DOI:
10.1039/C4NJ01355G
(Paper)
New J. Chem., 2015,
39, 439-444
C(sp2)–C(sp2) cross coupling reaction catalyzed by a water-stable palladium complex supported onto nanomagnetite particles
Received
(in Montpellier, France)
18th August 2014
, Accepted 21st October 2014
First published on 22nd October 2014
Abstract
A water-stable palladium complex supported onto nanomagnetite particles was prepared and characterized. The nanocatalyst showed excellent reusability and activity in aqueous phase processes including the C(sp2)–C(sp2) cross coupling reactions. The advantages of the protocol are its generality, high yields, short reaction time, a cleaner reaction profile, and simplicity.
Introduction
The Heck and Suzuki coupling reactions that are catalyzed by palladium-based catalysts have shown high efficiency in the construction of C–C bonds.1–6 The resulting products are very important in pharmaceutical applications due to their significant influences in the synthesis of bioactive compounds and organic products.7–9 Homogeneous catalysts have high activity for coupling and are used for the Heck and Suzuki coupling reactions. But these kinds of catalysts cannot be easily separated and reused in subsequent reactions.7 Hence, they cannot meet the sustainability demands. These catalysts classified as homogeneous catalysts lack the capability to be recycled and are unable to satisfy the requirements of “sustainability”, and hence they are not acceptable in this new approach.10 Other catalysts classified as heterogeneous catalysts can be recycled and recovered, but the low activity attributed to their low surface contact does not allow them to be selected as perfect catalysts.11 Nanochemistry as a new area of research gives us the ability to scale down the size and synthesize nanoparticles with a wide range of shapes and sizes and unique properties and specifications.12 Many research studies have been done to synthesize nanoparticles and use them as catalysts.13–19 Providing a high surface area to volume ratio is one of the attractive advantages of nanoparticles.
This property increases the contact between reactants and catalysts and can improve the activity of the catalyst, which is a desired parameter in most of the reactions.20 Some ideal specifications of catalysts such as high activity, small size and ease in separation using an external magnet are achievable by employing the nanochemistry technology to synthesize the magnetic nanoparticles.12 These types of catalysts can overcome the issue of low activity, and they can be easily recovered, separated, and reused in other reactions. They will satisfy the sustainability and “green chemistry” demands. So these catalysts have the advantage of high activity of homogeneous catalysts and the advantages of easy recovery and reusability of heterogonous catalysts.21 Fe3O4 nanoparticles are attractive nanocatalysts which have attracted great attention due to their unique properties such as a high surface to volume ratio, low toxicity, easy preparation and superparamagnetism.22–24 Fe3O4-supported nanoparticles can be simply separated, recovered and reused for other reactions, thus significantly reducing the cost and production of waste.25–27
In this work we synthesized a new Pd-catalyst based on magnetite Fe3O4 nanoparticles. The magnetite nanoparticles (MNPs) were prepared and coated with a layer of silica in order to avoid the aggregation of nanoparticles to form clusters or clumps, then they were capped with imine-functionalized silane and (2-[2-(2-formylphenoxy)ethoxy] benzaldehyde) dihydroxyaryl palladium complexes were immobilized on magnetite nanoparticles through a click reaction. We performed the Suzuki coupling reaction as a model reaction using this new nanocatalyst to test its activity (Scheme 1), and we chose an environmentally friendly solvent for the reaction exhibiting good efficiency and high yields. The catalyst could be easily separated, recovered and reused for other reactions.
 |
| Scheme 1 C(sp2)–C(sp2) cross coupling of phenylboronic acid with aryl halides in the presence of Pd nanocatalyst. | |
Results and discussion
Nanomagnetite particles were prepared by the literature method.28 The nanoparticles were coated with a layer of silica with tetraethyl orthosilicate (TEOS). Silanation of the silica-coated magnetite nanoparticles (SMNPs) with 3-aminopropyl triethoxysilane was performed to obtain compound 3. Compound 3 with dialdehyde of 2-[2-(2-formylphenoxy)ethoxy]benzaldehyde (D) was sonicated for 10 min to produce the structure of 4. In the last step, PdCl2 was added to the reaction to synthesize nanocatalyst 5. These steps are illustrated in Fig. 1. Transmission electron microcopy (TEM) images of the catalyst are shown in Fig. 2.
 |
| Fig. 1 The synthetic route toward nanocatalyst 5. | |
 |
| Fig. 2 TEM images of the nanocatalyst. | |
By analysing TEM images of the catalyst, we found that more than 70% of the catalyst size is <20 nm (Table 1).
Table 1 Particle size distribution histogram from TEM images
Entry |
Size (nm) |
Abundance |
I |
10–15 |
35.3 |
II |
15–20 |
35.3 |
III |
25–30 |
32.4 |
The nanocatalyst was analyzed by energy dispersive X-ray (EDX) spectroscopy and the outcome was acceptable with expected elements: iron, silicon, oxygen, carbon, nitrogen and palladium. EDX analysis results of the nanocatalyst are shown Fig. 3.
 |
| Fig. 3 EDX analysis of the nanocatalyst. | |
FT-IR spectra of compounds (3), (4) and (5) are illustrated in Fig. 4. A broad band near 1000–1100 cm−1 indicated the silica coated magnetite nanoparticles. The observation of a band at 1635 cm−1 in curve b—4 confirmed the C
N double bond. The band at 1635 cm−1 due to the reaction with Pd shifted to a lower frequency at 1625 cm−1 in curve c—5.
 |
| Fig. 4 FT-IR spectra of the compounds 3–5: curve a—3; curve b—4; curve c—5. | |
Magnetic measurements of the Fe3O4 nanoparticles and the nanocatalyst with Pd were investigated at room temperature by using a vibrating sample magnetometer (VSM). Based on magnetization curves, the saturation of the obtained catalyst dropped from 35 emu g−1 (Fe3O4) to 7 emu g−1. This reduction in saturation accounts for the surface coating on Fe3O4 nanoparticles that interact with the Pd-nanoparticle catalyst (Fig. 5).
 |
| Fig. 5 The vibrating sample magnetometer (VSM) of the Fe3O4 (a) in comparison with catalyst (b). | |
By inductively coupled plasma optical emission spectroscopy (ICP/OES) of the catalyst the weight percentage of Pd was found to be 3.8 wt% in the catalyst.
X-ray photoelectroscopy (XPS) was used to determine the oxidation state of the Pd surface in the nanocatalyst. The XPS spectrum of Pd is shown in Fig. 6. The binding energy pattern showed a doublet peak at 335 eV (3d5/2) and 340.7 eV (3d3/2). This result could be attributed to the Pd(0) oxidation state. This result is consistent with previously reported values in the literature (Fig. 6).29
 |
| Fig. 6 XPS spectra of the catalyst Pd(0). | |
The X-ray diffraction (XRD) pattern of silica-coated magnetite nanoparticles Fe3O4@SiO2 (Fig. 7a) exhibited an XRD broadened pattern because of its non-crystallinity at 2θ = 20°–29° and 30.2°, 35.5°, 43.3°, 53.6°, 57.3°, 62.79° and 74.2°, which confirms the Fe3O4@SiO2 structure. The XRD pattern of Pd-nanocatalyst exhibited at 2θ = 40.1°, 46.65°, 68.1° and 82.08° confirms the Pd(0) structure (Fig. 7b).30
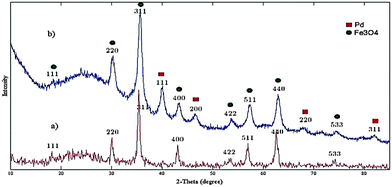 |
| Fig. 7 XRD patterns of (a) Fe3O4@SiO2 (b) SMNP-supported-(D)-Pd. | |
A new catalyst for the Suzuki reaction
We set up a Suzuki reaction to prove the activity of the new synthesized catalyst (structure (5)), where the reaction of bromobenzene with phenylboronic acid was performed as the model reaction. In the first experiment, the coupling reaction was performed in the presence of DMF as the solvent, K2CO3 as base and 0.2% catalyst loading at 100 °C for 3 hours (obtained yield was 92%). Different solvents such as H2O–DMF, water and toluene were investigated in these reactions. The greatest yield was observed with water/DMF (1
:
1), as shown in Table 2. Upon testing different bases such as NaOH, NaOAc, Na2CO3 and CS2CO3, a decrease in yield was observed (Table 2) and as for catalyst loading, the highest yield was obtained in the presence of 0.2% catalyst (Table 2).
Table 2 Influence of the base, solvent and palladium percentage in the model reactiona
Entry |
Solvent |
Base |
Pd (%) |
Time (h) |
Yieldb (%) |
Reaction conditions: bromobenzene (1 mmol), phenylboronic acid (1.5 mmol), K2CO3 (2 mmol), solvent (4 mL).
Isolated yield.
|
1 |
DMF |
K2CO3 |
0.2 |
3 |
92 |
2 |
DMF–H2O |
K2CO3 |
0.2 |
3 |
92 |
3 |
DMF–H2O |
NaOH |
0.2 |
3 |
83 |
4 |
DMF–H2O |
NaOAc |
0.2 |
3 |
70 |
5 |
DMF–H2O |
Na2CO3 |
0.2 |
3 |
71 |
6 |
DMF–H2O |
CS2CO3 |
0.2 |
3 |
91 |
7 |
H2O |
K2CO3 |
0.2 |
3 |
54 |
8 |
Toluene |
K2CO3 |
0.2 |
3 |
61 |
9 |
DMF–H2O |
K2CO3 |
0.1 |
3 |
80 |
10 |
DMF–H2O |
K2CO3 |
0.3 |
3 |
92 |
11 |
DMF–H2O |
K2CO3 |
0.2 |
1.5 |
80 |
The obtained optimized reaction conditions are presented in Table 2. The reactions were also investigated with various aryl halides and arylboronic acids under the determined optimized conditions, and the results are summarized in Table 3. We used aryl iodide to test the catalytic activity of the Pd-nanoparticle based catalyst. The time of reaction for aryl iodide was shorter than that for aryl bromides (1 h) and very good to excellent yields were obtained. It should be noted that the yield of the reaction for aryl bromides bearing an electron-withdrawing group was a little more than that obtained with an electron-releasing group (Table 3, entries 8 and 9). We also tried to perform the reaction with aryl chloride, but unfortunately a low yield was observed. We utilized this catalyst in coupling 2-naphthylboronic acid as a larger ring and the attempt was successful (entries 14 and 15).
Table 3 Investigations of the scope of substrates in the Pd-catalyzed C(sp2)–C(sp2) cross coupling reactiona
Entry |
Aryl halides |
Aryl boronic acids |
Time (h) |
Yieldb (%) |
Reaction conditions: bromobenzene (1 mmol), phenylboronic acid (1.5 mmol), K2CO3 (2 mmol), DMF/H2O (4 mL, v/v = 1 : 1), Pd catalyst (0.2 mol%), 100 °C.
Isolated yield.
|
1 |
Iodobenzene |
Phenylboronic acid |
1 |
92 |
2 |
1-Iodo-4-methylbenzene |
Phenylboronic acid |
1 |
92 |
3 |
4-Iodophenol |
Phenylboronic acid |
1 |
89 |
4 |
1-Iodo-4-methoxybenzene |
Phenylboronic acid |
1 |
94 |
5 |
Bromobenzene |
Phenylboronic acid |
3 |
92 |
6 |
1-Bromo-4-methylbenzene |
Phenylboronic acid |
3 |
91 |
7 |
1-Bromo-4-methoxybenzene |
Phenylboronic acid |
3 |
93 |
8 |
1-Bromo-4-nitrobenzene |
Phenylboronic acid |
3 |
93 |
9 |
4-Bromobenzonitrile |
Phenylboronic acid |
3 |
94 |
10 |
1-Bromo-2-methylbenzene |
Phenylboronic acid |
3 |
86 |
11 |
Iodobenzene |
4-Nitrophenylboronic acid |
1 |
95 |
12 |
Bromobenzene |
4-Nitrophenylboronic acid |
3 |
94 |
13 |
Chlorobenzene |
Phenylboronic acid |
6 |
11 |
14 |
Iodobenzene |
Naphthalen-2-ylboronic acid |
3 |
90 |
15 |
1-Iodo-4-methoxybenzene |
Naphthalen-2-ylboronic acid |
3 |
82 |
Another important advantage of this new nanocatalyst is its ability to be recovered and reused. The reaction of bromobenzene and phenylboronic acid was selected as a model for this reaction. After the coupling reaction was completed, the catalyst was separated using an external magnet, washed and dried.
A schematic representation of the proposed catalytic route for the Suzuki reaction is presented in Scheme 2. Firstly, the arylhalide reacts with the active palladium catalyst (oxidative addition) to produce the Pd(II) intermediate (II). Next, the aryl moiety of phenyl boronic acid is exchanged with halide on the surface of catalyst (III) and finally, III undergoes reductive elimination to produce the expected product.
 |
| Scheme 2 Proposed catalytic cycle for the Suzuki cross-coupling reaction. | |
After drying, the catalyst could be directly used in other similar coupling reactions. The catalyst was employed in the coupling reaction and recycling was performed five times, and analyzed by TEM. TEM images (Fig. 8) showed that not only the catalyst structure was stable but also the yield of the reaction was acceptable after each cycle.
 |
| Fig. 8 TEM images of the nanocatalyst after recycling five times. | |
Reusability of the magnetically separable Pd nanocatalyst is shown in Fig. 9. An insignificant decrease in the catalytic activity was observed after sixteen reactions; for example, the yield of reaction in the tenth run was roughly 80%. Metal leaching of the catalyst was studied before and after the reaction by ICP-OES analysis. The Pd content was found to be 3.8 wt% and 3.48 wt% before and after the five reaction series, respectively, which was verified to imply insignificant Pd leaching. Turnover frequency (TOF) of the catalyst was also determined (153.33 h−1 for the first reaction and 103 h−1 for sixteen reactions).
 |
| Fig. 9 Reusability of the magnetically separable Pd-nanocatalyst in sixteen reactions. | |
Experimental section
Materials
All the chemicals were purchased from Merck or Fluka Chemical Companies. The known products were identified by comparison of their spectral data with those in the authentic samples.
Characterization methods
The structure of the new magnetite nanocatalyst was characterized by FT-IR, XRD, UV-Vis, EDX, TEM, XPS and VSM analysis. FTIR-spectra were recorded on a Perkin Elmer PE-1600-FTIR spectrophotometer. The Pd content of the catalyst was determined by inductively coupled plasma (ICP) ICP-OES. X-ray photoelectron spectroscopy (XPS) was carried out using a dual anode (Mg and Al Kα) achromatic X-ray source. The size of the magnetite nanoparticles was measured by using a transmission electron microscope (Hitachi H 7600 TEM). X-ray diffraction (XRD) measurement was performed using an X-ray diffractometer ITAL STRUCTURES model APD2000 with application of Cu Kα radiation, in a 2θ range of 5° to 90°. Magnetic measurement of materials was performed using a vibrating sample magnetometer (VSM – 4 inch, Daghigh Meghnatis Kashan Co., Kashan, Iran) at room temperature.
Catalyst preparation
First, magnetic nanoparticles Fe3O4 and Fe3O4@SiO2 were synthesized according to the procedure previously reported in the literature.31
Silanation of the silica-coated magnetite nanoparticles.
Initially silica-coated magnetic nanoparticles were put under vacuum to dry. 2 g of dry particles were dispersed in 100 mL of dry toluene and sonicated for 30 min. 7.5 mL (32.04 mmol) of (3-aminopropyl) triethoxysilane was added dropwise to the suspended solid nanoparticles under mechanical stirring. The reaction was refluxed at 115 °C for 20 h. After refluxing, the nanoparticles were cooled down and then separated using a magnet. The nanoparticles were then washed three times with anhydrous methanol and then dried under vacuum. Next, a back titration was performed to determine the concentration of amines, which was measured to be 0.480–0.502 mmol g−1.
A general procedure for the preparation of 2-[2-(2-formylphenoxy)ethoxy]benzaldehyde (D) on silica-coated magnetite nanoparticles (SMNP-supported-D).
3 g of the material (3) was suspended in 50 mL of dry methanol, and after sonication for 15 min, 5 g (18 mmol) of 2-[2-(2-formylphenoxy)ethoxy]benzaldehyde was added and the mixture was heated at 50 °C for 2 days. After cooling to room temperature, the particles were separated magnetically, washed 3 times with dry methanol, and dried under vacuum for 24 h to give SMNP-supported-D.
A general procedure for the preparation of the palladium catalyst.
1 g of dry nanoparticles obtained from the final step and 15 mL of dry toluene were sonicated. Then, PdCl2 (0.6 mmol, 0.1 g) in 15 mL of toluene was added and the mixture was refluxed for 12 h under argon. The resulting product containing an external magnet was separated, subjected to a water wash (1 × 10 mL) and methanol wash (3 × 10 mL) and then dried under vacuum.
A general procedure for the Suzuki reaction.
A mixture of aryl halide (1 mmol), arylboronic acid (1.5 mmol), K2CO3 (2.0 mmol), DMF/H2O as a solvent (4.0 mL, v/v = 1
:
1) and the catalyst was added to a round bottom flask. The mixture of reaction was stirred at 100 °C in an air atmosphere for the required time to complete the reaction. When the reaction was completed, the reaction mixture was cooled and 25 mL of Et2O was added to the solution, the organic phase was washed with water (2 × 10 mL) and the solvent was evaporated. The residue of the reaction was purified by flash chromatography to provide the pure coupling product. The catalyst was separated magnetically by using an external magnet. The catalyst was washed with H2O, Et2O and recovered.
Conclusions
A novel, efficient, cost-effective, operationally simple and ecocompatible protocol for the C(sp2)–C(sp2) cross coupling reactions under ambient atmosphere in aqueous medium has been developed using a water-stable palladium complex supported onto nanomagnetite particles as an efficient, recyclable and stable heterogeneous catalyst. The salient features of the proposed methodology include generality, high efficiency and simplicity, which lead to short reaction time, high yields, a cleaner reaction profile and easy recyclability of the heterogeneous catalyst using a magnet.
Acknowledgements
The authors gratefully acknowledge the Bu-Ali Sina and Payame Noor, University Research Council, University of British Columbia and the Centre of Excellence in Development of Environmentally Friendly Methods for Chemical Synthesis (CEDEFMCS) for providing support to this work.
References
- P. D. Stevens, J. Fan, H. M. R. Gardimalla, M. Yen and Y. Gao, Org. Lett., 2005, 7, 2085–2088 CrossRef CAS PubMed.
- M. Zhu and G. Diao, J. Phys. Chem., 2011, 24743–24749 CAS.
- M. Ghotbinejad, A. R. Khosropour, I. Mohammadpoor-Baltork, M. Moghadam, S. Tangestaninejad and V. Mirkhani, J. Mol. Catal. A: Chem., 2014, 385, 78–84 CrossRef CAS PubMed.
- Y.-Q. Zhang, X.-W. Wei and R. Yu, Catal. Lett., 2010, 135, 256–262 CrossRef CAS PubMed.
- J. Wang, B. Xu, H. Sun and G. Song, Tetrahedron Lett., 2013, 54, 238–241 CrossRef CAS PubMed.
- A. Taher, J.-B. Kim, J.-Y. Jung, W.-S. Ahn and M.-J. Jin, Synlett, 2009, 2477–2482 CAS.
- N. Miyaura and A. Suzuki, Chem. Rev., 1995, 2457–2483 CrossRef CAS.
- A. F. Littke and G. C. Fu, Angew. Chem., Int. Ed., 2002, 41, 4176–4211 CrossRef CAS.
- H. Yang, Y. Wang, Y. Qin, Y. Chong, Q. Yang, G. Li, L. Zhang and W. Li, Green Chem., 2011, 13, 1352 RSC.
- F. Cozzi, Adv. Synth. Catal., 2006, 348, 1367–1390 CrossRef CAS.
- W. Teunissen, A. A. Bol and J. W. Geus, Catal. Today, 1999, 48, 329–336 CrossRef CAS.
- S. Shylesh, V. Schünemann and W. R. Thiel, Angew. Chem., Int. Ed., 2010, 49, 3428–3459 CrossRef CAS PubMed.
- Z. Wang, P. Xiao, B. Shen and N. He, Colloids Surf., A, 2006, 276, 116–121 CrossRef CAS PubMed.
- A. Schätz, M. Hager and O. Reiser, Adv. Funct. Mater., 2009, 19, 2109–2115 CrossRef.
- S. Wittmann, A. Schätz, R. N. Grass, W. J. Stark and O. Reiser, Angew. Chem., Int. Ed., 2010, 49, 1867–1870 CrossRef CAS PubMed.
- J. Mondal, T. Sen and A. Bhaumik, Dalton Trans., 2012, 41, 6173–6181 RSC.
- X. Jin, K. Zhang, J. Sun, J. Wang, Z. Dong and R. Li, Catal. Commun., 2012, 26, 199–203 CrossRef CAS PubMed.
- A. R. Moosavi-Zare, M. A. Zolfigol, V. Khakyzadeh, C. Böttcher, M. H. Beyzavi, A. Zare, A. Hasaninejad and R. Luque, J. Mater. Chem. A, 2014, 2, 770 CAS.
- M. A. Zolfigol, A. R. Moosavi-Zare, P. Moosavi, V. Khakyzadeh and A. Zare, C. R. Chim., 2013, 16, 962–966 CrossRef CAS PubMed.
- M. A. Zolfigol, V. Khakyzadeh, A. R. Moosavi-Zare, A. Rostami, A. Zare, N. Iranpoor, M. H. Beyzavi and R. Luque, Green Chem., 2013, 15, 2132 RSC.
- J. M. Campelo, D. Luna, R. Luque, J. M. Marinas and A. A. Romero, ChemSusChem, 2009, 2, 18–45 CrossRef CAS PubMed.
- Y.-S. Lin and C. L. Haynes, Chem. Mater., 2009, 21, 3979–3986 CrossRef CAS.
- Y. Deng, Y. Cai, Z. Sun, J. Liu, C. Liu, J. Wei, W. Li, C. Liu, Y. Wang and D. Zhao, J. Am. Chem. Soc., 2010, 132, 8466–8473 CrossRef CAS PubMed.
- L. M. Rossi, I. M. Nangoi and N. J. S. Costa, Inorg. Chem., 2009, 48, 4640–4642 CrossRef CAS PubMed.
- Y. Liao, L. He, J. Huang, J. Zhang, L. Zhuang, H. Shen and C.-Y. Su, ACS Appl. Mater. Interfaces, 2010, 2, 2333–2338 CAS.
- M. Yus, R. Cano and D. J. Ram, Tetrahedron, 2011, 67, 5432–5436 CrossRef PubMed.
- Q. Du, W. Zhang, H. Ma, J. Zheng, B. Zhou and Y. Li, Tetrahedron, 2012, 68, 3577–3584 CrossRef CAS PubMed.
- S. Qu, H. Yang, D. Ren, S. Kan, G. Zou, D. Li and M. Li, J. Colloid Interface Sci., 1999, 215, 190–192 CrossRef CAS PubMed.
- A. Khalafi-Nezhad and F. Panahi, Green Chem., 2011, 13, 2408 RSC.
- S. Navaladian, B. Viswanathan, T. K. Varadarajan and R. P. Viswanath, Nanoscale Res. Lett., 2008, 4, 181–186 CrossRef PubMed.
- N. Koukabi, E. Kolvari, A. Khazaei, M. A. Zolfigol, B. Shirmardi-Shaghasemi and H. R. Khavasi, Chem. Commun., 2011, 47, 9230–9232 RSC.
|
This journal is © The Royal Society of Chemistry and the Centre National de la Recherche Scientifique 2015 |
Click here to see how this site uses Cookies. View our privacy policy here.