DOI:
10.1039/C2RA20406A
(Paper)
RSC Adv., 2012,
2, 5637-5644
A simple and efficient synthesis protocol for sulfonation of nitrobenzene under solvent-free conditions via a microreactor
Received
6th March 2012
, Accepted 13th April 2012
First published on 18th April 2012
Abstract
A simple and efficient method for the sulfonation of nitrobenzene using SO3 as the sulfonating agent in a microreactor was developed and conducted in this work. The reaction enthalpy was determined using a microreactor-based calorimeter. The effects of molar ratio of reactants, reaction temperature and liquid hourly space velocity (LHSV) on the reaction performance were experimentally studied under solvent-free conditions. Under optimized reaction conditions, 94% conversion of nitrobenzene (NB) and 88% yield of meta-nitrobenzenesulfonic acid (m-NBSA) was obtained even when the residence time was less than 2 s. A microreactor-batch set-up was fabricated and developed to completely convert NB. The process safety has been improved and reaction time has been reduced compared to the batch method. These results demonstrate that the multifunctional integrated microreactor is an extremely useful and highly efficient tool for the sulfonation of NB under solvent-free conditions.
Introduction
Sulfonation of aromatics is one of the essential organic reactions for the production of various intermediates and fine chemicals, such as color intensifiers, pigments, detergents, pharmaceuticals and pesticides.1–2 It has drawn continuous interest to develop an efficient, safe and clean sulfonation process or technology.3–4 Sulfur trioxide (SO3), oleum, sulfuric acid and chlorosulfuric acid are the general sulfonating agents and of high industrial importance due to the high availability and low cost of these reagents.5 However, the sulfonation with sulfuric acid or oleum is an equilibrium process due to hydrolysis in produced water.6 Moreover, it requires a minimum concentration of sulfuric acid in the range of 78–90% by weight for reaction.7 Thus a high molar ratio of sulfonating agent to substrate is required to maintain a sufficiently high concentration of sulfuric acid which may lead to massive use of sulfuric acid. The sulfonation with chlorosulfuric acid can also create an acid disposal problem due to the generation of hydrogen chloride during the reaction process.8 SO3 as the sulfonating agent has some distinctive advantages compared with other sulfonating agents, such as high activity, fast reaction rate, high atom economy due to direct addition of SO3 group, low material cost and minimal waste acid generation. Thus, SO3 sulfonation is a clean and efficient process and has been extensively performed in chemical industry.9
However, SO3 sulfonation is usually a very fast and highly exothermic reaction. The enthalpy of sulfonation of aromatics is about 168 kJ mol−1.10 The state of SO3 can be gas or liquid according to the requests of different technological processes. The low heat and mass transfer capabilities of conventional reactors may give rise to the insufficient mixing and local overheating, and thus lead to the formation of many impurities or even the runaway of reaction.11 In a recent SO3 sulfonation process, a variety of reactors such as thin-film reactors, falling film reactors and jet loop reactors have been used.10–12 In particular, falling film reactors are often used on the anionic surfactant processes nowadays, and some methods to intensify heat and mass transfer have been taken such as adding corrugated walls and baffles.12 Even so, temperature control is not yet satisfactory and scale-up problem needs to be solved.1 To control the reaction in a mild way, SO3 is required to be premixed with large amounts of inert gas or solvents (e.g. dry air, nitrogen, dichloroethane, sulfur dioxide and dioxane) to lower its activity.13 Besides, large quantities of coolants are used in the external heat exchangers to strictly control the reaction temperature for these conventional reactors.14 Therefore, the reaction time, energy consumption and separation cost are still not ideal considering the requests of green processes.
For the purpose of solving the problems occurring during SO3 sulfonation mentioned above, it is significant to exploit the feasibility of microreaction technology for the SO3 sulfonation process. Microreaction technology has provided great opportunities for fast and highly exothermic reactions, production of unstable or toxic materials and other useful substances with improved process safety and high product quality.15–18 Microreactors, with dimensions in the sub-millimeter range, can offer a much shorter length and large surface-to-volume ratio for mass and heat transport, consequently intensifying the heat and mass transfer capability significantly. The mass and heat transfer coefficients in microreactors are larger than those in conventional reactors by two orders of magnitude.19,20 The sulfonation of toluene with a gas mixture of SO3 and N2 as the sulfonating agent has been investigated in a microreactor system by Müller and his co-workers.21 They found that high selectivity was obtained with precise temperature control and high pressure resistance of the microreactor at a SO3
:
toluene molar ratio of 0.05–0.15. This microreactor system contained separated microreactor, micromixer and micro heat exchanger, thus the removal of reaction heat was not synchronous with the reaction.
In this study, the sulfonation of nitrobenzene (NB) with liquid SO3 was carried out in a microreactor system to target the exploitation of green technology to reduce or eliminate solvents and optimize the sulfonation process. The functionalities of mixing, reaction and heat transfer were integrated in a compact multifunctional microreactor system to realize a large enhancement of heat and mass transfer.22 The main reaction is shown in Scheme 1. The corresponding desired product is meta-nitrobenzenesulfonic acid (m-NBSA) which is a useful dye intermediate for the synthesis of meta-nitrobenzenesulfonic acid sodium salt, meta-aminobenzenesulfonic, meta-aminophenol, aniline-2,5-disulfonic acid and meta-(diethylamino) phenol; and the main by-product is bis(3-nitrophenyl)sulfone (BNPS). The reaction mechanism proposed by Cerfontain et al. is described in Scheme 2.23,24 The sulfonation of NB with SO3 proceeds in a stepwise manner viz. the primary sulfonation from NB to (m-nitrophenyl) pyrosulfonic acid, and the secondary and undesired sulfonation from (m-nitrophenyl) pyrosulfonic acid, to the m-NBSA and BNPS, respectively. The reaction involves a SO3 phase and an organic phase and it takes place at the interface of the immiscible liquid–liquid phases and in the SO3 phase.25
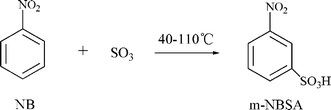 |
| Scheme 1 The SO3 sulfonation of NB with the desired product, m-NBSA. | |
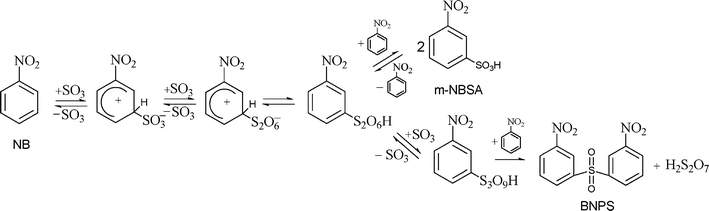 |
| Scheme 2 Reaction sequence for SO3–NB sulfonation with the formation of the desired product (m-NBSA) and by-product (BNPS). | |
Experimental
Material
γ-SO3 (AR, 99.5%) was purchased commercially from Tianjin Bohai Chemical Industry Company (Tianjin), and NB (AR), H2SO4 (AR, 98.0%) and NaOH (AR, 96.0%) from Kermel Chemical Reagent Company (Tianjin), respectively. These reagents were used without further purification, and NaOH was used as the absorbent solution for removing SO3 in exhaust gas.
Microreactor
The microreactor used in this study was fabricated on a stainless steel plate by micromachining technology in our CNC machining center. It mainly contained one reaction plate with 16 micro reaction channels and two heat exchanging plates. The mixing, reaction and heat exchange units had been integrated in this microreactor system. Both the SO3 and NB inlets had a microstructure of 16 distribution channels. The diameter of the mixing micropores is ca. 700 μm. The width, depth and length of each micro reaction channel were 750 μm, 280 μm and 57 mm, respectively. The total reaction volume of these microchannels was 0.27 ml. The picture of the compact multifunctional microreactor, the schematic diagrams of SO3 and NB fluid routes in the reaction plate and heat transfer plate are shown in Fig. 1.
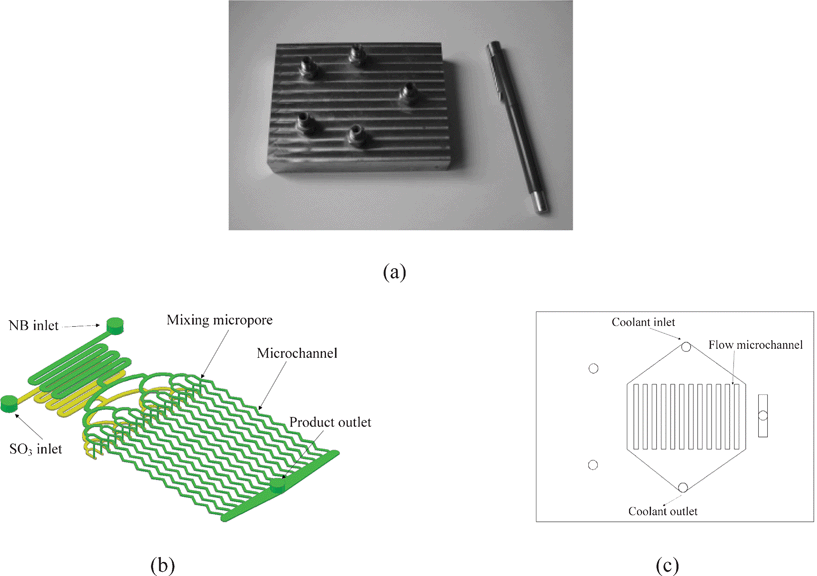 |
| Fig. 1 Picture of the compact multifunctional microreactor (a), schematic diagrams of SO3 and NB fluids routes in the reaction plate (b) and heat transfer plate (c). | |
Synthesis in batch mode, microreactor mode and microreactor-batch mode
In batch mode, SO3 (130 g, 1.625 mol) was added dropwise to NB solution (156 g, 1.267 mol) in a glass flask at 40–90 °C. During the period of the addition, the NB solvent in a flask was stirred by the impeller with a stirring speed of 600 rpm. The time for adding SO3 was 6 h, and then the reaction mixture was stirred for another 4 h at an elevated temperature of 110 °C. The total reaction time was 10 h.
For the microreactor mode, the experimental set-up is illustrated in Fig. 2. It mainly consists of two HPLC pumps, a microreactor, a temperature control system and a product collection system. The NB and SO3 streams were fed into the microreactor system simultaneously by the two HPLC pumps. They were divided into 16-branch flows via two fluid distributions, then mixed at the mixing micropores and reacted in the following microchannels. The electric heating rods as the heating elements were imbedded into the microreactor to supply heat, and the water as the cooling medium was circulated through the heat exchanger part of the multifunctional microreactor to absorb reaction heat. The inner temperature of the microreactor was monitored by the thermocouple (K-type) and controlled using an external circuit (Yudian thermostat, China). The temperatures of fluids in the inlet and the outlet of the microreactor were also measured, respectively. In order to change the reactant molar ratio and the residence time, each pump was adjusted to the desired volume flow rate and the flow rate was calibrated by measuring the ingoing and outgoing weights of SO3 and NB, respectively, while the density of each stream was measured previously.
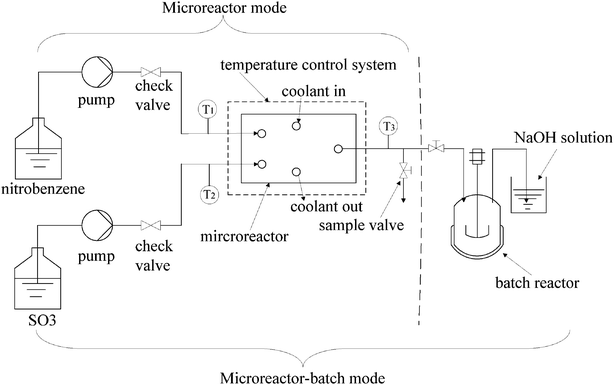 |
| Fig. 2 Experimental set-up of the microreactor system for the sulfonation of nitrobenzene. | |
The superficial liquid hourly space velocity (LHSV), the mean residence time (τ) and the space time yield (STY) of the microreactor were calculated by eqn (1)–(3), respectively.
| 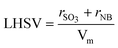 | (1) |
|  | (2) |
|  | (3) |
where rSO3 and rNB are the volume flow rate of SO3 and NB, respectively. Vm is the reaction volume of microreactor. mp is the weight of m-NBSA collected during the reaction time.
In microreactor-batch mode, the experimental set-up is also shown in Fig. 2. The difference from the microreactor mode was that a glass flask was connected with the microreactor in series and the sample valve was turned off. The effluent stream was collected for 0.5 h in a glass flask at a stirring rate of 600 rpm and temperature of 90 °C, then the supply of reactants was stopped and the reaction mixture in the glass flask was stirred continuously for 3.5 h at 110 °C. The total reaction time was 4 h.
Characterization
Each product sample was taken and instantly diluted in 30 ml methanol to terminate the reaction. For the determination of conversion and selectivity, a HPLC system (Shimadzu LC-10A, Japan) equipped with a column from Waters (Atlantis HILIC Silica 5 μm, 4.6 × 150 mm) was used. The mass fractions of NB, m-NBSA and BNPS were determined by using the UV-detector of HPLC at a wave length of 231 nm. The flow rate of eluent during HPLC measurements was 0.52 ml min−1 which consisted of 95% methanol and 5% water solution.
Results and discussion
Determination of the reaction enthalpy of sulfonation by microreactor-based calorimetery
To ensure the safety of the sulfonation process, the temperature is usually maintained at approximately 40–110 °C in a conventional batch reactor. When the reaction temperature of batch reactor exceeds 150 °C, the runaway of reaction will possibly come out or even carbonization. The fast heat transport rate as well as the low liquid hold up in the microreactor ensures excellent temperature control and the safety of the sulfonation process. In our experiments, the sulfonation process could proceed steadily without leaking of SO3.
The reaction enthalpy is one of the key characteristic parameters in fast exothermic reaction systems. Benefiting from quick and uniform mixing performance in microreactor, the microreactor-based calorimeter has been demonstrated as an effective tool to measure the enthalpy of fast exothermal reactions.26 The reaction enthalpy of the SO3 sulfonation of NB was determined according to the temperature variation of reactant fluids in the inlet and outlet of the microreactor under nearly adiabatic conditions by wrapping the microreactor with adiabatic cotton. With a high selectivity of m-NBPS, the effect of the side reaction on the measurement could be neglected. The energy conservation can be expressed as eqn (4).
|
| (4) |
where Δ
rHm is the reaction enthalpy of sulfonation, J mol
−1;
QL is the thermal loss rate of the microreactor system, J min
−1; Δ
H is thermal energy rise rate of the reaction system, J min
−1;
nNB is the molar feed rate of insufficient reactant NB, mol min
−1;
XNB is the conversion of NB, %.
The reaction enthalpy leads to a temperature rise in the reaction streams and the evaporation of SO3. ΔH is calculated based on the temperatures of the reaction stream in the inlets and outlet of the microreactor, as shown in eqn (5).
|
| (5) |
where
cNB,
c1, SO3 and
cg, SO3 (J mol
−1 K
−1) are the heat capacities of NB, liquid SO
3 and gaseous SO
3, respectively.
Tout and
Tin (K) are the temperatures of the outlet fluid and the inlet fluids, respectively. Δ
rHvap is the change in enthalpy of vaporization of SO
3, J mol
−1;
nSO3 is the molar feed rate of liquid SO
3, mol min
−1.
The heat capacities of reactants and products are given in Table 1.27–29 The thermal loss rate QL could be neglected due to short residence time and nearly adiabatic condition. When the flow rates of SO3 and NB were 10.0 ml min−1 and 20.0 ml min−1, the fluid temperatures in the inlet and the outlet of microreactor were 313.2 K and 376.2 K, respectively. The conversion of NB was 48.8% with a relatively high selectivity of 93.3%. The reaction enthalpy of the NB sulfonation with SO3 was calculated based on eqn (4), and its value was −177 kJ mol−1, which was similar to the result reported by Johnson et al.11
Table 1 The heat capacities and ΔrHvap of SO3 in the working system
Symbol |
Value or expression |
Applied range (T, P) |
c
NB
|
263.89 + 1.76 × (T −293.15) J mol−1 K−1 |
293–393 K,1 atm |
c
1, SO3
|
257.76 J mol−1 K−1 |
303 K, 1 atm |
c
g, SO3
|
24.03 + 119.46 × 10−3 × T − 94.39 × 10−6 × T2 + 26.96 × 10−9 × T3 − 0.118 × 106 × T−2 |
318–500 K, 1 atm |
ΔrHvap |
46.78 × 103 J mol−1 |
318 K, 1 atm |
Influence of molar ratio of reactants (microreactor mode)
In order to determine the appropriate reaction conditions, the influence of the SO3
:
NB molar ratio on the conversion of NB and selectivity of m-NBSA was first studied in the microreactor mode, at a fixed LHSV of 2000 h−1 and temperature of 60 °C. Fig. 3 demonstrates that NB conversion obviously increased when the molar ratio of SO3 to NB was increased. This can be explained from the reaction kinetics that the SO3 sulfonation of NB is a third-order reaction, and the reaction rate is first order with respect to NB and is second order with respect to SO3.30 An increase in the molar ratio of SO3 to NB resulted in the increase of the initial mass fraction of SO3 and the decrease of the initial mass fraction of NB, so the conversion of NB increased at the same reaction time. A low molar ratio will lead to an insufficient conversion of NB, while a high molar ratio will give a higher conversion of NB; but, a high molar ratio will lead to more SO3 waste which needs to be reused or neutralized.
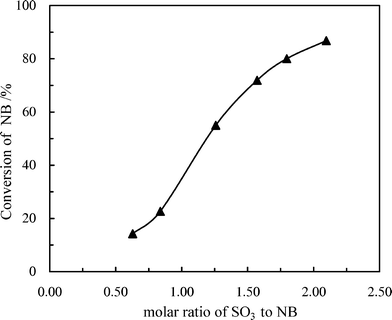 |
| Fig. 3 Effect of SO3 : NB molar ratio on the conversion of NB. T = 60 °C, LHSV = 2000 h−1. | |
Fig. 4 shows that selectivity of NB was almost the same when the SO3
:
NB molar ratio was varied from 0.63 to 2.10. For example, the selectivity of NB was 92.6% at a molar ratio of 0.63, and the selectivity was weakly decreased to 90.1% as the molar ratio was raised to 2.1. This may indicate that selectivity of m-NBSA is not sensitive to the change of molar ratio in the microreactor system.
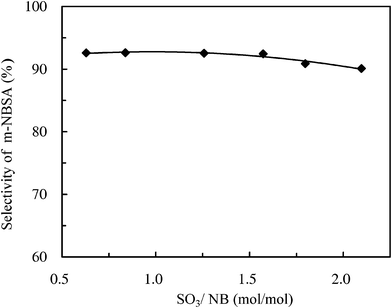 |
| Fig. 4 Effect of SO3 : NB molar ratio on the selectivity of m-NBSA. T = 60 °C, LHSV = 2000 h−1. | |
Influence of reaction temperature (microreactor mode)
Temperature usually plays a great role in the reaction performance because the intrinsic rate constant increases with the increasing of reaction temperature according to the Arrhenius Equation. Fig. 5 demonstrates the effect of reaction temperature on the conversion of NB in the microreactor mode. The conversion of NB decreased with the increasing of reaction temperature. It can be explained that high temperatures exceeded the boiling point of liquid SO3 (b.p. 44.8 °C, 1 atm) and thus it caused partial evaporation. The phenomenon of evaporation significantly reduced the actual residence time of reactants since the gas volume is usually several hundredfold larger than the liquid volume at the same weight of the material. In this experiment, the white smoke of a gaseous SO3–water mixture was generated at high temperatures if the effluent was exposed to the air; the phenomenon was more obvious at higher temperature. As a result, the rising temperature led to a decrease in the conversion of NB.
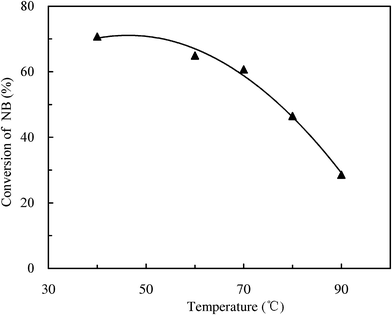 |
| Fig. 5 Effect of temperature on the conversion of NB. SO3 : NB = 1.26, LHSV = 2000 h−1. | |
Influence of space velocity (microreactor mode)
It is well known LHSV usually has great effects on the mass transfer process in liquid–liquid heterogeneous reactions. An increase in LHSV can lead to an increase in Reynolds numbers, which finally improves the mass transport on the reaction process.31 Tests were carried out to study the effect of LHSV on the conversion of NB in the microreactor mode. The gas leave effect at 50 °C was considered to be the same between different LHSVs since the gas phase can be immediately absorbed to or reacted with nitrobenzene.30 LHSV was varied from 800 to 8000 h−1 by changing the substrate flow rate. It can be observed from Fig. 6 that the conversion of NB first increased with the increase of LHSV, and then decreased. The highest conversion was obtained at an LHSV of approximately 4000 h−1. This is attributed to the fact that the reaction performance of a fast liquid–liquid multiphase reaction is dependent on both the mass transfer rate and the reaction time.16 In Fig. 6, the range of LHSV can be divided to two zones for this reaction process, including 800–4000 h−1 as zone-1 and 4000–8000 h−1 as zone-2. The reaction process was dominated by the mass transfer in zone-1, thus the increase in LHSV was beneficial to the conversion of NB. However, in zone-2 the reaction process was mainly determined by the reaction kinetics. Therefore, the reduction in the reaction time because of the increase of LHSV resulted in lower conversion of NB. It was expected that a sharp increase in viscosity happened during the reaction, which severely degraded the mass transfer ability in the microreactor. These results indicate that mass transfer is still one of the key factors even in the microreactor system, especially when highly viscous liquids exist in the reaction process.
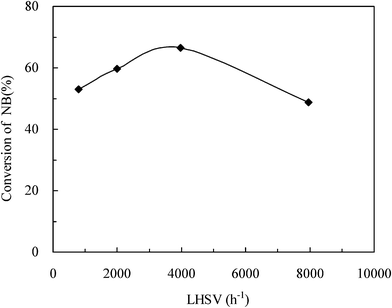 |
| Fig. 6 Effect of LHSV on the conversion of NB. T = 50 °C, SO3 : NB = 1.26. | |
Influence of solvent (microreactor mode)
In order to reduce the viscosity of the reaction system and increase the boiling point of the SO3 phase, H2SO4 was used as a solvent and premixed with SO3 due to its good solubility in sulfonation products. Fig. 7 shows that the conversion of NB with 90 wt.% SO3 was higher than that with pure SO3 as sulfonating agent at relatively high temperatures (70–90 °C) in the microreactor mode. This indicates that H2SO4 has a positive influence on the conversion of NB, which may be attributed to the improved boiling point of the sulfonating agent, decreased viscosity and the enhancement of mass transfer in the microreactor. However, the enhancement effect with H2SO4 addition is not obvious at low temperatures (50–70 °C), and the addition of H2SO4 requires the disposal of spent acid (H2SO4) and the premixing of SO3 with H2SO4. Therefore, the subsequent optimization will be based on the solvent-free conditions which greatly simplify the experimental process.
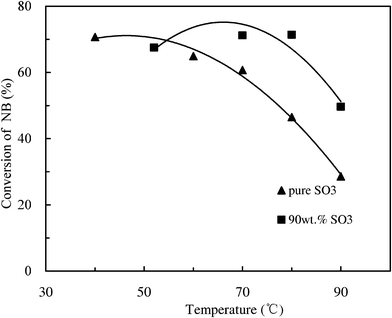 |
| Fig. 7 Comparison between two conditions with and without solvent under different temperatures. SO3 : NB = 1.26, LHSV = 2000 h−1. | |
Optimization in microreactor mode and microreactor-batch mode
More experimental tests in the microreactor mode were focused on choosing a suitable SO3
:
NB molar ratio to further optimize the reaction conditions while the other operating conditions were nearly optimal (i.e. temperature at 40 °C and LHSV at 2000 h−1). Table 2 shows the results of this optimization procedure. As expected, the conversion and yield increased with an increase in the molar ratio of SO3 to NB. At a high molar ratio of 1.76, the best result was obtained with 94% conversion of NB and 88% yield of m-NBSA (Table 2, entry 1). Even at a moderate molar ratio of 1.26, 71% conversion and 65% yield were obtained (Table 2, entry 3). To examine the durability and repeatability of the microreactor system, the continuous operation at the molar ratio of 1.76 was carried out for 4 h, and the yield of m-NBSA kept constant (88%) without the risk of clogging in the microreactor. Therefore it can realize a productivity of m-NBSA of 12 kg d−1 in this microreactor system.
Table 2 Optimization of sulfonation of NB in the microreactor
Entry |
SO3 : NB (mol/mol) |
Conversion (%) |
Yield (%) |
STY (103 kg h−1 L−3) |
Output (kg h−1) |
1 |
1.76 |
94 |
88 |
1.93 |
0.52 |
2 |
1.51 |
78 |
70 |
1.53 |
0.41 |
3 |
1.26 |
71 |
65 |
1.43 |
0.38 |
4 |
1.11 |
50 |
46 |
1.02 |
0.27 |
To further convert unreacted NB in the effluent from the microreactor, the microreactor-batch mode was also used under optimized conditions, i.e. 40 °C and 2000 h−1. At a molar ratio of 1.26, 100% conversion of NB and 92% selectivity of m-NBSA were obtained in 4 h. When the molar ratio dropped to 1.11, only 92% conversion was obtained in 4 h. The microreactor-batch mode was safe if the SO3
:
NB molar ratio was larger than 1.26. When 71% NB was converted in the microreactor and this part of the reaction heat was absorbed by a heat exchanger, the heat released from further reaction in the batch reactor was ca. 51 kJ mol−1, and the reaction rate had slowed down due to decreased concentration of SO3 and NB. External heating in a batch reactor is needed to maintain a proper reaction temperature and the reaction temperature can be easily controlled lower than 150 °C.
Comparison with the batch mode
The result from the bath mode (Table 3, entry 4) was compared with that from the microreactor mode and the microreactor-batch mode in order to further demonstrate the superiority of the microreactor. It must be emphasized that the dripping of SO3 to NB should be very slow to control the temperature under 90 °C for the purpose of preventing the reaction from becoming uncontrolled. The result was obtained with 100% conversion and 93% selectivity in 10 h. However, this batch mode may have a scale-up issue and safety risk. Other literature results in the batch mode were also summarized in Table 3 (entries 1–3).32–34 Entry 1 shows that only 50% yield was achieved in a long reaction time of 72 h. In addition, 2.l mol trifluoroacetic anhydride (TFFA) should be used as a catalyst per mol NB. Entry 2 demonstrates that an excellent yield of 98% was obtained at room temperature, but much more dichloroethane was used as a solvent, and the total ratio of (SO3 + H2SO4) to NB was as high as two. Entry 3 shows that sulfonation with 65% oleum reached 91% yield at a molar ratio of 1.53, and this process was somewhat complicated.
Entry |
Mode |
Sulfonating agent |
(SO3+H2SO4) : NB (mol/mol) |
T (°C) |
Time (h) |
Con. (%) |
Sel. (%) |
1 |
Batch |
98% H2SO4 TFFA as a catalyst |
1 |
60 |
72 |
50 |
100 |
2 |
Batch |
3.5% SO3, Dichloroethane as a solvent |
2 |
22 |
6 |
100 |
98 |
3 |
Batch |
65% Oleum |
1.51 |
100–110 |
10 |
100 |
91 |
4 |
Batch SO3 addition |
Liquid SO3 |
1.29 |
40–110 |
10 |
100 |
93 |
5 |
Continuous microreactor |
Liquid SO3 |
1.73 |
40 |
5 × 10−4 |
94 |
92 |
6 |
Continuous microreactor |
Liquid SO3 |
1.26 |
40 |
5 × 10−4 |
71 |
92 |
7 |
Microreactor + conventional vessel |
Liquid SO3 |
1.26 |
40–60 °C in microreator 90–110 °C in vessel |
4 |
100 |
92 |
In the microreactor mode (Table 3, entries5–6), with a residence time of 1.8 s and a temperature of 40 °C, 94% conversion of NB and 88% yield of m-NBSA were obtained at a high molar ratio of 1.76, and 71% NB was converted at a moderate molar ratio of 1.26. In the microreactor-batch mode (Table 3, entry 7), only 4 h was required for complete conversion of NB which was much less than required in the batch mode. Moreover, the total molar ratio 1.26 in entry 6 and 7 was lowest. It is worth noting that although the BNPS formed in entry 6 and 7 was somewhat higher than from other methods, the BNPS could be easily separated from filtration and then converted to another high-value intermediate for the synthesis of polysulfonamide fiber.35 It is therefore concluded that the sulfonation under microreactor conditions (microreactor mode and microreactor-batch mode) was better than that under batch conditions in solvent and reaction time. The reaction rate is much faster and the safety is greatly improved.
Concluding remarks
This investigation explored the feasibility of the microreactor system for the very fast and highly exothermic sulfonation reaction with liquid SO3 in a simple and efficient way under solvent-free conditions. The reaction enthalpy was determined with a microreactor-based calorimeter and the effects of some process parameters on the reaction performance were studied. The results demonstrate that the reaction time has been greatly reduced and the process safety has been improved both in the microreactor mode and microreactor-batch mode compared to those in the batch mode. Besides, in the microreactor-batch mode, the reaction was complete with a high selectivity of 92% when the molar ratio of SO3 to NB was 1.26 and the reaction time was 4 h. This study also indicates the potential commercial opportunity that the production of kilograms of sulfonated products per hour could be achieved by using a microreactor in a continuous way. Scale-up of production in microreactors can be easily realized with the method of numbering-up.
Acknowledgements
The work reported in this article was financially supported by research grants from the Ministry of Science and Technology of China (2012BAA08B02), and the frame work of the Sino-French project MIGALI via the National Natural Science Foundation of China (no.20911130358), and the Fund of Dalian Institute of Chemical Physics, CAS (no.K2009D01).
References
- D. W. Roberts, Org. Process Res. Dev., 2003, 7, 172–184 CrossRef CAS.
- R. Katritzky, M. S. Kim, D. Fedoseyenko, K. Widyan, M. Siskin and M. Francisco, Tetrahedron, 2009, 65, 1111–1114 CrossRef.
- F. Kucera and J. Jancar, Polym. Eng. Sci., 2009, 49, 1839–1845 CAS.
- S. Mukhopadhyay and A. T. Bell, Adv. Synth. Catal., 2004, 346, 913–916 CrossRef CAS.
- A. R. Hajipour, B. Mirjalili, A. Zarei, L. Khazdooz and A. E. Ruoho, Tetrahedron Lett., 2004, 45, 6607–6609 CrossRef CAS.
- S. Hawash, N. Kamal, G. El-Diwani, S. Sherif and S. Eissa, Ind. Eng. Chem. Res., 1993, 32, 1066–1070 CrossRef CAS.
-
A. Koebner, US Pat., 3,946,037, 1976 Search PubMed.
- A. Lanteri and G. Mazzoni, J. Am. Oil Chem. Soc., 1978, 55, 128–133 CrossRef CAS.
- D. W. Roberts, Org. Process Res. Dev., 1998, 2, 194–202 CrossRef CAS.
- J. C. Wu, B. H. Wang, D. L. Zhang, G. F. Song, J. T. Yuan and B. F. Liu, J. Chem. Technol. Biotechnol., 2001, 76, 619–623 CrossRef CAS.
- G. R. Johnson and B. L. Crynes, Ind. Eng. Chem. Process Des. Dev., 1974, 13, 6–14 CAS.
- T. A. Zaid, K. Benmaza and C. E. Chitour, Chem. Eng. J., 2000, 76, 99–102 CrossRef CAS.
- Y. Q. Zou and E. Khor, Carbohydr. Polym., 2009, 77, 516–525 CrossRef CAS.
- J. A. T. Ortega, G. M. Mdina, O. Y. S. Palacios and J. S. Castellanos, Chem. Prod. Process Model., 2009, 4, 1–18 Search PubMed.
- R. J. Davy and C. V. Stevens, Green Chem., 2007, 9, 386–390 RSC.
- L. J. Kong, Q. Lin, X. M. Lv, Y. T. Yang, Y. Jia and Y. M. Zhou, Green Chem., 2009, 11, 1108–1111 RSC.
- R. J. J. Jachuck, D. K. Selvaraj and R. S. Varma, Green Chem., 2006, 8, 29–33 RSC.
- J. N. Shen, Y. C. Zhao, G. W. Chen and Q. Yuan, Chin. J. Chem. Eng., 2009, 17, 412–418 CrossRef CAS.
- Y. H. Su, Y. C. Zhao, G. W. Chen and Q. Yuan, Chem. Eng. Sci., 2010, 65, 3947–3956 CrossRef CAS.
- Y. C. Zhao, Y. H. Su, G. W. Chen and Q. Yuan, Chem. Eng. Sci., 2010, 65, 1563–1570 CrossRef CAS.
- A. Müller, V. Cominos, V. Hessel, B. Horn, J. Schürer, A. Ziogas, K. Jähnisch, V. Hillmann, V. Groβer, K. A. Jam, A. Bazzanella, G. Rinke and M. Kraut, Chem. Eng. J., 2005, 107, 205–214 CrossRef.
- X. L. Fan, H. S. Chen, Y. L. Ding, P. K. Plucinskia and A. A. Lapkin, Green Chem., 2008, 10, 670–677 RSC.
- G. Koleva, B. Galabov, J. Kong, H. F. Schaefer and P. R. Schleyer, J. Am. Chem. Soc., 2011, 133, 19094–19101 CrossRef CAS.
- J. K. Bosscher and H. Cerfontain, Tetrahedron, 1968, 24, 6543 CrossRef CAS.
- K. Wang, Y. C. Lu, J. H. Xu, X. C. Gong and G. S. Luo, AIChE J., 2006, 52, 4207–4213 CrossRef CAS.
- K. Wang, Y. C. Lu, H. W. Shao and G. S. Luo, AIChE J., 2010, 56, 1045–1052 CrossRef CAS.
- M. W. Chase, J. Phys. Chem. Ref. Data, 1998, 9, 1–1951 Search PubMed.
- J. H. Colwell and G. D. Halsey, J. Phys. Chem., 1962, 66, 2179–2182 CrossRef CAS.
- K. D. Wadsworth and C. N. Hinshelwood, J. Chem. Soc., 1944, 469 RSC.
- A. A. C. M. Beenackers and W. P. M. W. Swaaij, Phosphorus and sulfur, 1981, 10, 217–229 CAS.
- Y. H. Su, Y. C. Zhao, F. J. Jiao, G. W. Chen and Q. Yuan, AIChE J., 2011, 57, 1409–1418 CrossRef CAS.
- B. W. Corby, A. D. Gray, P. J. Meaney, M. J. Falvey, G. P. Lawrence and T. P. Smyth, J. Chem. Res., 2002, 7, 326–327 CrossRef.
- H. Cerfontain, Y. S Zhou and B. H. Bakker, Recl. Trav. Chim. Pays-Bas, 1994, 113, 403–410 CAS.
- X. L. Jia, Y. H. Yu, G. Li, G. Sui, P. Li and X. P. Yang, Journal of Applied Polymer Science, 2011, 118, 1060–1067 Search PubMed.
|
This journal is © The Royal Society of Chemistry 2012 |
Click here to see how this site uses Cookies. View our privacy policy here.