DOI:
10.1039/C1RA00021G
(Paper)
RSC Adv., 2011,
1, 199-210
Highly efficient polyurethane ionomer corrosion inhibitor: the effect of chain structure
Received
8th April 2011
, Accepted 19th April 2011
First published on 28th July 2011
Abstract
A series of polyurethane (PU) ionomers with different degree of sulfonation (DS) have been synthesized and successfully used as corrosion inhibitor for mild steel (MS) in acidic medium. Nuclear magnetic resonance (NMR) and Fourier transform infra red (FTIR) spectra of the sulfonated PUs confirmed the sulfonation on the >NH group of the urethane linkage and DS increases with the increase in the ratio of the sulfonating agent and PU. More than 90% inhibition efficiency (IE) of sulfonated polyurethanes (SPU) has been reported using only 20 ppm of the ionomers. These ionomers inhibited the corrosion of MS through adsorption following the Langmuir adsorption isotherm. Surface coverage has been scaled using scanning electron microscopy (SEM) and atomic force microscopy (AFM). The effect of sulfonation on the electronic and chemical structure of PU molecules has also been investigated. Electronic structure calculations have been performed to predict the adsorption behavior of ionomers on the metal surface, and thereby, the relative inhibition has been quantitatively correlated with DS.
Introduction
Mild steel is one of the most important iron containing alloys which is used in many industries for construction of plants, equipments, storage tanks etc. due to its excellent physical and mechanical properties.1,2 The study on the inhibition of mild steel corrosion is of great industrial and academic importance as it corrodes rapidly when it comes in contact with acids.3 Acids are used in many industrial processes for pickling, cleaning, de-scaling of metals and also to acidify oil wells.4,5 Application of organic inhibitors is the most important and practical method for the protection of metallic corrosion.6,7 Widely used organic inhibitors contain nitrogen, sulfur, oxygen as hetero atoms, double and triple bonds, aromatic rings or combination of them.8–14 The inhibition efficiency of these organic molecules mainly depends on their ability to get adsorbed on the metal surface by displacing adsorbed water molecules at the interface to form a compact barrier film which isolates the metal surface from the corrosive medium.15 The extent of adsorption depends on the number of hetero atoms, the projected surface area and molecular weight of these organic molecules.16,17 Most of such compounds are toxic in nature and their adherence on metal surface is poor.
In recent years, polymers have drawn considerable attention as corrosion inhibitor because of their large surface area, inherent stability and cost effectiveness. These exhibit excellent inhibition even at very low concentration when added to the most of the aggressive media.16–21 A number of conducting polymers have been reported in the literature as corrosion inhibitors, but most of these show low inhibition efficiency due to their brittle nature and poor film forming capability.22–25 Thermoplastic polymers might prove promising in this respect by the virtue of their tendency to cover a wider surface area and excellent adhesion property. Polyurethanes constitute one of the most important and useful class of thermoplastic elastomers which have a wide range of applications as adhesives, coatings, foams, packaging materials and biomedical aids due to its excellent biocompatibility.26–30 But, the highly insoluble nature of these polymers in aqueous solutions limits their use as corrosion inhibitors. In order to use polyurethanes as corrosion inhibitors, it is necessary to chemically modify the polymer so as to make it water soluble and electrically conducting. Incorporation of some ionic functionality into the hard segment unit of the polymer chain leads to enhanced electrical conductivity and solubility of the polyurethane in aqueous solution.31 In our previous work, hexamethylene diisocyanate based aliphatic polyurethanes were successfully used as corrosion inhibitor for mild steel in acidic medium after chemical modification.32 The inhibition efficiency as high as 95% achieved using 100 ppm of sulfonated polyurethanes, was encouraging enough to continue this pursuit with the prime objective of getting better inhibition efficiency using still smaller dose.
The objective of the present work is to study the inhibitive effect of diphenyl methane diisocyanate based sulfonated polyurethanes with different degree of sulfonation (DS) on mild steel corrosion in 0.5 M H2SO4. Inhibitive effects of these polymers have been investigated using gravimetric, potentiodynamic polarization and electrochemical impedance spectroscopic techniques. Quantum chemical calculations of the polyurethane ionomer molecules with different degree of sulfonation have been carried out for theoretical prediction of inhibition efficiency.
Experimental
Materials
4,4′-diphenylmethane diisocyanate (MDI), polytetramethylene glycol (PTMG, Mn = 2900, g/mol), butane di-ol (BD), sodium hydride (NaH, 60% dispersion in mineral oil) and γ-propane sultone (PS) all from (Sigma-Aldrich, India) were used as received. The catalyst dibutyltin dilaurate and solvent N,N-dimethylacetamide (DMA) were procured from Himedia (India) and Merck (India), respectively. Analytical grade sulfuric acid (Merck, India) was used for the preparation of corrosive solution.
Synthesis
The segmented polyurethanes were synthesized by two-steps bulk polymerization, following a procedure reported earlier.33 In the first stage, polytetramethylene glycol and 4,4′-diphenylmethane diisocyanate were mixed at 70 °C for 4 h to form an isocyanate-terminated pre-polymer. In the second stage, the pre-polymer was treated with chain extender in the presence of catalyst (dibutyltin dilaurate) under rapid stirring at the same temperature for 24 h in an inert atmosphere. The polymer was then precipitated by pouring the reaction mixture into deionized water.
Sulfonated polyurethanes were prepared via a bimolecular nucleophilic substitution reaction in which the urethane hydrogen was removed by reacting polyurethane with NaH dissolved in DMA at −5 °C. The polyurethane was then reacted with propane sultone to yield a polymer with anionic sulfonate groups. The procedure adopted for sulfonation was the same as that described by Grasel et al.34 The extent of sulfonation was found to vary from 48 to 97% on successively replacing the urethane hydrogen atoms by sulfonate group. Scheme 1 represents the synthesis of polyurethane followed by its sulfonation. The number after SPU indicates the percentage sulfonation.
 |
| Scheme 1 Reaction scheme for the synthesis of pure and sulfonated polyurethanes. | |
Characterization
Fourier Transform Infrared Spectra (FTIR) of thin solid polymer films were recorded using Thermo Nicolet 5700 FTIR spectrometer taking 100 numbers of scans with the resolution of 4 cm−1. Proton NMR spectra of pure and modified PU were recorded on a JEOL AL 300 spectrometer using d6-DMSO as solvent. Each spectrum was recorded after the sample was equilibrated in the magnetic field at least for 10 min. The chemical shifts are reported in parts per million (ppm) relative to tetramethylsilane (TMS). The degree of sulfonation was calculated using the area under the NMR signals (peaks at 8.5, 4.4, 1.9 and 1.7 ppm). The molecular weights of the synthesized PU and various SPUs were determined by Gel Permeation Chromatography (GPC) using DMF as eluent with a flow rate of 1 ml/min employing polystyrene as standard. The UV-Vis spectra were recorded using a Perkin Elmer Lambda 25UV-Vis spectrophotometer.
Coupon preparation
The composition of mild steel used for all the experiments was as follows: C, 0.23; Mn, 0.11; Si, 0.02; P, 0.02; S, 0.02; Ni, 0.02; Cu, 0.01; Cr, 0.01; Fe, remainder. The specimens were successively polished with different grades (320–2000) of emery papers, washed with double distilled water, degreased with acetone, dried and stored in a desiccator.
Gravimetric measurements
Gravimetric experiments were carried out in 250 ml beaker containing 150 ml of the 0.5 M H2SO4 without and with different amounts of inhibitors. The beakers were kept in an air thermostat maintained at desired temperatures. The polished rectangular specimens of size (4 × 3 × 0.1 cm3) were weighed accurately and immersed in the electrolyte for 24 h. The specimens were then removed from the electrolyte, washed thoroughly with distilled water, dried and weighed. The mean of weight loss values of three identical experiments was used to calculate the corrosion rate and inhibition efficiency of the inhibitors.
Electrochemical experiments
The conventional three-electrode cell assembly was used with mild steel as the working electrode, platinum wire as the counter electrode and silver/silver chloride as the reference electrode. The working electrode of size (3 × 1 × 0.1 cm3) with an exposed area of 1 cm2 on one side of the specimen, leaving a part on top for electrical connection and remaining covered with extra pure paraffin wax was dipped in the test solution. All the electrochemical experiments were performed with CHI Electrochemical Analyzer (Model 604C). The polarization curves were obtained by changing the electrode potential from −250 mV to +250 mV with respect to open circuit potential (OCP), at a scan rate of 0.5 mV s−1. The linear Tafel segments of the anodic and cathodic curves were extrapolated to obtain corrosion potential (Ecorr) and corrosion current density (Icorr). Electrochemical impedance spectroscopic (EIS) measurements were carried out in a frequency range of 100 KHz to 0.01 Hz with an amplitude of 5 mV peak-to-peak, using AC signals at the OCP.
Morphological investigation
The surface morphology of the adsorbed film was investigated both by using scanning electron microscope (SEM) and atomic force microscope (AFM). The surface morphology of the thin film was examined with a LEO 435VP SEM instrument operated at 15 kV. All the samples were gold-coated by means of a sputtering apparatus before observation. A NT-MDT multimode atomic force microscope, Russia, controlled by Solver scanning probe was used for studying the surface morphology. Tapping mode was used with the tip mounted on 100 μm long single beam cantilever with resonant frequency in the range of 240–255 kHz, and the corresponding spring constant of 11.5 N/m. The inhibitor film formed on the metal surface after corrosion studies were used for AFM measurements. The roughness profile was calculated using a straight line across the 3D image.
Quantum chemical calculations
To understand the corrosion inhibition efficiency of different polyurethane molecules electronic structure calculations have been performed. These calculations yielded highest occupied molecular orbital (HOMO) and lowest unoccupied molecular orbital (LUMO) energies. Among quantum chemical methods, the Density Functional Theory (DFT) is found to be a suitable method53,54 for our calculations. All the calculations were performed using a hybrid version of DFT and Hartree–Fock (HF) methods, namely, B3LYP density functional theory in which the exchange energy from Becke's exchange functional is combined with the exact energy from Hartree–Fock theory. Along with the component exchange and correlation functionals, three parameters define the hybrid functional, specifying how much of the exact exchange is mixed in. Although the three semi-empirical parameters are optimized primarily to reproduce thermo-chemistry of small organic molecules, it has been proven to perform exceptionally well for relatively large organic molecules of heteroatoms. The geometries of inhibitor molecules (or ions) were optimized at the B3LYP/6-31G(d,p) level of theory. All the calculations were carried out using Gaussian 03 suits of program.35
Results and discussion
Chemical modification of polyurethane:
NMR spectroscopy has been employed to confirm sulfonation and its quantification. The NMR spectra of PU, SPU-60 and SPU-97 are shown in Fig. 1. A comparison of spectra of pure and sulfonated PUs reveals a gradual decrease in the intensity of the peak at 8.5 ppm due to >NH proton of urethane linkage36 with increasing DS. This shows that most of the urethane hydrogen was replaced with propyl sulfonate group from propane sultone. The appearance of three new peaks (levelled as 2, 3 and 4) at 1.7, 1.9 and 4.4 ppm, presumably due to incorporation of -CH2groups from propane sultone, further confirms the presence of sulfonate groups in the spectra of sulfonated PUs.37 The relative intensities of all these new peaks increased with increasing DS. The DS (%) was determined using the following expression;38 |  | (1) |
where, a is the peak area of the signal corresponding to the hydrogen atoms of >NH group and b is the peak area of the signal corresponding to hydrogen atoms of -CH2groups of propane sultone. Fig. 2 represents the plot of DS as a function of weight ratio of the sulfonating agent to the urethane linkage of polyurethane. The DS was observed to increase with increasing the concentration of the sulfonating agent and varied from 48 to 97% as the concentration of the propane sultone was increased from 0.2 to 0.96 wt%. FTIR studies further provided support to the successful sulfonation of the PU. Fig. 3 shows the FTIR spectra of PU, SPU-88 and SPU-97. On comparing the above three spectra, it is revealed that, the intensity of the >N–H vibration peak at 3390 cm−1 has gradually reduced with increasing DS. This suggests that most of the urethane hydrogen is replaced by propyl sulfonate group from propane sultone. The appearance of a new peak due to the symmetric stretching vibrations of “S=O” group at 1180 cm−1 confirms the successful introduction of the sulfonate groups which were absent in the spectrum of pure PU.39 The solubility of modified PU in water also indicates the formation of ionomer which is now ready to be used for corrosion inhibition in aqueous media. This is one of the novel ways of transforming thermoplastic elastomer into a corrosion inhibitor since the pristine PU is not soluble in water.
 |
| Fig. 1
1H NMR spectra of pure and sulfonated PU with two representative different degrees of sulfonation. | |
 |
| Fig. 2 Variation of the degree of sulfonation (DS) of polyurethane as a function of weight ratio of the sulfonating agent to the urethane group of polyurethane. | |
 |
| Fig. 3
FTIR spectra of pure and sulfonated PUs with two different degrees of sulfonation. | |
Gravimetric measurements:
The weight loss of the mild steel samples in 0.5 M H2SO4 in the absence and in the presence of various concentrations of SPU-48, SPU-60, SPU-88 and SPU-97 was determined after 24 h of immersion at 25 °C. The values of corrosion rate (CR) and inhibition efficiency (IE) were calculated using the following equations: |  | (2) |
|  | (3) |
where, Δm is the weight loss (mg) of the mild steel specimen, S is the surface area (cm2) of the specimen and t (h) is the exposure time in eqn (2); where as W° and W are the weight loss of the mild steel specimen without and with the addition of the inhibitors, respectively in the eqn (3).
The values of CR obtained from weight loss measurements and recorded in Table 1 clearly show that the CR values of mild steel in 0.5 M H2SO4 containing different SPUs decreases as the concentration and DS increases. The dependence of IE on concentration as well as on DS is presented in Fig. 4a. It is clearly seen in the figure that IE at first increased rapidly with increasing concentration of the polymer and reached an optimum value at 100 ppm for all the SPUs. Further increase in their concentration did not cause any significant change and hence ignored. The enhancement in the IE with respect to the polymer concentration suggests that more molecules are needed to adequately cover the metal surface when the concentration of inhibitor is low. No further increase in IE beyond 100 ppm of SPU is attributed to the saturation of the adsorption process. It is also observed from the figure that IE increases with increasing DS. The IE values followed the order SPU-48 < SPU-60 < SPU-88 < SPU-97. This increase in IE with DS is attributed to the enhanced adsorbability owing to the increase in the number of active centres (ionic sulfonate group) in the polymer. The curves in Fig. 4b illustrate the variation of IE with the exposure time at concentrations of 10 and 100 ppm. It is noted from the figure that IE increases with exposure time up to 48 h and there after it becomes nearly constant. This suggests that the process of adsorption of inhibitor attains its saturation limit in 48 h. The constancy region between 48 and 168 h further implies that the adsorbed polymer film is quite stable and remains intact at least for a week.
 |
| Fig. 4 Inhibition efficiency of sulfonated polyurethane (a) as a function of inhibitor concentrations and degree of sulfonation and (b) as a function of immersion time of electrode and (c) as a function of temperature. | |
Table 1 Corrosion parameters for mild steel in 0.5 M H2SO4 in absence and presence of different concentrations of inhibitors (SPU-48, SPPU-60, SPU-88 and SPU-97) measured by using gravimetric and electrochemical techniques
Inhibitor
|
Cinh ppm |
CR mg cm−2 h−1 |
Icorr μA cm−2 |
Rct Ω cm2 |
Y0 μ Ω sn cm−2 |
n |
Blank |
0 |
2.920 |
4399 |
5.0 |
239 |
0.89 |
SPU-48
|
1 |
2.092 |
2859 |
8.8 |
196 |
0.92 |
5 |
1.608 |
2254 |
9.4 |
146 |
0.91 |
10 |
1.320 |
1689 |
12.1 |
139 |
0.88 |
20 |
1.086 |
1301 |
20.1 |
112 |
0.93 |
40 |
0.907 |
1220 |
22.6 |
95.6 |
0.90 |
60 |
0.823 |
1149 |
24.5 |
93.0 |
0.91 |
80 |
0.797 |
1089 |
30.0 |
83.7 |
0.89 |
100 |
0.774 |
948 |
31.0 |
75.0 |
0.89 |
SPU-60
|
1 |
1.693 |
2320 |
10.5 |
154 |
0.90 |
5 |
1.220 |
1662 |
14.8 |
134 |
0.88 |
10 |
0.837 |
1142 |
22.4 |
96.0 |
0.90 |
20 |
0.607 |
864 |
24.7 |
93.7 |
0.88 |
40 |
0.573 |
738 |
30.1 |
89.7 |
0.88 |
60 |
0.531 |
689 |
32.5 |
87.0 |
0.89 |
80 |
0.517 |
624 |
40.9 |
79.6 |
0.88 |
100 |
0.431 |
567 |
49.3 |
33.5 |
0.93 |
SPU-88
|
1 |
1.393 |
1792 |
11.0 |
149 |
0.91 |
5 |
0.807 |
1149 |
30.0 |
126 |
0.87 |
10 |
0.545 |
681 |
44.7 |
81.2 |
0.89 |
20 |
0.358 |
401 |
64.2 |
79.8 |
0.90 |
40 |
0.198 |
320 |
76.4 |
73.0 |
0.88 |
60 |
0.184 |
263 |
112 |
54.0 |
0.90 |
80 |
0.162 |
149 |
176 |
31.0 |
0.91 |
100 |
0.126 |
76 |
213 |
24.0 |
0.93 |
SPU-97
|
1 |
1.270 |
1669 |
12.2 |
135 |
0.88 |
5 |
0.741 |
1015 |
40.4 |
88.9 |
0.91 |
10 |
0.490 |
579 |
69.0 |
82.0 |
0.88 |
20 |
0.354 |
377 |
74.3 |
78.0 |
0.88 |
40 |
0.171 |
263 |
142 |
27.5 |
0.91 |
60 |
0.135 |
168 |
175 |
26.2 |
0.91 |
80 |
0.126 |
103 |
225 |
25.0 |
0.93 |
100 |
0.110 |
56 |
228 |
23.0 |
0.92 |
The variation of IE in the temperature range from 25 to 65 °C for SPU-60 at 1 and 10 ppm is represented in Fig. 4c. It is apparent from the figure that in case of 1 ppm of inhibitor IE linearly increases with temperature from 42 to 53.5% and at 10 ppm it increases from 71.3 to 80.4%. The increase in IE with temperature is an indication of the inhibitor being chemically adsorbed on the metal surface. The values of apparent activation energy (Ea) were calculated from the linear Arrhenius plots of log CR versus 1/T in the absence and presence of 0, 1 and 10 ppm of the inhibitor and recorded in Table 2. The values of standard enthalpy of activation (ΔH°) and standard entropy of activation (ΔS°) were calculated using the following equation:
|  | (4) |
where, the terms have usual meaning. The plot of log (
CR/
T)
versus 1/
T yielded straight lines with a slope of (−Δ
H°/
2.303R) and an intercept of [{log (
R/
Nh) + (Δ
S°/
2.303R)]. The values of Δ
H° and Δ
S°, thus obtained, are recorded in
Table 2. Comparatively lower values of
Ea obtained in the presence of
inhibitor indicate that the
inhibitor is chemically adsorbed.
40 The heat released during chemisorption of the
inhibitor influences the corrosion process and consequently the observed
Ea value is lowered. The decrease in Δ
S° on addition of
inhibitor to the blank solution indicates that the activated complex is more ordered in the presence of the
inhibitor.
41,42
Table 2 Thermodynamic activation parameters for mild steel in 0.5 M H2SO4 in the presence and in absence of SPU-60
Thermodynamic parameters |
0.5 M H2SO4 |
SPU-60
|
1 ppm |
10 ppm |
E
a (kJ mol−1) |
34.12 |
29.63 |
26.51 |
ΔH° (kJ mol−1) |
31.53 |
29.02 |
23.89 |
−ΔS° (J mol−1K−1) |
130.50 |
150.30 |
166.75 |
−ΔstackGadso (kJ mol−1) |
- |
53.65 |
50.84 |
Potentiodynamic polarization measurements:
The influence of inhibitors on the kinetics of the partial cathodic and anodic reactions was evaluated from potentiodynamic polarization experiments. Fig. 5a exhibits the Tafel polarization curves for mild steel in 0.5 M H2SO4 solution containing 60 ppm of each of the inhibitor (SPU-97, SPU-88, SPU-60 and SPU-48) and in blank (0.5 M H2SO4). It is apparent from the figure that the addition of SPUs shifts the Ecorr slightly in the negative direction to the extent of ~30 mV or less and reduces both the anodic and the cathodic current densities. The observed variation in Ecorr is much less than ±85 mV and hence it cannot be classified as anodic or cathodic inhibitor.43,44 Further, the decrease in anodic and cathodic current densities at a given applied potential indicates that these polymers inhibit both the reduction of hydrogen ion as well as the dissolution of metal.
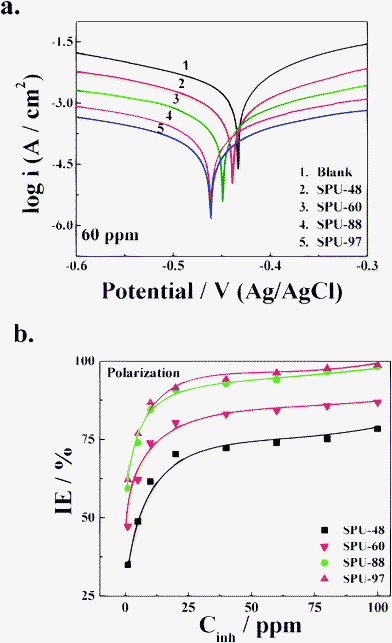 |
| Fig. 5 Potentiodynamic polarization measurements for mild steel in the absence and presence of inhibitors (a) tafel polarization curves and (b) inhibition efficiency as a function of inhibitor concentrations and degree of sulfonation. | |
The IE values of SPUs were calculated from Icorr values listed in Table1, using the relation;
|  | (5) |
where,
I˚corr and
Icorr are the corrosion current densities in the absence and presence of
inhibitors, respectively. A plot of
IE as a function of both
inhibitor concentration and that of
DS is illustrated in
Fig. 5b. On comparison of these curves with those in
Fig. 4a, it is observed that there is a good agreement between the two. However, the
IE obtained from gravimetric analysis is slightly lower than those from Tafel extrapolation method due to electrically accelerated adsorption under a potential field in the later case. The inhibition efficiency of 94% has been achieved using just 40 ppm of the
ionomer (SPU-97). The maximum efficiency of 77, 72 and 76% have earlier been reported using 280 ppm of polyacrylic acid,
17 100 ppm of recycled polyethyleneterphethalate
45 and 100 ppm of polyethyleneimine,
46 respectively. This work reports the highest ever efficiency using any thermoplastic as corrosion
inhibitor.
EIS measurements were performed to determine the impedance parameters of the mild steel/sulfuric acid interface in the absence and presence of various concentrations of different SPUs. Fig. 6a illustrates the Nyquist plots obtained at 0 and 10 ppm of SPU-48, SPU-60, SPU-88 and SPU-97, respectively. The EIS data were analyzed in terms of equivalent circuit shown in Fig. 6b which is a parallel combination of the charge transfer resistance (Rct) and the constant phase element of double layer (CPEdl), both in series with the solution resistance (Rs). The impedance of CPEdl is described by the expression: |  | (6) |
where, Y0 is a proportionality factor and n has the meaning of phase shift. The impedance spectra were similar for all the inhibitors, exhibiting a single depressed semicircle. The slight deviation of the capacitive loop from an ideal semicircle is brought about by surface roughness and is known as dispersion effect.47 It is clearly seen that the addition of different SPUs leads to an increase in the diameter of the semicircles. The values of Rct and CPEdl were calculated by ZSimpWin software 3.22d. The %IE was calculated from Rct values in the absence and presence of inhibitor using an equation similar to eqn (3) and (4).
 |
| Fig. 6 Impedance diagrams for mild steel in absence and presence of 10 ppm of different indicated inhibitors (a) Nyquist overlay plots and (b) equivalent electrical circuit. | |
The data obtained as above are presented in Table 1. It is observed from the data that the value of Rct increases and value of capacitance decreases with increasing DS and concentrations of the inhibitors. The increase in Rct and decrease in capacitance values can be attributed to a decrease in local dielectric constant and/or to an increase in the thickness of the electrical double layer, suggesting that the inhibitor molecules are adsorbed at the metal/solution interface.48 The maximum IE observed is 98%, which also indicates that the inhibitor molecules have the capability of forming a compact adsorbed layer over the metal surface.
It is generally accepted that mechanism and nature of the corrosion inhibition process can be explained in terms of the adsorption characteristics of the inhibitor molecules.49 The data obtained from electrochemical polarization measurements were used to determine the adsorption characteristics of SPUs on mild steel in 0.5 M H2SO4 solution. The values of surface coverage (θ) for various concentrations of all the inhibitors have been evaluated from the equation; |  | (7) |
where the terms have usual meanings. Several adsorption isotherms were applied to fit the surface coverage values at different concentrations of all the inhibitors. The surface coverage data fitted very well only in Langmuir eqn (8) and in all other cases large deviations were observed. |  | (8) |
where, Kads is the adsorption coefficient, Cinh is the molar concentration of the inhibitor. Fig. 7 represents the Langmuir isotherm plots for all the inhibitors. In the absence of exact molecular weight (discussed afterwards), the concentration of inhibitor has been expressed in terms of ppm. It is seen from the figure that all the inhibitors show a linear relationship between Cinh/θ versus Cinh and their slope values are 1.27, 1.14, 1.01, and 1.00 for SPU-48, SPU-60, SPU-88, and SPU-97, respectively. The deviation in slope values from unity is related with their IE values. Larger the IE of the inhibitor, smaller is the deviation from unity. The ideal slope value of 1(unity) indicates almost 100% inhibition efficiency of SPU-97 which we confirmed from the IE experiment earlier (Fig. 5b). Thus, it is evident that the deviation from unity is a function of surface heterogeneity and the degree of heterogeneity on that surface will be more which corrodes faster or where inhibition is less.32 The values of Kads are determined from the intercept of these plots and are 0.287, 0.486, 0.620 and 0.670 for SPU-48, SPU-60, SPU-88, and SPU-97, respectively. The values of Kads were found to increase with increase in DS which again suggests that SPU-97 is most strongly adsorbed on the metal surface followed by SPU-88, SPU-60 and SPU-48. The standard free energy of adsorption (ΔstackGadso) was calculated using the following expression: |  | (9) |
where 55.5 is the molar concentration of the water in the solution. The negative value of free energy of adsorption indicates spontaneous adsorption of the inhibitor molecules on the mild steel surface. Further, the value of free energy of adsorption less than −40 kJ mol−1 shows that the inhibitor molecules are chemically adsorbed on the mild steel surface.50
Evidence of surface coverage:
SEM
photomicrographs for mild steel in 0.5 M H2SO4 in the absence and presence of 5 and 60 ppm of SPU-88 have been presented in Fig. 8. The morphology of the mild steel specimen in the absence of inhibitor is very rough and the surface is damaged due to metal dissolution. However, the presence of as low as 5 ppm of inhibitor suppresses the rate of corrosion and surface damage has been diminished considerably as compared to the blank material (Fig. 8b). This effect is attributed to the formation of a protective inhibitor film at the metal surface. At 60 ppm of SPU-88, it has been found that the smoothness of the surface improved remarkably and the metal surface is almost free from corrosion due to better coverage of the metal surface (Fig. 8c). Hence, the surface coverage increases with the concentration of the inhibitor for a particular DS.
 |
| Fig. 8
SEM micrographs of electrodes after electrochemical measurements (a) blank, (b) 5 ppm SPU-88 and (c) 60 ppm SPU-88. | |
Further, the surface morphology of the mild steel specimens was studied by atomic force microscopy which also predicts the same trend as in SEM micrographs. Fig. 9 (a–c) show the 3D AFM micrographs of the mild steel samples in 0.5 M H2SO4 containing 5 and 60 ppm of SPU-88 and 60 ppm of SPU-48, respectively. The relative roughness has been plotted in Fig. 9d which also indicates smoother surface for higher DS at higher concentration. Average roughness factors have been calculated using the software and are 127, 78 and 52 nm for SPU-88 5 ppm, SPU-48 60 ppm and SPU-88 60ppm, respectively. The smoothening of the surface was caused by the deposition of the inhibitor molecules on the surface which protects the surface from the attack of corrosive medium. For a particular DS (e.g SPU-88), surface smoothening takes place with increasing concentration of inhibitor. Further, enhanced surface smoothening occurs for higher DS for a particular concentration of (e.g. 60 ppm) of the inhibitor. Hence, both SEM and AFM studies of the metal surface coverage support the results obtained from other techniques.
 |
| Fig. 9
AFM
micrographs of electrodes after electrochemical measurement for various SPU as inhibitor (a) 5 ppm SPU-88, (b) 60 ppm SPU-88, (c) 60 ppm SPU-48 and (d) the relative roughness of the surfaces from the above three micrographs. | |
The effect of modification on chain structure:
In the previous section, we observed significant surface coverage using sulfonated PU and it regularly increased with concentration and DS. Usually the larger size of polymeric chains has advantage to wrap the metal surface in a better way for corrosion inhibition. In order to understand the molecular size, GPC has been conducted before and after the sulfonation. The synthesized pure PU shows single peak while all the sulfonated PUs exhibit two distinct peaks at higher and lower elution time as compared to pure PU indicating the higher and low molecular weight fraction of the sulfonated polymers (Fig. 10a). The main peak of pure PU gradually vanishes and the peaks at lower and higher elution time are prominent with increasing DS. In particular, around 30,400 (=Mw) molecular weight of pure PU has been split into 95,000 and 3500 molecular weight after sulfonation in SPU-48. The molecular weight details have been presented in Table 3. The breakage (low molecular weight species) and formation of higher molecular weight polymer chain is presumably due to the nucleophilic attack by hydride ions during sulfonation followed by its addition to ester linkage of the other molecule. The mechanism has been shown in Scheme 2. The appearance of extra peak at elution time of about 550 s just after NaH treatment (without any sulfonating agent) confirms the nucleophilic addition leading to bigger chain size (Fig. 10b). Furthermore, both the lower and higher elution time peaks gradually shift towards higher time with increasing DS. It is mainly due to additional breakage of polymer chain when treated with higher concentration of sodium hydride (Fig. 10a). However, the ionic group and larger molecules, arising from sulfonation, help increasing the surface coverage and thereby the inhibition efficiency.
 |
| Fig. 10
Gel permeation chromatograms of (a) pure PU and indicated SPUs, (b) comparison of molecular weight with PU treated with NaH for 45 min. | |
 |
| Scheme 2 Schematic representation showing the evolution of lower and higher molecular weight species during sulfonation. | |
Table 3 Molecular weight of polymers as measured using GPC. Number within bracket indicates the percentage of the respective peak.
Sample |
Mw |
Peak I |
Peak II |
PU
|
30421 |
|
SPU-48
|
95901 (39) |
3248 (61) |
SPU-60
|
51569 (42) |
2854 (58) |
SPU-88
|
47172 (45) |
2313 (55) |
SPU-97
|
41468 (20) |
1947 (80) |
The absorbance in UV-Vis range has increased for sulfonated SPUs especially beyond 300 nm. The strong peak at 275 nm is attributed to benzene π→π∗ transition and remains same for pure and sulfonated polymer.51 Interestingly, the said peak becomes wider and an additional small peak appeared in tail part of sulfonated PUs presumably due to n→π∗ transition of sulfonate group and the peak gradually shifts52 to 334 nm for SPU-97 (Fig. 11). The red shift of the absorption peak indicates enhanced interaction of sulfonate group with rest of the polymer chains, mainly urethane linkage through dipole–dipole interaction with increasing degree of sulfonation. Hence, sulfonated PUs have more UV absorbing capabilities and, are thus, suitable as coating materials and demonstrate better interaction in ionomers.
 |
| Fig. 11
UV-Vis spectrum of pure polyurethane and indicated sulfonated PU. The Y-axes have been shifted for better clarity. | |
Quantum chemical calculations:
To understand the varying inhibition depending on degree of sulfonation, electronic structure calculations have been performed. Fig. 12 shows the frontier molecular orbital (highest occupied molecular orbital, HOMO) density distributions of (a) pure polyurethane and (b) sulfonated inhibitor (SPU). It is found that the electron density of HOMO for the pure PU unit is localized mainly on two benzene with small contribution from diisocyanate, while for the polymer with sulfonate group (SPU), the electron density of HOMO is localized predominantly on the sulfonate group. This indicates that the bonding of sulfonated inhibitor unit with metal containing vacant d-orbital will be more facile when compared to bonding though benzene ring in absence of sulfonate group. Our calculations reveal that the inhibitor adsorption further increases with increasing degree of sulfonation and hence the inhibition efficiency. To understand the effect of degree of sulfonation on inhibition efficiency, we have computed the HOMO–LUMO energy gap. Often, EHOMO refers to the tendency of inhibitor to donate electrons to vacant metal orbital. Higher value of EHOMO indicates greater electron donation tendency and, hence, stronger bond formation. On the other hand, lower value of ELUMO indicates more probable electron acceptance of the molecule. This will also be strengthening bond by accepting back donated electrons from metal. The energy gap ΔE(=ELUMO−EHOMO) is thereby an important parameter for determining reactivity of the inhibitor molecules towards the adsorption on metallic surface. The reactivity of the inhibitor molecule increases with decreasing ΔE, promoting the greater inhibition efficiency of the molecule.53,54 It is clear from Table 4 that the HOMO–LUMO energy gap decreases with increase in degree of sulfonation. Therefore, the reactivity of the inhibitor molecule for adsorption on metallic surface increases with increasing degree of sulfonation. It is to be noted that the inhibition reactivity rises very steeply when first sulfonate group is attached (~25% of sulfonation). This is based on the fact that the change in ΔE is highest when first sulfonate group is attached. The inhibition reactivity rises slowly thereafter on further sulfonation of the polymer as confirmed from the decreasing value of ΔE. Thus, the electronic structure calculations envisage the orbital density distribution of HOMO of the polymer molecule with and without the chemical modification and predict the electron donating capability of ionomer with varying degree of sulfonation. Our theoretical findings of increase in inhibition efficiency with increasing degree of sulfonation corroborate the experimental observations as mentioned earlier. However, nearly 100% inhibition efficiency has been achieved using low concentration (20 ppm) of chemically modified thermoplastic polymer like polyurethane. The same idea may be extended to other thermoplastics for corrosion inhibition. Further, it has been demonstrated the cause of inhibition both experimentally and theoretically. Brittleness and poor adherence of small molecular/π conjugated macromolecules have been resolved by using ionomers of thermoplastic.
 |
| Fig. 12 Frontier molecular orbital density: HOMO of (a) PU and (b) SPU (with single sulfonate group). A part of the chain is truncated to improve the clarity. | |
Table 4 Frontier molecular orbital energies of inhibitor molecules
Compounds |
Energy (Hartree) of frontier MOs |
Difference (ΔE) in Hartree |
Difference (ΔE) in kcal/mol |
PU
|
HOMO = −0.20595 LUMO=−0.00382 |
0.20213 |
126.8 |
SPU (1 sulphonate group) |
HOMO=−0.07568 LUMO=0.01457 |
0.09025 |
56.6 |
SPU (2 sulphonate group) |
HOMO=−0.04218 LUMO=0.04374 |
0.08592 |
53.9 |
Conclusion
A series of sulfonated polyurethanes have been synthesized and used as corrosion inhibitors for mild steel in 0.5 M sulfuric acid medium. The degree of sulfonation was controlled by using different weight ratios of the sulfonating agent to the urethane linkage of PU. The results of NMR and FTIR studies confirmed that sulfonation occurred at the secondary amine groups in the urethane linkages of PU chains. The results of weight loss and electrochemical measurements show that SPU has an excellent inhibiting property for acidic corrosion of mild steel. The inhibition efficiency of all the SPUs increased with increasing the polymer concentration and reached to its maximum at 100 ppm in all the cases. At the same concentration of the polymer; inhibition efficiency increases in the order SPU-48 < SPU-60 < SPU-88 < SPU-97 and reached almost 100% efficiency for SPU-97. This is generally attributed to the increase in the number of adsorption sites which allow higher inhibition. Potentiodynamic polarization measurements showed that all the SPUs function as mixed-type inhibitors, retarding both anodic and cathodic reactions at the same time. The results obtained from different techniques were in good agreement with each other. The relative surface coverage of sulfonated PUs has been verified by using SEM and AFM measurements. During the sulfonation process, the molecular weight increases significantly causing better surface coverage and thereby the inhibition efficiency of PUs. The appearance of a new peak in UV-visible spectra confirms the sulfonaton and its red shift with increasing DS indicates better interaction with rest of the molecules. The density distributions of the frontier molecular orbital HOMO of the inhibitor molecules obtained from quantum chemical calculations indicate the gradual increase in the relative inhibition with increasing degree of sulfonation which is in accord with the experimental observation.
Acknowledgements
The authors acknowledge the receipt of research funding from Council of Scientific and Industrial Research (CSIR) Project No. 22(0399)/06/EMR-II). The authors also acknowledge the kind support of Prof. A.S.K Sinha, and Niraj Vishwakarma of Banaras Hindu University for FTIR and GPC measurements.
References
- D. M. Strickland, Ind. Eng. Chem., 1923, 15, 566 CrossRef CAS.
- J. D. Hatfield, A. V. Slack, G. L. Crow and H. B. Shaffer Jr., J. Agric. Food Chem., 1958, 6, 524 CrossRef CAS.
- W. Guo, S. Chen, Y. Feng and C. Yang, J. Phys. Chem. C, 2007, 111, 3109 CAS.
- S. Lyon, Nature, 2004, 427, 406 CrossRef CAS.
- I. R. Glasgow, A. J. Rostron and G. Thomson, Corros. Sci., 1966, 6, 469 CAS.
- N. Hackerman, Langmuir, 1987, 3, 922 CrossRef CAS.
- P. G. Cao, J. L. Yao, J. W. Zheng, R. A. Gu and Z. Q. Tian, Langmuir, 2002, 18, 100 CrossRef CAS.
- D. D. N. Singh, M. M. Singh, R. S. Chaudhary and C. V. Agarwal, Electrochim. Acta, 1981, 26, 1051 CrossRef CAS.
- K. T. Carron, G. Xue and M. L. Lewis, Langmuir, 1991, 7, 2 CrossRef CAS.
- A. Popova, S. Raicheva, E. Sokolova and M. Christov, Langmuir, 1996, 12, 2083 CrossRef CAS.
- M. M. Singh, R. B. Rastogi, B. N. Upadhyay and M. Yadav, Mater. Chem. Phys., 2003, 80, 283 CrossRef CAS.
- K. Babic-Samardzija, C. Lupu, N. Hackerman and A. R. Barron, J. Mater. Chem., 2005, 15, 1908 RSC.
- D. Turcio-Ortega, T. Pandiyan, J. Cruz and E. Garcia-Ochoa, J. Phys. Chem. C, 2007, 111, 9853 CAS.
- E. E. Oguzie, S. G. Wang, Y. Li and F. H. Wang, J. Phys. Chem. C, 2009, 113, 8420 CAS.
- R. Solmaz, G. Kardas, M. Culha, B. Yazici and M. Erbil, Electrochim. Acta, 2008, 53, 5941 CrossRef CAS.
- P. Manivel and G. Venkatachari, J. Appl. Polym. Sci., 2007, 104, 2595 CrossRef CAS.
- M. A. Amin, S. S. Abd El-Rehim, E. E. F. El-Sherbini and O. A. Hazzazi, Corros. Sci., 2009, 51, 658 CrossRef CAS.
- A. Chetouani, K. Medjahed, K. E. Sif-Lakhdar, B. Hammouti, M. Benkaddour and A. Mansari, Corros. Sci., 2004, 46, 2421 CrossRef CAS.
- C. Jeyaprabha, S. Sathiyanarayanan, K. L. N. Phani and G. Venkatachari, Appl. Surf. Sci., 2005, 252, 966 CrossRef CAS.
- C. Jeyaprabha, S. Sathiyanarayanan, K. L. N. Phani and G. Venkatachari, J. Electroanal. Chem., 2005, 585, 250 CrossRef CAS.
- V. Srivastava, S. Banerjee and M. M. Singh, J. Appl. Polym. Sci., 2010, 116, 810 CAS.
- Y. Jianguo, W. Lin, V. Otieno-Alego and D. P. Schweinsberg, Corros. Sci., 1995, 37, 975 CrossRef CAS.
- M. A. Abd El-Ghaffar, E. A. M. Youssef, W. M. Darwish and F. M. Helaly, J. Elastomers Plast., 1998, 30, 68 CAS.
- H. Bhandari, V. Choudhary and S. K. Dhawan, Polym. Adv. Technol., 2008, 20, 1024 CrossRef.
- S. Prakash, C. R. K. Rao and M. Vijayan, Electrochim. Acta, 2008, 53, 5704 CrossRef CAS.
-
T. Thomson, Polyurethanes as Specialty Chemicals: Principles and Applications, CRC Press: Boca Raton, 2005. Search PubMed.
-
Z. Wirpsza, Polyurethanes: Chemistry, Technology and Application, Harwood Publs.: New York, 1993. Search PubMed.
- G. A. Abraham, A. A. A. de Queiroz and J. S. Roman, Biomaterials, 2001, 22, 1971 CrossRef CAS.
- A. Mishra, V. K. Aswal and P. Maiti, J. Phys. Chem. B, 2010, 114, 5292 CrossRef CAS.
- A. Mishra, B. P. D. Purkayastha, J. K. Roy, V. K. Aswal and P. Maiti, Macromolecules, 2010, 43, 9928 CrossRef CAS.
- S. R. Williams, W. Wang, K. I. Winey and T. E. Long, Macromolecules, 2008, 41, 9072 CrossRef CAS.
- S. Banerjee, A. Mishra, M. M. Singh and P. Maiti, J. Nanosci. Nanotechnol., 2011, 11, 966 CrossRef CAS.
- P. Maiti, G. Radhakrishnan, P. Aruna and G. Ghosh, Macromol. Symp., 2006, 24, 51 CrossRef.
- T. G. Grasel and S. L. Cooper, J. Biomed. Mater. Res., 1989, 23, 311 CrossRef CAS.
-
M. J. Frisch, G. W. Truncks, and H. B. Schlegel, GAUSSIAN 03, Revision E.01,Gaussian Inc., Wallingford, CT, 2007 Search PubMed.
- K. M. Zia, M. Barikani, I. A. Bhatti and M. Zuber, J. Appl. Polym. Sci., 2008, 109, 1840 CrossRef CAS.
- B. O. Jung, J. Na and C. H. Kim, J. Ind. Eng. Chem., 2007, 13, 772 CAS.
- Z. Shi and S. Holdcroft, Macromolecules, 2005, 38, 4193 CrossRef CAS.
- S. Ramesh and G. Radhakrishnan, Eur. Polym. J., 1995, 32, 993 CrossRef.
- T. Szauer and A. Brandt, Electrochim. Acta, 1981, 26, 1209 CrossRef CAS.
- S. Martinez and I. Stern, Appl. Surf. Sci., 2002, 199, 83 CrossRef CAS.
-
J. Marsh, Advanced Organic Chemistry, Third Edition, Wiley Eastern: New Delhi, 1988 Search PubMed.
- Y. Yana, W. Li, L. Cai and B. Hou, Electrochim. Acta, 2008, 53, 5953 CrossRef.
- X. Li, S. Deng and H. Fu, Corros. Sci., 2011, 53, 302 CrossRef CAS.
- M. A. Migahed, A. M. Abdul-Raheim, A. M. Atta and W. Brostow, Mater. Chem. Phys., 2010, 121, 208 CrossRef CAS.
- M. Finsgar, S. Fassbender, F. Nicolini and I. Milosev, Corros. Sci., 2009, 51, 525 CrossRef CAS.
- E. Maccafferty, Corros. Sci., 1997, 39, 243 CrossRef.
- M. Ozcan, I. Dehri and M. Erbil, Appl. Surf. Sci., 2004, 236, 155 CrossRef CAS.
- F. E. Heakal and A. M. Fekry, J. Electrochem. Soc., 2008, 155, 534 CrossRef.
- M. Bouklah, B. Hammouti, M. Lagrenee and F. Bentiss, Corros. Sci., 2006, 48, 2831 CrossRef CAS.
- L. Sacconi, M. Ciampolini and U. Campigli, Inorg. Chem., 1965, 4, 407 CrossRef CAS.
- M. Tumer, H. Koksal and S. Serin, Inorg. Met. Org. Chem., 1997, 27, 775 CrossRef CAS.
- Y. Yan, W. H. Li, L. K. Cai and B. Hou, Electrochim. Acta, 2008, 53, 5953 CrossRef CAS.
- X. Li, S. Deng, H. Fu and T. Li, Electrochim. Acta, 2009, 54, 4089 CrossRef CAS.
|
This journal is © The Royal Society of Chemistry 2011 |
Click here to see how this site uses Cookies. View our privacy policy here.