DOI:
10.1039/C4RA15159C
(Communication)
RSC Adv., 2015,
5, 15940-15943
A binder-free Si-based anode for Li-ion batteries
Received
24th November 2014
, Accepted 28th January 2015
First published on 29th January 2015
Abstract
A binder-free anode for lithium ion batteries consisting of micro-sized silicon particles and polyacrylonitrile (PAN) was prepared. By optimizing the size of the Si particles and the ratio of Si particles to PAN, the performance of the anode was greatly enhanced. Although its columbic efficiency in the first cycle is comparatively lower than that made by traditional methods, it increases to 99% in the 8th cycle, and remains above 99.5% for up to 190+ cycles. Due to its adhesivity and conductance, pyrolyzed PAN (PPAN) can be used both as a binder and the conductive agent at the same time.
Introduction
The development of high energy density batteries continues to be of great interest due to their numerous applications in information technology, consumer electronic devices, electric vehicles, implantable devices and the telecommunications industry.1,2 Developing a low-cost electrode material with a high energy capacity can lead to a significant improvement in the performance and lifetimes of products that use rechargeable batteries. In this regard, considerable efforts have been made to improve the performance of lithium ion batteries (LIBs). Silicon has become an attractive material because of its high theoretical capacity (4200 mA h g−1, ten times higher than graphite),3 low lithium alloying/dealloying potential (about 370 mV vs. Li/Li+),4 long discharge plateau5 and abundance. However, lithium alloying with silicon results in a large volume change (400% in maximum),6 which results in severe cracking in the active material and agglomeration in anode and eventual electrode failure. Several strategies have been developed to accommodate this severe volume expansion, including silicon sub micrometer pillars,7 silicon nanowires,6,8 silicon carbon composite,9 crystalline-amorphous silicon nanowires,10 porous thin films,11 silicon nanowire8,12 and so on. However, the preparation of structured Si material will increase the cost of anode, which hinders the application of the batteries. Facile materials like nanofilms13,14 and nanoparticles15–17 are also studied for Si anode materials, but the matching of binder and conductive agent with active materials is also an intractable issue to be resolved. Here, a binder-free anode composed of Si particles and PAN was prepared. After pyrolysis, there is a transformation in the structure and conductance of PAN. This increases the specific capacity of the battery and avoids the mismatching problems due to the absence of any other insulating binder and conductive agent.
Experimental section
Preparation
PAN was dissolved in dimethylacetamide (DMAC) with a weight ratio of 6.5%, by mixing at a constant temperature of 60 °C for 3 h. Si particles were dispersed in DMAC by ultrasonic. Afterwards, Si and PAN were mixed in different ratios to prepare anode materials. The mixture was stirred by a magnetic stirrer at 50 °C for 6 h to be evenly mixed, and to volatilize redundant solvent. The slurry was then coated on a copper foil with a thickness of 150 μm, followed by heated at 110 °C in a vacuum oven. After pyrolyzed at 550 °C with a heating rate and cooling rate of 2 °C min−1, the anode was ready for cell assembling. Scanning electron microscope (SEM) was utilized to investigate the morphology and uniformity of anode. X-ray photoelectron spectroscopy (XPS) and Fourier transform infrared spectroscopy (FTIR) were used to characterize the structure transformation of PAN through pyrolysis.
Electrochemical measurements
The coin-type half cells (2025R type), with lithium foils as counter electrodes, were assembled in a glove box (Mikrouna Super 1220/750) in the atmosphere of Argon. The electrolyte was LiPF6 (1 M) in ethylene carbonate–methyl ethyl carbonate (EC–EMC, 30
:
70 vol%), with vinylene carbonate (VC) and fluoroethylene carbonate (FEC) as additives. Glass fiber filter or nickel foam were used to stabilize the coin system. The coin-type half cells were cycled at a rate of 0.2 C (1 C = 900 mA h g−1) on land battery test system. The cyclic voltammetry (CV) curves (in the range of 20 mV to 2.7 V and at a rate of 0.1 mV s−1) and electrochemical impedance spectroscopy (EIS, in the range of 100
000 Hz to 0.01 Hz at a magnitude of 0.05 mV) were measured with an electrochemical workstation (PGSTAT302N, Autolab).
Results and discussion
In the process of pyrolysis, the structure of PAN is transformed to a conjugated chain as depicted in Fig. 1. This process was studied by FTIR as shown in Fig. 2. According to the previous reports,18 the –C
N stretch (2250–2500 cm−1) in Fig. 2a and c is due to the side chain of nitrile group in PAN. The disappearance of this stretch in Fig. 2b and d illuminates the disconnection of –C
N after pyrolysis. The peak at about 1265 cm−1 was attributed to the –C
C and/or –C
N and –C–N functional groups in conjugated chain like structure of pyrolyzed PAN. This peak is also observed in the sample of Si particles and PAN before pyrolysis (Fig. 2c) showing the partial structure transformation can happen at 60 °C in the process of stirring. The –CH and CH2 aliphatic stretch at 2800–3000 cm−1 from the hydrocarbon chain polymer backbone is observed for the samples both before and after pyrolysis, indicating that just partial transformation happens in PAN.
 |
| Fig. 1 The schemes of anodes before (a) and after pyrolysis (b). | |
 |
| Fig. 2 FTIR of different anodes. (a) Anode of pure PAN (b) pyrolyzed anode of PAN (c) anode of Si particle and PAN (d) pyrolyzed anode of Si particle and PAN. | |
In the experiments, nano- and micro-sized particles were used as anodes and were both well mixed with PAN (Fig. 3a and c). Clearly the battery composed of micro-sized Si particle as anode shows a better performance. Its columbic efficiency in the first cycle was 66.7%, 29.4% higher than that composed of nano-sized particle, and has better performance in the followed cycles (Fig. 3b and d). Although nano-sized Si particle is commonly considered as an effective method to avoid the short lifetime aroused by volume expansion in the process of discharging,19 in our experiment the micro-sized particles are believed to be conglutinated with the network of PPAN strongly and avoids the agglomeration during the cycling. Anodes composed of micro-sized particles are also advantageous in the larger areal capacity. The results were also compared with that of anode made by traditional method in Fig. 3e and f. Despite the relatively higher columbic efficiency in the 1st cycle, the anode made by traditional method had worse stability in the followed cycles.
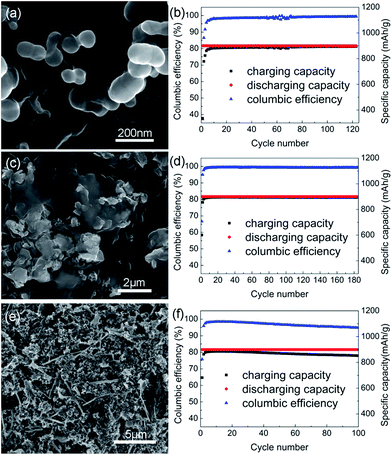 |
| Fig. 3 SEM, columbic efficiency and specific capacity of different anodes, (a and b) Si particle of about 100 nm with PAN, (c and d) Si particle of about 4 μm with PAN, (e and f) anode made by traditional method. | |
In this system, Li-ions are easily intercalated into PPAN but difficultly escaped out as shown by CV result in Fig. 4a. This is the main reason causing the low columbic efficiency in the first cycle. The redox peak at about 1.12 V originates from the Li-ion intercalation into PPAN, while there is not a distinct oxide peak in the process of charging in the voltage range of measurement. From the 2nd cycle, the redox peak is much smaller, indicating that the irreversible capacity do not exist any more.
 |
| Fig. 4 CV spectroscopy of anodes composed of pure PAN (a) and mixture of Si particle and PAN (b). | |
The weight ratio of particle and PAN is a key factor to control the performance of anodes. Three different anodes consisted of Si and PAN with 6
:
4, 5
:
5 and 4
:
6 (labelled as A, B, and C respectively) were used in our experiment. For anode A, the pyrolyzed anode was found to be cracked all over the surface (Fig. 5a) due to the lack of PAN, which also resulted in a low columbic efficiency and unstable cycle performance (Fig. 5b). For samples B and C, the morphology is intact (Fig. 5c and e) and sample B exhibits a better columbic efficiency and capacity density than that of C (Fig. 5d and f). More PPAN in the mixture will induce higher irreversible capacity due to Li-ion insertion into PPAN as discussed above.
 |
| Fig. 5 SEM images, columbic efficiency and specific capacity of anodes A (a and b), B (c and d) and C (e and f). | |
The voltage vs. capacity performance of sample B is shown in Fig. 6a. It can be found that the curves keep almost identical from the 2nd cycle, and obtain a long plateau. The plateaus at about 1.27 V and 0.75–0.5 V in the first cycle are original from reaction of PPAN. The impedance spectroscopy also confirmed the stability of the anode. In the first few circles, the impedance increases slightly due to some breakages of active material for the activation of anode. After this activation process, the impedance decreases greatly, indicating the stability of the anode.
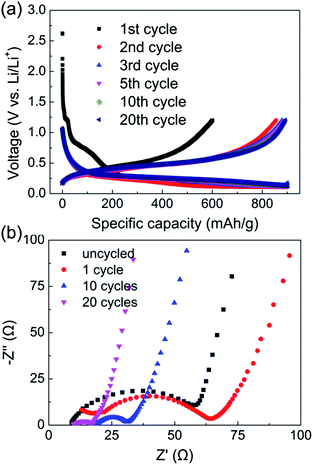 |
| Fig. 6 (a) Voltage vs. specific capacity of anode B. (b) Impedance spectroscopy of anode B after different cycles. | |
Conclusions
A binder-free anode for LIB was prepared. After pyrolysis, PPAN in the anode can act as both conductive agent and binder, which increase the specific capacity, and improve the conductivity for the absence of any other insulating polymer binder. With the optimal size of active material and ratio of Si and PAN, a stable anode with high battery performance was obtained. The columbic efficiency remains 99.5% up to 190+ cycles.
Acknowledgements
This work was supported in part by National Thousand Talents Program of China, the bilateral collaboration project between Chinese Academy of Sciences and Japan Society for the Promotion of Science (Grant no. GJHZ1316), Beijing Natural Science Foundation (Grant no. 2142031), Beijing Municipal Science and Technology Commission project (Grant no. Z141100003814002), the Major State Basic Research Development Program of China (Grant nos 2013CB632103 and 2011CBA00608), and the National High-Technology Research and Development Program of China (Grant nos 2012AA012202 and 2011AA010302).
Notes and references
- B. Kang and G. Ceder, Nature, 2009, 458, 190 CrossRef CAS PubMed.
- P. Simon and Y. Gogotsi, Nat. Mater., 2008, 7, 845 CrossRef CAS PubMed.
- T. Hatchard and J. Dahn, J. Electrochem. Soc., 2004, 151, A838 CrossRef CAS PubMed.
- H. Jung, M. Park, Y.-G. Yoon, G.-B. Kim and S.-K. Joo, J. Power Sources, 2003, 115, 346 CrossRef CAS.
- J. Besenhard, J. Yang and M. Winter, J. Power Sources, 1997, 68, 87 CrossRef CAS.
- C. K. Chan, H. Peng, G. Liu, K. McIlwrath, X. F. Zhang, R. A. Huggins and Y. Cui, Nat. Nanotechnol., 2007, 3, 31 CrossRef PubMed.
- M. Green, E. Fielder, B. Scrosati, M. Wachtler and J. S. Moreno, Electrochem. Solid-State Lett., 2003, 6, A75 CrossRef CAS PubMed.
- H. J. Kim, J. Lee, S. E. Lee, W. Kim, H. J. Kim, D. G. Choi and J. H. Park, ChemSusChem, 2013, 6, 2144 CrossRef CAS PubMed.
- T. Zhang, J. Gao, L. Fu, L. Yang, Y. Wu and H. Wu, J. Mater. Chem., 2007, 17, 1321 RSC.
- L.-F. Cui, R. Ruffo, C. K. Chan, H. Peng and Y. Cui, Nano Lett., 2008, 9, 491 CrossRef PubMed.
- H.-C. Shin, J. A. Corno, J. L. Gole and M. Liu, J. Power Sources, 2005, 139, 314 CrossRef CAS PubMed.
- M. Thakur, R. B. Pernites, N. Nitta, M. Isaacson, S. L. Sinsabaugh, M. S. Wong and S. L. Biswal, Chem. Mater., 2012, 24, 2998 CrossRef CAS.
- H. Choi, C. C. Nguyen and S.-W. Song, Bull. Korean Chem. Soc., 2010, 31, 2519 CrossRef CAS.
- T. Okubo, M. Saito, C. Yodoya, A. Kamei, M. Hirota, T. Takenaka, T. Okumura, A. Tasaka and M. Inaba, Solid State Ionics, 2014, 262, 39 CrossRef CAS PubMed.
- R. Chandrasekaran, A. Magasinski, G. Yushin and T. F. Fuller, J. Electrochem. Soc., 2010, 157, A1139 CrossRef CAS PubMed.
- S.-L. Chou, J.-Z. Wang, M. Choucair, H.-K. Liu, J. A. Stride and S.-X. Dou, Electrochem. Commun., 2010, 12, 303 CrossRef CAS PubMed.
- L.-F. Cui, L. Hu, H. Wu, J. W. Choi and Y. Cui, J. Electrochem. Soc., 2011, 158, A59 CrossRef PubMed.
- Q. Zhao and T. Cao, Ind. Eng. Chem. Res., 2012, 51, 4952 CrossRef CAS.
- H. Li, X. Huang, L. Chen, Z. Wu and Y. Liang, Electrochem. Solid-State Lett., 1999, 2, 547 CrossRef CAS PubMed.
|
This journal is © The Royal Society of Chemistry 2015 |
Click here to see how this site uses Cookies. View our privacy policy here.