DOI:
10.1039/C2RA22218C
(Paper)
RSC Adv., 2012,
2, 12337-12345
Synthesis and catalytic activity of mesostructured KF/CaxAl2O(x+3) for the transesterification reaction to produce biodiesel†
Received
19th September 2012
, Accepted 12th October 2012
First published on 12th October 2012
Abstract
A novel kind of highly efficient solid base, mesostructured KF/CaxAl2O(x+3), has been successfully fabricated via a new solvent-evaporation strategy followed by a KF impregnation process and the effects of the synthetic parameters of mesostructured KF/CaxAl2O(x+3) on the catalytic properties in the transesterification reaction of soybean oil with methanol for the production of a clean and green alternative fuel – biodiesel have been investigated in detail. It was found that the catalyst, 30KF/m-CaAl4(700)-700-3, with a Al/Ca molar ratio of 4, KF·2H2O loading amount of 30%, activated at 700 °C for 3 h, was the most efficient catalyst among those synthesized in this study due to its high total active basicity and basic strength. Compared to the traditional solid basic catalyst CaO, under the optimized reaction condition, the reaction catalyzed by the prepared 30KF/m-CaAl4(700)-700-3 catalyst with the unique mesoporous structure and large amount of super basic sites showed much higher reaction rate and TOF value in the initial 1 h, a comparable biodiesel yield of about 98% in 5 h, and near 100% selectivity for FAME. Also importantly, the Ca leaching amount with 30KF/m-CaAl4(700)-700-3 is far lower than that with CaO and meets the EN14214 standard. Therefore, this engineered mesostructured KF/CaxAl2O(x+3) provides an efficient catalytic platform for a green biodiesel production process.
1. Introduction
Biodiesel, obtained from renewable biological sources such as vegetable oils or animal fats, is a sort of environmentally friendly and renewable energy with low emission that can replace fossil diesel without substantial engine modification.1,2 The main content of biodiesel is C12–C22 fatty acid monoalkyl esters (FAME), fabricated mainly by the transesterification reaction of triglycerides obtained from renewable sources with short-chain alcohols such as methanol, ethanol and etc.1–3 However, it is difficult to obtain biodiesel from triglycerides transesterification with alcohols under normal mild conditions unless a catalyst or high pressure/temperature is applied. Therefore, it is highly significant to exploit catalysts which are effective in catalyzing the transesterification reaction of triglycerides with alcohols for a high yield of biodiesel.
At present, there are three kinds of catalysts for the transesterification reaction: enzymes, acids and bases.4 Enzymes are too expensive to be used in industry while acids are not suitable for industrial application either, due to the severe reaction conditions needed, such as high reaction temperature/pressure, high molar ratio of alcohol to oil as well as long reaction time.5 Presently, homogeneous bases are utilized as efficient catalysts in industry with high biodiesel yield. However, there are still many problems with them, such as corrosiveness, difficult catalyst separation from the biodiesel product and consequent poor circulation, and so on.6 To solve these problems, much attention has been paid to solid bases with high catalytic performance but without the above drawbacks.7–10 However, the solid bases have their own drawbacks such as leaching of active components, low activity under mild conditions, and high alcohol to oil ratio and catalyst amount, as well as long reaction duration, required for high yield, compared to homogeneous ones.11,12 Hence, the development of more active solid bases is urgently needed.
Metal oxides, especially alkali earth oxides have been studied extensively because of their suitable basic strength.13–16 Among them, calcium oxide has attracted much attention due to its abundant, low-cost and low toxic resources.17 However, the leaching of CaO during the transesterification reaction is very serious,18 resulting in a high content of Ca in the obtained biodiesel which cannot meet the standard of EN14214 and needs post-treatment. Zabeti et al. have found that loading CaO on Al2O3 can reduce the amount of Ca species leached into biodiesel because of the interaction between CaO and Al2O3,12,19 which suggested a good way to partially solve the leaching problem though the content of Ca in biodiesel (31 mg kg−1) was still much higher than the standard (5 mg kg−1) in EN14214. Later, Campos-Molina et al. investigated the catalytic activity of mayenite Ca12Al14O33 for the transesterification reaction of sunflower oil with methanol and came to a conclusion that mayenite is almost inactive.20 Gao et al. found that Ca–Al mixed-oxides obtained from Ca–Al hydrotalcites became very active after loading KF in the transesterification reaction of Palm oil with methanol due to the active species produced by the reaction between KF and Ca–Al mixed oxides. However, no leaching data was given in their report.21 Hence, a combination between KF and CaxAl2O(x+3) might be a good choice for both high activity and suppressed Ca leaching.
As we know, a good solid base catalyst should not only possess suitable basic strength but also enough basic active sites.22 Mesoporous materials have been widely used in catalysis either as catalysts23 or as carriers of active species24,25 because of their extensive nanoporous structure and high specific surface area (∼1500 m2 g−1), that can highly disperse the active species in their mesoporous network and thus provide large density of active sites. In addition, their large and uniform pore sizes (1.5–10 nm) and high pore volume are greatly beneficial for the transport of reactants and products, especially for large molecules.26,27 As triglyceride molecules in oils are relatively large, here we design a mesostructured KF/CaxAl2O(x+3) composite by loading/dispersing KF into the pore network of mesoporous CaxAl2O(x+3), hopefully to obtain high catalytic activity for the transesterification reaction of triglycerides with methanol with minimized Ca leaching.
There have been a few reports on the preparation of mesoporous CaxAl2O(x+3).28–34 Among them, two reports gave the detailed synthetic steps in which the prepared materials have well-defined mesoporous structure with high surface areas, uniform pore sizes and homogeneous framework compositions, but both of which had extremely low calcium content (the molar ratio of aluminum to calcium (Al/Ca) is about 9
:
1), and no catalytic properties were reported.33,34
Herein, we report the successful preparation of mesoporous CaxAl2O(x+3) (0 < x ≤ 1) with different molar ratios of aluminum to calcium (Al/Ca) as well as different calcination temperatures, and further explored their application as catalysts or supports in the transesterification reaction to produce biodiesel. From the literature, it was shown that the basicity of the catalyst is strongly influenced by the composition of supports, loading amount of KF, activation temperature and duration.35 Therefore, a set of experiments was designed to investigate the effects of the various material parameters aforementioned and reaction conditions on the catalytic properties of the generated catalyst in the transesterification reaction, which finally resulted in optimized catalyst composition, structure and reaction conditions for a high yield of biodiesel by the transesterification reaction.
2. Experimental
2.1 Synthesis of catalyst
The mesostructured KF/CaxAl2O(x+3) (0 < x ≤ 1) catalysts were prepared by a two-step route: the synthesis of mesoporous CaxAl2O(x+3) (0 < x ≤ 1) and loading KF in them.
2.1.1. Synthesis of mesoporous CaxAl2O(x+3) (0 < x ≤ 1).
The mesoporous CaxAl2O(x+3) (0 < x ≤ 1) was synthesized via solvent evaporation33 as follows: typically, 2.0 g of Pluronic P123 (BASF) and a certain amount of calcium nitrate tetrahydrate (≥99%, Alfa Aesar) were dissolved in 20.0 ml of anhydrous ethanol (≥99.7%, Shanghai Zhenxing Co.) and stirred for 4 h. Then, a certain amount of aluminum isopropoxide (>98%, Acros Organics) was dissolved in a mixture of 3.2 ml of 68 wt% nitric acid (65%–68%, Shanghai Lingfeng Co.) and 10.0 ml of anhydrous ethanol. Once dissolved, the two solutions were mixed together and 10.0 ml of anhydrous ethanol was used to transfer the aluminum isopropoxide solution thoroughly. The mixture was stirred for another 5 h and was then put into a 60 °C oven for 48 h to undergo the solvent evaporation. After that, the resultant solid was calcined at 450 °C, 700 °C, and 900 °C for 4 h with a heating rate of 1 °C min−1 to obtain the final mesoporous CaxAl2O(x+3) (0 < x ≤ 1). For the synthesis of all the mesoporous CaxAl2O(x+3) (0 < x ≤ 1), the total quantity of metal species was kept constant at 20 mmol while changing the molar ratio of Al/Ca from 9
:
1, 4
:
1 to 2
:
1. The samples are denoted as m-CaAly(a), where ‘m-CaAly’ stands for mesoporous CaxAl2O(x+3) (0 < x ≤ 1), ‘y’ is Al/Ca ratio and ‘a’ is the calcination T/°C.
2.1.2. Synthesis of mesostructured KF/CaxAl2O(x+3) (0 < x ≤ 1).
The KF/m-CaAly(a) were prepared as follows: m-CaAly(a) were wetted by KF·2H2O (≥99%, Sinopharm Chemical Reagent Co.) aqueous solution with different concentrations corresponding to the loading amounts of KF·2H2O to m-CaAly(a) (20%, 30%, and 40%) by incipient wetness impregnation. The obtained composites were placed static for 6 h after ultrasonic oscillation for 10 min, and then further dried at 120 °C overnight after the water was evaporated under reduced pressure in a rotary evaporator at 40 °C. Prior to use, the products were activated by calcining at different temperatures (500 °C, 600 °C, 700 °C and 800 °C) for several hours (1 h, 3 h and 5 h). The samples are denoted as zKF/m-CaAly(a)-b-c, where ‘m-CaAly(a)’ has the same meaning as above and ‘z’, ‘b’ and ‘c’ are the nominal weight amounts (%) of loaded KF·2H2O to m-CaAly(a), activation temperatures (°C) and durations (h), respectively.
2.2 Characterization
X-Ray diffraction (XRD) patterns were recorded on a Rigaku D/Max 2200PC diffractometer with Cu-Kα radiation (40 kV and 40 mA), a scanning rate of 4° min−1 for wide-angle tests and 0.4° min−1 for small-angle tests. N2 adsorption/desorption measurements were performed by using a Micromeritics Tristar 3000 at 77 K and the mesoporous specific surface area, pore size distribution were calculated using the Brunauer–Emmett–Teller (BET) and Barrett–Joyner–Halenda (BJH) methods, respectively. Transmission electron microscopy (TEM) images and field emission scanning electron microscopic (FE-SEM) images were obtained by a JEOL-2010F electron microscope operating at 200 kV and a Hitachi S-4800, respectively. The electron probe micro-analysis (EPMA) was carried out on a JXA-8100 and carbon dioxide temperature-programmed desorption (CO2-TPD) was performed on a CHEM BET-3000 instrument (Quanta Chrome, USA). About 50 mg of sample was put into a quartz “U” tube and pretreated under a helium stream at 500 °C for 1 h (10 °C min−1, 80 ml min−1). The sample was then cooled to 100 °C, and at this temperature a flow of mixed gas of CO2 and helium (80 ml min−1) was subsequently introduced into the quartz “U” tube for 1 h. Then the temperature was raised to 120 °C and the gas flow was changed to the helium gas flow again for 1 h to remove loosely adsorbed carbon dioxide molecules from the catalyst surface. The sample was then heated to 910 °C under helium flow (80 ml min−1) to desorb CO2, which was detected using an online thermal conductivity detector.
2.3 Transesterification reactions
The transesterification reaction of soybean oil with methanol was carried out in a three-necked flask equipped with a condenser and a magnetic stirrer under mild conditions: stirring at 200 rpm, atmospheric pressure and at 60 °C without protecting gas. Typically, 5.0 g of soybean oil (edible oil from the local supermarket), 0.8 g of methyl laurate (internal standard, >98%, TCI) and a specified volume of methanol (≥99.5%, Shanghai Lingfeng Co.) were added into the flask. Then, a certain amount of catalyst was added into the above mixture after it reached 60 °C. The product was collected with a micro syringe per hour and analyzed by a GC-MS (Agilent, 6890/5973N). The injector and detector temperatures were maintained at 240 °C and 260 °C, respectively. The oven temperature was increased to 195 °C from 60 °C at a heating rate of 5 °C min−1 and further to 205 °C at 1 °C min−1. The yield of biodiesel, turnover frequency (TOF) and reaction rate (r) were determined by the eqn (1), (2) and (3), respectively. The leaching of Ca species of catalysts into biodiesel was evaluated by measuring the Ca concentration in the biodiesel after evaporating methanol with ICP-OES (Vista AX). | Yield (%) = actual weight of total FAME × 100%/weight of soybean oil | (1) |
| TOF = actual mole amount of total FAME/(fm × mcata × t) | (2) |
| r = actual mole amount of total FAME/(mcata × t) | (3) |
The actual weight and mole amount of total FAME (fatty acid methyl esters) were decided by the result of GC-MS; fm was the surface mole amount of active basic sites, estimated by CO2-TPD;36mcata and t were the mass of the catalyst and the reaction time, respectively.
3. Results and discussion
3.1 Structural characterization
3.1.1. Mesoporous CaxAl2O(x+3) (0 < x ≤ 1).
The XRD diffraction patterns of m-CaAly(a) are shown in Fig. 1. From the figure, we can see that ordered m-CaAl9(a) materials have been obtained at the calcination temperatures from 450 to 900 °C, but only m-CaAl9(900) is crystalline. However, it seems that m-CaAl9(900) is less ordered in both mesoporous and lattice structures than m-Al2O3(900) (Fig. S1, ESI†) due to the partial replacement of Al by Ca. m-CaAl4(450) shows a partially ordered mesoporous structure which almost totally collapsed at elevated temperatures of samples m-CaAl4(700) and m-CaAl4(900), and only the m-CaAl4(900) framework has crystallized. None of the m-CaAl2(a) series has an ordered mesoporous structure and only m-CaAl2(900) has a crystallized CaAl2O4 wall. So we come to the conclusion that m-CaAly(a) possesses an ordered mesoporous structure mainly at the Al/Ca ratio = 9
:
1 or higher and a relatively high calcination temperature of 900 °C can result in the framework crystallization of m-CaAly(a).
 |
| Fig. 1 Wide angle and corresponding small angle (insets) XRD patterns of: (a) m-CaAl9, (b) m-CaAl4 and (c) m-CaAl2. (•) CaAl9; (▽) CaAl4O7; (♦) CaAl2O4. The numbers in each figure are the calcination temperatures (°C). | |
Fig. 2 shows the N2 sorption isotherms and pore-size distributions of m-CaAly(a). All adsorption–desorption curves exhibit typical type IV isotherms with a H1 hysteresis loop except for those of m-CaAl4(900) and the m-CaAl2(a) series. The corresponding pore-size distributions indicate that all the m-CaAly(a) samples have mesopores of around 7 nm in diameter except for m-CaAl4(900) and the m-CaAl2(a) series, which possess the most probable mesoporous diameters of around 20 nm and 40 nm. Therefore it is clear that all samples except m-CaAl4(900) and the m-CaAl2(a) series have well-defined mesoporous structures, and all textural parameters can be found in Table 1. Both the specific surface area and pore volume of m-CaAly(a) decrease with the increase of calcination temperature and the content of calcium especially at the calcination temperature of 900 °C and Al/Ca molar ratio of 2, which agree well with the XRD diffraction patterns. It may be the big difference of atomic radius (0.54 Å) between Al (1.43 Å) and Ca (1.97 Å) that makes the mesoporous structure of CaxAl2O(x+3) (0 < x ≤ 1) less ordered and partially collapsed at high contents of calcium and especially when calcined at elevated temperatures.
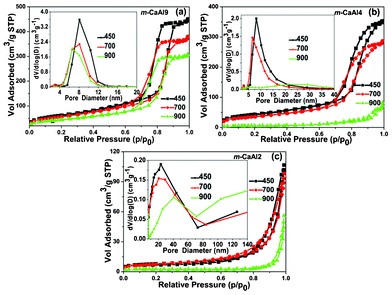 |
| Fig. 2 N2 adsorption–desorption isotherms and their corresponding pore-size distributions (insets) of (a) m-CaAl9, (b) m-CaAl4 and (c) m-CaAl2. The numbers in each figure are the calcination temperatures (°C). | |
Table 1 Texture properties of m-CaAly(a) (y: the molar ratios of Al/Ca; a: the calcination temperatures (°C))
Materials |
S
BET (m2 g−1) |
V
BJH (cm3 g−1) |
D
BJH (nm) |
m-CaAl9(450) |
226 |
0.70 |
8.07 |
m-CaAl9(700) |
206 |
0.59 |
8.07 |
m-CaAl9(900) |
162 |
0.48 |
6.56 |
m-CaAl4(450) |
156 |
0.55 |
8.21 |
m-CaAl4(700) |
130 |
0.44 |
6.58 |
m-CaAl4(900) |
20.9 |
0.13 |
21.5 |
m-CaAl2(450) |
27.6 |
0.16 |
22.6 |
m-CaAl2(700) |
27.1 |
0.15 |
20.3 |
m-CaAl2(900) |
8.6 |
0.087 |
40.4 |
TEM and SEM images of m-CaAly(700) are shown in Fig. 3 as representatives. We can see that m-CaAl9(700) has an ordered mesoporous structure while that of m-CaAl4(700) is disordered and only a few big mesopores can be found in m-CaAl2(700). Further EPMA tests confirmed that Ca and Al species were distributed homogeneously throughout sample m-CaAly(700) and there was no separated Ca- or Al-rich species detected.
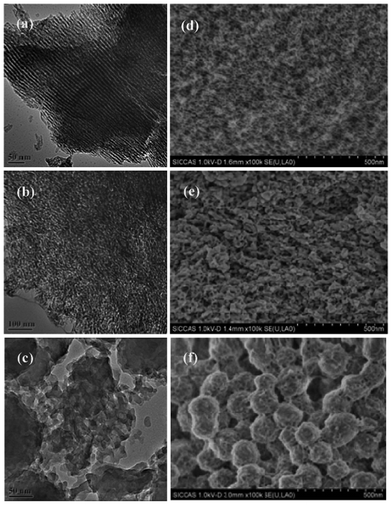 |
| Fig. 3 TEM (a-c) and SEM (d-f) images of (a, d) m-CaAl9(700), (b, e) m-CaAl4(700), and (c, f) m-CaAl2(700). | |
From the above result, it can be seen that the m-CaAly(700) series have similar textural properties to those of the m-CaAly(450) series (Fig. 1, Fig. 2 and Table 1), much better than those of the m-CaAly(900) series. Hence, in the next section, the m-CaAly(700) series are used as catalyst supports.
3.1.2.
zKF/m-CaAly(700)-b-c.
The XRD diffraction patterns of zKF/m-CaAly(700)-b-c are shown in Fig. 4. Fig. 4(a) shows that there are some new peaks belonging to active species KCaF3 and KCaCO3F21,37 and by-product CaF2 (PDF-# 35-0816) formed due to the reaction between KF and m-CaAly(700) supports after KF loading. However these peaks are strongly broadened probably due to their very small size and low content. In Fig. 4(b), the 20KF/m-CaAl4(700)-b-3 series have similar XRD diffraction patterns except for 20KF/m-CaAl4(700)-800-3 presenting strong peaks belonging to CaAl12O33 (PDF-# 09-0413), which can also be seen in the XRD patterns of 20KF/m-CaAl4(700)-600-3 and 20KF/m-CaAl4(700)-700-3 though they are much weaker. In Fig. 4(c), some new peaks belonging to other active species CaAl2(F,OH)8 (20.4°, 42.4°, 49.6°, 50.3°) (PDF-# 05-0307) and CaAlF5 (25.4°, 31.8°, 52.6°) (PDF-# 20-0197)21,37 in sample 30KF/m-CaAl4(700)-700-3 can be found as compared to 20KF/m-CaAl4(700)-700-3 probably due to the higher KF loading amount. In the pattern of 40KF/m-CaAl4(700)-700-3, the peaks belonging to CaAl12O33 (PDF-# 09-0413) become a little stronger compared to those of 30KF/m-CaAl4(700)-700-3 and 20KF/m-CaAl4(700)-700-3. Fig. 4(d) shows that all the 30KF/m-CaAl4(700)-700-c samples have similar XRD diffraction patterns which can be indexed to active species (KCaF3, KCaCO3F, CaAl2(F,OH)8 and CaAlF5), by-product CaF2 (PDF-# 35-0816) and CaAl12O33 (PDF-# 09-0413).
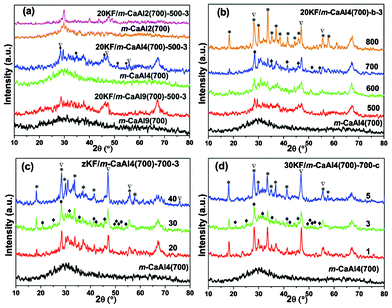 |
| Fig. 4 Wide angle XRD patterns of (a) 20KF/m-CaAly(700)-500-3 and the corresponding m-CaAly(700) supports (y = 2, 4, 9, the molar ratio of Al/Ca); (b) m-CaAl4(700) and 20KF/m-CaAl4(700)-b-3 (b = 500, 600, 700 and 800 °C, the activation temperatures); (c) m-CaAl4(700) and zKF/m-CaAl4(700)-700-3 (z = 20, 30, 40, the loading amounts (%) of KF·2H2O) and (d) m-CaAl4(700) and 30KF/m-CaAl4(700)-700-c (c = 1, 3, 5 h, durations of activation at 700 °C). (♦) Active species (KCaF3, KCaCO3F, CaAl2(F,OH)8 and CaAlF5); (▽) CaF2; (*) Ca12Al14O33. | |
The overall mesoporosity of as-prepared zKF/m-CaAly(a)-b-c is shown in Fig. 5 and the corresponding textural parameters are summarized in Table 2. In Fig. 5(a), it is indicated that all 20KF/m-CaAly(700)-500-3 samples have well-defined mesopore size distributions at around 3.7 nm in diameter except for 20KF/m-CaAl2(700)-500-3, the mesoporous structure of which has almost collapsed. Comparing the texture properties of 20KF/m-CaAly(700)-500-3 (Table 2) with those of m-CaAly(700) (Table 1), it was found that all the parameters of mesoporous structure became smaller, which is understandable and can be attributed to the KF loading in the pore channels and the partial collapse of the mesoporous structure caused by the reactions between KF and supports. Fig. 5(b), (c) and (d) show that all the zKF/m-CaAl4(700)-b-c series samples, except for 20KF/m-CaAl4(700)-800-3, have two sets of mesopores, one is mesopores of around 5 nm in diameter and the other is interparticle voids of tens of nanometers in size. As expected, both the specific surface area and pore volume of the nanocomposites (Table 2) decrease significantly at increased activation temperatures, durations and loading amounts of KF·2H2O due to the particle/crystallite growth in the framework, the mesoporous structure collapse and the pronounced reactions between KF and supports.
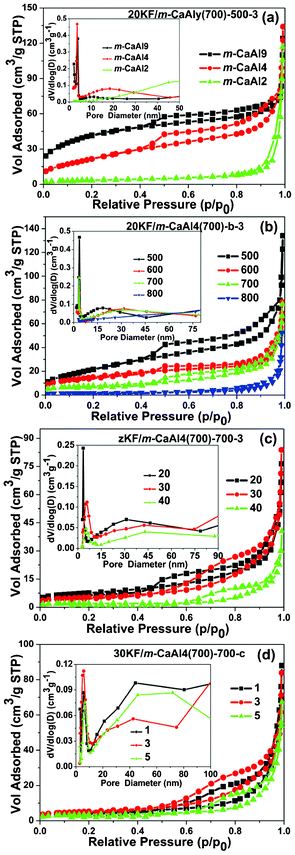 |
| Fig. 5 N2 adsorption–desorption isotherms and their corresponding pore-size distributions (insets) of (a) 20KF/m-CaAly(700)-500-3 (y = 2, 4, 9, the molar ratio of Al/Ca); (b) m-CaAl4(700) and 20KF/m-CaAl4(700)-b-3 (b = 500, 600, 700 and 800 °C, the activation temperatures); (c) m-CaAl4(700) and zKF/m-CaAl4(700)-700-3 (z = 20, 30, 40, the loading amounts (%) of KF·2H2O) and (d) m-CaAl4(700) and 30KF/m-CaAl4(700)-700-c (c = 1, 3, 5 h, durations of activation at 700 °C). | |
Table 2 Textural properties of zKF/m-CaAly(700)-b-c composites (z: the loading amounts (%) of KF·2H2O; y: the molar ratios of Al/Ca; b: activation temperatures and c: durations of activation)
Materials |
S
BET (m2 g−1) |
V
BJH (cm3 g−1) |
D
BJH (nm) |
20KF/m-CaAl9(700)-500-3 |
153.1 |
0.17 |
3.90 |
20KF/m-CaAl4(700)-500-3 |
81.8 |
0.21 |
3.59 |
20KF/m-CaAl2(700)-500-3 |
12.6 |
0.18 |
— |
20KF/m-CaAl4(700)-600-3 |
55.3 |
0.13 |
3.56 |
20KF/m-CaAl4(700)-700-3 |
26.7 |
0.12 |
3.34 |
20KF/m-CaAl4(700)-800-3 |
5.56 |
0.08 |
— |
30KF/m-CaAl4(700)-700-3 |
18.7 |
0.13 |
5.79 |
40KF/m-CaAl4(700)-700-3 |
6.6 |
0.06 |
5.27 |
30KF/m-CaAl4(700)-700-1 |
16.3 |
0.14 |
5.65 |
30KF/m-CaAl4(700)-700-5 |
11.8 |
0.10 |
6.71 |
The basicity of as-prepared zKF/m-CaAly(700)-b-c was measured by CO2-TPD and the TPD profiles are shown in Fig. 6. In all cases, two broad desorption bands can be observed. One is between 150 °C and 500 °C due to the interaction of CO2 with the weak and moderate basic sites while the other is between 520 °C and 900 °C due to the interaction of CO2 with the strong basic sites (520 °C to 710 °C) and super basic sites (710 °C to 900 °C) present in the catalysts.22,38–40 From Fig. 6(a), it can be seen that the amount and desorption temperature at the peak maxima of the super basic sites increase at elevated activation temperature while the amounts of weak, moderate and strong basic sites decrease except for 20KF/m-CaAl4(700)-800-3 which has lost its most super basic sites because of the formation of inactive by-products such as Ca12Al14O33 and/or the accompanying severe structure collapse, in accordance with the XRD analysis. This probably means that part of the weak, moderate and strong basic sites have transformed into super basic sites and the basic strength of super basic sites increased when the activation temperature was raised from 500 °C to 700 °C due to the reaction that happened at the increased temperatures. Fig. 6(b) shows that the zKF/m-CaAl4(700)-700-3 series have a similar total quantity of weak and moderate basic sites while the total quantity of strong and super basic sites of 30KF/m-CaAl4(700)-700-3 is a little higher than that of 20KF/m-CaAl4(700)-700-3 with the ratio of the peak areas of the second broad desorption bands between 30KF/m-CaAl4(700)-700-3 and 20KF/m-CaAl4(700)-700-3 being 1.17
:
1. Moreover, the CO2 desorption temperature at the peak maxima of super basic sites of 30KF/m-CaAl4(700)-700-3 (838 °C) is higher than that of 20KF/m-CaAl4(700)-700-3 (806 °C). These indicate that stronger basic strength and higher density of strong and super basic sites are present in 30KF/m-CaAl4(700)-700-3 than in 20KF/m-CaAl4(700)-700-3. However, the TPD profile of 40KF/m-CaAl4(700)-700-3 is unusual, with much more strong basic sites and fewer super basic sites than those of 30KF/m-CaAl4(700)-700-3, maybe also due to the formation of inactive by-products like Ca12Al14O33, as shown in the XRD analysis, and/or the mesoporous structure collapse. The profiles in Fig. 6(c) show that 30KF/m-CaAl4(700)-700-c series have almost the same desorption temperature at the peak maxima of the super basic sites and total quantity of strong and super basic sites with the ratio of the peak areas of the second broad desorption bands among 30KF/m-CaAl4(700)-700-1, 30KF/m-CaAl4(700)-700-3 and 30KF/m-CaAl4(700)-700-5 being 1
:
1.011
:
1.053, which means the basic strength and total quantity of strong and super basic sites of these catalysts are almost independent of activation durations from 1 to 5 h.
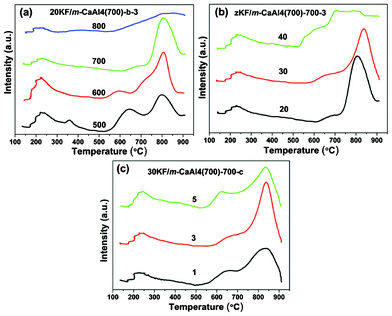 |
| Fig. 6 CO2-TPD profiles of (a) 20KF/m-CaAl4(700)-b-3 (b = 500, 600, 700 and 800 °C, the activation temperatures); (b) zKF/m-CaAl4(700)-700-3 (z = 20, 30, 40, the loading amounts (%) of KF·2H2O) and (c) 30KF/m-CaAl4(700)-700-c (c = 1, 3, 5 h, durations of activation at 700 °C). | |
3.2 Catalytic activity of zKF/m-CaAly(700)-b-c
We evaluated the catalytic properties of all prepared m-CaAly(a) supports as well as m-Al2O3 and KF·2H2O for the transesterification reaction. It was found that all of them showed neglectable catalytic activity, which is consistent with the previous reports21,37,41 and the above SEM/EPMA result that there is no isolated and active CaO present in m-CaAly(a).21 Hence, the catalytic activity of the KF-loaded composites, zKF/m-CaAly(700)-b-c, will be investigated in detail by probing the effect of the parameters ‘z’, ‘y’, ‘b’ and ‘c’ in the formula on the catalytic performance. All the transesterification reactions (Scheme 1) were performed at a fixed alcohol to oil molar ratio (A/O) of 12
:
1 and catalyst amount of 3 wt% with respect to oil mass.
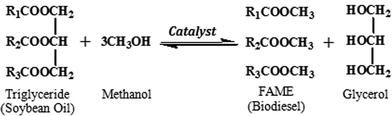 |
| Scheme 1 The transesterification reaction between soybean oil and methanol (FAME: fatty acid methyl esters). | |
3.2.1. Effect of the molar ratio of aluminum to calcium.
The effect of the molar ratio of aluminum to calcium (‘y’) on the catalytic activity of 20KF/m-CaAly(700)-500-3 has been investigated and the result is shown in Fig. 7(a). It can be seen that the highest yield of biodiesel can be obtained at y of 4. When using m-CaAl9(700) as the support, lower amounts of active species (CaAlF5, CaAl2 (F,OH)8, KCaF3 and KCaCO3F)21,37 were produced due to the lower calcium content in m-CaAl9(700). For sample m-CaAl2(700), because of its relatively smaller specific surface area among the synthesized m-CaAly(700) samples, relatively low catalytic activity was observed after KF loading. Additionally, the yield of biodiesel obtained from the reaction catalyzed by 20KF/m-Al2O3(700)-500-3 was found to be as low as ∼0.9% in 5 h of the transesterification reaction in this study. The CO2-TPD profile of 20KF/m-Al2O3(700)-500-3 (Fig. S2, ESI†) indicated that there were just a few basic sites present in 20KF/m-Al2O3(700)-500-3. Although the specific surface areas of both m-Al2O3(700) and 20KF/m-Al2O3(700)-500-3 were very high and the mesopores of 20KF/m-Al2O3(700)-500-3 were big enough for the transesterification reaction, the low amount of basic sites in 20KF/m-Al2O3(700)-500-3 led to the low yield of biodiesel.
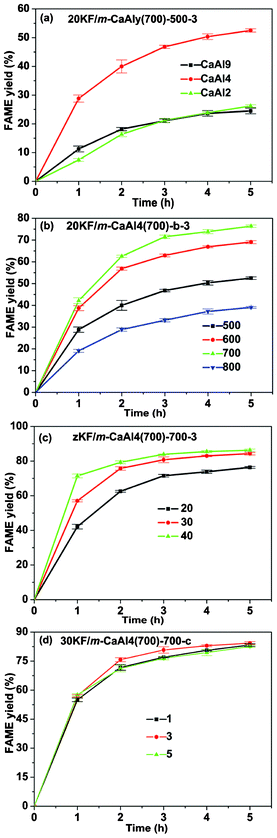 |
| Fig. 7 Yields of FAMEs (biodiesel) in the transesterification reaction of soybean oil with methanol catalyzed by (a) 20KF/m-CaAly(700)-500-3 (y = 2, 4, 9, the molar ratios of Al/Ca), (b) 20KF/m-CaAl4(700)-b-3 (b = 500, 600, 700 and 800 °C, the activation temperatures); (c) zKF/m-CaAl4(700)-700-3 (z = 20, 30, 40, the loading amounts (%) of KF·2H2O) and (d) 30KF/m-CaAl4(700)-700-c (c = 1, 3, 5 h, durations of activation at 700 °C). | |
Since the m-CaAl4(700) support gave the highest yield of biodiesel, this material was then used as the support in all the following experiments.
3.2.2. Effect of the activation temperature.
Fig. 7(b) shows the effect of the activation temperature on the catalytic activity of 20KF/m-CaAl4(700)-b-3. The result indicates that from 500 °C to 700 °C, higher temperature activation is in favor of the improvement of catalyst reactivity and results in higher yields of biodiesel. However, when this activation temperature was 800 °C, the lowest yield of biodiesel was obtained. Previous reports have found that only the strong and super basic sites are catalytically active to the transesterification reaction and both the basic strength and total quantity of strong and super basic sites determined the yield of biodiesel.22,38 In addition, super basic sites appeared to be a little more catalytically active than strong basic ones.42 Combining with the above analysis of CO2-TPD profiles (Fig. 6(a)), the effect of the activation temperature on the catalytic activity of 20KF/m-CaAl4(700)-b-3 is reasonable. Although the specific surface area decreased as the activation temperature increased (Table 2), the basic strength and total quantity of strong and super basic sites seemed to be more dominant in affecting the biodiesel yield.
3.2.3. Effect of the KF loading amount.
The effect of the KF loading amount on the catalytic activity of zKF/m-CaAl4(700)-700-3 was investigated and the result is shown in Fig. 7(c). We can know from the figure that 30KF/m-CaAl4(700)-700-3 produces a significantly higher yield of biodiesel than 20KF/m-CaAl4(700)-700-3, in accordance with the CO2-TPD profiles in Fig. 6(b), due to its stronger basic strength and higher density of strong and super basic sites than those of 20KF/m-CaAl4(700)-700-3. Compared to 30KF/m-CaAl4(700)-700-3, 40KF/m-CaAl4(700)-700-3 has lower amounts of super basic sites but with much higher amounts of strong basic sites, leading to the similar yields of the two samples. Similar to the above, though the specific surface area decreased as the KF loading amount increased (Table 2), the basic strength and total quantity of strong and super basic sites were the dominant factors affecting the biodiesel yield.
3.2.4. Effect of the activation duration.
We further investigated the effect of activation duration on the catalytic activity of 30KF/m-CaAl4(700)-700-c (Fig. 7(d)) and found that the biodiesel yields of using the three 30KF/m-CaAl4(700)-700-c samples are comparable with each other, in accordance with the results of CO2-TPD analysis, and follow the order of 30KF/m-CaAl4(700)-700-3 ≥ 30KF/m-CaAl4(700)-700-1 ≥ 30KF/m-CaAl4(700)-700-5. The relatively lower yield of the transesterification reaction catalyzed by 30KF/m-CaAl4(700)-700-5 can be attributed to its lower specific surface area (Table 2) as well as its relatively lower quantity of super basic sites (Fig. 6(c)).
3.2.5. Optimization of reaction conditions of the transesterification reaction.
The above study comes to a conclusion that 30KF/m-CaAl4(700)-700-3 has the highest catalytic activity for the transesterification reaction of soybean oil with methanol among all the catalysts employed in the present study. To optimize the catalytic reaction, we further investigated the influence of A/O and catalyst amount on the yield of biodiesel catalyzed by 30KF/m-CaAl4(700)-700-3. A/O was kept at 12
:
1 when varying the catalyst amount and the catalyst amount was kept at 3 wt% when changing A/O. Fig. 8(a) indicates that the biodiesel yield become ever higher with the increase of the catalyst amount, but the increment become lower at higher catalyst amounts. The effect of the catalyst amount on the yield of biodiesel is easily understandable. Fig. 8(b) indicates that the biodiesel yield becomes higher at A/O being raised from 6
:
1 to 18
:
1 while it becomes lower at A/O being further increased from 18
:
1 to 24
:
1. The effect of A/O is also expected. As we know, using one reactant excessively can increase the percent conversion of the other reactant and enhance the yield of the product calculated based on the conversion of the other in a chemical reaction with two reactants. Though the stoichiometric molar ratio of alcohol to oil is 3
:
1 in the transesterification reaction (Scheme 1), we have to use higher ratio of methanol to oil than the stoichiometric one to obtain enhanced yield of biodiesel. However, when the content of methanol in reaction system is too high with A/O of 24
:
1 or higher, it will dilute the reaction system and makes it difficult for oil molecules to access catalytic sites in the transesterification reaction of soybean oil with methanol. As a result, lower biodiesel yield was observed.
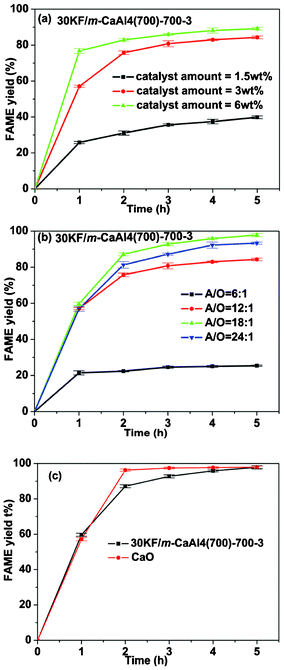 |
| Fig. 8 Influence of (a) the catalyst amounts and (b) molar ratios of alcohol to oil (A/O) on the yield of biodiesel catalyzed by 30KF/m-CaAl4(700)-700-3; (c) yields of biodiesel catalyzed by 30KF/m-CaAl4(700)-700-3 and CaO with A/O = 18 : 1 and catalyst amount = 3 wt%. | |
For comparison, we also used the traditional solid base CaO (≥98%, Sinopharm Chemical Reagent Co.) as the catalyst in the transesterification reaction at A/O of 18
:
1 and catalyst amount of 3 wt%. The result shows that 30KF/m-CaAl4(700)-700-3 and CaO have almost the same biodiesel yield of about 98% under the reaction condition over 5 h (Fig. 8(c)), which is in accordance with the report by Granados.43 However, the transesterification reaction rate and especially TOF value in the initial 1 h (Table 3) with 30KF/m-CaAl4(700)-700-3 as the catalyst are higher than those when pure CaO was used, which indicates that 30KF/m-CaAl4(700)-700-3 is significantly more active than CaO under the test conditions, probably due to its higher specific surface area (Table 2, S1, ESI†) and stronger basic strength (Fig. 6(c), S2, ESI†). Although the total quantity of strong and super basic sites of CaO is higher than that of 30KF/m-CaAl4(700)-700-3 (Table 3), the basic sites in 30KF/m-CaAl4(700)-700-3 are mostly the super basic ones (CO2 desorption temperature above 800 °C, Fig. 6(c)) while those in CaO are mainly the strong basic ones at much lower CO2 desorption temperature of <650 °C (Fig. S2, ESI†). Moreover, the leaching amount of Ca and K species from 30KF/m-CaAl4(700)-700-3 into biodiesel shown in Table 3 meets the EN14214 standard, most probably due to the strong combination of Ca species with the other element(s) (e.g., Al) in the as-prepared catalyst,2,12,19 and in great contrast, that from CaO is remarkably higher, indicating that CaO catalyzed the reaction in a way with both heterogeneous and homogeneous contributions.18 In addition, the leaching amount of K species from 30KF/m-CaAl4(700)-700-3 into biodiesel is also very low (Table 3) but a little higher than the EN14214 standard (<5 mg kg−1). Combining with the very low leaching amount of Ca species, it can be known that the catalytic reaction by 30KF/m-CaAl4(700)-700-3 is a heterogeneous one. Besides, neither monoglycerides nor diglycerides were detected during the reaction catalyzed by all the mesostructured KF/CaxAl2O(x+3) catalysts prepared, implying almost 100% selectivity of FAME by using these as-prepared catalysts, and naturally, the EN14214 standard in terms of the contents of monoglycerides and diglycerides can be well satisfied. In addition, the FAME yield of 98% also meets the EN14214 standard.
Table 3 Total amount of strong and super basic sites and catalytic performance (TOF, r and leaching amount of Ca species) of 30KF/m-CaAl4(700)-700-3 and CaO catalysts
Catalysts |
30KF/m-CaAl4(700)-700-3 |
CaO |
Estimated by CO2-TPD.
Reaction conditions: reaction temperature of 60 °C; A/O of 18 : 1 and catalyst amount of 3 wt%; reaction time of 1 h.
|
Total amount of strong and super basic sites (fm, μmol g−1)a |
304 ± 6 |
419 ± 9 |
TOF (×10−2 mol s−1 mol−1)b |
6.22 ± 0.08 |
4.32 ± 0.07 |
r (×10−5mol s−1 g−1)b |
1.89 ± 0.03 |
1.81 ± 0.03 |
Leached Ca (mg kg−1) |
<2.5 |
6498 ± 283 |
Leached K (mg kg−1) |
11.7 ± 1.63 |
— |
3.2.6. Reutilization of the as-prepared catalyst.
Table 4 shows the FAME yield catalyzed by the fresh and reused catalyst (30KF/m-CaAl4(700)-700-3). Unfortunately, it can be clearly seen that the FAME yield decreased significantly at the second cycle, similar to other KF loaded catalysts.37,44,45 From the XRD patterns (Fig. S3, ESI†, there are still strong XRD peaks belonging to the active species) and the extremely low leaching amounts of Ca and K species, the reduction of the FAME yield is believed not to be resulted from the loss of the active species but from the adsorption of the products, FAME or/and glycerin, on the active sites.37 One of our future efforts is to enhance the recyclability of the as-prepared catalyst.
Table 4 FAME yield catalyzed by the fresh and reused catalyst (30KF/m-CaAl4(700)-700-3)
Catalysts |
Fresh |
Used once |
FAME yield (%) |
97.82 ± 0.93 |
70.38 ± 0.13 |
Tantirungrotechai has reported the catalytic performance of KI loaded Mg–Al mixed-metal oxides,46 which was a mixture of γ-Al2O3 and MgO or of Mg6Al2CO3(OH)16·4H2O and MgO depending on the Mg/Al ratio. The biodiesel yield obtained using their most efficient catalyst was about 96% in 8 h at the reaction temperature, A/O and catalyst amount of 70 °C, 20
:
1 and 5 wt%, respectively. This means that mesoporous CaxAl2O(x+3) might be one of the best supports among those reported so far for loading species for biodiesel production.
Conclusions
Mesoporous CaxAl2O(x+3) (0 < x ≤ 1) of different molar ratios of aluminum to calcium and calcination temperatures have been synthesized and were first used as catalyst supports to load KF for biodiesel production via the transesterification reaction. Although mesoporous CaxAl2O(x+3) (0 < x ≤ 1) themselves showed no catalytic activity, the composites after KF loading became active in the transesterification reaction of soybean oil with methanol. An optimized composite, 30KF/m-CaAl4(700)-700-3, with the Al/Ca molar ratio of 4, KF·2H2O loading amount of 30%, activation temperature at 700 °C and duration of 3 h, was found to be the most efficient catalyst among the catalysts prepared due to its high total active basicity and basic strength. Under the optimized reaction condition at A/O of 18
:
1 and catalyst amount of 3 wt%, the reaction catalyzed by 30KF/m-CaAl4(700)-700-3 showed a comparable biodiesel yield of about 98% over 5 h to that using the traditional solid basic catalyst CaO. However, the reaction rate and especially the TOF value in the initial 1 h using 30KF/m-CaAl4(700)-700-3 as the catalyst are significantly higher than those when pure CaO was used because of the higher specific surface area and stronger basic strength of 30KF/m-CaAl4(700)-700-3. Moreover, the Ca leaching amount with 30KF/m-CaAl4(700)-700-3 is remarkably lower than that with CaO and meets the EN14214 standard, and the as-prepared catalyst 30KF/m-CaAl4(700)-700-3 is believed to work in the heterogeneous way. In addition, the selectivity of FAME catalyzed by all the mesostructured KF/CaxAl2O(x+3) prepared here is almost 100%. Therefore, this engineered mesostructured KF/CaxAl2O(x+3) composite catalyst is a kind of efficient and “green” heterogeneous catalyst for biodiesel production.
Acknowledgements
We greatly acknowledge financial support from the National Basic Research Program of China (973 Program, Grant No. 2013CB933200), National Nature Science Foundation of China (Grant No. 21177137, 51202278), State Key Laboratory of Heavy Oil Processing (2012-1-04) and Science Foundation for Youth Scholar of State Key Laboratory of High Performance Ceramics and Superfine Microstructures (SKL200901).
References
- W. Li, F. Ma, F. Su, L. Ma, S. Zhang and Y. Guo, ChemSusChem, 2011, 4, 744 CrossRef CAS.
- W. Thitsartarn and S. Kawi, Green Chem., 2011, 13, 3423 RSC.
- M. Alonso, F. Vila, A. R. Mariscal, M. Ojeda, M. L. Granados and J. Santamaria-Gonzalez, Catal. Today, 2010, 158, 114 CrossRef.
- P. M. Ejikeme, I. D. Anyaogu, C. L. Ejikeme, N. P. Nwafor, C. A. C. Egbuonu, K. Ukogu and J. A. Ibemesi, E-J. Chem., 2010, 7, 1120 CrossRef CAS.
- E. Rashtizadeh, F. Farzaneh and M. Ghandi, Fuel, 2010, 89, 3393 CrossRef CAS.
- M. López Granados, A. C. Alba-Rubio, F. Vila, D. Martín Alonso and R. Mariscal, J. Catal., 2010, 276, 229 CrossRef.
- R. S. Watkins, A. F. Lee and K. Wilson, Green Chem., 2004, 6, 335 RSC.
- E. Akbar, N. Binitha, Z. Yaakob, S. K. Kamarudin and J. Salimon, Green Chem., 2009, 11, 1862 RSC.
- K. Wilson, C. Hardacre, A. F. Lee, J. M. Montero and L. Shellard, Green Chem., 2008, 10, 654 RSC.
- G. J. Suppes, M. A. Dasari, E. J. Doskocil, P. J. Mankidy and M. J. Goff, Appl. Catal., A, 2004, 257, 213 CrossRef CAS.
- M. Di Serio, R. Tesser, L. Pengmei and E. Santacesaria, Energy Fuels, 2008, 22, 207 CrossRef CAS.
- M. Zabeti, W. Daud and M. K. Aroua, Appl. Catal., A, 2009, 366, 154 CrossRef CAS.
- E. Li and V. Rudolph, Energy Fuels, 2008, 22, 145 CrossRef CAS.
- X. J. Liu, H. Y. He, Y. J. Wang, S. L. Zhu and X. L. Piao, Fuel, 2008, 87, 216 CrossRef CAS.
- M. Verziu, B. Cojocaru, J. Hu, R. Richards, C. Ciuculescu, P. Filip and V. I. Parvulescu, Green Chem., 2008, 10, 373 RSC.
- T. Wan, P. Yu, S. Gong, Q. Li and Y. Luo, Korean J. Chem. Eng., 2008, 25, 998 CrossRef CAS.
- S. Gryglewicz, Bioresour. Technol., 1999, 70, 249 CrossRef CAS.
- M. L. Granados, M. D. Z. Poves, D. M. Alonso, R. Mariscal, F. C. Galisteo, R. Moreno-Tost, J. Santamaria and J. L. G. Fierro, Appl. Catal., B, 2007, 73, 317 CrossRef CAS.
- M. Zabeti, W. M. A. W. Daud and M. K. Aroua, Fuel Process. Technol., 2010, 91, 243 CrossRef CAS.
- M. J. Campos-Molina, J. Santamaria-Gonzalez, J. Merida-Robles, R. Moreno-Tost, M. C. G. Albuquerque, S. Bruque-Gamez, E. Rodriguez-Castellon, A. Jimenez-Lopez and P. Maireles-Torres, Energy Fuels, 2010, 24, 979 CrossRef CAS.
- L. Gao, G. Teng, G. Xiao and R. Wei, Biomass Bioenergy, 2010, 34, 1283 CrossRef CAS.
- K. Faungnawakij, B. Yoosuk, S. Namuangruk, P. Krasae, N. Viriya-empikul and B. Puttasawat, ChemCatChem, 2012, 4, 209 CrossRef CAS.
- J. Zhou, Z. L. Hua, J. L. Shi, Q. J. He, L. M. Guo and M. L. Ruan, Chem.–Eur. J., 2009, 15, 12949 CrossRef CAS.
- D. Meloni, R. Monaci, Z. Zedde, M. G. Cutrufello, S. Fiorilli and I. Ferino, Appl. Catal., B, 2011, 102, 505 CrossRef CAS.
- C. Samart, R. Sreetongkittikul and C. Sookman, Fuel Process. Technol., 2009, 90, 922 CrossRef CAS.
- Y. Wan and D. Y. Zhao, Chem. Rev., 2007, 107, 2821 CrossRef CAS.
- A. Corma, Chem. Rev., 1997, 97, 2373 CrossRef CAS.
-
Z. Zou, X. Fan, L. Liu and X. Chen, CN Pat., 101 219 908-A, 2008 Search PubMed.
- H. Dathe, A. Jentys, P. Haider, E. Schreier, R. Fricke and J. A. Lercher, Phys. Chem. Chem. Phys., 2006, 8, 1601 RSC.
- E. Schreier, R. Eckelt, M. Richter and R. Fricke, Appl. Catal., B, 2006, 65, 249 CrossRef CAS.
- S. Andonova, C. Vadov, B. Pawelec, I. Shtereva, G. Tyuliev, S. Damyanova and L. Petrov, Appl. Catal., A, 2007, 328, 201 CrossRef CAS.
- Y. Fan, X. B. Lu, Y. W. Ni, H. J. Zhang, L. Zhao, J. P. Chen and C. L. Sun, Environ. Sci. Technol., 2010, 44, 3079 CrossRef CAS.
- S. M. Morris, P. F. Fulvio and M. Jaroniec, J. Am. Chem. Soc., 2008, 130, 15210 CrossRef CAS.
- W. Q. Cai, J. G. Yu, C. Anand, A. Vinu and M. Jaroniec, Chem. Mater., 2011, 23, 1147 CrossRef CAS.
- Y. Wang, S.-y. Hu, Y.-p. Guan, L.-b. Wen and H.-y. Han, Catal. Lett., 2009, 131, 574 CrossRef CAS.
- D. E. Lopez, J. G. Goodwin, D. A. Bruce and E. Lotero, Appl. Catal., A, 2005, 295, 97 CrossRef CAS.
- L. Gao, G. Teng, J. Lv and G. Xiao, Energy Fuels, 2010, 24, 646 CrossRef CAS.
- B. Yoosuk, P. Krasae, B. Puttasawat, P. Udomsap, N. Viriya-empikul and K. Faungnawakij, Chem. Eng. J., 2010, 162, 58 CrossRef CAS.
- T. Seki and M. Onaka, J. Mol. Catal. A: Chem., 2007, 263, 115 CrossRef CAS.
- Y. H. Taufiq-Yap, H. V. Lee, M. Z. Hussein and R. Yunus, Biomass Bioenergy, 2011, 35, 827 CrossRef CAS.
- N. Boz, N. Degirmenbasi and D. M. Kalyon, Appl. Catal., B, 2009, 89, 590 CrossRef CAS.
- M. C. G. Albuquerque, I. Jimenez-Urbistondo, J. Santamaria-Gonzalez, J. M. Merida-Robles, R. Moreno-Tost, E. Rodriguez-Castellon, A. Jimenez-Lopez, D. C. S. Azevedo, C. L. Cavalcante and P. Maireles-Torres, Appl. Catal., A, 2008, 334, 35 CrossRef CAS.
- M. L. Granados, D. M. Alonso, A. C. Alba-Rubio, R. Mariscal, M. Ojeda and P. Brettes, Energy Fuels, 2009, 23, 2259 CrossRef.
- R. Song, D. Tong, J. Tang and C. Hu, Energy Fuels, 2011, 25, 2679 CrossRef CAS.
- C. Xu, J. Sun, B. Zhao and Q. Liu, Appl. Catal., B, 2010, 99, 111 CrossRef CAS.
- J. Tantirungrotechai, P. Chotmongkolsap and M. Pohmakotr, Microporous Mesoporous Mater., 2010, 128, 41 CrossRef CAS.
Footnote |
† Electronic supplementary information (ESI) available. See DOI: 10.1039/c2ra22218c |
|
This journal is © The Royal Society of Chemistry 2012 |
Click here to see how this site uses Cookies. View our privacy policy here.