Hierarchical macro/mesoporous TiO2/SiO2 and TiO2/ZrO2 nanocomposites for environmental photocatalysis
Received
25th February 2009
, Accepted 22nd April 2009
First published on 5th May 2009
Abstract
Photocatalytic purification methods for polluted air and wastewater show great promise for environmental remediation, allowing the “green” mineralization of organic pollutants under ambient conditions. The creation of macro/mesopores in semiconductor photocatalysts has been found to improve the overall photocatalytic efficiency, but porous systems are generally unstable against thermal sintering, which is indispensable for removing organic templates and enhancing structural crystallization. In this study, we employed nanosized ZrO2 and SiO2 as structural modifiers to improve the structural stability in a macro/mesoporous TiO2 photocatalyst. This was accomplished by soft-chemical synthesis in the presence of surfactants, followed by calcination at high temperatures. The resulting porous TiO2-based nanocomposites not only feature enhanced textural properties and improved thermal stability, but also show an improvement in photocatalytic activity over pure TiO2. The introduction of a secondary phase imparts the additional functions of improved surface acidity and extra binding sites onto the porous structures. The favorable textural properties, along with the improved surface functions contribute to the high photocatalytic activity of catalysts calcined at high temperatures.
Broader context
Semiconductor-mediated photocatalysis for the purification of polluted air and wastewater is becoming one of the most promising environmental remediation technologies. For the last 30 years intensive studies have focused on the light-harvesting semiconductor TiO2, but the low quantum efficiency of the TiO2 photocatalyst has limited its practical application. As the quantum yield of a photocatalyst strongly depends on crystal size and surface morphology, in addition to absorption and diffusion of the target molecules, there is a great deal of interest in the rational design of photocatalysts with a porous nanostructure to improve photocatalytic activity. This paper reports the use of structural stabilizers (SiO2 and ZrO2) to modify a hierarchically macro/mesoporous TiO2 material to improve the thermal stability and surface properties of the porous structure. The obtained catalysts exhibit high photocatalytic activity for the mineralization of organic pollutants in the gas phase.
|
1. Introduction
The development of porous architectures containing multiscale porosity has gained great attention because such structures could permit the improved mass-transfer of molecules in solid networks.1,2 The optimization of diffusion, coupled with high surface area and unique surface functionalities, makes multimodal porous materials of interest for applications in adsorption, separation, and catalysis.3,4 For photochemical applications, a porous semiconductor network should in principle facilitate the access of reactant molecules to active surface sites and also improve the distribution of photon energy over porous frameworks.5,6 Consequently, the mass transfer and light utilization efficiency of heterogeneous systems can be enhanced, and such porous systems are highly desirable for photocatalytic applications.
Methods for the fabrication of multimodal porous materials typically involve the combination of organic templating synthesis with micromoulding technologies using emulsion droplets,7 latex/silica spheres,8,9 or bacterial threads.10,11 This has produced porous structures with pore size in the order of two/three length scales. Recently, a strategy based on self-assembly of a single surfactant under hydrothermal conditions has been developed for synthesizing macro/mesoporous metal oxides including Al2O3, ZrO2, and TiO2.12,13 Among those materials, TiO2 is an intensively-studied light-harvesting material for artificial photosynthesis due to its physicochemical properties and economic advantages, which allow its use in solar energy conversion and environmental remediation.5,14–16 Fabrication of TiO2 structures of nanoscopic dimensions has had a positive effect on photocatalysis/photoelectrochemistry, which has motivated enormous interest in the design of porous TiO2nanostructures.17 Recently, we introduced macro/mesoporous TiO2 as a heterogeneous photocatalyst for the environmental purification of volatile organic pollutants in air. We found that the hierarchical structure was unstable upon sintering above 500 °C, which is indispensable for removing the surfactant and enhancing the crystallization of the TiO2 network, but this led to a loss in photocatalytic activity due to the collapse of porous structure at high temperatures.18 This intrinsic limitation of TiO2 structures against sintering has also been reported by Yu and co-workers.19 In their case, sintering at >500 °C destroyed the porous framework in association with anatase-to-rutile phase transformation, and also led to a loss in photoactivity.19 Therefore, the creative design of TiO2 hierarchical structures with high thermal stability is necessary to improve the photocatalytic functions, also a critical requirement for material applications in heterogeneous catalysis where the input of thermal energy is required.
To improve the stability of macro/mesoporous TiO2, we made a modification to a hierarchical porous TiO2 architecture using the structural stabilizers (ZrO2 or SiO2). The use of structural stabilizers to promote the anti-sintering properties of materials has been broadly employed for the production of porous catalysts with sufficient thermo–mechanical strength for high-temperature applications.7,20 The introduction of a secondary phase also imparts additional functionality, of improved surface chemistry particularly surface acidity, to the hierarchically porous composites.20,21 The acidity comes from strong surface hydroxyl groups which capture light-induced holes, thereafter initiating the generation of strong active species (e.g. ·OH) capable of oxidizing adsorbed organic substrates.22 These favorable textural properties in combination with improved surface functions are expected to yield a high reaction rate on macro/mesoporous composites for environmental purification of organic pollutants.
Ethylene was chosen as a probe for the photocatalytic reaction due to its relatively high reactivity and its close structural relationship to some toxic volatile organic compounds (e.g.trichloroethylene). The degradation of ethylene is also useful in industry for suppressing the ageing and ripening of fruits and flowers.
2. Experimental
2.1 Materials
All chemicals were used as received without further treatment. Titanium isopropoxide (Ti(OPri)4 or TTIP, 99%), zirconium propoxide [70% (w/w) in n-propyl alcohol], and tetraethyl orthosilicate [Si(OC2H5)4, TEOS, 99%] were purchased from Aldrich. Non-ionic poly(alkylene oxide)-based surfactant (decaoxyethylene cetyl ether, C16(EO)10, Brij56) was purchased from Acros. All solvents used were of analytical grade and purchased from Aldrich. Ultra-pure water was used in all experiments.
2.2 Synthesis of samples
TiO2/SiO2 and TiO2/ZrO2 were synthesized by hydrolysis of mixed metal alkoxide precursors in the presence of surfactant, followed by calcination at high temperature to remove surfactant and to promote crystallization. The metal alkoxide precursors were mixed to a composition of 15 wt% SiO2 or ZrO2 in TiO2. This composition was used because a previous study had found that it was the optimum mixture ratio for TiO2/ZrO2 and TiO2/SiO2 in photocatalysis applications.20 In a typical synthesis, TTIP (4.8 mL) was mixed with a calculated amount of zirconium propoxide or TEOS. The mixture was then sonicated in an ultrasonic cleaning bath for 10 min, and added dropwise to a 30 mL aqueous solution containing C16(EO)10 (10 wt%) under very gentle stirring at ambient conditions. After slowly stirring for 20 min, the mixture was transferred to a Teflon-lined autoclave to age at 80 °C for 24 h. The product was filtered and dried overnight at 55 °C in a vacuum oven. The resulting white monolithic pellets were calcined in static air at 350, 500, 650, 800 °C for 4 h at a heating rate of 1 °C min−1 to remove surfactant and solidify the porous frameworks. Batches of TiO2, TiO2/ZrO2 and TiO2/SiO2 samples are denoted as Tx, TZx and TSx respectively, where x stands for calcination temperature.
2.3 Characterization
X-ray diffraction measurements were performed on a Bruker D8 Advance X-ray diffractometer with Cu Kα1 irradiation (λ = 1.5406 Å). Scanning electron microscopy (SEM) was taken on a LEO 1450VP scanning microscope to investigate the morphology and surface roughness of the samples. Transmission electron microscopy (TEM) and high-resolution transmission electron microscopy (HR-TEM) were recorded on a Tecnai20 FEG microscope. The sample was suspended in methanol solution, followed by sonication for 10 min in an ultrasonic bath. Carbon-coated copper grids were used as the sample holders. Nitrogen sorption experiments were carried out at 77 K using Micromeritics ASAP 2010 equipment. All the samples were degassed at 180 °C and 10−6 torr for 24 h prior to measurement. A Varian Cary 500 Scan UV-visible system equipped with a Labsphere diffuse reflectance accessory was used to obtain the reflectance spectra of the catalysts over a range 200–800 nm. Labsphere USRS-99-010 was employed as a reflectance standard. Fourier transformed infrared (FTIR) spectra were recorded using a Nicolet Magna 670 FTIR spectrometer. The samples were mixed with KBr at a concentration of ca. 10%.
2.4 Activity measurements
Photocatalytic reactions were carried out in a fixed bed tubular quartz reactor operated in a single-pass mode. The catalyst (0.25 g) was loaded in the reactor surrounded by four 8W UV-bulbs with a wavelength centered at 254 nm. Ethylene diluted in a water-saturated zero air stream (21% oxygen, H2O <5 ppm, total hydrocarbons <1 ppm) was used to afford a reactant stream. The initial concentrations of ethylene and carbon dioxide in the stream were 640 ppm and 0 ppm, respectively. The reactant mixture flow rate was kept at 15 mL min−1. Analysis of reactor effluent was conducted with an online gas chromatograph (HP6890) equipped with a flame ionization detector (FID), a thermal conductivity detector (TCD), and a Porapak R column.
Fresh catalyst was used for each run, and ethylene was found to be thermally stable in the reactor without illumination, and no degradation was observed when it was illuminated in the absence of catalysts. The catalyst was allowed to come to adsorption equilibrium with the reactant gas before the reactor was illuminated. The expected 2
:
1 ratio of carbon dioxide produced to ethylene destroyed was observed at steady state. Steady state was achieved within ca. 3 h after illumination during which no byproducts were observed. No decrease in activity was noticed during the run, which lasted as long as a full day. Fractional conversions of ethylene at steady state and the CO2 produced were used to measure reactivity.
3. Results and discussion
3.1 Crystal structure and surface area
Fig. 1 shows the XRD patterns of the TZ (Fig. 1a) and TS (Fig. 1b) samples calcined at different temperatures. It can be seen that there is no observable peak corresponding to ZrO2 or SiO2. The absence of ZrO2 or SiO2 peaks in the composites implies that Zr or Si might be distributed homogeneously with Ti in the materials.23,24 All of the TZ and TS samples display dominantly XRD peaks corresponding to the anatase phase even when the samples were sintered at 800 °C, whereas pure TiO2 undergoes a phase transformation from anatase to rutile beginning at 500 °C.18 These results suggested that the addition of ZrO2 and SiO2 is effective in enhancing the thermal stability of titania, which is further confirmed by the results of the band gaps given in Table 1. The introduction of a secondary phase can also inhibit crystal growth in the solids, especially at high sintering temperature. As reported previously, the anatase crystal size of pure TiO2 increased noticeably from 5.7 nm to 28.5 nm as the temperature increased from 350 °C to 650 °C and the rutile crystal size also increased dramatically when the sample was heated above 650 °C.18 Such a remarkable change did not occur for the Si- or Zr- modified TiO2 systems. As can be seen in Table 1, the crystal size of anatase was well maintained in both Si- and Zr-modified TiO2 systems until the samples were sintered at 800 °C, and even at such a high temperature the anatase size in the TS and TZ hybrid catalysts was still much smaller than that of pure TiO2. This is a remarkable observation because nanocrystalline anatase has long been considered as the most photoactive form of titania photocatalysts.25
Table 1 Physicochemical properties of TZ and TS catalysts as a function of sintering temperature
Sample |
Phase
|
S
BET
a/m2 g−1 |
V
b/cm3 g−1 |
D
BJH
c/nm |
Crystal sized/nm |
E
g
e/eV |
BET surface area calculated from the linear part of the BET plot (P/P0 = 0.1–0.2).
Total pore volume, taken from the volume of N2 adsorbed at P/P0 = 0.991.
Average pore diameter, estimated using the desorption branch of the isotherm and the Barrett–Joyner–Halenda (BJH) formula.
Calculated by applying the Scherrer formula on the anatase (101) or rutile (110) diffraction peak.
Band gap energy estimated from UV-vis spectra.
|
TZ350 |
anatase
|
204 |
0.56 |
8.3 |
9.0 |
3.30 |
TZ500 |
anatase |
173 |
0.63 |
11 |
9.2 |
3.33 |
TZ650 |
anatase
|
105 |
0.52 |
15 |
9.6 |
3.26 |
TZ800 |
anatase |
45 |
0.36 |
28 |
17.1 |
3.28 |
TS350 |
anatase |
298 |
0.46 |
4.9 |
5.4 |
3.10 |
TS500 |
anatase
|
283 |
0.47 |
5.2 |
5.3 |
3.16 |
TS650 |
anatase |
193 |
0.38 |
6.3 |
6.6 |
3.11 |
TS800 |
anatase |
92 |
0.28 |
8.1 |
13.7 |
3.14 |
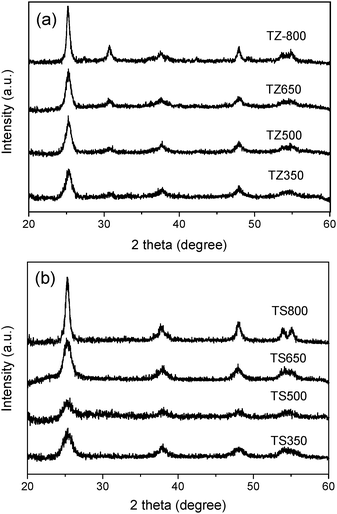 |
| Fig. 1
XRD patterns of (a) TZ and (b) TS calcined at 350 °C, 500 °C, 650 °C and 800 °C. | |
The textural properties of the TZ or TS samples were characterized by N2-sorption measurement. Fig. 2 shows the pore size distributions and N2-sorption isotherms for TZ (Fig. 2a) and TS (Fig. 2b) samples calcined at different temperatures. All the isotherms exhibit stepwise adsorption and desorption, indicative of three-dimensional intersection of a solid porous structure.26 Except for the 800 °C calcined samples, all the samples show a unimodal distribution of pores with a distribution of pores in the mesoscopic range. The mesopore sizes are enlarged with the increase of calcination temperature in the silica and zirconia modified titania systems. The surface area and pore volume of T350 was found to be 201 m2 g−1 and 0.40 cm3 g−1, but they decreased to 85 m2 g−1 and 0.26 cm3 g−1 after calcination at 500 °C. This was due to a partial collapse of the porous framework. A steady decrease from 85 m2 g−1 and 0.26 cm3 g−1 to 2 m2 g−1 and 0.01 cm3 g−1 has also been observed with increasing calcination temperature from 500 to 800 °C, indicating that the porous structure had almost completely collapsed at the high temperature of 800 °C.18 It should be noted that after modification with silica and zirconia, titania porous structures possess significantly higher surface areas and larger pore volumes than pure titania. In particular, TS exhibited a high surface area of 298 m2 g−1 at 350 °C and retained its surface area better than the others at high temperatures (see Table1). It remained as large as 92 m2 g−1 even after calcination at 800 °C for 4 h. The TZ system falls in between the pure TiO2 and TS catalysts in terms of surface area and stability. These results provide evidence that silica and zirconia are effective surface area stabilizers. The excessive crystallite growth is believed to be the main reason accounting for the destruction of the mesopore structures in the surfactant-templated metal oxide gels upon thermal treatment.27 Thus, the presence of a metal oxide as a secondary phase could inhibit crystallization and consequent crystal growth, contributing to the high surface area of the mixed oxides subjected to thermal treatment at high temperatures.
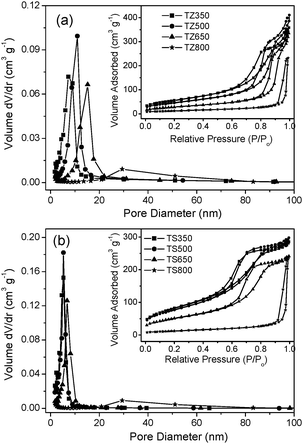 |
| Fig. 2
N2 sorption isotherms (inset) and corresponding BJH pore-size distribution curve of (a) TZ and (b) TS calcined at 350 °C, 500 °C, 650 °C and 800 °C. | |
3.2 Surface morphology
The macroporous structure of the TZ and TS samples was examined using SEM. Fig. 3 shows the SEM images of TZ500 and TS500. The TZ500 exhibited a macroscopic network structure with relatively homogeneous pore size, with diameters of 2–4 µm and wall thicknesses of 1–4 µm. Moreover, the macroporous channels are usually of one-dimensional orientation, parallel to each other and orthogonal to one side of the monolithic particles. These well-oriented macrochannels extend through the whole particle, which can be clearly seen from Fig. 3c. This result is consistent with those reported in the literature.17,24,28 Closer inspection of Fig. 3a also revealed that the walls of the macroporous structure in TZ500 were composed of closely packed nanoparticles, indicating that mesoporosity is probably due to both intraparticle porosity and interparticle porosity. The TS500 sample also preserved a macroscopic network structure with a relatively regular array of macropores, as shown in the SEM image in Fig. 3d–f. The sizes of the macropores are similar to those of the TZ sample. It has been reported that although the macroporous structure of pure T500 is mostly preserved,18 the tube size decreases from 2–4 µm to 1–2 µm when the calcined temperature is increased from 350 to 500 °C, which is mainly due to shrinkage and solidification of the macroporous framework during the high temperature treatment. Note that the hierarchically macro/mesostructured network with open and accessible pores was well preserved after the TZ and TS samples were calcined at 500 °C, indicating a high thermal stability, in good agreement with XRD and N2-sorption results.
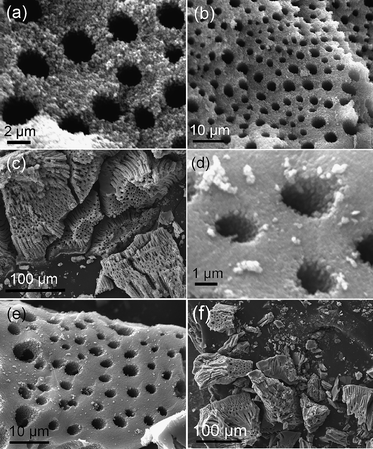 |
| Fig. 3
SEM images of TZ500 (a, b, c) and TS500 (d, e, f). | |
Fig. 4 shows the TEM images of TZ500 and TS500 samples. The TZ500 and TS500 samples have a honeycomb porous structure with fine particular morphology, confirming that mesoporosity is partly originated from interparticle porosity. Well-crystallized grains of TiO2nanoparticles can be clearly seen for the TZ500 and TS500 samples in Fig. 4a and 4c. The grain size was confirmed to be about 10 nm for TZ500 and 6 nm for TS500, which is in accord with XRD results. The HRTEM images of TZ500 and TS500 samples are depicted in Fig. 4b and 4d. In these images, the lattice fringes of d = 0.35 nm matching the (101) crystallographic planes of anatase–TiO2can be clearly observed, which is consistent with the XRD patterns. These results provide direct evidence that the addition of ZrO2 and SiO2 can effectively stabilize the porous structure at high temperature.
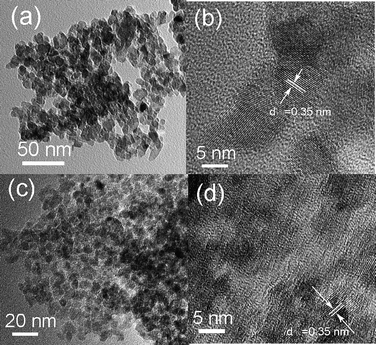 |
| Fig. 4
TEM and HRTEM images of (a, b) TZ500 and (c, d) TS500. | |
The FT-IR spectra of T500, TZ500 and TS500 are shown in Fig. 5. All of the samples show two bands at 3400 cm−1 and 1630 cm−1, corresponding to the surface hydroxyl groups or adsorbed water strongly bound to the catalyst surface.29 Obviously, the intensity of the bands in both TZ500 and TS500 is much stronger than those of T500, indicating that the introduction of ZrO2 and SiO2 make the sample possess more surface-adsorbed hydroxyl groups or water. It is known that surface hydroxyl groups play an important role in heterogeneous photocatalysis by capturing the photoinduced holes, producing reactive hydroxyl radicals with high oxidation capability.20
3.4 Photocatalytic activity
The photocatalytic activities of the macroporous TZ and TS samples were evaluated by the degradation of ethylene, with pure TiO2 as a comparison. Fig. 6 shows the photocatalytic performance of the catalysts as a function of sintering temperature. It can be seen that the sintering temperature had a great effect on the photocatalytic activity of TiO2. The activity of the TiO2 sample is initially as high as 42% at 350 °C but decays quickly with increasing sintering temperature. The decrease in activity can be partially attributed to the decreased surface area of the materials and the increase in rutile content with enhanced sintering temperature. In addition, the destruction of the macrochannels and the loss of mesoporosity also contributed to the dramatic decrease in the photocatalytic activity, as previously noted.18 For the modified samples, the addition of ZrO2 or SiO2 affects the photocatalytic activity of the catalysts towards oxidizing ethylene. In the case of the zirconia modified system, the activity steadily increased from 38% to 43% with increasing sintering temperature from 350 °C to 650 °C. Further increasing the sintering temperature to 800 °C, the activity remained 32%. For the silica modified system, when the sintering temperature increased to 500 °C, the sample showed the highest activity of 48%. Further increasing the sintering temperature gradually decreased the conversion of ethylene. When the sintering temperature increased to 800 °C ethylene conversion decreased to 17%. These results reveal that the modification of TiO2 with ZrO2 or SiO2 can effectively preserve photocatalytic activity, especially at high temperature.
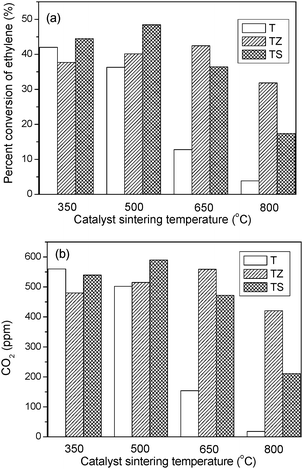 |
| Fig. 6 Photocatalytic performances of TZ, TS and pure TiO2 as a function of sintering temperature. | |
The enhanced photocatalytic performance of macroporous TZ and TS composites can be attributed to several factors. Firstly, it is known that gas–solid heterogeneous photocatalysis is a surface-based process, and thus a large specific surface area can offer more adsorption sites and photocatalytic reaction centers.15 The macroporous and mesoporous structures of composites provided them with higher BET surface area and stronger surface adsorption ability to the reactant molecules. Moreover, the hierarchical macro/mesoporous structures are also beneficial to enhance photoadsorption efficiency and the flow rate of the gas molecules.17,19 Therefore, the preservation of such hierarchical macro/mesoporous structures is very important for photocatalytic applications of the modified samples, especially for samples at high calcination temperatures. Secondly, the addition of ZrO2 or SiO2 into TiO2 suppresses the anatase-to-rutile phase transformation and the crystal growth of the catalyst during calcination. The presence of the anatase phase and the smaller particle size of the composites compared to pure TiO2 can also contribute to the improved activity. Finally, the mixture of ZrO2 or SiO2 into macro/mesoporous TiO2 can drastically inhibit the loss of surface hydroxyl groups during calcination (see IR spectra), thus the hydroxyl groups on the catalyst surface can be preserved.18,30,31 It is known that surface hydroxyl groups can accept holes generated by illumination and form active hydroxyl radicals, which can oxidize adsorbed molecules.32 The surface hydroxyl groups are also known as surface acidic sites. Therefore, the presence of a large number of surface acidic sites after modification is another reason that accounts for the higher activity of the modified structures.
4. Conclusions
Hierarchically macro/mesostructured TiO2/ZrO2 and TiO2/SiO2 mixed oxides have been synthesized by a surfactant-templated method. The modification of TiO2 with ZrO2 and SiO2 has an obvious effect on the hierarchical porous structure and photocatalytic activity. The addition of a secondary phase can effectively stabilize the porous structure during thermal treatment, indicating high thermal stability. The modification also maintains the high surface areas after sintering and inhibits the anatase-to-rutile phase transformation at high temperature. The hierarchically porous composites exhibit higher photocatalytic activity in comparison to pure titania, especially at sintering temperatures above 500 °C. The increase in activity can be explained by favorable textural properties and improved surface functions. These stable meso/macroporous TiO2 hybrid structures show great promise for various applications, after some chemical/physical modifications, especially when post-calcination at high temperatures is required.
Acknowledgements
This work was supported by the National Natural Science Foundation of China (Grant No. 20603007), the National Basic Research Program of China (973 Program, 2007CB613306), the New Century Excellent Talents in University of China (NCET-07-0192), the Program for Changjian Scholars and Innovative Research Team in University (PCSIR0818), and the National Natural Science Foundation of Fujian Province (No. 2006J0160 and 2008H0089).
References
- Z. Y. Yuan and B. L. Su, J. Mater. Chem., 2006, 16, 663 RSC.
- A. Stein, Adv. Mater., 2003, 15, 763 CrossRef CAS.
- M. E. Davis, Nature, 2002, 417, 813 CrossRef CAS.
- G. A. Umeda, W. C. Chueh, L. Noailles, S. M. Haile and B. S. Dunn, Energy Environ. Sci., 2008, 1, 484 RSC.
- J. Yu, J. C. Yu, M. K. P. Leung, W. Ho, B. Cheng, X. Zhao and J. Zhao, J. Catal., 2003, 217, 69 CAS.
- N. Tsubaki, Y. Zhang, S. Sun, H. Mori, Y. Yoneyama, X. Li and K. Fujimoto, Catal. Commun., 2001, 2, 311 CrossRef CAS.
- A. Imhof and D. J. Pine, Nature, 1997, 389, 948 CrossRef CAS.
- H. W. Yan, C. F. Blanford, B. T. Holland, W. H. Smyrl and A. Stein, Chem. Mater., 2000, 12, 1134 CrossRef CAS.
- M. Antonietti, B. Berton, C. Göltner and H. P. Hentze, Adv. Mater., 1998, 10, 154 CrossRef CAS.
- S. A. Davis, S. L. Burkett, N. H. Mendelson and S. Mann, Nature, 1997, 385, 420 CrossRef CAS.
- B. J. Zhang, S. A. Davis, N. H. Mendelson and S. Mann, Chem. Commun., 2000, 9, 781 Search PubMed.
- W. H. Deng, M. W. Toepke and B. H. Shanks, Adv. Funct. Mater., 2003, 13, 61 CrossRef CAS.
- Z. Y. Yuan, T. Z. Ren and B. L. Su, Adv. Mater., 2003, 15, 1462 CrossRef CAS.
- A. Fujishima and K. Honda, Nature, 1972, 238, 37 CAS.
- M. R. Hoffmann, S. T. Martin, W. Y. Choi and D. W. Bahnemann, Chem. Rev., 1995, 95, 69 CrossRef CAS.
- J. Nowotny, Energy Environ. Sci., 2008, 1, 565 RSC.
- M. Gratzel, Nature, 2001, 414, 338 CrossRef CAS.
- X. C. Wang, J. C. Yu, C. Ho, Y. D. Hou and X. Z. Fu, Langmuir, 2005, 21, 2552 CrossRef CAS.
- J. G. Yu, Y. R. Su and B. Cheng, Adv. Funct. Mater., 2007, 17, 1984 CrossRef CAS.
- X. Z. Fu, L. A. Clark, Q. Yang and M. A. Anderson, Environ. Sci. Technol., 1996, 30, 647 CrossRef CAS.
- C. Anderson and A. J. Bard, J. Phys. Chem. B, 1997, 101, 2611 CrossRef CAS.
- K. Kobayakawa, Y. Nakazawa, M. Ikeda, Y. Sato and A. Fujishima, Ber. Bunsen–Ges. Phys. Chem., 1990, 94, 1439.
- C. H. Wang, A. F. Geng, Y. H. Guo, S. J. Jiang, X. S. Qu and L. Li, J. Colloid Interface Sci., 2006, 301, 236 CrossRef CAS.
- Z. Y. Yuan, T. Z. Ren, A. Vantomme and B. L. Su, Chem. Mater., 2004, 16, 5096 CrossRef CAS.
- A. Sclafani and J. M. Herrmann, J. Phys. Chem., 1996, 100, 13655 CrossRef CAS.
- R. C. Nádia and F. V. S. Santana, Catal. Today, 2005, 107–108, 595.
- A. Corma, Chem. Rev., 1997, 97, 2373 CrossRef CAS.
- A. Collins, D. Carriazo, S. A. Davis and S. Mann, Chem. Commun., 2004, 5, 568 Search PubMed.
- K. L. Yeung, S. T. Yau, A. J. Maira, J. M. Coronado, J. Soria and P. L. Yue, J. Catal., 2003, 219, 107 CrossRef CAS.
- X. C. Wang, J. C. Yu, Y. L. Chen, L. Wu and X. Z. Fu, Environ. Sci. Technol., 2006, 40, 2369 CrossRef CAS.
- Y. D. Hou, X. C. Wang, L. Wu, X. F. Chen, Z. X. Ding, X. X. Wang and X. Z. Fu, Chemosphere, 2008, 72, 414 CrossRef CAS.
- C. S. Turchi and D. F. Ollis, J. Catal., 1989, 119, 483 CrossRef CAS.
|
This journal is © The Royal Society of Chemistry 2009 |
Click here to see how this site uses Cookies. View our privacy policy here.