DOI:
10.1039/C1PY00311A
(Paper)
Polym. Chem., 2011,
2, 2893-2899
Preparation of hierarchical porous polypyrrole nanoclusters and their application for removal of Cr(VI) ions in aqueous solution†
Received
10th July 2011
, Accepted 5th October 2011
First published on 19th October 2011
Abstract
Hierarchical porous polypyrrole (PPy) nanoclusters composed of small PPy nanospheres were successfully prepared in one-step by a reactive-template method without any surfactants. The Fe3O4 nanoclusters acted as both the template for shaping PPy structure and oxidant source simultaneously. The dosage of pyrrole monomer, the concentration of HCl acid had significant influence on the structures and conductivities of the resulting PPy nanoclusters. By carefully controlling the experimental conditions, hierarchical porous PPy nanoclusters with the surface area as high as 104 m2 g−1 were obtained. The value was about 3.5 times larger than that of traditional PPy nanoparticles. Based on the transmission electron microscope (TEM) images and Fourier-transform infrared (FT-IR) spectra, a possible formation mechanism was proposed and investigated in detail. To test the feasibility of using the PPy nanoclusters in real applications, the capacity of nanoclusters as a heavy metal ion remover was explored. The resulting PPy nanoclusters showed an excellent ability to remove Cr(VI) ions in aqueous solution.
Introduction
Conducting polymers have received considerable attention in the past few decades owing to their potential applications in biomedicine, actuators, electrochromic devices, and field effect transistors.1–4 Among various conducting polymers, polypyrrole (PPy) stands out due to its ease of synthesis, good biocompatibility, high conductivity, and excellent redox properties.5–8 Nowadays, there is an increasing interest in design and synthesis of PPy nanostructures, because of their superior properties, compared with their bulk counterparts, in conductivity, response time, and especially in surface area.9,10 As is known to us, the surface area is an important factor for the applications of PPy nanostructures in chemical sensors, batteries and adsorbents.11–13
There are many different routes to synthesize nanostructured PPy, including hard-template method, soft-template method, template-free method and electrochemical method.14–17 Among these strategies, hard-template method is the most frequently used approach. Compared with other routes, it is easier to control the morphologies, structures and sizes of PPy nanostructures. However, the major drawback of hard-template method is that the template-removing step is usually needed to liberate pure polymers, which results in a complex experimental process and destruction of resulting nanostructures.18–20 To overcome the weakness, Wan and co-workers have selected octahedral Cu2O as a template to synthesize corresponding hollow octahedral polyaniline microcapsules. Since soluble Cu2+ ions were produced by the reaction of Cu2O with oxidant, the need for post-process template removal was eliminated. This was so-called reactive-template method.21 It was a simple, one-step procedure, because the reactive-template was converted to the soluble ions during the polymerization process. As a result, no special purification steps were required in order to obtain the pure conducting polymers.
Recently, hierarchical porous nanomaterials have drawn more and more attention, because their surface area is usually much larger than traditional nanomaterials, including nanoparticles, nanocapsules and nanofibers.22–24 In this paper, we report a reactive-template method for preparation of hierarchical porous PPy nanoclusters in one step without any surfactants. The nanoclusters displayed large surface area and high conductivity. In the reaction system, the Fe3O4 nanoclusters acted as both the template for shaping PPy structure and initiator source simultaneously. The influence of pyrrole monomer dosage and HCl acid concentration on the structure and conductivity of the nanoclusters has been examined in detail. The formation mechanism was well suggested and discussed elaborately. As commonly known, Cr(VI) ion is one of the most toxic heavy metal ions, and is found to be carcinogenic.25 Since Rajeshwar and co-workers firstly reported PPy film could reduce Cr(VI) ions to less toxic Cr(III) ions,26 the application of PPy nanomaterials in heavy metal ion removal was intensively studied.27–30 To test the feasibility of using the PPy nanoclusters in real applications, we investigated their properties as a Cr(VI) ion remover. Compared with commercial activated carbon and traditional PPy nanoparticles, the resulting PPy nanoclusters exhibited outstanding ability to remove Cr(VI) ions. Thus, these porous PPy nanoclusters could be used as environmentally friendly materials for the removal of Cr(VI) ions in aqueous solution.
Experimental
Materials
Pyrrole monomer was purchased from Sigma-Aldrich, and was distilled under reduced pressure and stored at −4 °C prior to use. Poly(N-vinylpyrrolidone) (PVP), trisodium citrate, sodium acetate, hydrochloric acid (HCl, 38 wt%), ammonium hydroxide (NH3·H2O, 28 wt%), FeCl3, FeCl3·6H2O, FeCl2·4H2O, K2Cr2O7, NaOH and ethylene glycol were obtained from Sinopharm Chemical Reagent Co., Ltd. All of them were analytical grade and used as received. The activated carbon with the surface area larger than 500 m2 g−1 was also purchased from Sinopharm Chemical Reagent Co., Ltd.
Preparation of PPy nanoclusters
Firstly, the Fe3O4 nanoclusters were synthesized according to the previous report.24 Subsequently, pyrrole monomer was dissolved in 6.0 mL deionized water, followed by the addition of Fe3O4 nanoclusters (0.75 mL, 8.0 mg mL−1). After mechanically stirring for 0.5 h, 8.0 mL HCl acid with a concentration of 1.0 M was added to the system. The color of the solution gradually turned from dark brown to black, indicating the polymerization of pyrrole monomer took place. The reaction was allowed to proceed with stirring for 8.0 h at room temperature. Finally, the products were washed with deionized water and ethanol until the filtrate became colorless.
Removal of Cr(VI) ions
The Cr(VI) ion determination was carried out spectrophotometrically using a calibration curve. The calibration curve was obtained from standard solutions of K2Cr2O7 (0 ∼ 3.4 mmol L−1) solution prepared at pH = 5.0. 10 mg PPy nanoclusters were added into 20 mL K2Cr2O7 solution with a concentration of 3.4 mmol L−1 at pH = 5.0, after magnetic stirring for a certain time, the solution was extracted for ultraviolet analysis to determine its concentration. Based on the calibration curve, the removal amount of Cr(VI) ions could be calculated.
Characterization
The structures of PPy and Fe3O4 nanoclusters were characterized using a JEOL-2010 transmission electron microscope (TEM) operating at 200 kV. Fourier-transform infrared (FT-IR) spectra were measured in wavenumbers ranging from 400 to 4000 cm−1 using a Nicolet Avatar 360 FT-IR spectrophotometer. A Lambda 750 UV-Vis-NIR spectrophotometer was employed for analysis of Cr(VI) ions. Brunauer–Emmett–Teller (BET) measurements were carried out to determine the surface area of PPy nanostructures. Nitrogen sorption measurements were performed by using a Micromeritics ASAP 2010M analyzer on the dried sample which had been degassed at 120 °C under vacuum. The conductivity of samples was measured by using a KDY-1 four-point probe analyzer. Before the test, the products were dried in a vacuum oven overnight and then pressed into disks at room temperature. X-ray diffraction (XRD) data were collected on a Siemens D-5005 X-ray diffractometer with Cu-Kα radiation (λ = 1.5418 Å).
Results and discussion
Morphology and structure
The structure of the as-prepared Fe3O4 nanoclusters was characterized by TEM images. As shown in Fig. 1a, the Fe3O4 nanoclusters are uniform and nearly spherical in shape with a diameter about 200 nm. From the margin of Fe3O4 nanoclusters in the magnified image (Fig. 1b), it can be seen that the obtained Fe3O4 nanoclusters consist of numerous small Fe3O4 nanospheres. Fig. 1c shows the TEM image of hierarchical porous PPy nanoclusters. They have good dispersity and uniform size of about 210 nm which almost equals the diameter of Fe3O4 nanoclusters. In comparison with Fe3O4 nanoclusters, the surface of PPy nanoclusters is much rougher and interior is much looser. A TEM image at higher magnification in Fig. 1d clearly reveals that the PPy nanoclusters are made up of the small PPy nanospheres with the size ranging from 40 to 65 nm. These constituent nanospheres connect with each other and many pores remain among them, which results in a hierarchical porous structure.
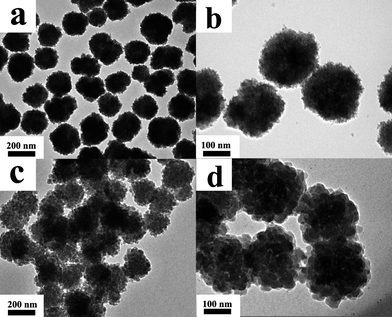 |
| Fig. 1 TEM images of (a) Fe3O4 nanoclusters; (b) Fe3O4 nanoclusters at higher magnification; (c) PPy nanoclusters; (d) PPy nanoclusters at higher magnification. | |
The chemical structures of the hierarchical porous PPy nanoclusters and Fe3O4 nanoclusters are characterized by FT-IR spectra as shown in Fig. 2. The main peaks for both of them in FT-IR spectra are in good agreement with the previous study.24,31,32 The PPy feature peaks can be distinguished clearly in curve (a). The characteristic bands at 1545 and 1471 cm−1 are attributed to the stretching mode of the C–C and C–N in the pyrrole ring. Besides this, ring deformation at 914 cm−1 is also observed. The peaks at 1308 and 1194 cm−1 are related to the in-plane vibrations of C–H. The band at 1042 cm−1 is assigned to the C–H in-plane bending mode and the peak at 786 cm−1 is attributable to C–H wagging vibration. Curve (b) displays the FT-IR spectrum of Fe3O4 nanoclusters. Two bands assignable to carboxyl group are observed at 1630 and 1393 cm−1. The peaks at 620 and 427 cm−1 are due to the stretching mode of Fe–O. The bands at 1028 and 3437 cm−1 are assigned to C–H and O–H vibrations, respectively. Compared spectrum (a) with (b), no feature peaks of Fe3O4 nanoclusters appeared in the spectrum of PPy nanoclusters, indicating the Fe3O4 nanoclusters were completely dissolved by HCl acid, and no residual Fe3O4 nanoclusters remained in resulting PPy nanoclusters.
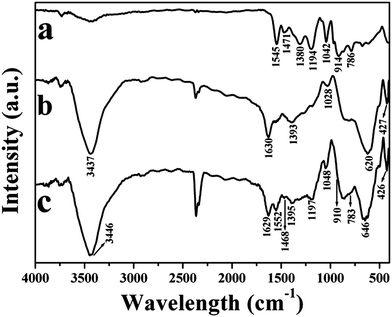 |
| Fig. 2 FT-IR spectra of (a) PPy nanoclusters; (b) Fe3O4 nanoclusters; (c) the Fe3O4/PPy core/shell nanoclusters after reaction for 40 min. | |
The XRD patterns of Fe3O4 and PPy nanoclusters are shown in Fig. 3. In Fig. 3a, six diffraction peaks appear at 2θ = 30.1, 35.4, 43.5, 53.4, 56.9 and 62.5°, which correspond to (220), (311), (400), (422), (511) and (440) Bragg reflections of face-centered cubic lattice of Fe3O4, respectively. The positions of all sharp peaks are in good agreement with those reported for Fe3O4 nanospheres (JCPDS no. 19-629). After reacting with pyrrole monomer in HCl acid for 8.0 h, the diffraction peaks of Fe3O4 nanoclusters vanish in Fig. 3b, which further suggests Fe3O4 nanoclusters are completely etched by HCl acid. XRD pattern reveals that the PPy nanoclusters obtained in this study are essentially amorphous, since a broad peak appears at 2θ = 24.2°, which is the characteristic of amorphous PPy caused by the scattering from their polymer chains at the interplanar spacing.33
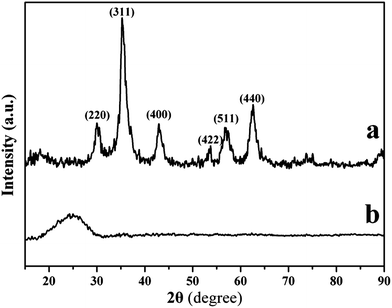 |
| Fig. 3 XRD patterns of (a) Fe3O4 nanoclusters and (b) PPy nanoclusters. | |
Effect of pyrrole monomer dosage
The volume of pyrrole monomer was believed to be able to adjust the morphologies of PPy nanoclusters. Fig. 4 shows the structures of PPy nanoclusters prepared in a solution that contains 8.0 mL HCl acid with a concentration of 1.0 M, 0.75 mL Fe3O4 nanoclusters, 6.0 mL H2O and different volume of pyrrole monomer. When pyrrole monomer volume is low, for example, 10 μL, the nanoclusters display hierarchical porous structure, which facilitates high surface area (Fig. 4a). BET results showed the surface area of hierarchical porous PPy nanoclusters was as high as 104 m2 g−1. When the volume of pyrrole monomer increases to 100 μL, the nanoclusters still exhibit a hierarchical structure. However, the interior of the PPy nanoclusters becomes compact and nearly no pores exist in it, as we can see in Fig. 4b. Their surface area has dramatically reduced to 30 m2 g−1, which was similar to the pure PPy nanoparticles.34 Compared hierarchical porous PPy nanoclusters with hierarchical imporous PPy nanoclusters, the surface area of the former was about 3.5 times larger than the latter (or pure PPy nanoparticles), indicating the porous structure had significant contribution to the high surface area. If the dosage of pyrrole monomer further increases to 300 μL, the interior of the PPy nanoclusters becomes more compact and the surface becomes smoother, which leads to the morphology of PPy nanoclusters gradually evolving from cluster-like to sphere-like (Fig. 4c). In addition, PPy aggregations appear around the nanoclusters (inset of Fig. 4c). Surprisingly, although the dosage of pyrrole monomer in Fig. 4c is about 30 times more than that in Fig. 4a, the diameters of nanoclusters in these three TEM images are nearly the same. All of them are about 210 nm, which is almost equal to the size of the original Fe3O4 nanoclusters. This was obviously different from the PPy nanomaterials prepared by the hard-template method. According to the previous reports,35–39 the diameter of PPy nanomaterials which were prepared by hard-template method increased with the increase of pyrrole monomer dosage. The reason will be discussed below.
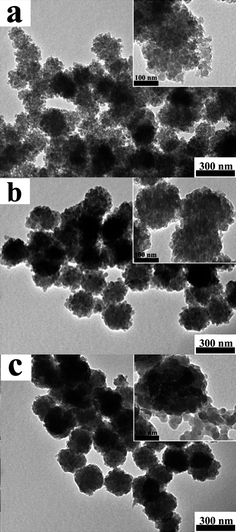 |
| Fig. 4 TEM images of PPy nanoclusters synthesized under different volume of pyrrole monomer, while other parameters were equal: (a) 10 μL; (b) 100 μL and (c) 300 μL. The insets showed the corresponding magnified images. | |
Effect of HCl acid concentration
In our study, the oxidant Fe3+ ions originated from dissolved Fe3O4 nanoclusters. The concentration of HCl acid had direct influence on the polymerization of pyrrole monomer, since it determined the release rate of oxidant Fe3+ ions. Fig. 5 demonstrates the structures of PPy nanoclusters as a function of HCl acid concentrations, while the dosage of pyrrole monomer maintains at 10 μL. When the concentration of HCl acid is 0.1 M, the PPy homopolymer only appears on the surface of Fe3O4 nanoclusters (Fig. 5a). The interior of the Fe3O4 nanoclusters is well-preserved, indicating Fe3O4 nanoclusters can not be completely dissolved by HCl acid under these conditions. With increasing HCl acid concentrations from 0.5 to 3.0 M, there seems to be no apparent difference between PPy nanocluster structures (Fig. 5b and c). Both of them exhibit the hierarchical porous structures that are similar to the TEM image in Fig. 4a. Further increase the concentration of HCl acid to 6.0 M, no PPy nanoclusters can be found and only PPy aggregations are observed in Fig. 5d. In this case, the Fe3O4 nanoclusters are quickly etched by HCl acid and they cannot serve as the template to shape the structure of the resulting PPy homopolymer. Therefore, pyrrole monomer polymerizes in solution and forms aggregations. Based on above results, it was easily concluded that the optimized concentrations of HCl acid for preparing PPy nanoclusters ranged from 0.5 to 3.0 M.
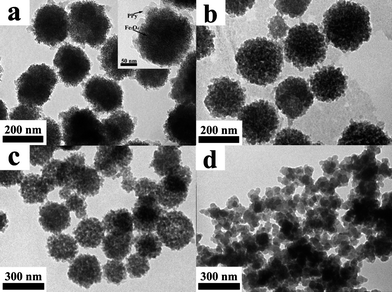 |
| Fig. 5 TEM images of PPy nanoclusters synthesized under different concentrations of HCl acid, while other parameters were equal: (a) 0.1 M, (b) 0.5 M, (c) 3.0 M and (d) 6.0 M. The PPy shell and Fe3O4 nanocluster were highlighted by arrows in the inset. | |
Conductivity
As a conducting polymer, the conductivity of PPy nanoclusters is a very important property. The dependence of conductivity on the dosage of pyrrole monomer, the concentration of HCl acid and raotio of peak areas at 1550 and 1470 cm−1 (A1550/A1470) has been summarized in Table 1. The conductivity of the samples shown in Fig. 4a–c (encode as sample 1, 2, and 3) is 0.64, 0.40 and 0.32 S cm−1, respectively. From the table, we could see their conductivities gradually declined. As we know, the conductivity of conducting polymer increased with the increase of the oxidant/monomer mole ratio.40 In our experiment, oxidant Fe3+ ions originated from the Fe3O4 nanoclusters. The dosage of Fe3O4 nanoclusters in all experiments were the same, therefore, the conductivity reduced with the increase of pyrrole monomer dosage.
Table 1 The conductivities of PPy nanoclusters under different polymerization conditions
Samples |
[HCl] (mol L−1) |
Pyrrole (μL) |
Conductivity (S cm−1) |
A
1550/A1470 |
Sample 1 |
1.0 |
10 |
0.64 |
3.65 |
Sample 2 |
1.0 |
100 |
0.40 |
5.50 |
Sample 3 |
1.0 |
300 |
0.32 |
6.10 |
Sample 4 |
0.1 |
10 |
1.4 × 10−3 |
— |
Sample 5 |
0.5 |
10 |
0.87 |
2.78 |
Sample 6 |
3.0 |
10 |
1.7 × 10−2 |
11.02 |
Sample 7 |
6.0 |
10 |
<1.0 × 10−4 |
— |
The samples 4–7 correspond to the products in Fig. 5a–d. With increasing the concentrations of HCl acid from 0.1 to 6.0 M, the conductivities of PPy nanoclusters sharply increased first and then steeply declined, exhibiting a maximum value of 0.87 S cm−1 in 0.5 M HCl acid solution. When the concentration of acid was low, the doping level of PPy became higher with the increase of HCl acid concentrations, consequently leading to the improvement of conductivity. However, if the concentration of acid was too high, severe cross-linking occurred in the polymer chain during the polymerization, which greatly destroyed the conjugate structure of PPy homopolymer, and hence reduced the conductivity.41 From the above data, it could be concluded that hierarchical porous PPy nanoclusters exhibited not only large surface area but also high conductivity. Compared with the dosage of pyrrole monomer, the concentrations of HCl acid had more significant influence on conductivity of PPy nanoculsters.
Besides the dosage of pyrrole monomer and concentrations of HCl acid, the molecular weight of conducting polymer also had great effect on the conductivities, as it determined the conjugation length in molecular chain.41,42 Therefore, the relationship between the molecular weight and conductivity was studied. The conjugation length could be measured by calculating the degree of delocalization. According to the previous report, the degree of delocalization was related to the ratio of peak areas at 1550 and 1470 cm−1, which was assignable to the C–C and C–N stretching vibrations in pyrrole ring, respectively (see Fig. S1 in ESI†). The measured value of A1550/A1470 was also listed in Table 1. It could be seen that the conductivities of PPy nanoclusters increased as the A1550/A1470 value reduced. A linear relationship existed between conductivity and A1550/A1470. The former was inversely proportional to the latter (see Fig. S2 in ESI†). From the above discussion, it could be concluded that the larger the molecular weight was, the longer the conjugated length was, and hence the higher the conductivity was.
Formation mechanism
In order to investigate the reaction mechanism, the products at different reaction stages were obtained to examine the structure evolution process of nanoclusters. Here, the volume of pyrrole monomer was fixed at 100 μL. Fig. 6 gives the TEM images of four stages that are taken from the reaction solution after HCl acid has been added. It was found that the structure of the PPy nanoclusters was affected by the polymerization time. At the early stage, for example, 5 min, the surface of Fe3O4 nanoclusters is slightly etched by HCl acid, and only a small amount of PPy nanoparticles with diameter around 10 nm appear on the surface of Fe3O4 nanoclusters (Fig. 6a). Upon further increasing the reaction time to 20 min, the PPy nanospheres connect with each other due to the increasing diameters, and eventually evolve into a thin shell around the Fe3O4 nanocluster surface (Fig. 6b). When the time extends to 40 min, the PPy nanospheres grow larger and larger, while the size of Fe3O4 nanoclusters becomes smaller and smaller. As shown in Fig. 6c, the diameter of Fe3O4 nanoclusters is reduced from original 200 to 150 nm. The FT-IR spectrum of the products after reaction for 40 min is presented in Fig. 2c. We can see that all the feature peaks of PPy nanoclusters and Fe3O4 nanoclusters appear. FT-IR spectrum, together with TEM image, indicated the Fe3O4/PPy core/shell composites had formed. As the reaction time prolongs to 60 min, the Fe3O4 nanoclusters are completely dissolved by HCl acid and the PPy nanoclusters have been prepared (Fig. 6d). From Fig. 6, it could be seen that the pyrrole monomer preferentially polymerizes from the surface to interior, which is in contrary to the previous report for preparation of PPy nanostructures by hard-template method.35–39
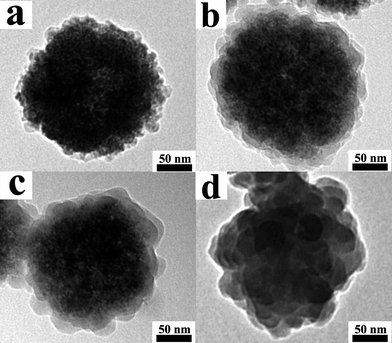 |
| Fig. 6 TEM images of PPy nanoclusters synthesized with different polymerization time: (a) 5.0 min; (b) 20 min; (c) 40 min and (d) 60 min. | |
In a control experiment, PPy nanocapsules instead of nanoclusters were prepared by using Fe3O4 nanoclusters as the hard-template and PVP as the stabilizer (see ESI†). It is necessary to point out that severe aggregations would appear without PVP molecules. As shown in Fig. 7, the resulting PPy nanocapsules display spherical shape with the external diameter of 260 nm. The thickness of shell is about 30 nm, while the inner diameter is around 200 nm which is the same as the diameter of Fe3O4 nanoclusters. Fig. 7 clearly indicated that the PPy nanoclusters could not be prepared by the hard-template method.
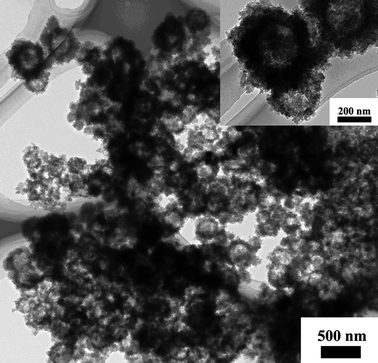 |
| Fig. 7 TEM image of hollow PPy nanocapsules prepared by the hard-template method. The inset showed the corresponding magnified image. | |
To further demonstrate why the PPy nanoclusters consisted of small PPy nanospheres, a control experiment was designed by a similar method to that for preparing PPy nanoclusters except that Fe3O4 nanoclusters were replaced by small Fe3O4 nanospheres (see Fig. S3a in the ESI†). After reacting with pyrrole monomer in HCl acid solution for 8.0 h, the Fe3O4 nanospheres were completely dissolved by HCl acid and the PPy nanospheres were synthesized (see Fig. S3b in the ESI†). The results indicated the PPy homopolymer tended to form a spherical shape by using Fe3O4 nanospheres as reactive-template. As mentioned above, The Fe3O4 nanoclusters were consisted of numerous Fe3O4 nanospheres (Fig. 1b). These Fe3O4 nanospheres acted as small reactive-templates, as a result, the final PPy nanoclusters were made up of small PPy nanospheres.
Based on the experimental results described above, a possible formation mechanism was proposed in Scheme 1. After addition of HCl acid into the reaction system, Fe3O4 nanoclusters were gradually etched from surface to the interior by HCl acid, and Fe3+ ions were released. The oxidative polymerization of pyrrole monomer was initiated by Fe3+ ions. After reaction proceeding for 1 h, the Fe3O4 nanoclusters were dissolved and PPy nanoclusters were prepared. When the dosage of pyrrole monomer was low, the resulting PPy homopolymer could not take up the total space inside the original Fe3O4 nanoclusters, therefore, porous structure was formed (Fig. 4a). If the dosage of pyrrole monomer was high, PPy homopolymer could completely take up the space inside the original Fe3O4 nanoclusters, the residual pyrrole monomer would react with Fe3+ ions diffused from the nanoclusters, and formed PPy aggregations (inset of Fig. 4c). The polymerization took place from the surface of Fe3O4 nanoclusters to interior, therefore, the diameters of resulting nanoclusters were the same as the original template, regardless of how much the pyrrole monomer was used.
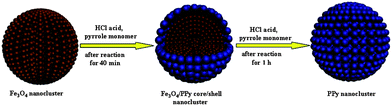 |
| Scheme 1 Schematic representation of the proposed PPy nanocluster formation mechanism. | |
Removal of Cr(VI) ions
The feasibility of the PPy nanoclusters as a Cr(VI) ion remover was explored. After adding the PPy nanoclusters into the solution, the concentration of Cr(VI) ions in solution was measured by UV-Vis-NIR spectrometer. Base on the calibration curve, the removal amount of Cr(VI) ions could be calculated.27Fig. 8 shows the removal capacity of Cr(VI) ions in the solution at different times. It can be seen that most of the removal occurs during the first 20 min. After 20 min, the removal capacity of Cr(VI) ions keep almost unchanged. The results indicated that the PPy nanoclusters could be used to quickly remove Cr(VI) ions in water.
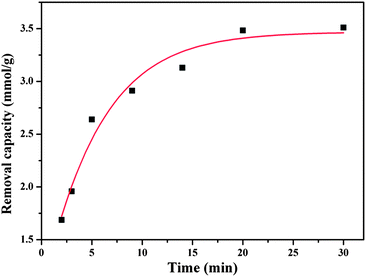 |
| Fig. 8 Removal capacity of Cr(VI) ions at different times (solution pH = 5.0). | |
The removal capacity of the PPy nanoclusters, activated carbon and PPy nanoparticles was compared. As shown in Fig. 9, the maximum removal capacity of Cr(VI) ions for PPy nanoparticles, activated carbon and PPy nanoclusters was 1.14, 1.83 and 3.47 mmol g−1, respectively. The removal capacity of PPy nanoclusters was higher than that of traditional PPy nanoparticles owing to their larger surface areas. Although the surface area of activated carbon (larger than 500 m2 g−1) was larger than that of PPy nanoclusters, the removal capacity of former was lower than the latter. For activated carbon, The Cr(VI) ion removal was mainly through physical adsorption.43,44 In comparison, for PPy nanoclusters, besides physical adsorption, the Cr(VI) ion could be chemically reduced to Cr(III) ion on their surface.25–30 From the above results, it could be concluded that the PPy nanoclusters had potential applications in Cr(VI) ion removal.
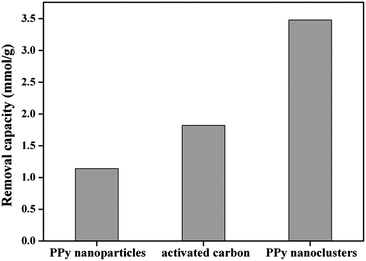 |
| Fig. 9 Maximum removal capacity of PPy nanoparticles, commercial activated carbon and PPy nanoclusters (solution pH = 5.0). | |
Conclusions
In summary, we have successfully synthesized hierarchical porous PPy nanoclusters by a reactive-template method. This exquisite structure could not be obtained by the hard-template method. Fe3O4 nanoclusters acted as both the template for shaping the PPy nanostructures and the oxidant source simultaneously. The procedure was one-step and avoided the need for post-process template removal. BET data showed that the PPy nanoclusters displayed a surface area as high as 104 m2 g−1 due to their special hierarchical porous structures. The dosage of pyrrole monomer played a crucial role for the formation of hierarchical porous structure. The optimized HCl acid concentrations for preparing PPy nanoclusters ranged from 0.5 to 3.0 M, and they had tremendous effect on the conductivities. The maximum removal amount of Cr(VI) ions for PPy nanoclusters was 3.47 mmol g−1 in aqueous solution at pH = 5.0. Their removal capacity was much higher than commercial activated carbon and traditional PPy nanoparticles, thus PPy nanoclusters exhibited potential applications in Cr(VI) ion removal.
Acknowledgements
This work has been supported by the National Natural Science Foundation of China (No. 21174033), the Fundamental Research Funds for the Central Universities (Grant Nos. HIT. NSRIF. 2009086, 2009082), the Open Project of State Key Laboratory of Supramolecular Structure and Materials (No. SKLSSM201111), the China Postdoctoral Science Foundation (Nos. 20090450978, 201003417) and the Heilongjiang Postdoctoral Science Foundation (No. LBH-Z09123).
References
- N. K. Guimard, N. Gomez and C. E. Schmidt, Prog. Polym. Sci., 2007, 32, 876 CrossRef CAS.
- G. Q. Shi, S. Jin, G. Xue and C. Li, Science, 1995, 267, 994 CAS.
- S. I. Cho, W. J. Kwon, S. J. Choi, P. Kim, S. A. Park, J. Kim, S. J. Son, R. Xiao, S. H. Kim and S. B. Lee, Adv. Mater., 2005, 17, 171 CrossRef CAS.
- J. A. Merlo and C. D. Frisbie, J. Phys. Chem. B, 2004, 108, 19169 CrossRef CAS.
- T. J. Yao, C. X. Wang, J. Wu, Q. Lin, H. Lv, K. Zhang, K. Yu and B. Yang, J. Colloid Interface Sci., 2009, 338, 573 CrossRef CAS.
- S. C. Wuang, K. G. Neoh, E. T. Kang, D. W. Pack and D. E. Leckband, Macromol. Rapid Commun., 2007, 28, 816 CrossRef CAS.
- H. Zhao, W. E. Price, P. R. Teasdale and G. G. Wallace, React. Polym., 1994, 23, 213 CrossRef CAS.
- D. G. Shchukin, K. Köhler and H. Möhwald, J. Am. Chem. Soc., 2006, 128, 4506 CrossRef.
- V. P. Menon, J. Lei and C. R. Martin, Chem. Mater., 1996, 8, 2382 CrossRef CAS.
- J. Jang, M. Chang and H. Yoon, Adv. Mater., 2005, 17, 1616 CrossRef CAS.
- H. D. Tran, K. Shin, W. G. Hong, J. M. D'Arcy, R. W. Kojima, B. H. Weiller and R. B. Kaner, Macromol. Rapid Commun., 2007, 28, 2289 CrossRef CAS.
- H. K. Song and G. T. R. Palmore, Adv. Mater., 2006, 28, 1764 CrossRef.
- M. M. Ayad and A. A. EI-Nasr, J. Phys. Chem. C, 2010, 114, 14377 CAS.
- C. R. Martin, Acc. Chem. Res., 1995, 28, 61 CrossRef CAS.
- H. D. Tran, D. Li and R. B. Kaner, Adv. Mater., 2009, 21, 1487 CrossRef CAS.
- M. X. Wan, Adv. Mater., 2008, 20, 2926 CrossRef CAS.
- H. Goto and K. Akagi, J. Polym. Sci., Part A: Polym. Chem., 2006, 44, 1042 CrossRef CAS.
- C. Laslau, Z. Zujovic and J. Travas-Sejdic, Prog. Polym. Sci., 2010, 35, 1403 CrossRef CAS.
- J. B. Fei, Y. Cui, X. H. Yan, Y. Yang, K. W. Wang and J. B. Li, ACS Nano, 2009, 3, 3714 CrossRef CAS.
- L. J. Pan, L. Pu, Y. Shi, S. Y. Song, Z. Xu, R. Zhang and Y. D. Zheng, Adv. Mater., 2007, 19, 461 CrossRef CAS.
- Z. M. Zhang, J. Sui, L. J. Zhang, M. X. Wan, Y. Wei and L. M. Yu, Adv. Mater., 2005, 17, 2854 CrossRef CAS.
- J. Q. Zhuang, H. M. Wu, Y. A. Yang and Y. C. Cao, Angew. Chem., Int. Ed., 2008, 47, 2208 CrossRef CAS.
- D. S. Wang, T. Xie, Q. Peng and Y. D. Li, J. Am. Chem. Soc., 2008, 130, 4016 CrossRef CAS.
- J. Liu, Z. K. Sun, Y. H. Deng, Y. Zou, C. Y. Li, X. H. Guo, L. Q. Xiong, Y. Gao, F. Y. Fu and D. Y. Zhao, Angew. Chem., Int. Ed., 2009, 48, 5875 CrossRef CAS.
-
F. Katz and H. Salem, The Biological and Environmental Chemistry of Chromium, VCH publisher, New York, 1994, p. 51 Search PubMed.
- C. Wei, S. German, S. Basak and K. Rajeshwar, J. Electrochem. Soc., 1993, 140, L60 CrossRef CAS.
- R. Ansari and N. K. Fahim, React. Funct. Polym., 2007, 67, 367 CrossRef CAS.
- Y. Wang and K. Rajeshwar, J. Electroanal. Chem., 1997, 425, 183 CrossRef CAS.
- F. J. Rodriguez, S. Gutierrez, J. G. Ibanez, J. L. Bravo and N. Batina, Environ. Sci. Technol., 2000, 34, 2018 CrossRef CAS.
- E. T. Kang, Y. P. Ting and K. L. Tan, J. Appl. Polym. Sci., 1994, 53, 1539 CrossRef CAS.
- S. Fujii, S. P. Armes, R. Jeans, R. Devonshire, S. Warren, S. L. McArthur, M. J. Burchell, F. Postberg and R. Srama, Chem. Mater., 2006, 18, 2758 CrossRef CAS.
- O. Y. Posudievsky and O. A. Kozarenko, Polym. Chem., 2011, 2, 216 RSC.
- K. J. Wynne and G. B. Street, Macromolecules, 1985, 18, 2361 CrossRef CAS.
- T. H. Chao and J. March, J. Polym. Sci., Part A: Polym. Chem., 1988, 26, 743 CrossRef CAS.
- X. F. Lu, H. Mao and W. J. Zhang, Nanotechnology, 2007, 18, 025604 CrossRef.
- T. J. Yao, Q. Lin, K. Zhang, D. F. Zhao, H. Lv, J. H. Zhang and B. Yang, J. Colloid Interface Sci., 2007, 515, 434 CrossRef.
- M. I. Redondo, M. V. García, E. S. Blanca, M. Pablos, I. Carrillo, M. J. González-Tejera and E. Enciso, Polymer, 2010, 51, 1728 CrossRef CAS.
- J. Wu, X. Zhang, T. J. Yao, J. Li, H. Zhang and B. Yang, Langmuir, 2010, 26, 8751 CrossRef CAS.
- S. F. Lascelles and S. P. Armes, J. Mater. Chem., 1997, 7, 1339 RSC.
- H. J. Ding, X. M. Liu, M. X. Wan and S. Y. Fu, J. Phys. Chem. B, 2008, 112, 9289 CrossRef CAS.
- X. G. Li, A. Li, M. R. Huang, Y. Z. Liao and Y. G. Lu, J. Phys. Chem. C, 2010, 114, 19244 CAS.
- M. K. Song, Y. T. Kim, B. S. Kim, J. Kim, K. Char and H. W. Rhee, Synth. Met., 2004, 141, 315 CrossRef CAS.
- D. D. Das, R. Mahapatra, J. Pradhan, S. N. Das and R. S. Thakur, J. Colloid Interface Sci., 2000, 232, 235 CrossRef CAS.
- M. A. Ferro-Garcia, J. Rivera-Utrilla, I. Bautista-Toledo and C. Moreno-Castilla, Langmuir, 1998, 14, 1880 CrossRef CAS.
Footnote |
† Electronic supplementary information (ESI) available: Experimental section and Fig. S1, S2 and S3. See DOI: 10.1039/c1py00311a |
|
This journal is © The Royal Society of Chemistry 2011 |
Click here to see how this site uses Cookies. View our privacy policy here.