DOI:
10.1039/B411357H
(Paper)
Green Chem., 2005,
7, 15-19
Industrial application of ionic liquids as performance additives†
Received
23rd July 2004
, Accepted 24th September 2004
First published on 25th November 2004
Abstract
Over the last decade ionic liquids have achieved much attention and are not any longer just a class of esoteric compounds, but are proving to be valuable and useful in a multitude of different applications. So far, ionic liquids have mainly been considered to be an alternative to conventional solvents in reaction and separation processes. Hence, it is not surprising that most of the recent publications report on the use of ionic liquids as a solvent for chemical and biochemical syntheses. This may be rationalized by the possibility of carrying out biphasic reactions for the separation and recovery of otherwise homogenous precious metal catalysts or enzymes, as ionic liquids form two phases with many organic product mixtures. In contrast, the use of ionic liquids as performance additives or as reactive component in the preparation of oligomers or pre-polymers has gained far less attention. The authors believe that due to their unique properties ionic liquids have a great potential to be used as performance additives in many materials and applications. The application of ionic liquids is in accordance with the chemical industry's guidelines and principles concerning the initiatives “sustainable development” and “responsible care”. The authors demonstrate this by provision of an example taken from Degussa's ongoing ionic liquids research program: The use of ionic liquids as secondary dispersant in universal pigment pastes, i.e. in the white base paint to be tinted.
Bernd Weyershausen | Bernd Weyershausen studied chemistry and biology at the University of Bonn, Germany. After completion of his diploma thesis at the University of Oviedo, Spain, he earned his doctorate at the University of Bonn in 1998. Supported by a grant of the Alexander von Humboldt Foundation he then worked for one and a half years at The Scripps Research Institute in La Jolla, United States, in the area of the total synthesis of natural products. In 2000 he started his industrial career as a group leader in the R&D department of Degussa’s Oligomers & Silicones Business Unit where in 2003 he became head of the section “Silicone Technology” directing about half of the Oligomers & Silicones Business Unit’s research capacities. As of January 2005 Bernd Weyershausen will assume responsibilities for Strategic Marketing and New Business Development in Degussa’s Industrial Specialties Business Line. |
Kathrin Lehmann | Kathrin Lehmann, born in 1967, studied chemistry at the Humboldt University in Berlin. After working five years for a pigment supplier with responsibility for the technical service activities for coatings she joined Tego Chemie Service in October 1999. She is in charge of novel developments of dispersants as well as substrate wetting and thickening agents in the development department of Degussa’s business line with the brand Tego. |
Introduction
Recently, ionic liquids have been extensively evaluated as environmentally friendly or “green” alternatives1 to conventional organic solvents for a broad range of organic synthetic applications.2 In addition, ionic liquids have been used e.g. as catalysts3 in organic synthesis, in compositions for stabilizing and/or isolating nucleic acids in or from micro-organisms,4 as process aids for the synthesis of polynucleotides,5 as lubricants6 and for the preparation and stabilization of nanoparticles.7 Furthermore, after the announcement of the first industrial process involving ionic liquids by BASF (BASIL8 process) in 2003 the potential of ionic liquids for new chemical processes and technologies is beginning to be recognized.
So far, academic and industrial research have paid very little attention to the use of ionic liquids as performance additives or as reactive component in the preparation of oligomers or pre-polymers.9 Only very few publications, mainly from academic sources, can be found in the literature reporting on the use of ionic liquids as e.g. plasticizers for polymers such as polyamides,10 PVC11 and PMMA.12 Some patent applications teach the use of ionic liquids in surface and air treating compositions for household and automobile applications,13 in ink composition14 and as an antistatic agent.15 A reason for this might be the high price of imidazolium-based ionic liquids compared to those prices of other solvents or additives. Another drawback of imidazolium-based ionic liquids is their listing status. Most of the imidazolium-based ionic liquids are not listed in EINECS (European Inventory of Existing Commercial Substances) or TSCA (Toxic Substances Control Act) which means that in order to be legally allowed to produce and use them in technical quantities they have to be toxilogically evaluated and registered. This would not only consume a significant amount of time but also financial resources depending on the quanitity to be dealt with, and the outcome would be an uncertain one. On the other hand, a whole range of already listed and toxicologically evaluated ionic liquids exists, but surprisingly has not achieved much attention until today. Therefore, we would like to draw the ionic liquids community's attention to these non-imidazolium-based ionic liquids which are readily available in technical quantities for reasonable prices and hence, represent an interesting alternative to the much more expensive and often not yet listed imidazolium-based ionic liquids. For the purpose (context) of this article we would like to refer to imidazolium-based ionic liquids as conventional and to non-imidazolium-based ionic liquids as unconventional ionic liquids. Many acyclic ammonium salts and quaternized heterocyclic compounds such as imidazolinium or oxazolinium salts satisfy the well accepted definition for ionic liquids which is a melting point below 100 °C or even below room temperature (RTILs). Thus, these salts can be regarded as unconventional ionic liquids. Whereas great attention has been paid to conventional ionic liquids, less research effort has focused on unconventional ionic liquids.16 Some of the unconventional ionic liquids we evaluated towards their use as performance additives during the course of our investigations are depicted in Fig. 1.
We believe that due to their unique properties ionic liquids and particularly unconventional ionic liquids have a great potential to be used in the sense of a performance additive. Unconventional ionic liquids are readily available and should find use not only as plasticizers for plastics, but also as additives in the area of coatings, lacquers and inks. Herein, we report on the first industrial application of ionic liquids as performance additives. Ionic liquids were incorporated either as secondary dispersant in universal pigment pastes or in the white base paints to be tinted.
Dispersants
It is common practice to use dispersing agents in order to homogeneously stabilize fillers and pigments in liquid media and to obtain storage stable pigment pastes, paints and lacquers. According to the state of the art, dispersing agents have to fulfill the following requirements:
• Easy incorporation of fillers and pigments leading to shorter dispersing times, respectively allowing for the use of simpler and cheaper dispersing aggregates (dissolver instead of ball mills).
• Reduction of the pigment paste viscosity allowing for high pigment loading and economical tinting systems.
• Development of optimal color strength, i.e. of the optimal hiding power when using opaque pigments.
• Avoidance of sedimentation in pigment pastes when stored over long periods of time or under extreme climatic conditions.
• Avoidance of flocculation for good reproducability of colors which is becoming particularly important when using mixing machines for the tinting of white base paints and lacquers.
The above listed requirements have to be independently fulfilled regardless of the liquid medium into which a filler or a pigment has to be dispersed. Hence, there has been no lack of attempts to develop polymeric dispersants17 with a truely universal applicability. Additionally, a good dispersant wets and stabilizes not only inorganic but also organic pigments exhibiting both hydrophilic and hydrophobic surfaces. Most modern polymeric dispersants are universal concerning the pigments but not with respect to the surrounding medium. Generally, a pigment in a solvent-based liquid medium (hydrophobic) is only sterically stabilized whereas a pigment in a water-based medium (hydrophilic) can be both sterically and electronically stabilized depending on the presence of appropriate functional groups in the polymeric dispersant (electro-steric stabilization). Naturally, steric stabilization is only possible when the pigment stabilizing functionalities, i.e. parts of a dispersant (e.g. side chains in comb-like structures or certain blocks in linear block co-polymeric dispersants) are fully compatible with the surrounding medium. Obviously, the broad range of technical requirements and the diversity of pigments and surrounding media make it extremely difficult to realize a truely universal dispersing agent.
Results and discussion
Accordingly, it is state of the art to have on the one hand dispersants which are optimized for water-based and on the other hand those dispersants that are designed for solvent-based coatings resulting in different tinting paste systems. The handling of different tinting systems in mixing machines requires a lot of time, money and cleaning operations for the manufacture of such pigment pastes. Moreover, the users of those pastes, e.g. building centers and do-it-yourself stores, need space for several tinting machines, as for each tinting, the mixing machine will handle only one specific type of pigment paste. Apparently, there is a high potential of saving costs and logistic efforts if truely universal dispersants were available to the market allowing for the stabilization of any pigment in water-based pastes and then using these water-based pastes for water- and solvent-based coatings. Without doubt there have been numerous efforts to develop so-called universal dispersants for the decorative industry during the past few years. Typical structures discussed in that context are alkyl phenol ethoxylates (APE),18 oleo block ABC derivatives19 or styrene oxide based polyether structures.20 However, in Europe the use of APEs is restricted in a variety of applications and will have to be completely ceased in the near future in the coating industry. The degradation process of APEs leads to phenolic species (intermediates) with high fish toxicity.21 Furthermore, it is assumed that APEs interfere with the human hormone cycle as endocrine disrupters. Recently, Degussa has developed a novel class of unique styrene oxide-based phosphorylated polyethers20
(illustrated in Fig. 2) and their corresponding anionic species as an environmental-friendly and promising alternative to alkyl phenol ethoxylates.
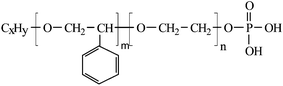 |
| Fig. 2 Phosphoric acid ester of a styrene oxide-based polyether. | |
These novel primary dispersants will expand the prevelance of water-based, i.e. universal pigment pastes. In doing so this will lead to a reduction of the consumption of VOCs, as improved universal pigment pastes are expected to successively replace solvent-based pigment pastes. Furthermore, since in the course of their degradation such styrene oxide-based phosphorylated polyethers do not lead to any kind of phenolic intermediates, their development can be seen as a contribution to the “responsible care” initiative. However, undoubtedly there is still room for improvement as shown in Table 1. Particularly, in the area of solvent-based coating systems and the search for better pigment pastes, i.e. better and more universal dispersants will continue.
Table 1 Suitability of different pigment paste systems in several coating systems
Pigment paste |
Coating system |
Water-based systems |
Typical solvent-based systems |
Special solvent-based systems (e.g. Pliolite®) |
Water-based |
✓ |
— |
— |
Solvent-based |
— |
✓ |
✓ |
Universal colorant |
✓ |
✓ |
× |
It is common practice to use modern water-based universal pigment pastes (also called colorants) to tint every kind of water-based coating or laquer, e.g. flat and high gloss acrylics, PVAc-based paints or alkyd emulsion-based systems, as well as typical solvent-based coating systems such as air-drying enamels based on conventional alkyds solubilized in white spirit or solvent-based polyurethane modified alkyds. However, using the same universal colorant in special solvent-based systems, e.g. high solid isoparaffin-based alkyds or so-called Pliolite® systems does not yield the desired result (see the “×” in Table 1). The phenomenon is illustrated in Fig. 3: A red, a purple and a blue universal colorant were used to tint a Pliolite® coating system. A significant color difference is observed when comparing the left top quadrants (I) of the draw downs with the left bottom quadrants (II). This difference is referred to as rub-out value ΔE.‡ Therefore, one could question the general validity of the term “universal” pigment paste.
 |
| Fig. 3 Draw downs of Pliolite® tinted with universal colorants based on Tego® Dispers 651 adjusted with ionic liquid Tego® Dispers 662C. | |
Even additional quantities of the universal colorant do not improve the result in terms of reduced brightness values§
(the lower L* the more effective is the colorant) and reduced ΔE values (the lower ΔE the better the pigment is stabilized against flocculation); see Table 2. The reason behind this is the inability of the dispersant used in the universal colorant to still stabilize the pigment when mixed with the isoparaffin-based alkyd or so-called Pliolite® system. Now, comparison of the right top quadrants (III) of the draw downs with the right bottom quadrants (IV) clearly demonstrates that this problem can be overcome by using unconventional ionic liquids as secondary dispersing agents. In all three cases (red, purple and blue universal colorant) the rub-out value ΔE is almost negligable. The use of ionic liquids indisputably enables universal colorants to be applicable in a truely universal way. Moreover, the combination of ionic liquids and ecofriendly universal dispersants does not only allow for previously unknown dimensions of the applicability of universal pigment pastes but also allows e.g. building centers and do-it-yourself stores to realize a improved profitability due to a reduced complexity of the required logistics to offer a large variety of differently colored paints and lacquers.
Table 2 Results obtained by using ionic liquids in mixtures made from Pliolite® and universal colorants
Ionic liquid |
Bayferrox®120 M |
Cromophtal® Violett GA |
|
L* |
ΔE |
L* |
ΔE |
[MMIM][MeSO4]
= 1,3-dimethylimidazolium methylsulfate.
|
without IL |
76.15 |
27.67 |
71.16 |
33.73 |
Tego® IL T16ES |
73.05 |
21.99 |
70.10 |
25.83 |
Tego® IL K5MS |
72.07 |
21.91 |
68.16 |
24.86 |
Tego® IL P9 |
64.70 |
12.49 |
69.24 |
29.14 |
[MMIM][MeSO4]a |
67.74 |
16.47 |
64.02 |
20.26 |
Tego® Dispers 662 C |
60.01 |
3.30 |
54.00 |
5.93 |
Experimental
Typically, the tinting of a white base paint is carried out using the following procedure. 20 parts of a white base paint are mixed with (a) 1.0 part of an inorganic pigment paste which contains e.g. 60% of iron oxide red (Bayferrox® 120 M) or (b) 0.5 parts of an organic pigment paste, which contains between 20–40% of dioxazine (Cromophtal® Violett GA) or phthalocyanine blue (Heliogenblue® L 7101 F).
Besides water, the pigment and the dispersant pigment pastes usually contain wetting additives, defoamers and preservatives.
After handmixing the colorant should develop the full color strength in the coating. The development of the full color strenght is indicated by a low L* value (brightness) and a low ΔE value. The results presented in Table 2 were obtained using a Pliolite® system (special solvent-based coatings particularly used in the South of Europe and in the UK) and universal pigment pastes based on the unique dispersant technology of Degussa (vide supra; Tego® Dispers 650 and Tego® Dispers 651).
Without the addition of an ionic liquid to the mixture of the Pliolite® coating system and one of the three colorants the development of the color strength is miserable and poor. We used four different commercially available unconventional ionic liquids and one conventional ionic liquid (dimethylimidazolium methyl sulfate) to evaluate their impact on the development of the color strength. It turned out that the addition of only 0.4–2% of an ionic liquid to these mixtures significantly improved the color strength. Particularly, when Tego® Dispers 662C was used, the rub-out value ΔE came close to zero. The higher the rub-out value ΔE the more color pigment has flocculated. Contrary to primary dispersing agents these ionic liquids are secondary dispersing agents. Therefore, they do not have to be used essentially during the grinding of the pigment but can be used at any step during pigment paste manufacture.
Ionic liquids provide the user and the manufacturer of commercial pigment pastes with a higher flexibility regarding the optimization of their products, as ionic liquids can be used according to one of the three following procedures in order to enhance the applicability of universal pigment pastes, respectively to improve the color strength of the final paints, coatings and lacquers:
(A) White base paint + pigment paste based on universal dispersing agent + ionic liquid as third component (so-called post addition),
(B) White base paint already containing an ionic liquid to have the highest flexibility concerning the use of different pastes based on a variety of primary dispersant technologies,
(C) White base paint + pigment paste which contains both the primary dispersant and the ionic liquid to make the colorant universal not only in the old-fashioned way but also in terms of critical solvent-based systems such as Pliolites® or isoparaffin-based alkyds.
It is noteworthy that the efficacy of procedure (A) is higher compared to (C), but requires higher quantities of the ionic liquid.
Conclusion
The combination of ionic liquids and universal ecofriendly primary dispersants is able to overcome severe problems relating to the use of colorants in problematic solvent-based coatings (e.g. Pliolites®). Specifically, unconventional ionic liquids provide a cost-wise attractive solution to the paint and coating industry for the tinting of such problematic solvent-based paints and coatings. Furthermore, the combination of ionic liquids and state of the art primary dispersants enables customers of pastes and manufacturers of those to reduce complexity of logistics during storage and manufacture. In summary, we have demonstrated that unconventional ionic liquids can be used in the sense of performance additives, and we believe that due to their unique properties and their broad applicability they will play a major role in the formulation of coating systems in the near future.
Summary
With this article we would like to change the perception that ionic liquids are mainly (only) environmentally friendly or “green” alternatives to conventional organic solvents. In fact, the application potential of ionic liquids is much broader than presumed. Of course, they can be used as an alternative to conventional organic solvents, but they also can be employed as process aids (e.g. in the immobilization22 of otherwise homogeneous catalysts). Sometimes it is not even necessary to use an ionic liquid in order to improve a chemical process, but one can take advantage of the formation of an ionic liquid during the process (e.g. BASIL8 process). Another possibility to benefit from the unique properties of ionic liquids is their application as performance additives. In this context, non-imidazolium-based (unconventional) ionic liquids should be of particular interest due to their availability in technical quantities and lower costs compared to their imidazolium-based counterparts. In this article we have shown that ionic liquids can significantly contribute to the chemical industry's initiatives “sustainable development” and “responsible care” when used as performance additives. To the best of our knowledge the use of ionic liquids as secondary dispersant is the first example of an industrial application of ionic liquids as performance additives. State of the art universal pigment pastes, which previously could not be used for the tinting of problematic solvent-based coatings and paints, now become applicable to all kinds of coatings and paints by employing ionic liquids. Due to the synergistic effect between ionic liquids and ecofriendly primary dispersants (e.g. styrene oxide-based phosphorylated polyethers20) the application and utilization of the latter will experience further promotion. Moreover, as in the past problematic solvent-based coatings and paints had to be tinted with solvent-based pigment pastes, the use of ionic liquids in combination with water-based, universal pigment pastes will help to reduce the consumption of VOCs in the future.
Acknowledgements
The authors would like to thank Kerstin Hell, Angela Rüttgerodt, Andreas Stüttgen and Stefan Silber for their assistance and support.
References
- R. D. Rogers and K. R. Seddon, Science, 2003, 302, 792 CrossRef.
-
P. Wasserscheid and T. Welton, Ionic Liquids in Synthesis, VCH, Weinheim, 2002 Search PubMed;
R. D. Rogers, K. R. Seddon and S. Volkov, Green Industrial Applications of Ionic Liquids, NATO Science Series II. Mathematics, Physics and Chemistry, Kluwer, Dordrecht, 2003, vol. 92 Search PubMed;
R. D. Rogers and K. R. Seddon, Ionic Liquids: Industrial Applications to Green Chemistry, ACS Symposium Series 818, ACS, Washington DC, 2002 Search PubMed.
-
H. J. Laas, R. Halpaap, F. Richter and J. Köcher, Ionic liquids (as catalysts for the oligomerization of isocyanates), Germ. Pat. Appl., DE 102 19 227, 30.4.2002, Bayer AG Search PubMed.
-
U. Oelmüller and T. Wille, Use of compositions consisting of cationic compounds and proton donors for stabilizing and/or isolating nucleic acids in or from micro-organisms such as prokaryots, fungi, protozoa or algae, PCT. Pat. Appl., WO 02/00600, 20.6.2001, Quiagen GmbH Search PubMed.
-
J. Myerson, M. G. M. Perobost, D. J. Dellinger and G. F. Dellinger, Method of synthesizing polynucleotides using ionic liquids, US Pat. Appl., US 03/0083489, 31.10.2001, Agilsent Technologies, Inc.. Search PubMed.
- R. A. Reich, P. A. Stewart, J. Bohaychick and J. A. Urbanski, Lubr. Eng., 2003, 59, 16 CAS; W. Liu, C. Ye, Q. Gong, H. Wang and P. Wang, Tribol. Lett., 2002, 13, 81 CrossRef CAS; C. Ye, W. Liu, Y. Chen and L. Yu, Chem. Commun., 2001, 21, 2245 Search PubMed.
- Y. Zhou and M. Antonietti, J. Am. Chem. Soc., 2003, 125, 14960 CrossRef CAS; V. Calo, A. Nacci, A. Monopoli, S. Laera and N. Cioffi, J. Org. Chem., 2003, 68, 2929 CrossRef CAS; J. Dupont, G. S. Fonseca, A. P. Umpierre, P. F. P. Fichtner and S. R. Teixeira, J. Am. Chem. Soc., 2002, 124, 4228 CrossRef CAS; G. S. Fonseca, A. P. Umpierre, P. F. P. Fichtner, S. R. Teixeira and J. Dupont, Chemistry, 2003, 9, 3263 Search PubMed.
-
M. Volland, V. Seitz, M. Maase, M. Flores, R. Papp, K. Massonne, V. Stegmann, K. Halbritter, R. Noe, M. Bartsch, W. Siegel, M. Becker and O. Huttenloch, Method for the separation of acids from chemical reaction mixtures by means of ionic fluids, PCT Int. Appl., WO03/06225, 31.7.2003, BASF AG Search PubMed; M. Huttenloch, Chem. Eng. News, 2003, 81, 9 Search PubMed.
- M. Freemantle, Chem. Eng. News, 2004, 82(18), 26.
-
F. G. Schmidt, F. M. Petrat, A. Pawlik, H. Haeger and B. Weyershausen, Polymeric compositions containing ionic liquids as plasticizers, PCT Int. Appl., WO04/005391, 15.1.2004, Creavis GmbH Search PubMed.
- M. Rahman and C. S. Brazel, Polym. Prepr. (Am. Chem. Soc.), 2004, 45(1), 301 CAS.
- M. P. Scott, M. Rahman and C. S. Brazel, Eur. Polym. J., 2003, 39(10), 1947 CrossRef CAS; M. P. Scott, C. S. Brazel, M. G. Benton, J. W. Mays, J. D. Holbrey and R. D. Rogers, Chem. Commun., 2002, 13, 1370 RSC; M. P. Scott, M. G. Benton, M. Rahman and C. S. Brazel, ACS Symp. Ser. (Ionic Liquids as Green Solvents), 2003, 856, 468 Search PubMed.
-
K. N. Price, R. T. Hartshorn, R. H. Rohrbaugh, W. M. Scheper, M. S. Showell, K. H. Baker, M. R. Sivik, J. J. Scheibel, R. R. Gardner, P. K. Reddy, J. D. Aiken III. and M. C. Addison, Ionic liquid based products and method of using the same, PCT Int. Appl., WO04/003120, 8.1.2004, The Procter & Gamble Company Search PubMed.
-
W. M. Schwarz, Ink Compositions Containing Ionic Liquid Solvents, US Pat. Appl., US6048388, 11.4.2000 Search PubMed.
-
S. Mori, K. Ida, T. Sato and A. Yonei, Polymer Compound Composite Material and its Production, JP10265674, 6.10.1998., Mitsubishi Chem. Corp Search PubMed.
- M. Freemantle, Chem. Eng. News, 2004, 82(11), 10.
-
S. Kirchmeyer, K. König, J. Mazanek and O. Wilmes, Polyaddition products for dispersing pigments in water-based paint, Eur. Pat. Appl., EP0731148, 11.9.1996, Bayer AG Search PubMed;
G. Merten, J. Zöller and E. Urbano, Hydrophilic polyurethane-polyureas and their use as a dispersant for synthetic resins, Germ. Pat. Appl., DE4416336, Hoechst AG Search PubMed;
H. L. Jakubauskas, Acrylic polymer dispersant for aqueous acrylic coating compositions, US Pat. Appl., US3980602, 14.9.1976, Du Pont Search PubMed;
I.-C. Chu, M. Fryd and L. E. Lynch, Aqueous graft copolymer pigment dispersants, PCT Pat. Appl., WO94/21701, 29.9.1994, Du Pont Search PubMed;
G. H. Denker, D. A. Pons and H. J. Wilhelmus, Water-soluble and air-drying resin, PCT Pat. Appl., WO94/18260, 18.8.1994, DSM Search PubMed;
P. H. Quednau and W. A. Wulff, Dispersant, Eur. Pat., EP0311157, 12.04.1989, assigned to EFKA Chemicals Search PubMed.
- J. Bielemann, Polymers Paint Colour Journal, 1995, 7, 21 Search PubMed;
P. H. Quednau and P. Dijkstra, Nonylphenol ethoxylate-free wetting agents and dispersants. An environmentally friendly product group with improved performance, at the 3rd Advances in Coatings Technology Conference, 20–23.10.1998, Katowice Search PubMed.
- J. Schmitz, H. Frommelius, U. Pegelow, H.-G. Schulte and R. Hofer, Prog. Org. Coat., 1999, 35(1–4), 191 CrossRef CAS.
- K. Lehmann and A. Stuettgen, Farbe + Lack, 2002, 108(3), 56–58 Search PubMed.
- P. Schoeberl, K. J. Bock, M. Huber and K. Huber, Tensides Surfactants Deterg., 1988, 25(2), 86 Search PubMed; K. Fent, Texte - Umweltbundesamt, 1996, 3, 69 Search PubMed.
-
P. Wasserscheid, Transition Metal Catalysis in Ionic Liquids in Ionic Liquids in Synthesis, ed. P. Wasserscheid and T. Welton, VCH, Weinheim, 2002, p. 213 Search PubMed; G. W. Parshall, J. Am. Chem. Soc., 1972, 94, 8716 Search PubMed; J. S. Wilkes and M. J. Zaworotko, J. Chem. Soc., Chem. Commun., 1992, 965 CrossRef CAS; P. A. Z. Suarez, J. E. L. Dullius, S. Einloft and R. F. de Souza, Polyhedron, 1996, 15, 1217 RSC; Y. Chauvin, L. Mußmann and H. Olivier, Angew. Chem. Int. Ed., 1995, 34, 1149 CrossRef CAS;
J. H. Davis, Synthesis of Task-specific Ionic Liquids, in Ionic Liquids in Synthesis, ed. P. Wasserscheid and T. Welton, VCH, Weinheim, 2002, p. 33 CAS;
K. Hell, U. Hesse and B. Weyershausen, Production of organo-polysiloxanes using ionic liquids, Eur. Pat. Appl., EP1382630, 21.1.2004, Goldschmidt AG CAS.
Footnotes |
† This work was presented at the Green Solvents for Synthesis Meeting, held in Bruchsal, Germany, 3–6 October 2004. |
‡ Rub-out test: The so-called rub-out test is performed in order to check whether or not a pigment is still well dispersed in the applied coating. For this purpose a portion of the applied coating, which still has to be partly wet, is rubbed with a finger. In the case of a poorly dispersed or even flocculated pigment the mechanical process of rubbing will lead to a homogenous dispersion again. In doing so the desired color strength of the homogeneous mixture is then developed. The color change, respectively the color difference (rub-out value ΔE) between the rubbed and unrubbed part of the coating, is a measure for the performance of the dispersant. |
§ Measuring colorimetric values (L*
= brightness): Paper board cards (Lineta® cards) were coated with the tinted (pigmented) paints and coatings. The colors were measured by means of a chromatometer (Type X-Rite, SP 62-162 with a D65/10 illuminant, Company X-Rite) and quantified using CIE (Commisson on Illumination) L*a*b*-color system scale (L*
= brightness, a* denotes the red/green value with a color measurement movement in the +a direction depicting a shift toward red, and b* denoting the yellow/blue value with a color measurement movement in the +b direction depicting a shift towards yellow). For clarity reasons the a* and b* values are omitted in Table 2. |
|
This journal is © The Royal Society of Chemistry 2005 |
Click here to see how this site uses Cookies. View our privacy policy here.