DOI:
10.1039/D2SU00014H
(Tutorial Review)
RSC Sustainability, 2023,
1, 179-212
Replacing all petroleum-based chemical products with natural biomass-based chemical products: a tutorial review
Received
12th August 2022
, Accepted 28th November 2022
First published on 3rd January 2023
Abstract
Immediate action is necessary to alleviate the severe environmental problems such as climate change, deforestation, and plastic pollution. One of the reasons for global warming is the emission of carbon dioxide (CO2), which has significantly increased due to the burning and consumption of petroleum fossil fuel by humans to produce chemical products and fuels in modern society. In this regard, natural biomass- or plant-derived chemical products and fuels can be considered as carbon neutral because plants absorb CO2 during their growth. In addition, the use of biomass biodegradable chemical products such as biodegradable plastic can also mitigate the plastic pollution problem. Nowadays, living organisms and the environment are not only contaminated by micro-plastics but also nano-plastic in the air. Thus, herein, some studies and products (biomass biodegradable plastic, coatings, paints, plasticizers, lubricants, etc.) are presented, aiming to replace all the petroleum-derived chemical products and fuels with natural biomass-derived products based on the concept of “no more petroleum, no more fossil fuels”.
Sustainability spotlight
Our company, Green Science Alliance (Fuji Pigment Co., Ltd. Group) focuses on green technology to create a sustainable, carbon neutral society. This includes creating and developing green chemicals, next-generation-type rechargeable batteries, fuel cells, solar cells and CO2 capture and conversion technologies. One of our topics is developing sustainable chemical products from natural biomass resources. We aim to replace all the petroleum-based chemical products with biomass-based chemical products. Although this is a bold statement and hot topic, we are headed towards that direction. Typical examples are biomass biodegradable plastics, biomass paints, and biomass coatings.
|
Introduction
Currently, the devastating environmental problems such as climate change, global warming, natural resource depletion, water pollution, deforestation, extinction of species and plastic pollution require immediate mitigating measures. One of the reasons for global warming is considered to be the emission of carbon dioxide (CO2), which has significantly increased by burning and consuming petroleum fossil fuel by humans to produce chemical products and fuels for modern society. In this regard, natural biomass- or plant-derived chemical products and fuels can be considered carbon neutral because plant absorbs CO2 during their growth and the total CO2 emission will be low or zero after they degrade after usage. Therefore, developing biomass-derived chemical products is one of the ways to reduce CO2 consumption to suppress global warming. In general, these types of biomass-based plastics tend to exhibit biodegradability due to their natural-origin molecular structure.1–3 Some biomass-derived plastic and biochemical products are not biodegradable. However, they contribute to the reduction of CO2 as their raw materials are considered carbon neutral. A good example is biomass polyethylene, as will be discussed in more detail in the following sections, which is made of biomass resources such as corn and sugarcane. These raw materials can be considered carbon neutral because they absorb CO2 from the surrounding environment during their growth. Ethylene is prepared from bio-ethanol, which is produced by fermenting agricultural crops. Biomass polyethylene can be manufactured via the polymerization of biomass-derived ethylene. If ethanol is made from the residual liquid after sugar has been taken from squeezed sugarcane juice, the food competition issue can also be avoided.4
Plastic pollution is also a concern, where micro-plastic pollution problem is destroying nature including the marine environment. Over the past century, plastics have been made from petroleum and consumed in large quantities, leading to huge amounts of CO2 emission during their production and consumption. Although some bioplastics have been developed and are being used, over 97% of plastics are still petroleum based, given that they are cheaper and stronger than bioplastics. However, it is obvious that these petroleum-derived plastics cause plastic pollution in the environment.5–7 Ultraviolet light exposure and physical mechanical force on these plastics after disposal break them down into micro-plastics. It has been found that micro-plastics enter the human body through the consumption of fish from oceans polluted with micro-plastics. In addition, the human body can be contaminated by inhaling nano-plastics present in air, which is worse than ingestion of micro-plastics.8–10 Specifically, nano-plastics have a size on the nanometer scale (1 × 10−9 m), which is similar to that of the COVID-19 virus. In particular, the chemical substance called phthalic ester, which is used as a plasticizer, has been found to be harmful to human health, and thus careful investigations are being carried out.11 Unfortunately, even though the above-mentioned concerns have been clarified, the production of petroleum-derived non-biodegradable plastics continues to increase. Therefore, the production and consumption of non-biodegradable plastics must be reduced and research and practical applications of biodegradable plastics that can decompose to CO2 and water and return to nature ultimately need to be accelerated.
Alternatively, considering actual plastic products such as plastic bags and packaging products, for example, coating materials and color paints, they also need to be biomass based and biodegradable because even if the internal plastic is biodegradable, if the covering coating material or paint is composed of petroleum-derived non-biodegradable chemicals, the entire product will not be bio-decomposed for thousands of years because its outer surface would protect the internal biodegradable plastics. Thus, it is necessary to also create these coating materials and color paints from natural biomass or plants.12–14 In the modern society, most chemical products are made from petroleum such as plastics, resins, rubber, textiles, color paints, and cosmetics (Fig. 1).15 Thus, it is an ideal concept to replace all these petroleum-derived chemical products and fuels with natural biomass-derived ones.
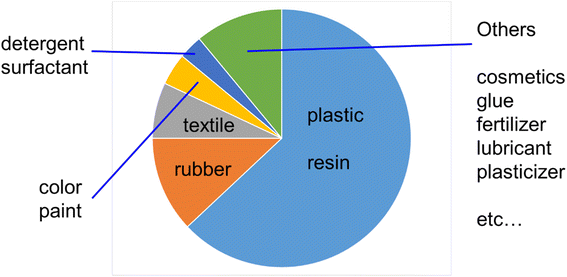 |
| Fig. 1 Production quantity of petroleum-derived chemical products.15 | |
Biomass-based chemical products. “No more petroleum, no more fossil fuel”
Herein, various types of biomass-based chemical products such as bioplastics, biomass coatings, biomass paints, biomass plasticizers, and biomass lubricants will be presented based on the above-mentioned concept of replacing all petroleum-derived chemical products with natural biomass-derived chemicals. Accordingly, the concept of “no more petroleum, no more fossil fuel” is proposed.
Initially, the aim is to explain what types of plastics exist, and also biodegradable plastics, biomass plastics, and bioplastics. The precise term for plastics is ‘thermoplastic resin’, which can be classified into four categories in terms of their biodegradability and biomass content.
Category 1. Petroleum-derived non-biodegradable plastics
This category of plastics has been produced and consumed for over 100 years and is the major contributor of plastic pollution. As mentioned above, over 98% of plastic production still involves this type of plastic. Consequently, plastic pollution is rapidly worsening daily. The typical examples of this type of plastic are polypropylene (PP: [C3H6]n), polyethylene (PE: [C2H4]n), polyvinyl chloride (PVC: [C2H3Cl]n), polyethylene terephthalate (PET: [C10H8O4]n), and polystyrene (PS: [C8H8]n). In brief, these plastics are called general plastics.
Category 2. Petroleum-derived biodegradable plastics
This category of plastics is made from petroleum but exhibit biodegradability. Typical examples include polybutylene succinate (PBS), poly(butylene adipate-co-terephthalate) (PBAT), and polyvinyl alcohol (PVA). These biodegradable plastics have recently been applied in the fields of agriculture, films, etc.
Category 3. Biomass-based non-biodegradable plastics
This category of plastics is made of biomass but does not exhibit biodegradability. An example is biomass polyethylene, which has recently been used to produce shopping bags in Japan. This type of plastic can be regarded as environmentally friendly in terms of reducing CO2 emissions because they are made of biomass, not petroleum.
Category 4. Biomass-based biodegradable plastics
According to the above-mentioned qualities, the ideal plastic is the one that is both biodegradable and made from biomass. Examples of this type of plastic are polylactic acid (PLA), starch-based biodegradable plastic, cellulose-based biodegradable plastic, and polyhydroxyalkanoate (PHA). Herein, the focus is biomass biodegradable plastics.
Categories 2 and 4 are called ‘biodegradable plastics’, categories 3 and 4 are called ‘biomass plastics’, and categories 2, 3, and 4 are called ‘bioplastics’. Although these terms may seem slightly complicated, by understanding the concept of the four types of plastics, one can recognize plastics in terms of raw material (petroleum or biomass) and functionality (biodegradable or non-biodegradable) (Fig. 2).16 These terms are also precise and easy to discuss.
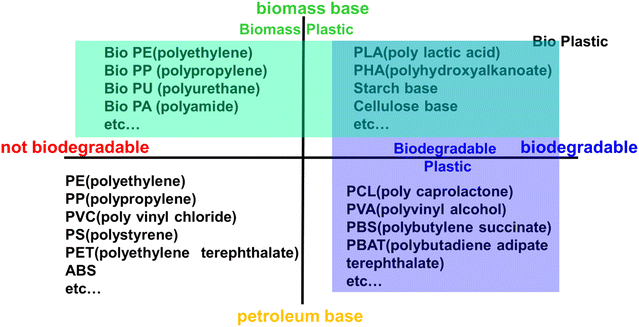 |
| Fig. 2 Classification of plastic according to biomass and biodegradability. | |
In the following sections, the various types of bioplastics will be explained based on the above-mentioned four categories. However, category 1 will be omitted given that it is simply petroleum-derived non-biodegradable plastics. In the following sections, several typical bioplastics are discussed, but there are several other bioplastics available.
Category 2
PBAT: polybutylene adipate-co-terephthalate: (H–(O–(CH2)4–O–CO–(CH2)4–CO–)n–(O–(CH2)4–O–CO–C6H4–(O–)m–H)
As mentioned above, some plastics are made of petroleum but possess good biodegradability. PBAT is one of these biodegradable plastics and it has practical applications in agricultural films, medical devices, and films. PBAT is also physically flexible and easy to process for industrial use. In addition, attempts have been made to use PBAT as a material for coating and packaging and in the fishing industry. The tensile strength, Young's modulus, and elongation at break of PBAT are all comparable to that of low-density polyethylene (LDPE).17,18 PBAT is a biodegradable polyester thermoplastic resin synthesized via the polymerization of 1,4-butanediol, terephthalic acid, and adipic acid. Given that PBAT is an aliphatic and aromatic copolymer, it has high biodegradability from the aliphatic polyester structure and strong mechanical strength from its aromatic polyester structure. In addition, PBAT has the advantageous features of high ductility, elongation at break, and impact strength. Also, PBAT has been certified as compost and soil-biodegradable.
PBS: polybutylene succinate: (C8H12O4)n
PBS is a polyester resin synthesized via the condensation polymerization of succinic acid and 1,4–butanediol. It has higher temperature durability and processability among the various types of biodegradable plastics, as well as higher impact strength, tear strength, and ductility.19,20 However, it is a petroleum-derived biodegradable plastic. Therefore, research is being conducted to replace petroleum-based succinic acid with a biomass-based, where half its mass can be replaced with biomass. Another challenge is replacing petroleum-derived 1,4-butanediol with biomass, which is also being investigated. Attempts have been made to apply PBS in the production of agricultural films, paper cups, straws, coffee capsules, etc. Due to the chemical composition of PBS, it is non-toxic and biodegradable in the presence of water and CO2 with various types of bacteria and enzymes of animals and plants. Therefore, it is being used for the production of cosmetic containers, medical devices, packaging containers, garbage bags, bottles, etc. PBS can be defined as home compostable, indicating that an industrial composting system is not required for this type of plastic. Furthermore, PBS is highly compatible with other biodegradable plastics such as PLA. PBS also has a high level of heat sealing, which is as good as that of polyethylene. PBS has been certified as compost, compost home and soil-biodegradable.
PVA: polyvinyl alcohol: [CH2CH(OH)]n
PVA can be used for many applications, including the production of vinylon fibers, texture processing, paper processing, films, glue, stabilizers for emulsion dispersion, binders, medical use, and polarizing films for television screens and computer monitors. It occupies approximately 70% of the market share of water-soluble petroleum-derived resin.21,22 PVA can be biodegraded by various types of bacteria in the environment. It has strong adhesion property toward materials with a hydrophilic surface such as paper or wood because PVA can be modified by acetalization reaction or with boric acid or borax owing to its hydroxyl group. Another feature of PVA is that a strong transparent film can be prepared. In this case, PVA with a higher degree of saponification and polymerization can exhibit a strong transparent film. PVA can be prepared by saponifying polyvinyl acetate, which can be obtained by polymerizing vinyl acetate. Highly saponified PVA has robust crystallinity due to the presence of hydrogen bonds in its molecular structure and it is insoluble in cold water. By contrast, PVA is soluble in cold water when it is partially saponified. In this case, the acetic acid group and hydroxyl group function as hydrophobic and hydrophilic groups, respectively. Thus, partially saponified PVA possesses surfactant-like ability, where it can lower the surface tension of a liquid.
PGA: polyglycolic acid: (C2H2O2)n
PGA is a biodegradable polyester resin composed of repeated base units of glycol acid, which is a α-hydroxyl carboxylic acid.23,24 Due to its simple structure, PGA has high strength, durability against organic solvents, and chemicals, and it is biodegradable under composting conditions. PGA is used as medical suture owing to its strength and biodegradability in the human body. The hydrolysis of PGA is faster and it possesses higher strength, elasticity, friction resistance, organic solvent resistance, and heat resistance compared with PLA. Hence, it is used to produce various types of industrial parts and non-woven fibers and filaments. Recently, owing to its toughness and good biodegradability, PGA has been applied in the shale gas and petroleum drilling fields, reducing their cost and environmental damage. However, the melting point of PGS is relatively high (220–230 °C) and it is a hard solid polymer. Therefore, to lower its melting temperature and increase its biodegradability, PGA is often mixed with PLA or poly-ε-polycaprolactone to prepare copolymers, and consequently they can be used for sutures that are better suited for medical operations. It should be mentioned that the high gas barrier of PGA is another one of its notable features. PGA has been certified as compost biodegradable.
PCL: polycaprolactone: (C6H10O2)n
PCL is a caprolactone polymer with a molecular weight of more than 25
000 and is a biodegradable thermoplastic resin with a relatively low melting temperature (60 °C), which can be obtained by polymerizing ε-polycaprolactone.25,26 Owing to the high heat stability and low melting temperature of PCL, thermal decomposition and hydrolysis are not serious problems in the extruder, making PCL suitable for the production of films, sheet molding, injection molding, and yarning. Attempts have been made to utilize PCL for the production of agricultural films and compost bags, as well as glue, because of its high adhesion property due to its high crystallinity. PCL has been considered as a polymer alloy and pigment dispersant because of its relatively high compatibility with other resins. Moreover, PCL can be applied for medical use; as an additive to optimize the impact strength or other properties such as viscosity, fluidity, and refractive index of other resins; as a binder for ceramic and metals; and as a thermal transfer ink. Because the molecular structure of PCL is similar to that of cutin, which is an aliphatic polyester polymer that exists on natural plant surfaces, its biodegradability is relatively high because cutin can be decomposed by various types of lipase. Also, PCL has been certified as compost biodegradable.
It should be noted that as mentioned above, category 2 bioplastics have been applied in the production of food packaging, garbage bags, paper cups, cosmetic containers, films, agricultural films, medical devices, bottle, paper processing, non-woven fibers and filaments, etc. However, these bioplastics are derived from petroleum, and thus they do not contribute to reducing CO2 emissions. Nevertheless, in the medical field, in which biodegradability is a critical issue for patients to experience high-quality surgery for their life and health, this type of bioplastic is very useful. It needs to be biodegraded in the human body after it is placed in the body during surgery. Another example is that it can be effective for agricultural use. This is because the available agricultural films are made of PE and farmers have to clean up the PE or fragmented PE films after agricultural products are harvested after each season. In this regard, if agricultural films are biodegradable, farmers do not have to clean up because they can go back into the soil by biodegradation.
Category 3
Biomass polyethylene: (C2H4)n
Biomass polyethylene is made from biomass and has been recently utilized as a raw material for the production of shopping bags in Japan. Firstly, bioethanol is made from biomass such as corn and sugarcane. Then, biomass polyethylene can be prepared by polymerizing ethylene, which is obtained by dehydrating bioethanol.27,28 This resin does not have biodegradability and becomes a polluting plastic after use. However, because sugarcane and corn, as the raw materials, absorb CO2 during their growth, the total CO2 emission can be regarded as zero (thus carbon neutral) when this material is disposed of. Thus, including the manufacturing process, CO2 can be reduced by up to 70% compared to petroleum-derived polyethylene.
Polyamide 11: C12H20N2O2
Polyamide 11 (nylon 11) is an engineering plastic derived from biomass and it is an aliphatic polyamide with a melting temperature of approximately 185 °C. It can be synthesized by polymerizing 11-aminoundecanoic acid, which can be obtained from castor oil.29,30 This polyamide has a relatively long methylene chain, which facilitates good heat and chemical resistance, which is a representative feature of polyamide. Compared to nylon 6, polyamide 11 is made from biomass and has higher abrasion resistance and flexibility even at low temperature. Its specific gravity is also ideal. Its amide bond concentration is lower than that of other polyamides, and thus it has a lower water absorption ratio. Therefore, it has the advantages of high dimensional stability and mechanical strength and it is not greatly affected by surrounding water. Given that polyamide 11 consists of an odd number of methylene groups, it will form a crystal structure that is different from that of polyamide 12, which has even number of methylene groups. Because of its high flexibility, processability, and gasoline resistance, polyamide 11 has been applied for the production of automotive fuel tubes, air brake tubes, food washing cages, connector covers for computers, cable ties, etc. Recently, attempts have been made to apply it for mechanical devices that use high-pressure hydrogen. Polyamide 11 is advantageous in terms of its raw material source because it is obtained from non-edible plant biomass and not edible ones such as corn and sugarcane.
Biomass PET: biomass polyethylene terephthalate: [C10H8O4]n
Biomass PET is made from terephthalic acid and monoethylene glycol, which is obtained from biomass such as sugarcane. Biomass PET has the same level of heat resistance and mechanical strength as petroleum-derived PET. PET bottles are commonly used for storing beverages. The other part of the PET raw material, terephthalic acid, is derived from p-xylene, which is somewhat difficult to source from plant biomass, although recent research has succeeded in preparing p-xylene from plant biomass. Some scientific studies have succeeded in creating 100% natural biomass-derived PET bottles by using both terephthalic acid and monoethylene glycol obtained from biomass.31,32 This research is being intensively carried out to take advantage of biomass PET to reduce not only environmental damage but also mass production costs.
Biomass polyurethane: C27H36N2O10
The raw materials of polyurethane are polyol, diisocyanate, and additives to elongate its polymer chain. Polyol with two or three functional groups and molecular weight in the range of 1000–3000 is often used. Polyol is the material with the highest content in urethane foam, and this if petroleum-derived polyol can be replaced with biomass-derived polyol, then this will be a big step for the polyurethane industry to move toward a sustainable industry. Therefore, intensive research on creating polyurethane foam from polyol derived from plants and plant-based oils, such as soy bean oil and castor oil, has been carried out. Castor oil is preferred over other plant oils such as sunflower oil, perm oil, and olive oil because it contains more hydroxyl groups, enabling it to be used without additional treatment. Polyol has also been synthesized from sugar derivatives such as D-glucose, D-mannitol, and meso-erythritol. Meanwhile, biomass-derived isocyanates such as hexamethylene diisocyanate and 1,6-diisocyanatohexane have been synthesized from unsaturated fatty acids such as oleic acid. Therefore, 100% biomass polyurethane has been prepared from these isocyanates and the above-mentioned polyols.33,34 Biomass polyurethane can be widely applied in the construction of buildings, electronic products, biomedical applications, and other industrial products as paints, foams, coating films, elastomers, adhesives, integral skins, and rigid plastics.
Polyethylene furanoate (PEF): (C8H6O5)
Polyethylene furanoate (PEF) was developed to potentially replace its fossil-fuel counterpart polyethylene terephthalate (PET) to reduce greenhouse gas emissions. PEF can be prepared via the polymerization of 2,5-furandicarboxylic acid and ethylene glycol. These raw materials can be derived from biomass renewable raw materials obtained from plants. Compared to PET, PEF demonstrates superior barrier ability, higher mechanical and thermal properties. Furthermore, PEF has a higher glass transition temperature and lower melting point than PET. It can be 100% biomass-based when both 2,5-furandicarboxylic acid and mono ethylene glycol are obtained from biomass resources. Especially 2,5-furandicarboxylic acid (C6H6O3; MW = 126.11) is a bio-based building block for the synthesis of resins and polymers. Thus, the potential of 2,5-furandicarboxylic acid is not only limited to PEF but also other materials including polyesters, polyamides, copolymers, solvents, coating resins, plasticizers, etc. It is made via the oxidative dehydration of hexose. The conversion can also be carried out via the oxidation of 5-hydroxymethylfurfural (HMF). Therefore, 2,5-furandicarboxylic acid has large potential to be a replacement for terephthalic acid. Furthermore, its manufacturing process is similar to that of PET and terephthalic acid can be substituted with 2,5-furan dicarboxylic acid.35,36 Thus, it is expected that PEF can be applied for the production of films, fibers, bottles, textiles, etc.
It should be noted here that category 3-type bioplastics contribute to a reduction in CO2 emissions because they are derived from natural biomass, but they still become microplastic pollution because they are not biodegradable.
Category 4
PLA: polylactic acid: (C3H4O2)n
PLA is one of the typical biomass biodegradable plastics made from biomass such as corn, sugarcane, and starch. Firstly, glucose is obtained via the enzymatic hydrolysis of starch and is converted to L-lactic acid by fermentation. Finally, PLA is obtained by polymerizing lactic acid. Approximately 0.4 kg of PLA can be prepared from 1 kg of biomass (corn). However, a drawback is that PLA is made from edible biomass such as corn and sugarcane, which can be nutritious food for human beings. Therefore, research has been carried out on preparing PLA from non-edible biomass such as cellulose. The crystalline structure, melting point, mechanical strength, and biodegradability of PLA depend on the quantity of D-lactic acid, L-lactic acid, and DL-lactic acid present in the polymer. The D- and L-lactic acids differ in terms of the position of the asymmetric carbon in lactic acid.37,38 Although PLA is difficult to decompose in the normal environment with slow biodegradability in the soil, water, and marine environment, it is biodegradable in composting conditions within half a year, which satisfies the ISO standard. Thus, PLA can be regarded as a biodegradable polymer in composting conditions. PLA can be used for the production of food packaging, wrappings, laminates, containers (bottles and cups), etc., as well in the biomedical field given that it can be applied as suture threads, bone fixation screws, devices for drug delivery, etc. PLA has been certified as compost biodegradable.
PHA: polyhydroxyalkanoate
Bacteria consume plant oil such as perm oil and store it as an energy source, and some biopolymers can be prepared from these raw materials in bacteria. Many types of bacteria in the soil produce PHA. The typical biodegradable plastics of this type are PHA, poly(3-hydroxybutyric acid) (P3BH), and poly(3-hydroxybutyrate-co-3-hydroxyvalerate) (PHBV: [COCH2CH(CH3)O]m[COCH2CH(C2H5)O]n).39,40 Initially, research focused on PHA with the simplest structure, which is P3BH. However, P3HB was found to deteriorate quickly after its synthesis. Therefore, efforts are focused on improving the properties of resins by varying and optimizing factors such as the type of bacteria, food for bacteria, culturing methods, gene mutation, chemical additives, and processing methods. The high cost of PHA is another problem, where it is approximately 3–4 times more expensive than the commonly used petroleum-derived plastics such as PE and PP. The high cost of PHA is mainly attributed to the requirement of food for bacteria, complexity of the production process, separation of bacteria from the biodegradable plastic, extraction and waste fluid extraction and treatment. In addition, the temperatures of the melting point and thermal decomposition are close, and thus it difficult to control the plastic melting process. This may result in poor resin properties of the final molded product due to the low molecular weight of the polymer. Hence, it is necessary to widen the temperature difference of the melting point and thermal decomposition point to make the final molding product from PHA in an easier manner with a simpler melting process. Consequently, PHA biodegradable plastics were initially difficult to handle, but thanks to efforts by researchers, PHA is now being used for the production of films, injection moldings, fibers, textiles, and biocompatible materials. Furthermore, P3HB is biodegradable by various kinds of bacteria in nature and even in the marine environment. PHA-derived poly 3-hydroxybutyrate-co-3-hydroxyhexanoate (PHBH) has been certified as marine biodegradable.
Starch-based biodegradable plastics: (C6H10O5)n
Annually, approximately 2.6 billion tons of grains are harvested, which are precious biomass resources. Starch can be obtained from grains, and with the well-established manufacturing process of starch, the cost of manufacturing starch from grain is low. As explained above, PLA can be obtained from starch by fermentation. Meanwhile, attempts have been made to develop biodegradable plastics from starch itself by providing starch with thermoplastic ability, which can be a cheaper process than the fermenting process. Starch is a sequential chain of glucose unit polymers and is composed of the straight chain structure of amylose and the branched structure of amylopectin. It has crystallinity and does not become thermoplastic given that it does not melt even when the thermal decomposition temperature is reached. Starch has already been used as a glue. By contrast, modified starch such as starch ether, esterified starch, and phosphor acid-linked starch has been implemented as food and for industrial use. Furthermore, starch-based biodegradable plastics have good compatibility with cellulose and polyester-based plastics.41,42 Thus far, starch-based biodegradable plastics have been applied in the production of films, cushioning materials, foaming materials, containers, injection molding, inks, paints, etc. Starch-based biodegradable plastic has been certified as compost to marine biodegradable depending on its grade and manufacture.
Cellulose-based biodegradable plastics: (C6H10O5)n
As explained above, PLA and starch-based biodegradable plastics originate from biomass such as corn, grains, potato, sugarcane, and starch. However, given that they are precious food for human beings, their use can aggravate hunger problems due to the increasing global population. Therefore, it is preferable to utilize non-edible biomass such as cellulose as the raw material for the production of biodegradable plastics. Cellulose is the main component of plants and wood and is the most abundant natural resource on Earth, making up half of the dry weight of all plants, wood, grass, and weeds. Its annual production is dozens of billions of tons. Thus, the quantity of available cellulose can be more than the quantity of petroleum. To obtain the raw material for biodegradable plastics, it will not be necessary to cut down new trees but rather use the sufficient amount of existing waste wood. Furthermore, the price of cellulose-based biodegradable plastics can be cheaper because they can be created efficiently.44 Some studies have attempted to decompose cellulose with acids or enzymes to form sugar and create cellulose-based plastics. However, this method is expensive because the cost of the decomposition or acid pretreatment process and the required enzymes is too expensive for practical industrial processes. A typical cellulose-based plastic is cellophane; however, some chemicals used during the cellophane manufacturing process are considered to be dangerous for industrial processes. Thus, a new type of cheap and safe cellulose-based biodegradable plastic is still to be developed. Cellulose-based biodegradable plastics such as cellulose acetate have been certified as marine biodegradable. However, their biodegradability is different depending on the type of cellulose-based chemical formula.
Safety of biodegradable plastics
It is necessary to test the safety of biodegradable plastics and the intermediate and final substances during and after biodegradation, considering their effects on human health and the natural environment, such as on plant growth.45 Biomass-based plastics such as PLA, starch-based, and cellulose-based biodegradable plastics can be considered sufficiently safe, whereas petroleum-derived biodegradable plastics are potentially dangerous because of the presence of chemical additives such as degradation promoters and plasticizers.46 In particular, testing of the safety of intermediate chemicals is very complicated. In addition, in the case of biodegradable plastics used for food packaging and containers, which may have direct contact with foods, it is necessary to consider food sanitation acts. Similarly, for medical or hygiene products, pharmaceutical law must be checked and for compost usage and fertilizer control regulations need to be checked.
Biodegradability and certification
The grade and degree of the biodegradability of biodegradable plastics in each condition are crucial topics. According to the accurate definition of biodegradation, biodegradation begins with the materials being consumed by bacteria to decompose them, finally being completely converted to water and CO2.47 An example of a typical organization that authorizes biodegradability is TÜV Austria in Europe. The following are the standards for biodegradation prescribed by TÜV.48
① OK compost industrial.
The lowest level of biodegradability and the necessary condition is that over 90% of the biodegradable plastic sample needs to be bio-decomposed under aerobic composting conditions at 58 °C within 6 months. Bacteria are abundant under compost conditions, and thus it is at least ideal to have this certification.
② OK compost home.
The next level of biodegradability is for the home environment and the necessary condition is that over 90% of the biodegradable plastic sample needs to be bio-decomposed under composting conditions at 28 °C within 6 months.
③ OK biodegradable soil.
For the biodegradability certificate in a soil environment, the necessary condition is that over 90% of the biodegradable plastic sample needs to be bio-decomposed in the soil at 25 °C within 2 years.
④ OK biodegradable water.
For the biodegradability certificate in water, the necessary condition is that over 90% of the biodegradable plastic sample needs to be bio-decomposed in water at 20–25 °C within 56 days.
⑤ OK biodegradable marine.
For the biodegradability certificate in sea water, the necessary condition is that over 90% of the biodegradable plastic sample needs to be bio-decomposed in sea water at 30 °C within 6 months. This is the most ideal biodegradation certification.
In addition, the certificate called OK Biobased indicates the degree of biomass content in the product material. Specifically, it is an index of how much of the material is made from biomass and not petroleum. The biomass degree is higher if the OK Biobased number is higher. TÜV Austria assigns this number by measuring the biobased carbon content (BCC), total organic carbon content (TOC), and ash content in the product material.
Biodegradability testing can also be carried out individually using a commercial biodegradability measuring machine (Fig. 3). It was found out that the biodegradability of a nanocellulose PLA composite material is faster than that of pure PLA (Fig. 4).49 It was suggested that the cellulose fibers in PLA biodegraded initially, which enhanced the biodegradability of whole PLA composite. There are also some green plastics and biomass plastic certificates from the Japan BioPlastics Association (JBPA) (Fig. 5).50
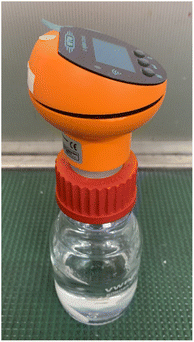 |
| Fig. 3 Commercial biodegradability measuring machine. | |
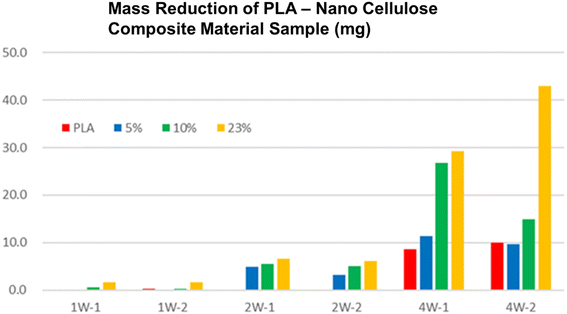 |
| Fig. 4 Biodegradability test result. It can be seen that biodegradability increased as the content of nanocellulose increases in the PLA-nanocellulose composite material.49 | |
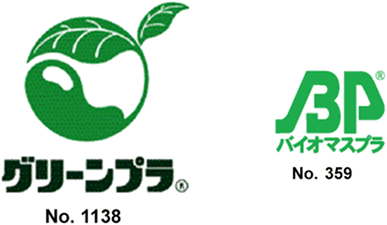 |
| Fig. 5 Green plastic certificate (Left) and biomass plastic certificate (Right) from JBPA.50 | |
It is preferable to develop bioplastics that are biomass-based and have a high degree of biodegradability, that is, belonging to category 4. Therefore, in the following section, the focus will be category 4 bioplastic materials and other bio based chemical products.
Starch-based biodegradable plastics
Sapuan et al. prepared starch-derived bioplastic via the casting method. They used corn starch, water and plasticizer to prepare a starch-based film at 85 °C (Fig. 6). They demonstrated that varying the concentration and type of plasticizer significantly affected the different properties of the plasticized films. Therefore, the selection of a suitable plasticizer at an appropriate concentration may significantly optimize the film properties to promote the utilization of films, sheet and food packaging applications.51 Because starch-based biodegradable plastics are mechanically weak and their water resistance is generally low, it is necessary to develop starch-based biodegradable plastics with better properties. Zhang et al. prepared an easily available novel starch derivative, i.e., dialdehyde starch-based polyimine. This type of resin exhibits high thermal malleability and can be thermoformed without any plasticizer. Dialdehyde starch-based polyimine plastics have mechanical strength as high as 40.6 MPa, possess high water and chemical resistance and high thermal stability, while they are also biodegradable.52 Moreover, Zdanowicz et al. created thermoplastic starch with a ternary deep eutectic solvent (DES) based on urea/resorcinol/choline chloride in a 2
:
1
:
1 molar ratio and combined it with lignin. DES was effective as a plasticizer to make potato starch-based plastic without a significant loss in its elasticity and thermo-compressing properties (tensile strength of 7.4 MPa and elongation at break of 65%). It was also clarified by XRD that the prepared starch-based plastic was an amorphous material. DES was found to dissolve lignin to facilitate the extruder process. Furthermore, cone calorimetry analysis of starch-based plastics revealed that they demonstrated better fire-retardant properties than the commercially used polymers (PE, PP, and PLA).53
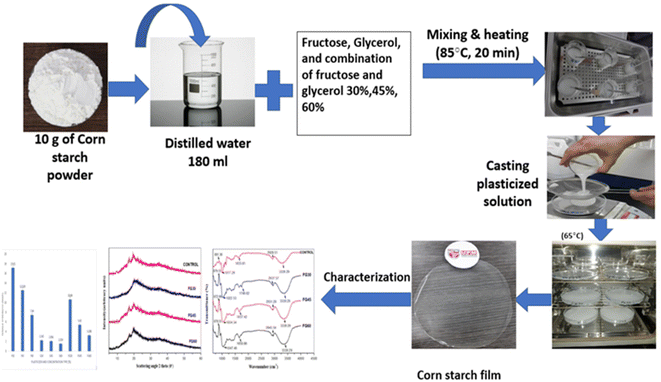 |
| Fig. 6 Procedure for the preparation of starch-based bioplastic by the casting method.51 Starch bioplastic was prepared by mixing corn starch, water and plasticizer. | |
As an alternative to their method, my group prepared a 100% natural biomass starch biodegradable plastic with a twin screw extruder, which could be applied for more industrial usage for mass production. Moreover, compared to other starch-based biodegradable plastics, these starch-based biodegradable plastics are composed of 100% natural biomass materials, including additives. As mentioned in the above-mentioned section, we tried not to use any petroleum-based chemicals. We have also developed nano cellulose composites with this starch-based bioplastic. It was possible to enhance the mechanical strength (tensile strength, bending strength, etc.) of starch-based bioplastics (Fig. 7).54
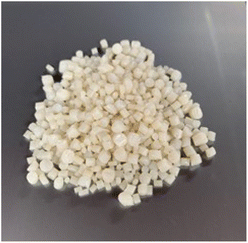 |
| Fig. 7 Starch-based biodegradable plastic prepared with twin-axis extruder composed of 100% biomass.54 | |
Cellulose-based biodegradable plastic and biomass biodegradable fiber, yarn, and textiles
As explained earlier, there are concerns about biodegradable plastics made from edible biomass such as corn, grains, sugarcane, potato, and starch because they use precious nutritious food for human beings. In this regard, it is ideal to utilize cellulose as the raw material for the production of biodegradable plastics because it is a non-edible biomass and is the most abundant organic resource on Earth. Furthermore, the types of cellulose-based biodegradable plastics will not require new trees to be cut down given that cellulose can be obtained from waste wood. Therefore, this material can be considered environmentally friendly and ideal in the aspect of not competing with human nutrition. Ngai et al. highlighted the importance of chemical modification to improve the hydrophilicity of cellulose for it to possess water resistance and mechanical strength. They also demonstrated the preparation of cellulose ester-based bioplastic for food packaging application via solvent casting, bar coating, spray coating and immersion coating (Fig. 8).55 Wang et al. prepared a cellulose-based bioplastic by hot pressing a cellulose hydrogel. The cellulose hydrogel was prepared from cellulose solution in an alkali hydroxide/urea aqueous system by physical cross-linking. The hot-pressing process induced a transition in the aggregated structure in the cellulose resin, resulting in plastic deformation. It was elucidated that the radial orientation of the cellulose molecules occurred in the planar direction of the plate, whereas an increase in amorphous zones appeared in the vertical direction. This type of cellulose-based bioplastic possesses a higher tensile strength, flexural strength and thermal stability and lower coefficient of thermal expansion than regenerated cellulose films.56 In addition, a large-scale manufacturing process to make high-performance cellulose bioplastic films composed of dual-crosslinked carboxymethylated cellulose fibers was investigated. Bleached softwood kraft pulp was carboxymethylated to form a homogeneous negatively charged carboxymethylated cellulose fiber slurry, which can further crosslink with the polyamide epichlorohydrin resin or aluminum sulfate [Al2(SO4)3] by strong electrostatic interaction. The prepared cellulose-based bioplastics demonstrated high mechanical strength (158.2 MPa), excellent water stability, improved wet strength (20.7 MPa), high optical transparency (89.4%), haze feature (77.9%), good thermal stability, and easy recyclability by mechanical disintegration.57
 |
| Fig. 8 Procedure for the preparation of cellulose-based bioplastic by casting method.55 | |
In contrast, Mori et al. developed a cellulose-based biodegradable plastic made using a twin screw extruder, which is very convenient for industrial application. In addition, their cellulose-based biodegradable plastic possessed good flexibility, and thus it can be applied to make films, sheets, yarn, and textiles (Fig. 9).58 Modifying this type of plastic with composite technology allows it to be implemented in most molding procedures, including injection molding, vacuum molding, blow molding, and heat press molding.
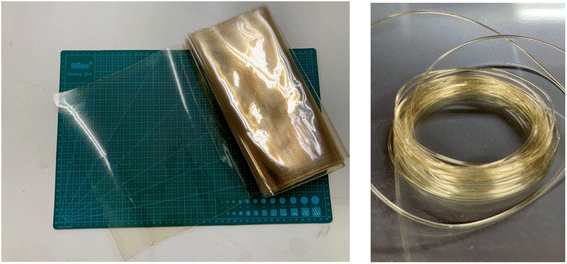 |
| Fig. 9 Biomass biodegradable film (Left) and yarn and fiber (Right) made of cellulose-based biodegradable plastic.58 | |
PLA-based 100% natural biomass biodegradable plastics for mass molding production
Currently, there are many types of bioplastics on the market. However, another important issue is the molding. For example, PLA is a 100% biomass biodegradable plastic but it is very difficult to perform injection molding with PLA and make the final molding product. The thermal decomposition and melting point temperatures are very similar, and thus it is difficult to carry out injection molding because PLA burns out before it melts. Additionally, PLA occasionally sticks to the metal molding and cannot be removed when attempting injection molding. Thus, it is challenging to achieve mass production with injection machines using pure PLA given that the temperature of the injection machine and metal molding must be precisely controlled each time. Therefore, in general, petroleum-based chemical additives are often used to avoid this problem, which eventually results in the final molding product containing petroleum-based chemicals.
In this regard, my group developed a PLA-based biodegradable plastic that can be molded into its final form, while maintaining 100% biomass composition without petroleum. In accordance with principle of creating a final molding product with a 100% natural biomass composition, no petroleum-derived chemicals were used, only natural additives to achieve mass production (Fig. 10).59 It should be mentioned that 100% natural biomass biodegradable plastic can be processed on even old and second-hand injection and biaxial stretch blow molding machines for mass production, while maintaining 100% biomass composition of the final molding product. With the successful developments, various molding products such as cutlery, cups, plates, dishes, bottles, tooth brushes, roller ball pens and clips with 100% biomass biodegradable composition were developed (Fig. 11). Nanocellulose was utilized as a nature-derived additive as a nucleating agent. Ariffin also applied nanocellulose as a nucleating agent to prepare a PLA composite material.60Fig. 12 shows some agglomerated nanocellulose in a PLA composite. They suggested that the appropriate amount of nanocellulose should be used to efficiently function as a nucleating agent.
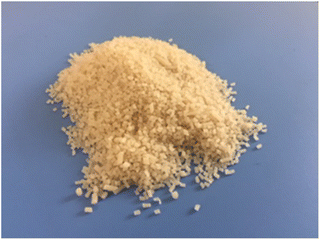 |
| Fig. 10 PLA-based 100% biomass biodegradable plastic for injection, biaxial stretch blow molding.59 | |
 |
| Fig. 11 From (Left), bottle, cup, tray, toothbrush, and cutlery, all with 100% biomass biodegradable plastic composition. Brush part of tooth brush (Left) is made of natural brush although toothbrush (Right) is made of petroleum-derived plastic.59 | |
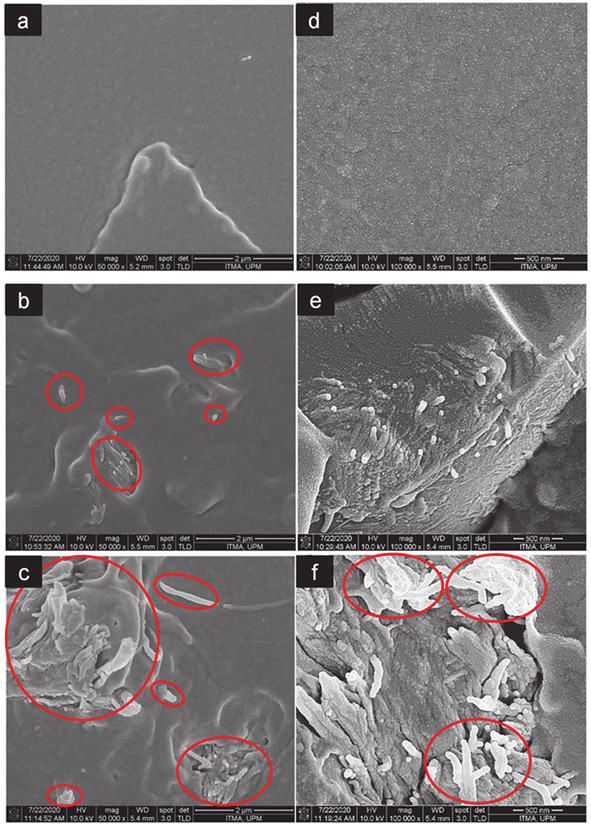 |
| Fig. 12 FESEM images at 500 00× and 1 000 00× magnification of the fractured surfaces of neat PLA (a and d), PLA/CNF3 (b and e), and PLA/CNF6 (c and f), respectively. Red circles show nanocellulose. PLA/CNF6 exhibits agglomerated nanocellulose. CNF: nanocellulose. Number after CNF indicates the % against the weight of PLA.60 | |
The functionalization of cellulose fibers with an aqueous solution of polyethylene oxide (PEO: C2nH4n+2On+1) was carried out, and subsequently extrusion, injection molding processes together with PLA. The PEO modification enhanced the interfacial interaction among the components and the cellulose fiber dispersion, allowing a loading of up to 30 wt% of cellulose fibers. It was proven that the storage modulus was higher than that of pure PLA. The stiffness and mechanical strength were found to be higher than that of PLA/PEO and remained comparable to that of pure PLA, whereas the elongation at break was 73–143% higher owing to the effective plasticizing and reinforcing effect exerted by PEO and CF, respectively. Moreover, it was also elucidated that the addition of PEO and cellulose fibers had a substantial influence on the thermal properties, particularly on the glass transition and cold crystallization temperatures.61 PLA and bleached softwood kraft were compounded with a twin screw extruder, and subsequently microcellular injection molded to prepare PLA/cellulosic fiber composite foams. Poly(ethylene glycol) (PEG) was used as a lubricant. As suggested by my group, it was also inferred that the cellulose fiber behaved as a crystal nucleating agent, which increased the crystallization temperature and the crystallinity and decreased the crystallization half time. It was also proven that the compared to PLA/PEG, a finer and more uniform cell structure was attained in the cellulosic fiber composite foams. The improved foam morphology was attributed to the cell-nucleating effects of the cellulose fibers and the gas- and fiber-induced crystallization.62
Nanocellulose and cellulose nanofiber
Nanocellulose (cellulose nanofiber: CNF) is a next-generation environmentally friendly material made from plants, which is considered to possess one-fifth the weight and seven to eight times the mechanical strength of steel.63 Nanocellulose is a fibrous material with a width of less than 100 nm. Also, its linear coefficient of thermal expansion (elongation and shrinkage degree caused by temperature difference) is as small as that of glass fiber. Upon contact, the elasticity of nanocellulose can be higher than that of glass fiber, indicating that it is hard and robust. Furthermore, because nanocellulose can be derived from plants, it is recyclable and causes very little environmental damage. It can be prepared from most types of natural organic resources such as plants, wood, grass, pulp, waste paper, and seaweed; hence, the raw material exists in huge quantities and can be very cheap when manufactured at a mass-production level. This is similar to the case of cellulose-based biodegradable plastics explained above.64
The width of each nanocellulose (cellulose nanofiber) ranges from several to several dozens of nanometers. Moreover, nanocellulose can be as light as one-fifth of the weight of steel but seven to eight times stronger.65 These properties are comparable to that of carbon fiber. From our experience, this may be somewhat unlikely to be true in all cases, but in some cases under certain conditions, it appears likely. Based on this, nanocellulose (or microcellulose) can be mixed with plastic or resins, to apply in automotives, buildings, furniture and plastic-based consumer goods, etc. Thus, lighter, cheaper, and more environmentally friendly products with reduced CO2 emission can be produced.
Given that the size of nanocellulose can be smaller than the wavelength of light (400–750 nm for visible light), nanocellulose does not cause light scattering and can be transparent.66 Some researchers created nanocellulose composite materials with acryl and epoxy resins, while improving their mechanical strength. Moreover, a composite material with over 90% nanocellulose was prepared with phenol resin, exhibiting mechanical strength comparable to that of steel, while having only one-fifth of the weight.
In addition, nanocellulose has a low coefficient of thermal expansion and does not expand, extend or change its shape much even when heated.67 In addition, nanocellulose can be dispersed uniformly during the molding process compared to a glass-fiber molding product. The molding product with nanocellulose-plastic composite exhibited uniform mechanical strength, which is an advantage over glass fiber molding products. Furthermore, as explained above, because nanocellulose is derived from natural resources, it is recyclable and biodegradable.68 Moreover, high absorption,69 large surface area,70 being edible,71 and high compatibility with biomedical-based materials72 are some other features of nanocellulose.
Thus, the application of nanocellulose includes the preparation of nanocellulose composite materials with plastic, resins, and rubber, which can be applied in the automotive, aerospace, building, and housing industries.73 In addition, various types of filters, films such as conductive transparent films for electronic devices such as solar cells, and electroluminescence (EL) materials can be prepared.74
Furthermore, nanocellulose is considered for application in separators for batteries, such as lithium-ion batteries and fuel cells.75 Artificial blood vessels and other biomedical usage are another possible application of nanocellulose,76 as well as an additive for food, cosmetics, paints, inks, and coatings.77
As a filter application, for example, Zhu et al. applied CNF as a porous filter to immobilize a Zn-based metal organic framework (MOF), i.e., zeolitic imidazolate framework-8 (ZIF-8), and a catalytic composite membrane was prepared having peroxymonosulfate-activating function to produce SO4˙−. The CNF was effective in fixing the ZIF-8 nanoparticles and making a durable porous filter. The peroxymonosulfate-induced ˙OH and SO4˙− radicals from ZIF-8 played an important role in the catalytic reaction and more than 90% of methylene blue and rhodamine B was degraded by the ZIF-8/CNF composite membrane within 60 min. Moreover, it was elucidated that the ZIF-8/CNF catalytic filters could be used several times without a reduction in their performance for the degradation of organic dyes. They also demonstrated the possible water purification application with CNF.78
In addition, CNF has been applied to make conductive films for solar cells. Nogi et al. combined CNF and silver nanowire to prepare a transparent conductive film with conductivity comparable to that of ITO (indium tin oxide). They deduced that the hydrophilic nature of both CNF and silver nanowire enabled the preparation of a stable transparent conductive film. They also found out that compared to the silver nanowire composite film prepared with PET and PVA, the film combined with CNF had much higher electrical conductivity against the number of times of film folding (Fig. 13).79 Wang et al. developed a CNF/PET separator for lithium-ion batteries. The CNF/PET separator exhibited higher porosity (70%) than the PP (polypropylene) separator (40%). They also elucidated that the CNF/PET separator could be wetted by electrolyte within a few seconds, while the PP separator could not be entirely wetted even after 1 min. The CNF/PET separator exhibited an electrolyte uptake of 250%, while the PP separator had only 65%. Additionally, the CNF/PET separator was proven to have better thermal stability and higher electrochemical properties than the PP separator (Fig. 14).80 CNF can be also utilized as an impurity absorbent. Seubsai et al. investigated the ability of CNF to eliminate Pb and Cd metal ions from contaminated water. They extracted nanocellulose from pineapple leaves and modified it with ethylenediaminetetraacetic acid (EDTA) and carboxymethyl (CM) groups. They exhibited that the adsorption efficiencies of the CNF modified with EDTA and CM were significantly higher than that of the unmodified cellulose in the pH range of 1–7 (Fig. 15).81
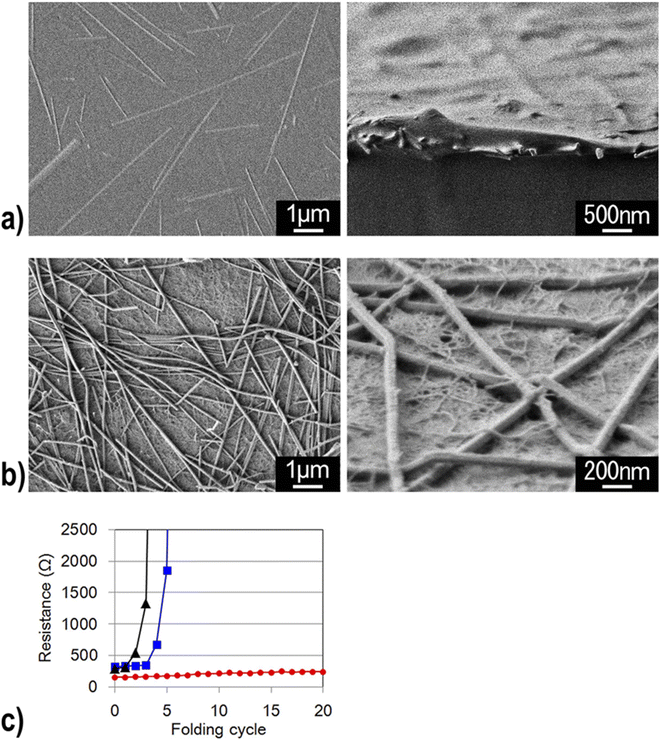 |
| Fig. 13 Silver nanowires were buried in the PVA substrate (Left: top view and Right: side view). (b) Silver nanowires were deposited on the transparent nanofiber paper and were entangled with the cellulose nanofibers (Left: top view and Right: side view). (c) Electrical resistance of transparent silver nanowires on a PET film (black), PVA film (blue), and transparent nanofiber paper (red) as a function of the number of folding cycles.79 | |
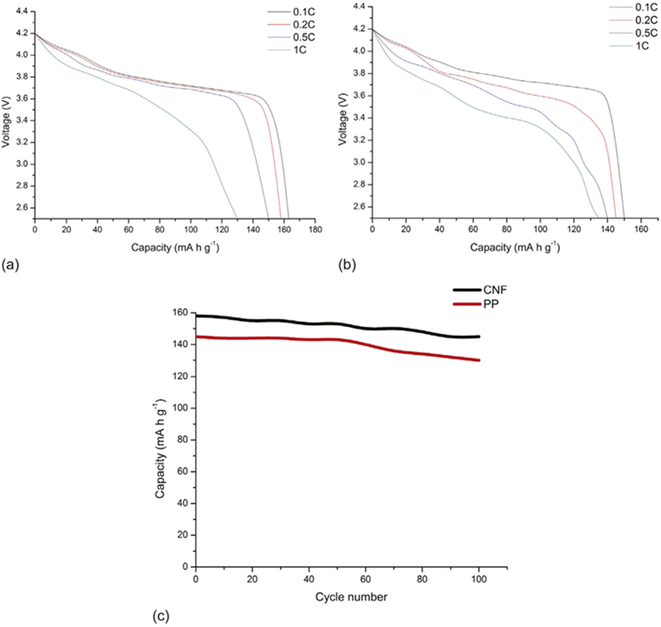 |
| Fig. 14 Discharge profiles of cells with (a) CNF separator and (b) PP separator. (c) Comparison of cycling performance between CNF separator and PP separator.80 | |
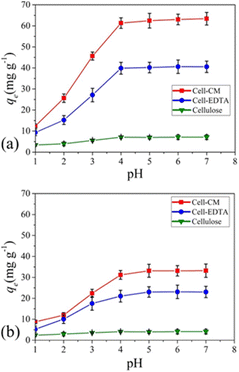 |
| Fig. 15 Adsorption efficiencies of extracted cellulose, cell-EDTA (ethylene diamine tetra acetic acid-modified nanocellulose), and cell-CM (carboxy methyl group-modified nanocellulose) for (a) Pb2+ and (b) Cd2+ in the pH range of 1–7. Conditions for adsorption: concentration of Pb2+ or Cd2+ = 100 mg L−1, at room temperature for 90 min.81 | |
Furthermore, CNF has been investigated as a drug delivery carrier owing to its biocompatibility and the presence of hydroxyl groups, which can be an advantage in the aspect of chemical modification and drug binding. Imae et al. applied folic acid-hybridized CNF for targeting tumor cells, carbon quantum dots for imaging and photodynamic/photothermal treatments and applied doxorubicin (DOX) as an anticancer drug. The prepared carriers exhibited excellent drug delivery capacity. In addition, the carbon quantum dot CNF composite demonstrated fluorescence, photosensitized singlet oxygen generation and photothermal behavior. This type of carrier exhibited pH-sensitive drug release due to the change in interactions with DOX, and this release proved to be effective against in vitro cervical cancer cells. These results proved the potential of multifunctional CNF carriers as platforms for multimodal photodynamic/photothermal-chemotherapy.82
Regarding my group, Mori et al., we developed a nanocellulose dispersion in water, with various types of organic solvents and vegetable oils (Fig. 16).83 The nanocellulose dispersion in water or glycol-based organic solvent could be utilized for the preparation of inks and paints, for example. Also, nanocellulose in vegetable oils could be used for cosmetics applications. We also prepared nanocellulose composites with various types of plastic and biodegradable plastics. It was possible to enhance the mechanical strength of plastics by chemically modifying the surface state of nanocellulose.
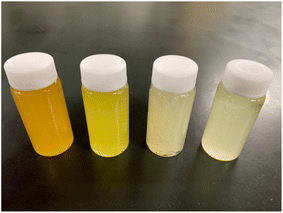 |
| Fig. 16 Nano cellulose dispersion in vegetable oil. From (Left), sesame oil, olive oil, castor oil, soy bean oil.83 | |
100% natural biomass-based biodegradable artificial nail tips and colors
As explained above, there are various types of environmentally friendly materials and products. However, the product cost and pricing remain a challenge in the case of their industrial application. Although the price of biomass biodegradable resin is feasible to some extent, some molding products such as spoons, forks, cups, dishes, plates, bottles, and tooth brushes are difficult to become practical products because consumers expect low prices for these types of products. Also, although these products are promoted as being made of 100% natural biomass-based biodegradable plastics, consumers may hesitate to pay the higher price. Therefore, cosmetic molding products were created, for which people may readily pay a higher price. Fig. 17 presents 100% biodegradable nail tips and nail colors. These biomass biodegradable artificial nail tips are made with normal injection molding machines. 100% natural biomass biodegradable nail polish in both natural organic solvents and water was also developed.84,85 These cosmetics products can be very interesting products for sustainable future.
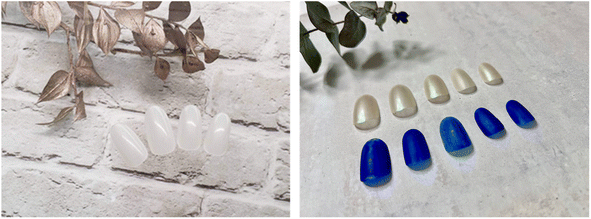 |
| Fig. 17 100% biomass biodegradable fake (artificial) nail tips (Left) and water-based biomass nail polish (Right).84,85 | |
100% natural biomass-based biodegradable thermoplastic materials made from wood and stone
With the aim to create ultimate environmentally friendly products, 100% natural biomass biodegradable thermoplastic materials made from wood and stone were created (Fig. 18). A new material called a ‘natural deep eutectic solvent’ was applied to make this innovative material from wood and stone. The main feature is that it is 100% natural biomass and derived from non-edible cheap materials, namely wood and stone.86 The weight of wood and stone is over 51% and various types of waste wood, plant and paper can be utilized. Moreover, this material can be manufactured easily with a normal twin extruder, which is an advantage for industrial use. The important point is that this material can be quite cheap given that the raw material and manufacturing cost will be economically friendly. A disadvantage is its weak water resistance, which is an issue for real industrial applications. However, this material has a relatively high compatibility with various type of bioplastics and petroleum-derived plastic such as PHBV, PP, and PE and water resistance can be recovered when it is mixed with other plastics. Given that a high quantity of material can be mixed with other plastics, we expect that it will be used as bulking agent for other plastics to increase their biomass content and biodegradability. Furthermore, marine biodegradability can be expected for this material, which is under investigation.
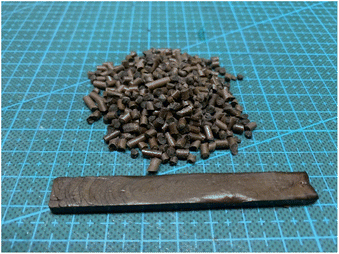 |
| Fig. 18 100% natural biomass biodegradable thermoplastic material made from wood, stone and natural deep eutectic solvent.86 | |
Wu et al. also applied a deep eutectic solvent to create softened wood via the microwave-assisted DES treatment of natural wood. It was found that the prepared softened wood possessed a highly porous network structure and partial lignin, hemicellulose, and cellulose were removed. They also demonstrated the great potential for its application in wood products.87 However, the material developed by my group may have advantage because it can be made with a commercial twin screw extruder on a larger scale and it is composed of 100% natural biomass material because the deep eutectic solvent is also prepared from biomass materials.
All the above-mentioned biomass biodegradable products are thermoplastic resins. Here, some thermosetting-based biomass biodegradable products are presented.
100% natural biomass-based biodegradable coating and glue
Thermosetting resin has been synthesized from petroleum-derived chemicals thus far, including epoxy (C21H25ClO5), polyurethane, unsaturated polyester, vinyl ester, melamine (C3H6N6), urea (CH4N2O), alkyd, formaldehyde (CH2O), phenol (C6H6O), amino, polyimide (C35H28N2O7) and silicon resin.88,89 Thermosetting resins have been applied in the production of paint, glue, construction industries, cement, automotive, electronics, furniture, industrial machines, consumer goods, packaging, etc.90 Epoxy resin is one of the representative thermosetting resins, which is widely used in various industries and is generally synthesized from bisphenol A (C15H16O2) and epichlorohydrin (C3H5ClO). However, bisphenol A is considered to be an endocrine disruptor (Fig. 19).91,92 Thus, biomass-derived thermosetting resins with less toxic materials are desirable. Cardanol (C21H30O), lignin (C81H92O28), itaconic acid (C5H6O4), cellulose, shellac (C30H50O11), alginate (C6H8O6)n, chitosan (C56H103N9O39), protein, tannin (C76H52O46), rosin (C15H20O6), furan (C4H4O), furfural (C5H4O2), sugar (isosorbide: C6H10O4), lactic acid (C3H6O3), vegetable oils, etc. can be employed as biomass-based raw materials for the preparation of thermosetting resins93,94 (Fig. 20). For example, a biobased phenolic adhesive was developed by substituting petroleum-based phenol and formaldehyde with an unmodified corn stover biorefinery lignin and glyoxal (a biobased dialdehyde), respectively. Lignin-glyoxal (C2H2O2) resins were synthesized using an alkaline catalyst with a molar ratio of lignin to glyoxal of 1
:
2. The prepared lignin-glyoxal resin had a higher curing temperature (167 °C) than the conventional phenol-formaldehyde resin (142 °C) and the formulated lignin-formaldehyde resin (146 °C). It was also found that lignin-glyoxal resin had a high dry adhesion strength (3.9 MPa) but failed the wet adhesion test (boiling water test). Although the prepared resin failed the boiling water test, it had excellent stability at room temperature water and remained intact after 1 week during the water immersion test.95
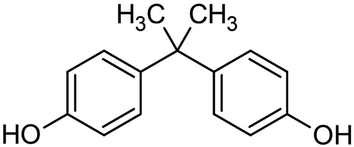 |
| Fig. 19 Molecular structure of bisphenol A.91,92 | |
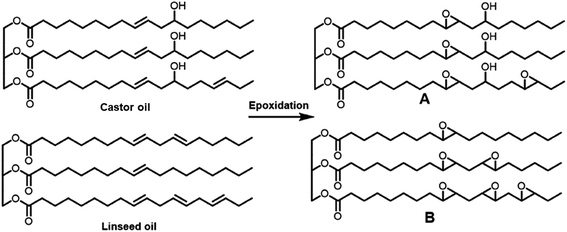 |
| Fig. 20 . Vegetable oil-based epoxy monomer derived from castor oil and linseed oil.93,94 | |
In addition, Wang et al. studied a hydrogel with a tunable structure, endowing it with adhesion, self-healing, and antibacterial properties. Aldehyde-chitosan was prepared from chitosan by oxidation. A Schiff base reaction was performed to make a chitosan/aldehyde-chitosan hydrogel. This type of composite material demonstrated good adhesion, self-healing properties, and high mechanical properties, which exhibited advantages to be used as a protective layer. Besides, it possessed inherent antibacterial activity and good biocompatibility, and thus it can be expected to be used for biological applications especially wound dressings.96
In the case of vegetable oils, saturated and unsaturated fatty acids are the main components of triglyceride vegetable oils.97 These fatty acids have industrial value depending on the chemical modification of the ester (–COOR) and carbon double bond (C
C). These fatty acids can be modified into epoxy,98 polyurethane,99 polyamide,100 polyester,101etc.
Sahoo et al. developed biobased polyurethane adhesives by reacting castor oil (C57H104O9)-based polyol with partially biobased polyisocyanate with the help of dibutyltin dilaurate (DBTDL) as the catalyst. The effect of the stoichiometric ratio of hard to soft segment on the bonding strength of wood-to-wood was evaluated. The experimental results also demonstrated that the same stoichiometric ratio had a considerable influence on the mechanical and thermal properties.102
Moreover, polyurethane adhesives for wood bonding were prepared from palm oil-based polyester polyol. The polyester polyol was synthesized from epoxidized palm olein prior to reacting with polymeric 4,4′-methylene diphenyl diisocyanate and toluene 2,4-diisocyanate to produce wood bonding polyurethane adhesives. The effect of glycerol cross-linker, dibutyltin dilaurate catalyst and isocyanate/OH ratio on lap shear strength and pot life of the polyurethane adhesives was investigated. The prepared polyurethane exhibited superior chemical resistance in cold water, hot water, acidic medium and alkaline medium by exhibiting light deterioration in lap shear strength. The polyurethane adhesives prepared from polymeric 4,4′-methylene diphenyl diisocyanate exhibited higher lap shear strength and thermal stability than that prepared from toluene 2,4-diisocyanate adduct. Furthermore, it was found that both adhesives resulted in improved mechanical performance compared to the commercial wood bonding adhesives.103
In general, coating materials, adhesives and glue are normally composed of thermosetting resins; in this regard, 100% natural biomass biodegradable coatings and glue were developed with rosin and cellulose-based resin. In addition, the mechanical strength and water resistance of paper and pulp-based molded products such as paper straw can be strengthened with this 100% biomass biodegradable coating material. It was also demonstrated that the water resistance and mechanical strength of paper straw was improved by coating with this resin (Fig. 21). Given that many paper- and pulp-based molded products are emerging in the market as alternatives to petroleum-based plastics, this can be one of the interesting solutions because the mechanical strength and water resistance of paper- and pulp-based products are weak.
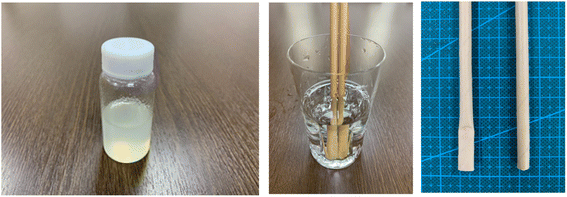 |
| Fig. 21 100% natural biomass coating (Left), water resistance improve test (Middle) and water resistance of paper straw have been improved (Right). | |
Natural biomass-based biodegradable color ink and paint without any petroleum-based chemicals
Colored paint and colored ink are generally prepared with coating, glue and adhesive technology. Similar to coatings, various types of vegetable oils have been utilized for the preparation of bio-based paint.104,105 For example, printing ink vehicles were prepared from modified vegetable oil. The average molecular weight of the vehicles made from representative vegetable oils, such as soybean, sunflower, cottonseed, safflower and canola oils, were compared by gel permeation chromatography, and the correlation between the viscosity and molecular weight of these vehicles was investigated. It was clarified that the physical properties of the formulated inks were comparable or even exceeded the performance of the industry standard inks for lithographic and letterpress newsprint applications. It was also found that these vegetable oils biodegraded faster than commercial soy or mineral oil-based vehicles.106
Moreover, vegetable-based offset printing inks were developed with safflower oil, grape seed oil and Pinus pinaster resin. Printing tests were carried out with coated papers and color, gloss, rub resistance, viscosity and tack values were measured on the test prints. The color difference values were within the tolerance value. It was suggested that the results of the printability tests exhibited the potential utilization of renewable biomass sources for the ecological development of offset printing inks.107
Biomass biodegradable color ink and paint without any petroleum chemicals were created based on the knowledge of 100% natural biomass biodegradable coatings and glue. Color pigments are inorganic pigments; hence, they can be considered to be made of non-petroleum materials. By combining both 100% natural biomass biodegradable plastics (thermoplastic resins) and color inks and paints (thermosetting resins), unique products can be created (Fig. 22). In addition, biomass-based biodegradable color masterbatches were developed, which are often used in the chemical industry as plastic colorants (Fig. 23).
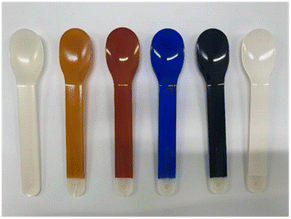 |
| Fig. 22 100% biomass biodegradable color ink on 100% biomass biodegradable plastic spoon. | |
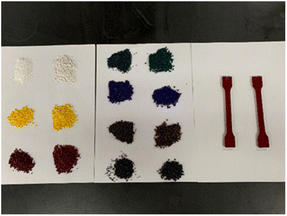 |
| Fig. 23 Biomass biodegradable color masterbatch. | |
Biomass-derived UV curable products
UV (ultraviolet) curable polymers have been employed in various types of products including hard coatings, adhesives, paints, inkjet ink, glue, 3D printer ink, cosmetics, dental products, and medical products.108,109 There are some investigations that demonstrated the possibility of obtaining biomass-derived UV curable polymers derived from furfural etc.110 Sangermano et al. also studied the preparation of bio-based UV materials from the pulp and paper industry. They focused on creating UV curable products from lignin, rosin and terpenes, given that they can be exploited as photo-curable starting materials (Fig. 24).111 Paul et al. developed bio-based UV curable pressure sensitive adhesives with ∼50% biomass content made from alkali lignin, cardanol, and linseed oil (C57H98O6). Bio-based prepolymers cardanol diol acrylate and acrylated epoxidized linseed oil were synthesized and used to prepare polyurethane acrylate-based pressure-sensitive adhesives. Alkali-lignin-based acrylates were introduced in the polyurethane acrylate/acrylated epoxidized linseed oil pressure-sensitive adhesives at 10–30 wt% loading to modify the properties. The single glass-transition temperature (Tg) clarified their good miscibility compared to oligomers/prepolymers. Convincible lap shear adhesion (166 kPa), tackiness and 180° peel strength (∼2.1 N/25 mm) for possible non-structural or semi-structural applications were obtained when 20% of alkali-lignin-based acrylates were incorporated in the polyurethane acrylate. It was also found that the lignin enhanced the thermal stability by suppressing the degradation rate at higher temperatures.112 Weems et al. created 3D-printed structures derived from linalool and limonene pre-polymer resins.113 In addition, Johansson et al. discussed the preparation of bio-based UV curable coating material derived from itaconic acid (Fig. 26).114 Furthermore, 82.9% content of biobased UV curable oligomer was prepared from epoxidized soybean oil (C57H98O12) and gallic acid (C7H6O5). Photo-polymerization was carried out by mixing with hydroxyethyl methacrylate. When the content of hydroxyethyl methacrylate was 50–60%, the viscosity was as low as (52–93 mPa s) and demonstrated excellent thermal and mechanical properties (Tg of 128–130 °C, Tp of >430 °C, and tensile strength of 42.2–44.4 MPa), which were comparable or superior to a commercial product. They had also applied the same resin to UV curable 3D printing and exhibited lower penetration depth (0.277 mm) than the commercial resin. This means that a higher resolution object can be created with this type of biobased UV resin.115
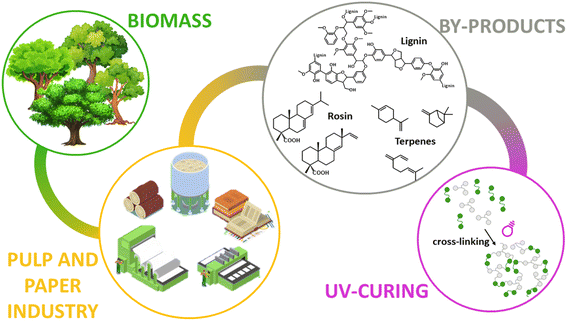 |
| Fig. 24 Concept image of biomass-derived UV curing products derived from pulp and paper industry.111 | |
Mori et al. also developed a UV curable hard coat resin, which had comparable hard coat mechanical properties as the petroleum-derived resin. We are also trying to prepare biomass-derived UV curable inkjet ink and 3D printer ink with similar technology (Fig. 25).
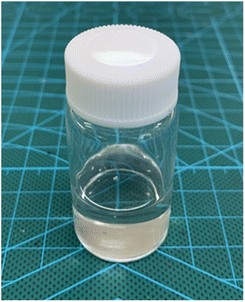 |
| Fig. 25 Image of biomass-derived UV curing hard coat material. | |
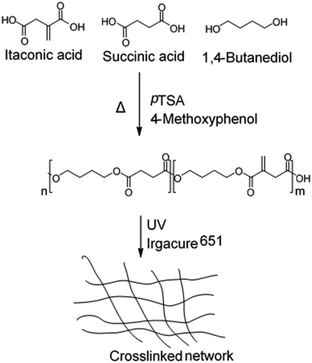 |
| Fig. 26 Synthesis and crosslinking of renewable polyesters containing itaconic acid, succinic acid, and 1,4-butanediol.114 | |
Biomass mark certified coating, glue and color ink
Biomass mark can be used for certification for some certain products. A water-based bamboo charcoal dispersion ink was developed, which can be applied as the concentrated base pigment for black color ink for inkjet ink, stationery, stamps, inks, etc. Since the bamboo charcoal part has a natural origin, the product was biomass certificate 50, where a minimum of 50% of biomass content is guaranteed in it, as certified by Japan Organics Recycling Association (JORA). A water-based biomass biodegradable liquid material certified with 100% biomass was also developed (Fig. 27).116 We expect that this material will be employed for the preparation of water-based coatings, glue, adhesives and paint, for example.
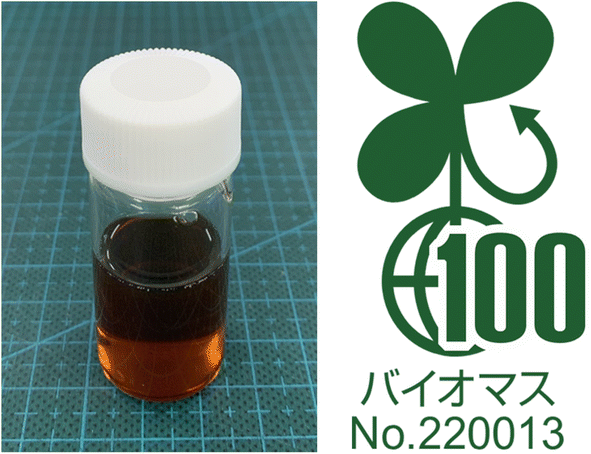 |
| Fig. 27 (Left) 100% biomass mark certified water-based coating material. (Right) 100% biomass mark from JORA.116 | |
100% natural biomass-based biodegradable plasticizers
A plasticizer is a chemical that gives good flexibility, elasticity, and processability to various types of plastics, resins, and rubbers. Although many people are not familiar with the word “plasticizers”, they are important chemicals in modern society. However, a typical plasticizer includes phthalate-based chemicals, which are considered detrimental to the environment43 (Fig. 28). Other types of plasticizers such as adipate, phosphate, and polyester are also generally petroleum-derived chemicals.117,118 Therefore, it is worth investigating biomass-based plasticizers. For example, plasticizers for polyvinyl chloride (PVC), which are derived from biomass resources (vegetable oil, cardanol, vegetable fatty acid, glycerol (C3H8O3), citric acid (C6H8O7), and lactic acid) have been widely studied to replace petroleum-based o-phthalate plasticizers. These bio-based plasticizers mainly include epoxidized plasticizer, polyester plasticizer, macromolecular plasticizer, flame-retardant plasticizer, citric acid ester plasticizer, and glyceryl ester plasticizer119–121 (Fig. 29). For example, Liu et al. synthesized bio-based acetylated lactic acid 1,4-cyclohexanedimethyl ester from L-lactic acid. The prepared acetylated lactic acid 1,4-cyclohexanedimethyl ester was applied to poly(vinyl chloride) (PVC) as a plasticizer and compared to the commercially used acetyl tributyl citrate (ATBC: C20H34O8). It was clarified that the prepared lactic-based plasticizer had better migration, volatility and stability than ATBC. Moreover, its strength, elongation and elasticity were superior when mixed to PVC. Furthermore, the glass transition temperature (Tg) of PVC films decreased from 61.3 °C to 55.0 °C. In short, acetylated lactic acid 1,4-cyclohexanedimethyl ester had better plasticizing effectiveness than ATBC.122
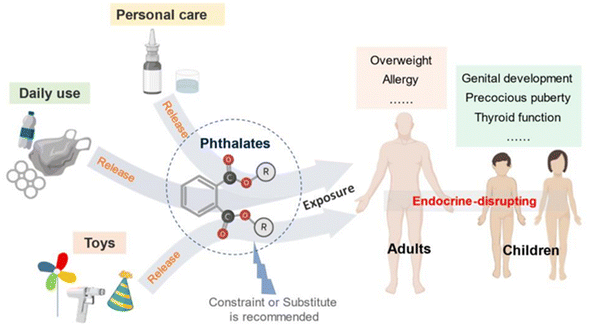 |
| Fig. 28 Phthalate applications and its impact on human health.43 | |
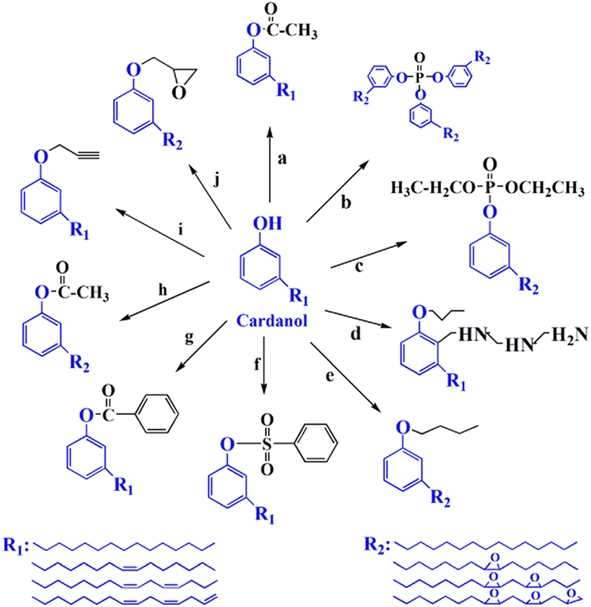 |
| Fig. 29 Chemical structure of cardanol-based plasticizer.119–121 | |
Generally, it is known that epoxy-based materials derived from various types of vegetable oil can be applied as plasticizers especially for PVC including epoxidized soy bean.123,124
In this case, epoxy groups were covalently bonded on fatty acid derived from waste cooking oil through addition and epoxidation reactions. Compared with commercial dioctyl phthalate plasticizer, this type of waste biomass-originated plasticizer enhanced the thermal stability and flexibility of PVC, and also resulted in a lower glass transition temperature. Moreover, it exhibited practical volatility and excellent resistance for migration in PVC matrix. It was proven that when epoxy groups were introduced to the ester and carbon–carbon double bonds in the fatty acid, even if they originated from waste resources, they could be utilized as good plasticizer for PVC.125
Alternatively, a new material named deep eutectic solvent (DES) has been reported to be function as a plasticizer.126,127 DESs are mixtures of so-called hydrogen bond acceptors (HBAs) and hydrogen bond donors (HBDs). They are solutions of Lewis or Brønsted acids and bases, which form a eutectic mixture. DESs exhibit much lower melting temperatures than their individual components. The parent components of DESs engage in a complex hydrogen bonding network, which results in significant freezing point depression compared to the parent compounds. Thus, DESs show a marked deviation from ideal-solution” behaviour.128,129 They share many similarities with ionic liquids, and some researchers acknowledge them as a subclass of ionic liquids. Generally, they show high thermal stability, non-flammability, low volatility, and vapor pressure. Unlike ionic liquids, they are mostly biodegradable, non-toxic, easy to prepare, and relatively inexpensive.130,131 DESs can be utilized in various types of applications including metallurgy and electrodeposition, separation and gas capture, battery, biocatalysis, extraction of plant-derived chemicals, organic chemistry, biomass processing, genomics and fundamental research of nucleic acids, pharmaceuticals and medical research, synthesis of nanomaterials, dissolution of cellulose, lignin, and plasticizers.132,133 Mori et al. developed 100% natural biomass-based plasticizer with natural deep-eutectic solvent technology. This plasticizer is effective especially for cellulose-based resin.
100% natural biomass-based lubricants and cutting fluid
Lubricants and cutting fluids are also inconspicuous but critical chemical products in modern society. These products are actively used in metal processing and machine industries. Typical lubricants and cutting fluids are heavy hydrocarbon-based chemicals and petroleum-derived chemicals. In general, they are phthalate diester, polyester, polyisobutylene (C4H8)n, polyester, alkylbenzene, mineral oil, etc.134 Therefore, it is worth looking for alternatives using biomass-based lubricants and cutting fluids. Vegetable oils are one of the good candidate materials to be used as a lubricant. Vegetable oils such as soybean oil, coconut oil (C33H62O6), castor oil, perm oil, rapeseed oil, and sunflower oil are primarily composed of triglycerides (C6H8O6), that is, tri-esters of long chain carboxylic acids (fatty acids) combined with glycerol. Most of these oils contain at least four and sometimes as many as twelve different fatty acids. The triglyceride structure of vegetable oils provides desirable qualities as a lubricant. Specifically, high natural viscosity and strong intermolecular interactions, which provide strong resilient to temperature changes and structural stability over reasonable operating temperature ranges. Anti-corrosion properties are also an important topic. The flash point of vegetable oils is high, which correlates to a very low vapor pressure and volatility, thereby eliminating potential hazards during use.135 However, one of the problems of vegetable oils is their poor performance at high temperature and pressure. They can be oxidized, which influences their chemical and physical composition. In the worst cases, the oxygen bond in vegetable oils can lead to metal oxidation, weakening the metal structure. Shakirin et al. evaluated the performance of vegetable oils as a lubricant with a fourball tribometer under extreme pressure conditions, according to ASTM D2783. Stamping oil, hydraulic oil, jatropha oil, RBD palm olein and palm fatty acid distillate were tested as specimens. The test normal load was 126 kg. The results demonstrated that vegetable oils have a high friction coefficient compared to mineral oil. Moreover, the wear scars caused by vegetable oil is lower than that produced by mineral oil. It was inferred that vegetable oils can be used as lubricants.136 Moreover, Adejuyigbe et al. investigated the utilization of soybean oil as an alternative cutting fluid to soluble oil in machining a mild steel material. Soybean oil and soluble oil (standard) were tested as cutting fluid and their influence on the mild steel material was observed for 70 days. It was demonstrated that the soybean oil resulted in slight corrosion of the mild steel compared to the soluble oil. It was inferred that the acidity of the soybean oil at high temperature had a corrosion effect on mild steel.137
Alternatively, DESs have also been studied as a potential bio-based lubricant when they are composed of biomass-based chemicals.138 Li et al. employed a betaine and sugar alcohol-based natural deep eutectic solvent as a lubricant. My group also had developed 100% natural biomass-based lubricants and cutting fluid using natural deep eutectic solvent technology (Fig. 30).
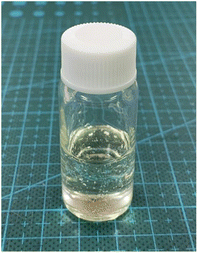 |
| Fig. 30 Natural deep eutectic solvent-based lubricant with 100% biomass composition. | |
Biomass-derived surfactant
Surfactants are important chemical products and mainly derived from petroleum thus far. Surfactants play an important role as cleaning, wetting, dispersing, emulsifying, foaming and anti-foaming agents and their actual applications include detergents, fabric softeners, motor oils, emulsions, soaps, cosmetics, shampoo, paints, adhesives, inks, anti-fog agent, washing and enzymatic processes, and biocides. There are several types of surfactants including anionic, cationic, zwitterionic, non-ionic and exoxylates. For example, one common surfactant is sodium stearate, which is classified as an anionic surfactant.139,140 However, considering that large volumes of surfactants are released into the environment, their biodegradation is of great interest. Thus, the demand for biomass-derived biodegradable surfactants has attracted much interest as “bio-surfactants”. Lecithin (C42H80NO8P),141,142 saponin (C58H94O27),143,144 casein (C81H125N22O39P),145 peptides,146 amino acid-based surfactant,147,148 sucrose fatty acid ester,149etc. are typical examples of biomass surfactants (Fig. 31). For example, an amino acid-based surfactant has been applied as a shampoo.
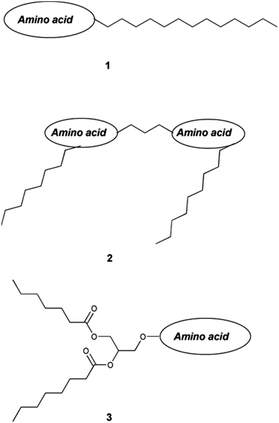 |
| Fig. 31 Structures of amino acid-based surfactants: (1) linear or single chain, (2) dimeric or gemini and (3) glycerolipid-like structures. The amino acid constitutes the polar head of the surfactant. The hydrocarbon alkyl chain constitutes the hydrophobic moiety.147,148 | |
In industry, the anionic surfactants linear alkyl benzene sulfonates (C18H30O3S) have been widely commercialized in a large variety of applications especially for the cleaning industry due to their high performance owing to optimized formulation and low cost. Accordingly, replacing linear alkyl benzene sulfonates with bio-based surfactants has been challenging because of these facts. Furan-based surfactants are candidate surfactants as a green alternative to replace petroleum-derived surfactants although they still suffer from lack of feedstock availability and low production yields. In this regard, Ghatta et al. developed a new class of furan surfactants, i.e., sulfonated alkyl furoates, which are prepared from the esterification of furoic acid and fatty alcohols, followed by a sulfonation step. Compared to traditional surfactants, it was found that they demonstrated superior performance in basic proprieties including critical micelle concentration, toxicity, water resistance and surface tension.150
Natural rubber nanocellulose composites
Rubber is an important chemical product that has been developed throughout history. Similar to plastics, rubber is used in many applications such as tires, glues, gloves, cables, sealing materials, and erasers. Some of the typical petroleum-derived rubbers are isoprene, butadiene, styrene-butadiene rubber, ethylene propylene rubber, fluorocarbon polymers, polyurethane, and silicon rubber.151 Alternatively, natural rubber is the typical rubber derived from nature and have been used by human since ancient time. Regarding natural rubber, one can enhance its mechanical strength by forming a composite with carbon black, glass fiber, etc.152,153 However, carbon black and glass fiber are not derived from nature. Carbon black can act as a reinforcing filler not only for natural rubbers but also various types of rubber elastomers. However, it has been reported that the production process of carbon black is not only energy-consuming, significantly contributing to an increase in global CO2 emissions, but it is also derived from non-renewable feedstock, making it unsustainable.154
In this regard, nanocellulose as a nature-derived material, was applied to reinforce the natural rubber.155–157 Dittanet et al. used H2SO4 to extract nanocellulose from dried rubber tree leaves and utilized it to reinforce natural rubber. The prepared nanocellulose appeared as needle-like shaped cellulose nanocrystals and demonstrated up to 30% enhancement in tensile strength with only 2 wt% nanocrystal addition to natural rubber, together with an increase in elongation at break of natural rubber.158
Furthermore, nanocellulose was used together with carbon nanotube to reinforce the natural rubber. Nanocellulose/natural rubber, carbon nanotube/natural rubber and nanocellulose/carbon nanotube/natural rubber composites were prepared and examined. It was found that the nanocellulose enhanced the nanocellulose/carbon nanotube hybrid filler dispersion, forming a 3D network, while the carbon nanotube increased the filler–matrix interaction. It was also clarified that the nanocellulose/carbon nanotube hybrid composite material had higher mechanical strength, dynamic mechanical properties and thermal conductivity.159
When cellulose is used to improve the mechanical properties of natural rubber, the application of biomass-derived natural rubber can be expanded because cellulose is also a nature-derived environmentally friendly material (Fig. 32).156 Mori et al. also developed natural rubber and nanocellulose composite materials and successfully enhanced their mechanical strength (Fig. 33).
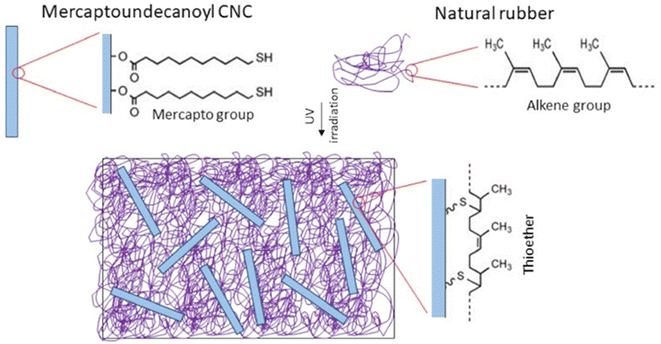 |
| Fig. 32 Illustration of the thiolene coupling reaction between natural rubber and modified cellulose nanocellulose in nanocomposite.156 | |
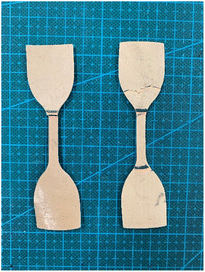 |
| Fig. 33 Dumbbell test piece of (Left) natural rubber and (Right) natural rubber nano cellulose composite material.180 | |
Biomass-based biodegradable plastics and paint with anti-bacterial functions
Since the COVID-19 pandemic, people all over the world have become more aware of viruses and bacteria and many anti-bacterial and anti-viral products have come onto the market. They include a number of anti-bacterial and anti-viral plastics160 and paints.161
Various types of biomass-derived plastics and paints have been explained above thus far, although there are not many products that have both functions. Nevertheless, recently, some biomass biodegradable plastics162 and paints163 with an anti-bacterial property were studied. Wei et al. prepared a PBAT/starch composite biodegradable plastic with anti-bacterial activity. They used polyhexamethylene guanidine hydrochloride (PHGH) as the anti-bacterial chemical and demonstrated its anti-bacterial activity with Escherichia coli (Fig. 34).164
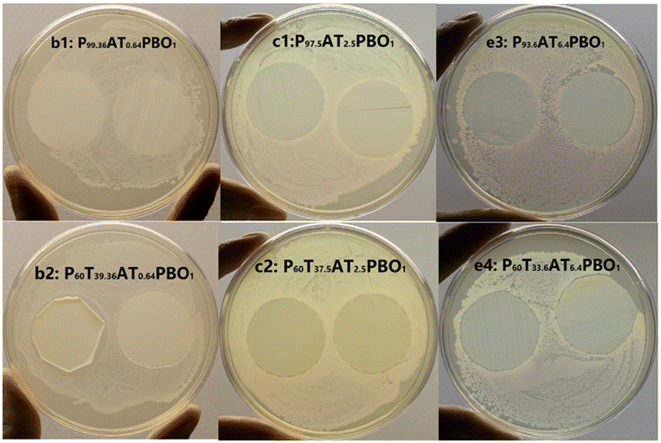 |
| Fig. 34 Pictures of different anti-bacterial PBAT films against Escherichia coli tested using the ring diffusion method. The subscripts represent the contents of the compositions. Where, P: PBAT, T: TPS (thermoplastic starch), AT: ATPS (anti-bacterial thermoplastic starch), and PB: 2,2′-(1,3-phenylene)-bis (2-oxazoline) as the coupling agent.164 | |
Chitosan-based materials have become a recent focus for the biodegradable food packaging sector due to their biodegradability, non-toxic nature, and antimicrobial properties. This is also due the fact that chitosan, which is obtained from chitin, is the most abundant biopolymer in nature after cellulose. Ghazvini et al. reported the use of chitosan-metal/metal oxide bio-nanocomposites as antimicrobial packaging materials. Also, metal/metal oxide, titanium dioxide, zinc oxide, and silver nanoparticles were evaluated.165
My group also developed a bioplastic and biomass coating with anti-bacterial functions (Fig. 35).160 We applied nanocellulose deposited with silver nanocolloids as an anti-microbial chemical in our PLA composite.
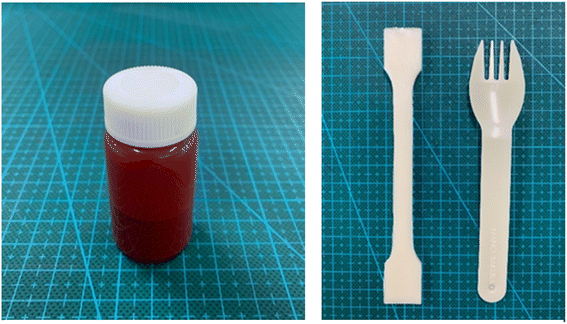 |
| Fig. 35 Biomass biodegradable paint (Left) and plastic (Right) with anti-bacterial activity.160 | |
100% natural biomass-based biodegradable resin powder (beads or scrubs)
Products such as shampoo, body wash, facial wash, toothpaste, and cosmetics contain plastic powder (beads or scrub) particles to act as scrub agents that eliminate dirt and dead skin from the body and also provide UV protection for cosmetics. These microscale particles are made of petroleum-derived plastics such as polyethylene (PE) and polypropylene (PP) and are the major cause of micro-plastic pollution because they are used in baths, showers, and bathrooms around the world daily in massive quantities and immediately flow into the drainage system after use (Fig. 36).166
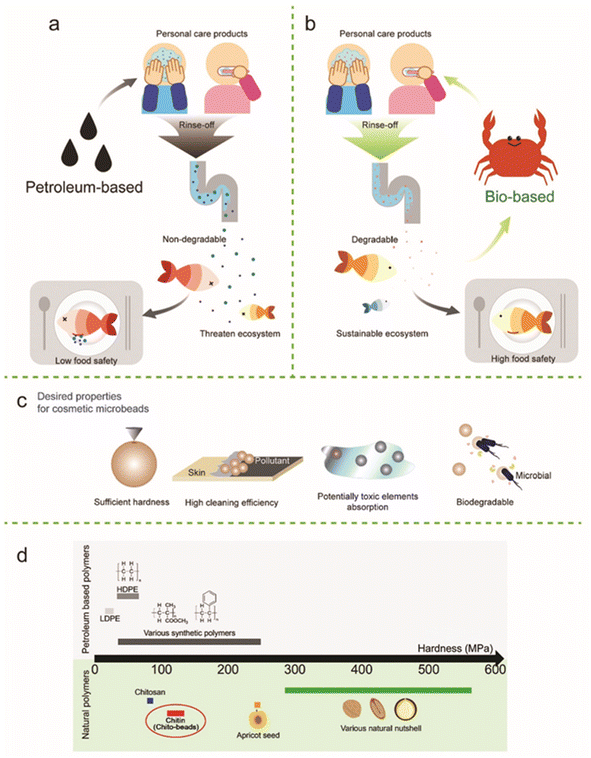 |
| Fig. 36 Applications of microbeads in daily care products and their potential impacts on the environment. (a) Petroleum-based microplastics and their main risks. (b) Bio-based microplastics and their desired consequences for sustainable cosmetics. (c) Desired cosmetic microbead properties and (d) comparison of the hardness between the materials in this study and some natural and synthetic abrasive materials (HDPE: high-density polyethylene and LDPE: low-density polyethylene).166 | |
Therefore, there is a strong demand to create biodegradable resin powder that can biodegrade when disposed from homes. Accordingly, Ju et al. developed a chitosan-derived biodegradable resin powder.167 It was prepared as uniform spherical microbeads with a diameter of 280 μm through the reacetylation of chitosan from waste crab via an inverse emulsion system. Mori et al. also created cellulose, starch and PLA-based biodegradable resin micro powder. Some of these products had a 100% natural biomass-based composition. The sizes of these particles ranged from several micrometers to 20 micrometers (Fig. 37).
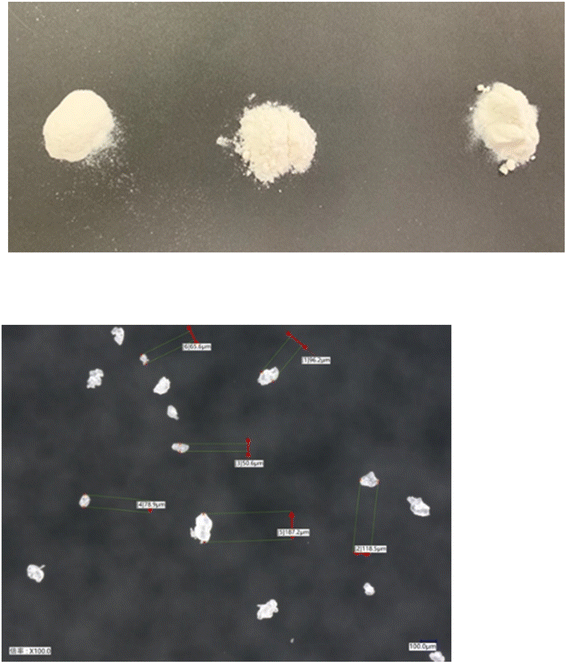 |
| Fig. 37 Biomass biodegradable resin powder. (Top left) PLA base, (Top middle) starch base and (Top right) cellulose base. Optical microscopic observation of PLA-based 100% biomass biodegradable resin powder (Below). | |
Biomass-based biodegradable resin for 3D printers
3D printers are very powerful technical tools in various fields. Thus far, thermoplastic polymer materials such as acrylonitrile butadiene styrene (ABS: [C8H8·C4H6·C3H3N]n), polylactic acid (PLA), polyamide (PA: C12H20N2O2) and polycarbonate (PC: C15H16O2) as well as thermosetting polymer materials such as epoxy resins can be processed by 3D printing technology.168,169 Among them, PLA can be regarded as biomass biodegradable 3D printer resin. Bhagia et al. studied fused deposition modeling (FDM) 3D printing of PLA with cellulose, hemicellulose and lignin. The printing properties, conditions and filament extrusion for PLA and PLA composites were investigated. Moreover, mechanical testing, thermal analysis, viscoelastic properties, imaging and spectroscopy were studied to understand the impact of filling biomass resources in PLA for 3D printing. It was also found that by optimizing the rheological properties of PLA filled with cellulose, hemicellulose and lignin and viscosity modifiers, the 3D printing speeds could be increased.170
In addition, hemicellulose-based polymers extracted from lignocellulosic agricultural wastes (corn cobs) were prepared and applied as ink for 3D printers. Practically applicable 3D printing of hemicellulose-based inks could be obtained under only the limited condition of water content, printing temperature, and extrusion multiplier. It was clarified that an even a slight change in water content could influence the hemicellulose-based ink viscosity and printability. It was also possible to make this type of hemicellulose-based 3D printer ink without any chemical modifications or mixing with another polymer.171
However, PLA is derived from edible biomass such as corn, sugarcane and starch, which can be an issue given that the food scarcity problem is rising recently due to climate change and explosion in human population.
In this regard, Mori et al. developed a cellulose-based biodegradable resin, which can be used for 3D printing. This is ideal given that cellulose is the most abundant natural organic resource on the planet and it does not compete with nutritious food for humans (Fig. 38).
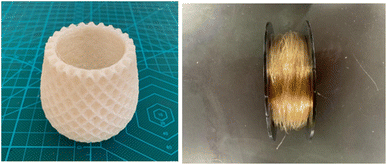 |
| Fig. 38 Cellulose-based biomass biodegradable resin mold product made by 3D printer and resin filament for 3D printer. | |
Bio-ethanol made from non-edible biomass
In modern society, most gasolines, various types of fuels, and jet fuel are still dependent on petroleum, and the production and consumption of these are significant, making them a major source of CO2 emissions. Similar to the efforts to replace all petroleum-based chemical products with biomass-based products, creating biofuel from biomass is desirable. In general, bio fuels can be classified to bio-ethanol, bio-diesel, sustainable aviation fuel (SAF), biomass-derived methane gas, biomass-derived hydrogen, bio coal, etc. In addition, it is known that the first generation of bio fuels are derived from edible biomass such as corn, sugarcane, potato, and grains, whereas the second generation of bio fuels are made from non-edible biomass such as wood waste, waste paper, and algae.
In the aviation sector, the development of renewable aviation fuel is identified as a promising alternative to replace fossil-based jet fuel in the current infrastructure. For example, Rios et al. proposed a mathematical model of biojet fuel production by hydro processing non-edible oils (such as Jatropha curcas, camelina, palm stearin, and Ricinus communis), together with renewable hydrogen production (produced from residual biomass in oil extraction). Taking the Mexican airport network as an example, the best economic scenario was a profit of 16
893
146 USD per year and 27.6% CO2 emission reduction, compared with fossil jet fuel. Moreover, it was suggested that when all conditions are optimized with the maximum effort, it is possible to satisfy the national jet fuel demand (4157.5 kilotonne per year) with the renewable fuel jet and even increase the profit with surplus sales (315 kilotonne per year).172
Bio-ethanol is also a good candidate as a bio-fuel because it has the potential to replace petroleum-based fuels. In addition, some chemical products such as ethylene and polyethylene can also be prepared from ethanol. Nowadays, bio-ethanol is produced from agricultural products such as corn, sugarcane, and starch-based materials.173 However, these edible biomass organic resources are not ideal because they compete with human nutritious foods174 (Fig. 39). Therefore, it is preferable to source bio-ethanol from non-edible biomass-based organic resources such as cellulose, as explained above. Thus, bio-ethanol from non-edible organic waste biomass such as waste of plants, wood, paper, waste food, and bamboo has been developed. Specifically, anything that contains cellulose. For example, bio-ethanol has been prepared from waste wood, which contains cellulose, and called second generation bio-ethanol.175–177 I also made bio-ethanol from bamboo residue using my bamboo particle dispersion technology, which was the pretreatment to enhance the following enzyme and yeast fermentation efficiency (Fig. 40).178
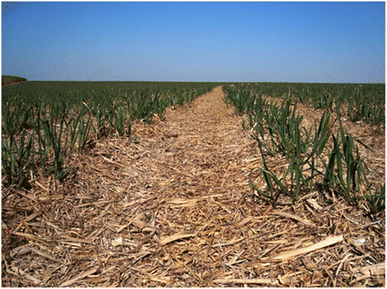 |
| Fig. 39 Recent view of sugarcane cultivation under green cane management conducted without the preharvest burning in Brazil. The trade-offs between the need to preserve soil health and produce more bioenergy have been the subject of intense discussion, given that the adoption of sustainable management practices such as crop residue retention can increase the productivity of agricultural ecosystems and mitigate the effects of climate change through enhanced carbon sequestration. Photographed by J. L. N. Carvalho.174 | |
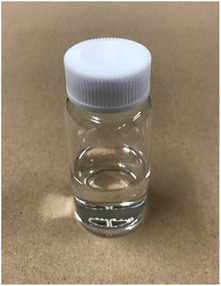 |
| Fig. 40 Bio-ethanol made from bamboo waste as non-edible biomass.178 | |
100% natural biomass-based biodegradable plastics made of natural organic waste such as waste wood, paper, seaweed, plant and waste food
Huge quantities of wood, paper, and food are disposed of daily around the world, which are precious organic resources that should not be wasted. By utilizing these waste organic resources, various types of biomass chemical products can be created. Especially bioplastic production from waste wood and waste paper is intensively under research (Fig. 41).179–181 For example, Krishnamurthy et al. developed bioplastic films from jackfruit waste flour and sago as a low-cost starch source. Specifically, 3 different types of composite films were prepared using starch with lemon extract and water, with different cross-linkers, as follows: (1) polylactic acid and crude palm oil, (2) glycerol and crude palm oil and (3) polylactic acid, glycerol and crude palm oil. It was demonstrated that when PLA and crude palm oil were used as cross linkers, the strongest tensile strength of 5.24 MPa and lowest elongation at break of 3.49% were obtained. It was also elucidated that the strong interaction of triglycerides (C
O stretching) was observed for all 3 types of films.182
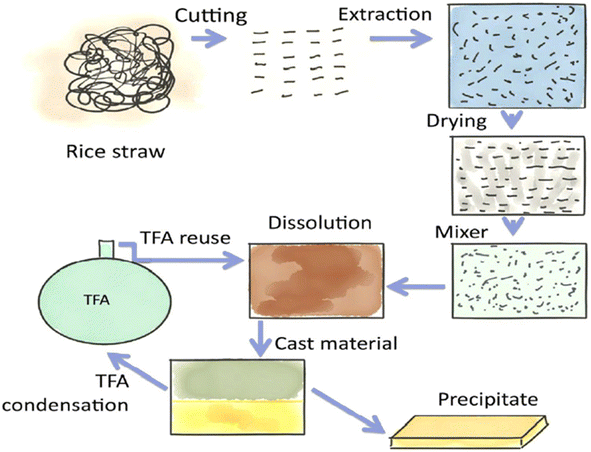 |
| Fig. 41 Synthesis of bioplastics from rice straw (TFA: trifluoroacetic acid).180 | |
My group also prepared 100% biomass biodegradable plastics from waste wood, bamboo, paper, newspaper, food, waste tofu, waste shochu (Japanese alcohol liquor), etc. In addition, we created plastics made from waste Sargassum, which is seaweed in the Caribbean Sea. Recently, the quantity of Sargassum there has been increasing because of global warming and the rich nutritious soil flowing into the ocean due to Amazon deforestation. In various places, including Antigua and Barbuda near the Caribbean, the state of Florida in the USA, Mexico, and some parts of South America, there are severe problems of decomposing Sargassum reaching the beaches, causing a foul smell. Thus, 100% natural biomass-based biodegradable resin pellets made from Sargassum waste were developed and injection molding products such as cutlery were also created (Fig. 42).
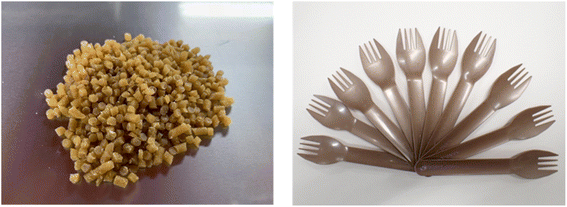 |
| Fig. 42 100% biomass biodegradable resin pellet (Left) and forks (Right) made from Sargassum waste. | |
Life cycle assessment (LCA) of bioplastics
As explained above, petroleum-based plastics have many environmental problems including greenhouse gas emissions, marine and terrestrial environment pollution. Alternatively, bioplastics and biodegradable plastics are presented as alternatives to conventional petroleum-based plastics. However, bioplastics also lead to some environmental issues such as greenhouse gas emissions and unfavorable land use changes, and thus it is necessary to evaluate the true impact of bioplastics on the environment for their life cycle assessment.
For example, petroleum-derived biodegradable plastics, which belong to category 2 herein, contribute to an increase in CO2 emission because they are derived from petroleum. Alternatively, biomass plastics, which belong to category 3 herein, do not have this issue given that they are made of natural biomass plants. However, they obviously result in microplastic pollution because they are not biodegradable. It should be remembered that similar to petroleum-based plastics, some bio-based plastics cannot be recycled. Consequently, many biodegradable bioplastics end up in landfills, which decompose gradually and produce methane gas to harm the environment. However, increasing research suggests that their environmental damage is still less severe than conventional petroleum-derived plastics. To ensure the environmentally friendliness of existing and newly developed bioplastics, we should conduct LCA analyses (Life Cycle Assessment) and land use change analyses. These studies will help policy makers to determine whether the use of bioplastics and newly developed bioplastics are indeed beneficial to the environment.183
One should also be aware of that bioplastics can be more energy intensive during their manufacturing process than their conventional competitors. Given that this is also a critical issue to be considered for overall environmental sustainability of a product, it is necessary to acquire a better understanding about the energy demand of bioplastics in the manufacturing process. Schulze et al. investigated on the energy demand of bioplastic materials in injection molding, milling and fused deposition modelling 3D printing procedure in the aspect of manufacturing process. Based on this concept, a quantitative energy related assessment of manufacturing bioplastics in comparison to conventional petroleum-derived plastics could be also possible. It was elucidated that in the case of the energy demand per product, milling has the highest specific energy demand and injection molding demonstrated a lower specific energy demand, but is compromised by the energy required for initial warm up and preparation of the machine. Considering these facts, 3D printing has the lowest energy demand. It was also shown that processing bioplastic and petrochemical materials in injection molding processes results in similar specific energy demands. This type of study of energy analysis regarding machine process impacts should be considered further to understand the true environmental impact of bioplastic production.184
Besides bioplastics, lab scale nanocellulose preparation routes were evaluated through a cradle-to-gate life cycle assessment adopting the Eco-Indicator 99 method. It was clarified that for the chemical and mechanical preparation procedure, the environmental impact of nanocellulose preparation depends on the chosen treatment process. For example, the environment impact is different between 2,2,6,6-tetramethylpiperidine-1-oxyl (TEMPO) oxidation and carboxymethylation process. It was also found that even though the manufacturing process of nanocellulose has a large environmental footprint markup compared to its raw material extraction process (kraft pulping), it still demonstrates better environmental advantages over other nanomaterials such as carbon nanotubes.185
Single-use plastics
In human history, the plastics industry has traditionally introduced mostly linear processes focusing on extracting raw materials and converting them into useful products, rather than recycling or reusing products. The overall production of plastics since 1950 has been dominated by PE (36.4%), polypropylene (PP; 21%) and polyvinylchloride (PVC; 12%) and the fiber market is occupied by mainly polyethylene terephthalate (PET; 70%). In addition, the largest global plastic volumes in the commercial sector in 2015 were in packaging (35.9%), construction (16.0%), textiles (14.5%) and consumer goods (10.3%). Furthermore, the automotive, electronics and agricultural industries also consume considerable amounts of plastics (for example, 10.1%, 6.2% and 3.4%, respectively, in the EU in 2016). However, packaging is considered to be the largest source of plastic waste globally, with 146 million tonnes produced in 2015, of which 141 million tonnes were unrecycled (96.6%). Packaging also have the shortest working life among the industrial plastic sectors, causing severe environmental damage.186,187
Furthermore, in the case of single-use plastics, their working lifetime, from use to disposal, can be even as short as a few minutes. In general, single-use plastics are composed of petroleum-derived plastic such as PE, PP, PVC and PET. Especially the COVID-19 pandemic has worsened the ‘plastic waste problem’, because of the urgent need for single-use plastic personal protective equipment such as masks, gloves and face shields. Because of the fears of virus spread, several bans on single-use plastic were temporarily cancelled. For example, reusable shopping bags were banned and, in some places, traditionally recyclable plastic food containers are considered hazardous, owing to potential pathogenic contamination. Consequently, the amount of medical plastic waste has increased by 3–10 fold and hundreds of millions of masks have ended up in landfills and the ocean.188
Thus, single-use disposable items made of bioplastics and biodegradable plastics are growing in popularity. However, the EU has announced a ban on the sale of several single-use plastic items (straws, cutlery, food and beverage containers made from polystyrene and cotton bud sticks and all oxo-degradable plastics) in EU240 under the framework of the European Green Deal and its Circular Economy Action Plan.189
In addition, China, the world's largest producer of single-use plastics, has also announced that they will ban non-recyclables other than degradable bioplastics by 2025. Consequently, Chinese manufacturers are planning to increase PLA production to 700
000 tonnes per year and combined PBAT and PBS output to 1.24 million tonnes per year by 2023.190
Other concerns and challenges
As shown above, various types of bioplastics and biochemical are expected to be alternative replacements for petroleum-derived plastic and chemicals although there remain some challenges. Firstly, bioplastics may be more expensive than petroleum-derived plastic because in general, these natural biomass resources, whether they are food (edible biomass) or non-edible biomass, are more expensive. Especially when edible biomass such as corn, sugarcane, grains, and potato are used as raw materials as in the case for PLA and starch, their price will be expensive and a problematic issue given that some people are suffering from hunger in the world. Vegetable oils such as perm oil can be a better choice even although they still may have some problems such as destroying indigenous rain forests to expand more perm tree forests to obtain more perm oils. There are also some reports that perm oil harvesting from perm trees is one of the causes for child labor exploitation. These facts may also influence supply chain issues because of the potential lack of natural resources and risks. Furthermore, bioplastics and biochemical products from natural resources often require additional chemical treatment process to utilize biomass resources such as cellulose and lignin, resulting in a higher cost. In this aspect, it may be an interesting new strategy to create and manufacture bioplastics by using whole waste wood, waste paper, waste food, waste seaweed, etc. as raw materials by combining with natural deep eutectic solvent or other cheap biomass-based raw materials, with just a simple twin extruder process. My group is promoting this direction in our research.
In addition, considering the supply chain of bioplastics, as explained above, some bioplastics are derived from nutritious food, and thus unsustainable practices will result in the destruction of natural habitats and the use of precious food-producing arable land. This will lead to the concept of raw material sourcing of biomass waste-streams, moving away from first-generation feedstocks. Instead, we should focus on sourcing second-generation feedstocks to create a sustainable supply chain for the production of biomass-derived bioplastics.
Bioplastic collecting and sorting are another important issue. If various types of bioplastics are not collected and classified separately, they can contaminate plastic recycling, organic waste streams, and the environment. Thus, solving this contamination problem requires effective identification and sorting to confirm that they are properly separated and composted. If this does not function properly, for example, compostable bioplastics such as PLA will contaminate the recycling of conventional plastics such as PE, PP and PET and decrease their value as recycled plastics. Practically, for example, FTIR (Fourier transform infrared light spectroscopy), NIR (near infrared spectroscopy) and hyperspectral imaging (HSI)-based separation technology have been applied to identify and separate plastics.191
In addition, the energy usage ratio is an advantage of biomass-derived plastic compared to petroleum-derived plastic. Tang et al. estimated that an average of about 13.8 exajoule (EJ), ranging from 10.9 to 16.7 EJ, of fossil-fuel energy consumed in 2019 was diverted to fossil-fuel feedstock for the production of plastics worldwide. This number indicates between 2.8% and 4.1% share of the total consumed fossil-fuel energy globally was used for the production of petroleum-derived plastics. Alternatively, the life cycle analysis estimate demonstrated that bioplastics produced from 1st generation feedstock required about 86% less non-renewable energy use (NREU) than that of petrochemical plastics. In addition, 2nd generation feedstock had even 25% less NREU than that of 1st generation.192
Further superiority can be suggested for biomass-derived plastics compared to petroleum-derived plastics regarding toxicity after their incineration. Plastic wastes can be potentially applied to waste-to-energy conversion technologies for supplementing the augmenting energy demands, instead of using them as just landfill. The direct incineration of municipal solid waste containing mixed plastic waste has been reported to be a primary factor for air pollution, as well as toxic gas such as furans, dioxins, and polychlorinated biphenyls. For example, the combustion of plastic products made of polyvinyl chloride such as plumbing pipes, mainly used in agriculture and household purposes, has the potential to deliver harmful halogenated compounds upon thermal degradation. This would increase the risk of pulmonary and cardiac diseases, respiratory ailments, nausea, headaches, skin rashes, cancer, birth defects, endocrine disruption, compromised immunity and severe damage to the nervous and reproductive system in humans, as well as severe damage to the environment. In this regard, biomass-derived plastics are harmless because in general, they do not contain many harmful substances and halogens.193
Besides the bioplastics and biochemical introduced herein, various types of challenges exist in achieving environmentally friendly green solutions in chemical industry. For example, applying ionic liquids and deep eutectic solvents have been as antistatic agents, electrolytes, lubricants, dissolving agents, CO2 absorber, etc. Another challenge is applying deep eutectic solvents as reaction media for chemical organic synthesis to replace the toxic organic solvents. Especially natural deep eutectic solvents can be more useful in this aspect given that they are composed of mild natural biomass raw materials.194
Utilizing microwave irradiation in synthetic chemistry is also an interesting method to achieve green chemistry. The reduction in the reaction time, enhanced yields, increased product purities and simplification of work can be attractive points in the energy-saving aspect, and in most cases, these conditions and results cannot be achieved by the classical heating process. In addition, the synergy with solvent-free conditions, solid catalysts and green solvents can expand to further environmentally friendly chemical reaction procedures.195
Considering energy saving for chemical reactions, it can be suggested that the use of twin screw extruders run by renewable solar energy or wind power generation to manufacture bioplastics can also be a green solution in the chemical industry.
Conclusions
Herein, the focus was explaining the various types of biomass-based chemical products such as bioplastics and biomass-based coatings and inks. They are based on the simple concept of replacing all petroleum-derived chemical products with biomass-based products. Specifically, “no more petroleum, no more fossil fuels”. Although achieving this goal seems difficult, it is a challenge worth our efforts toward a sustainable, carbon-neutral society.
Author contributions
Ryohei Mori: writing original draft, methodology, data curation, visualization, review, editing, supervision, conceptualization.
Conflicts of interest
There are no conflicts to declare.
Acknowledgements
The author wishes to express thanks to Mr Daiki Tanaka, Mr Yoshiyuki Konishi, Mr Kenji Tomatsu, Mr Yoshiteru Sato, Ms Maiko Mori and Ms Ayako Mori for their helpful discussions.
References
- L. P. M. Costa,
et al.
, Processes, 2021, 9, 759–837 CrossRef CAS.
- D. Tonini, D. Schrijvers, S. Nessi, P. G. Gutierrez and J. Giuntoli, Int J LCA, 2021, 26, 221–237 CrossRef.
- L. Cabernard, S. Pfister, C. Oberschelp and S. Hellweg, Nat. Sustain., 2022, 5, 139–148 CrossRef.
- I. Tsiropoulos,
et al.
, J. Cleaner Prod., 2015, 90(1), 114–127 CrossRef.
- J. G. Rosenboom, R. Langer and G. Traverso, Nature Rev. Mater., 2022, 7, 117–137 CrossRef.
- A. D. Bartoro, G. Infurna and N. T. Dintcheva, Polymers, 2021, 13, 1229–1254 CrossRef.
- G. Atiwesh, A. Mikhael, C. C. Parrish, J. Banoub and T. A. T. Lee, Heliyon, 2021, 7, e07918–07926 CrossRef.
- M. S. Yee,
et al.
, Nanomaterials, 2021, 11, 496–517 CrossRef PubMed.
- M. Llorca and M. Farre, Front. Toxicol., 2021, 3, 752140–752163 CrossRef PubMed.
- S. Noventa,
et al
, MPs, NPLs, 2021, 1, 9–35 Search PubMed.
- L. Edwards,
et al.
, JESEE, 2022, 32, 366–373 Search PubMed.
- R. V. I. Gadhave and C. R. Gadhave, Green Sustainable Chem., 2022, 12, 9–27 CrossRef.
- V. Gigante,
et al.
, Polymers, 2021, 13, 3640–3661 CrossRef.
- M. A. C. M. Haniffa, Y. C. Ching, L. C. Abdullah, S. C. Poh and C. H. Chuah, Polymers, 2016, 8, 246–278 CrossRef.
-
Japan Petrochemical Industry Association, https://www.jpca.or.jp/studies/junior/enyinfo03.html.
-
European Bioplastics, https://www.european-bioplastics.org/bioplastics/materials/.
- J. Jian, Z. Xiangin and H. Xianbo, Adv. Ind. Eng. Polym. Res., 2020, 3, 19–26 Search PubMed.
- C. L. Morelli, N. Belgacem, M. C. Branciforti and M. C. Brochier-Salon, Polym. Eng. Sci., 2016, 56, 1339–1348 CrossRef.
- S. A. Rafiqah, A. Khalina, A. S. Harmaen, I. A. Tawakkal, K. Zaman, M. Asim, M. H. Nurrazi and H. L. Ching, Polymers, 2021, 13, 1436–1463 CrossRef PubMed.
- A. Oishi, H. Iida and Y. Taguchi, Polym. J., 2010, 42, 411–415 CrossRef.
- N. B. Halima, RSC Adv., 2016, 6, 39823–39832 RSC.
- C. J. Moll, K. Meister, J. Kirschner and H. J. Bakker, J. Phys. Chem. B, 2018, 122, 10722–10727 CrossRef PubMed.
- P. K. Samantaray, Green Chem., 2020, 22, 4055–4081 RSC.
- Y. Reyhanoglu, E. Sahmetlioglu and E. Gokturk, ACS Sustainable Chem. Eng., 2019, 7, 5103–5110 CrossRef.
- M. Labeta and W. Thielemans, Chem. Soc. Rev., 2009, 38, 3484–3504 RSC.
- K. Kaluzynski, J. Pretula, P. Lewinski, S. Kaźmierski and S. Penczek, Macromolecules, 2022, 55, 2210–2221 CrossRef.
- J. G. Rosenboom, R. Langer and G. Traverso, Nat. Rev. Mater., 2022, 7, 117–137 CrossRef PubMed.
- V. Siracusa and I. Blanco, Polymers, 2020, 12, 1641–1657 CrossRef PubMed.
- M. L. D. Lorenzo, A. Longo and R. Androsch, Materials, 2019, 12, 2833–2846 CrossRef PubMed.
- L. Martino, L. Basilissi, H. Farina, M. A. Ortenzi, E. Zini, G. D. Silvestro and M. Scandola, Eur. Polym. J., 2014, 59, 69–77 CrossRef.
- B. Xiao,
et al.
, Ind. Eng. Chem. Res., 2015, 54, 5862–5869 CrossRef.
- J. Pang, M. Zheng, R. Sun, A. Wang, X. Wang and T. Zhang, Green Chem., 2016, 18, 342–359 RSC.
- P. Furtwenglera and L. Avérous, Polym. Chem., 2018, 9, 4258–4287 RSC.
- H. Li, Y. Liang, P. Li and C. He, J. Bioresour. Bioprod., 2020, 5, 163–179 CrossRef.
- Z. Terzopoulou,
et al.
, RSC Adv., 2016, 6, 84003–84015 RSC.
- T. Kim, J. Bamford, U. R. G. Alvarez and P. T. Benavides, ACS Sustainable Chem. Eng., 2022, 10(8), 2830–2843 CrossRef.
- S. D. Shetty and N. Shetty, Mater. Res. Express, 2019, 6, 112002 CrossRef.
- T. Casalini, F. Rossi, A. Castrovinci and G. Perale, Front. Bioeng. Biotechnol., 2019, 7, 259–274 CrossRef PubMed.
- Z. Li, J. Yang and X. J. Loh, NPG Asia Mater., 2016, 8, 265–284 CrossRef.
- K. Sudesh, H. Abe and Y. Doi, Prog. Polym. Sci., 2000, 25, 1503–1555 CrossRef CAS.
- M. K. Marichelvam, M. Jawaid and M. Asim, Fibers, 2019, 7, 32–45 CrossRef CAS.
- A. Shafqat, Biocatal. Agric. Biotechnol., 2020, 27, 101540 CrossRef.
- J. Simon, H. P. Müller, R. Koch and V. Müller, Polym. Degrad. Stab., 1998, 59, 107–115 CrossRef CAS.
- J. S. Yaradoddi,
et al
, Sci. Rep., 2020, 10, 21960–21972 CrossRef CAS PubMed.
- G. Atiwesh, A. Mikhael, C. C. Parrish, J. Banoub and T. A. T. Lee, Heliyon, 2021, 7, e07918–07927 CrossRef CAS PubMed.
- Y. Wang and H. Qian, Healthcare, 2021, 9, 603–611 CrossRef PubMed.
- R. S. Rose,
et al.
, Int. J. Mol. Sci., 2020, 21, 1176–1188 CrossRef CAS PubMed.
-
TüV Rheinland, https://www.tuv.com/world/en/biodegradability-testing.htmlhttps://taitec.net/.
-
R. Mori, Jp. Pat.,Trademark Office, PCT Application No. 2019035051, 2019 Search PubMed.
-
http://www.jbpaweb.net/english/
.
- W. Abotbina, S. M. Sapuan, M. T. H. Sultan, M. F. M. Alkbir and R. A. Ilyas, Polymers, 2021, 13, 3487–3504 CrossRef CAS PubMed.
- H. Zhang, Z. Su and X. Wang, ACS Sustainable Chem. Eng., 2022, 10(26), 8650–8657 CrossRef CAS.
- M. Zdanowicz, K. Sałasińska, K. Lewandowski and K. Skórczewska, ACS Sustainable Chem. Eng., 2022, 10(14), 4579–4587 CrossRef CAS.
-
R. Mori, Jp. Pat.,Trademark Office, JP Application No. 2019139856, 2019 Search PubMed.
- Z. Jiang and T. Ngai, Polymers, 2022, 14, 1533–1563 CrossRef CAS PubMed.
- Q. Wang,
et al.
, J. Mater. Chem. A, 2013, 1, 6678–6686 RSC.
- C. Lei,
et al.
, ACS Appl. Polym. Mater., 2022, 4(2), 1334–1343 CrossRef CAS.
-
R. Mori, Jp. Pat.,Trademark Office, JP Application No. 2021124670, 2021 Search PubMed.
-
R. Mori, Jp. Pat.,Trademark Office, JP Application No. 2019189629, 2019 Search PubMed.
- S. S. Shazleen, T. A. T. Yasim-Anuar, N. A. Ibrahim, M. A. Hassan and H. Ariffin, Polymers, 2021, 13, 389–407 CrossRef CAS.
- A. A. Singh, M. E. Genovese, G. Mancini, L. Marini and A. Athanassiou, ACS Sustainable Chem. Eng., 2020, 8(10), 4128–4136 CrossRef CAS.
- W. D. Ding,
et al.
, Composites, Part A, 2016, 83, 130–139 CrossRef CAS.
- V. Thakur, A. Guleria, S. Kumar, S. Sharmad and K. Singh, Mater. Adv., 2021, 2, 1872–1895 RSC.
- D. Trache,
et al.
, Front. Chem., 2020, 8, 392–424 CrossRef CAS.
- Q. F. Guan,
et al.
, Sci. Adv., 2020, 6, 1–8 Search PubMed.
- S. Gamage,
et al.
, J. Mater. Chem. C, 2020, 8, 11687–11694 RSC.
- P. G. Gan, S. T. Sam, M. F. B. Abdullah and M. F. Omar, J. Appl. Polym. Sci., 2020, 137, 48544–48557 CrossRef CAS.
- C. Zinge and B. Kandasubramanian, Eur. Polym. J., 2020, 133, 109758 CrossRef.
- F. Jiang and Y. L. Hsieh, J. Mater. Chem. A, 2014, 2, 350–359 RSC.
- S. Fujisawa, E. Togawa and S. Kimura, Mater. Today, 2018, 16, 105–110 Search PubMed.
- A. Pirozzi, G. Ferrari and F. Donsi, Coatings, 2021, 11, 990–1017 CrossRef.
- Y. Xue, Z. You and H. Xiao, Nanoscale, 2017, 9, 14758–14781 RSC.
- D. Y. S. Low,
et al.
, Polymers, 2021, 13, 550–584 CrossRef PubMed.
- Q. Yang,
et al.
, ACS Appl. Nano Mater., 2018, 1(9), 4972–4979 CrossRef CAS.
- H. Kim,
et al.
, ACS Appl. Mater. Interfaces, 2020, 12(37), 41211–41222 CrossRef CAS PubMed.
- R. Nicu, F. Ciolacu and D. E. Ciolacu, Pharmaceutics, 2021, 13, 1125–1181 CrossRef CAS PubMed.
- C. Aulin and G. Ström, Ind. Eng. Chem. Res., 2013, 52(7), 2582–2589 CrossRef CAS.
- W. Zhu,
et al.
, Environ. Res., 2022, 205(1), 112417 CrossRef CAS.
- M. Nogi, M. Karakawa, N. Komoda, H. Yagyu and T. T. Nge, Sci. Rep., 2015, 5, 17254–17260 CrossRef CAS PubMed.
- H. Zhang, X. Wang and Y. Liang, Heliyon, 2015, 1(2), e00032–e00047 CrossRef.
- A. Daochalermwong, N. Chanka, K. Songsrirote, P. Dittanet, C. Niamnuy and A. Seubsai, ACS Omega, 2020, 5, 5285–5296 CrossRef CAS PubMed.
- T. T. A. Do, S. Grijalvo, T. Imae, M. J. G. Celma and C. R. Abreu, Carbohydr. Polym., 2021, 270(15), 118366 CrossRef CAS PubMed.
-
R. Mori, Jp. Pat.,Trademark Office, JP Application No. 2020548318, 2020 Search PubMed.
-
R. Mori, Jp. Pat.,Trademark Office, JP Application No. 2020004357, 2020 Search PubMed.
-
R. Mori, Jp. Pat.,Trademark Office, JP Application No. 2022100198, 2022 Search PubMed.
-
R. Mori, Jp. Pat.,Trademark
Office, JP Application No. 2022130009, 2022 Search PubMed.
- Y. Wu,
et al.
, ACS Omega, 2020, 5(35), 22163–22170 CrossRef CAS.
- J. Song,
et al.
, Polymers, 2021, 13, 2224–2237 CrossRef CAS PubMed.
- S. K. Bobade, N. R. Paluvai, S. Mohanty and S. J. Nayak, Polym.-Plast. Technol. Eng., 2016, 55(17), 1863–1896 CrossRef CAS.
- A. Gomez-Lopez,
et al.
, ACS Sustainable Chem. Eng., 2021, 9(29), 9541–9562 CrossRef CAS PubMed.
- S. Flint, T. Markle, S. Thompson and E. Wallace, J. Environ. Manage., 2012, 104, 19–34 CrossRef CAS.
- S. Nikafshar,
et al.
, RSC Adv., 2017, 7, 8694–8701 RSC.
- S. Ma, T. Li, X. Liu and J. Zhu, Polm. Inter., 2016, 65(2), 164–173 CrossRef CAS.
- J. Liu,
et al.
, J. Polym. Sci., 2021, 59, 1474–1490 CrossRef.
- M. Siahkamari, S. Emmanuel, D. B. Hodge and M. Nejad, ACS Sustainable Chem. Eng., 2022, 10(11), 3430–3441 CrossRef.
- Y. Wang,
et al.
, ACS Sustainable Chem. Eng., 2020, 8(49), 18006–18014 CrossRef.
- V. Sharma and P. P. Kundu, Prog. Polym. Sci., 2006, 31(11), 983–1008 CrossRef.
- R. Auvergne, S. Caillol, G. David, B. Boutevin and J. Pascault, Chem. Rev., 2013, 114(2), 1082–1115 CrossRef PubMed.
- D. K. Chattopadhyay and K. V. S. N. Raju, Prog. Polym. Sci., 2007, 32(3), 352–418 CrossRef.
- L. Martino, L. Basilissi, H. Farina, M. A. Ortenzi, E. Zini, G. D. Silvestro and M. Scandola, Eur. Polym. J., 2014, 59, 69–77 CrossRef CAS.
- C. Liu, J. Li, W. Lei and Y. Zhou, Ind. Crops Prod., 2014, 52, 329–337 CrossRef CAS.
- S. Sahoo, H. Kalita, S. Mohanty and S. K. Nayak, Macromol. Res., 2017, 25, 772–778 CrossRef CAS.
- A. K. Poh, L. C. Sin, C. S. Foon and C. C. Hock, J. Adhes. Sci. Technol., 2014, 28(11), 1020–1033 CrossRef CAS.
- M. Alam, D. Akram, E. Sharmin, F. Zafar and S. Ahmad, Arabian J. Chem., 2014, 7(4), 469–470 CrossRef CAS.
- Y. Wang,
et al.
, ACS Appl. Mater. Interfaces, 2021, 13(48), 57930–57942 CrossRef CAS PubMed.
- S. Z. Erhan and M. O. Bugby, Ind. Crops Prod., 1995, 3(4), 237–246 CrossRef.
- P. Hayta, M. Oktav and ö. A. Duru, Color Res. Appl., 2022, 47(1), 164–171 CrossRef.
- S. C. Ligon-Auer, M. Schwentenwein, C. Gorsche, J. Stampfl and R. Liska, Polym. Chem., 2016, 7, 257–286 RSC.
- V. Shukla, M. Bajpai, D. K. Singh, M. Singh and R. Shukla, Pigm. Resin Technol., 2004, 33(5), 272–279 CrossRef CAS.
- J. Stouten, D. E. P. Vanpoucke, G. V. A. Assche and K. V. Bernaerts, Macromolecules, 2020, 53, 1388–1404 CrossRef CAS.
- L. Pezzana, E. Malmström, M. Johansson and M. Sangermano, Polymers, 2021, 13, 1530–1555 CrossRef CAS.
- R. Paul, B. John and S. K. Sahoo, Biomacromolecules, 2022, 23(3), 816–828 CrossRef CAS.
- A. C. Weems, K. R. D. Chiaie, J. C. Worch, C. J. Stubbs and A. P. Dove, Polym. Chem., 2019, 10, 5959–5966 RSC.
- S. Bränssöm, E. Malmström and M. Johansson, J. Coat. Technol. Res., 2017, 14(4), 851–861 CrossRef.
- G. Zhu,
et al.
, Green Chem., 2021, 23, 5911–5923 RSC.
-
R. Mori, Jp. Pat.,Trademark Office, JP Application No. 2022100198, 2022 Search PubMed.
- P. Jia,
et al.
, RSC Adv., 2015, 5, 41169–41178 RSC.
- A. Giuliani, M. Zuccarini, A. Cichelli, H. Khan and M. Reale, Int. J. Environ. Res. Public Health., 2020, 17(16), 5655–5699 CrossRef PubMed.
- P. Jia, H. Xia, K. Tang and Y. Zhou, Polymers, 2018, 10, 1303–1329 CrossRef PubMed.
- W. Gao,
et al.
, New J. Chem., 2021, 45, 123–130 RSC.
- S. Kumar, Ind. Eng. Chem. Res., 2019, 58(27), 11659–11672 CrossRef.
- T. Liu,
et al.
, Polym. Test., 2017, 61, 205–213 CrossRef.
- H. Hosney, B. Nadiem, I. Ashour, I. Mustafa and A. El-Shibiny, J. Appl.Poly. Sci., 135(20), 46270–46281 CrossRef.
- A. Zych,
et al.
, ACS Appl. Polym. Mater., 2021, 3(10), 5087–5095 CrossRef.
- D. L. Cai, X. Yue, B. Hao and P. C. Ma, J. Clean. Prod., 2020, 274(20), 122781 CrossRef.
- D. Skowronska and K. Wilpiszewska, Polymers, 2022, 14, 220–230 CrossRef PubMed.
- M. Zdanowicz, K. Sałasińska and K. S. Lewandowski, ACS Sustainable Chem. Eng., 2022, 10(14), 4579–4587 CrossRef.
- B. B. Hansen,
et al.
, Chem. Rev., 2021, 121, 1232–1285 CrossRef.
- A. S. Fernandez, S. Prevost and M. Wahlgren, Green Chem., 2022, 24, 4437–4442 RSC.
- J. Płotka-Wasylka, M. de la Guardia, V. Andruch and M. Vilková, Microchem. J., 2020, 159, 105539 CrossRef.
- T. E. Achkar, H. Greige-Gerges and S. Fourmentin, Environ. Chem. Lett., 2021, 19, 3397–3408 CrossRef.
- E. L. Smith, A. P. Abbotto and K. S. Ryder, Chem. Rev., 2014, 114(21), 11060–11082 CrossRef CAS PubMed.
- F. M. Perna, P. Vitale and V. Capriati, Curr. Opin. Green Sustainable Chem., 2020, 21, 27–33 CrossRef.
- X. Wu,
et al.
, J. Adv. Manuf. Technol., 2021, 117, 2565–2600 CrossRef.
- R. A. Kazeem,
et al.
, Lubricants, 2022, 10, 69–111 CrossRef CAS.
- S. Syahrullail, S. Kamitani and A. Shakirin, Procedia Eng., 2013, 68, 172–177 CrossRef CAS.
- S. B. Adejuyigbe and S. P. Ayodeji, Nigeria J. Pure Appl. Phys., 2000, 1, 18–24 Search PubMed.
- Y. Li,
et al.
, ACS Sustainable Chem. Eng., 2022, 10(22), 7253–7264 CrossRef CAS.
- M. S. Kamal, I. A. Hussein and A. S. Sultan, Energy Fuels, 2017, 31(8), 7701–7720 CrossRef CAS.
- S. Chowdhury, S. Shrivastava, A. Kakati and J. S. Sangwai, Ind. Eng. Chem. Res., 2022, 61(1), 21–64 CrossRef CAS.
- J. A. Balint, E. C. Kyriakides, G. D. V. Gunawardhane and H. Risenberg, Pediatr. Res., 1978, 12, 715–719 CrossRef CAS PubMed.
- K. Shinoda, M. Araki, A. Sadaghiani, A. Khan and B. Lindman, J. Phys. Chem., 1991, 95(2), 989–993 CrossRef CAS.
- S. Rai, E. A. Siwakoti, A. Kafle, H. P. Devkota and A. Bhattarai, Sci, 2021, 3, 44–62 CrossRef.
- Y. Liao, Inter. J. Pharma., 2021, 603(15), 120709 CrossRef CAS.
- Q. Tian,
et al.
, J. Agric. Food Chem., 2019, 67(22), 6336–6349 CrossRef CAS PubMed.
- S. Koutsopoulos, L. Kaiser, H. M. Erikssona and S. Zhang, Chem. Soc. Rev., 2012, 41, 1721–1728 RSC.
- L. Perez,
et al., Amino Acid-Based Surfactants, Green Chem., 7(5), 583–592 Search PubMed.
- N. A. Malik, Appl. Biochem. Biotechn., 2015, 176, 2077–2106 CrossRef PubMed.
- I. J. A. Baker,
et al.
, J. Surfactants Deterg., 2000, 3, 1–11 CrossRef.
- A. Ghatta,
et al.
, ACS Sustainable Chem. Eng., 2022, 10(27), 8846–8855 CrossRef PubMed.
- E. R. T. Esmaeil, A. Vahidifar, E. Esmizadeh and D. Rodrigue, Polymers, 2021, 13(10), 1565 CrossRef PubMed.
- Q. Zhang, Y. Li, P. Zhu and S. Yuan, Earth Environ. Sci., 2020, 508, 012196–012202 Search PubMed.
- S. J. Hashemi, A. Sadooghi, K. Rahmani and S. Nokhbehroosta, Polym. Test., 2020, 85, 106461 CrossRef.
- Y. Fan, G. D. Fowler and M. Zhao, J. Clean. Prod., 2020, 247(20), 119115 CrossRef.
- A. Kumagai,
et al.
, Int. J. Biol. Macromol., 2019, 121, 989–995 CrossRef.
- N. M. F. Hakimi, Polymers, 2021, 13, 3241–3265 CrossRef.
- P. B. Kanoth, M. Claudino, M. Johansson, L. A. Berglund and Q. Zhou, ACS Appl. Mater. Interfaces, 2015, 7, 16303–16310 CrossRef PubMed.
- P. Dittanet, W. Somphol, T. N. Lampang, P. Prapainainar and S. Loykulnan, AIP Conf. Proc., 2019, 2083, 030008 CrossRef.
- H. Kazemi, F. Mighri, K. W. Park, S. Frikha and D. Rodrigue, Polym. Compos., 2022, 43(4), 2362–2374 CrossRef.
-
R. Mori, Jp. Pat.,Trademark Office, JP Application No. 2020202774, 2022 Search PubMed.
- S. Gupta, Y. M. Puttaiahgowda, A. Nagaraja and M. D. Jalageri, Polym. Adv. Technol., 2021, 32(12), 4642–4662 CrossRef.
- Y. Zhong, P. Godwin, Y. Jin and H. Xiao, Adv. Ind. Eng. Polym. Res., 2020, 3(1), 27–35 Search PubMed.
- J. Ji,
et al.
, Polym. Degrad. Stab., 2022, 199, 109910 CrossRef.
- D. Wei,
et al.
, Mater. Sci. Eng. C, 2016, 58, 986–991 CrossRef.
- B. Ghazvini, B. Acharya and D. R. Korber, Polymers, 2021, 13(16), 2790 CrossRef PubMed.
- P. K. Cheung and L. Fok, Water Res., 2017, 122(1), 53–61 CrossRef.
- S. Ju,
et al.
, Green Chem., 2021, 23, 6953–6965 RSC.
- A. M. E. Arefin, M. R. Khatri, N. Kulkarni and P. F. Egan, Polymers, 2021, 13, 1499–1522 CrossRef.
- X. Wang, M. Jiang, Z. Zhou, J. Gou and D. Hui, Composites, Part B, 2017, 110(1), 442–458 CrossRef.
- S. Bhagia,
et al.
, Appl. Mater. Today, 2021, 24, 101078 CrossRef.
- E. G. BahçegülE, G. Bahçegül and N. Özkan, ACS Appl. Polym. Mater., 2020, 2(7), 2622–2632 CrossRef.
- Rios,
et al.
, ACS Sustainable Chem. Eng., 2022, 10(30), 9770–9786 CrossRef.
- M. M. Mekonnen,
et al.
, Environ. Sci. Technol., 2018, 52(24), 14508–14518 CrossRef PubMed.
- R. D. O. Bordonal,
et al.
, Agron. Sustainable Dev., 2018, 38, 13–35 CrossRef.
- K. Robak and M. Balcerek, Food Technol. Biotechnol., 2018, 56(2), 174–187 Search PubMed.
- M. E. Vallejo, J. Kruyeniski and M. C. Area, Biofuel Res. J., 2017, 15, 654–667 CrossRef.
- C. M. Mendieta,
et al.
, BioResources, 2021, 16(2), 4411–4437 Search PubMed.
-
R. Mori, Jp. Pat.,Trademark Office, JP Application No. 2019030199, 2019 Search PubMed.
- G. Coppola,
et al.
, Earth Syst. Environ, 2021, 5, 231–251 CrossRef.
- F. Bilo,
et al.
, J. Clean. Prod., 2018, 200(1), 357–368 CrossRef CAS.
- S. Nanda, B. R. Patra, R. Patel, J. Bakos and A. K. Dalai, Environ. Chem. Lett., 2022, 20, 379–395 CrossRef CAS.
- P. A. Krishnamurthy, SN Appl. Sci., 2019, 1, 1432 CrossRef.
- G. Atiwesh, A. Mikhael, C. C. Parrish, J. Banoub and T. A. T. Le, Heliyon, 2021, 7, e07918 CrossRef CAS PubMed.
-
C. Schulze, M. Juraschek, C. Herrmann and S. Thiede, Procedia CIRP, The 24th CIRP Conference on Life Cycle Engineering, 2017, 61, pp. 600–605 Search PubMed.
- Q. Li, S. McGinnis, C. Sydnor, A. Wong and S. Renneckar, ACS Sustainable Chem. Eng., 2013, 1(8), 919–928 CrossRef CAS.
- R. Geyer, J. R. Jambeck and K. L. Law, Sci. Adv., 2017, 3, 25–29 Search PubMed.
- D. G. Bucknall, Philos. Trans. R. Soc. A, 2020, 378, 20190268 CrossRef CAS.
- A. L. P. Silva,
et al.
, Chem. Eng. J., 2021, 405, 126683 CrossRef.
-
The European Parliament and the Council of the European Union, Directive (EU) 2019/904 of the European Parliament and of the Council of 5 June 2019 on the Reduction of the Impact of Certain Plastic Products on the Environment in Official Journal of the European Union, The European Parliament and the Council of the European Union, 2019 Search PubMed.
- J. G. Rosenboom, R. Langer and G. Traverso, Nature Rev. Mater., 2022, 7, 117 CrossRef.
- N. Taneepanichskul, D. Purkiss and M. Miodownik, Front. Sustain., 2022, 3, 901885 CrossRef.
- N. Singh, O. A. Ogunseitan, M. H. Wong and Y. Tang, Sustainable Horizons, 2022, 2, 100016 CrossRef.
- S. Nanda, B. R. Patra, R. Patel, J. Bakos and A. K. Dalai, Environ. Chem. Lett., 2022, 20, 379–395 CrossRef CAS PubMed.
- G. D. Carmine, A. P. Abbott and C. D'Agostino, React. Chem. Eng., 2021, 6, 582–598 RSC.
-
D. l. Hoz, A. D. Ortiza and P. Prietoa, CHAPTER: 1 Microwave-Assisted Green Organic Synthesis, in Alternative Energy Sources for Green Chemistry, from Book Series: Green Chemistry Series, 2016, pp. 1–33 Search PubMed.
|
This journal is © The Royal Society of Chemistry 2023 |
Click here to see how this site uses Cookies. View our privacy policy here.