DOI:
10.1039/D4RA03036B
(Review Article)
RSC Adv., 2024,
14, 23322-23331
On the role of disjoining pressure in nanofluid-assisted enhanced oil recovery: a mini-review
Received
24th April 2024
, Accepted 14th July 2024
First published on 24th July 2024
Abstract
Nanofluid application in enhanced oil recovery (EOR) recently emerged and garnered significant attention within the field. Nanofluids possess unique properties of reducing oil–water interfacial tension, stabilizing emulsions, altering rock surface wettability, and enhancing disjoining pressure between crude oil and rock surfaces, therefore have potential for the oil recovery process. This review provides an in-depth exploration of various aspects related to nanofluids in EOR. Different types of nanofluids are presented with their preparation methods and representative properties. More importantly, the disjoining pressure, a key physical concept in nanofluid-assisted EOR, is introduced and discussed in terms of the mechanism of oil displacement and measurement methods. Further understanding the role of disjoining pressure in nanofluid-assisted oil displacement is necessary for the development and application of effective nanofluids for EOR.
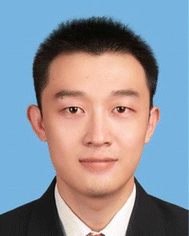 Baoliang Peng | Baoliang Peng is a senior engineer at the Research Institute of Petroleum Exploration and Development (RIPED), PetroChina. In 2007, he started his graduate study, and joined a dual-degree doctoral program between the University of Waterloo and East China University of Science and Technology (ECUST). He earned his PhD in 2014. His research interests focus on fundamental mechanism and chemical materials for enhanced oil recovery applications. |
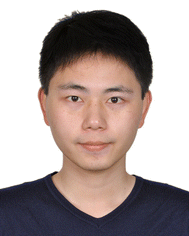 Han Gao | Han Gao is a PhD candidate in the School of Mechanical Engineering and Automation at Beihang University, China. His research focuses on the dynamics and manipulation of nanoparticles. |
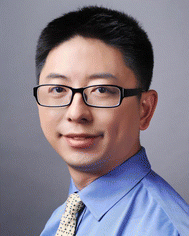 Ye Xu | Ye Xu is a professor of soft materials and mechanics in the School of Mechanical Engineering and Automation at Beihang University, China. He earned his PhD degree in 2012 from Yale University. His current research interests include soft matter physics and mechanics, flexible micro-nanomaterials and structures, and microfluidic devices. |
1. Introduction
In the petroleum industry, enhanced oil recovery (EOR) stands as a pivotal and indispensable phase within the oil production process, designed to extract crude oil from reservoirs that would otherwise remain unrecoverable.1–4 EOR is defined as the injection of a special solution/gas into the reservoir so that crude oil trapped inside can be driven out of the pore or gap.5 Four prevalent EOR techniques have emerged, including chemical injection, gas injection, microbial methods, and thermal processes.6–9 Briefly, chemical injection EOR is a process that injects selected chemicals into the reservoir, thereby altering the reservoir's physicochemical properties.10 Meanwhile, gas injection EOR mainly uses CO2 as the primary agent to displace oil.11 Microbial EOR, on the other hand, relies on the utilization of microorganisms and their metabolic byproducts to effectively mobilize oil from reservoirs.12 Thermal processes can decrease oil viscosity or change the rock's wettability by introducing heat into a light oil reservoir.6
Nanofluid EOR, a special chemical EOR method, has been proposed and attracted significant attention within the field recently.13–17 A nanofluid, in brief, is a suspension comprising solid nanoparticles that are uniformly dispersed within a solvent medium.18,19 It has been reported that nanofluids show many advantageous properties inherent in the context of EOR, including high stability, low erosion, and friction coefficients, and good lubrication.20–23 Furthermore, the distinctive characteristics exhibited by the contained nanoparticles, including their small size and high surface-to-volume ratio, significantly contribute to the reduction of oil–water interfacial tension and the alteration of rock wettability.24
Due to the potential advantages offered by nanofluids in EOR, researchers have dedicated efforts to investigating the mechanisms behind oil recovery through nanofluids. Prior studies have identified four primary aspects of the EOR mechanism involving nanofluids: (1) reduction of oil–water interfacial tension, (2) enhanced stability of oil–water emulsions, (3) alteration of rock wettability, and (4) increase of disjoining pressure between oil and rock surface. The reduction of the oil–water interfacial tension is the result of a single or multi-layer film of nanoparticles that are strongly adsorbed on the oil–water interface.25–27 In addition, these solid particles create an interconnected network that envelops the oil–water emulsions, giving rise to the enhanced stability and resistance to rupture.28,29 Moreover, nanoparticles can attach to the surface of rocks, generating diverse structures that effectively transform the wettability of the rock. The simulation proved that the water-wet state has a higher oil recovery than the oil-wet state for oil-saturated pores and wettability effects can help oil to detach from the pore walls for oil-unsaturated pores.30 More importantly, recent studies found that the disjoining pressure, generated by the orderly accumulation of nanoparticles at the oil–water–solid three-phase interface, can effectively separate the oil from the rock surface.13,31–33 While the reduced oil–water interfacial tension and altered wettability due to strong adsorption of nanoparticles to the oil–water interface or the rock surface are well understood, the systematic assessment of the role of disjoining pressures in EOR is still lacking.
This review focuses on the role of disjoining pressure in the presence of nanofluids and its consequential impact on the EOR processes. The review is structured in the following way. The first part introduces different types of nanofluids and their preparation methods. Key properties of those nanofluids, including suspension stability, thermophysical properties, and flow properties, are also presented. In the second part, the disjoining pressure is defined and formulated in terms of its three components including van der Waals force, electrostatic force, and structural disjoining pressure, followed by a discussion on the mechanism of the disjoining pressure in EOR. The third part reviews the measurement methods in the study of disjoining pressures, including the direct measurement of and the indirect method through the liquid film thickness. Finally, the prospects of the nanofluids in EOR are discussed, therefore offering a forward-looking perspective on this topic.
2. Nanofluids used in EOR
2.1 Preparation methods of nanofluids
Nanofluids are defined as suspensions obtained through the even dispersion of nano-sized solid particles in liquid media such as water, ethylene glycol, and oil. The liquid component is immiscible with solid particles, and the size of solid particles is in the range of 1–100 nm. As a major component of nanofluids, the appropriate selection of nanoparticles is crucial in improving the efficacy of EOR.19,55,56 Generally, nanoparticles can be categorized into four groups: metals, metal oxides, non-metallic oxides, and carbon nanotubes based on their chemical composition, as detailed in Table 1. There are also some nanoparticles not included in this category, such as copper quantum dot/polyacrylamide composite nanospheres,57 MoS2,29 Kaolinite-based Janus nanosheets,58 2D Janus polymer nanosheets.59 Currently, non-metallic oxide nanoparticles and metal oxide nanoparticles are widely applied in EOR, primarily due to their capacity to alter the wettability of rocks or reduce oil–water interfacial tension.46,50,51 Particularly, as a principal rock component, SiO2 nanoparticles are commonly used for EOR application.51,60–64 Chaturvedi et al. prepared a stable SiO2 nanofluid that interacts with polymer chains and creates a steric barrier to improve CO2 absorption for oilfield applications.65 Moreover, the SiO2 nanofluid could also improve CO2 flow and reduce formation damage in porous media for carbon utilization.66
Table 1 Nanoparticles in nanofluids and improvement in EOR
Categories |
Examples |
Advantages |
Metals |
Cu,34,35 Ag,36 Au,37,38 Fe,39 etc. |
Electrical conductivity and chemical catalysis |
Metal oxides |
Al2O3,40,41 CuO,42,43 TiO2,44,45 ZrO2,46,47 etc. |
Alter the wettability of carbonate reservoir rocks46 |
Non-metallic oxides |
SiO2,48 CaCO3,49 etc. |
Reducing oil–water interfacial tension in light reservoirs50 and non-polluting as the main component of rock51 |
Carbon nanotubes |
MWCNT,52 DWCNT53 |
Reducing the viscosity of crude oil54 |
There are two main preparation methods for nanofluids, namely the one-step method and the two-step method.67–70 In the one-step method, nanoparticles are generated and uniformly dispersed into the base liquid within the same preparation process.71 In the two-step method, by contrast, nanoparticles are first prepared, mostly using the solution-based method, and then dispersed in a certain proportion into the base fluid.72 To ensure uniform dispersion of nanoparticles, techniques including ultrasonic vibration, magnetic stirrer, and the addition of dispersant to the fluid are commonly employed.73,74 Nanofluids prepared by the one-step method usually exhibit high purity and good stability, which determine whether the nanoparticles can function effectively, especially in nanofluid flooding systems. For example, Aberoumand et al.75 used the one-step method to prepare a Cu nanofluid, composed of high-purity copper nanoparticles and engine oil without surfactant and exhibiting good stability at room temperature. Despite the advantage of avoiding the oxidation of nanoparticles and the separate processes like drying, transportation, storage, and additional dispersion of nanoparticles, the one-step process entails complexity and necessitates substantial equipment investment, rendering it unsuitable for large-scale production endeavors.75,76 On the other hand, the two-step preparation process is simple, cost-effective, and therefore feasible for large-scale production. Nevertheless, nanofluids produced through the two-step method tend to be relatively unstable, prone to coalescence and precipitation, and therefore often require stirring or the inclusion of dispersants.39,76
2.2 Properties of nanofluids
Compared to the general fluid without nanoparticles, nanofluids exhibit special characteristics of thermophysical and flow properties.77 The addition of nanoparticles can improve the thermal conductivity of simple fluids such as glycol and water. For example, Xing et al.78 found that the thermal conductivity of carbon nanotube nanofluid was higher than that of base fluid deionized water, and increased with the increase of the nanoparticle concentration and temperature. As for the flow property, it is well observed that the nanofluid shows higher viscosity than that of the base fluid, and the viscosity increases with the concentration of nanoparticles.79 The higher viscosity of nanofluids can improve the mobility ratio.80 For a high viscosity ratio, displacement occurred in the form of capillary fingers at low capillary numbers while the displacement gradually became stable at high capillary.81 Interestingly, even in cases where nanofluid viscosity rises with concentration, Sefiane et al.82 found that aluminum nanofluids exhibit greater spreading capability across solid surfaces compared to ordinary fluids, even though the viscosity of the nanofluids is higher.
In addition to the general ones discussed above, the properties of nanofluids particularly important for EOR are the ability to alter the interfacial tension (IFT) of oil–water and the wettability of rock. Joonaki and Ghanaatian83 studied the effect of three nanofluids (Al2O3, SiO2, Fe2O3) on IFT, revealing that increasing the nanoparticles concentration led to reduced IFT and a shift towards a more neutrally wetted solid surface. Notably, SiO2 was more efficient in reducing IFT between oil and water. Tohidi et al.84 proved that silica Janus nanoparticles can increase the viscosity of water phase and reduce the IFT using molecular dynamics simulation. Furthermore, a hydrophilic SiO2 nanofluid displayed the ability to enhance the performance of anionic surfactant in reducing IFT.85 Besides, Moradi et al.86 highlighted that SiO2 nanofluid can induce alterations in the wettability of carbonate rock by adsorbing it onto its surface. Particularly significant wettability changes were observed when the proportion of SiO2 nanoparticles was elevated.87 Wettability alteration can also be estimated using simulation methods. Boampong et al.88 developed a model that showed oil adsorption was still possible, even when the oil–brine and the rock–brine interfaces had the same polarity of zeta-potentials in a low-salinity water flooding system. Therefore, the wettability alteration is not related only to the polarities of the interface zeta-potentials, but also to the magnitude of the zeta-potentials.
Furthermore, the addition of surfactants, such as anionic sodium dodecyl sulfate (SDS)89 and cationic hexadecyltrimethylammonium bromide,90 nonionic pentaethylene glycol monododecyl ether,91 enhancing the stability of nanofluid can also promote the oil recovery. Kumar et al.92 found that the synergy between SDS and SiO2 nanofluid subdued surfactant adsorption in both unconsolidated and consolidated porous media even at high salinity. Besides, Chaturvedi et al.93 added SDS into SiO2 nanofluid leading to an improvement in the fluid stability by reducing salt-induced nanoparticles agglomeration. The displacement results also showed that the surfactant used in the SiO2 nanofluid for oil recovery applications provides better results than sole silica nanofluid at high temperatures and salinity.
Except for bare SiO2 nanoparticles, other nanoparticles such as bare ZrO2, functionalized MoS2, or grafted SiO2 nanoparticles were also reported to be used in EOR. Karimi et al.46 prepared a ZrO2 nanofluid that could alter the wettability of a carbonate reservoir rock from strongly oil-wet to a strongly water-wet condition. Moreover, the imbibition of ZrO2 nanofluid into core plugs which could quickly recover oil. Functionalized nanofluid also be used in EOR. Liang et al.29 improved the dynamic stability of MoS2 nanoparticles functionalized by octadecyl amine molecules. The prepared nanofluid could reduce IFT and emulsify crude oil to a micro size which was better for EOR. In addition to being directly used as a displacement agent, there are also many reports using nanoparticle grafting other materials for EOR. Pillai et al.94 found that adding lysine-grafted SiO2 nanoparticles into surfactant could also reduce IFT to the ultralow range and improve the stability of emulsions. Corredor et al.95 reported that the fabricated nanopolymer sols (polyacrylamide-grafted SiO2) exhibited lower IFT and the ability to alter the wettability of the substrate from oil-wet to intermediate-wet. Furthermore, the addition of the nanopolymer into hydrolyzed polyacrylamide solution could improve the solution's thickening behavior at all salinities, and increase the oil recovery of the polymer solution.
The addition of nanoparticles to assist in flooding control is also being considered. Saw et al.96 found that the synergistic effects of reducing IFT between low-salinity water and SiO2 nanoparticles can increase oil recovery significantly. In nano emulsion flooding systems, adding nanoparticles could increase droplet stability80 and ionic strength,97 which is also effective in EOR.
3. Disjoining pressure
3.1 Definition of disjoining pressure
Disjoining pressure is a thermodynamic concept proposed to describe the pressure difference between the inside and outside of a thin liquid film confined between two surfaces. This phenomenon arises due to the interaction forces at the molecular level and can influence the stability and behavior of liquid films in various contexts, including colloid science, wetting, and spreading phenomena,98,99 and also in EOR applications.26,100
In the surface physics framework, disjoining pressure is defined as the derivative of energy as a function of the film thickness for a liquid film confined between two surfaces, either attractive or repulsive. For two flat and parallel surfaces, the disjoining pressure can be calculated as the derivative of the Gibbs energy per unit area.
Considering the intermolecular interactions, the disjoining pressure (Π) comes from three main components.14
where
Πm,
Πe,
Πs indicate van der Waals force, electrostatic force, and structural disjoining pressure, respectively.
The van der Waals force (Πm) is given by
|
 | (2) |
where
h is the thickness of the film and
AH is the Hamaker constant determined by the three-phase dielectric constant, which is generally at the order of 10
−19 J for a strongly hydrophilic oil–water–solid system.
101 Πm is caused by intermolecular interactions and is a long-range attractive force, which is essential for microscale droplet spreading and film stability.
The electrostatic force (Πe) can be written as
|
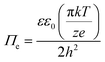 | (3) |
where
ε,
ε0 represent dielectric constants of vacuum and water respectively,
k is the Boltzmann constant,
T is the temperature,
z is the zeta potential, and
e is the electronic charge.
Πe can be a long-range repulsive force or attractive force, which depends on the zeta potential.
102 For example, the brine/oil zeta potential displays negative,
103 while the brine/calcite zeta potential is positive.
104
The structural disjoining pressure (Πs) is analytically expressed as
|
 | (4) |
where
Π0,
Π1,
ω,
φ2,
κ are coefficients related to the volume fraction of nanoparticles,
δ is the short-range decay coefficient,
d is the diameter of nanoparticles, and
P is the volume osmotic pressure, whose expression is
|
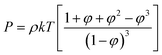 | (5) |
where
ρ denotes the particle concentration. As the volume fraction
φ of nanoparticles increases, the structural disjoining pressure and osmotic pressure also increase.
Πs is a short-range repulsive force and it plays an important role for the properties of the solid–liquid interface.
100
3.2 Effects of disjoining pressure in EOR
In the context of EOR, disjoining pressure is used to understand the interaction between oil, water, and solid surfaces within porous rock. When nanoparticles accumulate orderly at the oil–water–solid interface, they can create a pressure difference within the confined spaces of the rock's pores. This disjoining pressure can help detach oil from the rock surface, aiding in the recovery of oil during EOR processes.25,26
Within nanofluid flooding systems, structural disjoining pressure as a component of disjoining pressure described in 3.1 is dominating compared to the other two components. The reason is that the structural disjoining pressure has a greater range and magnitude than the van der Waals and electrostatic forces in terms of long-range properties. The foremost source of structural disjoining pressure arises from the organized arrangement of nanoparticles. Thus, the structural disjoining pressure is related to the volume fraction of nanoparticles, and increasing volume fractions lead to larger structural disjoining pressures and thus enhanced spreading.82 Recently, Shane32 used the microchip to visualize the EOR process induced by structural disjoining pressure in a porous environment and proved the disjoining pressure, not the IFT reduction enhanced oil recovery using high-volume fraction nanofluids. Under the combined effect of Brownian motion and electrostatic repulsion between particles, nanoparticles dispersed in water accumulate orderly and then form a gradually advancing wedge-shaped film at the three-phase interface (oil–nanofluid–substrate) as shown in Fig. 1(a).100 Further observations reveal that the structural disjoining pressure was perpendicular to the front oil–water interface and attenuated exponentially with the film thickness.100,107 The attenuation factor and the oscillation period were equal to the effective diameter of the nanoparticles. As a result, the structural disjoining pressure at the front of the wedge film was higher than that near the body of the fluids. Concurrently, as the structural disjoining pressure increases, the tension at the vertex of the wedge-shaped film rises gradually.
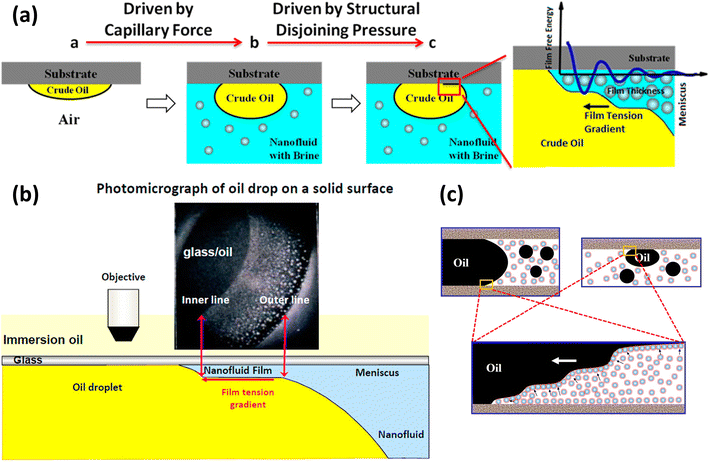 |
| Fig. 1 (a) Forces operating at the three-phase contact line when introducing nanofluids. Reprinted with permission from (ref. 100). Copyright 2014 American Chemical Society. (b) Photomicrograph taken by reflected-light interferometry depicting the nanofluids' structural disjoining pressure in the nanofluids film region. Reprinted with permission from (ref. 105). Copyright 2012 American Chemical Society. (c) The oil displacement mechanism of nanofluids in rock pores. Reprinted with permission from (ref. 106). Copyright 2018 American Chemical Society. | |
The effect of the structural disjoining pressure for the oil displacement in EOR is usually manifested in the contraction of the contact line of oil drops, which strips the crude oil from the rock surface. Kondiparty et al.105 observed two distinct contact lines during the separation of oil droplets from a solid silica surface in the presence of a nanofluid (Fig. 1(b)). The outer line is the macroscopic three-phase contact line, and the inner line corresponds to the advancing nanofluid film driven by structural disjoining pressure. The dynamics of the inner contact line depend on the combination of the nanoparticle formulation, contact angle, and capillary pressure.108 As for flooding in rock, porous rock can be regarded as a network structure composed of capillaries of different sizes. As shown in Fig. 1(c), due to Brownian motion and electrostatic force (described in Fig. 1(a)), whether the oil droplets are in the pipeline or on the wall, nanoparticles accumulate in the three-phase region.106 The inducing structural disjoining pressure promotes the detaching of the oil droplets, thus enhancing the efficacy of oil displacement.
3.3 Measurement of disjoining pressure: direct and indirect methods
3.3.1 Direct methods. A common way to measure the disjoining pressure is a variant of a Mysels cell proposed by Bergeron.109 As shown in Fig. 2(a), a porous glass with a micro hole in the center is welt with a capillary tube (radius r), and which other side is placed out of a chamber. The pressure of the air in the chamber controlled by a syringe pump is high compared to the pressure in the cell. Thus, a film will form in the hole when liquid is injected from the side tube, and the liquid will keep a height (h), because of the pressure difference internal and external of the chamber. Once the system is in the state of equilibrium, the disjoining pressure (Π) is |
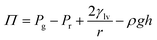 | (6) |
where γlv is the surface tension, ρ is the density of liquid. Pg − Pr can be measured by a pressure transducer.
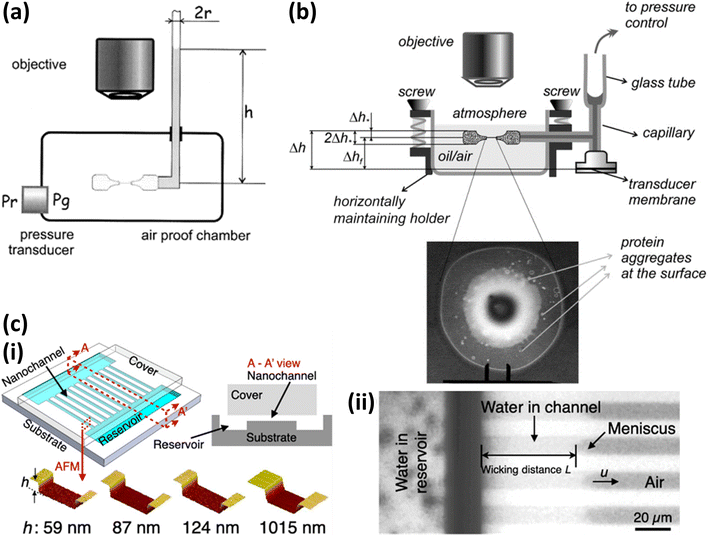 |
| Fig. 2 Experimental setups for measuring the disjoining pressure. (a) Setup proposed by Bergeron. Reprinted with permission from (ref. 110). Copyright 2001 American Chemical Society. (b) Setup to measure disjoining pressure and thickness of film. Reprinted with permission from (ref. 111). Copyright 2004 Elsevier. (c) (i) Nanochannels with different depth and reservoirs. (ii) Wicking experiments of water. Reprinted with permission from (ref. 112). Copyright 2021 American Chemical Society. | |
There are also some improved methods based on Mysels cells to measure disjoining pressure for specific liquid film systems. Dimitrova et al.110,111 replaced the chamber with an open container, and the capillary side welt with a glass tube that the other side is connected with the pressure controller (Fig. 2(b)). This setup can avoid the touch between a precise pressure transducer and the organic liquid as oil phase when investigating both foam and emulsion films. It also solves the practical difficulties of applying pressure jumps on the two sides of the chamber.
In addition to the conventional methods mentioned above, a new method based on microfluid channels to measure disjoining pressure is proposed by Zou et al.112 As shown in Fig. 2(c), a silicon wafer is etched to form several parallel nanochannels whose length and width are 2 cm and 10 μm, and two deeper reservoirs connect with these channels. When one reservoir is fulfilled with water, the water will be sucked into these nanochannels because of capillary pressure. Finally, the disjoining pressure is calculated using the wicking distance, contact angle measured by image analysis, and other constant parameters including dynamic viscosity and surface tension of water, channel's height, and width. This method can simplify device requirements, such as precise pressure transducer, in comparison to using Mysels cells. In addition, the depth of the microchannel, that is, the thickness of the formed film, can be customized by etching, so that the disjoining pressure corresponding to different film thickens can be measured.
3.3.2 Indirect methods: the measurement of liquid film thickness. An indirect way to characterize the disjoining pressure is to measure the thickness of the film, which is closely related to the disjoining pressure according to the definition. During the measurement of film thickness, the formation process of the film can be characterized by the change in the thickness of the nanoparticle layers. A common Scheludko interferometric method was applied to measure the thickness of emulsion films described in many works.110,111,113,114 While a monochromatic light reflects from the film, an interferometric image can be captured (Fig. 2(b)). Thus, the film thickness is calculated from the following relation |
 | (7) |
where I is the intensity of the reflected light, Imax and Imin are the maximal and minimal intensity of the reflected light, respectively, k = 0, 1, … is the order of the interference maximum, λ is the wavelength of the incident light, and n is the refractive index of the liquid film. For greater precision, a photomultiplier tube is employed to determine the intensity of the reflected light.110 Except for forming in a cell, the film also forms near the three-phase contact line of a drop on a solid surface. In this situation, to measure values of the film thickness, which is directly related to the number of particle layers on a solid surface, Nikolov et al.115 used the combined differential and commonly reflected light interferometric method to measure the film thickness of stacked nanoparticles (Fig. 3(a)). To achieve that, a specially designed glass cell eliminating light reflection from the solid substrate is combined with a differential interference microscope to observe nanoparticle self-structuring, the film thickness measured in this way can reach tens of nanometers.
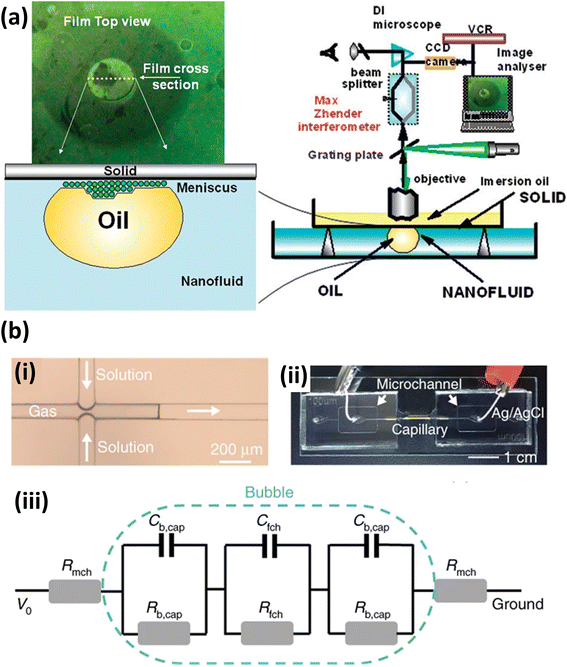 |
| Fig. 3 (a) Observation of nanoparticle self-structuring. Reprinted with permission from (ref. 115). Copyright 2010 American Chemical Society. (b) Bubble-based film nanofluidic for film thickness measurement. (i) A snapshot of bubble formation. (ii) Picture of setup. (iii) An equivalent circuit of the system. Reprinted with permission from (ref. 116). Copyright 2020 Springer Nature. | |
Different from the common Scheludko interferometric method using optical filtering, a new method to produce monochromatic interferograms or images is proposed. Karakashev et al.117 used a CCD high-speed camera to record the interferometric images of the whole transient films. The acquired images are then postprocessed using digital filtration techniques to generate monochromatic interferograms. In this way, different digital filters with different wavelengths to obtain the monochromatic interferograms can be provided.
In contrast to traditional optical measurements, electrical methods have also proven to be useful for measuring film thickness. Ma et al.116 proposed a method that measures the film conductance to calculate the film thickness based on the derived relation between the film thickness and conductance (Fig. 3(b)). In their measurement method, a liquid film nanochannel was constructed by inserting a gas bubble in a glass capillary, and the film thickness was calculated by measuring the resistance within the channel (Fig. 3(iii)). In contrast to the previous interferometric methods, this method requires less complex optical imaging equipment. However, this method can only measure the average film thickness of the system, while the interferometric method can observe the global and local changes in film thickness in real-time.
4. Conclusion and future prospects
Oil displacement is a complex process, especially when nanofluids are used as agents. Through the extensive review of the literature related to nanofluids and disjoining pressure, we can summarize the following findings on this topic:
(1) The integration of nanoparticles in nanofluids has demonstrated a remarkable ability to alter the oil–water interfacial tension and rock surface wettability. These changes are pivotal in enhancing the efficiency of oil recovery processes by improving the mobility and extraction of trapped crude oil.
(2) The concept of disjoining pressure, generated by the orderly self-assembly of nanoparticles at the oil–water–solid interface, is crucial in the nanofluid-assisted EOR. This pressure helps in detaching crude oil from rock surfaces, thereby significantly enhancing the oil displacement efficiency. Understanding the dynamics of disjoining pressure can lead to more effective EOR strategies.
(3) The primary research focus on nanofluid-assisted EOR is on identifying and developing more efficient nanoparticles that can optimize the flooding effect in EOR. This involves exploring different types of nanoparticles and their unique properties to determine the most effective combinations for oil recovery.
Despite the research progress survey in this review, there are still more work need to be done to further understand the crucial role of disjoining pressure in the nanofluid-assisted EOR. Particularly, it is imperative to delve deeper into the mechanisms of oil displacement facilitated by nanofluids beyond the identification of efficient nanoparticles. A comprehensive understanding of how disjoining pressure and other factors interact during the EOR process will be crucial for developing more effective applications. While indirect observations have provided valuable insights into the behavior of nanoparticles, there is a significant gap in the direct experimental observation of nanoparticle accumulation processes and the precise measurement of disjoining pressure in the three-phase region. Future research should aim to develop advanced experimental methods for direct observation and measurement. Additionally, theoretical and simulation studies should continue to evolve, providing deeper insights into the underlying mechanisms and guiding the practical application of nanofluids in EOR.
Data availability
No primary research results, software or code have been included and no new data were generated or analysed as part of this review.
Author contributions
Baoliang Peng: conceptualization, writing – original draft, supervision, funding acquisition. Han Gao: writing – original draft, writing – review & editing. Qiying Liu: writing – original draft, investigation. Ping Yi: supervision, funding acquisition. Yingying Li: supervision. Weidong Liu: resources, supervision. Ye Xu: resources, writing – review & editing, supervision, funding acquisition.
Conflicts of interest
There are no conflicts to declare.
Acknowledgements
This work was supported by the National Natural Science Foundation of China (NSFC 22008263, 11674019, and 12072010), PetroChina Basic Research and Strategic Reserve Technology Research Fund Project (2019D-500807), the Scientific Research and Technology Development Project of RIPED, PetroChina (YGJ2019-11-01), and Fundamental Research Funds for the Central Universities (YWF-22-K-101).
References
- V. Alvarado and E. Manrique, Energies, 2010, 3, 1529–1575 CrossRef
. - J. Wang, L. Yu and L. X. Huang, Pet. Sci. Technol., 2011, 29, 1504–1511 CrossRef CAS
. - F. S. Zhang, J. Ouyang, X. T. Ma, H. B. Zhang, D. W. Wang and X. F. Feng, Chem. Technol. Fuels Oils, 2012, 48, 202–207 CrossRef CAS
. - W. T. Zhang, Z. F. Ning, B. Zhang, Q. Wang, Z. L. Cheng, L. Huang, R. R. Qi and X. T. Shang, J. Pet. Sci. Eng., 2019, 180, 485–494 CrossRef CAS
. - G. Cheraghian and S. S. K. Nezhad, Pet. Sci. Technol., 2016, 34, 1397–1405 CrossRef CAS
. - M. Atilhan and S. Aparicio, J. Pet. Sci. Eng., 2021, 205, 108746 CrossRef CAS
. - L. Zhang, T. Petit, Y. Lu, B. E. Kratochvil, K. E. Peyer, R. Pei, J. Lou and B. J. Nelson, ACS Nano, 2010, 4, 6228–6234 CrossRef CAS PubMed
. - N. Lashari and T. Ganat, Chin. J. Chem. Eng., 2020, 28, 1995–2009 CrossRef CAS
. - A. J. Scott, L. Romero-Zeron and A. Penlidis, Processes, 2020, 8, 361 CrossRef CAS
. - M. Madani, G. Zargar, M. A. Takassi, A. Daryasafar, D. A. Wood and Z. Zhang, Fuel, 2019, 238, 186–197 CrossRef CAS
. - Y. Lu, Y. L. Zhu, Z. H. Xu and Q. X. Liu, Tenside, Surfactants, Deterg., 2019, 56, 407–416 CrossRef CAS
. - Q. F. Cui, S. S. Sun, Y. J. Luo, L. Yu and Z. Z. Zhang, Pet. Sci. Technol., 2017, 35, 2044–2050 CrossRef CAS
. - E. Jafarbeigi, A. Mohammadidoust and B. Ranjbar, Pet. Sci. Technol., 2022, 40, 1811–1828 CrossRef CAS
. - A. O. Gbadamosi, R. Junin, M. A. Manan, N. Yekeen, A. Agi and J. O. Oseh, J. Ind. Eng. Chem., 2018, 66, 1–19 CrossRef CAS
. - S. A. C. Natalya, G. T. M. Kadja, N. J. Azhari, M. Khalil and A. T. N. Fajar, Flatchem, 2022, 34, 100383 CrossRef CAS
. - Y. Pan, C. Zhang, S. Yang, Y. Liu and A. Muhammad, Nanotechnol. Rev., 2023, 12, 20220530 CrossRef CAS
. - R. Hosny, A. Zahran, A. Abotaleb, M. Ramzi, M. F. Mubarak, M. A. Zayed, A. E. Shahawy and M. F. Hussein, ACS Omega, 2023, 8, 46325–46345 CrossRef CAS PubMed
. - H. Farhangian, S. M. Abrishamifar, M. Palizian, M. J. Lariche and A. Baghban, Pet. Sci. Technol., 2018, 36, 287–292 CrossRef CAS
. - L. Hendraningrat and O. Torsaeter, Appl. Nanosci., 2015, 5, 181–199 CrossRef CAS
. - B. L. Peng, L. C. Zhang, J. H. Luo, P. M. Wang, B. Ding, M. X. Zeng and Z. D. Cheng, RSC Adv., 2017, 7, 32246–32254 RSC
. - B. L. Peng, J. T. Tang, J. H. Luo, P. M. Wang, B. Ding and K. C. Tam, Can. J. Chem. Eng., 2018, 96, 91–100 CrossRef CAS
. - K. Jiang, C. Xiong, B. Ding, X. Geng, W. Liu, W. Chen, T. Huang, H. Xu, Q. Xu and B. Liang, Energy Fuels, 2023, 37, 10045–10060 CrossRef CAS
. - Y. Ahmadi and S. M. A. Kariminia, J. Mol. Liq., 2023, 390, 123038 CrossRef CAS
. - M. S. Kamal, A. A. Adewunmi, A. S. Sultan, M. F. Al-Hamad and U. Mehmood, J. Nanomater., 2017, 2017, 2473175 Search PubMed
. - K. A. Hussain, C. Chen, R. Haggerty, M. Schubert and Y. S. Li, Ind. Eng. Chem. Res., 2022, 61, 17715–17734 CrossRef CAS
. - A. Keykhosravi, M. B. Vanani, A. Daryasafar and C. Aghayari, J. Mol. Liq., 2021, 324, 115093 CrossRef CAS
. - K. Wang, Q. You, Q.-M. Long, B. Zhou and P. Wang, Pet. Sci., 2023, 20, 382–395 CrossRef CAS
. - S. S. Ashrafmansouri and M. N. Esfahany, Int. J. Therm. Sci., 2014, 82, 84–99 CrossRef CAS
. - T. Liang, H. Wang and C. Yang, J. Mol. Liq., 2024, 397, 124043 CrossRef CAS
. - J. Zhao and D. S. Wen, RSC Adv., 2017, 7, 41391–41398 RSC
. - A. Rahman, PhD thesis, The University of Regina, Canada, 2023
. - S. Laibach, MSc thesis, State University of New York at Buffalo, 2023
. - G. A. Manjangkarani Giridharan, MSc thesis, State University of New York at Buffalo, 2023
. - M. B. Gawande, A. Goswami, F. X. Felpin, T. Asefa, X. X. Huang, R. Silva, X. X. Zou, R. Zboril and R. S. Varma, Chem. Rev., 2016, 116, 3722–3811 CrossRef CAS PubMed
. - A. Aziz, W. Jamshed, Y. Ali and M. Shams, Discrete and Continuous Dynamical Systems-Series S, 2020, 13, 2667–2690 Search PubMed
. - C. L. Zhang, L. C. Zheng, X. X. Zhang and G. Chen, Appl. Math. Model., 2015, 39, 165–181 CrossRef
. - X. Z. Wang, Y. R. He, X. Liu, L. Shi and J. Q. Zhu, Sol. Energy, 2017, 157, 35–46 CrossRef CAS
. - C. X. Wang, J. Yang and Y. L. Ding, Prog. Nat. Sci.: Mater. Int., 2013, 23, 338–342 CrossRef
. - K. S. Hong, T. K. Hong and H. S. Yang, Appl. Phys. Lett., 2006, 88, 031901 CrossRef
. - A. E. Bayat, R. Junin, A. Samsuri, A. Piroozian and M. Hokmabadi, Energy Fuels, 2014, 28, 6255–6266 CrossRef
. - S. Baek, D. Shin, G. Kim, A. Lee, J. Noh, B. Choi, S. Huh, H. Jeong and Y. M. Sung, Case Stud. Therm. Eng., 2021, 25, 100995 CrossRef
. - A. Komeilibirjandi, A. H. Raffiee, A. Maleki, M. A. Nazari and M. S. Shadloo, J. Therm. Anal. Calorim., 2020, 139, 2679–2689 CrossRef CAS
. - M. Zarringhalam, A. Karimipour and D. Toghraie, Exp. Therm. Fluid Sci., 2016, 76, 342–351 CrossRef CAS
. - H. M. Ali, H. Babar, T. R. Shah, M. U. Sajid, M. A. Qasim and S. Javed, Appl. Sci., 2018, 8(4), 587 CrossRef
. - L. Fedele, L. Colla and S. Bobbo, Int. J. Refrig., 2012, 35, 1359–1366 CrossRef CAS
. - A. Karimi, Z. Fakhroueian, A. Bahramian, N. P. Khiabani, J. B. Darabad, R. Azin and S. Arya, Energy Fuels, 2012, 26, 1028–1036 CrossRef CAS
. - X. Wang, L. He, P. Xue, Y. Feng, Y. Huang and X. Wang, Energy Fuels, 2024, 38, 7773–7785 CrossRef CAS
. - P. H. Shao, D. H. Liang, L. M. Yang, H. Shi, Z. S. Xiong, L. Ding, X. C. Yin, K. Zhang and X. B. Luo, J. Hazard. Mater., 2020, 387, 121676 CrossRef CAS PubMed
. - Z. Dong, L. Feng, Y. Hao, Q. Li, M. Chen, Z. Yang, H. Zhao and Z. Liu, Chem, 2020, 6, 1391–1407 CAS
. - A. Roustaei, S. Saffarzadeh and M. Mohammadi, Egypt. J. Pet., 2013, 22, 427–433 CrossRef
. - C. R. Miranda, L. S. de Lara and B. C. Tonetto, SPE International Oilfield Nanotechnology Conference and Exhibition, 2012, All Days, SPE-157033-MS, DOI:10.2118/157033-MS
. - T. Yousefi, E. Shojaeizadeh, F. Veysi and S. Zinadini, Sol. Energy, 2012, 86, 771–779 CAS
. - N. Domun, H. Hadavinia, T. Zhang, T. Sainsbury, G. H. Liaghat and S. Vahid, Nanoscale, 2015, 7, 10294–10329 RSC
. - K. A. P. Chandran, Universiti Teknologi PETRONAS, 2013 Search PubMed
. - K. Guo, H. L. Li and Z. X. Yu, Fuel, 2016, 185, 886–902 CrossRef CAS
. - M. Schneider, S. M. de Amorim, K. Cesca, J. da Silveira Salla, D. Hotza, E. Rodriguez-Castellon, R. A. Peralta and R. F. P. M. Moreira, J. Mol. Liq., 2023, 390, 123097 CrossRef CAS
. - X. Ma, H. Yang, X. Liu, L. Zeng, X. Li, L. Zheng, Y. Yang, L. Cao, W. Meng and J. Zheng, Polymers, 2024, 16(8), 1085 CrossRef CAS PubMed
. - Y. Mao, A. L. Lanzon, B. Zheng, Z. Xu, J. Jiang, D. Harbottle, K. Yu, M. Chen, Y. Sheng and H. Zhang, Polymers, 2023, 15(11), 2515 CrossRef CAS PubMed
. - H. Shen, Z.-H. Yang, G.-Z. Wang, Y.-L. Xiong, Q.-C. Lv, Q. Cao, Q.-Q. Niu, Y.-B. Wang and Z.-X. Dong, Pet. Sci., 2023, 20, 1584–1597 CrossRef CAS
. - K. R. Chaturvedi and T. Sharma, Mater. Today: Proc., 2021, 46, 5298–5303 CAS
. - W. Sun, H. Pu, D. Pierce and J. X. Zhao, Energy Fuels, 2023, 37, 16267–16281 CrossRef CAS
. - K. Abe, K. Negishi and H. Fujii, Energy Fuels, 2023, 37, 7122–7129 CrossRef CAS
. - J. Zhang, H. Huang, M. Zhang and W. Wang, RSC Adv., 2023, 13, 16165–16174 RSC
. - R. Fattahi, M. Lashkarbolooki, R. Abedini and H. Younesi, Energy Fuels, 2023, 37, 14741–14751 CrossRef CAS
. - K. Raghav Chaturvedi, R. Kumar, J. Trivedi, J. J. Sheng and T. Sharma, Energy Fuels, 2018, 32, 12730–12741 CrossRef CAS
. - K. R. Chaturvedi, J. Trivedi and T. Sharma, Energy, 2020, 197, 117276 CrossRef CAS
. - K. Y. Leong, R. Saidur, M. Khairulmaini, Z. Michael and A. Kamyar, Int. Commun. Heat Mass Transfer, 2012, 39, 838–843 CrossRef CAS
. - M. Parsazadeh, H. A. Mohammed and F. Fathinia, Int. Commun. Heat Mass Transfer, 2013, 46, 97–105 CrossRef CAS
. - A. M. Rashad, M. M. Rashidi, G. Lorenzini, S. E. Ahmed and A. M. Aly, Int. J. Heat Mass Transfer, 2017, 104, 878–889 CrossRef CAS
. - M. Sheikholeslami, M. Gorji-Bandpay and D. D. Ganji, Int. Commun. Heat Mass Transfer, 2012, 39, 978–986 CrossRef CAS
. - M. T. Jamal-Abad, A. Zamzamian, E. Imani and M. Mansouri, J. Thermophys. Heat Transfer, 2013, 27, 756–760 CAS
. - I. M. Mahbubul, E. B. Elcioglu, R. Saidur and M. A. Amalina, Ultrason. Sonochem., 2017, 37, 360–367 CrossRef CAS PubMed
. - Y. R. Sekhar and K. V. Sharma, J. Exp. Nanosci., 2015, 10, 86–102 CAS
. - T. P. Teng and Y. H. Hung, J. Exp. Nanosci., 2014, 9, 707–718 CrossRef CAS
. - S. Aberoumand and A. Jafarimoghaddam, J. Taiwan Inst. Chem. Eng., 2017, 71, 315–322 CrossRef CAS
. - H. A. Mohammed, A. A. Al-Aswadi, N. H. Shuaib and R. Saidur, Renewable Sustainable Energy Rev., 2011, 15, 2921–2939 CrossRef CAS
. - W. H. Fan and F. Q. Zhong, Thermochim. Acta, 2022, 712, 179229 CrossRef CAS
. - M. B. Xing, J. L. Yu and R. X. Wang, Int. J. Heat Mass Transfer, 2015, 88, 609–616 CAS
. - A. A. Minea, Curr. Nanosci., 2013, 9, 81–88 CAS
. - A. Kaushik, D. Joshi, R. K. Saw, K. B. Rathi, S. Mitra and A. Mandal, Fuel, 2024, 359, 130500 CAS
. - C. Y. Zhang, M. Oostrom, T. W. Wietsma, J. W. Grate and M. G. Warner, Energy Fuels, 2011, 25, 3493–3505 CAS
. - K. Sefiane, J. Skilling and J. MacGillivray, Adv. Colloid Interface Sci., 2008, 138, 101–120 CAS
. - E. Joonaki and S. Ghanaatian, Pet. Sci. Technol., 2014, 32, 2599–2607 CrossRef CAS
. - Z. Tohidi, A. Jafari and M. Omidkhah, Korean J. Chem. Eng., 2024, 41, 1077–1092 CrossRef CAS
. - H. Ma, M. X. Luo and L. L. Dai, Phys. Chem. Chem. Phys., 2008, 10, 2207–2213 RSC
. - B. Moradi, P. Pourafshary, F. Jalali, M. Mohammadi and M. A. Emadi, J. Nat. Gas Sci. Eng., 2015, 27, 64–73 CrossRef CAS
. - A. Maghzi, S. Mohammadi, M. H. Ghazanfari, R. Kharrat and M. Masihi, Exp. Therm. Fluid Sci., 2012, 40, 168–176 CrossRef CAS
. - L. O. Boampong, R. Rafati and A. S. Haddad, Fuel, 2023, 331, 125856 CrossRef
. - T. Sharma, S. Iglauer and J. S. Sangwai, Ind. Eng. Chem. Res., 2016, 55, 12387–12397 CrossRef CAS
. - S. Al-Anssari, M. Arif, S. Wang, A. Barifcani and S. Iglauer, J. Colloid Interface Sci., 2017, 508, 222–229 CrossRef CAS PubMed
. - S. Ahualli, G. R. Iglesias, W. Wachter, M. Dulle, D. Minami and O. Glatter, Langmuir, 2011, 27, 9182–9192 CrossRef CAS PubMed
. - R. S. Kumar, K. R. Chaturvedi, S. Iglauer, J. Trivedi and T. Sharma, J. Pet. Sci. Eng., 2020, 195, 107634 CrossRef CAS
. - K. R. Chaturvedi and T. Sharma, J. Pet. Sci. Eng., 2021, 196, 107704 CrossRef CAS
. - P. Pillai, R. K. Saw, R. Singh, E. Padmanabhan and A. Mandal, J. Pet. Sci. Eng., 2019, 177, 861–871 CrossRef CAS
. - L. M. Corredor, M. M. Husein and B. B. Maini, Ind. Eng. Chem. Res., 2019, 58, 9888–9899 CrossRef CAS
. - R. K. Saw, A. Singh, N. K. Maurya and A. Mandal, Colloids Surf., A, 2023, 666, 131308 CrossRef CAS
. - N. Pal, N. Kumar, R. K. Saw and A. Mandal, J. Pet. Sci. Eng., 2019, 183, 106464 CrossRef CAS
. - M. K. Chaudhury, Nature, 2003, 423, 131–132 CrossRef CAS PubMed
. - D. T. Wasan and A. D. Nikolov, Nature, 2003, 423, 156–159 CrossRef CAS PubMed
. - H. Zhang, A. Nikolov and D. Wasan, Energy Fuels, 2014, 28, 3002–3009 CrossRef CAS
. - P. X. Cui, W. W. Liang and B. C. Hou, Unconv. Oil Gas Resour.: Exploit. Dev., 2021, 8, 66 Search PubMed
. - P. C. Myint and A. Firoozabadi, Curr. Opin. Colloid Interface Sci., 2015, 20, 105–114 CrossRef CAS
. - R. A. Nasralla and H. A. Nasr-El-Din, SPE Asia Pacific Oil and Gas Conference and Exhibition, 2011, All Days, SPE-147937-MS, DOI:10.2118/147937-MS
. - U. Farooq, M. T. Tweheyo, J. Sjöblom and G. Oye, J. Dispersion Sci. Technol., 2011, 32, 519–531 CrossRef CAS
. - K. Kondiparty, A. D. Nikolov, D. Wasan and K. L. Liu, Langmuir, 2012, 28, 14618–14623 CrossRef CAS PubMed
. - Y. Y. Li, C. L. Dai, H. D. Zhou, X. K. Wang, W. J. Lv and M. W. Zhao, Energy Fuels, 2018, 32, 287–293 CrossRef CAS
. - D. Wasan, A. Nikolov and K. Kondiparty, Curr. Opin. Colloid Interface Sci., 2011, 16, 344–349 CrossRef CAS
. - S. Wu, A. Nikolov and D. Wasan, J. Colloid Interface Sci., 2013, 396, 293–306 CrossRef CAS PubMed
. - V. Bergeron, Doctoral, University of California, Berkeley, 1993 Search PubMed
. - T. D. Dimitrova, F. Leal-Calderon, T. D. Gurkov and B. Campbell, Langmuir, 2001, 17, 8069–8077 CrossRef CAS
. - T. D. Dimitrova, F. Leal-Calderon, T. D. Gurkov and B. Campbell, Adv. Colloid Interface Sci., 2004, 108, 73–86 CrossRef PubMed
. - A. Zou, S. Poudel, M. Gupta and S. C. Maroo, Nano Lett., 2021, 21, 7769–7774 CrossRef CAS PubMed
. - L. G. C. Pereira, C. Johansson, C. J. Radke and H. W. Blanch, Langmuir, 2003, 19, 7503–7513 CrossRef CAS
. - T. D. Dimitrova and F. Leal-Calderon, Adv. Colloid Interface Sci., 2004, 108, 49–61 CrossRef PubMed
. - A. Nikolov, K. Kondiparty and D. Wasan, Langmuir, 2010, 26, 7665–7670 CrossRef CAS PubMed
. - Y. Ma, M. Sun, X. X. Duan, A. van den Berg, J. C. T. Eijkel and Y. B. Xie, Nat. Commun., 2020, 11, 814 CrossRef CAS PubMed
. - S. I. Karakashev, A. V. Nguyen and E. D. Manev, J. Colloid Interface Sci., 2007, 306, 449–453 CrossRef CAS PubMed
.
Footnote |
† These authors contributed equally to this work and should be considered co-first authors. |
|
This journal is © The Royal Society of Chemistry 2024 |