DOI:
10.1039/C1RA00456E
(Paper)
RSC Adv., 2012,
2, 840-847
AGET
ATRP of methyl methacrylatevia a bimetallic catalyst
Received
14th July 2011
, Accepted 11th October 2011
First published on 23rd November 2011
Introduction
Atom transfer radical polymerization (ATRP), which was discovered by Matyjaszewski1 and Sawamoto2 in 1995, has been developed to be a powerful controlled/living radical polymerization (CRP) method. Plentiful well-defined functional polymers with predetermined molecular weight and low molecular weight distribution3–11 have been prepared by the ATRP technique in the last decades. In ATRP, the chain propagation of polymer is mediated by transition-metal complexes which establish a dynamic equilibrium between dormant species and active propagating radicals.1,2 Up to now, several new ATRP techniques including simultaneous reverse and normal initiation (SR&NI) ATRP12–14 or initiators for continuous activator regeneration (ICAR) ATRP,15–17 activators generated by electron transfer (AGET) ATRP,18–23 and activators regenerated by electron transfer (ARGET) ATRP,24–26 have been developed to overcome the drawbacks of normal or reverse ATRP.
Actually, catalytic system always plays a key role in all above-mentioned ATRP techniques. By far, many transition metals such as copper,27–29iron,30–35ruthenium,36–38nickel,39–41cobalt,42,43molybdenum44–48 and osmium49–50 have been used to catalyze an ATRP process solely. However, as for mono-metallic ATRP catalyst systems, in some cases, an extra additive needs to add in order to get faster polymerization rate and/or better controllability. What will happen if a co-catalyst (i.e., a bimetallic catalyst) is used in an ATRP process? As we know, only few bimetallic catalyst systems have been reported in an ATRP process. For instance, Zhang et al. reported ATRPs of methyl methacrylate (MMA) catalyzed by SnCl2·2H2O(FeCl2·4H2O)/FeCl3·6H2O/MA5-DETA51 and MCl2/FeCl3·6H2O/PPh3 (M = Ni, Co, or Mn) catalyst systems.52 Huang et al. reported a novel immobilized cobalt(II)/copper(II) bimetallic catalyst for ATRP of MMA.53 Very recently, Matyjaszewski and coworkers reported a well-controlled ATRP of MA with three zerovalent metals, Zn(0), Mg(0), and Fe(0), as reducing agents to continuously regenerate the activator in a copper-mediated ATRP process in polar solvent dimethyl sulfoxide (DMSO) at 25 °C.54
As we know, polar solvents such as DMSO plays a key role in a CRP process in the presence of zerovalent metals due to the fact that the alkyl halide could act as the initiator for the polymerization by the activation of zerovalent metals.55–57 Actually, there have been a number of excellent works on CRP in the presence of zerovalent metals in a polar solvent such as DMSO at room temperature.58–62 Considering the advantages of AGET ATRP and eliminating the effect of solvent and zerovalent metals on the polymerization mentioned above, in this work, a Fe/Cu bimetallic catalyst system was established to catalyze AGET ATRP of methyl methacrylate (MMA) in bulk for the first time, using ethyl 2-bromoisobutyrate (EBiB) as the initiator, FeCl3·6H2O and CuCl as the bimetallic catalysts and triphenylphosphine (PPh3) or tris(3,6-dioxaheptyl)amine (TDA-1) as the ligand. Compared with mono-metallic catalyst, the current bimetallic catalyst system showed higher catalytic activity, which provides a new strategy for highly efficient ATRP process.
Experimental section
Materials
Methyl methacrylate (MMA) was purchased from Shanghai Chemical Reagents Co. (Shanghai, China). It was washed with an aqueous solution of sodium hydroxide (5 wt%) three times, followed by deionized water until neutralization, and then dried over anhydrous magnesium sulfate, distilled under reduced pressure and stored at −18 °C. Iron(III) chloride hexahydrate (FeCl3·6H2O, +99%), ferrous chloride tetrahydrate (FeCl2·4H2O, +99%), triphenylphosphine (PPh3, +99%), cuprous chloride (CuCl, +99%) and ascorbic acid (+99.7%) were purchased from Shanghai Chemical Reagents Co. (Shanghai, China) and used as received. Tris(3,6-dioxaheptyl)amine (TDA-1) (97%) was purchased from Linhai Xinghua Chemical Factory (Zhejiang, China) and used as received. Ethyl 2-bromoisobutyrate (EBiB) (+98%) was purchased from Acros and used as received. Tetrahydrofuran (THF) (analytical reagent) and all other chemicals were obtained from Shanghai Chemical Reagents Co. and used as received unless mentioned.
General procedure for polymerization of MMA under different polymerization conditions
A typical bulk polymerization procedure for bulk AGET ATRP of MMA, using EBiB as the ATRP initiator and FeCl3·6H2O/PPh3/CuCl as the catalyst system with a molar ratio of [MMA]0/[EBiB]0/[FeCl3·6H2O]0/[PPh3]0/[CuCl]0 = 300
:
1
:
0.5
:
1.5
:
0.1, is as follows: a mixture was obtained by adding FeCl3·6H2O (12.8 mg, 0.046 mmol), CuCl (0.93 mg, 0.009 mmol), PPh3 (37.1 mg, 0.140 mmol), MMA (3.0 mL, 28.0 mmol) and EBiB initiator (13.8 μL, 0.093 mmol) to a dried ampoule. Another bulk polymerization procedure for AGET ATRP of MMA, using EBiB as the ATRP initiator and FeCl3·6H2O/TDA-1/CuCl as the catalyst system with a molar ratio of [MMA]0/[EBiB]0/[FeCl3·6H2O]0/[TDA-1]0/[CuCl]0 = 300
:
1
:
0.5
:
1.5
:
0.1, is as follows: a mixture was obtained by adding FeCl3·6H2O (12.8 mg, 0.046 mmol), CuCl (0.93 mg, 0.009 mmol), TDA-1 (45.3 mg, 0.140 mmol), MMA (3.0 mL, 28.0 mmol) and EBiB initiator (13.8 μL, 0.093 mmol) to a dried ampoule. For the deoxygenated system, the mixture was thoroughly bubbled with argon for 20 min to eliminate the dissolved oxygen, and then flame-sealed. For the oxygenated system, the ampoule was flame-sealed directly (no bubbling with argon) and then transferred into an oil bath held by a thermostat at the desired temperature (90 °C) to polymerize under stirring. The oxygen concentration from air ([O2]0 = 1.7 × 10−2 mol L−1, based on the reaction solution (3 mL)) was calculated from the residual volume (air volume, 5.3 mL) of ampoule after adding the reaction mixture and ignoring the amount of oxygen dissolved in the liquids.20 After the desired polymerization time, the ampoule was cooled by immersing it into iced water. Afterwards, it was opened and the contents were dissolved in THF (∼2 mL), and precipitated into a large amount of methanol (∼200 mL). The polymer obtained by filtration was dried under vacuum until constant weight at 50 °C. The monomer conversion was determined gravimetrically.
For AGET ATRP using ascorbic acid as the reducing agent, the polymerization procedure with the molar ratio of [MMA]0/[EBiB]0/[FeCl3·6H2O]0/[PPh3]0/[ascorbic acid]0 = 300
:
1
:
0.5
:
1.5
:
0.1 or [MMA]0/[EBiB]0/[FeCl3·6H2O]0/[TDA-1]0/[ascorbic acid]0 = 300
:
1
:
0.5
:
1.5
:
0.1 is the same as that in the deoxygenated system mentioned above except that an additional ascorbic acid (1.6 mg, 0.009 mmol) instead of CuCl was added.
Chain extension of PMMA via bimetal-catalyzed bulk AGET ATRP
A predetermined quantity of PMMA (obtained by bimetal-catalyzed AGET ATRP of MMA in the absence of oxygen) was added to a dried ampoule, and then the predetermined quantity of MMA, FeCl3·6H2O, CuCl and TDA-1 or PPh3 were added. The rest of the procedures were the same as the deoxygenated system described above. The chain-extension polymerization was carried out in bulk under stirring at 90 °C.
Characterizations
The number-average molecular weight (Mn,GPC) values and molecular weight distribution (Mw/Mn) values of the polymers were determined using Waters 1515 gel permeation chromatograph (GPC) equipped with a refractive index detector (Waters 2414), using HR 1, HR 2 and HR 4 (7.8 × 300 mm, 5 μm beads' size) columns with molecular weights in the range 102–5 × 105 g mol−1. THF was used as an eluent at a flow rate of 1.0 mL min−1 and 30 °C. The GPC samples were injected using a Waters 717 plus autosampler and calibrated with poly(methyl methacrylate) standards from Waters. 1H NMR spectrum was recorded on an Inova 400 MHz nuclear magnetic resonance (NMR) instrument using CDCl3 as the solvent and tetramethylsilane (TMS) as the internal standard at ambient temperature.
Results and discussion
The effect of the amounts of CuCl and FeCl3·6H2O on the polymerization of MMA with PPh3 as a ligand was first investigated. As shown in Table 1, when the molar ratio of [Cu(I)]0/[Fe(III)]0 was 1/10 and 1/5 (entries 2–3 in Table 1), the experimental results showed that the polymerizations were well-controlled with narrow Mw/Mn (1.25 and 1.21, respectively) and the molecular weights were close to their theoretical ones. In the absence of Cu(I)Cl, it was an iron(III)-mediated ATRP with FeCl3·6H2O/PPh3 catalyst system as reported by Noh's group.30,31 As shown in entry 1 in Table 1, the polymerization was controllable, but the polymerization rate was lower than that of bimetal-catalyzed polymerization. For instance, the monomer conversion could be reached up to 75% after 1.6 h for the bimetal-catalyzed AGET ATRP (entry 2 in Table 1), while 57.2% of conversion could be obtained after 1.6 h for the iron(III)-mediated ATRP (entry 1 in Table 1). However, for the FeCl2/PPh3 catalyst system (entry 8 in Table 1), in other words, the normal ATRP system, the Mw/Mn value for the obtained polymer became broader (1.37). Meanwhile, the polymerizations with different amounts of FeCl3·6H2O were also carried out. From Table 1, it can be seen that, along with decreasing amount of FeCl3·6H2O, from [Fe(III)]0/[Cu(I)]0 = 5/1 to 1/1 (entries 3–6 in Table 1), the Mw/Mn values increased gradually from 1.21 to1.43, and the molecular weights somewhat deviated from their corresponding theoretical values correspondingly. This is contributed to the fact that the total amount of catalyst reduced with the decreasing of the molar ratio of [Fe(III)]0/[Cu(I)]0 in these cases. Therefore, to obtain a well-controlled polymerization process, appropriate amount of Fe(III) catalyst should be employed. At the same time, we investigated the polymerization without FeCl3·6H2O, namely a normal copper-mediated ATRP of MMA using CuCl/PPh3 as the catalyst (entry 7 in Table 1). The molecular weight of the polymer with narrow Mw/Mn (1.21) agreed with the theoretical value, which indicated that Cu(I)Cl/PPh3 could mediate the polymerization well in this case. However, the polymerization rate was slower than that in the presence of FeCl3·6H2O significantly. For example, the monomer conversion could be reached up to 93.5% after 2 h for the bimetal-catalyzed AGET ATRP (entry 3 in Table 1); while 91.4% of conversion could be obtained after 46.3 h for the copper-mediated ATRP (entry 7 in Table 1). Therefore, it could be surmised that the adding of CuCl not only can accelerate the rate of polymerization, but also can take good control over molecular weight and molecular weight distribution of the polymers.
Table 1 Experimental results of the bimetal-catalyzed AGET ATRP of MMA in bulk with different amounts of FeCl3·6H2O in the absence of oxygen at 90 °C
Entry |
Ra |
Time (h) |
Conversion (%) |
M
n,th
b (g mol−1) |
M
n,GPC (g mol−1) |
M
w/Mn |
R = [MMA]0/[EBiB]0/[FeCl3·6H2O]0/[PPh3]0/[CuCl]0.
M
n,th
= ([M]0/[EBiB]0) × Mw,MMA × conversion%.
Fe(III)-mediated ATRP.
Normal ATRP catalyzed by CuCl/PPh3 complexes.
Using FeCl2·4H2O instead of FeCl3·6H2O, namely normal ATRP catalyzed by FeCl2/PPh3 complexes.
|
1c |
300 : 1 : 0.5 : 1.5 : 0 |
1.6 |
57.2 |
17 170 |
16 900 |
1.18 |
2 |
300 : 1 : 0.5 : 1.5 : 0.05 |
1.6 |
75.0 |
22 510 |
24 950 |
1.25 |
3 |
300 : 1 : 0.5 : 1.5 : 0.1 |
2.0 |
93.5 |
28 070 |
29 950 |
1.21 |
4 |
300 : 1 : 0.3 : 0.9 : 0.1 |
2.1 |
76.9 |
23 080 |
22 040 |
1.27 |
5 |
300 : 1 : 0.2 : 0.6 : 0.1 |
4.3 |
54.7 |
16 400 |
25 550 |
1.31 |
6 |
300 : 1 : 0.1 : 0.3 : 0.1 |
1.8 |
60.5 |
18 130 |
27 050 |
1.43 |
7d |
300 : 1 : 0 : 1.5 : 0.1 |
46.3 |
91.4 |
27 430 |
26 240 |
1.21 |
8e |
300 : 1 : 0.5 : 1.5 : 0 |
2.2 |
91.2 |
27 360 |
33 600 |
1.37 |
To investigate the effect of CuCl on the polymerization of MMA in detail, the kinetics was studied in bulk with a molar ratio of [MMA]0/[EBiB]0/[FeCl3·6H2O]0/[PPh3]0/[CuCl]0 = 300
:
1
:
0.5
:
1.5
:
0.1 in the absence of oxygen at 90 °C. Meanwhile, iron-catalyzed AGET ATRPs using ascorbic acid as a reducing agent with a molar ratio of [MMA]0/[EBiB]0/[FeCl3·6H2O]0/[PPh3]0/[ascorbic acid]0 = 300
:
1
:
0.5
:
1.5
:
0.1 were also carried out to make comparisons. As shown in Fig. 1a, the first-order kinetics was observed under both cases, indicating that the concentration of active species in two cases remained constant during the polymerization process. However, an induction period of about 20 min for the bimetallic catalyst system and about 60 min for iron catalyst system was respectively observed under both polymerization conditions, which indicated that it needed some time to establish a dynamic equilibrium between active and dormant species as the reaction proceeded. Besides, the polymerization rate of the bimetal-catalyzed AGET ATRP was much higher than that of the only iron-catalyzed case. By calculating the apparent rate constant of the polymerization, kpapp (Rp = -d[M]/dt = kp[Pn·][M] = kpapp [M]), as determined from the kinetic slopes, a kpapp of 1.04 × 10−4 s−1 for the iron(III)/ascorbic acid catalyst case and 4.48 × 10−4 s−1 for the bimetallic catalyst case were obtained. The latter was 4.3 times of the former. Fig. 1b shows the evolution of the number-average molecular weight (Mn,GPC) of PMMA and molecular weight distribution (Mw/Mn) on the conversion in both cases. From Fig. 1b, it can be found that Mn,GPC values of the polymers increased linearly with monomer conversion but deviated from the theoretical ones slightly. By comparing between the two catalyst cases, we can see that Mn,GPC values in the case of the bimetallic catalyst system were closer to their corresponding theoretical ones, which indicated that the Cu(I) played a positive role in this catalyst system. In addition, the Mw/Mn values of the polymers reduced to 1.21 gradually with the increase of monomer conversion for the bimetallic catalyst system. These results further indicated that in bimetallic catalyst system the polymerization was well-controlled with a relatively faster polymerization rate and good controllability over molecular weights and molecular weight distributions.
![Conversion and ln([M]0/[M]) as a function of time (a) and average-number molecular weight (Mn,GPC) and molecular weight distribution (Mw/Mn) versus the conversion (b) for the bulk AGET ATRP of MMA in the absence of oxygen using PPh3 as the ligand with bimetallic and iron(iii)/ascorbic acid catalyst system, respectively. Bimetallic catalyst system: [MMA]0/[EBiB]0/[FeCl3·6H2O]0/[PPh3]0/ [CuCl]0 = 300 : 1 : 0.5 : 1.5 : 0.1; Iron(iii)/ascorbic acid catalyst system: [MMA]0/[EBiB]0/ [FeCl3·6H2O]0/[PPh3]0/[ascorbic acid]0 = 300 : 1 : 0.5 : 1.5 : 0.1. MMA = 3 mL, T = 90 °C.](/image/article/2012/RA/c1ra00456e/c1ra00456e-f1.gif) |
| Fig. 1 Conversion and ln([M]0/[M]) as a function of time (a) and average-number molecular weight (Mn,GPC) and molecular weight distribution (Mw/Mn) versus the conversion (b) for the bulk AGET ATRP of MMA in the absence of oxygen using PPh3 as the ligand with bimetallic and iron(III)/ascorbic acid catalyst system, respectively. Bimetallic catalyst system: [MMA]0/[EBiB]0/[FeCl3·6H2O]0/[PPh3]0/ [CuCl]0 = 300 : 1 : 0.5 : 1.5 : 0.1; Iron(III)/ascorbic acid catalyst system: [MMA]0/[EBiB]0/ [FeCl3·6H2O]0/[PPh3]0/[ascorbic acid]0 = 300 : 1 : 0.5 : 1.5 : 0.1. MMA = 3 mL, T = 90 °C. | |
It is well-known that PPh3 is widely used as an efficient ligand for the iron(II)-mediated ATRP.63 Actually, it is quite clearly demonstrated by the results published by Noh and coworkers30,31 and the results listed in entry 1 of Table 1 where good control is obtained with FeCl3/PPh3 in the absence of any other additive. This is contributed to the spontaneous reduction of FeCl3/PPh3, to yield Fe(II) products, as described by Walker and Poli.64 Therefore, to eliminate the interference of redox reaction between metal ion and ligand, another efficient ligand TDA-1 for the iron catalyst was used to replace PPh3 in this work. As shown in Table 2, the polymerization rate decreased with the decreasing of the amount of TDA-1 whether there is CuCl or not and it was found that the polymerizations with CuCl (entries 4–6 in Table 2) had higher polymerization rates than that of iron(III)-catalyzed ATRPs (entries 1–3 in Table 2) in general. For instance, the monomer conversion could be reached up to 73.8% after 16.5 h for the bimetal-catalyzed AGET ATRP (entry 6 in Table 2); while 31.7% of conversion could be obtained after 48 h for the iron(III)-mediated ATRP (entry 3 in Table 2). In the presence of Cu(I)Cl, the polymerizations were well-controlled with narrower Mw/Mn values and the molecular weights were closer to their theoretical ones compared to iron(III)-catalyzed cases. The same trend was also observed in Table 3 (entries 1–4). However, the molecular weights were closer to their theoretical ones and narrow Mw/Mn values were observed when the molar ratio of [Cu(I)]0/[Fe(III)]0 was 1/5 (entry 2 in Table 3) by comparison of other cases. This is why we chosen the molar ratio mentioned above ([Cu(I)]0/[Fe(III)]0 = 1/5) as the optimal conditions to study the kinetics of polymerizations, as shown in Fig. 2.
![Conversion and ln([M]0/[M]) as a function of time (a) and average-number molecular weight (Mn,GPC) and molecular weight distribution (Mw/Mn) versus the conversion (b) for the bulk AGET ATRP of MMA in the absence of oxygen using TDA-1 as the ligand with bimetallic, iron(iii)/ascorbic acid, and iron(iii) catalyst system, respectively. Bimetallic catalyst system: [MMA]0/[EBiB]0/[FeCl3·6H2O]0/[TDA-1]0/[CuCl]0 = 300 : 1 : 0.5 : 1.5 : 0.1; Iron(iii)/ascorbic acid catalyst system: [MMA]0/[EBiB]0/ [FeCl3·6H2O]0/[TDA-1]0/ [ascorbic acid]0 = 300 : 1 : 0.5 : 1.5 : 0.1; Iron(iii) catalyst system : [MMA]0/[EBiB]0/[FeCl3·6H2O]0/[TDA-1]0 = 300 : 1 : 0.5 : 1.5. MMA = 3 mL, T = 90 °C.](/image/article/2012/RA/c1ra00456e/c1ra00456e-f2.gif) |
| Fig. 2 Conversion and ln([M]0/[M]) as a function of time (a) and average-number molecular weight (Mn,GPC) and molecular weight distribution (Mw/Mn) versus the conversion (b) for the bulk AGET ATRP of MMA in the absence of oxygen using TDA-1 as the ligand with bimetallic, iron(III)/ascorbic acid, and iron(III) catalyst system, respectively. Bimetallic catalyst system: [MMA]0/[EBiB]0/[FeCl3·6H2O]0/[TDA-1]0/[CuCl]0 = 300 : 1 : 0.5 : 1.5 : 0.1; Iron(III)/ascorbic acid catalyst system: [MMA]0/[EBiB]0/ [FeCl3·6H2O]0/[TDA-1]0/ [ascorbic acid]0 = 300 : 1 : 0.5 : 1.5 : 0.1; Iron(III) catalyst system : [MMA]0/[EBiB]0/[FeCl3·6H2O]0/[TDA-1]0 = 300 : 1 : 0.5 : 1.5. MMA = 3 mL, T = 90 °C. | |
Table 2 Experimental results of the bimetal-catalyzed AGET ATRP and iron(III)-catalyzed ATRP of MMA in bulk with different amounts of TDA-1 in the absence of oxygen at 90 °C
Entry |
R
|
Time (h) |
Conversion (%) |
M
n,th
c (g mol−1) |
M
n,GPC (g mol−1) |
M
w/Mn |
Iron(III)-catalyzed ATRP: R = [MMA]0/[EBiB]0/[FeCl3·6H2O]0/[TDA-1]0.
Bimetallic catalyst system: R = [MMA]0/[EBiB]0/[FeCl3·6H2O]0/[TDA-1]0/ [CuCl]0.
M
n,th
= ([M]0/[EBiB]0) × Mw,MMA × conversion%.
|
1a |
300 : 1 : 0.5 : 0.75 |
162 |
45.6 |
13 680 |
24 000 |
1.35 |
2a |
300 : 1 : 0.5 : 1 |
143 |
58.2 |
17 460 |
23 800 |
1.37 |
3a |
300 : 1 : 0.5 : 1.5 |
48 |
31.7 |
9520 |
13 480 |
1.34 |
4b |
300 : 1 : 0.5 : 0.75 : 0.1 |
75 |
43.6 |
13 080 |
18 400 |
1.28 |
5b |
300 : 1 : 0.5 : 1 : 0.1 |
75 |
50.1 |
15 030 |
16 700 |
1.33 |
6b |
300 : 1 : 0.5 : 1.5 : 0.1 |
16.5 |
73.8 |
22 160 |
25 430 |
1.21 |
Table 3 Experimental results of the bimetal-catalyzed AGET ATRP of MMA in bulk with different amounts of CuCl in the absence of oxygen at 90 °C
Entry |
Ra |
Time (h) |
Conversion (%) |
M
n,th
b (g mol−1) |
M
n,GPC (g mol−1) |
M
w/Mn |
R = [MMA]0/[EBiB]0/[FeCl3·6H2O]0/[TDA-1]0/[CuCl]0.
M
n,th
= ([M]0/[EBiB]0) × Mw,MMA × conversion%.
Normal ATRP catalyzed by CuCl/TDA-1 complexes.
Using FeCl2·4H2O instead of FeCl3·6H2O, namely normal ATRP catalyzed by FeCl2/TDA-1 complexes.
|
1 |
300 : 1 : 0.5 : 1.5 : 0 |
48 |
31.7 |
9520 |
13 480 |
1.34 |
2 |
300 : 1 : 0.5 : 1.5 : 0.1 |
16.5 |
73.8 |
22 160 |
25 430 |
1.21 |
3 |
300 : 1 : 0.5 : 1.5 : 0.3 |
24 |
42.8 |
12 840 |
21 150 |
1.25 |
4 |
300 : 1 : 0.5 : 1.5 : 0.5 |
17 |
45.8 |
13 740 |
23 180 |
1.19 |
5c |
300 : 1 : 0 : 1.5 : 0.1 |
3 |
17.8 |
5340 |
33 900 |
1.38 |
6d |
300 : 1 : 0.5 : 1.5 : 0 |
0.5 |
42.8 |
12 840 |
32 700 |
1.45 |
Besides, we investigated the polymerization without FeCl3·6H2O, namely a normal copper-mediated ATRP of MMA just using CuCl/TDA-1 as the catalyst (entry 5 in Table 3). And the reference experiment was also carried out in the presence of FeCl2·4H2O/TDA-1 solely (entry 6 in Table 3). The molecular weights of the obtained polymers with broader Mw/Mn values (1.38 and 1.45, respectively) were much higher than their corresponding theoretical values under both cases, which indicated that the Cu(I)Cl/TDA-1 or Fe(II)Cl2/TDA-1 was not a good catalyst system solely as compared with the bimetallic system.
The kinetics of bulk AGET ATRPs of MMA using TDA-1 as the ligand with a molar ratio of [MMA]0/[EBiB]0/[FeCl3·6H2O]0/[TDA-1]0/[CuCl]0 = 300
:
1
:
0.5
:
1.5
:
0.1 are shown in Fig. 2a. Iron(III)-catalyzed ATRPs of MMA with a molar ratio of [MMA]0/[EBiB]0/[FeCl3·6H2O]0/[TDA-1]0 = 300
:
1
:
0.5
:
1.5 and AGET ATRPs of MMA using ascorbic acid as a reducing agent with a molar ratio of [MMA]0/[EBiB]0/[FeCl3·6H2O]0/[TDA-1]0/[ascorbic acid]0 = 300
:
1
:
0.5
:
1.5
:
0.1 were also carried out for comparison. It can be seen that the polymerization rate of the bimetal-catalyzed AGET ATRP was much higher than that of the iron(III)-catalyzed case. And a longer induction period (∼37 h) was observed for the latter. For the bimetallic ATRP, the monomer conversion can reach up to 47% after 7.5 h, while 45% of conversion was obtained after 70 h for the iron(III)-catalyzed ATRP, which indicate that the addition of CuCl played a positive role in increasing the polymerization rate. Meanwhile, it was worth noting that the opposite trend appeared when ascorbic acid was employed instead of CuCl compared with the cases using PPh3 as the ligand, the polymerization rate of AGET ATRP using ascorbic acid as a reducing agent was slight higher than that of the bimetallic catalyst system while induction periods of about 2 h for the AGET ATRP and no induction time for bimetallic catalyst system at all were observed. These results may be due to that the reducing agent ascorbic acid has better solubility than that of CuCl for TDA-1 ligand system. In addition, the kpapp value of 2.20 × 10−5 s−1 for the bimetallic catalyst case, 4.41 × 10−5 s−1 for the ascorbic acid case, and 5.30 × 10−6 s−1 for the iron(III)-mediated case, were obtained, respectively. It was 4.1 and 8.3 times of the last one for the bimetallic catalyst case and the ascorbic acid case, respectively. From Fig. 2b, we can see that Mn,GPC values of the polymers increased linearly with monomer conversion but deviated from the theoretical ones slightly. It was found that Mw/Mn value of the polymers in the case of bimetallic catalyst system were the narrowest one via comparison of the three cases which proved that the bimetallic catalyst system containing iron(III) and Cu(I) was effective and relatively advanced.
Chain extension and analysis of chain end
A chain-extension experiment was used for verifying the obtained “living” polymer chains. The obtained PMMA (Mn,GPC = 22
950 g mol−1, Mw/Mn = 1.27 and Mn,GPC = 22
000 g mol−1, Mw/Mn = 1.27) was employed as macroinitiators in the bimetal-catalyzed AGET ATRP of a fresh feed of MMA. As shown in Fig. 3a, there was a peak shift from the macroinitiator (Mn,GPC = 22
950 g mol−1, Mw/Mn = 1.27) to the chain-extended PMMA with Mn,GPC = 39
880 g mol−1 and Mw/Mn = 1.33. From Fig. 3b, we can see a peak shift from the macroinitiator (Mn,GPC = 22
000 g mol−1, Mw/Mn = 1.27) obtained by using TDA-1 as a ligand to the chain-extended PMMA with Mn,GPC = 35
600 g mol−1 and Mw/Mn = 1.24. Fig. 4 shows the 1H NMR spectrum of the obtained PMMA (Mn,GPC = 18
500 g mol−1, Mw/Mn = 1.30) via bimetal-catalyzed AGET ATRP in the absence of oxygen at 90 °C. The chemical shift at 4.05 ppm could be assigned to the protons of the methylene (CH3–CH2–O, a in Fig. 4) from the initiator moieties of EBiB.17,20 These results showed that the EBiB moieties were successfully attached onto the chain end of the obtained PMMA and that the bimetal-catalyzed AGET ATRP of MMA could be carried out successfully with the feature of controlled/“living” radical polymerization of ATRP process. These results further demonstrated the feature of the “living”/controlled polymerization of the bimetal-catalyzed AGET ATRP based on FeCl3·6H2O/PPh3/CuCl catalytic system.
![GPC traces of before and after chain-extension using PMMA as macroinitiator prepared by the bimetallic catalyst system. Polymerization conditions: (a) [MMA]0/[PMMA]0/[FeCl3·6H2O]0/[PPh3]0/[CuCl]0 = 300 : 1 : 0.5 : 1.5 : 0.1; in bulk; MMA = 1.5 mL; time = 4 h; conversion = 49%; T = 90 °C; (b) [MMA]0/[PMMA]0/[FeCl3·6H2O]0/[TDA-1]0/[CuCl]0 = 300 : 1 : 0.5 : 1.5 : 0.1; in bulk; MMA = 1.5 mL; time = 28 h ; conversion = 43%; T = 90 °C.](/image/article/2012/RA/c1ra00456e/c1ra00456e-f3.gif) |
| Fig. 3
GPC traces of before and after chain-extension using PMMA as macroinitiator prepared by the bimetallic catalyst system. Polymerization conditions: (a) [MMA]0/[PMMA]0/[FeCl3·6H2O]0/[PPh3]0/[CuCl]0 = 300 : 1 : 0.5 : 1.5 : 0.1; in bulk; MMA = 1.5 mL; time = 4 h; conversion = 49%; T = 90 °C; (b) [MMA]0/[PMMA]0/[FeCl3·6H2O]0/[TDA-1]0/[CuCl]0 = 300 : 1 : 0.5 : 1.5 : 0.1; in bulk; MMA = 1.5 mL; time = 28 h ; conversion = 43%; T = 90 °C. | |
![1H NMR spectrum of PMMA (Mn,GPC = 18 500 g mol−1, Mw/Mn = 1.30) obtained in the presence of air with CDCl3 as solvent and tetramethylsilane (TMS) as internal standard. Polymerization conditions: [MMA]0/[EBiB]0/[FeCl3·6H2O]0/[PPh3]0/[CuCl]0 = 300 : 1 : 0.5 : 1.5 : 0.1; in bulk; MMA = 3 mL; time = 50 min; conversion = 49.6%; T = 90 °C.](/image/article/2012/RA/c1ra00456e/c1ra00456e-f4.gif) |
| Fig. 4
1H NMR spectrum of PMMA (Mn,GPC = 18 500 g mol−1, Mw/Mn = 1.30) obtained in the presence of air with CDCl3 as solvent and tetramethylsilane (TMS) as internal standard. Polymerization conditions: [MMA]0/[EBiB]0/[FeCl3·6H2O]0/[PPh3]0/[CuCl]0 = 300 : 1 : 0.5 : 1.5 : 0.1; in bulk; MMA = 3 mL; time = 50 min; conversion = 49.6%; T = 90 °C. | |
Bimetal-catalyzed AGET ATRP of MMA in the presence of a limited amount of air
In our previous works, polymers with narrow polydispersity and good agreement between theoretical and experimental Mn values could be successfully prepared by AGET ATRP in the presence of a limited amount of air.17 Inspired by those results, the bimetal-catalyzed AGET ATRP of MMA was also carried out in the presence of a limited amount of air in this work. As shown in Table 4, the molecular weights of the polymers with narrow Mw/Mn values were close to their corresponding theoretical ones, which indicated that the limited amount of oxygen in the bimetallic catalyst system did not sacrifice the controllability of the polymerization system.
Table 4 Experimental results of the bimetal-catalyzed AGET ATRP of MMA in bulk in the presence of a limited amount of air at 90 °C
Entry |
Time (h) |
Conversion (%) |
M
n,th
c (g mol−1) |
M
n,GPC (g mol−1) |
M
w/Mn |
Polymerization conditions: [MMA]0/[EBiB]0/[FeCl3·6H2O]0/[PPh3]0/[CuCl]0 = 300 : 1 : 0.1 : 1.5 : 0.1. [MMA]0/[EBiB]0/[FeCl3·6H2O]0/[TDA-1]0/[CuCl]0 = 300 : 1 : 0.1: 1.5 : 0.1; MMA = 3.0 mL. Mn,th = ([M]0/[EBiB]0) × Mw,MMA × conversion%; [O2]0 = 1.7 × 10−2 mol L−1. |
1a |
1.5 |
56.6 |
16 900 |
18 840 |
1.20 |
2b |
65 |
37.4 |
11 200 |
15 400 |
1.30 |
Plausible mechanism for the bimetal-catalyzed AGET ATRP
In AGET ATRP, electron transfer rather than organic radicals used to reduce the higher oxidation state transition metal complexes.65 Firstly, Cu(I)Cl acted as a reducing agent which reduced Fe(III) to Fe(II) salts. Upon generation of the activating transition metal complex, Fe(II)/ligand, the alkyl halide (R-X) could initiate the polymerization concurrently via a normal ATRP process. Since FeCl3 is reduced by CuCl to FeCl2 in this case, normal ATRP of MMA using FeCl2·4H2O as the catalyst was carried out for comparison. From entry 5 in Table 3 using TDA-1 as the ligand and entry 8 in Table 1 using PPh3 as the ligand, it can be seen that both the molecular weight distribution values (Mw/Mn = 1.45, 1.37, respectively) of the obtained PMMAs were relatively broader and the experimental Mn values were larger than their theoretical ones, which indicated that no participation of reducing agent Cu(I)Cl will bring down the controllability of polymerization. Besides, the polymerization solely using Cu(I)Cl as the catalyst was also well-controlled (entry 7 in Table 1), which indicated that Cu(I)Cl play another role as a co-catalyst during the polymerization. However, by comparison of the polymerization rate catalyzed by Cu(I)Cl/PPh3 (91.4% of monomer conversion after 46.3 h, entry 7 in Table 1) and FeCl2/PPh3 (91.2% of monomer conversion after 2.2 h, entry 8 in Table 1) complexes under similar conditions, it can be seen that the polymerization resulted from Cu(I)Cl/PPh3 complex can be ignored in this bimetallic system.
When TDA-1 was used as the ligand, from entry 2 in Table 3, the polymerization rate (73.8% of monomer conversion after 16.5 h) was much higher than that (31.7% of monomer conversion after 48 h) in the case of iron(III)-mediated ATRP process (entry 1 in Table 3) when Cu(I)Cl was used as the cocatalyst due to the reduction function of Cu(I)Cl. And much better controllability for the polymerization was obtained by the bimetallic catalyst system due to co-catalytic function. This is because the Fe(II)Cl2/TDA-1 catalyst system (entry 6 in Table 3) can result in a relatively quick polymerization process but the controllability was relatively poor (broader Mw/Mn values and higher Mn,GPC than theoretical one). However, when continued to increase the amount of CuCl (entries 3–4 in Table 3), the polymerization rate decreased significantly. This is contributed to the fact that Cu(I)Cl/TDA-1 (entry 5 in Table 3) catalyst system resulted in a relatively slower polymerization process as compared with Fe(II)Cl2/TDA-1 catalyst system (entry 6 in Table 3). So when the amount of CuCl continued to increase, the contribution catalyzed by Cu(I)Cl/TDA-1 enhanced and therefore resulted in the decreasing of the total rate of polymerization of MMA. At the same time, the controllability also decreased correspondingly. Therefore, a suitable amount of CuCl (i.e., [Cu(I)]0/[Fe(III)]0 = 1/5) should be used in this case in order to obtain a well-controlled polymerization process. Anyway, these results further confirmed that Cu(I)Cl acted not only as a reducing agent but also as cocatalyst in the polymerization process.
On the other hand, considering the fact that CuCl2 is an excellent deactivator of a polymer end radical and FeCl2 is a good activator of the dormant species, the most probable mechanism for the activation is governed by FeCl2 complex; and deactivation of a polymer end radical is governed by both CuCl2 and FeCl3 complexes. The oxidized FeCl3 and reduced CuCl react each other to regenerate FeCl2 and CuCl2 and the plausible mechanism for the bimetallic catalyst system is shown in Scheme 1.
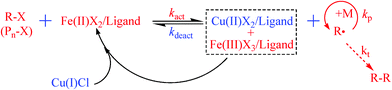 |
| Scheme 1 Plausible mechanism of the bimetal-catalyzed AGET ATRP. | |
Conclusions
A novel bimetallic catalyst system based on FeCl3·6H2O/TDA-1(or PPh3)/CuCl for AGET ATRP was developed by using MMA as the monomer in the absence/presence of a limited amount of air. The polymerization could be successfully carried out with a wide range of molar ratios of FeCl3·6H2O to TDA-1 and FeCl3·6H2O to CuCl. The current bimetallic catalyst system showed higher catalytic activity than any mono-metallic catalyst system, which provides a new strategy for the development of highly active ATRP catalyst system.
Acknowledgements
The financial support from the National Natural Science Foundation of China (Nos. 20974071 and 21174096), the Specialized Research Fund for the Doctoral Program of Higher Education (No. 20103201110005), the Project of Science and Technology Development Planning of Suzhou (No. SYG201026), the Project of International Cooperation of the Ministry of Science and Technology of China (No. 2011DFA50530), the Qing Lan Project, the Program of Innovative Research Team of Soochow University, and the Project Funded by the Priority Academic Program Development of Jiangsu Higher Education Institutions (PAPD) is gratefully acknowledged.
References
- J. S. Wang and K. Matyjaszewski, J. Am. Chem. Soc., 1995, 117, 5614–5615 CrossRef CAS.
- M. Kato, M. Kamigaito, M. Sawamoto and T. Higashimura, Macromolecules, 1995, 28, 1721–1723 CrossRef CAS.
- K. Matyjaszewski and J. H. Xia, Chem. Rev., 2001, 101, 2921–2990 CrossRef CAS.
- N. V. Tsarevsky and K. Matyjaszewski, Chem. Rev., 2007, 107, 2270–2299 CrossRef CAS.
- M. Ouchi, T. Terashima and M. Sawamoto, Chem. Rev., 2009, 109, 4963–5050 CrossRef CAS.
- F. J. Xu, K. G. Neoh and E. T. Kang, Prog. Polym. Sci., 2009, 34, 719–761 CrossRef CAS.
- S. Sasaki, T. Ooya and T. Takeuchi, Polym. Chem., 2010, 1, 1684–1688 RSC.
- H. Kakwere and S. Perrier, Polym. Chem., 2011, 2, 270–288 RSC.
- W. J. Wang, P. W. Liu, B. G. Li and S. P. Zhu, J. Polym. Sci., Part A: Polym. Chem., 2010, 48, 3024–3032 CrossRef CAS.
- R. Fu and G. -D. Fu, Polym. Chem., 2011, 2, 465–475 RSC.
- M. Machado, S. Faucher and S. P. Zhu, J. Polym. Sci., Part A: Polym. Chem., 2010, 48, 2249–2301 CrossRef.
- J. Gromada and K. Matyjaszewski, Macromolecules, 2001, 34, 7664–7671 CrossRef CAS.
- M. Li, K. Min and K. Matyjaszewski, Macromolecules, 2004, 37, 2106–2112 CrossRef CAS.
- M. Li, N. M. Jahed, K. Min and K. Matyjaszewski, Macromolecules, 2004, 37, 2434–2441 CrossRef CAS.
- L. Mueller, W. Jakubowski, W. Tang and K. Matyjaszewski, Macromolecules, 2007, 40, 6464–6472 CrossRef CAS.
- G. H. Zhu, L. F. Zhang, Z. B. Zhang, J. Zhu, Y. F. Tu, Z. P. Cheng and X. L. Zhu, Macromolecules, 2011, 44, 3233–3239 CrossRef CAS.
- L. F. Zhang, J. Miao, Z. P. Cheng and X. L. Zhu, Macromol. Rapid Commun., 2010, 31, 275–280 CrossRef CAS.
- P. Kwiatkowski, J. Jurczak, J. Pietrasik, W. Jakubowski, L. Mueller and K. Matyjaszewski, Macromolecules, 2008, 41, 1067–1069 CrossRef CAS.
- W. Li, K. Min, K. Matyjaszewski, F. Stoffelbach and B. Charleux, Macromolecules, 2008, 41, 6387–6392 CrossRef CAS.
- L. F. Zhang, Z. P. Cheng, S. P. Shi, Q. H. Li and X. L. Zhu, Polymer, 2008, 49, 3054–3059 CrossRef CAS.
- L. F. Zhang, Z. P. Cheng, F. Tang, Q. Li and X. L. Zhu, Macromol. Chem. Phys., 2008, 209, 1705–1713 CrossRef CAS.
- L. J. Bai, L. F. Zhang, J. Zhu, Z. P. Cheng and X. L. Zhu, J. Polym. Sci., Part A: Polym. Chem., 2009, 47, 2002–2008 CrossRef CAS.
- H. C. Dong and K. Matyjaszewski, Macromolecules, 2010, 43, 4623–4628 CrossRef CAS.
- W. Jakubowski and K. Matyjaszewski, Angew. Chem., 2006, 118, 4594–4598 CrossRef.
- H. C. Dong and K. Matyjaszewski, Macromolecules, 2008, 41, 6868–6870 CrossRef CAS.
- R. Nicolay, Y. Kwak and K. Matyjaszewski, Angew. Chem., 2010, 122, 551–554 CrossRef.
- O. Altintas, U. Tunca and C. Barner-Kowollik, Polym. Chem., 2011, 2, 1146–1155 RSC.
- J. Tom, B. Hornby, A. West, S. Harrisson and S. Perrier, Polym. Chem., 2010, 1, 420–422 RSC.
- J. -T. Sun, C. -Y. Hong and C. -Y. Pan, Polym. Chem., 2011, 2, 998–1007 RSC.
- L. J. Bai, L. F. Zhang, Z. B. Zhang, J. Zhu, N. C. Zhou, Z. P. Cheng and X. L. Zhu, J. Polym. Sci., Part A: Polym. Chem., 2011, 49, 3980–3987 CrossRef CAS.
- L. J. Bai, L. F. Zhang, Z. B. Zhang, J. Zhu, N. C. Zhou, Z. P. Cheng and X. L. Zhu, J. Polym. Sci., Part A: Polym. Chem., 2011, 49, 3970–3979 CrossRef CAS.
- L. F. Zhang, Z. P. Cheng, Y. T. Lu and X. L. Zhu, Macromol. Rapid Commun., 2009, 30, 543–547 CrossRef CAS.
- W. J. He, L. F. Zhang, L. J. Bai, Z. B. Zhang, J. Zhu, Z. P. Cheng and X. L. Zhu, Macromol. Chem. Phys., 2011, 212, 1474–1478 CrossRef CAS.
- L. J. Bai, L. F. Zhang, Z. B. Zhang, Y. F. Tu, N. C. Zhou, Z. P. Cheng and X. L. Zhu, Macromolecules, 2010, 42, 9283–9290 CrossRef.
- T. Guo, L. F. Zhang, H. J. Jiang, Z. B. Zhang, J. Zhu, Z. P. Cheng and X. L. Zhu, Polym. Chem., 2011, 2, 2385–2390 RSC.
- T. Shibata, K. Satoh, M. Kamigaito and Y. Okamoto, J. Polym. Sci., Part A: Polym. Chem., 2006, 44, 3609–3615 CrossRef CAS.
- M. Ouchi, T. Terashima and M. Sawamoto, Acc. Chem. Res., 2008, 41, 1120–1132 CrossRef CAS.
- K. Nakatani, T. Terashima and M. Sawamoto, J. Am. Chem. Soc., 2009, 131, 13600–13601 CrossRef CAS.
- E. Duquesne, J. Habimana, P. Degee and P. Dubois, Macromolecules, 2005, 38, 9999–10006 CrossRef CAS.
- R. K. O'Reilly, M. P. Shaver and V. C. Gibson, Inorg. Chim. Acta, 2006, 359, 4417–4420 CrossRef CAS.
- R. Gong, S. Maclaughlin and S. P. Zhu, Appl. Surf. Sci., 2008, 254, 6802–6809 CrossRef CAS.
- K. Matsubara and M. Matsumoto, J. Polym. Sci., Part A: Polym. Chem., 2006, 44, 4222–4228 CrossRef CAS.
- Z. X. Huang, Y. M. Zhang, H. Li and Y. G. Liu, Macromol. Chem. Phys., 2008, 209, 825–831 CrossRef CAS.
- J. A. M. Brandts, P. van de Geijn, E. E. van Faassen, J. Boersma and G. Van Koten, J. Organomet. Chem., 1999, 584, 246–253 CrossRef CAS.
- E. Le Grognec, J. Claverie and R. Poli, J. Am. Chem. Soc., 2001, 123, 9513–9524 CrossRef CAS.
- F. Stoffelbach, D. M. Haddleton and R. Poli, Eur. Polym. J., 2003, 39, 2099–2105 CrossRef CAS.
- S. Maria, F. Stoffelbach, J. Mata, J.-C. Daran, P. Richard and R. Poli, J. Am. Chem. Soc., 2005, 127, 5946–5956 CrossRef CAS.
- F. Stoffelbach, R. Poli, S. Maria and P. Richard, J. Organomet. Chem., 2007, 692, 3133–3143 CrossRef CAS.
- W. A. Braunecker, Y. Itami and K. Matyjaszewski, Macromolecules, 2005, 38, 9402–9404 CrossRef CAS.
- W. A. Braunecker, W. C. Brown, B. C. Morelli, W. Tang, R. Poli and K. Matyjaszewski, Macromolecules, 2007, 40, 8576–8585 CrossRef CAS.
- J. Chen, J. Chu and K. D. Zhang, Polymer, 2004, 45, 151–155 CrossRef CAS.
- J. Cao, J. Chen and K. D. Zhang, J. Polym. Sci., Part A: Polym. Chem., 2005, 43, 2625–2631 CrossRef.
- Z. X. Huang, Y. M. Zhang, H. Li and Y. G. Liu, Appl. Catal., A, 2007, 332, 192–199 CrossRef CAS.
- Y. Z. Zhang, Y. Wang and K. Matyjaszewski, Macromolecules, 2011, 44, 683–685 CrossRef CAS.
- A. D. Asaandei and V. Percec, J. Polym. Sci., Part A: Polym. Chem., 2001, 39, 3392–3418 CrossRef.
- Z. G. Xue, D. He, S. K. Noh and W. S. Lyoo, Macromolecules, 2009, 42, 2949–2957 CrossRef CAS.
- Z. B. Zhang, W. X. Wang, Z. P. Cheng, J. Zhu, N. C. Zhou, Y. G. Yang, Y. F. Tu and X. L. Zhu, Macromolecules, 2010, 43, 7979–7984 CrossRef CAS.
- V. Percec, T. Guliashvili, J. S. Ladislaw, A. Wistrand, A. Stjerndahl, M. J. Sienkowska, M. J. Monteiro and S. Sahoo, J. Am. Chem. Soc., 2006, 128, 14156–14165 CrossRef CAS.
- N. H. Nguyen, B. M. Rosen, G. Lligadas and V. Percec, Macromolecules, 2009, 42, 2379–2386 CrossRef CAS.
- M. E. Levere, I. Willoughby, S. O'Donohue, A. Cuendias, A. J. Grice, C. Fidge, C. R. Becer and D. M. Haddleton, Polym. Chem., 2010, 1, 1086–1094 RSC.
- N. Chan, M. F. Cunningham and R. A. Hutchinson, Macromol. Rapid Commun., 2011, 32, 604–609 CrossRef CAS.
- Q. F. Chen, Z. B. Zhang, N. C. Zhou, Z. P. Cheng, Y. F. Tu and X. L. Zhu, J. Polym. Sci., Part A: Polym. Chem., 2011, 49, 1183–1189 CrossRef CAS.
- T. Ando, M. Kamigaito and M. Sawamoto, Macromolecules, 1997, 30, 4507–4510 CrossRef CAS.
- J. D. Walker and R. Poli, Inorg. Chem., 1989, 28, 1793–1801 CrossRef CAS.
- W. Jakubowski and K. Matyjaszewski, Macromolecules, 2005, 38, 4139–4146 CrossRef CAS.
|
This journal is © The Royal Society of Chemistry 2012 |
Click here to see how this site uses Cookies. View our privacy policy here.