DOI:
10.1039/D2SU00116K
(Critical Review)
RSC Sustain., 2023,
1, 665-697
Advancements in organic and inorganic shell materials for the preparation of microencapsulated phase change materials for thermal energy storage applications
Received
1st December 2022
, Accepted 3rd April 2023
First published on 4th April 2023
Abstract
The current generation is looking for new materials and technology to reduce the dependency on fossil fuels, exploring sustainable energy sources to maintain the future energy demand and supply. The concept of thermal energy storage through phase change materials (PCMs) has been explored by many researchers from academics and industry and exhibits promising progress in terms of development and application. PCMs can be microencapsulated to improve heat conductivity, lower leakage, and prevent possible environmental interactions. The most important methods for the preparation of microencapsulated phase change materials (MPCMs) are emulsion polymerization, suspension polymerization, interfacial polymerization, coacervation, and spray drying. Recent developments in organic and inorganic shell materials that are mechanically, chemically, and thermally stable, as well as being suitable for manufacturing MPCMs in applications for thermal energy storage, are highlighted and examined in this review. Melamine-formaldehyde resin, polyurethane, urea-formaldehyde resin, poly(methyl methacrylate), polystyrene, polyester, silica, calcium carbonate, titanium dioxide, alumina, and others are frequently used materials for the manufacture of the shell of MPCMs. Encapsulating PCMs in inorganic shells can improve their thermal performance because they are non-flammable and have higher thermal conductivity than polymeric shell materials.
Sustainability spotlight
Thermal energy storage with microencapsulated phase change materials is a very successful approach due to its capacity to store large amounts of solar thermal energy, simple synthesis process, improved thermal conductivity, wide operating temperature range, and the great possibility of clean energy storage and supply and so on. It has great importance for the production of clean energy. Therefore, we describe in this article the recent advances in developing various shell materials along with organic phase change materials, which are highly effective in storing solar thermal energy, reducing environmental pollution, and other multifunctional characteristics. This aligns with the UN Sustainable Development Goals, which include inexpensive, sustainable energy storage and supply and climate action.
|
1. Introduction
The demand for renewable energy sources is increasing due to the depletion of fossil fuels, the greenhouse effect, and rapid industrialization. Greenhouse gas emissions, climate change, global warming, and the shortage of supply of electrical energy are currently the biggest global issues, and they are unquestionably related to the usage of fossil fuels.1 Because of this, it is anticipated that a wide variety of renewable and sustainable energy sources, including wind, wave, biomass, and solar, will be used to meet the increased need for energy demand. A significant portion of this sustainable energy comes from solar energy, and the practical applications of solar energy are space heating, solar lighting, solar photovoltaic, and water desalination.2 Renewable energy has been used over the last three decades to reduce the dependence on fossil fuels and environmental pollution. Nowadays, renewable energy is used to generate electricity. But the availability of renewable solar energy depends on weather conditions, time, etc. So renewable energy conservation is essential to solve the above difficulties.3 However, as solar energy is unpredictable and irregular, it must be captured during times of sunlight and then released with great efficiency during non-solar hours. Therefore, several researchers from both academics and industry are focusing on new kinds of materials that can store renewable energies. Solar energy is popular clean energy that is abundant, cheap, and pollution-free.4–6 But the problem associated with renewable energy is that the availability of renewable energy is not continuous, as its supply depends on seasons and day–night cycles. Therefore, the storage of renewable energy like solar energy is required to resolve intermittent problems and maintain energy demand and supply. So the right type of material is needed to store thermal energy to meet energy requirements.7–10 The desired characteristics of thermal energy storage materials are large storage capacity per unit mass, high ability to undergo charging and discharge, stability in the operating temperature range, inexpensiveness, and long durability.11–14 PCMs can be utilized for solar thermal energy storage and were identified as a class of sustainable energy materials with ideal performance, high phase-change enthalpies, acceptable phase-change temperatures, reasonable cost, and modest volume change. Numerous organic fatty acids, inorganic salt hydrates, paraffin wax, and other natural materials could be used as solid–liquid PCMs for solar thermal energy storage applications.3,15–18
Since PCMs emit, absorb, and store a large amount of latent heat during a phase transition, they can be used in a wide range of applications, including construction materials, thermo-regulated textiles, medical equipment, heat sinks for electronics, and food packaging. As PCMs undergo solidification and melting, leakage is a concern. Furthermore, their supercooling tendency, poor conductivity, and corrosivity limit their direct use in actual applications.16–18 To address the problems associated with the use of PCMs in various applications, various confinement techniques, such as porous confinement, core–shell structures, and composites, have been developed. The microencapsulation process, in which tiny droplets are wrapped in a film-forming substance, is popular for producing core–shell capsules and provides a workable solution to the problems of PCMs such as leakage, volume change, and low heat-transfer area.19–21 The microencapsulation of PCMs is a process that uses a solid wall to completely encapsulate PCMs (organic, inorganic, or eutectic) for various applications. The primary function of PCM microencapsulation is to prevent PCM leakage, improve thermal conductivity, protect the core material from the external environment, and maintain mass and energy exchange between the core and the external environment for a longer time.11,12 Microcapsules made of PCMs are used to store thermal energy because they can store and release large amounts of latent heat when they go through a phase transition at a constant temperature.22 Microencapsulation provides a practical solution to PCM problems such as leakage issues, poor thermal conductivity, supercooling, and volume change. Despite the fact that a PCM without microencapsulation is a low-cost option, the long-term durability of unprotected PCMs and their negative effects on working systems are a concern. For example, the high alkalinity of materials has an effect on the stability of PCMs such as fatty alcohols and fatty esters. Furthermore, corrosive inorganic PCMs used in building temperature control may harm building materials, and organic PCMs are flammable and can burn, releasing toxic vapors. Furthermore, porous building materials containing PCMs may leak if the temperature rises above the melting point of PCMs.23,24
Organic, inorganic, and eutectic PCMs have high potential for application in sustainable energy systems such as thermal management, food packaging, and energy-efficient buildings, textiles, and goods transportation systems, and are expected to play an important role in future energy development and utilization due to their higher energy storage capacity. However, in practice, common organic PCMs have issues such as low thermal conductivity, structural instability, leakages, and poor mechanical properties. Extensive research has been conducted to address the difficult issues associated with PCMs used in sustainable energy applications, and positive progress in PCM microencapsulation and form-stable PCMs greatly promotes shape stability, reduces leakage issues, improves structural stability, and improves thermal conductivity. Several studies have found that PCM microcapsules have a high PCM content and a high energy storage capacity, as well as acceptable thermal conductivity and mechanical properties.23–26 A variety of PCM microcapsule preparation techniques with different organic shells (e.g., poly(methyl methacrylate), polystyrene, and melamine-formaldehyde polymers) and inorganic shell materials (e.g., silica, calcium carbonate, titanium dioxide, and aluminium hydroxide) were reviewed in this paper. In addition to thermal energy storage ability, particle size distribution, anti-leakage performance, and mechanical properties, the effects of a variety of inorganic nanoparticles, including zinc oxide, silica, titania, cadmium sulfide, graphene oxide, and graphene, were assessed in terms of their fluorescent, photocatalytic, thermal, and electrical conduction properties. The findings of this review are anticipated to offer suggestions for producing high-quality microencapsulated PCMs (MPCMs) and applying organic and inorganic shell-based MPCMs for thermal energy storage, as well as for controlling temperature and managing renewable energy sources.
2. Phase change materials for thermal energy storage
Generally, materials that undergo phase change under operating conditions are used as heat storage materials. Phase change materials (PCMs) exhibit a high heat of fusion, leading to storing a high amount of energy on the building surface. PCMs can be classified into three main categories: organics, eutectic, and inorganics (as shown in Fig. 1). Table 1 shows the most popular organic, inorganic, and eutectic PCMs that have recently been investigated as possible thermal energy storage materials. Paraffin, fatty acids, fatty alcohols, and fatty esters are the most commonly used organic PCMs for thermal energy storage and are readily available, non-toxic, and chemically stable.3,71 Paraffin is mainly a straight-chain alkane that is waxy, having a boiling point between 6 and 80 °C. Paraffin is the by-product of oil refining that is characterized by the formula of CnH2n+2. Most paraffins are inexpensive, readily available, non-toxic, and chemically inert. The melting point and the latent heat of the fusion of various paraffin changes depending upon the number of carbon atoms. Generally, fatty acids are non-paraffinic organic PCMs defined by the formula of CH3(CH2)nCOOH.3,71,72 Organic PCMs generate some toxic compounds such as aldehydes, ketones, and carboxylic acid in the presence of air, which can dissolve in organic PCMs and reduce the energy storage capacity, and phase change temperatures. Therefore, the coating materials that prevent the leakage of organic PCMs should prevent oxygen diffusion from air. Organic PCMs are the most preferred PCMs, but organic PCMs have some drawbacks, such as low thermal conductivity, slight stickiness, and solidification on heat transfer surfaces that limit their real application. To overcome these difficulties of organic PCMs, several researchers have tried to bind organic PCMs into a secondary supporting structure employing microencapsulation.72 Salts, metallics, and salt hydrates are typically included in the family of inorganic PCMs. Typically, an inorganic salt is represented as AxBy·n(H2O), where AxBy stands for chloride, nitrite, oxide, sulfite, acetate, phosphate, and carbonate, and n is the number of water molecules.73,74 Salt hydrates are ionic compounds that contain water crystallization within their lattices and are typically connected by hydrogen bonds or ion-dipole interactions. Compared to organic PCMs, inorganic PCMs have greater thermal conductivity and can operate at higher temperatures.75,76 Hydrated salts have attracted a lot of attention because of their many beneficial characteristics, including incombustibility, widespread availability, high phase transition enthalpy, recyclable nature, biodegradability, environmental friendliness, and low cost. On the other hand, inorganic PCMs degrade metals, raising expenses and reducing system longevity. In the temperature range of 8 °C to 120 °C, salt hydrate PCMs are suitable for usage. They can be applied in a variety of industries, including solar water heat recovery, textiles, and cold-chain logistics.77,78 Many salt hydrates in the market have the requisite latent heat and appropriate phase change temperatures. Supercooling, phase segregation, and other problems can affect the ability of inorganic PCMs like salts and salt hydrates to store energy.79,80 Although inorganic materials are promising and suitable for their use as PCMs for thermal energy storage, they currently face challenges in becoming successful commercial products because of their several drawbacks. One of the most challenging properties of inorganic salts is the change in volume during phase transition, and one weakness of this field is the lack of knowledge of the relationship between density and temperature.81,82 Once inorganic PCMs are melted, they start to flow; for this reason, it is essential to use appropriate PCM encapsulations to overcome leakage, contamination, and corrosion problems. Although several salt hydrates have been considered potential PCMs for thermal energy storage for building, transportation, and textile applications, organic PCMs have been preferred over inorganic PCMs because of the salt hydrates' shortcomings, including phase separation, supercooling, and instability. PCMs are used for storing thermal energy as they can store and release large amounts of latent heat when they undergo a phase transition at a constant temperature.22,83–86 The application of phase change conventionally storing thermal energy is not possible commercially due to the necessity of special latent heat devices, which increase the additional cost and high thermal resistance between the environment and PCMs.87 One of the most realistic energy storage technologies for resolving environmental problems and fossil fuel limits is thermal energy storage from sunlight. PCMs have gained interest as a new type of sustainable energy storage material because of their large latent heat storage capacity, phase change at a constant temperature, and low volume change. PCMs have earned attention as a new kind of sustainable energy storage material due to their phase change at a constant temperature, substantial latent heat storage capacity, little volume change, and acceptable thermal reliability.46,88,89 PCMs release, absorb, and store a large amount of latent heat over a specified temperature range while undergoing a phase transition, allowing them to be used in various applications, including building materials, thermo-regulated textiles, medicine, heat sinks for electronic devices, and food packaging.
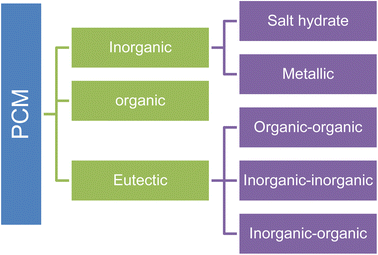 |
| Fig. 1 Classification of PCMs based on the type of material. | |
Table 1 Summary of PCMs utilised to store thermal energy
Organic PCMs |
Inorganic PCMs |
Eutectic PCMs |
Capric acid27,28 |
KOH29 |
LiOH–KOH30 |
Stearic acid31 |
CaCl2·6H2O32 |
Capric acid–palmitic acid–stearic acid33 |
Paraffin wax19,34,35 |
CaCl2·12H2O36 |
CaCl2·6H2O–SrCl2·6H2O37 |
Butyl stearate38 |
Na2CO3·10H2O39 |
CaCl2·6H2O–MgCl2·6H2O40 |
Hydroxystearic acid41 |
Na2HPO4·12H2O42 |
MgCl2·6H2O–Mg(NO3)2·6H2O43 |
Lauric acid44 |
LiNO3·3H2O45 |
Octadecane–heneicosane46 |
n-Hexadecane47,48 |
LiClO3·3H2O49 |
Myristic acid–palmitic acid eutectic50 |
1-Dodecanol46 |
Zn(NO3)2·6H2O3 |
CaCl2·6H2O-8 wt% Mg(NO3)2·6H2O4 |
n-Octadecane51 |
FeBr3·6H2O22 |
Capric acid–steric acid52 |
PEG-6000 (ref. 53 and 54) |
MgCl2·6H2O55,56 |
Methyl stearate–cetyl palmitate57 |
PEG-8000 (ref. 58 and 59) |
LiNO3·3H2O60 |
Octadecane–docosane61 |
Palmitic acid62 |
CaBr2·6H2O3 |
Capric acid–myristic acid63 |
Propyl palmitate64 |
Na2SO4·10H2O65 |
Octadecane–stearic acid66 |
Lauryl alcohol67 |
LiBO2·8H2O64 |
Capric acid–steric acid61 |
Polyglycol E 2000 (ref. 68) |
Na2HPO4·12H2O69 |
Acetanilide–benzoic acid70 |
3. Microencapsulation of organic phase change materials
Microencapsulation is a process where droplets of liquids, gases, and solids as the core material are coated with thin films (coatings) that protect the core material. The National Cash Register started encapsulation in 1930 for commercial application in carbonless copy paper.101 Microencapsulation has recently become a popular method for creating PCM microcapsules, in which small PCM droplets are covered with an organic, inorganic, or composite film-forming substance. It offers a practical answer to the problems that PCMs are known for, such as leakage avoidance, volume control during phase transition, and reduced heat-transfer area.19–21 Recently, the process of microencapsulation has been investigated in various fields, such as the food, coating, pharmaceutical, and biomedical industries, to encapsulate PCMs for developing better thermal management systems. Using microencapsulated PCMs has several benefits, including increased chemical stability, a larger area for heat transmission, a higher heat transfer rate, better volume control during phase transition, and minimal leakage issues. Many research studies have discussed the numerous forms of microencapsulated PCMs (MPCMs), and among them, the most frequently utilized organic PCMs are paraffin wax, fatty esters, fatty alcohols, and fatty acids.45,102–104 The leakage of PCMs used in thermal energy storage applications is a problem since they solidify and melt repeatedly. Furthermore, their corrosiveness, poor conductivity, and tendency to supercool limit their direct use in practical applications.16–18 Therefore, different confinement strategies for enclosing PCMs, such as porous confinement, core–shell structure, and composites, have emerged to overcome the problems of PCMs utilized in diverse applications. Several researchers developed a new type of material called the microcapsule of PCMs for the utilization of PCMs in the thermal energy storage system; a new type of material called the microcapsule of PCMs has been developed by a combination of a PCM and wall-forming material that completely covers the PCM.87,105 The main functions of microencapsulation are to provide the solution for preventing the leakage of the melted PCM, reduce the interaction of the PCM with the outside environment, increase the heat transfer rate, and control the volume change of the PCM during phase change.105,106 PCMs undergoing a solid-to-liquid phase transition from −10 °C to 80 °C are used for microencapsulation. Recently, many scientists from academics, industries, and research centers have shown interest in PCMs exhibiting a large heat of fusion and sharp melting points to store thermal energy, which exhibits promising progress in development and application.107–109 The concept of phase-changing materials to store thermal energy is not new, and this has been used for over a decade in building applications, and now they have replaced many traditional materials.109,110 Numerous researchers have extensively investigated the PCM properties, applications, and characterization.22 A higher amount of energy is necessary to meet the continuous demand for human comfort by using fossil fuels, which are non-renewable and have limited availability.111 A MPCM is composed of core and shell materials, whereas the core is PCMs. The shell is either polymeric or inorganic materials to prevent PCM leakage and maintain shape during the phase change process.3,111,112Table 2 summarises the procedures that are routinely used to produce different MPCMs utilizing common PCM core materials and shell materials. In situ polymerization,28,113 emulsion polymerization,16,46 complex coacervation,21 Pickering emulsion polymerization,18,114,115 interfacial polymerization,19,20 sol–gel,116 microfluidic method,117 and other synthesis strategies were used to create microcapsules. In the last three decades, many research papers have been published on the encapsulation of PCMs for thermal energy storage using a variety of polymers as shell-forming materials. The overall performance of MPCMs in thermal energy storage greatly depends on the characteristics of the shell materials.118 The desired characteristics of a good wall material of MPCMs are high thermal conductivity to maintain sufficient heat exchange, good mechanical strength to prevent the PCM core from leakage, inert nature to prevent any reaction with the core material, and good anti-osmosis properties.119–121 Many materials, including synthetic polymers, bio-based polymers, inorganic materials, composites, and metals, have been explored as wall materials for the microencapsulation of PCMs. Generally, chemically, mechanically, and thermally stable polymers under operating conditions with low cost and easy availability are used as shell materials for preparing MPCMs. The commonly used polymers for the preparation of the shell of MPCMs are melamine-formaldehyde (MF) polymer,122 polyurethane,120 urea-formaldehyde (UF) polymer,123 poly(methylmethacrylate) (PMMA),124 polystyrene (PS),125 polyester,122 polyurea (PU),126 silica,127,128 calcium carbonate,46,47 titanium dioxide,129 and others. In order to overcome these difficulties of organic PCMs, a number of researchers have tried to encapsulate organic PCMs into these organic and inorganic shell materials as secondary supporting structures by means of microencapsulation.72 In addition, organic PCMs generate some toxic compounds such as ketones, carboxylic acid, and aldehydes in the presence of air that can dissolve in organic PCMs and reduce the energy storage capacity and phase change temperature. Therefore, the coating materials that prevent the leakage of organic PCMs should prevent oxygen diffusion from air. For example, Wang et al.130 reported a stearic acid–based microencapsulated PCM for latent heat thermal energy storage in a building using stearic acid as the core material and PMMA as the shell material showing a stable microcapsule morphology with 51.8% of the PCM encapsulated into the microcapsule.130 The MPCM showed the ability to store a large amount of energy when they undergo phase change at a nearly constant temperature. The greater surface area with smaller enclosures facilitates heat transmission, increasing its usefulness by many orders of magnitude. The use of the microencapsulation process, which focused on the materials' mechanical, thermal, and chemical properties without ignoring leakage issues, was used to enclose PCMs in small containers. The composition of the shell material affects thermal performance; for instance, a shell with improved temperature conductivity would enable capsules to react quickly to thermal environmental changes and function as an effective energy storage/discharge device.4,5,7–9
Table 2 Few studies on different MPCM preparation methods
Shell material (organic/inorganic) |
PCM |
Synthesis process |
Ref. |
Poly(melamine-urea-formaldehyde) |
Pentadecane |
In situ polymerization |
90
|
Poly(methyl methacrylate) |
n-Octadecane |
Suspension polymerization |
91
|
Polystyrene |
Paraffin wax |
Pickering emulsion |
1
|
Silica |
n-Octadecane |
Spray drying |
92
|
Silica |
Na2HPO4·12H2O |
Inverse emulsion interfacial |
85
|
Silica |
n-Octadecane |
Sol–gel |
93
|
Poly(urea-formaldehyde) |
CrodathermTM60 |
Interfacial polymerization |
|
Silica |
Stearyl alcohol |
Sol–gel |
94
|
Poly(urea-formaldehyde) |
Paraffin wax |
In situ polymerization |
95
|
Polystyrene |
Lauric acid |
Emulsion polymerization |
96
|
Poly(melamine-formaldehyde) |
Paraffin |
In situ polymerization |
97
|
Poly(melamine-formaldehyde) |
n-Tetracosane |
In situ polymerization |
98
|
Chitosan |
Poly(octadecyl acrylate) |
Coacervation |
99
|
Polyurethane |
Butyl stearate |
Interfacial polymerization |
38
|
Poly(melamine-urea-formaldehyde) |
Paraffin |
In situ polymerization |
100
|
Organosilica |
Palmitic acid/myristic acid |
Sol–gel |
50
|
4. Melamine-formaldehyde polymer-based shells for MPCMs
Generally, melamine-formaldehyde polymer shows good mechanical strength, high thermal stability, excellent chemical resistance, and good fire resistance due to its highly cross-linked structure. Therefore, microcapsules with the melamine-formaldehyde wall material show good thermal, chemical, and mechanical properties.121,131,132 The preparation of the PCM microcapsule with the melamine-formaldehyde shell material via the in situ polymerization technique is a three step process. In the first step, oil in water emulsion is prepared with a phase change material using a suitable surfactant. In the second step, the melamine-formaldehyde prepolymer is prepared in an aqueous phase using melamine and formaldehyde as monomers. In the third step, a condensation reaction takes place at 70–80 °C for 1–3 hours to form the shell material on the core material under acidic conditions. Finally, filtration separates the resulting microcapsules from the emulsion.67,69,119,133,134 One of the drawbacks of the melamine-formaldehyde shell prepared by the in situ polymerization technique is the presence of free formaldehyde, which creates health and environmental problems. In order to resolve this issue, excess melamine or urea should be used which reduces the excess formaldehyde.118,120,131,135 Zhu et al.136 prepared a dodecane microcapsule with the melamine-formaldehyde wall material via the in situ polymerization method. Dodecane was dispersed in water using styrene-co-maleic anhydride polymer as a surfactant, and the melamine-formaldehyde prepolymer was prepared by mixing formalin and melamine in distilled water. The resulting microcapsule size was from 330 nm to 15.69 μm. According to their observation, the particle size of the microcapsule is the function of the stirring speed, and the particle size decreased with increasing stirring speed.137 Choi et al.137 prepared a MPCM using melamine-formaldehyde resin as the wall material and tetradecane as the core material by the in situ polymerization method. According to their research study, the particle size of the microcapsules depends on the mixing speed. The prepared microcapsules exhibited excellent latent heat storage capacity, durability, and good thermal stability and can be used for thermal energy storage. Li et al.135 synthesized a MPCM taking n-octadecane as a core, and melamine-formaldehyde resin as a shell material through in situ polymerization and found that the thermal stability of the synthesized microcapsule increased with reducing dropping rate of the melamine-formaldehyde prepolymer due to the formation of a smooth microcapsule surface. Zhang et al.138 prepared a MEPCM using melamine-formaldehyde (MF) resin (as illustrated in Fig. 2a0) and suggested that the mechanical properties such as brittleness and toughness of the microencapsulated phase change material can be improved by modification of MF resin using resorcinol. They also reported that the efficiency of the encapsulation increases by using a sodium salt of the styrene-maleic anhydride (SMA) copolymer as an emulsifier that helps to develop the spherical shape of the synthesized microcapsules. The SEM images of the microcapsules created utilising sodium dodecyl sulphate (SDS) and SMA as surfactants are shown in Fig. 2a–f. As can be seen in Fig. 2a–c, the microcapsules created by using the SMA surfactant have a smooth surface and a consistently spherical form. In the SDS-prepared samples, the microcapsules retain their spherical shape, but their surfaces are rather rough (as seen in Fig. 2d–f) melamine-formaldehyde copolymer nanoparticles flocculate on the surfaces of the microcapsules.
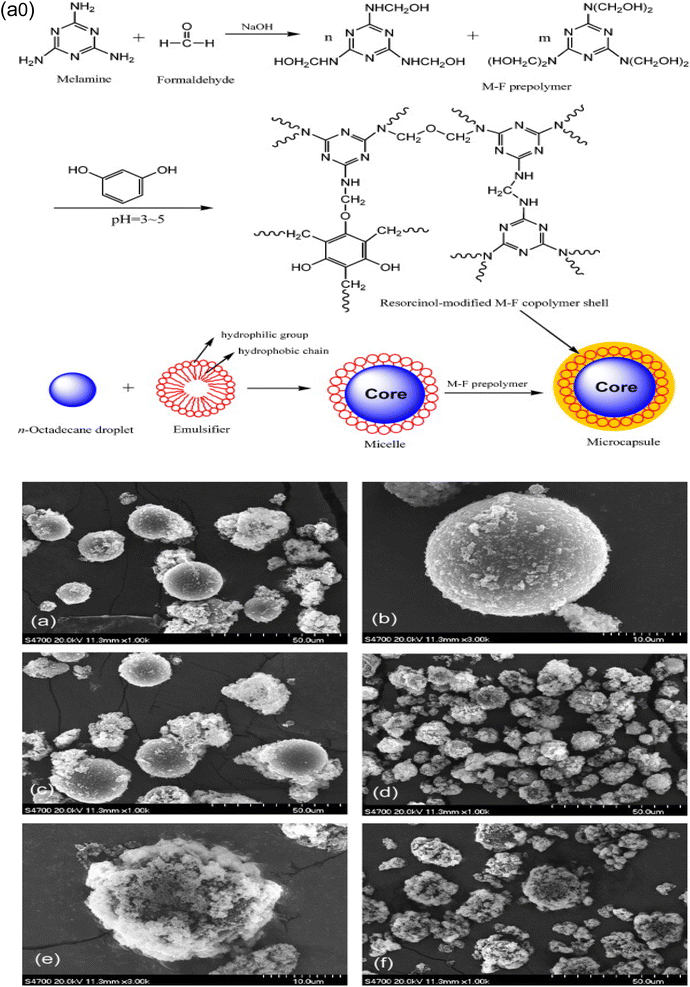 |
| Fig. 2 (a0) Schematic illustration of the preparation of the MPCMs based on an octadecane core and modified MF-based shell, and SEM pictures of the microcapsules with various weight ratios of core/shell materials; (a) and (b) 65/35 (c) 75/25 using SMA as a surfactant, (d) and (e) 70/30 and (f) 75/25 using SDS as a surfactant.138 Reproduced with permission from ref. 138. Copyright 2019 Elsevier. | |
Cao and co-workers68 prepared microcapsules using MF resin as a shell material, n-octadecane as a core material, and sodium dodecyl sulfate as an emulsifier through in situ polymerization. According to their study, the supercooling of the phase change material can be suppressed by optimizing the composition of the melamine-formaldehyde shell without adding any nucleation agent. Su and colleagues69 also improved the mechanical and thermal properties of microencapsulated lauryl alcohol with a double-layered shell made of MF and UF-based polymers. Therefore, many research studies have explored the process of synthesis, controlling the microstructure, latent heat storage, and applications of MPCMs based on MF polymer as a shell material. In situ polymerization is a commonly used technique for preparing MPCMs, where shell materials are based on MF polymer and UF polymer. MF and UF polymer-based shells exhibit good thermal and mechanical stability after forming three-dimensional crosslinked thermoset polymers. The typical steps of the synthesis of a MPCM through the in situ polymerization technique include the preparation of the pre-polymer solution, formation of oil/water emulsion using a suitable emulsifying agent, synthesis of microcapsules mixing the prepolymer into the oil/water emulsion, and separation of microcapsules from the emulsion.69,119,133,134 In general, an emulsifying agent is required for in situ polymerization for encapsulating phase change materials. The encapsulation of 1-dodecanol using various emulsifiers has been reported in several studies. Most research groups used styrene-maleic anhydride copolymer as an emulsifier, but its high-cost relative leads to high-priced microcapsules, limiting their use. In a study, 1-dodecanol microcapsules with a poly(melamine-paraformaldehyde) shell material were created using Pickering emulsion employing nano-TiO2 without using any emulsifier (as shown in Fig. 3a), in which the shell material itself acts as an emulsifier.139Fig. 3(S1–S6) show the surface morphologies of microcapsules created using a Pickering emulsion technique and TiO2 nanoparticles. According to SEM pictures, microcapsule sizes varied in a wide range due to the non-uniform dispersion of PCM droplets in the continuous water phase at a low rpm. Raspberry-like morphologies were seen on the outside of the microcapsules, and a higher core-to-shell ratio decreased the number of protruded spherical shapes of the microcapsules. In the microcapsules generated using Pickering emulsion, the encapsulation ratio and enthalpy content of surfactant-free microcapsules were 87.64% and 167.68 J g−1, respectively. The synthesized microcapsules were anticipated to find use in smart buildings, waste heat management, etc., due to their high latent heat capacity, melting temperature in the human comfort range, and thermal buffering capability.
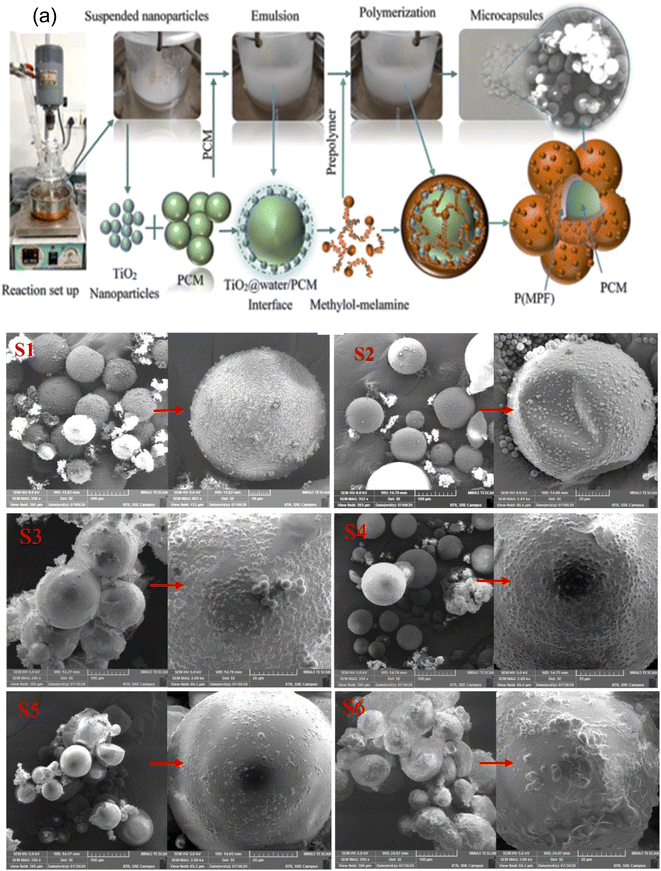 |
| Fig. 3 (a) Schematic illustration of synthesis steps of PCM (1-dodecanol) microcapsules with the MF polymer shell material through Pickering emulsion using nano-TiO2, Pickering emulsion-based microcapsules' FE-SEM images, (S1) synthesized with a core to shell ratio of 1 : 1.25, (S2) synthesized with a core to shell ratio of 1 : 1, (S3) synthesized with a core to shell ratio of 1.25 : 1, (S4) synthesized with a core to shell ratio of 1.5 : 1, (S5)synthesized with a core to shell ratio of 2 : 1, and (S6) synthesized with a core to shell ratio of 2.5 : 1.139 Reproduced with permission from ref. 139 Copyright 2018 Elsevier. | |
One of the main challenges of MEPCMs for commercial applications in the field of solar energy storage is leakage. If the capsule shell is not strong enough, the melting core material in the MEPCM may leak through the holes of the microcapsule. The development of composite shells using melamine-formaldehyde (MF) resin might significantly lessen the leakage issues that have been studied by numerous researchers. The leakage rate test revealed that MEPCMs with 0.2 wt% graphene had a 93.20% lower leakage rate than MEPCMs without graphene.140 When graphene stabilized the oil phase, the MF shell was synthesized on the top of the core PCM, and the generated MPCM had a MF and graphene double-shell structure, as shown in Fig. 4a0. Fig. 4(a–l) depict the shape of MPCMs with various graphene concentrations. When graphene was absent, the MPCM displayed a smooth surface, and the MPCM showed a near-spherical shape. As the graphene concentration increased, there was a discernible difference between the MPCMs, and the surfaces of the MPCMs with increasing graphene concentration became rougher.
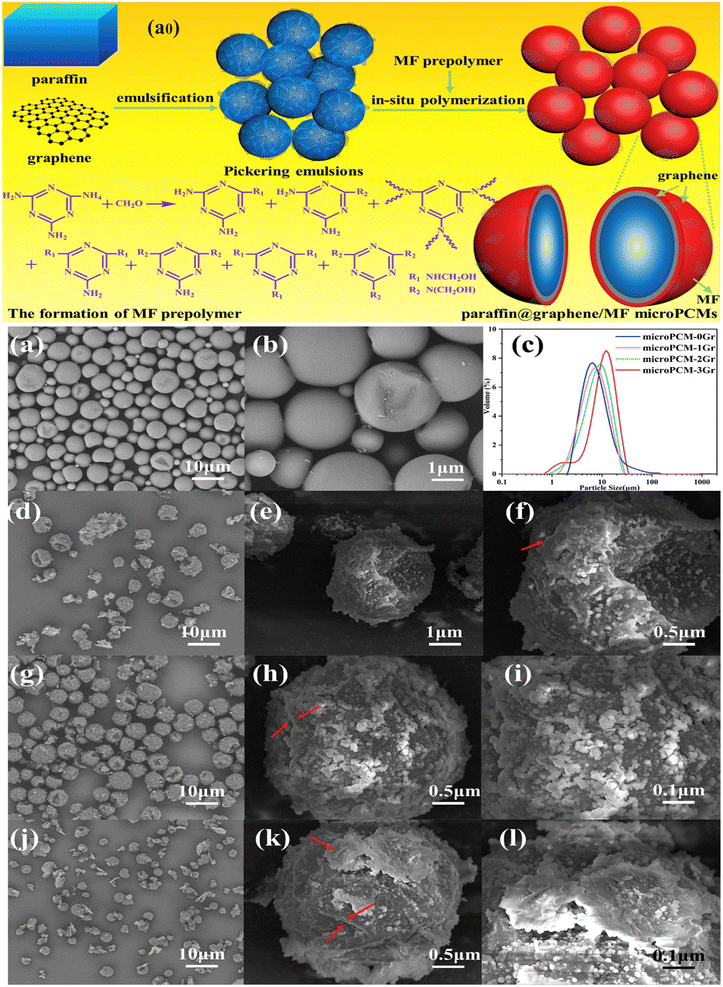 |
| Fig. 4 (a0) Schematic illustration of the preparation of the EPCM of paraffin@graphene/MF micro-PCMs by using the Pickering emulsion technique, SEM images of (a and b) the MPCM containing no graphene in the polymeric shell (microPCMs-0Gr), (d–f) the MPCM containing 1 wt% graphene (microPCMs-1Gr), (g–i) the MPCM containing 2 wt% graphene (microPCMs-2Gr), and (j–l) the MPCM containing 3 wt% graphene (microPCMs-3Gr), and (c) particle size distribution of the MPCMs.140 Reproduced with permission from ref. 140 Copyright 2019 Elsevier. | |
PCM microcapsules' shape, size, and morphology are critical for their functional effectiveness in thermal energy storage applications. However, the difficulty of producing PCM microcapsules with inexpensive and simple techniques is the key bottleneck for applications. Complex polymeric microstructures are being developed due to their high demand in several applications. For their functional efficiency and diverse applications, the size and morphology have significant importance. However, the development of quick, low-cost, and adaptable methods for creating microcapsules with a regulated morphology continues to be a barrier to advancements in the field of polymer colloids. A novel technique for producing complex polymeric microstructures using melamine derivatives with titanium dioxide nanoparticles with hexadecane cores was disclosed in a recent study.141 Composite shell structures were synthesized in a simple, inexpensive approach employing titanium dioxide nanoparticle embedded poly(melamine-urea-formaldehyde) (PMUF), where hexadecane was used as the core material. There are three main steps (MUF prepolymer, a stable oil in water Pickering emulsion, and shell formation on PCM) involved in the manufacture of TiO2-embedded PMUF microcapsules. The in situ polymerization process was used to construct diverse morphologies. The findings revealed that particle morphologies are beneficial in creating sophisticated functional materials, which can be used as latent heat storage materials and carriers for controlled release applications. Variations of different factors (e.g., composition, reaction conditions, etc.) were used to create and control the morphology of a complex PMUF composite shell-based microcapsule. Titanium dioxide nanoparticles were used to create a variety of microstructures and morphologies with particle diameters ranging from 5 to 20 μm. Fig. 5a shows the process used (preparation of MUF prepolymer, preparation of stable Pickering emulsion, and shell formation) to create poly(melamine-urea-formaldehyde) composite shell-based microcapsules with distinct morphologies. Smooth, hollow, raspberry-like, partially budded, single-holed, and closed-cell-like microstructures resulted from careful manipulation of shell components (i.e., PMUF and nano-TiO2) and reaction conditions. The content of titanium dioxide nanoparticles, the copolymer components, the core-to-shell ratio, the pH value, and the conversion efficiency affected particle attributes like the morphology, shell thickness, and size. The morphology of the microcapsules at different shell to core ratios that resemble a budded morphology is shown in Fig. 5(a1–e3).
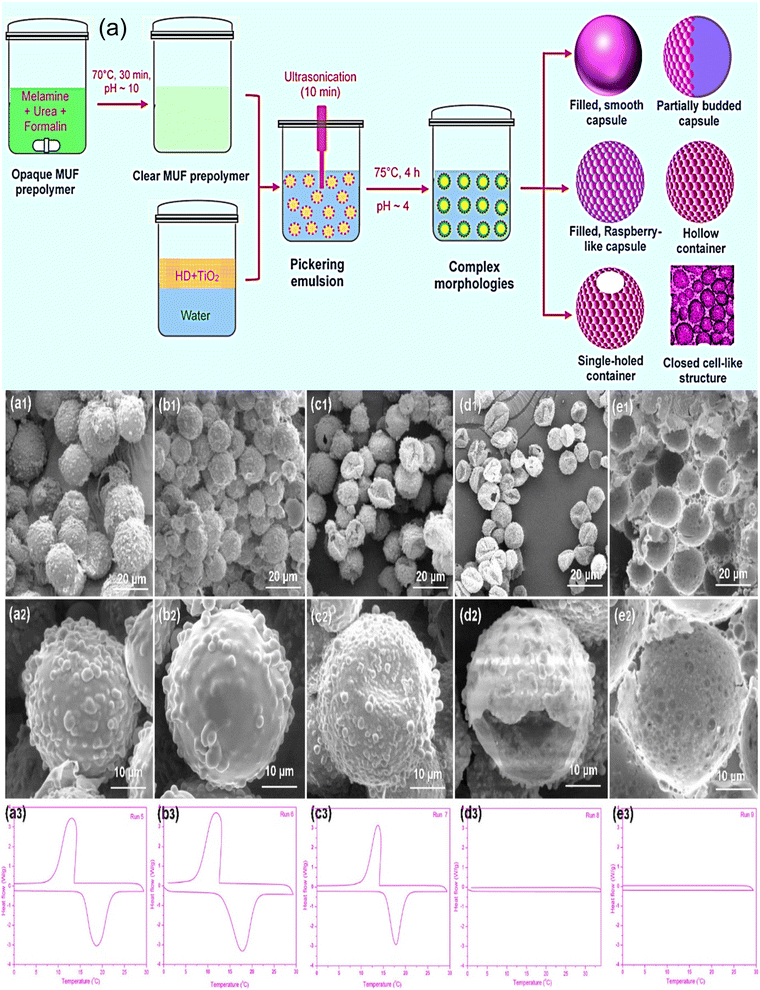 |
| Fig. 5 (a) Schematic illustration steps involved in creating a complex structure of TiO2/polyMUF microcapsules with distinct morphologies, DSC thermograms, and SEM images of the microcapsules at different core-to-shell ratios, (a1–a3) core-to-shell ratio of 1 : 2, (b1–b3) core-to-shell ratio of 1 : 1, (c1–c3) core-to-shell ratio of 1 : 0.5, (d1–d3) core-to-shell ratio of 1.5 : 1, and (e1–e3) core-to-shell ratio of 2 : 1.141 Reproduced with permission from ref. 141 Copyright ACS 2022. | |
5. Polystyrene-based shell materials for MPCMs
Polystyrene (PS) is a commercially available polymer that is broadly used in the synthesis of EPCMs because of its characteristics of good mechanical properties, chemical properties, thermal stability, non-toxicity, cost-effectiveness, and easy fabrication technique. Mochane et al.142 developed a microencapsulated paraffin core using polystyrene as a shell material through the emulsion polymerization technique, and the prepared microcapsules exhibited excellent latent heat storage properties when embedded in the polypropylene matrix. Sánchez et al.143 synthesized microencapsulated paraffin using polystyrene as the wall material through the suspension polymerization technique and explored the effect of the mass ratio of paraffin wax to styrene, stirring rate, and reaction temperature on the properties of the prepared microcapsules. Emulsion polymerization is discovered to be the most popular encapsulation method for poly(styrene) shell-based MPCMs due to its simplicity of synthesis, absence of toxic organic solvents, and capacity to produce polymeric shells with desired mechanical properties along with the inexpensive nature of synthesis. There are a few reports on the polystyrene shell's encapsulation of renewable PCMs. Through the use of the thermal buffering effect in packaging and the emulsion polymerization process, Ünal and colleagues144 described microencapsulating octanoic acid with a polystyrene shell through the emulsion polymerization process. In recent work, lauryl alcohol (1-dodecanol) was microencapsulated using a polystyrene-based copolymer shell that was produced via emulsion polymerization.46Fig. 6a shows a schematic representation of the copolymerization of styrene, divinyl benzene, and butyl acrylate that takes place during the microencapsulation of 1-dodecanol and the related process conditions. To choose the applications for the synthesized MEPCMs, it is essential to understand their surface morphology. To investigate the morphology of the MPCM, MEPCM-embedded poly(vinyl chloride) (PVC) film and pure PVC film, FESEM images (as shown in Fig. 6(b–d)) were used. After being covered with a PVC film, micro-PCM was tested for its thermal buffering ability. Because of their ability to store enthalpies, the synthetic PVC sheets with the MEPCM embedded in them can be used to create multilayer garments like vests and coats that provide thermal comfort and act as thermal buffers. This can also serve as a coating for automotive roofs, absorbing heat energy that enters the vehicle. Thus, the microcapsule containing dodecanol and its suggested applications are considered to motivate further study into a wide range of applications.
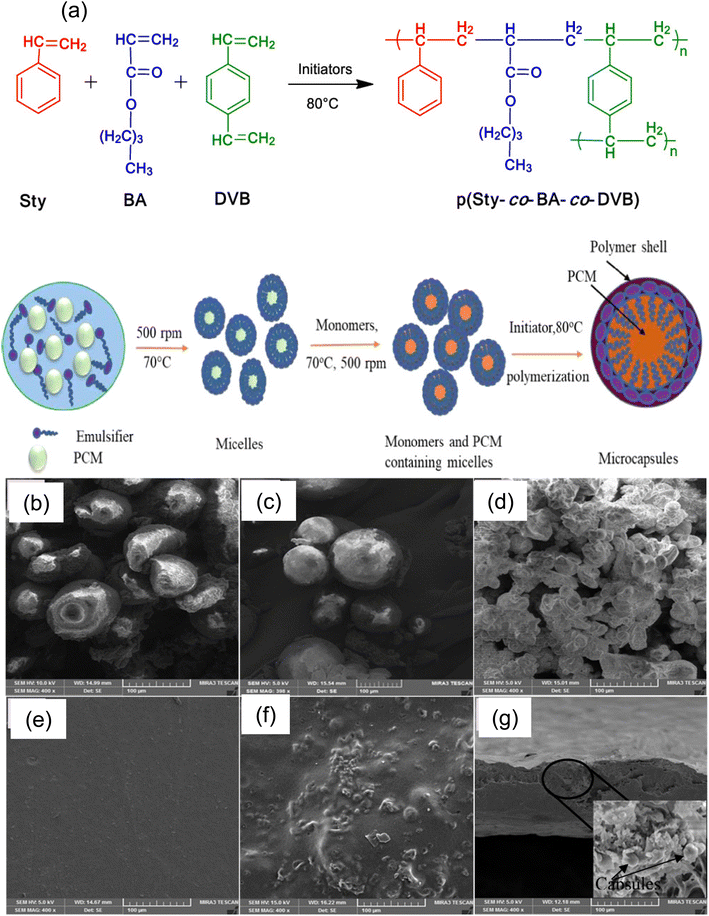 |
| Fig. 6 (a) Schematic diagram of copolymerization of styrene, divinyl benzene, and butyl acrylate that takes place during the microencapsulation of dodecanol, FESEM pictures of MPCM microcapsules, (b) microcapsules with a core : shell ratio of 0.75 : 1, (c) microcapsules with a core : shell ratio of 1 : 1, (d) microcapsules with a core : shell ratio of 1.5 : 1, (e) surface of the pure PVC film, (f) surface microcapsule (with a core : shell ratio of 1.5 : 1)-embedded PVC, and (g) cross section of surface microcapsule (with a core : shell ratio of 1.5 : 1)-embedded PVC.46 Reproduced with permission from ref. 46 Copyright 2020 ACS. | |
Among the many microcapsules that have been produced for thermal energy storage applications, a large amount of study has gone into creating multifunctional microcapsules with a crosslinked polystyrene shell. Three strategies can be used to achieve multifunctionality of polystyrene-based shell materials (i) using unique shell materials, (ii) inserting nanoparticles into the shell, and (iii) customizing the capsule morphology.117,145,146 Such microstructures offer a fantastic opportunity to combine different features in one substance, while also investigating a wide range of novel applications. Different types of inorganic nanoparticles, including zinc oxide, silica, silver, silicon nitride, graphene oxide, cadmium sulfide, iron oxides, etc., have been incorporated into the polymeric shell materials of MPCMs to impart properties like fluorescence, photocatalysis, magnetic, thermal conduction, antibacterial, photothermal conversion, and electrical conduction besides their thermal energy storage ability.147,148 In a recent research report, the synthesis of bifunctional microcapsules for photocatalysis and thermal energy storage that have a hexadecane core and a poly(4-methylstyrene-co-divinylbenzene)/TiO2 shell has been described.47 PCM-containing microcapsules with poly(4-methylstyrene-co-divinylbenzene) shells that were decorated with titanium dioxide nanoparticles were produced. The polymerization of 4-methylstyrene and divinylbenzene monomers with TiO2 nanoparticles was carried out to encapsulate hexadecane, as shown in Fig. 7. The FESEM image of TiO2 decorated PCM microcapsules (Fig. 8c) was used to determine the surface morphology and the synthesized microcapsules were discovered to have a clearly defined spherical shape without any indication of stickiness. The TiO2 decorated polymeric shell-based MPCM with 2.6 wt% TiO2 showed a maximum phase change enthalpy of 174 J g−1 and an encapsulation efficacy of 76.6%. According to differential scanning calorimetry (DSC) experiments, the performance could be maintained even after 100 melting–freezing cycles. After the 100th cycle, DSC thermograms (Fig. 8a) showed minimal variations in melting/freezing temperature values of 0.2 °C between the first and 100th cycles. The MPCMs containing 2.6 wt% TiO2 demonstrated high photocatalytic activity and exhibited methylene blue solution discoloration features with time as shown in Fig. 8b. Electronic transition in the chromogenic groups of methylene blue caused the absorption under the UV-visible irradiation peak. An absorption peak that diminished with time served as a sign that the concentration of methylene blue was decreased due to photodegradation.
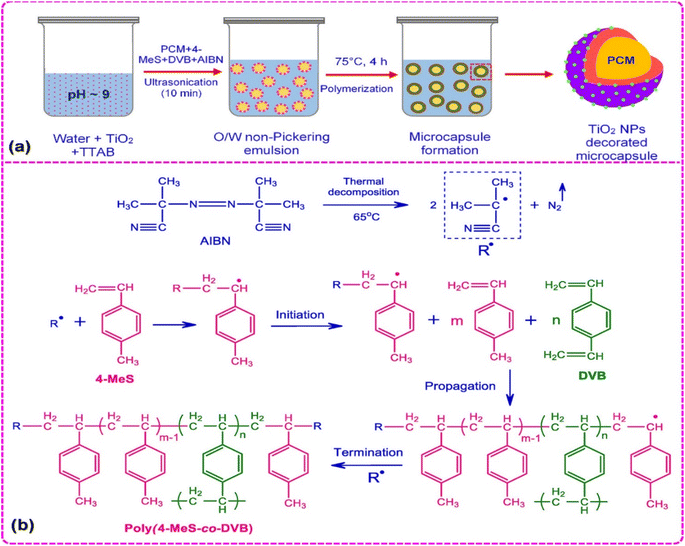 |
| Fig. 7 (a) Schematic illustration for the creation of a crosslinked polystyrene-based shell decorated with TiO2 nanoparticles and (b) free radical polymerization for the creation of the poly(4-methylstyrene-co-divinylbenzene) shell.47 Reproduced with permission from ref. 47. Copyright 2021 ACS. | |
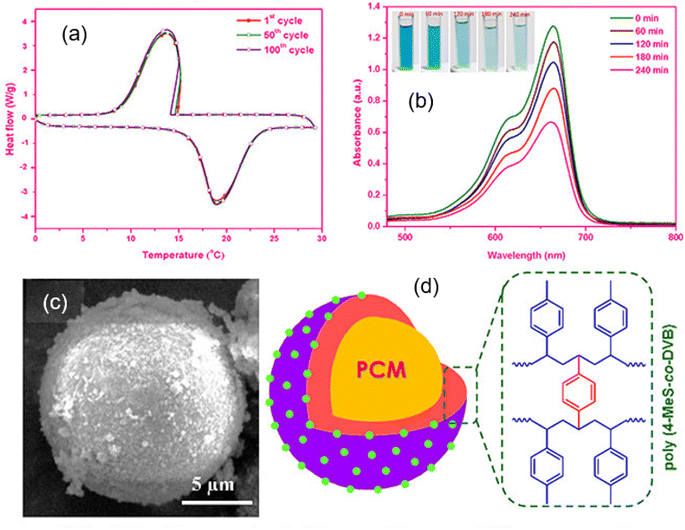 |
| Fig. 8 (a) DSC thermograms of the MPCM [with a TiO2 decorated poly(4-methylstyrene-co-divinylbenzene) shell and hexadecane PCM] showing thermal cycling capability with 2.6 wt% TiO2, (b) UV-visible absorbance spectra of the MPCM sample containing 2.6 wt% TiO2, (c) SEM image of the MEPCM, and (d) schematic illustration of the chemical structure of the polymer employed to prepare the MPCM with the decoration of TiO2 into the shell. Reproduced with permission from ref. 47 Copyright 2021 ACS. | |
6. Urea-based shell materials for MPCMs
Urea-based resin is a commonly used shell-forming material for the synthesis of MPCMs because it can form a highly flexible and tough shell. Generally, MPCMs composed of urea-based shells are prepared through the in situ polymerization technique.149,150 In the case of urea-based shell materials, the primary objective was to encapsulate the PCM made of organic macromolecules inside the shell. It should be noted that PCMs have the tendency to degrade and leak when in use; however, the polymer shell can not only successfully shield the PCMs from the outside environment but can also adjust to the volume shift brought about by the phase change.151–153 Thermal conductivity is crucial to the thermal response of energy storage materials. Numerous studies aim to increase the MPCMs' thermal conductivity by incorporating inorganic particles into them. Wang et al.28 prepared microencapsulated capric acid using MUF resin as the shell material (illustrated in Fig. 9a). The thermal stability, thermal conductivity, and mechanical strength of the prepared capric acid microcapsule were improved by the incorporation of nano-silicon carbide into the polymer shell. The FTIR spectra of capric acid (CA), nano-silicon carbide, a MPCM with 6 wt% silicon carbide, and a MPCM without silicon carbide are displayed in Fig. 9b. The successful incorporation of nano-silicon carbide into the MPCM was validated by the FTIR spectrum of MPCMs with 6 wt% silicon carbide. A variety of strong signals from the elements C, N, O, and Si were clearly visible in the Energy Dispersive Spectroscopy (EDS) spectra (Fig. 9c) of MPCMs with 6 wt% silicon carbide shell samples, with Si accounting for about 30.66 wt% of the total. The elemental distribution in the surface scanning diagram of the MPCM containing 6 wt% silicon carbide is shown in Fig. 9d. The thermal conductivity of the preparation has been improved by 59.2% at a 6 wt% loading level of nano-silicon carbide. Silicon carbide is well known as a semiconductor. It can easily absorb photons and store them in the phase change material as thermal energy. The nano-silicon carbide in the shell is responsible for improving thermal conductivity.
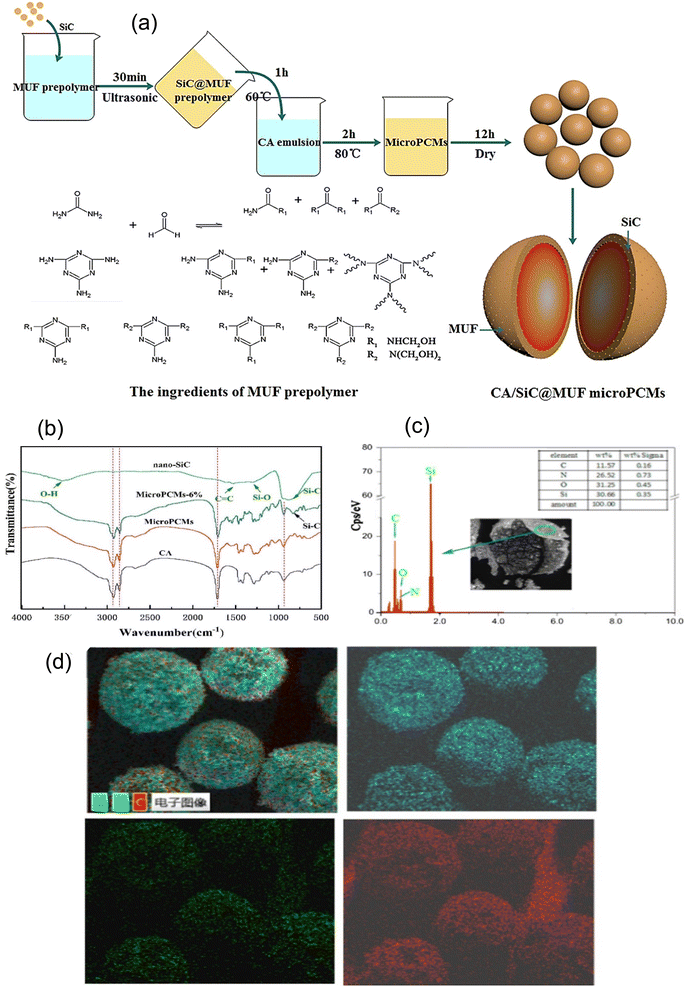 |
| Fig. 9 (a) Process of the preparation of MPCMs using capric acid as the core and MUF as the shell combination with nano-silicon carbide,28 (b) FTIR spectrum of CA, nano-silicon carbide, the MPCM with 6 wt% silicon carbide, and the MPCM without silicon carbide, (c) EDS spectra of the MPCM containing 6 wt% silicon carbide, and (d) EDS spectrum elemental distribution in the surface scanning diagram of the MPCM containing 6 wt% silicon carbide.28 Reproduced with permission from ref. 28 Copyright 2021 Elsevier. | |
In a research study using composite shells, microencapsulation was applied for thermal energy storage, which can cause the PCM to undergo phase change without any outside influence.20 The interfacial polymerization technique created MPCMs with poly(urea-urethane) composite shells encapsulating the treated cellulose nanocrystals (CNCs). The MPCM showed promising performance for potential usage in construction materials in terms of released heat and chemical and physical stability. Fig. 10 displays the SEM pictures of the microcapsules. C0P00M60 (Fig. 10a) microcapsules were produced from the toluene diisocyanate (TDI) monomer. The shell of the C0P40M60 microcapsules (Fig. 10c) was synthesized using DETA and poly(tetrahydrofuran) (PTMG). The microcapsules were observed to be uneven and have a small hole due to the high viscosity of the prepolymer employed. Due to their optimal reactivity with TDI, the C5P20M30 microcapsules' outer shell (Fig. 10d) became more regular, although they also displayed some agglomeration. These microcapsules have a 20% core composition synthesized with a post-added DETA and TDI-based prepolymer. Furthermore, it was found that the thin membrane of the C5P20M90 microcapsules had a 90% core content. Therefore, achieving the proper shape and surface of the encapsulated PCMs requires the optimal composition of both PTMG and the core component. The findings show that methyl laurate was effectively encapsulated inside the polyurea-urethane shell, and encapsulated PCMs demonstrated significantly better phase change behavior, much clearer core–shell structures, and higher encapsulation efficiencies.
 |
| Fig. 10 (a0) Schematic illustration of the poly(urea-urethane) shell-based microcapsule, (a) scanning electron micrographs of (a) C0P00M60 (methyl laurate-60%), (b) C0P10M60 (PTMG-10%, methyl laurate-60%), (c) C0P40M60 (PTMG-40%, methyl laurate-60%), (d) C5P20M30 (CNC-5%, methyl laurate-30% PTMG-20%), and (e) C5P20M90 (CNC-5%, PTMG-20%, methyl laurate-90%), and (f–h) cross-sectional images of the microcapsules.20 Reproduced with permission from ref. 20 Copyright 2017 ACS. | |
7. Silica-based shell for MPCMs
The limitations of organic polymeric shells, which include poor thermal stability, flammability, inferior chemical stabilities, and low thermal conductivity, motivate researchers to discover new inorganic shell materials even though organic polymeric shells play a significant role in improving the properties of MPCMs.127,128 Quick heat transfer is necessary for PCMs to respond quickly throughout the process of storing heat energy and regulating its temperature. It is well known that organic materials' thermal conductivities are consistently noticeably lower than those of inorganic materials.154–156 In addition, inorganic materials are more flame resistant and have more mechanical strength than organic materials. Selecting an appropriate inorganic wall material is a potential approach in order to improve the phase-change performance of MPCMs because of these appealing characteristics. Based on a review of the literature, some recent attempts have been undertaken to encapsulate paraffin PCMs with inorganic silica materials.46,47,157 Generally, the sol–gel process is used for the microencapsulation of organic PCMs with inorganic shell materials such as silica and titanium oxide. The mechanism of production of encapsulating PCMs with silica is described in several reports by an oil-in-water emulsion technique.127,128 Microencapsulated paraffin made of a silica shell was created using a sol–gel method as a thermal energy storage material, and it was shown that its thermal conductivity was significantly improved.46,47,157 Notably, tetraethoxysilane (TEOS) is used as a silica precursor in the r synthesis of the majority of the inorganic shell-based microencapsulated PCMs documented in the literature. The basic steps for the preparation of PCM microcapsules through the sol–gel process are a dispersion of the core material in water, the preparation of sol solution by dissolving the coating material, the formation of microcapsules by a condensation reaction after mixing the core material and sol solution together under stirring, and the recovery of microcapsules from the emulsion.110,158 He et al.159 prepared octadecane microcapsules with a silica shell material using a non-ionic surfactant for the preparation of a stable emulsion. The schematic process of creating silica shell-based PCM microcapsules using the sol–gel technique is shown in Fig. 11a0. Sodium silicate was dissolved in water under acidic conditions for the preparation of silica sol. As depicted in Fig. 11(a–f), the optical microscope captured a typical production process of microencapsulation of n-octadecane. The silica shell was successfully constructed onto the surface of the n-octadecane droplets as a result of the prolonged condensation reaction. It was discovered that the polycondensation reaction requires enough time in order to create structurally dense microcapsules. They have studied the effect of pH on the microstructure of the synthesized microcapsule. A smooth and compact microcapsule was formed at pH 2.95–3.05. The resultant PCM microcapsule exhibited excellent thermal conductivity, phase change behavior, and thermal and mechanical stability.
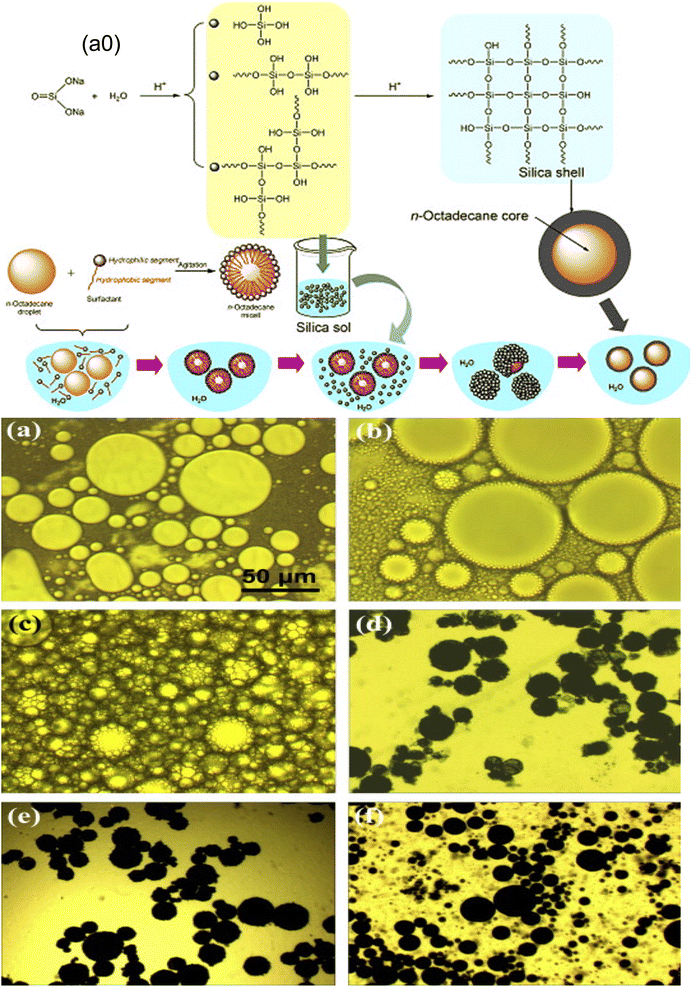 |
| Fig. 11 (a0) Scheme of the formation mechanism for the MPCM with a silica wall, and optical microscope pictures of the reactants at various stages of the synthesis: (a) droplets of octadecane, (b) micelles of octadecane, (c) the initial microcapsules after adding silica sol, (d) the microcapsules developed after 6 h polycondensation reaction, (e) the microcapsules developed after 6 h polycondensation reaction, (f) the microcapsules developed after 12 h polycondensation reaction, and (f) the microcapsules developed after 24 h polycondensation reaction.159 Reproduced with permission from ref. 159 Copyright 2014 Elsevier. | |
One of the important techniques for the preparation of silica particles or silica shell materials is the sol–gel technique, in which solid silica is prepared from a colloidal suspension.160 Sol–gel is a process of preparing a solid phase from a colloidal suspension or solution with a suitable starting material. In the conventional sol–gel technique, the sol is prepared from a solution of metal alkoxides. More accurately, the starting point in the sol–gel technique involves a solution, which converts to a sol form gradually during the conversion process from one phase to another. For example, in the case of silica-based shell preparation, tetraethyl orthosilicate is first dissolved in an alcoholic solution. The methods of preparation of silica-based microencapsulated PCMs are reported in the literature by combining the sol–gel technique with the emulsion technique. Wang et al.160 prepared silica-based microcapsules with organic phase change materials as the core. They prepared a microcapsule with a silica microsphere as a shell and n-pentadecane as the core. The cationic surfactants were used as emulsifying agents. The particle size of the prepared silica microcapsule containing n-pentadecane was 4–8 μm. The role of cationic and anionic emulsifiers in the preparation of microcapsules was investigated. It has been observed that the cationic emulsifier was more effective than the anionic emulsifier in preparing the stable microcapsule. Zhang et al.93 prepared a novel MPCM based on spherical micro-silica. They used n-octadecane as the core material and inorganic silica as the shell material. The inorganic silica shell was synthesized from tetraethyl orthosilicate through a sol–gel process as illustrated in Fig. 12a0. The chemical structure of the silica microcapsules was confirmed by FTIR analysis, and the spherical morphology was determined by scanning electron microscopy. The SEM images of the silica microcapsules produced at various weight ratios of n-octadecane to TEOS and pH values are shown in Fig. 12a–h. The SEM images of the shattered microcapsules were used to determine the inner microstructures. Regular spheres are seen in the sample produced at a pH of 2.26 and a weight ratio of 70
:
30 octadecane to TEOS; however, the size of these spherical microcapsules is not constant. The synthesized silica microcapsule containing an n-octadecane core exhibited improved thermal conductivity due to the presence of an inorganic shell, high encapsulation efficiency, excellent phase-change performance, and good anti-osmosis properties. It exhibits better thermal conductivity because the thermal conductivity of inorganic materials is higher than that of organic polymeric materials.
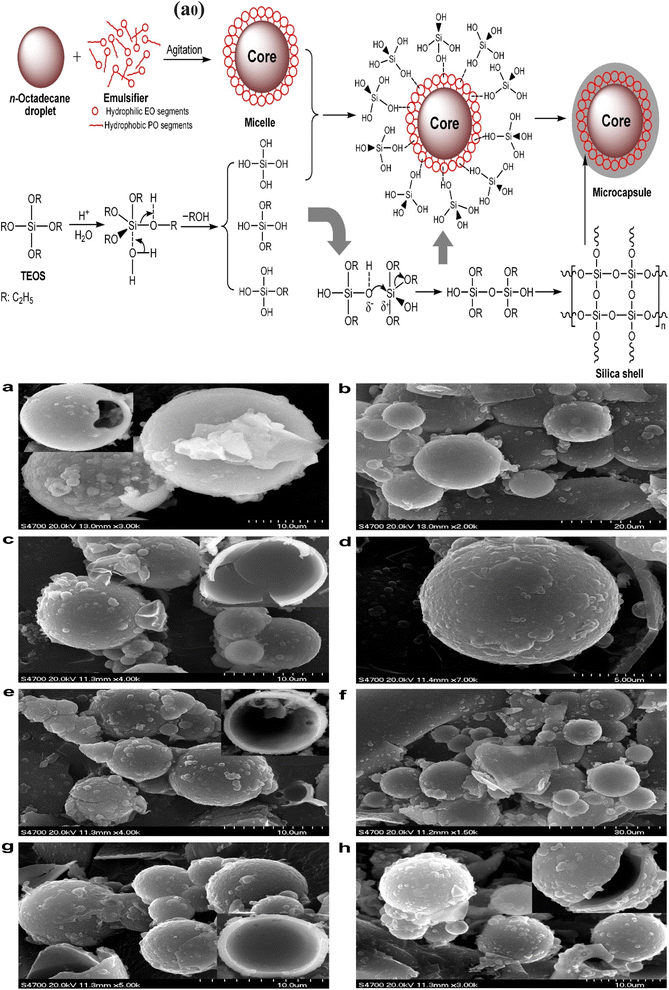 |
| Fig. 12 Schematic formation of the silica-microencapsulated n-octadecane via a sol–gel process. SEM pictures of the microcapsules prepared at various weight ratios of n-octadecane to TEOS and pH levels, (a and b) synthesized with an n-octadecane to TEOS ratio of 70/30 and pH 2.26, (c and d) synthesized with an n-octadecane to TEOS ratio of 70/30 and pH 2.45, (e and f) synthesized with an n-octadecane to TEOS ratio of 60/40 and pH 2.45, (g) synthesized with an n-octadecane to TEOS ratio of 50/50 and pH 2.45, and (h) synthesized with an n-octadecane to TEOS ratio of 70/30 and pH 2.89.93 Reproduced with permission from ref. 93 Copyright 2010 Elsevier. | |
In a recent study, Hu and colleagues2 created a MEPCM for thermal energy storage (TES) applications in buildings using octadecane as the core material. Octadecane/tributyl phosphate (TBP) hybrid core materials were effectively loaded into microcapsules with a silica shell and poly(ureaformaldehyde)-shelled microcapsules (PUF-MCs), which showed good TES characteristics and flame retardancy. Microcapsules with a silica shell were successfully created at a low temperature using a simple technique (Fig. 13a0), whereas PUF-MCs was created at a higher temperature using in situ polymerization in an oil-in-water emulsion. Spherical microcapsules with a silica shell with a diameter of 150–210 μm (Fig. 13a1) were produced, whereas PUF-MC showed a larger diameter of 330–447 μm (Fig. 13b1). Additionally, the various surface structures for microcapsules were significantly visible in the scanning electron microscopy (SEM) images at a greater magnification (Fig. 13a2 and b2). Microcapsules with a silica shell displayed a smooth structure with surface wrinkles, but PUF-MC revealed a hierarchical outer surface structure resembling a lotus leaf surface. Microcapsules with a silica shell (Fig. 13a3) and PUF-MC (Fig. 13b3) microcapsules clearly showed a core–shell structure, with average shell thicknesses of 6.5 and 9.4 μm, respectively. This suggests that the encapsulation conditions used were successful in producing capsules. Microcapsules with a silica shell (ΔHm = 124.6 J g−1) showed weaker TES capacity than PUF-MC (ΔHm = 186.8 J g−1) but better flame retardancy with a lower peak heat-release rate. The results showed that the concept of using PCMs and flame retardants as hybrid core materials in buildings has a lot of potential for ensuring environmental sustainability.
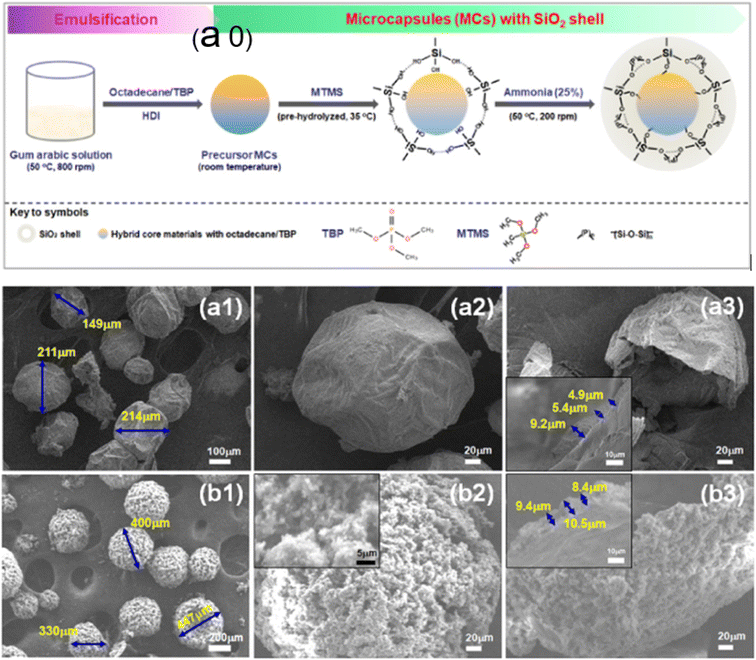 |
| Fig. 13 (a0) Representation of microcapsule formation with a silica shell and an octadecane/TBP hybrid core, and SEM pictures of a hybrid MEPCM with SiO2 (a1–a3) and PUF (b1–b3).2 Reproduced with permission from ref. 2 Copyright 2021 ACS. | |
8. TiO2 based shell materials for MPCMs
Numerous studies have demonstrated the viability of using both polymers and inorganic materials as PCM shell materials. It was noted that more than 50 polymers have been successfully employed to encapsulate PCMs, thereby preventing PCM leakage from the microcapsules and also endowing the microcapsules with structural stability.146,161,162 However, due to the low thermal conductivity of polymeric materials, the thermal conductivity of the MPCM was not increased. Encasing PCMs in inorganic shells can improve the thermal performance because of the strong thermal conductivity and nonflammability of inorganic materials. Several inorganic materials, including silica, calcium carbonate, titanium dioxide, aluminium, and hydroxide, were successfully employed to encapsulate PCMs.46,47,157 The finding of inorganic shell-based MPCMs showed that PCMs might be microencapsulated with inorganic materials to solve the issue of thermal conductivity. A practical technique for making the MPCM with a silica or titanium dioxide shell is hydrolysis polycondensation. According to some recent studies, the characteristics of an EPCM can be altered by adding inorganic nanoparticles like graphene or graphene oxide to the shell made of silica or titanium dioxide. For example, by hydrolyzing and polycondensing titanium butoxide, a TiO2/GO shell-based EPCM was produced as illustrated in Fig. 14a0.163 The latent heat of microcapsules was observed to be greater than 160.75 J g−1, and the thermal conductivity was greatly improved due to the extremely thermally conductive nature of GO nanosheets. Additionally, compared to paraffin, the thermal conductivity was observed to be roughly two times higher while maintaining a high phase change enthalpy. The surface morphology of the microcapsules was examined using a scanning electron microscope (SEM), and it was discovered that GO/TiO2/paraffin microcapsules have a compact core–shell structure with homogeneous spherical particles and a smooth shell surface. Meanwhile several findings suggested that paraffin, TiO2, and GO were physically joined (Fig. 14a–i) and most of the GO nanosheets were distributed evenly on the surface of TiO2/paraffin microcapsules without visible agglomeration. This structure was thought to be adequate to survive the phase volume shift brought about by the phase transition and helps to avoid the loss of liquid paraffin during the phase transition process. The work offered a fresh concept for the use of carbon material in the modification of microcapsule composite PCMs for thermal energy storage.
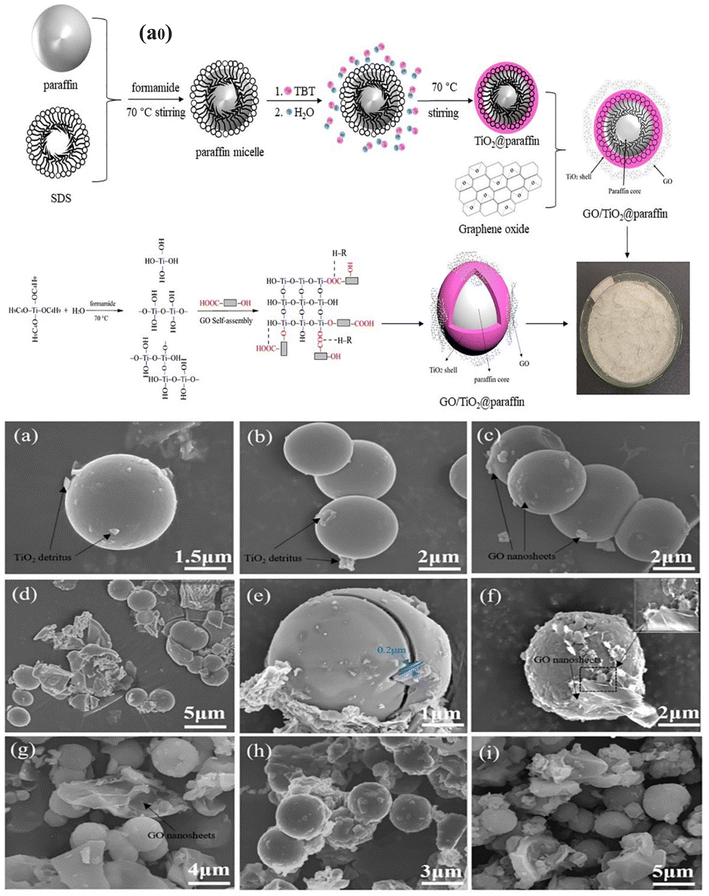 |
| Fig. 14 (a0) Schematic illustration of the method for creating GO/TiO2/paraffin microcapsules, SEM images of (a and b) TiO2/paraffin microcapsules, (c and d) GO/TiO2/paraffin microcapsules containing 1 wt% GO, (e–g) GO/TiO2/paraffin microcapsules containing 2 wt% GO, and (h and i) GO/TiO2/paraffin microcapsules containing 3 wt% GO.163 Reproduced with permission from ref. 163 Copyright 2021 Elsevier. | |
Graphene nanosheets, which are made of two-dimensional carbon, exhibit exceptional thermal conductivity. There are a few examples of the preparation of MPCMs with an inorganic shell containing graphene nanosheets, which show significant improvement of thermal conductivity.164,165 This research, however, only focused on the PCM core's role in temperature control and thermal energy storage. The technique of turning light energy into a chemical reaction is known as photocatalysis. By utilizing photocatalysts, nearly all organic compounds that are detrimental to people or the environment can be broken down without wasting resources. After band gap excitation, titanium dioxide could produce electrons. With the help of suitable substrates, these electrons may move to the catalyst surface and start redox processes. For instance, these electrons can produce OH radicals, one of the most potent oxidants. The organic species can then be oxidized by the hydroxyl radicals. However, titanium dioxide has limited photocatalytic activity because of the rapid recombination of electrons and positive holes. In recent research, it was found that the synthesized MPCMs with a titanium dioxide shell not only exhibited good latent-heat storage performance and higher thermal conductivity but also had an additional photocatalytic effectiveness derived from their crystalline titanium dioxide shell.129 As shown in Fig. 15a0, creating microcapsules with titanium dioxide shells and an n-eicosane core is a simple process. The crystalline titanium dioxide shell was successfully formed on the surfaces of the n-eicosane micelles using such a sol–gel procedure. SEM images were used to examine the morphologies of the resulting microcapsule samples, as shown in Fig. 15a–f. The microcapsules ranged in size from 1.5–2 μm, and the diameters of these microcapsules were observed nearly invariable with respect to the weight ratio of the core to the shell. All the microcapsules were seen to have an almost smooth, clean surface in the enhanced SEM micrographs. However, the SEM micrograph of the sample synthesized with a weight ratio of 40/60 of n-eicosane to tetrabutyl titanate (TBT) appears to show a few small irregular particles. The applicability of the MPCM can be significantly increased by such a combination of thermal energy storage and photocatalytic efficiency. The bifunctional eicosane microcapsule may find applications in advanced fabrics, medical protective apparel, food preservation, solar energy storage and recovery, waste heat recovery, and other fields. However, according to the existing synthetic methodologies, the development of the titanium dioxide shell must rely on some expensive organic titanium sources, which results in a high cost for the produced microcapsules.
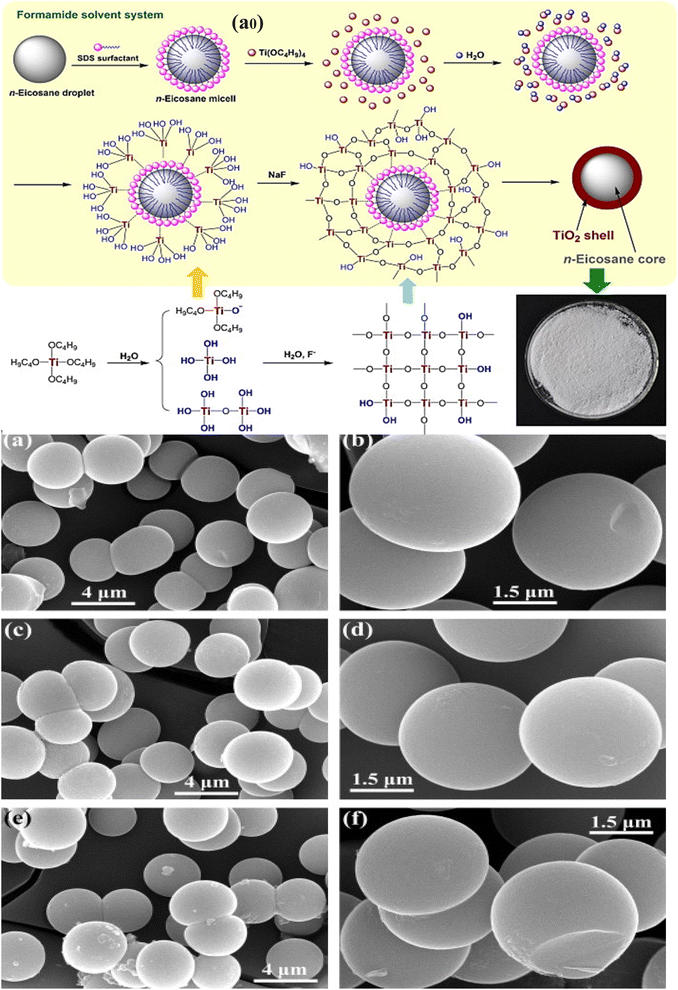 |
| Fig. 15 (a0) Schematic illustration of the fabrication of the n-eicosane microcapsule TiO2 shell, SEM images of the n-eicosane microcapsule (a and b) produced with a weight ratio of 60/40 n-eicosane/TBT, (c and d) produced with a weight ratio of 50/50 n-eicosane/TBT, and (e and f) produced with a weight ratio of 40/60 n-eicosane/TBT.129 Reproduced with permission from ref. 129 Copyright 2015 Elsevier. | |
Although high thermal conductivity inorganic materials such as calcium carbonate and silica are widely used, other inorganic materials (e.g., TiO2 shell) can sometimes serve as the shell for microencapsulated PCMs when used to encapsulate various PCMs. TiO2 shells can be formed on the organic PCM core using an O/W emulsion-templating system. Tetrabutyl titanate (TBT) was used by Cao and co-workers166 as a titanium source and SDS as a surfactant as a templating agent for creating microcapsules containing a palmitic acid core and TiO2 shell. Despite having only a 34% encapsulation efficiency, the microencapsulated palmitic acid still functioned as a shape shape-stabilized thermal energy-storage material. Zhao and coworkers167 reported the fabrication of microencapsulated n-octadecane with a TiO2 shell through in situ polycondensation in a nonaqueous O/W emulsion using anhydrous ethanol as a dispersion medium. SEM images (Fig. 16a–d) were used to determine the microstructures of the PCM microcapsules. The microcapsules have a spherical form and have an average size of 2–5 μm. The EDX pattern (Fig. 16e) was used to determine the chemical compositions of the shells of the MPCM sample. The peaks of the EDX pattern confirmed the presence of the elements Ti and O, indicating that the n-octadecane core was covered in a TiO2 shell. Fig. 16g displays the thermal degradation patterns for n-octadecane, pure TiO2, and the MPCM made using an 8
:
8 ratio of n-octadecane and TBT. The stability of the MPCM sample was also investigated using a thermal cycling test (Fig. 16g), and the DSC curve exhibited a very similar profile between the first cycle and the 100th one. The encapsulation process was found to be practical, straightforward, highly efficient, and environmentally friendly. Similar techniques were used by Li and cowerkers168 to microencapsulate stearic acid within the TiO2 shell, and the resulting microcapsules had an irregular spherical shape; they performed well in terms of latent heat storage and thermal stability. An innovative design of microencapsulated paraffin with a TiO2/SiO2 hybrid shell was published to improve thermal energy storage and conduction.169 By using a combination of TEOS and TBT as inorganic sources, they carried out the emulsion-templated in situ polycondensation of silica and titania precursors and effectively constructed a highly thermally conductive hybrid shell onto the paraffin core.
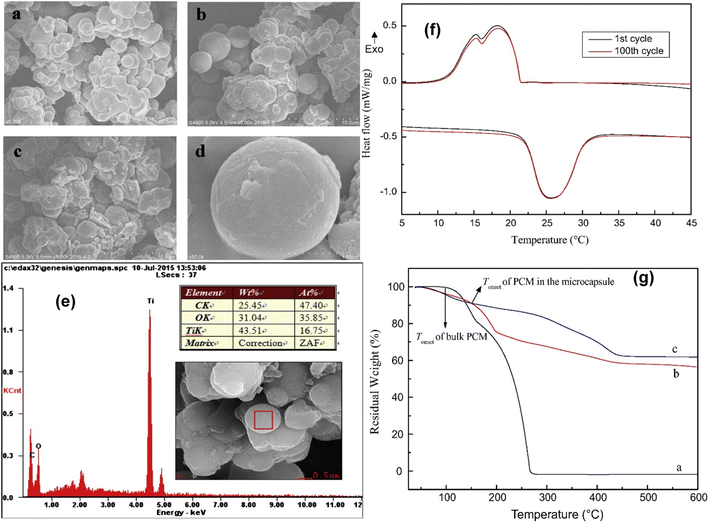 |
| Fig. 16 SEM pictures of (a and d) the MPCM produced using an 8 : 8 ratio of n-octadecane and TBT and (b and c) the MPCM made using a 5.4 : 8 ratio of n-octadecane, (e) EDX pattern of the sample of the MPCM made using an 8 : 8 ratio of n-octadecane and TBT, (f) DSC curves over 100-loop scans for the MPCM made using an 8 : 8 ratio of n-octadecane and TBT, and (g) TGA curves of n-octadecane, pure TiO2, the MPCM made using an 8 : 8 ratio of n-octadecane and TBT.167 Reproduced with permission from ref. 167 Copyright 2016 Elsevier. | |
9. Calcium carbonate-based shell materials for MPCMs
Based on the literature review, some attempts to encapsulate paraffin PCMs with inorganic materials have been made recently.89,170 The mechanism of production of encapsulating PCMs with silica is described in several reports by an oil-in-water emulsion technique.127,128 Microencapsulated paraffin made of a silica shell was created using a sol–gel method as a thermal energy storage material, and it was shown that its thermal conductivity was significantly improved.46,47,157 Notably, tetraethoxysilane (TEOS) is used as a silica precursor in the r synthesis of the majority of the inorganic shell-based microencapsulated PCMs documented in the literature. Although the PCM microcapsules with silica shells can achieve excellent thermal conductivity and good phase-change performance, the resulting silica shell is not compact and robust enough to shield PCM cores from leakage and penetration. These microcapsules are quickly broken, demonstrating the silica shell's poor mechanical strength. Additionally, due to its high price, TEOS is not an economic silica precursor for the commercial production of microencapsulated PCMs. Some recent studies have explored calcium carbonate as a shell material to prepare MPCMs. Calcium carbonate is one of the best shell materials for PCM microencapsulation because of its low synthesis cost, excellent mechanical characteristics, high chemical stability, and higher durability compared to other inorganic materials. For instance, n-octadecane core and calcium carbonate shell-based PCM microcapsules were manufactured using a self-assembly approach, and phase change behaviors and the useful performance of the resulting products were studied.171 The calcium carbonate shell that surrounds octadecane micelles was created via the precipitation reaction between carbonate ions (CO32−) and calcium ions (Ca2+). It is attractive to observe the properties of n-octadecane micelles and the development of microcapsules with the gradual precipitation of calcium carbonate, as shown in Fig. 17a–f, which shows a typical production process of microencapsulating through precipitation reaction techniques. Creating a highly thermally conductive calcium carbonate shell dramatically increased the thermal conductivity and the high durability of octadecane microcapsules. The morphologies of the microcapsules created at three distinct n-octadecane/CaCl2 mass ratios are depicted in Fig. 17g–j. The microcapsules exhibited a consistent spherical form. These spherical microcapsules were found to have a particle size of ∼5 μm, and their surfaces are smooth and undamaged. This synthetic process suggests high feasibility in commercial manufacture for the microencapsulated PCMs with inorganic shells due to the low cost of calcium carbonate.
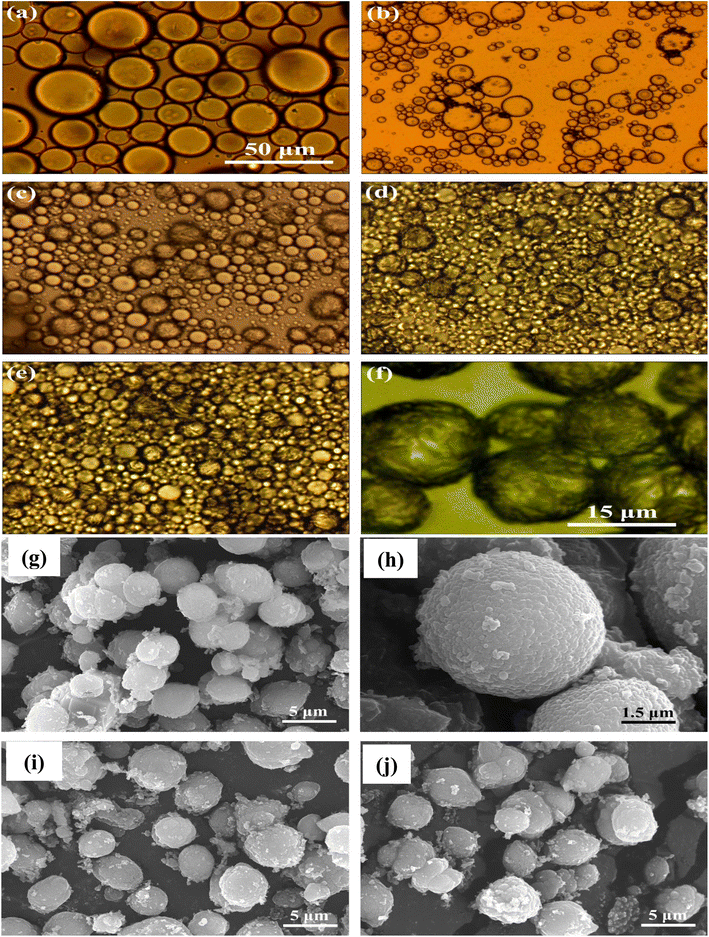 |
| Fig. 17 Photographs taken under an optical microscope at various stages of the synthesis of calcium carbonate shell-based microcapsules, (a) octadecane droplets, (b) octadecane micelles, (c) initial microcapsules, (d) microcapsules formed after one and half hour reaction, (e) microcapsules formed after 3 h reaction, and (f) microcapsules formed after 6 h reaction, SEM images of the microcapsules (g and h) created at a mass ratio of 30 : 70 for n-octadecane to calcium chloride, (i) created at a mass ratio of 40 : 60 for f n-octadecane to calcium chloride, and (j) created at a mass ratio of 50 : 60 for f n-octadecane to calcium chloride.171 Reproduced with permission from ref. 171 Copyright 2014 Elsevier. | |
Major MPCM research has been reported in the literature using organic polymer shells such as polystyrene, polymethylmethacrylate, and melamine formaldehyde, which are known for having lower heat conductivities. In a few investigations, how to use inorganic fillers to create organic shell materials with greater thermal conductivity has been reported. The simplest method to boost the thermal conductivity of MPCMs is to develop an inorganic shell made of calcium carbonate or silica or titanium dioxide, and these inorganic shell materials are widely accessible at a low price. Inorganic materials have higher thermal conductivity, superior flame resistance, and better chemical and thermal stability than polymeric ones. Thus, for improving MPCM's thermal performance, choosing appropriate inorganic shells is essential. Heptadecane was enclosed in a calcium carbonate shell by Sarı and co-workers,172 and they noted that the microcapsules showed remarkable chemical stability up to 1000 cycles. According to reports on calcium carbonate encapsulations, achieving high encapsulation efficiency without leakage problems is still a difficult task. Yu and co-workers171 observed an encapsulation efficiency of 40.04% for n-octadecane inside the CaCO3 shell using Span 80 and Tween 80 as surfactants. In some studies, the role of the amount of surfactant in the formulation of the MPCM was examined. According to a study conducted by Shi and colleagues,173 sodium dodecyl benzene sulfonate (SDBS) outperformed sodium dodecyl sulfonate (SDS) in terms of the efficacy of encapsulating commercial paraffin using a CaCO3 shell. A hexadecane PCM was microencapsulated with a calcium carbonate shell using sodium dodecyl sulfate and polyvinylpyrrolidone surfactants.174 Hexadecane was microencapsulated in calcium carbonate (shell) via a self-assembly precipitation reaction, as shown in Fig. 18a0. The microcapsule morphologies with hexadecane (core) and calcium carbonate shells created using various SDS/PVP mass ratios are shown in Fig. 18a–d. Images taken with a field emission scanning electron microscope revealed that a core and shell with a mass ratio of 1
:
1 produced a spherical morphology.
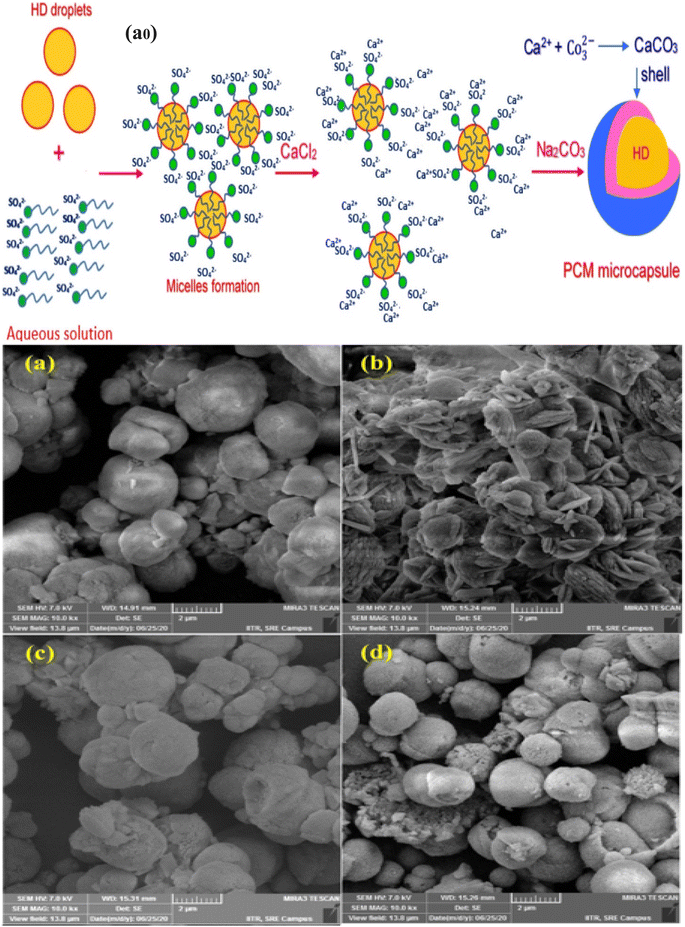 |
| Fig. 18 (a0) Schematic illustration of the preparation of hexadecane (core) with a calcium carbonate shell, (a–d) SEM pictures of MPCM capsules, (a) synthesized by using only SDS, (b) synthesized by using only PVP, (c) synthesized by using SDS and PVP surfactants at a 3 : 1 (SDS/PVP) weight ratio and (d) synthesized by using SDS and PVP surfactants at a 1 : 1 (SDS/PVP).174 Reproduced with permission from ref. 174 Copyright 2022 Elsevier. | |
Creating microencapsulated PCMs with a calcium carbonate shell presents several technological difficulties. The water-soluble calcium salts and carbonates (e.g., Na2CO3) on the surface of the PCM core often precipitate in an interfacial precipitation reaction to form the calcium carbonate shell. This type of microencapsulated PCM must be made using a very complicated technological procedure since calcium carbonate cannot be deposited on the core surface because of a precipitation reaction. A past study initially described an interfacial self-assembly technique for microencapsulating n-octadecane with a calcium carbonate shell in 2014.171 An oil-in-water emulsion-templating system was developed using non-ionic surfactants. This system was utilized to assemble calcium ions through complexation and subsequently precipitate carbonate at the micelle interface. Because of its high heat conductivity, great strength, and low cost, calcium carbonate is found to be frequently employed as the preferable material for shells. Microencapsulated PCMs were created by Wang and co-workers175 using calcium carbonate as the shell and paraffin-based binary core materials with differing melting temperatures. By altering the weight ratio of the binary core, the microcapsules' phase transition temperature was changed from 25 to 50 °C. Jiang and co-workers176 created paraffin microcapsules with calcium carbonate shells and added graphene oxide to the microcapsules to improve performance. Microcapsules were created by Yu and co-workers171 using n-octadecane as the core and calcium carbonate as the outside shell. The encapsulated alkane was found to have good thermal stability and endurance. Using self-assembly precipitation, new PCM microcapsules with a paraffin core and Ce3+ dopped calcium carbonate shell were created.177Fig. 19a depicts the development of paraffin microcapsules with morphological characteristics. The particle sizes of the microcapsules with varying Ce3+ concentrations range from 10 to 20 μm, and they have a consistent spherical morphology. Ce3+ was successfully inserted into the crystal lattice of calcium carbonate, replacing certain calcium ions. Following a 10 hour heating period in an oven set to 60 °C, Fig. 19b displays the leak rate of paraffin microcapsules. The findings of the leak rate test demonstrated that the addition of Ce3+ during the manufacture of microcapsules has no impact on the development of a compact protective shell made of calcium carbonate. The microcapsules were highly efficient in sealing, regulating temperature, and storing energy. In addition, the increased concentration of Ce3+ improved the fluorescence intensity of the paraffin microcapsules. The melting and freezing enthalpy values for PCM microcapsules containing 0.6 wt% Ce3+ with respect to calcium carbonate (micro-PCMs-0.6) were measured to be 148.6 J g−1 and 142.3 J g−1 during the first cycle, and 119.2 J g−1 and 114.7 J g−1 during the 500th cycle, as shown in Fig. 19c. This might be caused by a few micro-PCMs leaking as the number of cycles increases. Furthermore, the phase transition temperature of the curve after the 500th cycle is nearly synced with the temperature at the beginning of the cycle. These findings demonstrate the outstanding thermal reliability of PCM microcapsules even after numerous cycles. Simulated sunlight was used to examine paraffin and paraffin microcapsules' heat release and heat storage characteristics. After reaching room temperature, all microcapsules were heated. Fig. 19d displays the microcapsules' temperature–time curve during release (blue) and storage (red). Due to differences in thermal conductivity, which is a crucial component of the photothermal conversion process, the samples exhibited varying rates of heating. The paraffin microcapsules composed of a Ce3+ dopped calcium carbonate shell offered a fresh perspective on bifunctional microcapsules (Table 3).
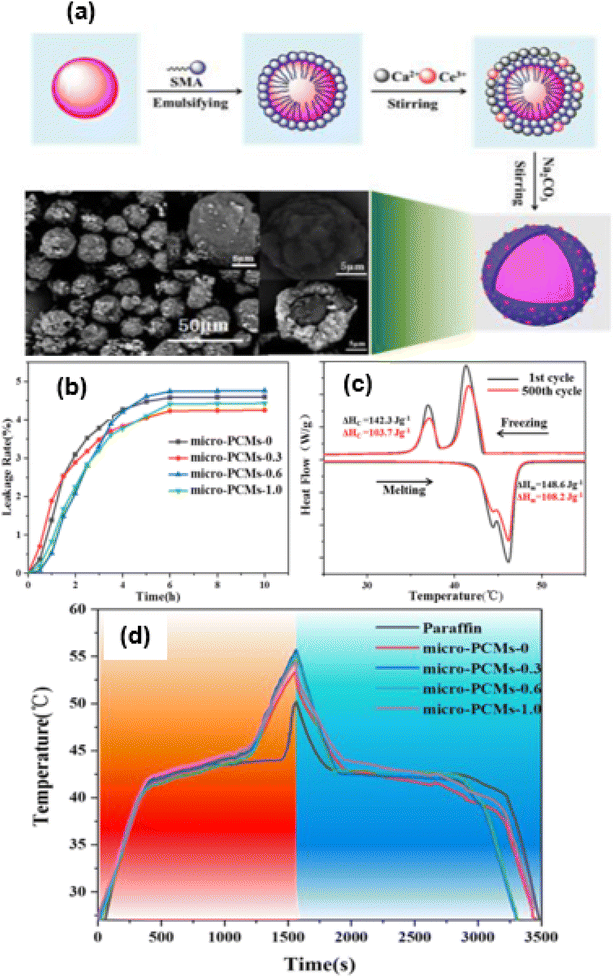 |
| Fig. 19 (a) Schematic of synthesis for paraffin microcapsules composed of Ce3+ dopped calcium carbonate with SEM images; (b) Leakage rate of paraffin microcapsules; (c) DSC curves of PCM microcapsules containing 0.6 wt% Ce3+ with respect to calcium carbonate; (d) paraffin and paraffin microcapsules' temperature–time curves during the release processes (blue) and storage (red).177 Reproduced with permission from ref. 177 Copyright 2019 ACS. | |
Table 3 Comparison of encapsulation efficiency of microcapsules reported in the literature
Shell (polymer) |
PCM (core) |
Encapsulation technique |
Encapsulation efficiency (%) |
Ref. |
Polyurea |
Dodecanol |
Interfacial polymerization |
73.0 |
178
|
Poly(BA-co-MMA) |
Hexadecane |
Suspension polymerization |
28.8 |
48
|
Poly(melamine-formaldehyde) |
Paraffin |
Interfacial polymerization |
74.1 |
140
|
Polyurethane |
Paraffin |
Interfacial polymerization |
44.5 |
179
|
Poly(melamine-urea-formaldehyde) |
Hexadecane |
Emulsion polymerization |
77.8 |
140
|
Poly(2-hydroxyethyl methacrylate) |
Hydroxystearic acid |
Emulsion polymerization |
56.0 |
41
|
Poly(hydroxyethyl acrylate) |
Hydroxystearic acid |
Emulsion polymerization |
32.0 |
124
|
Poly(BA-co-MMA) |
Hexadecane |
Suspension polymerization |
28.8 |
160
|
Poly(lauryl methacrylate) |
Paraffin wax |
Suspension polymerization |
52.9 |
35
|
Polystyrene |
Capric acid |
Emulsion polymerization |
45.7 |
27
|
Poly(melamine-urea-formaldehyde) |
Capric acid |
In situ polymerization |
65.7 |
28
|
10. Current challenges and future study
The microencapsulation of PCMs for their practical application in the field of sustainable energy was used to improve thermal characteristics, reduce leakage and contamination during the application, and increase chemical stability. To address the issues associated with PCMs for thermal energy storage, such as improving heat conductivity, reducing leakage, and reducing supercooling, PCMs are microencapsulated inside shell materials. The three kinds of PCM microencapsulation techniques are physical, chemical, and physicochemical. The selection of one of these microencapsulation methods takes into account both the benefits and limitations of the various procedures in addition to the desired qualities of the microcapsules. In recent years, research on the microencapsulation of PCMs used in energy storage applications has concentrated on the novel functionality of shell materials, the selection of new materials for shell preparation, and the creation of ecologically friendly procedures. As a result, microencapsulated PCMs are now multifunctional, with the shell protecting the active from the outside environment, enhancing heat transfer, or offering an additional function in addition to energy storage. The addition of new shell materials and a change to the PCM composition can create additional functionalities. As a result, the creation of multifunctional microcapsules broadens the range of applications for technologies like photocatalytic activity for the breakdown of pollutants, photoluminescence for thermosensitive, antibacterial for use in healthcare, photosensitive sensors, etc. Leakage, poor chemical stability, and low encapsulation efficiency are some of the main challenges of PCM microencapsulation for commercial applications in the field of solar energy storage. If the capsule shell is not sufficiently strong, the melting core material in PCM microcapsules may leak through the microcapsule's holes. The development of composite shells using appropriate polymers and nanomaterials could significantly reduce the leakage issues studied by numerous researchers. Supercooling is a common phenomenon of PCM microcapsules that can be minimized by optimizing microcapsule composition or adding some enucleating agents to the core materials. Furthermore, poor thermal conductivity is a major disadvantage of PCM microcapsules that can be overcome by using a composite wall-forming material made up of both organic and inorganic materials. Some PCM microcapsules are extremely brittle due to the high glass transition temperature of the shell polymer, which can be reduced by adding an additive that increases the shell material's flexibility. By incorporating nanomaterials into the polymeric shells, it was found that the leakage rate of the PCM core was significantly lower with a significant improvement in thermal conductivity compared to PCM microcapsules without nanomaterials. Furthermore, the most significant challenge in performing microencapsulation using various techniques is the complex synthesis route, low encapsulation efficiency, poor reproducibility, and expensive synthesis, which can be overcome by developing PCM composites. As a result, various research groups are looking for the best porous materials to use as microencapsulation alternatives to prevent leaking even after the PCM melts when heated. To produce form-stable PCM composites, numerous porous support matrices were investigated, including those based on silica, clay, carbon, diatomite, expanded graphite, expanded perlite, calcium silicate, and gypsum. The difficulty in choosing appropriate low-cost raw materials has a significant impact on the commercialization of PCM microcapsules in thermal energy storage technology. Developing cost-effective microcapsules by choosing the right raw materials is the biggest challenge and has a significant impact on the efficiency of thermal energy storage technology. Lower material costs and high energy storage efficiency are crucial for the large-scale implementation of thermal energy storage. Furthermore, it is important to focus on increasing the thermal conductivity of PCM microcapsules. Thus, it is necessary to optimize the thermophysical characteristics of PCM microcapsules to enhance heat transfer and maintain the PCM shape. Also, it will be advantageous and greatly influence the future course of PCM research to investigate how economically viable MPCMs could be manufactured. Unfortunately, the microencapsulation of PCMs in polymeric shells falls short of application requirements in several respects because of the inherent constraints of organic materials. Inorganic encapsulation will receive considerably more attention in basic research and commercial development in the future since it can benefit microencapsulated PCMs more. Although many inorganic PCMs have higher latent heat than organic PCMs, supercooling, phase segregation, and other problems can negatively affect inorganic PCMs' ability to store energy and they have faced challenges in becoming successful commercial products. Furthermore, the change in volume during phase transition is one of the most difficult properties of inorganic PCMs. When inorganic PCMs are melted, they begin to flow; therefore, proper PCM encapsulation is required to avoid contamination and prevent leakage and corrosion problems. Furthermore, bio-based PCM microcapsules have the potential to be used in the food industry, the pharmaceutical sector, smart textiles, healthcare, and bio-catalysis. There is still a lot of work to be done to overcome several technological challenges because there are not many suitable bio-based shell materials that can be used to build microcapsule shells. Because of their large latent heat storage capacity, ability to phase change in their operating temperature range, and acceptable thermal reliability, PCM microcapsules will be gaining more interest as a new type of sustainable energy storage material in the near future. PCM microcapsules are expected to be used commercially on a large scale in a variety of applications, including building materials, medicine, heat sinks for electronic devices, and food packaging. In addition, advanced electronic device heat management, human thermal control, and other intelligent applications frequently require flexibility. The currently produced microencapsulated PCMs do not match the requirements for flexibility due to their high brittleness and low mechanical strength. Hence, flexible PCMs must be created for a variety of applications. The development and characterization of flexibility are still in their infancy in the study of flexible PCMs, which is still in a relatively early stage. Thus, it is also important to pay attention to the development of flexible standards and appropriate measurement techniques to serve as a guide for future studies. Finding various shell materials with tailored qualities to achieve desired outcomes should also be a major focus of future research; doing so will help advance the use of microencapsulated PCMs. Given that the world is heading towards sustainable development, where efficient energy use will play a critical role, the technology of microencapsulated PCMs is quite futuristic in nature and has a very broad variety of applications in the near future.
11. Summary and outlook
Phase change materials (PCMs) are expected to have high thermal conductivities, large latent heat capacities, minimal volume changes during phase changes, reproducible melting behavior in the desired operating temperature range, no phase separation, non-toxicity, nonexplosiveness, non-flammability, and high chemical resistance for their application in thermal energy storage and temperature control. Depending on the characteristics of the phase change materials and operating temperature ranges, several inorganic, organic, and eutectic PCMs have been investigated as thermal energy storage applications. Numerous academic and industrial researchers have investigated the idea of thermal energy storage through PCMs, showing promising advancements in terms of thermal energy storage, reducing reliance on fossil fuels, and investigating the possibility of utilizing sustainable energy sources. The microencapsulation of PCMs is a suitable approach for preventing leakage during the melting process, increasing thermal conductivity and preventing possible interaction with the various surrounding of PCMs. The most important methods for the preparation of microencapsulated phase change materials (MPCMs) are emulsion polymerization, suspension polymerization, interfacial polymerization, coacervation, and spray drying. When it comes to storing thermal energy, improving thermal conductivity, protecting PCMs from the outside environment, preventing leakage during the melting process, maintaining the volume stability of the PCM core, and creating specific desired characteristics, microencapsulated phase change materials (MPCMs) have shown a lot of potential. The size of the synthesized microcapsule, the kind of core and wall material utilized to manufacture the capsule, the mechanical and thermal properties of the capsule, the thickness of the microcapsule wall, encapsulation efficiency, and other factors are the most crucial ones that affect how well a MPCM performs. The most common polymers employed as shell materials for creating MPCMs are commonly available, inexpensive, mechanically, chemically, and thermally stable in operating circumstances, and easy to manufacture. Polymers such poly(methylmethacrylate), polyurethane, polyurea, polyurea-formaldehyde-based resin, polystyrene, polyester, and others are frequently utilized to make the shell of MPCMs. Many inorganic nanoparticles, including zinc oxide, silicon carbide, titanium dioxide, graphene, graphene oxide, cadmium sulfide, and iron oxides, have been incorporated into the polymeric shell materials of MPCMs to add properties like fluorescence, photocatalysis, magnetic, and better thermal conduction in addition to their capacity to store thermal energy. It is also advantageous to adjust these inorganic fillers so that they can take the place of conventional surfactants during preparation and produce MPCMs of higher caliber. The thermal conductivity property of the polymeric shell can be modified by incorporating carbon nanotubes, silicon carbide, expanded graphite, graphene, graphene oxide, or other highly thermally conductive materials into the polymer matrix. The thermal conductivity of MPCMs has not increased to a greater extent despite the fact that numerous studies have shown the viability of using polymers as PCM shell materials to encapsulate PCMs, preventing PCM leakage from the microcapsules and also providing the microcapsules with structural stability; this is because polymeric materials have a low thermal conductivity. Since inorganic shell materials are non-flammable and have higher thermal conductivity than polymeric shell materials, encasing PCMs in them can enhance their thermal performance. PCMs have been effectively enclosed in a variety of inorganic materials, including silica, calcium carbonate, titanium dioxide, and aluminium hydroxide. The discovery of inorganic shell-based MPCMs demonstrated that the thermal conductivity problem in PCMs may be resolved by microencapsulating them with inorganic shell materials.
Abbreviations
CNC | Cellulose nanocrystal |
DSC | Differential scanning calorimetry |
DVB | Divinylbenzene |
DETA | Diethylenetriamine |
EDS | Energy dispersive spectroscopy |
PMMA | Poly(methyl methacrylate) |
MF | Melamine-formaldehyde |
MUF | Melamine-urea-formaldehyde |
MPCM | Microencapsulated phase change material |
PCM | Phase change material |
PA | Polyamide |
PEAA | Poly(ethylene-co-acrylic acid) |
PMMA | Poly(methyl methacrylate) |
PMMA-co-MA | Poly(methyl methacrylate-co-methyl acrylate) |
PS | Polystyrene |
PSAA | Poly(styrene-co-acrylic acid) |
PU | Polyurea |
PVC | Poly(vinyl chloride) |
TEOS | Tetraethoxysilane |
TBT | Tetrabutyl titanate |
TGA | Thermogravimetric analysis |
UF | Urea-formaldehyde |
Conflicts of interest
The authors state that they have no recognized competing financial interest.
Acknowledgements
We gratefully acknowledge the Ministry of Human Resources Development (MHRD) for providing the financial assistance plan grant (2021–22) for this study and IIT Roorkee for offering all literature and financing.
References
- B. Zhang, Z. Zhang, S. Kapar, P. Ataeian, J. Da Silva Bernardes, R. Berry, W. Zhao, G. Zhou and K. C. Tam, ACS Sustainable Chem. Eng., 2019, 7, 17756–17767 CrossRef CAS
.
- Z. T. Hu, V. H. Reinack, J. An, Z. Indraneel, A. Dasari, J. Yang and E. H. Yang, Langmuir, 2021, 37, 6380–6387 CrossRef CAS PubMed
.
- A. Abhat, Sol. Energy, 1983, 30, 313–332 CrossRef CAS
.
- W. Aftab, X. Huang, W. Wu, Z. Liang, A. Mahmood and R. Zou, Energy Environ. Sci., 2018, 11, 1392–1424 RSC
.
- D. Lefebvre and F. H. Tezel, Renewable Sustainable Energy Rev., 2017, 67, 116–125 CrossRef CAS
.
- A. Zonarsaghar, M. Mousavi-Kamazani and S. Zinatloo-Ajabshir, J. Mater. Sci.: Mater. Electron., 2022, 33, 6549–6554 CrossRef CAS
.
- A. G. Hassabo and A. L. Mohamed, Carbohydr. Polym., 2017, 165, 421–428 CrossRef CAS PubMed
.
- P. Tatsidjodoung, N. Le Pierrès and L. Luo, Renewable Sustainable Energy Rev., 2013, 18, 327–349 CrossRef
.
- F. Gao, X. Wang and D. Wu, Sol. Energy Mater. Sol. Cells, 2017, 168, 146–164 CrossRef CAS
.
- E. Paroutoglou, P. Fojan, L. Gurevich, S. Furbo, J. Fan, M. Medrano and A. Afshari, Sustain., 2022, 14(20), 13317 CrossRef CAS
.
- K. Wazarkar, D. Patil, A. Rane, D. Balgude, M. Kathalewar and A. Sabnis, RSC Adv., 2016, 6, 106964–106979 RSC
.
- C. A. Moyer, Tex. State J. Med., 1949, 45, 635–639 CAS
.
- P. F. De Castro, S. Minko, V. Vinokurov, K. Cherednichenko and D. G. Shchukin, ACS Appl. Energy Mater., 2021, 4, 12789–12797 CrossRef PubMed
.
- G. Hekimoğlu, M. Nas, M. Ouikhalfan, A. Sarı, V. V. Tyagi, R. K. Sharma, Ş. Kurbetci and T. A. Saleh, Energy, 2021, 219, 119588 CrossRef
.
- K. Venkateswarlu and K. Ramakrishna, J. Braz. Soc. Mech. Sci. Eng., 2022, 44, 1–17 CrossRef
.
- X. Du, S. Wang, Z. Du, X. Cheng and H. Wang, J. Mater. Chem. A, 2018, 6, 17519–17529 RSC
.
- S. Chai, K. Sun, D. Zhao, Y. Kou and Q. Shi, ACS Appl. Polym. Mater., 2020, 2, 4464–4471 CrossRef CAS
.
- N. Sun and Z. Xiao, Energy Fuels, 2017, 31, 10186–10195 CrossRef CAS
.
- Z. Jiang, W. Yang, F. He, C. Xie, J. Fan, J. Wu and K. Zhang, ACS Sustainable Chem. Eng., 2018, 6, 5182–5191 CrossRef CAS
.
- Y. Yoo, C. Martinez and J. P. Youngblood, ACS Appl. Mater. Interfaces, 2017, 9, 31763–31776 CrossRef CAS PubMed
.
- M. Raeesi, S. M. Mirabedini and R. R. Farnood, ACS Appl. Mater. Interfaces, 2017, 9, 20818–20825 CrossRef CAS PubMed
.
- M. M. Farid, A. M. Khudhair, S. A. K. Razack and S. Al-Hallaj, Energy Convers. Manage., 2004, 45, 1597–1615 CrossRef CAS
.
- X. Guo and J. Feng, Composites, Part B, 2022, 245, 110203 CrossRef
.
- P. K. Latha, Y. Darshana and V. Venugopal, J. Build. Eng., 2015, 3, 104–113 CrossRef
.
- S. Zhang and J. Niu, Sol. Energy Mater. Sol. Cells, 2010, 94, 1038–1048 CrossRef CAS
.
- J. Liu, L. Chen, X. Fang and Z. Zhang, Sol. Energy Mater. Sol. Cells, 2017, 159, 159–166 CrossRef CAS
.
- A. Sari, C. Alkan and A. Altintaş, Appl. Therm. Eng., 2014, 73, 1160–1168 CrossRef CAS
.
- X. Wang, C. Zhang, K. Wang, Y. Huang and Z. Chen, J. Colloid Interface Sci., 2021, 582, 30–40 CrossRef CAS PubMed
.
- W. Zhao, S. Neti and A. Oztekin, Appl. Therm. Eng., 2013, 50, 143–151 CrossRef CAS
.
- F. J. Ruiz-Cabañas, A. Jové, C. Prieto, V. Madina, A. I. Fernández and L. F. Cabeza, Sol. Energy Mater. Sol. Cells, 2017, 159, 526–535 CrossRef
.
- A. Sharma, S. D. Sharma and D. Buddhi, Energy Convers. Manage., 2002, 43, 1923–1930 CrossRef CAS
.
- X. Bao, H. Yang, X. Xu, T. Xu, H. Cui, W. Tang, G. Sang and W. H. Fung, Sol. Energy Mater. Sol. Cells, 2020, 208, 110420 CrossRef CAS
.
- Z. Luo, H. Zhang, X. Gao, T. Xu, Y. Fang and Z. Zhang, Energy Build., 2017, 147, 41–46 CrossRef
.
- T. R. Heera, Int. J. Ambient Energy, 2020, 1–4 Search PubMed
.
- X. Qiu, L. Lu, J. Wang, G. Tang and G. Song, Thermochim. Acta, 2015, 620, 10–17 CrossRef CAS
.
- B. F. Gibbs, S. Kermasha, I. Alli and C. N. Mulligan, Int. J. Food Sci. Nutr., 1999, 50, 213–224 CrossRef CAS PubMed
.
- X. Xu, H. Cui, S. A. Memon, H. Yang and W. Tang, Energy Build., 2017, 156, 163–172 CrossRef
.
- S. Lu, T. Shen, J. Xing, Q. Song, J. Shao, J. Zhang and C. Xin, Mater. Lett., 2018, 211, 36–39 CrossRef CAS
.
- N. Xie, Z. Huang, Z. Luo, X. Gao, Y. Fang and Z. Zhang, Appl. Sci., 2017, 7(12), 1317 CrossRef
.
- G. Li, B. Zhang, X. Li, Y. Zhou, Q. Sun and Q. Yun, Sol. Energy Mater. Sol. Cells, 2014, 126, 51–55 CrossRef CAS
.
- N. Şahan and H. Paksoy, Int. J. Energy Res., 2018, 42, 3351–3360 CrossRef
.
- S. Peng, J. Huang, T. Wang and P. Zhu, Thermochim. Acta, 2019, 675, 1–8 CrossRef CAS
.
- Z. Ling, J. Liu, Q. Wang, W. Lin, X. Fang and Z. Zhang, Sol. Energy Mater. Sol. Cells, 2017, 172, 195–201 CrossRef CAS
.
- A. Sarı and K. Kaygusuz, Energy Convers. Manage., 2002, 43, 2493–2507 CrossRef
.
- S. Boskovic, B. V. Reddy and P. Basu, Int. J. Energy Res., 2002, 26, 159–171 CrossRef
.
- J. Singh, S. Parvate, P. Dixit and S. Chattopadhyay, Energy Fuels, 2020, 34, 8919–8930 CrossRef CAS
.
- S. Parvate, J. Singh, P. Dixit, J. R. Vennapusa, T. K. Maiti and S. Chattopadhyay, ACS Appl. Polym. Mater., 2021, 3, 1866–1879 CrossRef CAS
.
- S. Lashgari, H. Arabi, A. R. Mahdavian and V. Ambrogi, Appl. Energy, 2017, 190, 612–622 CrossRef CAS
.
- W. Li, G. Song, G. Tang, X. Chu, S. Ma and C. Liu, Energy, 2011, 36, 785–791 CrossRef CAS
.
- G. Alva, X. Huang, L. Liu and G. Fang, Appl. Energy, 2017, 203, 677–685 CrossRef CAS
.
- E. Y. Kim and H. Do Kim, J. Appl. Polym. Sci., 2005, 96, 1596–1604 CrossRef CAS
.
- S. Song, L. Dong, S. Chen, H. Xie and C. Xiong, Energy Convers. Manage., 2014, 81, 306–311 CrossRef CAS
.
- M. H. Zahir, K. Irshad, M. A. Aziz, M. Shafiullah, M. M. Rahman and M. M. Hossain, Energy Fuels, 2019, 33, 12041–12051 CrossRef CAS
.
- C. Wang, L. Feng, W. Li, J. Zheng, W. Tian and X. Li, Sol. Energy Mater. Sol. Cells, 2012, 105, 21–26 CrossRef CAS
.
- S. Höhlein, A. König-Haagen and D. Brüggemann, Materials, 2017, 10(4), 444 CrossRef PubMed
.
- S. Ushak, A. Gutierrez, H. Galleguillos, A. G. Fernandez, L. F. Cabeza and M. Grágeda, Sol. Energy Mater. Sol. Cells, 2015, 132, 385–391 CrossRef CAS
.
- S. Zhang and J. Niu, Energy Build., 2016, 127, 512–520 CrossRef
.
- C. Chen, W. Liu, Z. Wang, K. Peng, W. Pan and Q. Xie, Sol. Energy Mater. Sol. Cells, 2015, 134, 80–88 CrossRef CAS
.
- X. Min, M. Fang, Z. Huang, Y. Liu, Y. Huang, R. Wen, T. Qian and X. Wu, Sci. Rep., 2015, 5, 1–11 Search PubMed
.
- A. M. Borreguero, J. F. Rodríguez, J. L. Valverde, T. Peijs and M. Carmona, J. Appl. Polym. Sci., 2013, 128, 582–590 CrossRef CAS
.
- A. Sari, C. Alkan and A. N. Özcan, Energy Build., 2015, 90, 106–113 CrossRef
.
- N. Sathishkumar, V. Ashok Kumar, M. Gokulnath and G. Kalai Raj, Int. J. Res. Rev., 2020, 7, 3 Search PubMed
.
- A. Karaipekli and A. Sari, Sol. Energy, 2009, 83, 323–332 CrossRef CAS
.
- M. S. Uddin, H. J. Zhu and M. N. A. Hawlader, Int. J. Sol. Energy, 2002, 22, 105–114 CrossRef
.
- B. K. Purohit and V. S. Sistla, Thermochim. Acta, 2018, 668, 9–18 CrossRef CAS
.
- D. Su, Y. Jia, G. Alva, F. Tang and G. Fang, Energy Build., 2016, 131, 35–41 CrossRef
.
- F. Salaün, E. Devaux, S. Bourbigot and P. Rumeau, Chem. Eng. J., 2009, 155, 457–465 CrossRef
.
- F. Cao and B. Yang, Appl. Energy, 2014, 113, 1512–1518 CrossRef CAS
.
- Z. Yang, H. Peng, W. Wang and T. Liu, J. Appl. Polym. Sci., 2010, 116, 2658–2667 CAS
.
- K. Purohit, V. V. S. Murty, R. C. Dixit and A. Sharma, Bull. Mater. Sci., 2019, 42, 1–9 CrossRef CAS
.
-
R. J. Pushaw, B. T. Perry, D. M. Wyner, R. H. W. Associates and W. Bridgewater, Fabric coating containing energy absorbing phase change material and method of manufacturing same, US Pat., US 6514362B1, 2003, pp. 1–14 Search PubMed
.
- M. N. A. Hawlader, M. S. Uddin and H. J. Zhu, Int. J. Sol. Energy, 2000, 20, 227–238 CrossRef
.
- A. Kardam, S. S. Narayanan, N. Bhardwaj, D. Madhwal, P. Shukla, A. Verma and V. K. Jain, RSC Adv., 2015, 5, 56541–56548 RSC
.
- J. H. Jing, H. Y. Wu, Y. W. Shao, X. D. Qi, J. H. Yang and Y. Wang, ACS Appl. Mater. Interfaces, 2019, 11, 19252–19259 CrossRef CAS PubMed
.
- T. Khadiran, M. Z. Hussein, Z. Zainal and R. Rusli, Renewable Sustainable Energy Rev., 2016, 57, 916–928 CrossRef CAS
.
- X. Zhang, X. Li, Y. Zhou, C. Hai, Y. Shen, X. Ren and J. Zeng, Energy Fuels, 2018, 32, 916–921 CrossRef CAS
.
- N. Beaupere, U. Soupremanien and L. Zalewski, Thermochim. Acta, 2018, 670, 184–201 CrossRef CAS
.
- E. Miyasaka, M. Takai, H. Hidaka, Y. Kakimoto and I. Hirasawa, Ultrason. Sonochem., 2006, 13, 308–312 CrossRef CAS PubMed
.
- Y. Deng, J. Li, Y. Deng, H. Nian and H. Jiang, ACS Sustainable Chem. Eng., 2018, 6, 6792–6801 CrossRef CAS
.
- X. Li, Z. Fu, Y. Qiao, Z. Zhang, Y. Zhou, C. Hai, Y. Shen, Y. Sun, J. Zeng and X. Ren, Energy Fuels, 2020, 34, 6439–6447 CrossRef CAS
.
- K. Huang, J. Li, X. Luan, L. Liu, Z. Yang and C. Wang, ACS Omega, 2020, 5, 15210–15217 CrossRef CAS PubMed
.
- C. Liu, C. Wang, Y. Li and Z. Rao, RSC Adv., 2017, 7, 7238–7249 RSC
.
- H. Liu, X. Wang and D. Wu, Sustainable Energy Fuels, 2019, 3, 1091–1149 RSC
.
- W. Aftab, A. Usman, J. Shi, K. Yuan, M. Qin and R. Zou, Energy Environ. Sci., 2021, 14, 4268–4291 RSC
.
- Z. Liu, Z. Chen and F. Yu, Sol. Energy Mater. Sol. Cells, 2019, 200, 110004 CrossRef CAS
.
- N. Navarrete, R. Mondragón, D. Wen, M. E. Navarro, Y. Ding and J. E. Juliá, Energy, 2019, 167, 912–920 CrossRef CAS
.
- Y. Hong and G. Xin-shi, Sol. Energy Mater. Sol. Cells, 2000, 64, 37–44 CrossRef CAS
.
- P. Dixit, J. R. Vennapusa, S. Parvate, J. Singh, A. Dasari and S. Chattopadhyay, Energy Fuels, 2021, 35, 2704–2716 CrossRef CAS
.
- V. J. Reddy, J. S. Yadav and S. Chattopadhyay, Mater. Chem. Phys., 2020, 247, 122859 CrossRef CAS
.
- Y. Konuklu and F. Erzin, Int. J. Energy Res., 2019, 43, 6322–6326 CrossRef CAS
.
- H. Wang, J. Luo, Y. Yang, L. Zhao, G. Song and G. Tang, Sol. Energy, 2016, 139, 591–598 CrossRef CAS
.
- R. Methaapanon, S. Kornbongkotmas, C. Ataboonwongse and A. Soottitantawat, Powder Technol., 2020, 361, 910–916 CrossRef CAS
.
- H. Zhang, X. Wang and D. Wu, J. Colloid Interface Sci., 2010, 343, 246–255 CrossRef CAS PubMed
.
- C. Zhu, Y. Lin and G. Fang, Appl. Therm. Eng., 2020, 169, 114943 CrossRef CAS
.
- J. H. Huo, Z. G. Peng and Q. Feng, J. Appl. Polym. Sci., 2020, 137, 1–10 CrossRef
.
- S. Sami, S. M. Sadrameli and N. Etesami, Appl. Therm. Eng., 2018, 130, 1416–1424 CrossRef CAS
.
- A. Khezri, M. Sahebi and M. Mohammadi, J. Therm. Anal. Calorim., 2022, 147, 7683–7691 CrossRef CAS
.
- A. T. Naikwadi, A. B. Samui and P. A. Mahanwar, Sol. Energy Mater. Sol. Cells, 2020, 215, 110676 CrossRef CAS
.
- X. Huo, W. Li, Y. Wang, N. Han, J. Wang, N. Wang and X. Zhang, Carbohydr. Polym., 2018, 200, 602–610 CrossRef CAS PubMed
.
- S. Han, Y. Chen, S. Lyu, Z. Chen, S. Wang and F. Fu, Colloids Surf., A, 2020, 585, 124046 CrossRef CAS
.
- T.-Y. Sheu and M. Rosenberg, J. Food Sci., 1995, 60, 98–103 CrossRef CAS
.
- H. Ettouney, H. El-Dessouky and E. Al-Kandari, Ind. Eng. Chem. Res., 2004, 43, 5350–5357 CrossRef CAS
.
- A. Sharma, V. V. Tyagi, C. R. Chen and D. Buddhi, Renewable Sustainable Energy Rev., 2009, 13, 318–345 CrossRef CAS
.
- G. A. Lane, Int. J. Ambient Energy, 1980, 1, 155–168 CrossRef
.
- A. Sari and A. Karaipekli, Sol. Energy Mater. Sol. Cells, 2009, 93, 571–576 CrossRef CAS
.
- G. Fang, Z. Chen and H. Li, Chem. Eng. J., 2010, 163, 154–159 CrossRef CAS
.
- N. Soares, J. J. Costa, A. R. Gaspar and P. Santos, Energy Build., 2013, 59, 82–103 CrossRef
.
- S. Mondal, Appl. Therm. Eng., 2008, 28, 1536–1550 CrossRef CAS
.
- D. C. Hyun, N. S. Levinson, U. Jeong and Y. Xia, Angew. Chem., Int. Ed., 2014, 53, 3780–3795 CrossRef CAS PubMed
.
- D. Zhou, C. Y. Zhao and Y. Tian, Appl. Energy, 2012, 92, 593–605 CrossRef CAS
.
- C. Alkan, A. Sari, A. Karaipekli and O. Uzun, Sol. Energy Mater. Sol. Cells, 2009, 93, 143–147 CrossRef CAS
.
- Y. Farnam, M. Krafcik, L. Liston, T. Washington, K. Erk, B. Tao and J. Weiss, J. Mater. Civ. Eng., 2016, 28, 1–10 CrossRef
.
- M. K. Moghaddam, S. M. Mortazavi and T. Khayamian, J. Electrost., 2015, 73, 56–64 CrossRef CAS
.
- H. Zhang, W. Li, R. Huang, N. Wang, J. Wang and X. Zhang, New J. Chem., 2017, 41, 14696–14707 RSC
.
- R. Huang, W. Li, J. Wang and X. Zhang, New J. Chem., 2017, 41, 9424–9437 RSC
.
- X. Zhang, X. Wang and D. Wu, Energy, 2016, 111, 498–512 CrossRef CAS
.
- X. Han, T. Kong, P. Zhu and L. Wang, Langmuir, 2020, 36, 8165–8173 CrossRef CAS PubMed
.
- J. F. Su, Z. Huang and L. Ren, Colloid Polym. Sci., 2007, 285, 1581–1591 CrossRef CAS
.
- Y. F. Fan, X. X. Zhang, S. Z. Wu and X. C. Wang, Thermochim. Acta, 2005, 429, 25–29 CrossRef CAS
.
- J. Zhou, J. Zhao, Y. Cui and W. Cheng, Polym. Int., 2020, 69, 140–148 CrossRef CAS
.
- X. Jiang, R. Luo, F. Peng, Y. Fang, T. Akiyama and S. Wang, Appl. Energy, 2015, 137, 731–737 CrossRef CAS
.
- Z. Zhong-qing, G. Qiang, Y. Jing-min, W. Yan, Y. Jing-yi, Z. Xue, F. Guo-zhong, C. Zhi-Qiang, W. Shao-jie and S. Hong-ge, Sci. Total Environ., 2020, 704, 135394 CrossRef CAS PubMed
.
- X. Wang, Z. Chen, W. Xu and X. Wang, Composites, Part B, 2020, 184, 107744 CrossRef CAS
.
- A. Sari, C. Alkan, A. Karaipekli and O. Uzun, Sol. Energy, 2009, 83, 1757–1763 CrossRef CAS
.
- S. Han, S. Lyu, Z. Chen, F. Fu and S. Wang, Carbohydr. Polym., 2020, 234, 115923 CrossRef CAS PubMed
.
- S. A. Mohamed, F. A. Al-Sulaiman, N. I. Ibrahim, M. H. Zahir, A. Al-Ahmed, R. Saidur, B. S. Yılbaş and A. Z. Sahin, Renewable Sustainable Energy Rev., 2017, 70, 1072–1089 CrossRef CAS
.
- S. Lechtenböhmer, L. J. Nilsson, M. Åhman and C. Schneider, Energy, 2016, 115, 1623–1631 CrossRef
.
- A. Safari, R. Saidur, F. A. Sulaiman, Y. Xu and J. Dong, Renewable Sustainable Energy Rev., 2017, 70, 905–919 CrossRef CAS
.
- L. Chai, X. Wang and D. Wu, Appl. Energy, 2015, 138, 661–674 CrossRef CAS
.
- Y. Wang, T. D. Xia, H. X. Feng and H. Zhang, Renewable Energy, 2011, 36, 1814–1820 CrossRef CAS
.
- C. A. Ikutegbe, R. Al-shannaq and M. M. Farid, Appl. Energy, 2022, 321, 119347 CrossRef CAS
.
-
M. Yadav, N. Pasarkar, A. Naikwadi and P. Mahanwar, Applications, Thermal Conductivity and Modification of Polymeric Phase Change Material for Thermal Energy Storage Applications, Springer Berlin Heidelberg, 2022 Search PubMed
.
- M. You, X. Xiang Zhang, X. Chen Wang, L. Zhang and W. Wen, Thermochim. Acta, 2010, 500, 69–75 CrossRef CAS
.
- D. Fu, Y. Su, B. Xie, H. Zhu, G. Liu and D. Wang, Phys. Chem. Chem. Phys., 2011, 13, 2021–2026 RSC
.
- W. Li, X. X. Zhang, X. C. Wang and J. J. Niu, Mater. Chem. Phys., 2007, 106, 437–442 CrossRef CAS
.
- K. Zhu, H. Qi, S. Wang, J. Zhou, Y. Zhao, J. Su and X. Yuan, J. Macromol. Sci., Part B: Phys., 2012, 51, 1976–1990 CrossRef CAS
.
- J. K. Choi, J. G. Lee, J. H. Kim and H. S. Yang, J. Ind. Eng. Chem., 2001, 7, 358–362 CAS
.
- H. Zhang and X. Wang, Colloids Surf., A, 2009, 332, 129–138 CrossRef CAS
.
- J. Singh, S. Parvate, J. R. Vennapusa, T. K. Maiti, P. Dixit and S. Chattopadhyay, J. Energy Storage, 2022, 49, 104089 CrossRef
.
- Q. Zhao, F. He, Q. Zhang, J. Fan, R. He, K. Zhang, H. Yan and W. Yang, Sol. Energy Mater. Sol. Cells, 2019, 203, 110204 CrossRef CAS
.
- S. Parvate and S. Chattopadhyay, Langmuir, 2022, 38, 1406–1421 CrossRef CAS PubMed
.
- M. J. Mochane and A. S. Luyt, Thermochim. Acta, 2012, 544, 63–70 CrossRef CAS
.
- L. Sánchez-Silva, Á. Alcázar, A. De Lucas, M. Carmona and J. F. Rodríguez, J. Chem. Technol. Biotechnol., 2011, 86, 437–446 CrossRef
.
- M. Ünal, Y. Konuklu and H. Paksoy, Int. J. Energy Res., 2019, 43, 4495–4505 CrossRef
.
- C. Huang, Q. Li, Y. Yang, S. Wei, R. Ji, Q. Zhang, Y. Zhu, H. Zhang, F. Xu, L. Sun and Y. Xia, Sustainable Energy Fuels, 2020, 4, 5203–5214 RSC
.
- M. Alhuyi Nazari, A. Maleki, M. E. H. Assad, M. A. Rosen, A. Haghighi, H. Sharabaty and L. Chen, Sol. Energy, 2021, 228, 725–743 CrossRef CAS
.
- H. Liu, X. Wang and D. Wu, ACS Sustainable Chem. Eng., 2017, 5, 4906–4915 CrossRef CAS
.
- X. Ma, Y. Liu, H. Liu, B. Xu, J. Zhou and F. Xiao, J. Mater. Sci.: Mater. Electron., 2018, 29, 15241–15248 CrossRef CAS
.
- T. A. Saleh, J. Mol. Liq., 2022, 359, 119340 CrossRef CAS
.
- T. A. Saleh, Trends Environ. Anal. Chem., 2020, 25, 1–8 Search PubMed
.
- K. Yuan, J. Liu, X. Fang and Z. Zhang, J. Mater. Chem. A, 2018, 6, 4535–4543 RSC
.
- Y. Li, C. Li, N. Lin, B. Xie, D. Zhang and J. Chen, Mater. Today Energy, 2021, 22, 100866 CrossRef CAS
.
- R. Guo, L. Shan, Y. Wu, Y. Cai, R. Huang, H. Ma, K. Tang and K. Liu, Mater. Today Energy, 2022, 23, 100888 CrossRef CAS
.
- D. Kim, J. Jung, Y. Kim, M. Lee, J. Seo and S. B. Khan, Int. J. Heat Mass Transfer, 2016, 95, 735–741 CrossRef CAS
.
- C. Li, B. Zhang, B. Xie, X. Zhao and J. Chen, Energy Convers. Manage., 2020, 208, 112586 CrossRef CAS
.
- G. Fang, M. Yu, K. Meng, F. Shang and X. Tan, Energy Fuels, 2020, 34, 10109–10119 CrossRef CAS
.
- S. Parvate, J. Singh, J. Reddy Vennapusa, P. Dixit and S. Chattopadhyay, J. Ind. Eng. Chem., 2021, 102, 69–85 CrossRef CAS
.
- L. F. Cabeza, A. Castell, C. Barreneche, A. De Gracia and A. I. Fernández, Renewable Sustainable Energy Rev., 2011, 15, 1675–1695 CrossRef CAS
.
- F. He, X. Wang and D. Wu, Energy, 2014, 67, 223–233 CrossRef CAS
.
- L. Y. Wang, P. S. Tsai and Y. M. Yang, J. Microencapsulation, 2006, 23, 3–14 CrossRef CAS PubMed
.
- H. Li, X. Liu and G. Fang, Energy Build., 2010, 42, 1661–1665 CrossRef
.
- W. Su, J. Darkwa and G. Kokogiannakis, Renewable Sustainable Energy Rev., 2015, 48, 373–391 CrossRef CAS
.
- W. Ji, X. Cheng, S. Chen, X. Wang and Y. Li, Powder Technol., 2021, 385, 546–556 CrossRef CAS
.
- S. Sharma, A. Tahir, K. S. Reddy and T. K. Mallick, Sol. Energy Mater. Sol. Cells, 2016, 149, 29–39 CrossRef CAS
.
- S. Altin, Ö. Anil, M. E. Kara and M. Kaya, Composites, Part B, 2008, 39, 680–693 CrossRef
.
- L. Cao, F. Tang and G. Fang, Sol. Energy Mater. Sol. Cells, 2014, 123, 183–188 CrossRef CAS
.
- L. Zhao, H. Wang, J. Luo, Y. Liu, G. Song and G. Tang, Sol. Energy, 2016, 127, 28–35 CrossRef CAS
.
- C. Li, G. He, H. Yan, H. Yu and Y. Song, Energy Procedia, 2018, 152, 390–394 CrossRef CAS
.
- M. Li, J. Liu and J. Shi, Sol. Energy, 2018, 167, 158–164 CrossRef CAS
.
- Y. Zhao, X. Zhang, X. Xu and S. Zhang, J. Energy Storage, 2020, 30, 101455 CrossRef
.
- S. Yu, X. Wang and D. Wu, Appl. Energy, 2014, 114, 632–643 CrossRef CAS
.
- A. Sarı, T. A. Saleh, G. Hekimoğlu, V. V. Tyagi and R. K. Sharma, J. Mol. Liq., 2021, 328, 115508 CrossRef
.
- J. Shi, X. Wu, R. Sun, B. Ban, J. Li and J. Chen, Colloids Surf., A, 2019, 571, 36–43 CrossRef CAS
.
- P. Dixit, S. Parvate, V. Jagadeeswara, J. Singh, T. Kanti, A. Dasari and S. Chattopadhyay, J. Energy Storage, 2022, 55, 105491 CrossRef
.
- T. Wang, S. Wang, R. Luo, C. Zhu, T. Akiyama and Z. Zhang, Appl. Energy, 2016, 171, 113–119 CrossRef CAS
.
- Z. Jiang, W. Yang, F. He, C. Xie, J. Fan, J. Wu and K. Zhang, Langmuir, 2018, 34, 14254–14264 CrossRef CAS PubMed
.
- H. Wei, F. He, Y. Li, Q. Zhang, Y. Zhou, H. Yan, R. He, J. Fan and W. Yang, ACS Sustainable Chem. Eng., 2019, 7, 18854–18862 CrossRef CAS
.
- C. Cai, X. Ouyang, L. Zhou, G. Liu, Y. Wang, G. Zhu, J. Yao, J. Militky, M. Venkataraman and G. Zhang, Sol. Energy, 2020, 199, 721–730 CrossRef CAS
.
- S. Zhan, S. Chen, L. Chen and W. Hou, Powder Technol., 2016, 292, 217–222 CrossRef CAS
.
|
This journal is © The Royal Society of Chemistry 2023 |
Click here to see how this site uses Cookies. View our privacy policy here.