DOI:
10.1039/C3RA46514D
(Paper)
RSC Adv., 2014,
4, 8582-8589
Microwave hydrothermal growth of In2S3 interconnected nanoflowers and nanoparticles on graphene for high-performance Li-ion batteries
Received
8th November 2013
, Accepted 16th January 2014
First published on 16th January 2014
Abstract
This paper reports microwave-assisted fast hydrothermal synthesis of In2S3 nanoparticles and unprecedented interconnected nanoflowers on graphene surface. The growth mechanisms for various In2S3-based products are investigated. These obtained In2S3 nanoparticles and nanoflowers are found to be uniformly dispersed on graphene nanosheets, forming sandwiched particle-on-sheet and unprecedented flower-on-sheet nanostructures. When fabricated as anode materials, In2S3–graphene composites show extraordinary large reversible capacities and good cycling performances and high rate capabilities. A reversible initial lithium-extraction capacity of 1249 mA h g−1 is observed for the novel In2S3–graphene flower-on-sheet nanostructure at 70 mA g−1, which can be retained at 913, 782, 690 mA h g−1 at large currents of 700, 1400, 3500 mA g−1 respectively. In comparison, the In2S3–graphene nanoparticle-on-sheet composite shows slightly lower reversible capacities but more stable cycling performances at both small and high currents mainly due to the presence of more graphene.
1. Introduction
Owing to high energy density and long cycle life, the lithium-ion battery has been a popular choice for portable electronic devices and its possible application for stationary energy storage is also promising.1–5 Recently, metal sulfides-based anodes have attracted significant research interest such as In2S3, CoS, SnS2, MnS2, MoS2, etc.6–10 Among them, indium sulfide has been studied for its versatile applications in solar cells, photocatalysts, semiconductor,11–17 and lithium ion batteries.18–24 As an anode material, In2S3 has a large theoretical capacity of 713 mA h g−1, which is substantially larger than commercial graphite anode with a limited capacity of 372 mA h g−1. Flower-like In2S3 microspheres exhibits an initial discharge (lithium insertion) capacity of 1150 mA h g−1 and charge (lithium extraction) capacity of 302 mA h g−1, which decreases to below 100 mA h g−1 after 10 cycles.18 In2S3 nanosheets show substantially higher initial charge capacity of 829 mA h g−1 and a capacity of 450 mA h g−1 can be retained after 40 cycles.19 It is believed that the cycle life of pristine In2S3 nanostructure still needs to be improved in spite of a large reversible capacity.
The capacity fading is mainly ascribed to the large volume change, which results in the electrode pulverization and the loss of the Li-ion storage activities.1,2,5 Carbon coating20 or carbon support21,22 has been suggested as a promising strategy to improve the cycling performance of the electrode materials. This is because carbon is a soft, flexible, conductive material, which is able to relieve the volume change and increases the mechanical stability and electrical contact of the composite.1 As an intriguing carbon material, graphene exhibits superior electrical conductivity, high surface area-to-volume ratio, stable structural flexibility, and chemical stability.25–28 Graphene nanosheets (GNS)-supported anode materials have not only large reversible capacity but also improved cycle life.21,22,29–37
Herein, this paper reports a rapid microwave-assisted hydrothermal method to synthesize In2S3–graphene particle-on-sheet and unprecedented flower-on-sheet nanocomposites. These two composites are also fabricated as anode materials for Li-ion batteries and show very large reversible capacities and good cycling performances and high rate performances.
2. Experimental
2.1 Preparation of In2S3 and In2S3–graphene composites
Graphene nanosheets (GNS) were synthesized by a modified Hummers method as reported elsewhere previously,29,30 except that graphite nanopowders (XF NANO, 40 nm in thickness) were used as the starting graphite to be exfoliated. 0.176 g InCl3·4H2O (Sinopharm Chemical) and 0.0676 g thioacetamide (TAA, Sinopharm Chemical) were dissolved in 15 ml distilled water and stirred for 30 min. 0.03 g hexadecyl trimethyl ammonium bromide (HTAB, Sinopharm Chemical) was added in the above solution and stirred for 15 min. 0.01 or 0.04 g graphene was ultrasonically dispersed in 15 ml deionized water for 30 min, and then mixed with the solution containing InCl3, TAA and HTAB. The mixture was sealed in a specialized glass tube under microwave irradiation at 140 °C (pressure: ∼5.5 bar) for 20 min in a single mode microwave reactor (Nova, EU Microwave Chemistry). In2S3–graphene precipitates were collected by centrifuging and washing with copious de-ionized water before drying at 80 °C. The tawny powders and black powders were obtained as sample A (0.01 g graphene, In2S3–graphene flower-on-sheet) and sample B (0.04 g graphene, In2S3–graphene particle-on-sheet) respectively. The mixed precursor solution was also reacted at 100 °C (pressure: ∼1–1.1 bar), 140 °C, 160 °C (pressure: ∼8.5 bar) for various times (2.5 min, 5 min, 10 min, 20 min, 30 min) to explore the growth process. For materials comparison, pristine In2S3 (yellow color) was prepared following similar experimental procedure in the absence of graphene.
2.2 Materials characterizations
The products were characterized by X-ray diffraction (XRD, Rigaku D/max-2550V, Cu Kα radiation), field-emission scanning electron microscopy (FE-SEM, JSM-6700F) with an energy dispersive X-ray spectrometer (EDS), and transmission electron microscopy/energy dispersive X-ray spectrometer (TEM/EDS, JEOL JEM-200CX and JEM-2010F) in the Instrumental Analysis and Research Center, Shanghai University. The electrical conductivity was measured by a four-electrode method using a conductivity detection meter (Shanghai Fortune Instrument, FZ-2010). The carbon and sulphur elements were measured by a high-frequency infrared carbon–sulphur analyzer (Keguo Instrument, HCS-500P). Raman spectroscopy was recorded on Renishaw in plus laser Raman spectrometer (excitation wavelength: 785 nm, excitation power: 3 mW, spot size: ∼1.2 μm).
2.3 Electrochemical measurements
A N-methyl pyrrolidinone (NMP) slurry consisting of 80 wt% of active anodes, 10 wt% each of carbon black (Super-P) and polyvinylidene fluoride (PVDF, Aldrich) was uniformly applied to a copper foil (0.7 mm). The loading amount of the electrode was kept at ∼2 mg. The coated foil was cut into disk electrodes 11 mm in diameters. The electrodes were vacuum dried overnight at 130 °C followed by compression at 2.0 × 106 Pa.38 They were then assembled into Li test cells using lithium foil (China Energy Lithium) as counter and reference electrode, microporous polypropylene separator, and an electrolyte of 1 M LiPF6 in a 1
:
1 w/w mixture of ethylene carbonate (EC) and diethyl carbonate (DEC). Cell assembly was carried out in a recirculating argon glove box where both the moisture and oxygen contents were below 1 ppm each. Electrochemical measurements were performed on a LAND-CT2001 test system. The Swagelok-type cells were discharged (lithium insertion) and charged (lithium extraction) at a constant current (70 mA g−1, 0.1C, 1C = 700 mA g−1) and higher hourly rates (1C, 2C or 5C) in the fixed voltage range 5 mV to 3.0 V. When the batteries were tested at large currents, the first cycle discharging (lithium insertion) was kept at a small current of 0.1C.
3. Results and discussion
Hydrothermal synthesis has been extensively used to promote preferred nanostructure growth such as nanorod, nanoflower, nanosheet. However it is hard to control the size and morphology uniformity of the product due to its inhomogeneous environment during long reaction times (∼10–24 hours). Single-mode microwave irradiation can offer a homogenous reaction environment, which has been suggested as an effective tool to obtain carbon-supported composites with uniform dispersion and size and morphology control.10,35 This work integrates microwave irradiation and hydrothermal technique to fabricate graphene composites. Notably, the microwave-assisted hydrothermal reaction time is only 20 min, which is substantially reduced compared to common hydrothermal reaction in an electrical oven. Fig. 1a shows the X-ray powder diffraction (XRD) patterns of the products prepared after same microwave irradiation time (20 min) at various temperatures of 100 °C, 140 °C, 160 °C. A few characteristic peaks can be ascribed to (012), (110), (113) and (300) planes, which agrees well with the standard In2S3 (PDF 33-0624).19 TEM images in Fig. 1b–d show the In2S3 products at different heating temperatures. There is slight size growth with the increased heating temperature. It seems that a medium temperature of 140 °C would lead to less agglomerated In2S3 nanoflower products. Therefore the temperature was set to be 140 °C and the effect of reaction time was explored in the following experiments. SEM image in Fig. 2a shows the obtained In2S3 nanoflowers at 140 °C for 20 min. These In2S3 nanoflowers are around several hundred nanometers in size.
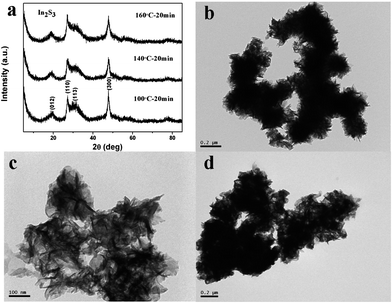 |
| Fig. 1 In2S3 products prepared at various temperatures after 20 min microwave irradiation (a) X-ray diffraction patterns, TEM images: (b) 100 °C, (c) 140 °C and (d) 160 °C. | |
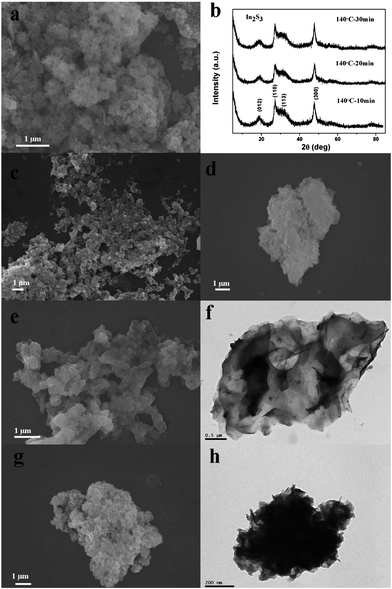 |
| Fig. 2 (a) SEM image of In2S3 at 140 °C after 20 min microwave irradiation, In2S3 products prepared at 140 °C after various microwave irradiation times: (b) X-ray diffraction patterns, (c) SEM image, 2.5 min, (d) SEM image, 5 min, (e) SEM image, 10 min, (f) TEM image, 10 min, (g) SEM image, 30 min and (h) TEM image, 30 min. | |
Fig. 2b shows the X-ray powder diffraction (XRD) patterns of various In2S3 products prepared after 10, 20, and 30 min at 140 °C. There is no apparent change of crystalline structure. All characteristic peaks can be also assigned to In2S3 (PDF 33-0624).19 SEM or TEM images in Fig. 2c–h show various In2S3 products prepared after various reaction times while the temperature was kept same (140 °C). It is clear that the In2S3 products were nanoparticles after very short reaction time (2.5 and 5 min) of microwave irradiation as shown in Fig. 2c and d. Nanosheet nanostructure begun to be observed after 10 min of microwave irradiation (Fig. 2e and f). The In2S3 nanosheet was folded after prolonged reaction time of 20 min, which was driven possibly by heating impetus. It is believed that the nanoflower nanostructure was formed by self-assembly of the folded intermediate product of nanosheets. When reaction time was increased further to 30 min, nanosheets were heavily folded and a heavy agglomeration of many flowers was formed (Fig. 2g and h).
The crystallographic structures of In2S3–graphene (sample A: flower-on-sheet and sample B: particle-on-sheet) were analyzed by X-ray powder diffraction (XRD) in Fig. 3a. A few characteristic (012), (110), (113), and (300) peaks were observed at 2θ = 18.6°, 27.2°, 31.2°, and 48.0° respectively. This is similar to pristine In2S3 product as shown in Fig. 1a and 2b. The (002) peak of graphene is overlapped with (110) peak in the composite. Fig. 3b shows the Raman spectra of graphene and two In2S3–graphene nanocomposites. The presence of graphene in the composite was confirmed. The D/G intensity ratio of carbon was 1.18, indicating that the disordered carbon structure was obtained in the imperfect graphene by the modified Hummer's method.34 This value increased to 1.20 and 1.23 respectively for In2S3–graphene nanoparticle-on-sheet (sample A) and flower-on-sheet (sample B) composites. The more disordered carbon structure in the In2S3–graphene composite may be due to partial insertion of In2S3 into graphene layers.35,36 This can be also confirmed by the pore size distribution and Brunauer–Emmett–Teller (BET) analysis of two In2S3–graphene composites with the nitrogen adsorption–desorption isotherm as shown in Fig. 3c and d. The flower-on-sheet composite displays a dominant pore size of 3.4 nm and a BET surface area of 36.8 m2 g−1 (Fig. 3c). In comparison, the particle-on-sheet composite has a larger surface area of 58.6 m2 g−1 (Fig. 3d), which is mainly ascribed to the presence of more graphene (33.8% graphene) in the particle-on-sheet composite compared to the flower-on-sheet composite (15.7% graphene). A similar mesopore size of ∼3.2 nm is dominant for the particle-on-sheet composite (BJH analysis).
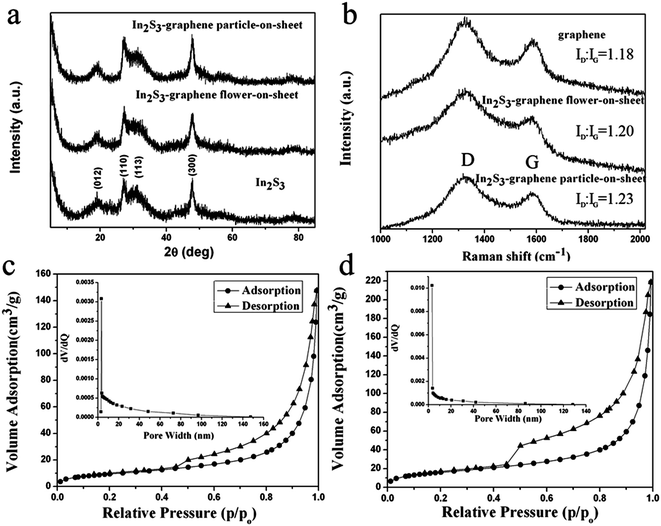 |
| Fig. 3 (a) X-ray diffraction patterns of In2S3–graphene composites (sample A: flower-on-sheet and sample B: nanoparticle-on-sheet); (b) Raman spectrum of graphene nanosheets (GNS) and In2S3–graphene composites; nitrogen adsorption–desorption isotherm and pore size distribution curves; (c) In2S3–graphene flower-on-sheet composite and (d) In2S3–graphene nanoparticle-on-sheet composite. | |
The obtained products were ultrasonically dispersed in ethyl alcohol and then on silicon wafer after drying for SEM measurements. SEM image in Fig. 4a shows very thin graphene nanosheets (GNS) with wrinkled surface. In2S3–graphene flower-on-sheet nanostructure (sample A: 0.01 g graphene) is shown in SEM image (Fig. 4b) and TEM image (Fig. 4d). A large amount of flower-like structure are dispersed uniformly on graphene nanosheets and connected with each other. There is no observation of flower outside graphene support because graphene can bind and immobilize their movements. The corresponding EDS spectra is shown in Fig. 4c, which confirms the presence of C, In and S elements in the composite. Fig. 4e and g show the In2S3–graphene particle-on-sheet composite when more graphene (0.03 g) was used in the synthesis. Interestingly, nanoflower nanostructure was not observed and only a number of nanoparticles were obtained as the final product. As investigated previously,30 there are still many functional groups (carboxyl and hydroxyl) on the chemically-derived graphene surface, which should have a crucial effect in the nucleus formation and crystal growth of In2S3. A similar phenomenon was found in our previous study.10 SnS2 nanoparticles were obtained in the presence of a large amount of graphene although flower structure could be prepared in the absence of graphene.10 The size of In2S3 nanoparticles were about 30–50 nm. The EDS spectra as shown in Fig. 4c also confirms the presence of In2S3 and carbon in the composite. Fig. 5a–f are mapping images of three elements (C, In, S) in two In2S3–graphene composites. In general, three elements are distributed uniformly in the image. It is clear that the carbon content in In2S3–graphene flower-on-sheet (sample A) is less than that of In2S3–graphene particle-on-sheet (sample B) due to the usage of different amount of graphene in the experiment. The results of elemental analysis indicated that the weight percentages of graphene and In2S3 are ∼15.7 wt% and 84.3 wt% in In2S3–graphene flower-on-sheet composite and ∼33.8 wt% and 66.2 wt% in In2S3–graphene particle-on-sheet composite. Remarkably, the In2S3–graphene flower-on-sheet composite is tawny, which is more close to the yellow color of pristine In2S3. However the particle-on-sheet composite is completely black indicating the presence of a large amount of black graphene materials in the composite.
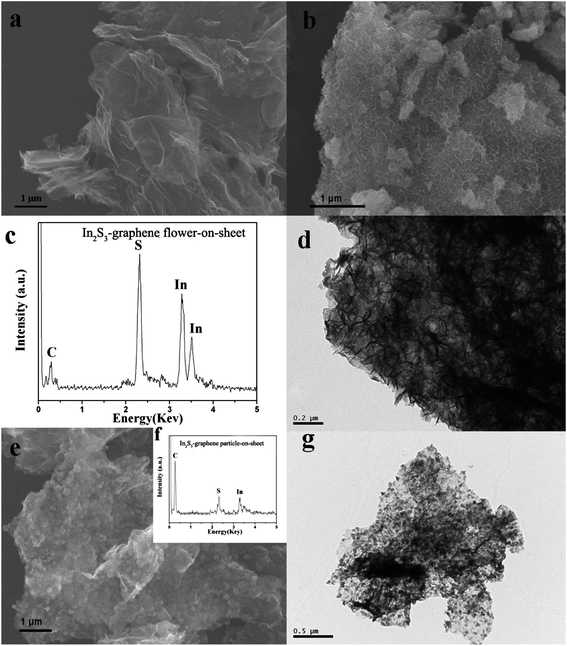 |
| Fig. 4 (a) SEM image of graphene nanosheets (GNS). In2S3–graphene composite (sample A: flower-on-sheet): (b) SEM image, (c) EDS spectra, (d) TEM image. In2S3–graphene composite (sample B: particle-on-sheet): (e) SEM image, (f) EDS spectra and (g) TEM image. | |
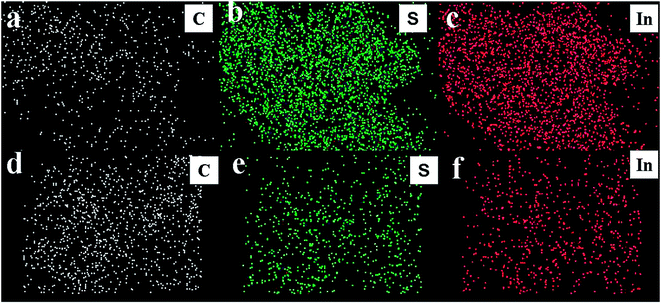 |
| Fig. 5 Element mapping images of (a–c) In2S3–graphene (sample A: 15.7% of carbon and 84.3% of In2S3) and (d–f) In2S3–graphene (sample B: 33.8% of carbon and 66.2% of In2S3). | |
Fig. 6a shows the initial discharge and charge curves of In2S3 and two In2S3–graphene composites (sample A: flower-on-sheet and sample B: particle-on-sheet) at a current density of 70 mA g−1 and a voltage range between 3.0 V and 5 mV. There are a small plateau around 1.5 V and a long slope around 1.0 V for the products. The observed plateau agrees well with a strong cathodic peak at ∼1.5 V as shown in the cyclic voltammetry of In2S3–graphene flower-on-sheet (Fig. 6b). This should be ascribed to the reduction reaction of In2S3 by lithium to form In and Li2S.18–20 The flower-on-sheet and particle-on-sheet composites both displayed high initial charge (lithium extraction) capacities of 1249 mA h g−1 and 1056 mA h g−1 respectively. These values are higher than the theoretical values of both In2S3 (∼713 mA h g−1) and graphene (∼744 mA h g−1), indicating an excellent synergetic effect between graphene and In2S3 in the composite. Notably, such a large charge (lithium extraction) capacity (1249 mA h g−1) is not witnessed in previous In2S3-relative anodes.18–24 This large capacity may be ascribed to those microcavities associated with porous In2S3 nanoflowers and more disordered carbon structure of graphene induced by the partial insertion of In2S3 into graphene layer as confirmed by Raman spectrum (Fig. 3b) and pore size distribution curves (Fig. 3c and d). The initial Coulombic efficiencies of In2S3–graphene flower-on-sheet (sample A) and particle-on-sheet (sample B) were ∼68.6% and 57.4% mainly because of the lithium consumption in the formation of a solid electrolyte interface (SEI) film around In2S3–graphene composites.
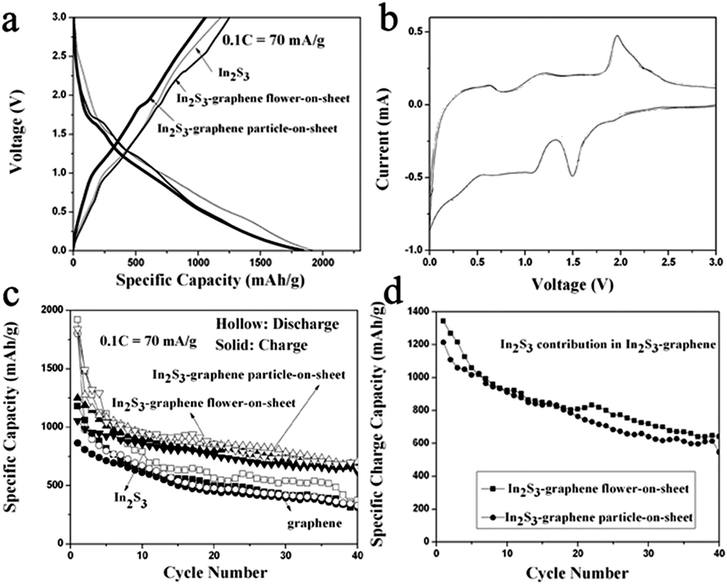 |
| Fig. 6 Electrochemical performances of In2S3–graphene composites at 0.1C (70 mA g−1): (a) the first cycle discharge (lithium insertion) and charge (lithium extraction) curves, (b) cyclic voltammetry of In2S3–graphene flower-on-sheet composite, (c) cycling performances (hollow: discharge, solid: charge) and (d) In2S3 contribution in the composite. The charge capacity of In2S3 contribution was calculated as (composite capacity − graphene capacity × weight fraction of graphene)/(weight fraction of In2S3). | |
Fig. 6c shows the cycling performances of graphene, pristine In2S3, and In2S3–graphene (sample A and sample B) at 70 mA g−1 (0.1C). Pristine In2S3 showed a fast capacity fading during 40 cycles and only a small charge capacity of 381 mA h g−1 was observed at the end of the run. In comparison, In2S3–graphene flower-on-sheet (sample A) and particle-on-sheet (sample B) displayed higher charge capacities of 657 mA h g−1 and 614 mA h g−1 after 40 cycles of discharge and charge. These reversible capacities are more than ∼1.5 times as large as that of pristine In2S3. This substantial cyclability improvement should be ascribed to the presence of graphene matrix in the composite, which can relieve the volume expansion of In2S3 electrode and improve their mechanical stability and electrical contact. On the other hand, the presence of In2S3 in the composite can prevent the agglomeration or reassembly of graphene to graphite platelets. Therefore the unique properties relative to few-layer graphene could be preserved in long-term Li-storage application. Fig. 6d shows the capacity contribution of In2S3 in the composite assuming that graphene in the composite displays same capacities to that of bare graphene during 40 cycling. It is clear that although flower-on-sheet structure has a larger capacity, the cycle life is slightly worse than particle-on-sheet structure. It is suggested that there are many more defects or micro-pores associated with flower-like nanostructure compared to nanoparticle. These spaces can be applied to store an extra amount of lithium ions, which, on the other hand, are harder to be extracted reversibly.1 Moreover, the weight percentage of graphene (33.8%) for nanoparticle-on-sheet composite is more than two times as large as that of flower-on-sheet nanostructure (15.7%). The presence of flexible and robust graphene support should be an important factor for better cycle life in the particle-on-sheet composite despite porous flower may be more suitable to overcome volume change problem.20,26
Fig. 7a and b show the first-cycle discharge (lithium insertion) and charge (lithium extraction) curves of In2S3–graphene flower-on-sheet (sample A) and particle-on-sheet (sample B) composites at large currents of 1C, 2C, 5C (1C = 700 mA g−1). The initial charge capacities of sample A were 913 mA h g−1, 782 mA h g−1 and 690 mA h g−1 at large currents of 700 mA g−1 (1C), 1400 mA g−1 (2C), and 3500 mA g−1 (5C) respectively. Compared to sample A, sample B showed lower charge capacities, but more stable cycling performance as shown in Fig. 7d. For instance, a reversible charge capacity of 522 mA h g−1 was retained after 100 cycles at 1C. The more stable cycling performances of sample B compared to sample A at large currents should be largely ascribed to the presence of more graphene materials in the sample B (33.8% graphene) compared to sample A (15.7% graphene). Graphene can improve the mechanical stability of In2S3 and increase the electrical conductivity in the composite. Therefore reversible and fast enough lithium ions insertion and extraction can be assured during high discharge and charge current rates. As determined by a four-electrode technique, the electrical conductivity of In2S3–graphene particle-on-sheet (sample B) was 0.014 S cm−1, which is ∼three times as large as that of the flower-on-sheet structure (sample A, 0.004 S cm−1). Notably, pristine In2S3 is not conductive and its electrical conductivity is too small to be investigated by the conductivity detection meter.
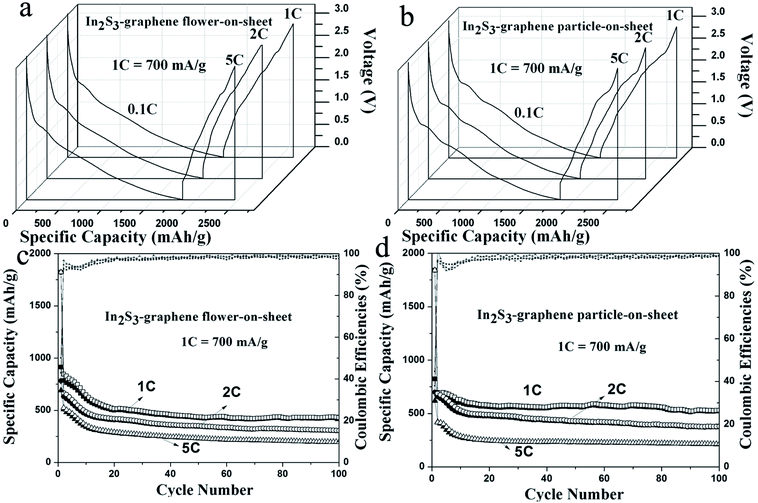 |
| Fig. 7 Electrochemical performances of In2S3–graphene composites at high current rates of 1–5C (1C = 700 mA g−1): (a–b) the first-cycle discharge (lithium insertion) and charge (lithium extraction) curves and (c–d) high-rate cycling performances of In2S3–graphene (hollow: discharge, solid: charge). | |
4. Conclusions
In summary, pristine In2S3 and In2S3–graphene composites were fabricated by a rapid microwave-assisted hydrothermal method in this work. The growth mechanisms of various In2S3 nanostructures and two In2S3–graphene composites (flower-on-sheet and particle-on-sheet) nanostructures were explored. When fabricated as anode materials for Li-ion batteries, two composites showed initially higher-than-theoretical reversible capacities and good cycling performances at both small and high currents. In particular, the unprecedented flower-on-sheet structure showed larger reversible capacities, but slightly worse cycle life compared to the particle-on-sheet structure. The latter also displayed very stable cycling performances at large currents due to the presence of more graphene in the composite.
Acknowledgements
The authors gratefully acknowledge the follow-up Program for Professor of Special Appointment in Shanghai (Eastern Scholar), the National Natural Science Foundation of China (51271105), Shanghai Municipal Government (11JC1403900, 11SG38, S30109) for financial support.
References
- N. A. Kaskhedikar and J. Maier, Lithium storage in carbon nanostructures, Adv. Mater., 2009, 21(25–26), 2664–2680 CrossRef CAS.
- F. L. Cheng, J. Liang, Z. L. Tao and J. Chen, Functional materials for rechargeable batteries, Adv. Mater., 2011, 23(15), 1695–1715 CrossRef CAS PubMed.
- M. G. Kim and J. Cho, Reversible and high-capacity nanostructured electrode materials for Li-ion batteries, Adv. Funct. Mater., 2009, 19(10), 1497–1514 CrossRef CAS.
- Y. Xie and C. Z. Wu, Design of nanoarchitectured electrode materials applied in new-generation rechargeable lithium ion batteries, Dalton Trans., 2007,(45), 5235–5240 RSC.
- C. M. Park, J. H. Kim, H. Kim and H. J. Sohn, Li-alloy based anode materials for Li secondary batteries, Chem. Soc. Rev., 2010, 39(8), 3115–3141 RSC.
- L. Zhang, L. Zhou, H. B. Wu, R. Xu and X. W. Lou, Unusual formation of single-crystal manganese sulfide microboxes Co-mediated by the cubic crystal structure and shape, Angew. Chem., Int. Ed., 2012, 51(29), 7267–7270 CrossRef CAS PubMed.
- Q. Wang, L. Jiao, H. Du, Y. Si, Y. Wang and H. Yuan, Co3S4 hollow nanospheres grown on graphene as advanced electrode materials for supercapacitors, J. Mater. Chem., 2012, 22(40), 21387–21391 RSC.
- Q. Wang, L. Jiao, H. Du, W. Peng, Y. Han, D. Song, Y. Si, Y. Wang and H. Yuan, Novel flower-like CoS hierarchitectures: one-pot synthesis and electrochemical properties, J. Mater. Chem., 2011, 21(2), 327–329 RSC.
- Y. G. Li, H. L. Wang, L. M. Xie, Y. Y. Liang, G. S. Hong and H. G. Dai, MoS2 nanoparticles grown on graphene: an advanced catalyst for the hydrogen evolution reaction, J. Am. Chem. Soc., 2011, 133(19), 7296–7299 CrossRef CAS PubMed.
- Y. Q. Zou and Y. Wang, Sn@CNT nanostructures rooted in graphene with high and fast Li-storage capacities, ACS Nano, 2011, 5(10), 8108–8114 CrossRef CAS PubMed.
- L. Y. Chen, Z. D. Zhang and W. Z. Wang, Self-assembled porous 3D flowerlike-In2S3 structures: synthesis, characterization, and optical properties, J. Phys. Chem. C, 2008, 112(11), 4117–4123 CAS.
- M. A. Franzman and R. L. Brutchey, Solution-phase synthesis of well-defined indium sulfide nanorods, Chem. Mater., 2009, 21(9), 1790–1792 CrossRef CAS.
- X. Zhu, J. Ma, Y. Wang, J. Tao, J. Zhou, Z. Zhao, L. Xie and H. Tian, Fabrication of indium sulfide nanofibers via a hydrothermal method assisted by AAO template, Mater. Res. Bull., 2006, 41(8), 1584–1588 CrossRef CAS PubMed.
- W. Han, L. Yi, N. Zhao, A. Tang, M. Gao and Z. Tang, Synthesis and shape-tailoring of copper sulfide/indium sulfide-based nanocrystals, J. Am. Chem. Soc., 2008, 130(39), 13152–13161 CrossRef CAS PubMed.
- J. Zhou, G. Q. Bian, Y. Zhang, Q. Y. Zhu, C. Y. Li and J. Dai, One-dimensional indium sulfides with transition metal complexes of polyamines, Inorg. Chem., 2007, 46(16), 6347–6352 CrossRef CAS PubMed.
- M. Roy, B. P. Mandal, D. P. Dutta and A. K. Tyagi, A novel ultrasonic method for the preparation of a β-In2S3 nanorod in a CNT nanovessel, Scr. Mater., 2010, 63(1), 93–96 CrossRef CAS PubMed.
- Z. Yang, X. Huang, J. Li, Y. Zhang, S. Yu, Q. Xu and X. Hu, Carbon nanotubes-functionalized urchin-like In2S3 nanostructure for sensitive and selective electrochemical sensing of dopamine, Microchim. Acta, 2012, 177(3–4), 381–387 CrossRef CAS.
- L. Liu, H. Liu, H. Z. Kou, Y. Wang, Z. Zhou, M. Ren, M. Ge and X. He, Morphology control of β-In2S3 from chrysanthemum-like microspheres to hollow microspheres: synthesis and electrochemical properties, Cryst. Growth Des., 2009, 9(1), 113–117 CAS.
- F. Ye, C. Wang, G. Du, X. Chen, Y. Zhong and J. Z. Jiang, Large-scale synthesis of In2S3 nanosheets and their rechargeable lithium-ion battery, J. Mater. Chem., 2011, 21(43), 17063–17065 RSC.
- G. Li and H. Liu, Improved electrode performance of mesoporous β-In2S3 microspheres for lithium ion batteries using carbon coated microspheres, J. Mater. Chem., 2011, 21(45), 18398–18402 RSC.
- J. Choi, J. Jin, J. Lee, J. H. Park, H. J. Kim, D. H. Oh, J. R. Ahn and S. U. Son, Columnar assembly and successive heating of colloidal 2D nanomaterials on graphene as an efficient strategy for new anode materials in lithium ion batteries: the case of In2S3 nanoplates, J. Mater. Chem., 2012, 22(22), 11107–11112 RSC.
- F. Ye, G. Du, Z. Jiang, Y. Zhong, X. Wang, Q. Cao and J. Z. Jiang, Facile and rapid synthesis of RGO–In2S3 composites with enhanced cyclability and high capacity for lithium storage, Nanoscale, 2012, 4(23), 7354–7357 RSC.
- Y. Liu, H. Xu and Y. Qian, Double-source approach to In2S3 single crystallites and their electrochemical properties, Cryst. Growth Des., 2006, 6(6), 1304–1307 CAS.
- A. Kulińska, M. Uhrmacher, R. Dedryvère, A. Lohstroh, H. Hofsäss, K. P. Lieb, A. Picard-Garcia and J. C. Jumas, Lithium insertion into In2S3 studied by perturbed γ–γ angular correlation, J. Solid State Chem., 2004, 177(1), 109–118 CrossRef.
- K. S. Novoselov, A. K. Geim, S. V. Morozov, D. Jiang, Y. Zhang, S. V. Dubonos, I. V. Grigorieva and A. A. Firsov, Electric field effect in atomically thin carbon films, Science, 2004, 306(5696), 666–669 CrossRef CAS PubMed.
- M. Pumera, Graphene-based nanomaterials for energy storage, Energy Environ. Sci., 2011, 4(3), 668–674 CAS.
- Y. Zhu, S. Murali, W. Cai, X. Li, J. W. Suk, J. R. Potts and R. S. Ruoff, Graphene and graphene oxide: synthesis, properties, and applications, Adv. Mater., 2010, 22(35), 3906–3924 CrossRef CAS PubMed.
- M. Liang and L. Zhi, Graphene-based electrode materials for rechargeable lithium batteries, J. Mater. Chem., 2009, 19(33), 5871–5878 RSC.
- L. Q. Lu and Y. Wang, Facile synthesis of graphene supported shuttle- and urchin-like CuO composites for high and fast Li-ion storage, Electrochem. Commun., 2012, 14(1), 82–85 CrossRef CAS PubMed.
- Y. Zou and Y. Wang, NiO nanosheets grown on graphene nanosheets as superior anode materials for Li-ion batteries, Nanoscale, 2011, 3(6), 2615–2620 RSC.
- S. Yoon and A. Manthiram, Microwave-hydrothermal synthesis of W0.4Mo0.6O3 and carbon-decorated WOx–MoO2 nanorod anodes for lithium ion batteries, J. Mater. Chem., 2011, 21(12), 4082–4085 RSC.
- D. Chen, L. H. Tang and J. H. Li, Graphene-based materials in electrochemistry, Chem. Soc. Rev., 2010, 39(8), 3157–3180 RSC.
- B. Wang, X. L. Wu, C. Y. Shu, Y. G. Guo and C. R. Wang, Synthesis of CuO/graphene nanocomposite as a high-performance anode material for lithium-ion batteries, J. Mater. Chem., 2010, 20(47), 10661–10664 RSC.
- A. C. Ferrari, J. C. Meyer, V. Scardaci, C. Casiraghi, M. Lazzeri, F. Mauri, S. Piscanec, D. Jiang, K. S. Novoselov, S. Roth and A. K. Geim, Raman Spectrum of Graphene and Graphene Layers, Phys. Rev. Lett., 2006, 97(18), 187401 CrossRef CAS.
- Y. Zou, J. Kan and Y. Wang, Fe2O3–graphene rice-on-sheet nanocomposite for high and fast lithium ion storage, J. Phys. Chem. C, 2011, 115(42), 20747–20753 CAS.
- L. Q. Lu and Y. Wang, Sheet-like and fusiform CuO nanostructures grown on graphene by rapid microwave heating for high Li-ion storage capacities, J. Mater. Chem., 2011, 21(44), 17916–17921 RSC.
- Y. J. Mai, X. L. Wang, J. Y. Xiang, Y. Q. Qiao, D. Zhang, C. D. Gu and J. P. Tu, CuO/graphene composite as anode materials for lithium-ion batteries, Electrochim. Acta, 2011, 56(5), 2306–2311 CrossRef CAS PubMed.
- F. Su, X. S. Zhao, Y. Wang and J. Y. Lee, Bridging mesoporous carbon particles with carbon nanotubes, Microporous Mesoporous Mater., 2007, 98(1–3), 323–329 CrossRef CAS PubMed.
|
This journal is © The Royal Society of Chemistry 2014 |
Click here to see how this site uses Cookies. View our privacy policy here.