DOI:
10.1039/B815058C
(Paper)
Green Chem., 2009,
11, 127-131
Nanoparticle-supported and magnetically recoverable nickel catalyst: a robust and economic hydrogenation and transfer hydrogenation protocol
Received 29th August 2008, Accepted 21st October 2008
First published on 18th November 2008
Introduction
The metal-catalyzed hydrogenation of an alkyne and the transfer hydrogenation of ketones have received much interest in the past because of the immense number of opportunities that exist to prepare high-value products.1 These reactions are featured in numerous multistep organic syntheses, which are generally catalyzed by precious metal catalysts.2–5 However, the efficient separation and subsequent recycling of homogeneous transition metal catalysts remain scientific challenges of economical and ecological relevance. The practical use of the ever increasing number of tailor-made transition metal catalytic species is indeed connected with the problem of separation and reuse of the rather costly catalyst systems.6 Several strategies for advanced catalyst recycling have been explored, including supported catalysts.7–9 Unfortunately, in this research area, a single solution to the separation problem does not exist, and problems such as solubility of different components, catalyst instability, and metal leaching during the recycling procedure strongly limit the utility of some of these concepts.Recently, functionalized magnetic nanoparticles have emerged as viable alternatives to conventional materials, as a robust, readily available, high-surface-area heterogeneous catalyst support.10 They offer an added advantage of being magnetically separable, thereby eliminating the requirement of catalyst filtration after completion of the reaction. Also, there is an urgent need to develop less expensive and easily available, non-precious metal catalysts for the hydrogenation of alkynes.11 Engaged in the development of greener and sustainable pathways for organic transformations12 and nanomaterials,13 herein, we report a simple and efficient synthesis of a nano-ferrite-supported, magnetically recyclable, and inexpensive Ni catalyst and its application in hydrogenation and transfer hydrogenation reactions. At the outset of this study, no example of a nanoparticle-supported Ni catalyst had been reported, despite the potential inherent stability and activity of such a material.
Results and discussion
The first step in the accomplishment of this goal was the synthesis and functionalization of magnetic nanoparticles (Scheme 1). The catalyst was prepared by sonicating nano-ferrites with dopamine in water for 2 h, followed by the addition of Ni chloride at a basic pH. Material with Ni nanoparticles on the amine-functionalized nano-ferrites was obtained in excellent yield.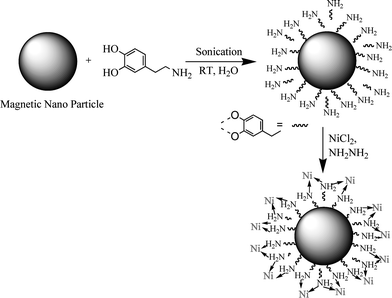 |
| Scheme 1 Synthesis of functionalized nano-ferrite with Ni-coating. | |
Catalyst characterization by X-ray diffraction (XRD) (Fig. 1) and transmission electron microscopy (TEM) (Fig. 2) confirm the anchoring of Ni nanoparticles on amine-functionalized ferrite surfaces. The XRD pattern confirms the formation of single-phase Fe3O4 nanoparticles. The crystallite size, calculated from the Scherrer formula, was found to be 9.21 nm. XRD peaks at 2θ = 15.1 and 43.2 indicate the formation of an amine–nickel complex. TEM micrographs show the particles to be highly dispersed with spherical morphology and a size range of 10–13 nm, which is comparable with the crystallite size calculated from the X-ray spectrum. The weight percentage of Ni was found to be 8.3% by inductively coupled plasma-atomic emission spectroscopy (ICP-AES) analysis.
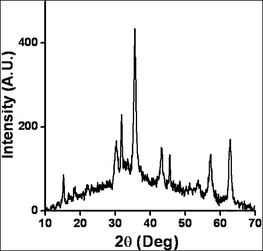 |
| Fig. 1 XRD of functionalized nano-ferrite with Ni-coating. | |
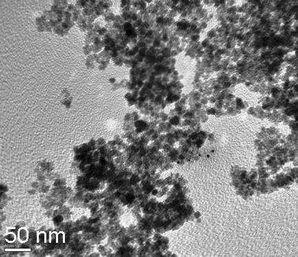 |
| Fig. 2 TEM of functionalized nano-ferrite with Ni-coating. | |
This Ni-coated nanomaterial was then explored as a heterogeneous catalyst for hydrogenation reactions of alkynes (Scheme 2).
Initially, experiments were performed to optimize reaction conditions for the hydrogenation of phenylacetylene as a substrate. Interestingly, we observed two products, i.e. alkene and alkane, depending on the solvent used and reaction time (Table 1). In methanol, hydrogenation of phenylacetylene yielded ethylbenzene as the major product; however, in dichloromethane, styrene was the major product.
Subsequently, this catalyst was explored for the hydrogenation of a variety of alkynes in methanol (Table 2) and dichloromethane (Table 3). Each of the reactions described proceeded smoothly at room temperature to give the desired products. Alkynes were hydrogenated in methanol to yield alkanes, with greater than or equal to 90% of product yield (Table 2, entries 1 through 8). However, heterocyclic alkyne (Table 2, entry 9) yielded a negligible amount of product and nitro groups were not hydrogenated (NR) under these conditions (Table 2, entries 10 and 11). Alkynes can also be hydrogenated in dichloromethane selectively to alkenes in good yield (Table 3, entries 1 through 8). The selectivity of the catalyst (based on reaction solvent) can be very useful in total synthesis of drug molecules, wherein it is possible to hydrogenate an alkyne to an alkene or alkane by simply changing the solvent.
Entry | Substrate | Product | Yield (%) |
---|
Reactions were carried out with 1 mmol of alkyne, 50 mg of nano-ferrite–Ni, and 2 mL of methanol at room temperature, in an autoclave at 100 psi hydrogen pressure for 24 h. |
---|
1 |  |  | 97 |
2 | 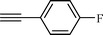 |  | 92 |
3 | 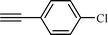 |  | 91 |
4 | 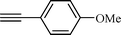 | 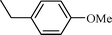 | 90 |
5 |  |  | 90 |
6 |  |  | 90 |
7 | CH3(CH2)7CCH | CH3(CH2)7CH2CH3 | 98 |
8 | CH3(CH2)9CCH | CH3(CH2)9CH2CH3 | 96 |
9 |  |  | 10 |
10 |  |  | NR |
11 |  |  | NR |
Entry | Substrate | Product | Yield (%) |
---|
Reactions were carried out with 1 mmol of alkyne, 50 mg of nano-ferrite–Ni, and 2 mL of dichloromethane at room temperature, in an autoclave at 100 psi hydrogen pressure for 48 h. |
---|
1 |  |  | 80 |
2 | 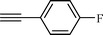 |  | 82 |
3 | 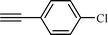 |  | 80 |
4 | 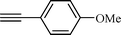 | 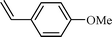 | 76 |
5 |  |  | 72 |
6 |  |  | 76 |
7 | CH3(CH2)7CCH | CH3(CH2)7CH CH2 | 78 |
8 | CH3(CH2)9CCH | CH3(CH2)9CH CH2 | 78 |
9 |  |  | NR |
10 |  |  | NR |
11 |  |  | NR |
The reduction of carbonyl compounds to the corresponding alcohols is a synthetically important transformation and catalytic transfer hydrogenation is one of the best possible methods. In general, a precious metal such as Pd or Au is used for this protocol.14 We decided to explore the inexpensive nano-ferrite–Ni catalyst for transfer hydrogenation of a variety of ketones (Scheme 3) under microwave (MW) irradiation conditions (Table 4).
Entry | Substrate | Product | Yield (%) |
---|
Reactions were carried out with 1 mmol of ketone, 50 mg of nano-ferrite–Ni, and 2 mL of isopropanol at 100 °C, under MW-irradiations for 45 min. |
---|
1 |  |  | 98 |
2 | 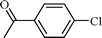 | 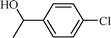 | 98 |
3 | 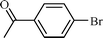 |  | 95 |
4 |  | 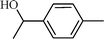 | 98 |
5 |  |  | 80 |
6 |  |  | 80 |
7 |  |  | 5 |
8 | 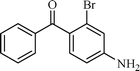 | 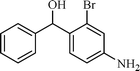 | 5 |
The scope of the catalyst was established for a wide range of ketones and in all cases the reaction was completed within 30–45 min with an excellent yield. Interestingly, in bromo-substituted ketones, debromination of the alcohol was observed (Table 4, entries 3, 4), while for nitro-substituted ketones (Table 4, entries 5, 6), reduction of nitro to amine predominates over hydrogenation of the carbonyl group. These are highly valuable chemoselective transformations that can be useful in multistep organic synthesis. However, our attempt for the transfer hydrogenation of amino-substituted ketones (Table 4, entries 7, 8) produced desired alcohols in low yield, which is due to the cyclization of amino-ketones to yield heterocyclic by-products.
For practical applications of heterogeneous systems, the lifetime of the catalyst and its level of reusability are very important factors. To clarify this issue, we established a set of experiments using the recycled catalyst for the hydrogenation reaction of phenylacetylene (Fig. 3). The reactions were carried out under similar conditions in methanol. After the completion of the first reaction to afford the corresponding ethylbenzene in 97% yield, the catalyst was recovered magnetically, washed with methanol and finally dried at 60 °C for 30 min. A new reaction was then performed with fresh solvent and reactants under the same conditions. To our satisfaction, nano-ferrite-supported Ni catalyst could be used at least five times without any change in activity.
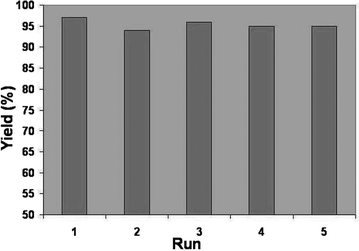 |
| Fig. 3 Recyclability and reusability of nano-ferrite–Ni catalyst. | |
Metal leaching was studied by ICP-AES analysis of the catalyst before and after the reaction. The Ni concentration was found to be 8.3% before the reaction and 8.21% after the reaction, which confirmed negligible Ni leaching. Also, no Ni-metal was detected in the final hydrogenated product. In fact, to date there is no 100% leach-proof metal catalyst; hence, the most important criterion in choosing the catalyst is metal recovery. It would be more preferable to use a more accessible, lower cost Ni-catalyst, provided that the process works at high turn over numbers and turn over frequencies and that the catalyst leaves no remnants of metal in the end product, since metal contamination is highly regulated by the pharmaceutical industry. All the above conditions are well satisfied by our recyclable nano-ferrite-supported Ni catalyst.
Conclusions
In summary, we have developed a convenient synthesis of a nano-ferrite-supported Ni catalyst which was readily prepared from inexpensive starting materials in water. Nano-ferrites were then functionalized and coated with inexpensive Ni-metal which then catalyzed the hydrogenation of alkynes and transfer hydrogenation of ketones with high yields. Also, being magnetically separable eliminated the requirement of catalyst filtration after completion of the reaction, which is an additional eco-friendly attribute of this synthetic protocol.Experimental
The phase of the as-synthesized nanoparticles was determined by XRD in an MMS X-ray diffractometer with a Cu Kα source in the 2θ range 10 to 70. The data were collected with a step of 0.5 deg min−1. TEM micrographs were recorded on a JEOL JSM-1200 II microscope at an operating voltage of 120 kV. The particles were dispersed in ethanol by ultrasonication, loaded on a carbon-coated copper grid, and then allowed to dry at room temperature before recording the micrographs. Elemental analyses of the catalyst before as well as after the reactions were performed on a Perkin Elmer Optima 3300 DV ICP-AES. Five mg of each sample was dissolved in 2.5 mL of concentrated aqua regia and the volume was adjusted to 50 mL in a volumetric flask. This solution was then used for the elemental analysis. Gas chromatography–mass spectrometry (GC–MS) spectra were collected on a HP 6890 series GC system coupled with a 5973 Mass Selective Detector.Synthesis of magnetic nano-ferrites
FeSO4·7H2O (13.9 g) and Fe2(SO4)3 (20 g) were dissolved in 500 mL of water in a 1000 mL beaker. Ammonium hydroxide (25%) was added slowly to adjust the pH of the solution to 10. The reaction mixture was then continually stirred for 1 h at 60 °C. The precipitated nanoparticles were separated magnetically, washed with water until the pH reached 7, and then dried under a vacuum at 60 °C for 2 h. This magnetic nano-ferrite (Fe3O4) was then used for further chemical modification.Surface modification of nano-ferrites
Nano-Fe3O4 (2 g) was dispersed in 25 mL of water by sonication for 30 min. Dopamine hydrochloride (2 g) dissolved in 5 mL of water was added to this solution and again sonicated for 2 h. The amine-functionalized nanomaterial was then precipitated using acetone, isolated by centrifugation, and dried under vacuum at 60 °C for 2 h.Synthesis of nano-ferrite–Ni catalyst
Amine-functionalized nano-Fe3O4 (1 g) was dispersed in water and nickel chloride solution in water was added to the mixture to get 10 wt% of Ni. Hydrazine monohydrate solution in water was added drop-wise to bring the pH of this mixture to 9, followed by the addition of 0.1 g of NaBH4. The reaction mixture was then stirred for 24 h at room temperature. The product was allowed to settle, washed several times with water and acetone, and dried under vacuum at 60 °C for 2 h. The weight percentage of Ni in the catalyst was found to be 8.3% by ICP-AES analysis.To a solution of alkynes (1 mmol) in 2 mL methanol–dichloromethane, 50 mg of nano-ferrite–Ni catalyst was added. The reaction vessel was purged three times with hydrogen and charged to 100 psi, and then closed off to the source of hydrogen. The reaction was stirred at room temperature and, after completion of the reaction, the product was isolated by removing the catalyst magnetically from the reaction mixture. All the products are known in the literature and were identified by the 1H NMR of representative compounds and by comparing the GC–MS spectra of the products with a standard Wiley mass spectral library.In a typical reaction, 1 mmol of the ketone was taken in 2 mL of isopropyl alcohol in a 10 mL glass tube, to which 50 g of catalyst and 0.1 mmol of potassium hydroxide were added. The reaction mixture was then subjected to MW irradiation in a CEM Discover microwave system at 100 °C for 30–45 min. After completion of the reaction, the product was isolated by removing the catalyst magnetically from the reaction mixture. All products are known in the literature and were identified by comparing the GC–MS spectra of the products with a standard Wiley mass spectral library.
Acknowledgements
V. P. and B. B. were supported by the Postgraduate Research Program at the National Risk Management Research Laboratory administered by the Oak Ridge Institute for Science and Education through an interagency agreement between the U.S. Department of Energy and the U.S. Environmental Protection Agency.References
-
(a) D. Teschner, E. Vass, M. Hävecker, S. Zafeiratos, P. Schnörch, H. Sauer, A. Knop-Gericke, R. Schlögl, M. Chamam, A. Wootsch, A. S. Canning, J. J. Gamman, S. D. Jackson, J. McGregor and L. F. Gladden, J. Catal., 2006, 242, 26 CrossRef CAS;
(b) G. W. Kabalka and R. S. Varma, Comprehensive Organic Synthesis, ed. B. M. Trost and I. Fleming, Pergamon Press, Oxford, 1991, vol. 8, p. 363 Search PubMed;
(c) T. Ikariya and A. J. Blacker, Acc. Chem. Res., 2007, 40, 1300 CrossRef.
- A. Dedieu, S. Humbel, C. Elsevier and C. Grauffel, Theor. Chem. Acc., 2004, 112, 305 CAS.
- A. M. Kluwer, T. S. Koblenz, T. Jonischkeit, K. Woelk and C. J. Elsevier, J. Am. Chem. Soc., 2005, 127, 15470 CrossRef CAS.
- M. W. van Laren, M. A. Duin, C. Klerk, M. Naglia, D. Rogolino, P. Pelagatti, A. Bacchi, C. Pelizzi and C. J. Elsevier, Organometallics, 2002, 21, 1546 CrossRef CAS.
- J. López-Serrano, S. B. Duckett, S. Aiken, K. Q. A. Leñero, E. Drent, J. P. Dunne, D. Konya and A. C. Whitwood, J. Am. Chem. Soc., 2007, 129, 6513 CrossRef CAS.
- B. Chen, U. Dingerdissen, J. G. E. Krauter, H. G. J. Lansink Rotgerink, K. Möbus, D. J. Ostgard, P. Panster, T. H. Riermeier, S. Seebald, T. Tacke and H. Trauthwein, Appl. Catal., A, 2005, 280, 17 CrossRef CAS.
- S. D. Jackson and A. Monaghan, Catal. Today, 2007, 128, 47 CrossRef CAS.
- A. Papp, Á. Molnár and Á. Mastalir, Appl. Catal., A, 2005, 289, 256 CrossRef CAS.
- N. Marín-Astorga, G. Pecchi, T. J. Pinnavaia, G. Alvez-Manoli and P. Reyes, J. Mol. Catal. A: Chem., 2006, 247, 145 CrossRef CAS.
-
(a) A. Hu, G. T. Yee and W. Lin, J. Am. Chem. Soc., 2005, 127, 12486 CrossRef CAS;
(b) R. Abu-Reziq, H. Alper, D. Wang and M. L. Post, J. Am. Chem. Soc., 2006, 128, 5279 CrossRef;
(c) C. O. Dalaigh, S. A. Corr, Y. Gunko and S. J. Connon, Angew. Chem., Int. Ed., 2007, 46, 4329 CrossRef CAS;
(d) T. Hara, T. Kaneta, K. Mori, T. Mitsudome, T. Mizugaki, K. Ebitanic and K. Kaneda, Green Chem., 2007, 9, 1246 RSC;
(e) A. H. Latham and M. E. Williams, Acc. Chem. Res., 2008, 41, 411 CrossRef CAS.
- F. Studt, F. Abild-Pedersen, T. Bligaard, R. Z. Sørensen, C. H. Christensen and J. K. Nørskov, Science, 2008, 320, 1320 CrossRef CAS.
-
(a) V. Polshettiwar and R. S. Varma, Chem. Soc. Rev., 2008, 37, 1546 RSC;
(b) V. Polshettiwar and R. S. Varma, Acc. Chem. Res., 2008, 41, 629 CrossRef CAS;
(c) V. Polshettiwar and R. S. Varma, Curr. Opin. Drug Discovery Dev., 2007, 10, 723 CAS;
(d) V. Polshettiwar and R. S. Varma, J. Org. Chem., 2008, 73, 7417 CrossRef CAS;
(e) V. Polshettiwar and R. S. Varma, J. Org. Chem., 2007, 72, 7420 CrossRef CAS.
-
(a) V. Polshettiwar, M. N. Nadagouda and R. S. Varma, Chem. Commun., 2008 10.1039/b814715a;
(b) M. N. Nadagouda and R. S. Varma, Cryst. Growth Des., 2008, 8, 291 CrossRef CAS;
(c) M. N. Nadagouda and R. S. Varma, Cryst. Growth Des., 2007, 7, 686;
(d) M. N. Nadagouda and R. S. Varma, Cryst. Growth Des., 2007, 7, 2582 CrossRef CAS;
(e) H. Choi, Y. J. Kim, R. S. Varma and D. D. Dionysiou, Chem. Mater., 2006, 18, 5377 CrossRef CAS;
(f) V. Polshettiwar and R. S. Varma, Org. Biomol. Chem., 2008 10.1039/b817669h;
(g) B. Baruwati, M. N. Nadagouda and R. S. Varma, J. Phys. Chem. C, 2008 DOI:10.1021/jp807245g.
- F.-Z. Su, L. He, J. Ni, Y. Cao, H.-Y. He and K.-N. Fan, Chem. Commun., 2008, 3531 RSC.
|
This journal is © The Royal Society of Chemistry 2009 |
Click here to see how this site uses Cookies. View our privacy policy here.