DOI:
10.1039/C1RA00387A
(Paper)
RSC Adv., 2011,
1, 1287-1293
Hydrothermal self-assembly of hierarchical cobalt hyperbranches by a sodium tartrate-assisted route
Received
30th June 2011
, Accepted 11th August 2011
First published on 23rd September 2011
Abstract
Three-dimensional (3D) hierarchical cobalt (Co) hyperbranches are synthesized by a sodium tartrate-assisted hydrothermal self-assembly route. The route includes the fabrication of the Co hyperbranches in a solution of cobalt chloride (CoCl2·6H2O) and sodium hydroxide (NaOH) at 110 °C for 24 h using sodium tartrate (Na2C4H4O6·2H2O) as the complex reagent and sodium hypophosphite (NaH2PO2·H2O) as the reducing agent. Each Co hyperbranch is 50–100 μm in length and consists of a main branch with several secondary branches and leaves. The adjustments of the molar ratio of Na2C4H4O6 to CoCl2 and the concentration of NaOH in the solution lead to the formation of the Co products with different morphologies. A possible growth mechanism for the Co hyperbranches is proposed based on the characterization results of X-ray diffraction and scanning electron microscopy. The magnetic hysteresis loops at room temperature of the resulting Co products with different morphologies show ferromagnetic characteristics with high dependence on their sizes and morphologies. An increased coercivity (Hc) of 231 Oe and a reduced saturation magnetization (Ms) of 152 emu/g are observed in the Co hyperbranches compared to their bulk counterpart. This relatively simple, efficient, and morphologically controllable route can be applied to the synthesis of complex 3D micro/nanoarchitectures of other materials.
Introduction
Self-assembly of inorganic building blocks generally yields collective physical properties, depending on their sizes, spacing, and high-order structures.1–4 The study of crystal growth kinetics is tightly related to the creation of inorganic building blocks and their ordered self-assemblies.5 As a result, considerable research effort has been paid in the recent years to the synthesis of materials with hierarchical architectures self-assembled by building blocks, both for technological applications in optoelectronic, magnetoelectronic, and biomedical fields and for scientific understanding of crystal growth kinetics.6–26 A number of wet chemical methods have been employed for the fabrication of hierarchical architectures based on different driving mechanisms, including surface tension, capillary effects, electromagnetic forces, and hydrophobic interactions.27–31 Among them, the hydrothermal method is considered as one of the most promising methods because: (1) it is relatively simple and inexpensive for large-scale preparation, and (2) it can alter the chemical properties of reactants so that some high-temperature and/or high-pressure required reactions can be enabled at relatively mild conditions.32 However, since the chemical reactions associated with the hydrothermal method is quite complicated and uncontrollable, exploring a rather simple, efficient, and controllable synthesis route for self-assembling hierarchical architectures has been a hot topic of research.
Cobalt (Co) micro/nanomaterials, as important magnetic materials, have received increasing attention because of their interesting physical (i.e., magnetic), chemical, and catalytic properties.33,34 Various Co building blocks and their multidimensional self-assemblies have been synthesized, and their properties and morphologies studied. These Co products include one-dimensional (1D) Co nanowires, nanobelts, nanorods, nanotubes, nanofibers, and chains;35–43 two-dimensional (2D) Co nanoplatelets, nanodisks, and superlattices;44,45 three-dimensional (3D) Co hollow spheres and snow-flake-like microcrystals;46,47 as well as other Co hierarchical architectures.48–53 In terms of synthesis method, for instance, the 1D Co nanowires and nanobelts were obtained by a surfactant and complex-assisted hydrothermal reduction route.36,37 The 2D Co nanodisks and their assemblies of ribbons were prepared by rapid decomposition of carbonylcobalt in the presence of trioctylphosphane and oleic acid41 and the 3D flower-like Co nanocrystals were acquired by a reduction of Co 2-hydroxy-4-(1-methytheptyl)benzophenone oxime (N530) complex.50
To date, although a variety of Co compounds with different morphologies have been reported using distinct synthesis methods,35–53 and while Co dendritic superstructures with ordered symmetrical branches have been fabricated by a hydrothermal reduction route with sodium citrate (C6H5O7Na3·2H2O) as the complex reagent,54 limited work has focused on the “morphology control” of self-assembled 3D hierarchical Co hyperbranches. In this paper, we report the synthesis of 3D hierarchical Co hyperbranches, each comprising a main branch with several secondary branches and leaves, using a simple, efficient, and morphologically controllable hydrothermal self-assembly route with sodium tartrate (Na2C4H4O6·2H2O) as the complex reagent and sodium hypophosphite (NaH2PO2·H2O) as the reducing agent. The effects of the reaction parameters on the morphologies of the resulting Co products are investigated, and a possible growth mechanism for the Co hyperbranches is proposed. The ferromagnetic characteristics at room temperature are reported and compared to those of the bulk. The applicability of the proposed route is also discussed.
Experimental details
All reagents used were commercially purchased with analytical pure and used without further purification. In a typical procedure, cobalt chloride (CoCl2·6H2O) of 0.238 g (1 mmol), sodium tartrate (Na2C4H4O6·2H2O) of 3.45 g (15 mmol), and sodium hydroxide (NaOH) of 3.2 g (80 mmol) were dissolved in distilled water of 40 ml, and the solution was constantly stirred for 15 min at room temperature. Sodium hypophosphite (NaH2PO2·H2O) of 0.85 g (8 mmol) was then added, and the solution was stirred steadily for another 30 min. A pink solution was obtained and transferred into a Teflon-lined stainless steel autoclave of volume 50 ml. The autoclave was sealed and maintained at 110 °C for 24 h before being cooled to room temperature naturally. The as-prepared product was filtered off, washed with distilled water and ethanol several times, and dried in a vacuum oven at 60 °C for 4 h. Control experiments were carried out by adjusting the amount of Na2C4H4O6·2H2O (0–40 mmol), the reaction temperature (110–170 °C), and the concentration of NaOH (1–7 M), respectively, while keeping the other reaction parameters unchanged.
The X-ray diffraction (XRD) data of the as-prepared products was obtained by a Rigaku D/max 2500pc X-ray diffractometer with Cu Kα radiation (λ = 1.54156 Å) at a scan rate of 0.04°/s. The morphology and size were investigated using scanning electron microscopy (SEM) with a JEOL-6490 scanning electron microscope operated at an acceleration voltage of 20 kV. The magnetic hysteresis loops were measured at room temperature using a Lakeshore 7600 vibrating sample magnetometer (VSM) at fields up to 20 kOe.
Results and discussion
Structure and morphology
The typical XRD pattern of the hierarchical Co hyperbranches prepared at 110 °C for 24 h is shown in Fig. 1. The XRD peaks can be indexed to the hcp-phase Co and are consistent with the standard card JCPDS No. 5-727 (space groupP63/mmc; a = 2.503 Å; c = 4.060 Å). The comparison of these peaks with the standard diffraction peaks find no other peaks regarding the impurities, such as CoCl2, NaOH, Na2C4H4O6, and other precursor compounds.
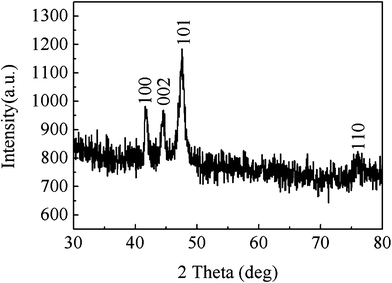 |
| Fig. 1 Typical XRD pattern of hierarchical Co hyperbranches prepared at 110 °C for 24 h. | |
Fig. 2(a) shows the low-magnification SEM image of the as-prepared Co hyperbranches obtained at 110 °C for 24 h. It is clear that our Co hyperbranches have high uniformity of 50–100 μm in length. Fig. 2(b) displays the high-magnification SEM image of Fig. 2(a). Each Co hyperbranch is composed of three parts: a main branch, several secondary branches, and many leaves. The secondary branches, with lengths of 20–30 μm, are closely connected to the main branch. The leaves, with different lengths and widths, grow on the secondary branches. The secondary branches located at the top of the main branch are thicker and longer than those located at the root of the main branch. Fig. 2(c) illustrates the enlarged SEM image of an individual Co hyperbranch based on the circular region marked on the high-magnification SEM image in Fig. 2(b). It is seen that the leaves have lengths ranging from 2 to 10 μm and widths of about 2 μm. In short, the morphologies and sizes as obtained from Fig. 2 confirm that our Co hyperbranches belong to a 3D hierarchical architecture.
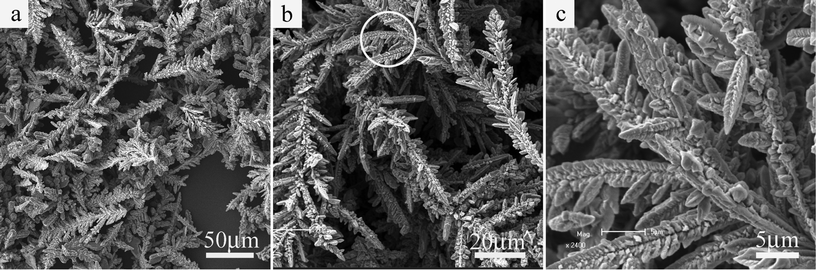 |
| Fig. 2 (a) Low-magnification and (b) high-magnification SEM images of the as-prepared Co hyperbranches obtained at 110 °C for 24 h. (c) Enlarged SEM image of an individual Co hyperbranch based on the circular region marked on Fig. 2(b). | |
Growth mechanism
We found that the molar ratio of the complex reagent Na2C4H4O6 to CoCl2 in the solution and the concentration of NaOH in the solution have the predominant effect on the morphology of the resulting Co products. When the molar ratio of Na2C4H4O6 to CoCl2 in the solution (represented by ST/Co2+ ratio) is adjusted, while the amount of CoCl2 to 1 mmol is fixed, Co products with obviously different morphologies are obtained. In the absence of Na2C4H4O6 (i.e., ST/Co2+ = 0), the Co products show an irregular aggregation of spherical particles, and each sphere has a diameter of about 10 μm, as shown in Fig. 3(a). When the ST/Co2+ ratio is increased to 5, 10, and 15, hierarchical Co hyperbranches are formed as the products corresponding to the ones shown in Fig. 3(b), 3(c), and 2, respectively. Further increasing the ST/Co2+ ratio, for example, to 30 does not produce hierarchical hyperbranches, but a chain-like morphology self-assembled by spheres with a diameter of about 5 μm are produced (Fig. 3(d)). The results reveal that the morphologies of the resulting Co products can be controlled by changing the ratio of ST/Co2+. As one of the most important ligands, Na2C4H4O6, which is capable of coordinating with Co2+ and Ni2+ ions to form the corresponding complex, has been used as the capping reagent in the fabrication of Co and Ni assemblies.48,55 In the solution, the complex Co(C4H2O6)2− is first produced in an excess amount of Na2C4H4O6, and the redox reaction then occurs during the hydrothermal reaction process. The redox reaction can be expressed as follows: | Co(C4H2O6)2− + H2PO2− + OH−→ Co + C4H4O62− + HPO32− | (1) |
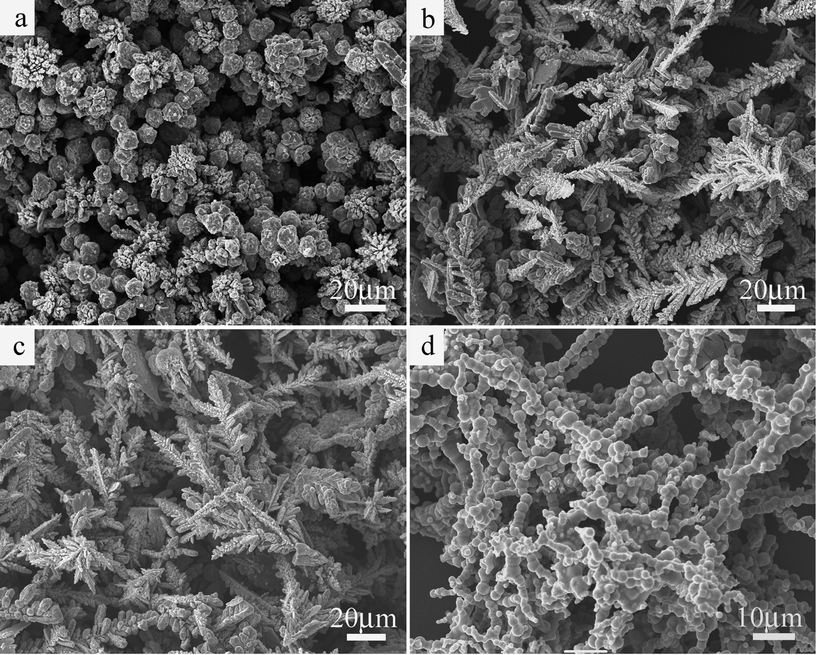 |
| Fig. 3
SEM images of Co products prepared using different molar ratios of Na2C4H4O6 to CoCl2 (represented by ST/Co2+ ratio) of (a) 0, (b) 5, (c) 10, and (d) 30. | |
Following eqn (1), it can describe the overall growth mechanism of the Co products in two stages: the initial formation of nuclei and the subsequent growth of the nuclei. In the absence of Na2C4H4O6, the concentration of free Co2+ ions in the solution of CoCl2 and NaOH is high enough so that almost all Co nuclei are reduced at the initial stage and almost no Co particles are available for subsequent nuclei growth. Accordingly, the nuclei aggregates become spheres, driven by magnetic dipolar interaction and minimization of surface energies according to the Gibbs–Thomson law.56 With the necessary increase in the amount of Na2C4H4O6, the concentration of free Co2+ ions is reduced so that fewer nuclei are produced at the initial stage and the Co particles available for the later nuclei growth stage are relatively high, resulting in a high growth rate. In the meantime, the Co particles are gradually reduced due to the complex function of Na2C4H4O6. This growth mechanism is kinetically favorable for growing branched architectures according to the well-known diffusion-limited aggregation (DLA) model.57 However, further increasing the amount of Na2C4H4O6 tends to lower the concentration of free Co2+ ions and hence the release rate of free Co2+ ions, leading to a reduction in nuclei formation and a decrease in nuclei growth rate. Hence, the chain-like architecture self-assembled by microspheres (Fig. 3(d)) forms as the product rather than the Co hyperbranches (Fig. 2, 3(b), and Fig. 3(c). The results suggest that the use of an excess amount of Na2C4H4O6 can incur a slower growth rate which, in turn, produces products with nearly spherical shape.58 It has been proposed that the complex reagent plays at least two roles in the formation of inorganic building blocks and assemblies.54 Firstly, the complex reagent can coordinate with metallic ions to form complexes, giving rise to a lower concentration of metallic ions in the solution and hence a lower reaction rate. In other words, the growth rate of the products can be adjusted by varying the amount of the complex reagent. Secondly, the preferential capping or stabilization by a complex reagent of some crystal faces brings about the kinetic control of the growth of different crystal faces and the further efficient control of the morphology of the final products.6,54,59–61 The SEM images in Fig. 2 and 3 indicate that the complex reagent of hierarchical Co hyperbranches plays a crucial role in both aspects.
In addition to the ST/Co2+ ratio, the concentration of NaOH and the reaction temperature have a significant effect on the morphologies of the resulting Co products. It is found that the hierarchical Co hyperbranches can only be obtained at a limited range of NaOH concentration of 2–5 M. At a lower NaOH concentration of 1 M, the Co products have a spherical morphology with limited Co hyperbranches, as shown in Fig. 4(a) and 4(b). Although 3D hierarchical Co hyperbranches are observed at a higher NaOH concentration of 6 M, as in Fig. 4(c) and 4(d), the products are physically assembled by “rods” rather than by “leaves”. This may be attributed to the accelerated growth rate caused by the increased NaOH concentration according to eqn (1). Moreover, increasing the reaction temperature produces similar results to the increase in the NaOH concentration. The width of leaves on the Co branches increases with increasing the reaction temperature. Similar results have been reported in the synthesis of NiS nanostructures.17
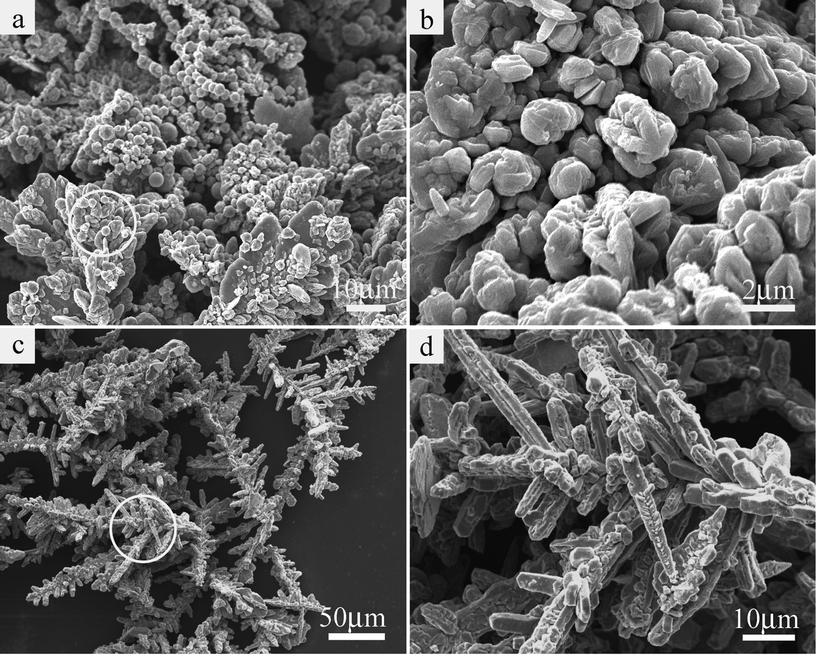 |
| Fig. 4
SEM images of Co products prepared using two different concentrations of NaOH: (a) and (b) 1 M, (c) and (d) 6 M. (b) and (d) are the enlarged images based on the circular region marked on (a) and (c), respectively. | |
To further understand the growth mechanism of the hierarchical Co hyperbranches, systematic time-dependent experiments illustrating the evolution of the morphology are inspected by a SEM technique at different reaction times (5, 10, and 24 h) of the hydrothermal reaction process. When the reaction has been proceeding for 5 h, the precipitation of some grey powders in the light pink solution is observed, reflecting an incomplete reaction. The resulting Co product exhibits a poorly branched morphology with shorter main branches of 10–20 μm and fewer secondary branches, as shown in Fig. 5(a). When the reaction is extended to 10 h, the main branches grow longer to around 25 μm in length and more secondary branches appear on them (Fig. 5(b)). The reaction completely finishes at 24 h time, and hierarchical Co hyperbranches are obtained as shown in Fig. 2. On the basis of the above experimental observations, it becomes possible to interpret the formation process of hierarchical Co hyperbranches using an Ostwald ripening process, which describes the dissolution of small crystals or sol particles and the redeposition of the dissolved species on the surfaces of larger crystals or sol particles over time,62 as illustrated in Fig. 6. Four consecutive steps are possibly included in an Ostwald ripening process. Step I: Numerous Co nuclei with different sizes are reduced from the complexes. Step II: Larger particles grow at the expense of the smaller ones due to the different solubilities between the larger and smaller particles.58 Some of the crystal faces of the products are limited by the selective adsorption of Na2C4H4O6 combined with the diffusion-limited growth model, producing an initial form of the hierarchical Co hyperbranches. Step III: The main and secondary branches grow longer and thicker and the leaves begin to grow on the secondary branches. Step IV: The undeveloped branches grow into hyperbranched architectures by the self-assembly of newly reduced Co particles through the same Ostwald ripening process as in step II. It is noted that magnetic dipole–dipole interaction is one of the main driving forces for growing any Co architectures mentioned above because it helps Co particles to attach to each other.63 It has been reported that the magnetically induced effect plays a key role in producing Ni dendritic structure.64
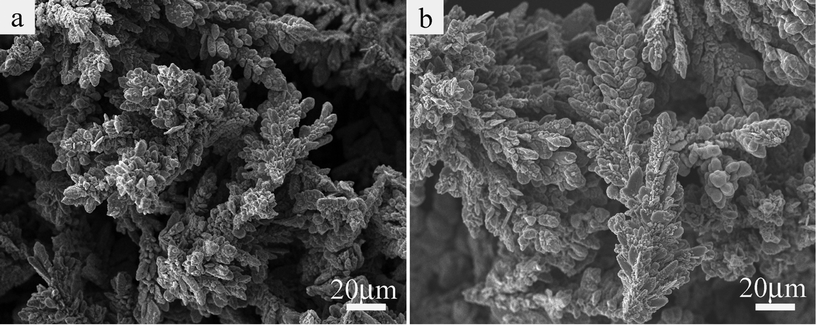 |
| Fig. 5
SEM images of Co products prepared using different growth stages of the hydrothermal reaction process: (a) 5 h, (b) 10 h. | |
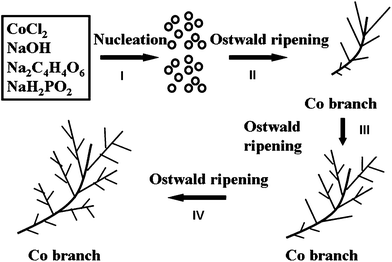 |
| Fig. 6 Schematic illustration of the possible formation process of hierarchical Co hyperbranches. | |
Magnetic properties
The magnetic hysteresis loops (M–H curves) at room temperature of the Co products with different morphologies are shown in Fig. 7. The Co products include products A, B, and C for microspheres (Fig. 3(a)), hyperbranches (Fig. 3(c)), and chains (Fig. 3(d)) with the ST/Co2+ ratio of 0, 15, and 30, respectively. The coercivities (Hc) of products A, B, and C are found to be 161, 231, and 258 Oe, respectively, which are all enhanced compared to their bulk material of a few tens of Oersteds.36 These enhancements may be due to the fact that ferromagnetic particles with smaller sizes often exhibit enhanced Hc44,45,54 and the shape anisotropy of the Co products tends to increase Hc.36 The higher Hc in product C (chains) than product A (microspheres) and product B (hyperbranches) may be ascribed to the larger length-to-diameter aspect ratio. The saturation magnetizations (Ms) of products A, B, and C are measured to be 158, 152, and 121 emu/g, respectively, which are all lower than their bulk material of 168 emu/g36 as a result of the presence of impurities,65 surface antiferromagnetic oxidation,65 and surface spin disorder66 in the products. In fact, resident Na2C4H4O6 exist inevitably in our products, and there is more resident Na2C4H4O6 in product C than in products A and B (even though they have been washed several times). This resident occupation leads to an eventually reduction in Ms. Besides, the spherical building blocks being relatively small size for product C, together with more surface spin disorder, are responsible for the decrease of Ms. Nevertheless, the results show that our products possess ferromagnetic characteristics, which are adjustable by controlling the sizes and morphologies of the products.
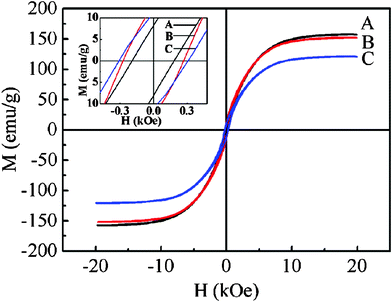 |
| Fig. 7 Magnetic hysteresis loops at room temperature of Co products with different morphologies. Products A, B, and C are for microspheres, hyperbranches, and chains with the ST/Co2+ ratio of 0, 15, and 30, respectively. The inset shows the low-field region of the loops. | |
Conclusions
3D hierarchical Co hyperbranches have been synthesized by a hydrothermal self-assembly route with the aid of a complex reagent of sodium tartrate. It has been found that the molar ratio of Na2C4H4O6 to CoCl2 in the solution of CoCl2·6H2O and NaOH plays a crucial role in the synthesis of the Co hyperbranches, while the other reaction parameters, such as reaction temperature, concentration of NaOH, and reaction time, have close relationships with the final morphology of the Co products. The growth mechanism for the Co hyperbranches have been proposed. The Co hyperbranches have exhibited enhanced Hc (161, 231, and 258 Oe for products A, B, and C, respectively) and reduced Ms (158, 152, and 121 emu/g for products A, B, and C, respectively) in comparison with their bulk material, as well as possessing different magnetic properties, adjustable by the size and morphology of the products. This simple, efficient, and morphologically controllable self-assembly route can be used to synthesize complex 3D micro/nanoarchitectures of other materials.
Acknowledgements
This work was supported by the Research Grants Council of the HKSAR Government (PolyU 5266/08E), the Central Research Grant of The Hong Kong Polytechnic University (1-ZV7P, 4-ZZ7L, and G-U741), and the National Nature Science Foundation of China (50331030).
References
- C. P. Collier, T. Vossmeyer and J. R. Heath, Annu. Rev. Phys. Chem., 1998, 49, 371–404 CrossRef CAS.
- M. P. Pileni, J. Phys. Chem. B, 2001, 105, 3358–3371 CrossRef CAS.
- B. Kim, S. L. Tripp and A. Wei, J. Am. Chem. Soc., 2001, 123, 7955–7956 CrossRef CAS.
- A. Wei, B. Kim, B. Sadtler and S. L. Tripp, ChemPhysChem, 2001, 2, 743–745 CrossRef CAS.
- A. G. Kanaras, C. Sönnichsen, H. T. Liu and A. P. Alivisatos, Nano Lett., 2005, 5, 2164–2167 CrossRef CAS.
- H. G. Yang and H. C. Zeng, Angew. Chem., Int. Ed., 2004, 43, 5930–5933 CrossRef CAS.
- G. Kaltenpoth, M. Himmelhaus, L. Slansky, F. Caruso and M. Grunze, Adv. Mater., 2003, 15, 1113–1118 CrossRef CAS.
- M. Yada, C. Taniguchi, T. Torikai, T. Watari, S. Furata and H. Katsuki, Adv. Mater., 2004, 16, 1448–1453 CrossRef CAS.
- L. Manna, D. J. Milliron, A. Meisel, E. C. Scher and A. P. Alivisatos, Nat. Mater., 2003, 2, 382–385 CrossRef CAS.
- Y. C. Cao and J. H. Wang, J. Am. Chem. Soc., 2004, 126, 14336–14337 CrossRef CAS.
- Z. P. Zhang, X. Q. Shao, H. D. Yu, Y. B. Wang and M. Y. Han, Chem. Mater., 2005, 17, 332–336 CrossRef CAS.
- Q. Gong, X. F. Qian, X. D. Ma and Z. K. Zhu, Cryst. Growth Des., 2006, 6, 1821–1825 CAS.
- C. B. Murray, C. R. Kagan and M. G. Bawendi, Science, 1995, 270, 1335–1338 CAS.
- J. Geng, J. J. Zhu and H. Y. Chen, Cryst. Growth Des., 2006, 6, 321–326 CAS.
- W. Shenton, D. Pum, U. B. Sleytr and S. Mann, Nature, 1997, 389, 585–587 CrossRef CAS.
- J. Du and Y. Chen, Angew. Chem., Int. Ed., 2004, 43, 5084–5087 CrossRef CAS.
- H. B. Li, L. L. Chai, X. Q. Wang, X. Y. Wu, G. C. Xi, Y. K. Liu and Y. T. Qian, Cryst. Growth Des., 2007, 7, 1918–1922 CAS.
- V. F. Puntes, K. M. Krishnan and A. P. Alivisatos, Science, 2001, 291, 2115–2117 CrossRef CAS.
- M. Ruben, U. Ziener, J. M. Lehn, V. Ksenofontov, P. Gutlich and G. B. M. Vaughan, Chem.–Eur. J., 2005, 11, 94–100 CrossRef.
- Y. Y. Li, J. P. Liu, X. T. Huang and G. Y. Li, Cryst. Growth Des., 2007, 7, 1350–1355 CAS.
- M. H. Cao, X. Y. He, J. Chen and C. W. Hu, Cryst. Growth Des., 2007, 7, 170–174 CAS.
- Y. Huang, X. F. Duan, Q. Q. Wei and C. M. Lieber, Science, 2001, 291, 630–633 CrossRef CAS.
- T. Yonezawa, S. Onoue and N. Kimizuka, Adv. Mater., 2001, 13, 140–142 CrossRef CAS.
- S. Park, J. H. Lim, S. W. Chung and C. A. Mirkin, Science, 2004, 303, 348–351 CrossRef CAS.
- T. D. Ewers, A. K. Sra, B. C. Norris, R. E. Cable, C. H. Cheng, D. F. Shantz and R. E. Schaak, Chem. Mater., 2005, 17, 514–520 CrossRef CAS.
- H. T. Shi, L. M. Qi, H. M. Cheng and B. Y. Zhu, Adv. Mater., 2003, 15, 1647–1651 CrossRef CAS.
- S. L. Tripp, S. V. Pusztay, A. E. Ribbe and A. Wei, J. Am. Chem. Soc., 2002, 124, 7914–7915 CrossRef CAS.
- X. W. Teng and H. Yang, Nano Lett., 2005, 5, 885–891 CrossRef CAS.
- X. S. Fang, C. H. Ye, L. D. Zhang, J. X. Zhang, J. W. Zhao and P. Yan, Small, 2005, 1, 422–428 CrossRef CAS.
- H. Q. Yan, R. R. He, J. Johnson, M. Law, R. J. Saykally and P. D. Yang, J. Am. Chem. Soc., 2003, 125, 4728–4729 CrossRef CAS.
- F. Gao, Q. Y. Lu, S. H. Xie and D. Y. Zhao, Adv. Mater., 2002, 14, 1537–1540 CrossRef CAS.
- H. L. Niu, Q. W. Chen, Y. S. Jia, H. F. Zhu and M. Ning, Nanotechnology, 2004, 15, 1054–1058 CrossRef CAS.
- S. H. Sun, Adv. Mater., 2006, 18, 393–403 CrossRef CAS.
- A. P. Alivisatos, Science, 1996, 271, 933–937 CAS.
- F. Dumestre, B. Chaudret, C. Amiens, M. Respaud, P. Fejes, P. Renaud and P. Zurcher, Angew. Chem., Int. Ed., 2003, 42, 5213–5216 CrossRef CAS.
- Q. Xie, Y. T. Qian, S. Y. Zhang, S. Q. Fu and W. C. Y, Eur. J. Inorg. Chem., 2006, 37, 2454–2459 CrossRef.
- Q. Xie, Z. Dai, W. W. Huang, J. B. Liang, C. L. Jiang and Y. T. Qian, Nanotechnology, 2005, 16, 2958–2962 CrossRef CAS.
- H. Q. Cao, Z. Xu, H. Sang, D. Sheng and C. Y. Tie, Adv. Mater., 2001, 13, 121–123 CrossRef CAS.
- Y. Henry, K. Qunadjela, L. Piraux, S. Dubois, J. M. George and J. L. Duyail, Eur. Phys. J. B, 2001, 20, 35–54 CrossRef CAS.
- F. Dumestre, B. Chaudret, C. Amiens, M. C. Fromen, M. J. Casanove, P. Renaud and P. Zurcher, Angew. Chem., Int. Ed., 2002, 41, 4286–4289 CrossRef CAS.
- Y. J. Zhang, S. Ma, D. Li, Z. H. Wang and Z. D. Zhang, Mater. Res. Bull., 2008, 43, 1957–1965 CrossRef CAS.
- Y. J. Zhang, Q. Yao, Y. Zhang, T. Y. Cui, D. Li, W. Liu, W. Lawrence and Z. D. Zhang, Cryst. Growth Des., 2008, 8, 3206–3212 CAS.
- L. Guo, F. Liang, X. G. Wen, S. H. Yang, L. He, W. Z. Zheng, C. P. Chen and Q. P. Zhong, Adv. Funct. Mater., 2007, 17, 425–430 CrossRef CAS.
- V. F. Puntes, D. Zanchet, C. K. Erdonmez and A. P. Alivisatos, J. Am. Chem. Soc., 2002, 124, 12874–12880 CrossRef CAS.
- R. Xu, T. Xie, Y. G. Zhao and Y. D. Li, Cryst. Growth Des., 2007, 7, 1904–1911 CAS.
- H. Yoshikawa, K. Hayashida, Y. Kozuka, A. Horiguchi, K. Awaga, S. Bandow and S. Iijima, Appl. Phys. Lett., 2004, 85, 5287–5289 CrossRef CAS.
- X. H. Liu, R. Yi, Y. T. Wang and X. G. Qiu, J. Phys. Chem. C, 2007, 111, 163–167 CAS.
- Y. L. Hou, H. Kondoh and T. Ohta, Chem. Mater., 2005, 17, 3994–3996 CrossRef CAS.
- A. K. Srivastava, S. Madhavi, T. J. Whit and R. V. Ramanujan, J. Mater. Chem., 2005, 15, 4424–4428 RSC.
- Y. C. Zhu, Q. Yang, H. G. Zheng, W. C. Yu and Y. T. Qian, Mater. Chem. Phys., 2005, 91, 293–297 CrossRef CAS.
- Y. C. Zhu, H. G. Zheng, Q. Yang, A. L. Pan, Z. P. Yang and Y. T. Qian, J. Cryst. Growth, 2004, 260, 427–434 CrossRef CAS.
- X. M. Ni, D. G. Li, Y. F. Zhang and H. G. Zheng, Chem. Lett., 2007, 36, 908–909 CrossRef CAS.
- Y. J. Zhang, Y. Zhang, Z. H. Wang, D. Li, T. Y. Cui, W. Liu and Z. D. Zhang, Eur. J. Inorg. Chem., 2008, 17, 2733–2738 CrossRef.
- L. P. Zhu, H. M. Xiao, W. D. Zhang, Y. Yang and S. Y. Fu, Cryst. Growth Des., 2008, 8, 1113–1118 CAS.
- Z. P. Liu, S. Li, Y. Yang, S. Peng, Z. K. Hu and Y. T. Qian, Adv. Mater., 2003, 15, 1946–1948 CrossRef CAS.
-
J. W. Mullin, Crystallization, 3rd ed.; Butterworth-Heinemaan: Oxford, U. K., 1997 Search PubMed.
- T. C. Halsey, B. Duplantier and K. Honda, Phys. Rev. Lett., 1997, 78, 1719–1722 CrossRef CAS.
-
M. Adachi, D. J. Lockwood, Self-Organized Nanoscale Materials, U. S. A. 2006.
- M. P. Mallin and C. Murphy, Nano Lett., 2002, 2, 1235–1237 CrossRef CAS.
- H. M. Xiao, S. Y. Fu, L. P. Zhu, Y. Q. Li and G. Yang, Eur. J. Inorg. Chem., 2007, 1966–1971 CrossRef CAS.
- G. J. Zhou, M. K. Lu, Z. S. Yang, H. P. Zhang, Y. Y. Zhou, S. M. Wang, S. F. Wang and A. Y. Zhang, J. Cryst. Growth, 2006, 289, 255–259 CrossRef CAS.
- A. R. Roosen and W. C. Carter, Phys. A, 1998, 261, 232–247 CrossRef CAS.
- J. H. Gao, B. Zhang, X. X. Zhang and B. Xu, Angew. Chem., Int. Ed., 2006, 45, 1220–1223 CrossRef CAS.
- J. Ye, Q. W. Chen, H. P. Qi and N. Tao, Cryst. Growth Des., 2008, 8, 2464–2468 CAS.
- L. Zhang and A. Manthiram, Phys. Rev. B, 1996, 54, 3462–3467 CrossRef CAS.
- D. Lin, A. C. Nunes, C. F. Majkrzak and A. E. Berkowitz, J. Magn. Magn. Mater., 1995, 145, 343–348 CrossRef CAS.
|
This journal is © The Royal Society of Chemistry 2011 |
Click here to see how this site uses Cookies. View our privacy policy here.