyrolysis gases and initial thermoset compositions are similar and the oxidation of the nitrogen atoms is not considered. Indeed, it seems that the nitrogen reacts with oxygen only at high temperature around 1600 °C.32 Thus, a PCFC experiment does not allow oxidizing the nitrogen atoms of the thermoset.
References
- R. Auvergne, S. Caillol, G. David, B. Boutevin and J. P. Pascault, Biobased thermosetting epoxy: Present and future, Chem. Rev., 2014, 114, 1082–1115 CrossRef CAS PubMed.
- J. Hong, D. Radojčić, M. Ionescu, Z. S. Petrović and E. Eastwood, Advanced materials from corn: isosorbide-based epoxy resins, Polym. Chem., 2014, 5, 5360–5368 RSC.
- C. S. Kovash, E. Pavlacky, S. Selvakumar, M. P. Sibi and D. C. Webster, Thermoset coatings from epoxidized sucrose soyate and blocked, bio-based dicarboxylic acids, ChemSusChem, 2014, 7, 2289–2294 CrossRef CAS PubMed.
- N. Supanchaiyamat, A. J. Hunt, P. S. Shuttleworth, C. Ding, J. Clark and A. Matharu, Bio-based thermoset composites from epoxidised linseed oil and expanded starch, RSC Adv., 2014, 4, 23304–23313 RSC.
- G. Wu, D. Liu, G. F. Liu, J. Chen, S. P. Huo and Z. W. Kong, Thermoset nanocomposites from waterborne bio-based epoxy resin and cellulose nanowhiskers, Carbohydr. Polym., 2015, 127, 229–235 CrossRef CAS.
- S. Benyahya, C. Aouf, S. Caillol, B. Boutevin, J. P. Pascault and H. Fulcrand, Functionalized green tea tannins as phenolic prepolymers for bio-based epoxy resins, Ind. Crops Prod., 2014, 53, 296–307 CrossRef CAS PubMed.
- M. Fache, R. Auvergne, B. Boutevin and S. Caillol, New vanillin-derived diepoxy monomers for the synthesis of biobased thermosets, Eur. Polym. J., 2015, 67, 527–538 CrossRef CAS PubMed.
- R. Chang, J. Qin and J. Gao, Fully biobased epoxy from isosorbide diglycidyl ether cured by biobased curing agents with enhanced properties, J. Polym. Res., 2014, 21, 7–12 Search PubMed.
- P. Kiliaris and C. D. Papaspyrides, Polymers on Fire, Polymer Green Flame Retardants, Elsevier B.V., 2014, pp. 1–43 Search PubMed.
- A. M. Sakharov, P. A. Sakharov, S. M. Lomakin and G. E. Zaikov, Novel Class of Eco-Flame Retardants Based on the Renewable Raw Materials, Polymer Green Flame Retardants, Elsevier B.V., 2014, pp. 255–266 Search PubMed.
- C. Réti, M. Casetta, S. Duquesne, S. Bourbigot and R. Delobel, Flammability properties of intumescent PLA starch and lignin, Polym. Adv. Technol., 2008, 19, 628–635 CrossRef PubMed.
- S. Hu, L. Song, H. Pan, Y. Hu and X. Gong, Thermal properties and combustion behaviors of flame retarded epoxy acrylate with a chitosan based flame retardant containing phosphorus and acrylate structure, J. Anal. Appl. Pyrolysis, 2012, 97, 109–115 CrossRef CAS PubMed.
- M. Moreno, G. Lligadas, J. C. Ronda, M. Galià and V. Cáldiz, Phospha-Michael addition to enone-containing triglyceride derivatives as an efficient route to flame retardant renewable thermosets, J. Polym. Sci., Part A: Polym. Chem., 2012, 50, 3206–3213 CrossRef CAS PubMed.
- L. de Montero Espinosa, J. C. Ronda, M. Galià and V. Cádiz, A straightforward strategy for the efficient synthesis of acrylate and phosphine oxide-containing vegetable oils and their crosslinked materials, J. Polym. Sci., Part A: Polym. Chem., 2009, 47, 4051–4063 CrossRef PubMed.
- J. Alongi, R. Carletto, F. Bosco, F. Carosio, A. Di Blasio, F. Cuttica, V. Antonucci, M. Giordano and G. Malucelli, Caseins and hydrophobins as novel green flame retardants for cotton fabrics, Polym. Degrad. Stab., 2014, 99, 111–117 CrossRef CAS PubMed.
- M. Canetti, F. Bertini, A. de Chirico and G. Audisio, Thermal degradation behaviour of isotactic polypropylene blended with lignin, Polym. Degrad. Stab., 2006, 91, 494–498 CrossRef CAS PubMed.
- A. de Chirico, M. Armaninia, P. Chinib, G. Cioccolob, F. Provasolia and G. Audisioa, Flame retardants for polypropylene based on lignin, Polym. Degrad. Stab., 2003, 79, 139–145 CrossRef CAS.
- L. Ferry, G. Dorez, A. Taguet, B. Otazaghine and J. M. Lopez-Cuesta, Chemical modification of lignin by phosphorus molecules to improve the fire behavior of polybutylene succinate, Polym. Degrad. Stab., 2014, 113, 135–143 CrossRef PubMed.
- Y. Yu, S. Fu, P. Song, X. Luo, Y. Jin, F. Lu, Q. Wu and J. Ye, Functionalized lignin by grafting phosphorus–nitrogen improves the thermal stability and flame retardancy of polypropylene, Polym. Degrad. Stab., 2012, 97, 541–546 CrossRef CAS PubMed.
- P. Thirukumaran, A. Shakila Parveen and M. Sarojadevi, Synthesis and Copolymerization of Fully Biobased Benzoxazines from Renewable Resources, ACS Sustainable Chem. Eng., 2014, 2, 2790–2801 CrossRef CAS.
- B. A. Howell and Y. G. Daniel, Thermal degradation of phosphorus esters derived from isosorbide and 10-undecenoic acid, J. Therm. Anal. Calorim., 2015, 121, 411–419 CrossRef CAS.
- R. Ménard, C. Negrell-Guirao, L. Ferry, R. Sonnier and G. David, Synthesis of biobased phosphate flame retardants, Pure Appl. Chem., 2014, 86, 1637–1650 CrossRef.
- P. Joseph and J. Ebdon, in Fire retardancy of polymeric materials, ed. C. Wilkie and A. Morgan, CRC Press, 2010, pp. 107–127 Search PubMed.
- H. Vahabi, R. Sonnier and L. Ferry, Effects of ageing on the fire behaviour of flame-retarded polymers: a review, Polym. Int., 2015, 64, 313–328 CrossRef CAS PubMed.
- R. Ménard, C. Negrell-Guirao, L. Ferry, R. Sonnier and G. David, Synthesis of new flame-retardants by radical chain transfer copolymerization of glycidyl methacrylate and dimethoxy-phosphorylmethyl methacrylate, Eur. Polym. J., 2014, 57, 109–120 CrossRef PubMed.
- G. Lligadas, J. C. Ronda, M. Galià and V. Cádiz, Development of novel phosphorus-containing epoxy resins from renewable resources, J. Polym. Sci., Part A: Polym. Chem., 2006, 44, 6717–6727 CrossRef CAS PubMed.
- S. Ma, X. Liu, Y. Jiang, L. Fan, J. Feng and J. Zhu, Synthesis and properties of phosphorus-containing bio-based epoxy resin from itaconic acid, Sci. China: Chem., 2014, 57, 379–388 CrossRef CAS.
- L. Gu, G. Chen and Y. Yao, Two novel phosphorus nitrogen-containing halogen-free flame retardants of high performance for epoxy resin, Polym. Degrad. Stab., 2014, 108, 68–75 CrossRef CAS PubMed.
- C. Huggett, Estimation of rate of heat release by means of oxygen consumption measurements, Fire Mater., 1980, 4, 61–65 CrossRef CAS PubMed.
- F. Laoutid, L. Bonnaud, M. Alexandre, J. M. Lopez-Cuesta and P. Dubois, New prospects in flame retardant polymer materials: From fundamentals to nanocomposites, Mater. Sci. Eng., R, 2009, 63, 100–125 CrossRef PubMed.
- R. E. Lyon and M. Janssens, Polymer Flammability, Off. Aviat. Res., DOT/FAA/AR, Washington, D.C. 20591, 2005 Search PubMed.
- S. Correa, Formation Under Gas-Turbine Combustion Conditions, Combust. Sci. Technol., 1993, 87, 329–362 CrossRef CAS PubMed.
- H. Nouailhas, C. Aouf, G. Le Gueverné, S. Caillol, B. Boutevin and H. Fulcrand-Hoh, Synthesis and properties of biobased epoxy resins. part 1. Glycidylation of flavonoids by epichlorohydrin, J. Polym. Sci., Part A: Polym. Chem., 2011, 49, 2261–2270 CrossRef CAS PubMed.
- M. Baboulene and G. Sturtz, Reactive De Phosphites Sodes, En Milieu Alcoolique, vis-a-vis D'Oxiranes. Synthese De Phosphonates Fonctionnels, Phosphorus Sulfur Relat. Elem., 1979, 7, 101–107 CrossRef CAS PubMed.
- E. Nifantev, M. Koroteev, L. Kolchonova and A. Sokurenko, Dialkylphosphite reaction with glycide phenol esters, Zh. Obshch. Khim., 1986, 56, 220–221 CAS.
- E. Ryazantsev, D. Ponomarev and V. Albitskaya, Interaction of organophosphorus alpha-oxides with alcohols and phenols, Zh. Obshch. Khim., 1987, 57, 2300–2303 CAS.
- Z. Li, S. Racha, L. Dan, H. El-subbagh and E. Abushanab, A General and Facile Synthesis, J. Org. Chem., 1993, 5779–5783 CrossRef CAS.
- A. Sardarian and Z. Shahsavari-Fard, Convenient and Regioselective One Pot Solvent Free Synthesis of β-Hydroxyphosphonates, Synth. Commun., 2007, 37, 289–295 CrossRef CAS PubMed.
- Y. Catel, U. K. Fischer and N. Moszner, Monomers for adhesive polymers, 10-synthesis, radical photopolymerization and adhesive properties of methacrylates bearing phosphonic acid groups, Macromol. Mater. Eng., 2013, 298, 740–756 CrossRef CAS PubMed.
- X. He, A. H. Conner and J. A. Koutsky, Evaluation of Furfurylamines as Curing Agents for Epoxy Resins, J. Polym. Sci., Part A: Polym. Chem., 1992, 533–542 CrossRef CAS PubMed.
- M. S. Holfinger, A. H. Conner, D. R. Holm and C. G. Hill, Synthesis of difurfuryl diamines by the acidic condensation of furfurylamine with aldehydes and their mechanism of formation, J. Org. Chem., 1995, 60, 1595–1598 CrossRef CAS.
- L. González, F. Ferrando, X. Ramis, J. M. Salla, A. Mantecón and A. Serra, Characterization of new reworkable thermosetting coatings obtained by cationic and anionic curing of DGEBA and some Meldrum acid derivatives, Prog. Org. Coat., 2009, 65, 175–181 CrossRef.
- M. Bertoncini, J. Hoepfner and S. Pezzin, A Novel Route for the Amidation of Carbon Nanotubes and their Use as Rein-forcement in Epoxy Matrix Compositese, Curr. Org. Chem., 2013, 17, 1838–1843 CrossRef CAS.
- H. Vothi, C. Nguyen, K. Lee and J. Kim, Thermal stability and flame retardancy of novel phloroglucinol based organo phosphorus compound, Polym. Degrad. Stab., 2010, 95, 1092–1098 CrossRef CAS PubMed.
- N. Grassie, M. I. Guy and N. H. Tennent, Degradation of epoxy polymers. Part 5—Photo-degradation of bisphenol-A diglycidyl ether cured with ethylene diamine, Polym. Degrad. Stab., 1986, 14, 209–216 CrossRef CAS.
- S. V. Levchik and E. D. Weil, Thermal decomposition, combustion and flame-retardancy of epoxy resins – A review of the recent literature, Polym. Int., 2004, 53, 1901–1929 CrossRef CAS.
- D. Price, Thermal behaviour of covalently bonded phosphate and phosphonate flame retardant polystyrene systems, Polym. Degrad. Stab., 2007, 92, 1101–1114 CrossRef CAS PubMed.
Footnote |
† Electronic supplementary information (ESI) available. See DOI: 10.1039/c5ra12859e |
|
This journal is © The Royal Society of Chemistry 2015 |
Click here to see how this site uses Cookies. View our privacy policy here.