DOI:
10.1039/B809215J
(Perspective)
Energy Environ. Sci., 2008,
1, 639-644
Soybean oil as a renewable feedstock for nitrogen-containing derivatives
Received
30th May 2008
, Accepted 6th August 2008
First published on 19th September 2008
Abstract
A review is given of the use of soybean oil as a renewable feedstock to produce a range of different materials that contain nitrogen. In the past, most efforts have been concentrated on converting triglycerides to fatty amines and amides. Indeed, many industrially significant fatty amines and amides are known and widely used. More recently, several research groups have developed novel approaches to functionalize the fatty acid chain structures to produce novel compounds, surfactants, and even polymers that contain nitrogen. Some of the approaches (involving organic and enzymatic reactions) may have industrial relevance. Included in this review are reactions with triglyceride oils, fatty acid esters, and methyl soyate (methyl esters of triglyceride oils).
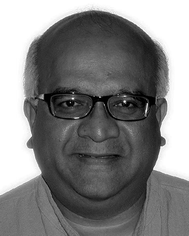 Atanu Biswas | Atanu Biswas is a research chemist. He received his PhD from the University of Notre Dame. After a postdoctoral stay at Case Western Reserve University, he worked at Hercules Incorporated for 14 years. Six years ago he joined USDA where he has published 27 papers. His research deals with green chemistry, polysaccharides, and vegetable oils. A recent focus has been chemical and enzymatic modifications of renewable resources to produce value-added products. |
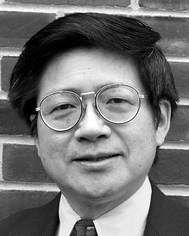
H. N. Cheng | H. N. Cheng is a Senior Research Fellow at Hercules Incorporated in Wilmington, DE. He obtained his BS from UCLA and his PhD from the University of Illinois at Urbana-Champaign. He has authored or co-authored 130 papers and 21 patent publications. His recent publications deal with enzyme biocatalysis, polymer reactions, green chemistry, and the use of renewable natural materials. |
1. Introduction
Soybean oil is a renewable natural resource and an environmentally friendly alternative to petroleum-based products. The major components of soybean oil (SBO) are triacylglycerols with a mixture of fatty acids moieties (typically 51% linoleic acid, 25% oleic acid, 10% palmitic acid, 7% linolenic acid, and 5% stearic acid). There has been increasing interest in using SBO as a raw material to produce SBO derivatives and even polymers, particularly driven by the current interest in green chemistry and sustainability. Already numerous SBO derivatives have been produced. Some materials have been commercialized with great success, such as epoxidized oil,1,2 and SBO methyl ester (methyl soyate)3,4 These developments have been the subject of several review articles.5–7
In this review article, we choose to concentrate on a subset of soybean products, namely those that contain nitrogen. This subset is particularly interesting because nitrogen-containing functionalities often entail different chemistry that permits different synthons and different products to be generated. As a result, the development of nitrogen-containing derivatives should enrich this field and permit greater possibilities to be attained with soybean oil as the feedstock. Already in the past, fatty amines and amides have been produced and are successful as commercial products. Recent efforts have concentrated on functionalizing the fatty acid chain structures to produce novel compounds and even polymers. Both the older and the newer technologies are reviewed below.
A large number of reactions have been reported. Given below are some of the more commercially important processes.
These industrially significant compounds are produced in two steps (Scheme 1), first by reacting fatty acids with ammonia to produce nitriles and amides, and secondly by hydrogenation with a nickel catalyst to convert the nitriles and amides to amines.8,9
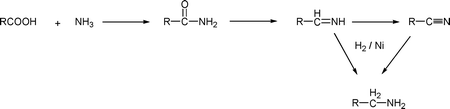 |
| Scheme 1 Preparation of fatty amine. | |
Several commercial processes are available, some involving two discrete reactions for the two steps, and some involving a single reaction incorporating both steps5,10,11 Variations of the process use triglyceride oil or fatty alcohol as the starting materials12,13 The fatty amines are starting compounds for the manufacture of quaternary ammonium compounds and various cationic and amphoteric substances. These derivatives find wide application as biocides, sanitizing agents, algae control in water treatment, ore floatation agents in mining, effective corrosion inhibitors, and lubricants in drilling mud formulations.
2b. Derivatives of fatty amines
The fatty amines are starting materials for a family of compounds, mostly for surface active applications.5 Thus, alkylation or oxidation produces quaternary ammonium and amine oxides. Alkoxylation yields fatty amine poly(alkylene oxide) ethers. The reaction with monochloroacetic acid produces betaines, which are amphoteric surfactants.
The reaction of triglycerides or fatty acids with amines readily yields fatty acid amides. These have been around for a long time and are used, for example, as antislip agents for polymer films14 and ingredients in defoamers.15 Some examples of amides are shown in Scheme 2 below.
The amide formed from the reactions of fatty acids with diethanolamine has been reported to be an ingredient for a lubricating oil in the manufacturing of woolen cloth.16–18 These alkanolamides are nonionic surface active agents used in dry cleaning soaps, fuel oil additives, rust inhibitors, textile scouring, and dye leveling agents. Similarly, the amide from hydrogenated soybean oil or coconut oil glycerides and a hydroxyalkyl polyamine has been reported to be an ingredient useful in lubricating and softening textile materials such as rayon fabrics.19
The reaction of a fatty acid with a polyamine produces an amide with extra amine groups.20 Similarly, the reaction of these amines with unsaturated or halogenated carboxylic acids, carboxylated amine compounds or acid anhydrides can form different amphoteric structures which have been claimed to modify softness and texture of paper, textiles, human skin and hair tresses.21
Dimer acids obtained from soybean oil can be converted into both reactive and nonreactive polyamide resins.22–24 The condensation of dimer acids with ethylenediamine results in nonreactive low-molecular weight polyamides. Dimer acids typically contain 10–30% trimer acids which lead to three dimensional polymers that cause stickiness, narrow melting ranges, cold flow resistance, and rheological properties useful in adhesives. These polyamides are used without solvents and have applications as hot-melt adhesives in packaging, can seam solders, book bindings, shoe soles, flexographic printing inks for food packaging films and thixotropic alkyd paints. The condensation of dimer acids in slight excess of polyamines (diethylene triamine and triethylene tetramine) results in reactive polyamides resins of low molecular weight having a free amino group in the chain.24 These are used as curing agents in epoxy resins that find application in surface coatings, adhesives, potting and casting compounds, and patching and sealing compounds.25 Epoxy adhesives are typically two-component systems including an epoxy-resin and a polyamide curing agent. The two-component epoxy systems are used in toppings for concrete floors, bridge decks, and airport landing strips.
2d. Fatty imidazolines
These are cationic surfactants obtained from ethylene diamine derivatives. One of the reaction pathways is shown in Scheme 3 below.
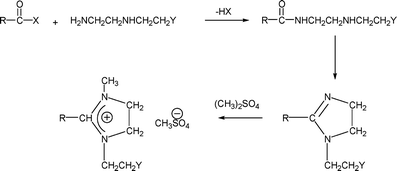 |
| Scheme 3 Preparation of fatty imidazoline. | |
The surfactant is amphoteric if the Y carries an anionic charge (e.g., carboxyl). A variety of different applications have been reported, e.g., dispersants, detergents, flocculants, rheology modifiers, corrosion inhibitors, and paper debonders. This type of material has been recently reviewed.26
Soybean oil contains a fair amount of unsaturation due to oleic, linoleic and linolenic moieties present. Yet, surprisingly only a few reports have been made to take advantage of the unsaturation to incorporate nitrogen. The following reactions can be cited as examples.
Alkyl nitrate derivatives of soybean oil and other oils have been synthesized as cetane improvers for use in diesel fuel.27,28 Among the several nitration methods evaluated, mixtures of nitric acid and acetic anhydride are preferred.
3b. Soybean oil azadicarboxylate diethyl ester
In this novel synthetic approach (Scheme 4), structural modification of soybean oil is carried out using diethyl azadicarboxylate (DEAD) in the absence of catalyst and solvent.29 The reaction has been shown to occur in a microwave oven in 5–15 minutes. The reaction can also proceed via conventional heat, albeit for a longer time. The products are fully characterized by 1H, 13C, and two-dimensional NMR.
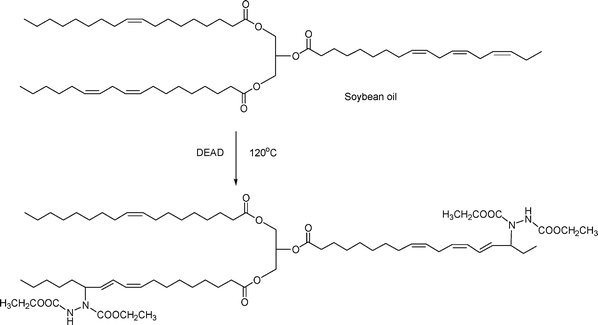 |
| Scheme 4 Preparation of soybean oil azadicarboxylate diethyl ester. | |
In a subsequent work, soybean oil and DEAD have been shown to react at room temperature to undergo a self-curing and thickening reaction.30 The modified soybean oil first forms oligomers and (with time) eventually polymerizes. This reaction permits soybean oil to be used as the raw material for a variety of novel products that require curing, thickening, or adhesive properties.
3c. Derivatives of soybean oil diethyl-azadicarboxylate
The above compound has been hydrolysed chemically and enzymatically,31,32 Chemical hydrolysis gives hydrazino-fatty acids, whereas enzymatic hydrolysis gives the fatty acids derivatized with the diethyl-azadicarboxylate functionality (Scheme 5). Both are useful synthons for further reactions to yield new materials. The hydrazino-fatty acids are especially interesting. Hydrazine, for example, can be reduced to amine to give a new kind of amino acid from the fatty acid.
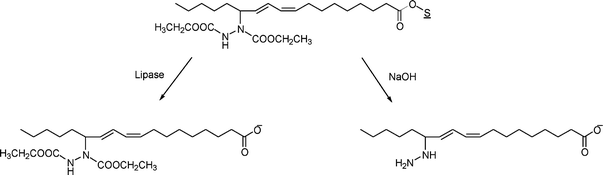 |
| Scheme 5 Chemical and enzymatic hydrolysis products of soybean oil azadicarboxylate diethyl ester. ‘S’ refers to the glycerol moiety in the soybean oil. | |
4. Reactions with epoxy functionality of epoxidized soybean oil/fatty acid esters
One of the successful reactions of soybean oil is epoxidation. Epoxidized soybean oil is commercially available and relatively cheap. The epoxide can be readily opened to form diols (with water), aminohydrins (with amine), cyanohydrin (with HCN), N-hydroxyalkylamide (with RCONH2), among others. Some examples are shown below.
This reaction has been carried out with primary and secondary amines. For example, Biswas, et al.33 have grafted diethylamine onto epoxidized oil, using ZnCl2 as a catalyst (Scheme 6).
Liu and Erhan34 have reacted epoxidized soybean oil with triethylene tetraamine and hydrolysed the glycerides with NaOH to produce ion exchange resins. The resins have been found to remove Cu(II), Ni(II), and Co(II) ions from dilute aqueous solutions. They also utilized various polyamines as cross-linking agents in the formation of epoxidized SBO-based composites using extrusion solid freeform,35 and compression molding fabrication methods36 with various fillers, such as glass fiber, flax fiber, nanoclay and others.
4c.
Azide derivatives
Recently, an environmentally friendly water-based pathway to form the azide derivatives of soybean oil and fatty esters has been found via the reaction of SBO epoxide with sodium azide in water with only a small amount of an ionic liquid as a catalyst.37 The distribution of azide and alcohol functionalities on the fatty acid moiety is approximately random. This reaction has been applied to epoxidized methyl oleate, methyl linoleate, soybean oil, and methyl soyate. The reaction for epoxidized methyl oleate is shown in Scheme 7.
4d. Click reaction
The azide product in the previous section has been subjected to the click reaction with phenyl acetylene.38 This turns out to be a facile method to attach additional functionality onto the soybean molecule (phenyl group, in this case). The reaction is depicted in Scheme 8.
5. Formation of urethanes
One of the hot areas of research is to use vegetable oils to produce polyurethanes. In order to produce the polyurethane, hydroxyl groups need to be generated from the oils. The hydroxyl group can then react with an isocyanate to form the urethane. To form a linear polymer, a diol and a diisocyanate are needed (Scheme 9). A large number of papers has appeared. For convenience, these methods are grouped into three categories.
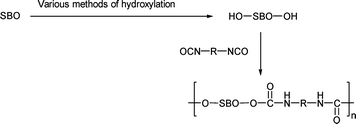 |
| Scheme 9 Formation of a diol from soybean oil (SBO) and the reaction of this diol with diisocyanate to form polyurethane. | |
5a.
Hydroxy-containing oils
Some triglyceride oils contain hydroxy groups. A good example is castor oil, which comprises ricinoleic moiety. This can be used to make polyurethanes, although the hydroxyl number is low.
5b. Reactions at the unsaturated sites
The double bonds are good sites to introduce the hydroxyl groups. There are at least four general methods to achieve this:
(i) Air oxidation, which is straightforward, but the results may be uneven. A recent example is given in Pechar et al.39
(ii) Epoxidation followed by hydroxylation in acidic solution40,41 An alternative is epoxidation followed by hydrogenation.42 Several similar studies have been made.43,44 The extent of cross-linking affects the stiffness of the polymer.
An interesting approach has been taken45 to convert the epoxide to five-membered cyclic carbonates by reacting with carbon dioxide in the presence of tetrabutylammonium bromide as catalyst at 110 °C. Reaction of the carbonate with primary amine forms a β-hydroxyurethane. Reactions with di- or tri- primary amines give polyurethane networks. The physical properties of the polymeric networks have been studied and found to correlate with type and stoichiometry of the amine used.
(iii) Hydroformylation followed by hydrogenation or reduction46,47 Typically the oil is heated with a mixture of carbon monoxide (to form the aldehyde) and hydrogen (to form the alcohol) in the presence of suitable organometallic catalysts.
(iv) Ozone cleavage of double bonds in the oil and coupling of a polyol to the cleaved ends of the molecules.48
5c. Reactions at the carboxyl ester
Again, there are multiple approaches.
(i) The most common method is to trans-esterify the triglyceride with a polyol. Examples are Shah,49 Kurth,50 and Dwan'Isa.51 A variation is to react vegetable oil with an alkene oxide.52
(ii) A slightly different process first heat-modifies the soybean oil and then uses lipase enzymatic hydrolysis to generate primary alcohols from the glycerides.53
The alcohols produced in the above methods can then be converted to polyurethanes through suitable reactions with diisocyanates (Scheme 9).
6. Biotransformation
One of the advantages of soybean oil as a feedstock is its amenability to biocatalysis. A good example was shown recently by several biotransformation reactions done on soybean oil azadicarboxylate diethyl ester.32 Three enzymatic reactions have been reported. Enzymatic hydrolysis (shown in Scheme 5) gives the free fatty acids. Enzymatic reaction with methanol generates methyl soyate with the additional azadicarboxylate ester functionality that may modify the properties of the biodiesel. Enzymatic transesterification with glycerol and poly(ethylene glycol) gives the corresponding derivatives, which may perhaps be used as surfactants. The latter two reactions are shown in Scheme 10.
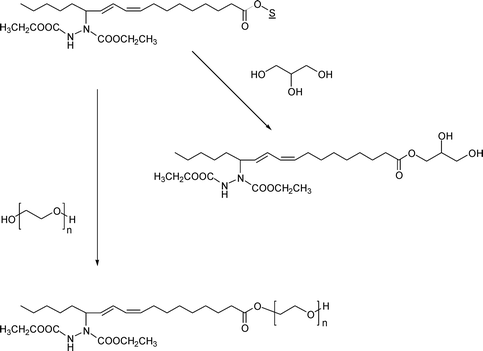 |
| Scheme 10 Enzymatic transesterification reactions of soybean oil azadicarboxylate diethyl ester with glycerol and poly(ethylene glycol). In both reactions, a lipase is used as the catalyst. ‘S’ refers to the glycerol moiety in the soybean oil. | |
7. Conclusion
A question may be asked as to how the various soy-derived chemicals may replace current petroleum-derived chemicals. This question depends very much on the price of petroleum crude ($140 per barrel as of this date) relative to vegetable oils. A simple comparison can be made with the price of soybean oil versus paraffin oil (both currently at about 70 cents per lb). If the price of paraffin oil rises faster than that of soybean oil, we may expect some applications that require paraffin oil to be partly replaced by soybean oil.
In this review a large number of soybean oil derivatives that contain nitrogen are described. It is clear that soybean oil is capable of many versatile transformations, leading to increasingly large number of reactions. Some of the resulting products are materials of commerce, or being commercialized, e.g., fatty amines, fatty amides, fatty imidazolines, and soybean oil-based urethanes. Others are still in the laboratory stages.
Despite recent research activities on vegetable oils, we are only scratching the surface of many promising synthetic approaches. For example, a major R&D thrust today is biorefining, i.e., converting starch or cellulosic materials to alcohol. If these developments prove to be viable, we can envision vegetable oils (from corn, soybean, or other crops) to increase in availability and even more competitive in price. In such a scenario, soybean oil would be a growing renewable feedstock for many more applications.
8. References
- M.-C. Kuo and T.-C. Chou, Ind. Eng. Chem. Res., 1987, 26, 277 CrossRef CAS.
- Z. S. Petrovic, A. Zlatanic, C. C. Lava and S. Sinadinovic-Fiser, Eur. J. Lipid Sci. Technol., 2002, 104, 293 CrossRef CAS.
- G. Knothe, Fuel Process. Technol., 2005, 86, 1059 CrossRef CAS.
- A. Srivastava and R. Prasad, Renewable Sustainable Energy Rev., 2000, 4, 111 CrossRef CAS.
- H. Baumann et al., Angew. Chem,, Int. Ed. Engl., 1988, 27, 41–62 CrossRef.
- U. Biermann et al., Angew. Chem., Int. Ed., 2000, 39, 2206 CrossRef CAS.
- V. Sharma and P. P. Kundu, Prog. Polym. Sci., 2006, 31, 983 CrossRef CAS.
- J. O. Metzger and U. Bornscheuer, Appl. Microbiol. Biotechnol., 2006, 71(1), 13–22.
- J. A. Zerkowski and D. K. Y. Solaiman, J. Am. Oil Chem. Soc., 2006, 83(7), 621–628.
- S. Billenstein and G. Blaschke, J. Am. Oil Chem. Soc., 1984, 61, 350 CrossRef.
-
H. Rutzen. US Patent, 3
579
585, 1968 Search PubMed.
-
S. Billenstein, B. Kukla and H. Stuehler, US Patent, 4
234
509, 1980 Search PubMed.
-
P. H. Moss, E. L. Yeakey and G. P. Speranza, Br. Patent, 1
074
,603, 1967 Search PubMed.
-
J. Murphy, Additives for Plastics Handbook, Elsevier, Oxford, UK, 2nd edn, 2001 Search PubMed.
-
Defoaming: Theory and Industrial Applications, ed. P. R. Garrett, Marcel Dekker, New York, 1993 Search PubMed.
- S. H. Feairheller, R. G. Bistline Jr, A. Bilyk, R. L. Dudley, M. F. Kozempel and M. J. Haas, J. Am. Oil Chem. Soc., 1994, 71(8), 863–866.
- L. I. Kopylov, Y. N. Shekhter, A. A. Gureev and M. B. Bakaleinikov, Chem. Technol. Fuels Oils, 1980, 16(1–2), 62–64.
- A. J. Maltby and M. Read, Antistatic agents – The effectiveness of ethoxylated fatty acid amides in reducing the static charge decay time of LDPE film as compared with commercially available materials, TAPPI – Polymers, Laminations and Coatings Conference, 2000, pp. 1103–1114.
-
M. J. Kelley and E. A. Robinson US Patent 2,340,881 ( 1944).
-
J. E. Perella, J. A. Komor and R. D. Katstra, U.S. Patent, 6
369
997, 2002 Search PubMed.
-
J. E. Perella, J. A. Komor and R. D. Katstra, U.S. Patent, 6
004
914, 1999 Search PubMed.
- X. Chen, H. Zhong, L. Jia, J. Ling, R. Tang, J. Qiao and Z. Zhang, J. Appl. Polym. Sci., 2001, 81(11), 2696–2701.
- X. D. Fan, Y. Deng, J. Waterhouse and P. Pfromm, J. Appl. Polym. Sci., 1998, 68(2), 305–314.
- V. Kale, H. S. Vedanayagam, R. Subbarao and M. B. Rao, J. Appl. Polym. Sci., 1994, 53(6), 807–814.
- E. C. Leonard, in Fatty Acids, ed. E. H. Pryde, AOCS Press, Champaign, IL, 1980.
- D. Bajpai and V. K. Tyagi, J. Oleo Sci., 2006, 55, 319–329 Search PubMed.
- M. H. Mason, Diss. Abstr. Int. B, 2001, 61(8), 4162 Search PubMed , University of Kansas, Lawrence, KS, 2000, 181 pp.
- G. J. Suppes and M. A. Dasari, Ind. Eng. Chem. Res., 2003, 42, 5042–5053 CrossRef.
- A. Biswas, B. K. Sharma, J. L. Willett, K. Vermillion, S. Z. Erhan and H. N. Cheng, Green Chem., 2007, 9, 85 RSC.
- A. Biswas, B. K. Sharma, J. L. Willett, S. Z. Erhan and H. N. Cheng, Green Chem., 2008, 10, 298 Search PubMed.
- A. Biswas, R. L. Shogren, J. L. Willett, S. Z. Erhan and H. N. Cheng, ACS Polym. Prepr., 2006, 47(2), 259 CAS.
- A. Biswas, R. L. Shogren, J. L. Willett, S. Z. Erhan and H. N. Cheng, ACS Symp. Ser., 2008, 999, 76 CAS.
- A. Biswas, A. Adhvaryu, S. H. Gordon, S. Z. Erhan and J. L. Willett, J. Agric. Food Chem., 2005, 53, 9485 CrossRef CAS.
- Z. S. Liu and S. Z. Erhan, J. Appl. Polym. Sci., 2002, 84, 2386–2396 CrossRef CAS.
- Z. S.Liu and S. Z. Erhan, Development of soy composites by direct deposition, in Industrial Uses of Vegetable Oils, ed. S. Z. Erhan, AOCS Press, Champaign, IL, 2005, pp. 131–142.
- Z. Liu, S. Z. Erhan, D. E. Akin and F. E. Barton, J. Agric. Food Chem., 2006, 54(6), 2134–2137.
- A. Biswas, B. K. Sharma, J. L. Willett, S. Z. Erhan and H. N. Cheng, J. Agric. Food Chem., 2008, 56, 5611 CrossRef CAS.
-
A. Biswas; B. K. Sharma; J. L. Willett; S. Z. Erhan; H. N. Cheng, 2008, manuscript in preparation.
- T. W. Pechar, S. Sohn., G. L. Wilkes, S. Ghosh, C. E. Frazier, A. Fornof and T. E. Long, J. Appl. Polym. Sci., 2006, 101, 1432–1443 CrossRef CAS.
-
H. Kluth; A. Meffert,US Patent, 4
508
853, 1985 Search PubMed.
-
Z. S. Petrovic, I. Javni, A. Guo and W. Zhang, US Patent, 6
433
121, 2002 Search PubMed.
- Z. S. Petrovic, L. Yang, A. Zlatanic, W. Zhang and I. Javni, J. Appl. Polym. Sci., 2007, 105, 2717–2727 CrossRef CAS.
- J. Djonlagic and Z. S. Petrovic, J. Polym. Sci., Part B: Polym. Phys., 2004, 42(21), 3987–3999.
- A. Guo, W. Zhang and Z. S. Petrovic, J. Mater. Sci., 2006, 41(15), 4914–4920.
- B. Tamami, S. Sohn and G. L. Wilkes, J. Appl. Polym. Sci., 2004, 92, 883 CrossRef CAS.
-
D. A. Babb, A. K. Schrock, Z. Lysenko and A. Larre, The Dow Chemical Company starts industrial production of natural oil-based polyols for polyurethanes, 11th Annual Green Chemistry and Engineering Conference, ACS, Washington, DC, June 26–29, 2007 Search PubMed.
-
Z. S. Petrovic, I. Javni, A. Zlatanic and A. Guo, US Patent Application, 20060041157, 2/23/2006 Search PubMed.
-
R. Narayan, D. Graiver, K. W. Farminer and P. T. Tran, US Patent Application, 20060194974, 8/31/2006 Search PubMed.
- A. Shah and T. Shah, WO 2001/04225, 1/18/2001.
-
T. M. Kurth, R. A. Kurth, R. B. Turner, L. P. Kreifels and T. A. Van Thomme, US Patent Application, 20020058774, 5/16/2002 Search PubMed.
-
J.-P. L. Dwan'Isa, L. T. Drzal, A. K. Mohanty and M. Misra, US Patent, 7
125
950, 10/24/2006 Search PubMed.
-
T. M. Kurth, R. A. Kurth, R. B. Turner and L. P. Kreifels, US Patent Application, 20030191274, 10/9/2003 Search PubMed.
- P.-P. Kiatsimkul, G. J. Suppes and W. R. Sutterlin, Industrial Crops and Products, 2007, 25, 202–209 Search PubMed.
Footnote |
† Names are necessary to report factually on available data; however, the USDA neither guarantees nor warrants the standard of the product, and the use of the name by USDA implies no approval of the product to the exclusion of others that may also be suitable. |
|
This journal is © The Royal Society of Chemistry 2008 |
Click here to see how this site uses Cookies. View our privacy policy here.