DOI:
10.1039/C1GC15619E
(Paper)
Green Chem., 2012,
14, 98-110
Catalytic fast pyrolysis of wood and alcohol mixtures in a fluidized bed reactor
Received
27th May 2011
, Accepted 19th August 2011
First published on 18th October 2011
Abstract
Catalytic fast pyrolysis (CFP) of pine wood, alcohols (methanol, 1-propanol, 1-butanol and 2-butanol) and their mixtures with ZSM-5 catalyst were conducted in a bubbling fluidized bed reactor. The effects of temperature and weight hourly space velocity (WHSV) on the product carbon yields and selectivities of CFP of pure pine wood and methanol were investigated. A maximum carbon yield of petrochemicals (aromatics + C2–C4olefins + C5 compounds) from pine wood of 23.7% was obtained at a temperature of 600 °C and WHSV of 0.35 h−1. A maximum petrochemical yield from methanol of 80.7% was obtained at a temperature of 400 °C and WHSV of 0.35 h−1. Thus, the optimal conditions for conversion of pine wood and methanol are different. The CFP of pine wood and methanol mixtures was conducted at 450 °C and 500 °C. The hydrogen to carbon effective (H/Ceff) ratio of the feed was adjusted by changing the relative amount of methanol and wood. The petrochemical yield was a function of the H/Ceff ratio and more petrochemicals are produced from biomass when methanol is added to the CFP process. Co-feeding of 12C pine wood and 13C methanol was carried out at 450 °C. The isotopic study showed that all the hydrocarbon products contained mixtures of 12C and 13C, indicating that the carbon is mixed within the zeolite. However, the distribution of carbon was skewed depending on the product. The toluene, xylene, propylene and butenes contained more 13C. The naphthalene and ethylene contain more 12C. Wood was also co-processed with 1-propanol, 1-butanol, and 2-butanol, which showed a similar effect as methanol with an increasing petrochemical yield with an increasing H/Ceff ratio of the feed. This paper demonstrates that CFP can selectively produce a mixture of compounds where the overall yield is a function of the H/Ceff ratio of the feed.
1. Introduction
Environmental issues caused by using fossil fuels, the growing energy demand and the depletion of petroleum resources have stimulated the development of new sources for the production of renewable liquid fuels.1,2 Due to its low cost and abundant availability, lignocellulosic biomass has been studied world wide to produce liquid fuels and chemicals.3–59 There are several routes for converting solid biomass or its derivatives to liquid fuels and chemicals, such as aqueous-phase reformation,18–24pyrolysis followed by vapors upgrading,25–29gasification followed by Fischer–Tropsch synthesis to produce liquid alkanes,30–32 hydrodeoxygenation of pyrolysis oil,33–35 and the conversion of pyrolysis oil or its derivatives to aromatic hydrocarbons over zeolite catalysts.36–46 All of these routes involve multiple steps and thus greatly increase the cost of biomass processing. Catalytic fast pyrolysis (CFP) is a new promising technology to directly convert solid biomass into hydrocarbon products that fit directly into the current infrastructure.47–55 CFP is a single step process that uses inexpensive zeolite catalysts. Furthermore, the reactor is operated at atmospheric pressure and does not require the use of hydrogen. One of the critical factors that will influence the future prospects of biofuels is product flexibility.56 CFP of biomass can produce five of the six primary petrochemicals, including benzene, toluene, xylene, ethylene and propylene.48 One of the critical challenges with CFP is to increase the yield of usable petrochemicals.
A parameter called the hydrogen to carbon effective (H/Ceff) ratio (also called the effective hydrogen index) can be used to compare the relative amount of hydrogen present in different feeds.57 The H/Ceff ratio is defined in eqn (1), where H, C and O are the mol of hydrogen, carbon and oxygen, respectively.
| 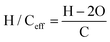 | (1) |
Chen et al.57 showed that feedstocks with an H/Ceff ratio less than 1 are difficult to upgrade to premium products over a ZSM-5 catalyst due to rapid deactivation of the catalyst. The H/Ceff ratio of petroleum-derived feeds ranges from 1 (for benzene) to slightly over 2 (for liquid alkanes), whereas that of biomass is only from 0 to 0.3. Thus, biomass is a hydrogen-deficient molecule. We have recently shown that the yield of usable petrochemical products from zeolite conversion of different biomass-derived feedstocks is a function of the H/Ceff ratio of the feedstock.58,59 This suggests that the petrochemical yield from CFP of biomass could be increased by co-feeding in an additional feedstock that has a high H/Ceff ratio. Methanol has an H/Ceff ratio of 2 and has been shown to give high yields of hydrocarbon products when processed over a zeolite catalyst.60–62 Therefore, methanol could potentially be co-fed with biomass to increase the overall H/Ceff ratio of the feed. Methanol is a liquid at room temperature and easier to transport than hydrogen, which is a gas at room temperature.
The reaction pathways for co-catalytic fast pyrolysis (co-CFP) of cellulose (a biomass model compound) and methanol are shown in Fig. 1. The CFP of cellulose involves both homogeneous and heterogeneous reactions. The first step is the homogeneous thermal decomposition of cellulose to a liquid intermediate that is then converted into anhydrosugars.63–65 The anhydrosugars are relatively thermally stable and do not form large amounts of coke in the gas phase.66 However, the anhydrosugars can undergo dehydration and re-arrangement reactions to form intermediate oxygenates, such as furans and smaller aldehydes. These reactions can happen in either the gas phase or in the presence of a catalyst.67 In the second step, these intermediate oxygenates then diffuse into the zeolite catalyst pores and form monocyclic aromatics, C2–C4olefins and C5 compounds through a series of dehydration, decarbonylation, decarboxylation and oligomerization reactions. The aromatic formation rate is relatively slow compared to the pyrolysis reactions.67 The major competing reaction with the formation of aromatics is the formation of coke from the polymerization of the furans and oxygenated pyrolysis vapors. The aromatic formation reaction proceeds through a common intermediate or “hydrocarbon pool” within the zeolite framework.68–75 Co-feeding methanol with biomass may alter the “hydrocarbon pool” and increase the rate of aromatic production.
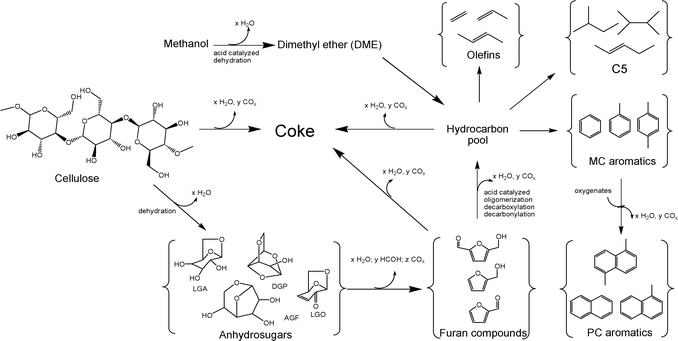 |
| Fig. 1 Overall reaction chemistry for the co-catalytic fast pyrolysis of cellulose and methanol. Adapted from Carlson et al.48 | |
We know of three papers in the literature that have previously reported on co-feeding of biomass or its derivatives with methanol over HZSM-5 catalysts.40,76,77 These studies all reported increased aromatic and olefin yields when methanol is co-fed with the biomass or its derivatives. Gayubo et al.40,76 conducted co-feeding of bio-oil and methanol in a fluidized bed and conical spouted bed reactor with HZSM-5 and Ni/HZSM-5 catalysts. They reported that co-feeding of methanol with the pyrolysis oil increased the C2–C4olefin yield and decreased the CO, CO2, and coke yields. Evans and Milne77 co-fed methanol with wood in a quartz microreactor with HZSM-5 catalyst. They showed that more aromatic products were formed with the co-feeding process.
The objective of this work is to study the CFP of pine wood and methanol mixtures in a fluidized bed reactor to see if the overall petrochemical yield can be improved by the addition of alcohol feeds. The effect of temperature and weight hourly space velocity (WHSV) on the product carbon yields and selectivities of CFP of pine wood and methanol are studied to determine a suitable operation condition for co-CFP of these feed mixtures. We compare the economic potential of CFP of pine wood and methanol mixtures to assess the potential benefits of co-feeding. Isotopically labelled 13C methanol was processed with pine wood to identify how methanol and wood are incorporated into the final products. We also study the co-CFP of pine wood with other alcohols, such as 1-propanol, 1-butanol and 2-butanol to determine if these feeds can be used to enhance the petrochemical yield. This paper thus provides critical insights as to how the yield of petrochemicals can be increased by co-feeding of pine wood with feeds that have a high H/Ceff ratio like alcohols.
2. Experimental section
2.1 Materials
2.1.1 Feeds.
12C methanol, 1-propanol, 1-butanol and 2-butanol were purchased from Sigma-Aldrich and used as feedstocks without any pretreatment. 13C methanol (Product ID: CLM-359-5) with 99 atom% 13C was bought from Cambridge Isotope Laboratories, Inc. The wood used in this study is eastern pine wood sawdust sourced from a local sawmill. Prior to the experiments, the wood was ground with a high-speed rotary cutting mill and then sieved to yield a particle size of 18–120 mesh (120–880 micron). The elemental composition of the wood is 46.2 wt% carbon, 6.0 wt% hydrogen and 47.3 wt% oxygen (by difference). The proximate analysis result is 4.0 wt% moisture, 74.2 wt% volatile, 21.3 wt% fixed carbon and 0.5 wt% ash. On the dry basis the approximate molecular formula of the wood is therefore C3.8H5.8O2.7.
2.1.2
Catalyst
.
The catalyst used in this work is a commercial spray dried 40% ZSM-5 catalyst (Intercat. Inc.). The particle size of the catalyst is from 150 to 230 mesh (62–106 micron). For a typical run, 30 g catalyst is loaded in the reactor. Prior to reactions, the catalyst was calcined in the fluidized bed reactor for 5 h at 600 °C in 800 mL min−1 flowing air.
2.2 Experimental setup
CFP and co-CFP of pine wood and alcohols were conducted in a fluidized bed reactor system, as shown in Fig. 2, which can be found elsewhere.48 The fluidized bed reactor is a 2 inch ID 316 stainless steel tube with a freeboard height of 10 inch. The catalyst bed is supported by a distributor plate made from stacked 316 stainless steel mesh (300 mesh). The pine wood is fed into the side of the reactor (1 inch above the distributor plate) by a stainless steel auger from a sealed feed hopper. The hopper is swept with helium at a rate of 200 mL min−1 to maintain an inert environment in the feeding unit. Methanol is fed into the fluidizing gas stream at the inlet of the plenum by a syringe pump. The methanol vaporizes in the gas stream and enters the reactor through the distributor plate as vapours. Ultra high purity helium (99.99%) was used as the fluidizing gas. The gas flow rate was set as 1200 mL min−1 and controlled by a mass flow controller. Both the reactor and the inlet gas stream are heated to reaction temperature before reaction. A cyclone is located at the exit of the reactor to remove and collect entrained solid particles. Following the cyclone, the vapours flow into a condenser train. The first three condensers are operated at 0 °C in an ice bath and the following four condensers are operated at −55 °C in a dry ice/acetone bath. The non-condensable vapours exiting the condenser train are collected by a gas sampling bag and analyzed by GC/FID and GC/TCD. A carrier gas flow rate of 1400 mL min−1 was used for all experiments, as measured by a bubble flow meter. We used GC/FID to analyze the amount of gas products produced. Ethanol was added to the condensers to help condense the condensable products. All liquid products were soluble in the ethanol. These liquid products were then analyzed by GC-FID. For the isotopically labelled feed run, the gas samples and liquids were further analyzed by GC/MS. For a typical run, pine wood is fed to the reactor for 30 min. At the end of the run, the reactor is purged with 1200 mL min−1 for another 30 min to strip any remaining product from the catalyst. After reaction, the catalyst is regenerated at 600 °C in 800 mL min−1 flowing air. The effluent gas during regeneration mainly contains CO2, CO and H2O, which was passed in series through a copper catalyst, a dryrite trap and an ascarite trap. The copper catalyst is a copper oxide powder (13% CuO on alumina, Sigma-Aldrich) and is operated at 250 °C to convert CO to CO2. The coke carbon yield is determined by the mass of CO2 captured by the ascarite trap.
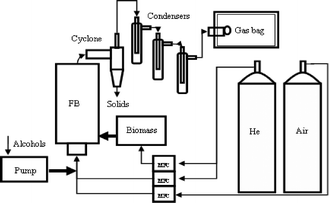 |
| Fig. 2 The schematic of the fluidized bed reactor system for catalytic fast pyrolysis of biomass and alcohols. | |
3. Results
3.1
Catalytic fast pyrolysis of pine wood
3.1.1 Effect of reaction temperature on pyrolysis product yields and selectivities.
Fig. 3 and Table 1 show the product carbon yields for CFP of pine wood in the fluidized bed reactor at different temperatures. As can be seen from the figure, the aromatic and olefin yields go through a maximum of 13.9% and 9.4% at 600 °C, respectively. The maximum total carbon yield of petrochemicals (aromatics + C2–C4olefins + C5 compounds) is 23.7%, which occurs at 600 °C. The coke and unidentified oxygenates yields decrease with increasing temperature from 40.4% and 28.4% at 400 °C to 19.7% and 2.9% at 650 °C, respectively. The CO and methane yields increase with increasing temperature from 16.2% and 0.3% at 400 °C to 44.1% and 6.9% at 650 °C, respectively. The detailed product carbon yields and selectivities are listed in Table 1. The main aromatic products include benzene, toluene, xylene and naphthalene. Benzene and naphthalene selectivities increase, while xylene and ethyl benzene selectivities decrease with increasing temperature. The main C2–C4olefins produced in the reactions include ethylene, propylene, butenes and butadiene. Propylene and butenes selectivities decrease and ethylene selectivity increases with increasing temperature.
Table 1 Detailed product yields and selectivities for CFP of pine wood at various temperatures and WHSV = 0.35 h−1. Aromatic selectivity is defined as the moles of carbon in the product divided by the total moles aromatic carbon. Olefin selectivity is defined as the moles of carbon in the product divided by the total moles olefin carbon
Compound |
T/°C |
|
400 |
450 |
500 |
600 |
650 |
Overall yields
|
Aromatics |
4.6 |
5.9 |
10.5 |
13.9 |
7.8 |
C2–C4olefins |
2.7 |
4.3 |
5.4 |
9.4 |
6.8 |
C5 compounds |
0.3 |
0.5 |
0.3 |
0.5 |
0.3 |
Petrochemicals |
7.6 |
10.7 |
16.2 |
23.7 |
14.9 |
Methane
|
0.3 |
0.6 |
2.1 |
4.3 |
6.9 |
CO2 |
7.1 |
8.9 |
7.7 |
9.5 |
11.6 |
CO
|
16.2 |
19.7 |
25.6 |
32.2 |
44.1 |
Coke |
40.4 |
41.6 |
31.7 |
26.7 |
19.7 |
Total balance |
71.7 |
81.4 |
83.3 |
96.4 |
97.1 |
Unidentified |
28.4 |
18.6 |
16.7 |
3.6 |
2.9 |
Aromatic selectivity
|
Benzene
|
13.4 |
10.8 |
15.3 |
20.8 |
38.8 |
Toluene
|
30.9 |
32.2 |
34.7 |
37.1 |
30.7 |
Ethyl-benzene
|
4.9 |
3.4 |
4.5 |
2.3 |
0 |
p-Xylene and m-Xylene |
29.6 |
33.2 |
24.1 |
16.6 |
8.9 |
o-Xylene
|
7.1 |
4.8 |
3.5 |
3.2 |
2.2 |
Styrene
|
0 |
0 |
3.7 |
2.8 |
0 |
Benzofuran
|
3.0 |
4.3 |
1.6 |
1.9 |
0 |
Indene
|
2.4 |
2.6 |
3.3 |
2.6 |
1.8 |
Phenol
|
1.4 |
1.1 |
1.5 |
1.4 |
1.3 |
Naphthalene
|
7.3 |
7.7 |
7.7 |
11.2 |
16.4 |
Olefin
selectivity
|
Ethylene
|
36.5 |
54.9 |
49.0 |
52.8 |
66.4 |
Propylene
|
48.1 |
36.0 |
37.8 |
36.0 |
26.4 |
Butenes
|
7.2 |
7.2 |
7.0 |
6.0 |
3.8 |
Butadiene
|
8.2 |
1.9 |
6.2 |
5.2 |
3.4 |
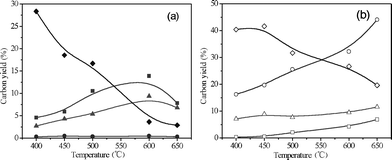 |
| Fig. 3 Product yields as a function of temperature for CFP of pine wood. Reaction conditions: ZSM-5 catalyst, 0.35 h−1WHSV. 1200 mL min−1helium fluidizing flow rate, 30 min reaction time. Key: (a) ■ Aromatics, ▲ C2–C4olefins, ● C5 compounds, ◆ Unidentified; (b) □ Methane, △ CO2, ○ CO, ◇ Coke. | |
3.1.2 Effect of weight hourly space velocity on pyrolysis product yields and selectivities.
The product carbon yields for CFP of pine wood at 600 °C as a function of weight hourly space velocity (WHSV) are shown in Fig. 4 and Table 2. WHSV is defined as the mass flow rate of feed divided by the mass of catalyst in the reactor. A WHSV of 0.11–1.98 h−1 was used for these experiments, which corresponds to feeding between 1.65–29.7 g of wood to the reactor. The aromatic and olefin yields go through a maximum at WHSV = 0.35 h−1. The unidentified oxygenates yield increases from 2.6% at WHSV = 0.11 h−1 to 17.3% at WHSV = 1.98 h−1 with increasing WHSV. The methane yield increases from 3.0% to 6.5% with increasing WHSV. The CO yield goes through a maximum of 36.3% at WHSV = 0.60 h−1. The CO2 and coke yields decrease with increasing WHSV. The xylene and toluene selectivities decrease, whereas the benzene and naphthalene selectivities increase with increasing WHSV. The ethylene and butenes selectivities decrease with the increase of WHSV.
Table 2 Detailed product yields and selectivities for CFP of pine wood at various WHSV values and 600 °C. Aromatic selectivity is defined as the moles of carbon in the product divided by the total moles aromatic carbon. Olefin selectivity is defined as the moles of carbon in the product divided by the total moles olefin carbon
Compound |
WHSV (h−1) |
|
0.11 |
0.18 |
0.35 |
0.60 |
0.97 |
1.98 |
Overall yields
|
Aromatics |
6.7 |
10.4 |
13.9 |
11.4 |
9.8 |
4.4 |
C2–C4olefins |
7.6 |
8.6 |
9.4 |
7.8 |
7.0 |
7.7 |
C5 compounds |
0.7 |
0.8 |
0.5 |
0.3 |
0.4 |
0.1 |
Petrochemicals |
15.0 |
19.8 |
23.7 |
19.5 |
17.2 |
12.3 |
Methane
|
3.0 |
2.9 |
4.3 |
5.9 |
5.3 |
6.5 |
CO2 |
18.2 |
14.3 |
9.5 |
8.2 |
7.7 |
8.4 |
CO
|
28.3 |
29.2 |
32.2 |
36.3 |
32.0 |
30.8 |
Coke |
32.9 |
30.6 |
26.7 |
23.6 |
23.5 |
24.8 |
Total balance |
97.4 |
96.8 |
96.4 |
93.4 |
85.7 |
82.7 |
Unidentified |
2.6 |
3.2 |
3.6 |
6.6 |
14.3 |
17.3 |
Aromatic selectivity
|
Benzene
|
25.4 |
21.7 |
20.8 |
24.3 |
29.2 |
36.4 |
Toluene
|
40.1 |
37.2 |
37.1 |
32.0 |
24.8 |
20.9 |
Ethyl-benzene
|
1.7 |
1.8 |
2.3 |
2.0 |
2.6 |
2.0 |
p-Xylene and m-Xylene |
18.1 |
19.0 |
16.6 |
14.2 |
13. 5 |
9.0 |
o-Xylene
|
3.8 |
1.1 |
3.2 |
4.2 |
2.8 |
2.8 |
Styrene
|
0 |
3.8 |
2.8 |
2.0 |
2.7 |
1.6 |
Benzofuran
|
0.3 |
1.6 |
1.9 |
2.2 |
2.8 |
2.9 |
Indene
|
1.4 |
2.3 |
2.6 |
3.5 |
2.6 |
2.3 |
Phenol
|
0.6 |
1.0 |
1.4 |
1.7 |
1.4 |
1.0 |
Naphthalene
|
8.7 |
10.6 |
11.2 |
13.9 |
17.7 |
21.3 |
Olefin
selectivity
|
Ethylene
|
55.6 |
49.3 |
52.8 |
61.1 |
53.3 |
49.4 |
Propylene
|
24.9 |
32.3 |
36.0 |
29.5 |
37.0 |
40.1 |
Butenes
|
14.2 |
12.3 |
6.0 |
4.6 |
4.8 |
5.9 |
Butadiene
|
5.2 |
6.0 |
5.2 |
4.9 |
4.9 |
4.6 |
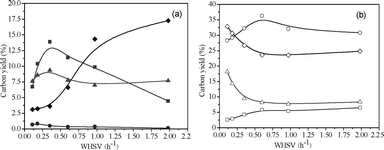 |
| Fig. 4 Product yields as a function of WHSV for CFP of pine wood. Reaction conditions: ZSM-5 catalyst, 600 °C. 1200 mL min−1helium fluidizing flow rate, 30 min reaction time. Key: (a) ■ Aromatics, ▲ C2–C4olefins, ● C5 compounds, ◆ Unidentified; (b) □ Methane, △ CO2, ○ CO, ◇ Coke. | |
3.2
Catalytic conversion of methanol
3.2.1 Effect of reaction temperature on product yields and selectivities.
Product carbon yields of catalytic conversion of methanol at different temperatures with WHSV of 0.35 h−1 are shown in Fig. 5 and Table 3. Temperature has a pronounced effect on the product distribution. The yields of C2–C4olefins, aromatics, C5 compounds and unidentified oxygenates decrease with increasing temperature. The yields of methane, CO2, CO and coke increase with increasing temperature. Temperature has the biggest effect on the olefin and CO yields. The olefin yield decreases from 52.3% at 400 °C to 0.2% at 600 °C. The CO yield increases from 1.3% at 400 °C to 59.7% at 600 °C. The petrochemical yield decreases from 80.7% at 400 °C to 3.8% at 600 °C. Table 3 lists the detailed product yields and selectivities. The benzene and toluene selectivities increase and xylene selectivity decreases with the increase of temperature. At high temperature (600 °C) almost all the methanol is converted into CO, CO2, methane and coke.
Table 3 Detailed product yields and selectivities for catalytic conversion of methanol at various temperatures and WHSV = 0.35 h−1. Aromatic selectivity is defined as the moles of carbon in the product divided by the total moles aromatic carbon. Olefin selectivity is defined as the moles of carbon in the product divided by the total moles olefin carbon
Compound |
T/°C |
|
400 |
450 |
500 |
600 |
Overall yields
|
Aromatics |
14.8 |
11.1 |
5.5 |
3.5 |
C2–C4olefins |
52.3 |
52.6 |
34.6 |
0.2 |
C5 compounds |
13.6 |
7.9 |
1.8 |
0.1 |
Petrochemicals |
80.7 |
71.5 |
41.9 |
3.8 |
Methane
|
1.8 |
4.5 |
11.0 |
8.4 |
CO2 |
3.7 |
8.9 |
21.5 |
21.1 |
CO
|
1.3 |
5.1 |
21.0 |
59.7 |
Coke |
1.8 |
2.1 |
2.9 |
5.5 |
Total balance |
89.3 |
92.1 |
98.3 |
98.4 |
Unidentified |
10.7 |
7.9 |
1.7 |
1.6 |
Aromatic selectivity
|
Benzene
|
1.8 |
3.3 |
9.6 |
23.7 |
Toluene
|
11.1 |
15.6 |
19.3 |
40.6 |
Ethyl-benzene
|
1.8 |
1.6 |
2.5 |
2.0 |
p-Xylene and m-Xylene |
57.3 |
56.5 |
43.3 |
20.8 |
o-Xylene
|
9.5 |
9.5 |
7.6 |
1.2 |
Indene
|
18.5 |
13.6 |
11.0 |
2.6 |
Olefin
selectivity
|
Ethylene
|
14.3 |
18.0 |
20.2 |
0 |
Propylene
|
43.7 |
50.2 |
51.5 |
100 |
Butenes
|
38.3 |
25.9 |
24.9 |
0 |
Butadiene
|
3.7 |
5.9 |
3.4 |
0 |
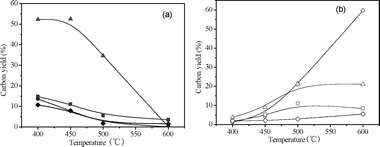 |
| Fig. 5 Product yields as a function of temperature for catalytic conversion of methanol. Reaction conditions: ZSM-5 catalyst, 0.35 h−1WHSV. 1200 mL min−1helium fluidizing flow rate, 30 min reaction time. Key: (a) ■ Aromatics, ▲ C2–C4Olefins, ● C5 compounds, ◆ Unidentified; (b) □ Methane, △ CO2, ○ CO, ◇ Coke. | |
3.2.2 Effect of weight hourly space velocity on product yields and selectivities.
Fig. 6 and Table 4 show product yields as a function of WHSV for catalytic conversion of methanol at 450 °C. The petrochemical yields increase rapidly at lower WHSV, while CO, CO2, methane and coke yields show the opposite trend. At WHSV above 0.50, little change is observed. The petrochemical yield increases from 19.5% to 59.7% when the WHSV increases from 0.08 h−1 to 0.15 h−1. The petrochemical yield increases to 71.5% at WHSV = 0.35 h−1, however, further increasing the WHSV has little effect on the total yield. This indicates that methanol conversion is sensitive at low WHSV. Benzene selectivity decreases, and xylene selectivity increases with increasing WHSV. Ethylene selectivity decreases, and propylene and butenes selectivities increase with the increase of WHSV. These experiments show that the maximum petrochemical yield for methanol conversion occurs at low temperatures and high WHSV.
Table 4 Detailed product yields and selectivities for catalytic conversion of methanol at various WHSV values and 450 °C. Aromatic selectivity is defined as the moles of carbon in the product divided by the total moles aromatic carbon. Olefin selectivity is defined as the moles of carbon in the product divided by the total moles olefin carbon
Compound |
WHSV (h−1) |
|
0.08 |
0.15 |
0.35 |
0.68 |
2.11 |
Overall yields
|
Aromatics |
2.8 |
9.7 |
11.1 |
14.0 |
13.5 |
C2–C4olefins |
14.2 |
45.2 |
52.6 |
50.8 |
51.2 |
C5 compounds |
2.6 |
4.8 |
7.9 |
12.7 |
14.2 |
Petrochemicals |
19.5 |
59.7 |
71.5 |
77.5 |
78.9 |
Methane
|
9.9 |
10.5 |
4.5 |
3.6 |
2.2 |
CO2 |
27.8 |
12.0 |
8.9 |
7.0 |
3.0 |
CO
|
36.0 |
8.1 |
5.1 |
1.8 |
0.9 |
Coke |
6.4 |
5.7 |
2.1 |
1.1 |
0.3 |
Total balance |
99.7 |
95.9 |
92.1 |
90.9 |
85.3 |
Unidentified |
0.3 |
4.1 |
7.9 |
9.1 |
14.7 |
Aromatic selectivity
|
Benzene
|
9.2 |
3.8 |
3.3 |
2.9 |
2.2 |
Toluene
|
22.1 |
16.5 |
15.6 |
17.7 |
16.0 |
Ethyl-benzene
|
0 |
1.3 |
1.6 |
2.2 |
2.6 |
p-Xylene and m-Xylene |
49.5 |
54.9 |
56.5 |
55.7 |
58.8 |
o-Xylene
|
13.1 |
10.2 |
9.5 |
9.8 |
9.2 |
Indene
|
6.2 |
13.2 |
13.6 |
11.6 |
11.3 |
Olefin
selectivity
|
Ethylene
|
35.0 |
17.3 |
18.0 |
14.9 |
12.6 |
Propylene
|
34.1 |
52.7 |
50.2 |
42.6 |
42.3 |
Butenes
|
27.7 |
25.3 |
25.9 |
37.4 |
43.2 |
Butadiene
|
3.2 |
4.7 |
5.9 |
5.1 |
1.9 |
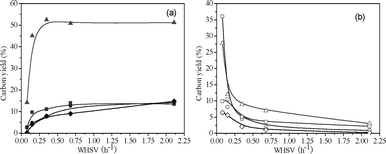 |
| Fig. 6 Product yields as a function of WHSV for catalytic conversion of methanol. Reaction conditions: ZSM-5 catalyst, 450 °C. 1200 mL min−1helium fluidizing flow rate, 30 min reaction time. Key: (a) ■ Aromatics, ▲ C2–C4olefins, ● C5 compounds, ◆ Unidentified; (b) □ Methane, △ CO2, ○ CO, ◇ Coke. | |
3.3 Co-catalytic fast pyrolysis of pine wood and methanol
3.3.1 Effect of hydrogen to carbon effective (H/Ceff) ratio at 450 °C.
CFP of pine wood and methanol mixtures was carried out by co-feeding them to the reactor. The H/Ceff ratio of the feed was adjusted by changing the space velocity ratio of pine wood and methanol. Based on our previous methanol and wood runs, we decided to operate the reactor at 450 °C and 500 °C. The product yields of co-CFP of pine wood and methanol at 450 °C as a function of H/Ceff ratio is shown in Fig. 7 and Table 5. The petrochemical yield increases non-linearly with increasing H/Ceff ratio. This curvature indicates that there is a synergistic effect between the feeds since pure addition of the yields would yield a straight line with increasing H/Ceff ratio. This synergistic effect of co-feeding is very apparent in the aromatic yield. The aromatic yield is 5.9% for the only pine wood run and 11.1% in the only methanol run. However, at the intermediate value of H/Ceff = 1.05, a maximum yield of 21.4% aromatics is realized. This result indicates that the aromatic yield is enhanced by co-feeding methanol and is not purely additive. The unidentified oxygenates yield decreases from 18.6% at H/Ceff = 0.11 to 7.9% at H/Ceff = 2. As shown in Fig. 7(b), the yields of CO and coke decrease significantly with the increase of the H/Ceff ratio as non-linear curves, while that of CO2 remains constant. Fig. 8 shows the selectivities of benzene, toluene, xylene and naphthalene in the aromatic products and ethylene, propylene, butenes and butadiene in olefin products. As shown in the figure, the selectivities of the more valuable chemicals, such as xylene, propylene, butenes and butadiene, increase significantly with the increase of H/Ceff ratio, while the selectivities of the less valuable chemicals, such as naphthalene decreases.
Table 5 Detailed product yields and selectivities for co-CFP of pine wood and methanol at various H/Ceff ratios and 450 °C. Aromatic selectivity is defined as the moles of carbon in the product divided by the total moles aromatic carbon. Olefin selectivity is defined as the moles of carbon in the product divided by the total moles olefin carbon
Compound |
H/Ceff (mol/mol) ratio |
|
0.11 |
0.47 |
0.76 |
1.05 |
1.25 |
1.64 |
2.00 |
Pine wood WHSV (h−1) |
0.35 |
0.46 |
0.23 |
0.28 |
0.20 |
0.06 |
0 |
Methanol WHSV (h−1) |
0 |
0.13 |
0.15 |
0.35 |
0.37 |
0.34 |
0.35 |
Total WHSV (h−1) |
0.35 |
0.59 |
0.38 |
0.63 |
0.56 |
0.41 |
0.35 |
Overall yields
|
Aromatics |
5.9 |
14.8 |
18.8 |
21.4 |
21.1 |
14.0 |
11.1 |
C2–C4olefins |
4.3 |
13.5 |
18.7 |
26.4 |
32.9 |
47.9 |
52.6 |
C5 compounds |
0.5 |
1.2 |
2.9 |
3.7 |
4.7 |
6.3 |
7.9 |
Petrochemicals |
10.7 |
29.4 |
40.5 |
51.4 |
58.7 |
68.3 |
71.5 |
Methane
|
0.6 |
1.4 |
2.6 |
1.5 |
2.1 |
3.1 |
4.5 |
CO2 |
8.9 |
7.3 |
6.8 |
7.1 |
7.2 |
7.8 |
8.9 |
CO
|
19.7 |
14.9 |
12.6 |
9.4 |
7.7 |
5.8 |
5.1 |
Coke |
41.6 |
30.3 |
23.4 |
17.8 |
14.5 |
7.4 |
2.1 |
Total balance |
81.4 |
83.3 |
85.8 |
87.2 |
90.2 |
92.3 |
92.1 |
Unidentified |
18.6 |
16.7 |
14.2 |
12.8 |
9.8 |
7.7 |
7.9 |
Theoretical petrochemical yield |
64.3 |
71.2 |
76.6 |
82.2 |
85.8 |
93.2 |
100 |
Aromatic selectivity
|
Benzene
|
10.8 |
6.5 |
6.7 |
5.8 |
5.8 |
4.5 |
3.3 |
Toluene
|
32.2 |
24.6 |
21.8 |
20.2 |
16.9 |
18.0 |
15.6 |
Ethyl-benzene
|
3.4 |
2.9 |
2.5 |
3.1 |
2.4 |
1.5 |
1.6 |
p-Xylene and m-Xylene |
33.2 |
48.6 |
51.0 |
51.1 |
53.6 |
52.2 |
56.5 |
o-Xylene
|
4.8 |
8.2 |
9.2 |
11.4 |
9.3 |
11.3 |
9.5 |
Benzofuran
|
4.3 |
2.2 |
1.0 |
1.0 |
0.6 |
0.4 |
0 |
Indene
|
2.6 |
2.4 |
3.0 |
3.8 |
8.5 |
11.6 |
13.6 |
Phenol
|
1.1 |
0.4 |
0.3 |
0.2 |
0.2 |
0 |
0 |
Naphthalene
|
7.7 |
4.4 |
4.5 |
3.5 |
2.8 |
0.6 |
0 |
Olefin
selectivity
|
Ethylene
|
54.9 |
37.9 |
30.9 |
23.2 |
19.6 |
16.1 |
18.0 |
Propylene
|
36.0 |
40.1 |
44.4 |
48.7 |
50.3 |
51.4 |
50.2 |
Butenes
|
7.3 |
19.9 |
21.3 |
24.9 |
26.4 |
27.6 |
25.9 |
Butadiene
|
1.8 |
2.1 |
3.4 |
3.2 |
3.7 |
4.9 |
5.9 |
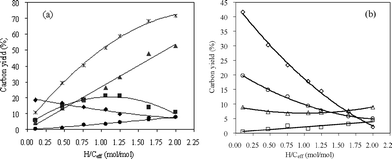 |
| Fig. 7 Product yields as a function of H/Ceff ratio for co-CFP of pine wood and methanol at 450 °C. Key: (a) ■ Aromatics, ▲ C2–C4olefins, ● C5 compounds, ◆ Unidentified, * Petrochemicals; (b) □ Methane, △ CO2, ○ CO, ◇ Coke. | |
3.3.2 Effect of hydrogen to carbon effective (H/Ceff) ratio at 500 °C.
The product carbon yields and selectivities as a function of H/Ceff ratio for co-CFP of pine wood and methanol at 500 °C are shown in Fig. 9 and 10 and Table 6. It can be seen from Fig. 9 that the unidentified compounds, CO and coke yields decrease with the increasing H/Ceff ratio, while C2–C4olefins, CO2 and methane yields increase significantly. Aromatic yield is relatively constant at around 10% when the H/Ceff ratio increases from 0.11 to 1.15. The aromatic yield decreases to 5.5% with further increase of the H/Ceff ratio to 2. As shown in Fig. 10, xylene selectivity increases with increasing H/Ceff ratio, and toluene selectivity decreases. Propylene selectivity increases with increasing H/Ceff ratio. Ethylene selectivity decreases non-linearly with the increasing of the H/Ceff ratio, whereas butenes selectivity shows the opposite trend and increases non-linearly. These non-linear curves indicate that the products are affected by the co-feeding, and again a synergistic effect occurs at 500 °C.
Table 6 Detailed product yields and selectivities for co-CFP of pine wood and methanol at various H/Ceff ratios and 500 °C. Aromatic selectivity is defined as the moles of carbon in the product divided by the total moles aromatic carbon. Olefin selectivity is defined as the moles of carbon in the product divided by the total moles olefin carbon
Compound |
H/Ceff ratio (mol/mol) |
|
0.11 |
0.51 |
0.74 |
1.15 |
2.00 |
Pine wood WHSV (h−1) |
0.41 |
0.24 |
0.28 |
0.18 |
0 |
Methanol WHSV (h−1) |
0 |
0.08 |
0.18 |
0.27 |
0.35 |
Total WHSV (h−1) |
0.41 |
0.33 |
0.46 |
0.44 |
0.35 |
Overall yields
|
Aromatics |
10.5 |
10.3 |
10.6 |
9.6 |
5.5 |
C2–C4olefins |
5.4 |
11.1 |
13.5 |
21.1 |
34.6 |
C5 compounds |
0.3 |
1.2 |
1.3 |
1.1 |
1.8 |
Petrochemicals |
16.2 |
22.6 |
25.4 |
31.8 |
41.9 |
Methane
|
2.1 |
4.3 |
5.5 |
8.0 |
11.0 |
CO2 |
7.7 |
9.8 |
14.1 |
17.3 |
21.5 |
CO
|
25.6 |
24.0 |
23.7 |
21.8 |
21.0 |
Coke |
31.7 |
24.6 |
20.1 |
12.7 |
2.9 |
Total balance |
83.3 |
85.3 |
88.7 |
91.5 |
98.3 |
Unidentified |
16.7 |
14.7 |
11.3 |
8.5 |
1.7 |
Theoretical petrochemical yield |
64.3 |
72.0 |
76.2 |
83.9 |
100 |
Aromatic selectivity
|
Benzene
|
15.3 |
11.7 |
10.6 |
10.6 |
9.7 |
Toluene
|
34.7 |
28.5 |
27.7 |
26.9 |
19.3 |
Ethyl-benzene
|
4.5 |
2.2 |
2.3 |
1.9 |
2.5 |
p-Xylene and m-Xylene |
24.1 |
28.8 |
33.6 |
41.8 |
43.3 |
o-Xylene
|
3.5 |
0.9 |
0.8 |
7.6 |
7.7 |
Styrene
|
3.7 |
5.2 |
6.2 |
0 |
4.4 |
Benzofuran
|
1.6 |
9.0 |
7.7 |
2.8 |
0 |
Indene
|
3.3 |
2.0 |
1.7 |
1.2 |
11.0 |
Phenol
|
1.5 |
1.0 |
0.8 |
0.5 |
0 |
Naphthalene
|
7.7 |
10.8 |
8.6 |
6.7 |
2.2 |
Olefin
selectivity
|
Ethylene
|
49.0 |
33.2 |
26.5 |
24.1 |
20.2 |
Propylene
|
37.8 |
41.9 |
44.1 |
46.3 |
51.5 |
Butenes
|
7.0 |
20.9 |
24.8 |
25.5 |
24.9 |
Butadiene
|
6.2 |
4.0 |
4.6 |
4.1 |
3.4 |
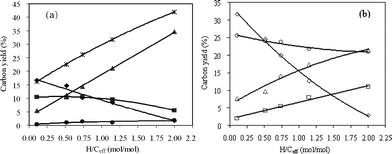 |
| Fig. 9 Product yields as a function of H/Ceff ratio for co-CFP of pine wood and methanol at 500 °C. Key: (a) ■ Aromatics, ▲ C2–C4olefins, ● C5 compounds, ◆ Unidentified, * Petrochemicals; (b) □ Methane, △ CO2, ○ CO, ◇ Coke. | |
3.3.3 Effect of the total space velocity at constant H/Ceff ratio.
Fig. 11 and 12 show the product carbon yields and selectivities of co-CFP of pine wood and methanol at different total WHSV with a constant H/Ceff ratio of 1.05 at 450 °C. It can be seen from Fig. 11, lower total WHSV favors C2–C4olefins and coke productions, while higher WHSV produces more CO and unidentified oxygenates. The aromatic and total petrochemical yields go through a maximum value of 21.4% and 51.4% at a WHSV of 0.63 h−1, respectively. The aromatic and olefin selectivities are relatively constant over the WHSV range tested, with the exception of toluene and butenes that increase slightly with WHSV. Table 7 shows the detailed product carbon yields and selectivities for co-CFP of pine wood and methanol at different total space velocities.
Table 7 Detailed product yields and selectivities for co-CFP of pine wood and methanol at various total space velocities, H/Ceff = 1.05 and 450 °C. Aromatic selectivity is defined as the moles of carbon in the product divided by the total moles aromatic carbon. Olefin selectivity is defined as the moles of carbon in the product divided by the total moles olefin carbon
Compound |
Total WHSV (h−1) |
|
0.27 |
0.63 |
1.33 |
T/°C |
450 |
450 |
450 |
Pine wood WHSV (h−1) |
0.12 |
0.28 |
0.65 |
WHSV of co-feeding alcohol (h−1) |
0.15 |
0.35 |
0.68 |
H/Ceff (mol/mol) |
1.05 |
1.05 |
0.98 |
Overall yields
|
Aromatics |
17.1 |
21.4 |
18.9 |
C2–C4olefins |
27.6 |
26.3 |
21.5 |
C5 compounds |
2.4 |
3.7 |
2.8 |
Petrochemicals |
47.1 |
51.4 |
43.2 |
Methane
|
2.2 |
1.5 |
1.3 |
CO2 |
6.6 |
7.1 |
4.6 |
CO
|
8.9 |
9.4 |
12.8 |
Coke |
23.6 |
17.8 |
16.4 |
Total balance |
88.4 |
87.2 |
78.2 |
Unidentified |
11.6 |
12.8 |
21.8 |
Theoretical petrochemical yield |
82.2 |
82.2 |
80.8 |
Aromatic selectivity
|
Benzene
|
3.8 |
5.8 |
4.3 |
Toluene
|
16.5 |
20.2 |
21.0 |
Ethyl-benzene
|
1.8 |
3.1 |
3.6 |
p-Xylene and m-Xylene |
49.8 |
51.1 |
51.6 |
o-Xylene
|
9.6 |
11.4 |
9.0 |
Benzofuran
|
1.8 |
1.0 |
0.5 |
Indene
|
13.2 |
3.8 |
7.0 |
Phenol
|
0.5 |
0.2 |
0.2 |
Naphthalene
|
3.0 |
3.5 |
2.9 |
Olefin
selectivity
|
Ethylene
|
24.3 |
23.2 |
24.3 |
Propylene
|
52.9 |
48.7 |
48.3 |
Butenes
|
19.5 |
24.9 |
24.1 |
Butadiene
|
3.3 |
3.2 |
3.3 |
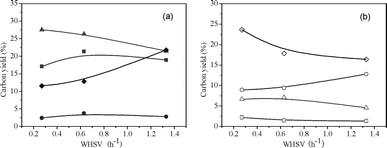 |
| Fig. 11 Product carbon yields of co-CFP of pine wood and methanol at different total WHSV values, H/Ceff = 1.05 and 450 °C. Key: (a) ■ Aromatics, ▲ C2–C4olefins, ● C5 compounds, ◆ Unidentified; (b) □ Methane, △ CO2, ○ CO, ◇ Coke. | |
3.3.4
Isotopic labelling studies of co-catalytic fast pyrolysis of pine wood and methanol.
Co-CFP of 12C pine wood and isotopically labeled 13C methanol was conducted at 450 °C to determine how methanol enters the hydrocarbon pool. The WHSV values of 12C pine wood and 13C methanol were 0.30 h−1 and 0.29 h−1, respectively. The H/Ceff ratio of the mixture was 0.97. The mass spectra of the most abundant products are shown in Fig. 13. The fragmentation patterns for the pure 12C or pure 13C compounds are shown in black and white, respectively. The spectra of the product obtained during the co-feeding experiment are shown in grey. The results show that all the main products are a mixture of 12C and 13C labeled carbons. The distribution of carbon in benzene is a random mixture of the 12C and 13C carbons. However, the distributions of carbon within the other aromatics show trends. The distribution of toluene and xylene are both shifted to the higher masses. This indicates that a randomly distributed benzene molecule was preferably alkylated by a 13C-containing radical over a 12C-containing radical. Naphthalene shows the opposite trend as its spectrum is shifted toward the lower masses. This shows that the rate of naphthalene formation from the pine wood is higher than that from the methanol. The methyl naphthalene is not as shifted as the naphthalene, which shows that the methyl group probably also came from methanol, similar to toluene and xylene. The olefin compounds spectra also show obvious trends. When taking into account the overlap of the fragmentation peaks, the ethylene appears to be composed of more 12C than 13C carbon, while propylene and butenes show more 13C carbon. In summary, 12C and 13C are distributed in all the hydrocarbon product molecules. Benzene is a random mixture of the 12C and 13C carbons, whereas naphthalene is formed much faster from the carbon of pine wood than methanol. However, their alkylated products were preferably alkylated by a 13C-containing radical over a 12C-containing radical. This indicates that the methanol enters zeolite catalytic process of biomass and it is feasible to use feeds with high H/Ceff ratio to provide hydrogen to the hydrocarbon pool for biomass conversion.
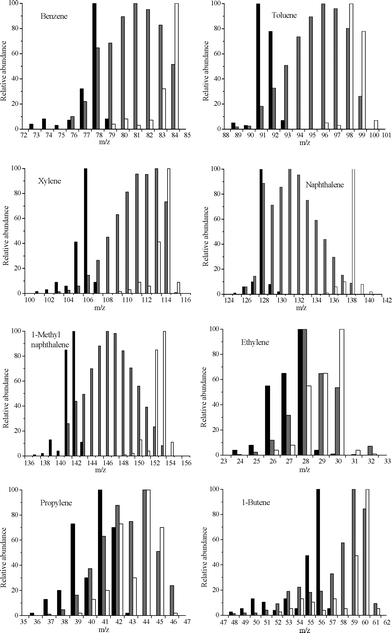 |
| Fig. 13 Isotopic distributions for benzene, toluene, xylene, naphthalene, 1-methyl naphthalene, ethylene, propylene and 1-butene from the co-CFP of 12C pine wood and 13C methanol. Pure 12C and 13C mass spectra for the given molecules are shown in black and white, respectively. The co-feeding run results are shown in grey. Reaction conditions: catalyst, ZSM-5; reaction temperature, 450 °C; WHSV of 12C pine wood, 0.30 h−1; WHSV of 13C methanol, 0.29 h−1; the hydrogen to carbon effective (H/Ceff) ratio, 0.97; helium fluidizing flow rate, 1200 mL min−1; reaction time, 30 min. | |
Fig. 14 and Table 8 shows the petrochemical yield of co-CFP of pine wood and other alcohols at H/Ceff = 1.25 and 450 °C. The “calculated” values for the mixtures were found by a weighted average of the yields from CFP of pine wood and the alcohol separately. As shown in the figure, CFP of pine wood produced 10.7% hydrocarbon yield, while methanol, 1-propanol, 1-butanol and 2-butanol gave 71.5%, 86.8%, 86.3% and 90.3% of hydrocarbon yield, respectively. The co-feeding of pine wood and methanol yielded the lowest amount of petrochemicals (58.7%), while co-feeding of pine wood and 2-butanol produced the highest carbon yield of 65.2%. However, compared with their calculated values, co-CFP of pine wood and methanol gave the highest increase of hydrocarbon yield and the best synergistic effect. The product carbon yields and selectivities of co-CFP of pine wood and the various alcohols at H/Ceff = 1.25 and 450 °C are listed in Table 8. As shown in the table, the product selectivities of co-CFP of pine wood and 1-propanol, 1-butanol and 2-butanol are very similar, but there is a great difference with co-feeding pine wood and methanol, especially in aromatic selectivities. Co-conversion of pine wood and methanol gave 62.9%, 5.8% and 16.9% selectivities of xylene, benzene and toluene, respectively. Co-conversion of pine wood with other alcohols gave about 39.2–40.2%, 10.4–11.0% and 38.6–39.3% of xylene, benzene and toluene, respectively. This can be explained by the fact that methanol produced more methyl radicals than other alcohols at the same H/Ceff ratio. Thus more benzene and toluene molecules were alkylated to xylene molecules.
Table 8 Detailed product yields and selectivities for CFP of pine wood and methanol, 1-propanol, 1-butanol and 2-butanol at H/Ceff = 1.25 and 450 °C. Aromatic selectivity is defined as the moles of carbon in the product divided by the total moles aromatic carbon. Olefin selectivity is defined as the moles of carbon in the product divided by the total moles olefin carbon
Compound |
Co-feeding alcohol |
|
Pine wood |
Methanol
|
1-Propanol
|
1-Butanol
|
2-Butanol
|
Pine wood WHSV (h−1) |
0.35 |
0 |
0.20 |
0 |
0.24 |
0 |
0.30 |
0 |
0.29 |
WHSV of co-feeding alcohol (h−1) |
0 |
0.35 |
0.36 |
0.34 |
0.34 |
0.34 |
0.34 |
0.35 |
0.35 |
Total WHSV (h−1) |
0.35 |
0.35 |
0.56 |
0.34 |
0.58 |
0.34 |
0.64 |
0.35 |
0.64 |
H/Ceff ratio (mol/mol) |
0.11 |
2.00 |
1.25 |
2.00 |
1.34 |
2.00 |
1.27 |
2.00 |
1.31 |
Overall yields
|
Aromatics |
5.9 |
11.1 |
21.1 |
13.3 |
16.3 |
15.2 |
17.2 |
15.2 |
15.6 |
C2–C4olefins |
4.3 |
52.6 |
32.9 |
66.2 |
43.3 |
60.7 |
38.4 |
67.2 |
44.6 |
C5 compounds |
0.5 |
7.9 |
4.7 |
7.3 |
4.6 |
10.3 |
6.0 |
7.9 |
5.0 |
Petrochemicals |
10.7 |
71.5 |
58.7 |
86.8 |
64.3 |
86.3 |
61.5 |
90.3 |
65.2 |
Methane
|
0.6 |
4.5 |
2.1 |
0.2 |
0.4 |
0.2 |
0.4 |
0.2 |
0.4 |
CO2 |
8.9 |
8.9 |
7.2 |
0.2 |
2.3 |
0.2 |
2.2 |
0.2 |
2.8 |
CO
|
19.7 |
5.1 |
7.7 |
0.4 |
6.5 |
1.1 |
6.9 |
0.5 |
7.6 |
Coke |
41.6 |
2.1 |
14.5 |
1.6 |
10.7 |
1.0 |
14.3 |
1.0 |
12.8 |
Total balance |
81.4 |
92.1 |
90.2 |
89.2 |
84.1 |
88.7 |
85.5 |
92.1 |
88.8 |
Theoretical (Toluene) |
64.3 |
100 |
85.8 |
100 |
87.5 |
100 |
86.2 |
100 |
86.9 |
Experimental/theoretical |
16.6 |
71.5 |
68.4 |
86.8 |
73.5 |
86.3 |
71.4 |
90.3 |
75.0 |
Aromatic selectivity
|
Benzene
|
10.8 |
3.3 |
5.8 |
11.8 |
11.0 |
11.5 |
10.6 |
12.0 |
10.4 |
Toluene
|
32.2 |
15.6 |
16.9 |
43.1 |
39.3 |
40.8 |
38.7 |
43.8 |
38.6 |
Ethyl-benzene
|
3.4 |
1.6 |
2.4 |
3.6 |
3.7 |
3.5 |
4.2 |
3.7 |
4.2 |
p-Xylene and m-Xylene |
33.2 |
56.5 |
53.6 |
31.0 |
32.8 |
27.9 |
34.2 |
30.5 |
34.0 |
o-Xylene
|
4.8 |
9.5 |
9.3 |
7.0 |
6.4 |
6.0 |
6.0 |
6.7 |
6.2 |
Benzofuran
|
4.3 |
0 |
0.6 |
0.1 |
0.5 |
0.1 |
0.5 |
0.1 |
0.4 |
Indene
|
2.6 |
13.6 |
8.5 |
2.5 |
2.3 |
2.0 |
2.5 |
2.3 |
2.6 |
Phenol
|
1.1 |
0 |
0.2 |
0.2 |
0.5 |
0.1 |
0.2 |
0.2 |
0.5 |
Naphthalene
|
7.7 |
0 |
2.8 |
0.8 |
3.6 |
0.6 |
3.1 |
0.7 |
3.1 |
Olefin
selectivity
|
Ethylene
|
54.9 |
18.0 |
19.5 |
10.9 |
12.8 |
12.2 |
12.4 |
10.0 |
13.4 |
Propylene
|
36.0 |
50.2 |
50.3 |
55.7 |
54.5 |
52.7 |
53.8 |
53.8 |
51.5 |
Butenes
|
7.3 |
25.9 |
26.5 |
29.6 |
28.6 |
31.4 |
29.8 |
32.6 |
30.9 |
Butadiene
|
1.8 |
5.9 |
3.7 |
3.8 |
4.1 |
3.7 |
4.0 |
3.6 |
4.2 |
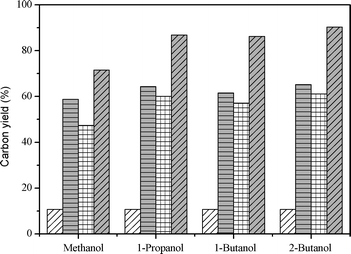 |
| Fig. 14 The petrochemical yield of co-CFP of pine wood and methanol, 1-propanol, 1-butanol and 2-butanol at H/Ceff = 1.25 and 450 °C. Key: Pure pine wood; Experimental values for co-feeding of pine wood with alcohol; Calculated values of co-feeding of pine wood with alcohols; Pure alcohol. | |
4. Discussions
4.1 Comparison of products of co-catalytic fast pyrolysis of pine wood and methanol at 450 °C and 500 °C
Fig. 15 shows the petrochemical yield as a function of H/Ceff ratio for co-CFP of pine wood and methanol at 450 °C and 500 °C. As shown in the figure, co-CFP of pine wood and methanol at 450 °C produced much more petrochemicals than that at 500 °C, and the gap increases with increasing H/Ceff ratio. The theoretical yields of dry pine wood and methanol are calculated by assuming toluene as the reaction hydrocarbon product. The calculating equations are shown in eqn (2) and (3). |  | (2) |
| 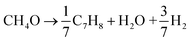 | (3) |
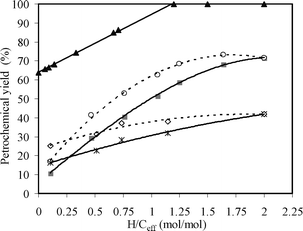 |
| Fig. 15 The petrochemical yield as a function of H/Ceff ratio at 450 °C and 500 °C. Key: Petrochemical experimental yield at reaction temperature of ■ 450 °C and * 500 °C; ▲ Theoretical yield; Experimental/theoretical ratio at reaction temperature of ○ 450 °C, ◇ 500 °C. | |
The theoretical yield of dry pine wood is about 67% carbon according to eqn (2), while that of methanol is 100% carbon shown in eqn (3). The pine wood used in this study contains about 4% moisture, thus the theoretical yield of pine wood based on the feed is 64.3%. The theoretical yield plot in Fig. 15 is drawn according to the theoretical yields that would be achieved if all the carbon in the biomass is converted into toluene, water, and carbon monoxide. Data points are added to this based on our previous study, which used ten different feedstocks.58
Also included in Fig. 15 is the ratio of experimental to the theoretical (experimental/theoreteical) yield of the different feedstocks. This ratio allows us to determine how close to the theoretical carbon yield we are for each experiment. At 450 °C, this ratio increases non-linearly from 16.6% at H/Ceff = 0.11 (only pine wood) to about 70% at H/Ceff = 1.25. Further increasing the H/Ceff ratio above 1.25 only gives a small change in the experimental/theoreteical ratio. This result suggests that the co-feeding of wood and methanol allows us to more efficiently convert the carbon in these feedstocks into petrochemicals by co-feeding rather than feeding the two reactants separately. Furthermore, the H/Ceff ratio = 1.25 is an inflection point, where the petrochemical yield does not increase as rapidly. This result is consistent with our previous study in which we catalytically deoxygenated ten biomass-derived feedstocks with different H/Ceff ratios with a zeolite catalyst and found an H/Ceff ratio = 1.2 to be the inflection point.58 This suggests that the amount of methanol co-fed with pine wood should be enough to bring the mixtures to an H/Ceff ratio of 1.25. It should be noted that co-CFP can not run at high temperature since methanol would be converted into CO, CO2, methane and coke at high temperature and pine wood would be converted into coke and unidentified oxygenates with this catalyst. The suitable temperature for co-CFP of pine wood and methanol is 450 °C.
Although co-feeding pine wood and methanol at 450 °C produced much more petrochemicals than reacting the two feeds at 450 °C separately, the petrochemical yield of co-feeding is still lower than running the two feeds at their optimal temperatures (pine wood: 600 °C; methanol: 400 °C). Therefore, to be more effective at co-utilization of wood and methanol, the catalyst should be designed to decrease the optimal temperature of pine wood CFP or increase that of methanol conversion.
4.2 Chemistry of co-catalytic fast pyrolysis of pine wood and methanol
Co-feeding of 12C pine wood and 13C methanol results show that all the hydrocarbon products contained 12C and 13C in their molecules. Our previous results observed this same phenomenon with a 1
:
1 w/w mixture of pure 12C and 13C glucose as reactants.78 This suggests that the feeds (or their derived/pyrolysis products) enter the zeolite catalyst, lose their identity within a hydrocarbon pool and combine stochastically with other molecules. This proves that adding hydrogen to biomass conversion process via co-feeding it with other higher H/Ceff ratio feeds is feasible.
From the isotopic distribution of benzene, we can see that the amount of 12C and 13C is almost the same in the benzene molecule. The toluene and xylene are probably produced from alkylation of benzene. However, their isotopic distributions are not normal distributions and lean to 13C. Combining this with benzene's isotopic distribution, it seems that almost all the methyl radicals for benzene alkylation are from methanol. Our previous study showed that naphthalene is formed by monocyclic aromatics with oxygenated fragments that are the derived products of biomass pyrolysis.78 The isotopic distribution of naphthalene, shown in Fig. 15, agrees with this conclusion because the distribution is skewed to 12C. In this study, the naphthalene is produced by randomly formed benzene combining with the oxygenated fragments (usually that are based on a furanic structure) that are the derived products of biomass pyrolysis. Methanol makes almost no naphthalene in the separate and co-feeding it with pine wood runs. Compared with the isotopic distribution of naphthalene, 1-methyl naphthalene distribution leans to 13C by 1 carbon. Thus methanol is also able to alkylate naphthalene.
4.3 Economic potential
In Section 3.3.1 it was shown that co-feeding pine wood and methanol at 450 °C increases the total aromatic yield. However, the total petrochemical yield is always highest for the pure compounds. A simple economic analysis is done to determine whether co-feeding methanol with wood is economically beneficial with the conditions used in this paper. The economic potential (EP) was used to evaluate the potential economic benefit of co-feeding wood with methanol. The EP is calculated by eqn (4): | EP = Σprice of products − Σprice of feeds | (4) |
EP is calculated for the different temperatures used in this paper. The scale of the refinery was set at 250
,000 tons products/year for all these calculations. Wood and methanol prices usually range between $20–100/ton1 and $260–360/ton,79 respectively. Five groups of price combinations were used for comparison to allow us to determine the sensitivity of these different scenarios with feedstock prices. These five groups are (a) low methanol price and low wood price, (b) high methanol price and high wood price, (c) low methanol price and high wood price, (d) high methanol price and low wood price and (e) medium methanol price and medium wood price. These figure groups of price combinations are shown in Fig. 16a–e. Each figure also shows the results with pure wood and pure methanol. The product prices were based on the following values: $889/ton-benzene, $735/ton-toluene, $1521/ton-styrene, $690/ton-indene, $690/ton-naphthalene, $804/ton-mixed xylenes, $970/ton-ethylene, $1212/ton-propylene, $1200/ton-butenes, $2270/ton-butadiene and $690/ton-gasoline (C5 compounds).79
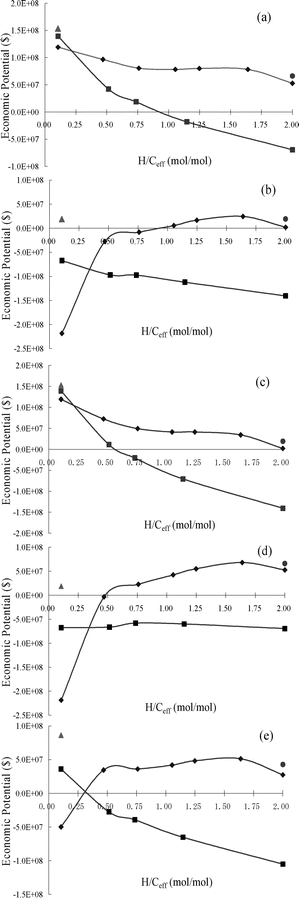 |
| Fig. 16 Economic potential (EP) for CFP and co-CFP of wood and methanol as a function of H/Ceff ratio at different feed prices. Price for wood (W) and methanol (M) ($/metric ton): (a) W = 20, M = 267; (b) W = 100, M = 334; (c) W = 20, M = 334; (d) W = 100, M = 267; (e) W = 60, M = 300. Key: ■ Co-feeding of pine wood and methanol at 500 °C; ◆ Co-feeding of pine wood and methanol at 450 °C; ▲ Pine wood at 600 °C; ● Methanol at 400 °C. | |
As can be seen from Fig. 16, co-feeding pine wood and methanol at a reaction temperature of 450 °C gives a higher EP than at a reaction temperature of 500 °C for all price scenarios when the H/Ceff ratio of the feed is greater than or equal to 0.50. When wood price is low (Fig. 16a), the EP is highest when pure wood is added to the reactor. When wood price is high, co-feeding pine wood and methanol at 450 °C made the EP increase non-linearly with increasing H/Ceff ratio (see Fig. 16(b, d and e)). This considerable curvature indicates that co-feeding of pine wood and methanol has much higher EP than that of running them separately. However, the EP of co-feeding pine wood and methanol is still lower than that of running them separately at their optimal conditions (pine wood: 600 °C and 0.35 h−1; methanol: 400 °C and 0.35 h−1).
5. Conclusions
In this work, we conducted catalytic fast pyrolysis (CFP) of pine wood, alcohols (methanol, 1-propanol, 1-butanol and 2-butanol) and their mixtures with ZSM-5 catalyst in a fluidized bed reactor. The maximum petrochemical yield when pine wood was the feedstock was 23.7%, which occurred at 600 °C and 0.35 h−1. Both the coke and unidentified oxygenates yields decrease with increasing temperature, whereas the coke yield decreases and the unidentified oxygenates yield increases with increasing WHSV. The maximum petrochemical yield when methanol was the feed was 80.7% and occurred at 400 °C and 0.35 h−1. The yields of petrochemicals and unidentified compounds decrease with increasing temperature, and the yields of methane, CO2, CO and coke increase with the increasing temperature. The petrochemical yields increase rapidly at lower WHSV, while CO, CO2, methane and coke yields show the opposite trend.
CFP of pine wood and methanol mixtures with different ratios were tested at 450 °C and 500 °C. The results show that the petrochemical yield increases non-linearly with increasing H/Ceff ratio of the feed, and more petrochemicals can be produced from wood when methanol is added to the CFP process. H/Ceff = 1.25 is an inflection point in this process, where the petrochemical yield begins to reach an asymptote. This suggests that the amount of methanol co-fed with wood should be enough to bring the mixtures to an H/Ceff ratio of 1.25. Adding more methanol would be a waste of methanol and increase the cost of the process, since methanol price is much higher than wood's. Co-CFP of pine wood and other alcohols also increases the petrochemical yield, whereas co-CFP of pine wood and methanol gave the highest increase of petrochemical yield.
The isotopic studies of CFP with 12C methanol and 13C pine wood showed that the products were produced from mixtures of methanol and pine wood. Benzene was made from random mixtures of methanol and pine wood. Propylene and butenes were produced more from methanol than wood. Naphthalene contained more 12C and therefore were produced more from pine wood than methanol. This indicates that it is feasible to use feeds with high H/Ceff ratio to provide hydrogen to the hydrocarbon pool for biomass conversion.
In summary, the petrochemical yield produced by CFP of biomass can be enhanced by co-feeding it with feeds that have a high H/Ceff ratio. In the co-feeding process, the two feeds can be converted together within the zeolite and have a positive synergistic effect. This study provides insights into how biomass resources can be used more efficiently to produce renewable petrochemicals. It is likely that future advances in the design of improved catalysts combined with reaction engineering will lead to the design of even more efficient processes for the production of renewable fuels and chemicals.
Acknowledgements
The authors are grateful for the U. S. National Science Foundation (Grant No. EFRI-0937895), National Basic Research Program of China (973 Program, Grant No. 2010CB732206), National Natural Science Foundation of China (Grant No. 51076031), China Scholarship Council and the Scientific Research Foundation of Graduate School of Southeast University.
References
- G. W. Huber, S. Iborra and A. Corma, Chem. Rev., 2006, 106, 4044–4098 CrossRef CAS.
- E. L. Kunkes, D. A. Simonetti, R. M. West, J. C. Serrano-Ruiz, C. A. Gartner and J. A. Dumesic, Science, 2008, 322, 417–421 CrossRef CAS.
- S. Czernik, J. Scahill and J. Diebold, J. Sol. Energy Eng., 1995, 117, 2–6 CrossRef CAS.
- A. V. Bridgwater, Int. J. Global Energy Issues, 2007, 27, 160–203 CrossRef.
- A. Demirbas, Energy Convers. Manage., 2001, 42, 1357–1378 CrossRef CAS.
- M. Olazar, R. Aguado, J. Bilbao and A. Barona, AIChE J., 2000, 46, 1025–1033 CrossRef CAS.
- G. W. Huber and A. Corma, Angew. Chem., Int. Ed., 2007, 46, 7184–7201 CrossRef CAS.
- R. French and S. Czernik, Fuel Process. Technol., 2010, 91, 25–32 CrossRef CAS.
- M. Stocker, Angew. Chem., Int. Ed., 2008, 47, 9200–9211 CrossRef CAS.
- Y. C. Lin and G. W. Huber, Energy Environ. Sci., 2009, 2, 68–80 CAS.
- M. Garcia-Perez, X. S. Wang, J. Shen, M. J. Rhodes, F. J. Tian, W. J. Lee, H. W. Wu and C. Z. Li, Ind. Eng. Chem. Res., 2008, 47, 1846–1854 CrossRef CAS.
- D. Mohan, C. U. Pittman and P. H. Steele, Energy Fuels, 2006, 20, 848–889 CrossRef CAS.
- D. A. Laird, R. C. Brown, J. E. Amonette and J. Lehmann, Biofuels, Bioprod. Biorefin., 2009, 3, 547–562 CrossRef CAS.
- C. J. Deng, R. H. Liu and J. M. Cai, J. Energy. Inst, 2008, 81, 211–217 CrossRef CAS.
- H. Y. Zhang, R. Xiao, D. H. Wang, G. Y. He, S. S. Shao, J. B. Zhang and Z. P. Zhong, Bioresour. Technol., 2011, 102, 4258–4264 CrossRef CAS.
- R. C. Saxena, D. K. Adhikari and H. B. Goyal, Renewable Sustainable Energy Rev., 2009, 13, 156–167 CrossRef CAS.
- M. F. Demirbas and M. Balat, J. Sci. Ind. Res., 2007, 66, 797–804 CAS.
- R. D. Cortright, R. R. Davda and J. A. Dumesic, Nature, 2002, 418, 964–967 CrossRef CAS.
- G. W. Huber, J. N. Chheda, C. J. Barrett and J. A. Dumesic, Science, 2005, 308, 1446–1450 CrossRef CAS.
- T. P. Vispute and G. W. Huber, Green Chem., 2009, 11, 1433–1445 RSC.
- R. Xing, A. V. Subrahmanyam, H. Olcay, W. Qi, G. P. van Walsum, H. Pendse and G. W. Huber, Green Chem., 2010, 12, 1933–1946 RSC.
- N. Li and G. W. Huber, J. Catal., 2010, 270, 48–59 CrossRef CAS.
- N. Li, G. A. Tompsett, T. Y. Zhang, J. Shi, C. E. Wyman and G. W. Huber, Green Chem., 2011, 13, 91–101 RSC.
- R. Luque, J. H. Clark, K. Yoshida and P. L. Gai, Chem. Commun., 2009, 5305–5307 RSC.
- J. P. Diebold and J. W. Scahill, ACS Symp. Ser., 1988, 376, 264–276 CrossRef CAS.
- J. Adam, E. Antonakou, A. Lappas, M. Stocker, M. H. Nilsen, A. Bouzga, J. E. Hustad and G. Oye, Microporous Mesoporous Mater., 2006, 96, 93–101 CrossRef CAS.
- E. Antonakou, A. Lappas, M. H. Nilsen, A. Bouzga and M. Stocker, Fuel, 2006, 85, 2202–2212 CrossRef CAS.
- E. F. Iliopoulou, E. V. Antonakou, S. A. Karakoulia, I. A. Vasalos, A. A. Lappas and K. S. Triantafyllidis, Chem. Eng. J., 2007, 134, 51–57 CrossRef CAS.
- E. Putun, B. B. Uzun and A. E. Putun, Energy Fuels, 2009, 23, 2248–2258 CrossRef CAS.
- C. N. Hamelinck, A. P. C. Faaij, H. den Uil and H. Boerrigter, Energy, 2004, 29, 1743–1771 CrossRef CAS.
- M. J. A. Tijmensen, A. P. C. Faaij, C. N. Hamelinck and M. R. M. van Hardeveld, Biomass Bioenergy, 2002, 23, 129–152 CrossRef CAS.
-
D. L. Klass, Fuels and Chemicals, Academic Press, San Diego, CA, 1998 Search PubMed.
- B. Donnis, R. G. Egeberg, P. Blom and K. G. Knudsen, Top. Catal., 2009, 52, 229–240 CrossRef CAS.
- D. C. Elliott, Energy Fuels, 2007, 21, 1792–1815 CrossRef CAS.
- J. Wildschut, M. Iqbal, F. H. Mahfud, I. M. Cabrera, R. H. Venderbosch and H. J. Heeres, Energy Environ. Sci., 2010, 3, 962–970 CAS.
- J. D. Adjaye and N. N. Bakhshi, Fuel Process. Technol., 1995, 45, 161–183 CrossRef CAS.
- J. D. Adjaye and N. N. Bakhshi, Fuel Process. Technol., 1995, 45, 185–202 CrossRef CAS.
- B. Valle, A. G. Gayubo, A. Alonso, A. T. Aguayo and J. Bilbao, Appl. Catal., B, 2010, 100, 318–327 CrossRef CAS.
- B. Valle, A. G. Gayubo, A. T. Aguayo, M. Olazar and J. Bilbao, Energy Fuels, 2010, 24, 2060–2070 CrossRef CAS.
- A. G. Gayubo, B. Valle, A. T. Aguayo, M. Olazar and J. Bilbao, Ind. Eng. Chem. Res., 2010, 49, 123–131 CrossRef CAS.
- A. G. Gayubo, A. T. Aguayo, A. Atutxa, B. Valle and J. Bilbao, J. Chem. Technol. Biotechnol., 2005, 80, 1244–1251 CrossRef CAS.
- T. Q. Hoang, X. L. Zhu, L. L. Lobban, D. E. Resasco and R. G. Mallinson, Catal. Commun., 2010, 11, 977–981 CrossRef CAS.
- T. Q. Hoang, X. L. Zhu, T. Danuthai, L. L. Lobban, D. E. Resasco and R. G. Mallinson, Energy Fuels, 2010, 24, 3804–3809 CrossRef CAS.
- T. Danuthai, S. Jongpatiwut, T. Rirksomboon, S. Osuwan and D. E. Resasco, Appl. Catal., A, 2009, 361, 99–105 CrossRef CAS.
- A. Ausavasukhi, T. Sooknoi and D. E. Resasco, J. Catal., 2009, 268, 68–78 CrossRef CAS.
- A. Corma, G. W. Huber, L. Sauvanaud and P. O'Connor, J. Catal., 2007, 247, 307–327 CrossRef CAS.
- T. R. Carlson, T. R. Vispute and G. W. Huber, ChemSusChem, 2008, 1, 397–400 CrossRef CAS.
- T. R. Carlson, Y. T. Cheng, J. H. Jae and G. W. Huber, Energy Environ. Sci., 2011, 4, 145–161 CAS.
- J. H. Jae, G. A. Tompsett, Y. C. Lin, T. R. Carlson, J. C. Shen, T. Y. Zhang, B. Yang, C. E. Wyman, W. C. Conner and G. W. Huber, Energy Environ. Sci., 2010, 3, 358–365 CAS.
- F. A. Agblevor, O. Mante, N. Abdoulmoumine and R. McClung, Energy Fuels, 2010, 24, 4087–4089 CrossRef CAS.
- A. A. Lappas, M. C. Samolada, D. K. Iatridis, S. S. Voutetakis and I. A. Vasalos, Fuel, 2002, 81, 2087–2095 CrossRef CAS.
- F. A. Agblevor, S. Beis, O. Mante and N. Abdoulmoumine, Ind. Eng. Chem. Res., 2010, 49, 3533–3538 CrossRef CAS.
- H. Y. Zhang, R. Xiao, H. Huang and G. Xiao, Bioresour. Technol., 2009, 100, 1428–1434 CrossRef CAS.
- H. Y. Zhang, R. Xiao, D. H. Wang, Z. P. Zhong, M. Song, Q. W. Pan and G. Y. He, Energy Fuels, 2009, 23, 6199–6206 CrossRef CAS.
- A. Aho, N. Kumar, K. Eranen, T. Salmi, M. Hupa and D. Y. Murzin, Process Saf. Environ. Prot., 2007, 85, 473–480 CrossRef.
- R. Luque, L. Herrero-Davila, J. M. Campelo, J. H. Clark, J. M. Hidalgo, D. Luna, J. M. Marinas and A. A. Romero, Energy Environ. Sci., 2008, 1, 542–564 CAS.
- N. Y. Chen, J. T. F. Degnan and L. R. Koenig, Chem. Tech., 1986, 16, 506 CAS.
- H. Y. Zhang, Y. T. Cheng, T. P. Vispute, R. Xiao and G. W. Huber, Energy Environ. Sci., 2011, 4, 2297–2307 CAS.
- T. P. Vispute, H. Y. Zhang, A. Sanna, R. Xiao and G. W. Huber, Science, 2010, 330, 1222–1227 CrossRef CAS.
- U. Mentzel, A. Rovik and C. Christensen, Catal. Lett., 2009, 127, 44–48 CrossRef CAS.
- A. Demirbas, Energy Sources, Part A, 2009, 31, 1056–1062 CrossRef CAS.
- M. Kaarsholm, B. Rafii, F. Joensen, R. Cenni, J. Chaouki and G. S. Patience, Ind. Eng. Chem. Res., 2010, 49, 29–38 CrossRef CAS.
- J. M. Cho, J. M. Davis and G. W. Huber, ChemSusChem, 2010, 3, 1162–1165 CrossRef CAS.
- Y. C. Lin, J. Cho, G. A. Tompsett, P. R. Westmoreland and G. W. Huber, J. Phys. Chem. C, 2009, 113, 20097–20107 CAS.
- P. J. Dauenhauer, J. L. Colby, C. M. Balonek, W. J. Suszynski and L. D. Schmidt, Green Chem., 2009, 11, 1555–1561 RSC.
- P. R. Patwardhan, J. A. Satrio, R. C. Brown and B. H. Shanks, J. Anal. Appl. Pyrolysis, 2009, 86, 323–330 CrossRef CAS.
- T. R. Carlson, J. Jae, Y. C. Lin, G. A. Tompsett and G. W. Huber, J. Catal., 2010, 270, 110–124 CrossRef CAS.
- I. M. Dahl and S. Kolboe, J. Catal., 1994, 149, 458–464 CrossRef CAS.
- I. M. Dahl and S. Kolboe, J. Catal., 1996, 161, 304–309 CrossRef CAS.
- M. Stocker, Microporous Mesoporous
Mater., 1999, 29, 3–48 CrossRef CAS.
- J. F. Haw, W. G. Song, D. M. Marcus and J. B. Nicholas, Acc. Chem. Res., 2003, 36, 317–326 CrossRef CAS.
- D. M. McCann, D. Lesthaeghe, P. W. Kletnieks, D. R. Guenther, M. J. Hayman, V. Van Speybroeck, M. Waroquier and J. F. Haw, Angew. Chem., Int. Ed., 2008, 47, 5179–5182 CrossRef CAS.
- M. Bjorgen, S. Svelle, F. Joensen, J. Nerlov, S. Kolboe, F. Bonino, L. Palumbo, S. Bordiga and U. Olsbye, J. Catal., 2007, 249, 195–207 CrossRef CAS.
- M. Bjorgen, S. Akyalcin, U. Olsbye, S. Benard, S. Kolboe and S. Svelle, J. Catal., 2010, 275, 170–180 CrossRef CAS.
- C. M. Wang, Y. D. Wang, H. X. Lie, Z. K. Xie and Z. P. Liu, J. Catal., 2010, 271, 386–391 CrossRef CAS.
- A. G. Gayubo, B. Valle, A. T. Aguayo, M. Olazar and J. Bilbao, Energy Fuels, 2009, 23, 4129–4136 CrossRef CAS.
- R. J. Evans and T. Milne, ACS Symp. Ser., 1988, 376, 311–327 CrossRef CAS.
- T. R. Carlson, J. Jae and G. W. Huber, ChemCatChem, 2009, 1, 107–110 CrossRef CAS.
- From http://www.icis.com/v2/magazine/home.aspx/.
|
This journal is © The Royal Society of Chemistry 2012 |
Click here to see how this site uses Cookies. View our privacy policy here.