DOI:
10.1039/C3NR04102F
(Paper)
Nanoscale, 2014,
6, 392-399
Highly tough and transparent layered composites of nanocellulose and synthetic silicate†
Received
5th August 2013
, Accepted 15th October 2013
First published on 17th October 2013
Abstract
A highly tough and transparent film material was prepared from synthetic saponite (SPN) nanoplatelets of low aspect ratios and nanofibrillar cellulose. The nanofibrillar cellulose was chemically modified by topological surface oxidation using 2,2,6,6-tetramethylpiperidinyl-1-oxyl (TEMPO) as a catalyst. Both synthetic SPN nanoplatelets and TEMPO-oxidized cellulose nanofibrils (TOCNs) have abundant negative charges in high densities on their surfaces and are dispersed in water at the individual nanoelement level. Layered nanocomposite structures of the SPN nanoplatelets and TOCNs were formed through a simple cast-drying process of the mixed aqueous dispersions. The TOCN/SPN composites with 0–50% w/w SPN content were optically transparent. Mechanical properties of the TOCN/SPN composites varied depending on the SPN content. The composite with 10% w/w SPN content (5.6% volume fraction) exhibited characteristic mechanical properties: Young's modulus of 14 GPa, tensile strength of 420 MPa, and strain-to-failure of 10%. The work of fracture of the composites increased from 4 to 30 MJ m−3 – or by more than 700% – as the SPN content was increased from 0 to 10% w/w. This surprising improvement in toughness was interpreted based on a model for fracture of polymer composites reinforced with low-aspect-ratio platelets.
Introduction
Polymer/layered silicate (PLS) nanocomposites have been used in a range of practical materials from automobile parts to packaging materials. Layered silicates can effectively improve mechanical, thermal, and gas-barrier properties of host polymeric materials as compared with other reinforcing fillers.1,2 The earliest example of PLS nanocomposites was shown by researchers at Toyota; they prepared a nanocomposite from nylon 6 and a layered silicate and found significant improvement in the mechanical and thermal properties.3,4 Later, many other researchers embraced the new composite material concept and further developed many polymer/layered silicate combinations, composite nanostructures, and synthesis methods.
The main source of layered silicates is clay minerals. Representative layered silicates used in industry are montmorillonite (MTM) and saponite (SPN), both of which belong to the smectite group, which is a major component of swelling clay minerals. A smectite nanoplatelet is about 1 nm thick, and has a sandwiched structure comprising an inner octahedral metal layer and two outer silicate tetrahedral layers. In the outer silicate layers, some of the central silicon ions, Si4+, are substituted with other metal ions, Al3+ or Mg2+, such that the surface of a smectite nanoplatelet is negatively charged.5,6 In contrast, the edges of the smectite nanoplatelets are positively charged.7,8 The main differences between MTM and SPN are that (1) the silicon ions are substituted mainly with Al3+ and Mg2+, respectively, and (2) the platelet size of SPN (∼50 nm) is much smaller than that of MTM (∼300 nm).6,7 MTM and SPN nanoplatelets are often modified using cationic surfactants to be organophilic to prepare PLS nanocomposites with hydrophobic polymers.1,9 It was reported that surfactant-modified nanoplatelets disperse well in hydrophobic polymer matrices, resulting in improved material properties.10–17 These surfactants act to expand the galleries between the nanoplatelets, which allows the polymer chains to more easily intercalate between the nanoplatelet layers.
A new PLS nanocomposite that uses native cellulose as the polymer component has recently been reported.18 Cellulose is the most abundant polymer material on earth and is biosynthesized as nanofibrillar crystal structures 2–20 nm in width. These nanofibrillar structures have high strength (2–6 GPa),19 high elastic moduli (30–150 GPa),20–23 high thermal stability (Tm > Td ∼300 °C), and large surface areas (100–1000 m2 g−1). When cellulose nanofibrils are combined with layered silicates, the composites exhibit excellent mechanical, thermal, and gas-barrier properties.17,18,24 In a previous study, we prepared PLS nanocomposites from MTM nanoplatelets and cellulose nanofibrils that had been chemically modified by topological surface oxidation using 2,2,6,6-tetramethylpiperidinyl-1-oxyl (TEMPO) as a catalyst. The TEMPO-oxidized cellulose nanofibrils (TOCNs) can be fully isolated and stably dispersed in water.25 The PLS nanocomposites were prepared by mixing water dispersions of the TOCNs and MTM nanoplatelets and oven drying. Despite the simple preparation process, the resulting TOCN/MTM nanocomposites exhibited a high strength of 270–510 MPa, high elastic moduli of 11–19 GPa, and low oxygen permeabilities of 0.001–0.01 mL μm m−2 day−1 kPa−1 at 0% RH.17
For material properties of PLS nanocomposites, knowledge of the aspect ratio, or the ratio of the platelet size to the thickness, of silicate nanoplatelets is important.6 High-aspect-ratio nanoplatelets of high surface area can achieve both a high stress transfer from the polymer matrix to the nanoplatelets and a high barrier to gas diffusion, leading to dramatic improvement in the mechanical, thermal, and gas-barrier properties. To realize these improvements, the nanoplatelets must be oriented parallel to the loading direction, or perpendicular to the gas-diffusion direction, and have favorable interactions at the polymer matrix interface. Polymer composites reinforced with high-aspect-ratio nanoplatelets exhibit high strength but are relatively brittle. In contrast, the composites reinforced with low-aspect-ratio nanoplatelets have lower strength than those with higher aspect ratios, but are more ductile and tough. These properties can be explained based on models of PLS composite fracture behavior;13,26 high-aspect-ratio platelets of high surface area can accept sufficient interfacial shear stress to be fractured in the composite, while low-aspect-ratio platelets of low surface area are pulled out from the polymer matrix under the same loading conditions, allowing the composites to strain more. In addition, the aspect ratio and dispersibility of silicate nanoplatelets are often in a reciprocal relationship; low-aspect-ratio nanoplatelets are dispersed better than high-aspect-ratio ones.
Here, we report a highly tough and transparent PLS nanocomposite prepared from synthetic low-aspect-ratio SPN nanoplatelets and TOCNs. We show that the advantages of using low-aspect-ratio nanoplatelets can be fully realized using TOCNs as the polymer component.
Experimental
Materials
A softwood bleached kraft pulp in a never-dried state (water content 80%) was supplied by Nippon Paper Industries (Tokyo, Japan). For demineralization, the pulp was stirred in a dilute HCl solution at pH ∼2.5 for 2 h and washed with deionized water by filtration. A synthetic SPN in powder form was supplied by Kunimine Industries (Tokyo, Japan). The platelet size of the SPN nanoplatelets is ∼50 nm, and the surface negative charge and edge positive charge densities are ∼1.0 mmol g−1 and ∼0.1 mmol g−1, respectively, according to the manufacturer. Other chemicals were purchased from Wako Pure Chemicals (Osaka, Japan) and used as received.
TOCN dispersion
Aqueous dispersions of TOCNs were prepared from a softwood bleached kraft pulp according to a previously reported method.27,28 The pulp (1 g) was suspended in water (100 mL) containing TEMPO (0.016 g) and sodium bromide (0.1 g). The TEMPO-mediated oxidation was started by adding 1.8 M NaClO (3.8 mmol g−1 of the pulp) to the suspension. The suspension was maintained at a pH of 10 by adding 0.5 M NaOH with a pH-stat. After 1 h, the oxidized pulp was washed with distilled water by filtration. The TEMPO-oxidized pulp was further treated with 1% w/v NaClO2 in 0.1 M acetate buffer at pH 4.8 for 2 days. The carboxylate content of the oxidized pulp was 1.2 mmol g−1 of the pulp, as determined by electric conductivity titration. The oxidized pulp was mechanically disintegrated in water to individual nanofibrils as follows; a 0.11% w/v suspension of the oxidized pulp (150 mL) was treated with a double-cylinder-type homogenizer (Physcotron NS-56; Microtec, Tokyo, Japan) for 1 min and then with an ultrasonic homogenizer for 4 min (US-300T; Nihon Seiki, Tokyo, Japan). The unfibrillated fraction (<10%) was removed by centrifugation at 12
000g for 20 min, and the supernatant was used as a TOCN dispersion. Widths and lengths of the TOCNs thus prepared were ∼3 nm and ∼1.1 ± 0.4 μm, respectively.19,29 The concentration of the TOCN dispersions was adjusted to 0.1% w/v using an evaporator at 42 °C under reduced pressure.
SPN nanoplatelet dispersion
SPN powder (0.6 g) was incrementally added to distilled water (30 mL) under stirring. After 1 h, the 2% w/v SPN suspension was treated with a double-cylinder-type homogenizer (Physcotron NS-56; Microtec) for 1 min and subsequently with an ultrasonic homogenizer (US-300T; Nihon Seiki) for 4 min. The resulting dispersion of SPN nanoplatelets was optically transparent and highly viscous (Fig. S1 in the ESI†).
TOCN/SPN composites
The 2% w/v dispersion of SPN nanoplatelets (0.015–1.5 mL) was added to the 0.1% w/v TOCN dispersion (30 mL) under stirring. After stirring for 1 h, the TOCN/SPN dispersion was poured into a polystyrene Petri dish of 50 mm diameter and oven dried at 40 °C for 3 days. The TOCN/SPN composite film formed on the dish was peeled off and stored at 23 °C and 50% relative humidity (RH). Thicknesses of the films increased as the amount of added SPN dispersion was increased, and were 5.0–11.7 μm when measured using a digital micrometer (Mitutoyo Series 227; Mitutoyo, Tokyo, Japan). The standard deviation of the film thickness was within 5% of the mean value for all the film samples. The TOCN/SPN composite films with TOCN
:
SPN weight ratios of 99
:
1, 95
:
5, 90
:
10, 75
:
25, and 50
:
50 were coded as TS01, TS05, TS10, TS25, and TS50, respectively.
Characterization
The moisture content of the films was determined from weight losses at 150 °C by thermogravimetric analysis using a Rigaku Thermoplus TG-8120. Light transmittance spectra of the films were measured using a JASCO V-670 UV-Vis spectrophotometer. Tensile tests of the films were performed using a Shimadzu EZ-TEST instrument equipped with a 500-N load cell at 23 °C and 50% RH. Rectangular strips 2 × 30 mm in size were cut from the films and tested with a span length of 10 mm at a rate of 1.0 mm min−1. In tensile testing, at least 10 measurements were carried out for each sample. Young's modulus was determined from the slope of the initial linear region of the stress–strain curve. Yield stress was determined as the intersection of the tangents to the lines joining the initial elastic and subsequent plastic curves. Work of fracture was calculated as the area below the stress–strain curve. Scanning electron microscope (SEM) observation of the film cross-sections was carried out with a Hitachi S4800 field-emission microscope equipped with an energy-dispersive X-ray (EDX) analyzer at 1 kV. The EDX spectra were recorded at 5.0 kV for 30 min. The samples subjected to SEM observation were coated with osmium using a Meiwafosis Neoc Osmium Coater at 10 mA for 5 s. X-ray diffraction (XRD) patterns of the films were obtained in reflection mode using a Rigaku RINT 2000 diffractometer with monochromator-filtered Cu Kα radiation (λ 0.15418 nm) at 40 kV and 40 mA. Oxygen permeabilities (PO2) of the TOCN/SPN-coated poly(ethylene terephthalate) (PET) films were determined at 0% or 50% RH using a MOCON OX-TRAN Model 2/21 MH instrument according to a standard method (ASTM 3985). Each sample was conditioned in the chamber for 3 h, and the oxygen transmission rates were measured for 50 cm2 areas at atmospheric pressure over 1–3 days until a stable value was reached. The PO2 of the TOCN/SPN layer in the TOCN/SPN-coated PET film was calculated using the following equation:
where T is the thickness of the TOCN/SPN layer, PET film, or TOCN/SPN-coated PET film. Thicknesses of the TOCN/SPN layers and PET films were 1 μm and 50 μm, respectively.
Results and discussion
Optical properties and structures of TOCN/SPN composites
The TOCN/SPN composite films were prepared by cast-drying mixed dispersions of TOCNs and SPN nanoplatelets. The SPN content in the composites varied from 1% to 50% w/w by controlling the mixing ratios. Densities and moisture contents of the composite films at 23 °C and 50% RH were 1.5–2.0 g cm−3 and 7–10% w/w, respectively. The density linearly increased with SPN content. Assuming the true densities of the TOCNs and SPN nanoplatelets to be 1.6 g cm−3 and 2.8 g cm−3, respectively, porosities of all the composite films are less than 5%, regardless of the SPN content. These low porosities suggest dense packing of TOCNs and SPN nanoplatelets in the composites.
Fig. 1a shows light transmittance spectra of the TOCN/SPN composite films. All the composite films with 1–50% SPN content were transparent. The transmittance spectra showed the Fabry–Perot interference over a wide range of wavelengths, indicating that the composite films have flat and smooth reflecting surfaces. These transparent composite films were flexible (Fig. 1b–d) and even foldable (Fig. 1e). It should be noted that even the composite film with a high 50% w/w SPN content is transparent and foldable. In general, the optical transparency of polymer nanocomposites reinforced with high-aspect-ratio silicates such as MTM significantly decreases with increasing silicate content.17
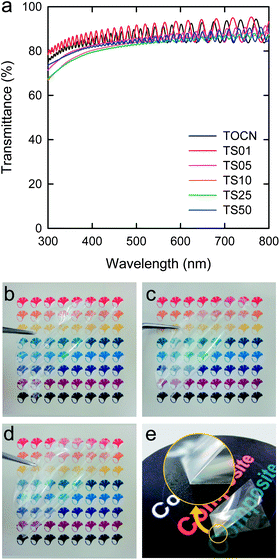 |
| Fig. 1 (a) Light transmittance of the TOCN/SPN composites with 0–50% w/w SPN contents. Flexible transparent films of the (b) neat TOCN, (c) TS10, and (d) TS50. (e) A folded film of TS50. | |
Fig. 2 shows SEM images of cross-sections of the neat TOCN, TS10, TS50, and neat SPN films. Both the neat TOCN film (Fig. 2a) and the neat SPN film (Fig. 2b) have layered structures; the layered structures in the TOCN film are composed of in-plane oriented nanofibrils,30,31 while those in the SPN film are composed of stacked nanoplatelets. Layered structures were also observed in the composite films (Fig. 2c and d). These layers were oriented parallel to the film surfaces. The layered structures in the composite become sharply defined and plate-like with increasing SPN content. Similar layered structures have been observed for composites of MTM nanoplatelets and cellulose nanofibrils.17,18 The layered structures in the TOCN/SPN composites are more finely segregated than those in the cellulose/MTM composites. Elemental mapping of the film cross-sections by EDX (Fig. 2e and f) showed that the SPN nanoplatelets are homogeneously distributed within the composites at the micron scale. Furthermore, XRD analyses of the TOCN/SPN composites showed that SPN nanoplatelets in the composites with low SPN content are highly dispersed in the TOCN matrix at the nanometer scale (Fig. 3); the (001) diffraction of SPN nanoplatelets, corresponding to the inter-platelet spacing of the nanoplatelets, was undetected for the TS10, TS05, and TS01.17 The broad (001) diffraction pattern for the TS50 and TS25 indicates that some of the SPN nanoplatelets are aggregated in the composites. These aggregates in TS50 and TS25 were likely formed when the water dispersions with high SPN contents of 25–50% were dried.
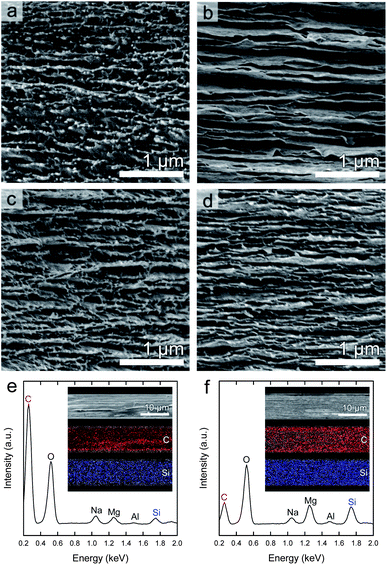 |
| Fig. 2 SEM images of the cross-sections of (a) neat TOCN, (b) neat SPN, (c) TS10, and (d) TS50 films. SEM-EDX spectra of the film cross-sections for (e) TS10 and (f) TS50. The insets show whole images of the film cross-sections and the elemental mapping of carbon (TOCN) and silicon (SPN). | |
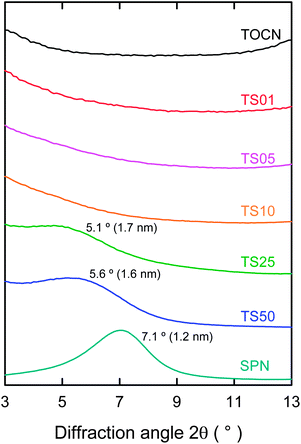 |
| Fig. 3 XRD patterns of the neat TOCN, TOCN/SPN composites, and neat SPN films, showing changes in the (001) diffraction of SPN nanoplatelets as a function of SPN content in the composites. For the TS25, TS50, and neat SPN, the peak center positions and corresponding d-spacings are presented in parentheses next to each peak. | |
Mechanical properties of TOCN/SPN composites
Mechanical properties of the TOCN/SPN composites varied depending on the SPN content. Fig. 4 shows tensile properties of the composites. All the stress–strain curves showed similar trends; the linear elastic region was observed until a strain of 0.5–1%, and at a higher strain, strong strain-hardening was observed in the plastic region. The Young's modulus and yield stress of the composites increased almost linearly with increasing SPN content up to 25% and 10%, respectively, after which these values reached a plateau. This result indicated that the energy required for reaching the yield stress or the maximum elastic strain energy increased with increasing SPN content up to 10%, and then decreased. The yielding was probably caused by interfacial slippage of TOCNs and SPN nanoplatelets in the composite.30 Tensile strength, strain-to-failure, and work of fracture of the composite also increased with increasing SPN content up to 10% and then decreased. All the composites showed similar strain-hardening in the plastic region, so that the tensile strength of the TOCN/SPN composites is correlated with strain-to-failure. The decrease in mechanical properties at the SPN contents of over 10% is probably due to aggregation of SPN nanoplatelets within the composites, as indicated in the XRD analyses of TS25 and TS50 (Fig. 3).
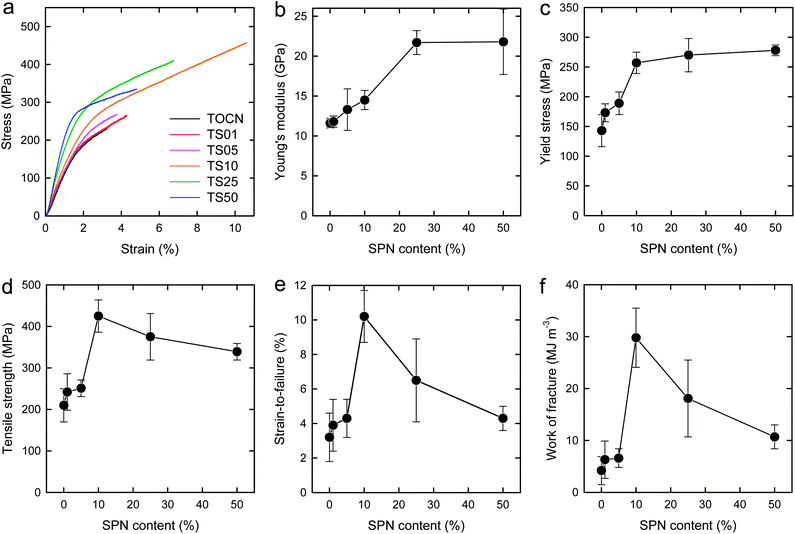 |
| Fig. 4 Mechanical properties of the TOCN/SPN composite films with an SPN content of 0–50% w/w: (a) stress–strain curve, (b) Young's modulus, (c) yield stress, (d) tensile strength, (e) strain-to-failure, and (f) work of fracture. | |
The TOCN/SPN composite with an SPN content of 10% (TS10) showed a unique combination of Young's modulus (14.5 GPa), tensile strength (425 MPa), and strain-to-failure (10.2%). As a result, the work of fracture of the TS10 is as high as 30 MJ m−3. The tensile strength of TS10 is comparable to that of some steels, while the modulus is one order of magnitude lower than those of the steels, revealing that the TOCN/SPN composite has a great advantage over the steels in terms of flexibility. The work of fracture of 4.2 MJ m−3 of neat TOCN films increased by more than 7-fold as the SPN content was increased to 10% w/w. This increase in the work of fracture for the TOCN/SPN composites is outstanding, and is, to our knowledge, higher than those for a range of the PSL nanocomposites reported to date. In the previous study, we prepared a PLS nanocomposite from TOCNs and MTM nanoplatelets. The TOCN/MTM composite with an MTM content of 5% w/w showed an excellent mechanical performance of Young's modulus of 18 GPa, tensile strength of 509 MPa, strain-to-failure of 7.6%, and work of fracture of 25.6 MJ m−3. The TOCN/SPN composite prepared in the present study showed lower values for modulus and strength, yet higher values for strain-to-failure and work of fracture than the TOCN/MTM composite. The high work of fracture of the TOCN/SPN composites can be interpreted based on a model for fracture of polymer composites reinforced with low-aspect-ratio platelets (see the fourth paragraph of Introduction); the low-aspect-ratio SPN nanoplatelets embedded in the TOCN matrix were pulled out from the matrix, so that the composite strained more and displayed a higher work of fracture. Although transparent SPN-based PLS nanocomposites have been reported,7,8 mechanical properties of those nanocomposites are inferior to the TOCN/SPN composites prepared in the present study.
The reinforcement efficiency of the SPN nanoplatelets embedded in the TOCN matrix was assessed by calculating the effective Young's modulus and tensile strength of the SPN nanoplatelets (Fig. 5). Young's modulus Ec of the polymer composites reinforced with low-aspect-ratio silicates is estimated using the following equation:32,33
where
Er and
Es are the Young's moduli of the silicate platelets and polymer matrix, respectively,
Vr is the volume fraction of the silicate platelets, and
α is an empirical efficiency factor. The factor
α is described as follows:
where
where
p is the aspect ratio of the silicate platelets, and
v is Poisson's ratio of the polymer matrix. In this prediction, the silicate platelets in the composite are assumed to orient parallel to the loading direction and have ideal interactions with the polymer matrix. In the present study, a Young's modulus of 11.6 GPa for the neat TOCN films and an aspect ratio of 50 for the SPN nanoplatelets were applied to
Es and
p, respectively, Poisson's ratio
v of the TOCN matrix was assumed to be −0.1,
23 and the volume fraction
Vr was calculated assuming densities of the TOCN matrix and SPN nanoplatelets to be 1.5 g cm
−3 and 2.8 g cm
−3, respectively.
Fig. 5a shows the best fitting of the estimated modulus
Ec to the experimental values. This fitting was obtained when the modulus
Er of the nanoplatelets was 100 GPa; in fact, the effective Young's modulus of the SPN nanoplatelets in TOCN/SPN composites was estimated to be 100 GPa. The effective modulus value of 100 GPa for the SPN nanoplatelets is lower than that for the MTM nanoplatelets in the TOCN/MTM composite (250 GPa),
17 but is the same as the value reported for MTM nanoplatelets embedded in a xyloglucan matrix, one of the PLS nanocomposite systems that displays the highest modulus reinforcement efficiencies.
15 It is significant that an effective modulus of 100 GPa was obtained without covalent cross-linking between the polymer matrix and the silicate platelets.
10,11
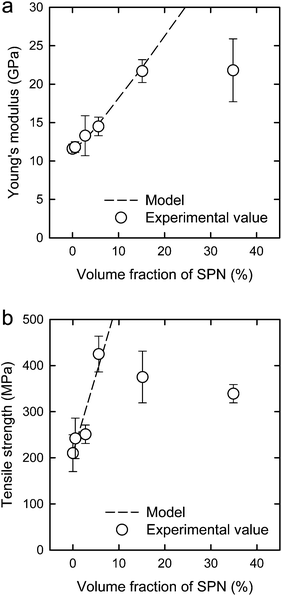 |
| Fig. 5 (a) Young's modulus and (b) tensile strength of the TOCN/SPN composites as a function of volume fraction of SPN nanoplatelets in comparison with models for polymer composites reinforced with low-aspect-ratio silicates. | |
Conversely, the tensile strength σc of polymer composites reinforced with low-aspect-ratio silicates can be estimated using the following equation:13,26
where
σr and
σs are the tensile strengths of the silicate platelets and polymer matrix, respectively, and
β is an empirical efficiency factor. The factor
β is described as follows:
where
τy is the yield shear strength of the polymer matrix. In this prediction, the polymer matrix in the PLS composite is assumed to yield before the platelets break, and the composites fail under the platelet-pull-out mode. In the present study, the tensile and yield strengths of 210 MPa and 143 MPa, respectively, of the TOCN matrix were used for
σs and
τy, and the volume fraction
Vr and aspect ratio
p of the SPN nanoplatelets were set as the same values as those used in the modulus calculations. As a result, the strength of TOCN/SPN composites was well described by this fracture model of the platelet-pull-out mode (
Fig. 5b). The best fit of the estimated strength
σc to the experimental values was obtained when the strength
σr of the nanoplatelets, or effective strength of the SPN nanoplatelets in the TOCN/SPN composites, was estimated to be 5 GPa. The high strength of 5 GPa indicates that the SPN nanoplatelets embedded within the TOCN matrix are highly functional reinforcement materials, considering that the strength of synthetic inorganic fibers and platelets is from 2 to 5 GPa.
The high reinforcement efficiency of the SPN nanoplatelets suggests the presence of favorable interactions between the SPN nanoplatelets and TOCNs in the composites. It is plausible that these interactions comprise electrostatic attractions between polar groups, such as hydroxyl groups and carboxylate groups (–COO−Na+) on TOCN surfaces and magnesium oxide groups (–MgO−Na+) on SPN nanoplatelet surfaces.34 The surfaces of both SPN nanoplatelets and TOCNs are negatively charged in water, and they are stably dispersed even in the mixed dispersion. However, once the aqueous dispersions are dried and the composite films are formed, no nanoparticles are charged in the solid composite structures; these ionic groups on the nanoparticle surfaces are not dissociated at all in solid, which likely interact with each other as polar groups. Furthermore, the dense packing of the SPN nanoplatelets and TOCNs in the composites (porosities < 5%) suggests dense, strong interactions between these nanoparticles.
Oxygen permeability of TOCN/SPN composites
Fig. 6 shows oxygen permeabilities of the TOCN/SPN composite layers coated on PET films. At 0% RH, the oxygen permeability of the composites decreased by one order of magnitude as the SPN content was increased, resulting in a very low oxygen permeability value of 0.005 mL μm m−2 day−1 kPa−1 for the 50% w/w SPN content composite. As a reference, the oxygen permeability of ethylene vinylalcohol copolymer films, commonly used as oxygen-barrier films, is 0.01–0.1 mL μm m−2 day−1 kPa−1 at 0% RH.35 However, the oxygen-barrier efficiency of the synthetic SPN nanoplatelets used in the present study is low because the aspect ratio of the SPN nanoplatelets is low (∼50).36 In the previous study, the oxygen permeability of the TOCN/MTM composites at 0% RH decreased by one order of magnitude with an MTM content of only 10% w/w. At 50% RH, the oxygen permeability of the TOCN/SPN composites was high, with values of 1–2 mL μm m−2 day−1 kPa−1, regardless of the SPN content; no significant contribution of the SPN nanoplatelets to the oxygen permeabilities was observed. These high oxygen permeabilities at 50% RH are probably due to the 7–10% w/w moisture adsorption of the hydrophilic TOCN/SPN composites under humid conditions.1,25
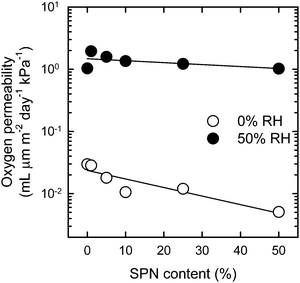 |
| Fig. 6 Oxygen permeabilities of the TOCN/SPN composite layers coated on PET films measured at 0% or 50% RH. | |
Conclusions
A tough and transparent PLS nanocomposite was prepared from synthetic, low-aspect-ratio SPN nanoplatelets and TOCNs. Both the SPN nanoplatelets and TOCNs have negative charges on their surfaces and are highly dispersed in water. Layered nanocomposite structures in which the SPN nanoplatelets are homogeneously distributed in the TOCN matrix are formed through a simple process of cast drying the mixed aqueous dispersions. The optical transparency of the neat TOCN matrix is maintained even as SPN nanoplatelets are incorporated at concentrations up to 50% w/w. In contrast, mechanical properties of the TOCN/SPN composites varied, depending on the SPN content. The 10% w/w SPN content composite exhibited characteristic mechanical properties of the Young's modulus of 14.5 GPa, tensile strength of 425 MPa, and strain-to-failure of 10.2%. The work of fracture of the composites increased from 4.2 to 30 MJ m−3 with increasing SPN content up to 10% w/w. To our knowledge, this increase of more than 7-fold in the work of fracture is unprecedented as toughening of polymer-based materials by layered silicates. These superior material properties of the TOCN/SPN composites arise from (1) the high dispersibility of both synthetic SPN nanoplatelets and TOCNs in water, (2) strong interactions between the SPN nanoplatelets and TOCNs in the solid composite, and (3) the low aspect ratio of the synthetic SPN nanoplatelets, allowing the composites to fail under the platelet-pull-out mode.
Acknowledgements
This study was supported by the Japan Society for the Promotion of Science (JSPS): Grants-in-Aid for Scientific Research S (21228007), Encouragement of Young Scientists A (23688020), and Challenging Exploratory Research (2658059).
References
- S. S. Ray and M. Okamoto, Prog. Polym. Sci., 2003, 28, 1539–1641 CrossRef CAS PubMed.
- P. Calvert, Nature, 1996, 383, 300–301 CrossRef CAS.
- A. Usuki, Y. Kojima, M. Kawasumi, A. Okada, Y. Fukushima, T. Kurauchi and O. Kamigaito, J. Mater. Res., 1993, 8, 1179–1184 CrossRef CAS.
- A. Okada and A. Usuki, Mater. Sci. Eng., C, 1995, 3, 109–115 CrossRef.
- J. Wang, Q. Cheng and Z. Tang, Chem. Soc. Rev., 2012, 41, 1111–1129 RSC.
- D. R. Paul and L. M. Robeson, Polymer, 2008, 49, 3187–3204 CrossRef CAS PubMed.
- T. Ebina and F. Mizukami, Adv. Mater., 2007, 19, 2450–2453 CrossRef CAS.
- H. Tetsuka, T. Ebina, H. Nanjo and F. Mizukami, J. Mater. Chem., 2007, 17, 3545–3550 RSC.
- T. D. Fornes and D. R. Paul, Macromolecules, 2004, 37, 1793–1798 CrossRef CAS.
- A. Walther, I. Bjurhager, J. M. Malho, J. Pere, J. Ruokolainen, L. A. Berglund and O. Ikkala, Nano Lett., 2010, 10, 2742–2748 CrossRef CAS PubMed.
- P. Podsiadlo, A. K. Kaushik, E. M. Arruda, A. M. Waas, B. S. Shim, J. Xu, H. Nandivada, B. G. Pumplin, J. Lahann, A. Ramamoorthy and N. A. Kotov, Science, 2007, 318, 80–83 CrossRef CAS PubMed.
- A. Okada and A. Usuki, Mater. Sci. Eng., C, 1995, 3, 109–115 CrossRef.
- L. J. Bonderer, A. R. Studart and L. J. Gauckler, Science, 2008, 319, 1069–1073 CrossRef CAS PubMed.
- M.-L. Chan, K.-T. Lau, T.-T. Wong, M.-P. Ho and D. Hui, Composites, Part B, 2011, 42, 1708–1712 CrossRef PubMed.
- J. J. Kochumalayil, M. Bergenstråhle-Wohlert, S. Utsel, L. Wågberg, Q. Zhou and L. A. Berglund, Biomacromolecules, 2013, 14, 84–91 CrossRef CAS PubMed.
- Q. Yang, C.-N. Wu, T. Saito and A. Isogai, Carbohydr. Polym., 2014, 100, 179–184 CrossRef CAS PubMed.
- C.-N. Wu, T. Saito, S. Fujisawa, H. Fukuzumi and A. Isogai, Biomacromolecules, 2012, 13, 1927–1932 CrossRef CAS PubMed.
- A. Liu, A. Walther, O. Ikkala, L. Belova and L. A. Berglund, Biomacromolecules, 2011, 12, 633–641 CrossRef CAS PubMed.
- T. Saito, R. Kuramae, J. Wohlert, L. A. Berglund and A. Isogai, Biomacromolecules, 2013, 14, 248–253 CrossRef CAS PubMed.
- I. Sakurada, Y. Nukushina and T. Ito, J. Polym. Sci., 1962, 57, 651–660 CrossRef CAS.
- A. Šturcová, G. R. Davies and S. J. Eichhorn, Biomacromolecules, 2005, 6, 1055–1061 CrossRef PubMed.
- J. Wohlert, M. Bergenstråhle-Wohlert and L. A. Berglund, Cellulose, 2012, 19, 1821–1836 CrossRef CAS PubMed.
- S. Tanpichai, F. Quero, M. Nogi, H. Yano, R. J. Young, T. Lindström, W. W. Sampson and S. J. Eichhorn, Biomacromolecules, 2012, 13, 1340–1349 CrossRef CAS PubMed.
- C. Aulin, G. Salazar-Alvarez and T. Lindström, Nanoscale, 2012, 4, 6622–6628 RSC.
- A. Isogai, T. Saito and H. Fukuzumi, Nanoscale, 2011, 3, 71–85 RSC.
- B. Glavinchevski and M. Piggott, J. Mater. Sci., 1973, 8, 1373 CrossRef CAS.
- Y. Okita, T. Saito and A. Isogai, Biomacromolecules, 2010, 11, 1696–1700 CrossRef CAS PubMed.
- T. Saito, Y. Nishiyama, J. L. Putaux, M. Vignon and A. Isogai, Biomacromolecules, 2006, 7, 1687–1691 CrossRef CAS PubMed.
- S. Fujisawa, T. Ikeuchi, M. Takeuchi, T. Saito and A. Isogai, Biomacromolecules, 2012, 13, 2188–2194 CrossRef CAS PubMed.
- M. Henriksson, L. A. Berglund, P. Isaksson, T. Lindström and T. Nishino, Biomacromolecules, 2008, 9, 1579–1585 CrossRef CAS PubMed.
- T. Saito, T. Uematsu, S. Kimura, T. Enomae and A. Isogai, Soft Matter, 2011, 7, 8804–8809 RSC.
- H. L. Cox, Br. J. Appl. Phys., 1952, 3, 72–79 CrossRef.
- G. E. Padawer and N. Beecher, Polym. Eng. Sci., 1970, 10, 185–192 CAS.
- R. K. Shaha, D. L. Hunterb and D. R. Paul, Polymer, 2005, 46, 2646–2662 CrossRef PubMed.
- J. Lange and Y. Wyser, Packag. Technol. Sci., 2003, 16, 149–158 CrossRef CAS.
- T. V. Duncan, J. Colloid Interface Sci., 2011, 363, 1–24 CrossRef CAS PubMed.
Footnote |
† Electronic supplementary information (ESI) available: Fig. S1 shows turbidities of 2% w/v SPN dispersions before and after homogenization treatments using a mechanical homogenizer of double-cylinder type and an ultrasonic homogenizer. The inset is a photograph of the homogenized SPN dispersion standing upside down, showing transparency and high viscosity of the dispersion. In Table S1, mechanical and oxygen barrier properties of the TOCN/SPN composite films are summarized. See DOI: 10.1039/c3nr04102f |
|
This journal is © The Royal Society of Chemistry 2014 |
Click here to see how this site uses Cookies. View our privacy policy here.