DOI:
10.1039/C5RA00367A
(Paper)
RSC Adv., 2015,
5, 33990-33998
Catalytic hydrogenation of phenol, cresol and guaiacol over physically mixed catalysts of Pd/C and zeolite solid acids†
Received
8th January 2015
, Accepted 7th April 2015
First published on 7th April 2015
Abstract
Highly reactive phenolic compounds of pyrolysis bio-oil are recognized as a major cause of the unpleasant properties of this biofuel. Catalytic hydrodeoxygenation of phenolic compounds of bio-oil is an efficient technique for improving the quality of bio-oil. Dual function catalysts consisting of metal and acid sites are usually used for transformation of bio-oil/bio-oil model compounds to high value hydrocarbons. Metal and acid sites are generally involved in hydrogenation/hydrodeoxygenation and dehydration/hydrocracking/dealkylation/alkylation reaction mechanisms, respectively. In this work, the product selectivity of hydrogenation of phenol, o-cresol, m-cresol and guaiacol was investigated over combined catalysts of Pd/C with zeolite solid acids of HZSM-5 (Si/Al of 30, 50 and 80) and HY (Si/Al of 30 and 60). Catalytic activity and product distribution in the hydrogenation process were affected by the density and strength of zeolite acid sites. HZSM-5 (30) with only weak acid sites showed lower cyclohexane selectivity compared with HZSM-5 (50) and HZSM-5 (80) which had both weak and strong acid sites. HY (30) and HY (60) containing only strong acid sites favored production of cycloketones.
1. Introduction
Bio-oil produced through biomass pyrolysis is considered as a renewable and sustainable source of energy.1,2 Due to the high oxygen content of biomass (around 50 wt%),3 bio-oil is highly oxygenated consisting of reactive chemical components (phenols, carboxylic acids, aldehydes, ketones, furfurals, carbohydrates and alcohols)4–7 and water (around 30 wt%).8 High content of such oxygen-containing compounds in bio-oil results in undesirable properties such as high viscosity, low heating value, low thermal and chemical stabilities, corrosiveness and immiscibility with fossil fuels.4,5,7,9–11 Therefore, bio-oil needs to be upgraded in order to be considered as a standard fuel. One of the most applicable and effective techniques for bio-oil upgrading is catalytic hydrodeoxygenation1,3,5,6,10 which treats bio-oil at high hydrogen pressure (50–350 bar) and moderate temperature (150–450 °C).12–14 Due to the wide variety of compounds which are present in bio-oil and involved in upgrading process, it is difficult to predict the reaction mechanism of bio-oil hydrotreating. The hydrodeoxygenation of different model compounds of bio-oil could be studied in order to find out the mechanisms of their transformation and to predict the overall reaction pathway in bio-oil hydrotreating. Since the phenolic fraction of bio-oil is highly reactive causing bio-oil instability, phenols have been widely used as bio-oil model compounds.11,15,16
Catalysts including both metal and acid functions are highly efficient for hydrotreating of bio-oil. Metal and acid sites accomplish hydrotreating reaction through hydrogenation/hydrogenolysis and dehydration/isomerization/alkylation/condensation mechanisms, respectively.3,4,17 These dual functional catalysts are generally prepared by embedding metals into acidic supports. As an alternative to dual functional catalysts, supported or unsupported metal catalysts such as Pd/C and RANEY® Ni could be physically mixed with liquid (H3PO4) and/or solid acids (HZSM-5, sulfated zirconia, Nafion/SiO2, Amberlyst 15) and used for hydrogenation of phenolic compounds of bio-oil.1,3,8,16 Zhao et al.8 reported that substituting liquid acid with solid acid enhances the hydrotreating efficiency of the mixed catalyst system. Brønsted acids are appropriate for hydrotreatment of oxygenated compounds due to the presence of H+ sites in their structure which promote dehydration reaction. Zeolites contain Brønsted acid sites and have high shape selectivity and thermal/hydrothermal stability which have been widely used in acid catalyzed reactions such as isomerization, cracking and alkylation.18 Zeolites with optimum density and strength of acid sites seem to be suitable for hydrodeoxygenation of bio-oil/bio-oil model compounds. The structural framework of zeolite includes the atoms of silicon and/or aluminium having tetrahedral coordination to four oxygen atoms.19,20 A zeolite consisting of only SiO4 is electrically neutral but the presence of each AlO4 in zeolite framework makes a negative charge which can be compensated by a cation.19,20 The presence of AlO4 species and cations in zeolite structure changes catalytic properties of zeolites. By compensating the negative charges with protons, zeolites become strong solid acids.
In this study, the reaction mechanisms of hydrogenation of phenols over physically mixed catalysts containing metal and acid active sites are investigated. Phenol, o-cresol, m-cresol and guaiacol (the most abundant phenolic compounds of bio-oil) were used as model compounds to investigate the hydrogenation activity of 10 wt% Pd/C and combined catalysts of 10 wt% Pd/C with HZSM-5 or HY zeolites. Effects of metal and acid active sites on catalytic activity and product selectivity of hydrogenation process were studied. The dependency of catalytic properties of zeolite on its aluminium content was investigated by the use of HZSM-5 and HY with different Si/Al ratios of 30, 50, 80 and 30, 60, respectively.
2. Results and discussion
2.1. Catalyst characterization
Textural properties of 10 wt% Pd/C catalyst and zeolite solid acids determined by N2 isothermal adsorption–desorption are presented in Table 1. The BET surface area of all catalysts is high (>290 m2 g−1) and the micropore surface area of all catalysts predominates on external surface area. The increase of Si/Al ratio in all the zeolites led to higher BET surface area and pore volume. As depicted in Fig. 1, all the catalysts showed type IV of adsorption isotherm with hysteresis loop H4. The H4 hysteresis loop and nearly horizontal curve of isotherms demonstrate that Pd/C and zeolite solid acids are mostly microporous. Meanwhile, the distribution of meso scale pores in catalysts determined by BJH desorption pore size distribution (Fig. S1†) exhibits that Pd/C has a very broad pore size distribution between 3 and 60 nm. HY zeolites have two pore size distributions of 3–4 nm (very narrow) and 4–50 nm (very broad) which the dominant part of pores have a diameter in the range of 3–4 nm. HZSM-5 (30) and HZSM-5 (50) have also a bimodal distribution with maximum peaking at 3–10 and 3–4 nm, respectively. Substantial part of the mesopore volume found in HZSM-5 (80) was in the range of 3–10 nm.
Table 1 Textural properties of 10 wt% Pd/C and zeolite solid acids
Catalyst |
Pd/C |
HZSM-5 (Si/Al = 30) |
HZSM-5 (Si/Al = 50) |
HZSM-5 (Si/Al = 80) |
HY (Si/Al = 30) |
HY (Si/Al = 60) |
BET surface area (m2 g−1) |
694 |
291 |
326 |
345 |
645 |
664 |
Micropore surface area (m2 g−1) |
390 |
192 |
216 |
214 |
487 |
487 |
External surface area (m2 g−1) |
304 |
99 |
110 |
131 |
158 |
177 |
Pore volume (cm3 g−1) |
0.53 |
0.19 |
0.20 |
0.21 |
0.43 |
0.44 |
Micropore volume (cm3 g−1) |
0.19 |
0.09 |
0.10 |
0.10 |
0.24 |
0.24 |
Mesopore volume (cm3 g−1) |
0.34 |
0.10 |
0.10 |
0.11 |
0.19 |
0.20 |
 |
| Fig. 1 Nitrogen adsorption–desorption isotherms of 10 wt% Pd/C, HY (30), HY (60), HZSM-5 (30), HZSM-5 (50), and HZSM-5 (80). | |
The NH3-TPD curves of HZSM-5 and HY zeolites are shown in Fig. 2. It can be seen from this figure that HZSM-5 (50) and HZSM-5 (80) have two ammonia desorption peaks at low and high temperature regions (Table 2) which belong to weak and strong acid sites, respectively.4,11 These acid sites could be both types of Lewis and Brønsted acids.3,8,21–23 Jin and Li23 professed that Lewis acid sites are dominant at desorption temperature range of 200–300 °C while at 300–450 °C, Brønsted acid sites are the major acid sites of ZSM-5. Desorption temperature is associated to the strength of interaction between ammonia and acid sites; high temperature is required for separation of ammonia adsorbed on strong acid sites. By the increase of Si/Al ratio from 50 to 80, both the low- and high-temperature desorption peaks shifted to lower temperature which means that the acid strength is decreased. HZSM-5 (30) has only one broad desorption peak at low-temperature (221 °C) indicating that its acidic strength is low. Since standard condition volume of ammonia desorbed per gram of catalyst typically signifies the concentration of acid sites,24 HZSM-5 (30) has higher density of acid sites compared to HZSM-5 (50) and HZSM-5 (80) (Table 2). TPD analysis of HY (30) and HY (60) zeolites resulted in only one ammonia desorption peak in the temperatures of 315 and 330 °C, respectively. By increase of Si/Al ratio in HY zeolites, desorption peak moved to higher temperature indicating that acidity is strengthened. Based on a theoretic analysis, Brønsted acid strength of zeolites (
Si–OH–Al
) depends on the composition of second coordination sphere around the spanning OH group; the strongest Brønsted acid site is the one with six Si4+ species in the second coordination sphere around OH group and replacing the Si4+ by Al3+ decreases the acid strength.20 According to the high-temperature desorption peak, it can be concluded that the acid strength of zeolites follows the trend: HZSM-5 (50) ∼ HZSM-5 (80) > HY (60) > HY (30).
 |
| Fig. 2 NH3-TPD curves of HZSM-5 and HY zeolites with different Si/Al ratios. | |
Table 2 Ammonia desorption temperature and amount of desorbed ammonia from zeolite acid sites obtained by TPD analysis
Zeolites |
HZSM-5 (30) |
HZSM-5 (50) |
HZSM-5 (80) |
HY (30) |
HY (60) |
Desorption peak temperature (°C) |
221 |
225 |
382 |
203 |
378 |
315 |
330 |
Volume of desorbed ammonia (ml g−1 STP) |
6.247 |
1.592 |
3.219 |
1.276 |
2.810 |
4.822 |
3.136 |
2.2. Catalytic hydrogenation of phenol
Reactant conversion and product distribution obtained from catalytic hydrogenation of phenol over Pd/C catalyst and combined catalysts of Pd/C and zeolite solid acids are presented in Table 3. Using mixture of Pd/C and zeolite led to higher phenol conversion compared to the use of Pd/C alone. Maximum phenol conversion of 96.89 mol% was achieved over mixed catalyst of Pd/C-HZSM-5 (80) while phenol was converted only 48.05 mol% over Pd/C. By increase in density of acid sites in both zeolites of HZSM-5 and HY (decrease of Si/Al ratio), phenol conversion decreased. This could be due to the fact that higher density of acid sites causes higher formation of coke and zeolite deactivation.4
Table 3 Hydrogenation of phenol over mixed catalysts of Pd/C and zeolite solid acids
Catalyst |
Pd/C-HZSM-5 (80) |
Pd/C-HZSM-5 (50) |
Pd/C-HZSM-5 (30) |
Pd/C-HY (60) |
Pd/C-HY (30) |
Pd/C |
Conversion (mol%) |
96.89 |
68.24 |
49.00 |
53.15 |
50.27 |
48.05 |
Product compounds |
Product selectivity (mol%): (mole of product compound/mole of total product) × 100 |
Benzene |
— |
— |
3.12 |
— |
2.34 |
— |
Cyclohexanone |
70.71 |
75.99 |
76.86 |
87.09 |
85.94 |
83.86 |
Cyclohexanol |
— |
— |
— |
— |
1.14 |
14.35 |
Cyclohexane |
22.83 |
22.14 |
19.97 |
11.11 |
10.40 |
— |
Dicyclohexane |
3.25 |
— |
— |
— |
— |
— |
2-Cyclohexylcyclohexanone |
0.85 |
— |
— |
— |
— |
— |
2-Cyclohexylphenol |
0.57 |
— |
— |
— |
— |
— |
Tetralin |
1.80 |
1.88 |
0.20 |
1.90 |
0.24 |
1.97 |
Reaction mechanisms of phenol hydrogenation on Pd/C or mixed catalysts of Pd/C and zeolite is depicted in Scheme 1. Over Pd/C, hydrogenation of benzene ring of phenol was the main reaction pathway producing cyclohexanone and cyclohexanol (path I); cyclohexanol is the end product since it is not dehydrated in the absence of Brønsted acid sites. The addition of zeolite solid acids to Pd/C led to dehydration of cyclohexanol to cyclohexene (not detected in product samples) and further hydrogenation of cyclohexene on metal catalyst producing cyclohexane as oxygen-free product (path II). Except HY (30), other zeolites dehydrated all produced cyclohexanol to cyclohexene. Low hydrogen pressure of 15 bar in phenol hydrogenation stabilized the production of cyclohexanone intermediate. Our result is in accordance with that of Zhao and Lercher16 who noted that low hydrogen pressure in phenol hydrodeoxygenation stabilizes cycloketone intermediate and decreases cycloalkane formation. Meanwhile, our data reveal that zeolites cannot be involved in hydrogenation mechanism; no conversion of phenol was observed in hydrogenation of phenol over HZSM-5 (80) and HY (60) catalysts without Pd/C, indicating that zeolites do not possess proper active sites for activation of hydrogen molecules to be involved in hydrogenation reaction. In addition, benzene formation was only observed over mixed catalysts of Pd/C-HY (30) and Pd/C-HZSM-5 (30). The proposed reaction pathway for benzene production (path III) is as follows: phenol decarbonylation to cyclopentadiene which is converted to naphthalene via Diels–Alder mechanism,25,26 naphthalene hydrogenation to tetralin, tetralin ring-opening/isomerization to alkyl benzene and dealkylation of alkyl benzene to benzene. High density of acid sites in HY (30) (4.822 ml g−1) and HZSM-5 (30) (6.247 ml g−1) resulted in dealkylation of alkyl benzene and production of benzene. Selectivity toward benzene in the presence of HY (30) and HZSM-5 (30) was 2.34 and 3.12 mol%, respectively. As depicted in Table 3, HZSM-5 was more efficient than HY for catalytic transformation of phenol to cyclohexane. In the case of using HZSM-5 (80), phenol hydrogenation occurred via two reaction pathways; (i) the common pathway of ring hydrogenation of phenol to cyclohexanone and cyclohexanol with subsequent dehydration of cyclohexanol to cyclohexene followed by further hydrogenation of cyclohexene to cyclohexane (paths I and II), (ii) phenol hydrogenation to cyclohexanol and subsequent production of 2-cyclohexylphenol through electrophilic aromatic substitution (EAS) of phenol with cyclohexyl cation followed by further hydrogenation of 2-cyclohexylphenol to 2-cyclohexylcyclohexanone and dicyclohexane (paths I and IV).27 In fact, Brønsted acid sites of zeolite catalyze the alkylation of phenol with cyclohexanol to form 2-cyclohexylphenol.15 Generally, alkylation of phenol by cyclohexanol and production of bicyclic compounds is possible over combined catalysts of acid zeolite and palladium.15 One significant factor for possibility of alkylation reaction is molar ratio of phenol to Pd which should be sufficient to proceed alkylation. At low ratios of phenol to Pd, phenol undergoes hydrogenation rather than alkylation, while at high phenol to Pd ratios and sufficient concentration of cyclohexanol, phenol could be alkylated. Zhao et al.15 reported that at low phenol to Pd molar ratio of 564, only 2.1 C% selectivity of bicyclic products was achieved. In our work, the ratio of phenol to Pd is very low (∼227) which prevents the alkylation mechanism and only by the use of Pd/C mixed with HZSM-5 (80), very low concentrations of bicyclic products were observed. Furthermore, the possibility of phenol alkylation has reverse dependency on density of acid sites; higher density of acid sites favors dehydration reaction rather than alkylation.15 Therefore, bicyclic compounds were only produced over HZSM-5 (80) which has lower density of acid sites compared to HZSM-5 (50) and HZSM-5 (30) (Table 2).
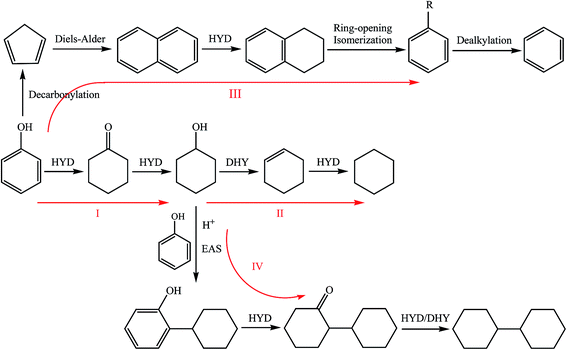 |
| Scheme 1 Reaction pathways of phenol hydrogenation over Pd/C and Pd/C mixed with HZSM-5 or HY zeolites; HDO: hydrodeoxygenation, HYD: hydrogenation, DHY: dehydration, EAS: electrophilic aromatic substitution. | |
2.3. Catalytic hydrogenation of cresol
Results obtained from hydrogenation of o-cresol and m-cresol over 10 wt% Pd/C and zeolite solid acids are presented in Tables 4 and 5. Compared to phenol molecule, the presence of methyl group in cresol favors aromatic production. This is in agreement with the results reported by Massoth et al.28 who showed that higher aromatic yield is achieved from hydrogenation of methyl-substituted phenols rather than phenol over sulfided CoMo/Al2O3 catalyst. Generally, conversion of o-cresol was lower than that of m-cresol; maximum conversion of m-cresol was 76.23 mol% which was achieved over Pd/C-HY (60) while maximum conversion of o-cresol was only 50.65 mol% obtained by Pd/C-HZSM-5 (50). Lower conversion of o-cresol, with the methyl group adjacent to hydroxyl group, could be due to the presence of steric hindrance to adsorption of o-cresol on catalytic active sites. Hydrogenation of o-cresol (Scheme 2) was proceeded through pathways of direct hydrodeoxygenation of cresol to toluene (path III), cresol alkylation to 2,6-dimethylphenol (path IV), and hydrogenation of benzene ring to 2-methylcyclohexanone/2-methylcyclohexanol (path I) followed by dehydration of 2-methylcyclohexanol to methylcyclohexane (path II). In addition to the above mentioned reaction mechanisms for hydrogenation of o-cresol, m-cresol seems to be hydrogenated through some more reaction pathways resulting in some different products (Table 5). The proposed reaction mechanisms for hydrogenation of m-cresol are depicted in Scheme 3. The results obtained in this work indicate that the effects of addition of zeolite solid acids to Pd/C on product selectivity are dependent on the methyl group position in cresol molecule. For instance, zeolite addition did not have negative effect on toluene selectivity in hydrogenation of o-cresol while in m-cresol hydrogenation, zeolite addition led to the decrease of toluene production (except HZSM-5 (30)) due to dehydration, demethylation and alkylation reactions which are competitively occurred to produce methylcyclohexane, phenol and 2-ethylphenol, respectively.
Table 4 Hydrogenation of o-cresol over mixed catalysts of Pd/C and zeolite solid acids
Catalyst |
Pd/C-HZSM-5 (80) |
Pd/C-HZSM-5 (50) |
Pd/C-HZSM-5 (30) |
Pd/C-HY (60) |
Pd/C-HY (30) |
Pd/C |
Conversion (mol%) |
38.16 |
50.65 |
35.90 |
39.38 |
47.75 |
35.20 |
Product compounds |
Product selectivity (mol%): (mole of product compound/mole of total product) × 100 |
Toluene |
29.58 |
29.52 |
29.84 |
19.98 |
18.24 |
16.23 |
Methylcyclohexane |
2.59 |
2.09 |
1.83 |
— |
— |
— |
2-Methylcyclohexanone |
66.24 |
67.33 |
66.92 |
79.07 |
80.63 |
79.80 |
2-Methylcyclohexanol |
— |
— |
— |
— |
0.33 |
3.96 |
2,6-Dimethylphenol |
1.58 |
1.06 |
1.41 |
0.95 |
0.80 |
— |
Table 5 Hydrogenation of m-cresol over mixed catalysts of Pd/C and zeolite solid acids
Catalyst |
Pd/C-HZSM-5 (80) |
Pd/C-HZSM-5 (50) |
Pd/C-HZSM-5 (30) |
Pd/C-HY (60) |
Pd/C-HY (30) |
Pd/C |
Conversion (mol%) |
48.02 |
66.95 |
39.63 |
76.23 |
42.00 |
39.58 |
Product compounds |
Product selectivity (mol%): (mole of product compound/mole of total product) × 100 |
Toluene |
15.30 |
9.26 |
20.57 |
14.47 |
18.63 |
19.51 |
Methylcyclohexane |
1.48 |
2.87 |
0.22 |
0.20 |
0.97 |
— |
Phenol |
6.80 |
11.19 |
1.24 |
1.00 |
— |
— |
Cyclohexanone |
2.33 |
3.16 |
1.00 |
1.25 |
— |
— |
3-Methylcyclohexanone |
73.61 |
73.40 |
76.50 |
80.79 |
79.73 |
80.00 |
3-Methylcyclohexanol |
— |
— |
— |
— |
0.16 |
1.29 |
2-Ethylphenol |
— |
— |
0.38 |
0.08 |
0.52 |
— |
2-Ethylcyclohexanone |
— |
— |
— |
0.12 |
— |
— |
1,1′-Bicyclopentyl |
0.64 |
— |
— |
— |
— |
— |
1-Butylcyclohexene |
0.34 |
— |
— |
— |
— |
— |
1,1′-Bicyclohexyl, 4,4′-dimethyl |
— |
— |
— |
0.20 |
— |
— |
1-Phenyl-1-cyclohexylethane |
— |
— |
— |
0.14 |
— |
— |
4,4′-Dimethylbiphenyl |
— |
— |
— |
1.76 |
— |
— |
Cyclohexylbenzene |
— |
— |
0.12 |
— |
— |
— |
 |
| Scheme 2 Mechanisms of hydrogenation of o-cresol over combined catalysts of Pd/C and zeolite solid acids. | |
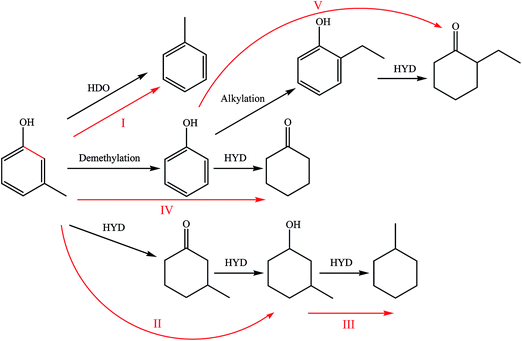 |
| Scheme 3 Mechanisms of hydrogenation of m-cresol over combined catalysts of Pd/C and zeolite solid acids. | |
In o-cresol transformation, catalytic activity of mixed catalysts of Pd/C and zeolite solid acids decreased in the order Pd/C-HZSM-5 (50) > Pd/C-HY (30) > Pd/C-HY (60) > Pd/C-HZSM-5 (80) > Pd/C-HZSM-5 (30) > Pd/C. Hydrogenation of benzene ring of o-cresol to 2-methylcyclohexanone and 2-methylcyclohexanol (Scheme 2, path I) was the dominant reaction mechanism over Pd/C, while the addition of HZSM-5 led to dehydration of 2-methylcyclohexanol and formation of methylcyclohexane as oxygen-free product (path II). Lower density of acid sites in HZSM-5 zeolites led to higher selectivity of methylcyclohexane over mixed catalysts. However, HY zeolites were not selective to the production of methylcyclohexane. This is in agreement with the results obtained by Zhao et al.8 who demonstrated that ketone was selectively formed over HY zeolite in hydrodeoxygenation of 4-n-propylphenol. As is depicted in Scheme 2, HDO of o-cresol to toluene is another reaction mechanism over Pd/C and mixed catalysts (path III). The addition of HZSM-5 strongly affected the selectivity toward toluene while HY did not have remarkable effect on HDO selectivity. It is also inferred from Table 4 that toluene selectivity is not a function of density and strength of zeolite acid sites. The results show that Brønsted acid sites of zeolites were not efficient for dehydration of 2-methylcyclohexanol to methylcyclohexane. Meanwhile, the combination of zeolite solid acids with Pd/C catalyst led to alkylation of o-cresol (path IV) which occurs concurrently with hydrogenation and hydrodeoxygenation reactions.
The study of catalytic hydrogenation of m-cresol over Pd/C and mixed catalysts of Pd/C–zeolite revealed that conversion of m-cresol decreased in the order Pd/C-HY (60) > Pd/C-HZSM-5 (50) > Pd/C-HZSM-5 (80) > Pd/C-HY (30) > Pd/C-HZSM-5 (30) > Pd/C. Direct hydrodeoxygenation (Scheme 3, path I) and benzene ring hydrogenation (path II) were the only reaction mechanisms in hydrogenation of m-cresol over Pd/C. Selectivity towards toluene reduced in the order Pd/C-HZSM-5 (30) > Pd/C-HY (30) > Pd/C > Pd/C-HZSM-5 (80) > Pd/C-HY (60) > Pd/C-HZSM-5 (50). Dehydration of 3-methylcyclohexanol to methylcyclohexane (path III) was activated by zeolite addition and maximum selectivity of methylcyclohexane was obtained in the presence of HZSM-5 (50) which has highest strength of acidity compared to other zeolites. Meanwhile, addition of HZSM-5 zeolites and HY (60) resulted in demethylation of m-cresol to phenol followed by phenol hydrogenation and cyclohexanone formation (path IV). Phenol alkylation to 2-ethylphenol and further hydrogenation of 2-ethylphenol to 2-ethylcyclohexanone was also occurred (path V). High density of acid sites in HZSM-5 (30) and HY (30) favored 2-ethylphenol production. Unlike m-cresol, demethylation mechanism was not occurred in transformation of o-cresol illustrating that the methyl group adjacent to hydroxyl group prevents dealkylation reaction on zeolite acid site. Production of large molecule compounds over HY (60) might be due to the large pore size of this zeolite which allows formation of such large molecules through aromatic ring condensation or isomerization reactions.
2.4. Catalytic hydrogenation of guaiacol
The addition of HZSM-5 and HY zeolites to Pd/C caused enhanced catalytic performance in transformation of guaiacol (Table 6). Compared to HY zeolite, HZSM-5 showed higher catalytic activity, and complete conversion of guaiacol was achieved over mixed catalysts of Pd/C-HZSM-5 (80). Phenol, cyclohexanone and cyclopentanone were the highly selective products of guaiacol hydrodeoxygenation over Pd/C. Reaction mechanisms of guaiacol hydrogenation on Pd/C is depicted in Scheme 4. Benzene ring hydrogenation and dehydroxylation of guaiacol took place to form 2-methoxycyclohexanone (path I) and anisole (path II), respectively. Concurrently, demethoxylation of guaiacol occurred to produce phenol (path III) which was transformed to cyclohexanone/cyclohexanol (path IV), o-cresol/2-methylcyclohexanone (path V) and o-cresol/toluene (path VI) through hydrogenation, methylation–hydrogenation and methylation–dehydroxylation reactions, respectively. o-Cresol could be produced via methylation of phenol with methanol which is formed through demethoxylation of guaiacol. Unusual production of cyclopentanone from guaiacol deoxygenation might be due to ring hydrogenation, ring opening/closing and decarbonylation reactions of catechol (path VII).29 Ring opening reaction is supposed to be catalyzed by metal catalyst.29,30 Since catechol was not detected in product analysis, it can be considered as an intermediate product which was completely consumed during the reaction. In comparison with HY zeolite, HZSM-5 remarkably improved the selectivity toward phenol, and HZSM-5 with higher density of acid sites led to higher phenol selectivity. On the other hand, cyclopentanone formation notably decreased by the addition of HZSM-5 to Pd/C while HY did not show remarkable effect on the selectivity of cyclopentanone. Except HY (60), addition of all other zeolites caused a reduction in dehydroxylation reaction and anisole production. Meanwhile, low concentration or absence of 2-methoxycyclohexanone in product composition observed in guaiacol hydrogenation over Pd/C mixed with zeolites illustrates that the addition of zeolite solid acids to metal catalyst resulted in the reduction of benzene ring hydrogenation of guaiacol.
Table 6 Hydrogenation of guaiacol over mixed catalysts of Pd/C and zeolite solid acids
Catalyst |
Pd/C-HZSM-5 (80) |
Pd/C-HZSM-5 (50) |
Pd/C-HZSM-5 (30) |
Pd/C-HY (60) |
Pd/C-HY (30) |
Pd/C |
Conversion (mol%) |
100.00 |
93.95 |
92.08 |
62.79 |
56.43 |
37.38 |
Product compounds |
Product selectivity (mol%): (mole of product compound/mole of total product) × 100 |
Phenol |
61.07 |
66.87 |
71.08 |
33.61 |
33.03 |
31.91 |
Cyclohexanone |
30.90 |
23.62 |
20.50 |
37.03 |
40.84 |
27.23 |
Cyclohexanol |
— |
— |
— |
— |
— |
4.62 |
Cyclohexane |
0.24 |
0.37 |
0.09 |
0.21 |
0.20 |
— |
Toluene |
1.11 |
1.21 |
1.22 |
2.20 |
3.32 |
2.88 |
Cyclopentanone |
2.91 |
2.88 |
3.12 |
16.37 |
17.35 |
17.97 |
Anisole |
3.36 |
4.44 |
3.15 |
9.89 |
5.02 |
8.85 |
o-Cresol |
0.39 |
0.62 |
0.78 |
— |
0.16 |
0.20 |
2-Methylcyclohexanone |
0.01 |
— |
— |
0.51 |
0.08 |
0.15 |
2-Methoxycyclohexanone |
— |
— |
— |
0.19 |
— |
6.21 |
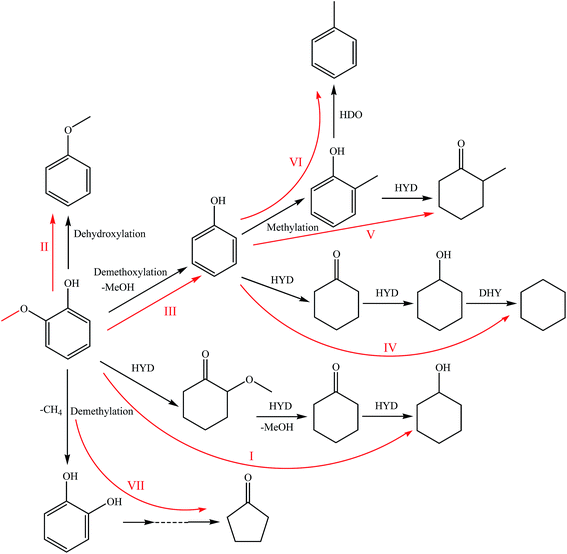 |
| Scheme 4 Reaction mechanisms of guaiacol hydrogenation over 10 wt% Pd/C catalyst and combined catalysts of Pd/C and zeolite solid acids. | |
3. Experimental section
3.1. Chemicals
Phenol (C6H6O, ≥99%), m-cresol (C7H8O, ≥98%), o-cresol (C7H8O, ≥99%), guaiacol (C7H8O2, natural, ≥98%) and 2-isopropylphenol (C9H12O, ≥98%) were purchased from Sigma-Aldrich. Ethyl acetate was purchased from R&M Chemicals. All the chemicals were used as received without any purification. Purified hydrogen and nitrogen were supplied from Linde Malaysia Sdn. Bhd.
3.2. Catalysts
Pd/C (10 wt% loading, matrix activated carbon support) was obtained from Sigma-Aldrich. ZSM-5 (Si/Al of 30, 50 and 80) and Y-zeolite (Si/Al of 30 and 60) were purchased from Zeolyst International. Prior to catalytic activity measurements, all the zeolites were calcined in air at 550 °C overnight.
3.3. Catalyst characterization
BET surface area, pore volume and pore size distribution of fresh samples of Pd/C, HZSM-5 (30), HZSM-5 (50), HZSM-5 (80), HY (30) and HY (60) were determined from the N2 isothermal (−196 °C) adsorption–desorption using Micromeritics ASAP 2020 surface area and porosity analyzer. Before textural analysis, the samples were outgassed at 180 °C under vacuum for 4 h.
The acidity of HZSM-5 and HY was studied by temperature programmed desorption of ammonia (NH3-TPD) on Micromeritics ChemiSorb 2720 instrument using mixed gas of 10%NH3/90%He. 200 mg of each sample was loaded in TPD cell and heated from ambient temperature to 700 °C with a heating rate of 20 °C min−1 and was held at 700 °C for 1 h in a stream of He (20 ml min−1). Then, the sample was cooled down to 210 °C and ammonia was adsorbed after change of gas from pure He to 10%NH3/90%He for 30 min. The sample was purged with He for 30 min to remove physisorbed molecules. Ammonia desorption measurement was carried out from 70 °C to 600 °C with the heating rate of 10 °C min−1 using He carrier gas (20 ml min−1).
3.4. Catalytic activity measurement
Hydrogenation of phenol, o-cresol, m-cresol and guaiacol was conducted in an autoclave batch reactor equipped with a magnetic drive stirrer and water cooling coil (1000 ml volume, maximum temperature and pressure of 500 °C and 100 bar, respectively). Before reaction, mixed catalysts of Pd/C (0.6 g) and calcined zeolite (1 g) were pretreated by hydrogen gas at 300 °C and 20 bar for 1 h. Then, the system was cooled to ambient temperature and pressure was released to atmosphere. Reactant (12 g) and H2O (140 ml) were loaded into the reactor under the inert atmosphere of nitrogen. Hydrogen gas was charged–discharged for four times to displace the nitrogen. Afterward, reactor was pressurized with hydrogen gas to 15 bar and heating was started. Reaction was carried out at 275 °C and stirring speed of 500 rpm. In the beginning of the reaction, total pressure of the system was decreased (from 70 to 66 bar at 275 °C) due to the high activity of catalysts for hydrogenation reaction leading to high hydrogen consumption. After a short while, rate of pressure reduction was decreased due to the decrease of hydrogen consumption rate with the reaction time, and pressure of the reactor was fixed at 64 bar till the end of reaction. After 2 h reaction, reactor was rapidly cooled to ambient temperature and products were collected. Solid catalysts were separated from liquid product by vacuum filtration. Organic phase of product was separated by use of ethyl acetate as solvent and analyzed by GC-MS (Shimadzu QP 2010, DB-5 30 m × 0.25 mm × 0.25 μm) coupled with flame ionization and mass spectrometry detection. The products were identified by using NIST (National Institute of Standards and Technology) library. 2-Isopropylphenol was used as internal standard for quantitative analysis of product samples based on the equation of Cx = Cis(Ax/Ais) which Cx, Cis, Ax and Ais are concentration of component x, concentration of internal standard, peak area of component x and peak area of internal standard, respectively. Conversion and product selectivity were calculated as follows: conversion = (mole of consumed reactant/mole of initial reactant) × 100; selectivity = (mole of a certain product/mole of total product) × 100.
4. Conclusion
The influence of density and strength of acid sites on transformation of different phenolic reactants was studied in a physically mixed catalyst system. In hydrogenation of phenol, o-cresol, m-cresol and guaiacol, the combination of 10 wt% Pd/C catalyst with HZSM-5 (Si/Al of 30, 50 and 80) or HY (Si/Al of 30 and 60) zeolites resulted in enhanced catalytic activity compared to the use of Pd/C alone. Zeolites containing strong acid sites showed better catalytic performance for transformation of phenol, o-cresol, m-cresol and guaiacol. Zeolite solid acids led mostly to the reactions of alkylation, dealkylation and dehydration of cyclic alcohols. In phenol hydrogenation over the combined catalysts, Brønsted acid sites were mainly involved in dehydration of cyclohexanol to form cyclohexane as an oxygen-free product. Hydrogenation reaction selectivity of phenol molecules containing methyl (o-cresol and m-cresol) or methoxy (guaiacol) groups is entirely different from that of the simple phenol molecule. As can be concluded from the data obtained in this research, the presence of methyl and methoxy groups in cresol and guaiacol structures favors direct hydrodeoxygenation mechanism in the hydrogenation reaction. Meanwhile, the position of methyl group and spatial structure of cresol molecules affects the product selectivity of hydrogenation reaction. In conversion of o-cresol, selectivity toward toluene was enhanced by the use of mixed catalysts, while in m-cresol hydrogenation, zeolites led to dealkylation and phenol production and decrease of hydrodeoxygenation. The presence of methoxy group in guaiacol structure resulted in dehydroxylation reaction and anisole production. Demethoxylation was the dominant reaction mechanism in guaiacol transformation over the combined catalysts.
Acknowledgements
The authors wish to acknowledge the Faculty of Engineering at University of Malaya for financial support through the HIR Grant (D000011-16001).
References
- C. Zhao, Y. Kou, A. A. Lemonidou, X. Li and J. A. Lercher, Angew. Chem., Int. Ed., 2009, 48, 3987–3990 CrossRef CAS PubMed.
- M. Selvaraj, K. Shanthi, R. Maheswari and A. Ramanathan, Energy Fuels, 2014, 28, 2598–2607 CrossRef CAS.
- J. He, C. Zhao and J. A. Lercher, J. Catal., 2014, 309, 362–375 CrossRef CAS PubMed.
- S. Echeandia, B. Pawelec, V. L. Barrio, P. L. Arias, J. F. Cambra, C. V. Loricera and J. L. G. Fierro, Fuel, 2014, 117, 1061–1073 CrossRef CAS PubMed.
- S. Boullosa-Eiras, R. Lødeng, H. Bergem, M. Stöcker, L. Hannevold and E. A. Blekkan, Catal. Today, 2014, 223, 44–53 CrossRef CAS PubMed.
- J. Lee, Y. Xu and G. W. Huber, Appl. Catal., B, 2013, 140–141, 98–107 CrossRef CAS PubMed.
- P. S. Rezaei, H. Shafaghat and W. M. A. W. Daud, Appl. Catal., A, 2014, 469, 490–511 CrossRef CAS PubMed.
- C. Zhao, Y. Kou, A. A. Lemonidou, X. Li and J. A. Lercher, Chem. Commun., 2010, 46, 412–414 RSC.
- J. Jae, G. A. Tompsett, A. J. Foster, K. D. Hammond, S. M. Auerbach, R. F. Lobo and G. W. Huber, J. Catal., 2011, 279, 257–268 CrossRef CAS PubMed.
- K. Li, R. Wang and J. Chen, Energy Fuels, 2011, 25, 854–863 CrossRef CAS.
- P. M. Mortensen, J. D. Grunwaldt, P. A. Jensen and A. D. Jensen, ACS Catal., 2013, 3, 1774–1785 CrossRef CAS.
- J. Wildschut, M. Iqbal, F. H. Mahfud, I. M. Cabrera, R. H. Venderbosch and H. J. Heeres, Energy Environ. Sci., 2010, 3, 962–970 CAS.
- J. Wildschut, F. H. Mahfud, R. H. Venderbosch and H. J. Heeres, Ind. Eng. Chem. Res., 2009, 48, 10324–10334 CrossRef CAS.
- F. D. M. Mercader, P. J. J. Koehorst, H. J. Heeres, S. R. A. Kersten and J. A. Hogendoorn, Am. Inst. Chem. Eng., 2011, 57, 3160–3170 CrossRef PubMed.
- C. Zhao, D. M. Camaioni and J. A. Lercher, J. Catal., 2012, 288, 92–103 CrossRef CAS PubMed.
- C. Zhao and J. A. Lercher, ChemCatChem, 2012, 4, 64–68 CrossRef CAS PubMed.
- D. Prochazkova, P. Zamostny, M. Bejblova, L. Cerveny and J. Cejka, Appl. Catal., A, 2007, 332, 56–64 CrossRef CAS PubMed.
- Z. Yu, S. Li, Q. Wang, A. Zheng, X. Jun, L. Chen and F. Deng, J. Phys. Chem., 2011, 115, 22320–22327 CAS.
- B. Smit and T. L. M. Maesen, Nature, 2008, 451, 671–678 CrossRef CAS PubMed.
- A. Primo and H. Garcia, Chem. Soc. Rev., 2014, 43, 7548–7561 RSC.
- J. Kim, M. Choi and R. Ryoo, J. Catal., 2010, 269, 219–228 CrossRef CAS PubMed.
- N. Katada and M. Niwa, Catal. Surv. Asia, 2004, 8, 161–170 CrossRef CAS.
- F. Jin and Y. Li, Catal. Today, 2009, 145, 101–107 CrossRef CAS PubMed.
- D. C. Dayton, M. S. Pavani, J. R. Carpenter and H. M. Von, WO Pat., 089131, 2014.
- X. Nitsch, J. M. Commandreé, P. Clavel, E. Martin, J. Valette and G. Volle, Energy Fuels, 2013, 27, 5459–5465 CAS.
- H. Egsgaard, J. Ahrenfeldt, P. Ambus, K. Schaumburg and U. B. Henriksen, J. Anal. Appl. Pyrolysis, 2014, 107, 174–182 CrossRef CAS PubMed.
- D. Y. Hong, S. J. Miller, P. K. Agrawal and C. W. Jones, Chem. Commun., 2010, 46, 1038–1040 RSC.
- F. E. Massoth, P. Politzer, M. C. Concha, J. S. Murray, J. Jakowski and J. Simons, J. Phys. Chem. B, 2006, 110, 14283–14291 CrossRef CAS PubMed.
- T. Nimmanwudipong, C. Aydin, J. Lu, R. C. Runnebaum, K. C. Brodwater, N. D. Browning, D. E. Block and B. C. Gates, Catal. Lett., 2012, 142, 1190–1196 CrossRef CAS PubMed.
- G. B. McVicker, M. Daage, M. S. Touvelle, C. W. Hudson, D. P. Klein, W. C. Baird Jr, B. R. Cook, J. G. Chen, S. Hantzer, D. E. W. Vaughan, E. S. Ellis and O. C. Feeley, J. Catal., 2002, 210, 137–148 CrossRef CAS.
Footnote |
† Electronic supplementary information (ESI) available. See DOI: 10.1039/c5ra00367a |
|
This journal is © The Royal Society of Chemistry 2015 |
Click here to see how this site uses Cookies. View our privacy policy here.