DOI:
10.1039/C1RA00036E
(Paper)
RSC Adv., 2011,
1, 607-610
Formation of a chrome-free and coloured conversion coating on AA6063 aluminium alloy
Received
15th April 2011
, Accepted 3rd July 2011
First published on 18th August 2011
Abstract
A new passivation process has been developed for producing a chrome-free and coloured conversion coating on aluminium alloy AA6063. The method is based on the reaction of the aluminium alloy with a potassium hexafluorozirconate based solution at room temperature. The conversion coating obtained has a grey colour, which enables visual assessment of the coating development and coating quality during processing. The colouring effect is a significant advantage over the zirconium and titanium based conversion coatings currently used in the industry, which are largely colourless. The new treatment process is simple and allows a uniform coating to be formed within a few minutes. The composition and the surface morphology of the coatings were characterized. The corrosion resistance of the coated samples was evaluated by electrochemical tests. The results have shown that the treatment yields a zirconium based conversion coating with a microcrystalline structure, which is desirable for paint adhesion, and substantially improves the corrosion resistance of the aluminium alloy.
1. Introduction
Aluminium and its alloys have very limited resistance to corrosion. Improving their corrosion resistance by surface modification is essential for their practical applications. This surface modification primarily involves the formation of a protective coating or conversion coating on the metal surface. At present, the most effective method for active protection of these metals is to employ chromate containing conversion coatings.1–3 These coatings not only provide excellent anticorrosion performance and good adhesion to organic finishes, but also yield a coloured coating effect. The coating colour varies depending on the composition of the treatment solution. The conversion coatings composed of hexavalent chrome are usually brownish yellow. However, due to the toxicity and environmental issues of chromium, chromate-based conversion coatings are no longer acceptable.4
Although considerable efforts have been made to develop chrome-free protective coatings,3–21 it remains to be a great challenge to broadly match the performance, ease of application and low cost of chromate coatings. At present, the most promising methods for aluminium alloys that have potential to be alternatives to the chromate treatment method involve hexafluorozirconic or hexafluorotitanic based treatments, which lead to the formation of a coating containing aluminium oxyfluoride, titanium dioxide and zirconium oxyfluoride.7–14 These conversion coatings, however, are largely colourless, which prevents the operators from visually checking the actual execution of the process or the quality of the coating obtained. In addition, these treatment methods also have a relatively low yield compared to the chromium-based treatments.5
In this paper, a new chrome-free treatment method based on the use of potassium hexafluorozirconate was introduced for obtaining a coloured protective coating on aluminium alloys. A widely used aluminium alloy AA6063 was selected as the substrate for this investigation. The morphology and composition of the resulting coatings were determined by optical microscopy, scanning electron microscopy (SEM), energy dispersive X-ray spectroscopy (EDS) and X-ray diffraction (XRD). The corrosion resistance of the coatings were evaluated by electrochemical testing.
2.
Experimental methods
2.1 Preparation of conversion coatings on AA6063
All of the chemicals used were of reagent grade obtained from Aldrich. The samples of AA6063 with the approximate dimensions of 25 mm × 25 mm × 2 mm were polished with 800# abrasive paper and rinsed with distilled water. The samples were then cleaned in ethanol in an ultrasonic bath, followed by rinsing with distilled water.
A saturated potassium hexafluorozirconate (K2ZrF6) solution was prepared with distilled water at room temperature (25 °C), and used for the passivation treatment of the AA6063 samples. The pH of the solution was 4.2. The pre-treated aluminium alloy samples were immersed in the K2ZrF6 solution at room temperature (25 °C) for various periods of time from 1 to 30 minutes. After the surface treatment, the samples were rinsed thoroughly with water and dried at room temperature for 24 hours.
2.2. Characterization of the conversion coatings prepared
The composition of the coating was characterized with X-ray diffraction (XRD; D/Max-IIIA, Japan) using a Cu Kα source. The surface morphology was studied with an optical microscope and scanning electron microscope (SEM; S-3700N, Japan). The elemental distribution was investigated by energy-dispersive spectroscopy (EDS; Quantax, Germany).
2.3. Corrosion resistance evaluation
Electrochemical tests were carried out by using a VMP3 Multichannel Workstation (Bio-Logic, France, with EC-Lab software) in a standard three-electrode system (with a platinum foil as a counter electrode, a saturated calomel electrode as an auxiliary electrode, and the aluminium alloy sample with exposed area of 5 mm × 15 mm as a working electrode). The electrolyte was 3.5 wt% NaCl, and the potential scan rate was set at 5.00 mV/s.
3. Results and discussion
3.1. Colouring effect and surface morphology of the conversion coatings
The AA6063 samples before and after the passivation treatment were examined with an optical microscope. The optical images in Fig. 1 clearly show that the colour of the as-polished aluminium AA6063 sample is silver white (a), but the AA6063 sample treated with the K2ZrF6 solution for 10 minutes became dark grey in colour (b), indicating the formation of a conversion coating on the surface. This colouring effect will enable the operators to visually monitor the coating development and assess the quality of the resulting coating. This is considered as a significant advantage over the zirconium and titanium based conversion coatings currently used in industry, which are largely colourless.
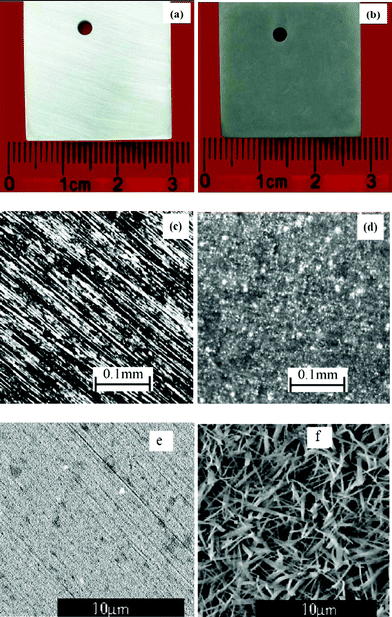 |
| Fig. 1 Optical and SEM images of the AA6063 samples: (a) & (c) optical images of a polished and cleaned sample, (b) & (d) optical images of a sample treated with the K2ZrF6 solution, (e) a SEM image of the untreated AA6063, (f) a SEM image of the conversion coating formed on AA6063. | |
The surface textures of the passivation treated and untreated samples also exhibit significant difference as shown in Fig. 1 (c) and (d). The as-polished AA6063 aluminium sample (c) displays sharp and oriented lines on the surface, which were generated by polishing with the 800# sandpaper. In comparison, the sample treated with the passivator exhibits a completely different surface texture (d), and the polishing marks cannot be observed due to the formation of a conversion coating on the surface that covers the background pattern.
The microstructure of the conversion coating was further examined by SEM. The image in Fig. 1 (e & f) reveals that the coating is composed of needle-like and/or ribbon-like microcrystals grown parallel to the substrate surface, forming a distinctive microcrystalline and microporous structure of the coating. The microcrystalline structure is desirable for the subsequent painting process, which would be expected to improve the paint adhesion due to the formation of mechanical interlocks. This is considered as another advantage over the conventional zirconium and/or titanium conversion coatings, which generally do not have very good adhesion with organic paints.2
3.2. Composition of the conversion coatings
The elemental distribution of the coating was obtained by EDS analysis. The results in Fig. 2 show that the conversion coating consisted of Zr, F, K, O and Al elements. In particular, the Zr and F contents were high, accounting for 24.67% and 25.53% by weight respectively, and aluminium was 32.74% by weight. The results indicate that a passive coating based on the zirconium complex was effectively generated on the surface of the aluminium substrate. This was also confirmed by an XRD analysis. The X-ray diffraction pattern of the coating (formed after 30 min treatment) is presented in Fig. 3. The outstanding diffraction peaks show that the coating was mainly composed of Al2O3,AlF3, KZrF3(OH)2H2O and KZrF3O2H2O and Al. The main reactions are as follows. | 2K+ + 5OH− + 4H+ + 2ZrF62− → KZrF3(OH)2H2O + KZrF3O2H2O + 6F+ + 2H2 | (3) |
3.3. Electrochemical test of the conversion coatings
The corrosion resistance of the treated aluminium alloy sample was evaluated using a VMP3 multichannel workstation in a 3.5% NaCl solution, and compared with that of an untreated control sample. The potentiodynamic polarization curves of the treated and untreated samples are shown in Fig. 4, and their corresponding parameters Ecorr (mV) and Icorr (μA) are presented in Table 1.
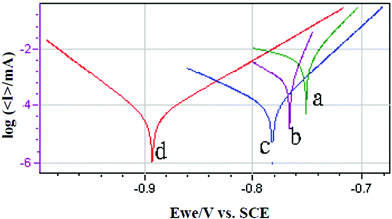 |
| Fig. 4 The potentiodynamic polarization curves of the untreated and K2ZrF6 treated AA6063 samples (a) untreated, (b) treated for 1 min, (c) treated for 3 min, (d) treated for 5 min. | |
Table 1 Potentiodynamic polarization parameter values of the untreated and K2ZrF6 solution treated AA6063 samples
Sample |
Ecorr (mV) |
Icorr (μA) |
a
|
−750.79 |
4.074 |
b
|
−765.45 |
0.569 |
c
|
−781.93 |
0.089 |
d
|
−892.94 |
0.035 |
It can be seen that the corrosion current Icorr (μA) of the untreated aluminium alloy (a) was 4.074 μA, while the corrosion currents of all of the treated samples were substantially lower, indicating a significantly improved corrosion resistance. Furthermore, increasing the treatment time in the K2ZrF6 solution from 1 min to 3 min resulted in a significant decrease in the corrosion current from 0.569 μA to 0.089 μA, and when the treatment time was extended to 5 min, the corrosion current fell to 0.035 μA, which represents over two orders of magnitude in reduction compared to that of the untreated aluminium alloy. The corrosion potential (−705.79 to 892.94 mV) is lower than other reported examples (−640 to −665 mV).22 These results have clearly demonstrated that the aluminium alloy has been effectively passivated in the K2ZrF6 solution, and that the passive film is growing with time.
4. Conclusions
This investigation has demonstrated that aluminium alloys can be successfully passivated in a K2ZrF6-based solution at room temperatures. The conversion coating obtained exhibits a typical microcrystalline structure and grey colour. The colouring effect of the coating enables visual assessment of the coating development and coating quality during processing, and thus is considered to have a significant advantage over the zirconium and titanium based conversion coatings currently used in the industry, which are largely colourless. The phase composition of the coating has been shown to be mainly zirconium complex. The electrochemical tests have demonstrated that this surface treatment substantially improved the corrosion resistance of the aluminium alloy. The treatment process is simple, effective, inexpensive, and allows a uniform coating to be formed within a few minutes, indicating a great potential for practical applications.
References
- J. H. Osborne, Prog. Org. Coat., 2001, 41, 280–286 CrossRef CAS.
- M. W. Kendig and R. G. Buchheit, Corrosion, 2003, 59(5), 379–400 CrossRef CAS.
- D. G. Shchukin, M. Zheludkevich, K. Yasakau, S. Lamaka, M. G. S. Ferreira and H. Möhwald, Adv. Mater., 2006, 18, 1672–1678 CrossRef CAS.
- R. L. Twite and G. P. Bierwagen, Prog. Org. Coat., 1998, 33, 91–100 CrossRef CAS.
-
B. W. Dalla, F. Vincenzi and F. Vincenzi, Patent No. EP 1612294 A1, Italtecno S.R.L., 2005.
- C. C. Chang, C. C. Wang, C. W. Wu, S. C. Liu and F. D. Mai, Appl. Surf. Sci., 2008, 255(4), 1531–1533 CrossRef CAS.
- G. Gusmano, G. Montesperelli, M. Rapone, G. Padeletti, A. Cusmà and S. Kaciulis, Surf. Coat. Technol., 2007, 201(12), 5822–5828 CrossRef CAS.
- M. Schem, T. Schmidt, J. Gerwann, M. Wittmar, M. Veith and G. E. Thompson, Corros. Sci., 2009, 51(10), 2304–2315 CrossRef CAS.
- P. D. Deck, M. Moon and R. J. Sujdak, Prog. Org. Coat., 1997, 34(1–4), 39–48 CrossRef.
- F. Andreatta, A. Turco, I. de Graeve, H. Terryn, J. H. W. de Wit and L. Fedrizzi, Surf. Coat. Technol., 2007, 201(18), 7668–7685 CrossRef CAS.
- S. Verdier, N. van der Laak, F. Dalard, J. Metson and S. Delalande, Surf. Coat. Technol., 2006, 200(9), 2955–2964 CrossRef CAS.
- S. H. Wang, C. S. Liu and F. J. Shan, Acta Metallurgica Sinica (English Letters), 2008, 21(4), 269–274 CrossRef CAS.
- M. Dabalà, L. Armelaob, A. Buchberger and I. Calliari, Appl. Surf. Sci., 2001, 172(3–4), 312–322 CrossRef.
- T. Y. Chen, W. F. Li and J. Du, Journal of Functional Materials., 2010, 41, 260–263 Search PubMed.
- G. Decher, J. D. Hong and J. Schmitt, Thin Solid Films, 1992, 210, 831–835 CrossRef.
- M. L. Zheludkevich, R. Serra, M. F. Montemor and M. G. S. Ferreira, Electrochem. Commun., 2005, 7, 836–840 CrossRef CAS.
- M. Kendig, M. Hon and L. Warren, Prog. Org. Coat., 2003, 47, 183–189 CrossRef CAS.
- H. Tatematsu and T. Sasaki, Cem. Concr. Compos., 2003, 25, 123–129 CrossRef CAS.
- M. L. Zheludkevich, I. M. Salvado and M. G. S. Ferreira, J. Mater. Chem., 2005, 15, 5099–5111 RSC.
- L. S. Kasten, J. T. Grant, N. Grebasch, N. Voevodin, F. E. Arnold and M. S. Donley, Surf. Coat. Technol., 2001, 140, 11–15 CrossRef CAS.
- A. N. Khramov, N. N. Voevodin, V. N. Balbyshev and M. S. Donley, Thin Solid Films, 2004, 447, 549–557 CrossRef.
- M. A. Smit, J. A. Hunter, J. D. B. Sharman, G. M. Scamans and J. M. Sykes, Corrosion Science., 2004, 46, 1713–1727 CrossRef CAS.
|
This journal is © The Royal Society of Chemistry 2011 |
Click here to see how this site uses Cookies. View our privacy policy here.