DOI:
10.1039/C4RA02959C
(Paper)
RSC Adv., 2014,
4, 27522-27525
Au–Fe/Ni alloy hybrid nanowire motors with dramatic speed†
Received
3rd April 2014
, Accepted 28th May 2014
First published on 28th May 2014
Abstract
Au–Fe/Ni alloy nanowire motors, having an average length of 5.4 ± 1.2 μm and a diameter of 280 ± 10 nm, can move fast in a mixed fuel containing H2O2 and N2H4. The powered motion is attributed to the bubble thrust produced from catalytic decomposition of hydrogen peroxide on the Fe/Ni alloy segments, while hydrazine seems to act as a co-catalyst. The regulation of speed can be achieved by modulating the proportion of alloy composition, and the highest speed obtained is up to 850 μm s−1 (ca. 157 body-length per s), which is the fastest among all nanowire motors. Because of the ferronickel segment's magnetism, the Au–Fe/Ni alloy nanomotors also can be guided by the magnetic force, in addition to being controlled by the propelling force generated by the bubble thrust.
Introduction
Drawing inspiration from biomotors, fuel-powered and fuel-free nanomotors have become the focus of nanotechnology.1,2 In 2004, Sen et al. were the first to fabricate Au–Pt nanowire motors.1 In the past decade, considerable advances in nanomotors have offered many opportunities for fabrications;3–6 moreover, with the advanced toxicity research, the nanomotors have been gradually applied in biological surroundings.7,8 The locomotion of most nano-/micro-scale machines is mainly based on the catalytic decomposition of fuel, especially hydrogen peroxide. The efficiency of energy conversion is vital for behaviour of nano-/micro-vehicles. To achieve this purpose, new materials and catalytic reactions are highly desired for fabricating novel nanomotors. Some researchers have paid close attention to diversification of nano-/micro-motors, such as by using mixed fuel with an accelerative effect, magnetic energy, alloy/polymer materials and new forms with nano-tube/ball shaped motors, etc.9–13
In 2008, Wang and co-workers illustrated Pt–Ag/Au alloy nanowire motors with hydrogen peroxide as a fuel, which possessed the fastest speed of 150 μm s−1 (outlier);10 moreover, they also found that Au/Pt-CNT nanomotors could be accelerated to over 200 μm s−1 (outlier) after adding hydrazine (0.15 wt%) to hydrogen peroxide solution (2.5 wt%),11 which was the previous fastest speed among all nanowire motors. Here, we design Au–Fe/Ni alloy nanowire motors (Scheme 1) possessing the highest velocity of all wire-shaped nanomotors in a mixed fuel composed of hydrogen peroxide and hydrazine. The velocity of wire-shaped nanomotor is up to 850 μm s−1 (ca. 157 body-lengths per s) with an average speed that could be more than 350 μm s−1. Note that the content of the mixed fuel can affect the velocities of the alloy nanomotors. The regulation of speed can also be achieved by modulating the proportion of alloy composition. Using their magnetic properties, these nanomotors can not only travel freely in a mixed fuel, but also move directionally guided by an external magnetic field without bubble thrust.
 |
| Scheme 1 Schematic image of Au–Fe/Ni alloy nanomotors. The yellow area represents Au, while the gray area represents Fe/Ni alloy. | |
Experimental section
Synthesis procedure
The Au–Fe/Ni alloy nanowire motors were fabricated by template-directed electroplating (TDEP) (ESI Fig. 1†).14 A porous aluminum oxide membrane (Φ 25 mm, Catalogue no. 6809-6022, Whatman, Maidstone, U.K.) sputtered with a copper layer was used as a working electrode. A Ag/AgCl reference electrode and a platinum wire counter electrode were employed in the electrodeposition process. A copper layer was firstly electrodeposited into the template using a 0.3 M cupric sulfate pentahydrate solution at −0.6 V for 15 min. Then, the pre-plated gold segment was deposited at −0.1 mA for 45 min to avoid the erosion of the sacrificial copper layer. At the end the Au and Fe/Ni alloy segments were subsequently deposited. The Au segment was deposited galvanostatically at −0.5 mA for 90 min, after which the Fe/Ni alloy segment was deposited potentiostatically at −1.3 V for 60 min. The plating solutions of pre-plated gold, Au and ferronickel segment were all homemade. All the chemical reagents in common use were provided by Sinopharm Chemical Reagent Inc (Shanghai, China). After the electrodeposition process, the sacrificial copper layer was erased using a solution containing hydrogen peroxide and hydrochloric acid. Then, the membrane was ultrasonicated in 3.0 M NaOH for 5 min to dissolve aluminium oxide. For purification, the solution was centrifuged in a high speed centrifuge (TGL-16C, Anting, Shanghai, China) at 10
000 rpm for 5 min and washed with ultrapure water (over 18.2 MΩ cm) repeatedly until pH of the solution reached around 7.0. Then, the nanowires were separated from impurities by a magnetic force, and stored in ultrapure water at room temperature.
Characterizations
The nanowires were characterized by scanning electron microscopy (Nova NanoSEM 230, FEI, USA), and the composition of the Fe/Ni alloy segment was determined using an atomic absorption spectrophotometer (TAS-986, Pukinje General, China).
Locomotive behaviour
The locomotive behaviour of nanomotors was observed in (A) hydrogen peroxide solution; (B) hydrazine solution; and (C) a mixed solution containing hydrogen peroxide and hydrazine.
In order to monitor the movement of nanomotors, an upright metallurgical microscope (LEICA DM2500M, Leica Microsystems Inc, Germany) equipped with a digital color camera (TCA-5.0C, Tusen Imaging Inc, China) was employed. TSView 7.1.1.5 software (Tusen Imaging Inc, China) and Avidemux 2.5 software were employed to calculate the speed of nanomotors.15
Magnetic control
We applied an external magnetic field, tracking the locomotion with or without a mixed fuel. In our work, we had rotated the magnetic field by 90°. The upright metallurgical microscope (LEICA DM2500M, Leica Microsystems Inc, Germany) equipped with a digital color camera (TCA-5.0C, Tusen Imaging Inc, China) was employed to monitor the movement of nanomotors.
Results and discussion
Characterizations
The Au–Ni nanomotors are straight, rod-shaped with an average length of 5.4 ± 1.2 μm and an average diameter of 280 ± 10 nm (Fig. 1).
 |
| Fig. 1 SEM image of a single Au–Fe/Ni alloy nanowire motor. Scale bar indicates 5 μm. | |
Co-catalytic system
The Au–Fe/Ni nanomotors are stagnant in either hydrogen peroxide or hydrazine (Fig. 2A & B), and only move fast in the mixed fuel of hydrogen peroxide and hydrazine (Fig. 2C). Here, hydrazine is not stimulative but necessary for the movement of Au–Fe/Ni vehicles, which is different from hydrazine's accelerative effect for the motion of an Au/Pt-CNT nanomotor (from 50 to 200 μm s−1).10,16,17 However, the nanomotors cannot travel in the hydrazine; thus, the reaction's mechanism is not the same as that of the Ir–SiO2 Janus micromotors in 10−3–10−7 wt% hydrazine,18 or ferronickel's catalytic effect for the hydrazine at 70 °C.19 For Au–Fe/Ni nanomotors in the mixed fuel, hydrazine seems to act as an unconsumable co-catalyst while the hydrogen peroxide is reduced, and the catalytic decomposing reaction is supposedly as follows:
 |
| Fig. 2 (A & B) No obvious locomotion of Au–Fe/Ni nanomotors in the water solution of (A) only hydrogen peroxide or (B) only hydrazine. (C) Ultrafast movement of nanomotors in the mixed fuel composed of hydrogen peroxide and hydrazine. | |
Different contents of a mixed fuel
We attempted to change the content of hydrazine in the mixed fuel and found that the speeds of alloy nanomotors were accelerated noticeably with increasing concentration of hydrazine in the mixed fuel (Table 1 & Fig. 3).
Table 1 The minimum, maximum and average speed of Au–Fe/Ni alloy nanowires in the mixed fuel of different content. The statistical data of every component is based on 100 nanomotors. (Error limits represent 95% confidence intervals)
Content of mixed fuel |
10.0 wt% H2O2 + 0.01 wt% N2H4 |
10.0 wt% H2O2 + 0.03 wt% N2H4 |
10.0 wt% H2O2 + 0.06 wt% N2H4 |
Minimum speed (μm s−1) |
5.06 |
6.34 |
6.51 |
Maximum speed (μm s−1) |
446.2 |
554.1 |
790.2 |
Average speed (μm s−1) |
139.4 ± 9.1 |
227.6 ± 13.2 |
368.6 ± 16.8 |
 |
| Fig. 3 The velocity distributions of Au–Fe/Ni nanomotors in fuel containing 10.0 wt% hydrogen peroxide and 0.01 (A), 0.03 (B) and 0.06 (C) wt% hydrazine each. The histogram of every composition is based on 100 nanomotors. | |
Bubble-powered behaviours
The catalytically powered motion of the alloy nanomotors is attributed to the bubble thrust generated from the Fe/Ni alloy segments. Some nanomotors move straight along their long axes (ESI Video 2†). In addition, when Au heads of nanomotors land on the base, the ejected bubbles would make them rotate around the Au pivot (ESI Video 3†). As the linear motion interchanges with rotation, different views of the same nanowire swimmers can be observed (ESI Video 4†) Fig. 4.
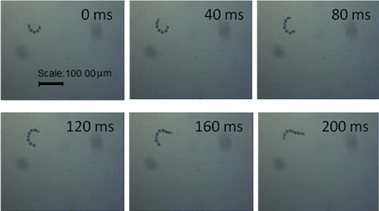 |
| Fig. 4 Movement of an Au–Fe/Ni alloy nanomotor at 0, 40, 80, 120, 160, and 200 ms intervals. The corresponding average speed in this period is as fast as 390 μm s−1. | |
The time-lapse images at 200 ms taken from ESI Video 4† are shown in Fig. 4. The average speed of this nanomotor is 390 μm s−1 in a mixed fuel composed of 10.0 wt% H2O2 and 0.03 wt% N2H4. It has been reported that Ag/Au–Pt alloy nanomotors had an average speed of 113 μm s−1 in 15 wt% hydrogen peroxide.11 This indicated that a larger driving force is generated to propel the nanowire motor compared with Ag/Au–Pt nanowire motors. The corresponding efficiency of energy conversion and the output power of the Au–Fe/Ni nanowire motors are, as expected, higher than those of the Ag/Au–Pt ones.
Alloy composition
Fig. 5 demonstrates the velocity distributions of nanomotors in a fuel containing 10.0 wt% hydrogen peroxide and 0.03 wt% hydrazine. Fig. 5A shows that Au–Fe/Ni nanomotors (obtained from the plating solution of Fe/Ni = 1
:
1) move at an average speed of 130 μm s−1, and their fastest speed is up to 300 μm s−1. When the ratio of Fe/Ni in the plating solution is changed to 1
:
3, the average speed of Au–Fe/Ni nanomotors is ca. 270 μm s−1, and the highest speed is above 850 μm s−1 (Fig. 5B & ESI Video 1†). Our AAS data indicates that alloy plating solution proportion leads to an alloy segment containing about 38 (A) and 43 (B) wt% nickel. The increase in the nickel content in plating solution leads to the faster movement of these alloy nanomotors. However, the velocity of the other Ni-containing nanomotors (Au–Ni) was less than only 10 μm s−1 in 5 wt% hydrogen peroxide,20,21 indicating that the fast speed of our nano-swimmers was attributed to the Fe/Ni alloy segment.
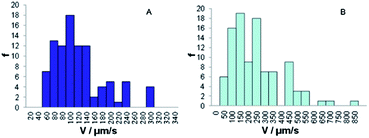 |
| Fig. 5 Histograms show the velocity distributions of nanomotors in fuel containing 10.0 wt% hydrogen peroxide and 0.03 wt% hydrazine. The concentration ratio of Fe/Ni in the alloy plating solutions is 1 : 1 (A) and 1 : 3 (B). The histogram of each composition is based on 100 nanowire motors. | |
Magnetic control
Compared with other alloy nanomotors, the significant characteristics of the Au–Fe/Ni nanovehicles are their magnetic properties; thus, they can be effectively controlled by an external magnetic field. In our research, we found that the magnetized nanowires suspended in water could orient themselves along their long axis and respond sensitively following the applied magnetic field. As shown in Fig. 6(A) and (B), a nanowire motor was attracted straight toward the external magnet (ESI Videos 5†). When Au–Fe/Ni nanoengines were placed in the mixed fuel, a combined movement could be observed, which was dominated by the external magnetic force (MF) and bubble propelling force (PF) together, as described in Fig. 6(C) and (D) (ESI Video 6†).
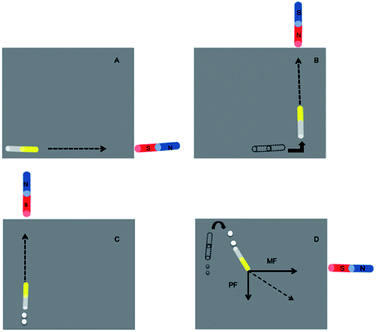 |
| Fig. 6 (A) An Au–Fe/Ni nanowire oriented itself toward the external magnet; (B) the orientation of nanowire was switched using a rotating magnet at 90°; (C) combined movement of a nanowire as the propelling force (PF) and the magnetic force (MF) is aligned; (D) combined movement of a nanowire as the propelling force (PF) and the magnetic force (MF) is not aligned. | |
Conclusions
In this work, Fe/Ni alloy is firstly utilized for substituting Pt to fabricate Au–Fe/Ni nanomotors. The alloy nanowire motors possess the wire-shaped nanomotors' fastest speed, which is up to 850 μm s−1 (ca. 157 body-length per s), in a mixed fuel containing hydrogen peroxide and hydrazine. The powered motion is attributed to the bubble thrust produced from catalytic decomposition of hydrogen peroxide on the Fe/Ni alloy segments, while hydrazine seems to act as a co-catalyst. The regulation of speed can be achieved by modulating the proportion of alloy composition. Using their magnetic properties, the Au–Fe/Ni hybrid nanomotors can be controlled by both bubble thrust and an external magnetic force. The ultrafast catalytically/magnetically hybrid nanomotors adapting to different situations would play an important role in various tasks in the near future.
Acknowledgements
This work was supported by National Basic Research Program of China (no. 2010CB732403), the National Science Foundation of China (nos 21275030), and the Program for Changjiang Scholars and Innovative Research Team in University (no. IRT1116).
Notes and references
- W. F. Paxton, K. C. Kistler, C. C. Olmeda and A. Sen, et al., J. Am. Chem. Soc., 2004, 126, 13424–13431 CrossRef CAS PubMed.
- W. Wang, L. A. Castro, M. Hoyos and T. E. Mallouk, ACS Nano, 2012, 6, 6122–6132 CrossRef CAS PubMed.
- J. G. Gibbs and Y. P. Zhao, Small, 2009, 5, 2304–2308 CrossRef CAS PubMed.
- R. Liu and A. Sen, J. Am. Chem. Soc., 2011, 133, 20064–20067 CrossRef CAS PubMed.
- J. Wang and W. Gao, ACS Nano, 2012, 6, 5745–5751 CrossRef CAS PubMed.
- M. Guix, J. Orozco, M. García and W. Gao, et al., ACS Nano, 2012, 6, 4445–4451 CrossRef CAS PubMed.
- A. K. Singh, A. K. K. Dey, A. Chattopadhyay, T. K. Mandald and D. Bandyopadhyay, Nanoscale, 2014, 6, 1398–1405 RSC.
- E. L. K. Chng, G. J. Zhao and M. Pumera, Nanoscale, 2014, 6, 2119–2124 RSC.
- F. Z. Mou, C. R. Chen, H. R. Ma and Y. X. Yin, et al., Angew. Chem., 2013, 52, 1–6 Search PubMed.
- U. K. Demirok, R. Laocharoensuk, K. M. Manesh and J. Wang, Angew. Chem., 2008, 120, 9489–9491 CrossRef.
- R. Laocharoensuk, J. Burdick and J. Wang, ACS Nano, 2008, 2, 1069–1075 CrossRef CAS PubMed.
- W. Gao, K. M. Manesh, J. Hua, S. Sattayasamitsathit and J. Wang, Small, 2011, 7, 2047–2051 CrossRef CAS PubMed.
- W. Gao, A. Pei and J. Wang, ACS Nano, 2012, 6, 8432–8438 CrossRef CAS PubMed.
- S. R. Nicewarner-Pena, R. G. Freeman, B. D. Reiss, L. He, D. J. Pena, I. D. Walton, R. Cromer, C. D. Keating and M. J. Natan, Science., 2001, 294, 137 CrossRef CAS PubMed.
- S. Balasubramanian, D. Kagan, C. M. Hu, S. Campuzano, M. J. Lobo-Castañon and N. Lim, Angew. Chem., 2011, 50, 4161–4164 CrossRef CAS PubMed.
- J. S. Moon, K. K. Park, J. H. Kim and G. Seo, Appl. Catal., A, 1999, 184, 41–48 CrossRef CAS.
- D. R. Shankaran and Y. B. Shim, Electroanalysis, 2002, 14, 704–707 CrossRef CAS.
- W. Gao, A. Pei, R. F. Dong and J. Wang, J. Am. Chem. Soc., 2014, 136, 2276–2279 CrossRef CAS PubMed.
- S. K. Singh, A. K. Singh and K. Aranishi, et al., J. Am. Chem. Soc., 2011, 133, 19638–19641 CrossRef CAS PubMed.
- Y. Wang, R. M. Hernandez, T. R. Kline and A. Sen, Langmuir, 2006, 22, 10451–10456 CrossRef CAS PubMed.
- S. Fournier-Bidoz, A. C. Arsenault, I. Manners and G. A. Ozin, Chem. Commun., 2005, 441–443 RSC.
Footnotes |
† Electronic supplementary information (ESI) available: The videos of Au–Fe/Ni alloy nanowire motors' movements and figure about fabricating steps of Au–Fe/Ni nanomotors. See DOI: 10.1039/c4ra02959c |
‡ These two authors contributed equally to the work. |
|
This journal is © The Royal Society of Chemistry 2014 |
Click here to see how this site uses Cookies. View our privacy policy here.