DOI:
10.1039/B108249C
(Paper)
Analyst, 2002,
127, 169-173
Comparison of sampling methods for 1,6-hexamethylene diisocyanate, (HDI) in a commercial spray box
Received 11th September 2001, Accepted 22nd October 2001
First published on 6th December 2001
Abstract
In this study three different types of samplers for the determination of 1,6-hexamethylene diisocyanate in air were compared. The experimental set up was a simulation of real life conditions with spray painting operations performed inside a commercial, full sized, spray box. The sampling methods were 1-(2-methoxyphenyl)-piperazine impregnated on glass fibre filter, and the same reagent in impinger, and also dibutylamine in impinger. All analyses were performed by LC-MS-MS. The determined concentrations varied between 20 and 90 μg m−3 with relative standard deviations from 7 to 17% for each method. No significant difference was found between the three methods using ANOVA with a significance level of α = 0.05.
Introduction
Diisocyanates are widely used in the manufacture of different polyurethane (PUR) products such as flexible and rigid foams, paints and glues. The annual world production of PUR products in 1993 was estimated at 6.1 million tons.1 For production of PUR products, diisocyanates and its larger oligomers and prepolymers are used. The aliphatic 1,6-hexamethylene diisocyanate (HDI) is frequently used in automotive painting and finishing of other surfaces that are exposed to sunlight. Occupational exposure may occur through skin contact but primarily through inhalation of the vapour or aerosol. Isocyanates are irritants to eyes and respiratory tracts and may also, after sensitisation, cause asthma.1 The Swedish threshold limit value for isocyanate exposure is 5 ppb for 8 h exposure, and 10 ppb for a 5 min short-term exposure.2Determination in air is complicated since isocyanates may exist as vapour or in an aerosol. Also, isocyanates aside from being monomers, may also exist as a dimers, trimers or as prepolymers. The curing reaction is stopped during the sampling or directly after sampling by dissolving the aerosol droplets in a reagent solution. Different derivatising reagents have been used for the air sampling of isocyanates, e.g. 1-(2-methoxyphenyl)-piperazine (2MP), 1-(2-pyridyl)-piperazine (2PP), 1-(9-anthracenylmethyl)-piperazine (MAP), 9-(methylaminomethyl) anthracene (MAMA), dibutylamine (DBA) and tryptamine (TRYP).3–8 These reagents have been used in solutions in impinger flasks or coated on filters. The formed derivatives have been analysed mainly by HPLC with UV-detection and sometimes in combination with fluorescence or electrochemical detection, or with mass spectrometric detection. Mass spectrometry (MS), with its property
to selectively monitor certain ions, is suitable for the quantification of isocyanates in complex field samples. The total isocyanate content could be measured by using a reagent that for each isocyanate group, regardless of origin, results in one discrete analyte. This kind of approach is under development.9
For occupational health measurements it is desirable to have methods that are as user-friendly as possible. This applies both for the occupational hygienist as well as for the worker wearing the equipment. Impingers are not user-friendly, however as aerosol droplets are dissolved in reagent solution an impinger is better suited than impregnated filters to derivatise isocyanate groups in aerosols during sampling.10,11 The most common impinger solvent is toluene. Due to its volatile properties, however, it is difficult to use it with the appropriate flow (2 l min−1) that gives the ideal impacting effect. It has been shown that submicron particles will not be collected in a commonly used impinger when the flow while using toluene is set to 1 l min−1.12 By attaching a filter downstream this modified impinger method can collect these submicron particles.13
The filter methods are user-friendlier but losses of isocyanates can occur due to continued curing in aerosol droplets caught on the filter. Putting the filter into a reagent solution directly after the measurement reduces this effect.14
To assess the performance of a measurement method it is essential to use field trials as a part of the test program. Some studies on comparison of isocyanate measurement methods have been performed with paired sampling, either stationary, with samplers placed on a mannequin or when placed on workers.15–18
The aim of this study was to compare two impinger methods, one with 2MP and the other with DBA reagent, and a filter method with 2MP impregnated filters. For both impinger methods a filter was attached downstream of the flask to account for submicron particles. In order to expose all samplers (five of each kind, for the same HDI concentration in air) they were put together inside a sampling chamber. This type of equipment, described in more detail in this paper, has been developed for gas and welding fume measurement methods and has been used for the generation of replicate filter samples of asbestos.19 The three methods were compared for sampling HDI in atmospheres produced by spray painting. Analyses were all performed by LC-MS-MS.
Experimental
Chemicals
Hexamethylene diisocyanate (HDI) (Aldrich, 99%), 1-(2-methoxyphenyl)-piperazine (2MP) (Aldrich, 98%), dibutylamine (Fluka Chemika, >99%), acetic anhydride (Fluka Chemika, >99.5%) and calcium hydride (Fluka, > 95%) were delivered from Sigma-Aldrich Sweden AB (Stockholm, Sweden). Trideuterated 1-(2-methoxyphenyl)-piperazine (2MP(d3)) was purchased from Synthelec (Lund, Sweden) and di-N-butylamine-d18 (DBA(d18)) (Cambridge Isotope Laboratories, Inc (Andover, USA) (98% d)) from Larodan Fine Chemicals AB (Malmö, Sweden). Methanol (HPLC), toluene (Baker analysed) and anhydrous magnesium sulfate (>99%) were all from J. T. Baker and delivered by Mallinckrodt Baker BV (Deventer, Holland). Isooctane (>99.5%) and ammonium acetate (>98%) were from Merck (Darmstadt, Germany), formic acid from Riedel-de Haën AG (98–100%) (Seelze, Germany), ammonium formate from BDH (>98%) (Poole, England) and acetonitrile (HPLC), from Rathburn
(Walkerburn, Scotland) or Labscan (Dublin, Ireland). Deuterated chloroform (99.5%D) for NMR was purchased from Dr.Glaser AG Basel (Basel, Switzerland). Two component paint consisting of STANDOX 2K Hardener Fast and Herberts Multimix 2k, both purchased from Herberts Norden AB (Hisings Kärra, Sweden).Synthesis of reference compounds for analytes and internal standards
HDI was derivatised with 2MP according to the procedure described in MDHS 25/3.3 The DBA derivative of HDI was synthesised as described by Karlsson and co-workers.7The deuterated 2MP and DBA derivatives were prepared in similar ways as their nondeuterated homologues but on a small-scale synthesis. Toluene was dried with calcium hydride and distilled before use. HDI (80.4 μmol in 2 ml toluene) was slowly added to 2MP(d3) (160.3 μmol in 2.5 ml toluene). The formed crystals were filtrated and dried. DBA(d18) (0.34 mmol in 2 ml acetonitrile) was slowly added to HDI (0.17 mmol in 5 ml isooctane). After reaction the solution was evaporated to dryness.
The identity and purity was verified with LC-MS-MS and NMR.
N, N′- (Hexamethylene) bis[4-(2-methoxyphenyl)-1-piperazinecarboxamide], HDI-2MP2. NMR (CDCl3): 1H(Bruker DRX 400 MHz): δ 7.4–6.98 (m, 2H, Ph–H), 6.94–6.85 (m, 6H, Ph–H), 4.82 (t, 2H, J = 5.7, 5.6 Hz, O
C–N–H), 3.86 (s, 6H, OCH3), 3.55 (t, 8H, J = 5, 5.1 Hz, piperazine-H), 3.24 (q, 4H, J = 6.8, 12.6 Hz, N–CH2 (C1 and C6)), 3.03 (t, 8H, J = 5, 5.1 Hz, piperazine-H), 1.52 (m, 4H, –CH2– (C2 and C5)), 1.36 (m, 4H, –CH2– (C3 and C4)), purity 97%.LC-MS-MS ESP+(PE SCIEX, API 2000): Product ion scan of molecular ion m/z 553 u [M+H]+ results in following fragmentation (relative intensity): m/z 193 (100) [2MP+H]+, 150 (2) [2MP-NC2H4]+.
HDI-2MP(d3)2, deuterated homologue of HDI-2MP2. Except from the missing singlet at 3.86 ppm the 1H NMR spectrum is identical with the one of HDI-2MP2.LC-MS-MS ESP+(PE SCIEX, API 2000): Product ion scan of molecular ion m/z 559 u [M+H]+ results in the following fragmentation (relative intensity): m/z 364 (2) [M-2MP(d3)+H]+, 196 (100) [2MP(d3)+H]+, 153 (5) [2MP(d3)-NC2H4]+.
1, 1′-Hexamethylene- 3, 3, 3′, 3′-tetrabutyl diurea, HDI-DBA2. NMR (CDCl3): 1H(Bruker DRX 400 MHz): d 4.35 (t, 2H, J = 5.5 Hz, –N–H), 3.09–3.24 (m, 12H, J = 5.5, 7.7 Hz, 2×
–H2C–N–H and 2×
–N(–CH2–)–CH2–), 1.53–1.44 (m, 12H, J = 7.7, 7.5 Hz, 2×
–N(–CH2–CH2–)–CH 2–CH2–) and 2×
–N(–H)–CH2–CH2), 1.35–1.24 (m, 12 H, J = 7.5, 7.3 Hz, 2×
–N(–CH2–CH2–CH2–)–CH 2–CH2–CH2– and 2×
–N(–H)–CH2–CH2–CH 2),
0.91 (t, 12H, J = 7.3 Hz, 4×
–CH3), purity > 98%.LC-MS-MS ESP+(PE SCIEX, API 2000): Product ion scan of molecular ion m/z 427 u [M + H]+ results in the following fragmentation (relative intensity): m/z 298 (44) [M-DBA + H]+, 156 (61) [DBACO]+, 130 (100) [DBA + H]+, 100 (12) [CODBA-C4H9 + H]+, 74 (3) [C4H9NH3]+, 57 (25) [C4H9]+.
HDI-DBA(d18)2, deuterated homologue of HDI-DBA2. NMR (CDCl3):1H (Bruker DRX 360 MHz):d 4.35(t, 2H, –N–H), 3.09–3.24(m, 12H, 2×
–H2C–N–H), 1.45 (m, 4H, 2×
–N(–H)–CH2–CH2), 1.27 (m, 4H, 2×
–N(–H)–CH2–CH2–CH2).LC-MS-MS ESP+(PE SCIEX, API 2000): Product ion scan of molecular ion m/z 463 u [M + H]+ results in the following fragmentation (relative intensity): m/z 316 (70) [M-DBA(d18) + H]+, 174 (71) [DBA(d18)CO]+, 148 (100) [DBA(d18) + H]+, 110 (10) [CODBA(d18)-C4D9 + D]+, 66 (29) [C4D9]+.
General analytical instrument settings
The liquid chromatograph consisted of two Perkin Elmer series 200 micro pumps and a Perkin Elmer 200 autosampler fitted with a 200 μl loop (Perkin-Elmer, Norwalk, CT, USA). The column was a Grom-sil 80 ODS-7, 4 μm 200 × 3mm column (Grom Analytik + HPLC GmbH, Herrenberg Germany). The column outlet was coupled to a triple quadrupole mass spectrometer (API 2000 PE Biosystem, Foster City, CA, USA) equipped with electrospray interface. All sample and instrument data were collected by the API 2000-computer system MassChrome v 1.1. (PE Sciex, Foster City, CA, USA). The mass spectrometer was calibrated against a PPG-standard (PE Biosystem, Foster City, CA, USA). Quantitative data were evaluated with TurboQuan 1.0 (PE Sciex Instruments, Foster City, CA, USA) by integrating and calculating the area ratio between the analyte (HDI) and the deuterated internal standard as a function of mass isocyanate per sample in external standard solutions.Mass spectrometric analysis of 2MP and DBA derivatised isocyanates
Two eluents, A and B, were used in gradient elution. For the 2MP method the eluents used were A: acetonitrile with 5% v/v water and B: water. Two mmol l−1 ammonium acetate were added to both eluents. For the DBA method the eluents used were; A: methanol and B: water. Two mmol dm−3 ammonium formate and 0.05% v/v formic acid were added to both eluents. For both methods, after four minutes of equilibration, five microliters of sample were injected and eluted with a flow of 400 μl min−1 in a gradient elution. The 2MP method starts with A∶B, 60∶40 isocratic elution for one minute, followed by a three minute gradient up to 95∶5. At 95∶5 the sample is eluted in isocratic mode for 5.9 min. The DBA method starts with a 13 min gradient from A∶B, 80∶20 to 95∶5 and ends with one minute of isocratic elution at this composition. In the 2MP method no split capillary was used, whereas in the DBA method a split
capillary was used to introduce one fifth of the injection volume to the mass spectrometer. In the mass spectrometer the capillary was set at 5.5 kV for both methods and the added drying gas temperature was set at 320 °C for the 2MP method and 100 °C for the DBA method. Selected reaction monitoring (SRM) was performed on the transition [M + H]+ to [2MP + H]+ and [M + H]+ to [DBA + H]+ for 2MP and DBA , respectively. Individual values for orifice and collision energy were obtained and data collected with a dwell time of 150 ms (2MP) and 200ms (DBA). The SRM result from the first quadrupole (comparative to single ion monitoring (SIM) on the protonated molecule [M + H]+) was used for quantification.Air sampling methods
For each sampler the flow was measured before and after sampling with a DryCal DC-Lite Primary Air Flow Meter from BIOS International Corporation (Pompton Plains, NJ, USA). All samples were stored in a refrigerator until the work-up the following day. Samples were thereafter stored in the freezer and analysed within three days of sampling.2MP impregnated filter. Glass fibre filters GFA, 25 mm diameter, from SKC Inc. (Pennsylvania, USA) (of binder free type AE with the pore size of 1μm) were impregnated by applying 200 μl of 2MP in toluene (0.052 mol l−1) per filter with a Finnpipette from Labsystems OY (Helsinki, Finland). The filters were dried overnight in a gentle stream, (2 l min−1) of filtered compressed air . The dried filters were each spiked with 100 μl of internal standard HDI-2MP(d3)2 in acetonitrile (15 μmol l−1) using a Finnpipette. The filters were placed in aerosol analysis monitor cassettes, 25 mm in polystyrene, from Millipore (Milford, MA, USA). During sampling a flow of 2 l min−1 was drawn through the cassette in the closed face mode. Immediately after sampling each filter was put in 2 ml of 2MP reagent solution in toluene (260 μmol l−1).
Impinger with reagent solution and back-up filter. The 2MP concentration in the impinger reagent solution was 260 μmol l−1 in toluene. For the 2MP impinger method, the back-up filters were impregnated by applying 54 μl of 2MP in toluene (0.052 mol l−1) per filter with a Finnpipette. Filters were dried as described for 25 mm filters.For the DBA impinger method, the concentration of DBA in the impinger reagent solution was 0.01 mol l−1 in toluene. DBA is rather volatile and the back-up filters were not prepared by impregnation.
Spill resistant midget impingers from Svenska Labglas service AB (Stockholm, Sweden) were filled with 10 ml of reagent solution (for concentrations see above). To each impinger 100 μl of internal standard in acetonitrile (15 μmol l−1) was added. Glass fibre filters GFA, 13 mm diameter, from SKC Inc. (Pennsylvania, USA) were placed in a Swinnex filter holder, 13 mm in polypropylene, from Millipore (Milford, MA, USA). The filter holders were attached directly to the impinger outlet with silicone tubing. During sampling a flow of 1 l min−1 was drawn through the impinger plus filter. After sampling the back-up filters were put into the corresponding impingers.
Work-up procedures
The excess of reagent in 2MP samples was acetylated with 100 μl of acetic anhydride. After one hour, 200 μl aliquots of all 2MP filter samples were transferred to 200 μl Chromacol vials (02 CVG) (Trumbull, CT, USA). For impinger samples, three times 300 μl aliquots were transferred to 300 μl vials of the same make (03 CVG). Samples were evaporated to dryness in a Speed Vac Concentrator with a condensation trap (Savant Instruments Inc., Farmingdale, USA). Before analysis the 2MP samples were dissolved in 200 μl acetonitrile and the DBA in 200 μl methanol. The vials were sealed with a chromacol crimp cap (8 AC7) and centrifugated for 5 min at 5000 rpm in Uniequip UEC 13 (Martinsried, Germany).Exposure chamber and experimental set up for spray painting
Spray painting operations were performed inside a PIVAB spray box (inner dimensions 200 × 200 × 300 cm) (PIVAB International AB, Veddige, Sweden) with a High pressure Spray gun SATAjet/B (MSB nozzle, without swivel joint) from SATA Farbspritztechnik GmbH&Co (Kornwestheim, Germany). The painting distance was 15 cm from the object to be painted and the inlet compressed air pressure was 3 bar.Homogeneity-tests were performed to assure an even concentration in the atmosphere inside the exposure chamber. In the homogeneity-tests only one type of sampler was used. Aerosol cassettes with 2MP filter occupied all positions in the sampling chamber. Samplers representing the impinger positions were placed on top of the impinger inlet. The positions were adjusted so that the aerosol cassette inlets were at the same level as the ones on top of the impinger inlet. For the homogeneity tests 150 ml paint was consumed over 11–12 min. For the sampling method comparisons 120 ml paint was consumed over 9–10 min. The sampling times were equal to the times for paint consumption. During sampling, the ventilation in the spray box was turned off to attain measurable levels and to avoid undesirable turbulence. The painter was outside the box and conducted the spray painting inside the box with the use of gloves attached to holes in the door, like a glove box. The portable sampling chamber
(National Institute of Occupational Health, Oslo, Norway) was situated in the ceiling, with its centre 78 cm from the short side. When painting, the spray gun was pointing in a direction away from the sampling chamber. Fig. 1 shows a principal sketch of the experimental materials and the enlargement provides a cross-section diagram of the sampling chamber. A plate with a total of 36 critical orifices separates the sampling region from the part of the chamber that is connected to a powerful vacuum pump. Accurate dimensions of the orifices will give proper and constant sampling flows as the pressure is reduced in the upper part of the chamber. The aerosol monitor cassettes were attached to the chamber’s critical orifices by the use of silicone tubing and cut off 1 ml syringes (Codan Medical ApS, Rødby, Denmark), the impingers were placed in the chamber with a metal holder and also attached to critical orifices with silicone tubing. Sampler inlets
were adjusted to the same level in height.
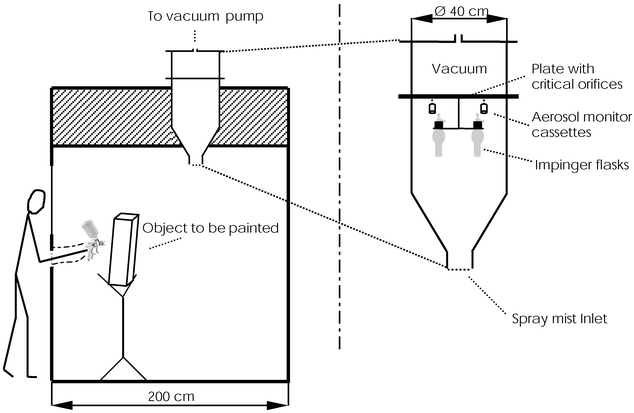 |
| Fig. 1 Spray painting in the 300 cm wide spray box. The sampling chamber is situated in the ceiling. The location of the samplers to be compared is shown in the, two times enlarged, cross-section sketch. | |
Statistics
An analysis of variance, ANOVA, single factor was used to examine whether there was any difference between the different types of samplers. The significance level was set to a = 0.05. With a given sample size, the smallest detectable difference that could be seen between samplers was calculated from operating characteristic curves with a given power of 90% and a significance level of α = 0.05. The operating characteristic curves are normally used to calculate what sample size is needed in order to detect a certain effect.Results
In the homogeneity tests, the relative standard deviation between the samplers was 6.8% at 0.25 mg m−3 (n = 36), and 7.8% at 0.15 mg m−3 (n = 35).The sampler comparisons were made at two different levels as defined by the outcome of the LC-MS-MS analysis. At the lower level the mean HDI concentration (and standard deviation) for each method were as follows: 2MP filter, 18 μg m−3 (σ = 1.7); 2MP impinger, 21 μg m−3 (σ = 1.5); and DBA impinger, 19 μg m−3 (σ = 2.4). The measures for each type of sampler are displayed to the left in Fig. 2. At the higher level the mean HDI concentration (and standard deviation) for each method were as follows: 2MP filter, 76 μg m−3 (σ = 8.7); 2MP impinger, 93 μg m−3 (σ = 11); and DBA impinger, 87 μg m−3 (σ = 15). The measures for each type of sampler are displayed to the right in Fig. 2. According to the ANOVA there was no significant
difference between samplers, at either the lower or the higher level. Table 1 shows the ANOVA results.
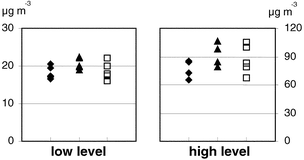 |
| Fig. 2 Results from the sampler comparison at the lower and the higher level. ◆ 2MP filter, ▲ 2MP impinger and □ DBA impinger. | |
Table 1 ANOVA table. There was no significant difference between the different sampler types
Source of variation | SS | df | MS | F | Fcrit |
---|
Low level | | | | | |
Between sampler | 16.58 | 2 | 8.3 | 2.2 | 3.89 |
Error | 44.67 | 12 | 3.7 | | |
Total | 61.25 | 14 | | | |
High level | | | | | |
Between sampler | 749.3 | 2 | 375 | 2.6 | 3.89 |
Error | 1728 | 12 | 144 | | |
Total | 2477 | 14 | | | |
Discussion
In this experimental set up, real life conditions, which might be found in the working environment, were imitated. Other ways of generating HDI aerosols are described in the literature.20,21 The advantage of using paints, spray gun and other conditions that are utilised daily in workplaces, is that there can be little doubt about the relevance of the experimental results. HDI in a curing spray mist exists as both as gas and in particulate form in variable sizes. In spray painting operations coarse aerosol particles are 1–100 μm in size.12 This characteristic of HDI has a disadvantage in that the variation in concentration will be rather large in space and in time.In the homogeneity tests the variation was less than 10% and the atmosphere in the sampling chamber was satisfactorily homogenous to perform comparative measurements. This variation includes all possible errors from sampling to analysis, and is of the same magnitude as can be expected when sampling in the field. In the sampler comparison tests, the relative standard deviations are larger than 10%, and to some extent this is explained by the smaller sampling size. In our experimental apparatus, there was only room for ten impinger samplers in the sampling chamber. Theoretically an experimental design including repeated measurements could have been a way to circumvent the small sample size number, but despite many tries we have not been successful in predicting the level of HDI to be measured. There are simply too many factors involved in spray painting operations with two component paints to be controllable. With the limited sample size, the smallest difference in HDI concentration in
air that could be seen was 5 μg m−3 at the low level (20 μg m−3), and 31 μg m−3 at the high level (85 μg m−3).
Since no difference could be seen between the different sampler types, the conclusion is that for spray painting operations either 2MP filter, 2MP impinger or DBA impinger can be used to collect monomers of HDI in occupational air.
Acknowledgements
Many thanks to Yngvar Thomassen and Geir Fladseth at the National Institute of Occupational Health in Oslo, Morten Berndtsen at the National Institute of Technology in Oslo and Peter von Zweigbergk and Leif Wiklund at the National Institute for Working Life in Umeå.References
- Encyclopedia of Chemical Technology, Thioglycolic Acid to Vinyl Polymers, ed. J. I. Kroschwitz and M. Howe-Grant, Wiley, New York, 4th edn., 1997, vol. 24, pp. 695–727 Search PubMed.
- Arbetarskyddsstyrelsen, Hygieniska gränsvärden och åtgärder mot luftföroreningar (in Swedish), AFS 2000:3, Stockholm, 2000, ISBN: 91–7930–357–9.
- Health and Safety Laboratory (HSE), Organic Isocyanates in Air, MDHS 25/3, HSE Books, Sudbury, 1999 Search PubMed.
- Occupational Safety and Health Administration (OSHA), Diisocyanates,
Methods Manual 42, OSHA , Salt Lake City, 1989 Search PubMed.
- R. P. Streicher, J. E. Arnold, M. K. Ernst and C. V. Cooper, Am. Ind. Hyg. Assoc. J., 1996, 57, 905 CrossRef CAS.
- C. Sangö and E. Zimerson, J. Liq. Chromatogr., 1980, 3, 971.
- D. Karlsson, M. Spanne, M. Dalene and G. Skarping, Analyst, 1998, 123, 117 RSC.
- W. S. Wu, R. E. Stoyanoff, R. S. Szklar, V. S. Gaind and M. Rakanovic, Analyst, 1990, 115, 801 RSC.
- Y. M. Roh, R. P. Streicher and M. K. Ernst, Analyst, 2000, 125, 1691 RSC.
- H. E. Myer, S. T. O′Block and V. Dharmarajan, Am. Ind. Hyg. Assoc. J., 1993, 54, 663 CrossRef CAS.
- V. Dharmarajan, R. D. Lingg, K. S. Booth and D. R. Hackathorn, Recent Developments in the Sampling and Analysis of Isocyanates in Air, Sampling and Calibration for Atmospheric Measurements, ASTM Special Technical Publication, American Society for Testing and Materials, Philadelphia, PA, 1987 Search PubMed.
- M. Spanne, P. Grzybowski and M. Bohgard, Am Ind Hyg. Assoc. J., 1999, 60, 540 CrossRef CAS.
- R. Streicher, E. Kennedy and C. Lorberau, Analyst, 1994, 119, 89 RSC.
- W. J. Karoly, Am. Ind. Hyg. Assoc. J., 1998, 59, 645 CrossRef CAS.
- W. E. Rudzinski, J. Yin, E. England, G. Carlton, R. Key-Schwartz and J. Lesage, Aihaj, 2001, 62, 246 Search PubMed.
- H. Tinnerberg, D. Karlsson, M. Dalene and G. Skarping, J. Liq. Chromatogr. Relat. Technol., 1997, 20, 2207 CAS.
- E. England, R. Key-Schwartz, J. Lesage, G. Carlton, R. Streicher and R. Song, Appl. Occup. Environ. Hyg., 2000, 15, 472 CrossRef CAS.
- W. E. Rudzinski, B. Dahlquist, S. A. Svejda, A. Richardson and T. Thomas, Am. Ind. Hyg. Assoc. J., 1995, 56, 284 CrossRef CAS.
- A. Skogstad, W. Eduard and P. O. Huser, Am. Ind. Hyg. Assoc. J., 1996, 57, 741 CrossRef CAS.
- C. K. Huynh, T. Vu Duc and H. Savolainen, Ann. Occup. Hyg., 1989, 33, 573 CAS.
- C. K. Huynh, T. Vu-Duc and H. Savolainen, Am. Ind. Hyg. Assoc. J., 1992, 53, 157 CAS.
|
This journal is © The Royal Society of Chemistry 2002 |
Click here to see how this site uses Cookies. View our privacy policy here.