DOI:
10.1039/B821113M
(Minireview)
Energy Environ. Sci., 2009,
2, 491-497
Thermochemical water-splitting cycle using iodine and sulfur
Received
25th November 2008
, Accepted 26th February 2009
First published on
12th March 2009
Abstract
Research and development on the thermochemical water-splitting cycle using iodine and sulfur, a potential large-scale hydrogen production method, is reviewed. Feasibility of the closed-cycle continuous water splitting has been demonstrated by coupling the Bunsen reaction, thermal decomposition of hydrogen iodide and that of sulfuric acid. Studies are in progress to realize efficient hydrogen production. Also, development of chemical reactors made of industrial materials has been carried out, especially those used in the corrosive process environment of sulfuric acid vaporization and decomposition.
Kaoru Onuki | Dr Kaoru Onuki is Group Leader of IS Process Technology Group at Nuclear Science and Engineering Directorate of the Japan Atomic Energy Agency. He received a BS from Tohoku University, MS from the University of Tokyo, both in Applied Chemistry, and a PhD in Chemical Engineering from Yokohama National University. Dr Onuki has been working on hydrogen production research for the last 25 years. |
Shinji Kubo | Mr Shinji Kubo is assistant principal researcher of JAEA. He received a BS and MS in Mechanical Engineering from Utsunomiya University. He was engaged in high density heat transport technology research and received a prize from the Japan Society of Mechanical Engineers in recognition of his work on micro capsule phase change materials. In 1999, Mr Kubo joined the thermochemical cycle development research at JAEA and led the closed-cycle demonstration study. |
Atsuhiko Terada | Mr Atsuhiko Terada received a BS in Physics from Shizuoka University. From 1992 to 2004, Mr Terada worked at Ishikawajima Harima Heavy Industry Co. Ltd. where he was engaged in design and development related to vacuum systems for beam accelerators and, also, in conceptual design of target systems (neutron spallation source, proton beam window, etc.) for a neutron scattering facility which JAEA and KEK constructed in the J-PARC project. His main research interests are in thermal hydraulics analyses and experiments such as flow visualization, he is now engaged in component development research for thermochemical processes as an assistant principal researcher of JAEA. |
Nariaki Sakaba | Dr Nariaki Sakaba is an assistant principal researcher of HTGR Development Promotion Office of Policy Planning and Administration Department in JAEA. He received a BS from Waseda University Tokyo in Applied Chemistry, and PhD from Tohoku University in Quantum Science and Energy Engineering. He is currently working on a high-temperature gas-cooled reactor and hydrogen production system for one of JAEA's heat application systems. |
Ryutaro Hino | Dr Ryutaro Hino is Director of the Research Co-ordination and Promotion Office of the Nuclear Science and Engineering Directorate (NSED) of the Japan Atomic Energy Agency. He arranges and promotes all research carried out in NSED, particularly in nuclear hydrogen production technology with high-temperature gas-cooled reactors. He is a visiting professor of Utsunomiya University. |
Broader context
Thermochemical water-splitting cycles have a history of study of over 40 years since the pioneering work of Funk and Reinstrom. Amid mounting concern about the decreasing availability of fossil fuels caused by the oil crisis, the concept of a hydrogen energy system attracted interest and, in searching for a low-cost and efficient hydrogen production process, a number of studies were carried out from the 1970's until about the mid-1980's on thermochemical cycles considering mainly high temperature gas-cooled reactors that can supply nuclear heat of about 1000 °C as a heat source. The study in this period resulted in the invention of some promising chemical reaction cycles such as the so-called “sulfur family cycles”. Then, since around 2000 there has been growing interest in hydrogen energy mainly due to concerns about global warming, so the study of thermochemical cycles has revived worldwide, the main subject of which has been on R&D of the most promising cycles. The cycle using iodine and sulfur is representative of such a promising cycle and researchers are now working to bring forward technology developments from laboratory-scale to engineering-scale.
|
1. Introduction
The “thermochemical water-splitting cycle” offers a method for transforming heat energy into hydrogen energy, the energy carrier. Although direct thermal decomposition of water requires high temperatures, a few thousand Kelvin, it is possible to decompose water at lower temperatures by combining high temperature endothermic chemical reactions and low temperature exothermic chemical reactions, where the net chemical change resulting from the sequence of chemical reactions is water decomposition. The cycle of chemical reactions produces the free energy of water splitting.
Thermochemical water-splitting cycles were first studied by Funk and Reinstrom,1,2 and an actual example was proposed by De Beni and Marchetti in the early 70's.3 Since then, a number of thermochemical cycles have been proposed and studied assuming utilization of large-scale high temperature heat sources such as solar or nuclear, in particular the High Temperature Gas-Cooled Reactor (HTGR) which can supply heat at temperatures close to 1000 °C.4,5
The concept of thermochemical water-splitting cycle represents carbon-free hydrogen production. Compared with present counterparts, like water electrolysis, this method is in the early stages of development. However, it has potential merit for economical large-scale hydrogen production because of its expected economies of scale, which can meet the large hydrogen demand expected from a future hydrogen society. This paper summarizes state-of-the-art research in one of the most promising thermochemical cycles.
2. Thermochemical IS process
Among the many cycles proposed so far, those that utilize thermal decomposition of sulfuric acid as the highest temperature endothermic reaction have been categorized as “sulfur cycles” and have attracted much interest.5–7 The thermal decomposition of sulfuric acid, reaction (1), | H2SO4 → H2O + SO2 + 0.5O2 | (1) |
actually proceeds in the following two steps.
H2SO4(aq) → H2O(g) + SO3(g) 300∼500 °C |
SO3(g) → SO2(g) + 0.5O2(g) 800∼900 °C |
Both steps are highly endothermic and proceed smoothly without side reactions and with a high equilibrium conversion ratio at the temperature range indicated. The endothermic characteristics match well with the temperature distribution of the heat source, HTGR. The heat produced by HTGR is transferred to the chemical process through the sensible heat of helium gas, the temperature of which varies, e.g. 400∼900 °C. These characteristics make the reaction quite suited as a high temperature endothermic reaction for thermochemical water-splitting cycles.8
The Iodine–Sulfur cycle (or Sulfur–Iodine cycle, or Ispra Mark 16 cycle, hereafter termed as the IS process) utilizes the following two chemical reactions which combine with the sulfuric acid decomposition reaction to close the thermochemical water-splitting cycle (Fig. 1).
| SO2 + I2 + 2H2O → 2HI + H2SO4 | (2) |
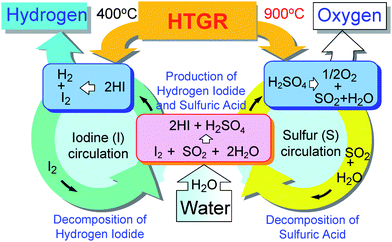 |
| Fig. 1 Scheme of a thermochemical water-splitting cycle using iodine and sulfur. | |
Here, reaction (2), known as the “Bunsen reaction”, is a low-temperature exothermic reaction, where the raw material, water, reacts with iodine and sulfur dioxide producing spontaneously an aqueous solution of hydriodic acid and sulfuric acid. The thermal decomposition of hydrogen iodide (3) can be carried out either in gas phase or in liquid phase with the help of a catalyst. The IS process is a pure thermochemical cycle and can be an all fluid process that enjoys easy scale up.
3. Process chemistry and process design
For the combined operation of reactions (1)–(3), it was necessary, at first, to find a separation method for HI and H2SO4 produced by the Bunsen reaction, since conventional distillation of the mixed acid solution resulted in decomposition of the acids due to the occurrence of the reverse reaction of the Bunsen reaction. So far, the following ideas have been examined on the separation issue. De Beni et al.9 studied utilization of a solvent extraction method. Dokiya et al.10 proposed carrying out the Bunsen reaction using an electrochemical cell equipped with an ion exchange membrane. Introduction of a third element such as Ni,11 Mg12 was attempted to replace the acid separation with a separation of the corresponding salts, which could be carried out utilizing the difference in their solubility. However, the most intensive work has been carried out using a liquid–liquid separation phenomenon (LL separation), which researchers at General Atomics (GA) found and proposed to use for the HI/H2SO4 separation.8,13 The LL separation occurs spontaneously in the presence of excess iodine. The heavier phase produced is mainly composed of HI, I2, and H2O, and is called “HIx” solution. The main components of the lighter phase are H2SO4 and H2O. Fig. 2 shows the density of the phase-separated solution.14
 |
| Fig. 2 Relationship between density and H2O molar fraction in H2O + HI + H2SO4 of the mixed acid solution (H2O + HI + H2SO4 + I2 system) at 25 °C under iodine saturation conditions.14 | |
The LL separation offered an easy way for the separation; however, it presented another problem, “How to separate HI from HIx solution?” In the studies carried out up to now, the composition of HIx solution produced by the Bunsen reaction hardly exceeded those of the quasi-azeotrope, and conventional distillation of the HIx solution resulted in a distillate of azeotropic hydriodic acid, the H2O/HI molar ratio of which was ca. 5. Therefore, the distillation requires large reboiler duty, which reduces the conversion efficiency of heat to hydrogen energy. To overcome this the researchers at GA proposed an extractive distillation using phosphoric acid.8 Later, Engels et al.15 proposed the interesting concept of reactive distillation operated at elevated pressure, this enabled the separation of HI from the HIx solution and the decomposition of HI into hydrogen and iodine to be carried out in one column by utilizing the pressure shift of azeotropic and quasi-azeotropic composition. Recently, the application of membrane techniques such as electro–electrodialysis,16 pervaporation17 and membrane distillation18 have been examined to facilitate HI separation. However, at present, it is not clear which one is the best solution to the separation problem. At the same time, in pursuing a deeper understanding of the Bunsen reaction, parametric studies on the reaction system have been carried out in the LL separation condition by Giaconia et al.,19 Lee et al.,20 and Nakajima et al.21Fig. 3 shows the effect of sulfur dioxide pressure on the concentration of HIx solution produced by the Bunsen reaction.21 These studies will be useful for constructing an efficient process scheme including the discussed separation of HI from the HIx solution.
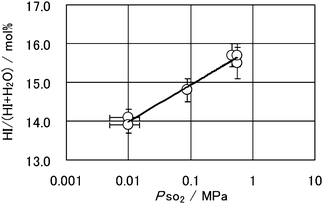 |
| Fig. 3 Effect of SO2 partial pressure on the Bunsen reaction under iodine saturation condition at 50 °C. HI/(HI + H2O) denotes the molar ratio in a hypothetical HIx solution that can be obtained by performing an ideal purification of the product heavy phase solution using back reaction of the Bunsen reaction.21 | |
In the thermal decomposition of SO3 and of HI, catalysts are required to achieve engineeringly feasible reaction rates, and these have been studied.8,22,23 Also, the utilization of hydrogen separation membranes has been attempted as a way to purify the product hydrogen or to enhance HI decomposition (this equilibrium conversion ratio is limited to a low value of 20–30%.)24
In parallel with these studies on process chemistry, the heat/mass balance of the water-splitting process has been studied by various plausible flowsheets. Researchers at GA published the results of a total flowsheet analysis, where the LL separation and the extractive distillation were considered.25 A “process thermal efficiency”, defined as the ratio of the Higher Heating Value (HHV) of hydrogen produced and the net thermal energy input to the process, was estimated to be 47%. In their design, intensive heat recovery was assumed to include application of a steam recompression method to recover the vaporization heat of solvent water in the concentration of sulfuric acid and phosphoric acid. The application of a multi-effect evaporator was proposed to concentrate sulfuric acid by Knoche and co-workers.26 Also, two different versions of the oxygen generation step were presented by Bilgen and co-workers.27 As for the processing of HIx solution, reactive distillation has been attracting a lot of interest because of its simplicity.6
Precise thermodynamic data concerning the concentrated process solutions is desired for accurate evaluation and optimization of the heat/mass balance.28 Especially, knowledge of the vapor–liquid equilibrium of the HI–I2–H2O system is insufficient in spite of its importance, and measurements to enhance the database are in progress at Commissariat à l'énergie atomique (CEA),29 Ente per le Nuove tecnologie, l'Energia e l'Ambiente (ENEA)30 and Japan Atomic Energy Agency (JAEA).31Fig. 4 shows the T–x–y curves at elevated pressures reported by JAEA.31
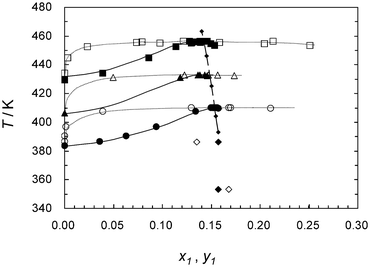 |
| Fig. 4 Isobaric VLE data of the binary system HI(1) + H2O(2). (■, □; 0.58 MPa), (▲, △; 0.30 MPa), (●, ○; 0.15 MPa), (◆, ◇: 0.016 MPa at 386 K, and 0.059 MPa at 353 K from Ref. 29. Here, filled keys denote bubbling point, whereas open keys denote dew point. A broken line with ◆ keys indicates the azeotrope calculated by Berndhäuser from Ref. 15b. (bubbling point curves) and ⋯ (dew point curves) were drawn by eye.31 | |
4. Demonstration of closed-cycle continuous water-splitting
GA built a test apparatus named the “Closed-Loop Cycle Demonstrator (CLCD)” with a designed hydrogen production rate of 1.2 L h−1.25 The glass-made CLCD comprised a Bunsen reactor, HIx purifier, HI decomposer, H2SO4 purifier, H2SO4 decomposer, and was operated in batch mode to demonstrate the feasibility of water splitting. Following CLCD, GA built a bench-scale glass apparatus featuring the extractive distillation with a designed hydrogen production rate of 60 L h−1. The unit operation was performed successfully in the Bunsen reaction step and in the sulfuric acid decomposition step, although it was not in the HI decomposition step.25
Closed-cycle continuous operation of the water-splitting process featuring the LL separation was attempted by JAEA. Key points in the continuous operation were the selection and the control of the Bunsen reaction condition, by which possible side reactions forming sulfur and/or hydrogen sulfide should be avoided and also the composition of LL separated solution should be kept constant. With the help of an optical sensor for monitoring the composition fluctuation of the Bunsen solution, the continuous water-splitting was carried out with a hydrogen production rate of 1 L h−1 using a small glass apparatus comprising Bunsen reactor, HIx purifier, HIx distillation column, HI decomposer, H2SO4 purifier/concentrator, H2SO4 decomposer.32 Later, a scaled-up glass apparatus equipped with an automatic control system featuring an ultrasonic sensor was built. Continuous and stable water-splitting was demonstrated for one week using the apparatus with a hydrogen production rate of ca. 30 L h−1.33Fig. 5 shows a simplified scheme of the apparatus. Although the basic technique for process control was developed by this work, improvement in composition monitoring is necessary to realize water-splitting under more efficient conditions. Recently, Kubo et al34 derived a set of empirical equations for the densities and the composition of LL separated solutions, which will be a good basis for more versatile and convenient monitoring of the Bunsen reaction system.
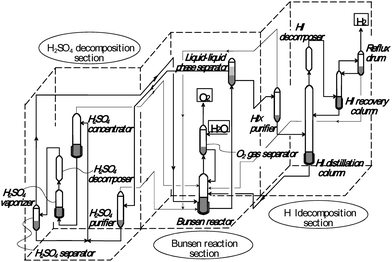 |
| Fig. 5 Scheme of continuous hydrogen production test apparatus.33 | |
The next step will be a demonstration of the continuous operation including an energy-efficient scheme for HI separation from HIx solution such as the extractive distillation, the reactive distillation, or the membrane processes. Recently, Sandia National Laboratory (SNL), GA and CEA collaborated to build a water-splitting test apparatus featuring the extractive distillation with a designed hydrogen production rate of 100–200 L h−1, and operational tests are underway.35
5. Development of components
Since sulfuric acid and iodine are very corrosive, the selection of construction materials is an important issue for the development of any large-scale plant. Corrosion tests have been carried out on commercially available materials at GA36 and JAEA.37 The knowledge obtained so far may be summarized as shown in Fig. 6. In the highest temperature process environment of gas-phase SO3 decomposition, some refractory alloys that have been used in conventional industrial plants show good corrosion resistance. In the gaseous environment of HI decomposition at 450 °C, a Ni–Cr–Mo–Ta alloy was found to show good corrosion resistance. As for the Bunsen reaction step operating at around 100 °C, glass, Ta, Nb, SiC etc. showed good corrosion resistance, so be used as lining materials. In the environment of HIx distillation operating at around 230 °C, Ta showed excellent corrosion resistance. The most severe environment is in the boiling of concentrated sulfuric acid under high pressure (e.g. 2 MPa) at temperatures of up to about 400 °C, where materials containing Si, such as Si–SiC, SiC, Si3N4 and Fe–Si were the only materials that showed excellent corrosion resistance.
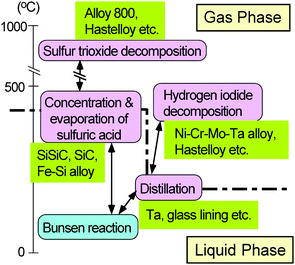 |
| Fig. 6 Candidate construction materials which exhibited good corrosion resistance in simulated IS process environments. | |
Based on this knowledge, development of key components has been implemented. Researchers at JAEA, in co-operation with Toshiba Corp., have proposed the concept of a sulfuric-acid decomposer, in which the sulfuric acid of concentration more than 90 wt% is evaporated and, simultaneously, part of the H2SO4 spontaneously decomposes into gaseous SO3 and H2O using the heat supplied by high temperature helium gas.38Fig. 7 shows a cut-away view of the sulfuric acid decomposer designed for a future test plant with a hydrogen production rate of 30 m3 h−1. The decomposer is equipped with multi-hole heat exchanger blocks made of SiC. Two blocks of 0.25 m in outer diameters and 0.75 m in height are piled vertically with gold gaskets and tie-lods. Helium gas flows through the inside channels of the ceramic blocks, and exchanges heat with the counter-current sulfuric acid flow. Test fabrication of the ceramic heat exchanger was successfully completed which confirmed its fabricability. Also, helium leak tests using the test-fabricated heat exchanger under simulated seismic load confirmed its good seal performance.39
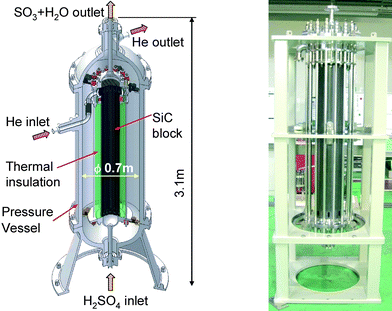 |
| Fig. 7 A Sulfuric Acid Decomposer. Left: concept of 30 m3 H2 h−1 scale model. Right: test-fabricated ceramic heat exchanger made of SiC.38 | |
Recently, researchers at SNL developed an interesting bayonet-type reactor made of SiC for the vaporization and decomposition of sulfuric acid for use in the hydrogen production test apparatus mentioned in Section 4. The reactor was composed of two concentric tubes and the outer tube had a hemispherical upper end. The SO3 decomposition catalyst is set at the upper part of the annular space. Sulfuric acid is fed to the bottom of the annular space and vaporized by heating from outside of the outer tube. The vaporized sulfuric acid is superheated and decomposed into SO2 and O2 in the catalyst zone at a temperature of 800 °C. Then, the decomposed gaseous mixture flows down the inner tube while exchanging the heat with the gases flowing up the annular space. Sulfuric acid processing was successfully tested with the reactor.40
Development of ceramic components for the sulfuric acid processing step is also in progress in Korea41 and in the EU.42
6. Conclusions
The present status of research and development on thermochemical IS processing for hydrogen production is briefly reviewed. It should be noted that an international cooperation project has started on the development of a thermochemical water-splitting process, as one of the important research subjects in the framework of Very-High Temperature Reactor (VHTR) systems in the Generation IV International Forum. All of the research subjects mentioned in this paper will be studied in this project.
It is desirable that these activities produce fruitful results that will bring about a demonstration of large-scale economical hydrogen production.
References
-
J. E. Funk and R. M. Reinstrom, System study of hydrogen generation by thermal energy, TID 20441; EDR 3714, Volume II, Suppl. A, Allison Division of General Motors Corporation, 1964 Search PubMed.
- J. E. Funk and R. M. Reinstrom, Energy requirements in the production of hydrogen from water, IEC Proc. Des. Dev., 1966, 5, 336–342 Search PubMed.
- G. De Beni and C. Marchetti, Hydrogen: Key to the energy market, Eurospectra, 1970, 9, 46–50 Search PubMed.
-
S. Sato, Thermochemical hydrogen production, in Solar–Hydrogen Energy Systems, ed. T. Ohta, Oxford, Pergamon Press, 1979, pp. 81–114 Search PubMed.
- J. E. Funk, Thermochemical hydrogen production: past and present, Int. J. Hydrogen Energy, 2001, 26, 185–190 CrossRef CAS.
-
L. C. Brown, G. E. Besenbruch, R. D. Lentsch, K. R. Schultz, J. E. Funk, P. S. Pickard, A. C. Marshall, S. K. Showalter, High efficiency generation of hydrogen fuels using nuclear power, GA-A24285, 2003 Search PubMed.
-
http://www.gen-4.org/Technology/systems/vhtr.htm
.
-
J. H. Norman, G. E. Besenbruch, D. R. O'Keefe, Thermochemical water-splitting for hydrogen production, GRI-80/0105, 1981 Search PubMed.
- G. De Beni, G. Pierini and B. Spelta, The reaction of sulphur dioxide with water and halogen. The case of iodine: reaction in the presence of organic solvents, Int. J. Hydrogen Energy, 1980, 5, 141–149 CrossRef CAS.
- M. Dokiya, T. Kameyama and K. Fukuda, Thermochemical hydrogen preparation - part V. A feasibility study of the sulfur–iodine cycle [1–4], Int. J. Hydrogen Energy, 1979, 4, 267–277 CrossRef CAS.
- S. Shimizu, S. Sato, H. Nakajima and Y. Ikezoe, The nickel–iodine–sulfur process for thermochemical hydrogen production. I. Proposal, Denki Kagaku, 1981, 49, 699–704 Search PubMed (in Japanese).
- S. Mizuta and T. Kumagai, Thermochemical hydrogen production by the magnesium–sulfur–iodine cycle, Bull. Chem. Soc. Jpn., 1982, 55, 1939–1942 CrossRef CAS.
-
J. L. Russell, Jr., K. H. McCorkle, J. H. Norman, J. T. Porter II, T. S. Roemer, J. R. Schuster, R. S. Sharp, Water Splitting - A Progress Report, Proc. 1st World Hydrogen Energy Conf., Miami Beach, Florida, USA, March 1976, Vol. 1, pp.1A-105–1A-124 Search PubMed.
-
S. Shimizu, H. Nakajima, K. Onuki, A progress report on bench scale studies of the iodine-sulfur process for thermochemical hydrogen production, in High temperature application of nuclear energy, Proceedings of a Technical Committee meeting held in Oarai, Japan, 19-20 October 1992, IAEA-TECDOC-761, IAEA, August 1994, pp.114–119 Search PubMed.
-
(a)
H. Engels, K. F. Knoche, M. Roth, Direct dissociation of hydrogen iodide - an alternative to the General Atomic proposal, Proc. 6th World Hydrogen Energy Conf., Vienna, Austria, July 1986, Vol. 2, pp.657–662 Search PubMed;
(b) C. Berndhäuser and K. F. Knoche, Experimental investigations of thermal HI decomposition from H2O–HI–I2 solutions, Int. J. Hydrogen Energy, 1994, 19, 239–244 CrossRef.
-
(a) K. Onuki, G. J. Hwang, Arifal and S. Shimizu, Electro-electrodialysis of hydriodic acid in the presence of iodine at elevated temperature, J. Membr. Sci., 2001, 192, 193–199 CrossRef CAS;
(b) S. D. Hong, J. K. Kim, K. K. Bae, S. H. Lee, H. S. Choi and G. J. Hwang, Evaluation of the membrane properties with changing iodine molar ratio in HIx (HI–I2–H2O mixture) solution to concentrate HI by electro-electrodialysis, J. Membr. Sci., 2007, 291, 106–110 CrossRef CAS.
-
(a) C. J. Orme, M. G. Jones and F. F. Stewart, Pervaporation of water from aqueous HI using Nafion®-117 membranes for the sulfur-iodine thermochemical water splitting process, J. Membr. Sci., 2005, 252, 245–252 CrossRef CAS;
(b) F. F. Stewart, C. J. Orme and M. G. Jones, Membrane processes for the sulfur-iodine thermochemical cycle, Int. J. Hydrogen Energy, 2007, 32, 457–462 CrossRef CAS.
- G. Caputo, C. Felici, P. Tarquini, A. Giaconia and S. Sau, Membrane distillation of HI/H2O and H2SO4/H2O mixtures for the sulfur–iodine thermochemical process, Int. J. Hydrogen Energy, 2007, 32, 4736–4743 CrossRef CAS.
- A. Giaconia, G. Caputo, A. Ceroli, M. Diamanti, V. Barbarossa, P. Tarquini and S. Sau, Experimental study of two phase separation in the Bunsen section of the sulfur–iodine thermochemical cycle, Int. J. Hydrogen Energy, 2007, 32, 531–536 CrossRef CAS.
- B. J. Lee, H. C. No, H. J. Yoon, S. J. Kim and E. S. Kim, An optimal operating window for the Bunsen process in the I–S thermochemical cycle, Int. J. Hydrogen Energy, 2008, 33, 2200–2210 CrossRef CAS.
- H. Nakajima, Y. Imai, S. Kasahara, S. Kubo and K. Onuki, Effect of sulfur dioxide partial pressure on the reaction of iodine, sulfur dioxide and water, Kagaku Kogaku Ronbunshu, 2007, 33, 257–260 CrossRef CAS (in Japanese).
-
(a) H. Ishikawa, E. Ishii, I. Uehara and M. Nakane, Catalyzed thermal decomposition of H2SO4 and production of HBr by the reaction of SO2 with Br2 and H2O, Int. J. Hydrogen Energy, 1982, 7, 237–246 CrossRef CAS;
(b) H. Tagawa and T. Endo, Catalytic decomposition of sulfuric acid using metal oxides as the oxygen generating reaction in thermochemical water splitting process, Int. J. Hydrogen Energy, 1989, 14, 11–17 CrossRef CAS;
(c) V. Barbarossa, S. Brutti, M. Diamanti, S. Sau and G. De Maria, Catalytic thermal decomposition of sulphuric acid in sulphur-iodine cycle for hydrogen production, Int. J. Hydrogen Energy, 2006, 31, 883–890 CrossRef CAS;
(d) D. M. Ginosar, L. M. Petkovic, A. W. Glenn and K. C. Burch, Stability of supported platinum sulfuric acid decomposition catalysts for use in thermochemical water splitting cycles, Int. J. Hydrogen Energy, 2007, 32, 482–488 CrossRef CAS;
(e) A. M. Banerjee, M. R. Pai, K. Bhattacharya, A. K. Tripathi, V. S. Kamble, S. R. Bharadwaj and S. K. Kulshreshtha, Catalytic decomposition of sulfuric acid on mixed Cr/Fe oxide samples and its application in sulfur-iodine cycle for hydrogen production, Int. J. Hydrogen Energy, 2008, 33, 319–326 CrossRef CAS.
-
(a) Y. Oosawa, Y. Takemori and K. Fujii, Catalytic decomposition of hydrogen iodide in the magnesium-iodine thermochemical cycle - catalyst search -, Nippon Kagaku Kaishi, 1980, 1081–1087 CAS (in Japanese);
(b) Y. Oosawa, T. Kumagai, S. Mizuta, W. Kondo, Y. Takemori and K. Fujii, Catalytic decomposition of hydrogen iodide, Bull. Chem. Soc. Jpn., 1981, 54, 742–748 CrossRef CAS;
(c) Y. Shindo, N. Ito, K. Haraya, T. Hakuta and H. Yoshitome, Kinetics of the catalytic decomposition of hydrogen iodide in the thermochemical hydrogen production, Int. J. Hydrogen Energy, 1984, 9, 695–700 CrossRef CAS;
(d) Y. Zhang, Z. Wang, J. Zhou, J. Liu and K. Cen, Effect of preparation method on platinum–ceria catalysts for hydrogen iodide decomposition in sulfur-iodine cycle, Int. J. Hydrogen Energy, 2008, 33, 602–607 CrossRef CAS;
(e) Y. Zhang, J. Zhou, Z. Wang and K. Cen, Detailed kinetic modeling and sensitivity analysis of hydrogen iodide decomposition in sulfur-iodine cycle for hydrogen production, Int. J. Hydrogen Energy, 2008, 33, 627–632 CrossRef CAS.
-
(a) N. Ito, Y. Shindo, T. Hakuta and H. Yoshitome, Enhanced catalytic decomposition of HI by using a microporous membrane, Int. J. Hydrogen Energy, 1984, 9, 835–839 CrossRef CAS;
(b) H. Ohya, H. Nakajima, N. Togami, H. Ohashi, M. Aihara, S. Tanisho and Y. Negishi, Hydrogen purification using zirconia-silica composite membranes for thermochemical process, Int. J. Hydrogen Energy, 1997, 22, 509–515 CrossRef CAS;
(c) G. J. Hwang, K. Onuki, S. Shimizu and H. Ohya, Hydrogen separation in H2–H2O–HI gaseous mixture using the silica membrane prepared by chemical vapor deposition, J. Membr. Sci., 1999, 162, 83–90 CrossRef CAS;
(d) S. Tosti, R. Borelli, F. Borgognoni, P. Favuzza, C. Rizzello and P. Tarquini, Study of a dense metal membrane reactor for hydrogen separation from hydroiodic acid decomposition, Int. J. Hydrogen Energy, 2008, 33, 5106–5114 CrossRef CAS.
-
J. H. Norman, G. E. Besenbruch, L. C. Brown, D. R. O'Keefe, C. L. Allen, Thermochemical water-splitting cycle, bench-scale investigations, and process engineering, GA-A16713, 1982 Search PubMed.
-
K. F. Knoche, H. Schepers, K. Hesselmann, Second law and cost analysis of the oxygen generation step of the general atomic sulfur–iodine cycle, Proc. 5th World Hydrogen Energy Conf., Toronto, Canada, July, 1984, Vol. 2, 487–502 Search PubMed.
-
(a) I. T. Öztürk, A. Hammache and E. Bilgen, A new process for oxygen generation step for the hydrogen producing sulphur-iodine thermochemical cycle, Trans. IChemE., 1994, 72(Part A), 241–250 Search PubMed;
(b) I. T. Öztürk, A. Hammache and E. Bilgen, An improved process for H2SO4 decomposition step of the sulfur-iodine cycle, Energy Convers. Manage., 1995, 36, 11–21 CrossRef CAS.
-
(a) S. Goldstein, J. M. Borgard and X. Vitart, Upper bound and best estimate of the efficiency of the iodine sulphur cycle, Int. J. Hydrogen Energy, 2005, 30, 619–626 CrossRef CAS;
(b) S. Kasahara, K. Onuki, M. Nomura and S. Nakao, Static analysis of the thermochemical hydrogen production IS process for assessment of the operation parameters and the chemical properties, J. Chem. Eng. Jpn., 2006, 39, 559–568 CrossRef CAS.
- D. Doizi, V. Dauvois, J. L. Roujou, V. Delanne, P. Fauvet, B. Larousse, O. Hercher, P. Carles, C. Moulin and J. M. Hartmann, Total and partial pressure measurements for the sulphur–iodine thermochemical cycle, Int. J. Hydrogen Energy, 2007, 32, 1183–1191 CrossRef CAS.
- R. Liberatore, A. Ceroli, M. Lanchi, A. Spadoni and P. Tarquini, Experimental vapor-liquid equilibrium data of HI–H2O–I2 mixtures for hydrogen production by sulphur-iodine thermochemical cycle, Int. J. Hydrogen Energy, 2008, 33, 4283–4290 CrossRef CAS.
- M. Hodotsuka, X. Yang, H. Okuda and K. Onuki, Vapor-Liquid Equilibria for the HI + H2O System and the HI + H2O + I2 System, J. Chem. Eng. Data, 2008, 53, 1683–1687 CrossRef CAS.
- H. Nakajima, K. Ikenoya, K. Onuki and S. Shimizu, Closed-cycle continuous hydrogen production test by thermochemical IS process, Kagaku Kogaku Ronbunshu, 1998, 24, 352–355 CAS (in Japanese).
-
S. Kubo, H. Nakajima, S. Shimizu, K. Onuki, R. Hino, A bench scale hydrogen production test by the thermochemical water-splitting iodine–sulfur process, Proc. Global 2005, Tsukuba, Japan, October, 2005, Paper No. 474 Search PubMed.
-
S. Kubo, H. Nakajima, Y. Imai, S. Kasahara, N. Tanaka, H. Okuda, R. Miyashita, K. Onuki, An estimation technique for composition of Bunsen reaction solutions on thermochemical water-splitting IS process, Proc. 17th World Hydrogen Energy Conf., Brisbane, Australia, June, 2008, paper 311 Search PubMed.
-
R. Buckingham, B. Russ, R. Moore, P. Pickard, M. Helie, P. Carles, Status of the INERI sulfur–iodine integrated loop experiment, Proc. 17th World Hydrogen Energy Conf., Brisbane, Australia, June, 2008, paper 310 Search PubMed.
-
(a)
P. W. Trester and H. G. Staley, Assessment and investigation of containment materials for the sulfur–iodine thermochemical water-splitting process for hydrogen production, GRI-80/0081, 1981 Search PubMed;
(b) B. Wong, R. T. Buckingham, L. C. Brown, B. E. Russ, G. E. Besenbruch, A. Kaiparambil, R. Santhanakrishnan and Ajit Roy, Construction materials development in sulfur-iodine thermochemical water-splitting process for hydrogen production, Int. J. Hydrogen Energy, 2007, 32, 497–504 CrossRef CAS.
- N. Tanaka, K. Onuki, S. Shimizu and A. Yamaguchi, Corrosion resistance of materials of construction for high temperature sulfuric acid service in Thermochemical IS Process (Alloy 800, Alloy 600, SUSXM15J1 and SiC), Zairyo-to-Kankyo, 2006, 55, 320–324 Search PubMed (in Japanese) and references therein.
- A. Terada, H. Ota, H. Noguchi, K. Onuki and R. Hino, Development of sulfuric acid decomposer for thermochemical hydrogen production IS process, Trans. At. Energy Soc. Jpn., 2006, 5, 68–75 Search PubMed (in Japanese).
-
H. Noguchi, H. Ota, A. Terada, S. Kubo, K. Onuki, R. Hino, Development of sulfuric acid decomposer for thermo-chemical IS process, Proc. ICAPP '06, Reno, NV, USA, June, 2006, Paper 6166 Search PubMed.
-
(a)
R. C. Moore, F. Gelbard, E. J. Parma, M. E. Vernon, R. X. Lenard, P. S. Pickard, A laboratory-scale sulfuric acid decomposition apparatus for use in hydrogen production cycles, Proc. 2007 International Topical Meeting on Safety and Technology of Nuclear Hydrogen Production, Control and Management, Boston, Massachusetts, USA, June, 2007 Search PubMed;
(b)
F. Gelbard, R. C. Moore, E. J. Parma, M. E. Vernon, H. B. J. Stone, Sulfuric acid decomposition experiments for thermochemical hydrogen production from nuclear power, Proc. 2007 International Topical Meeting on Safety and Technology of Nuclear Hydrogen Production, Control and Management Search PubMed.
-
J. W. Park, H. Kim, Y. Kim, A study on a process heat exchanger for SO3 decomposer using Ni-based alloys surface-modified by a SiC coating and N+ ion beam bombardment, Proc. 2007 International Topical Meeting on Safety and Technology of Nuclear Hydrogen Production, Control and Management, Boston, Massachusetts, USA, June, 2007 Search PubMed.
-
http://cordis.europa.eu/fetch?CALLER=FP7_PROJ_EN&ACTION=D&DOC=21&CAT=PROJ&QUERY=011c6e800548:5b0f:63d1e70a&RCN=85748
.
|
This journal is © The Royal Society of Chemistry 2009 |
Click here to see how this site uses Cookies. View our privacy policy here.