DOI:
10.1039/C2RA20797D
(Paper)
RSC Adv., 2012,
2, 6178-6184
Single crystal α-Fe2O3 with exposed {104} facets for high performance gas sensor applications†
Received
27th April 2012
, Accepted 30th April 2012
First published on 8th June 2012
Abstract
The controlled fabrication of metal oxide nanocrystals with exposed high-index facets has drawn enormous research attention. In this article, we have synthesized single-crystalline α-Fe2O3 crystals bound by six {104} high-index facets using a simple hydrothermal method. The formation mechanism of the unique crystal structure has been systematically studied, revealing that the α-Fe2O3 crystals are formed through an aggregation–phase transformation–recrystallization mechanism. More importantly, we have demonstrated that the unique α-Fe2O3 crystals with {104} high-index facets are highly advantageous for high performance gas sensors. This work sheds some new light on using high-index faceted nanocrystals for high performance functional device applications.
Introduction
In recent years, the shape-controlled synthesis of nanocrystals and nanomaterials with specifically exposed facets has attracted enormous attention from the perspectives of both fundamental studies and technological applications.1–8 Particularly, the fabrication of nanocrystals with high-index crystal facets has emerged as an effective means to improve the materials' physiochemical properties and performance because high-index crystal facets possess higher surface energies, more atom terraces, steps and dangling bonds when compared to those with low-index facets.9–16 For instance, Han and co-workers have demonstrated that the use of octahedral SnO2 particles with high-index {221} facets can noticeably improve the sensing properties for ethanol detection.16 This has been attributed to the rich coordinatively unsaturated Sn atoms, dangling bonds and oxygen vacancies on the {221} facets with a markedly enhanced capability to adsorb oxygen species (e.g., O2−, O2−, O−etc.) that facilitates the surface sensing reactions. However, the fabrication of nanocrystals with high index surface is extremely challenging because high index surfaces are normally unstable and tend to transform into lower energy surfaces during growth.1,13,15,17 A pioneer work by Lu et al.15 successfully demonstrated the preparation of TiO2 crystals with 47% exposed {001} facets via a hydrothermal route using fluoride ions as a facet-control and protecting agent. Since then, great progress has been made to produce TiO2 nanostructures with a higher percentage of exposed {001} facets for various application such as lithium ion batteries and photocatalysts.9,10,12,13
Hematite (α-Fe2O3) is one of the most important iron oxides and has received extensive research attention for many applications such as gas sensing, magnetism, energy storage and so on.17–23 It is well known that the physiochemical properties of nanostructured α-Fe2O3 crystals are largely determined by their size, shape and crystal facets.17,19,20,23–30 Over recent years, different forms of α-Fe2O3 single nanocrystals have been synthesized including nanodiscs,18 nanododecahedrons,20 nanorings,21,31 nanospindles,32 nanorhombohedrons,17,20,33 nanocubes,34–36 and nanotubes.37 Despite success in the fabrication of diverse α-Fe2O3 nanocrystals, the facile fabrication of single nanocrystal α-Fe2O3 with exposed high-index facets remains as a challenging task.17,19 Although various iron oxide crystals have been reported, a well-defined application for high-index faceted α-Fe2O3 crystals has not yet been reported.
In this work, we report a facile hydrothermal approach to fabricate α-Fe2O3 single nanocrystals with six exposed high-index {104} facets. By using gas sensing as a probe reaction, we depicted an enhanced functionality of high-index crystal facets and the importance of crystal-engineering for applications of functional nanomaterials.
Experimental section
Materials
Chemicals such as FeCl3·6H2O, ethanol, urea, and formamide were of analytical grade and purchased from Guangfu Fine Chemical Research Institute (Tianjin). Distilled water was used throughout the experiments.
Synthesis of α-Fe2O3 crystals
In a typical synthesis of rhombohedral α-Fe2O3 crystals, 1.10 g FeCl3·6H2O and 1.21 g urea were dissolved in 40 ml of distilled water to form a clear yellow solution, and then 1.65 g formamide was added. The reacting solution was transferred to 50 mL Teflon-lined stainless autoclave and heated to 120 °C for 12 h. After cooling down to room temperature, the product was collected by centrifugation and washed by distilled water and absolute ethanol 4 times, and then dried at 80 °C for several hours.
Chracterization
The samples were characterized by means of X-ray diffraction analysis (XRD, Rigaku D/max-2500, graphite monochromator, Cu-Kα, λ = 1.5418 Å), scanning electron microscope (SEM, Shimadzu SS-550, 15 kV), high-resolution transmission electron microscopy (HRTEM, FEI Tecnai F20), energy-dispersive X-ray spectroscopy (EDS), X-ray photoelectron spectroscopy (XPS, Kratos Axis Ultra DLD spectrometer, Al-Kα X-ray monochromator) and N2 adsorption–desorption (TriStar 3000). The specific surface area was calculated by using the Brunauer–Emett–Teller (BET) method. Gas sensing tests were performed on a commercial HW-30A Gas Sensing Measurement System (HanWei Electronics Co., Ltd., Henan, China) at an operating temperature of 300 °C using air as the reference gas at a relative humidity of 26–37%. The sensor response is defined as the ratio of Ra
:
Rg, where Ra and Rg are the electrical resistance of the sensor in air and in test gas. Details of the sensor fabrication, photograph and gas sensing test principle can be seen in our previous work.38
Results and discussion
Typically, the α-Fe2O3 single crystals were synthesized via a formamide-assisted hydrothermal procedure. Fig. 1a shows the powder X-ray diffraction (XRD) patterns of the as-synthesized sample. All diffraction peaks can be well indexed to the triclinic structure of α-Fe2O3 (JCPDS No. 33-0664). No impurity peaks were observed. The intensity of the diffraction peaks suggests the as-synthesized sample possesses high crystallinity. The scanning electron microscopy (SEM) images shown in Fig. 1b reveal a rhombohedral-shaped crystal morphology. The enlarged SEM image (inset of Fig. 1b) shows that the rhombohedral crystals have a smooth and clean surface. N2 adsorption–desorption analysis demonstrates that the rhombohedral crystals have a specific surface area of 21.1 m3 g−1.
The crystallographic structure of the as-synthesized α-Fe2O3 crystals was studied by detailed transmission electron microscopy (TEM) analysis. Fig. 2a shows the isometric morphology of a rhomboidal crystal representing the as-synthesized α-Fe2O3 crystals in this work. Such a crystal possesses a single {104} closed form, i.e., its surface is completely enclosed by (10
4), (1104), (0
14), (
01
), (1
0
), and (01![[1 with combining macron]](https://www.rsc.org/images/entities/char_0031_0304.gif)
) faces. Fig. 2b is the TEM image viewed along the [841] direction, showing a rhombic shape with an angle of 64.8°. Fig. 2d displays (
104) and (0
14) atomic planes with a lattice spacing of 2.7 Å and an interfacial angle of 64.8°. The corresponding SAED pattern (inset in Fig. 2d) matches well with the high-resolution TEM (HRTEM) image. The TEM image viewed along the diagonal [42
] direction shows a rectangular shape (Fig. 2c). Two atomic planes with equal spacing of 3.7 Å having an angle of 86.0° were identified in the HRTEM image (Fig. 2e). These are corresponding to the (1
02) and (01
2) planes of the α-Fe2O3 crystal. Additionally, the spacing of the plane parallel to the apical surface was measured to be 2.7 Å, corresponding to the (10
4) plane. This is further confirmed by selected area electron diffraction (SAED) pattern shown in the inset of Fig. 2e. By collectively considering the above results, we confirm that all surfaces of the rhomboidal α-Fe2O3 crystal are bound by equivalent {104} planes with identical spacing of 2.7 Å. Fig. S1† shows the energy-dispersive X-ray spectroscopy (EDS) collected from an individual rhombohedral α-Fe2O3 crystal. The EDS pattern indicates that the crystal is mainly composed of Fe and O elements, together with a trace amount of C, which is probably from the residue formamide in the product.
![(a) Geometrical model of the rhomboidal α-Fe2O3 crystal bound by {104} facets. (b, c) TEM images with the incident electron beams along [841] and [421] directions respectively. (d, e) HRTEM images and SAED patterns (insets) of the areas in (b) and (c) marked by dashed rectangles. (f) Possible mechanism for the formation of α-Fe2O3 crystals.](/image/article/2012/RA/c2ra20797d/c2ra20797d-f2.gif) |
| Fig. 2 (a) Geometrical model of the rhomboidal α-Fe2O3 crystal bound by {104} facets. (b, c) TEM images with the incident electron beams along [841] and [421] directions respectively. (d, e) HRTEM images and SAED patterns (insets) of the areas in (b) and (c) marked by dashed rectangles. (f) Possible mechanism for the formation of α-Fe2O3 crystals. | |
A series of control experiments with different amounts of formamide were conducted to investigate the effect of the amount of formamide on the growth of α-Fe2O3 crystals. As shown in Fig. 3, in the absence of formamide, the product contains a large quantity of irregular shaped particles with sizes ranging from tens of nanometres to one micrometre. In the presence of formamide, the rhombohedral shaped α-Fe2O3 crystals gradually become the dominant product with an increased amount of formamide (Fig. 3b–d). With 1.65 g formamide, almost 100% of the produced crystals were rhombohedral-shaped crystals. When the dosage of formamide is further increased to 3.20 g (SEM in Fig. S2†), all the α-Fe2O3 particles present a rhombohedral morphology. This demonstrates the crucial role that formamide plays in the formation of α-Fe2O3 crystals with exposed {104} facets. To further elucidate the formation process, experiments with different hydrothermal durations were performed. Fig. 4 displays the SEM images of the products obtained with different hydrothermal reaction times. These images reveal that the hydrothermal reaction time also has a marked effect on the morphology of the products. When the hydrothermal reaction times were less than 2 h (Fig. 4a and b), the obtained products were dominated by tiny particles tens of nanometres in size. When the reaction time was increased to 6 h (Fig. 4c), the sample was composed of both tiny nanoparticles and rhombohedral shaped crystals. Almost 100% of rhombohedral shaped crystals were obtained when the reaction time was prolonged to 8 h (Fig. 4d). Under such conditions, only a few irregular shaped small nanoparticles were observed. XRD patterns of these time-dependent samples reveal that hydrothermal reaction time has a significant effect on the phase composition of the products (Fig. 5). When the reaction times were less than 2 h, the XRD patterns of the nanoparticles shown in Fig. 5 agree well with that of akaganeite β-FeOOH (JCPDS No. 34-1266). With 6 h reaction time, the XRD data indicate the domination of hematite α-Fe2O3 (JCPDS 33-0664) with a small diffraction peaks for β-FeOOH. The XRD pattern of the product after 8 h hydrothermal reaction matches perfectly with that of hematite α-Fe2O3, indicating the occurrence of phase transformation during the formation of α-Fe2O3 crystals that is similar to the case of formation of monodisperse α-Fe2O3 nanocrystals.39–41 It is therefore believed that the formation of α-Fe2O3 crystals involves both phase transformation and aggregation of β-FeOOH particles, which is in good agreement with the study of Sugimoto et al.39 Accordingly, a tentative mechanism is proposed to describe the formation process of the novel high-index α-Fe2O3 single crystal (Fig. 2f). Han et al.,42 have reported that the amount of formamide molecules adsorbed on different crystal planes are different and can lead to an anisotropic aggregation of primary CuO nanoparticles into single crystalline CuO nanoellipsoids. In this work, the selective adsorption ability of formamide molecules on crystal surfaces could be responsible for the preservation of {104} plane. More specifically, the formamide molecules adsorbed on the {104} plane of β-FeOOH particles serve as a facet-directing agents to assemble the β-FeOOH particles into α-Fe2O3 crystals via aggregation and phase transformation processes. Through a further recrystallization process, the aggregated α-Fe2O3 crystals convert into perfect single rhombohedral α-Fe2O3 crystals with clean surfaces. The entire growth process of rhombohedral α-Fe2O3 crystals should be energetically favoured, because the surface energy of the primary β-FeOOH particles can be decreased through the aggregation and recrystallization of β-FeOOH into α-Fe2O3.
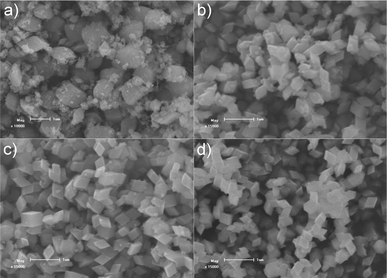 |
| Fig. 3 SEM images of the products prepared at 120 °C for 12 h with different amounts of formamide: a) 0 g; b) 0.41 g; c) 0.82 g and d) 1.65 g. In the absence of formamide, the product contains a large quantity of irregular particles with a poor size distribution, while with 1.65 g formamide, nearly 100% of the nanocrystals have a uniform rhombohedral shape. | |
 |
| Fig. 4 SEM images of the products prepared with 1.65 g formamide at different hydrothermal durations: a) 1 h; b) 2 h; c) 6 h and d) 8 h. | |
 |
| Fig. 5 XRD patterns of the products prepared with 1.65 g formamide at different hydrothermal durations. | |
It is well known that the high-index crystal facets of materials can significantly affect their surface properties, especially the surface adsorptivity due to the improved surface reactivity.1,3,4,12,16,34,43,44 Inspired by this, we applied the obtained α-Fe2O3 crystals to gas sensing applications as the analytical signal of such a type of sensing system is highly dependent on the surface adsorptivity.16,20,43 For comparison, we have also tested the sensing performances of commercial α-Fe2O3 powder under the same experimental conditions. Fig. 6a–e shows the original sensor responses of the α-Fe2O3 crystals and the commercial α-Fe2O3 powder for acetone detection. For all cases, an increase in the acetone concentration results in an increase in sensor response. For a given acetone concentration, the sensor response obtained from the α-Fe2O3 crystals is significantly higher than that obtained from the commercial α-Fe2O3 powder. In this work, Ra and Rg are defined as the electrical resistance of the sensor in air and in the test gas, and the ratio of Ra
:
Rg is defined as the response (R). Fig. 6f shows the plot of R(Ra
:
Rg) against the acetone concentration. For both α-Fe2O3 crystals and commercial α-Fe2O3 powder sensors, the response linearly increases with acetone concentrations up to 200 ppm and then levels off at higher concentrations above 200 ppm. In Fig. 6f, the slope of the R–C curve represents the sensor's sensitivity. The obtained slope value for the α-Fe2O3 crystals sensor is 0.019 ppm−1, which is over 1.7 times of the slope obtained for the commercial α-Fe2O3 powder sensor (0.011 ppm−1), suggesting a 1.7 times improved sensitivity for the α-Fe2O3 crystals sensor. The sensing performance was also evaluated using ethanol as the testing compound. Similar to the case of acetone, higher responses were obtained from α-Fe2O3 crystals sensor for all ethanol concentration investigated (see Fig. 7a–e). The linear range (Fig. 7f) for both α-Fe2O3 crystals and commercial α-Fe2O3 powder sensors were found to be 100 ppm. The slope value obtained for the α-Fe2O3 crystals sensor is 0.015 ppm−1, which is nearly 1.9 times of the slope obtained for the commercial α-Fe2O3 powder sensor (0.008 ppm−1), suggesting a 1.9 times improved sensitivity for the α-Fe2O3 crystals sensor in determination of ethanol.
 |
| Fig. 6 (a–e) Dynamic response–recovery curves for acetone detection (10–300 ppm) and (f) sensor responses of α-Fe2O3 crystals and commercial α-Fe2O3 powder to acetone (10–400 ppm). | |
 |
| Fig. 7 (a–e) Dynamic response–recovery curves for ethanol detection (10–300 ppm) and (f) sensor responses of α-Fe2O3 nanocrystals and commercial α-Fe2O3 powder to ethanol (10–300 ppm). | |
Despite the large surface area of the α-Fe2O3 crystals (21.1 m2 g−1) compared to that (1.5 m2 g−1) of commercial α-Fe2O3 powder, the enhanced sensor performance could also be attributed to the unique surface structure of the α-Fe2O3 crystals. SEM (Fig. S3†) observation reveals that the commercial α-Fe2O3 powder consists of random particles. These particles possess irregular morphologies that differ dramatically from the well defined rhombohedral α-Fe2O3 crystals. It is now widely accepted that, for metal oxide semiconductors, the gas sensing behaviors derive from the redox reaction between gas molecules and chemisorbed oxygen species (O2−, O2− and O−)45–47 on the surface of semiconductors. Consequently, the surface structure of crystals should have a strong influence on the sensor performance. Fig. 8 displays a schematic atomic structure for the {104} faceted α-Fe2O3. It can be seen that rows of Fe atoms lie on the (104) plane in an unsaturated coordination form. Therefore, a large amount of dangling bonds or oxygen vacancies are present on this plane, making the surface highly active for adsorption of ionized oxygen species, which would likely contribute to the enhanced sensing reactions on the surface.16,43 To prove this hypothesis, X-ray photoelectron spectroscopy (XPS) studies have been performed for the α-Fe2O3 rhombohedral crystals and commercial powder, and their corresponding O 1s XPS spectra after Gaussian fitting are given in Fig. 8b and c. Both spectra show a similar peak at 529.5 and 529.6 eV, corresponding to the lattice oxygen (O2−) in α-Fe2O3. It is worth noting that the α-Fe2O3 rhombohedral crystals also show another two significant peaks at 531.5 and 532.8 eV, which can be attributed to the oxygen vacancies and chemisorbed oxygen species on the surface of metal oxide,43,48 respectively, while the commercials α-Fe2O3 powder only shows a fitting peak at 531.5 eV for oxygen vacancies. In other words, there are a larger number of chemisorbed oxygen species on the {104} surfaces of rhombohedral crystals, which is likely to be responsible for the enhanced sensitivity compared to commercial α-Fe2O3 powder.
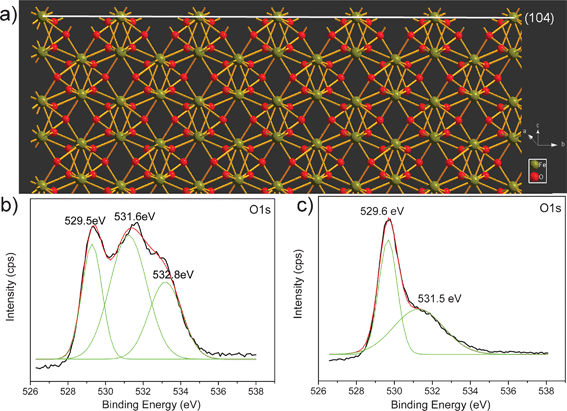 |
| Fig. 8 (a) Schematic structure for atom configuration on the (104) facets of α-Fe2O3 and XPS spectra of O 1s for (b) α-Fe2O3 crystals and (c) commercial α-Fe2O3 powder. | |
Conclusion
In conclusion, single-crystalline rhombohedral α-Fe2O3 crystals with six exposed {104} facets were synthesized by a hydrothermal method using formamide as a structure-directing agent. Control experiments reveal that formamide plays a curial role in the formation of the unique α-Fe2O3 crystals. Gas sensing studies demonstrate that the as-prepared α-Fe2O3 crystals showed improved sensing performances towards acetone and ethanol detection when compared with commercial α-Fe2O3 powder, probably due to the special atomic arrangement on the high-index {104} facets. This work proposes an example for engineering α-Fe2O3 crystals with high-index facets for enhanced functional properties.
Acknowledgements
This work was supported by the National Natural Science Foundation of China (Nos. 20871071 and 21171099) and the Applied Basic Research Programs of Science and Technology Commission Foundation of Tianjin (Nos. 09JCYBJC03600 and 10JCYBJC03900).
References
- Z. Y. Jiang, Q. Kuang, Z. X. Xie and L. S. Zheng, Adv. Funct. Mater., 2011, 20, 3634–3645 CrossRef.
- Y. Sun and Y. Xia, Science, 2002, 298, 2176 CrossRef CAS.
- Z. Y. Zhou, N. Tian, J. T. Li, I. Broadwell and S. G. Sun, Chem. Soc. Rev., 2011, 40, 4167–4185 RSC.
- A. Mclaren, T. Valdes-Solis, G. Q. Li and S. C. Tsang, J. Am. Chem. Soc., 2009, 131, 12540–12541 CrossRef CAS.
- X. Xie, Y. Li, Z. Q. Liu, M. Haruta and W. Shen, Nature, 2009, 458, 746–749 CrossRef CAS.
- A. Gurlo, Nanoscale, 2011, 3, 154–165 RSC.
- S. Ding and X. W. Lou, Nanoscale, 2011, 3, 3586–3588 RSC.
- J. S. Chen, T. Zhu, C. M. Li and X. W. Lou, Angew. Chem., Int. Ed., 2011, 50, 650–653 CrossRef CAS.
- J. S. Chen, Y. L. Tan, C. M. Li, Y. L. Cheah, D. Y. Luan, S. Madhavi, F. Y. C. Boey, L. A. Archer and X. W. Lou, J. Am. Chem. Soc., 2010, 132, 6124–6130 CrossRef CAS.
- Y. Q. Dai, C. M. Cobley, J. Zeng, Y. M. Sun and Y. N. Xia, Nano Lett., 2009, 9, 2455–2459 CrossRef CAS.
- C. T. Dinh, T. D. Nguyen, F. Kleitz and T. O. Do, ACS Nano, 2009, 3, 3737–3743 CrossRef CAS.
- X. G. Han, Q. Kuang, M. S. Jin, Z. X. Xie and L. S. Zheng, J. Am. Chem. Soc., 2009, 131, 3152–3153 CrossRef CAS.
- B. H. Wu, C. Y. Guo, N. F. Zheng, Z. X. Xie and G. D. Stucky, J. Am. Chem. Soc., 2008, 130, 17563–17567 CrossRef CAS.
- H. G. Yang, G. Liu, S. Z. Qiao, C. H. Sun, Y. G. Jin, S. C. Smith, J. Zou, H. M. Cheng and G. Q. Lu, J. Am. Chem. Soc., 2009, 131, 4078–4083 CrossRef CAS.
- H. G. Yang, C. H. Sun, S. Z. Qiao, J. Zou, G. Liu, S. C. Smith, H. M. Cheng and G. Q. Lu, Nature, 2008, 453, 638 CrossRef CAS –U634.
- X. Han, M. Jin, S. Xie, Q. Kuang, Z. Jiang, Y. Jiang, Z. Xie and L. Zheng, Angew. Chem., 2009, 121, 9344–9347 CrossRef.
- J. Yin, Z. Yu, F. Gao, J. Wang, H. Pang and Q. Lu, Angew. Chem., 2010, 122, 6472–6476 CrossRef.
- J. S. Chen, T. Zhu, X. H. Yang, H. G. Yang and X. W. Lou, J. Am. Chem. Soc., 2010, 132, 13162–13164 CrossRef CAS.
- B. Lv, Z. Liu, H. Tian, Y. Xu, D. Wu and Y. Sun, Adv. Funct. Mater., 2010, 22, 3987–3996 CrossRef.
- X. Li, W. Wei, S. Wang, L. Kuai and B. Geng, Nanoscale, 2011, 3, 718–724 RSC.
- C. J. Jia, L. D. Sun, F. Luo, X. D. Han, L. J. Heyderman, Z. G. Yan, C. H. Yan, K. Zheng, Z. Zhang, M. Takano, N. Hayashi, M. Eltschka, M. Klaui, U. Rudiger, T. Kasama, L. Cervera-Gontard, R. E. Dunin-Borkowski, G. Tzvetkov and J. Raabe, J. Am. Chem. Soc., 2008, 130, 16968–16977 CrossRef CAS.
- J. Zhang, X. Liu, L. Wang, T. Yang, X. Guo, S. Wu, S. Wang and S. Zhang, J. Phys. Chem. C, 2011, 115, 5352–5357 CAS.
- F. Jiao, A. Harrison, J. C. Jumas, A. V. Chadwick, W. Kockelmann and P. G. Bruce, J. Am. Chem. Soc., 2006, 128, 5468–5474 CrossRef CAS.
- Z. Wu, K. Yu, S. Zhang and Y. Xie, J. Phys. Chem. C, 2008, 112, 11307–11313 CAS.
- C. Wu, P. Yin, X. Zhu, C. OuYang and Y. Xie, J. Phys. Chem. B, 2006, 110, 17806–17812 CrossRef CAS.
- L. Vayssieres, C. Sathe, S. M. Butorin, D. K. Shuh, J. Nordgren and J. H. Guo, Adv. Mater., 2005, 17, 2320 CrossRef CAS.
- T. P. Raming, A. J. A. Winnubst, C. M. van Kats and A. P. Philipse, J. Colloid Interface Sci., 2002, 249, 346–350 CrossRef CAS.
- D. Larcher, C. Masquelier, D. Bonnin, Y. Chabre, V. Masson, J. B. Leriche and J. M. Tarascon, J. Electrochem. Soc., 2003, 150, A133–A139 CrossRef CAS.
- X. Hu, J. C. Yu, J. Gong, Q. Li and G. Li, Adv. Mater., 2007, 19, 2324 CrossRef CAS.
- J. H. Adair and E. Suvaci, Curr. Opin. Colloid Interface Sci., 2000, 5, 160–167 CrossRef CAS.
- X. L. Hu, J. C. Yu, J. M. Gong, Q. Li and G. S. Li, Adv. Mater., 2007, 19, 2324–2329 CrossRef CAS.
- M. Ozaki, S. Kratohvil and E. Matijevi, J. Colloid Interface Sci., 1984, 102, 146–151 CrossRef CAS.
- R. D. Rodriguez, D. Demaille, E. Lacaze, J. Jupille, C. Chaneac and J. P. Jolivet, J. Phys. Chem. C, 2007, 111, 16866–16870 CAS.
- Y. Zheng, Y. Cheng, Y. Wang, F. Bao, L. Zhou, X. Wei, Y. Zhang and Q. Zheng, J. Phys. Chem. B, 2006, 110, 3093–3097 CrossRef CAS.
- S. B. Wang, Y. L. Min and S. H. Yu, J. Phys. Chem. C, 2007, 111, 3551–3554 CAS.
- L. L. Wang and L. Gao, J. Phys. Chem. C, 2009, 113, 15914–15920 CAS.
- C.-J. Jia, L.-D. Sun, Z.-G. Yan, L.-P. You, F. Luo, X.-D. Han, Y.-C. Pang, Z. Zhang and C.-H. Yan, Angew. Chem., 2005, 117, 4402–4407 CrossRef.
- X. H. Liu, J. Zhang, L. W. Wang, T. L. Yang, X. Z. Guo, S. H. Wu and S. R. Wang, J. Mater. Chem., 2011, 21, 349–356 RSC.
- T. Sugimoto and A. Muramatsu, J. Colloid Interface Sci., 1996, 184, 626–638 CrossRef CAS.
- W. Wang, J. Y. Howe and B. Gu, J. Phys. Chem. C, 2008, 112, 9203–9208 CAS.
- Z. F. Pu, M. H. Cao, Y. Jing, K. L. Huang and C. W. Hu, Nanotechnology, 2006, 17, 799–804 CrossRef CAS.
- Z. P. Zhang, H. P. Sun, X. Q. Shao, D. F. Li, H. D. Yu and M. Y. Han, Adv. Mater., 2005, 17, 42–47 CrossRef CAS.
- X. G. Han, H. Z. He, Q. Kuang, X. Zhou, X. H. Zhang, T. Xu, Z. X. Xie and L. S. Zheng, J. Phys. Chem. C, 2008, 113, 584–589 Search PubMed.
- N. Tian, Z. Y. Zhou, S. G. Sun, Y. Ding and Z. L. Wang, Science, 2007, 316, 732 CrossRef CAS.
- Y. Shimizu and M. Egashira, Mrs Bull, 1999, 24, 18–24 CAS.
- N. Barsan and U. J. Weimar, J. Electroceram., 2001, 7, 143–167 CrossRef CAS.
- D. E. Williams, Sens. Actuators, B, 1999, 57, 1–16 CrossRef.
- A. G. Nasibulin, S. Rackauskas, H. Jiang, Y. Tian, P. R. Mudimela, S. D. Shandakov, L. I. Nasibulina, J. Sainio and E. I. Kauppinen, Nano Res., 2009, 2, 373–379 CrossRef CAS.
Footnote |
† Electronic supplementary information: EDS spectrum of rhombohedral α-Fe2O3 crystal (Fig. S1), SEM image of the α-Fe2O3 products prepared with 3.2 g formamide (Fig. S2) and the commercial α-Fe2O3 powder (Fig. S3). |
|
This journal is © The Royal Society of Chemistry 2012 |
Click here to see how this site uses Cookies. View our privacy policy here.