DOI:
10.1039/D0NH00332H
(Review Article)
Nanoscale Horiz., 2020,
5, 1188-1199
Recent progress on hollow array architectures and their applications in electrochemical energy storage
Received
2nd June 2020
, Accepted 29th June 2020
First published on 29th June 2020
Abstract
The structural design of electrode materials is one of the most important factors that determines the electrochemical performance of energy storage devices. In recent years, hollow micro-/nanoarray structures have been widely explored for energy applications due to their unique structural advantages. Their complex hollow interior and shell arrays enable fast ion diffusion/transport, provide abundant active sites and accommodate volume changes. Moreover, the direct contact of hollow arrays with substrates enhances the mechanical stability during long-term cycling. To date, huge progress has been achieved in the rational design of various hollow array architectures. However, a review on this topic has been rarely reported. Herein, the multifunctional merits and typical synthetic strategies for hollow array structures are analyzed in detail. Furthermore, their applications in electrochemical energy storage (such as supercapacitors and batteries) are summarized. The development and challenges of hollow arrays in terms of substrates, technique improvement and material innovation are discussed. Finally, their applications for energy storage and conversion are prospected.
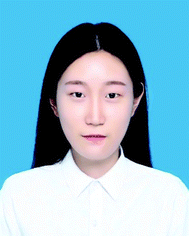
Chenyu Zhu
| Chenyu Zhu is currently pursuing her MS Degree at the Institute of Flexible Electronics, Northwestern Polytechnical University under the supervision of Prof. Cao Guan. She received BS Degree in the School of Materials Science and Engineering from Xi’an Shiyou University in 2018. Her research focuses on the design of nanomaterials for flexible energy storage. |
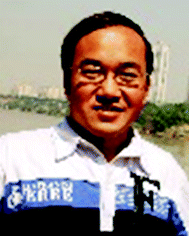
Huanwen Wang
| Huanwen Wang is currently a Professor at China University of Geosciences, Wuhan. He received his PhD from Tongji University in 2014, followed by Postdoc training at Nanyang Technological University, Singapore. His research interests focus on the electrochemical storage applications of advanced electrode materials (including supercapacitors, batteries and metal-ion capacitors). |

Cao Guan
| Cao Guan is a Professor and Vice Dean of Frontiers Science Center for Flexible Electronics, Northwestern Polytechnical University. He received his BS Degree from the School of Physics, Wuhan University, China in 2009 and completed his PhD study in the School of Physics and Mathematics Sciences, Nanyang Technological University, Singapore in 2013. He worked as a Research Fellow in the Department of Materials Science and Engineering, National University of Singapore from 2014–2018. His research focuses on the design of nanostructure materials for flexible energy storage and conversion. |
1. Introduction
Nowadays, with the rapid development of discontinuous and renewable resources such as wind energy, tidal energy and solar energy, the development of high-performance energy storage devices that can make full use of these sustainable energy resources has become an urgent research topic.1,2 In this regard, it is necessary to exploit high-performance and green electrode materials for energy storage, which are capable of a stable energy supply and long-time cycling.3–6 To date, various micro- and nano-architectures have been proposed to improve the energy-storage properties of materials.7–9 Among them, “hollow + array” nanostructures exhibit unique structural advantages, as illustrated in Fig. 1.
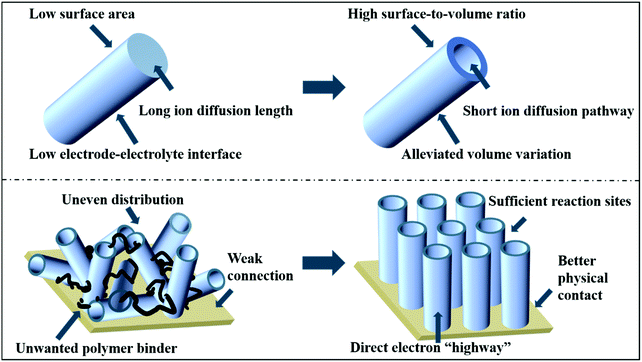 |
| Fig. 1 Schematic of the hollow nanoarray architectures in energy storage applications. | |
Based on the perspective of “hollow”, various hollow structures (such as hollow spheres, hollow polyhedrons, hollow tubes and hollow walls)10–12 have been reported with promising energy storage properties. Firstly, the hollow configuration enables a shorter ion diffusion pathway, thus enhancing the rate capability.13–15 Secondly, the formation of internal voids within shells can accommodate volume variation, thus ensuring good cycling stability during repeated long-term operation. Lastly, hollow structures provide a higher surface area than their solid counterparts, and thus contribute higher capacities/capacitances.16–19
Based on the perspective of “array”, the direct growth of array-structured electrodes has also attracted extensive attention with up-and-coming electrochemical properties. Firstly, array electrodes can increase specific capacities/capacitances with abundant reaction sites because they are free of any polymer binders (e.g., PVDF) or conductive additives (e.g., super P).20 Secondly, compared to conventional powder-formed electrodes, arrays have direct electric contact with substrates, which provides an electron “highway” for an enhanced rate capability. Lastly, array electrodes also have better physical contact with the substrate, and thus maintain good cycling stability.21–23 Taking Na3(VO)2(PO4)2F as an example, the array electrode exhibited much improved sodium storage properties compared to its powder counterpart because of its faster electron/ion transport and larger electrolyte–electrode contact area. In addition, VS2 arrays also demonstrated a higher revisable capacity and longer cycling life than that of VS2 powder during sodium-storage.24,25
Considering the above double merits, “hollow + array” materials are very attractive for application in advanced electrochemical energy storage devices,26–28 and accordingly various hollow arrays have been reported.29–31 Although some reviews summarized the progress of either hollow structures or array electrodes,32,33 the progress on hollow array structures has not been reviewed systematically. In this work, we mainly focus on the synthetic strategies and energy-storage applications of hollow nanoarray materials. Firstly, we analyze several commonly used synthetic methods of hollow arrays in detail and summarize the reaction mechanism briefly. Secondly, the principles and latest applications of hollow nanoarray materials in energy storage, especially in batteries and supercapacitors, are further discussed. Lastly, the development prospects and challenges of hollow array nanomaterials in the energy field are summarized.
2. Synthetic methods of hollow arrays
2.1. Synthesis for array precursors on substrates
Two-step methods are commonly used to synthesize hollow nanoarrays. The first step is to construct an ideal nanoarray (such as nanowire array, nanofiber array and nanotube array) on a substrate (such as nickel foam, carbon cloth and stainless steel plate),34,35 and the second step is to convert it into a hollow structure.36,37 The widely used methods for the synthesis of array precursors, as shown in Fig. 2, are summarized as follows.
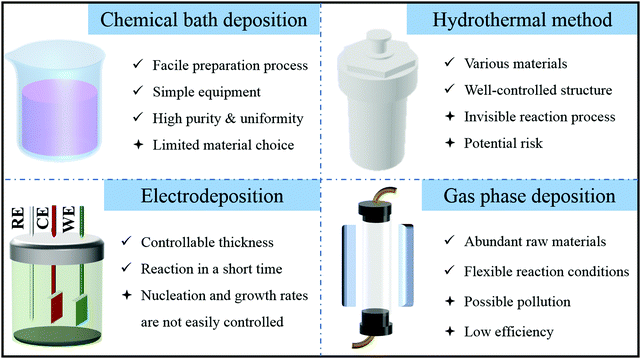 |
| Fig. 2 Schematic of the widely used methods for the synthesis of arrays. | |
(1) Chemical bath deposition (CBD).
The CBD process involves “oriented attachment” and “self-assembly” on the surface of a substrate. Specifically, the substrate is firstly immersed in a supersaturated solution containing available ions.38 When the solution is left to stand or stirred for a period of time, the ions in solution will react with each other, leading to nucleation, which minimizes the interfacial energy barrier of nanocrystals, and thus promotes the subsequent growth of nanoarrays.39–42 For example, in the synthetic process for ZnO microrod arrays via the CBD method,43 the seed layer of ZnO is firstly produced via hydrolysis and then deposited on the substrate surface, which guides the further growth of ZnO arrays on nickel foil. CBD is widely used for array growth because of its facile preparation process, mild reaction, simple equipment and good controllability. In addition, the obtained samples through CBD have high purity and good uniformity, which make CBD suitable for industrial production.44,45
(2) Hydrothermal method.
The hydrothermal process involves a heterogeneous reaction at high temperature and high pressure. In general, a solution with dissolved reactants is sealed in a polytetrafluoroethylene reactor, and the material recrystallizes on the substrate at a controlled reaction time and temperature.46 The hydrothermal method is typically used for some reactions that cannot not easily to occur at room temperature and normal pressure. In addition, the crystal structure, morphology and size of the products can be well-controlled by adjusting the time and temperature in the hydrothermal process.47,48 Because it has little particle agglomeration, this method is often used to synthesize transition metal hydroxide, oxide, sulfide and other metal compound arrays on metal and carbon substrates via in situ growth.33,49 However, the hydrothermal method requires high temperature and high pressure, and thus strongly depends on equipment and instruments, which may limit its wide practical application.
(3) Electrodeposition.
In the electrodeposition process, nanoarrays can be grown on the solid–liquid surface of an electrode via redox reaction through the migration of ions in the electrolyte under a certain voltage or current. It can be categorized into direct current electrodeposition, pulse electrodeposition (various current waveforms), jet electrodeposition (local high speed) and composite electrodeposition (co-deposition of nanoparticles and metal ions). Generally, the appearance of electrodeposited materials is accompanied by a gain and loss of ions at the electrode, which can be used to grow the desired array materials on the electrode surface.50–52 Through electrodeposition, nanoarrays can be prepared in a short time. The composition and morphology of arrays can be well adjusted by changing the electrolyte, current density, reaction time and other parameters.53,54 Although the nucleation and growth of the crystals are largely influenced by the diffusion rate between the electrode–electrolyte interface, the thickness of the obtained electrodes by electrodeposition is easier to control compared with other methods.55 Electrodeposition can be used for the fabrication of various arrayed metal oxides and metal compounds on conductive substrates, and it is also widely used for the growth of polymer arrays, where the morphology can be well controlled by the polymerization time.56,57
(4) Gas-phase deposition.
Gas-phase deposition, also named vapor deposition, utilizes physical or chemical reactions in the gas phase to deposit electrode materials on the surface of a substrate.58,59 According to the formation mechanism, the gas-phase method can be divided into physical vapor deposition (PVD) and chemical vapor deposition (CVD). In the PVD process, the source materials are directly evaporated/vaporized and deposited on the surface of the substrate. In CVD, materials are formed by vapor-phased chemical reactions of the source materials and then deposited on the substrate.60 These methods are commonly used to obtain solid deposits on the substrate by controlling the atmosphere and temperature.61 Despite these advantages, the accuracy of the morphology and structure of the product require the exact control of many parameters such as air flow, temperature and heating rate.
2.2. Formation mechanisms of hollow arrays
The template method is one of the most important processes to transform solid precursors into hollow nanomaterials,62 in which the original templates can be fully removed or partially dissolved. Many types of hollow nanoarrays (such as II–VI and III–V family compound materials) can be prepared via the template method.63 Various materials or chemicals can be selected as templates according to the different requirements of structure and applications. The coating sequence can be also adjusted to prepare nanomaterials with an ideal structure and particular performance.64 The commonly used template methods for the construction of hollow arrays can be divided into three types, including hard template method, soft template method and self-template method.
2.2.1. Hard template method.
In the hard template method, the template precursor is removed upon further reaction or at high temperature, while maintaining the original array skeleton of the outside materials.65,66 The commonly used hard templates include inorganic metals, molecular sieves and other rigid materials, such as polystyrene spheres, silicon spheres and metal oxide arrays.67 The hard template method guarantees high stability, good repeatability and controllable structures, and thus is widely used to prepare hollow nanomaterials.37,68,69 However, due to its simple pattern, the structural diversity of the templates is limited.
For example, SiO2 spheres are commonly used as hard templates to prepare hollow arrays. Hu at al. used self-assembled monolayer SiO2 templates to successfully fabricate a novel hollow spherical nanoarray composed of MoSe2 and MoS2 on flexible polyethylene terephthalate.66 As shown in Fig. 3a, monodispersed SiO2 spheres were assembled at the air/water interface and transferred to the SiO2/Si substrate. After MoSe2 and MoS2 were deposited via CVD, SiO2 was removed using 10% hydrofluoric acid (HF). Then hollow spherical shell arrays with spheres possessing a diameter of 450 nm and shell thickness of 10 nm were obtained (Fig. 3b–d). However, it should be noted that the SiO2 template is not suitable for the synthesis of active material arrays because it is easily etched by HF. Similarly, ZnO is another commonly-used hard template that can be easily etched by mild acid/alkaline solutions or high temperature annealing. For example, hollow carbon tube arrays with porous N-doped carbon bubbles can be uniformly synthesized using ZnO as a hard template, as shown in Fig. 3e.67 ZnO nanorod arrays were firstly grown on carbon cloth by low-temperature hydrothermal method and then the ZnO@ZIF-8 core–shell structures were prepared through ion exchange. After annealing in an H2 atmosphere, ZnO was removed and ZIF-8 was carbonized, and thus ZnO@ZIF-8 was successfully transformed into hollow carbon tube arrays (Fig. 3f and g).
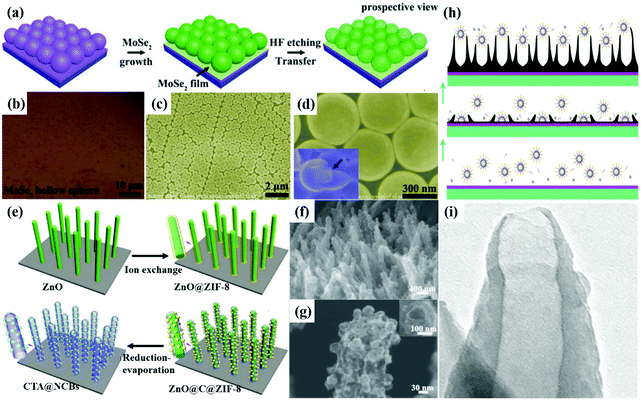 |
| Fig. 3 (a) Schematic of the synthetic process and (b)–(d) Optical and SEM images of MoSe2 hollow nanoshell sphere arrays.66 Copyright 2018, Wiley. (e) Schematic of the fabrication processes of 3D porous N-doped carbon bubbles connected by carbon tube arrays (CTAs@NCBs). (f)–(g) Hierarchical porous CTAs@NCBs-500 on flexible carbon fibers. Inset: Cross-section SEM image of the CTAs@NCBs-500 (reduction at 500 °C), confirming the tubular morphology of the final structures.67 Copyright 2018, Elsevier. (h) Schematic of the polymerization process of PPy films with hollow micro/nanohorn arrays. (i) SEM images of PPy hollow arrays.73 Copyright 2014, American Chemical Society. | |
2.2.2. Soft-template method.
In the soft template method, the templates are usually ordered polymers formed by emulsion droplets, surfactant molecules, and polymer micelles.70,71 When bubbles are dispersed in a liquid, a soft template will be formed at the gas–liquid interface, in which substances can diffuse in and out through the cavity wall. Micelles are usually spheres with their hydrophilic side facing outward, while vesicles are a double-layer multi-layer hollow spheres with their hydrophilic side facing the solvent. Different from rigid templates, the force to maintain soft templates is the weak interaction between or within the molecules, which may cause aggregation at the structure interface.71 Although soft templates have more choices with different morphologies compared with hard templates, the stability of their overall structure is poor and the structure of the product cannot be accurately controlled.71,72 Xu et al. proposed an electrodeposition method to fabricate hollow polypyrrole arrays, as shown in Fig. 3h and i. During the polymerization of pyrrole monomers, the formed micelles were used as soft templates for the construction of hollow nanoarray structures.73 The surface of the micelle was filled with surfactants and the interior was full of pyrrole monomer. The hydrophobic side of the surfactant was connected with pyrrole, and the hydrophilic groups were exposed in solution. The study also revealed that the structure of PPy nanoarrays can be influenced by the matrix/electrolyte interface, pH value and other factors.
2.2.3. Self-template method.
The self-template method is another effective way to obtain hollow structures, in which the template participates in physical or chemical reactions itself as a part of the shell material resulting in hollow nanoarrays.74,75 In the self-template method, arrayed templates are firstly formed, then several techniques such as ion exchange and selective etching can be adopted to transform them into hollow arrays, in which Ostwald ripening, the Kirkendall effect and other mechanisms are often involved.32,75,76 Compared with the former hard and soft template methods, the self-template method can avoid the overall template removal steps, and the shell uniformity can be better controlled with morphological or compositional transformation of the templates. The self-template method not only provides a framework of arrays, but also serves as a part of the shell or catalyst of the target products.33,77 The mechanisms commonly involved in self-templates to construct hollow arrays are follows.
(1) Kirkendall diffusion.
The method based on the Kirkendall effect is normally used in the self-template process. The Kirkendall effect is a classical phenomenon in metallurgy experiments, which occurs when the diffusion rates of two components are different. A typical example is when copper and brass are welded together, because the diffusion rate of zinc to copper is faster than that of copper to zinc at high temperature, the initial interface between them will move.77,78 On the macro level, this diffusion difference leads to vacancy defects, and then the agglomerated vacancies form holes and destroy the interface. In nanoscale materials, the Kirkendall effect can be fully utilized as an effective method to prepare hollow nanomaterials.79,80 In 2004, starting with uniform cobalt nanocrystals in solution, Yin et al. reported the Kirkendall effect of Co nanocrystals in oxidation and sulfidation at high temperature, and fabricated hollow CoO nanocrystals and cobalt sulfide nanospheres.78 Additionally, the Kirkendall effect has been widely used in the synthesis of various hollow nanoarrays for catalysis and energy storage.81,82
During the preparation of hollow arrays using the Kirkendall effect (Fig. 4a), the diffusion of the nuclear material is faster than that of the shell material, and thus atoms or ions from the nuclear material diffuse outwards preferentially. This enables the rapidly moving vacancies to flow near the interface, resulting in a hollow structure. When the diffusing vacancies become saturated due to the balance in the diffusion rate difference, they aggregate and form hollow nanocrystals with binary components.83–87 For example, Zheng et al. prepared binder-free solid Ni–Co arrays as precursors. During the sulfuration process, S2− released from the Na2S aqueous solution first reacted with Co2+ and Ni2+, forming a thin layer of NiCo2S4 on the surface to inhibit the direct reaction between the external S2− and the internal Ni–Co precursors. Since the outer diffusion rate of the metal ions were faster than that of S2−, the shell of NiCo2S4 was gradually formed until the core disappeared completely.86 Moosavifard et al. successfully prepared CuCo2S4 hollow nanoarrays through a two-step hydrothermal method. The CuCo nanoneedle array precursor was firstly grown on nickel foam, which was then transformed into a hollow nanoneedle through the reaction among urea, Co2+, Cu2+ and TAA.88 In another work, Co(OH)F nanowires (Fig. 4b and c) were prepared as both precursors and self-templates to obtain CoMoS4 hollow nanotube arrays on carbon cloth (CoMoS4 NTA/CC) (Fig. 4d and e) based on the Kirkendall effect between OH− and F− in Co(OH)F and MoS42−.87
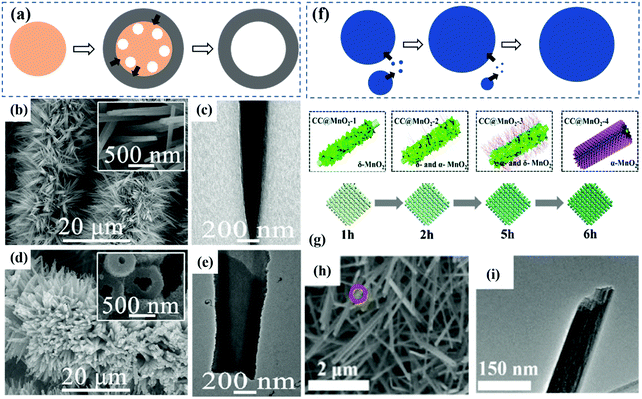 |
| Fig. 4 (a) Schematic of the Kirkendall effect. (b) SEM images and (c) TEM image of Co(OH)F nanowire arrays on carbon cloth (Co(OH)F NWA/CC). (d) SEM images and (d) TEM image of CoMoS4 NTA/CC.87 Copyright 2017, Wiley. (f) Schematic of Ostwald ripening. (g) Schematic of the synthetic procedures for various CC@MnO2 samples. (h) and (i) SEM image and TEM image of MnO2-4 (6 h reaction).91 Copyright 2019, Royal Society of Chemistry. | |
(2) Ostwald ripening.
Ostwald ripening is a typical phenomenon in solid solution, where with time, small crystals or particles dissolve and then deposit on the surface of large crystals or particles, as shown in Fig. 4f.89 The surface energy of large particles is smaller than that of small particles. Even for a particle molecule, its surface energy is higher than that of internal molecules. Therefore, driven by the thermodynamic process, the small second phases recrystallize and coarsen. Finally, in the solvent, the small particles shrink and become smaller, while the large particles continue to swallow up the small particles.90
To prepare internal hollow array structures, Ostwald ripening was used through the mass diffusion process from smaller particles to the outer larger crystals.79,91 Zheng et al. proposed the growth of one-dimensional α-MnO2 nanotube arrays on carbon cloth by Ostwald ripening (Fig. 4g).91 δ-MnO2 nanoflakes were initially formed and α-MnO2 nanotubes grew along the [001] axis on the front of the nanoflakes. Due to the high surface energy inside, δ-MnO2 nanoflakes started to dissolve from the inside to outside. When KMnO4 was completely consumed, the continuous growth of nanotubes and the dissolution of nanosheets resulted in hollow nanotubes (Fig. 4h and i).
(3) Ion exchange.
Ion exchange refers to the exchange between ions to obtain new compounds, which is an effective and facile strategy used to achieve hollow arrayed materials.92,93 As shown in Fig. 5a, in a typical ion exchange process, the internal diffusion, external diffusion and ion exchange reaction of solid–liquid mass transfer occur simultaneously, and the reaction rate is mainly determined by the mass transfer rate.94,95 For example (Fig. 5b–d), Co(CO3)0.5(OH)·0.11H2O arrays were transformed into hollow Co0.85Se nanorod arrays through the ion exchange reaction between carbonate and selenide.93 Further, Cai et al. prepared Zn–Co-ZIF nanoarrow arrays directly grown on Ni foam as a precursor. In the subsequent sulfurization process, thioacetamide was decomposed to produce H2S, which slowly dissolved the Ni foam, and the produced Ni2+ reacted with S2− to form Ni–Zn–Co–S hollow arrays.47 In addition, Co-based metal–organic framework (Co-MOF) arrays were converted to CoMoO4 hollow microplate arrays through ion exchange between MoO42− ions and BDC2−.96
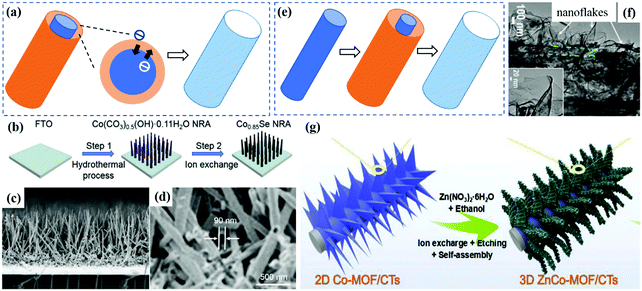 |
| Fig. 5 (a) Schematic of the ion exchange process. (b) Synthetic route for Co0.85Se nanorod arrays (Co0.85Se NRA). (c) Cross-sectional SEM image of the Co0.85Se NRA on FTO. (d) Magnified SEM image of the broken nanorods in (c).93 Copyright 2018, Elsevier. (e) Schematic of the selective etching process. (f) TEM images of 3D self-branched ZnCo2O4@N-doped carbon hollow nanowalls. (g) Fabrication of the carbon textile-supported 3D self-branched ZnCo2O4@N-doped carbon nanowall arrays.71 Copyright 2019, Elsevier. | |
(4) Selective chemical etching.
Selective chemical etching is also named the surface protection etching method, which uses chemical reagents (such as acid, alkali, and solvent) to selectively remove certain templates and surface residues.97 Since it is an effective method to remove sacrificial templates, selective chemical etching has been widely used in the preparation of hollow nanoarrays (Fig. 5e). Selective chemical etching requires a suitable chemical solvent,98 which should not only etch unnecessary chemicals, but also maintain the overall structure stability. As shown in Fig. 5g, Yang et al. prepared Co-MOF nanoarrays grown on a flexible fiber substrate as a precursor. Based on the reaction equation Zn2+ + 2H2O ↔ Zn(OH)2 + 2H+, the H+ formed by exchange with Zn2+ promoted the etching of Co-MOF. It also boosted the deposition of Co(OH)2 and Zn(OH)2 on the surface of MOF, which generated hollow arrays. Finally, the obtained 3D self-branched ZnCo2O4@N-doped carbon hollow nanoarrays could expose more active sites with continuous ion transport paths (Fig. 5f).71
3. Flexible applications in energy storage devices
3.1. Applications in supercapacitors
Compared with batteries, supercapacitors can provide faster charge and discharge rates, higher power density and longer cycling life. Based on these characteristics, supercapacitors have become one of the most promising energy storage devices for high-power electronic equipment.99–101 In recent decades, hollow nanoarrays have received much attention in supercapacitor applications due to their unique internal structure compared with their solid bulk or hollow particle counterparts.102–104 As reported, solid CoMoO4 nanoplate arrays on Ni foam showed a capacitance of 0.78 F cm−2 at a current density of 32 mA cm−2,105 while hollow microplate arrays of CoMoO4 on Ni foam exhibited a much larger areal capacitance of about 10 F cm−2 at 50 mA cm−2,96 clearly demonstrating the advantages of the hollow design. As another comparison, hierarchical CuCo2S4 hollow spheres (in powder form) illustrated a specific capacitance of 1137.5 F g−1 at 2 A g−1 and 964.2 F g−1 at 20 A g−1,106 while hierarchical CuCo2S4 hollow nanoneedle arrays (binder-free) delivered a much high capacitance of 1406 F g−1 at 60 A g−1,88 which also confirms the benefits with the array design.
Guan et al. reported the in situ growth of a two-dimensional cobalt-based MOF on flexible substrates as a precursor for hollow arrays.16 After ion exchange, etching and heat treatment, the obtained hollow NiCo2O4 array exhibited a capacitance of 1055.3 F g−1 (Fig. 6a). The assembled CC@NiCo2O4//CC@NC asymmetric supercapacitor delivered a capacitance of 89.7 F g−1 at a current density of 2 mA cm−2. When the power density was 2.9 kW kg−1, the maximum energy density reached 31.9 W h kg−1. It also showed 86.7% capacitance retention after 20
000 cycles, demonstrating good cycling stability (Fig. 6b and c). In another work, hollow NiCo2S4 nanoarrow arrays and hollow nanoneedle-like arrays were synthesized (Fig. 6d).86 These structures provided short a transmission path and good mechanical stability in the charging and discharging processes. Consequently, the NiCo2S4 hollow nanoarrow arrays (NiCo2S4-HNA) showed a high specific capacity (1297 F g−1 at 1 A g−1) and excellent cycle stability (92.4% capacitance retention after 10
000 cycles). As shown in Fig. 6e and f, the obtained NiCo2S4-HNA//AC hybrid supercapacitor with an output voltage of 1.6 V delivered a specific capacity of 191 C g−1 at 1 A g−1 and maintained a good stability of 84.9% after 10
000 cycles. Thus, the abovementioned reports demonstrate that hollow nanoarrays are advantageous for electrochemical reactions because of their larger surface area and abundant active sites compared to their disorganized counterparts.
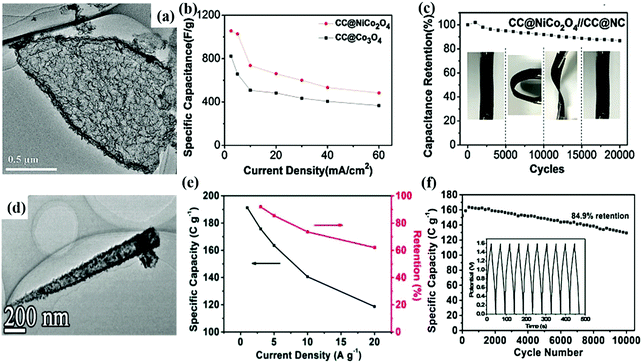 |
| Fig. 6 (a) TEM image of NiCo2O4 hollow nanostructure. (b) Plots of specific capacitance versus current density of CC@NiCo2O4 and CC@Co3O4. (c) Cycling test results of the full cell. Digital images of the full cell under the flat, bending, and twisting states during the test are inserted.16 Copyright 2017, Wiley. (d) TEM image of NiCo2S4-HNN. (e) Rate capability and capacity retention at various current densities ranging from 1 to 20 A g−1 of NiCo2S4-HNA//AC HSC. (f) Cycling stability of NiCo2S4-HNA//AC HSC at a current density of 5 A g−1 over 10 000 cycles (inset: GCD curves for the last 10 periods).86 Copyright 2018, Wiley. | |
3.2. Applications in batteries
Batteries are another commonly used energy storage devices arising from spontaneous redox reactions.107–109 Generally, batteries have one-magnitude higher energy density than that of supercapacitors,110 but their power density is normally lower than that of supercapacitors. Huge research efforts have been devoted to designing various batteries with high electrochemical performances.111 To evaluate the properties of a battery, typical indictors such as energy density, power density, charge and discharge platform, cycling life, safety and flexibility are mostly emphasised.112–114 It should be noted that the volumetric power/energy density are also important factors that determine advanced electrochemical energy storage performances for flexible and wearable devices.25,115
In this review, we mainly focus on the applications of hollow arrays in three types of batteries, including metal-ion batteries, metal–air batteries and Li–S batteries. Li-ion batteries have been dominant in the power supply market of advanced electric vehicles and portable electronic products due to their high energy density and long cycle life.116 Na metal anodes are used to assemble Na–air batteries and Na–S batteries because of their low cost, high theoretical capacity (1166 mA h g−1) and low redox potential (2.714 V vs. RHE).117,118 Rechargeable Zn–air batteries have a high theoretical specific energy density (up to 1086 W h kg−1), high safety, and may meet the increasing demand of mobile or portable devices.42 However, their poor cycling life is a bottleneck in most reported batteries. For Li-ion batteries, their capacity is gradually reduced with an increase in the number of cycles, which results in serious obstacles in their industrial application, and the same problem exists in Na batteries.117 For rechargeable metal–air batteries, they can store and release energy repeatedly through the oxygen evolution reaction (OER) and oxygen reduction reaction (ORR), but these processes are plagued by the huge overpotential caused by slow kinetics.119 The abovementioned problems can be partly relieved by the structural design of materials. Most powder-type electrode materials need to be mixed with conductive additives and polymer binders,32,120 which undoubtedly cause dead volume in the electrochemical reactions and result in high resistance and low capacity. In addition, negative electrode materials need to store metal ions through redox reactions in metal ion batteries, which have the challenge of volume expansion during long-time cycle, causing the collectors to be crushed and electrodes to fall off.116 Therefore, many researchers are inclined to investigate electrode materials directly grown on flexible current collectors with hollow array structures,16,117 which will effectively alleviate the volume strain and achieve good stability.111
Taking the Na-ion battery as an example, Wang et al. prepared hollow MoS2 nanoarrays with a diameter in the range of 400–500 nm on carbon cloth (Fig. 7a) via CVD.41 The design of hollow nanoarrays can greatly shorten the diffusion of ions and adapt to the volume change during cycling. As a self-supported anode, it showed a good sodium-storage performance and good cycling stability. The initial discharge capacity reached 989 mA h g−1 at 200 mA g−1, and the corresponding area capacity reached 1.978 mA h cm−2. After 200 cycles it showed 80% reversible capacity retention, as shown in Fig. 7b and c.
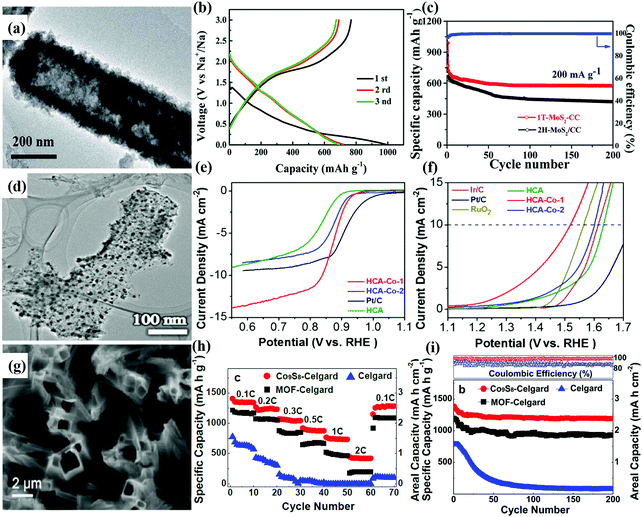 |
| Fig. 7 (a) TEM image of hollow 1T MoS2 arrays on carbon cloth (1T-MoS2/CC arrays). (b) Discharge/charge profiles of three initial cycles at 200 mA g−1. (c) Cycling performance and rate performance of 1T-MoS2/CC and 2H-MoS2/CC electrodes.41 Copyright 2018, Royal Society of Chemistry. (d) TEM image of HCA-Co-1 nanoarrays. (e) Oxygen reduction and (f) oxygen evolution polarization curves at a rotating speed of 1600 rpm for HCA-Co-1, HCA-Co-2 (with 0.2 mmol Co2+ solution) and Pt/C catalysts.121 Copyright 2019, Elsevier. (g) SEM image of Co9S8-Celgard after a slight scratch. (h) Rate performances at various cycling rates with Celgard, MOF-Celgard, and Co9S8-Celgard separators. (i) Cyclic stability of the cells with the Celgard, MOF-Celgard, and Co9S8-Celgard separators at a rate of C/10 for 200 cycles.122 Copyright 2018, Royal Society of Chemistry. | |
For metal–air batteries, Guan et al. constructed bimetallic Zn/Co ZIF on ZnO nanowires as a precursor and the ZnO template was removed by sintering in an inert atmosphere.121 As a result, a hollow N-doped carbon nanotube array embedded with confined cobalt nanoparticles (HCA-Co) was prepared (Fig. 7d). As shown in Fig. 7e and f, HCA-Co-1 (with 0.02 mmol Co2+ solution) illustrated a high half-wave potential of 0.87 V and an onset potential of 0.92 V. The assembled Al–air battery achieved a high open circuit voltage (1.966 V) and good mechanical flexibility.
To solve the problems of excessive volume expansion and lithium dendrite formation, Chen et al. also utilized hollow arrays as a separator.122 They synthesized hollow Co9S8 arrays on a commercial Celgard membrane as a barrier layer in an Li–S battery (Fig. 7g). The adsorption layer can accelerate the electron transport for the upper collecting fluid and improve the utilization rate of active substances. According to the electrochemical performances shown in Fig. 7h and i, the cell with the Co9S8-Celgard separator exhibited a discharge capacity of 428 mA h g−1 at a high cycling rate of 2C, while it recovered to 1270 mA h g−1 at 0.1C. The capacity of the Li–S battery with Co9S8 Celgard as a separator was 1190 mA h g−1 and the capacity retention was 85.9% after 200 cycles at a rate of 0.1C. This good stability is attributed to the highly regular hollow array of Co9S8, which confined polysulfides and inhibited the shuttle effect, thus improving the utilization of the active material sulfur.
4. Summary and perspectives
In summary, with the continuous development of nanotechnology and the application of nanomaterials in emerging industries, such as flexible energy storage devices, sensors, and catalysis, the rational design of advanced nanomaterials with good performances has become an increasingly important topic for researchers. Electrode materials with hollow + array structures have promising properties for electrochemical energy storage. Hollow arrays with sufficiently exposed active sites are favorable for fast redox reaction processes. In addition, faster charge transport, shorter ion pathway and more stable structure are important benefits for their wide applications in energy storage and conversion. Herein, starting from the advantages of hollow nanoarray materials, we generally summarized their preparation principles and synthetic methods, including the synthesis of array precursors and the transformation from a solid precursor to hollow structure. It can be seen that the synthesis of hollow array materials mainly depends on the template method, including hard template method, soft template method and self-template method. Then, taking the applications of supercapacitors and batteries (including Na-ion battery, Zn–air battery and Li–S battery) as examples, the research progress of hollow nanoarray materials in energy storage were described. Among them, hollow array materials are used as the electrodes of supercapacitors, and also used to modify the separator in batteries.
Presently, although the research of hollow nanoarrays in energy storage has achieved great progress, some problems still need to be solved. Some typical issues of future research work should be focused on the following aspects.
Firstly, some substrates such as metal foil and metal foam that support hollow nanoarrays are expensive and account for too much volume and/or weight, and their mechanical flexibility is also limited. Therefore, advanced substrates that are inexpensive, have good environmental adaptability and excellent mechanical stability are required to expand the advanced applications of hollow nanoarray materials. In addition, three-dimensional substrates offer a greater mass loading of active materials compared with 2D supports, which are favored for improved performances. However, the trap density in 3D substrates is relatively low since much inner void space is wasted. Furthermore, substrate-free electrodes that only contain hollow arrayed materials are very promising for high energy and power devices. Considering that the energy and power densities of energy storage devices are based on the whole mass/volume, substrate-free electrodes can further enhance their overall performance.
Secondly, in the preparation of hollow nanoarray materials, it is still a challenge to accurately control their morphology with effective methods. In the hard template method, the available rigid templates that can be easily removed in the last step are limited. The soft template can be recycled, but its structure is usually unstable and inefficient. A part of sacrificial template is always retained or transformed and becomes a part of product. Although this method can make full use of the desirable advantages of templates, it adds many uncontrollable factors to the final shape and influence the structure uniformity. Previous studies have reported a large number of three-dimensional self-synthesized hollow nanostructures, but these hollow arrays with random growth orientations and sites are difficult to be applied in flexible energy storage devices. Therefore, new synthetic methods and new templates with precise morphology control are key in the design and preparation of hollow nanoarray materials. In recent reports, 3D printing has been used for the design of hollow nanostructures for flexible energy storage devices, where the structures and materials can be well controlled with systematic and personalized design.123,124 When exploring new synthetic methods, the industrial scalability (i.e., suitability for large-scale production), environmental adaptability (i.e., safety and environmental protection) and cost should also be considered. Furthermore, the basic materials science and chemical reactions (such as the Kirkendall effect) should be deeply explored and applied in the rational design and precise control of hollow nanoarray structure.
Lastly, the design of hollow arrayed electrodes with a thick layer and high mass loading is another challenge. Aiming at better electrochemical performances, three-dimensional structures are constructed with a large specific surface area and sufficient active sites. For example, specially-designed three-dimensional hierarchical zinc hollow arrays may show great potential as anode materials for Zn–air batteries because they may effectively alleviate structural changes and prevent dendrite growth. However, for these three-dimensional active materials, the layer thickness often needs to be thin enough for high rate properties, which results in a low mass loading. Thus, it remains a challenge to obtain a thicker layer in electrodes with good flexibility and high rate capabilities.
Briefly, the research on the design, fabrication and application of hollow nanoarray structures has become a hot topic in nanotechnology and energy storage. The rapid development of hollow arrayed materials provides many opportunities for applications in batteries, supercapacitors, catalysis, etc., and will greatly promote the progress of energy storage and energy conversion technology.
Conflicts of interest
There are no conflicts to declare.
Acknowledgements
The authors acknowledge the financial supports by National Natural Science Foundation of China (Grant No. 51902265), Fundamental Research Funds for the Central Universities, Shaanxi Provincial Key R&D Program (No. 2020KWZ-001), and Project for graduate Innovation team of Northwestern Polytechnical University.
References
- H. Zhang, Q. Liu, Y. Fang, C. Teng, X. Liu, P. Fang, Y. Tong and X. Lu, Adv. Mater., 2019, 31, 1904948 CrossRef CAS PubMed.
- J. Park, J. C. Hwang, G. G. Kim and J. U. Park, InfoMat, 2019, 2, 33–56 CrossRef.
- H. Cheng, J. Meng, G. Wu and S. Chen, Angew. Chem., Int. Ed., 2019, 58, 17465–17473 CrossRef CAS PubMed.
- H. Wang, Y. Yang and L. Guo, Adv. Energy Mater., 2017, 7, 1601709 CrossRef.
- P. Zhang and X. W. Lou, Adv. Mater., 2019, 31, 1900281 CrossRef PubMed.
- H. Wang, D. Xu, G. Jia, Z. Mao, Y. Gong, B. He, R. Wang and H. J. Fan, Energy Storage Mater., 2020, 25, 114–123 CrossRef.
- X.-H. Xia, J.-P. Tu, X.-L. Wang, C.-D. Gu and X.-B. Zhao, Chem. Commun., 2011, 47, 5786–5788 RSC.
- Y. Sun and Y. Xia, Science, 2002, 298, 2176–2179 CrossRef CAS PubMed.
- C. Guan, X. Wang, Q. Zhang, Z. Fan, H. Zhang and H. J. Fan, Nano Lett., 2014, 14, 4852–4858 CrossRef CAS PubMed.
- S. Wang, W. Sun, D. Yang and F. Yang, Mater. Today Energy, 2019, 13, 50–55 CrossRef.
- D. Cao, W. Fan, W. Kang, Y. Wang, K. Sun, J. Zhao, Z. Xiao and D. Sun, Mater. Today Energy, 2019, 12, 53–61 CrossRef.
- H. Wang, G. Chen, X. Long, L. Chen, W. Tang, H. Wang, W. Ma, X. Liu and R. Ma, Mater. Today Energy, 2019, 14, 100354 CrossRef.
- Y. Tachibana, L. Vayssieres and J. R. Durrant, Nat. Photonics, 2012, 6, 511–518 CrossRef CAS.
- X. Han, G. Wang, L. Zhou and J. Hou, Chem. Commun., 2006, 212–214 RSC.
- A.-L. Wang, C.-L. Liang, X.-F. Lu, Y.-X. Tong and G.-R. Li, J. Mater. Chem. A, 2016, 4, 1923–1930 RSC.
- C. Guan, X. M. Liu, W. N. Ren, X. Li, C. W. Cheng and J. Wang, Adv. Energy Mater., 2017, 7, 1602391 CrossRef.
- M. Xiao, Z. Wang, M. Lyu, B. Luo, S. Wang, G. Liu, H. M. Cheng and L. Wang, Adv. Mater., 2019, 31, 1801369 CrossRef PubMed.
- E. Peer, A. Artzy-Schnirman, L. Gepstein and U. Sivan, ACS Nano, 2012, 6, 4940–4946 CrossRef CAS PubMed.
- H. Xu, B. Fei, G. Cai, Y. Ha, J. Liu, H. Jia, J. Zhang, M. Liu and R. Wu, Adv. Energy Mater., 2019, 10, 1902714 CrossRef.
- C. Liang, P. Zou, A. Nairan, Y. Zhang, J. Liu, K. Liu, S. Hu, F. Kang, H. J. Fan and C. Yang, Energy Environ. Sci., 2020, 13, 86–95 RSC.
- L. Xu, F.-T. Zhang, J.-H. Chen, X.-Z. Fu, R. Sun and C.-P. Wong, ACS Appl. Energy Mater., 2018, 1, 1210–1217 CrossRef CAS.
- H. Zhang, Y. Liu, H. Wu, W. Zhou, Z. Kou, S. J. Pennycook, J. Xie, C. Guan and J. Wang, J. Mater. Chem. A, 2018, 6, 20214–20223 RSC.
- Y. F. Zhang, L. Q. Li, H. Q. Su, W. Huang and X. C. Dong, J. Mater. Chem. A, 2015, 3, 43–59 RSC.
- D. M. Xu, H. W. Wang, R. Y. Qiu, Q. Wang, Z. F. Mao, Y. J. Jiang, R. Wang, B. B. He, Y. S. Gong, D. B. Li and X. L. Hu, Energy Storage Mater., 2020, 28, 91–100 CrossRef.
- Z. Mao, R. Wang, B. He, Y. Gong and H. Wang, Small, 2019, 15, 1902466 CrossRef PubMed.
- B. X. Yu, G. Ye, J. Chen and S. Q. Ma, Environ. Pollut., 2019, 253, 39–48 CrossRef CAS PubMed.
- K. Zhong, J. Q. Li, S. Van Cleuvenbergen and K. Clays, Nanoscale, 2016, 8, 15845–15849 RSC.
- Y. P. Zhu, T. Y. Ma, M. Jaroniec and S. Z. Qiao, Angew. Chem., Int. Ed., 2017, 56, 1324–1328 CrossRef CAS PubMed.
- H. N. Fan, S. L. Chen, X. H. Chen, Q. L. Tang, A. P. Hu, W. B. Luo, H. K. Liu and S. X. Dou, Adv. Funct. Mater., 2018, 28, 1805018 CrossRef.
- Z. H. Huang, Y. Song, D. Y. Feng, Z. Sun, X. Sun and X. X. Liu, ACS Nano, 2018, 12, 3557–3567 CrossRef CAS PubMed.
- W. Zhang, G. Z. Fan, H. Yi, G. Jia, Z. S. Li, C. W. Yuan, Y. F. Bai and D. G. Fu, Small, 2018, 14, 1703713 CrossRef PubMed.
- J. Wang, Y. Cui and D. Wang, Adv. Mater., 2019, 31, 1801993 CrossRef PubMed.
- H. H. Li and S. H. Yu, Adv. Mater., 2019, 31, 1803503 CrossRef.
- C. Guan, X. Liu, A. M. Elshahawy, H. Zhang, H. Wu, S. J. Pennycook and J. Wang, Nanoscale Horiz., 2017, 2, 342–348 RSC.
- R. Hou, M. Miao, Q. Wang, T. Yue, H. Liu, H. S. Park, K. Qi and B. Y. Xia, Adv. Energy Mater., 2019, 10, 1901892 CrossRef.
- S. Dang, Q.-L. Zhu and Q. Xu, Nat. Rev. Mater., 2017, 3, 17075 CrossRef.
- Z. X. Cai, Z. L. Wang, J. Kim and Y. Yamauchi, Adv. Mater., 2019, 31, 1804903 CrossRef.
- S. J. He, C. M. Zhang, C. Du, C. F. Cheng and W. Chen, J. Power Sources, 2019, 434, 226701 CrossRef CAS.
- Z. Mao, H. Wang, D. Chao, R. Wang, B. He, Y. Gong and H. Fan, Small, 2020, 16, 2001950 CrossRef PubMed.
- W. Xia, C. Qu, Z. Liang, B. Zhao, S. Dai, B. Qiu, Y. Jiao, Q. Zhang, X. Huang, W. Guo, D. Dang, R. Zou, D. Xia, Q. Xu and M. Liu, Nano Lett., 2017, 17, 2788–2795 CrossRef CAS PubMed.
- W. J. Tang, X. L. Wang, D. Xie, X. H. Xia, C. D. Gu and J. P. Tu, J. Mater. Chem. A, 2018, 6, 18318–18324 RSC.
- D. Ji, L. Fan, L. Tao, Y. Sun, M. Li, G. Yang, T. Q. Tran, S. Ramakrishna and S. Guo, Angew. Chem., Int. Ed., 2019, 58, 13840–13844 CrossRef CAS PubMed.
- M. Qi, Y. Zhong, M. Chen, Y. Dai and X. Xia, J. Alloys Compd., 2018, 750, 715–720 CrossRef CAS.
- V. K. Mariappan, K. Krishnamoorthy, P. Pazhamalai, S. Sahoo, S. S. Nardekar and S.-J. Kim, Nano Energy, 2019, 57, 307–316 CrossRef CAS.
- T. Wang, H. C. Chen, F. Yu, X. Zhao and H. Wang, Energy Storage Mater., 2019, 16, 545–573 CrossRef.
- X. Gao, H. Zhang, Q. Li, X. Yu, Z. Hong, X. Zhang, C. Liang and Z. Lin, Angew. Chem., Int. Ed., 2016, 55, 6290–6294 CrossRef CAS.
- Y. Huang, L. Quan, T. Liu, Q. Chen, D. Cai and H. Zhan, Nanoscale, 2018, 10, 14171–14181 RSC.
- S. Deng, Y. Zhong, Y. Zeng, Y. Wang, X. Wang, X. Lu, X. Xia and J. Tu, Adv. Sci., 2018, 5, 1700772 CrossRef PubMed.
- J. Lee, B. Llerena Zambrano, J. Woo, K. Yoon and T. Lee, Adv. Mater., 2020, 32, 1902532 CrossRef CAS PubMed.
- W. Zhang, X. Y. Yan, X. L. Tong, J. Yang, L. Miao, Y. Y. Sun and L. Y. Peng, Mater. Lett., 2016, 178, 120–123 CrossRef CAS.
- J. Chen, J. Xu, S. Zhou, N. Zhao and C.-P. Wong, Nano Energy, 2016, 21, 145–153 CrossRef CAS.
- S. Poongodi, P. S. Kumar, D. Mangalaraj, N. Ponpandian, P. Meena, Y. Masuda and C. Lee, J. Alloys Compd., 2017, 719, 71–81 CrossRef CAS.
- S. F. Zhuo, Y. S. Shi, L. M. Liu, R. Y. Li, L. Shi, D. H. Anjum, Y. Han and P. Wang, Nat. Commun., 2018, 9, 3132 CrossRef PubMed.
- Y. X. Zhao, S. J. Mu, W. F. Sun, Q. Z. Liu, Y. P. Li, Z. F. Yan, Z. Y. Huo and W. J. Liang, Nanoscale, 2016, 8, 19994–20000 RSC.
- Y. Liu, X. Li, W. Shen, Y. Dai, W. Kou, W. Zheng, X. Jiang and G. He, Small, 2019, 15, 1804737 CrossRef PubMed.
- C. Niu, J. Meng, X. Wang, C. Han, M. Yan, K. Zhao, X. Xu, W. Ren, Y. Zhao, L. Xu, Q. Zhang, D. Zhao and L. Mai, Nat. Commun., 2015, 6, 7402 CrossRef PubMed.
- Y. M. Chen, Z. Li and X. W. Lou, Angew. Chem., Int. Ed., 2015, 54, 10521–10524 CrossRef CAS PubMed.
- J. L. Liu, D. D. Zhu, Y. Zheng, A. Vasileff and S. Z. Qiao, ACS Catal., 2018, 8, 6707–6732 CrossRef CAS.
- Q. Zhang, W. S. Wang, J. Goebl and Y. D. Yin, Nano Today, 2009, 4, 494–507 CrossRef CAS.
- Y. Shao, M. F. El-Kady, J. Sun, Y. Li, Q. Zhang, M. Zhu, H. Wang, B. Dunn and R. B. Kaner, Chem. Rev., 2018, 118, 9233–9280 CrossRef CAS PubMed.
- H. Tabassum, R. Zou, A. Mahmood, Z. Liang, Q. Wang, H. Zhang, S. Gao, C. Qu, W. Guo and S. Guo, Adv. Mater., 2018, 30, 1705441 CrossRef PubMed.
- X. Xu, Q. Yang, N. Wattanatorn, C. Zhao, N. Chiang, S. J. Jonas and P. S. Weiss, ACS Nano, 2017, 11, 10384–10391 CrossRef CAS PubMed.
- D. Liu, J. Wan, G. Pang and Z. Tang, Adv. Mater., 2019, 31, 1803291 CrossRef PubMed.
- X. H. Xia, J. P. Tu, Y. J. Mai, X. L. Wang, C. D. Gu and X. B. Zhao, J. Mater. Chem., 2011, 21, 9319–9325 RSC.
- Y. Sun, H. Yang, X. Yu, H. Meng and X. Xu, RSC Adv., 2015, 5, 70387–70394 RSC.
- X. S. Chen, H. H. Yang, G. B. Liu, F. Gao, M. J. Dai, Y. X. Hu, H. Y. Chen, W. W. Cao, P. A. Hu and W. P. Hu, Adv. Funct. Mater., 2018, 28, 1705153 CrossRef.
- Z. Y. Tang, G. H. Zhang, H. Zhang, L. Wang, H. M. Shi, D. H. Wei and H. G. Duan, Energy Storage Mater., 2018, 10, 75–84 CrossRef.
- S. Shen, W. Zhong, X. Huang, Y. Lin and T. Wang, Materials, 2019, 12, 1193 CrossRef CAS PubMed.
- F. Li, R. C. Xu, Y. M. Li, F. Liang, D. F. Zhang, W. F. Fu and X. J. Lv, Carbon, 2019, 145, 521–528 CrossRef CAS.
- Z. Liu, W. Zhao, P. Kumar, X. Li, Y. Al Wahedi, K. A. Mkhoyan, M. Tsapatsis and A. Stein, Angew. Chem., Int. Ed., 2018, 57, 15707–15711 CrossRef CAS PubMed.
- D. Z. Kong, Y. Wang, S. Z. Huang, J. P. Hu, Y. Von Lim, B. Liu, S. Fan, Y. M. Shi and H. Y. Yang, Energy Storage Mater., 2019, 23, 653–663 CrossRef.
- K. Kim, D. S. Park, H. M. Lu, W. Che, K. Kim, J. B. Lee and C. H. Ahn, J. Micromech. Microeng., 2004, 14, 597–603 CrossRef CAS.
- Y. Bai, Y. Xu, J. Wang, M. Gao and J. Wang, ACS Appl. Mater. Interfaces, 2014, 6, 4693–4704 CrossRef CAS PubMed.
- Y. P. Zhu, T. Y. Ma, M. Jaroniec and S. Z. Qiao, Angew. Chem., Int. Ed., 2017, 56, 1324–1328 CrossRef CAS PubMed.
- Z. Xue, P. Wang, A. Peng and T. Wang, Adv. Mater., 2019, 31, 1801441 CrossRef PubMed.
- V. P. Zhdanov, Phys. Rev. E, 2019, 99, 012132 CrossRef CAS PubMed.
- J. Feng and Y. Yin, Adv. Mater., 2019, 31, 1802349 CrossRef PubMed.
- Y. Yin, R. M. Rioux, C. K. Erdonmez, S. Hughes, G. A. Somorjai and A. P. Alivisatos, Science, 2004, 304, 711–714 CrossRef CAS PubMed.
- Y. Tang and M. Ouyang, Nat. Mater., 2007, 6, 754–759 CrossRef CAS PubMed.
- F. Lyu, Y. Bai, Z. Li, W. Xu, Q. Wang, J. Mao, L. Wang, X. Zhang and Y. Yin, Adv. Funct. Mater., 2017, 27, 1702324 CrossRef.
- W. Wen, J. C. Yao, H. Tan and J. M. Wu, J. Mater. Chem. A, 2019, 7, 21378–21385 RSC.
- L. Yu, J. F. Yang and X. W. Lou, Angew. Chem., Int. Ed., 2016, 55, 13422–13426 CrossRef CAS PubMed.
- H. J. Fan, U. Gosele and M. Zacharias, Small, 2007, 3, 1660–1671 CrossRef CAS PubMed.
- W. Wang, M. Dahl and Y. Yin, Chem. Mater., 2012, 25, 1179–1189 CrossRef.
- Y. Da, J. Liu, L. Zhou, X. Zhu, X. Chen and L. Fu, Adv. Mater., 2019, 31, 1802793 CrossRef PubMed.
- Y. Cui, J. Zhang, C. Jin, Y. Liu, W. Luo and W. Zheng, Small, 2019, 15, 1804318 Search PubMed.
- W. Wang, X. Ren, S. Hao, Z. Liu, F. Xie, Y. Yao, A. M. Asiri, L. Chen and X. Sun, Chem. – Eur. J., 2017, 23, 12718–12723 CrossRef CAS PubMed.
- S. E. Moosavifard, S. Fani and M. Rahmanian, Chem. Commun., 2016, 52, 4517–4520 RSC.
- Z. Liu, L. Wang, Y. F. Cheng, X. Cheng, B. Lin, L. Yue and S. Chen, ACS Appl. Nano Mater., 2018, 1, 997–1002 CrossRef CAS.
- E. Zhang, N. Fulik, G. P. Hao, H. Y. Zhang, K. Kaneko, L. Borchardt, E. Brunner and S. Kaskel, Angew. Chem., Int. Ed., 2019, 58, 13060–13065 CrossRef CAS PubMed.
- X. Li, L. Wang, W. You, L. Xing, L. Yang, X. Yu, J. Zhang, Y. Li and R. Che, Nanoscale, 2019, 11, 13269–13281 RSC.
- E. Hu, J. Ning, D. Zhao, C. Xu, Y. Lin, Y. Zhong, Z. Zhang, Y. Wang and Y. Hu, Small, 2018, 14, 1704233 CrossRef PubMed.
- Z. T. Jin, M. R. Zhang, M. Wang, C. Q. Feng and Z. S. Wang, J. Power Sources, 2018, 378, 475–482 CrossRef CAS.
- S. Tang, B. Zhu, X. Shi, J. Wu and X. Meng, Adv. Energy Mater., 2017, 7, 1601985 CrossRef.
- Y. Lu, L. Yu, M. Wu, Y. Wang and X. W. D. Lou, Adv. Mater., 2018, 30, 1702875 CrossRef PubMed.
- Q. Li, Y. L. Li, J. Zhao, S. H. Zhao, J. J. Zhou, C. Chen, K. Tao, R. Liu and L. Han, J. Power Sources, 2019, 430, 51–59 CrossRef CAS.
- X. G. Liang, R. T. Dong and J. C. Ho, Adv. Mater. Technol., 2019, 4, 1800541 CrossRef.
- N. Luo, Y. Huang, J. Liu, S. C. Chen, C. P. Wong and N. Zhao, Adv. Mater., 2017, 29, 1702675 CrossRef PubMed.
- S. L. Wang, Z. C. Huang, R. Li, X. Zheng, F. X. Lu and T. B. He, Electrochim. Acta, 2016, 204, 160–168 CrossRef CAS.
- R. Farzana, K. Hassan and V. Sahajwalla, Sci. Rep., 2019, 9, 8982 CrossRef PubMed.
- Z. H. Wang, L. Qie, L. X. Yuan, W. X. Zhang, X. L. Hu and Y. H. Huang, Carbon, 2013, 55, 328–334 CrossRef CAS.
- S. Sun, T. Zhai, C. Liang, S. V. Savilov and H. Xia, Nano Energy, 2018, 45, 390–397 CrossRef CAS.
- D. P. Dubal, N. R. Chodankar and S. Qiao, Small, 2019, 15, 1804104 CrossRef PubMed.
- Y. L. Wang, L. Cai and Y. N. Xia, Adv. Mater., 2005, 17, 473–477 CrossRef CAS.
- D. Guo, H. M. Zhang, X. Z. Yu, M. Zhang, P. Zhang, Q. H. Li and T. H. Wang, J. Mater. Chem. A, 2013, 1, 7247–7254 RSC.
- H. H. You, L. Zhang, Y. Z. Jiang, T. Y. Shao, M. Li and J. L. Gong, J. Mater. Chem. A, 2018, 6, 5265–5270 RSC.
- H.-F. Wang and Q. Xu, Matter, 2019, 1, 565–595 CrossRef.
- Y. Zhang, C. W. Wang, H. S. Hou, G. Q. Zou and X. B. Ji, Adv. Energy Mater., 2017, 7, 1600173 CrossRef.
- Z. Liu, J. Xu, D. Chen and G. Shen, Chem. Soc. Rev., 2015, 44, 161–192 RSC.
- Y. Zhang, C. W. Foster, C. E. Banks, L. D. Shao, H. S. Hou, G. Q. Zou, J. Chen, Z. D. Huang and X. B. Ji, Adv. Mater., 2016, 28, 9391–9399 CrossRef CAS PubMed.
- R. Luo, Q. Yu, Y. Lu, M. Zhang, T. Peng, H. Yan, X. Liu, J.-K. Kim and Y. Luo, Nanoscale Horiz., 2019, 4, 531–539 RSC.
- X. Wu, J. Dong, M. Qiu, Y. Li, Y. Zhang, H. Zhang and J. Zhang, Nanoscale Horiz., 2020, 5, 359–365 RSC.
- D. Chao, W. Zhou, C. Ye, Q. Zhang, Y. Chen, L. Gu, K. Davey and S. Z. Qiao, Angew. Chem., Int. Ed., 2019, 58, 7823–7828 CrossRef CAS PubMed.
- K. S. Yu, X. L. Pan, G. B. Zhang, X. B. Liao, X. B. Zhou, M. Y. Yan, L. Xu and L. Q. Mai, Adv. Energy Mater., 2018, 8, 1802369 CrossRef.
- Y. Li, H. Wang, L. Wang, Z. Mao, R. Wang, B. He, Y. Gong and X. Hu, Small, 2019, 15, 1804539 CrossRef PubMed.
- E. Wang, M. Chen, X. Guo, S. L. Chou, B. Zhong and S. X. Dou, Small Methods, 2019, 4, 1900163 CrossRef.
- L. Ye, M. Liao, T. Zhao, H. Sun, Y. Zhao, X. Sun, B. Wang and H. Peng, Angew. Chem., Int. Ed., 2019, 58, 17054–17060 CrossRef CAS PubMed.
- Y. Fang, X.-Y. Yu and X. W. Lou, Matter, 2019, 1, 90–114 CrossRef.
- X. Liu, Y. Yuan, J. Liu, B. Liu, X. Chen, J. Ding, X. Han, Y. Deng, C. Zhong and W. Hu, Nat. Commun., 2019, 10, 4767 CrossRef PubMed.
- H. Chen, M. Q. Wang, Y. Yu, H. Liu, S. Y. Lu, S. J. Bao and M. Xu, ACS Appl. Mater. Interfaces, 2017, 9, 35040–35047 CrossRef CAS PubMed.
- C. Y. Zhu, Y. Y. Ma, W. J. Zang, C. Guan, X. M. Liu, S. J. Pennycook, J. Wang and W. Huang, Chem. Eng. J., 2019, 369, 988–995 CrossRef CAS.
- J. R. He, Y. F. Chen and A. Manthiram, Energy Environ. Sci., 2018, 11, 2560–2568 RSC.
- Q. Zhang, F. Zhang, X. Xu, C. Zhou and D. Lin, ACS Nano, 2018, 12, 1096–1106 CrossRef CAS PubMed.
- P. Cheng, H. Mei, S. Zhou, K. G. Dassios and L. Cheng, J. Mater. Chem. A, 2019, 7, 4230–4258 RSC.
|
This journal is © The Royal Society of Chemistry 2020 |
Click here to see how this site uses Cookies. View our privacy policy here.