DOI:
10.1039/C0NR00076K
(Paper)
Nanoscale, 2010,
2, 1674-1683
Complex ZnO nanotree arrays with tunable top, stem and branch structures†
Received
2nd February 2010
, Accepted 15th April 2010
First published on
25th May 2010
Abstract
Hierarchical tree-, mushroom- and cockscomb-like ZnO arrays with increasing branching order and complexities have been grown in situ on cheap zinc plates by a simple hydrothermal oxidation approach. Their morphology, crystal structure and orientation relationship are characterized by powder X-ray diffraction, scanning electron microscopy (SEM) and cross-sectional high-resolution transmission electron microscopy (HRTEM). The wurtzite ZnO arrays, growing mainly in the [0001] direction, show a special orientation relationship between the stem and the branch as well as a novel stem–branch boundary which might be attributed to the least mismatch between {10
1} and (0002) lattice planes. The co-solvent ethylenediamine (en) was used to control the morphology and complexing of these complex ZnO nanostructures. Correspondingly, the physical properties of ZnO nanostructure assembly arrays were tuned and a stronger UV emission was observed with negligible emissions in the visible range, indicating the highly crystalline features of the complex ZnO micro-/nanostructured materials.
Introduction
Materials chemists have demonstrated exquisite control over the composition, phase, size, shape, morphology, hierarchical architecture and orientation of nanostructures.1 One-dimensional (1D) semiconductors are primary building blocks for “bottom-up” assembly in optoelectronic devices with designed functions.2 Remarkable advances have been achieved in dendritic and complex nanospecies composed of 1D nanostructures.3–27 Semiconducting nanotetrapods including their more complex linear and branched topology have been extensively developed as a typical family, which are generally randomly orientated within synthesis systems, although their arrangement in arrays would surely enhance their physical performance to some extent as is generally the case for 1D nanostructure arrays.23–27 Because a stable interface should have a low interfacial energy, there could be several structural types of connections between core and branches, such as a zinc blende (ZB) core and ZB pods [both (111) boundary planes], ZB core [(111) boundary plane] and wurtzite (WZ) pods [(0001) boundary plane] and WZ core and WZ pods (such as the well-known tetrapod ZnO), respectively.9–14,28 In the phase-pure WZ tetrapods, the interfaces are generally based on the presence of multiple [11
0] twin planes.12–14 Other twinning structures such as (10
l) (l = 1, 2, 3 or 4) and (1
14) are also described.28 The growth and characterization of a phase-pure dendritic wurtzite semiconductor crystallite with unexploited structure might be of great interest in pure science and of significance in developing new complex nanostructures and related functional materials.
Although substantial effort has been devoted to synthetic methodologies for branched nanostructures,3–30 considerable challenges still remains to develop rational strategies and facile routes to grow aligned and hierarchical structure arrays on a large scale with increasing complexity. Very rare cases of tree-like and phase-pure semiconductor arrays with both oriented branches and stems have been presented. Representative examples are GaP nanotrees8 and ZnO nanopropellers prepared by thermal evaporation and condensation processes with the assistance of metal nanoparticles.16 Another example is dendritic wurtzite InAs co-existing with a sphalerite phase grown by metal–organic vapor epitaxy.7 However, inert and refractory substrates are required for this oriented growth and it may leave metal nanoparticles behind as impurities. The complexity and branching events will not be rationally controlled without the help of catalysts in these approaches. Moreover, these approaches generally require economically prohibitive high temperatures and involve meticulous conditions. Therefore, a simple low-temperature route is needed to produce integrated semiconductor arrays with pure phases and compositions. Facile solution synthesis at relatively low temperature has good potential for scale-up and is a simple and cheap route to grow wurtzite ZnO nanostructures,19–23,30–40 one of the most promising materials in solid electronic and optical devices.24 Significantly, solution routes to ZnO nanorod (nanowire), nanotube and nanodisk arrays have been developed.23,31–39 However, a very attractive desire for materials chemistry might be one-pot growth of tree-like ZnO column arrays with tunable complexity under facile conditions.19,20 A pioneering ZnO nanorod-seeded sequential solution process was adopted by Liu and Tian et al. to produce hierarchical wurtzite ZnO crystallites with gradually branching events.19 The branching growth behavior was supposed to be performed by a twinning operation about the (1
02) twin planes.19 It was also mentioned that the particular branching might be also caused by other growth behavior such as coincident lattice matching, but direct evidence has not been illustrated. However, this nanorod-seeding process has several limitations. Firstly, primary nanorods are required before seeding growth on the substrate can occur. Secondly, tedious procedures for continuing branching growth are necessary. Thirdly, large-area densely packed and oriented arrays are not favorably produced due to the sparse distribution of the primary rods on the substrate. Finally, and more significantly, the structural modification of the linear core “stem” is limited by that of the primary rods. Up to now, a rational and facile solution chemistry route to highly branched and long ZnO column arrays with increasing complexity and tunable complex structures has not been developed. Herein we present a one-step, low-cost and environmentally benign route to grow large-scale and densely packed arrays of phase-pure, symmetrical and profusely branched ZnO complexities with tunable branch, top and even core stem structures. The new branching structure is characterized and confirmed for the first time and the unique, complicated and attractive morphologies are elucidated concisely.
Results and discussion
The complex ZnO structures could be grown on zinc foils in a carefully selected hydrothermal system. Thick and compact zinc foil is one of the cheapest and easily commercially available zinc sources.14,23,37–39 Although zinc metal can be dissolved and oxidized thermodynamically in aqueous solution of amine, the dissolution and oxidation is kinetically very slow and the velocity can be greatly reduced by the compact nature of the zinc foil. In addition, the saturation in aqueous solution is maintained at a certain level by the presence of zinc–diamine complex ions and the growth of ZnO, at least partially, is from the re-decomposition of zinc–diamine complexes as follows: | Zn + xen + H2O → [Zn(en)x]2+ + 2OH− + H2 | (1) |
| [Zn(en)x]2+ ↔ Zn2+ + xen | (2) |
| Zn2+ + 2OH− → Zn(OH)2 → ZnO + H2O | (3) |
Thus, compared to either common solution or ZnO nanoparticle-seeding chemistry, the nucleation and growth of ZnO might be mediated by the use of diamine and zinc foil.30 The growth stage might proceed for a period of time and controlled growth could be feasible. The longer lasting growth of complex structures might lead to a generation of longer ZnO rods as branches. In addition, a variety of zinc complex ions can be generated in aqueous solution with the change of diamine concentrations and the growth of ZnO within the hydrothermal system can be modified and more complex structures might be yielded.30,41 Moreover, since zinc and ZnO have very similar anisotropic space groups (Zn: JCPDS card No. 04-0813, P63/mmc, a = 2.665, c = 4.947 Å; ZnO: JCPDS card No. 80-0075, P63mc, a = 3.253, c = 5.209 Å), the oriented/textured growth might be readily achieved.14,23,37–39 Therefore, with the experience in simulating naturally and synthetically seeded growth of preferentially oriented plants and nanorods, we could grow high and dense hierarchical ZnO crystal arrays from and rooted at the zinc foil in the presence of amine by optimizing the growth conditions.
Pine-tree-like ZnO arrays: Growth and structural characterizations
First of all, we describe the growth of a pine-tree-like ZnO crystallite array and illustrate the basic but unique structure in the wurtzite semiconductor family. The wurtzite crystal structure was detected by powder X-ray diffractions first (see Fig. S1 of the ESI†). Fig. 1a shows a typical continuous film of wurtzite ZnO tree arrays grown at 140 °C for 10 h in the aqueous solution of en at a typical concentration of 3.75 mol L−1. Each individual ZnO tree is composed of a hexagonal prismatic microcrystal as the main stem and abundant oriented nanobranches on its six {10
0} side surfaces (Fig. 1b and c), thus forming a nanostructured “pine-tree forest” (Fig. 1a and Figs. S2 and S3 of the ESI†). The height measured from the root to the top can be up to ca. 25 μm (Fig. S2). On each of the side surfaces, the branches mainly form multi-rows (Fig. 1b and Fig. S2c). The stem is preferentially grown in the direction nearly perpendicular to the substrate while the aligned branches are pointing to the substrate, but both the stem and branches grow along their [0001] crystallographic directions respectively (Fig. 1c and Fig. 2).
![(a) SEM image of typical branched ZnO nanotrees. The inset shows two top-view ZnO trees with a six-fold symmetry. (b) An enlargement of a side-view single nanotree. (c) TEM image of a single ZnO tree (middle) recorded along the [12̄10] direction, selected-area electron diffraction patterns (top left, top right and center) taken respectively from the branches and the trunk and lattice image (bottom left) and high-magnification TEM image (bottom right) of the branches. The green arrows indicate the major growth directions of the trunk and the branch, which share the [12̄10] direction. (d) A simple structural model of a branched ZnO nanotree projected along the [12̄10] direction. The relaxation at the interface between the trunk and the branch to achieve minimum interface energy is ignored here.](/image/article/2010/NR/c0nr00076k/c0nr00076k-f1.gif) |
| Fig. 1 (a) SEM image of typical branched ZnO nanotrees. The inset shows two top-view ZnO trees with a six-fold symmetry. (b) An enlargement of a side-view single nanotree. (c) TEM image of a single ZnO tree (middle) recorded along the [1 10] direction, selected-area electron diffraction patterns (top left, top right and center) taken respectively from the branches and the trunk and lattice image (bottom left) and high-magnification TEM image (bottom right) of the branches. The green arrows indicate the major growth directions of the trunk and the branch, which share the [1 10] direction. (d) A simple structural model of a branched ZnO nanotree projected along the [1 10] direction. The relaxation at the interface between the trunk and the branch to achieve minimum interface energy is ignored here. | |
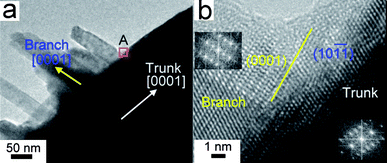 |
| Fig. 2 (a) High-magnification TEM image of parallel branches grown on a ZnO trunk, showing a special orientation relationship between the branches and the trunk. (b) HRTEM image of the branch/trunk (stem) junction marked by A, indicating that the branch/trunk boundary (the yellow line) is nearly parallel to the branch (0001) plane and the trunk (stem) (10![[1 with combining macron]](https://www.rsc.org/images/entities/char_0031_0304.gif) ) plane. Insets are FFT patterns of the branch and trunk (stem) areas, respectively. | |
These high ZnO nanotrees have unusual top structures (Figs. S2c and S4 of the ESI†). The stem top surface is neither smooth nor flat, but composed of short and bundled nanoribbon arrays. The nanoribbons are about 15 nm in diameter. The multiple nano-tips at the stem top surface might promote electron emission, having potential application for multiple-field-emission guns.
These ZnO trees have a novel branch structure. The branches are not generally hexagonal nanoprisms but quadrilateral blades and the surfaces of the nanoblades are not stepped16 but quite smooth (Figs. 1b and c). More detailed investigation confirms that the individual blade-like branch has two larger (top and bottom) surfaces parallel to ±(
010) and two smaller side surfaces parallel to ±(1
10) (Fig. 1c). Therefore, the branch cross-sections are quadrilateral with a large width/thickness ratio and the long edge parallel to the [1
10] direction (Fig. 1c). The thickness and width of the branch is about a few tens of nanometres in general and the length may be a couple of microns.
These ZnO nanotrees have unique connections between branches and stems compared to published hierarchical ZnO structures.13–18,28,29 Both the stem and branches are grown along their [0001] directions (Fig. 1c). This is similar to the reported complex ZnO in which the favorable growth direction is perpendicular to the (0001) lattice plane in most cases. However, the branches are not perpendicular, but oblique to the straight stem. This is quite different to those complex ZnO nanostructures grown within evaporation and condensation processes.14–17,29 The special orientation relationship between the stem and branches is that the [0001] major growth directions of the branch and stem form an angle of about 108°. The branch shares the [1
10] zone axis with the stem and the (0001) plane of the branch is nearly parallel to the (10
1) plane of the stem, which was confirmed by SAED and high-resolution TEM (Fig. 2). Considering such an orientation relationship, the successful growth of these branched ZnO trees could be attributed to the least (5%) mismatch between {10
1} and (0002) lattice spaces of wurtzite ZnO. Thus, a structure model is proposed in Fig. 1d in which the relaxation at the interface between the stem and the branch to achieve a minimum interface energy is ignored. Compared to previously reported branching ZnO nanostructures, such as nanotetrapods,13 nanocombs17a and nanopropellers,16 this structural model is quite unique.
Time-dependent experimental results imply there might be a layer precursor to the blade-like nanobranches. After 1 h of the reaction, the stems are enclosed by packed nanoslices (Fig. 3a) which are probably associated with a layered zinc complex.30,42 This is supported by the trace diffraction peak at low angle in the powder XRD pattern (Fig. S1a). These ZnO nanoslices (Fig. S1a) are the precursors to the blade-like nanobranches (Fig. 3). Heating for 5 h would result in short nanobranches which fully cover the microstems (Fig. 3b). They should be ZnO as detected by powder XRD pattern (Fig. S1b). The longer hydrothermal treatment such as for 10 h would generate 25-micron-tall oriented microstems, which might be among the tallest of such oriented arrays with phase purity on substrates (Fig. S2). Now based on the crystallographic relationship between the stem and blade-like nanobranches, a growth procedure may be understood as such, although no ZnS(en)0.5-like solid ZnO(en)x [or ZnO(OH)x(en)y] compounds have been detected directly so far.42 First, the precursory nanoslices on the side surface of a trunk at their early growth stage, probably with wurtzite slabs, serve as the nucleation site of the ZnO nanobranches. Second, each nanobranch grows along its [0001] direction. To reduce the interface strain energy, the nanobranch (0001) plane is nearly parallel to the trunk (10![[1 with combining macron]](https://www.rsc.org/images/entities/char_0031_0304.gif)
) plane and both the branch and the trunk share an identical [1
10] zone axis (Fig. 1).
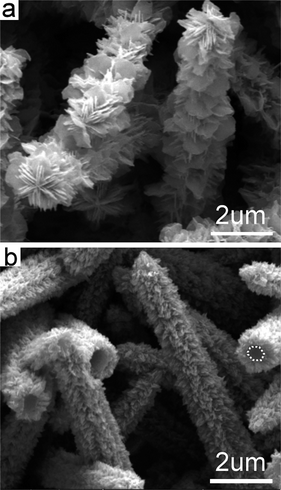 |
| Fig. 3 SEM images of ZnO products prepared with different reaction time: (a) 1.0 h and (b) 5.0 h, respectively. Other growth conditions are the same as those indicated in Fig. 1. A hexagonal trunk cross-section is indicated by white dashed lines. | |
Multiple-branching
Besides the reaction time, other synthesis conditions have great effects on the growth of our hierarchical ZnO crystallites. It is found that the diamine in the aqueous solution plays a crucial role in the successful growth of the hierarchical ZnO nano-/microstructures herein. Without the diamine, hierarchical ZnO structures could not be produced. Both the dimensions and complexity of ZnO crystallites could be tuned by the synthesis parameters. Diamine is a strong bidentate chelating agent to zinc ions with a higher stability constant than the hydroxyl group. The ZnO nanorod-seeded sequential solution process to produce hierarchical wurtzite ZnO crystallites suggests the gradually branching event resulted from light surface dissolution, i.e. chemical etching of diamine molecules on ZnO surfaces.19 The chemical reaction can be described as: | ZnO + yen + H2O ↔ [Zn(en)y]2+ + 2OH− | (4) |
Diamine molecules can etch the top and side surfaces of ZnO stems and produce site-specific heterogeneous nucleation and secondary growth. With the etching, some bud-like islands appear on the top and side surfaces. Simultaneously, more Zn complex ions for crystal growth are formed with increasing en concentration in the aqueous solution. With the release of zinc from the zinc complex ions and the mass transport of zinc from the solution to the surfaces of the solid bud-like islands, ZnO branches grow along the <0001> direction either on the top and side surfaces (Fig. 1b and c) because of the faster growth rate perpendicular to (0001) planes as indicated in Fig. 1c. Thus, the more diamine molecules are present in the solution, the more the etching sites on the surfaces. And consequently, the increasing diamine concentration yields more plentiful side branches and results in more complex top structures (Fig. 4). During these growth stages, diamine molecules play a significant catalyst-like role in the modification of the complicated micro/nanostructures (eqns (2)–(4)).30 In addition, high temperature will promote the growth of branched ZnO crystallites kinetically but the branching structure tends to deteriorate quickly (Fig. S5) while low temperature keeps the branched structures growing slowly and surviving for a long time (6 days, Fig. 5). Thus, at a relatively low temperature much more complex nano-/microstructures might be yielded (Fig. 5) while at a relatively high temperature, such as 180 °C for 10 h, the branches disappear (Fig. S5). This is because the boundary with ca. 5% mismatch is a metastable structure and can not survive at much higher temperature for a long time. That both the top and side surfaces are not smooth in Fig. S5 further suggests the possibility of chemical etching.
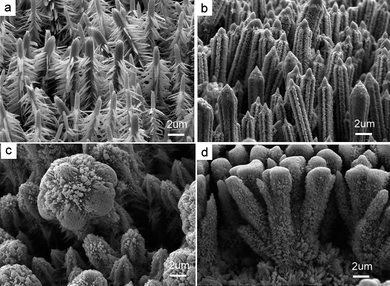 |
| Fig. 4 SEM images of hierarchical ZnO crystallite arrays grown by simple hydrothermal oxidation of zinc foil at the same temperature (140 °C), but different en concentrations: (a) 3.75, (b) 7.50, (c) 11.25 and (d) 15.0 mol L−1.The complexity of ZnO hierarchical structures increases with increasing en concentration. | |
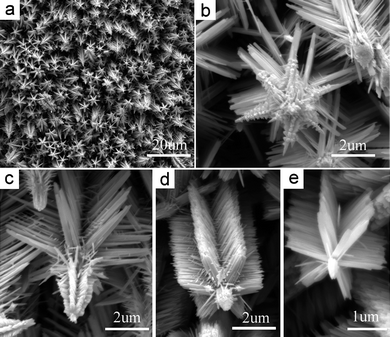 |
| Fig. 5 SEM images show (a) the top-view of a complex ZnO array grown at 100 °C with en concentration of 3.75 mol L−1 and (b)–(e) several unique individual ZnO crystalline trees. The fine ternary branches grown from the secondary branches with the specific angle 108° can be observed. These top structures become more exquisite from (e) to (b). | |
Ternary branches (TBs) grown on a secondary blade-like branch (SB) are observed in the high-magnification SEM images in Fig. 5b–d. The angle between the TBs and the SB is fixed at about 108°, the same as that between the SBs and the primary stem (PT), revealing that the growth behavior corresponds to the smallest mismatch between the {10
1} and (0002) lattice planes of wurtzite ZnO too. Additional TBs on the side surfaces near the stem tops are also observed in a few larger ZnO crystallites. These TBs are either nanoblades or hexagonal nanoprisms with sharp tips. Interestingly, on the side surfaces of the hexagonal prismatic TBs near the stem top (Fig. 5b), there exists orientated and orderly aligned nanobundles as TBs (Fig. 5b and c). However, the ZnO nanotrees hiding inside the film are generally smaller with negligible branches near the top parts and with negligible TBs on the blade-like primary branches (Fig. 5e). This might be attributed to lower en concentrations below the top surface of the film. This also indicates that higher en concentrations favor more complex structures. The further growth of the hyperbranches indicates that even without the assistance of metal catalysis, branching can occur endlessly under such conditions to generate more complex nanostructures. Figs. 5b–e show the different complexities of the top structures. With further increase of en concentration to 7.50 mol L−1, ZnO nanotree arrays with higher hierarchies are observed using microscopy (Fig. 6).
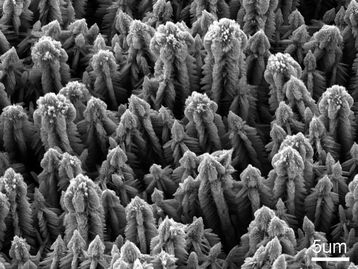 |
| Fig. 6 SEM image of complex ZnO crystals prepared at 100 °C in the reaction medium with amine concentration of 7.50 mol L−1. | |
More complex crystallite arrays: ZnO mushrooms
With the increase of en concentration, hierarchical growth of complex ZnO crystallite arrays has been successfully achieved with tuned branch, top and stem features. A higher diamine concentration will enhance the solubility of zinc and there will be more zinc species for crystal growth as the monomer in the solution medium (eqns (1)–(4)). Consequently, more complex structures with denser branches might be created at the top part on the film surface. In addition, with increasing diamine concentrations, more abundant branches tend to be more densely packed on the stem and the top part. Figs. 6–9 are SEM images of three typical ZnO products grown at 100 °C with increasing en concentrations, illustrating that branched ZnO crystallite arrays with increasing complexity have been grown.
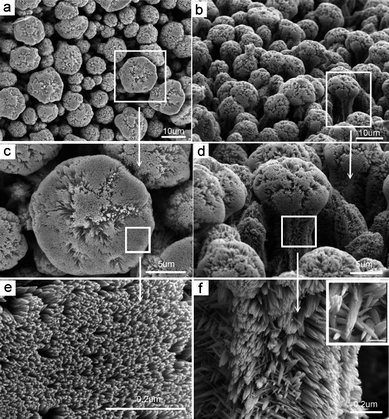 |
| Fig. 7 SEM images of the complex ZnO crystals prepared from the medium with en concentration of 11.25 mol L−1 at 100 °C. The top view (left panel) shows that the hexagonal-like top of an individual ZnO complex comprises closely packed nanowires. The side view (right panel) reveals the densely packed mushroom-like ZnO complex arrays and bushy branches on the side surface. | |
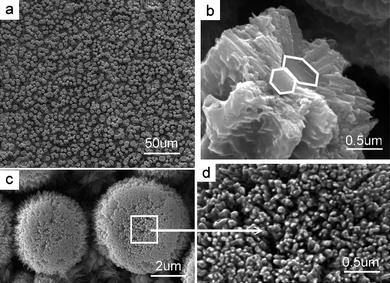 |
| Fig. 8 Different magnification SEM images illustrate surface features at an earlier growth stage before the complete growth of the complex ZnO mushrooms crowned by densely packed ZnO nanowires as shown in Fig. 7. (a) Shows that such an embryo crystallite array has been grown in orientation on a large area, (b) shows that this column is united by two aligned individual stems, and (c) is an enlarged image from (d) of two individual embryo ZnO mushrooms whose tops are capped by crowns formed by nanowire-like materials. | |
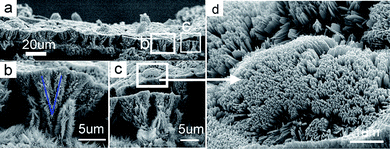 |
| Fig. 9 SEM images of the extremely complex cockscomb-like crystalline ZnO arrays grown with an en concentration of 15.0 mol L−1. Each cluster of cockscomb-like crystallites is aggregated by several individual branched stems covered densely by nanobranches at both top and sides. In each cluster, these ZnO stems are grown from one and the same root. In (d), it can be observed that the top is formed from rectangular blade-like sheets (short ribbons). | |
A typical example of abundantly branched ZnO crystallites with higher complexity is shown in Fig. 7. Their arrays look like a field of densely packed opulent mushrooms. Both the sides and top of a stem are covered by orientated nanorods. The diameters of branches on the side surfaces are about 100 nm. More detailed investigations indicate that these side branches are nanobundles (inset to Fig. 7f ), in most cases, composed of much thinner nanowires, which might result from the splitting of nanoblades. From these nanobundles, TBs are grown sparsely. Countless nanowires with diameters below 50 nm assemble radially on the top of individual stems to form a hemispherical crown up to a diameter of about 15 μm (Fig. 7a–e). A top view illustrates that these nanowires are favorably packed into hexagonal and chrysanthemum-like structures (Fig. 7c). It is revealed from cross sections of a broken ZnO stem that each ZnO column generally not only consisted of a single ZnO microprism, but of several microprims by self-coalescence side by side (Fig. S6 of the ESI†). Although a self-assembled ZnO column is formed by several aligned prismatic microcrystallites, it possesses a sixfold-like crown constructed by densely gathered and radially grown nanowires (Fig. 7c and Fig. S6). To the best of our knowledge, such self-coalescence of sub-complex-structures to form a larger branched complex structure while keeping the sixfold symmetry has not been mentioned in previous literature. The hexagonal cross-sections of the microprisms as sub-stems indicate that the entire stem is grown along the c-direction as indicated in Fig. 1. A low-magnification view demonstrates that the mushroom-like complex ZnO micro-/nanocrystallite columns which form a film with a smooth surface can be grown on a large scale by such a facile route (Fig. S7). In fact, several hexagonal ZnO microprisms with enclosed sheaths have self-combined inside one column embryo and the embryo arrays with mushroom-like outer geometry have been generated on large scale at an early growth stage (Fig. 8). The embryo arrays in Fig. 8 were confirmed to be crystalline ZnO by powder XRD (Fig. S8 of the ESI†). The coalescence of ZnO microprisms occurs with side-face attachment in the early growth stage to build larger complex structures. The sheath is not composed of well crystalline individual nanowires but highly stacked ZnO species (Fig. 8b). The nanowires as branches are grown from theses species during aging. The nanowire arrays atop have emerged at this early growth stage (Fig. 8c and d). During the aging (Ostwald ripening) with high saturation at high diamine concentration, some smaller ZnO species re-dissolve and more perfect crystallites are formed on the top and side surfaces respectively. In conclusion, the coalescence of prismatic ZnO microcrystallites plays a key role in the growth of such a large complex mushroom-like structure.
Much more complex crystallite arrays: Stem-splitting to ZnO cockscombs
Not only can the aligned coalescence of sub-stems side by side into a large column be achieved, but the splitting growth of one stem into two or more sub-stems can be observed. A further example of extremely complex ZnO structure array is displayed in Fig. 9, which looks like large-area blooming cockscombs (Fig. 9a). The side view indicates that cockscomb-like ZnO microcrystallites are composed of bushy nanobranches (Fig. 9b and c). The top crowns consist of densely orientated nanowires (Fig. 9c and d). Some of these aligned nanowires are closely packed into a nanosheet, implying that they are formed from the splitting of the possible blade-like precursor.
This extraordinary structure can be anatomized hierarchically as follows. Firstly, a cluster of cockscomb-like structure assembled by several individual nanobranch-covered stems poses a radial feature from the root to the top part. Secondly, an individual nanobranch-covered stem splits into two or more sub-stems and the newly formed sub-stem might split into several secondary sub-stems and so on (Fig. 9b and c). Thus, the sequential splitting growth of a main stem can generate countless sub-stems to form a tremendously large dendritic structure if the growth continues. This will be favorable at extremely high en concentrations and giant multiply branched ZnO trees might be created. A clearer illustration of splitting growth is observed from those “bald” stems produced before the generation of branching nanowires on their side surfaces and tops (Fig. 10). Several stems in a cluster in Fig. 9 and Fig. 10 can share the same root. An individual large cluster composed of several ZnO stems is nucleated from the same site and grown through splitting growth. Such a splitting growth has never been revealed in the synthesis of complex ZnO nano-/microstructures in previous literature, although the splitting growth of nanowires has been observed in other materials.43
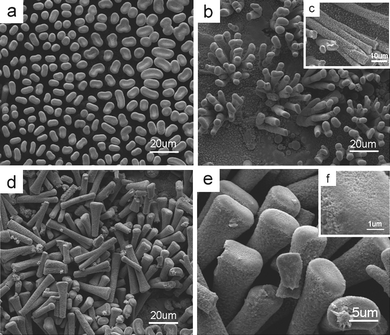 |
| Fig. 10 SEM images of the resultant film grown on an earlier stage before the growth of the cockscomb-like ZnO crystals (Fig. 9). (a) A top view of a virginal one with large area. (b) A slightly titled view of a photograph with vacant spaces after pulling lets us discover the bundle-like structures of the stems which share the same single root. The inset to (c) indicates the splitting growth; one can split into three. (d) An image shows the stems along different directions on the surface to indicate that the splitting growth is very common. (e) An enlarged SEM image showing a clearer surface and top structures. (f) At this early stage, the nanometre-sized branches have been previously yielded but packed. The powder XRD pattern indicates the film is composed of ZnO (Fig. S9 of the ESI†). | |
With further increase of en concentration to nearly pure amine solvent, complex ZnO nanostructures are obtained as illustrated in Fig. S10. Such an increasing complexity with increasing en concentration should be attributed to the etching, dissolution of some solid zinc species and the formation of various Zn(en)n2+ complexes in the growth medium, such as a possibly layered compound as the precursor to initiate the yield of blade-like branches.41,43 With the etching, some bud-like islands are formed and serve as new nucleation sites at an early growth stage for stem splitting growth, and with the etching on some blade-like branches, their splitting may take place. As it has been difficult to detect the chemical composition and even the presence of the precursory complex so far, investigations to illustrate the real growth mechanism and the detailed crystal structure of various precursory branches down to atomic level is under progress. However, it can be confirmed that the use of diamine plays a crucial role in the formation of the complex nanostructures (eqns (1)–(4)). The etching of diamine on a zinc plate surface and ZnO surface is the key issue to initiate the branching and splitting growth. With Ostwald ripening, the embryo ZnO structures (Figs. 3, 8, and 10) tend to have more symmetrical and complete architectures (Figs. 1, 7, and 9). The effect of en concentration on the growth of hierarchical ZnO nanostructured arrays can be schematically summarized in Scheme 1. Although hierarchical ZnO nanostructure arrays can be achieved with the addition of diamine to the aqueous solution (Fig. 4), evidence of much more complex nanostructures with multiple branching and splitting growth can only be observed at lower temperature (Figs. 5–10) due to kinetic control.
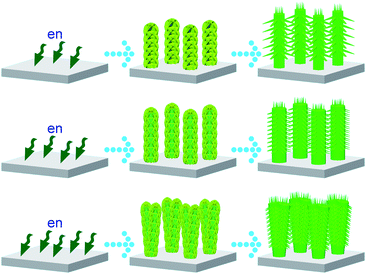 |
| Scheme 1 The effect of en concentration on the growth of hierarchical ZnO nanostructured arrays. The en concentrations increase from the first row to the third one. | |
Luminescence properties
The study of luminescence properties can shed light on defects in the ZnO crystals which are good candidates for optoelectronic and catalytic materials. Not only can the complexity of branched ZnO nano-/microstructures be controlled by varying the growth parameters as described above, but the photoluminescence properties can also be tuned. Under excitation using 255 nm ultraviolet, these complex ZnO crystallites exhibit a narrow emission at about 380 nm and a broad emission in the range of 450–600 nm, respectively (Fig. 11a). The nature of the band appearing in the range of 450–600 nm in un-doped ZnO remained controversial for decades, strong evidence was later presented in favor of oxygen vacancies (Vo) as the defect responsible for the band.9,24,44 Herein, the wide band around 450–600 nm indicates the presence of a variety of defects, typically attributed to oxygen vacancies. The broad band in the visible region decreases with enhancement of 380 nm emission for increasing en concentration from 3.75 to 11.25 mol L−1, then further increase in en concentration results in an increase in the intensity of the band in the visible range with a corresponding reduction of the 380 nm UV emission. These results demonstrate that the luminescence properties can be tuned by the preparation conditions (en concentration). Furthermore, there is an optimal concentration of en (11.25 mol L−1) for fabricating high quality dendritic nanostructured ZnO crystal arrays. Beside relatively weak UV emission, these hexagonal ZnO nanotrees as exhibited in Fig. 6 and Fig. 9 display broad green emissions representative of the deep level defects resulting from oxygen vacancies.9,24,45 However, our highly oriented mushroom-like complex ZnO nanostructures (Fig. 7) prepared at an en concentration of 11.25 mol L−1 displays the strongest UV emission peak at 380 nm with negligible deep level emission at the visible range. The strong emission at 380 nm is typically a free exciton peak.24 The above results illustrate that the physical performance of the ZnO nanostructures is significantly related to the growth conditions and the optimal en concentration herein to generate complex nanostructured arrays with low defect density.
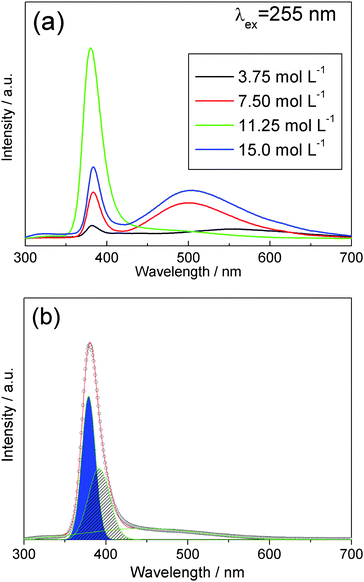 |
| Fig. 11 (a) Room-temperature photoluminescence of the complex ZnO crystallite arrays prepared with different en concentrations and (b) the deconvolution analysis of the green spectral curve in (a). | |
In order to have a better understanding of spectral feature, we applied deconvolution analysis to identify the UV light emission and the green band (Fig. 11b). The emission spectra can be deconvoluted into three Gaussian peaks with peak positions at 380 nm, 390 nm and 460 nm. Intrinsic photoluminescence from ZnO is at the wavelength of about 380 nm and the corresponding band-tail emission at about 390 nm is observed which is due to the surface effect of nanomaterials.24 The relatively weak green band indicates that there is only small amount of oxygen vacancies or other defects in the complex nanostructure which leads to strong UV light emission. These results convince us that highly crystalline ZnO complexes and their arrays can be developed through this facile solution approach. Furthermore, all the light emission is in the UV band which implies our new method to grow UV-emitting nanomaterials is a promising candidate for UV-sensitive nano-integrated optoelectronic systems and nanolasing applications.
Experimental section
The complex ZnO films were prepared by a hydrothermal oxidation (corrosion) of metallic zinc foils in an aqueous medium in the temperature range 100–180 °C within 1–120 h. The procedure is as follows: Ultrasonically washed metallic zinc foil was placed on the bottom of a Teflon cup (20 mL) in a stainless autoclave and then the cup was filled with a co-solvent of distilled water and en. After the solution growth of ZnO on the zinc foil at a temperature for a period of time, the autoclave was taken out and cooled naturally to the ambient temperature. After the zinc foil was washed with acetone, ethanol and distilled water, respectively, it was dried in a desiccator. A basic en concentration of 3.75 mol L−1 in the aqueous solution is the typical reaction condition to yield highly oriented ZnO nanotrees as shown in Fig. 1. The molecules of en can strongly coordinate zinc atoms and subsequently modulate the growth of ZnO and the morphologies of the ZnO films. Thus, the use of en can modify the surface patterns of ZnO films.
Crystal structures of the products were characterized by powder X-ray diffraction (XRD) and electron microscopy. Powder XRD patterns were collected on a diffractometer (Philips PW1830) using Cu Kα radiation (λ = 0.1541 nm). SEM images were taken on a JEOL JSM-6330F scanning electron microscope equipped with a field-emission gun or FEI Quanta 400 Thermal FE Environment Scanning Electron Microscope. The TEM and HRTEM work was done using JEM-2010HR and JEM-2100F transmission electron microscopes operated at an accelerating voltage of 200 kV. The TEM specimens were prepared using carbon-coated copper grids and a standard method for powder samples.
Photoluminescence (PL) was studied on a Fluorolog-3 fluorescence spectrophotometer at room temperature. An ozone-free, 450 W xenon lamp passing through the double-grating excitation and single-grating emission monochromators in a Czerny–Turner configuration was used as the excitation light source. The excitation wavelength is located at 255 nm.
Conclusions
In summary, we have rationally developed an easy environmentally benign solution approach to hierarchically controlled growth of dendritic ZnO crystallite arrays on a large scale. These progressively complex ZnO nanostructures are featured by unique top, branch and even stem structures. The increasing structural complexity is associated with the modification of the whole three parts: top, branches and stem. (1) The top structure can be modified by increasing the density and shape of its capping nanowires and nanoblades; (2) the branching behavior can be achieved with increasing density and sequential hyperbranch growth with blade-like structures; (3) the stem structures can be controlled with single, coalescent and splitting growth behavior. Beside the structural complexities, the physical properties can be tuned by reaction conditions. Complex and largest dendritic ZnO crystallites of high quality with negligible deep-level defects have been fabricated on a large scale. Structural characterization reveals a new branching mechanism based on the least distortion. This finding may develop a new catalogue of branched nanostructures and nanojunctions in wurtzite semiconductors which are surely to have new applications in mechanical, chemical, optical and electronic fields.
Acknowledgements
This work is supported financially by the National Natural Science Foundation (NSF) of China and the Government of Guangdong Province for NSF (Grants U0734002, 50872158 and 8251027501000010). Prof. M. Wu expresses great thanks to Prof. X. Y. Huang from Rutgers and now at Fujian Institute of Research on the Structure of Matter (CAS) for helpful discussions.
References
-
(a) C. Burda, X. B. Chen, R. Narayanan and M. A. El-Sayed, Chem. Rev., 2005, 105, 1025–1102 CrossRef CAS;
(b) Y. W. Jun, J. S. Choi and J. Cheon, Angew. Chem., Int. Ed., 2006, 45, 3414–3419 CrossRef CAS;
(c) G. W. Meng, F. M. Han, X. L. Zhao, B. S. Chen, D. C. Yang, J. X. Liu, Q. L. Xu, M. G. Kong, X. G. Zhu, Y. J. Jung, Y. J. Yang, Z. Q. Chu, M. Ye, S. Kar, R. Vajtai and P. M. Ajayan, Angew. Chem., Int. Ed., 2009, 48, 7166–7170 CrossRef CAS;
(d) C. C. Chen, A. B. Herhold, C. S. Johnson and A. P. Alivisatos, Science, 1997, 276, 398 CrossRef CAS;
(e) H. J. Lee, S. E. Habas, S. Kweskin, D. Butcher, G. A. Somorjai and P. D. Yang, Angew. Chem., Int. Ed., 2006, 45, 7824–7828 CrossRef CAS;
(f) J. Zhu, H. L. Peng, A. F. Marshall, D. M. Barnett, W. D. Nix and Y. Cui, Nat. Nanotechnol., 2008, 3, 477–481 CrossRef CAS;
(g) L. Manna, D. J. Milliron, A. Meisel, E. C. Scher and A. P. Alivisatos, Nat. Mater., 2003, 2, 382–385 CrossRef CAS;
(h) A. Fiore, R. Mastria, M. G. Lupo, G. Lanzani, C. Giannini, E. Carlino, G. Morello, M. D. Giorgi, Y. Q. Li, R. Cingolani and L. Manna, J. Am. Chem. Soc., 2009, 131, 2274–2282 CrossRef CAS;
(i) H. Cölfen and M. Antonietti, Angew. Chem., Int. Ed., 2005, 44, 5576–5591 CrossRef;
(j)
G. A. Ozin and A. C. Arsenault, Nanochemistry: A Chemical Approach to Nanomaterials, RSC Publishing: Cambridge, UK, 2005 Search PubMed;
(k)
M.-P. Pileni, Nanocrystals Forming Mesoscopic Structures, Wiley-VCH; Weinheim, 2005 Search PubMed.
-
(a) C. M. Lieber, MRS Bull., 2003, 28, 486–491 CAS;
(b) Y. N. Xia, P. D. Yang, Y. G. Sun, Y. Y. Wu, B. Mayers, B. Gates, Y. D. Yin, F. Kim and H. Q. Yan, Adv. Mater., 2003, 15, 353–389 CrossRef CAS;
(c) H. J. Fan, P. Werner and M. Zacharias, Small, 2006, 2, 700–717 CrossRef CAS;
(d) N. I. Kovtyukhova and T. E. Mallouk, Adv. Mater., 2005, 17, 187–192 CrossRef CAS;
(e)
Z. L. Wang, Nanowires and Nanobelts, Materials, Properties and Devices, New York, 2003 Search PubMed;
(f) T. H. Yu and S. L. Brock, ACS Nano, 2008, 2, 1563–1570 CrossRef CAS;
(g) H. M. Cheng, W. H. Chiu, C. H. Lee, S. Y. Tsai and W. F. Hsieh, J. Phys. Chem. C, 2008, 112, 16359–16364 CrossRef CAS;
(h) C. L. Choi, K. J. Koski, S. Sivasankar and A. P. Alivisatos, Nano Lett., 2009, 9, 3544–3549 CrossRef CAS;
(i) J. P. Mondia, R. Sharma, J. Schäfer, W. Smith, Y. P. Zhao, Z. H. Lu and L. J. Wang, Appl. Phys. Lett., 2008, 93, 121102 CrossRef;
(j) M. J. Bierman and S. Jin, Energy Environ. Sci., 2009, 2, 1050–1059 RSC;
(k) D. B. Suyatin, J. Sun, A. Fuhrer, D. Wallin, L. E. Fröberg, L. S. Karlsson, I. Maximov, L. R. Wallenberg, L. Samuelson and H. Q. Xu, Nano Lett., 2008, 8, 1100–1104 CrossRef CAS;
(l) H. Y. Xu, Y. Liang, Z. A. Liu, X. T. Zhang and S. K. Hark, Adv. Mater., 2008, 20, 3294–3297 CrossRef CAS.
-
(a) D. F. Zhang, L. D. Sun, C. J. Jia, Z. G. Yan, L. P. You and C. H. Yan, J. Am. Chem. Soc., 2005, 127, 13492–13493 CrossRef CAS;
(b) H. G. Yang and H. C. Zeng, J. Am. Chem. Soc., 2005, 127, 270–278 CrossRef CAS;
(c) Q. Kuang, Z. Y. Jiang, Z. X. Xie, S. C. Lin, Z. W. Lin, S. Y. Xie, R. B. Huang and L. S. Zheng, J. Am. Chem. Soc., 2005, 127, 11777–17784 CrossRef CAS;
(d) H. T. Shi, L. M. Qi, J. M. Ma and H. M. Cheng, J. Am. Chem. Soc., 2003, 125, 3450–3451 CrossRef CAS;
(e) U. K. Gautam, X. S. Fang, Y. Bando, J. H. Zhan and D. Golberg, ACS Nano, 2008, 2, 1015–1021 CrossRef CAS;
(f) H. J. You, J. X. Fang, F. Chen, M. Shi, X. P. Song and B. J. Ding, J. Phys. Chem. C, 2008, 112, 16301–16305 CrossRef CAS;
(g) Y. H. Chen, H. H. Hung and M. H. Huang, J. Am. Chem. Soc., 2009, 131, 9114–9121 CrossRef CAS;
(h) X. F. Yang, J. L. Zhuang, X. Y. Li, D. H. Chen, G. F. Ouyang, Z. Q. Mao, Y. X. Han, Z. H. He, C. L. Liang, M. M. Wu and J. M. Yu, ACS Nano, 2009, 3, 1212–1218 CrossRef CAS.
-
(a) W. M. Chiu, C. H. Lee, H. M. Cheng, H. F. Lin, S. C. Liao, J. M. Wu and W. F. Hsieh, Energy Environ. Sci., 2009, 2, 694–698 RSC;
(b) S. O. Cho, E. J. Lee, H. M. Lee, J. G. Kim and Y. J. Kim, Adv. Mater., 2006, 18, 60–65 CrossRef CAS;
(c) J. Q. Hu, Y. Bando, J. H. Zhan, X. L. Yuan, T. Sekiguchi and D. Golberg, Adv. Mater., 2005, 17, 971–975 CrossRef CAS;
(d) S. Mathur and S. Barth, Small, 2007, 3, 2070–2075 CrossRef CAS;
(e) Y. J. Hsu and S. Y. Lu, Small, 2008, 4, 951–955 CrossRef CAS;
(f) Y. W. Jun, Y. Y. Jung and J. Cheon, J. Am. Chem. Soc., 2002, 124, 615–619 CrossRef CAS;
(g) D. Milliron, J. S. M. Hughes, Y. Cui, L. Manna, J. B. Li, L. W. Wang and A. P. Alivisatos, Nature, 2004, 430, 190–195 CrossRef CAS;
(h) Y. D. Yin and A. P. Alivisatos, Nature, 2005, 437, 664–670 CrossRef CAS;
(i) J. Zheng, Y. Yang, B. Yu, X. B. Song and X. G. Li, ACS Nano, 2008, 2, 134–142 CrossRef CAS.
-
(a) D. L. Wang, F. Qian, C. Yang, Z. H. Zhong and C. M. Lieber, Nano Lett., 2004, 4, 871–874 CrossRef CAS;
(b) X. G. Han, M.
S. Jin, Q. Kuang, X. Zhou, Z. X. Xie and L. S. Zheng, J. Phys. Chem. C, 2009, 113, 2867–2872 CrossRef CAS;
(c) C. W. Cheng, B. Liu, H. Y. Yang, W. W. Zhou, L. Sun, R. Chen, S. F. Yu, J. X. Zhang, H. Gong, H. D. Sun and H. J. Fan, ACS Nano, 2009, 3, 3069–3076 CrossRef CAS;
(d) A. Purkayastha, Q. Y. Yan, M. S. Raghuveer, D. D. Gandhi, H. F. Li, Z. W. Liu, R. V. Ramanujan, T. Borca-Tasciuc and G. Ramanath, Adv. Mater., 2008, 20, 2679–2683 CrossRef CAS.
-
(a) K. L. Hull, J. W. Grebinski, T. H. Kosel and M. Kuno, Chem. Mater., 2005, 17, 4416–4425 CrossRef CAS;
(b) Y. Liu, Z. H. Chen, Z. H. Kang, I. Bello, X. Fan, I. Shafiq, W. J. Zhang and S. T. Lee, J. Phys. Chem. C, 2008, 112, 9214–9218 CrossRef CAS;
(c) A. Dong, R. Tang and W. E. Buhro, J. Am. Chem. Soc., 2007, 129, 12254–12262 CrossRef CAS.
- S. J. May, J. G. Zheng, B. W. Wessels and L. J. Lauhon, Adv. Mater., 2005, 17, 598–602 CrossRef CAS.
- K. A. Dick, K. Deppert, M. W. Larsson, T. MÅrtensson, W. Seifert, L. R. Wallenberg and L. Samuelson, Nat. Mater., 2004, 3, 380–384 CrossRef CAS.
-
(a) Q. Wan, T. H. Wang and J. C. Zhao, Appl. Phys. Lett., 2005, 87, 083105 CrossRef;
(b) L. Lazzarini, G. Salviati, F. Fabbri, M. Z. Zha, D. Calestani, A. Zappettini, T. Sekiguchi and B. Dierre, ACS Nano, 2009, 3, 3158–3164 CrossRef CAS.
- Y. C. Zhu, Y. Bando, D. F. Xue and D. Golberg, J. Am. Chem. Soc., 2003, 125, 16196–16197 CrossRef CAS.
-
(a) Y. W. Jun, S. M. Lee, N. J. Kang and J. Cheon, J. Am. Chem. Soc., 2001, 123, 5150–5151 CrossRef CAS;
(b) L. Manna, E. C. Scher and A. P. Alivisator, J. Am. Chem. Soc., 2000, 122, 12700–12706 CrossRef CAS.
-
(a) L. Carbone, S. Kudera, E. Carlino, W. J. Parak, C. Giannini, R. Cingolani and L. Manna, J. Am. Chem. Soc., 2006, 128, 748–755 CrossRef CAS;
(b) J.-Q. Hu, Y. Bando and D. Golberg, Small, 2005, 1, 95–99 CrossRef CAS.
- Y. Dai, Y. Zhang and Z. L. Wang, Solid State Commun., 2003, 126, 103–633 CrossRef CAS.
- Z. L. Wang, X. Y. Kong, Y. Ding, P. X. Gao, W. L. Hughes, R. Yang and Y. Zhang, Adv. Funct. Mater., 2004, 14, 943–956 CrossRef CAS.
-
(a) P. X. Gao and Z. L. Wang, J. Phys. Chem. B, 2002, 106, 12653–12658 CrossRef CAS;
(b) C. X. Xu, X. W. Sun, B. J. Chen, Z. L. Dong, M. B. Yu, X. H. Zhang and S. J. Chua, Nanotechnology, 2005, 16, 70–73 CrossRef CAS.
- P. X. Gao and Z. L. Wang, Appl. Phys. Lett., 2004, 84, 2883–2885 CrossRef CAS.
-
(a) H. Q. Yan, R. R. He, J. Johnson, L. Matthew, R. J. Saykally and P. D. Yang, J. Am. Chem. Soc., 2003, 125, 4728–4729 CrossRef CAS;
(b) H. Q. Yan, R. R. He, J. Pham and P. D. Yang, Adv. Mater., 2003, 15, 402–405 CrossRef CAS.
-
(a) J. Y. Lao, J. G. Wen and Z. F. Ren, Nano Lett., 2002, 2, 1287–1291 CrossRef CAS;
(b) J. Y. Lao, J. Y. Huang, D. Z. Wang and Z. F. Ren, J. Mater. Chem., 2004, 14, 770–773 RSC;
(c) R. F. Zhuo, H. T. Feng, J. T. Chen, D. Yan, J. J. Feng, H. J. Li, B. S. Geng, S. Cheng, X. Y. Xu and P. X. Yan, J. Phys. Chem. C, 2008, 112, 11767–11775 CrossRef CAS.
-
(a) T. L. Sounart, J. Liu, J. A. Voigt, J. W. P. Hsu, E. D. Spoerke, Z. R. Tian and Y. B. Jiang, Adv. Funct. Mater., 2006, 16, 335–344 CrossRef CAS;
(b) T. L. Sounart, J. Liu, J. A. Voigt, M. Huo, E. D. Spoerke and B. McKenzie, J. Am. Chem. Soc., 2007, 129, 15786–15793 CrossRef CAS;
(c) T. R. Zhang, W. J. Dong, M. Keeter-Brewer, S. Konar, R. N. Njabon and Z. R. Tian, J. Am. Chem. Soc., 2006, 128, 10960–10968 CrossRef CAS.
- F. H. Zhao, X. Y. Li, J.-G. Zheng, X. F. Yang, F. L. Zhao, K. S. Wong, J. Wang, W. J. Lin, M. M. Wu and Q. Su, Chem. Mater., 2008, 20, 1197–1199 CrossRef CAS.
- X. P. Gao, Z. F. Zheng, H. Y. Zhu, G. L. Pan, J. L. Bao, F. Wu and D. Y. Song, Chem. Commun., 2004, 1428–1429 RSC.
-
(a) B. Liu and H. C. Zeng, J. Am. Chem. Soc., 2004, 126, 16744–16746 CrossRef CAS;
(b) M. S. Mo, J. C. Yu, L. Z. Zhang and S. K. A. Li, Adv. Mater., 2005, 17, 756–760 CrossRef CAS.
-
(a) Z. R. Qiu, K. S. Wong, M. M. Wu, W. J. Lin and H. F. Xu, Appl. Phys. Lett., 2004, 84, 2739–2941 CrossRef CAS;
(b) C. Li, G. S. Hong, P. W. Wang, D. P. Yu and L. M. Qi, Chem. Mater., 2009, 21, 891–897 CrossRef CAS.
-
(a) Ü. Özgür, Y. I. Alivov, C. Liu, A. Teke, M. A. Reshchikov, S. Doğan, V. Avrutin, S. J. Cho and H. Morkoç, J. Appl. Phys., 2005, 98, 041301 CrossRef;
(b) A. B. Djurišić and Y. H. Leung, Small, 2006, 2, 944–961 CrossRef CAS;
(c) Z. Y. Fan and J. G. Lu, J. Nanosci. Nanotechnol., 2005, 5, 1561–13 CrossRef CAS.
- G. Z. Shen, Y. Bando, B. D. Liu, D. Golberg and C. J. Lee, Adv. Funct. Mater., 2006, 16, 410–416 CrossRef CAS.
- M. H. Huang, S. Mao, H. Feick, H. Q. Yan, Y. Y. Wu, H. Kind, E. Weber, R. Russo and P. D. Yang, Science, 2001, 292, 1897–1899 CrossRef CAS.
- L. E. Greene, M. Law, D. H. Tan, M. Montano, J. Goldberger, G. Somorjai and P. D. Yang, Nano Lett., 2005, 5, 1231–1236 CrossRef CAS.
-
(a) J. H. Zhan, Y. Bando, J. Q. Hu, D. Golberg and K. Kurashima, Small, 2006, 2, 62–65 CrossRef CAS;
(b) Y. Ding and Z. L. Wang, J. Phys. Chem. B, 2004, 108, 12280–12291 CrossRef CAS;
(c) S. G. Hussain, D. Liu, X. Huang, S. Ali and M. H. Sayyad, J. Phys. Chem. C, 2008, 112, 11162–11168 CrossRef CAS;
(d) X. Li, F. Zhao, J. Fu, X. Yang, J. Wang, C. Liang and M. Wu, Cryst. Growth Des., 2009, 9, 409–413 CrossRef CAS.
- R. C. Wang, C. P. Liu, J. L. Huang and S. J. Chen, Appl. Phys. Lett., 2005, 87, 053103 CrossRef.
-
(a) X. D. Gao, X. M. Li and W. D. Yu, J. Phys. Chem. B, 2005, 109, 1155–1161 CrossRef CAS;
(b) M. Yang, G. S. Pang, L. F. Jiang and S. H. Feng, Nanotechnology, 2006, 17, 206–212 CrossRef CAS;
(c) Y. Lv, C. P. Li, L. Guo, Q. X. Wang, R. M. Wang, H. B. Xu, S. H. Yang, X. C. Al and J. P. Zhang, Appl. Phys. Lett., 2005, 87, 163103 CrossRef;
(d) F. Lu, W. P. Cai and Y. G. Zhang, Adv. Funct. Mater., 2008, 18, 1047–1056 CrossRef CAS.
- Z. R. Tian, J. A. Voigt, J. Liu, B. Mckenzie, M. J. Mcdermott, M. A. Rodriguez, H. Konishi and H. F. Xu, Nat. Mater., 2003, 2, 821–826 CrossRef CAS.
- Z. R. Tian, J. A. Voigt, J. Liu, B. Mckenzie and M. J. Mcdermott, J. Am. Chem. Soc., 2002, 124, 12954–12955 CrossRef CAS.
- L. E. Greene, M. Law, J. Goldberger, F. Kim, J. C. Johnson, Y. F. Zhang, R. J. Saykally and P. D. Yang, Angew. Chem., Int. Ed., 2003, 42, 3031–3134 CrossRef CAS.
-
(a) L. Vayssieres, K. Keis, A. Hagfeldt and S. E. Lindquist, Chem. Mater., 2001, 13, 4395–4398 CrossRef CAS;
(b) H. Q. Le, S. J. Chua, K. P. Loh, E. A. Fitzgerald and Y. W. Koh, Nanotechnology, 2006, 17, 483–488 CrossRef CAS;
(c) Z. Wang, X. F. Qiang, J. Yin and Z. K. Zhu, Langmuir, 2004, 20, 3441–3448 CrossRef CAS;
(d) Y. Sun, G. M. Fuge, N. A. Fox, D. J. Riley and M. N. R. Ashfold, Adv. Mater., 2005, 17, 2477–2481 CrossRef CAS.
-
(a) H. D. Yu, Z. P. Zhang, M. Y. Han, X. T. Hao and F. R. Zhu, J. Am. Chem. Soc., 2005, 127, 2378–2379 CrossRef CAS;
(b) H. Zhang, D. R. Yang, X. Y. Ma and D. L. Que, J. Phys. Chem. B, 2005, 109, 17055–17059 CrossRef CAS.
-
(a) J. H. Choy, E. S. Jang, J. H. Won, J. H. Chung, D. J. Jang and Y. W. Kim, Adv. Mater., 2003, 15, 1911–1914 CrossRef CAS;
(b) K. Govender, D. S. Boyle, P. O'Brien, D. Binks, D. West and D. Coleman, Adv. Mater., 2002, 14, 1221–1224 CrossRef CAS.
- Z. P. Zhang, H. D. Yu, X. Q. Shao and M. Y. Han, Chem.–Eur. J., 2005, 11, 3149–3154 CrossRef CAS.
-
(a) Z. Q. Li, Y. Ding, Y. J. Xiong, Q. Yang and Y. Xie, Chem.–Eur. J., 2004, 10, 5823–5828 CrossRef CAS;
(b) X. F. Wu, H. Bai, C. Li, G. W. Lu and G. Q. Shi, Chem. Commun., 2006, 1655–1657 RSC.
-
(a) Q. Tang, W. J. Zhou, J. M. Shen, W. Zhang, L. F. Kong and Y. T. Qian, Chem. Commun., 2004, 712–713 RSC;
(b) Y. P. Fang, Q. Pang, X. G. Wen, B. N. Wang and S. H. Yang, Small, 2006, 2, 612–615 CrossRef CAS.
- F. Li, Y. Ding, P. X. Gao, X. Q. Xin and Z. L. Wang, Angew. Chem., Int. Ed., 2004, 43, 5238–5242 CrossRef CAS.
-
(a) O. Y. Kurtova, V. I. Kravtsov and E. G. Tsventarnyi, Russ. J. Electrochem., 2004, 40, 893–897 CrossRef CAS;
(b) G. A. Carlson, J. P. McReynolds and F. H. Verhoek, J. Am. Chem. Soc., 1945, 67, 1334–1339 CrossRef CAS;
(c) C. J. Nyman, E. W. Murbach and G. B. Millard, J. Am. Chem. Soc., 1955, 77, 4194–4197 CrossRef CAS.
-
(a) C. Y. Moon, G. M. Dalpian, Y. Zhang, S. H. Wei, X. Y. Huang and J. Li, Chem. Mater., 2006, 18, 2805–2809 CrossRef CAS;
(b) X. Y. Huang, H. R. Heulings, V. Le and J. Li, Chem. Mater., 2001, 13, 3754–3759 CrossRef CAS;
(c) W. T. Yao, S. H. Yu, J. Jiang and L. Zhang, Chem.–Eur. J., 2006, 12, 2066–2672 CrossRef CAS;
(d) X. J. Chen, H. F. Xu, N. S. Xu, F. H. Zhao, W. J. Lin, G. Lin, Y. L. Fu, Z. L. Huang, H. Z. Wang and M. M. Wu, Inorg. Chem., 2003, 42, 3100–3106 CrossRef CAS;
(e) X. Y. Huang and J. Li, J. Am. Chem. Soc., 2007, 129, 3157–3162 CrossRef CAS.
-
(a) J. Tang and A. P. Alivisatos, Nano Lett., 2006, 6, 2701–2706 CrossRef CAS;
(b) J. Q. Hu, Y. Jiang, X. M. Meng, C. S. Lee and S. T. Lee, Small, 2005, 1, 429–438 CrossRef CAS.
- A. B. Djurišić, W. C. H. Choy, V. A. L. Roy, Y. H. Leung, C. Y. Kwong, K. W. Cheah, R. T. K. Gundu, W. K. Chan, H. F. Lui and C. Suryu, Adv. Funct. Mater., 2004, 14, 856–864 CrossRef CAS.
- B. Guo, Z. R. Qiu and K. S. Wong, Appl. Phys. Lett., 2003, 82, 2290–2292 CrossRef CAS.
|
This journal is © The Royal Society of Chemistry 2010 |
Click here to see how this site uses Cookies. View our privacy policy here.