DOI:
10.1039/C5RA08851H
(Paper)
RSC Adv., 2015,
5, 51078-51085
Temperature-responsive nanofibers for controllable oil/water separation†
Received
12th May 2015
, Accepted 2nd June 2015
First published on 3rd June 2015
Abstract
Surface functionalization with stimuli-responsive materials can turn an ordinary material into a smart one that shows adaptive properties upon external stimuli. In this study, an electrospun regenerated cellulose (RC) nanofibrous membrane was firstly prepared; subsequently, poly(N-isopropylacrylamide) (PNIPAAm), a thermo-responsive polymer, was surface grafted to form the polymer chains/brushes on the surface of RC nanofibers via the surface-initiated atom transfer radical polymerization (SI-ATRP) method. Thereafter, the PNIPAAm-modified RC nanofibrous membrane was investigated for its temperature-responsive surface wettability at temperatures below/above the lower critical solution temperature (LCST). Furthermore, the nature of the hydrophilic/hydrophobic transitions of the modified nanofibrous membrane was also investigated through the water up-take and release experiment at various temperatures. Especially, as responses to different temperatures, the PNIPAAm-grafted nanofibrous membrane exhibits switchable super-lyophilic/super-lyophobic properties at a water–oil–solid three-phase interface. With the large surface area and switchable surface wettability, the as-prepared PNIPAAm-grafted nanofibrous membrane exhibits excellent properties of controllable oil/water separation, and possesses great potential towards both wastewater treatment and oil purification.
Introduction
Oil/water separation technology has attracted much attention in recent years due to the increasing problems of industrial oily waste water discharge, offshore oil spillage, and the high cost of treating domestic waste water. Therefore, a large number of oil/water separation materials have been fabricated based on polymer membranes,1,2 metal nets,3,4 nanoparticles,5,6 or textiles7,8 with special surface wettability. In addition to fixed surface wettability, materials with switchable surface wettability have also been developed for controllable oil/water separation triggered by pH value,9 electric field,10 thermo-treatment,11 or multiple stimuli.12 Considering the recycling and anti-fouling properties of the separation materials, some responsive hydrophilic/underwater superoleophobic membranes were developed with self-cleaning or anti-fouling function.13,14 Overall, materials with the stimuli-responsive property, which are generally defined as ‘smart materials’, have shown great potential to offer on-demand treatments towards liquid pollution.
Among the various fabrication methods of all the smart materials mentioned above, surface modification is the most popular one, which can turn an ordinary material into a smart one with certain stimulus sensibility. Usually, the modification agent determines the stimulus a material responds to, while the substrate determines the functional efficiency and capacity of the material. Specifically, with the purpose of waste water treatment or oil purification, high adsorption efficiency and capacity of the material is greatly required.15,16 Nanofibers with the diameter in submicron range or even nanoscale have shown great promise to serve as substrates of functional materials,17–19 because the large surface area provided by nanofibers means more chemical reaction sites and a higher degree of physical contact, which can result in improved adsorption efficiency.20 To fabricate nanofibers with such advantages, electrospinning has been considered as a versatile technique.18
In our experiments here, regenerated cellulose (RC) nanofibers were modified with poly(N-isopropylacrylamide) (PNIPAAm) via surface-initiated atom transfer radical polymerization (SI-ATRP).21–23 PNIPAAm, as a temperature-responsive polymer, has attracted more attention, because of the transition between coil and globule with the change of wettability (hydrophilic and hydrophobic, respectively) in an aqueous solution at lower critical solution temperature (LCST, +32 °C).24,25 As suggested, the grafted temperature-sensitive PNIPAAm brushes can turn the RC nanofiber into a smart material, the surface wettability of which can be switched between hydrophilic and hydrophobic with the change of temperature of the environment.
The switchable wettability, triggered by temperature, enables the material to provide specific solutions towards the separation of various oil/water mixtures. To be specific, at room temperature, the PNIPAAm-RC nanofiber presents a hydrophilic and under-water superoleophobic property. As a result, water can pass through and the oil will be blocked by the pre-wetted PNIPAAm layer. Therefore, in a water-in-oil mixture, the PNIPAAm-RC nanofiber can clean the oil phase by removing water drops out without much oil adhering. In contrast, the PNIPAAm layer can let the oil pass through and block the water due to the oleophilic and under-oil superhydrophobic property at temperature above the LCST. This enables the PNIPAAm-RC nanofibers to treat the oil polluted water by drawing the oil drops out at a high temperature. With the combination of responsive wettability and high adsorption efficiency, the PNIPAAm-RC nanofiber shows outstanding potential in various types of oil/water separation situations, for instance, wastewater treatment and oil purification. Scheme 1 shows the fabrication procedures and the thermo-responsive wettability at a water–oil–solid interface of PNIPAAm-RC nanofibers.
 |
| Scheme 1 The fabrication process of PNIPAAm-RC nanofibers undergoing electrospinning, hydrolysis and SI-ATRP; and the temperature-responsive super-lyophobic/super-lyophilic property at water–oil–solid interface of the prepared PNIPAAM-RC nanofiber membrane. | |
In this report, RC nanofibers were fabricated through electrospinning method from a cellulose acetate (CA) solution, followed by hydrolysis in strong base. Hydrolysis of CA was referred to in Menkhaus's work,16 and had no damage on well-defined cylindrical morphology of the nanofibers. Thereafter, through SI-ATRP, the RC nanofibers were surface functionalized by PNIPAAm brushes, which introduced a thermal-responsive wettability at oil–water–solid interfaces. The results indicate that the prepared PNIPAAm-RC nanofibers show excellent water absorption from water/oil mixture at 22 °C and oil absorption from oil/water mixtures at 40 °C. To date, most of the existing oil/water separation materials can hardly have versatile applications due to the fixed wettability;26–28 and even if some stimuli-responsive materials have been designed for selective oil/water separation, few of them are qualified for the in situ oil/water removal because of the poor adsorbability.29,30 Innovatively, the study presented here can lead to a simple method to realize controllable oil/water separation in situ.
Experimental section
Materials
Cellulose acetate (CA, ACROS, Mn ∼ 100
000 g mol−1), acetone (VWR International 99.8%), dimethylacetamide (DMAc, Duksan Chemical 99.5%), sodium hydroxide (NaOH, VWR International 99%), 2-bromoisobutyryl bromide (BiB, Aldrich 98%), triethylamine (TEA, Aldrich 99%), 4-(dimethylamino) pyridine (DMAP, Aldrich 99%), tetrahydrofuran (THF, J&K 99.9%), N-isopropylacrylamide (NIPAAm, J&K 99%), methanol (MeOH, Duksan Chemical 99.9%), pentamethyldiethylenetriamine (PEMDETA, Aldrich 99%), copper(I) bromide (CuBr, J&K 98%).
Characterization
Field emission scanning electron microscopy (FE-SEM, JSM-6335F, Japan) was used to observe the surface morphologies of the electrospun CA nanofibers, RC nanofibers and PNIPAAm-grafted RC nanofibers, with a gold sputtering prior to imaging. All the samples were dried at 40 °C under vacuum and then fixed on the sample stage by electroconductive double-tape at room temperature before the FE-SEM test. Then, the samples were observed at room temperature under vacuum condition by FE-SEM.
Atomic force microscopy (AFM, Veeco, USA) was utilized to observe topography of the RC nanofibers before and after SI-ATRP.
Differential scanning calorimetry (DSC, PerkinElmer Diamond DSC, USA) was employed to investigate the interaction between polymer and water. The test was performed in the temperature range of 23 °C to 60 °C using a heating rate of 5 °C min−1. Prior to the test, 5 mg of as-prepared PNIPAAm-RC nanofibers were soaked with 5 mg of distilled water.
Fourier transform infrared (FT-IR, PerkinElmer Spectrum 100, USA) was used to characterize the functional groups of the CA, RC and PNIPAAm-grafted nanofibers.
Static oil/water contact angle (CA) measurements were carried out with OCA20 (Data Physics, Germany) using a sample chamber to control the test temperature. The data of each contact angle was calculated averagely from five repeated measurements.
Fabrication of electrospun RC nanofibers
Prior to electrospinning, 15 g of CA was dissolved in 100 mL mixture of acetone and DMAc (3
:
1, v/v). The electrospinning setup was purchased from Micro & Technologies Expert (TL-Pro), Shenzhen, China. During electrospinning, a positive high voltage of 15 kV was applied to the needle, and the flow rate of 0.5 mL h−1 was maintained. The CA nanofibers were collected as an overlaid membrane on a roller covered with aluminium foil. The rotational speed of the collector was set at 10 rpm during electrospinning. The ambient relative humidity in the chamber was around 55%.
The as-electrospun CA nanofibrous membrane was hydrolysed upon immersion into 0.05 M NaOH aqueous solution for 24 h to obtain the RC nanofibrous membrane. The RC nanofibrous membrane was then rinsed with deionized (DI) water for three times and dried in a vacuum oven.
Immobilization of the ATRP-initiator on the RC nanofibers
The dried electrospun RC nanofibrous membrane was immersed into a mixture solution containing 15 mL anhydrous THF, 10 mg DMAP and 0.2 mL TEA, and then 0.2 mL of BiB was added into the mixture. Subsequently, the reaction mixture was kept at room temperature for 12 h under stirring in a nitrogen atmosphere. After reaction, the initiator-modified electrospun RC nanofibrous membranes were rinsed thoroughly with THF, acetone, and DI water and finally dried at 40 °C under vacuum for 24 h.
Surface-grafted with PNIPAAm
4 mL of the mixture of MeOH and DI water solution (3
:
1, v/v) was added into a Schlenk flask and deoxygenated by a nitrogen flow for 15 minutes. The initiator-modified RC nanofibers (35 mg), NIPAAm (1.2 g), CuBr (16 mg), and PMDETA (0.05 mL) were then added into the deoxygenated mixture. Subsequently, the mixture was degassed by three vacuum–nitrogen cycles under an ice-salt bath to remove the oxygen from the system, followed by been sealed for 6 hours (products with grafting duration of 2 hours and 10 hours have also been made as shown in Fig. S1†) with slow magnetic stirring at room temperature. Next, the PNIPAAm-RC nanofibers were sequentially rinsed by MeOH and DI water to remove the residual monomers, unbonded polymers, and catalyst complex. Finally, the PNIPAAm-RC nanofibers were dried under vacuum overnight.
Investigation of water collection/release and separation of oil/water mixtures
In order to further illustrate the temperature-responsive behavior of the modified nanofibers and the accompanied interfacial phenomenon with water, water collection and release performance of the as-prepared PNIPAAm-RC nanofibers was investigated, using the unmodified RC nanofibers as reference. Water collection of the as-prepared PNIPAAm-RC nanofibers was firstly conducted at room temperature (22 °C) and in an artificial humid atmosphere generated by an ultrasonic humidifier (Midea S40U-T, China). Typically, the PNIPAAm-RC nanofibers were placed in the generated fog (with relative humidity, RH, around 95% and the sprayed flow being 1/3 of maximum to avoid vast water condensation in short time), and the water uptake (weight percent) along with the humidity exposure time was recorded. Then, the water release rate of the modified samples were also investigated by measuring the water loss along with the exposure time in an oven at 40 °C. It is noted that the samples had a 375% (weight percent to the samples) initial water uptake prior to the water release test. The water collection and release of the unmodified RC nanofibers were also studied for reference.
Oil/water separation was carried out through the absorption of methylene blue (MB) dyed deionized (DI) water, in n-hexane and the absorption of chloroform drops, colored by oil-based ink, in DI water. Typically, the as-prepared PNIPAAm-RC nanofibers were placed into the mixtures under magnetic stirring for 30 seconds.
Measurement of liquid absorption capacity and reusability
In order to investigate the absorption capacity of the modified RC nanofibers for water and common oils (including n-hexane, CHCl3, paraffin oil, silicone oil, peanut oil and gasoline), the experiments were performed in the water/hexane mixture (with a weight ratio of 10
:
90) and oil/water mixture (with a weight ratio of 10
:
90) for water absorption and for oil absorption, respectively, and the final absorption capacity was generated by average value of 5 times experiments. Noted that, the water absorption capacity was measured at room temperature (22 °C); while the oil absorption capacity was measured at 40 °C. In a typical absorption measurement, the samples were immersed in the mixture for 30 seconds. After removed from the mixtures, the samples were cleaned with tissue paper to remove the adherent excess of water or oil. The weight of the sample before and after absorption (defined as Winitial and Wfinal, respectively) were used for the calculation of absorption capacity C, defined as C = (Wfinal − Winitial)/Winitial.
The reusability of the PNIPAAm-RC nanofibers was evaluated by repeated absorption-clean process. Normally, the absorbate saturated PNIPAAm-RC nanofibers were cleaned using ethanol and acetone, and dried in an oven before the next absorption-clean cycle. The absorption-clean cycle was repeated for 5 times.
Results and discussion
Characterization and morphology
As shown in Fig. 1a, the electrospun CA nanofibrous membrane consisted of overlaid nanofibers with diameters of ∼200–500 nm, and the nanofibers were relatively uniform without obvious beads and beaded nanofibers. After hydrolysis with 0.05 M NaOH aqueous solution, the RC nanofibers maintained well-defined cylindrical morphology and the diameter had no obvious change (as shown in Fig. 1b). After the surface modification for 6 hours via the ATRP method, the RC nanofiber was fully covered by a concentric and rough PNIPAAm layer causing the increase of diameter by ∼50% (Fig. 1c). The grafting reactions proceeding for shorter and longer time were also considered, but it was found that the long-time reaction led to the clogging of fibrous pores (see Fig. S1c and S1f, ESI†), while the short-time one resulted in an insufficient grafting content (the fiber base could not be evenly covered by a continuous polymer coating, as shown in Fig. S1a and S1d†). The atomic force microscopy (AFM) was further applied for characterization of the electrospun RC nanofibers before and after PNIPAAm modification (as shown in Fig. 1d and e). Additionally, Fig. 1c and e reveal the hierarchical structure of the materials including sub-micro-scaled roughness from the nanofibers and nano-scale roughness due to the formation of PNIPAAm layer on RC nanofibers. Wenzel31 reported that surface morphology or roughness assists in determining the macroscopic wettability of solid surface by magnifying the wettability levels to their extreme. As a result, the apparent surface wettability of PNIPAAm layer, either hydrophilicity or hydrophobicity, can be raised to a higher degree by the increased surface roughness.
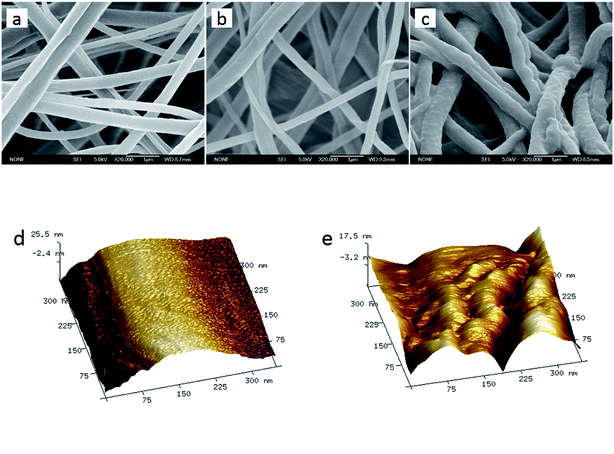 |
| Fig. 1 SEM images of CA nanofibers (a), RC nanofibers (b), and PNIPAAm-RC nanofibers (c); and AFM topography images of RC nanofibers before (d) and after (e) PNIPAAm modification. | |
FT-IR was employed to study differences among the CA, RC, and PNIPAAm-RC nanofibrous membranes (Fig. 2). After hydrolysis, the characteristic ester band of CA at 1750 cm−1 completely disappeared, which indicates that CA was thoroughly converted into RC.32 After SI-ATRP, the primary amide band (–C
O) at 1640 cm−1 and the secondary amide band (–N–H) at 1540 cm−1 can be clearly identified in the spectrum, which means that the PNIPAAm has been successfully grafted onto the RC nanofibers.33,34
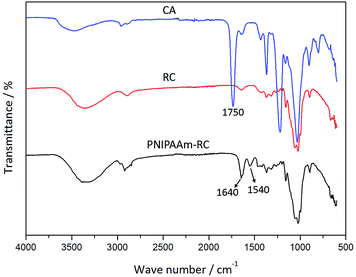 |
| Fig. 2 FTIR spectra of CA nanofibers, RC nanofibers, and PNIPAAm-RC nanofibers. | |
Thermo-responsive behavior
The pre-wetted PNIPAAm-RC nanofibers were further investigated by DSC for consecutive heating/cooling cycles, and the results were shown in Fig. 3. Repeated LCST transition was detected by the presence of the typical endothermic peaks at 29 °C on cooling experiment and exothermic peaks at 32 °C on heating experiment. These thermal transitions are mainly attributed to the forming and breaking of hydrogen bonds between polymer and water molecules along with the change of polymer configuration.24,35,36 When the PNIPAAm-RC nanofibers are heated to the LCST, the hydrogen bonds between PNIPAAm and water start to be broken due to the aggregating and collapse of the polymer chains. When temperature is lower than the LCST in the presence of water, the polymer chains stretch and the amide groups on the polymer brushes bind to the surrounding water molecules by forming hydrogen bonds. The responsive stretching/shrinking behavior and the interaction with surrounding water of the grafted PNIPAAm brushes can be simulated as the illumination in Fig. 3b. These structural changes occurring around the LCST directly cause the reversible change of surface wettability of the PNIPAAm-RC nanofibers, which can be observed from the static water contact angle (WCA) measured by switching the temperature at 22 °C and 40 °C. As shown in Fig. 3c, the WCA was ∼0° at 22 °C, while a WCA of ∼113° could be observed at 40 °C. The phenomena of WCA oscillation between 0° and 113° indicated a transition between hydrophilic and hydrophobic, which is consistent to previous research.24
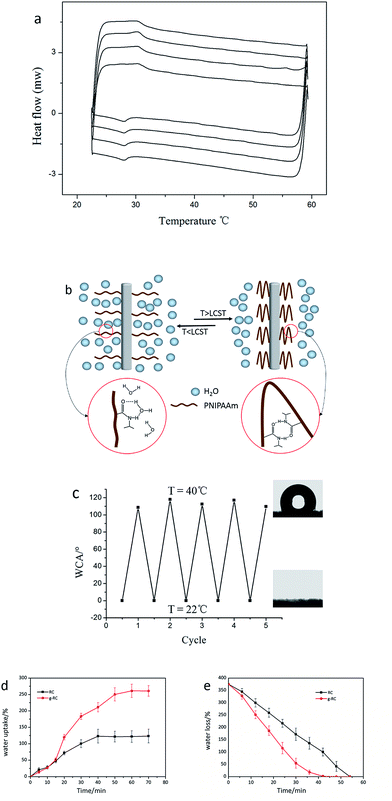 |
| Fig. 3 Reversible responsive behavior of PNIPAAm-RC nanofibers: DSC thermogram showing the thermo transition around the LCST in continuous cycles (a). Mechanism graph of the responsive interfacial phenomenon with water (b). Reversible WCA of PNIPAAm-RC nanofibrous membrane at 22 °C and 40 °C (inset: images of the droplets at the respective temperatures) (c). Water collection (d) and release (e) efficiency of the PNIPAAm-RC nanofibers at 22 °C and 40 °C respectively (with unmodified RC nanofibers as reference). | |
The water collection/release performance of the as-prepared PNIPAAm-RC nanofibers were investigated to further illustrate the responsive polymer behavior and accompanied interfacial phenomenon with water. Water collection performance was studied in an artificial humid atmosphere (RH: ∼95%) at room temperature (22 °C), and the water uptake along with the exposure time under humid atmosphere was plotted in Fig. 3d. At the beginning of humidity exposure, the bare and PNIPAAm grafted RC nanofibers had the same weight increasing rate due to physical water adsorption from the fog. About 15 min later, water adsorbed by the PNIPAAm-RC nanofibers became enriched and formed hydrogen bonds with PNIPAAm brushes (referring to Fig. 3b). And the hydrogen bonds between polymer chains and water molecules could limit the water lost in wind, which resulted in an increase of water uptake speed. Finally, under the experimental condition of this study (a small fog flow), the PNIPAAm-RC nanofibers showed a high water uptake of approximately 260% only after around one hour adsorption. While, the water uptake of bare RC nanofibers gradually tended to be stable at about 123% indicating the equilibration between physical water adsorption and evaporation lost in the wind. The high capacity of water collection of PNIPAAm-RC nanofibers at room temperature is attributed to the rough surface modified nanofibers and the hydrogen bonding between water molecules and polymer chains. Moreover, the PNIPAAm-RC nanofibers also showed fast water release when the temperature was above LCST. Compared with the unmodified RC nanofibers, the PNIPAAm grafted RC nanofibers had a much higher water loss rate at 40 °C, as shown in Fig. 3e. The easier water release of PNIPAAm-RC nanofibers is attributed to the shrinkage of the PNIPAAm brushes and the formation of intra-polymer hydrogen bonds when the temperature is above LCST, which squeezes the water molecules out of the PNIPAAm layer and thus increase the water evaporation rate.
The in-air oil contact angles (OCA) were measured at different temperatures. Fig. 4a and b show that the PNIPAAm-RC nanofibers are always oleophilic (∼0°) in air at both 22 °C and 40 °C. Note that each OCA of 0° was measured at a steady state (10 s after placing the oil droplet on the membrane). Before the steady state, there was indeed a minor difference between the OCA test results at 22 °C and 40 °C. As shown by Fig. S2,† the OCA switched to 0° after 9.13 s at 22 °C, a little slower than that at 40 °C (3.69 s). This is because the surface energy of the oil droplet is most likely to be decreased with increasing temperature, endowing it with a higher affinity to PNIPAAm-RC nanofibers.37 However, the PNIPAAm-RC nanofibers always show oleophilic even with a relative difference at various temperatures. Therefore, the wettability of PNIPAAm-RC nanofibers at oil–water–solid interface (Fig. 4c–f) was mainly determined by the in-air WCA at different temperature. As shown in Fig. 4c and d, the PNIPAAm-RC nanofibers exhibited a transition from superoleophobic (∼160.2°) to superoleophilic (∼0°) under water when the temperature increased from 22 °C to 40 °C. This apparent OCA (θOW) transition with temperature variation in aqueous environment can be explained by:38
|
 | (1) |
Where
θW and
θO represent the WCA and OCA in air, respectively;
γOA,
γWA and
γOW are interface tensions of oil–air, water–air and oil–water interfaces, respectively. According to
eqn (1), it is reasonable that the in-air hydrophilic and oleophilic PNIPAAm-RC nanofibers show oleophobic property under water at the solid–water–oil interface at room temperature. This can be attributed to the generally much lower surface tension of oil/organic liquids than that of water, which results in a commonly negative value of
γOA![[thin space (1/6-em)]](https://www.rsc.org/images/entities/char_2009.gif)
cos
θO −
γWA![[thin space (1/6-em)]](https://www.rsc.org/images/entities/char_2009.gif)
cos
θW. However, at a temperature above the LCST, the PNIPAAm-RC nanofibers become hydrophobic in air, which in turn makes the right hand of
eqn (1) always larger than 0, thus, makes the surface oleophilic. Similarly, the
eqn (1) can be transformed to
eqn (2) to predict the WCA (
θWO) altering of the PNIPAAm-RC nanofibrous membrane in an oily environment,
i.e., superhydrophilic (∼0°) at 22 °C but superhydrophobic (∼156.3°) at 40 °C (
Fig. 4e and f).
|
 | (2) |
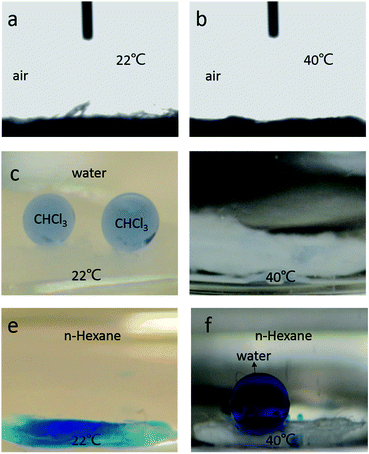 |
| Fig. 4 In-air OCA of the PNIPAAm-RC nanofibrous membrane at 22 °C (a) and 40 °C (b). Oil and water wettability of the PNIPAAm-RC nanofibrous membrane at the oil–water–solid interface: under-water superoleophobic (∼160.2°) at 22 °C (c), under-water superoleophilic (∼0°) at 40 °C (d); under-oil superhydrophilic (∼0°) at 22 °C (e), under-oil superhydrophobic (∼156.3°) at 40 °C (f). | |
As mentioned above, when the temperature is below the LCST, γWA
cos
θW and γOA
cos
θO are both positive and the value of the former one is normally larger than that of the latter one, which makes the θWO always less than 90°. In contrast, at a high temperature of 40 °C, θWO is always larger than 90° because of a definite negative value of the right hand of eqn (2) resulting from the hydrophobicity and oleophilicity of PNIPAAm-RC nanofibers in air. Furthermore, combining the high surface roughness of the PNIPAAm layer, the PNIPAAm-RC nanofibers ultimately exhibit extreme dual-scale wettability at temperatures below/above the LCST, including under-water superoleophobic/superoleophilic and under-oil superhydrophilic/superhydrophobic.
Thermo-responsive controllable oil/water separation
The obtained PNIPAAm-RC nanofibers were further used to absorb either oil or water from different oil–water mixture due to their temperature-responsive wettability. In a water-in-oil mixture, MB colored DI water was dropped into n-hexane. As shown in Fig. 5a, after the PNIPAAm-RC nanofibers were placed in the mixture under magnetic stirring at room temperature, blue water drops gradually disappeared and the nanofibers turned blue, indicating the efficient water absorption by PNIPAAm-RC nanofibers. To remove 0.04 g of water, less than 0.01 g of PNIPAAm-RC nanofibers were needed (referring to Table 1). Additionally, the PNIPAAm-RC nanofibers absorbed with water can be easily recycled by being dried in an oven. Analogously, the oil removal from water by PNIPAAm-RC nanofibers was performed at 40 °C, and the procedure is shown in Fig. 5b. Hence, by simply adjusting the operating temperature (below or above the LCST), the as-prepared PNIPAAm-RC nanofibers can be applied in dual-mode oil/water separation due to its responsive transition of wettability.
 |
| Fig. 5 Water removal from water-in-oil mixture at 22 °C (a) and oil removal from oil-in-water mixture at 40 °C (b) by using the as-prepared PNIPAAm-RC nanofibers. | |
Table 1 Absorption capabilities of the as-prepared PNIPAAm-RC nanofibers from different oil/water mixtures at 22 °C and 40 °C
Mixture |
Water-in-oil (22 °C) |
Oil-in-water (40 °C) |
Absorbate |
Water |
n-hexane |
CHCl3 |
Paraffin oil |
Silicone oil |
Peanut oil |
Gasoline |
Absorption capacity/% |
440 ± 22.0 |
346 ± 22.1 |
496 ± 29.8 |
318 ± 20.3 |
332 ± 29.3 |
295 ± 21.0 |
276 ± 19.8 |
Moreover, the oil/water absorption capacities of the PNIPAAm-RC nanofibers were studied by measuring the absorption weight in five cycles. The water-in-oil mixture was made with DI water and n-hexane. Varied oils (including n-hexane, CHCl3, paraffin oil, silicone oil, peanut oil and gasoline) were used for preparing the oil-in-water mixtures, which were used to investigate the oil absorption capacity and recycling property of the PNIPAAm-RC nanofibers. These mixtures were chosen to represent common pollutions from industrial drainage and daily emission. Table 1 shows the water and oil absorption capacities of the PNIPAAm-RC nanofibers (water uptake from water-in-oil mixture at 22 °C and oil uptake from varied oil-in-water mixtures at 40 °C) in weight percentage. It is obvious that the PNIPAAm-RC nanofibers show an excellent absorption capacity of about 4 times of its own weight for water from the water/hexane mixture at 22 °C, and also exhibit significant absorption capacities of about 3–5 times of its own weight for oils from oil/water mixture at 40 °C. Overall, the as-prepared PNIPAAm-RC nanofibers can be suitable for a wide range of oil/water separation with good capabilities. The specific absorption amount of the PNIPAAm-RC nanofibers may be determined by density, viscosity, or other physico-chemical properties of the absorbate.
It is noted that the PNIPAAm-RC nanofibers could also be reused for absorbing water and various oils with high capacities, which is significant for practical applications. After absorption, the PNIPAAm-RC nanofibers were rinsed using ethanol and acetone to remove the absorbates for the next absorption cycle. The varied absorption capacities are shown in Fig. 6. As shown in curve A (water absorption at 22 °C), the water absorption had no remarkable decrease after five cycles, indicating an excellent reusability for water absorption from water–oil mixture. Significantly, oil absorption could be negligible in this process due to the superoleophobicity of the water absorbed PNIPAAm-RC nanofibers at room temperature. Additionally, the PNIPAAm-RC nanofibers also showed great recycling properties for varied oils (curve B–G in Fig. 6). For oils with strong volatility (n-hexane, CHCl3 and gasoline, showed by curve B, C and D, respectively), the absorption capacities remained almost constant after five absorption cycles. For absorbates with poor volatility and high viscosity—paraffin oil, silicone oil and peanut oil (curve D, E and G, respectively), the absorption capacities had reduction after each absorption cycle. But still the absorption capacities can remain over 75% of the original after five absorption cycles.
 |
| Fig. 6 Absorption capacities of PNIPAAm-RC nanofibers in different cycles of absorption–desorption from varied mixtures. | |
As suggested by the results above, the as-prepared PNIPAAm-RC nanofiber can be suitable for the separation of various types of oil/water mixtures with both high absorption efficiency and easy recycling. This makes it a promising material to treat either oil-polluted water or water-polluted oil from both industrial drainage and daily emission.
Conclusion
In summary, we have demonstrated the preparation of a thermo-responsive nanofibrous membrane through grafting PNIPAAm chains/brushes on the electrospun RC nanofibers via a surface-initiated atom transfer radical polymerization method. The as-prepared PNIPAAm-RC membrane shows a switchable wettability, which makes it a smart material with controllable oil/water separation function. As reported, the oil/water separation mode can be switched by simply changing the operating temperature. Benefiting from the large surface area provided by electrospun nanofibers, the efficiency and capacity of oil/water absorption were highly improved.
In addition, PNIPAAm brushes with more adaptive LCST can be synthesized by fine-adjusting the polymer characteristics, e.g., Mn and PDI, or grafting density.35,39 Furthermore, by copolymerization with other polymers or synergy with other molecules, the reported method may be extended to a variety of applications (e.g., drug delivery, chemical separation, ion exchange, and molecule detection).
Acknowledgements
The authors gratefully acknowledge the financial support from The Hong Kong Polytechnic University Internal Fund (project code: Polyu G-YK50). We acknowledge Dr Jinlian Hu and Mr Lin Tan for the assistance of the electrospinning device.
References
- H. Ju, B. D. McCloskey, A. C. Sagle, Y. H. Wu, V. A. Kusuma and B. D. Freeman, J. Membr. Sci., 2008, 307, 260–267 CrossRef CAS PubMed.
- X. Y. Zhu, W. T. Tu, K. H. Wee and R. B. Bai, J. Membr. Sci., 2014, 466, 36–44 CrossRef CAS PubMed.
- J. An, J. F. Cui, Z. Q. Zhu, W. D. Liang, C. J. Pei, H. X. Sun, B. P. Yang and A. Li, J. Appl. Polym. Sci., 2014, 131, 40759 Search PubMed.
- Y. Z. Cao, X. Y. Zhang, L. Tao, K. Li, Z. X. Xue, L. Feng and Y. Wei, ACS Appl. Mater. Interfaces, 2013, 5, 4438–4442 CAS.
- L. P. Xu, X. W. Wu, J. X. Meng, J. T. Peng, Y. Q. Wen, X. J. Zhang and S. T. Wang, Chem. Commun., 2013, 49, 8752–8754 RSC.
- F. Novio and D. Ruiz-Molina, RSC Adv., 2014, 4, 15293–15296 RSC.
- J. P. Zhang and S. Seeger, Adv. Funct. Mater., 2011, 21, 4699–4704 CrossRef CAS PubMed.
- M. Zhang, C. Y. Wang, S. L. Wang and J. Li, Carbohydr. Polym., 2013, 97, 59–64 CrossRef CAS PubMed.
- L. B. Zhang, Z. H. Zhang and P. Wang, NPG Asia Mater., 2012, 4, e8 CrossRef PubMed.
- G. Kwon, A. K. Kota, Y. X. Li, A. Sohani, J. M. Mabry and A. Tuteja, Adv. Mater., 2012, 24, 3666–3671 CrossRef CAS PubMed.
- V. Janout, S. B. Myers, R. A. Register and S. L. Regen, J. Am. Chem. Soc., 2007, 129, 5756–5759 CrossRef CAS PubMed.
- Y. Z. Cao, N. Liu, C. K. Fu, K. Li, L. Tao, L. Feng and Y. Wei, ACS Appl. Mater. Interfaces, 2014, 6, 2026–2030 CAS.
- L. B. Zhang, Y. J. Zhong, D. Cha and P. Wang, Sci. Rep., 2013, 3, 2326 Search PubMed.
- S. J. Gao, Z. Shi, W. B. Zhang, F. Zhang and J. Lin, ACS Nano, 2014, 8, 6344–6352 CrossRef CAS PubMed.
- K. C. Krogman, J. L. Lowery, N. S. Zacharia, G. C. Rutledge and P. T. Hammond, Nat. Mater., 2009, 8, 512–518 CrossRef CAS PubMed.
- T. J. Menkhaus, H. Varadaraju, L. F. Zhang, S. Schneiderman, S. Bjustrom, L. Liu and H. Fong, Chem. Commun., 2010, 46, 3720–3722 RSC.
- J. Doshi and D. H. J. Reneker, PTB-Mitt., 1995, 105, 208 Search PubMed.
- T. Subbiah, G. S. Bhat, R. W. Tock, S. Pararneswaran and S. S. Ramkumar, J. Appl. Polym. Sci., 2005, 96, 557–569 CrossRef CAS PubMed.
- A. K. Gautam, C. L. Lai, H. Fong and T. J. Menkhaus, J. Membr. Sci., 2014, 466, 142–150 CrossRef CAS PubMed.
- P. M. Ajayan, L. S. Schadler and P. V. Braun, Nanocomposite science and technology, Wiley-VCH, Weinheim, 2003 Search PubMed.
- A. Carlmark and E. Malmstrom, J. Am. Chem. Soc., 2002, 124, 900–901 CrossRef CAS PubMed.
- A. Carlmark and E. E. Malmstrom, Biomacromolecules, 2003, 4, 1740–1745 CrossRef CAS PubMed.
- N. Singh, Z. Chen, N. Tomer, S. R. Wickramasinghe, N. Soice and S. M. Husson, J. Membr. Sci., 2008, 311, 225–234 CrossRef CAS PubMed.
- H. G. Schild, Prog. Polym. Sci., 1992, 17, 163–249 CrossRef CAS.
- Y. Ono and T. Shikata, J. Am. Chem. Soc., 2006, 128, 10030–10031 CrossRef CAS PubMed.
- M. H. Tai, P. Gao, B. Y. L. Tan, D. D. Sun and J. O. Leckie, ACS Appl. Mater. Interfaces, 2014, 6, 9393–9401 CAS.
- Y. Si, Q. X. Fu, X. Q. Wang, J. Zhu, J. Y. Yu, G. Sun and B. Ding, ACS Nano, 2015, 9, 3791–3799 CrossRef CAS PubMed.
- M. Obaid, N. A. M. Barakat, O. A. Fadali, M. Motlak, A. A. Almajid and K. A. Khalil, Chem. Eng. J., 2015, 259, 449–456 CrossRef CAS PubMed.
- B. L. Xue, L. C. Gao, Y. P. Hou, Z. W. Liu and L. Jiang, Adv. Mater., 2013, 25, 273–277 CrossRef CAS PubMed.
- L. X. Xu, N. Liu, Y. Z. Cao, F. Lu, Y. N. Chen, X. Y. Zhang, L. Feng and Y. Wei, ACS Appl. Mater. Interfaces, 2014, 6, 13324–13329 CAS.
- R. N. Wenzel, Ind. Eng. Chem., 1936, 28, 988–994 CrossRef CAS.
- L. F. Zhang, T. J. Menkhaus and H. Fong, J. Membr. Sci., 2008, 319, 176–184 CrossRef CAS PubMed.
- Y. V. Pan, R. A. Wesley, R. Luginbuhl, D. D. Denton and B. D. Ratner, Biomacromolecules, 2001, 2, 32–36 CrossRef CAS PubMed.
- M. Kaholek, W. K. Lee, S. J. Ahn, H. W. Ma, K. C. Caster, B. LaMattina and S. Zauscher, Chem. Mater., 2004, 16, 3688–3696 CrossRef CAS.
- H. G. Schild and D. A. Tirrell, J. Phys. Chem., 1990, 94, 4352–4356 CrossRef CAS.
- E. C. Cho, J. Lee and K. Cho, Macromolecules, 2003, 36, 9929–9934 CrossRef CAS.
- R. H. Dettre and R. E. Johnson Jr, J. Phys. Chem., 1967, 71, 1529–1531 CrossRef CAS.
- Y. C. Jung and B. Bhushan, Langmuir, 2009, 25, 14165–14173 CrossRef CAS PubMed.
- K. N. Plunkett, X. Zhu, J. S. Moore and D. E. Leckband, Langmuir, 2006, 22, 4259–4266 CrossRef CAS PubMed.
Footnote |
† Electronic supplementary information (ESI) available: Characterization of the PNIPAAm-modified regenerated cellulose (RC) nanofibers with shorter time and longer time grafting reaction by field-emission scanning electron microscopy (FE-SEM). Pictures recording the time needed by oil droplets to become 0° on PNIPAAm-RC nanofibrous membrane at 22 °C and 40 °C. Images of water contact angle (WCA) in air, oil contact angle (OCA) in air, oil and water wettability in oil–water–solid interfaces of unmodified RC nanofibers. See DOI: 10.1039/c5ra08851h |
|
This journal is © The Royal Society of Chemistry 2015 |
Click here to see how this site uses Cookies. View our privacy policy here.