DOI:
10.1039/C5RA02639C
(Paper)
RSC Adv., 2015,
5, 37768-37773
Fabrication of novel wave-transparent HMPBO fibre/BADCy laminated composites
Received
10th February 2015
, Accepted 8th April 2015
First published on 8th April 2015
Abstract
The method of “impregnation–winding–lamination–mould pressing” was performed to fabricate novel wave-transparent high modulus poly(p-phenylene-2,6-benzobisoxazole) fibre/bisphenol A cyanate ester resin (HMPBO fibre/BADCy) laminated composites. The “two-step approach” of methanesulfonic acid/γ-glycidoxy propyl trimethoxy silane (MSA/KH-560) was also proposed to functionalize the HMPBO fibres’ surface. Results revealed that KH-560 was grafted on the HMPBO fibres’ surface successfully. The functionalized HMPBO fibre/BADCy laminated composites possessed better ILSS & flexural strength, lower ε & tan
δ, and higher heat-resistance index & Tg. The ILSS and flexural strength of the functionalized HMPBO/BADCy laminated composites were increased to 53.7 MPa and 753.7 MPa, respectively. The corresponding ε and tan
δ were decreased to 2.93 and 0.00097, respectively. The corresponding heat-resistance index and Tg were increased to 219 °C and 236 °C, respectively. The functionalized HMPBO fibre/BADCy laminated composites display potential application in radomes and the antenna systems of aircrafts.
Introduction
Cyanate ester (CE) resins possess superior dielectric properties (dielectric constant of 3.0–4.0 and dielectric loss of 0.005–0.010), which reveal good stability in a wide range of temperature and electric field frequency,1–4 better than other thermosetting resins, such as epoxy resin, polyimide and bismaleimide, etc. Furthermore, CE resins possess excellent high-temperature mechanical properties, very low water-adsorption, good heat & humidity resistance, preferable dimensional stability and an epoxy-like processability, etc., and have been widely applied in aerospace, electronics, insulations, adhesives and other areas.5–8
Poly(p-phenylene-2,6-benzobisoxazole) (PBO) fibres possess light weight, superior dielectric properties (dielectric constant of 3.0 and dielectric loss of 0.001), outstanding specific tensile strength & modulus, excellent thermal stability, and good chemical & flame resistance,9–13 far exceeding other organic fibres. PBO/polymer advanced structural composites show promising applications in aerospace, navigation, bulletproof materials and reinforced materials.14,15
However, due to PBO fibres’ low surface activity and chemical inertia, the interfacial adhesion of the PBO fibre/polymer matrix is poor, which restricts the application of PBO fibres in high-performance composites. Work by Lu and coworkers16,17 has shown that surface functionalization of carbon fibres can effectively improve the interfacial adhesion properties of carbon fibre/polymeric matrix composites. Given that, surface functionalization of PBO fibres is also an effective method to increase the interfacial interactions between PBO fibres and polymer matrices. Recently, different functionalized methods have been proposed to improve the interfacial adhesion between PBO fibres and polymer matrices, including chemical treatment,18 plasma treatment,19 enzymatic treatment,20 γ-ray irradiation treatment,21 discharge treatment,22,23 polyhedral oligomeric silsesquioxane (POSS) molecules,24 and the combination treatment of several methods.25
In our previous work, the methods of polyphosphoric acid/absolute alcohol,26 γ-glycidoxy propyl trimethoxy silane (KH-560),27 γ-aminopropyl triethoxy silane (KH-550),28 oxygen plasma/POSS29 and methanesulfonic acid/KH-550/POSS,30 were adopted to functionalize the surface of PBO fibres. The results indicated that polar groups were successfully introduced on the PBO fibres’ surface and the interfacial adhesion of the PBO fibres to the polymer matrix was also improved effectively. Compared with the latter two methods, the former three methods are more applicable to functionalize lots of PBO fibres and much easier to fabricate PBO fibre/polymer matrix laminated composites.
In our present work, the method of “impregnation–winding–lamination–mould pressing” was performed to fabricate novel wave-transparent high modulus poly(p-phenylene-2,6-benzobisoxazole) fibre/bisphenol A cyanate ester resin (HMPBO fibre/BADCy) laminated composites. The “two-step approach” of methanesulfonic acid/γ-glycidoxy propyl trimethoxy silane (MSA/KH-560) was also proposed to functionalize the surface of the HMPBO fibres, to effectively improve their interfacial adhesion to the BADCy matrix. In addition, the influences of the HMPBO fibres’ surface functionalization on the mechanical properties, dielectric properties and thermal stabilities of the HMPBO fibre/BADCy laminated composites were also investigated. This paper is part of a large project on the development and preparation of novel wave-transparent polymeric composites with light weight, thermal insulation and high load-bearing capacity, which display potential application in radomes and the antenna systems of aircrafts, promising to replace the present wave-transparent composites of glass fibre/BADCy, quartz fibre/BADCy and/or kevlar fibre/BADCy composites.
Materials and methods
Materials
Bisphenol A cyanate ester (BADCy) resins were purchased from the Jiangdu Wuqiao Resin Factory (Jiangsu, China); epoxy resins were received from the Wuxi Resin Factory of Blue Star New Chemical Materials Co., Ltd. (Jiangsu, China); high modulus poly(p-phenylene-2,6-benzobisoxazole) (HMPBO) fibres, with the trade name Zylon™, were purchased from Toyobo Co. Ltd. (Osaka, Japan); γ-glycidoxy propyl trimethoxy silane (KH-560) was supplied by the Nanjing Shuguang Chemical Group Co., Ltd. (Jiangsu, China); methanesulfonic acid (MSA) was received from the Chengdu Kelong Chemical Co. Ltd. (Sichuan, Chian); absolute ethanol (EtOH), acetone and formaldehyde were all received from the Tianjin Ganglong Chemical Group Co., Ltd. (Tianjin, China).
Purification of BADCy
BADCy was dissolved in acetone and evaporated under 40 °C to obtain a saturated solution. It was then cooled to room temperature and kept for 3 h. The solid was filtered out from the liquid. The steps above were repeated three times to obtain white crystals, which were then ground into powders and dried for 24 h in a vacuum oven at 40 °C. Finally, purified white dry BADCy powder was obtained.
Surface functionalization of HMPBO fibres
HMPBO fibres were first immerged in EtOH and formaldehyde for 24 h at room temperature for each step, then washed with distilled water, and finally dried at 100 °C in a vacuum oven for 24 h. The obtained HMPBO fibres were then soaked in a 60 wt% MSA/distilled water solution for 12 h at 60 °C under ultrasonic vibration, and then washed with distilled water. The obtained HMPBO fibres and a KH-560/EtOH/distilled water solution (1/50/50, wt/wt/wt) were reacted for 6 h at 70 °C (pH ≈ 9), followed by ultrasonic vibration at the set temperature & power (100 W, 50 °C) for another 2 h. Finally, the MSA/KH-560 functionalized HMPBO fibres were washed with EtOH and distilled water, and dried at 120 °C for 24 h.
Fig. 1 shows the general fabrication process of the MSA/KH-560 functionalized HMPBO fibres.
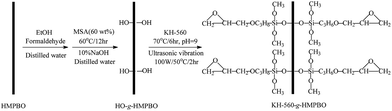 |
| Fig. 1 General fabrication process of the MSA/KH-560 functionalized HMPBO fibres. | |
Fabrication of the HMPBO fibre/BADCy composites
Mixtures of BADCy/epoxy resin (19/1, wt/wt) were heated to 150 °C and prepolymerized for 4 h. They were then cooled to below 100 °C, and excess acetone and an appropriate amount of dibutyltin dilaurate were added to obtain the prepreg glue. The dried HMPBO fibres were then immerged in the prepreg glue above, followed by filament winding, and then the HMPBO fibre/BADCy mixtures were laminated and moulding pressed at 10 MPa according to the following cured technology: 160 °C/1 h + 180 °C/2 h + 200 °C/5 h, followed by post-curing in a vacuum oven at 220 °C for 2 h.
Characterization
Thermo-gravimetric analyses of the samples were performed using a thermoanalyzer (STA 449F3, Netzsch Group, Germany) in the temperature range of 40–900 °C with a heating rate of 20 K min−1 under an argon atmosphere. Dynamic mechanical analysis (DMA) of the samples was performed using a DMA/SDTA861e (Mettler-Toledo Co. Switzerland) at 5 °C min−1 at 1 Hz. The morphologies of the samples were analyzed by scanning electron microscopy (SEM) using a VEGA3-LMH (TESCAN Corporation, Czech Republic). The flexural strength and the interlaminar shear strength (ILSS) of the samples were measured using an Electron Omnipotence Experiment Machine SANS-CMT5105 (Shenzhen New Sansi Corp., China) according to standard ASTMD 7264-2007 and ASTMD 2344-2000, respectively. The dielectric constant and dielectric loss of the samples were measured using a high frequency Q instrument (QBG-3D) and dielectric constant detector (S914) from Aiyi Electronic Equipment Co. Ltd. (Shanghai, China).
Results and discussion
Analysis and characterization of the HMPBO fibres
Fig. 2 shows the entire XPS scanning spectra of the native HMPBO fibres and functionalized HMPBO fibres. According to Fig. 2, various element contents can be calculated and are listed in Table 1.
 |
| Fig. 2 XPS scanning spectra of the native HMPBO and functionalized HMPBO fibres. | |
Table 1 Concentrations of various elements on the HMPBO surface
HMPBO samples |
Concentrations of elements/% |
C |
O |
N |
Si |
Native HMPBO fibres |
79.35 |
14.02 |
6.63 |
— |
Functionalized HMPBO fibres |
71.27 |
18.04 |
7.26 |
3.43 |
Carbon, oxygen and nitrogen elements are presented on the native HMPBO fibres’ surface. After the surface functionalization, the corresponding C1s, O1s and N1s peaks are all changed at different levels, due to the contribution of the KH-560 molecules. Meanwhile, the appearance of Si2p and Si2s peaks in Fig. 2 further confirms that KH-560 has covered on the HMPBO fibres’ surface successfully. The corresponding SEM morphologies of the native HMPBO fibres and functionalized HMPBO fibres are also shown in Fig. 3.
 |
| Fig. 3 SEM morphologies of the native HMPBO fibres and functionalized HMPBO fibres. | |
The surface of the native HMPBO fibres is smooth (Fig. 3a). After the surface functionalization, the surface of the HMPBO fibres becomes coarser, and there are several white substances adhering to the HMPBO fibres’ surface (Fig. 3b), which are ascribed to the KH-560 molecules grafting on the HMPBO fibres’ surface (also proved in Table 2).
Table 2 The elements and contents of the white substances on the functionalized HMPBO fibres’ surface
Element |
Weight/% |
Atom/% |
C |
36.01 |
43.39 |
O |
61.16 |
55.33 |
Si |
2.83 |
1.28 |
Total |
100.00 |
100.00 |
Mechanical properties of the HMPBO fibre/BADCy composites
Fig. 4 shows the mechanical properties of the HMPBO fibre/BADCY composites.
 |
| Fig. 4 The mechanical properties of the HMPBO fibre/BADCy composites. | |
Compared with the native HMPBO fibre/BADCy composites (40.8 MPa for ILSS and 618.1 MPa for flexural strength), the corresponding ILSS (53.7 MPa) and flexural strength (753.7 MPa) of the functionalized HMPBO fibre/BADCy composites are increased by 31.6 percent and 21.9 percent, respectively.
This can be attributed to the introduction of hydroxyl and epoxy polar groups on the surface of the functionalized HMPBO fibres after the surface functionalization, which can react with the active groups of the BADCy matrix and contribute to the improvement of the interfacial compatibility of the HMPBO fibre/BADCy matrix. Thus, the interfacial adhesion between the HMPBO fibres and the BADCy matrix is also enhanced, and finally the mechanical properties of the HMPBO fibre/BADCy composite are further increased accordingly. The corresponding SEM morphologies of the HMPBO fibre/BADCy micro-composites after a single fibre pull-out test are shown in Fig. 5. After the single fibre pull-out test, there is much more of the BADCy matrix remaining on the surface of the functionalized HMPBO fibres than on the native HMPBO fibres, which further proves that the functionalized HMPBO fibres possess a much larger interfacial adhesion to the BADCy matrix than the native HMPBO fibres. Thus, accordingly, the functionalized HMPBO fibres possess better friction with the BADCy matrix.
 |
| Fig. 5 SEM morphologies of the HMPBO fibre/BADCy micro-composites after the single fibre pull-out test. | |
Dielectric properties of the HMPBO fibre/BADCy composites
The dielectric properties of the HMPBO fibre/BADCy composites are shown in Table 3.
Table 3 Dielectric properties of the HMPBO fibre/BADCy composites
Samples |
ε |
tan δ |
Native HMPBO fibre/BADCy |
3.11 |
0.0016 |
Functionalized HMPBO fibre/BADCy |
2.93 |
0.00097 |
Compared with the native HMPBO fibre/BADCy composite (3.11 for the dielectric constant, ε and 0.0016 for the dielectric loss tangent, tan
δ), the corresponding ε and tan
δ of the functionalized HMPBO fibre/BADCy composite are decreased to 2.93 and 0.00097, respectively. After the surface functionalization, the interfacial compatibility between the functionalized HMPBO fibres and the BADCy matrix are improved effectively, and the corresponding interfacial polarization of the HMPBO fibre/BADCy and voidages of the inner HMPBO fibre/BADCy composite system are synchronously decreased, thus decreasing the ε and tan
δ of the HMPBO fibre/BADCy composite.
Thermal properties of the HMPBO fibre/BADCy composites
Fig. 6 shows the DMA curves of the HMPBO fibre/BADCy composites.
 |
| Fig. 6 DMA curves of the HMPBO fibre/BADCy composites. | |
HMPBO fibre/BADCy composites possess high storage modulus & excellent heat resistance, and the corresponding glass transition temperatures (Tg) of the native HMPBO fibre/BADCy composite and functionalized HMPBO fibre/BADCy composite is 214 °C and 236 °C, respectively. It can be deduced that the surface functionalization of HMPBO fibres can improve the Tg of the composite effectively. The reason is that surface functionalization of HMPBO fibres can improve the interfacial adhesion between the HMPBO fibres and the BADCy matrix and thereby increase the Tg of the HMPBO fibre/BADCy composite.
TGA curves of the HMPBO fibre/BADCy composites are presented in Fig. 7. The corresponding characteristic thermal data of the HMPBO fibre/BADCy composites are listed in Table 4.
 |
| Fig. 7 TGA curves of the HMPBO fibre/BADCy composites. | |
Table 4 Thermal data of the HMPBO fibre/BADCy composites
Samples |
Temperature/°C |
Heat-resistance index*/°C31 |
5 |
30 |
50 |
Native HMPBO fibre/BADCy |
361 |
480 |
745 |
212 |
Functionalized HMPBO fibre/BADCy |
367 |
501 |
778 |
219 |
The weight loss of the HMPBO fibre/BADCy composites is 1 percent at the beginning of the experiment (0–280 °C), and is mostly due to the loss of absorbed water and other small molecule volatilization. The weight loss reaches 37 percent over the range of 280–590 °C, which can be attributed to the BADCy matrix fusing, charring and decomposing. The weight loss of the HMPBO fibre/BADCy composite is 54 percent till 900 °C, which is mainly ascribed to the decomposition of the HMPBO fibres at high temperatures.
The corresponding weight loss temperatures of the functionalized HMPBO fibre/BADCy composite are all increased at the same stages (weight loss of 5%, 30% and 50%). When the weight loss is 50 wt%, the corresponding heat decomposition temperature of the functionalized HMPBO fibre/BADCy composite is increased from 745 °C to 748 °C, and the corresponding heat-resistance index is also increased from 212 °C to 219 °C. This suggests that the functionalized HMPBO fibre/BADCy composite possesses better thermal stability than that the native HMPBO fibre/BADCy composite. The reason is that a more efficient combination of the functionalized HMPBO fibres and the BADCy matrix can further increase the thermal stability of the HMPBO fibre/BADCy composite.
Conclusion
XPS and SEM-EDS analysis confirm that KH-560 is grafted on the HMPBO fibres’ surface successfully after the surface functionalization by MSA/KH-560. HMPBO fibre/BADCy composites possess outstanding mechanical properties, excellent dielectric properties & good thermal stabilities, and the surface functionalization of HMPBO fibres can further improve the mechanical properties, dielectric properties and thermal stabilities of the HMPBO fibre/BADCy composites, by improving the interfacial compatibility of the HMPBO fibre/BADCy matrix. Compared with those of the native HMPBO fibre/BADCy composite, the functionalized HMPBO fibre/BADCy composite possesses better ILSS & flexural strength, lower ε & tan
δ and higher heat-resistance index & Tg. The corresponding ILSS (53.7 MPa) and flexural strength (753.7 MPa) of the functionalized HMPBO fibre/BADCy composite are increased by 31.6 percent and 21.9 percent, respectively. The corresponding ε and tan
δ of the functionalized HMPBO fibre/BADCy composite are decreased to 2.93 and 0.00097, respectively. The corresponding heat-resistance index is increased from 212 °C to 219 °C, and the corresponding Tg is also increased from 214 °C to 236 °C. The functionalized HMPBO fibre/BADCy laminated composites display potential application in radomes and the antenna systems of aircrafts, promising to replace the present wave-transparent composites of glass fibre/BADCy, quartz fibre/BADCy and/or kevlar fibre/BADCy composites.
Acknowledgements
The authors are grateful for the support and funding from the Foundation of Natural Science Foundation of China (no. 51403175 and no. 81400765 to J. W. Gu); Shaanxi National Science Foundation of Shaanxi Province (no. 2014JQ6203 to J. W. Gu); Space Supporting Fund from China Aerospace Science and Industry Corporation (no. 2014-HT-XGD to J. W. Gu and Y. S. Tang) and the Fundamental Research Funds for the Central Universities (no. 3102015ZY066 to J. W. Gu and no. 3102015ZY063 to Y. S. Tang).
References
- B. H. Wang, Y. C. Jiao, A. J. Gu, G. Z. Liang and L. Yuan, Compos. Sci. Technol., 2014, 91, 8–15 CrossRef CAS PubMed.
- Y. S. Tang, J. W. Gu, Y. X. Yu and J. Kong, Polym. Compos., 2015 DOI:10.1002/pc.23111.
- S. K. Dai, A. J. Gu, G. Z. Liang and L. Yuan, Polym. Adv. Technol., 2011, 22, 262–269 CrossRef CAS PubMed.
- H. Y. Wu, A. J. Gu, G. Z. Liang and L. J. Yuan, Mater. Chem., 2011, 21, 14838–14848 RSC.
- X. Ning, J. Dang, X. K. Yue and J. P. Yuan, Polym. Compos., 2014, 34, 564–569 CrossRef PubMed.
- Y. S. Tang, J. Kong, J. W. Gu and G. Z. Liang, Polym.-Plast. Technol. Eng., 2009, 48, 359–366 CrossRef CAS.
- P. Badrinarayanan, M. K. Rogalski and M. R. Kessler, ACS Appl. Mater. Interfaces, 2012, 4, 510–517 CAS.
- W. Sun, M. R. Kessler, N. Bowler, K. W. Dennis, R. W. McCallum, Q. Li and X. Tan, ACS Appl. Mater. Interfaces, 2013, 5, 1636–1642 CAS.
- H. X. Yan, S. Y. Feng, Z. J. Zhang and S. H. Hu, J. Appl. Polym. Sci., 2014, 131, 40204 Search PubMed.
- L. Chen, F. Wei, L. Liu, W. L. Cheng, Z. Hu, G. S. Wu, Y. Z. Du, C. H. Zhang and Y. D. Huang, Compos. Sci. Technol., 2015, 106, 32–38 CrossRef CAS PubMed.
- L. Chen, Z. Hu, L. Liu and Y. D. Huang, RSC Adv., 2013, 3, 24664–24670 RSC.
- Z. Liu, P. Chen, D. B. Han, F. Lu, Q. Yu and Z. F. Ding, Vacuum, 2013, 92, 13–19 CrossRef CAS PubMed.
- T. Zhang, J. H. Jin, S. L. Yang, G. Li and J. M. Jiang, Carbohydr. Polym., 2009, 78, 364–366 CrossRef CAS PubMed.
- E. Mäder, S. Melcher, J. W. Liu, S. L. Gao, A. D. Bianchi, S. Zherlitsyn and J. Wosnitza, J. Mater. Sci., 2007, 42, 8047–8052 CrossRef PubMed.
- D. Liu, P. Chen, J. J. Mu, Q. Yu and C. Lu, Appl. Surf. Sci., 2011, 257, 6935–6940 CrossRef CAS PubMed.
- H. B. Lu and W. M. Huang, Appl. Phys. Lett., 2013, 102, 231910 CrossRef PubMed.
- H. B. Lu, Y. T. Yao, W. M. Huang and D. Hui, Composites, Part B, 2014, 67, 290–295 CrossRef CAS PubMed.
- G. M. Wu and Y. T. Shyng, Composites, Part A, 2014, 35, 1291–1300 CrossRef PubMed.
- K. Tamargo-Martínez, A. Martínez-Alonso, M. A. Montes-Morán and J. M. D. Tascon, Compos. Sci. Technol., 2011, 71, 784–790 CrossRef PubMed.
- J. L. Wang, G. Z. Liang, W. Zhao and Z. P. Zhang, Surf. Coat. Technol., 2007, 201, 4800–4804 CrossRef CAS PubMed.
- C. H. Zhang, Y. D. Huang and Y. D. Zhao, Mater. Chem. Phys., 2005, 92, 245–250 CrossRef CAS PubMed.
- Z. Liu, P. Chen, X. L. Zhang, Q. Yu, K. M. Ma and Z. F. Ding, Appl. Surf. Sci., 2013, 283, 38–45 CrossRef CAS PubMed.
- G. M. Wu and Y. T. Shyng, Arch. Comput. Mater. Sci. Surf. Eng., 2007, 28, 722–728 Search PubMed.
- B. Song, L. H. Meng and Y. D. Huang, Appl. Surf. Sci., 2012, 258, 10154–10159 CrossRef CAS PubMed.
- D. D. Liu, J. Hu, Y. M. Zhao, X. S. Zhou, P. Ning and Y. J. Wang, Appl. Polym. Sci., 2006, 102, 1428–1435 CrossRef CAS PubMed.
- J. W. Gu, T. Bai, J. Dang, J. J. Feng and Q. Y. Zhang, Fibres Polym., 2013, 14, 781–785 CrossRef CAS.
- J. W. Gu, J. Dang, W. C. Geng and Q. Y. Zhang, Fibres Polym., 2012, 13, 979–984 CrossRef CAS.
- Y. S. Tang, J. W. Gu and T. Bai, Fibres Polym., 2012, 13, 1249–1253 CrossRef CAS PubMed.
- H. L. Li, Y. S. Tang, J. W. Gu, J. Dang, T. Bai and J. J. Feng, Polym. Compos., 2013, 34, 2026–2030 CrossRef CAS PubMed.
- J. W. Gu, T. Bai, J. Dang, J. J. Feng and Q. Y. Zhang, Polym. Compos., 2014, 35, 611–616 CrossRef CAS PubMed.
- J. W. Gu, J. J. Du, J. Dang, W. C. Geng, S. H. Hu and Q. Y. Zhang, RSC Adv., 2014, 4, 22101–22105 RSC.
|
This journal is © The Royal Society of Chemistry 2015 |
Click here to see how this site uses Cookies. View our privacy policy here.