Esterification of 2-keto-L-gulonic acid catalyzed by a solid heteropoly acid
Received
16th July 2012
, Accepted 25th October 2012
First published on 26th October 2012
Abstract
The efficacy of a potassium 12-phosphotungstate (KPW) catalyst in the synthesis of methyl 2-keto-L-gulonat from 2-keto-L-gulonic acid (2-KLGA) and methanol is investigated. The KPW catalyst gives high yields in short reaction times. The present procedure represents a clean, efficient, practical, simple, mild, time-saving and eco-friendly method for the synthesis of methyl 2-keto-L-gulonat. The KPW catalyst is found to be a truly heterogeneous catalyst, highly efficient and reusable in the synthesis of methyl 2-keto-L-gulonat.
1. Introduction
The 2-keto-L-gulonic acid (2-KLGA) esterification reaction plays an important role in the industrial manufacture of vitamin C.1–3 Homogeneous acid catalysts, such as sulfuric acid and heteropoly acids (HPAs), have been used for the esterification reaction.4–6 However, the use of homogeneous acid catalysts for esterification causes difficulties in recovery after the reaction has taken place and produces toxic wastewater.7 To overcome this shortcoming of homogeneous catalysts, heterogeneous catalysts have been used in esterification reactions in recent years,8 although the catalytic activity of heterogeneous catalysts is often lower than that of homogeneous catalysts.9
Heterogeneous acid catalysis by a HPA with a Keggin structure is one of the most important and growing areas of research in recent years because of its potential economic rewards and green benefits.10,11 HPAs with Keggin structures possess special characteristics that allow for their use as catalysts in esterification reactions as they have a very high intrinsic acidity.12 The catalytic acidity of HPAs is stronger than that of conventional solid acid catalysts such as acidic oxides and zeolites. The acid strength of Keggin HPAs decreases in the order: H3PW12O40 > H4SiW12O40 > H3PMo12O40 > H4SiMo12O40.13 In addition, the acid sites in HPA are more uniform and easier to control than those in other solid acid catalysts.14 Usually, phosphotungstic acid (HPW) is the catalyst of choice because of its stronger acidity, higher thermal stability and lower oxidation potential compared to phosphomolybdic acid.15 However, due to the low surface area and difficulty in the reutilization of the homogeneous tungsten HPAs, it is advisable to support tungsten HPAs on a carrier with a high surface area, such as silica, activated carbon, alumina or clays.16 Another alternative approach is to prepare HPA-salts by partially exchanging protons of the parent HPAs with large cations, such as K+ and Cs+, which have high porosity.9,15 Thus, the HPA-salt not only has a high surface area but can also be reused in the esterification of methyl 2-keto-L-gulonat.
In our present studies, potassium 12-phosphotungstate (KPW) was prepared by the partially exchanging protons process. The Keggin structure of KPW was examined by X-ray Diffraction Spectra analysis (XRD). An automated BET sorptometer was used to study the increasing surface area of the HPA-salt compared with that of HPA. The surface area of Amberlyst 15 was also characterized by a BET sorptometer. The number of acid sites in the catalyst was examined by TPD-NH3. Fourier Transform Infrared Spectroscopy (FTIR) was used to study the Keggin structure of the KPW catalyst. The catalytic activity of KPW was tested in the esterification of methyl 2-keto-L-gulonat. The aim of the present work is to compare the KPW catalyst performance with other known catalyst systems, such as the homogeneous catalyst 12-phosphotungstic acid and heterogeneous catalyst Amberlyst 15 on the esterification reaction.
2. Experimental
2.1. Materials and catalysts
Monohydrous 2-keto-L-gulonic acid (90 wt%), 12-phosphotungstic acid (H3PW12O40·21H2O) and methanol (99.5 wt%) were purchased from Sigma Aldrich. Amberlyst 15 resin was obtained from Rohm & Hass Co.
The acidic heteropoly salt (KPW) was prepared according to the literature procedure18 by adding dropwise the required amount of an aqueous solution of H3PW12O40 (0.1 M) to an aqueous saturated solution of KCl at 40 °C with stirring. The precipitate obtained was filtrated and washed with distilled water and then dried at 70 °C for 10 hours and after that in an oven at 120 °C for 5 hours.
2.2. Techniques
Powder X-ray diffraction (XRD) spectra of KPW and H3PW12O40 (HPW) were recorded on a D8 Advance diffractometer (XRD) with monochromatic Cu–Kα radiation using a Brucker Tensor 37.
The nature of the acid sites of these catalysts was determined by NH3-TPD on an Autochem 2020 (micrometric) at the temperature range of 100 °C to 600 °C at a rate of 10 °C min−1, using nitrogen as a gas carrier.
The thermal stability of the catalyst was examined by thermogravimetric/differential thermal analysis (TG/DTA) using a Perkin Elmer instrument. The samples were heated at a rate of 10 °C min−1. The TG and DTA curves were recorded.
The Brunauer–Emmett–Teller (BET) surface area and porosity of the catalysts were measured from the N2 adsorption isotherm at 77 K using a BET Sorptometer (Automated BET Sorptometer 201-A, USA).
Infrared spectra were recorded on a Brucker FTIR spectrometer with samples prepared as KBr disks in the 400–4000 cm−1 range.
The yield of the esterification reaction was determined by HPLC chromatography. HPLC was performed using a Model 1200 Agilent, a model UV (210 nm) and a C18 column.
The chemical composition of the KPW catalyst was analysed using X-ray fluorescence, XRF (Model: Bruker S4 Pioneer, USA).
2.3. Catalytic reactions
The catalytic activity of KPW was tested in 2-keto-L-gulonic acid esterification, which was carried out under atmospheric pressure in a 250 ml bottom glass reactor. The 2-KLGA was mixed with methanol at various molar ratios of 2-KLGA
:
methanol: 1
:
24, 1
:
48, 1
:
96, 1
:
192, 1
:
384, 1
:
720, 1
:
1440 (mol
:
mol−1). The mixtures were heated to 65 °C and then the catalyst was added to the 2-KLGA–methanol solutions with the weight ratio of catalyst to 2-KLGA of 1
:
10 (g
:
g−1). The esterification reaction time was started by charging the catalyst. The product of the reaction was periodically taken out at 5 min, 15 min, 30 min, 60 min, 120 min, 180 min, 240 min, 300 min, 360 min and 420 min and analyzed by HPLC analysis.
Catalyst recycling experiments were performed as follows: after the reaction, the heterogeneous KPW catalyst was recovered from solution by simple filtration. The catalyst was washed with copious amounts of methanol solvent. Then the catalyst was reused in the reaction. The efficacy on the esterification reaction when using the KPW catalyst was determined after each recycling.
2.4. Scale up reaction
Apparatus.
The experiments were performed in a 2000 ml round bottom glass reactor dipped in a constant temperature water bath. The reactor was equipped with a temperature indicator (Pt-100) and speed monitoring facility. It was also equipped with a condenser to avoid any possible loss of methanol.
Esterification reaction.
In the scaled up esterification reaction, the molar ratio of 2-KLGA
:
methanol was 1
:
24 (mol mol−1), which is the highest concentration of 2-KLGA in methanol at 65 °C. A mixture solution was prepared by mixing 200 g of a 2-keto-L-gulonic acid solution with 1000 ml of a CH3OH solution. The mixture was stirred at a rate of 500 r min−1 and heated to 65 °C. 20 g of the catalyst was then added to the mixture. The esterification reaction time was started by charging the catalyst. The products of the reaction were periodically taken out at 5 min, 15 min, 30 min, 60 min, 120 min, 180 min, 240 min, 300 min, 360 min and 420 min. The products were diluted 30 times by methanol and were analyzed by HPLC analysis.
3. Results and discussion
3.1. Chemical composition
The chemical composition of the KPW catalyst was determined by XRF analysis (as shown in Table 1). The results confirm that the potassium element is present in the catalyst structure. The presence of potassium in the catalyst structure can change the physicochemical properties of the catalyst from a homogeneous catalyst to a heterogeneous catalysts.15 From the results in Table 1, we can calculate the content of potassium ions in KPW. The structure formula of KPW is K2.2H0.8PW12O40.
Table 1 The chemical composition of the KPW catalyst
Element |
Chemical composition (%) |
W |
94.6 |
K |
3.67 |
P |
1.04 |
Se |
0.20 |
As |
0.14 |
Si |
0.122 |
Al |
0.106 |
Ge |
590 (ppm) |
V |
430 (ppm) |
3.2. Catalyst characterization
3.2.1 TG/DTA analysis.
The thermal stability of KPW was investigated by means of thermogravimetric (TG) and differential thermal analysis (DTA) (Fig. 1). The TG curve of the KPW catalyst shows that there is one weight loss step which is attributed to crystallization water desorption between room temperature to 150 °C. In the DTA curve, one endothermic peak was observed at 70 °C which associated with the mass losses observed in the TG curve. No endothermic peaks or weight losses were observed in the DTA and TG analysis between 150–600 °C. These results indicate that the KPW catalyst has a high thermal stability which can be uses in the esterification reaction of 2-KLGA and methanol.
3.2.2 Surface area.
Table 2 summarizes the results from the BET surface area measurements of the KPW, HPW and Amberlyst 15 catalysts. The specific surface area of the KPW and HPW catalysts are 96.37 m2 g−1 and 11.55 m2 g−1, respectively. The KPW catalyst shows a relatively higher specific surface area compared to the HPW catalyst. Specifically, the specific surface area of the heteropoly acid was dramatically increased from 11.55 to 96.37 m2 g−1 after the exchange process of protons and potassium cations. This is attributed to the potassium cations of the KPW, which improved the surface area of the catalyst.
Table 2 BET specific areas of HPW, KPW and Amberlyst 15 dry
|
KPW |
HPW |
Amberlyst 15 dry |
S
BET (m2 g−1) |
96.37 |
11.55 |
45.00 |
S
pores (m2 g−1) |
43.07 |
— |
— |
V
pores (cm3 g−1) |
0.06 |
— |
— |
∅
pores (nm) |
5.20 |
<2 |
25 |
3.2.3 FTIR.
The FTIR spectra of the KPW catalyst (as shown in Fig. 2) exhibits the characteristic frequencies of the Keggin structure (as shown in Fig. 3) in the range of 1100–600 cm−1. It is found that the KPW catalyst presents strong bands at 1080.7 cm−1 and 986.0 cm−1, which are characteristic of the P–Oa and W–Od absorption bands, respectively. The peaks at 891.3 cm−1 and 808.0 cm−1 are characteristic of W–Ob–W bridges (inter bridges between corner-sharing octahedra) and W–Oc–W bridges (intra bridges between edge-sharing octahedra), respectively (as shown in Fig. 2).10,11,15 The results of the FTIR spectra indicate that the Keggin structure is retained in the KPW catalyst.
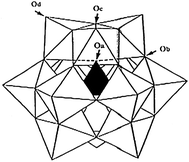 |
| Fig. 3 Keggin structure. | |
3.2.4 X-ray diffraction.
The Keggin structure of the catalyst was also confirmed using XRD analysis. Fig. 4 shows the XRD patterns of HPW (a) and KPW before use (b). The strong reflections at 2θ values of 19.8°, 26.1°, 29.5° and 36.2° were assigned to the Keggin structure of the HPW catalyst (as shown in Fig. 4(a)).17,18 The characteristic peaks of the KPW catalyst were at 2θ 21.1°, 26.2°, 30.1°, and 36.4°, which was quite similar to that of HPW, indicating that the Keggin structure was retained in the KPW catalyst (as shown in Fig. 4(b)).19 A shift in the reflections between the KPW and HPW catalysts was due to the ion exchange between a potassium ion and a proton. This behavior can be explained by the fact that the atom dimension of the potassium ion is larger than that of a proton and therefore caused the shift in the reflection.
3.2.5 Acidity measurements – TPD of NH3.
The ammonia adsorption–desorption technique usually enables the determination of the strength of the acid sites present on the catalyst surface together with the total acidity.20Fig. 5 shows the NH3-TPD profiles of HPW and KPW before use and Table 3 presents the amount of NH3 desorbed per g. It was observed that the number of strong Brönsted and Lewis acid sites of these catalysts (desorption peaks are distributed beyond 500 °C) is more than that of the weak and intermediate acid sites of the catalyst.5,21,22 In the catalyst, the number of strong acid sites is about 3 and 2.5 times as high as the number of weak and intermediate sites, respectively. It is evident from Table 3 that the total acidity for KPW is lower than that for HPW due to the ion exchange between a potassium ion and proton in the catalysts.
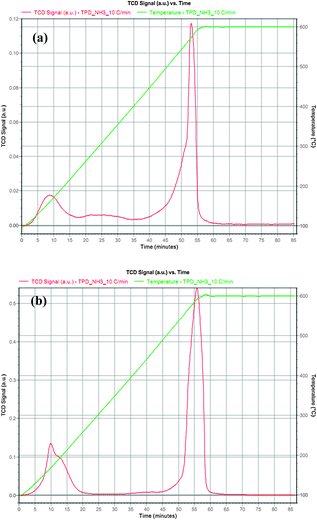 |
| Fig. 5 NH3 temperature-programmed-desorption profiles of (a) KPW and (b) HPW. | |
Table 3 Data from the NH3 temperature-programmed-desorption results of the catalysts
|
Temperature (°C) |
Concentration (mL NH3 g−1) |
Concentration (mmol NH3 g−1) |
HPW |
Peak 1 |
175.9 |
1.0367 |
0.0525 |
Peak 2 |
591.4 |
3.1022 |
0.1570 |
|
Total |
4.1389 |
0.2095 |
KPW before use |
Peak 1 |
159 |
0.1808 |
0.0092 |
Peak 2 |
297.9 |
0.0826 |
0.0042 |
Peak 3 |
578.7 |
0.6447 |
0.0326 |
|
Total |
0.9081 |
0.0460 |
3.3.2 Effect of the initial reactant molar ratios.
2-KLGA can be dissolved in methanol at 65 °C with molar ratios of 2-KLGA to methanol up to 1
:
24 (mol
:
mol−1). Therefore, the effect of the molar ratios of 2-KLGA
:
methanol on the equilibrium yield of the esterification reaction was investigated at various molar ratios of 2-KLGA
:
methanol: 1
:
24, 1
:
48, 1
:
96, 1
:
192, 1
:
384, 1
:
720 and 1
:
1440 (mol
:
mol−1). The results are presented in Fig. 7. It was found that identical results were observed with each fraction obtained. This indicated that the molar ratios of 2-KLGA
:
methanol have no effect on the equilibrium yield of the esterification reaction with ratios up to 1
:
24 (mol mol−1). In addition, by using a large excess of alcohol, the products of the esterification reaction can be directly pumped into the column of the HPLC to determine the yield of the reaction without diluting with methanol. Thus, further experiments were performed at a 2-KLGA
:
methanol molar ratio of 1
:
1440 (mol
:
mol−1).
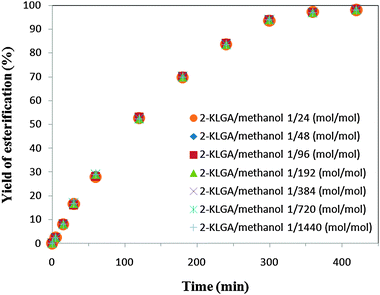 |
| Fig. 7 The yield of the esterification reaction at various molar ratios of 2-KLGA to methanol. | |
3.3.3 Catalytic activity studies.
The catalytic activity of the heterogeneous KPW catalyst was demonstrated on the esterification of 2-KLGA and compared with that of other known catalyst systems: the homogeneous HPW catalyst and commercial heterogeneous Amberlyst 15 catalyst. The yield of the esterification reaction when using different catalysts is presented in Fig. 8. From a comparison of the results between line (a) and line (b) in Fig. 8, the yield of the esterification reaction using the KPW catalyst is slightly lower than that of the esterification reaction using the homogeneous HPW catalyst. In return, the heterogeneous process is an environmentally friendly process and greatly minimizes the steps needed for the separation and recovery of the product.5,14,24,25 In a comparison of the results between line (b) and line (c) in Fig. 8, the yield of the esterification reaction using the commercial heterogeneous KPW catalyst is slight higher than that of the reaction using the heterogeneous Amberlyst catalyst. Thus, due to the useful properties of the KPW catalyst, it can be regarded as a good heterogeneous catalyst for the esterification of 2-KLGA.
3.3.4 Heterogeneity catalyst.
In order to prove that the esterification reaction of 2-KLGA using KPW catalysts is truly a heterogeneous process, we investigated the yield of the esterification reaction with and without filtration of the KPW catalyst. Fig. 9(a) shows that the yield of the esterification reaction using the KPW catalyst depends on time. Another esterification reaction of 2-KLGA was carried out with the KPW catalyst at 120 minutes. The KPW catalyst was filtered out of the reaction mixture and then the reaction was resumed with the filtrate, in the absence of any externally added catalyst. The results on the yield of the reaction are shown in Fig. 9(b). From Fig. 9(a) it was observed that the yield of the reaction using the KPW catalyst increases with increasing time. From the result in Fig. 9(b), the yield of the reaction also tended to increase with increasing time from 0 to 120 min. There was no increase in the yield of the esterification after filtration of the KPW catalyst from 120 to 300 min. These results prove that the KPW catalyst is a real heterogeneous catalyst.
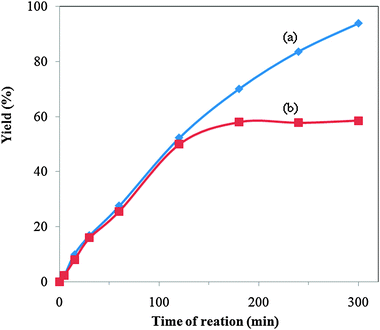 |
| Fig. 9 Evaluation the catalytic heterogeneity of the KPW catalyst: (a) the esterification reaction when using the KPW catalyst, (b) the esterification reaction with the filtrate of the KPW catalyst after 120 min. | |
3.3.5 Catalyst recycling.
To investigate the catalyst recycling, the KPW catalyst, used in the first cycle of the esterification reaction for 300 min, was separated by filtration, washed with methanol and dried 100 °C for 3 h and returned to a fresh reaction mixture under identical conditions as the first cycle. The reaction was repeated to check the second and the third cycle of the KPW catalyst. The results of initial rates of esterification are shown in Fig. 10. There was no difference in the initial rate of the esterification reaction between each cycle, meaning that the KPW catalysts possess high stability. Thus, the KPW catalyst can be reuses in the esterification reaction of 2-KLGA.
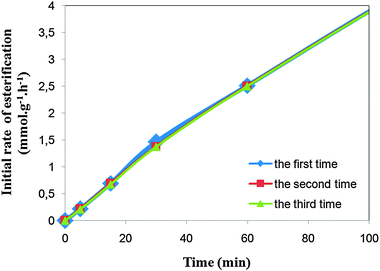 |
| Fig. 10 The effect of time on the initial rate of esterification in three cycles. | |
Fig. 11 shows the XRD patterns of the KPW catalyst after recycling 3 times. It was found that the characteristic peaks of KPW after recycling 3 times also tended to be the same as those of the fresh KPW. There was no difference in the reflections between the KPW catalyst before and after recycling 3 times, indicated that the KPW catalyst can be recycled in the esterification reaction of 2-KLGA.
3.3.6 Scale up esterification reaction.
Fig. 12 shows the yield of the esterification reaction with and without scale up. From a comparison of the results between line (a) and line (b) in Fig. 12, the equilibrium yield of the scaled up reaction is 96% at 360 min, which is quite similar to that of the esterification reaction without scale up, indicating that with scale up, the esterification reaction did not affect the equilibrium condition of the reaction.
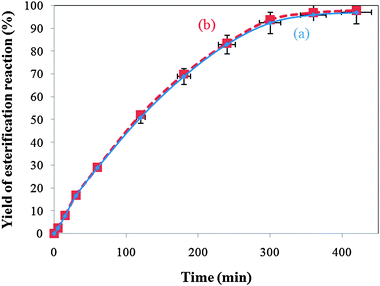 |
| Fig. 12 Yield of the esterification reaction using the KPW catalyst with and without scale up: (a) with scale up; (b) without scale up. | |
4. Conclusion
The KPW catalyst was successfully synthesised by an ion exchange process between a potassium ion and proton. It was found that the KPW catalyst shows a high efficiency for the esterification of 2-KLGA. The KPW catalyst is a real heterogeneous catalysts in the esterification reaction. The catalytic activity of the heterogeneous KPW catalyst is slightly lower than that of the homogeneous HPW catalyst and is approximate to that of the commercial heterogeneous Amberlyst catalyst. The KPW catalysts are effective, environmentally friendly and recyclable. The present procedure also represents a clean, practical, simple and mild method for the esterification of 2-KLGA with excellent equilibrium yields of approximately 96% at 360 min.
Acknowledgements
This work was supported by the National Key Programs on Research of the sciences and technology for developing the pharmaceutical industry to 2020 of the Ministry of Industry and Trade, Vietnam.
References
- A. C. Blaga and T. Malutan, J. Chem. Eng. Data, 2011, 57, 431 CrossRef.
- J. J. Giovanno, Proc. Natl. Acad. Sci. U. S. A., 2007, 104, 9109 CrossRef.
-
J. C. Hubbs, Patent US, No. 6,022,719, 2000 Search PubMed.
- M. N. Timofeeva, R. I. Maksimovskaya, E. A. Paukshtis and I. V. Kozhevnikov, J. Mol. Catal. A: Chem., 1995, 102, 73 CrossRef CAS.
- Y. Liu, E. Lotero and J. G. Goodwin, Jr., J. Catal., 2006, 242, 278 CrossRef CAS.
- J. M. Marchetti and A. F. Errazu, Biomass Bioenergy, 2008, 32, 892 CrossRef CAS.
- B. Y. Xu, H. J. Shang, X. M. Zheng and J. Hebei, Indian J. Sci. Technol., 2006, 23, 193 CAS.
- A. P. L. de Meireles, A. K. da Silva Rocha, V. I. Kozhevnikov and V. E. Gusevskaya, Appl. Catal., A, 2011, 409–410, 82 CrossRef CAS.
- M. A. Alsalme, V. P. Wiper, Z. Y. Khimyak, F. E. Kozhevnikova and V. I. Kozhevnikov, J. Catal., 2010, 276, 181 CrossRef.
- F. Bamoharram, Molecules, 2009, 14, 3214 CrossRef CAS.
- C. Rocchiccioli-Deltcheff, R. Thouvenot and R. Franck, Spectrochim. Acta, Part A, 1976, 32, 587 CrossRef.
- V. I. Kozhevnikov, Catal. Rev. Sci. Eng., 1995, 37, 311 Search PubMed.
- T. Okuhara, N. Mizuno and M. Misono, Adv. Catal., 1996, 41, 113 CrossRef CAS.
- I. V. Kozhevnikov, J. Mol. Catal. A: Chem., 2009, 305, 104 CrossRef CAS.
- E. Rafiee, M. Joshaghani, F. Tork, A. Fakhri and S. Eavani, J. Mol. Catal. A: Chem., 2008, 283, 1 CrossRef CAS.
- R. L. Pizzio, V. C. Cáceres and N. M. Blanco, Appl. Catal., A, 1998, 167, 283 CrossRef.
- B. B. Bardin and J. R. Davis, Appl. Catal., A, 2000, 200, 219 CrossRef CAS.
- Y. Zhang and S. Yang, J. Wuhan Univ. Technol., Mater. Sci. Ed., 2008, 23, 346 CrossRef CAS.
- G. M. Brown, M. R. Noe-Spirlet, W. R. Busing and H. A. Levy, Acta Crystallogr., Sect. B: Struct. Crystallogr. Cryst. Chem., 1977, 1038 CrossRef CAS.
- G. Sunita, M. B. Devassy, A. Vinu, P. D. Sawant, V. V. Balasubramanian and B. S. Halligudi, Catal. Commun., 2008, 9, 696 CrossRef CAS.
- Z. Zhu and W. Yang, J. Phys. Chem. C, 2009, 113, 17025 CAS.
- F. Chambon, F. Rataboul, C. Pinel, A. Cabiac, E. Guillon and N. Essayem, Appl. Catal., B, 2011, 105, 171 CrossRef CAS.
- B. Xu, X. Zheng, W. Zhang, X. Zhang, Z. Zhang and H. Shang, Transactions of Tianjin University, 2008, 14, 37 CrossRef CAS.
- M. J. Marchetti and F. A. Errazu, Fuel, 2008, 87, 3477 CrossRef.
- W. Zhang, Y. Leng, D. Zhu, Y. Wu and J. Wang, Catal. Commun., 2009, 11, 151 CrossRef CAS.
|
This journal is © The Royal Society of Chemistry 2013 |
Click here to see how this site uses Cookies. View our privacy policy here.