DOI:
10.1039/C0PY00242A
(Paper)
Polym. Chem., 2011,
2, 1287-1292
Synthesis and properties of poly[2,2′-(4,4′-(2,6-bis(phenoxy) benzonitrile))-5,5′-bibenzimidazole] for proton conducting membranes in fuel cells
Received
31st July 2010
, Accepted 19th March 2011
First published on 30th March 2011
Abstract
Poly[2,2′-(4,4′-(2,6-bis(phenoxy) benzonitrile))-5,5′-bibenzimidazole] (PBI-CN) was synthesized via the polycondensation of 3,3′,4,4′-tetraaminobiphenyl and 2,6-bis(4-carboxyphenoxy) benzonitrile. The introduction of the nitrile group to the main chain of PBI-CN can provide both strong polarity and a reactive site for further reaction. The effects of different reaction conditions on the intrinsic viscosity of the synthesized polymer are discussed, which is consistent with the regular pattern. After appropriate purification of starting materials and optimization of polymerization conditions, the synthesized polymer can exhibit higher intrinsic viscosity, which means higher molecular weight. The solubility, chemical oxidation stability, thermal degradation behavior, acid doping ability, and proton conductivity of the synthesized polymers were studied. Compared with poly[2,2′-(m-phenylene)-5,5′-bibenzimidazole] (PBI-ph), the introduction of –C≡N and –O– group in PBI-CN provides the polymer with better acid doping ability and chemical oxidation stability, while the solubility and thermal stability decrease a little. The proton conductivity of PBI-CN/3.5H3PO4 composite membranes can reach ∼10−3 S cm−1 at 170 °C under anhydrous condition. The temperature dependence of proton conductivity of the acid doped membranes can be modeled by an Arrhenius relation.
1. Introduction
Polymer electrolyte membrane fuel cells (PEMFCs) have attracted a lot of attention in recent years due to their use as a candidate power source in automobile and stationary applications.1–3 The widely used proton exchange membranes (PEMs) for PEMFCs are perfluorosulfonic acid polymers, such as Nafion® and Flemion®. However, the disadvantages of this kind of PEM, such as high cost, the dropdown of proton conductivity at low humidity and at temperature higher than 80 °C limit their further application.4–6 Intermediate temperature (100–200 °C) PEMFCs, with the advantages of higher tolerance to the fuel impurities, faster electrode kinetics, and simplified water management design, have attracted increasing attention in recent years.7,8 Among various anhydrous proton exchange membranes developed for intermediate temperature PEMFCs, phosphoric acid (PA) doped polybenzimidazole (PBI) has emerged as a promising candidate. It has been shown that this kind of polymer electrolyte membrane exhibits high proton conductivity at low humidity, low gas permeability, excellent thermal stability at a temperature as high as 200 °C, and a nearly zero water drag coefficient.9–13
Among various PBIs with different structures,10–13 only poly[2,2′-(m-phenylene)-5,5′-bibenzimidazole] (PBI-ph) and poly[2,5-benzimidazole] (ABPBI) were widely investigated for fuel cell applications. In recent years, PBIs with different structures have attracted more and more attention due to their different properties,14–16 and introduction of functional groups in a PBI backbone can provide PBI with further space for chemical modification to improve its performance. In the present work, poly[2,2′-(4,4′-(2,6-bis(phenoxy)benzonitrile))-5,5′-bibenzimidazole] (PBI-CN) will be synthesized and the parameters that affect the polycondensation process, the solubility, acid doping ability, proton conductivity, chemical oxidation stability, and thermal stability of the polymer will be discussed.
2. Experimental
2.1 Materials
3,3′,4,4′-tetraaminobiphenyl was purchased from Shanghai Chemical Reagent Co., and recrystallized before used. 2,6-difluorobenzonitrile (DFBN) was purchased from Acros Chemical Co. p-hydroxybenzoic acid (p-HDBC), potassium carbonate, and other chemicals or solvents were purchased from Shanghai Chemical Reagent Co., and all used as received. PBI-ph, with the structure as shown in Fig. 1, was synthesized according to the method in ref. 17 and 18.
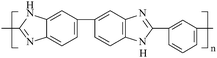 |
| Fig. 1 Chemical structure of PBI-ph. | |
2.2 Synthesis and characterization of 2,6-bis(4-carboxyphenoxy)benzonitrile
2,6-bis(4-carboxyphenoxy)benzonitrile (BCPB) was prepared by condensation of DFBN and p-HDBC in the presence of potassium carbonate in DMSO, as shown in Fig. 2. A 250 mL three-necked flask was equipped with a magnetic stirring device, a nitrogen inlet and outlet. 13.80 g p-HDBC (0.1 mol), 90 mL DMSO, 30 mL toluene, and 11.1 g potassium carbonate (0.08 mol) were added to the flask. The contents of the flask were then heated for 4 h at 150 °C. During the process, the water was evaporated as an azeotrope with toluene, and the remaining toluene was distilled from the flask. When the mixture was cooled to 70 °C, a solution of 6.96 g DFBN (0.05 mol) in 10 mL DMSO was added to the flask and the reaction was stirred for 6 h at 190 °C. The mixture was precipitated in 300 mL acetone. The precipitated product was filtered and successively dissolved by water. Excess hydrochloric acid was added to the solution and BCBP was precipitated during the process. The product was then purified by recrystallization in ethanol.
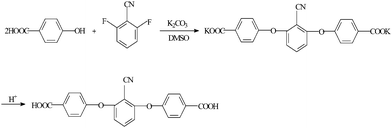 |
| Fig. 2 Synthetic procedure of BCBP. | |
FTIR analysis of BCBP synthesized was carried out by a thermo Bruker EQUINOXSS/HYPERION2000 spectrometer. KBr pellet method was used. 1H-NMR spectra of BCBP in deuterated dimethyl sulfoxide (DMSO) were recorded on a Varian Bruker AC-250 instrument.
2.3 Synthesis and characterization of PBI-CN
The synthesis of PBI-CN is similar to that of PBI-ph.6,17,18 The general synthetic procedure is shown in Fig. 3. A 100 mL three-neck flask equipped with a mechanical stirrer, a nitrogen inlet and calcium chloride drying tube was charged with 40 g polyphosphoric acid (PA), and then heated to 140 °C. 1.07 g of purified 3,3′,4,4′-tetraaminobiphenyl (5 mmol) was added into the flask, and then the mixture was stirred for 4 h at 140 °C under the nitrogen flow to dissolve 3,3′,4,4′-tetraaminobiphenyl. After that, 1.87 g BCBP (5 mmol) was added to this mixture. Then the mixture was heated up to 220 °C and stirred for 20 h. The hot reaction mixture was poured into deionized (DI) water in order to isolate the polymer, and neutralized with sodium bicarbonate. Afterwards, the polymer powder was rinsed several times with DI water until reaching neutrality and left to dry overnight at 150 °C inside an oven. Finally, the polymer was ground to obtain a black powder. The Ubbelohde viscometer was used to determine the molecular weight of the polymer. It was dissolved in 96% sulfuric acid and the flow time of the solution and the solvent was measured respectively, from which the intrinsic viscosity can be calculated.19,20 The solubility of the polymer is tested by dissolving it in different kinds of solvents. FTIR analysis of the polymer was carried out by a thermo Bruker EQUINOXSS/HYPERION2000 spectrometer. KBr pellet method was used. Thermal stabilities of the polymer were investigated by thermogravimetric analysis (TGA) with STA 449C equipment (Netzsch Co.). The sample was heated from room temperature to 700 °C with a heating rate of 10 °C min−1 under nitrogen atmosphere.
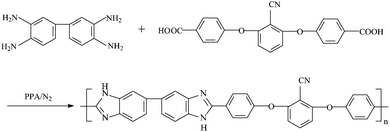 |
| Fig. 3 Synthetic procedure for PBI-CN. | |
2.4 Preparation and characterization of the membranes
PBI-CN powder was dissolved in N-methyl-2-pyrrolidone (NMP) by stirring at a temperature of 160 °C for 20 h. The solution was then filtered to eliminate impurities. The membrane was prepared by casting the solution on a glass plate and the solvent was slowly evaporated at 120 °C during a period of 12 h. The membranes were then stripped off from the plate and placed under vacuum at a temperature between 180 °C and 200 °C for 24 h in order to remove the remnant solvent.
Small pieces of membrane with a thickness about 30 μm were immersed in phosphoric acid solution with different concentration for 3 days at room temperature. The membranes were then washed with distilled water and dried at 100 °C under vacuum for 24 h. The weight gain due to phosphoric acid was obtained by comparing the weight change before and after the acid doping. The acid doping level was quantified by the number of doped H3PO4 molecules per repeat unit of PBI.
The chemical oxidation stability of the membranes was measured by Fenton reagent (3%H2O2 aqueous solution containing 4 ppm FeSO4). The membranes were soaked in Fenton reagent at the temperature of 20 °C and 80 °C, respectively. The chemical oxidation stability of the membranes was evaluated by the elapsed time when the Fenton reagent began to have flocky precipitates.21
The proton conductivity of H3PO4 doped membranes in an anhydrous state was measured by Electrochemical Impedance Lab CHI 604B (CH Instruments Inc.), which worked in the galvanostatic mode and produced a proton current across the membrane. The applied current was typically of the order of 5 mA. DC conductivities were calculated from Cole-Cole plots (Z′′ vs. Z′).
3. Results and discussion
3.1 Chemical structure of 2,6-bis(4-carboxyphenoxy)benzonitrile and poly[2,2′-(4,4′-(2,6-bis(phenoxy)benzonitrile))-5,5′-bibenzimidazole]
The FTIR spectrum of 2,6-bis(4-carboxyphenoxy)benzonitrile (BCPB) is shown in Fig. 4. The characteristic absorption bands at 3100–2850 cm−1 (–OH) and 1693 cm−1 (C
O) in the spectrum suggest that the formation of carboxylic acid. The absorption at 2239 cm−1 in the spectrum is assigned to –C≡N stretching vibration. The absorption bands at 1578, 1506, and 1468 cm−1 are related to the stretching vibration of phenyl ring backbone and the bands around 1248 cm−1 and 1019 cm−1 are due to –O– stretch vibration. Fig. 5 shows 1H-NMR spectrum of BCBP. The signals at 6.8–8.1 ppm are assigned to Ar–H. The peaks around 13.0 ppm are attributed to the carboxyl group. From the FTIR and 1H-NMR spectra, it can safely be concluded that BCBP has been synthesized successfully.
The FTIR spectrum of PBI-CN is shown in Fig. 6. The FTIR spectrum of PBI-ph has been studied extensively in the past.22,23 Similar to that, the strong band from 2500 to 3500 cm−1 in the spectrum of PBI-CN is ascribed to strong hydrogen bonding of the type N–H⋯H, and the absorption at 2270 cm−1 in the spectrum is assigned to –C≡N stretching vibration. The bands at 1612 cm−1 and 1443 cm−1 correspond to C
N and C–N stretching vibrations, respectively. The bands around 1251 cm−1 and 1158 cm−1 are due to –O– stretch vibrations. Additionally, there is no absorption band around 1700 cm−1 (–COOH), which means that the carboxylic acid has completely reacted to form a benzimidazole ring on one hand; on the other hand, the absorption by end groups of –COOH on the chain disappears due to the lower content of the end groups with increasing molecular weight of the polymer.
3.2 Effects of the polymerization conditions on the molecular weight of PBI-CN
As with most polybenzimidazoles, PBI-CN was also produced at laboratory scale by diamine-acid condensation in polyphosphoric acid (PPA). Table 1 shows the effects of the polymerization conditions on the intrinsic viscosity of PBI-CN. It can be observed that PBI-CN synthesized under different conditions will achieve different intrinsic viscosities. Compared with Sample 1, Sample 2 using monomers without purification gives lower intrinsic viscosity. Based on the Carothers equation, the purity and accurate stoichiometry of the monomers are crucial to obtain the polymers with high molecular weight.14 Additionally, the polymerization with shorter reaction time (Sample 3) and lower reaction temperature (Sample 4) will also have the decreased intrinsic viscosity. The synthesis of PBI-CN is a step-growth polycondensation process, with prolonged time and improved temperature provide suitable conditions to form PBI-CN with higher molecular weight. What's more, when the dehydrating reagent P2O5 is absent from the reaction (Sample 5), the water formed in the reaction is more difficult to remove and the polycondensation process will be affected, which will result in the formation of PBI-CN with low molecular weight. However, the addition of P2O5 is limited by the accompanied increase of viscosity of the reaction mixture. If too much P2O5 is added, the PPA mixture cannot be easily stirred, which will block the monomers from reacting with each other.
Table 1 Effects of polymerization conditions on intrinsic viscosity of PBI-CN, DABA/DCPB (mol/mol) = 1/1
No. |
T (°C) |
Time (h) |
DABA/PPA/P2O5 (mmol g−1 g−1) |
Monomers |
Intrinsic viscosity (dL g−1) |
R, recrystallized.
U, without purification by recrystallization.
|
1 |
220 |
20 |
5/40/3 |
Ra |
1.29 |
2 |
220 |
20 |
5/40/3 |
Ub |
0.88 |
3 |
220 |
10 |
5/40/3 |
R
|
0.74 |
4 |
150 |
20 |
5/40/3 |
R
|
0.91 |
5 |
220 |
20 |
5/40/0 |
R
|
1.06 |
3.3 Solubility and thermal stability of PBI-CN
The solubility of the polymer can reflect its film forming ability. As shown in Table 2, PBI-CN is only soluble in two kinds of polar solvents, dimethyl acetamide (DMAc) and NMP, at high temperature (the boiling point of the solvents). Compared with PBI-ph, the solubility of PBI-CN is a little poorer. According to the literature,24 the solubility parameter of PBI-ph is 10.5 (cal cm−3)1/2, similar to that of NMP and DMAc (11.1 (cal cm−3)1/2). Normally, the incorporation of polar groups in PBI-CN should make it less soluble in the common solvents, however the incorporation of ether-groups in the backbone of PBI has been known to increase solubility of the polymer, due to greater flexibility of the chains.25
Table 2 Solubility of PBI-CN in different solventsa
|
NMP
|
DMAc
|
DMSO
|
DMF
|
THF
|
H2SO4 |
H3PO4 |
s: soluble; sh: soluble when heating; n: non-soluble.
|
PBI-ph
|
sh |
sh |
sh |
n |
n |
s |
n |
PBI-CN
|
sh/n |
sh/n |
n |
n |
n |
s |
n |
TGA curve of PBI-CN is shown in Fig. 7. For comparison, the curve of PBI-ph is also represented. The thermal degradation process of PBI-ph is quite clear.13,26,27 For PBI-CN, the major weight loss beginning at 510 °C is the degradation of the backbone of the polymer; while for PBI-ph, it is about 580 °C. As seen from the molecular structure of both kinds of PBIs, PBI-CN has –O– group in the main chain, and it needs less energy to break the backbone of the polymer,28 which leads to the declined thermal stability of PBI-CN. Besides this, the small weight loss of PBI-CN at 235 °C may be attributed to the partial degradation of the introduced C–CN bond.29 Meanwhile, PBI-ph also has a smaller weight loss at 380 °C due to the degradation of N–H of benzimidazole. However, such weight loss stage almost disappears in TGA curve of PBI-CN, which may be due to the decreased N–H weight percentage in PBI-CN compared with PBI-ph.
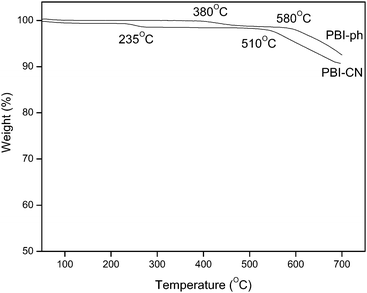 |
| Fig. 7
TGA thermograms of PBI-CN, N2 atmosphere, heating rate 10 °C min−1. | |
3.4 Doping ability of phosphoric acid in PBI-CN
Fig. 8 shows the comparison of the doping ability of phosphoric acid in PBI-ph and PBI-CN membranes. The method used to measure the doping level of acid in PBI by comparing the weight change of the membranes before and after acid doping is widely used in ref. 6, 9 and 15. The data points in Fig. 8 are the average values of two measurements. It can be found that the acid doping level in PBI-ph and PBI-CN all increases with increasing concentration of phosphoric acid solution. However, at the same acid concentration, PBI-CN can be doped with a little more H3PO4 than PBI-ph.
The factors that affect the acid doping level of PBI-ph/H3PO4 membranes have been studied before.30,31 The higher acid concentration and longer doping time result in higher acid doping level in the membranes, which can also be found in Fig. 8. Meanwhile, the structure of PBIs also has influence on acid doping level.6,10 Chemically, PBI-ph is a basic polymer (pKa = 5.5 as protonated)32 and can readily be doped with strong acid such as H3PO4 due to the existance of imidazole in PBI-ph. On one hand, –C≡N and –O– with lone pair electrons will provide additional proton acceptors, which can help imidazole attract more acidic moieties; on the other hand, the –O– structure in PBI-CN will provide more flexible chains, which is beneficial for the diffusion of the acids. Thus, the acid doping ability of PBI-CN is improved a little compared with PBI-ph.
3.5 Chemical oxidation stability of the membranes
The chemical oxidation stability of the membranes is very important to the lifetime of PEMFCs. The chemical oxidation stability of PBI-CN and PBI-ph membranes measured by Fenton reagent is listed in Table 3. It can be found that the oxidation stability of PBI-CN membrane is a little higher than that of PBI-ph. The reason is that the oxidation test using Fenton reagent is a chemical procedure in which the free radical species (HO˙ and HOO˙) attack the hydrogen-containing bonds in polymer membranes. When HO˙ inserts into the polymer chain, it will destroy the structure of the polymer chain and cause the polymer to be oxidized and form the floccules.21,33 A suggestion has been made that the lone pair electrons on –C≡N and –O– groups in PBI-CN may form a conjugated structure with a benzyl ring nearby, which may stabilize the free radicals and prevent the further degradation of the chain.
Table 3 Chemical oxidation stability of PBI-CN and PBI-ph
Sample |
T (°C) |
Average flocculation time (h) |
PBI-ph
|
20 |
9.7 |
PBI-ph
|
80 |
3.2 |
PBI-CN
|
20 |
15.5 |
PBI-CN
|
80 |
7.3 |
3.6
Proton conductivity of PBI-CN/H3PO4 composite membranes
Proton conductivity of acid-doped PBI-CN and PBI-ph under anhydrous condition was measured as functions of a temperature and acid-doping level. The results are shown in Fig. 9. An increase of proton conductivity was observed for all the samples with increasing temperature. The temperature dependence of the conductivity in polymer electrolyte has often been taken as an indicative of a particular type of conduction mechanism.34 The temperature dependence of proton conductivity follows two different types of equations. Arrhenius law (eqn (1)) can be used to explain the proton hopping mechanism, while the Vogel-Tammann-Fulcher (VTF) equation (eqn (2)) is usually used to describe the segmental motion mechanism. | 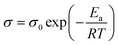 | (1) |
where σ0 is the pre-exponential factor, Ea is the apparent activation energy; R is Boltzmann constant, and T is the temperature of the membranes. | 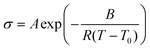 | (2) |
A, B, and T0 are three parameters. R and T are the same as that of the Arrhenius equation.
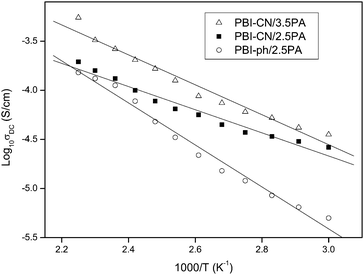 |
| Fig. 9
Proton conductivity of different PBI/H3PO4 composite membranes as a function of temperature. | |
It is already known that the function of proton conductivity vs. temperature of H3PO4 doped PBI-ph exhibits a simple Arrhenius behavior.34 PBI-ph is a fairly rigid polymer with glass transition temperature (Tg) above 400 °C. Under the temperature investigated, the chains of PBI are frozen. Therefore, the proton transport for PBI-ph/H3PO4 composite membranes is mainly controlled by a hopping mechanism rather than the segmental motion. Table 4 lists the pre-exponential factor σ0 and activation energy Ea of PBI-CN/H3PO4 membranes. Ea values of the membranes with different acid doping level are quite approachable, which means that the proton transport of the composite membrane is independent of the segmental motion of PBI-CN.
Table 4 Pre-exponential factor σ0 and activation energy Ea of PA doped membranes
Membranes
|
σ
0 (S cm−1) |
E
a (kJ/mol) |
PBI-ph/2.5PA |
10.09 |
41.37 |
PBI-CN/2.5PA |
0.07 |
22.57 |
PBI-CN/3.5PA |
1.04 |
29.45 |
Comparing the proton conductivities of PBI-CN/H3PO4 membranes with those of PBI-ph/H3PO4 membranes, it can be found that PBI-CN/H3PO4 membranes have higher proton conductivity than PBI-ph/H3PO4 membranes with x = 2.5 for both under all temperatures investigated. The proton conductivity of PBI-ph/H3PO4 drops more quickly than that of PBI-CN/H3PO4 membrane when the temperature decreases. Previous research has shown that the possible way for the proton transport in the membranes is based on the continual ‘forming-breaking-forming’ process of hydrogen bonds between PBI molecules and H3PO4 molecules.35,36PBI-CN is also a basic polymer, with the benzimidazole part as the proton donor and acceptor. It provides the possibility for proton mobility via structure diffusion involving proton transfer between H3PO4 and PBI-CN with a corresponding reorganization of the hydrogen bond network. On one hand, the –C≡N and –O– structure in PBI-CN will reduce the content of imidazole in the chain and reduce the number of proton acceptors and proton donors; on the other hand, C≡N and –O– with lone pair electrons will provide additional proton acceptors, which is beneficial for the improving of the proton conductivity.
4. Conclusions
A new kind of polybenzimidazole, poly[2,2′-(4,4′-(2,6-bis(phenoxy) benzonitrile))-5,5′-bibenzimidazole], was synthesized via the polycondensation between 3,3′,4,4′-tetraaminobiphenyl and 2,6-bis(4-carboxyphenoxy) benzonitrile. Effects of different reaction conditions on the intrinsic viscosity of the synthesized polymer are discussed, which is consistent with the regular pattern. After appropriate purification of starting materials and optimization of polymerization conditions, the synthesized polymer can exhibit higher intrinsic viscosity, which means higher molecular weight. The solubility, chemical oxidation stability, thermal degradation behavior, acid doping ability, and proton conductivity of the synthesized polymers were studied. Compared with PBI-ph, the introduction of –C≡N and –O– group in PBI-CN provides the polymer with better acid doping ability and chemical oxidation stability, while the solubility and the thermal stability decrease a little. The proton conductivity of PBI-CN/3.5H3PO4 composite membranes can reach ∼10−3 S cm−1 at 170 °C under anhydrous conditions. The temperature dependence of the proton conductivity of the acid doped membranes can be modeled by an Arrhenius relation. On one hand, the –C≡N and –O– structure in PBI-CN will reduce the content of imidazole in the chain and reduce the number of proton acceptors and proton donors; on the other hand, –C≡N and –O– with lone pair electrons will provide additional proton acceptors, which is beneficial for the improving of the proton conductivity. With this kind of PBI, further research work can be carried out to improve PBI performance by functionalizing the –C≡N group in its main chain.
Acknowledgements
The project is supported by Natural Science Foundation of China (50773055), Foundation for Nano Science & Technology of Shanghai (0852nm02200), and Program for New Century Excellent Talents in University (NCET-06-0379).
References
- R. K. Nagarale, W. Shin and P. K. Singh, Polym. Chem., 2010, 1, 388 RSC.
- H. T. Pu, Y. J. Qin, D. C. Wan and Z. L. Yang, Macromolecules, 2009, 42, 3000 CrossRef CAS.
- S.-K. Kim, T.-H. Kim, J.-W. Jung and J.-C. Lee, Polymer, 2009, 50, 3495 CrossRef CAS.
- M. Ingratta, M. Elomaa and P. Jannasch, Polym. Chem., 2010, 1, 739 RSC.
- G. Q. Qian, D. W. Smith Jr and B. C. Benicewicz, Polymer, 2009, 50, 3911 CrossRef CAS.
- H. T. Pu, L. Wang, H. Y. Pan and D. C. Wan, J. Polym. Sci., Part A: Polym. Chem., 2010, 48, 2115 CrossRef CAS.
- Q. F. Li, J. O. Jensen, R. F. Savinell and N. J. Bjerrum, Prog. Polym. Sci., 2009, 34, 449 CrossRef CAS.
- H. T. Pu, L. Qiao, Q. Z. Liu and Z. L. Yang, Eur. Polym. J., 2005, 41, 2505 CrossRef CAS.
- Q. F. Li, R. H. He, J. O. Jensen and N. J. Bjerrum, Fuel Cells, 2004, 4, 147 CrossRef CAS.
- A. Carollo, E. Quartarone, C. Tomasi, P. Mustarelli, F. Belotti, A. Magistris, F. Maestroni, M. Parachini, L. Garlaschelli and P. P. Righetti, J. Power Sources, 2006, 160, 175 CrossRef CAS.
- S. C. Kumbharkar, Md. N. Islam, R. A. Potrekar and U. K. Kharul, Polymer, 2009, 50, 1403 CrossRef CAS.
- J. A. Asensio, S. Borrós and P. Gómez-Romero, Electrochim. Acta, 2004, 49, 4461 CrossRef CAS.
- H. T. Pu, Polym. Int., 2003, 52, 1540 CrossRef CAS.
- T. Brock, D. C. Sherrington and H. G. Tang, Polymer, 1991, 32, 353 CrossRef CAS.
- J. A. Asensio and P. Gómez-Romero, Fuel Cells, 2005, 5, 336 CrossRef CAS.
- H.-S. Lee, A. Roy, O. Lane and J. E. McGrath, Polymer, 2008, 49, 5387 CrossRef CAS.
- Y. S. Guan, H. T. Pu, H. Y. Pan, Z. H. Chang and M. Jin, Polymer, 2010, 51, 5473 CAS.
- J. Lobato, P. Cañizares, M. A. Rodrigo, J. J. Linares and J. A. Aguilar, J. Membr. Sci., 2007, 306, 47 CrossRef CAS.
- Y. X. Yuan, F. Johnson and I. Cabasso, J. Appl. Polym. Sci., 2009, 112, 3436 CrossRef CAS.
- J. S. Wainright, J. T. Wang, D. Weng, R. F. Savinell and M. Litt, J. Electrochem. Soc., 1995, 142, L121.
- Z. H. Chang, H. T. Pu, D. C. Wan, L. Liu, J. J. Yuan and Z. L. Yang, Polym. Degrad. Stab., 2009, 94, 1206 CrossRef CAS.
- P. Musto, F. E. Karasz and W. J. MacKnight, Polymer, 1993, 34, 2934 CAS.
- P. Musto, F. E. Karasz and W. J. MacKnight, Polymer, 1989, 30, 1012 CrossRef CAS.
- S. C. Kumbharkar, P. B. Karadkar and U. K. Kharul, J. Membr. Sci., 2006, 286, 161 CrossRef CAS.
- T. H. Kim, S. K. Kim, T. W. Lim and J. C. Lee, J. Membr. Sci., 2008, 323, 362 CrossRef CAS.
- S. R. Samms, S. Wasmus and R. F. Savinell, J. Electrochem. Soc., 1996, 143, 1225 CAS.
- P. Musto, F. E. Karaszt and W. J. MacKnight, Polymer, 1993, 34, 2934 CAS.
- H. Q. Zhang, X. F. Li, C. J. Zhao, T. Z. Fu, Y. H. Shi and H. Na, J. Membr. Sci., 2008, 308, 66 CrossRef CAS.
- M. Arous, A. Kallel, H. Kaddami, M. Lahcini, A. Belfkira and M. Raihane, J. Appl. Polym. Sci., 2009, 114, 1094 CrossRef CAS.
- C. E. Hughes, S. Haufe, B. Angerstein, R. Kalim, U. Mähr, A. Reiche and M. Baldus, J. Phys. Chem. B, 2004, 108, 13626 CrossRef CAS.
- H. T. Pu and G. H. Liu, Polym. Adv. Technol., 2004, 15, 726 CrossRef CAS.
- J. T. Wang, J. S. Wainright, R. F. Savinell and M. Litt, J. Appl. Electrochem, 1996, 26, 751 CAS.
- Q. F. Li, C. Pan, J. O. Jensen, P. Noyé and N. J. Bjerrum, Chem. Mater., 2007, 19, 350 CrossRef CAS.
- H. T. Pu, W. H. Meyer and G. Wegner, J. Polym. Sci., Part B: Polym. Phys., 2002, 40, 663 CrossRef CAS.
- R. Bouchet and E. Siebert, Solid State Ionics, 1998, 118, 287.
- X. Glipa, B. Bonnet, B. Mula, D. J. Jones and J. Rozière, J. Mater. Chem., 1999, 9, 3045 RSC.
|
This journal is © The Royal Society of Chemistry 2011 |
Click here to see how this site uses Cookies. View our privacy policy here.