DOI:
10.1039/D2RA04661J
(Review Article)
RSC Adv., 2022,
12, 30985-31003
Influence of VO2 based structures and smart coatings on weather resistance for boosting the thermochromic properties of smart window applications
Received
26th July 2022
, Accepted 28th September 2022
First published on 31st October 2022
Abstract
Vanadium dioxide (VO2)-based energy-saving smart films or coatings aroused great interest in scientific research and industry due to the reversible crystalline structural transition of VO2 from the monoclinic to tetragonal phase around room temperature, which can induce significant changes in transmittance and reflectance in the infrared (IR) range. However, there are still some obstacles for commercial application of VO2-based films or coatings in our daily life, such as the high phase transition temperature (68 °C), low luminous transmittance, solar modulation ability, and poor environmental stability. Particularly, due to its active nature chemically, VO2 is prone to gradual oxidation, causing deterioration of optical properties during very long life span of windows. In this review, the recent progress in enhancing the thermochromic properties of VO2-hybrid materials especially based on environmental stability has been summarized for the first time in terms of structural modifications such as core–shell structures for nanoparticles and nanorods and thin-films with single layer, layer-by-layer, and sandwich-like structures due to their excellent results for improving environmental stability. Moreover, future development trends have also been presented to promote the goal of commercial production of VO2 smart coatings.
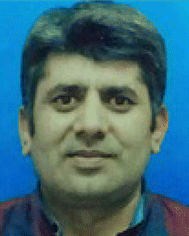 Muhammad Khuram Shahzad | Dr Muhammad Khuram Shahzad was born in Chiniot, Pakistan, in 1986. He received his M.S. degree (2015) in Physics from the University of Agriculture Faisalabad, and his PhD degree (2019) in Physics under the guidance of Prof. Dr Yundong Zhang at Electronics Science and Technology building,, Harbin Institute of Technology, China. After graduation, he became an Assistant Professor in Khwaja Fareed University of Engineering and Information Technology (KFUEIT), Rahim Yar Khan, Pakistan, in 2021. Currently, he is working in the Institute of Physics, KFUEIT, Pakistan. His current research focuses on the synthesis of up-conversion nanomaterials, smart windows, 2D materials, DFT and its biological, sensor, energy applications. |
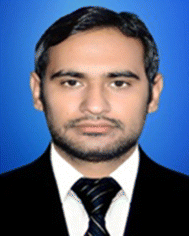 Rashid Ali Laghari | Dr Rashid Ali Laghari is currently working as a postdoctoral research fellow at Interdisciplinary Research Center for Intelligent Manufacturing and Robotics, King Fahd University of Petroleum and Minerals, Dhahran, Saudi Arabia. His current research interests include FEA and predictive modeling and optimization of metal matrix composite material machining process, cutting simulation and machining process of titanium alloys, applied materials, manufacturing and computational mechanics, fabrication of metal matrix composite materials, and multi sensing IIoT platforms for process monitoring of CNC machines. He has authored/coauthored more than 25 publications and attended a number of international conferences. |
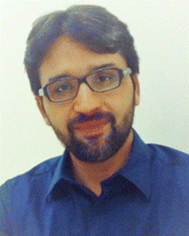 Syed Sohail Akhtar | Dr Syed Sohail Akhtar currently holds the rank of Professor in the Department of Mechanical Engineering at King Fahd University of Petroleum & Minerals (KFUPM). His research areas are applied materials, manufacturing, and computational mechanics focusing on a mix of futuristic and present-day research that is of practical significance and has immediate relevance and impact in the industry. He has authored/co-authored more than 100 archival technical publications, including more than 90 ISI journal papers, and published 02 books, and many book chapters. He presented his research at several international conferences as an invited speaker. In collaboration with other research fellows, he worked on more than 20 basic and applied research projects; some of them were internally funded by the KFUPM, while others were funded by external agencies and institutes. |
1. Introduction
Immense amount of energy is consumed every year to sustain thermal comfort in residential and commercial buildings, needing heat and air conditioning. All these processes lead to an increase in the consumption of electricity, CO2 emissions, and the formation of huge amounts of air pollutants, including SO2 and NO2 emissions and particulate matter (PM10 and PM2.5).1–5 To alleviate these environmental problems, new advanced materials are needed to synchronize the transfer of energy for optimizing energy requirements. About 35% of the heat energy gets out through windows, leading to huge losses in energy.6–8 Buildings (i.e., the residence of modern humans) are among the utmost energy consumers and have a large impact on the environment. Buildings account for 39% of energy consumption in the USA and 40–45% in Europe.9,10 The good news is that the capability for energy saving in buildings is also wide, if sharp energy-efficient technologies and designs are utilized.11 Windows are essential for buildings for providing lighting and visual association with the outside world, and their existence demands much attention in advanced architecture. In terms of energy efficiency, simple windows are not playing a positive role due to some elements; windows regularly let in or let out a large amount of energy and add to energy consumption especially in summers and winters.12 Therefore, as windows have a large effect on energy consumption/saving, they need to be made energy-efficient. Smart windows, which can be implemented in modern energy-saving buildings are currently being extensively investigated (coating with photochromic, thermochromic, and electrochromic materials).13 Additionally, radiative cooling materials spontaneously radiate long-wave infrared (LWIR) to the cold outer space, providing cooling power that is preferred in hot seasons. Radiative cooling has been widely explored for walls and roofs but rarely for windows, which are one of the least energy-efficient parts of buildings. On-demand and selective regulation of radiative cooling (long-wave infrared, LWIR) and solar heat gain (ultraviolet, visible, near-IR, and UV-vis-NIR) of building facades is a grand challenge but essential to decrease energy usage in buildings.14–16
To expand the smart window technology, vanadium dioxide (VO2) has attracted large attention due to its tunable different properties under the effects of external factors. Mostly, the common polymorphs are: VO2(A) (tetragonal), VO2(B) (monoclinic), VO2(R) (tetragonal-rutile), and VO2(M) (monoclinic-distorted rutile).17 VO2(A) is a metastable phase that occurs during the conversion of VO2(B) into VO2(R)18 or VO2(M),19 depending upon the conditions of synthesis. Temperature sensing optical switching20 and optical modulation and smart windows are all the areas of applications for the final device defined by the phase composition of the VO2 powder or layers,21 for example, Li-ion batteries and Na-ion batteries.22–25 The phase structure of VO2 is changeable depending upon the value of temperature, which is called the critical temperature (Tc = 68 °C). V. Wittwer and coworkers made the first observation of the semiconductor to metal phase transition in VO2.26 Below 68 °C VO2 changes to the monoclinic from tetragonal phase, having transmittance properties instead of the reflection of infrared radiation, but it remains lucid to the visible range of radiation. Phase transition and functional properties such as morphology and dimensionality,27 stoichiometry, doping,28–30 and type of lattice (low-temperature phase) are now commonly discussed. On the basis of these properties, thermochromic windows can efficiently reduce energy consumption in residential and commercial buildings because phase transitions successfully adjust solar irradiation in the wavelength region of 800–2500 nm.31–35 Based on these properties, VO2 represents a promising active material in the field of energy-efficient smart windows.
Nevertheless, there are still many hurdles for commercial applications as smart coatings on energy-efficient fenestrations, which seriously limit the relative usefulness of VO2 smart coatings. (i) The phase transition temperature (Tc) of pure bulk VO2 (at 68 °C) is mostly applicable on building fenestrations when a Tc of about 40 °C is considered appropriate; (ii) VO2 coatings' relative modulation capabilities are not much efficient to save energy due to the fact that the modulation of VO2 for sun oriented radiation is mostly relegated to the transmittance switch within the near-infrared region, which is accounted for 43% of sun powered vitality within the sun oriented spectrum; (iii) the glowing transmittance Tlum for a single layer of VO2 with alluring ΔTsol is, as a rule, less than 40% (indeed 30%) due to retention within the short-wavelength region extending in both the semiconducting states and metallic states of VO2, which is anticipated to exceed by at least 50% for regular applications; (iv) as an advanced coating, VO2 must maintain good thermochromic performances for at least a decade for practical applications.36–39
However, in the real environment, VO2 finally changes to the V2O5 phase, which is the most thermodynamically stable phase.40–42 Considering, the environmental conditions, VO2, could be an awesome challenge for general applications such as modern coating. These challenges must be solved for practical applications to be realized, and various attempts have begun to accomplish this goal. Distinctive strategies have been proposed to solve these issues including doping with different particles in a viable way to tweak the phase-transition temperature of VO2,43–45 multilayer structures,46,47 nanocomposites, and manufacturing nanostructures to enhance the optical properties,48–50 counting improving solar-modulation abilities and progressing better luminous transmittances. Many works have used these tactics which have been detailed in earlier reviews.51–55
Unfortunately, except for the above-mentioned hindrances there exist new but critical challenges for VO2 based coatings that may have been overlooked in the foregoing work. The constraints of VO2 based smart coatings are presented in this review, to address these difficulties, merging current research with future possibilities. Furthermore, as researchers' interest in this topic has grown, this work highlights broad evaluation standards that can be used to compare qualities objectively. In this review, we have focused on thermochromic VO2 smart coatings for enhanced thermochromic performance, environmental stability, and mass production for commercial applications on building fenestrations. With the development of material fabrication technology, various VO2 nanostructures, e.g., thin films and low-dimensional structures (LDSs), have been successfully fabricated and have been widely investigated to enhance environmental stability in thermochromic smart windows, as shown in Scheme 1. Thin films and LDSs are suitable for micromachining processes, which promotes the development of both macro and micro-scale devices. As we know, the metal-insulator transition (MIT) temperature and behavior of VO2 are extremely sensitive to external stimuli, including doping, strain, surface/interface effects, electrochemical gating, electric field, light, electron beam, etc. Besides, the morphology also has a great influence on the properties of the VO2 material. VO2 LDSs-nanowires (NWs), nanodots (NDs), nanoparticles (NPs), nanorods (NRs), nanobelts (NBs), nanosheets (NSs), etc. exhibit unique electrical, mechanical and optical properties different from their bulk counterparts due to the size and surface/interface effects. Thus, we categorized the literature based on structures such as coatings in the form of core–shell structures for nanoparticles and nanorods, and thin-films, which led to the layered and layer-by-layer and double-layer structures, etc. The coating layers of various materials on VO2 particles played an outstanding role to enhance the durability of hybrids by preventing the direct contact between air and VO2 particles, which led to the improvement of the thermochromic performance (Tlum and Tsol) of VO2 and its hybrids. On the basis of a survey of excellent experimental works on VO2, we aim to provide a wide range of insights into the recent studies in the above mentioned field.
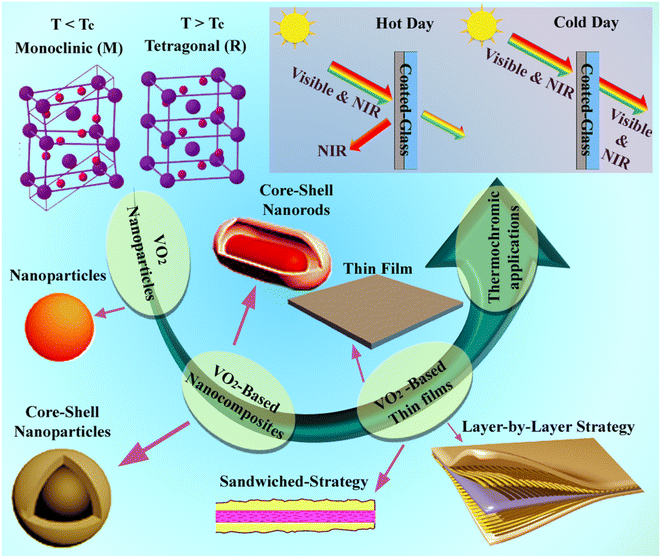 |
| Scheme 1 Overview of VO2-based composites on durability against a harsh environment. | |
2. Structures of VO2 for durability
The unstable behavior of VO2 particles is the major problem for their practical application in smart windows. The stabilization of VO2 has been deemed a key factor for realizing the outstanding candidate for smart window applications. To improve the structural integrity of active materials in various fields, surface modification remained an excellent strategy through different structures of active materials. However, the surface modification of VO2 also has huge potential for improving its stability against a harsh environment by avoiding the direct contact between air and the surface of VO2 particles. As a result of the prevention of direct contact with air, the durability of thermochromic performances of VO2 is significantly enhanced, which is summarized below.56–60
2.1 VO2 nanoparticle-based core–shell structures
In the core–shell structure strategy, the shell materials provide the protection of the core from various factors such as oxidation, harsh environments, and produced stress in the core materials. Because of the synergic effects of the core–shell structure, the composites emerge with excellent properties instead of intrinsic properties of core materials. As a result of the combined properties of core materials and modification, the composites deliver excellent performances in practical applications.61–65 VO2 particles have been used as core materials to evaluate the performance in smart window applications. Y. Chen and coworkers presented the fabrication of VO2@ZnO core–shell nanoparticles, which improved the stability of VO2-based films in practical architecture (Fig. 1(a)).66 In the entire process of forming a VO2-based film, the transmission electron microscopy (TEM) image exhibits that nanoparticles were covered with a ZnO shell with a thickness of roughly 20 nm as seen in Fig. 1(b). Furthermore, the durability of VO2-based smart windows was significantly improved by VO2@ZnO core–shell structures. The coated shell acted as a barrier to the flow of oxygen and water. It prevented the oxidation of VO2 to V2O5. They created a harsh atmosphere with a constant temperature of 60 °C and a humidity of 90%. The degree of decline in thermochromic performance was used to assess the durability of VO2-based films. They analyzed the transmittance spectra of an uncoated VO2 film and VO2@ZnO film. After 12 hours, the transmittance contrast between the low-temperature semiconductor phase and high-temperature phase in the uncoated VO2 film began to decrease. For the uncoated VO2 film, the ΔTsol was 17.2% within the initial state and decreased to 0% after 30 h. It is evident through Fig. 1(c) and (d) that the organized VO2@ZnO nanoparticles primarily based for smart windows totally demonstrated strong sun modulation efficiency, excessive luminous transmittance, and fantastic sturdiness in a hot, humid, and oxygenic environment. It could well be found that the transmittance contrast between 20 and 80 °C at λ = 1500 nm (ΔTλ = 1500) started to decrease with the time increasing. S. Zhao and coworkers applied an inorganic–organic hybrid lined of VO2 nanoparticles for more advantageous durability.67 They proposed a VO2@MgF2@polydopamine (PDA) inorganic–organic hybrid. Fig. 1(e) shows the synthesis process of VO2@MgF2@PDA. The coated architecture greatly enhances the optical durability more than 13 times in contrast to pristine VO2 and the transmittance difference between room and high temperature changed within 20% (decreasing from 25 to 20.1%) at λ = 1200 nm after an ageing time of 1000 h at constant temperature (60 °C) and relative humidity (90%). The SEM image can be seen clearly from Fig. 1(f). It depicts the representative core–shell structure. For the durability portrayal of inorganic core–shell nanoparticles, temperature-responsive optical films were ready and positioned in a soggy warming environment (T = 60 °C, RH = 90%) for testing their optical properties in a predetermined time frame. After different aging times, the visible infrared (vis-IR) transmittance of VO2 nanoparticles demonstrates the durability of VO2@MgF2 core–shell architectures. It is observed that it was worse than the VO2 core only. The hydration effect of the VO2 core surface in the core-preparation process could be the reason. Further, the VO2 nanoparticles can be damaged after many days of soaking in water and the disassembling process can accelerate if the pH of water is not neutral. Fortunately, the durability of VO2@MgF2 has been increased by almost ∼6.5 times (from 77.5 h to more than 500 h) in EG solvent. Under the same conditions as VO2@MgF2, the optical durability of VO2@MgF2@PDA inorganic–organic core–shell nanoparticles is presented in Fig. 1(g). The durability has substantially improved after PDA coating and the value of ΔT changed by 20% (from 25 to 20.1%) after 1000 hours of treatment at constant temperature (60 °C) and humidity (90%). In comparison to pristine VO2 (the durability time is higher than that of others) the durability time of VO2@MgF2@PDA has been increased by more than 13 times. The differential scanning calorimetry (DSC) curves of VO2@MgF2 have the endothermic peak at 64.1 °C in the heating process and the exothermic peak at 41.3 °C in the cooling process, as illustrated in detail, and it showed that the DSC cycle corresponds to one cycle of high–low–high transmittance. Bifunctional template-induced VO2@SiO2 Dual-Shelled Hollow Nanosphere-based coatings (DSHNs) were prepared by Z. Qu and coworkers.68 They investigated the thermochromic and optical performances of VO2@SiO2 DSHN coatings; a UV-vis-IR spectrophotometer with the assistance of the warming stage was used to quantify the temperature-dependent transmittance. The test results and the determined optical performances (Tlum and ΔTsol) are examined in detail. Concentrating with the nonstop and dense VO2 coatings, the VO2@SiO2 DSHN coatings introduced much better optical work. With the rise of the refluxing time, the Tlum increased from 42.5% to 66.3% (VS1) first and then, at that point, decreased to 61.7% (VS2) and 61.8% (VS3), separately. Meanwhile ΔTsol expanded from 7.6% to 10.7% (VS1), 10.5% (VS2), and 12.6% (VS3), independently. The RI of VO2@SiO2 DSHN coatings gained in the current work exhibited a dramatic reduction, and reached 1.63 at a wavelength of 630 nm, diffusing the coating with the best anti-reflection (AR) effect. They also matched the transmittance spectra at low temperature by finite-difference time-domain (FDTD) using the measured optical constants. It is found that the calculated results are in strong accordance with the experimental spectra. Consequently, the dual-shell hollow nanoparticles of VO2@SiO2 demonstrated extraordinary potential in enhancing the optical performance of thermochromic coatings. K. Tong and coworkers synthesized VO2 nanoparticles covered with Al–O-based shell (V/AO) nanoparticles by utilizing a facile method.69 The strengthened V/AO nanoparticles had shown great durability for the unique environment. TEM images can be seen in Fig. 1(h); it showed the typical structures of the annealed V/AO nanoparticles in a better way. Moreover, Fig. 1(i) represents the VO2 nanoparticles that had directly reacted with water and oxygen. The reaction had begun at the outer layer of the VO2 nanoparticle, and V4+ had oxidized to V5+. Subsequently, the VO2 no longer has the thermochromic property but an un-annealed Al–O-based shell allowed for a shelter to the VO2 center, which delayed down the diffusion of water and oxygen into the VO2 cross section. The un-annealed (V/AO) nanoparticles reliably decreased the thermochromic property. The annealed (V/AO) nanoparticles outlined the preferred stability over un-annealed (V/AO) nanoparticles because the previous shell had more excellent compactness and gave sufficient protection for the core. Further, shell of Al–O-based to the VO2 center, the stability of the thermochromic nanoparticles, is estimated and put into a climate chamber to replicate the result of humidity and temperature. The annealed Al–O-based shell had shown the most stability of the VO2 core. The transmittance of the films had been estimated around the same value. It showed the progression of ΔTsol for different values. The annealed V/AO nanoparticles explain the most generous stability of three samples, with ΔTsol changing from 9.62% to 9.30% after 20 days of aging, which indicates that the annealed Al–O-based shell is compact and blocks the diffusion of moisture and oxygen more effectively. So the annealed V/AO nanoparticle had the capacity for the broad application of the VO2-based thermochromic film. Fig. 1(j) reveals that VO2 nanoparticles had been secured by the Al–O shell and stayed stable when placed in a damp warming climate. The temperature of VO2 only shows high at (350 °C in the air) which assure the presence of the Al–O-based shell. These core–shell structure nanoparticles had shown good optical properties and chemical stability. The shell had a successful boundary layer to keep away from oxygen and water from diffusing into the VO2 materials. So, VO2 is protected by the Al–O-based shell and applied in smart
windows, such as automobiles, buildings, etc. It was found that the above mentioned techniques are suitable for durability-enhancement against weather resistance of smart window applications.
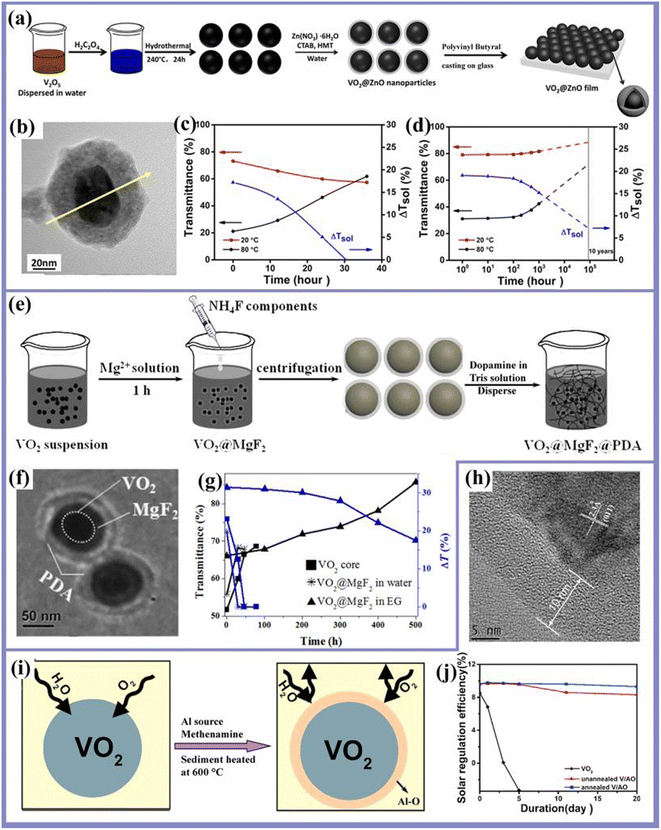 |
| Fig. 1 (a) Experimental flow chart for the synthesis of VO2@ZnO core–shell structure nanoparticles and VO2@ZnO films. (b) TEM images of VO2@ZnO core–shell structure nanoparticles. Optical transmittance spectra of (c) uncoated VO2 and (d) VO2@ZnO. Reproduced with permission66 copyright © 2017, American Chemical Society. (e) Flow chart for the whole process of flexible film preparation and influence of reaction parameters for depositing MgF2 on the surface of the VO2 core. (f) TEM images of VO2 nanoparticles with different shell thicknesses of VO2@MgF2. Vis-IR transmittance spectra of the VO2 core. (g) Curves of visible light transmittance and the transmittance difference (ΔT) between room and high temperature at λ = 1200 nm of these samples with the change of treatment time. Reproduced with permission67 Copyright © 2019, American Chemical Society. (h) SEM image of the sample. (i) Preparation of VO2 and AlO. (j) Transmittance spectra with different time spans. Reproduced with permission69 Copyright © 2017, Elsevier. | |
The coatings of metals as a shell on different core materials have shown extraordinary results in various applications.70–73 By taking the advantages of different coating materials, Y. Gao and coworkers used the dip-coating technique to create transparent flexible hybrid VO2-based films with exceptionally high thermochromic characteristics as shown in Fig. 2(a).74 Fig. 2(b) displays the TEM images of the original VO2 nanoparticles and the silica-coated VO2 nanoparticles with a PVP prepared sample. PVP pre-treatment favored the production of smooth, uniform silica shells. PVP is an amphiphilic polymer, which could keep the nanoparticles stable in water and a variety of non-aqueous solvents. The transmittance spectra of coated and uncoated samples after various acid exposure times are shown in Fig. 2(c). After the first 200 seconds, the uncoated particles had a quick 56.2 percent rise in transmittance, from 8.6% to 64.8%. The coated particles experienced an increase of 10.9%, from 8.1% to 19.0%. This result exhibits that VO2@SiO2 was able to confront the acidic treatment due to the protection of the SiO2 shell. The films had great flexibility and fair visible transmittance due to the above mentioned results. Generally optical transmittance of spectra and thermal hysteresis loops are presented at the wavelength of 1500 nm of films. J. Zhu and coworkers tried to prepare VxW1−xO2(M) NPs, which were subsequently coated with a thin layer of silica, shielding VO2 NPs from aggregating and forming during the annealing process.75 The production process of VxW1−xO2(M)@SiO2 and nano-crystal coated VO2 with SiO2 materials is discussed. They presented the TEM pictures of the VO2(M)@SiO2 and the annealed VO2(M)@SiO2 nano-materials. It was noted that essentially every single VO2 nanoparticle was coated with a SiO2 shell independently. The crystallinity of VO2 nanoparticles was essential for the best thermochromic execution of vanadium dioxide-based thermochromic smart coating (VTSC). They addressed the transmittance spectra of VTSC based on the prepared particles. Both the silica coating and annealing showed excellent effects on the thermochromic properties. The Tlum and ΔTsol were increased from 56.6% and 8.7% to 59.7% and 11.3%, respectively, after the original VO2(M) NPs were coated with a layer of silica. The thermochromic performance was good enough to obtain VTSC suitable for practical construction. Y. Chen and coworkers prepared the core–shell structure by applying the ascorbic acid shell on VO2 nanoparticles and measured the thermochromic properties for smart window application (Fig. 2(d)).76 The covalently bonded ascorbic acid shell played an outstanding role to uplift the durability and anti-oxidation properties of VO2 by avoiding further oxidation with air, which became fruitful for enhancing the life span of VO2 in a humid environment. Transmittance spectra of the ascorbic acid-coated sample and uncoated sample were compared. It delivered excellent anticorrosion properties in H2SO4 and H2O2 environments, which led to enhance the thermochromic properties. Ascorbic acid remained firmly on VO2 particles due to strong interfacial interaction between VO2 particle surfaces and ascorbic acid coating, which was confirmed by SEM (Fig. 2(e)). It was found that the thermochromism of pure VO2 completely vanished within 3 days due to phase changes, but coated VO2 remained stable and the thermochromic property existed without phase changes against a humid environment. The result can be easily observed in Fig. 2(f). The durability of ascorbic acid-coated VO2 was also investigated under a highly humid environment (humidity 90% and temperature 60 °C) through differential scanning calorimetry in Fig. 2(g). This method provides a promising way for weather resistance applications.
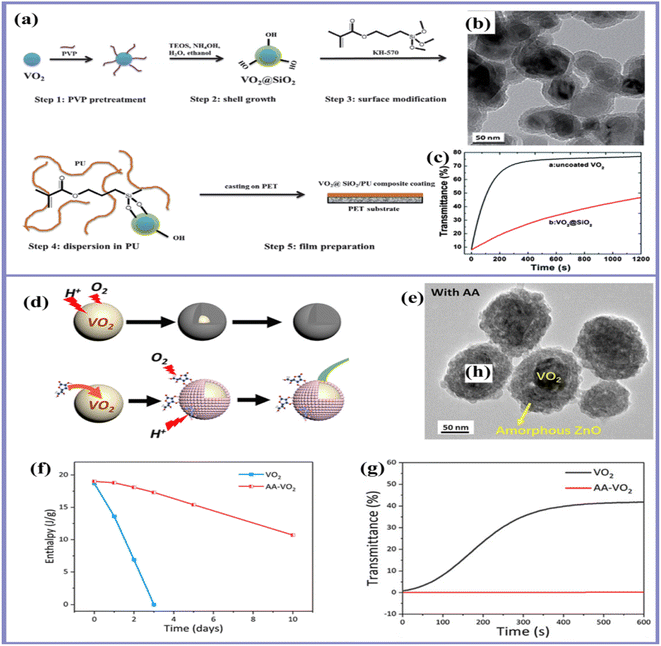 |
| Fig. 2 (a) Preparation procedure for VO2@SiO2 nanoparticles and flexible composite films. (b) TEM images of the VO2@SiO2 composite film. (c) Transmittance spectra of coated and un-coated samples. Reproduced with permission74 Copyright © 2012, The Royal Society of Chemistry. (d) Preparation process of VO2 and AA-VO2. (e) TEM images of VO2 nanoparticles and AA-VO2. (f) Transmittance spectra with time in days. (g) Transmittance spectra with time in seconds. Reproduced with permission76 Copyright © 2019, American Chemical Society. | |
2.2 VO2 nanorod-based core–shell structures
The nanorod structure core exhibits a remarkable modulation ability for thermochromic and solar infrared light. Nanorod structures with both thermochromic and photocatalytic properties offer significant potential for creating a multifunctional smart coating. Thus, nanorods have proved to be the best for structural modification compared to spherical particles for various applications and have gained huge attention because of the best shape anisotropy. The good physical properties of nanorods could mostly be achieved by using different metals. Considering the advantages of nanorods, this structural modification of VO2 with a core–shell structure has also been tried in smart window applications.77–80 For example, A. Huang and coworkers arranged VxW1−xO2(M)@SiO2 ultra-thin nanostructures.81 They had prepared ultra-thin VO2(B) nanostructures with a diameter of approximately 15 nm by a simple post-annealing method, and the VO2(M) nanoparticles were obtained in this process as shown in Fig. 3(a). The arranged VO2(M) and VO2(M) execution show that the VO2(M) nanoparticles that is required excessive temperatures and longer times with the assistance of the hydrothermal process. Fig. 3(b) clearly demonstrates the TEM images of the prepared VO2@SiO2 sample and SiO2 had an external shadow portion and the inside darker section had VO2. The presence of the silica shell had greatly enhanced the anti-oxidation ability of the VO2 powders and had subdued nanoparticles throughout the thermal method. However, the luminous transmittance increases with the SiO2 shell because it had a transparent structure. It simply represents that Tc had decreased with increasing the amount of doping at 20 °C. The optical transmittance spectra of the as-arranged VO2(M)@SiO2 nano particles with various amounts of W-doping (W1, W3, and W5) at low temperature (20 °C) and high temperature (90 °C) were discussed. When the measured value of W-doping expanded, Tlum diminished moderately due to an increase of the free-electron density, which was related to the increase in the absorption and reflection of visible light at previously mentioned below temperature. The top free electron density narrows the VO2(M) energy gap in the semiconductor case. It reduced the value of enthalpy VO2(M/R) via the phase transition of ΔTsol. Due to dispersion and addition of the inert silica coating in the optical transmittance spectra, Tlum was increased from 15.73% to 24.69%. ΔTsol was improved from 4.6% to 7.15% due to the anti-reflection of SiO2. The most beneficial and accurate method is via W-doping, which was done in this sample, as seen in the DSC curves (Fig. 3(c)). W. Li and coworkers fabricated VO2(M)–ZnO heterostructured dandelions.82 Fig. 3(d) elaborates the mechanism of the VO2(M)–ZnO, which was used to examine the dandelions, and three different samples were synthesized for ZnO NR measurements, VO2(M)–ZnO without Na-CA and VO2(M)–ZnO without ZnO seeds. The scanning electron microscopy (SEM) image displayed that the samples comprised ZnO and VO2(M), as seen in Fig. 3(e). The reversible stages of the transition temperature of the pure VO2(M) and VO2(M)–ZnO composite powders were demonstrated by using differential scanning calorimetry (DSC). Moreover, Fig. 3(f) demonstrates that the ZnO NRs were consistently propagated on the surface of the VO2(M) NPs to develop the VO2(M)–ZnO hetero-junction because of interfacial contacts. Following recreated sunlight irradiation, the electrons and holes were photo-generated to save separately. The enhanced thermochromic features and chemical stability were associated with the ZnO. The composite film of VO2(M)–ZnO showed a diminished stage transition temperature (Tc = 62.6 °C) with an increasing visible transmission (Tvis-l = 52.2%) and solar modulating ability (ΔTsol = 9.3%) as contrasted with the pure VO2(M) film. R. Li and coworkers prepared vanadium dioxide (M)@SiO2 NPs.83 The rectangular parts of VO2(B) nano-plates with a diameter ranging from 20 to 30 nm were hydrothermally manufactured, and the VO2(B)@SiO2 core–shell structure was made by utilizing an advanced Stober technique; Fig. 3(g) represents the thin layer of SiO2 (30 nm) that was homogeneously surfaced on VO2(M). In particular, the nano-pores showed two particular sizes: more prominent ones lied at the interface between VO2(M) and SiO2, and shorter ones laid inside the VO2(M). Significantly, different nano-pores were made inside VO2(B)@SiO2 nanoparticles because of the variety in thickness between VO2(B) and VO2(M), which was given by higher optical transmittance and thermal protection. The optical transmittance of VO2(B)@SiO2 in comparison to VO2(M) was discussed. It was noticed that VO2(M) showed a sharp optical distinction between the high and low-temperature phases, indicating the single-phase characteristic and high crystallinity of the VO2(M) film. VO2(B)@SiO2 exhibited a vastly improved optical performance with a higher visible transmittance and a more extensive solar modulation process, which was observed by the corresponding spectra in Fig. 3(h). The given data were contrasted to the obvious transmittance of 31.72% for VO2(M), and the VO2(B)@SiO2 exhibited an obvious transmittance of 35.96%, with an increment of 13.4%.
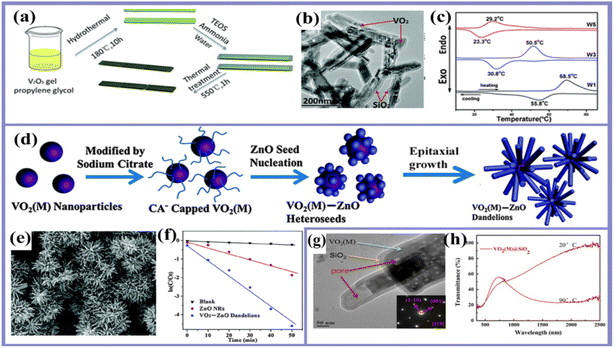 |
| Fig. 3 (a) Experimental flow chart for the synthesis of the vanadium dioxide rod structure. (b) SEM images of VO2@SiO2 rod structure nanoparticles. (c) Exo and endo curves with different temperatures. Reproduced with permission81 Copyright © 2013, The Royal Society of Chemistry. (d) Flow chart for the whole process of VO2(M)–Zno dandelions. (e) TEM images of VO2(M)–Zno dandelions. (f) Thermochromic graph at different times for Zno nanoparticles and VO2–Zno. Reproduced with permission82 Copyright © 2016, The Royal Society of Chemistry. (g) SEM images of pore, VO2(M) and SiO2. (h) Transmittance spectra of VO2(M)@SiO2. Reproduced with permission83 Copyright © 2013, Elsevier. | |
Y. Li and coworkers synthesized the VO2@TiO2 core/shell nano particles as seen in Fig. 4(a).84 Fig. 4(b) expresses the SEM images of TiO2 shell composites. It also depicts the behavior of the VO2@anatase composite. Moreover, Fig. 4(c) presents the dark and light on graph. The transmittance curves exhibited an un-doped VO2 process after preparation of a layer, and the average transmittance was improved with the deteriorated modulation technique. And the loop width was also down by 5.7 °C. The above mentioned methods depicted good thermochromic performance against weather resistance potential for practical application of VO2-based smart windows. T. D. Vu and coworkers reported a new strategy of nanocompositing vanadium dioxide preparation with excellent durability.85 They employed the glass industry compatible process of magnetron sputtering, followed by rapid thermal annealing (RTA). Instead of the usual continuous films, this thin film process gave a unique structure where VO2 NPs are dispersed in a V2O5/V3O7 matrix with a dense thermodynamically stable V2O5 overcoat. The key factor that allows for the deposition of nanorod VO2 embedded inside the V2O5 matrix is the introduction of seeding, followed by delayed injection of O2. As shown in Fig. 4(d), the sputtering process is divided into two phases. The first phase is the seeding of vanadium on the substrate. In this phase, the isolated island of vanadium nucleus is formed through the sputtering of the vanadium metal target for a short duration of 10 s in this study. At the end of the seeding phase, O2 is slowly injected into V metal. The SEM image shows the presence of V metal seeds and crystalline VO2 behaviour. It can be seen clearly in Fig. 4(e). This new type of nanocomposite gives a nearly doubled ΔTsol (20%) compared with that of the best reported continuous single vanadium oxide film (10%) and high duration as seen in Fig. 4(f). The accelerated test suggested that the expected service life of this film is 23 years, which is a breakthrough in VO2 based thermochromic smart windows. Fig. 4(g) depicts that the VO2 nanorod structure is formed by introducing seeding guided growth along with manipulation of gas injection timing and target current during reactive sputtering, resulting in the V2O5/VO2 thermochromic composite film. The high durability, due to the encapsulation of V2O5, together with the significantly enhanced thermochromic properties and facile industry compatible process, provides a new strategy to scale up this technology into real-world applications.
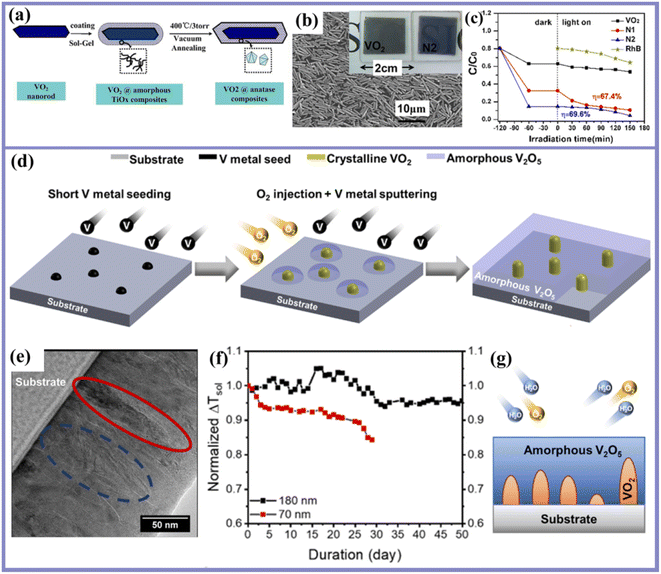 |
| Fig. 4 (a) Preparation of the VO2@anatase composite. (b) SEM images of the VO2@anatase composite. (c) Transmittance spectra of VO2@anatase. Reproduced with permission84 Copyright © 2013, The Author(s). (d) Preparation of V2O5/VO2 seeding via a one-step high-powered impulse magnetron sputtering process. (e) SEM images of the amorphous V2O5 matrix. (f) Transmittance spectra of V2O5/VO2. (g) Amorphous V2O5/VO2 process. Reproduced with permission85 Copyright © 2022, Elsevier. | |
Combining VO2 particles with polymers and two dimensional materials is deemed to boost the thermochromic properties of VO2-hybrids for long term durability.86–90 W. Li and coworkers arranged useful fiber mats with tunable diffuse reflectance and VO2/PVP composite fiber mats.91 The VO2/PVP composite fibers were scattered by the inter-fiber scattering process, which means light phenomena. Every scattering process involved absorption and reflection was due to the dispersion of the incident light. The absorption expanded to understand the absorption coefficient of VO2 nanoparticles, and the cross-sectional of these fibers was modified to investigate the optical property. The VO2 and W doped VO2 nano particles were phase-stable. The diffraction peak shift created by W doping was apparent in the nanoparticles immersed in PVP. They showed that the W-doped VO2 nano particles consisted of the diffuse reflection spectrum of fiber mats. They tuned their temperature phase transition in to 40 °C and its diameter was 800 nm that exhibited the diffuse reflection range by the blue line in the infra-red range. The diffuse reflectance demonstrated that no variation existed above 68 °C, which was more than that of the fiber mat included 0.05 g of VO2, then the appropriate diffuse reflection property associated with VO2 particles. J. Zhou and coworkers arranged nano-scale VO2 and performed characterization of VO2(M)–SnO2 thermochromic films, and annealing was utilized to change over them into VO2(M)/SnO2 hetero-structures.92 The optical band gap of the VO2 crystals was expanded. Thus, the optical properties were enhanced. The nanosized particles (SnO2) are bigger as compared to outer layer of the VO2(M). They showed the reversible phase transition temperature of the VO2(M) and VO2(M)/SnO2. It was concluded that the sharp endothermic peak of the pure VO2(M) was determined at 73.7 °C, which was marginally bigger than 68 °C. Yet, the phase transition temperature of the VO2(M)/SnO2 hetero-structure was decreased from 69.8 °C. The change between endothermic and exothermic peaks for the VO2(M)/SnO2 hetero-structure was 9.6 °C, which was a lot lower than the 15.9 °C of the pure VO2(M). It was seen that the loop amplitude of the VO2(M)/SnO2 hetero-organized film was 10.7 °C, which was limited by 7.1 °C related to the pure VO2(M) film. The limited hysteresis has raised the affectability of phase transition responses to the different values of temperatures. They demonstrated the optical transmittance spectra and the corresponding film images. The optically improved performance of nano-sized SnO2 on the surface of exposed VO2 nano-rods yielded better results. The above mentioned results have expressed the best performance of weather resistance of smart window applications.
2.3 Thin film strategies of VO2 at the device level
2.3.1 VO2-based thin film structures. The layer by layer thin film preparation strategy is one of the simplest and most effective methods for preparing thin films. Compared with mixing film-growth techniques, layer by layer preparation of thin films provides better control of the structure at the molecular level.The coating of materials on VO2 particles at the nanoscale level is considered an expensive method of fabrication at the industrial level. The structural modification based on the thin film is the easiest and cheapest process for coating at a bulk level, which may affect the cost of the final product.93–100 The thin film coating has also been investigated by combining different materials through various methods. For example, by a simple mixing method, a thin film has been tried by J. Sang and coworkers, in which they achieved the VO2–ZnO combined films with improved thermochromic features by a facile ball-milling method.101 Fig. 5(a) depicts the facile ball-milling method by which VO2–ZnO composites were made, and the combined films were built. The morphology of the as synthesized sample was presented by the SEM image as seen in Fig. 5(b). The ZnO NPs were represented as a scattering medium that was consistently filled in the space between the VO2 powders throughout the process of ball milling. The ZnO NPs were added to optimize the thermochromic properties of the VO2. The addition of ZnO uniformly increased the thermochromic properties, and its excellent performance was achieved, having results of Tlum = 64.2% and ΔTsol = 11.3%. Moreover, the film coated with two layers displayed an ultra-high ΔTsol of 18.8%, and likewise, kept an excellent Tlum of 54.3%, which was preferred to most VO2 nano-composite films and multilayered VO2 films. Fig. 5(c) shows the spectra between transmittance and ZnO/VO2. They observed that the reflectance of various samples was reduced by enhancing the content of ZnO NPs. This indicated that ZnO NPs separated uniformly in the VO2–ZnO composite layer that decreased the reflectance of VO2 films similar to the anti-reflection coatings (ARCs), and increased both Tlum and ΔTsol concurrently. Further, instead of metal oxides, the polymer material has been tried to explore the thermochromic properties of the hybrid of VO2. Z. Qu and coworkers prepared VO2 nanoparticles that were embedded on cross-linked polymethyl methacrylate (PMMA) chains as seen in Fig. 5(d).102 The enhanced luminous transmittance of light along with a better solar transmittance was obtained by this synthesized VO2 NP. They obtained a luminous transmittance of about 50%, a solar modulation ability of about 17.1%, and a haze of about 11% via the cross-linked PMMA-VO2 film. The graphical results represented that the luminous transmittance was decreased at a high temperature of 90 °C, while it increased largely at 25 °C. The values obtained from the graph were ∼50% luminous transmittance and approximately equal to 17.1% solar modulation ability. The graph represented value is decreasing by increasing the wavelength of light. It can be further reduced by decreasing the size of the VO2 NP. The graph provides us with an average value of haze equal to 11% that was in the luminous range. In Fig. 5(e) a comparison graph between solar modulation and time (h) shows the transmittance and durability of VO2. To check the durability of PMMA-VO2, the following conditions were sustained: low temperature of 25 °C (insulating phase), high temperature of 90 °C (metallic phase), and relative humidity of ∼95%, and an aging chamber for aging tests had a constant temperature of 60 °C. The results exhibited that the cross-connected PMMA-VO2 film had a longer life than the non-cross-connected PMMA-vanadium dioxide film having a large molecular weight. So, this research shows a greater enhancement in the durability of VO2 for smart window applications. The PMMA-VO2 film played a greater role in weather-resistance; it minimized the cooling demands at high temperatures and enhanced the warm comfort in cooling climates. The fabricated VO2 nanoparticle enhanced the luminous transmittance (∼50%), solar modulation ability (∼17.1%), haze (∼11%), and lifespan as compared to simple VO2 nanoparticles. These results of nanoparticle-based thermochromic films exhibit a robust durability.
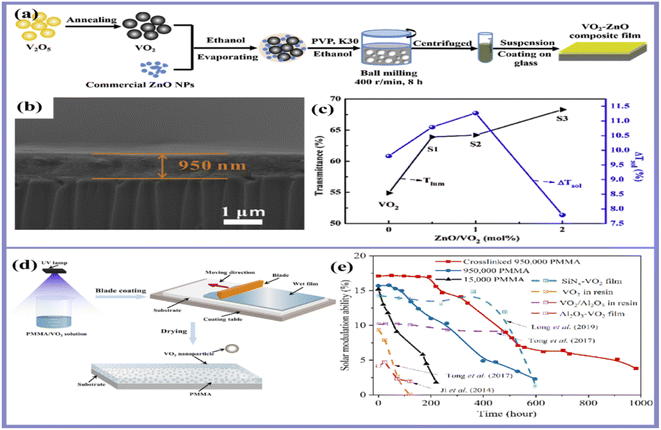 |
| Fig. 5 (a) Experimental flow chart for the synthesis of VO2@ZnO core–shell structure nanoparticles and VO2@ZnO film. (b) TEM images of VO2@ZnO core–shell structure nanoparticles. (c) Optical transmittance spectra of VO2@ZnO at a constant temperature (60 °C) and humidity (90%). Reproduced with permission101 Copyright © 2019, Elsevier. (d) Flow chart for the whole process of VO2@PMMA film preparation. (e) Solar modulation of the VO2@PMMA film. Reproduced with permission102 Copyright © 2020, Elsevier. | |
2.3.2 VO2-based thin film structures via the layer-by-layer strategy. The thin film is prepared via spin coating method, the matrix materials are entangled with active VO2 nanoparticles. The effects of coating materials in thin-film structural modification are clearly seen by the sputtering method based thin film.103–106 Like other physical vapor deposition techniques, ion beam sputtering provides advantages such as deposition rate, uniformity, composition, thickness control, adhesion, and material properties. However, ion beam sputtering offers additional sputter deposition features, which include a wide range of materials with indifference to target thickness or properties, precision deposition stops, clean and low pressure processing (<0.5 mTorr), and reactive deposition not susceptible to high energy arcs due to cathode target poisoning. In the ion beam deposition process, there is no plasma between the substrate and the target as one would find with magnetron sputtering. This means that the ion beam deposition technique can be used for deposition on sensitive materials and reduces the likelihood that the final product will contain gas molecules.To elaborate the effects of thin film coating on the durability of VO2 in smart window applications, thin films have been tried by altering the various coating materials. For example, additionally, S. Long and coworkers prepared a high-quality V2O3/VO2 bi-layer structure.107 To enhance the crystallinity of the VO2 thin film, the bottom layer of V2O3 behaved as the buffer layer as seen in Fig. 6(a). The fabricated film was used to increase the luminous transmittance, solar modulation ability, and durability of the vanadium dioxide film. They displayed the durability of the fabricated film; the film was kept at 60 °C and had a humidity of 90%. The SEM images clearly show the presence of V2O3 and VO2 as can be seen in Fig. 6(b). The simple VO2 film was damaged after 72 hours and completely depleted after 144 h (∼6 days) as compared to this V2O3/VO2 thin film which retained itself at 144 h (∼6 days) (Fig. 6(c)); the same is the case for solar modulation ability ΔTsol. Finally, Fig. 6(d) describes that the fabricated films (V2O3/VO2) had maintained the luminous intensity for a long duration and also provided good durability and solar modulation ability of 13.2%, which was increased by 76%. T. Chang and coworkers designed VO2/HfO2 thin films via the sputtering method, the SEM images of which can be seen in Fig. 6(e) and (f).108 The fabricated film had an encapsulation structure that has more stability than a single vanadium film. The thermochromic properties were enhanced by using HfO2 with VO2. This increased luminous intensity and solar modulation ability. The fabricated film VO2/HfO2 protected the VO2 layer from weather changes and provided comprehensive protection. It also increased the service life of VO2 and the stability of the VO2 film. A comparison of the simple VO2 film and VO2/HfO2 showed that the VO2/HfO2 layer has high luminous transmittance, Tlum = 55.8% (at low temperature) and Tlum 43.6% (at high temperature), and high solar modulation ΔTsol = 15.9%. So, as a result, we can see a total of 80.1% improved properties with VO2/HfO2. For testing the durability of the fabricated films, the sample was placed in a harsh environment at a temperature of 60 °C and humidity of 90% as shown in Fig. 6(g). Moreover, Fig. 6(h) represents the graph of solar modulation ability versus aging time; it is clear that the simple VO2 film lost its thermochromic properties, and showed enhanced properties that last for a few time span when combined with silicon weatherproof sealant. The sample showed greater stability that lasted for 100 days, proving that the product was more efficient than simple VO2. The guaranteed life for their fabricated film was about 16 years as indicated from the graph that satisfied the demand for practical applications. The VO2 converts into V2O5 oxide when heated at high temperature (annealing temperature) but the use of HfO2 as an antireflection agent protects it from the formation of oxides. So, by introducing the VO2/HfO2 film they got large luminous intensity ranging from 55.8% and sun modulation of 15.9%, and the film was more stable than it could be in the actual form for 16 years.
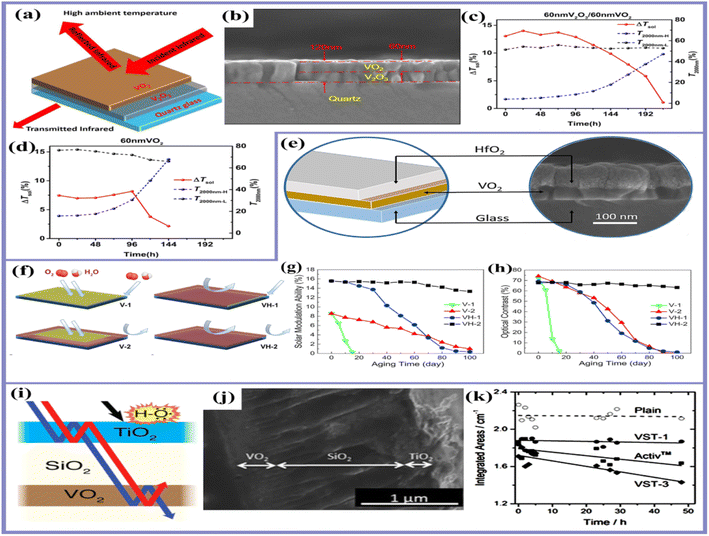 |
| Fig. 6 (a) Experimental flow chart for the synthesis of the V2O3/VO2 bi-layer structure and (b) SEM images of the V2O3/VO2 bi-layer structure. (c) Transmittance spectra of 60 nm VO2 at different times in hours. (d) 60 nm V2O3/VO2 at different times in hours. Reproduced with permission107 Copyright © 2018, Elsevier. (e and f) Flow chart for the whole process of VO2/HfO2 thin films by using the sputtering method and SEM images. (g) Graph of solar modulation ability versus aging time. (h) Durability of the fabricated films with the graph between optical contrast and aging time (days). Reproduced with permission108 Copyright © 2019, Elsevier. (i) Preparation of VO2/SiO2/TiO2 thin layers. (j) TEM images of VO2/SiO2/TiO2 thin layers. (k) Durability graph of the VO2/SiO2/TiO2 thin film. Reproduced with permission109 Copyright © 2016, American Chemical Society. | |
Further, the double layer of the thin film consisting of different materials on VO2 has also been investigated in terms of thermochromic properties. For example, M. J. Powell and coworkers prepared the VO2/SiO2/TiO2 thin layers.109 In the structure, the VO2 layer with SiO2 was over layered by TiO2 as shown in Fig. 6(i). Furthermore, Fig. 6(j) depicts the TEM of VO2/SiO2/TiO2 thin layers. The results indicated that by inserting these layers the transmission of visible light dramatically increased and the solar modulation of the material doubled. The scotch tape test was performed, which justified that the single VO2 layer could be easily delaminated but the multilayer VO2/silicon di-oxide/TiO2 demonstrated high adherence to glass substrates. Moreover, the deposited films were irradiated with broad band light sources. The values of transmittance were taken between the regions with direct contact between air with TiO2 and region of SiO2 (glass) in direct contact with the bottom layer of VO2. The modern window metrics Tlum and ΔTsol were measured for every layer of VO2. The results with an incoherent layer of SiO2 exhibited the lesser resonant peaks. For the sample of VST-1, the smart window was demonstrated by a model of transfer matrix showing the thickness of VO2, which enhanced and reached the value of 50 nm. This suggests that the VO2 film has a low density. The graph in Fig. 6(k) represents the durability of the VO2/SiO2/TiO2 thin film. Their new manufactured thin layer coating on VO2 resulted from an increase in solar modulation and visible light transmittance. SiO2/TiO2 layers on VO2 enhanced the mechanical properties of the smart windows. The solar modulation value acquired in the said experiment was 15.29%, which is the best value for VO2. This result about environmental durability, which has rarely been considered, is also so vital for practical application.
The bilayer coating strategy has delivered the most prominent results for fixing the oxidation problems of VO2 against humid environments.110–115 X. Zhou and coworkers developed a new strategy to fabricate a VO2 coating with long-term stability, low critical temperature (tc), significantly enhanced thermochromic performance and low fabrication cost by using the room temperature PVD deposition of amorphous VOx.116 It is followed by rapid thermal annealing (RTA) in air for less than 10 min. This process renders a fascinating VO2 nanocomposite structure within a V2O5 and V3O7 matrix encapsulated in a dense amorphous V2O5 overcoat, which is impossible to obtain by the usual PVD approach. Moreover, the sample could be exposed to the normal atmosphere for more than 2 years and remain intact. Accelerated results suggested that the sample can maintain the good thermochromic performance of Tlum (42.2%) and ΔTsol (14.6%) after 23 years. H. Zhou and coworkers prepared a multifunctional bilayer VO2/ZnO (VZ) film to improve the thermochromic properties of the VO2 film.117 The ZnO thin film acts as an anti-reflection layer to protect the film from corrosion. Furthermore, transmittance spectra shows a comparison graph between concentrations and immersion durations for simple VO2 and VO2/ZnO films. In comparison to the simple VO2 film, the VO2/ZnO film depicted a greater antireflection property. The ZnO behaves differently in weather conditions; in cold days it absorbs light to warm up the room, while in hot days it is reflective to IR light but transparent to visible light, displaying a luminous transmittance of 50.3% enhanced from 40.6% and solar modulation ability of 11.2% enhanced from 7.7%. J. Zhang and coworkers prepared a mesoporous silicon dioxide/VO2 double layer system.118 The film was fabricated to increase the refractive index from 1.243 to 1.354. The extinction coefficient Kv and refractive index nv were calculated by fitting the results which were obtained by the Drude Lorentz method. The graph showed that a refractive index lesser than 2 was obtained by the said fabrication method. The transmission of visible light was promoted by lowering the refractive index. The near infrared ray (NIR) switching and high visible transmittance were obtained by the fabricated film that demonstrated the existence of monoclinic VO2. The NIR switching ability was obtained to be 32.1% at 2000 nm, and the transmittance of visible light (Tvis, L) was obtained to be 69.8% in addition to a solar transmittance (ΔTsol) of 12.6%. The graph depicted the high crystallinity, which assured the good quality of synthesized VO2. The visible transmittance was 80% by using a refractive index of 1.299 that of SiO2. This work would be a milestone in energy-saving smart windows of VO2-based thermochromic coatings. S. Loquai and coworkers deposited a VO2 thin film to study the environmental stability.119 The SEM images exhibited an increase in surface roughness due to identical ΔT2500 nm behavior, and both radio-frequency magnetron sputtering (RFMS) and high-power impulse magnetron sputtering (HiPIMS) behaved almost similarly in critical temperature (Tc) performance as seen in Fig. 7(a) and (b). Moreover, a graph between transmittance and time (h) depicts that the as synthesized materials have better thermochromic characteristics, which can be easily observed in Fig. 7(c). But visible transmission of HiPIMS was lower due to its higher refractive index and high extinction coefficient of the film, which illustrates the loss per hour for both RFMS and HiPIMS film. The RFMS film had a 2.3% loss per hour, while HiPIMS acquired a 0.3% loss per hour, which exposed that HiPIMS deposition was better than RFMS deposition. The research says that HIPIMS deposition is significantly better for environmental stability as compared with RFMS due to its larger grain size, high density, and lower hydrogen intake. As compared to RFMS the HiPIMS film deposition has approximately three times longer lifespan. The suggested deposition method with the help of achieved results was considered attractive via HiPIMS.
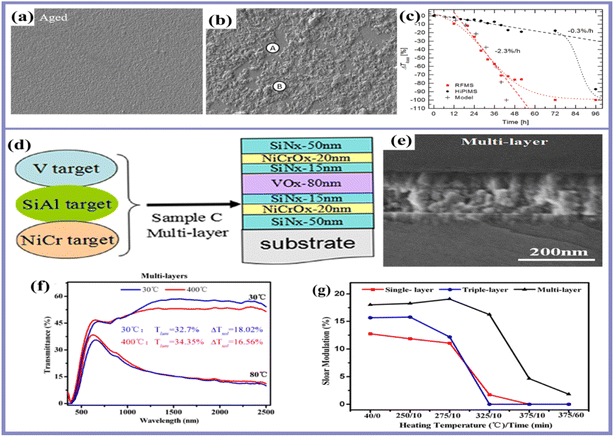 |
| Fig. 7 (a and b) SEM images of the deposited VO2 thin film and comparison study between RFMS and HiPIMS. (c) Transmittance spectra of the thin film. Reproduced with permission119 Copyright © 2016, Elsevier. (d) Preparation of films such as single layer as G/VOx, triple-layer as G/SiNx/VOx/SiNx, and multi-layer. (e) SEM images of the as synthesized films. (f) Optical transmittance spectra of the films. (g) Solar modulation of the triple layer. Reproduced with permission125 Copyright © 2017, Elsevier. | |
Further, for making a thin film, the multilayer strategy has also been investigated by choosing various materials (TiO2, NiCr, SiN, etc.) with VO2 and their thermochromic properties have been explored against weather resistance.120–124 For example, Y. Zhan and coworkers designed three VOx-based thin films having different layers, i.e., single, triple and multi-layered.125 The distributions of films were prepared, such as single layer as G/VOx, triple-layer as G/SiNx/VOx/SiNx, and multi-layer as G/SiNx/NiCrOx/SiNx/VOx/SiNx/NiCrOx/SiNx as observed in Fig. 7(d). The cross-sectional SEM images reveal the stress, grain size, and other defects present in the fabricated film. Fig. 7(e) shows the surface roughness of the multilayer. It is verified that the triple-layer and multilayer have a higher density of grain boundaries that is good for transmission from the semiconductor to metal. The optical transmittance of the three fabricated layers before and after thermal treatment at a low temperature of 30 °C and a high temperature of 60 °C was discussed. The luminous transmittance of all samples increased with increasing temperature as seen in Fig. 7(f) but above 325 °C the switching decreased greatly due to another phase in films. The vanadium pentoxide (V2O5) formed at 375 °C due to which thermochromic properties vanished at that temperature. In Fig. 7(g), a good optical switching in the triple layer was observed at 275 °C and it became zero level above 325 °C due to formation of VO2. Moreover, the thermal stability of the multi-layer thin film was excellent below 325 °C and came to zero at 375 °C, and the Tlum remained stable below 325 °C. The luminous transmittance got stable at a high temperature of 80 °C with a numerical value of 34.35% and a solar modulation of 16.56% also stabled as discussed in Fig. 7(f). As defining the results of this film, we can say that this fabricated film enhances the thermochromic property of VO2. As VO2 was reduced to V2O5 after being placed in air, this imperfection in VO2 was removed by making multilayers from this method. Hence, multilayers provided us a Tlum value of 34.35% and solar modulation ability of 18.02%. The above mentioned nanomaterials represent a promising candidate for energy-efficient thermochromic smart windows for enhancing weather resistance properties.
2.3.3 VO2-based thin film structures via a sandwich-strategy. The major advantages of sandwich composites over conventional materials are that sandwich composites (1) have a low overall density, a high strength-to-weight ratio, and a high stiffness-to-weight ratio; (2) are capable of providing good thermal and acoustic insulation; and (3) have uniform energy absorption capacity. To avoid contamination of VO2 in hybrids from environment and substrate, the sandwich-like structural modification is played an excellent role in stabilizing the hybrid against harsh environments. Sandwich-like structural adaptions have been tried by using different materials in the thin film strategy.126–135 For example, S. Long and coworkers designed SiNx/VO2(SV), VO2/SiNx (VS), and SiNx/VO2/SiNx (SVS) multilayers as shown in Fig. 8(a).136 The fabricated film played a better role in the advancement of solar modulation ability and luminous transmittance. The TEM images show the different size of thin layers as seen in Fig. 8(b). An experimental test was performed to observe the retention of luminous transmittance and solar modulation ability of the VO2 film in comparison with the fabricated SVS thin film. The luminous transmittance T2500 nm started to decrease after 1600 cycles for the simple VO2 film and retained only 20.1%. But in the case of the SVS film after passing 10
000 cycles, the luminous intensity decreased very slowly such that it retained 98.3% of its initial value. Moreover, it retained 88.1% of its initial value after passing 27
000 cycles, showing the best performance of the fabricated film. The experimental results revealed that the lifespan of the SVS film would be approximately 27 years, which was more than that of the simple VO2, which was just 4 years. To check out the durability of the SVS film, the film was kept at 60 °C and humidity of 90% as observed in Fig. 8(c). The simple VO2 film was damaged after 144 hours and completely depleted after 192 h (∼8 days). As compared to this, the SVS thin-film caught depletion after 480 h and completely depleted after 600 h (∼25 days) as shown in Fig. 8(d). This demonstrated that the fabricated film sustained 3 times more than VO2 films; solar modulation ability had a similar tendency, which depicted a luminous transmittance of 39.1% and solar modulation ability of 14.2% for SiNx/VO2/SiNx films. The SVS structure has more lifespan and durability as compared to a single VO2 layer. Further, by varying the materials in the layers of a sandwich structure, the hybrids were also investigated; T. Chang and coworkers arranged a sandwiched structure of Cr2O3/VO2/SiO2 (CVS) on a glass substrate as observed in Fig. 8(e).137 The bottom layer of Cr2O3 had improved the crystallinity of VO2 and increased the luminous transmittance of the structure. The upper layer of SiO2 acted as an anti-reflectant to light and also increased the environmental stability by providing a self-cleaning layer. The results of the as-prepared thin film have enhanced the durability of simple VO2 as well as the luminous intensity and solar transmittance. The solar modulation ability of the fabricated CVS thin film is 16.1%, which is more efficient, and the obtained luminous transmittance is 54%. The durability graphs of simple VO2, Cr2O3/VO2, and Cr2O3/VO2/SiO2 exhibited the credibility of fabricated CVS thin films over other ones. The graph presented that the CVS film retained its thermochromic properties after thousands of hours, while the simple VO2 had left over after a few hours only. The sample was kept at a high temperature of 60 °C and relative humidity of 90% for many hours. To endure the environmental damages, the VO2 has to undergo phase transition between metallic and semiconducting states once a day as can be seen in Fig. 7(f). The results of the fatigue test for different cycles showed that the single VO2 layer deteriorated after 4000 cycles and only 33% thermochromic properties were sustained, while the CVS thin film had constant thermochromic properties after 4000 cycles as observed in Fig. 7(g). It was clear that we can get a more reliable and durable product by using the above mentioned method. This thin film has two non-reflecting agents at both ends that enhance the solar modulation ability of the VO2, as well as luminous intensity. By using this film they achieved a luminous intensity of 54% and solar modulation ability of about 16.1%, enhancing the thermochromic properties of VO2. Furthermore, both layers of the sandwich structure were replaced by metals and thermochromic properties were explored. S. Long and coworkers prepared a sandwiched structure of WO3/VO2/WO3 that was deposited on VO2 to improve the transmittance of visible light and durability.138 The TEM image depicts that a 50 nm layer of VO2 was sandwiched between 30 nm layers of WO3 as clearly observed in Fig. 8(h), where WO3 acted as an anti-reflection (AR) agent at both the top and bottom sides. The sandwiched structure of VO2 with WO3 has many useful effects on the smart window. The luminescence of light, as well as transmittance for infrared light, was enhanced by using this thin layer. The luminescence (Tlum) was dramatically increased by a factor of 49% (from 37.2% to 55.4%), and also the hysteresis loop became sharper as the double layer of WO3 enhanced the luminous transmittance (Tlum) and it acted as a better-guarding layer for the thermo chromic property of VO2. The transition temperature for the single VO2 layer is 54.5 °C, which was reduced to 52 °C by inserting WO3 layers (WO3/VO2/WO3). Fig. 8(i) represents the durability of the prepared layer under different temperature and humidity conditions. The VO2 sample and thin-film WO3/VO2/WO3 have remained in 20 °C temperature and 90% humidity for 5, 10, 15, and 20 days. The results displayed that the thermo chromic property of a single layer of VO2 vanished after 20 days. When VO2 was coated with WO3 on the top and bottom side, the durability enhanced such that it remained unaffected after 20 days as shown in Fig. 8(j). So the obtained results have an excellent proof for the preparation of thin films such as WO3/VO2/WO3 which had better results than the single VO2, and enhanced the luminous transmittance of light with increasing the durability for smart window application. The results about VO2-based thin film structures via the sandwich-strategy showed the best performance for weather resistance in smart windows.
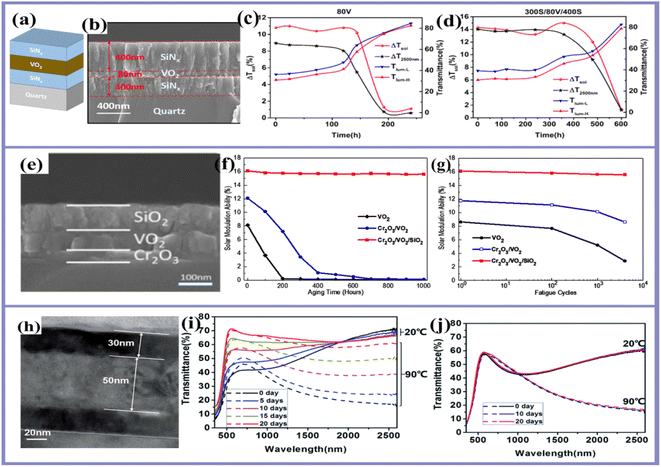 |
| Fig. 8 (a) Preparation of SiNx/VO2(SV), VO2/SiNx (VS), and SiNx/VO2/SiNx (SVS) multilayers by using the reactive magnetron sputtering method. (b) Field Emission Scanning Electron Microscopy (FE-SEM) of the multilayers. (c) Durability graph of the SVS film at 60 °C and humidity of 90%. (d) Comparison graph of the aging test. Reproduced with permission136 Copyright © 2018, Elsevier. (e) Preparation of the sandwiched structure of Cr2O3/VO2/SiO2 (CVS) on a glass substrate by using the magnetron sputtering process and SEM images. (f) Fatigue test of simple VO2 and structures. (g) Comparison graph of single VO2 layer and SVS layers. Reproduced with permission137 Copyright © 2017, Elsevier. (h) SEM image of the as prepared sandwiched structure of WO3/VO2/WO3 on VO2 by using the medium frequency reactive magnetron sputtering technique (MFRMST) and HRTEM images. (i) Durability graph of the prepared layer under different temperature and humidity conditions. (j) Aging test of the VO2 sample and thin-film WO3/VO2/WO3. Reproduced with permission138 Copyright © 2016, The Royal Society of Chemistry. | |
3. Summery/future outlook
VO2 depicts great potential as the next-generation smart glazing for architecture owing to its automatic thermochromic effect depending on ecological temperatures. The thermochromic characteristics of VO2 smart windows have been improved previously with tremendous efforts. However, the fundamental obstacle in the practical application of VO2 in smart windows is the poor stability of VO2 against an environment containing air moisture and other active elements. In order to establish carbon-neutral future, it is thus necessary to reduce the consumption of energy from non-renewable sources and decrease the energy demand through energy saving, environmentally friendly technologies. In this perspective, thermochromic smart windows, which can regulate the flow of energy during the day and provide lighting during the night, might reduce the demand for separate lighting systems and reduce the demand for energy for cooling. To overcome the effects emerging from unstable VO2 in an open environment, some attempts have been made through different strategies in our review. This review investigates the challenges and opportunities of VO2-based smart glazing that may be beneficial in accelerating the realization of real-world applications. This systematically summarises the recent progress in weather resistance that is currently in the stage of research and examines the quantitative parameters of smart window devices. Currently existing and still developing thermochromic technologies open up a very wide range of possibilities for their use in construction. This is the reason why broad research is necessary, and hopefully it will finally be able to identify technologies that have the potential of scaling, which seems to be one of the most important challenges of the weather resistance technology. Even though earlier research has overcome many of the other issues that impede practical applications, much development is still required before the technology becomes fully incorporated into our lives. The following are some suggestions for further study on VO2 based energy-efficient windows. Firstly, there are many different hues for colors, and colors can change throughout time. To obtain an aesthetic appeal, VO2 based coatings on smart windows must be changed from their unattractive brown-yellowish color. VO2 can produce a variety of colors and temperature-responsive color shifts when combined with other thermochromic or functional chemicals. More focus is needed to increase the longevity of VO2 hybrids, which could involve structural changes made with other types of materials. Secondly, material modification is an effective tool for creating new useful materials. Developing VO2 based film smart windows could be possible by combining VO2 films with additional functional materials that can provide new functions and/or enhance VO2 based films. Such kinds of functional materials ought to be used to improve the stability of VO hybrids for applications in smart windows. Lastly, the final product under consideration must be produced in large quantities at low cost and with high quality. The future development of thermochromic smart coatings will depend on the creation of straightforward but effective scaling up procedures for synthesis and film deposition. This capability necessitates proper changes in order to integrate various technologies into glass manufacturing lines effectively.
Author contributions
Muhammad Khuram Shahzad and Rana Zafar Abbas Manj have equal contributions and wrote the whole review manuscript including idea, Ghulam Abbas, Rashid Ali Laghari, Syed Sohail Akhtar, Muhammad Aslam Khan and Muhammad Bilal Tahir prepared all the figures and reviewed the manuscript, and Sami Znaidia and Meshal Alzaid revised the reviewer comments.
Conflicts of interest
No conflict of interest.
Acknowledgements
The author (Sami Znaidia) extends his appreciation to the Deanship of Scientific Research at King Khalid University for funding this work through Large Groups Project under grant number RGP.2/166/43.
References
- C. G. Granqvist, S. Green, G. A. Niklasson, N. R. Mlyuka, S. von Kræmer and P. Georén, Thin Solid Films, 2010, 518, 3046–3053 CrossRef.
- C. G. Granqvist, Thin Solid Films, 2016, 614, 90–96 CrossRef.
- C. G. Granqvist, Mater. Today: Proc., 2016, 3, S2–S11 Search PubMed.
- G. Wei, X. Fan, Y. Xiong, C. Lv, S. Li and X. Lin, Appl. Phys. Express, 2022, 15(4), 043002 CrossRef.
- C. G. Granqvist, P. C. Lansåker, N. R. Mlyuka, G. A. Niklasson and E. Avendaño, Sol. Energy Mater. Sol. Cells, 2009, 93, 2032–2039 CrossRef.
- S. K. Deb, Sol. Energy Mater. Sol. Cells, 2008, 92, 245–258 CrossRef.
- C. G. Granqvist, İ. Bayrak Pehlivan, Y. X. Ji, S. Y. Li and G. A. Niklasson, Thin Solid Films, 2014, 559, 2–8 CrossRef.
- J. Wang, L. Zhang, L. Yu, Z. Jiao, H. Xie, X. W. Lou and X. Wei Sun, Nat. Commun., 2014, 5, 4921 CrossRef PubMed.
- F. Zhang, X. Zhao, R. Li, S. He, X. Tan, J. Zhu and R. Ang, J. Mater. Chem. A, 2022 10.1039/D2TA06980F.
- X. Fan, G. Wei, X. Lin, X. Wang, Z. Si, X. Zhang and W. Zhao, Matter, 2020, 2(6), 1582–1590 CrossRef.
- C. G. Granqvist, Sol. Energy Mater. Sol. Cells, 2012, 99, 1–13 CrossRef.
- J. Zheng, S. Bao and P. Jin, Nano Energy, 2015, 11, 136–145 CrossRef.
- S. M. Babulanam, T. S. Eriksson, G. A. Niklasson and C. G. Granqvist, Sol. Energy Mater., 1987, 16, 347–363 CrossRef CAS.
- S. Wang, T. Jiang, Y. Meng, R. Yang, G. Tan and Y. Long, Science, 2021, 374(6574), 1501–1504 CrossRef PubMed.
- Y. Ke, Y. Li, L. Wu, S. Wang, R. Yang, J. Yin, G. Tan and Yi Long, ACS Energy Lett., 2022, 7(5), 1758–1763 CrossRef.
- S. Wang, Y. Zhou, T. Jiang, R. Yang, G. Tan and Y. Long, Nano Energy, 2021, 89, 106440 CrossRef.
- R. Binions, G. Hyett, C. Piccirillo and I. P. Parkin, J. Mater. Chem., 2007, 17, 4652–4660 RSC.
- P. Evans, M. E. Pemble, D. W. Sheel and H. M. Yates, J. Photochem. Photobiol., A, 2007, 189, 387–397 CrossRef CAS.
- J. Shi, S. Zhou, B. You and L. Wu, Sol. Energy Mater. Sol. Cells, 2007, 91, 1856–1862 CrossRef CAS.
- S. Li, C. Lv, X. Lin, G. Wei, Y. Xiong, W. Yang and W. Zhao, Appl. Phys. Lett., 2021, 119(12), 122401 CrossRef CAS.
- M. La, H. Zhou, N. Li, Y. Xin, R. Sha, S. Bao and P. Jin, Appl. Surf. Sci., 2017, 403, 23–28 CrossRef CAS.
- W. U. Rehman, H. Wang, R. Z. A. Manj, W. Luo and J. Yang, Small, 2021, 17, 1904508 CrossRef CAS.
- M. K. Shahzad, Y. Zhang, L. Cui, L. Liu, M. K. Butt and H. Li, RSC Adv., 2018, 8, 19362–19368 RSC.
- W.-L. Jang, Y.-M. Lu, C.-L. Chen, Y.-R. Lu, C.-L. Dong, P.-H. Hsieh, W.-S. Hwang, J.-L. Chen, J.-M. Chen, T.-S. Chan, J.-F. Lee and W.-C. Chou, Phys. Chem. Chem. Phys., 2014, 16, 4699–4708 RSC.
- C. Guo, Z. Zhang, Y. Wu, Y. Wang, G. Ma, J. Shi and Y. Zhao, Supercond. Sci. Technol., 2022, 35, 075014 CrossRef.
- V. Wittwer, M. Datz, J. Ell, A. Georg, W. Graf and G. Walze, Sol. Energy Mater. Sol. Cells, 2004, 84, 305–314 CrossRef.
- N. Li, Y. Li, G. Sun, Y. Ma, T. Chang, S. Ji, H. Yao, X. Cao, S. Bao and P. Jin, Chem.–Asian J., 2017, 12, 1709–1714 CrossRef PubMed.
- N. Li, Y. Li, Y. Zhou, W. Li, S. Ji, H. Yao, X. Cao and P. Jin, Sol. Energy Mater. Sol. Cells, 2017, 160, 116–125 CrossRef.
- N. Li, Y. Li, W. Li, S. Ji and P. Jin, J. Phys. Chem. C, 2016, 120, 3341–3349 CrossRef.
- Z. Chen, Y. Gao, L. Kang, J. Du, Z. Zhang, H. Luo, H. Miao and G. Tan, Sol. Energy Mater. Sol. Cells, 2011, 95, 2677–2684 CrossRef CAS.
- M. K. Dietrich, F. Kuhl, A. Polity and P. J. Klar, Appl. Phys. Lett., 2017, 110, 141907 CrossRef.
- J. Schläefer, C. Sol, T. Li, D. Malarde, M. Portnoi, T. J. Macdonald, S. K. Laney, M. J. Powell, I. Top, I. P. Parkin and I. Papakonstantinou, Sol. Energy Mater. Sol. Cells, 2019, 200, 109944 CrossRef.
- S. Saitzek, F. Guinneton, L. Sauques, K. Aguir and J.-R. Gavarri, Opt. Mater., 2007, 30, 407–415 CrossRef CAS.
- H. Zhou, X. Cao, M. Jiang, S. Bao and P. Jin, Laser Photonics Rev., 2014, 8, 617–625 CrossRef CAS.
- F. J. Morin, Phys. Rev. Lett., 1959, 3, 34–36 CrossRef CAS.
- Z. Zhang, Y. Gao, H. Luo, L. Kang, Z. Chen, J. Du, M. Kanehira, Y. Zhang and Z. L. Wang, Energy Environ. Sci., 2011, 4, 4290–4297 RSC.
- N. Li, Y. Li, G. Sun, Y. Zhou, S. Ji, H. Yao, X. Cao, S. Bao and P. Jin, Nanoscale, 2017, 9, 8298–8304 RSC.
- M. Tazawa, H. Asada, G. Xu, P. Jin and K. Yoshimura, MRS Online Proc. Libr., 2004, 785, 105 CrossRef.
- M. Li, S. Magdassi, Y. Gao and Y. Long, Small, 2017, 13, 1701147 CrossRef PubMed.
- M. E. A. Warwick and R. Binions, J. Mater. Chem. A, 2014, 2, 3275–3292 RSC.
- Y. Gao, H. Luo, Z. Zhang, L. Kang, Z. Chen, J. Du, M. Kanehira and C. Cao, Nano Energy, 2012, 1, 221–246 CrossRef CAS.
- Y. Gao, S. Wang, L. Kang, Z. Chen, J. Du, X. Liu, H. Luo and M. Kanehira, Energy Environ. Sci., 2012, 5, 8234–8237 RSC.
- G. Sun, H. Zhou, X. Cao, R. Li, M. Tazawa, M. Okada and P. Jin, ACS Appl. Mater. Interfaces, 2016, 8, 7054–7059 CrossRef.
- G. Sun, X. Cao, X. Li, S. Bao, N. Li, M. Liang, A. Gloter, H. Gu and P. Jin, Sol. Energy Mater. Sol. Cells, 2017, 161, 70–76 CrossRef.
- G. Sun, X. Cao, H. Zhou, S. Bao and P. Jin, Sol. Energy Mater. Sol. Cells, 2017, 159, 553–559 CrossRef.
- S. Li, Y. Li, M. Jiang, S. Ji, H. Luo, Y. Gao and P. Jin, ACS Appl. Mater. Interfaces, 2013, 5, 6453–6457 CrossRef CAS.
- Y. Li, S. Ji, Y. Gao, H. Luo, S. Li, M. Jiang, Y. Zhou, R. Li, B. Wang and P. Jin, CrystEngComm, 2013, 15, 8330–8336 RSC.
- J. Zhu, A. Huang, H. Ma, Y. Chen, S. Zhang, S. Ji, S. Bao and P. Jin, New J. Chem., 2017, 41, 830–835 RSC.
- Y. Ke, X. Wen, D. Zhao, R. Che, Q. Xiong and Y. Long, ACS Nano, 2017, 11, 7542–7551 CrossRef CAS.
- Y. Li, S. Ji, Y. Gao, H. Luo and P. Jin, ACS Appl. Mater. Interfaces, 2013, 5, 6603–6614 CrossRef CAS.
- H. Liu, D. Wan, A. Ishaq, L. Chen, B. Guo, S. Shi, H. Luo and Y. Gao, ACS Appl. Mater. Interfaces, 2016, 8, 7884–7890 CrossRef CAS PubMed.
- S.-D. Lan, C.-C. Cheng, C.-H. Huang and J.-K. Chen, Appl. Surf. Sci., 2015, 357, 2069–2076 CrossRef.
- M. Li, H. Wu, L. Zhong, H. Wang, Y. Luo and G. Li, J. Mater. Chem. C, 2016, 4, 1579–1583 RSC.
- J. Wan, Q. Ren, N. Wu and Y. Gao, J. Alloys Compd., 2016, 662, 621–627 CrossRef.
- Y. Li, P. Jiang, W. Xiang, F. Ran and W. Cao, J. Colloid Interface Sci., 2016, 462, 42–47 CrossRef PubMed.
- J. Zhang, T. Wang, W. Xu, X. Yang, X. Zuo, W. Cheng and C. Zhou, Nanotechnology, 2021, 32, 225402 CrossRef CAS.
- Y. Luo, M. Li, K. Li, C. Xu, S. Xu and G. Li, Sol. Energy Mater. Sol. Cells, 2019, 191, 258–265 CrossRef CAS.
- H. Ji, D. Liu, C. Zhang and H. Cheng, Sol. Energy Mater. Sol. Cells, 2018, 176, 1–8 CrossRef CAS.
- D. Wang, D. Guo, Z. Zhao, C. Ling, J. Li, S. Hong, Y. Zhao and H. Jin, Sol. Energy Mater. Sol. Cells, 2019, 200, 110031 CrossRef CAS.
- L. Xuanming, RSC Adv., 2016, 6, 47249–47257 RSC.
- M. Xygkis, E. Gagaoudakis, L. Zouridi, O. Markaki, E. Aperathitis, K. Chrissopoulou, G. Kiriakidis and V. Binas, Coatings, 2019, 9(3), 163 CrossRef.
- M. Saini, B. S. Dehiya and A. Umar, Ceram. Int., 2020, 46, 986–995 CrossRef CAS.
- S. Y. Li, G. A. Niklasson and C. G. Granqvist, J. Appl. Phys., 2011, 109, 113515 CrossRef.
- Z. Wen, Y. Ke, C. Feng, S. Fang, M. Sun, X. Liu and Y. Long, Adv. Mater. Interfaces, 2021, 8, 2001606 CrossRef CAS.
- Y. Chen, J. Zhu, H. Ma, L. Chen, R. Li and P. Jin, Sol. Energy Mater. Sol. Cells, 2019, 196, 124–130 CrossRef.
- Y. Chen, X. Zeng, J. Zhu, R. Li, H. Yao, X. Cao, S. Ji and P. Jin, ACS Appl. Mater. Interfaces, 2017, 9, 27784–27791 CrossRef.
- S. Zhao, Y. Tao, Y. Chen, Y. Zhou, R. Li, L. Xie, A. Huang, P. Jin and S. Ji, ACS Appl. Mater. Interfaces, 2019, 11, 10254–10261 CrossRef.
- Z. Qu, L. Yao, J. Li, J. He, J. Mi, S. Ma, S. Tang and L. Feng, ACS Appl. Mater. Interfaces, 2019, 11, 15960–15968 CrossRef.
- K. Tong, R. Li, J. Zhu, H. Yao, H. Zhou, X. Zeng, S. Ji and P. Jin, Ceram. Int., 2017, 43, 4055–4061 CrossRef CAS.
- Z. Fang, S. Tian, B. Li, Q. Liu, B. Liu, X. Zhao and G. Sankar, Appl. Surf. Sci., 2021, 540, 148414 CrossRef CAS.
- M. Salamati, G. Kamyabjou, M. Mohamadi, K. Taghizade and E. Kowsari, Constr. Build. Mater., 2019, 218, 477–482 CrossRef CAS.
- M. K. Shahzad, U. Farooq, A. Raza, G. Abbas, M. Ikram and Y. Zhang, RSC Adv., 2021, 11, 36569–36576 RSC.
- R. Zafar Abbas Manj, F. Zhang, W. Ur Rehman, W. Luo and J. Yang, Chem. Eng. J., 2020, 385, 123821 CrossRef CAS.
- Y. Gao, S. Wang, H. Luo, L. Dai, C. Cao, Y. Liu, Z. Chen and M. Kanehira, Energy Environ. Sci., 2012, 5, 6104–6110 RSC.
- J. Zhu, Y. Zhou, B. Wang, J. Zheng, S. Ji, H. Yao, H. Luo and P. Jin, ACS Appl. Mater. Interfaces, 2015, 7, 27796–27803 CrossRef CAS.
- Y. Chen, Z. Shao, Y. Yang, S. Zhao, Y. Tao, H. Yao, H. Luo, X. Cao and P. Jin, ACS Appl. Mater. Interfaces, 2019, 11, 41229–41237 CrossRef CAS.
- L. Mao and C. Liu, Mater. Res. Bull., 2008, 43, 1384–1392 CrossRef CAS.
- P. Liu, K. Zhu, Y. Gao, Q. Wu, J. Liu, J. Qiu, Q. Gu and H. Zheng, CrystEngComm, 2013, 15, 2753–2760 RSC.
- S.-Y. Li, K. Namura, M. Suzuki, G. A. Niklasson and C. G. Granqvist, J. Appl. Phys., 2013, 114, 033516 CrossRef.
- K. C. Kam and A. K. Cheetham, Mater. Res. Bull., 2006, 41, 1015–1021 CrossRef CAS.
- A. Huang, Y. Zhou, Y. Li, S. Ji, H. Luo and P. Jin, J. Mater. Chem. A, 2013, 1, 12545–12552 RSC.
- W. Li, S. Ji, G. Sun, Y. Ma, H. Guo and P. Jin, New J. Chem., 2016, 40, 2592–2600 RSC.
- R. Li, S. Ji, Y. Li, Y. Gao, H. Luo and P. Jin, Mater. Lett., 2013, 110, 241–244 CrossRef.
- Y. Li, S. Ji, Y. Gao, H. Luo and M. Kanehira, Sci. Rep., 2013, 3, 1370 CrossRef PubMed.
- T. D. Vu, H. Xie, S. Wang, J. Hu, X. Zeng and Y. Long, Mater. Today Energy, 2022, 26, 100978 CrossRef.
- T. Chang, Y. Zhu, J. Huang, H. Luo, P. Jin and X. Cao, Sol. Energy Mater. Sol. Cells, 2021, 219, 110799 CrossRef CAS.
- H. Zhou, J. Li, Y. Xin, X. Cao, S. Bao and P. Jin, J. Mater. Chem. C, 2015, 3, 5089–5097 RSC.
- H. Kim, Y. Kim, T. Kim, A. R. Jang, H. Y. Jeong, S. H. Han, D. H. Yoon, H. S. Shin, D. J. Bae, K. S. Kim and W. S. Yang, Nanoscale, 2013, 5, 2632–2636 RSC.
- H. Li, H. Djaoued, J. Robichaud and Y. Djaoued, J. Mater. Chem. C, 2020, 8, 11572–11580 RSC.
- S. Li, Y. Li, K. Qian, S. Ji, H. Luo, Y. Gao and P. Jin, ACS Appl. Mater. Interfaces, 2014, 6, 9–13 CrossRef CAS.
- W. Li, S. Ji, K. Qian and P. Jin, J. Colloid Interface Sci., 2015, 456, 166–173 CrossRef CAS.
- J. Zhou, Y. Gao, Z. Zhang, H. Luo, C. Cao, Z. Chen, L. Dai and X. Liu, Sci. Rep., 2013, 3, 3029 CrossRef.
- G. Sun, X. Cao, X. Gao, S. Long, M. Liang and P. Jin, Appl. Phys. Lett., 2016, 109, 143903 CrossRef.
- M. Maaza, K. Bouziane, J. Maritz, D. S. McLachlan, R. Swanepool, J. M. Frigerio and M. Every, Opt. Mater., 2000, 15, 41–45 CrossRef CAS.
- H. Koo, H. You, K.-E. Ko, O. J. Kwon, S.-H. Chang and C. Park, Appl. Surf. Sci., 2013, 277, 237–241 CrossRef CAS.
- I. Takahashi, M. Hibino and T. Kudo, Jpn. J. Appl. Phys., 2001, 40, 1391–1395 CrossRef.
- L. Kang, Y. Gao and H. Luo, ACS Appl. Mater. Interfaces, 2009, 1, 2211–2218 CrossRef.
- M. Kumar, J. P. Singh, K. H. Chae, J. Park and H. H. Lee, Superlattices Microstruct., 2020, 137, 106335 CrossRef.
- B. Li, J. Liu, S. Tian, B. Liu, X. Yang, Z. Yu and X. Zhao, Ceram. Int., 2020, 46, 2758–2763 CrossRef.
- X. P. Zhao, S. A. Mofid, T. Gao, G. Tan, B. P. Jelle, X. B. Yin and R. G. Yang, Mater. Today Phys., 2020, 13, 100205 CrossRef.
- J. Sang, W. Zhu, Y. Feng, Y. Liu, J. Shang, J. Sun, L. Guo, Y. Zhang, S. Zhao, V. Chigrinov and D.-S. Seo, ACS Appl. Electron. Mater., 2021, 3, 4882–4890 CrossRef CAS.
- Z. Qu, L. Yao, S. Ma, J. Li, J. He, J. Mi, S. Tang and L. Feng, Sol. Energy Mater. Sol. Cells, 2019, 200, 109920 CrossRef CAS.
- X. Lv, Y. Cao, L. Yan, Y. Li and L. Song, Appl. Surf. Sci., 2017, 396, 214–220 CrossRef CAS.
- C. Nakamura, K. Manabe, M. Tenjimbayashi, Y. Tokura, K.-H. Kyung and S. Shiratori, ACS Appl. Mater. Interfaces, 2018, 10, 22731–22738 CrossRef CAS.
- L. Zhou, M. Hu, X. Song, X. Qiang and J. Liang, Appl. Phys. A: Mater. Sci. Process., 2018, 125, 19 CrossRef.
- X. Fan, G. Wei, X. Lin, X. Wang, Z. Si, X. Zhang and W. Zhao, Matter, 2020, 2(6), 1582–1592 CrossRef.
- S. Long, X. Cao, G. Sun, N. Li, T. Chang, Z. Shao and P. Jin, Appl. Surf. Sci., 2018, 441, 764–772 CrossRef CAS.
- T. Chang, X. Cao, N. Li, S. Long, Y. Zhu, J. Huang, H. Luo and P. Jin, Matter, 2019, 1, 734–744 CrossRef CAS.
- M. J. Powell, R. Quesada-Cabrera, A. Taylor, D. Teixeira, I. Papakonstantinou, R. G. Palgrave, G. Sankar and I. P. Parkin, Chem. Mater., 2016, 28, 1369–1376 CrossRef CAS.
- I. Top, R. Binions, C. Sol, I. Papakonstantinou, M. Holdynski, S. Gaiaschi and I. Abrahams, J. Mater. Chem. C, 2018, 6, 12555–12565 RSC.
- H. Koo, D. Shin, S.-H. Bae, K.-E. Ko, S.-H. Chang and C. Park, J. Mater. Eng. Perform., 2014, 23, 402–407 CrossRef CAS.
- Y. Ji, A. Mattsson, G. A. Niklasson, C. G. Granqvist and L. Österlund, Joule, 2019, 3, 2457–2471 CrossRef.
- Y. Dang, L. Zhao and J. Liu, Ceram. Int., 2020, 46, 9079–9085 CrossRef.
- M. K. Shahzad, Y. Zhang, A. Raza, M. Ikram, K. Qi, M. U. Khan, M. J. Aslam and A. Alhazaa, Nanoscale Res. Lett., 2019, 14, 270 CrossRef PubMed.
- I. Top, R. Binions, M. E. A. Warwick, C. W. Dunnill, M. Holdynski and I. Abrahams, J. Mater. Chem. C, 2018, 6, 4485–4493 RSC.
- X. Zhou, Y. Meng, T. D. Vu, D. Gu, Y. Jiang, Q. Mu, Y. Li, B. Yao, Z. Dong, Q. Liu and Y. Long, J. Mater. Chem. A, 2021, 9, 15618–15628 RSC.
- H. Zhou, J. Li, S. Bao, J. Li, X. Liu and P. Jin, Appl. Surf. Sci., 2016, 363, 532–542 CrossRef CAS.
- J. Zhang, J. Wang, C. Yang, H. Jia, X. Cui, S. Zhao and Y. Xu, Sol. Energy Mater. Sol. Cells, 2017, 162, 134–141 CrossRef CAS.
- S. Loquai, B. Baloukas, J. E. Klemberg-Sapieha and L. Martinu, Sol. Energy Mater. Sol. Cells, 2017, 160, 217–224 CrossRef CAS.
- N. R. Mlyuka, G. A. Niklasson and C. G. Granqvist, Sol. Energy Mater. Sol. Cells, 2009, 93, 1685–1687 CrossRef CAS.
- N. R. Mlyuka, G. A. Niklasson and C. G. Granqvist, Phys. Status Solidi A, 2009, 206, 2155–2160 CrossRef CAS.
- Y. Zhan, X. Xiao, Y. Lu, Z. Cao, S. Qi, C. Huan, C. Ye, H. Cheng, J. Shi, X. Xu and G. Xu, Surf. Interfaces, 2017, 9, 173–181 CrossRef CAS.
- M. J. Miller and J. Wang, Sol. Energy Mater. Sol. Cells, 2016, 154, 88–93 CrossRef.
- H. Liu, H. Song, H. Xie and G. Yin, Eur. Phys. J.: Appl. Phys., 2019, 88, 30301 CrossRef.
- Y. Zhan, X. Xiao, Y. Lu, Z. Cao, S. Qi, C. Huan, H. Cheng, J. Shi and G. Xu, Sol. Energy Mater. Sol. Cells, 2018, 174, 102–111 CrossRef.
- Y. Zhao, R. Xu, X. Zhang, X. Hu, R. J. Knize and Y. Lu, Energy Build., 2013, 66, 545–552 CrossRef.
- L. Kang, Y. Gao, Z. Chen, J. Du, Z. Zhang and H. Luo, Sol. Energy Mater. Sol. Cells, 2010, 94, 2078–2084 CrossRef CAS.
- H. Liu, H. Zong, L. Yan, D. Zhou, Y. Yin, G. Cao, L. Bian, C. Kang and M. Li, Infrared Phys. Technol., 2021, 113, 103648 CrossRef CAS.
- S. Li, C. Lv, X. Lin, G. Wei, Y. Xiong, W. Yang and W. Zhao, Appl. Phys. Lett., 2021, 119(12), 122401 CrossRef CAS.
- L. Zhou, M. Hu, X. Song, P. Li, X. Qiang and J. Liang, Appl. Phys. A: Mater. Sci. Process., 2018, 124, 505 CrossRef.
- H. Zong, D. Zhou, L. Yan, H. Liu, J. Wu, Q. Hu, C. Kang and M. Li, Appl. Phys. A: Mater. Sci. Process., 2021, 127, 472 CrossRef CAS.
- C. Guo, Z. Zhang, Y. Wu, Y. Wang, G. Ma, J. Shi and Y. Zhao, Supercond. Sci. Technol., 2022, 35, 075014 CrossRef.
- Y. Chen, L. Fan, Q. Fang, W. Xu, S. Chen, G. Zan, H. Ren, L. Song and C. Zou, Nano Energy, 2017, 31, 144–151 CrossRef CAS.
- Q. He, Y. Wang, Y. Zhou, M. He, R. Xu, S. Hu, W. Wu and R. Wang, Opt. Mater., 2019, 97, 109367 CrossRef CAS.
- H. Zong, D. Zhou, L. Yan, M. Li, W. Qiao, S. Zhang, Q. Hu and L. Bian, Ceram. Int., 2022, 48, 6734–6744 CrossRef CAS.
- S. Long, X. Cao, N. Li, Y. Xin, G. Sun, T. Chang, S. Bao and P. Jin, Sol. Energy Mater. Sol. Cells, 2019, 189, 138–148 CrossRef CAS.
- T. Chang, X. Cao, L. R. Dedon, S. Long, A. Huang, Z. Shao, N. Li, H. Luo and P. Jin, Nano Energy, 2018, 44, 256–264 CrossRef.
- S. Long, H. Zhou, S. Bao, Y. Xin, X. Cao and P. Jin, RSC Adv., 2016, 6, 106435–106442 RSC.
|
This journal is © The Royal Society of Chemistry 2022 |
Click here to see how this site uses Cookies. View our privacy policy here.