Selective synthesis of dimethyl carbonate from urea and methanol over Fe2O3/HMCM-49†
Received
13th June 2011
, Accepted 11th October 2011
First published on 2nd November 2011
Abstract
The supported material Fe2O3/HMCM-49 was prepared and characterized by XRD, FT-IR and NH3-TPD. This material was tested for the catalytic synthesis of dimethyl carbonate (DMC) from methanol and urea in a batch reactor without any specially designed equipment. The results showed that Fe2O3/HMCM-49 is an effective catalyst, exhibiting 34.2% conversion of urea and 97.4% selectivity to DMC at 453 K. Furthermore, the catalyst can be recovered due to its heterogeneous nature and reused three times without a significant loss in its activity and the reaction mechanism via mutual activation of urea and methanol was proposed.
1. Introduction
Dimethyl carbonate (DMC), as an environmentally benign building block, is becoming increasingly important in the chemical industry.1,2 It is mainly used as a carbonylating and methylating reagent substituting dimethyl sulfate and phosgene, which are corrosive and toxic agents.3 In addition, it is also a promising octane enhancer.4 Currently, DMC synthesis techniques internationally reported mainly include phosgenation of methanol, oxidative carbonylation of methanol5,6 and transesterification of cyclic carbonate with methanol.7 Each of the aforementioned processes has commercial or technical and environmental disadvantages. Phosgenation of methanol has been phased out because of the extreme toxicity of phosgene. The oxidative carbonylation of methanol suffers from low production rate, need for corrosion resistant reactors, toxicity and potential explosion of carbon monoxide.8,9 Besides, major disadvantages of the transesterification method are high energy consumption, high investment and production costs due to the requirement of the intermediate separation.10 Recently, carbon dioxide, a readily available, inexpensive and environmentally acceptable material, has widely been investigated as raw material for DMC synthesis.11–18 But, the direct synthesis of DMC from methanol and carbon dioxide is still unsatisfactory due to the difficulty in activation of carbon dioxide, deactivation of the catalyst and thermodynamic limitation.
The alcoholysis of urea for producing DMC is one kind of new process developed, which is widely considered as indirect synthesis of DMC from CO2 and methanol since the released NH3 can be recycled to produce urea by reaction with CO2. There are several advantages, such as abundant resource and low cost of urea and methanol, no formation of ternary azeotrope of methanol–water–DMC resulting in easier separation of DMC. Several researchers reported the synthesis of DMC from methanol and urea in the presence of organotin, simple basic compounds such as K2CO3, CH3ONa, CaO, MgO, etc.,19–22 but the DMC yield in these systems is very low. However, in the research work reported by Sun and co-workers,23 29.0% yield was attained by using a ZnO catalyst. Sun et al.24 reported that polyphosphoric acid was an effective catalyst in the DMC synthesis by the alcoholysis of urea with 67.4% yield of DMC. The latter suffers from low selectivity due to the formation of several byproducts such as N-methyl urea, methyl carbamate, N-methyl methyl carbamate and it needs a corrosion resistant reactor. Yang et al.25 have reported the synthesis of DMC from urea and methanol catalyzed by metallic compounds at atmospheric pressure. 29% yield was obtained, but this method also has disadvantages such as low selectivity to DMC, complicated procedure and the difficulty in the separation between the product and the catalyst. Very recently, mixed oxides from hydrotalcite-like compounds,26Zn/Fe mixed oxide27 and lanthanum compounds28 were found to have high activity for the synthesis of DMC from methyl carbamate and methanol. The low selectivity to DMC is also the main problem in these processes. Zhao et al.29 have further reported the catalytic nature of ZnO used as the precursor for homogeneous catalytic synthesis of DMC from urea and methanol. Our group has disclosed highly selective synthesis of DMC from urea and methanol catalyzed by metal-chloride ionic liquids in a homogeneous system.30Zinc-chloride ionic liquids represented high selectivity and activity for this reaction. As our continuous research work, here, we wish to report effective synthesis of DMC over a supported catalyst Fe2O3/HMCM-49 in a batch reactor. As compared with the reported literature, this report on highly selective synthesis of DMC by heterogeneous catalysis is very rare up to now.
2. Experimental
2.1 Materials
Chemicals used in this study include methanol (A. R.) and ethanol (A. R.), which were obtained from Tianjin Fuchen Chemical Reagent Company. Iron nitrate (A. R.) was provided by Tianjin Guangfu Institute of Fine Chemicals and urea (A. R.) was obtained from Shenyang Third Reagent Company. All the chemicals were commercial reagents with purity greater than 99 mass percent. MCM-49 zeolite (Si/Al = 22) was provided by Shanghai Novel Chemical Technology Co., Ltd. The standard DMC sample (≥99.0%) was purchased from Sinopharm Chemical Reagent Co., Ltd. (China).
2.2 Preparation and characterization of the catalyst
HMCM-49 was prepared by the following procedure: 3.0 g of MCM-49 was added to 150 mL of 2.0 mol L−1NH4NO3 aqueous solution. The resulting mixture was heated to 353 K in a water bath and stirred at this temperature for 12 h. After cooling to room temperature, the mixture was filtered under reduced pressure, affording a white solid. The solid was then dried at 373 K for 5 h after washing with deionized water, followed by calcination at 823 K for 3 h in an oven. The above procedure was repeated two times. At last a white HMCM-49 was obtained.
A typical procedure used for preparing Fe2O3/HMCM-49 was as follows: 1.0 g HMCM-49 was impregnated with 5.8% Fe(NO3)3 solution in ethanol and stirred at room temperature for 12 h. Thereafter, the resulting mixture was filtered, affording a solid material and the solid was dried at 373 K for 3 h after washing with deionized water, followed by calcination at 773 K for 2 h. Fe2O3/HMCM-49 was obtained after cooling to room temperature.
The XRD of the samples was performed on a Bruker-D8 Advance X-ray diffractometer with Cu Kα radiation (40 kV and 36 mA). FT-IR spectra of the samples were recorded on a vertex 80 infrared spectrometer (Brucker Company). The loading of Fe2O3 on HMCM-49 was determined by 7500CE ICP-MS (Agilent Company).
2.3
Catalytic tests
The catalytic reaction was conducted in a stainless steel 0.5 L autoclave with an electric heater and a mechanical stirrer. In a typical procedure, 68 mL (1.68 mol) of anhydrate methanol, 0.632 g (0.0105 mol) of urea and 0.3 g of the catalyst (Fe2O3/HMCM-49) were charged into the reactor in turns. After purging three times with N2 gas, the reactor was heated to 453 K with a stirring rate of 500 rpm and the reaction was carried out for 8 h. At the end of the reaction, the mixture solution was filtered to remove the catalyst and the filtrate was analyzed by GC and GC-MS.
3. Results and discussion
3.1
Catalyst characterization
Fig. 1 illustrates XRD patterns of HMCM-49 and Fe2O3/HMCM-49 as compared with that of MCM-49. The materials HMCM-49 and Fe2O3/HMCM-49 basically retain the original structure of MCM-49, although addition of iron has a negative effect on the crystalline structure. Moreover, no diffraction peak corresponding to crystalline iron oxides could be observed in the XRD pattern of Fe2O3/HMCM-49. Possibly, the particle size of iron oxides in the sample was too small to be detected by X-ray diffraction. When the loading of iron onto HMCM-49 was increased from 0.69% to 5.04%, two characterization peaks at 33.5° and 35.3° corresponding to highest peaks of α-Fe2O3 (hematite form) were observed in the XRD pattern (not listed here), which suggested that iron has been supported on the materials in the α-Fe2O3 style. Furthermore, the brown color of the obtained solid materials and chemical analysis of the supported materials by ICP-MS verified the existence of iron species in the sample.
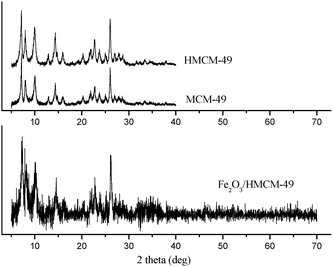 |
| Fig. 1
XRD patterns of MCM-49, HMCM-49 and Fe2O3/HMCM-49. | |
TPD profiles of NH3 adsorbed on MCM-49, HMCM-49, SBA-15, ZSM-5, HY and SO42−/ZrO2 were recorded (Fig. 2). Two broad desorption peaks were observed on MCM-49 and HMCM-49 at 523 K and 639 K, which represent the weak and strong acid centers on the molecular sieves, respectively. However, the two peaks on HMCM-49 are remarkably stronger than that on MCM-49, suggesting that the exchange of NH4+ with Na+ on MCM-49, that is, the preparation of HMCM-49 was successful. A very low desorption peak on SBA-15 was observed at 498 K, which implied that SBA-15 possesses much weaker acidity as compared with the two molecular sieves, MCM-49 and HMCM-49. Comparatively, ZSM-5 and HY zeolites possess stronger acidity than HMCM-49 does and a very weak desorption peak was found on the solid superacid SO42−/ZrO2 although it usually possesses strong acidity.
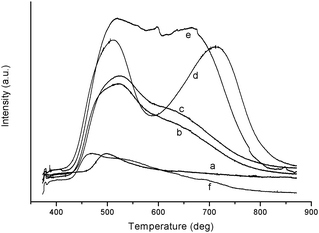 |
| Fig. 2
NH3-TPD profiles of SBA-15 (a), MCM-49 (b), HMCM-49 (c), ZSM-5 (d), HY (e) and SO42−/ZrO2 (f). | |
3.2
Catalytic performance of various catalysts
The alcoholysis of urea for producing DMC over various catalytic materials MCM-49, HMCM-49, SBA-15, α-Fe2O3, Fe2O3/SBA-15, Fe2O3/MCM-49, Fe2O3/HMCM-49, Fe2O3/HY, Fe2O3/HZSM-5 and Fe2O3/SO42−–ZrO2 was tested and the results are shown in Table 1. In blank reactions, the pure microporous molecular sieves, MCM-49, HMCM-49 and α-Fe2O3, exhibited very low activity (entries 2–4), while pure mesoporous SBA-15 was completely inactive for the reaction (entry 1). In contrast, the Fe2O3 supported materials Fe2O3/SBA-15, Fe2O3/MCM-49 and Fe2O3/HMCM-49 were found to be more active than the above simple catalysts (entries 5–7). It was noted that Fe2O3/HMCM-49 exhibited the highest activity for DMC synthesis from methanol and urea with 20.5% yield of DMC and about 98.0% selectivity, as compared with Fe2O3/MCM-49 and Fe2O3/SBA-15. The differences in the catalytic activity between the simple and supported catalytic materials might be explained on the basis of the highly dispersed Fe2O3 on porous materials, also the acidity on the surface of the materials plays a key role in the activation of urea and methanol. For example, the activity order of these catalysts is: Fe2O3/HMCM-49 > Fe2O3/MCM-49 > Fe2O3/SBA-15 for supported materials and HMCM-49 > MCM-49 > SBA-15 for simple ones, which is consistent with their activity order. In order to explore the role of the surface acidity, other iron supported catalysts Fe2O3/HY, Fe2O3/HZSM-5 and Fe2O3/SO42−–ZrO2 with stronger acidity than Fe2O3/HMCM-49 were tested and they exhibited very low activity for the reaction (entries 8–10). This result suggested that strong acidity on the material surface is disadvantageous for the synthetic reaction, which may cause the strong interaction with NH2 in the urea molecule to restrain its further reaction. Therefore, the catalyst with medium acidity could effectively activate urea and methanol and interact with NH3 gas released in the reaction to promote shift of the reaction equilibrium to the direction producing DMC, which is validated in the following sections.
Table 1
Catalytic performance over various catalysts
Entry |
Catalyst
|
Yield (%) |
1 |
SBA-15 |
0 |
2 |
MCM-49
|
3.7 |
3 |
HMCM-49
|
4.1 |
4 |
Fe2O3 |
2.4 |
5 |
Fe2O3/SBA-15 |
10.0 |
6 |
Fe2O3/MCM-49 |
14.7 |
7 |
Fe2O3/HMCM-49 |
20.5 |
8 |
Fe2O3/HY |
7.0 |
9 |
Fe2O3/HZSM-5 |
3.2 |
10 |
Fe2O3/SO42−/ZrO2 |
2.4 |
3.3 Effect of reaction conditions
3.3.1 Effect of the catalyst dose.
The effect of catalyst (Fe2O3/HMCM-49) dose on the yield and selectivity to DMC was studied by varying its amount from 0.1 to 1.0 g at 453 K with 0.69% loading of iron, as shown in Fig. 3. The yield was increased from 14.5% to 33.4% with increase in the catalyst amount from 0.1 to 0.3 g, which should be due to increase in the amount of acidic sites. Thereafter, the yield declined rapidly as the catalyst amount continuously increased. The excess amount of the catalyst could cause the reactants or the product DMC to further convert into some byproducts, i.e. N-methyl urea, N-methyl methyl carbamate. As a result, the selectivity to DMC inevitably decreased, leading to the sharp fall of the yield.
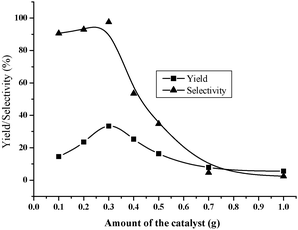 |
| Fig. 3 Effect of the catalyst dose. Reaction conditions: methanol/urea ratio 160 : 1; reaction temperature 453 K; time 8 h; loading of Fe 0.69%. | |
3.3.2 Effect of reaction temperature.
The effect of reaction temperature on DMC yield is shown in Fig. 4. It could be seen that the DMC yield increased as the temperature increased in the range of 423–453 K, and then it decreased when the reaction temperature exceeded 453 K. Since the reaction is an endothermic reaction, it is greatly advantageous for the synthesis of DMC from urea and methanol at a higher reaction temperature from a viewpoint of thermodynamics. In the viewpoint of kinetics, raise of the reaction temperature can accelerate the reaction and shorten the time to approach the equilibrium. Therefore, the yield increased with rising temperature in the range from 423 to 453 K. Nevertheless, it was known that urea begins to decompose into NH3 and isocyanic acid HNCO at a temperature of 408 K under ambient pressure. The formation of active species HNCO is advantageous for the synthesis of DMC as reported by Wang et al.31 At the same time, the rapid decomposition of urea at high temperature can lead to reaction of HNCO with urea or DMC to generate byproducts. Thus, the rapid decline in the DMC yield observed over 453 K was due to the sharp decline in selectivity.
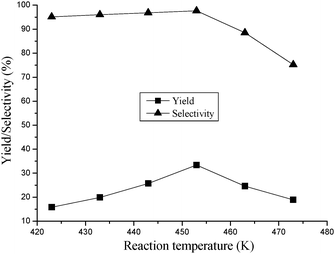 |
| Fig. 4 The effect of reaction temperature on DMC yield. Reaction conditions: methanol/urea ratio 160 : 1; reaction time 8 h; amount of catalyst 0.3 g; loading of Fe 0.69%. | |
3.4 Reusability of the catalyst
In order to further evaluate the performance of the catalyst, recovery and reuse of the catalyst were explored. At the end of the reaction, the reaction mixture was centrifuged and the catalyst was separated. After being calcined at 773 K for 2 h it was reused in the next run under the same conditions. The results shown in Table 2 indicate that the activity of the catalyst was almost not affected even at the fourth run, but the selectivity to DMC was greatly dependent on the number of times it was reused. The selectivity remarkably declined after the catalyst was reused three times, which may be ascribed to iron species agglomeration of small particles on the surface of the catalyst. This was affirmed by the XRD patterns of fresh and reused Fe2O3/HMCM-49 (Fig. 6). In the XRD pattern the characteristic peaks of α-Fe2O3 were obviously observed for the catalysts after used two or three times, verifying iron species agglomeration on the surface. It is the bulk iron oxide on the surface that causes by-reactions to occur due to the activity of Fe(III) on the compounds containing nitrogen in the molecules, resulting in the decrease of the selectivity. In addition, the catalyst used for the second time without calcination showed low activity for the DMC synthesis, which was likely ascribed to Fe2O3/HMCM-49 absorbing NH3 produced in the reaction to form Fe2O3/NH4MCM-49. The FT-IR spectrum of the used catalyst verified the existence of NH4+ (Fig. 7). In the spectrum, the absorption bands observed at 2958.1 and 2858.9 cm−1 were attributed to the stretching vibrations of the N–H bond and the bands at 1687.3 and 1485.6 cm−1 were likely due to the bending vibration of N–H and N+–H bonds. This result also suggested that the catalyst can absorb the released NH3 to shift the reaction equilibrium to the direction producing DMC.
Times |
Conversion (%) |
Selectivity (%) |
Yield (%) |
Reused once without calcination.
|
1 |
34.2 |
97.6 |
33.4 |
2 |
33.6 |
90.2 |
30.3 |
3 |
27.8 |
81.9 |
22.8 |
4 |
30.0 |
42.6 |
12.8 |
2a |
14.5 |
93.0 |
13.5 |
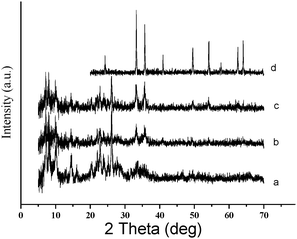 |
| Fig. 6
XRD patterns of reused catalysts (a) fresh; (b) after first reuse; (c) after second reuse; (d) α-Fe2O3. | |
In addition, the leaching of Fe2O3/HMCM-49 was investigated after the reaction. The Fe3+ content in the reaction mixture was not detected, which implied that the Fe3+ content in the reaction mixture is lower than 10−10 according to ICP-MS precision although the iron species agglomeration on the surface was found for the reused catalyst. This confirmed that the catalytic process is really heterogeneous.
3.5 Reaction mechanism
It was known that the complexes were easily formed by urea molecules coordinating to metal ions through the oxygen as well as the nitrogen atoms.32,33 On the basis of these facts, as well as the experimental results obtained in this case, the reaction mechanism of DMC synthesis from urea and methanol catalyzed by Fe2O3/HMCM-49 was proposed and is shown in Scheme 1. This reactive procedure involves the mutual activation of urea by Fe [O] and H+ on the catalyst surface to form activated intermediate I and the activation of methanol by Fe [O] to generate methoxide anion CH3O−. Then, methoxide anion CH3O− attacks the positively charged carbonyl carbon in the molecule of the intermediate I to generate the intermediate II, which is methyl carbamate coordinated to Fe [O] and H+. Finally, the activated methyl carbamate reacts with another CH3O− to produce the target product DMC and release Fe [O] and H+ realizing the catalytic cycle. In this mechanism, it was worthy to note that the two activated particles, CH3O− and activated methyl carbamate, in the reaction, possess high reactivity to form DMC, which may make the selectivity of DMC reach too high due to the fast rate of the second step of the synthesis reaction.
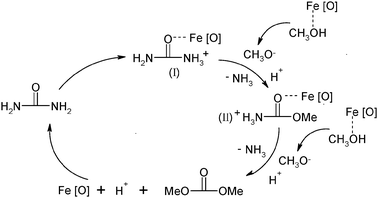 |
| Scheme 1 Reaction mechanism. | |
4. Conclusions
The prepared Fe2O3/HMCM-49 was found to be an effective catalyst for the DMC synthesis from urea and methanol, exhibiting a high conversion of 34.2% with a TON of 284.1 mol per molFe and a selectivity of 97.4%. This high catalytic activity for the reaction was verified to be dependent on the medium acidity of the surface and highly dispersed Fe2O3 on the surface of the catalyst. The catalyst was easily recovered and reused. The catalytic activity of the reused catalyst was almost not affected even at the fourth run, but the selectivity to DMC was greatly dependent on the number of times it was reused. The investigation showed that this decline in the selectivity may be ascribed to iron species agglomeration of small particles on the surface of the material. Besides, on the basis of the previous report in literature and the experimental results obtained in this case the mechanism of the synthesis reaction via the mutual activation of urea by Fe [O] and H+ was proposed.
Acknowledgements
We greatly acknowledge the financial support of this work by the Natural Science Foundation of Heilongjiang Province, P. R. China (No. ZD200820-01, B201119 and B200814).
Notes and references
- P. Tundo, Pure Appl. Chem., 2001, 73, 1117 CrossRef CAS.
- D. Delledonne, F. Rivetti and U. Romano, Appl. Catal., A, 2001, 221, 241 CrossRef CAS.
- T. Pietro and S. Maurizio, Acc. Chem. Res., 2002, 35, 706 CrossRef.
- U. Romano, R. Tesel and M. M. Maurl, Ind. Eng. Chem. Prod. Res. Dev., 1980, 19, 396 CrossRef CAS.
- A. Behr, Angew. Chem., Int. Ed. Engl., 1988, 27, 661 CrossRef.
- T. Matsuzaki and A. Nakamura, Catal. Surv. Jpn., 1997, 1, 77 CrossRef CAS.
- H. Cui, T. Wang, F. Wang, C. Gu, P. Wang and Y. Dai, J. Supercrit. Fluids, 2004, 30, 63 CrossRef CAS.
- Y. J. Wang, X. Q. Zhao and B. G. Yuan, Appl. Catal., A, 1998, 171, 255 CrossRef CAS.
- Y. Yamamoto, T. Matsuzaki, S. Tanaka, K. Nishihira, K. Ohdan, A. Nakamura and Y. Okamoto, J. Chem. Soc., Faraday Trans., 1997, 93, 3721 RSC.
- S. G. Zhang and Y. S. Luo, Chem. React. Eng. Technol., 1991, 7, 10 CAS.
- S. Fang and K. Fujimoto, Appl. Catal., A, 1996, 142, L1 CrossRef CAS.
- S. Fujita, M. Bhalchandra, Y. Ikushima and M. Arai, Green Chem., 2001, 3, 87 RSC.
- Q. Cai, C. Jin, B. Lu, H. Tangbo and Y. Shan, Catal. Lett., 2005, 103, 225 CrossRef CAS.
- K. T. Jung and A. T. Bell, J. Catal., 2001, 204, 339 CrossRef CAS.
- Q. Cai, L. Zhang, Y. Shan and M. He, Chin. J. Chem., 2004, 22, 422 CrossRef CAS.
- M. Aresta, A. Dibenedetto, C. Pastore, A. Angelini, B. Aresta and I. Pápai, J. Catal., 2010, 269, 44 CrossRef CAS.
- J.-C. Choi, L.-N. He, H. Yasuda and T. Sakakura,
et al.
, Green Chem., 2002, 4, 230 RSC.
- Y. Yoshida, Y. Arai, S. Kado, K. Kunimori and K. Tomishige, Catal. Today, 2006, 115, 95 CrossRef CAS.
-
C. Tsurahide and T. Tkaaki, US 5,534,649, 1994 Search PubMed.
-
R. Y. Saleh and R. C. Michaelson, US 5,565,603, 1996 Search PubMed.
-
R. J. Yong, US 5,902,894, 1999 Search PubMed.
- M. Wang, H. Wang, N. Zhao, W. Wei and Y. Sun, Catal. Commun., 2006, 7, 6 CrossRef CAS.
- M. Wang, N. Zhao, W. Wei and Y. Sun, Ind. Eng. Chem. Res., 2005, 44, 7596 CrossRef CAS.
- J. Sun, B. Yang, X. Wang, D. Wang and H. Lin, J. Mol. Catal. A: Chem., 2005, 239, 82 CrossRef CAS.
- B. Yang, D. Wang, H. Lin, J. Sun and X. Wang, Catal. Commun., 2006, 7, 472 CrossRef CAS.
- D. Wang, X. Zhang, Y. Gao, F. Xiao, W. Wei and Y. Sun, J. Phys. Chem. Solids, 2010, 71, 427 CrossRef CAS.
- D. Wang, X. Zhang, W. Zhao, W. Peng, N. Zhao, F. Xiao, W. Wei and Y. Sun, Catal. Commun., 2010, 11, 430 CrossRef CAS.
- D. Wang, X. Zhang, Y. Gao, F. Xiao, W. Wei and Y. Sun, Fuel Process. Technol., 2010, 91, 1081 CrossRef CAS.
- W. Zhao, W. Peng, D. Wang, N. Zhao, J. Li, F. Xiao, W. Wei and Y. Sun, Catal. Commun., 2009, 10, 655 CrossRef CAS.
- H. Wang, B. Lu, X. Wang, J. Zhang and Q. Cai, Fuel Process. Technol., 2009, 90, 1198 CrossRef CAS.
- H. Wang, M. Wang, W. Zhao, W. Wei and Y. Sun, React. Kinet., Mech. Catal., 2010, 99, 381 CAS.
- P. Vaughan and J. Donohue, Acta Crystallogr., 1952, 5, 530 CrossRef CAS.
- W. D. Kumler and G. M. Fohlen, J. Am. Chem. Soc., 1942, 64, 1944 CrossRef CAS.
Footnote |
† Electronic supplementary information (ESI) available. See DOI: 10.1039/c1cy00216c |
|
This journal is © The Royal Society of Chemistry 2012 |
Click here to see how this site uses Cookies. View our privacy policy here.