DOI:
10.1039/C4RA09014D
(Paper)
RSC Adv., 2014,
4, 43772-43777
Hydrothermal deposition of a zinc oxide nanorod array on a carbon nanotube film as a piezoelectric generator
Received
3rd July 2014
, Accepted 1st September 2014
First published on 3rd September 2014
Abstract
Piezoelectric generators based on zinc oxide (ZnO) nanowires/nanorods require not only an aligned assembly morphology but also Schottky contacts between ZnO and electrodes to rectify the piezoelectric signals. Here we demonstrate that two-dimensional carbon nanotube (CNT) assembly films can serve as highly efficient electrode materials to meet these two requirements. The flexibility, porosity and pore size distribution, and intimate contact with ZnO of CNT films have advantages in controllable hydrothermal deposition to generate highly aligned ZnO nanorods with high crystallinity at a high density. Due to the Schottky characteristics between ZnO and CNT, aluminum and titanium are suggested to serve as the negative electrode of a piezoelectric energy supply, by using their ohmic contacts with ZnO. The three-layered piezoelectric generator outputs a signal of 50–60 mV by using bending deformations, one order of magnitude larger than the signal generated by fast pressing deformations. This study presents a method to design ZnO-based piezoelectric generators without using precious metals or rare earth elements.
Introduction
Piezoelectric generators based on zinc oxide (ZnO) nanostructures have attracted great interest over the last decade.1,2 In principle, the wurtzite structure of ZnO has a non-central crystal structure and therefore allows a piezoelectric effect once the material is strained. The piezoelectric responses can be remarkably high. For example, for a ZnO nanowire with a length of 1200 nm and a hexagonal side length of 100 nm, a tensile force of 85 nN creates a potential drop of ∼0.4 V between the two ends.3 To improve the collection of piezoelectric signals, these ZnO nanowires were highly aligned in many cases. It is also necessary to introduce Schottky diodes across the electrodes contacted with ZnO.4 By controlling the Schottky barrier the output current was found to range from pA to a few nA.5–7 As the electron affinity of ZnO is ∼4.2 eV, high work function metals such as gold (Au), palladium (Pd), and platinum (Pt), and rare earth oxides like indium tin oxide (ITO) are often used to produce a high Schottky barrier, even up to 0.96 eV.8 Therefore, these metals have been widely used in the ZnO piezoelectric and piezo-phototronic generators.3–6,9–13
Herein, without using precious metals or rare earth elements, and by avoiding the complicated multi-layered electrode structure, we report a sandwich metal/ZnO nanorod/carbon nanotube (CNT) piezoelectric generator which takes advantages from the two-dimensional (2D) CNT assembly films. Aluminum (Al) and titanium (Ti) are suggested, because the ohmic ZnO–metal contact and the Schottky ZnO–CNT contact result in asymmetric rectifying that allows a preferential current through ZnO from the CNT electrode to the metal electrode. The controllable and direct deposition of ZnO nanorods on CNT films simplifies the fabrication of piezoelectric generator. The hydrothermal deposition method can also optimize the ZnO–CNT interface and reduce the ZnO–CNT spacing within a tolerance of about 1 μm.14 The high flexibility and processing ability of the 2D CNT assembly15 allow a design to double the piezoelectric effect by depositing ZnO on its two sides. The flexibility of the composite film also makes it possible to enhance the piezoelectric signals up to 50–60 mV by using bending deformations, which is one order of magnitude larger than the signals generated by fast pressing deformations.
Results and discussion
Sandwich structure of piezoelectric generator
The fabrication of sandwich metal/ZnO/CNT piezoelectric generator was schematically shown in Fig. 1. A CNT film was used as one electrode to utilize its flexibility and ability to conduct electrons. By thermally decomposing zinc acetate to form ZnO nanoparticle seeds on the CNT film, ZnO nanorod arrays were uniformly grown from these seeds in an aqueous solution containing zinc nitrate (Zn(NO3)2) or zinc chloride (ZnCl2) and hexamethylenetetramine (HMTA) or ammonium hydroxide (NH3·H2O). The set of overall reactions involves16 |
(CH2)6N4 + 6H2O → 6HCHO + 4NH3
| (1) |
|
NH3 + H2O ⇌ NH4+ + OH−
| (2) |
|
2OH− + Zn2+ ⇌ ZnO + H2O
| (3) |
where HMTA decomposes upon heating to form formaldehyde (HCHO) and ammonia (NH3), then ammonia reacts to produce hydroxide anion (OH−), and OH− finally drives the crystallization of ZnO. The hydrothermal method was used because this route is more convenient and economic than other approaches including vapour–liquid–solid growth, chemical vapour deposition, and electrochemical deposition.16,17 Finally, a 2 μm-thick Al or Ti film was coated by magnetron sputtering to cover the top side of the ZnO nanorod array to form the sandwich structure. The metal film can also be directly covered on the top of the array for a simplified fabrication. The sandwich structure had an area ranging from 2 × 2 to 2.5 × 2.5 cm2 and the edges were fixed by using an insulating paste to avoid the direct connection of two electrodes. The two electrodes were conducted to a current/voltage measurement meter by copper wires with the aid of silver paste.
 |
| Fig. 1 Schematic diagram of the sandwich metal/ZnO/CNT flexible piezoelectric generator. The CNT and metal electrodes can sever as the positive and negative terminals of a piezoelectric power supply. | |
Preparation of CNT films
The CNT films were produced by winding a thin CNT film drawn out of a chemical vapour deposition (CVD) furnace where an injection CVD growth was performed,18 or by a vacuum filtration of CNT suspension,19 and thus were named as the iCNT or sCNT films, respectively. The iCNTs contained mainly double-walled CNTs20 while the sCNTs were many (over 30)-walled.19 The thickness of the iCNT film was 50–80 μm by controlling the winding number, and the sCNT thickness was related to the total amount of CNT suspension and ranged from 100 to 200 μm.
The CNTs were entangled to give the 2D assembly strength, flexibility, and porosity (pore size < 1 μm). Due to the different synthesis methods and the different CNT sizes, the packing densities and pore sizes of the iCNTs and sCNTs differed greatly from each other, see the scanning electron microscopy (SEM) images shown in Fig. 2. The iCNTs had a higher number density and smaller pore sizes than the sCNTs. As a result, the iCNTs had a tensile strength up to 183 MPa, more than one order of magnitude higher than the strength of the sCNTs (<10 MPa), see Fig. 2c. Both the films had also high flexibility (Fig. 2d), making it possible to develop lightweight and flexible multifunctional materials.
 |
| Fig. 2 (a and b) SEM images of two different types of CNT films. The iCNTs (a) were more densified and had smaller pore sizes than the sCNTs (b). (c) The iCNT film had a higher tensile and larger strain at break than the sCNT film. (d) High flexibility of a 1 cm-wide iCNT film. | |
Hydrothermal deposition of ZnO nanorods
We found that the different CNT assembly structures required different deposition conditions. Here we first consider the hydrothermal deposition on sCNT films, whose pore sizes were up to 1 μm. The introduction of ZnO nanoparticle seeds on CNT films was necessary for the deposition. The seeds were formed along the CNTs by thermally decomposing zinc acetate (Zn(CH3COO)2) at 350 °C (see experimental). Fig. 3a shows that the ZnO nanoparticles seeds were uniformly distributed along the CNTs. Without these seeds, it was difficult to grow ZnO nanostructures on the film. Fig. 3b shows the growth result using high concentrations of Zn(NO3)2 and HMTA (0.5 and 1.5 M). Only ZnO particles with lateral sizes over 1 μm were sparsely found on the film. This is because the pore size is one order of magnitude larger than the size of the designed ZnO nanorods (about 80 to 200 nm). Thus it is difficult to anchor ZnO nanorods on the film surface.
 |
| Fig. 3 Hydrothermal deposited ZnO nanostructures. (a) sCNTs with ZnO nanoparticle seeds. (b) Deposition on an sCNT film without using ZnO seeds. (c–h) Deposition on sCNT films under different concentration ratios of Zn(NO3)2 to HMTA. (i and j) Deposition using ZnCl2 as zinc source on an sCNT film and an iCNT film, respectively. | |
The seeds made the growth of ZnO nanorods initialized from them and resulted in intimate contact between ZnO and CNT. For the deposition using Zn(NO3)2 and HMTA, we set the deposition temperature to 90 °C and the reaction time to 10 h while changed the concentration ratio of Zn(NO3)2 to HMTA through a large range.
The optimal ratio should be within 1
:
2 to 1
:
3. According to eqn (3), large concentrations of OH− can accelerate the reaction to produce ZnO. When HMTA was not fully provided, the reaction was not accelerated and there were quite few ZnO nanostructures grown from the seeds, see Fig. 3c where the ratio was 0.2 M
:
0.2 M. When the amount of HMTA was increased, up to a ratio of 0.2 M
:
0.4 M, ZnO nanorods were grown on CNT films, however, with poor alignment (Fig. 3d). By increasing the concentrations with maintaining the ratio, up to 0.5 M
:
1 M, thicker ZnO nanorods were formed on CNT films (Fig. 3e). The nanorods were about 2 to 2.5 μm in length (Fig. 3f), corresponding to an aspect ratio of 30–50. Further increasing the concentrations made the thick nanorods tightly packed with each other (Fig. 3g), and therefore made the composite film rigid and hindered the piezoelectric performance. Thus the Zn2+ concentration was fixed to 0.5 M to prepare the sandwich piezoelectric generators. At the ratio of 0.5 M
:
1.5 M, which was slightly better than the 1
:
2 ratio, ZnO nanorods with moderate size and alignment were obtained, see Fig. 3h.
We also tried different source materials to grow ZnO nanorods, namely ZnCl2 and NH3·H2O. The concentration of the latter was also set to be about quadruple the Zn2+ concentration, to accelerate the reaction according to eqn (3). Fig. 3i shows the results using ZnCl2 as zinc source. As compared to Fig. 3e and h, the nanorods had a similar level of alignment but were slightly larger in diameter.
For the iCNT films, the most significant difference from the sCNTs was the smaller pore size. All the same deposition parameters on the sCNTs were valid for the iCNTs. However, the grown ZnO nanorods were denser and thinner, see Fig. 3j.
Characterization of ZnO nanorods
Fig. 4 shows X-ray diffraction (XRD) results of three sCNT films without or with ZnO nanostructures. The ZnO nanorods had a high level of crystallinity, and all the diffraction peaks can be indexed to wurtzite structure (JCPDS card no. 36-1451). The (002) diffraction peak was much stronger than the others, indicating that the nanorods were highly c-axis oriented and normal to the substrate surface. These features had natural advantages in generating piezoelectric effect.1
 |
| Fig. 4 XRD patterns of three sCNT films without or with ZnO nanostructures. | |
Piezoelectric responses
To investigate the piezoelectric performance of the sandwich film, a pushing force of 30–40 N was applied on the film (either the metal side or the CNT side) with a push–pull force gauge. The contact between the force tip and the film was a circle with a diameter of 1.3 cm. The pushing force can induce a compressive deformation on ZnO nanorods along the c-axis. The piezoelectric signals were also generated by bending the film with hand, as this way can also induce a bending deformation on ZnO nanorods. As a larger deformation can be generated, the bending-induced piezoelectric signals were found to be much higher than the pressing-induced signals. The main text of the article should go here with headings as appropriate.
Fig. 5 shows the measured signals of different sandwich films. The forward and reverse connections were both used in order to show the asymmetric rectifying effect. (In the forward connection, for example, the metal and CNT electrodes of the sandwich film were conducted to the positive and negative terminals of a current/voltage measurement meter.) The pressing-induced voltage pulse was stably up to 3 mV for an Al/ZnO/CNT film (Fig. 5a). The “switching-polarity” tests by using the forward and reverse connections confirmed that the piezoelectric current passed through the ZnO nanorods from the CNT electrode to the Al electrode, indicating the existence of rectifying effect by Schottky contacts. When the bending mode was used, the piezoelectric signals were enhanced by more than one order of magnitude and were larger than 50 mV (Fig. 5b). We suspect that the length of ZnO nanorods played an important role in determining the magnitude of piezoelectric responses. The small aspect ratio (30–50) resulted in a high ability to resist external normal loads, whereas it was not difficult to introduce a bending deformation.7 (Notice that due to this aspect ratio, we prefer to call the nanostructures as nanorods rather than nanowires.)
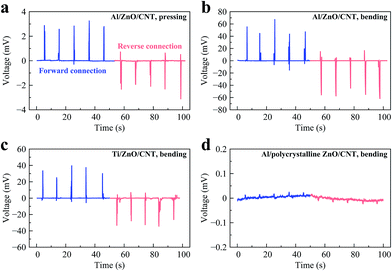 |
| Fig. 5 Piezoelectric responses of different metal/ZnO/CNT sandwich films. (a and b) The pressing-induced and bending-induced piezoelectric voltages of an Al/ZnO/CNT film. (c) The bending-induced responses of a Ti/ZnO/CNT film. (d) The responses were negligible when the polycrystalline ZnO nanostructures were used. Here sCNT films were used to deposit ZnO nanostructures. | |
The use of Ti electrode instead of Al showed the same ability to rectify the piezoelectric signals (Fig. 5c). However, when the ZnO nanostructures were no longer aligned, the polycrystallinity annihilated the piezoelectric responses to be below 0.01 mV (Fig. 5d). These polycrystalline nanostructures had a thickness of hundreds of nm to 1 μm, and were formed on an sCNT film by a fast magnetron sputtering deposition method.
Schottky contact between CNT and ZnO
The selection of Al and Ti in this study is due to their low work functions of 4.28 and 4.33 eV, respectively. This means that the ZnO–metal contacts were ohmic as the electron affinity of ZnO is also about 4.2 eV. Therefore, the rectifying effect should be provided by the contact between ZnO and CNT, according to the experimental and theoretical predictions of 4.95–5.05 eV for the CNT’s work function.21,22 Fig. 6 shows the I–V measurement of an Al/ZnO/CNT film, where asymmetric characteristics was clearly observed. As such measurement was a collective response of a large number of ZnO nanorods, there was no plateau with zero current that usually existed in the I–V curve of a single ZnO nanorod/nanowire.7 Interestingly, the fast increase in current took place at voltage below ∼0.3–0.4 V, indicating that the possible largest piezoelectric signals can be up to hundreds of mV, one order of magnitude larger than the present results.
 |
| Fig. 6 Asymmetric I–V curve of an Al/ZnO/CNT film. | |
Piezoelectricity against change in resistance
In applications, the pressing or bending deformations might be maintained rather than being released immediately. Therefore we designed a new method to characterize the piezoelectric signals, as shown in Fig. 7. First, all the deformations were maintained or released for 10 s, therefore the piezoelectric signals should be generated only at the beginning or the release of a new deformation. Second, a constant electric current (I) was applied to pass through the sandwich structure. As a result, the measured voltage is a sum of the piezoelectric signal (Upiezo) and the Ohm's voltage (IR), where R is the resistance of the film and might vary under deformations. Under I = −0.001 A, the bending deformation caused a change in IR of ∼60 mV (or a decrease in R of ∼60 Ω). Such change was large enough to overlap the positive Upiezo at the beginning of bending. Fortunately, when the bending deformation was released, there existed a negative Upiezo superposing IR. When the current was amplified up to 0.01 A, the change in IR was also amplified up to ∼200 mV. (Here the change in R, ∼20 Ω, was different from the previous result, possibly due to the different bended structures.) As the sign of I was changed, this time the bending-induced positive Upiezo was found to be well superposed upon IR, while the releasing-induced signals were overlapped.
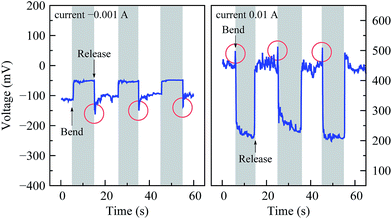 |
| Fig. 7 Piezoelectric responses of an Al/ZnO/CNT film under constant electric currents. The film was bent or released for 10 s in order to maintain the structure changes. | |
The most important observation of Fig. 7 was that the magnitude of piezoelectric signals did not vary with I. This indicates the validation of superposition law and that the deformation-induced voltage signals were indeed piezoelectric.
Experimental
The iCNTs were mainly double-walled20 and were synthesized using an injection CVD growth.18 In the growth, a mixture of ethanol, ferrocene, and thiophene was injected into a heated gas flow reactor (diameter 40 mm) at a feeding rate of 0.15 ml min−1. A gas mixture of Ar and H2 (volume ratio 1
:
1) was also flowed through the reactor tube at a rate of 4000 sccm. The reaction region was set to 1300 °C. The grown CNTs formed a sock-like aerogel in the gas flow and were blown out with the carrier gas. The CNTs were winded on a roller with the aid of liquid densification (ethanol was used here). By controlling the winding number, iCNT films with thickness ranging from 50–80 μm were finally obtained.
The many-walled CNTs were synthesized in the form of aligned arrays by a floating catalyst CVD,19,23 and were called as sCNTs due to the suspension treatment on them. The sCNTs were >30 nm in diameter and about 10–20 μm in lengthen after being sonicated. The sCNTs were dispersed in water with polyoxyethylene (20) sorbitan monooleate (Tween 80) and sonicated at 200 W for 1.5 h with a Bilon-500DL tip sonicator. The sCNT films were prepared by a vacuum filtration with a 40 mm diameter filter membrane. After the filtration, the sCNT films were immersed in acetone for sufficiently long time to get rid of the filter membrane.
To deposit ZnO nanoparticle seeds, both the iCNT and sCNT films were immersed in 0.05 M Zn(CH3COO)2/ethanol solution for 10 s and dried. After being repeated for 3 to 5 times, the film was transferred into a CVD furnace and heated up to 350 °C for 5 min. The thermal decomposition of Zn(CH3COO)2 formed ZnO nanoparticles seeds side along CNT surfaces.
The CNT films were immersed into solutions containing Zn(NO3)2 and HMTA or ZnCl2 and NH3·H2O. The optimal Zn2+ concentration to fabricate aligned and dense ZnO nanorods was 0.4–0.5 M and the corresponding concentration of HMTA or NH3·H2O was about triple the Zn2+ concentration. The hydrothermal deposition was performed at 90 °C for 10 h. Stirring treatment was used during the deposition. The obtained composite films were washed by deionized water.
The piezoelectric signals were recorded by open circuit voltage measurements with a CHI-660C electromechanical workstation (Chenhua Instrument Co., Ltd., Shanghai, China) or Model 4200-SCS semiconductor characterization system (Tektronix, Inc., Beaverton, USA). As the piezoelectric voltages were up to several to tens of mV, several orders of magnitude larger than the precisions, the equipment showed no influence on the measurements. In the pressing mode, a normal force was applied quickly every 10 s on the sandwich structure, and similarly, a bending deformation was applied periodically in the bending mode. Besides the direct measurement of the piezoelectric voltages, the total voltage between two electrodes of the sandwich structure were recorded with passing a constant current I through the electrodes. Therefore, a sum of the piezoelectric signal (Upiezo) and the Ohm's voltage (IR, R the resistance between two electrodes) was detected. This is another way to show the piezoelectricity.
Conclusions
Three-layered piezoelectric generators were fabricated by hydrothermally depositing ZnO nanorods on buckypapers and properly using Al or Ti as the other electrode. This design takes advantages from the Schottky ZnO–CNT contact and possesses high flexibility from the buckypapers. The generator can generate a piezoelectric voltage up to 50–60 mV upon fast bending deformations, much larger than the pressing-induced voltages. Further, the parallel connection can be easily established by depositing ZnO nanorods on the both sides of buckypaper. The present study successfully demonstrated a new strategy to simply the electrode structure and to adopt advantages from CNT as many as possible.
Acknowledgements
This work was supported by the National Natural Science Foundation of China (21273269, 11302241), National Basic Research Program by the Ministry of Science and Technology (2010CB934700), and International Science & Technology Cooperation Project of Jiangsu Province (BZ2011049).
Notes and references
- Z. L. Wang, Adv. Mater., 2012, 24, 4632–4646 CrossRef CAS PubMed.
- Z. L. Wang, Piezotronics and Piezo-Phototronics; Microtechnology and MEMS, Springer-Verlag, Berlin Heidelberg, 2012 Search PubMed.
- Z. Gao, J. Zhou, Y. Gu, P. Fei, Y. Hao, G. Bao and Z. L. Wang, J. Appl. Phys., 2009, 105, 113707 CrossRef PubMed.
- C. S. Lao, J. Liu, P. Gao, L. Zhang, D. Davidovic, R. Tummala and Z. L. Wang, Nano Lett., 2006, 6, 263–266 CrossRef CAS PubMed.
- X. Wang, J. Song, J. Liu and Z. L. Wang, Science, 2007, 316, 102–105 CrossRef CAS PubMed.
- Y. Qin, X. Wang and Z. L. Wang, Nature, 2008, 451, 809–813 CrossRef CAS PubMed.
- R. Yang, Y. Qin, L. Dai and Z. L. Wang, Nat. Nanotechnol., 2009, 4, 34–39 CrossRef CAS PubMed.
- L. J. Brillson and Y. Lu, J. Appl. Phys., 2011, 109, 121301 CrossRef PubMed.
- Z. L. Wang and J. Song, Science, 2006, 312, 242–246 CrossRef CAS PubMed.
- J. Liu, P. Fei, J. Song, X. Wang, C. Lao, R. Tummala and Z. L. Wang, Nano Lett., 2008, 8, 328–332 CrossRef CAS PubMed.
- M.-P. Lu, J. Song, M.-Y. Lu, M.-T. Chen, Y. Gao, L.-J. Chen and Z. L. Wang, Nano Lett., 2009, 9, 1223–1227 CrossRef CAS PubMed.
- J. Bae, Y. J. Park, M. Lee, S. N. Cha, Y. J. Choi, C. S. Lee, J. M. Kim and Z. L. Wang, Adv. Mater., 2011, 23, 3446–3449 CrossRef CAS PubMed.
- F. Zhang, S. Niu, W. Guo, G. Zhu, Y. Liu, X. Zhang and Z. L. Wang, ACS Nano, 2013, 7, 4537–4544 CrossRef CAS PubMed.
- C. J. Hu, Y. H. Lin, C. W. Tang, M. Y. Tsai, W. K. Hsu and H. F. Kuo, Adv. Mater., 2011, 23, 2941–2945 CrossRef CAS PubMed.
- L. Liu, W. Ma and Z. Zhang, Small, 2011, 7, 1504–1520 CrossRef CAS PubMed.
- K. M. McPeak, T. P. Le, N. G. Britton, Z. S. Nickolov, Y. A. Elabd and J. B. Baxter, Langmuir, 2011, 27, 3672–3677 CrossRef CAS PubMed.
- M. Guo, P. Diao and S. Cai, J. Solid State Chem., 2005, 178, 1864–1873 CrossRef CAS PubMed.
- Y. L. Li, I. A. Kinloch and A. H. Windle, Science, 2004, 304, 276–278 CrossRef CAS PubMed.
- Y. Xing, X. Zhang, H. Chen, M. Chen and Q. Li, Carbon, 2013, 61, 501–506 CrossRef CAS PubMed.
- M. Motta, A. Moisala, I. A. Kinloch and A. H. Windle, Adv. Mater., 2007, 19, 3721–3726 CrossRef CAS PubMed.
- M. Shiraishi and M. Ata, Carbon, 2001, 39, 1913–1917 CrossRef CAS.
- W. S. Su, T. C. Leung and C. T. Chan, Phys. Rev. B: Condens. Matter Mater. Phys., 2007, 76, 235413 CrossRef.
- R. Andrews, D. Jacques, A. M. Rao, F. Derbyshire, D. Qian, X. Fan, E. C. Dickey and J. Chen, Chem. Phys. Lett., 1999, 303, 467–474 CrossRef CAS.
|
This journal is © The Royal Society of Chemistry 2014 |
Click here to see how this site uses Cookies. View our privacy policy here.