DOI:
10.1039/C4RA02166E
(Paper)
RSC Adv., 2014,
4, 24211-24216
Template-free synthesis of Cu2O–Co3O4 core–shell composites and their application in gas sensing†
Received
12th March 2014
, Accepted 13th May 2014
First published on 13th May 2014
Abstract
Cu2O–Co3O4 core–shell composites were prepared via a hydrothermal method. The influences of the molar ratio of Cu/Co and reaction time on the morphology of Cu2O–Co3O4 core–shell composites were studied in detail. A possible mechanism was proposed on the basis of a series of experiments. Furthermore, these core–shell composites were integrated into a sensorial structure, which exhibited excellent ethanol sensing properties. These properties make the Cu2O–Co3O4 core–shell composites good candidates for ethanol detection.
1. Introduction
Metal oxide semiconductor materials have attracted sustained interest due to their fantastic physical, chemical and other properties. Recently, a lot of efforts, including experimental and theoretical, have been made to study these materials.1–5 It is known that the morphologies and structures of the metal oxide semiconductor materials have significant influence on their electrical, chemical, optical or other properties.6–8 Thus, synthesizing novel materials with well-shaped morphology and structure is of great significance. Hetero-nanostructure composites exhibit good performance in many fields, such as gas sensing and electrocatalytic materials. Core–shell nanostructure, as one of hetero-nanostructure composites, has already been widely applied due to its satisfactory performances.9,10 Moreover, the solution phase route, one method to synthesize hetero-nanostructure oxide composites, is considered to be an efficient method for its low cost, environmental friendliness and controllable structure.
In recent years, the application of nanotechnology in the field of chemosensors has increased rapidly, which results in a growing number of related publications.11,12 A variety of nanomaterials, such as nanoparts and nanorods, have been applied for VOC sensing elements. These nano-sized building blocks provide many merits, including large surface-to-volume ratio and excellent chemical as well as electrical properties.13,14 Cu2O and Co3O4, as two important semiconductor materials, have already been investigated and applied as gas sensor.15–18 Many investigations have demonstrated that hierarchical heterostructural nanomaterials, which are assembled from low dimensional, nano-building blocks, such as 0D nanoparticles, 1D nanowires, nanorods, nanotubes, and 2D nanosheets, exhibit improved gas sensing performance.19–21 Moreover, to the best of our knowledge, there are few reports on synthesis of hierarchical Cu2O–Co3O4 core–shell structures. Thus, the investigation of synthesis of Cu2O–Co3O4 core–shell composites, as well as their gas sensing properties, has important scientific and practical significance.
In this work, we successfully prepared Cu2O–Co3O4 core–shell composites through a hydrothermal method. As far as we know, such novel Cu2O–Co3O4 composites obtained by such a simple method have rarely been reported. In order to understand the formation mechanism of these composites, a series of experiments were conducted. As a potential application, these core–shell composites were applied to a gas sensor, and they exhibited excellent ethanol gas sensing performance.
2. Experimental section
2.1 Chemicals
CuSO4·5H2O, trisodium citrate, and KOH were purchased from Beijing Chemicals Co., Ltd. (Beijing, China). CoCl2·6H2O and glycine were purchased from Xilong Chemical Reagent Co. (Guangdong, China). All of these chemicals were analytical grade and used without any further purification.
2.2 Synthesis of Cu2O–Co3O4 core–shell nanoarchitectures
At first, CuSO4·5H2O (0.5 mmol) was dissolved in a mixture of water (20 ml) and ethanol (13 ml) to form a clear solution, followed by the addition of CoCl2·6H2O (1 mmol), trisodium citrate (Na3Cit) (0.10 g), glycine (0.3 mmol), and KOH (3.0 ml, 200 mmol). The mixture was stirred vigorously for 30 min, and then transferred to a Teflon-lined stainless-steel autoclave (50 ml capacity). The autoclave was heated and maintained at 180 °C for 10 h, and then cooled to room temperature. The resulting precursor was washed several times and dried in vacuum at 60 °C for 4 h. Then, the obtained powders were calcined in air at 300 °C for 2 h, and Cu2O–Co3O4 core–shell composites were prepared.
2.3 Sample characterization
X-ray diffraction (XRD) analysis was conducted on a Scintag XDS-2000 X-ray diffractometer with Cu Kα radiation (λ = 1.5418 Å). X-ray photoelectron spectroscopy (XPS) data was obtained with a VG ESCALAB MK II spectrometer with an Mg KR excitation (1253.6 eV). Scanning electron microscopy (SEM) images were performed on a SHIMADZU SSX-550 (Japan) instrument. N2 adsorption–desorption isotherms were measured at 77 K on a Micromeritics ASAP2000 system. Surface area and pore-size distribution were evaluated using Brunauer–Emmett–Teller (BET) and Barrett–Joyner–Halenda (BJH) methods, respectively (Quantachrome Instruments AUTOSORB-1, Boynton Beach, FL).
2.4 Gas sensor fabrication and response test
The as-prepared sample was mixed with deionized water in a weight ratio of 100
:
25 and ground in a mortar for 3 h to form a paste. The paste was then coated on a ceramic tube to form a sensing film (with a thickness of about 300 μm), on which a pair of Au electrodes was previously printed. Pt lead wires were attached to these electrodes and used as electrical contacts. The morphology (variance), which is produced by the “pasting” technique, is the reason for the different signals obtained from the different sensing results processes, as has been obtained in other (previous) publications.22–25 After the ceramic tube was calcined at 300 °C for 2 h, a Ni–Cr heating wire was inserted in the tube to control the operating temperature. The structure of the sensor is shown in Fig. 1a. The details of the sensor fabrication were similar to our previous works.26,27
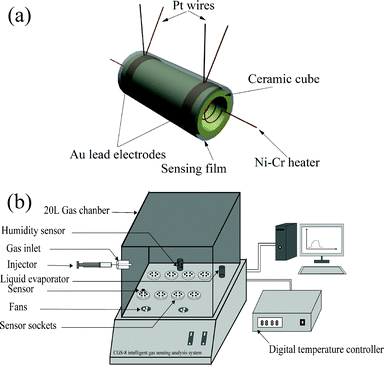 |
| Fig. 1 Schematic illustration of (a) the gas sensor and (b) CGS-8 intelligent gas sensing analysis system. | |
Gas sensing properties were measured by a CGS-8 (Chemical gas sensor-8) intelligent gas sensing analysis system (Beijing Elite Tech Co., Ltd., China) (Fig. 1b). The sensors were pre-heated at different operating temperatures for about 30 min. When the resistances of all the sensors were stable, saturated target gas was injected into the test chamber (20 l in volume) by a microinjector through a rubber plug. Our target liquid, i.e. ethanol, was injected into the evaporator to form ethanol vapour. The saturated target gas was mixed with air (relative humidity was about 40%, which was measured by a humidity sensor) by two fans in the analysis system. After the sensor resistances reached a new constant value, the test chamber was opened to recover the sensors in air. All the measurements were performed in a laboratory fume hood in a super-clean room. The sensor resistance and response values were acquired by the analysis system automatically. The response value (R) was defined as R = Rg/Ra, where Ra and Rg denoted the sensor's resistance in the absence and in the presence of the target gases, respectively. The time taken by the sensor to achieve 90% of the total resistance change was defined as the “response time” in the case of response (target gas adsorption) or the “recovery time” in the case of recovery (target gas desorption).
3. Results and discussion
3.1 Characterization of Cu2O–Co3O4 core–shell composites
The crystal phase of Cu2O–Co3O4 core–shell composites was identified by X-ray powder diffraction (XRD), which was shown in Fig. 2a. The curve exhibited sharp diffraction peaks, which indicated the optimal crystallization of Cu2O–Co3O4 core–shell composites. All the peaks in Fig. 2a can be indexed to Co3O4 (JCPDS File no. 42-1467) and Cu2O (JCPDS File no. 78-2076). There were no other clear sharp peaks coincident with those peaks of other impurities. These results confirmed that Cu2O–Co3O4 core–shell composites with relatively high crystal purity were obtained. Moreover, the XPS peaks were indexed to the composite Cu2O–Co3O4 core–shell nanostructures. The binding energy for the C 1s peak (284.7 eV) was used as an internal reference. As depicted in Fig. 2e, peaks centred at 932.7 eV and 952.6 eV correspond to the Cu 2p3/2 and Cu 2p1/2 of Cu2O composites, respectively.28 Similarly, the peak centred at 779.8 eV corresponds to Co 2p3/2 and another one centred at 794.8 eV corresponds to Co 2p1/2. Note that the energy difference between Co 2p3/2 and Co 2p1/2 splitting is 15.0 eV, which indicated the existence of both Co2+ and Co3+.29,30 Moreover, the intensity of Co peaks is higher than that of Cu peak, which possibly confirms that the 2p3/2 and Co 2p1/2 splitting was 15.0 eV, thus confirming the hierarchical core–shell structure. In order to confirm the porosities of the product, the BET surface area and the pore-size distribution of the product were determined by measuring the corresponding nitrogen adsorption–desorption isotherms, which are shown in Fig. 2b. It can be observed that at a high relative pressure, the curve exhibits a type IV isotherm with an H3 hysteresis loop according to Brunauer–Deming–Deming–Teller (BDDT) classification, which indicates the presence of slit-like mesopores (2–50 nm) in our sample.31 The BET surface area of core–shell composites is determined to be 95.1 m3 g−1. The inset is the pore-size distribution of the composites, and most of the pores fall into the size range of 5–50 nm.
 |
| Fig. 2 (a) XRD pattern, (b) typical N2 adsorption–desorption isotherms and pore-size distribution curve (the inset), (c–f) XPS spectra of Cu2O–Co3O4 core–shell nanostructures: (c) full spectrum; (d) Cu 2p; (e) Co 2p; (f) O 1s. | |
The morphology and structure of the as-prepared products were observed by scanning electron microscopy (SEM). Fig. 3a shows the low-magnification of SEM image of the product, from which we can observe that the products consist of relatively uniform Cu2O–Co3O4 composites with diameters from 600 to 800 nm. The high-magnification SEM images shown in Fig. 3b and c provide detailed information of the product's surface, which is assembled from 2D nanosheets (or 1D nanorods) with a thickness of about 10 nm. Fig. 3d shows the SEM image of a broken single microsphere. It could be observed that the microsphere was assembled from a core and shell, which confirm the core–shell structure of the as-prepared products.
 |
| Fig. 3 (a) Low- and (b) high-magnification SEM images of the Cu2O–Co3O4 core–shell nanostructures. (c) High-magnification SEM image of the Co3O4 shell. (d) SEM image of a broken Cu2O–Co3O4 core–shell microsphere. | |
The influence of different molar ratios of Cu/Co on morphology was investigated by varying the molar ratio of Cu/Co (1
:
0, 2
:
1, 1
:
2 and 0
:
1) while keeping the other conditions the same. The SEM images of the products of different molar ratios are shown in Fig. S1.† From Fig. S1,† we can conclude that with the increase of molar ratio of Cu/Co from 1
:
0 to 1
:
2, the petals of the products grew, and the quantity of the as-prepared core–shell products was also increased. The perfect products were obtained at the molar ratio of 1
:
2. When the molar ratio of Cu/Co reaches 0
:
1, there is no core–shell structure observed, which is shown in Fig. S1d.†
In order to study the formation mechanism of the Cu2O–Co3O4 core–shell composites in this work, a series of time-dependent experiments were conducted. Fig. 4a–d exhibited typical results received at 2, 5, 7, 10 h. It was observed that there was rarely shaped product after 3 h (Fig. 4a), and when the time is further increased to 5 h, the cores all grew well and some shells appeared, which are shown in Fig. 4b. With a further increase to 7 h, the most basic core–shell structure had already formed, although Co(OH)2 core–shell composites (Fig. 5d) were completely formed. Fig. 4e showed the product (Cu2O–Co3O4 core–shell composites) of the calcined Cu2O–Co(OH)2 core–shell composites. It could be observed that the surface of Cu2O–Co(OH)2 core–shell composites became rough after being calcined. In order to prove the components of the products obtained above, the XRD patterns of the products were measured and shown in Fig. S2.†
 |
| Fig. 4 SEM images of the morphology evolution at different reaction times: (a) 2 h, (b) 5 h, (c) 7 h, and (d) 10 h. (e) SEM image of the products after being calcined at 300 °C for 1 h. | |
 |
| Fig. 5 Schematic illustration of the formation process of the hierarchical Cu2O–Co3O4 core–shell nanostructures. | |
According to the evidence above, a possible mechanism shown in Fig. 5 may explain the growth of the core–shell composites. Firstly, Cu2O nanoparticles form in the water, and with the presence of Cit3−, they aggregate together to grow into sphere-like shapes.32 Thus, Cit3− is adsorbed on the surface of the Cu2O core. Then, Co2+ is absorbed by Cu2O cores, because Co2+ can chelate with Cit3−. With increase in time, the Co(OH)2 nanosheets form on the surface of the Cu2O cores and the shell eventually forms. After being calcined, the Cu2O–Co(OH)2 core–shell composites transfer to Cu2O–Co3O4 composites. The detailed mechanism for the formation of porous Cu2O–Co3O4 core–shell flower-like structures is still under investigation by our group. Herein is a working hypothesis that agreed well with the electron microscopy and XRD pattern of the obtained products.
3.2 Gas sensing properties
In order to evaluate the optimum operating temperature for Cu2O–Co3O4 core–shell composites, different tests were measured for different target gases. The gas sensor response was collected upon exposure to different target gases under dry air for the operating temperatures from 200 to 400 °C. Fig. 6a shows the sensor responses values as a function of operating temperature for 100 ppm ethanol, acetone and xylene. It was observed that the responses of the tested sensor varied with operating temperature. According to Fig. 6a, 300, 350 and 370 °C were suggested to be the optimum operating temperature for xylene, ethanol and acetone detection, respectively. The maximum response of the sensor to 100 ppm xylene, ethanol and acetone reached 8.7, 17.3 and 6.2. The variation in the optimum operating temperatures for xylene, ethanol and acetone could be understood by the dynamic equilibrium state of the initial adsorption and the subsequent desorption of the gases.33
 |
| Fig. 6 (a) Response of sensor, based on the as-prepared core–shell nanoarchitecture, to 100 ppm xylene, ethanol and acetone as a function of the operating temperature. (b) Response of the sensor versus different ethanol concentrations at 350 °C (the inset shows the corresponding response versus the concentrations from 5–100 ppm). (c) Response transients of the sensor to 50 ppm ethanol gas at 350 °C, τres and τrecov stand for the response time and recovery time, respectively. (d) Response of sensor based on hierarchical Cu2O–Co3O4 core–shell nanostructure to 100 ppm various gases at 350 °C. | |
Fig. 6b shows the responses of the sensor versus different ethanol concentration at 350 °C. According to the curve, we can observe that the response increased with increase in the ethanol concentration from 5 to 500 ppm. When the concentration was below 100 ppm, the response increased relatively fast. When the concentration reached 100 ppm, with a further increase of the ethanol concentration, the response of the sensor gradually tended to saturation. A linear relationship (y = 0.16256x + 1.19849) between the response and ethanol concentration was observed in range of 5–100 ppm. The detection limit of ethanol for the sensor based on the as-prepared Cu2O–Co3O4 core–shell composites was estimated to be approximately 92 ppb, when the criterion for gas detection was set to Rg/Ra > 1.2.
Fig. 6c shows the response behaviour and recovery behavior of the sensor exposed to 50 ppm ethanol at 350 °C. From the curve, we could read out that the response time (τres) and the recovery time (τrecov) were 5 and 22 s, respectively. The τres and τrecov of other ethanol concentrations are shown in Table 1. The responses of the sensor based on Cu2O–Co3O4 core–shell composites to different VOC gases (100 ppm) were measured at the operating temperature of 350 °C, which is shown in Fig. 6d. The result showed that the sensor had an obvious response to ethanol, and less effective response to other tested gases. This indicated that the sensor exhibited excellent ethanol gas sensing properties, which may have excellent selectivity by ANN models.11,34
Table 1 Response and recovery time of the Cu2O–Co3O4 core–shell composites sensor to various concentrations of ethanol at 350 °C
Ethanol conc. (ppm) |
Response time (s) |
Recovery time (s) |
5 |
5 |
10 |
50 |
5 |
22 |
100 |
13 |
35 |
200 |
18 |
41 |
500 |
20 |
44 |
It is known that the hysteresis effect (if large), would mask or cause “artifacts.”35 Thus, we checked the influence of hysteresis effect on our sensor's gas sensing properties, which is shown Fig. 7. It can be observed that the sensor's response to 100 ppm ethanol decreases with the humidity increasing from 11 to 95% RH (adsorption process). When the humidity decreases from 95 to 11% RH (desorption progress), the sensor's response increases. The maximum hysteresis value is less than 5% RH, indicating that the hysteresis effect of the sensor was not too large to influence the application in real-world conditions.
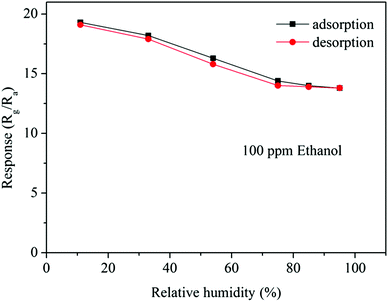 |
| Fig. 7 Humidity hysteresis characteristics of the sensor based on Cu2O–Co3O4 core–shell composites. | |
A comparison between the sensing performances of the sensor and literature reports is summarized in Table 2. To date, many studies have reported ethanol gas sensing properties. It is noteworthy that the sensor fabricated in our work exhibits better sensing performance compared with those reported in the literatures and the commercial ethanol sensor (TGS2620, Figaro Engineering Inc., Japan).17,36,37
Table 2 Comparison of gas-sensing characteristics of the as-prepared ethanol sensors with other ethanol gas sensor
Materials |
Ethanol conc. (ppm) |
Response |
Response time (s) |
Reference |
Cu2O–Co3O4 composites |
100 |
17.3 |
13 |
This work |
Porous Co3O4 microspheres |
100 |
10.5 |
— |
17 |
Au-supported Cu2O nanocubes |
100 |
4.34 |
6 |
36 |
α-Fe2O3/ZnO heterostructures |
100 |
13.0 |
20 |
37 |
Commercial ethanol sensor |
100 |
10 |
— |
TGS2620 (Figaro Engineering Inc., Japan) |
4. Conclusion
In summary, we reported the synthesis of Cu2O–Co3O4 core–shell composites via a hydrothermal method and investigated their ethanol sensing properties. A possible mechanism was proposed on the basis of a series of experiments. An excellent ethanol sensing property was observed. The excellent gas sensing properties can be probably attributed to the synergetic effect of Cu2O and Co3O4, as well as the assembled heterojunction. The results demonstrate that the hierarchical core–shell nanostructure sensor is a potential candidate for high performance ethanol gas sensors.
Acknowledgements
This work was supported by the National Natural Science Foundation of China (Grant no. 61274068, and 61275035), Chinese National Programs for High Technology Research and Development (Grant no. 2013AA030902), Project of Science and Technology Development Plan of Jilin Province (Grant no. 20120324, and 20130206021GX), and the Opened Fund of the State Key Laboratory on Integrated Optoelectronics (no. IOSKL2012KF03).
Notes and references
- J. Elias, C. Lévy-Clément, M. Bechelany, J. Michler, G.-Y. Wang, Z. Wang and L. Philippe, Adv. Mater., 2010, 22, 1607–1612 CrossRef CAS PubMed.
- J. Liu, J. Jiang, C. Cheng, H. Li, J. Zhang, H. Gong and H. J. Fan, Adv. Mater., 2011, 23, 2076–2081 CrossRef CAS PubMed.
- H. Zhang, R. Wu, Z. Chen, G. Liu, Z. Zhang and Z. Jiao, CrystEngComm, 2012, 14, 1775–1782 RSC.
- X. Liu, J. Zhang, Y. Kang, S. Wu and S. Wang, CrystEngComm, 2012, 14, 620–625 RSC.
- X. Xiao, X. Liu, H. Zhao, D. Chen, F. Liu, J. Xiang, Z. Hu and Y. Li, Adv. Mater., 2012, 24, 5762–5766 CrossRef CAS PubMed.
- A. Gurlo, Nanoscale, 2011, 3, 154–165 RSC.
- M. S. Lord, M. Foss and F. Besenbacher, Nano Today, 2010, 5, 66–78 CrossRef CAS PubMed.
- H. N. Tsao, D. Cho, J. W. Andreasen, A. Rouhanipour, D. W. Breiby, W. Pisula and K. Müllen, Adv. Mater., 2009, 21, 209–212 CrossRef CAS.
- S. Zhang, J. Li, T. Wen, J. Xu and X. Wang, RSC Adv., 2013, 3, 2754–2764 RSC.
- C. Locatelli, A. Minguzzi, A. Vertova and S. Rondinini, J. Appl. Electrochem., 2013, 43, 171–179 CrossRef CAS.
- G. Konvalina and H. Haick, Acc. Chem. Res., 2014, 47, 66–76 CrossRef CAS PubMed.
- H. Haick, Y. Y. Broza, P. Mochalski, V. Ruzsanyi and A. Amann, Chem. Soc. Rev., 2014, 43, 1423–1449 RSC.
- Y. Y. Broza and H. Haick, Nanomedicine, 2013, 8, 785–806 CrossRef CAS PubMed.
- Y. Paska, T. Stelzner, S. Christiansen and H. Haick, ACS Nano, 2011, 5, 5620–5626 CrossRef CAS PubMed.
- L. Guan, H. Pang, J. Wang, Q. Lu, J. Yin and F. Gao, Chem. Commun., 2010, 46, 7022–7024 RSC.
- S. Deng, V. Tjoa, H. M. Fan, H. R. Tan, D. C. Sayle, M. Olivo, S. Mhaisalkar, J. Wei and C. H. Sow, J. Am. Chem. Soc., 2012, 134, 4905–4917 CrossRef CAS PubMed.
- C. Sun, S. Rajasekhara, Y. Chen and J. B. Goodenough, Chem. Commun., 2011, 47, 12852–12854 RSC.
- B. Geng, F. Zhan, C. Fang and N. Yu, J. Mater. Chem., 2008, 18, 4977–4984 RSC.
- C. C. Li, X. M. Yin, Q. H. Li and T. H. Wang, CrystEngComm, 2011, 13, 1557–1563 RSC.
- W. Zeng, T. Liu and Z. Wang, J. Mater. Chem., 2012, 22, 3544–3548 RSC.
- S. Zhang, F. Ren, W. Wu, J. Zhou, X. Xiao, L. Sun, Y. Liu and C. Jiang, Phys. Chem. Chem. Phys., 2013, 15, 8228–8236 RSC.
- M. Segev-Bar, G. Shuster and H. Haick, J. Phys. Chem. C, 2012, 116, 15361–15368 CAS.
- Y. Zilberman, U. Tisch, G. Shuster, W. Pisula, X. Feng, K. Müllen and H. Haick, Adv. Mater., 2010, 22, 4317–4320 CrossRef CAS PubMed.
- N. Gozlan, U. Tisch and H. Haick, J. Phys. Chem. C, 2008, 112, 12988–12992 CAS.
- N. Gozlan and H. Haick, J. Phys. Chem. C, 2008, 112, 12599–12601 CAS.
- C. Feng, W. Li, C. Li, L. Zhu, H. Zhang, Y. Zhang, S. Ruan, W. Chen and L. Yu, Sens. Actuators, B, 2012, 166–167, 83–88 CrossRef CAS PubMed.
- W. Li, C. Li, L. Zhu, C. Feng, W. Chen, W. Guo and S. Ruan, Integr. Ferroelectr., 2012, 138, 71–76 CrossRef CAS.
- L. Li, C. Nan, Q. Peng and Y. Li, Chem.–Eur. J., 2012, 18, 10491–10496 CrossRef CAS PubMed.
- J. Xu, P. Gao and T. S. Zhao, Energy Environ. Sci., 2012, 5, 5333–5339 CAS.
- J. Yang, H. Liu, W. N. Martens and R. L. Frost, J. Phys. Chem. C, 2010, 114, 111–119 CAS.
- F. Qu, C. Feng, C. Li, W. Li, S. Wen, S. Ruan and H. Zhang, Int. J. Appl. Ceram. Technol., 2013, 1–7 Search PubMed.
- T. Togashi, H. Hitaka, S. Ohara, T. Naka, S. Takami and T. Adschiri, Mater. Lett., 2010, 64, 1049–1051 CrossRef CAS PubMed.
- Z. Wen and L. Tian-mo, Phys. B, 2010, 405, 1345–1348 CrossRef PubMed.
- B. Wang, J. C. Cancilla, J. S. Torrecilla and H. Haick, Nano Lett., 2014, 14, 933–938 CrossRef CAS PubMed.
- Y. Paska and H. Haick, ACS Appl. Mater. Interfaces, 2012, 4, 2604–2617 CAS.
- Y. Sui, Y. Zeng, L. Fu, W. Zheng, D. Li, B. Liu and B. Zou, RSC Adv., 2013, 3, 18651–18660 RSC.
- C. L. Zhu, Y. J. Chen, R. X. Wang, L. J. Wang, M. S. Cao and X. L. Shi, Sens. Actuators, B, 2009, 140, 185–189 CrossRef CAS PubMed.
Footnote |
† Electronic supplementary information (ESI) available. See DOI: 10.1039/c4ra02166e |
|
This journal is © The Royal Society of Chemistry 2014 |
Click here to see how this site uses Cookies. View our privacy policy here.