DOI:
10.1039/C5RA11243E
(Paper)
RSC Adv., 2015,
5, 63012-63016
SiO2@NiO core–shell nanocomposites as high performance anode materials for lithium-ion batteries
Received
12th June 2015
, Accepted 16th July 2015
First published on 16th July 2015
Abstract
SiO2@NiO core–shell nanocomposites of ca. 80 nm in diameter with a thin NiO shell were assembled via a facile online deposition of NiO and investigated as an anode for lithium ion batteries. The results indicated that the specific discharge capacity of the obtained SiO2@NiO core–shell nanocomposite electrode still retains 585 mA h g−1 at a discharge current density of 100 mA g−1 after 60 cycles and presents a coulombic efficiency of almost 100%, exhibiting good cycling stability and excellent rate capability after the first few cycles. This might be accounted for by the reversible lithiation/delithiation of the product Si due to the irreversible lithiation of SiO2 while the irreversible lithiation of NiO to produce metal Ni nanoparticles is responsible for the activation of SiO2, which is demonstrated by comparing the cyclic voltammetries (CVs) and electrochemical impedance spectra (EIS) of SiO2, NiO and SiO2@NiO electrodes.
Introduction
Considerable efforts have been devoted to rechargeable lithium-ion batteries (LIBs) with high energy and power densities and long cycles to meet the ever-increasing energy demands and environmental concerns, which have also been extended to large scale devices such as electric vehicles (EVs) including EVs and plug-in EVs.1–3 However, the energy and power densities of current LIBs with commercial graphite anodes are still below the requirements for EVs development in terms of their relatively low theoretical specific capacity of 372 mA h g−1 for LiC6 and poor rate-capability.4–7 As a result, various materials with high specific capacity have been making attempts to be explored as new anode candidates, such as alloys, metal oxides, and metal dichalcogenide etc.8–11 Among them, silicon is considered to be an optimal anode material for the next-generation LIBs thanks to its highest theoretical specific capacity (approximately 4200 mA h g−1, with the formation of Li22Si5 alloy).12,13 However, Si electrode presents poor cycling performance due to its severe volume expansion upwards of 300% upon Li insertion generating large mechanical large mechanical stresses and subsequent cracking or pulverization and solid electrolyte interphase (SEI) degradation.8,12,14 Consequently, substantial endeavours have been made to alleviate its electrochemical cycling performance by preparing nanoparticles, thin films and Si-based composites.14–20 Nevertheless, the cost of silicon makes the anode composite far from industrial application level.
As an alternative, tremendous attention has recently turned to silica (SiO2) as a viable anode material for LIBs due to its high abundance on earth, low discharge potential, and high theoretical specific capacity of 1965 mA h g−1 since Gao et al. claimed that commercial SiO2 nanoparticles (7 nm in diameter) can react with Li between 0.0 and 1.0 V (vs. Li/Li+) with a reversible capacity of 400 mA h g−1,13 albeit bulk SiO2 is generally considered as an electrochemically inactive material due to its strong Si–O bond and low electronic conductivity. The mechanism investigation on SiO2 as anode material for LIBs shows lithium ions react with SiO2 to produce nano-Si domains imbedded inert Li4SiO4/Li2O matrix, which prevents the nano-Si from electrochemical aggregation during cycling and buffer in a certain degree the big volume change caused by the lithiation of active Si as well, thus keeping the geometric integrity of the electrode. This indicates that SiO2 anode as alternative Si anode essentially relieves the lithiation/delithiation of Si to overcome the drastic volume expansion during charge/discharge process.21 Thus, it is crucial for the electrochemical performance of SiO2 as anode for LIBs to initiate the first lithiation process of SiO2 to produce nano-Si. Given strong Si–O bond and low electronic conductivity of SiO2, some strategies have been employed to ameliorate the lithiation/delithiation of SiO2 as anode for LIBs, such as tree-like thin films, carbon-coated nanoparticles, hollow nanostructures and so on.21–26 Nonetheless, those could rarely activate essentially SiO2 with respect to strong Si–O bond as anode for LIBs. Recent investigations on some metal oxides as Li-storage materials revealed that the reversible electrochemical reactions of metal oxides with lithium are driven by the formation of nano-sized metal in the range 1–5 nm.27–29 Inspired by this, we conceive that SiO2 should be able to be activated electrochemically by the nano-sized metal formed online via electrochemical reaction of metal oxide so that SiO2 is lithiated rapidly to produce nano-Si embedded in the produced matrix Li2O, followed by the reversible lithiation/delithiation of nano-Si.
Hereby, we incorporated metal oxide NiO into SiO2 to fabricate SiO2@NiO core–shell nanocomposites and explored the electrochemical performance of the as-obtained SiO2@NiO core–shell nanocomposites as anode materials for LIBs.
Experimental
Materials and synthesis
All of the chemical reagents used were purchased from Sinopharm Chemical Reagent Co., Ltd., Shanghai and used without further purification unless otherwise stated. In a typical synthesis of silica of ca. 80 nm in diameter, 3 ml of 25% NH3·H2O solution was added into a mixed solution containing 28 ml of deionized water and 140 ml absolute ethanol. Then 4 ml of tetraethylorthosilicate (TEOS) was promptly injected into the above solution under vigorous stirring and the milky suspension was formed. After continuous stirring for 24 h, the formed silica was collected by centrifugation, washed with absolute ethanol for 2 times in order to remove the unreacted precursor and then dried at 80 °C for 5 h. The white silica nanostructures were obtained after annealing in a muffle furnace at 400 °C for 4 h. For the synthesis of SiO2@NiO core–shell nanocomposites, 1.454 g of nickel nitrate and 9 g of urea were added into the above prepared monodispersed silica milky suspension under vigorous stirring to mix uniformly, and then reacted at 80 °C for 5 h. The resulting mixture was centrifuged and washed with deionized water and absolute ethanol for 3 times, respectively. The final product of SiO2@NiO core–shell nanocomposite was dried at 80 °C and sintered at 500 °C for 3 h.
Characterization
The X-ray diffraction (XRD) patterns were collected by a Shimadzu DX-6000 advanced X-ray diffractometer using the Cu Kα radiation with λ = 0.15418 nm over 2θ degree from 10° to 70° at a scan rate of 4° min−1. Field emission scanning electron microscopy (FESEM) images were taken by a Hitachi SEM and the transmission electron microscopy (TEM) images were acquired using a JEOL TEM-2010 operating with an acceleration voltage of 200 kV. Energy-dispersive spectrum (EDS) was taken on JEOL TEM-2000.
Electrochemical measurements
Electrochemical performance of the prepared SiO2@NiO core–shell nanocomposite was characterized vs. Li using CR2016 coin cells with an electrolyte comprising 1 M LiPF6 in ethylene carbonate and diethyl carbonate (EC
:
DEC = 1
:
1 v/v). Electrodes were prepared via mixing SiO2@NiO core–shell nanocomposite powder, Super P acetylene black, and polyvinylidene fluoride (PVdF) in a weight ratio of 7
:
2
:
1, with n-methyl pyrrolidone (NMP) as dispersant. The resulting slurry was then compressed onto copper foils and allowed to dry at 80 °C for 24 h. The cells were assembled in an argon-filled Mikrouna lab glovebox. All cells were tested vs. Li at room temperature from 0 to 3.0 V using a program-controlled Battery Test system (Land®, Wuhan, China) at varying current densities. Cyclic voltammetry measurements were conducted on a CHI660B electrochemical workstation (Chenghua, Shanghai, China) at a scan rate of 0.2 mV s−1. EIS measurements were measured at open potential with an AC amplitude of 5 mV over the frequency range from 100 kHz to 0.001 Hz.
Results and discussion
The uniformly monodispersed silica nanospheres of ca. 80 nm in diameter (Fig. 1a) were fabricated by general sol–gel process of tetraethylorthosilicate (TEOS), followed by the deposition of online produced NiO nanoparticles, yielding uniform SiO2@NiO core–shell nanocomposites with an average diameter of ca. 80 nm, as shown in Fig. 1b and c for the typical SEM and TEM images of SiO2@NiO core–shell nanocomposites, respectively. Obviously, TEM image demonstrates an extremely thin NiO wrinkled layer coated on the surface of SiO2 nanosphere with nearly negligible layer thickness (<1 nm) owing to the similar size of SiO2@NiO core–shell nanocomposite (Fig. 1b and c) with SiO2 nanoparticles (Fig. 1a). The energy dispersive spectroscopy (EDS) for a selected area on the copper TEM grid was further performed to identify the composition of the obtained SiO2@NiO core–shell nanoparticles (Fig. 1d), showing about 3 wt% of the coated NiO around SiO2 nanospheres. The phase purity analysis of the obtained SiO2@NiO core–shell nanocomposites by the powder X-ray diffraction (XRD) is compared with those of pure SiO2 and NiO in Fig. 2a. The broad and weak diffraction peak in the 2θ range of 21–23° for both pure SiO2 and SiO2@NiO core–shell nanocomposite is observed, indicating the existence of amorphous SiO2. The diffraction peaks due to NiO in the case of SiO2@NiO core–shell nanocomposites are much more broader and less intense compared to that of pure NiO nanoparticle, suggesting the smaller size of NiO nanoparticle in SiO2@NiO core–shell nanocomposites than pure NiO. Therefore, the SiO2@NiO core–shell nanocomposites with thin NiO shell are prepared by our proposed approach.
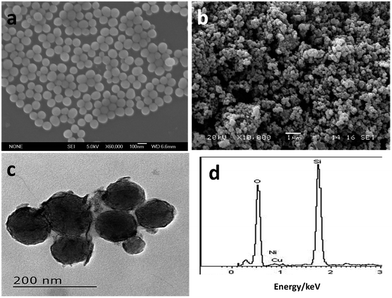 |
| Fig. 1 (a) SEM image of SiO2; (b) and (c) SEM and TEM images of the obtained SiO2@NiO core–shell nanocomposites; (d) EDS spectrum of SiO2@NiO core–shell nanocomposites on selected region of image. | |
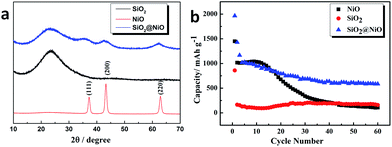 |
| Fig. 2 (a) Powder X-ray diffraction patterns of the obtained SiO2, NiO and SiO2@NiO; (b) cycling stabilities of NiO, SiO2 and SiO2@NiO electrodes at a rate of 100 mA g−1. | |
To evaluate the electrochemical performance of the obtained SiO2@NiO core–shell nanocomposites as anode material for Li ion battery, three two-electrode 2016 coin cells with SiO2@NiO core–shell nanocomposites, SiO2 and NiO as anode, respectively, were also assembled with Li metal as the counter electrode for comparison. The galvanostatic discharge/charge behaviors of the obtained three two-electrode cells were performed for 60 cycles in the voltage range of 0–3 V at 100 mA g−1, as shown in Fig. 2b. The SiO2@NiO core–shell nanocomposite electrode delivers an initial discharge capacity of 1961 mA h g−1 at a rate of 100 mA g−1, which is the highest among the obtained three electrodes. Subsequently, a sharp decrease in capacity after the first cycle is observed. Such a large irreversible capacity could be attributed to the formation of the SEI layer and two irreversible electrochemical reactions of the lithiations of NiO and SiO2 to produce metal Ni nanoparticle and semiconductive metal Si nanoparticles, respectively, because the theoretical specific capacities of both NiO and SiO2 are remarkable.25,30–32 After ca. 50 cycles, the discharge capacity of the SiO2@NiO core–shell nanocomposite electrode almost levels off and still retains approximately 585 mA h g−1 at 100 mA g−1. However, the discharge capacity of the individual NiO or SiO2 electrode almost decreases up to 140 mA h g−1 or 170 mA h g−1, respectively at a rate of 100 mA h g−1 after 50 cycles albeit their large initial discharge capacity of 1449 mA h g−1 or 859 mA h g−1, respectively, indicating the great amelioration of the capacity fading due to the incorporation of NiO into SiO2.
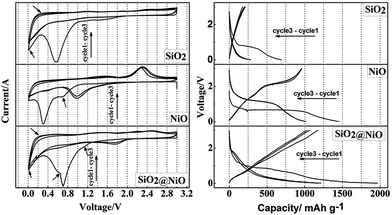 |
| Fig. 3 Comparison of cyclic voltammetries and galvanostatic voltage profiles of the first three cycles for NiO, SiO2 and SiO2@NiO electrodes. | |
To rationalize the above electrochemical performance of the obtained SiO2@NiO core–shell nanocomposites as anode material for Li ion battery, the cyclic voltammetries (CVs) at a scan rate of 0.2 mV s−1 and the galvanostatic discharge/charge voltage profiles of three prepared electrodes for the first three cycles in the voltage window of 0–3.0 V at the discharge current density of 100 mA g−1 were carried out (Fig. 3). Comparing CVs of the SiO2@NiO core–shell nanocomposite electrode with those of the other two electrodes, an obvious broad cathodic peak in the first cycle is observed and located at 0.56 V, 0.3 V and 0.7 V for SiO2, NiO and SiO2@NiO electrode, respectively, corresponding to the decomposition of electrolyte or the formation of SEI layer,33,34 which contributes to the large irreversible discharge capacity of the first cycle. However, in the subsequent cycles of the three electrodes, the broad cathodic peak disappears, suggesting the sole occurrence of SEI layer formation during the first cycle for the three electrodes. These are in good agreement with the corresponding galvanostatic discharge/charge voltage profiles of the first three cycles in which the corresponding voltage plateau is observed. On the other hand, in CV of NiO electrode, the distinctive cathodic and anodic peaks located at 0.7 V and 2.3 V, respectively for the first cycle and at 1.0 V and 2.3 V, respectively for the subsequent cycles, are attributed to the reversible oxidation and reduction reactions of NiO with lithium as follows:35,36 NiO + 2Li ↔ Ni0 + Li2O, the shift of cathodic peaks to the large voltage after the first cycle manifests the less polarization due to the disappearance of SEI layer. Nevertheless, it is noteworthy that in CV of SiO2@NiO core–shell nanocomposite electrode, the cathodic peak is located at 1.1 V for the first cycle and at 1.7 V for the subsequent cycles due to the lithiation of NiO while the anodic peaks are not observed, showing the irreversible lithiation of NiO in SiO2@NiO core–shell nanocomposite electrode as follows: NiO + 2Li → Ni0 + Li2O, which attributes to large discharge capacity of SiO2@NiO electrode for the first few cycles. This might be due to small amount of NiO coated on the surface of SiO2, otherwise NiO undergoes the reversible lithiation/delithiation in SiO2@NiO core–shell nanocomposite electrode. Meanwhile, the cathodic peak located at 0.64 V for SiO2@NiO core–shell nanocomposite electrode due to the irreversible lithiation of SiO2 is perceived, followed by the reversible lithiation/delithiation (alloying/dealloying) of the product Si nanoparticles owing to the lithiation of SiO2, as detected at 0.01 V and 0.22 V, which is in accordance with CV of SiO2 electrode and the literatures.15,37 These reactions involving SiO2 in SiO2@NiO core–shell nanocomposite electrode are illustrated in the following:21,26,38
|
SiO2 + Li+ → Li2O + Si
| (1) |
Reaction (1) is irreversible and Reaction (2) is reversible. Obviously, Reaction (2) is responsible for the cycling stability and excellent rate capability of SiO2@NiO core–shell nanocomposite electrode. The irreversible lithiation of NiO to produce metal Ni nanoparticles facilitates the subsequent electrochemical reaction of SiO2 because metal Ni nanoparticles might catalyze the reaction of SiO2 with lithium to generate Si nanoparticles imbedded in Li2O matrix.39 Subsequently, Si nanoparticles imbedded in Li2O matrix performs reversible lithiation/delithiation process, which can accommodates the volume expansion of Si during the lithiation, thus alleviating the cycling performance of SiO2.
Furthermore, the rate capability of the obtained SiO2@NiO core–shell nanocomposite electrode at different charge/discharge rates, measured after 10 cycles at each rate from 100 mA g−1 to 500 mA g−1 in an ascending order, followed by a return to 100 mA g−1 is shown in Fig. 4a. During the first 10 cycles at a rate of 100 mA g−1, large irreversible discharge capacity and remarkable capacity fading with low coulombic efficiency are observed, which is in agreement with Fig. 2b for cycling stability. Expectedly after 10 cycles, cycling at higher rates produces lower discharge capacities as follows: 680 mA h g−1 at 200 mA g−1, 500 mA h g−1 at 300 mA g−1, and 350 mA h g−1 at 500 mA g−1. After 50 cycles the discharge capacity retains approximately 585 mA h g−1 at 100 mA g−1 and the coulombic efficiency is almost 100%, indicating the stable cycling and excellent rate capability after initial few cycles. Besides, the incorporation of NiO into SiO2 might also ameliorate the electrochemical conductivity of SiO2, which is vital for SiO2 as alternative of anode due to the poor intrinsic electrochemical conductivity of SiO2. Impedance experiments were applied to explore the effect of NiO layer coated on SiO2 nanoparticles on the interfacial impedance of SiO2@NiO core–shell nanocomposite electrode. Fig. 4 shows Nyquist plots of the SiO2@NiO core–shell nanocomposite electrode and the SiO2 nanoparticles before cycling. The semicircles of the Nyquist plots in Fig. 4 indicates that interfacial impedance of SiO2@NiO core–shell nanocomposite electrode is lower than the corresponding SiO2 nanoparticle, revealing the favourable electrode conductivity of SiO2@ NiO core–shell nanocomposite electrode compared to pure SiO2 electrode.
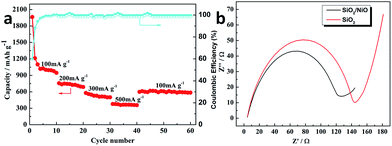 |
| Fig. 4 (a) Rate capability and coulombic efficiency of the SiO2@NiO nanocomposite between 3 and 0 V; (b) comparison of electrochemical impedance spectra of SiO2 electrode and SiO2@NiO core–shell nanocomposite electrode. | |
Conclusions
SiO2@NiO core–shell nanocomposites with thin NiO shell were fabricated successfully by a facile online deposition of NiO and explored as anode for lithium-ion battery. The obtained SiO2@NiO core–shell nanocomposite electrode undergoes the irreversible lithiation of NiO to produce metal Ni nanoparticle and matrix Li2O, which activates the followed irreversible lithiation of SiO2 to produce Si nanoparticle embedded in matrix Li2O due to the catalysis of metal Ni nanoparticle and the favorable electronic conductivity of NiO. Subsequently, the obtained Si nanoparticles embedded in matrix Li2O proceed the reversible alloying/dealloying of Si with lithium, which could enhance the Si structural stability and accommodates the volume expansion. Therefore, the SiO2@NiO core–shell nanocomposite electrode exhibits good cycling stability and excellent rate capability, showing the promising as anode for lithium ion battery.
Acknowledgements
This work was supported by Hubei Provincial Natural Science Foundation of China (No. 2015CFC842), Education Science Foundation of Hubei Province (No. T200908), Project of Chinese Ministry of Education (No. 208088).
Notes and references
- M. Armand and J. M. Tarascon, Nature, 2008, 451, 652–657 CrossRef CAS PubMed.
- J. Tollefson, Nature, 2008, 456, 436–440 CrossRef CAS PubMed.
- B. Scrosati and J. Garche, J. Power Sources, 2010, 195, 2419–2430 CrossRef CAS PubMed.
- S. Flandrois and B. Simon, Carbon, 1999, 37, 165–180 CrossRef CAS.
- J. B. Goodenough and Y. Kim, Chem. Mater., 2010, 22, 587–603 CrossRef CAS.
- V. Etacheri, R. Marom, R. Elazari, G. Salitra and D. Aurbach, Energy Environ. Sci., 2011, 4, 3243–3262 CAS.
- M. Endo, C. Kim, K. Nishimura, T. Fujino and K. Miyashita, Carbon, 2000, 38, 183–197 CrossRef CAS.
- C.-M. Park, J.-H. Kim, H. Kim and H.-J. Sohn, Chem. Soc. Rev., 2010, 39, 3115–3141 RSC.
- M. V. Reddy, G. V. Subba Rao and B. V. R. Chowdari, Chem. Rev., 2013, 113, 5364–5457 CrossRef CAS PubMed.
- P. Roy and S. K. Srivastava, J. Mater. Chem. A, 2015, 3, 2454–2484 CAS.
- L. Ji, Z. Lin, M. Alcoutlabi and X. Zhang, Energy Environ. Sci., 2011, 4, 2682–2699 CAS.
- M. Delong, C. Zhanyi and H. Anming, Nano-Micro Lett., 2014, 6, 347–358 CrossRef.
- B. Gao, S. Sinha, L. Fleming and O. Zhou, Adv. Mater., 2001, 13, 816–819 CrossRef CAS.
- M. T. McDowell, S. W. Lee, I. Ryu, H. Wu, W. D. Nix, J. W. Choi and Y. Cui, Nano Lett., 2011, 11, 4018–4025 CrossRef CAS PubMed.
- T. Zhang, L. Fu, J. Gao, L. Yang, Y. Wu and H. Wu, Pure Appl. Chem., 2006, 78, 1889–1896 CrossRef CAS.
- L.-F. Cui, R. Ruffo, C. K. Chan, H. Peng and Y. Cui, Nano Lett., 2009, 9, 491–495 CrossRef CAS PubMed.
- J. K. Lee, K. B. Smith, C. M. Hayner and H. H. Kung, Chem. Commun., 2010, 46, 2025–2027 RSC.
- M.-H. Park, M. G. Kim, J. Joo, K. Kim, J. Kim, S. Ahn, Y. Cui and J. Cho, Nano Lett., 2009, 9, 3844–3847 CrossRef CAS PubMed.
- J. Song, S. Chen, M. Zhou, T. Xu, D. Lv, M. L. Gordin, T. Long, M. Melnyk and D. Wang, J. Mater. Chem. A, 2014, 2, 1257–1262 CAS.
- J. Song, M. Zhou, R. Yi, T. Xu, M. L. Gordin, D. Tang, Z. Yu, M. Regula and D. Wang, Adv. Funct. Mater., 2014, 24, 5904–5910 CrossRef CAS PubMed.
- B. Guo, J. Shu, Z. Wang, H. Yang, L. Shi, Y. Liu and L. Chen, Electrochem. Commun., 2008, 10, 1876–1878 CrossRef CAS PubMed.
- P. Lv, H. Zhao, J. Wang, X. Liu, T. Zhang and Q. Xia, J. Power Sources, 2013, 237, 291–294 CrossRef CAS PubMed.
- N. Yan, F. Wang, H. Zhong, Y. Li, Y. Wang, L. Hu and Q. Chen, Sci. Rep., 2013, 3, 1568 Search PubMed.
- Q. Sun, B. Zhang and Z.-W. Fu, Appl. Surf. Sci., 2008, 254, 3774–3779 CrossRef CAS PubMed.
- W.-S. Chang, C.-M. Park, J.-H. Kim, Y.-U. Kim, G. Jeong and H.-J. Sohn, Energy Environ. Sci., 2012, 5, 6895–6899 CAS.
- Z. Favors, W. Wang, H. H. Bay, A. George, M. Ozkan and C. S. Ozkan, Sci. Rep., 2014, 4, 4605 Search PubMed.
- S. Grugeon, S. Laruelle, R. Herrera-Urbina, L. Dupont, P. Poizot and J. M. Tarascon, J. Electrochem. Soc., 2001, 148, A285–A292 CrossRef CAS PubMed.
- P. Poizot, S. Laruelle, S. Grugeon and J. M. Tarascon, J. Electrochem. Soc., 2002, 149, A1212–A1217 CrossRef CAS PubMed.
- P. Poizot, S. Laruelle, S. Grugeon, L. Dupont and J. M. Tarascon, Nature, 2000, 407, 496–499 CrossRef CAS PubMed.
- J. Tu, Y. Yuan, P. Zhan, H. Jiao, X. Wang, H. Zhu and S. Jiao, J. Phys. Chem. C, 2014, 118, 7357–7362 CAS.
- L. Liu, Y. Guo, Y. Wang, X. Yang, S. Wang and H. Guo, Electrochim. Acta, 2013, 114, 42–47 CrossRef CAS PubMed.
- X. H. Huang, J. P. Tu, C. Q. Zhang, X. T. Chen, Y. F. Yuan and H. M. Wu, Electrochim. Acta, 2007, 52, 4177–4181 CrossRef CAS PubMed.
- D. Xie, Q. Su, W. Yuan, Z. Dong, J. Zhang and G. Du, J. Phys. Chem. C, 2013, 117, 24121–24128 CAS.
- L. Su, Z. Zhou and M. Ren, Chem. Commun., 2010, 46, 2590–2592 RSC.
- J. Xu, L. Li, F. He, R. Lv and P. Yang, Electrochim. Acta, 2014, 148, 211–219 CrossRef CAS PubMed.
- Z. Wang, L. Zhou and X. W. David Lou, Adv. Mater., 2012, 24, 1903–1911 CrossRef CAS PubMed.
- H. Li, Electrochem. Solid-State Lett., 1999, 2, 547–549 CrossRef CAS PubMed.
- Y. Yao, J. Zhang, L. Xue, T. Huang and A. Yu, J. Power Sources, 2011, 196, 10240–10243 CrossRef CAS PubMed.
- U. Boesenberg, M. A. Marcus, A. K. Shukla, T. Yi, E. McDermott, P. F. Teh, M. Srinivasan, A. Moewes and J. Cabana, Sci. Rep., 2014, 4, 7133 CrossRef CAS PubMed.
|
This journal is © The Royal Society of Chemistry 2015 |
Click here to see how this site uses Cookies. View our privacy policy here.