Direct allylic amination of allylic alcohols with aromatic/aliphatic amines using Pd/TPPTS as an aqueous phase recyclable catalyst†
Received
20th November 2011
, Accepted 20th December 2011
First published on 21st December 2011
Abstract
Direct activation of C–O bonds in cinnamyl/allyl alcohols with aromatic/aliphatic amines in aqueous medium using a water soluble Pd(OAc)2/TPPTS catalyst has been reported. The catalyst is highly efficient, chemoselective, simple, atom economical, greener and reusable up to eight consecutive cycles without aid of any co-catalyst. The protocol is applicable to a wide range of hindered and functionalized aromatic/aliphatic amines with excellent yield of the corresponding allyl amines.
Introduction
The palladium catalysed Tsuji–Trost reaction1 is a powerful tool in organic synthesis for the construction of C–C, C–N and C–O bonds, and involves Pd-catalyzed allylations of various C–, N– and O– pronucleophiles. Among these allylations, allyl amine synthesis stands to be one of the important reactions due to its wider applications in fine chemicals and pharmaceuticals.2 Allyl amines can be synthesized via allylic amination of internal alkynes3 or allylic amination of allylic alcohols4–6 and derivatives of allylic alcohols such as allyl esters,7 allyl ethers8 and allyl carbonates9 in the presence of palladium based catalysts. The use of allylic alcohols as an allylating agent for the synthesis of allyl amines was found to be more advantageous as other allylating agents generate stoichiometric amounts of waste in the reaction medium. Previous protocols on allylic amination of allylic alcohols using a palladium-catalyst require either stoichiometric or catalytic amounts of co-catalysts such as PPh3-DEAD, As2O3, B2O3, BF3·Et2O, BEt3, BPh3, SnCl2, Ti(O–iPr)4 and carboxylic acids, due to the inherent low leaving aptitude of the hydroxyl group. There is only one report on palladium catalysed reactions in the literature, where a co-catalyst has not been used for the allylic amination of allylic alcohols by Oshima et al. but the same Pd–TPPTS catalyst has been used under biphasic conditions at room temperature.4c However, they failed to perform the amination of cinnamyl alcohol, also studied a limited number of amine substrates and the recyclability of the catalyst is also not reported. It should be noted that most of the reported protocols for allylic amination are with the use of organic solvents. Organic transformations in aqueous reaction medium have several advantages over organic solvents, as water is inexpensive, readily available, renewable, safe and environmentally benign solvent. On the other side, use of water-soluble catalysts allows an easy separation of the catalysts from products, leading to the possible reuse of aqueous solution containing the catalyst.10,11
Apart from these, the reported protocols required longer reaction times, higher palladium-loading, excess amount of the co-catalyst, expensive ligands and all of them employed a homogeneous non-recyclable catalyst. However, the use of homogeneous catalysts has the problem of catalyst–product separation, which is especially problematic if catalyst recycling is desired. It should be noted that traces of palladium contamination in the product is not acceptable for pharmaceutical applications as palladium is not desirable and can cause adverse effects on health. Therefore, the development of new protocols which can separate and reuse the palladium-catalyst without leaching is desirable. In this context, we herein report a co-catalyst free, recyclable palladium-catalyzed protocol for allylic amination of allylic alcohols in water using the triphenylphosphine trisulfonate sodium salt (TPPTS) as ligand with Pd(OAc)2 as a palladium-precursor (Scheme 1). Pd(OAc)2/TPPTS is a well known catalytic system and has been successfully utilised for various organic transformations11 including the Tsuji–Trost reaction.4c
Results and discussion
Allylic amination of cinnamyl alcohol with N-methylaniline as a model reaction with Pd(OAc)2/TPPTS as a catalyst, benzoic acid as a co-catalyst (for screening purpose only) and water as a solvent (Table 1, entries 1–17) was selected for optimization study. While performing the test experiments to examine the role of each component, it was observed that palladium acetate and TPPTS were essential to catalyze the allylic amination reaction. We too observed that the present catalytic system endows excellent results without a co-catalyst, i.e. benzoic acid (please refer Table S1, ESI†). These unusual results obtained may be due to the use of TPPTS as a ligand which is playing a dual role of a co-catalyst (due to its acidic moieties) and a ligand. The role of various reaction parameters such as the effects of catalyst concentration, metal
:
ligand ratio, temperature, time and recyclability of the catalyst with various metal
:
ligand ratios are summarized in Table 1.
Entry |
Catalyst conc. (mol%) |
Metal : ligand ratio |
Temp./°C |
Time/h |
Yieldb (%) |
Reaction conditions: Cinnamyl alcohol (5 mmol), N-methyl aniline (6 mmol), Pd(OAc)2 (metal precursor), TPPTS (ligand), water (10 mL).
GC yield.
|
Effect of catalyst concentration |
1 |
5.0 |
1 : 4 |
100 |
4 |
98 |
2 |
2.5 |
1 : 4 |
100 |
4 |
98 |
3 |
1.0 |
1 : 4 |
100 |
4 |
98 |
4 |
0.5 |
1 : 4 |
100 |
4 |
98 |
5 |
0.2 |
1 : 4 |
100 |
4 |
98 |
6 |
0.1 |
1 : 4 |
100 |
4 |
82 |
Effect of metal : ligand ratio |
7 |
0.2 |
1 : 1 |
100 |
4 |
66 |
8 |
0.2 |
1 : 2 |
100 |
4 |
83 |
9 |
0.2 |
1 : 3 |
100 |
4 |
88 |
10 |
0.2 |
1 : 5 |
100 |
4 |
98 |
Effect of temperature |
11 |
0.2 |
1 : 4 |
30 |
4 |
— |
12 |
0.2 |
1 : 4 |
60 |
4 |
— |
13 |
0.2 |
1 : 4 |
80 |
4 |
58 |
14 |
0.2 |
1 : 4 |
90 |
4 |
70 |
Effect of time |
15 |
0.2 |
1 : 4 |
100 |
2 |
98 |
16 |
0.2 |
1 : 4 |
100 |
1 |
98 |
17 |
0.2 |
1 : 4 |
100 |
0.5 |
40 |
In the case of transition metal-catalyzed reactions, the amount of catalyst employed is one of the important factors and hence efforts were made to determine the optimum concentration of the catalyst required. Reactions of cinnamyl alcohol (5.0 mmol) and N-methylaniline (6 mmol) were performed in the presence of Pd(OAc)2
:
TPPTS = 1
:
4 at various catalyst loadings ranging from 5 to 0.1 mol% (Table 1, entries 1–6). Initially, the reaction was carried out using 5 mol% of the catalyst, which provided the desired product N-cinnamyl-N-methylaniline (3a) with 98% yield. The decrease in the catalyst concentration up to 1 mol% shows similar results (Table 1, entry 3). Further decrease in the catalyst concentration up to 0.2 mol% also gives an excellent yield of 3a (Table 1, entry 5), however with more decrease in catalyst concentration to 0.1 mol% the yield of 3a decreased up to 82% (Table 1, entry 6). Thus 0.2 mol% of catalyst loading was selected as optimum concentration for further studies. Furthermore, the effect of various ratios of Pd(OAc)2
:
TPPTS was investigated (Table 1, entries 7–10). The yield of the reaction increased to 98% with a metal to ligand ratio of 1
:
4 (Table 1, entry 5); further decrease in this ratio (e.g., 1
:
5, Table 1, entry 10) did not improve reaction performance. Hence, a metal to ligand ratio of 1
:
4 was the optimum concentration for allylic amination. The effect of various temperatures on the reaction outcome was studied and an excellent result at 100 °C providing 98% yield (Table 1, entry 5) was achieved. It was observed that 1 h is sufficient to catalyze the reaction, offering an excellent yield of desired product 3a (Table 1, entry 16). It should be noted that an earlier report on a similar catalytic system by Oshima and co-workers observed that cinnamyl alcohol is not giving any product.4c
Allylic amination of cinnamyl alcohol with different aromatic amines (Table 2, entries 1–10) was explored further under optimized reaction conditions. Initially various aniline derivatives with electron donating substituents such as –CH3 and –OCH3 and electron withdrawing substituents such as –F, –Cl, and –CN were used under optimum reaction conditions. It was observed that ortho-substituted aniline derivatives reacted smoothly with the formation of only monoallylated products (Table 2, entries 2–6). The ortho-substituted aniline derivatives with electron donating substituents such as –CH3 and –OCH3 worked very well, providing excellent yield of the desired product within 1 h (Table 2, entries 2 and 3). Aniline derivatives with electron withdrawing substituents such as –F, –Cl and –CN at the ortho-position were also examined and were found to be compatible for the present protocol (Table 2, entries 4–6). In the case of aniline, methodology worked effectively with 100% conversion of cinnamyl alcohol providing 88% selectivity for the monoallylated product (Table 2, entry 7). Moreover, we treated para-toluidine with cinnamyl alcohol under present optimized reaction conditions, which offered monoallylated amine as a major product (Table 2, entry 8). The para-toluidine reacted sluggishly in the present catalytic system providing 83% conversion of cinnamyl alcohol and 80% combined yield of isolated products with 90% selectivity for the monoallylated product. This may be due to lower solubility of para-toluidine in water which acts as a reaction medium. In the case of the reaction of α-naphthylamine with cinnamyl alcohol, the N-cinnamyl naphthylamine was obtained with excellent yield (Table 2, entry 9). Aromatic cyclic secondary amines like indoline reacted well with cinnamyl alcohol providing excellent yield within 1 h (Table 2, entry 10).
Entry |
Substrate |
Product |
Time/h |
Yieldb (%) |
Reaction conditions: Cinnamyl alcohol (5 mmol), amine (6 mmol), Pd(OAc)2 (0.2 mol%), TPPTS (4 eq. to Pd(OAc)2), water (10 mL), temperature (100 °C).
Isolated yield.
|
1 |
|
|
1 |
94 |
2 |
|
|
1 |
92 |
3 |
|
|
1 |
94 |
4 |
|
|
1 |
94 |
5 |
|
|
1 |
93 |
6 |
|
|
2 |
90 |
7 |
|
|
1 |
94 (88 : 12) |
8 |
|
|
4 |
80 (90 : 10) |
9 |
|
|
2 |
90 |
10 |
|
|
1 |
91 |
Encouraged by the results, allylic amination of aliphatic allyl alcohol was explored further to extend the scope of the present methodology (Table 3). It was observed that in the case of primary amines like aniline an excess amount of aniline (alcohol
:
amine = 1.0
:
1.2) is necessary to avoid di-allylation products. However, in the case of secondary amines and ortho-substituted aromatic amines, an excess amount of allyl alcohol (alcohol
:
amine = 1.2
:
1) was used to achieve higher conversion which also offers ease of product purification. The reaction of allyl alcohol with aniline provided the appreciable yield with excellent chemoselectivity for the monoallylated product (Table 3, entry 1). In the case of earlier reported protocols for allylic amination of allylic alcohols, the poor selectivity for the monoallylated product was obtained (60–70%).4
Entry |
Substrate |
Product |
Time/h |
Yieldb (%) |
Reaction conditions: allyl alcohol (6 mmol), amine (5 mmol), water (10 mL), temperature (100 °C).
Isolated yield.
Allyl alcohol (5 mmol), amine (6 mmol).
|
1c |
2g
|
|
2 |
91 (86 : 14) |
2 |
2b
|
|
2 |
90 |
3 |
2c
|
|
2 |
90 |
4 |
2d
|
|
4 |
88 |
5 |
2e
|
|
2 |
91 |
6 |
2i
|
|
4 |
90 |
7 |
2a
|
|
2 |
90 |
8 |
2j
|
|
2 |
92 |
9 |
|
|
2 |
90 |
10 |
|
|
2 |
92 |
Further, allylic amination of allyl alcohol with various substituted aniline derivatives bearing both electron donating (–CH3 and –OCH3) as well as electron withdrawing (–F and –Cl) substituents at the ortho-position was studied (Table 3, entries 2–5). It is noteworthy to mention that ortho-substituted substrates are well tolerated, providing excellent yields of desired monoallylated products with 100% selectivity, whereas earlier protocols also offered di-allylated products in significant quantity (30%).4 Treatment of more nucleophilic anilines like 2-methylaniline and 2-methoxy aniline with allyl alcohol offered the respective allylated products with excellent yield and 100% selectivity for monoallylated products (Table 3, entries 2 and 3). Subsequently, we treated 2-fluoroaniline and 2-chloroaniline with allyl alcohol and they provided 88% and 90% yield of the respective monoallylated products (Table 3, entries 4 and 5). The reaction of α-naphthylamine with allyl alcohol gives chemoselectively 90% yield towards the monoallylated product only (Table 3, entry 6). Secondary aromatic amines such as N-methylaniline and indoline were also well tolerated in the present protocol (Table 3, entries 7 and 8). Moreover, we treated aliphatic secondary amines such as morpholine and dibutylamine with allyl alcohol and observed that both of them reacted smoothly endowing excellent yield (90% and 92%) of desired allylated products (Table 3, entries 9 and 10).
Catalyst separation and recyclability is a serious consideration for homogeneous reactions. In this case, we overcome this problem via product extraction from the catalyst containing the aqueous phase. The catalyst containing the water phase can be recycled further. In this case the Pd–TPPTS catalyst is completely insoluble in the ethyl acetate and remains in the water phase. Recycle experiments at different Pd
:
P ratios were studied for a model reaction of allylic amination of cinnamyl alcohol with N-methylaniline under optimized reaction conditions. Initially, we studied a Pd
:
P ratio of 1
:
4 and observed that the colour of the catalyst containing the aqueous phase changed from yellow to black and the yield of reaction declined up to 85% on completion of the fourth recycle run indicating partial Pd precipitation. Hence, we decreased the Pd
:
P ratio up to 1
:
8 and found no change in the colour of the catalyst containing the aqueous phase, without decrease in its catalytic activity up to eight recycle runs. The study revealed that an excess amount of the phosphine ligand was essential to maintain the stability of the Pd–TPPTS complex (Fig. 1).
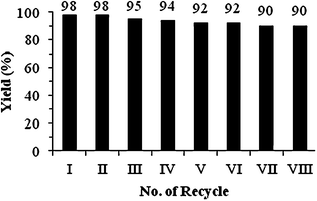 |
| Fig. 1 Recyclability study of the Pd/TPPTS catalyst: (a) Reaction conditions: cinnamyl alcohol (5 mmol), 2-methyl aniline (6 mmol), Pd(OAc)2 (0.2 mol%), TPPTS (4 eq. to Pd(OAc)2), water (10 mL), temperature (100 °C); (b) isolated yield. | |
Conclusions
In conclusion, we report co-catalyst free palladium catalyzed aqueous phase recyclable methodology for allylic amination of allylic alcohols with primary/secondary aromatic as well as aliphatic amines. The developed methodology provided good to excellent yield of the desired allylated product with remarkable selectivity using only 0.2 mol% of catalyst concentration. TPPTS is explored as an efficient water soluble ligand, which brings palladium in the aqueous phase and enables the significant reuse of the catalyst for allylic amination of allylic alcohols. TPPTS proved to be a good ligand as well as it effectively played the role of co-catalyst.
Experimental
General information
All the chemicals and catalyst were purchased from firms of repute with their highest purity available and were used as it is. All the reactions were carried out under a nitrogen atmosphere. The progress of the reaction was monitored on a gas chromatograph (Perkin Elmer, Clarus 400) (BP-10 GC column, 30 m × 0.32 mm ID, film thickness 0.25 mm). The product was purified by column chromatography on silica gel (60–120) mesh. All yields reported in Tables 2 and 3 are isolated yields, while yields reported in Table 1 are on the basis of GC analysis. All the products obtained and discussed in this work have been previously reported and representative products were characterized by suitable techniques such as 1H NMR (Varian 300 MHz) or (Bruker 400 MHz) and GC-MS (Shimadzu QP 2010) analysis.
A typical procedure for preparation of the triphenylphosphine trisulfonate sodium salt.
The solid triphenylphosphine trisulfonate sodium salt was prepared using a reported literature procedure.11 In a typical experimental procedure, 100 mL fuming sulfuric acid (30% of free SO3) was added in a 500 mL three necked round bottom flask. The flask was equipped with a guard tube and a thermometer and connected to an overhead stirrer. Then it was placed in an ice bath and cooled to −5 to −10 °C. The finely ground triphenylphosphine (10 g) was added in small portions to the above mixture and it was done portion wise for about 1 h. With the added phosphine, the ice/salt bath was removed and the resulting mixture was stirred at room temperature for 78 h. The mixture was chilled again using an ice/salt bath and crushed ice was added over 1 h in order to stop the reaction. During the procedure the argon atmosphere was changed several times above the solution. The dilute solution of NaOH was added over 1 h to neutralize the solution. Fine adjustment of the pH to 7 was carried out using a digital pH meter. The water was removed in a vacuum. The solid residue was extracted with a mixture of methanol and water (400 mL/2 mL), and then remaining Na2SO4 was washed with methanol (400 mL) repeatedly. The methanol was evaporated in a vacuum and the phosphine was dissolved in water. Removal of water in a vacuum yielded the methanol free phosphine as a shiny powder and was characterized by 31P NMR.
A typical experimental procedure for direct allylic amination of cinnamyl alcohol with various amines.
In a 25 mL two necked round-bottomed flask, 10 mL deionised water was added and dry nitrogen gas was purged for 1 h. Then Pd(OAc)2 (3 mg, 0.2 mol%) and triphenylphosphine trisulfonate sodium salt (22 mg) were charged to the above degassed deionised water and the solution was stirred for 5 min at 100 °C. The above solution was cooled to room temperature followed by addition of cinnamyl alcohol (5 mmol, 675 mg) and amine (6 mmol) and was then refluxed for 1–4 h. The progress of the reaction was monitored using GC analysis. On completion, the reaction mixture was cooled to room temperature and the products were extracted with ethyl acetate, dried over Na2SO4 and the solvent was evaporated under vacuum. The obtained crude product was then purified by column chromatography using silica gel (60–120 mesh size), with petroleum ether/ethyl acetate (95/5) as an eluent to afford the pure product. All the products obtained and discussed in this work have been previously reported and representative products were characterized by suitable techniques such as 1H NMR (Varian 300 MHz) or (Bruker 400 MHz) and GC-MS (Shimadzu QP 2010) analysis.
A typical procedure for direct allylic amination of allyl alcohol with various amines.
In a 25 mL two necked round-bottomed flask 10 mL deionised water was charged and dry nitrogen gas was purged for 1 h. Then Pd(OAc)2 (3 mg, 0.2 mol%) and triphenylphosphine trisulfonate sodium salt (22 mg) were added to the above degassed deionised water and the solution was stirred for 5 min at 100 °C. The above solution was cooled to room temperature followed by addition of allyl alcohol (6 mmol, 348 mg) and amine (5 mmol). The above reaction mixture was then refluxed for 1–4 h. The progress of the reaction was monitored using GC analysis. On completion, the reaction mixture was cooled to room temperature and the products were extracted with ethyl acetate, dried over Na2SO4 and solvent was evaporated under vacuum. The obtained crude product was further purified by column chromatography using silica gel (60–120 mesh size), with petroleum ether/ethyl acetate (95/05) as an eluent to afford the pure product. All the products obtained and discussed in this work have been previously reported and representative products were characterized by suitable techniques such as 1H NMR (Varian 300 MHz) or (Bruker 400 MHz) and GC-MS (Shimadzu QP 2010) analysis.
General procedure for recycling and reuse of palladium catalysts.
After completion of the reaction, the reaction mixture was cooled to room temperature, the product was extracted in ethyl acetate and the aqueous layer containing the catalyst was subjected for further catalyst recyclability experiment. The study revealed that the recovered catalyst could be reused for eight consecutive cycles, without loss in activity affording excellent yield of the desired allylated product.
Characterization data of some selected compounds
N-Cinnamyl-N-methylaniline (3a).
Yield 94%. 1H NMR (400 MHz, CDCl3, 25 °C): δ = 7.18–7.36 (m, 7H, Ar), 6.78 (d, J = 8.0 Hz, 2H, Ar), 6.72 (t, J = 7.2 Hz, 1H, Ar), 6.51 (d, J = 16.0 Hz, 1H, CH
CH-Ph), 6.24 (dt, J = 16.0, 5.6 Hz, 1H, CH2-CH
CH), 4.07 (dd, J = 5.6, 1.6 Hz, 2H, N-CH2-CH), 2.97 (s, 3H, N-CH3) ppm. GC-MS (EI, 70 eV): m/z (%) = 223 (40) [M+], 118 (12), 117 (100), 115 (45), 91 (25), 51 (9), 44 (15).
N-Cinnamyl-2-methoxyaniline (3c).
Yield 94%. 1H NMR (400 MHz, CDCl3, 25 °C): δ = 7.2–7.4 (m, 5H, Ar), 6.6–6.9 (m, 5H (4H, Ar & 1H, CH
CH-Ph)), 6.35 (dt, J = 15.6, 5.6 Hz, 1H, CH2-CH
CH), 4.42 (bs, 1H, NH), 3.95 (dd, J = 6.0, 1.2 Hz, 2H, HN-CH2-CH), 3.85 = (s, 3H, -OCH3) ppm. GC-MS (EI, 70 eV): m/z (%) = 239 (43) [M+], 117 (100), 115 (41), 91 (31), 77 (10), 45 (46), 44 (38).
N-Cinnamyl-2-fluoroaniline (3d).
Yield 94%. 1H NMR (400 MHz, CDCl3, 25 °C): δ = 7.2–7.4 (m, 5H, Ar), 6.94–7.0 (m, 2H, Ar), 6.74 (t, J = 8.0 Hz, 1H, Ar), 6.58–6.67 (m, 2H (1H, Ar and 1H, CH
CH-Ph)), 6.3 (dt, J = 15.6, 5.6 Hz, 1H, CH2-CH
CH), 4.1 (bs, 1H, NH), 3.96 (d, J = 5.5, 2H, HN-CH2-CH) ppm. GC-MS (EI, 70 eV): m/z (%) = 227(33.7) [M+], 117 (100), 115 (44), 91 (20), 77 (10).
N-Allyl-2-methylaniline (6b).
Yield 90%. 1H NMR (300 MHz, CDCl3, 25 °C): δ = 6.64–7.1 (m, 2H, Ar), 6.54–6.64 (m, 2H, Ar), 5.87–6.0 (m, 1H, CH2-CH
CH2), 5.24 (d, J = 17.1 Hz, 1H, CH
CH2 (trans)), 5.12 (d, J = 10.2 Hz, 1H, CH
CH2 (cis)), 3.75 (d, J = 5.4 Hz, NH-CH2-CH), 3.42 (bs, NH), 2.1 (s, 3H, Ar-CH3) ppm. GC-MS (EI, 70 eV): m/z (%) = 147 (100) [M+], 146 (26), 120 (79), 118 (58), 106 (48), 91 (43), 65 (28).
N-Allyl-2-methoxyaniline (6c).
Yield 90%. 1H NMR (300 MHz, CDCl3, 25 °C): δ = 6.62–6.91 (m, 4H, Ar), 6.0 (m, 1H, CH2-CH
CH2), 5.31 (d, J = 16.5 Hz, 1H, -CH
CH2 (trans)), 5.18 (d, J = 9.6 Hz, 1H, -CH
CH2 (cis)), 4.4 (bs, 1H, Ar-NH-CH2), 3.87 (s, 3H, Ar-OCH3), 3.8 (m, 2H, NH-CH2-CH) ppm. GC-MS (EI, 70 eV): m/z (%) = 163 (100) [M+], 148 (35), 121 (25), 120 (64), 92 (24), 77 (24), 65 (33), 41 (28).
N-Allyl-2-fluoroaniline (6d).
Yield 88%. 1H NMR (300 MHz, CDCl3, 25 °C): δ = 6.9–7.0 (m, 2H, Ar), 6.56–6.68 (m, 2H, Ar), 5.87–6.0 (m, 1H, CH2-CH
CH2), 5.26 (d, J = 17.1 Hz, 1H, CH
CH2 (trans)), 5.15 (d, J = 10.2 Hz, 1 H, CH
CH2 (cis)), 4.0 (bs, 1H, -NH), 3.76 (d, J = 4.8 Hz, 2H, NH-CH2-CH) ppm. GC-MS (EI, 70 eV): m/z (%) = 151 (100) [M+], 150 (55), 124 (93), 77 (45), 41 (23).
N-Allyl-2-chloroaniline (6e).
Yield 91%. 1H NMR (300 MHz, CDCl3, 25 °C): δ = 7.22 (d, J = 7.5 Hz, 1H, Ar), 7.1 (t, 1H, J = 7.5 Hz, Ar), 6.56–6.61 (m, 2H, Ar), 5.84–5.96 (m, 1H, NH-CH
CH2), 5.25 (d, J = 17.1 Hz, 1H, CH
CH2(trans)), 5.15 (d, J = 10.2 Hz, 1H, CH
CH2 (cis)), 4.43 (bs, 1H, NH), 3.76 (d, J = 4.8 Hz, 2H, NH-CH2-CH) ppm. GC-MS (EI, 70 eV): m/z (%) = 169 (28) [M+2], 167 (88) [M+], 166 (25), 140 (97), 138 (26), 132 (100), 130 (59), 99 (20), 77 (33), 41 (22).
N-Allylnaphthalene-1-amine (6f).
Yield 90%. 1H NMR (300 MHz, CDCl3, 25 °C): δ = 7.7–7.75 (m, 2H, Ar), 7.2–7.4 (m, 4H, Ar), 6.5 (d, J = 7.5 Hz, 1H, Ar), 6.0 (m, 1H, CH2-CH
CH2), 5.3 (d, J = 17.4 Hz, 1H, CH
CH2(trans)), 5.2 (d, J = 10.2 Hz, 1H, CH
CH2 (cis)), 4.37 (bs, 1H, NH), 3.86 (d, J = 5.1 Hz, 2H, NH-CH2-CH) ppm. GC-MS (EI, 70 eV): m/z (%) = 183 (94) [M+], 142 (37), 115 (100), 77 (13).
Acknowledgements
The authors (YSW) are greatly thankful to Council of Scientific and Industrial Research (CSIR), India, for providing fellowship.
References
-
(a)
J. Tsuji, in Handbook of Organopalladium Chemistry for Organic Synthesis, ed. E.-i. Negishi, John Wiley & Sons, Inc., New York, USA, 2003, vol. 2, ch 1.1 Search PubMed;
(b)
Comprehensive Organic Synthesis, ed. B. M. Trost and I. Fleming, Pergamon, New York, 1991, vol. 4, p. 585 Search PubMed.
-
(a) C. Torborg and M. Beller, Adv. Synth. Catal., 2009, 351, 3027–3043 CrossRef CAS;
(b) M. Prashad, J. Med. Chem., 1993, 36, 631–632 CrossRef CAS;
(c) E. T. Michalson and J. Szmuszkovicz, Prog. Drug Res., 1989, 22, 135–149 CrossRef;
(d) G. Petranyi, N. S. Ryder and A. Stutz, Science, 1984, 224, 1239–1241 CAS;
(e) B. M. Trost and M. L. Crawley, Chem. Rev., 2003, 103, 2921–2943 CrossRef CAS.
-
(a) T. E. Muller, K. C. Hultzsch, M. Yus, F. Foubelo and M. Tada, Chem. Rev., 2008, 108, 3795–3892 CrossRef;
(b) I. Kadota, A. Shibuya, L. M. Lutete and Y. Yamamoto, J. Org. Chem., 1999, 64, 4570–4571 CrossRef CAS;
(c) N. T. Patil, H. Wu, I. Kadota and Y. Yamamoto, J. Org. Chem., 2004, 69, 8745–8750 CrossRef CAS;
(d) Y. S. Wagh, P. J. Tambade, D. N. Sawant and B. M. Bhanage, Eur. J. Org. Chem., 2010, 5071–5076 CrossRef CAS;
(e) Y. S. Wagh, D. N. Sawant, P. J. Tambade, K. P. Dhake and B. M. Bhanage, Tetrahedron, 2011, 67, 2414–2421 CrossRef CAS.
-
(a) K. E. Atkins, W. E. Walker and R. M. Manyik, Tetrahedron Lett., 1970, 3821–3824 CrossRef CAS;
(b) S.-C. Yang and Y.-C. Tsai, Organometallics, 2001, 20, 763–770 CrossRef CAS;
(c) H. Kinoshita, H. Shinokubo and K. Oshima, Org. Lett., 2004, 6, 4085–4088 CrossRef CAS;
(d) S.-C. Yang, Y.-C. Hsu and K.-H. Gan, Tetrahedron, 2006, 62, 3949–3958 CrossRef CAS;
(e) T. Nishikata and B. H. Lipshutz, Org. Lett., 2009, 11, 2377–2379 CrossRef CAS.
-
(a) D. Xing and D. Yang, Org. Lett., 2010, 12, 1068–1071 CrossRef CAS;
(b) P. Mukherjee and R. A. Widenhoefer, Org. Lett., 2010, 12, 1184–1187 CrossRef CAS;
(c) P. Mukherjee and R. A. Widenhoefer, Org. Lett., 2011, 13, 1334–1337 CrossRef CAS.
-
(a) S.-C. Yang, W.-H. Feng and K.-H. Gan, Tetrahedron, 2006, 62, 3752–3760 CrossRef CAS;
(b) M. Utsunomiya, Y. Miyamoto, J. Ipposhi, T. Ohshima and K. Mashima, Org. Lett., 2007, 9, 3371–3374 CrossRef CAS;
(c) T. Ohshima, Y. Miyamoto, J. Ipposhi, Y. Nakahara, M. Utsunomiya and K. Mashima, J. Am. Chem. Soc., 2009, 131, 14317–14328 CrossRef CAS.
-
(a) I. Dubovyk, I. D. G. Watson and A. K. Yudin, J. Am. Chem. Soc., 2007, 129, 14172–14173 CrossRef CAS;
(b) L. Adak, K. Chattopadhyay and B. C. Ranu, J. Org. Chem., 2009, 74, 3982–3985 CrossRef CAS;
(c) T. Nagano and S. Kobayashi, J. Am. Chem. Soc., 2009, 131, 4200–4201 CrossRef CAS;
(d) M.-C. Liao, X.-H. Duan and Y.-M. Liang, Tetrahedron Lett., 2005, 46, 3469–3472 CrossRef CAS;
(e) H. Danjo, D. Tanaka, T. Hayashi and Y. Uozumi, Tetrahedron, 1999, 55, 14341–14352 CrossRef CAS;
(f) M. Feuerstein, D. Laurenti, H. Doucet and M. Santelli, Tetrahedron Lett., 2001, 42, 2313–2315 CrossRef CAS;
(g) Y. Uozumi, H. Tanaka and K. Shibatomi, Org. Lett., 2004, 6, 281–283 CrossRef CAS.
-
(a) T. Nishikata and B. H. Lipshutz, Chem. Commun., 2009, 6472–6474 RSC.
-
(a) M. Moreno-Manas, L. Morral and R. Pleixats, J. Org. Chem., 1998, 63, 6160–6166 CrossRef CAS.
-
(a) K. H. Shaughnessy, Chem. Rev., 2009, 109, 643–710 CrossRef CAS;
(b) U. M. Lindstrom, Chem. Rev., 2002, 102, 2751–2772 CrossRef;
(c) A. N. Marziale, D. Jantke, S. H. Faul, T. Reiner, E. Herdtweck and J. Eppinger, Green Chem., 2011, 13, 169–177 RSC;
(d) D. B. Bagal, Z. S. Qureshi, K. P. Dhake, S. R. Khan and B. M. Bhanage, Green Chem., 2011, 13, 1490–1494 RSC;
(e) S. Shirakawa and S. Shimizu, Synlett, 2008, 1539–1542 CAS.
- References for TPPTS:
(a) H. Gulyas, A. Szolloosy, B. E. Hanson and J. Bakos, Tetrahedron Lett., 2002, 43, 2543–2546 CrossRef CAS;
(b)
V. Michelet, M. Savignac and J.-P. Genet, Electronic Encyclopedia of Reagents for Organic Synthesis, John Wiley, New York, 2004 Search PubMed;
(c)
L. Leseurre, J.-P. Genet and V. Michelet, in Handbook of Green Chemistry Series: Water as a Green Solvent, ed. P. Anastas and C.-J. Li, John Wiley and Sons, 2010, ch. 5 Search PubMed;
(d)
J. P. Genet, M. Savignac and S. Lemaire-Audoire, in Chemistry for the 21st century IUPAC Monographs, ed. S. I. Murahashi and S. G. Davies, New York, 1999, pp. 55–79 Search PubMed;
(e) B. M. Bhanage, S. S. Divekar, R. M. Deshpande and R. V. Chaudhari, Org. Process Res. Dev., 2000, 4, 342–345 CrossRef CAS;
(f) H. Shaughnessy, Eur. J. Org. Chem., 2006, 1827–1835 CrossRef;
(g) F. Neatu, L. Protesescu, M. Florea, V. I. Parvulescu, C. M. Teodorescu, N. Apostol, P. Y. Toullec and V. Michelet, Green Chem., 2010, 12, 2145–2149 RSC;
(h) E. Blart, J. P. Genet, M. Safi, M. Savignac and D. Sinou, Tetrahedron, 1994, 50, 505–514 CrossRef CAS;
(i) S. Sigismondi and D. Sinou, J. Mol. Catal. A: Chem., 1997, 116, 289–296 CrossRef CAS;
(j) A. Choplin, S. dos Santos, F. Quignard, S. Sigismondi and D. Sinou, Catal. Today, 1998, 42, 471–478 CrossRef CAS;
(k) S. Santos, Y. Tong, F. Quignard, A. Choplin, D. Sinou and J. P. Dutasta, Organometallics, 1998, 17, 78–89 CrossRef;
(l) J. P. Genet, E. Blart and M. Savignac, Synlett, 1992, 715–717 CrossRef CAS;
(m) J. P. Genet, E. Blart, M. Savignac, S. Lemeune, S. Lemaire-Audoire, J.-M. Paris and J.-M. Bernard, Tetrahedron, 1994, 50, 497–503 CrossRef CAS;
(n) J. P. Genet and M. Savignac, J. Organomet. Chem., 1999, 576, 305–317 CrossRef;
(o) C. Amatore, E. Blart, J. P. Genet, A. Jutand, S. Lemaire-Audoire and M. Savignac, J. Org. Chem., 1995, 60, 6829–6839 CrossRef CAS;
(p) C.-J. Li, Acc. Chem. Res., 2002, 35, 533–538 CrossRef CAS.
Footnote |
† Electronic supplementary information (ESI) available: Experimental details and characterization data of selected products. See DOI: 10.1039/c2cy00474g |
|
This journal is © The Royal Society of Chemistry 2012 |
Click here to see how this site uses Cookies. View our privacy policy here.