DOI:
10.1039/C9PY01036J
(Review Article)
Polym. Chem., 2019,
10, 6073-6090
Slow release fertilizer hydrogels: a review
Received
13th July 2019
, Accepted 16th October 2019
First published on 17th October 2019
Abstract
In agriculture, there are problems such as the high porosity of soils, high irrigation of water and low fertilizer retention. Therefore, materials with the ability to absorb a high amount of water and release it over a long period of time in combination with a fertilizer may be a possible solution. To meet these demands, slow release fertilizer hydrogels (SRFH) have been developed. SRFHs are a combination of a super absorbant hydrogel (SAH) and a fertilizer with both water retention and slow release properties. In this article, basic principles such as definitions, classifications and properties of SRFHs are critically investigated. Raw materials and preparation techniques of SRFHs are briefly described. In addition, recent studies on SRFHs are highlighted.
 Ros Azlinawati Ramli | Ros Azlinawati Ramli received her Ph.D degree from Universiti Teknologi Malaysia (UTM) in 2014. She was awarded a Ph.D. scholarship from the Ministry of Higher Education Malaysia (MOHE) and Best Student Doctor of Philosophy (Polymer Engineering) from UTM. Previously, she was a senior chemist at Synthomer R&D Asia. Currently, she is a senior lecturer in the Material Technology Program, Universiti Malaysia Pahang (UMP). Her research interests include emulsion polymerization and emulsion polymers, polymer composites, microgels for biomedical applications and hydrogels for agricultural applications. |
1. Introduction
Superabsorbent hydrogels (SAHs), also known as superabsorbent polymers (SAPs) are cross-linked polyelectrolyte polymeric materials that can absorb large amounts of water, and retain and release them slowly under osmotic pressure.1–4 Based on these properties, SAHs have been used in agricultural and horticultural areas to reduce irrigation frequency and improve the physical properties of soil.5 However, the application of SAHs in this area has encountered some problems, because most SAHs are based on fully synthetic polymers, which are expensive and unsuitable for saline-containing water and soils.6 SAHs also increase economic burden for farmers and do not significantly improve the crop yield if applied alone without fertilizer.7
In agricultural areas, the suitable distributions of water and fertilizer play important roles in maintaining soil fertility, improving harvest quality and increasing production yield. However, a significant amount of fertilizer and water is lost through volatilization and leaching, which increases agricultural costs and leads to environmental pollution.8–10 Therefore, finding a better technology to slow down the release of water and fertilizer is very important. Slow release fertilizers (SRF) or controlled release fertilizers (CRF) are fertilizers which release nutrients into the environment in a slow manner.11,12 There is no official differentiation between the term controlled release and slow release fertilizers.11 The Association of American Plant Food Control Officials (AAPFCO) has stated that SRF is a fertilizer that delays its nutrient availability for plant uptake and use after application.13
Nowadays, the combination of SAH and fertilizer is the newest trend in the research on hydrogels14–16 and there is a growing trend to regulate nutrients and water in one material.17 This combination produces slow release fertilizer hydrogels (SRFHs), mainly created to improve plant nutrition and reduce the environmental impact of conventional fertilizers, lessen evaporation losses and frequency of irrigation.18 SRFHs act by absorption of some water and nutrients, holding them tightly and releasing them slowly. This can be described as a “mini reservoir”, which supplies water and fertilizer for plants through osmotic pressure difference.19,20 As a result, plants can still access water and fertilizer over extended period of times, resulting in improved performance rates and growth.21 Combining SAHs with fertilizer via a blending and in situ polymerization method leads to a high release rate and “burst effect”.22 Fertilizer also decompose when exposed to acrylic acid, the monomer most widely used to prepare SAHs. Moreover, high ionic concentration originating from the dissolution of fertilizer inhibits the polymerization of monomer and reduces the water absorption of SAHs.23
Conventional fertilizer is chemically degradable, however most SRFH-based synthetic polymers such as poly(acrylic acid), poly(acrylamide) and copolymer are non-biodegradable, meaning that they contribute to environmental pollution. The half-life of hydrogels means that it takes five to seven years for them to degrade into carbon dioxide, ammonium and water.24 Consequently, the use of natural polymers in a slow release system for agriculture applications has become the focus of research due to their biodegradability, abundant/renewable resources and low cost.20,25,26 SAHs can be blended, coated or grafted with natural polymers, such as starch,27 chitosan,28 cellulose,29 oil palm empty fruit bunches,3,30 wheat bran31 and other materials to create new hydrogels.
A number of slow release fertilizers (SRF) have been commercialized over the past few decades. There are three types of SRF: matrix-type formulations make up the biggest category of SRFs due to their simple fabrication. The active content is dispersed in a matrix and diffuses through pores in the carrier phase.32 Coated fertilizers are the second major category of SRFs, in which a fertilizer core is surrounding by inert materials. The release of fertilizer nutrients is controlled by diffusion through a shell.33 The third major category of SRFs is chemically controlled release products, such as urea-formaldehyde and polyphosphates. The release of fertilizer is controlled by the degradation rate, which is affected by many factors, such as temperature, pH, ions, molecular weight of the polymer and microorganisms in the soil.32 This review focuses on the first and second major categories. Table 2 summarizes the materials that form SRFHs, and the classification and preparation methods of the SRFHs.
2. Classification
SRFHs can be classified depending on their material resources, into natural and synthetic polymers, and depending on the preparation methods used, into matrix and coated-types, as shown in Fig. 1. Natural polymers SRFHs can be divided into cellulose, chitosan, starch, alginate, etc. Synthetic polymer SRFHs can be divided into purely synthetic and combined synthetic-natural materials. Purely synthetic SRFHs are made from petroleum-based hydrophilic monomers and combined synthetic-natural SRFHs are made from synthetic and natural/inorganic materials.
 |
| Fig. 1 Classification of SRFHs according to different parameters. | |
2.1. Material resources of SRFHs
2.1.1. Natural SRFHs.
Natural polysaccharides such as chitosan, starch, cellulose, alginate, and lignin are well known examples of bio-renewable resources for environmentally friendly hydrogels.34 Currently, most of the commercially available SAHs are made of petroleum-based vinyl monomers, such as acrylic acid and acrylamide, thus they are very difficult to degrade and are not environmentally friendly. Due to the rise in environmental protection and green chemistry, biodegradability is taken into account when developing new materials.35 Therefore, the utilization of renewable biodegradable polymers has been given much attention due to their biodegradability and abundant resources.36
Cellulose is the most abundant biopolymer on Earth, obtained from renewable resources such as cotton,37 wheat straw,7,38,39 oil palm empty fruit bunches,30,40 wood, hemp and other plant-based materials.41 Chitosan (CS) is the second most abundant natural polysaccharide, a derivative obtained via the partial deacetylation of the N-acetyl group of chitin.42 It is a major constituent of the exoskeletons of crustaceans, such as shrimps and crabs.43 Chitosan has been used in many applications, including agriculture, due to its degradability, abundance in nature and nontoxicity.10 Starch is the most widely used polysaccharide in SAH production and has become the target of industrial and academic studies.44 It is the second most abundant biopolymer after cellulose and is present in cassava, maize and potato.45 The advantages of starch are that it is low cost, able to replace synthetic polymers, its plasticity, its ease of chemical modification and good mechanical properties.46
Leon et al. prepared hydrogels based on chitosan from the shells of waste seafood. The chitosan was modified by mild oxidation and grafting with itaconic acid, then loaded with urea of different concentrations. The urea release of chitosan hydrogels with a high amount of urea does not change over 24 to 96 h, meaning that they are suitable as SRFs.47 Senna and Botaro prepared a hydrogel from cellulose acetate crosslinked ethylenediaminetetraacetic dianhydride (HEDTA) by esterification crosslinking and loading with NPK (ammonium, phosphate and potassium) fertilizer. The HEDTA considerably reduces the leaching of NPK fertilizer compared to commercial fertilizer. 1.9% of ammonium, 1.6% of phosphate and 8.5% of potassium were leached out from HEDTA compared to commercial fertilizer, with values of 1.7%, 80% and 98%, respectively.48 Sabadini et al. prepared hydrogels with different gellan gum/chitosan (GG/CTS) ratios of 1
:
4, 1
:
3, 1
:
2, 1
:
1, 2
:
1, 3
:
1 and 4
:
1. The solutions were mixed and stirred vigorously to form the hydrogels and then loaded with monopotassium phosphate, KH2PO4 (MKP), fertilizer. In all of the samples, MKP was almost completely released in 8 h. The released amount is mainly influenced by MKP concentration rather than GG/CTS composition.49
2.1.2. Synthetic SRFHs.
2.1.2.1. Purely synthetic SRFHs.
Purely synthetic SRFHs are made from acrylamide (AAm), acrylic acid (AAc), or copolymers of AAm and AAc.8 Previously, research related to SRFHs focused on the optimization of the formulation and then release studies of fertilizers such as urea and NPK from purely synthetic SAHs. Thong et al. studied the controlled release of urea from polyacrylic acid SAHs using a mathematical model. Static release experiments showed that the degree of crosslinking and size of the hydrogel have significant effects on the release rate of urea.50 Liu et al. studied the slow release of nitrogen from P(AAc)/urea. The product showed good slow release properties: the nitrogen released did not exceed 80% after being incubated in water for 28 days.51 Teodorescu et al. studied the release properties of P(AAc)/NPK fertilizer in distilled water at room temperature. They found that the release rate of the fertilizer was lower for higher MBA/AAc ratios.52 Tyliszczak et al. studied the release of P(AAc) SAHs for phosphorus fertilizers and found that the release of P(AAc)/phosphorus fertilizer is related to the water absorption kinetics.53 Helaly et al. studied the release of urea from acrylamide/maleic acid (AAm/MA) and acrylic acid/maleic acid (AAc/MA) SAHs and found that the release of urea from both SAHs could be extended for up to four months and was faster for AAm/MA SAHs.54
2.1.2.2. Combined synthetic-natural SRFHs (organic–inorganic).
Combined synthetic-natural organic–inorganic SRFHs are made from synthetic polymers and inorganic materials. The organic components have good elasticity, low density, formability and toughness, while the inorganic constituents are hard, stiff and thermally stable.55 Even though hydrogels have advantages as fertilizer carriers, the end price of hydrogels in the market make them impractical for agriculture applications. To solve the problem of high cost, one strategy is to form hydrogels with inorganic materials such as clay minerals (attapulgite, montmorillonite, bentonite and kaolin) in high proportions, which reduces the final production cost and improves some properties of the hydrogels, such as swelling. In another alternative, inorganic nano fillers are added into the hydrogels, which not only reduces the final cost, but also improves the swelling, barrier, mechanical and thermal properties of the hydrogels.56 The presence of inorganic materials also improves the degradability of SRFHs, as reported by Liang and Liu and Xiang et al.24,57
Early research on organic–inorganic SRFHs was reported by Liang et al., who employed kaolin nanopowder in a poly(acrylic acid-co-acrylamide)/kaolin [P(AAc-co-AAm)/kaolin] composite hydrogel to act as a release carrier for urea fertilizer. Fig. 2 shows scanning electron microscope (SEM) images of the P(AAc-co-AAm)/kaolin composite hydrogel with (a) 10% kaolin with no kaolin aggregations and (b) 30% kaolin, where aggregation of kaolin has occurred. The pores and channels in the polymer matrix are blocked by the aggregation of kaolin particles, resulting in a decrease in the release of urea from the composite hydrogel upon an increase in the kaolin content. Other factors that affect urea release from P(AAc-co-AAm)/kaolin are ionic strength, AAm content, temperature and crosslinker. The diffusion coefficient of urea decreases upon an increase in ionic strength, increase in AAm content from 20 to 50%, and increase in crosslinker content from 0.5 to 2%, and increases upon an increase in temperature from 5 to 65 °C.24
 |
| Fig. 2 SEM images of composite hydrogels with (a) 10% kaolin showing no aggregation of kaolin and (b) 30% kaolin showing that aggregation of kaolin occurs. Reprinted with permission from ref. 24. Copyright (2007) John Wiley and Sons. | |
Bortolin et al. developed a new hydrogel nanocomposite using poly(acrylamide) (PAAm), montmorillonite (MMt) and polysaccharide methylcellulose (MC) for the slow release of fertilizers. The components show a synergistic effect with very high fertilizer loading in their structure. The best result for the controlled desorption of urea was for a hydrolyzed hydrogel containing 50% calcic MMt. This system demonstrated the best desorption results, releasing large amounts of nutrient 200 times slower than pure urea. Fig. 3 shows SEM images of the hydrolyzed hydrogel at 500× magnification, (a) shows a decrease in pore size upon the addition of 1
:
1 MMt or 50% hydrogel
:
50% MMt in weight and (b) 3
:
1 or 75% hydrogel
:
25% MMt.58
 |
| Fig. 3 SEM images of (a) hydrolyzed hydrogel (1 : 1) and (b) hydrolyzed hydrogel (3 : 1).58 Reprinted with permission from ref. 58. Copyright (2013) American Chemical Society. | |
Sarkar et al. prepared hydrogel composites for the controlled release of zinc using PAAm, cellulosic, zeolite and carboxymethyl cellulose (CMC). The zeolite hydrogel composite improved the water holding capacity of sandy soil and slowly released zinc, with 18.64–22.16% released on the thirtieth day compared to 30.92–40.48% for zeolite-free hydrogels.59 In 2014, Rashidzadeh prepared a hydrogel nanocomposite based on sodium alginate-g-poly (acrylic acid-co-acrylamide)/clinoptilolite (NaAlg-g-poly(AAc-co-AAm)/clin and studied its application for the slow release of fertilizer. Clinoptilolite zeolite was added to the pure hydrogel to form a hydrogel nanocomposite. The clinoptilolite functions as a physical crosslinking agent, resulting in a porous structure of the hydrogel nanocomposite and the controlled release of NPK fertilizer, where 54.23% had been released by the thirtieth day compared to 82% for a pure hydrogel.60
In another contribution, Rashidzadeh and Olad used MMt in a NaAlg-g-P(AAc-co-AAm) (Hyd) superabsorbent nanocomposite and found that the presence of MMt gave a high water absorbent capacity (WAC) and slowly released NPK fertilizer in soil. Hyd/MMT/NPK had released 68.34% of fertilizer by the thirtieth day compared to 73.1% by Hyd. The slower release is related to the highly porous structure of Hyd/MMT/NPK. Fig. 4(a) shows an SEM image of freeze-dried Hyd and (b) Hyd/MMT/NPK with a highly porous structure and NPK fertilizer is homogeneously deposited on to the walls of the pores of the Hyd/MMT. The presence of inorganic materials in hydrogels results in a porous structure that leads to the controlled release of fertilizer.61
 |
| Fig. 4 SEM micrographs of (a) Hyd and (b) Hyd/MMT/NPK. Reprinted with permission from ref. 61. Copyright (2014) Elsevier. | |
2.1.2.3. Combined synthetic-natural SRFHs (organic–organic).
Combined synthetic-natural organic–organic SRFHs are made from synthetic polymer and natural polymers/fibers. Natural polymers/fibers are blended/grafted with synthetic polymers to improve the properties of SAHs, such as biodegradability, mechanical properties and WAC. Natural polymers are abundant in nature and can also reduce the production costs of hydrogels and environmental pollution, producing natural polymer-biomass waste. A lot of research has been focused on grafting or blending hydrogels with natural polymers/fibers, such as wheat straw, starch, cellulose, jute, chitosan, and other materials to develop new hydrogels with good biodegradable properties. Normally, natural fibers from crop waste are burned or buried, causing environmental pollution and waste of resources.62 The synergistic effects between natural polymers/fibers and synthetic polymers lead to biodegradability, a reduction in cost, non-toxicity, increased water absorbency and plant growth performance.63 Most hydrogels are soft, weak, brittle and fracture at high strains compared to engineering materials. The strength of hydrogels is lower than elastomers with a similar crosslink density.64 Hydrogels can be copolymerized with other monomers or have added natural polymers/fibers to improve their strength. For example, the copolymerization of acrylamide (AAm) and cashew gum successfully produced a hydrogel with good mechanical properties.65
2.1.2.3.1. Natural polymer/fiber SRFHs.
Alharbi et al. prepared phosphorylated carboxymethyl starch-g-polyacrylamide (P-CMS-g-PAAm) to enhance phosphorus use efficiency. The CMS monophosphate was produced from the carboxymethylation and phosphorylation of starch maize. A release study showed that the cumulative release of phosphorus in samples containing CMS/phosphate in a ratio of 1
:
0.66 was about 87% on the thirtieth day.66 Zhong et al. prepared a SAP based on sulfonated corn starch/poly(acrylic acid)/phosphate rock (SCS/P(AAc)/PHR) for controlled-release fertilizers. The SCS was produced from a sulfonation process to be polymerized with polyacrylic acid and phosphate rock (PHR), a traditional fertilizer. The SCS can suspend and disperse the PHR well, and help the citric acid soluble phosphorus in PHR transform into water-soluble phosphorus, thus greatly improving the amount of phosphorus released.66 Bai et al. prepared cassava starch-g-(acrylic acid-co-methyl methacrylate) [(starch-g-(AAc-co-MMA)] as a carrier for carbendazim. Water absorbance (WA) affects the release profile significantly, with the release longevity reaching 240 h for 800 g g−1 of WA in deionized water. The solution pH influenced the release profiles and the lowest release rate occurred at the lowest pH.34 Pourjavadi et al. prepared novel (salep phosphate)-based hydrogels via graft copolymerization of acrylic acid (AAc) monomer onto salep phosphate backbones. Salep is a multi-component polysaccharide obtained from dried tubers of certain natural terrestrial orchids. The effect of phosphate content on the potential of carrying of potassium nitrate (KNO3) fertilizers was investigated. The results indicated that phosphorylation of salep greatly improves the equilibrium water absorbency, swelling rate and fertilizer release.67 Essawy et al. prepared superabsorbent hydrogels via the graft polymerization of acrylic acid from a chitosan-cellulose (CTS/CS)-g-P(AAc) hybrid. The release of NPK fertilizer in soil did not exceed 75% after 30 days.68 Li et al. prepared a novel wheat straw cellulose-grafted-poly(acrylic acid/polyvinyl alcohol) (WSCS-g-P(AAc)/PVA) hydrogel and studied the release of nitrogen and phosphorus (NP) fertilizer using different particle sizes of the product (10–20, 20–40, and 40–60 mesh). The results in Table 1 indicate that the fertilizer in a hydrogel with a smaller size is released faster than in larger sized materials; the total fertilizer release amount of the smaller sample (40–60 mesh) was also higher than those of the larger ones. This is due to the samples with a smaller size having both greater interstitial volume and interfacial area between the swollen gel and water.38
Table 1 Swelling kinetic parameters and diffusion coefficients of fertilizers for WSCS-g-P(AAc)/PVA/NP under different conditions. Reproduced with permission from ref. 38. Copyright (2016) Elsevier
Conditions |
|
Q
∞
(g g−1) |
K
is (g g−1 s−1) |
R
2
|
Diffusion coefficient (×10−5) |
Nitrogen (cm2 s−1) |
Phosphorus (cm2 s−1) |
Salt solutions |
NaCl |
123.92 |
0.3985 |
0.9973 |
4.47272 |
4.37805 |
KCl |
103.73 |
0.2124 |
0.9987 |
4.42555 |
4.31076 |
CaCl2 |
— |
— |
— |
1.73057 |
3.13461 |
Na2SO4 |
83.06 |
0.1518 |
0.9989 |
— |
— |
Particle size (mesh) |
10–20 |
183.15 |
0.3983 |
0.9914 |
1.21681 |
3.04834 |
20–40 |
228.83 |
0.5112 |
0.9849 |
1.33895 |
3.64364 |
40–60 |
243.31 |
0.5241 |
0.9996 |
3.2938 |
3.88832 |
NaCl concentration (mM) |
10 |
123.92 |
0.3985 |
0.9973 |
2.01071 |
4.88426 |
50 |
66.98 |
0.4116 |
0.9990 |
2.68261 |
5.30878 |
100 |
58.96 |
0.2259 |
0.9965 |
2.85624 |
6.98786 |
500 |
32.54 |
0.1077 |
0.9934 |
4.47272 |
8.48744 |
Table 2 Materials that form SRFHs, and the classification and preparation methods of SRFHs
SRFH |
Classification |
Preparation |
Ref. |
Method |
Technique |
P(AAc)-g-cotton/urea |
Organic–organic |
Matrix |
Two steps |
37
|
P(NVP)/urea – core, EC – inner, P(AAc-co-AAm)-outer |
Organic–organic |
Double coated |
|
8
|
NP-core, starch/P(AAc-co-AAm)-shell |
Organic–organic |
Single coated |
|
15
|
WS-g-P(AAc)/urea |
Organic–organic |
Matrix |
Two steps |
17
|
P(AAc-co-AAm)/kaolin |
Organic–inorganic |
Matrix |
Two steps |
24
|
OPEFB-g-P(AAc-co-AAm) |
Organic–organic |
Matrix |
Two steps, in situ |
30
|
UF/PAK-Core |
Organic–inorganic |
Single coated |
|
32
|
P(AAc-co-AM)/kaolin-shell |
Starch-g-(AAc-co-MMA)/carbendazim |
Organic–organic |
Matrix |
Two steps |
34
|
WSC-g-P(AAc)/PVA/NP |
Organic–organic |
Matrix |
In situ
|
38
|
P(AAc-co-AMPS)/WS/NH4+ |
Organic–organic |
Matrix |
Two steps |
39
|
Urea-core, EC-inner, starch/PAAm-outer |
Organic–organic |
Double coated |
|
132
|
P(AAc)/urea |
Purely synthetic |
Matrix |
Two steps |
50
|
P(AAc)/urea |
Purely synthetic |
Matrix |
In situ
|
51
|
P(AAc)/NPK |
Purely synthetic |
Matrix |
In situ
|
52
|
P(AAc)/phosphorus |
Purely synthetic |
Matrix |
In situ
|
53
|
PAAm/MA/urea |
Purely synthetic |
Matrix |
In situ
|
54
|
AAm/MA/urea |
P(AAc-co-AAm)/Kaolin/urea |
Organic–inorganic |
Matrix |
Two steps |
24
|
PAAm/MS/MMt/urea |
Organic–inorganic |
Matrix |
Two steps |
58
|
P(CMC-g-PAAm)/zeolite/Zn |
Organic–inorganic |
Matrix |
In situ
|
59
|
NaAlg-g-P(AAc-co-AAm)/clin/NPK |
Organic–inorganic |
Matrix |
Two steps |
60
|
NaAlg-g-P(AAc-co-AAm)/MMT/NPK |
Organic–inorganic |
Matrix |
In situ
|
61
|
P-CMS-g-PAM |
Organic–organic |
Matrix |
In situ
|
66
|
CTS/CS-g-P(AAc)/NPK |
Organic–organic |
Matrix |
Two steps |
68
|
PVA/CTS/potassium |
Organic–organic |
Matrix |
In situ
|
136
|
Salep-g-P(AAc)/KNO3 |
Organic–organic |
Matrix |
Two steps |
67
|
OPEFB-g-P(AAc-co-AAm)/urea |
Organic–organic |
Matrix |
Two steps |
30
|
OPEFB-g-P(AAc-co-AAm)/urea |
Organic–organic |
Matrix |
In situ
|
|
Urea-core, PS-inner, P(AAc)/urea-outer |
Purely synthetic |
Double coated |
|
84
|
NPK-core, PVA, CTS-inner, P(AAc-co-AAm)-outer |
Organic–organic |
Multi-coated |
|
85
|
Urea-core, EC-inner, starch/PAAm-outer |
Organic–organic |
Double coated |
|
45
|
Urea/APT/AGT-core, CMWS-g-P(AAc)/APT-outer |
Organic–organic |
Single coated |
|
94
|
GT/PAAm/MAA/urea |
Organic–organic |
Matrix |
Two steps |
106
|
SCMC/P(AAc)/PVP/silica/NPK |
Organic–inorganic |
Matrix |
In situ
|
109
|
Xanthan gum/P(AAc)/urea |
Organic–organic |
Matrix |
Two steps |
118
|
P(AAc)-g-OPEFB |
Organic–organic |
Matrix |
Two steps |
97 and 98
|
Urea/Apt-core, SA-inner |
Organic–organic |
Multi-coated |
|
122
|
NaAlg-g-P(AAc-co-AM)/HA-outer |
BC/P(AAc)/LF |
Organic–organic |
Matrix |
In situ
|
131
|
Starch-g-PAAm/urea |
Organic–organic |
Matrix |
Two steps |
132
|
In situ
|
NaAlg-g-P(AAc-co-AAm)/RHA |
Organic–organic |
Matrix |
In situ
|
134
|
LR-g-P(AAc)/MMT/urea |
Organic–inorganic |
Matrix |
In situ
|
135
|
Besides that, Liang et al. synthesized a wheat straw-g-poly(acrylic acid) [WS-g-P(AAc)] superabsorbent composite and submerged it with urea fertilizer to produce a SRFH. Fig. 5 shows the results of urea release from WS/PAA in (a) distilled water and (b) soil. The release of urea in water and soil show similar patterns, however the release rate in soil was slower. After 10 days, the release of urea from WS/PAA (B) was 78.5% compared to untreated urea (A) at almost 100%.17
 |
| Fig. 5 The release of urea (a) in distilled water from WS/PAA (b) in soil, where (A) is untreated urea and (B) is WS/PAA. Reprinted with permission ref. 17. Copyright (2009) Elsevier. | |
Xie et al. also used WS to develop a superabsorbent composite of poly(acrylic acid-co-2-acryloylamino-2-methyl-1-propanesulfonic acid)/wheat straw (PAAc-co-AMPS/WS). The introduction of 20 wt% WS into polymer networks gave the highest adsorption capacity of ammonium, NH4+, ions. Fig. 6 shows SEM images of (a) P(AAc-co-AMPS) and (b) P(AAc-co-AMPS)/WS containing 20 wt% of WS. P(AAc-co-AMPS)/WS has interconnected open channels that facilitate the movement of NH4+ ions to active adsorption sites (–COO−, –SO3−, and –CONH), allowing equilibrium to be reached in a short time. Slow release results of P(AAc-co-AMPS)/WS showed that 23.5% of nitrogen was released in soil within 24 h compared to untreated NH4Cl, at 98%. Besides that, P(AAc-co-AMPS)/WS contains –SO3H and –COOH groups, which react with OH− in soil to buffer soil alkalinity and acidity and provide the optimum pH for plant growth.39
 |
| Fig. 6 SEM images of (a) P(AAc-co-AMPS) and (b) P(AAc-co-AMPS)/WS superabsorbent composites containing 20 wt% WS. Reprinted with permission from ref. 39. Copyright (2013) American Chemical Society. | |
According to Laftah and Hashim, hydrogels containing natural fibers with higher cellulose content have better swelling properties than hydrogels with lower cellulose content and plain hydrogels.3 The introduction of natural polymers/fibers into hydrogels not only improves water absorbency, biodegradability, cost and mechanical properties, but also improves fertilizer efficiency. When water is absorbed into the SRFH matrix, the hydrogel containing nutrients expand. The release of nutrients might therefore be controlled by the chemistry of the hydrogel.69
3. Preparation methods of SRFHs
Different types of polymerization techniques can be used to synthesis SRFHs, such as solution polymerization or aqueous polymer solution,70 photopolymerization,71,72 suspension polymerization,73 reversible addition–fragmentation chain transfer (RAFT) polymerization74 and free radical polymerization.71,75,76 Fertilizer can be added into a hydrogel matrix using two methods; two-step and in situ techniques that involve fertilizer in liquid form.77 In a two step technique, dried hydrogel is immersed in liquid fertilizer and the swollen hydrogel is dried. This technique allows better control of SRFH formation but involves two drying stages.18,62 In the in situ technique, all materials including fertilizer are adding into the reaction mixture during polymerization where the fertilizer is entrapped within the hydrogel matrix.78,79 The in situ technique is costly and time consuming but involves only one drying stage. Both methods have advantages and disadvantages; the first technique allows better control of SRFH formation by eliminating side reactions from adding all materials together.80 In exchange, the method has more disadvantages than the second method as it requires many steps: (1) the synthesis of the hydrogel, (2) drying, (3) absorption of the fertilizer, and (4) drying. Besides that, the hydrogel must also have sufficient crosslinking to entrap fertilizer.81 The advantage of this technique lies in its simplification, since it requires only one drying step. From a technological perspective, it reduces drying costs and is less time consuming. However, the polymerization must be strictly controlled until completion to avoid unreacted materials and impurities that are very difficult to remove.52,77 At high temperature, urea is converted into biuret, which is toxic to plants.18,82
Another way to control fertilizer release is to coat the fertilizer, which involves the use of fertilizer in solid form. Solid fertilizer can be obtained through synthesis or the use of conventional fertilizers such as NPK and urea. The fertilizer as a core is coated using natural/synthetic polymers. The release of nutrients is controlled by diffusion through the polymer surface, which acts as a membrane.33,69 Double and multilayer coatings are applied to reduce the release rate via the formation of a compact structure and less porosity. However, this method leads to slow release properties of the fertilizers being achieved, but does not change the water retention properties.83 For slow release and water retention, the fertilizer needs to be coated with a SAH as the outer layer.5,45,84,85
3.1. Matrix-type SRFHs
Matrix-type SRFHs can be prepared using two preparation techniques, two-step (T1) and in situ techniques (T2). Rabat et al. prepared an oil palm empty fruit bunch-grafted-poly(acrylic acid-co-acrylamide) [OPEFB-g-P(AAc-co-AAm)] SRFH using T1 and T2 techniques. They found that SRFH T1 has irregular porous structures that facilitate the diffusion of water into the hydrogel. However, SRFH T2 is less porous, which limits the diffusion of water into the hydrogel, resulting in good slow release properties.30,86 In another contribution, Rabat et al. studied the nutrient shortage of an OPEFB-g-P(AAc-co-AAm) SRFH in rose balsam plants. Fig. 7 shows that SRFH T2 in soil enhanced the plant growth performance compared to SRFH T1. After 10 weeks, the rose balsam plant in SRFH T2 produced flowers faster than the plant in SRFH T1. The great growth of the rose balsam plant in the soil containing SRFH T2 may be due to it having better slow release properties than SRFH T1.86,87
 |
| Fig. 7 Plant growth performance of rose balsam plants in SRFHs prepared using two-step (T1) and in situ (T2) techniques after 10 weeks.86 | |
Zhang et al. prepared mulberry branch-g-poly(acrylic acid-co-acrylamide) [MB-g-P(AAc-co-AAm)] slow release urea fertilizer (SRUF) using a two-step (T1) technique. First, mulberry branches were cleaned and dried. After that, a MB-g-P(AAc-co-AAm) superabsorbent was synthesized by solution polymerization. Then, the dried superabsorbent was mixed with urea, sodium alginate and CaCl2 solution to form the SRUF. Fig. 8 shows a schematic of the preparation process of MB-g-P(AAc-co-AAm) SRUF.88
 |
| Fig. 8 Schematic of the preparation process of slow-release urea fertilizer (SRUF). Reprinted with permission ref. 88. Copyright (2014) American Chemical Society. | |
3.2. Coated-type SRFHs
Coated-type SRFHs are prepared by coating solid fertilizer with inert materials that can reduce dissolution rate. The dissolution rate is strongly dependent on the physical properties of the coating material, such as hydrophobicity/hydrophilicity and porosity.33 Various materials have been used as coating materials for SRF, such as polysulfone,33 polyvinyl chloride,89 polystyrene,84 polyethylene, polypropylene and acrylonitrile-butadiene styrene polymer.90,91 However, these coating materials are very difficult to degrade in soils and are thus very polluting.92 Therefore, biodegradable and environmentally friendly coating materials are expected to be used for coated-SRFHs.8 Studied show that the double-coated SRFH release rate is lower than that of single-coated SRFH due to the lower porosity of the hydrogel and compact structure of the coating. They also found out that the release rate of ammonium, NH4+, was three times faster using a hydrophilic coating. Thus, hydrophobic coating materials with lower porosity are required.8 The coating process involves coating a solid fertilizer using natural polymers in solution, such as starch,45 chitosan,93 polyvinylalcohol (PVA)85 or ethylcellulose (EC)8 and then polymerizing them with a hydrophilic monomer to form a SAH outer layer. In situ inverse suspension polymerization is typically used to form the SAH outer layer. However, this technique is tedious as it involves multiple steps, especially for multilayer-coated SRFHs.
Fig. 9 shows SEM images of a double–coated SRFH, where (a) shows the surface, coarseness and porosity and (b) shows a cross-section of the three-layer structure. The rough outer layer is poly(acrylic acid)/urea (PAAU), which endows the material with water retention properties. The compact middle layer is polystyrene (PS), which promotes slow release properties. When the core (urea granule) is dissolved using water, it must pass through two layers to release into soil, which results in good slow release properties.84
 |
| Fig. 9 SEM images of a double-coated SRFH, showing the (a) surface, and (b) a cross-section. Reprinted with permission from ref. 84. Copyright (2006) American Chemical Society. | |
Noppakundilograt et al. prepared a novel trilayer-coated NPK fertilizer hydrogel by coating poly(vinyl alcohol) (PVA) and chitosan (CTS) onto NPK granules, as shown in Fig. 10. At first, NPK granules were dipped in PVA and CTS solutions, followed by crosslinking of the CS layer via glutaraldehyde vapor deposition to form crosslinked-CTS. Finally, the formation of the P(AAc-co-AAm) outer layer was achieved via in situ inverse suspension polymerization. The results showed that the crosslinking of the CTS layer increases water penetration, while the increased number of coated layers increases the water dissolution time. The release rate was therefore controlled by the hydrogel structure.85
 |
| Fig. 10 PVA/CTS/P(AAc-co-AAm) trilayer-coated hydrogel synthesized using AAc : AAm in a 97 : 3 molar ratio. Reprinted with permission from ref. 85. Copyright (2014) John Wiley and Sons. | |
Qiao et al. developed a novel double-coated SRFH using ethyl cellulose (EC) as an inner coating and a starch-based superabsorbent polymer (starch-SAP) as an outer coating. A series of starch-SAP samples using starches from potato maize and cassava were synthesized using a twin-roll mixer. After that, EC and stearic acid were dissolved in ethanol and the solutions were sprayed on urea granules (2–3 mm in diameter) to coat them and form the first layer. Finally, the EC coated urea granules were added into a rotating pan and the starch-SAP outer layer was adhered to the fertilizer core by atomizing the EC solution. Fig. 11 shows a schematic diagram of the relationship between the slow release behavior of the double-coated SRFH and the starch-SAP characteristics. Nutrients were released from the coated-fertilizer in three stages: (i) water was imbibed into the starch-SAP and penetrated through the EC layer, (ii) nutrients in the urea core were dissolved by water, (iii) nutrients were delivered into soil by penetrating the double layers. The release behavior of fertilizer mainly depends on the characteristics of the starch-SAP layer. Potato-SAP has the smallest grid size, relatively loose fractal gels, the largest water absorbent capacity and lowest water diffusion rate, thus provides the best SRF properties.45
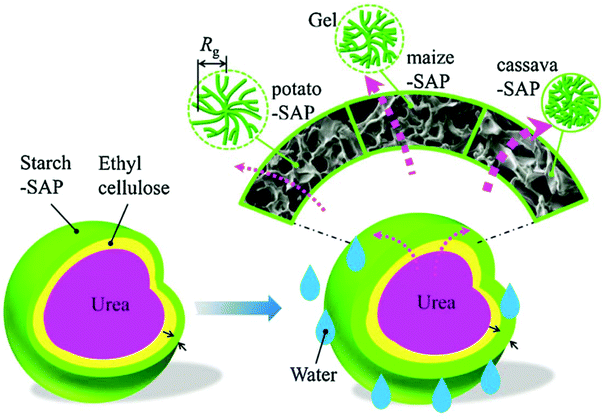 |
| Fig. 11 Schematic representation of the relationship between the slow release behavior of a double-coated SRFH and its starch-SAP characteristics. Reprinted with permission from ref. 45. Copyright (2016) Elsevier. | |
Ni et al. prepared a double-coated urea fertilizer with a three-layer structure. A poly(N-vinyl-pyrrolidone)/urea core (PCU) was first polymerized, then dried. The dried PCU was mixed with pure urea in a sodium alginate matrix to form granules. After that, the dried granules were immersed repeatedly in EC solution to form multiple coatings. Finally, the EC-coated urea granules were coated with a poly(acrylic acid-co-acrylamide) SAH by inverse suspension polymerization. Slow release experiments showed that the release of fertilizer was below 75% after being incubated in soil for 30 days.8 Jin et al. grafted corn starch onto a poly(acrylic acid-co-acrylamide) [starch/P(AAc-co-AAm)] hydrogel, then coated nitrogen and phosphorus (NP) fertilizer with the hydrogel. The rate of NP release as a function of time showed excellent slow release properties. As a comparison, 60% of the nitrogen was released from the starch/P(AAc-co-AAm) hydrogel in 30 days, while the untreated fertilizer had released 93% of its nitrogen by the second day. The elementary unit of the cellulose macromolecule is anhydro-glucose, which contains three hydroxyl groups (–OH). These OH groups form intramolecular and intermolecular hydrogen bonds. Thus, the WAC of SRFHs can also be enhanced by incorporating natural fibers into a system.15
Xie et al. prepared a coated-type SRFH with urea in an attapulgite and alginate matrix as a core, and a chemically modified wheat straw-g-poly(acrylic acid)/attapulgite (CMWS-g-P(AAc)/APT) SAH containing urea and borax as a shell layer. At first, the SAH was prepared via solution polymerization, followed by the synthesis of fertilizer granules using urea, raw attapulgite and alginate. Finally, the dried granules were coated with the SAH (less than 110 mesh) after being sprinkled with distilled water and then dried to form a coated-type SRFH product. When the weight ratio of CMWS to AAc was less than 5%, the water absorbency of the coated-SRFH increased. This SRFH possessed preferable slow release properties, with 91.6 wt% nitrogen and 95.4 wt% boron being released in soil after 10 days. Fig. 12 shows SEM images of (a) a cross-section of the coated-SRFH with a coarse and porous SAH shell layer increased surface area and (b) a swollen SAH shell with connected open channels.94
 |
| Fig. 12 SEM images of (a) a cross-section of a coated-SRFH and (b) a swollen SAP shell layer. Reprinted with permission from ref. 94. Copyright (2011) Elsevier. | |
4. SRFH properties
4.1. Slow release behaviour
Fertilizers contain nutrients for plants in the form of water soluble salts. These salts are highly water soluble and their dissolution causes them to leach away from plants root and be lost to the environment, resulting in environmental pollution.85 SRFHs are a key approach for improving fertilizer use efficiency by plants and alleviating environmental problems.95 In order to evaluate the validity of using SRFHs as materials for the slow release of soil nutrients, it is necessary to follow the release of these nutrients under similar conditions to that of the soil environment. The slow release behavior of SRFH in water and soil has been determined by methods as reported by a number of researchers.5,15,19,39,45,61,68 There is no standard method to investigate the amount of nutrient release from SRFHs. Basically, slow release of SRFHs in water can be determined by adding dry SRFHs into distilled water with no stirring. The quantity of fertilizer released from SRFHs in solution can be measured using UV-Vis spectroscopy or a conductivity meter at various time intervals. However, slow release from SRFHs in soil can be determined by placing SRFHs and soil into a column or leaching container and adding tap/distilled water periodically to keep the soil moist. Leached water is collected at various time intervals and the amount of fertilizer released is determined using the same method for release in water.
Islam et al. invented a lysimeter (35 cm in diameter, 150 cm in depth, with a surface area of 962.5 cm2) to study fertilizer release from SRFHs. Fig. 13 shows a schematic diagram of the lysimeter. The casing consists of a poly(vinyl chloride) (PVC) cylinder (35 cm internal diameter, 38 cm external diameter and 150 cm in depth). Leachate samples were collected for a period of time and the nutrient quantity was measured using UV-Vis spectroscopy. The cumulative volume of leachate was reduced by 16.3% at level 1 (15 kg ha−1) and 34.7% at level 2 (30 kg ha−1) with the application of a SAP. The application of a SAP considerably reduced the nitrate leaching to 28.3% at level 1 and 56.06% at level 2.96
 |
| Fig. 13 Schematic diagram of a lysimeter. Reprinted with permission from ref. 96. Copyright (2011) John Wiley and Sons. | |
Another invention was reported by Laftah and Hashim, the experimental device setup of which is illustrated in Fig. 14. A certain amount of SRFH was placed in one vessel and urea granules were placed in another to serve as a control. Both samples were covered by sandy soil to a depth of 100 mm. Tap water was allowed to flow slowly into the vessels until the water reached 50 mm from the soil surface. An outlet sample was taken at certain time intervals and the nutrient release was measured using UV-Vis spectroscopy.97,98 Generally, urea leaching loss rate (ULLR) from OPEFB-g-P(AAc) in sandy soil was lower than for a blank sample. OPEFB-g-P(AAc) loaded with 16.5% urea had a ULLR of 19% after 100 h, compared with a blank sample that had a ULLR of more than 90% after 20 h.40,97,98
 |
| Fig. 14 Experimental device setup for a fertilizer release study.40 | |
4.2. Water retention
The most important application of SRFHs in agriculture is the effectiveness of its water holding capacity or water retention properties in soil. This property is very important for proving SRFHs to be soil conditioners for improved soil quality and enhanced fertilizer efficiency.99 SRFHs with great water retention are always a better choice as soil conditioners than other materials because they are easy to apply. The distribution of SRFHs in soil also does not require any specific instrumentation.86 The water retention properties of a SRFH can be determined by adding a dried SRFH to soil and watering it.57,100–103 The SRFH in soil absorbs and retains the water, thus reducing the loss of water due to drainage and evaporation. When the soil dries, the SRFH releases the stored water under osmotic pressure difference.19,20 In can be concluded that when there is a reduction in soil moisture, water absorbed in the hydrogel is gradually released and absorbed by the plant. At the same time, nutrients entrapped in the hydrogel are also released along with the water. The swollen hydrogel can thus be described as a mini-reservoir for plants and this is superior property over other conventional fertilizers.7
Kumar et al. reported the synthesis of gum tragacanth (GT) with acrylamide (AAm) and a methacrylic acid (MAA) hydrogel interpenetrating polymer network (hydrogel-IPN) to improve water retention capacity and controlled release of fertilizer. The water retention capacity of sandy loam soil and clay soil with 1% hydrogel-IPN were increased by up to 7% and 8%, respectively, after 36 h. This is the best result compared to other hydrogels reported previously using the same system.104,105 The high water retention capacity of soil containing the hydrogel-IPN is due to the network structure of the hydrophilic monomer, AAm and MAA.106 This result suggests that adding hydrogel into soil can improve the water retention capacity of soil and reduce water evaporation. The same conclusion was also reached in other studies.7,104,107,108 Olad et al. compared the water retention behavior of a neat hydrogel, P(AAc)/NPK and modified hydrogel, P(AAc)/PVP/silica/NPK, in loamy sandy soil. Soil with P(AAc)/NPK was completely dry after 14 days, however soil containing P(AAc)/PVP/silica/NPK still retained 40% water after 30 days. This result demonstrates that the incorporation of polyvinylpyrrolidone (PVP) and silica nanoparticles in a hydrogel network enhances the water retention of a formulation.109
4.3. Biodegradability of SRFHs
Biodegradability can be defined as a chemical change in a polymer due to chemical breakdown processes facilitated by living organisms, usually microorganisms or enzymes.110 SRFHs can be degraded by incorporating portions of natural polymers such as gelatin, alginate, chitosan, xanthan gum and collagen that are likely to be enzymatically or hydrolytically attacked by microbes.111,112 There are two kinds of biodegradable hydrogels. The first group is made from natural polymers such as chitosan, hyaluranic, alginate, proteins, heparin, chondroitin sulfate and the other group is made from synthetic polymers.113 Despite great advances, these materials lacking mechanical and other important properties. Therefore, combinations of natural and synthetic polymers have been widely investigated for the development of hydrogels with improved properties.110 Soil burial testing is the most widely used method to study the biodegradability of hydrogels.114–116 The method is based on weight loss over time and can be carried out by adding a SRFH into soil.117,118 It is a traditional and standard method for degradation because of its similarity to the actual conditions of waste disposal. Hydrogels behaves like waste when they enter the humus cycle. The degradation rate of a hydrogel was found to be 5.9% under aerobic conditions over about 500 days, as reported by Huettermann et al. The rates of decomposition of crosslinked polyacrylate hydrogels were reported to be in the range of 1–9% per year. This is comparable to the rate that is observed throughout the breakdown of organic materials in forest environments.119
Kaith et al. prepared a biodegradable hydrogel based on xanthan gum and polyacrylic acid and carried out a biodegradability study based on a method reported by Sharma et al. The hydrogel was degraded by up to 78.3% within 70 days.118,120 Laftah and Hashim compared the degradation of a polymer hydrogel-grafted-oil palm empty fruit bunch, P(AAc)-g-OPEB, with a plain P(AAc) SAH. The amount of weight loss after 12 weeks for P(AAc)-g-OPEFB was 1.5% and 0.1% for the plain P(AAc) SAH.98 The high degradation of the PHG-g-OPEFB is due to the enzymatic degradation of the OPEFB cellulosic chains.121 Ni et al. studied the degradation of a multi-coated SRFH with different amounts of sodium alginate (NaAlg) and humic acid (HA). A sodium alginate-g-poly(acrylic acid-co-acrylamide)/humic acid (NaAlg-g-P(AAc-co-AAM)/HA) SAH was the outer coating. After 90 days, the percentage of degradation (PD %) for the sample with the highest NaAlg (7.5%) and HA (10%) content was 19.3%. The results showed that the PD increases with an increase in the amount of NaAlg and HA due to a large number of HA and NaAlg molecules approaching soil microorganisms.122
4.4. Plant growth performance
Most SRFH studies progress no further until their application in plants. This might be due to this research being relatively new and needing a lot of fundamental study before application is possible. This is in contrast with SAP studies, where a lot of research was carried out before applications were developed. However, there have been some reports on SRFH plant applications.87,97,98,123–125 The results reveal that SRFHs work effectively as soil conditioners and slow release systems. Basically, a small amount of dried SRFH is mixed with soil and then added to plant seeds. The growth patterns of plants, such as plant height and leaf width, have been compared with those of untreated plants.126,127 The effect of P(AAc)-g-OPEFB/urea on okra plant growth was reported by Laftah and Hashim, as shown in Fig. 15. The results indicate that okra plant growth is better in soil with 2 wt% P(AAc)-g-OPEFB/urea, due to reduced urea leaching as a result of the material holding on to the urea and delivering it to the plant over a long time period.40,97
 |
| Fig. 15 Okra plant growth after 12 weeks in (a) blank soil, (b) soil with urea, (c) soil with 2 wt% P(AAc)-g-OPEFB and (d) soil with 2 wt% of P(AAc)-g-OPEFB/urea.40 | |
Wen et al. studied the effects of cotton stalk-g-poly(acrylic acid)/bentonite/polyvinylpyrrolidone/urea [CS-g-P(AAc)/bent/PVP/urea] on the growth of cotton plants. The germination rate and plant height of cotton seedlings treated with CS-g-P(AAc)/bent/PVP/urea increased by 22.04% and 25.23% compared to pure urea, respectively. Fig. 16 shows photographs of cotton plants treated with (a) pure urea and (b) CS-g-PAA/bent/PVP/urea.124 These effects are due to CS-g-P(AAc)/bent/PVP/urea decreasing the release of urea and water, consequently improving the availabilities of nutrients and water to the plant.128
 |
| Fig. 16 Photographs of cotton plants treated with (a) pure urea and (b) CS-g-PAA/bent/PVP/urea. Reprinted with permission from ref. 124. Copyright (2016) American Chemical Society. | |
5. Recent studies on SRFHs
Over the past 40 years, hydrogels have been widely suggested for agricultural applications due to swollen hydrogels being able to act as water reservoirs and efficiently improve plant water absorption.104 However, most hydrogels on the market are made from synthetic polymers, and show poor biodegradability and biocompatibility compared to natural polymers.129 Nowadays, the development of environmentally friendly hydrogels has arisen due to increasing awareness of the need for environmental protection. Natural polymers such as starch, chitosan, lignin, alginate and cellulose are widely known as environmentally friendly materials and bio-renewable resources.130 In this section, recent studies on biodegradable sources of SRFHs are reviewed.
Zaharia et al. prepared hydrogels based on bacterial cellulose (BC) and poly(acrylic acid-co-N,N′-methylene-bis-acrylamide) via radical polymerization. The BC was obtained by static culture using pollen as a nitrogen source and fructose as a carbon source. Liquid fertilizer (LF) containing phosphorus, potassium, micronutrients and ammonium oxides was then encapsulated into the hydrogels during synthesis. Fertilizer release results showed that the presence of BC prolonged the release of fertilizer, proving that this formulation is good for agricultural applications.131 Xiao et al. reported a one-step process of reactive melt mixing to prepare starch-based superabsorbent polymers (SBSAPs) for the slow release of urea as a fertilizer. Corn starches with different amylose/amylopectin ratios were used in this study. Slow release urea in water showed that less than 15% of urea was released within 1 day, exceeding 80% after 30 days and lasted for more than 45 days. The present study provides cost effective slow urea release technology, which shows promise for agriculture applications.132 Ghazali et al. prepared fertilizer coated with a carbonaceous-g-poly (acrylic acid-co-acrylamide) SAH. Empty fruit bunches (EFB) were pyrolyzed in a furnace to obtain a carbonaceous material. The carbonaceous-SAH was then synthesized using a solution polymerization technique and used to coat fertilizer granules. The addition of the carbonaceous filler in the formulation of the SAH increases the water uptake compared to an unfilled SAH.133 Olad et al. prepared a new SRFH via the in situ graft polymerization of sulfonated carboxymethyl cellulose (SCMC) with AAc in the presence of PVP, silica nanoparticles and an NPK fertilizer compound. The silica nanoparticles were obtained from rice husk (RH). First, the RH was washed with distilled water to remove any soil and dust and then was washed with acid twice.109,134 Zhou et al. developed a novel slow release fertilizer of leftover rice-g-poly(acrylic acid)/montmorillonite/urea [LR-g-P(AAc)/MMT/urea]. LR was dried to a constant weight at 70 °C, ground to a powder using a planetary ball mill machine and passed through a 100 mesh sieve.135
6. Conclusions
This review presents a general overview of SRFHs. The combination of a SAH and fertilizer is a growing trend for regulating water and nutrients in one system. Biodegradability is the most critical property to consider when developing a new type of SRFH. The presence of inorganic materials and natural polymers/fibers in hydrogels not only improves their biodegradability but also leads to increased water absorbance capacity and controlled release of fertilizer. Coarse and porous structured SAHs have increased surface area, which provides good water retention and slow release properties. A two-step technique is the most used method to prepare SRFHs, however, in situ techniques offer economical advantages to producing SRFHs. The presence of a SAH outer layer onto a coated-type SRFH endows it with water retention as well as slow release properties.
A number of remarkable developments have been made fundamentally, therefore extensive research is required to fully develop SRFH products for application. A few research studies have been carried out to the point of application. However, the field evaluation is based on lab samples and there are limitations on achieving this, for example on a farm. Accordingly, scaling up this product is needed to produce an industrial scale quantity for agriculture application. Scale-up is expected to face critical challenges, such as scale-up feasibility, reproducibility and consistency. Therefore, future research needs to overcome these critical challenges. Another challenge is the degradation of SRFHs, especially natural SRFHs that are made up purely of natural polymers. Natural polymers are susceptible to enzymes and microbes and cannot control fertilizer release over a long period. For combined synthetic-natural SRFHs, there are two concerns about their degradability. First is the allowable percentage of natural polymers in combined synthetic-natural SRFHs, second is the acceptable percentage of degradability in claiming the degradability of combined synthetic-natural SRFHs.
Abbreviations
AAc | Acrylic acid |
AAc/MA | Acrylic acid/maleic acid |
AAm | Acrylamide |
AAm/MA | Acrylamide/maleic acid |
APT | Attapulgite |
BC | Bacteria cellulose |
CA | Cellulose acetate |
CC-g-P(AAc)/bent/PVP/urea | Corncob-g-poly(acrylic acid)/bentonite/polyvinylpyrrolidone/urea |
CMC | Carboxymethyl cellulose |
CMWS-g-P(AAc)/APT | Chemically modified wheat straw-g-poly(acrylic acid)/attapulgite |
CRF | Controlled release fertilizer |
CS-g-P(AAc)/bent/PVP/urea | Cotton stalk-g-poly(acrylic acid)/bentonite/polyvinylpyrrolidone/urea |
CTS/CS | Chitosan–cellulose |
EC | Ethylcellulose |
GG | Gellan gum |
GT | Gum tragacanth |
HA | Humic acid |
Hyd | Sodium alginate-g-poly (acrylic acid-co-acrylamide) |
KNO3 | Potassium nitrate |
LF | Liquid fertilizer |
LR-g-P(AAc)/MMT/urea | Leftover rice-g-poly(acrylic acid)/montmorillonite/urea |
MB-g-P(AAc-co-AAm) | Mulberry branch-g-poly(acrylic acid-co-acrylamide) |
MC | Methylcellulose |
MKP | Monopotassium phosphate |
MMt | Montmorillonite |
MS | Methyl cellulose |
NaAlg | Sodium alginate |
NaAlg-g-P(AAc-co-AAm)/clin | Sodium alginate-g-poly (acrylic acid-co-acrylamide)/clinoptilolite |
NP | Nitrogen and phosphorus |
NPK | Nitrogen, phosphorus, potassium |
OPEFB-g-P(AAc) | Oil palm empty fruit bunch-grafted-poly(acrylic acid) |
OPEFB-g-P(AAc-co-AAm) | Oil palm empty fruit bunch-grafted-poly(acrylic acid-co-acrylamide) |
P(AAc) | Poly(acrylic acid) |
P(AAc-co-AAm)/kaolin | Poly(acrylic acid-co-acrylamide)/kaolin |
P(AAc)-co-AMPS/WS | Poly(acrylic acid-co-2-acryloylamino-2-methyl-1-propanesulfonic acid)/wheat straw |
PAAU | Poly(acrylic acid)/urea |
P-CMS-g-PAAm | Phosphorylated carboxymethyl starch-g-polyacrylamide |
PCU | Poly(N-vinyl-pyrrolidone)/urea |
PD % | Percentage of degradation |
PS | Polystyrene |
PVA/CTS | Poly(vinyl alcohol)/chitosan |
PVP | Polyvinylpyrrolidone |
RH | Rice husk |
SAH | Super absorbance hydrogel |
SAP | Superabsorbent polymer |
SBSAPs | Starch-based superabsorbent polymers |
SCS/P(AAc)/PHR | Sulfonated corn starch/poly(acrylic acid)/phosphate rock |
SCMC | Sulfonated carboxymethyl cellulose |
SRF | Slow release fertilizer |
SRFH | Slow release fertilizer hydrogel |
Starch-g-(AAc-co-MMA) | Starch-g-(acrylic acid-co-methyl methacrylate) |
WS-g-P(AAc) | Wheat straw-g-poly(acrylic acid) |
WSCS-g-P(AAc)/PVA | Wheat straw cellulose-grafted-poly(acrylic acid/polyvinyl alcohol) |
Conflicts of interest
There are no conflicts to declare.
Acknowledgements
The author would like to thank the Ministry of Education Malaysia (PRGS/1/2019/TK10/UMP/02/2) and Universiti Malaysia Pahang (RDU190807) for financial support.
References
- N. Seetapan, J. Wongsawaeng and S. Kiatkamjornwong, Polym. Adv. Technol., 2011, 22, 1685–1695 CrossRef CAS.
- D. Feng, B. Bai, C. Ding, H. Wang and Y. Suo, Ind. Eng. Chem. Res., 2014, 53, 12760–12769 CrossRef CAS.
- W. A. Laftah and S. Hashim, J. Compos. Mater., 2014, 48, 555–569 CrossRef CAS.
- N. Peng, Y. Wang, Q. Ye, L. Liang, Y. An, Q. Li and C. Chang, Carbohydr. Polym., 2016, 137, 59–64 CrossRef CAS PubMed.
- L. Xie, M. Liu, B. Ni and Y. Wang, Ind. Eng. Chem. Res., 2012, 51, 3855–3862 CrossRef CAS.
- S. J. Kohls, D. D. Baker, D. A. Kremer and J. O. Dawson, Plant Soil, 1999, 214, 105–115 CrossRef CAS.
- X. Li, Q. Li, Y. Su, Q. Yue, B. Gao and Y. Su, J. Taiwan Inst. Chem. Eng., 2015, 55, 170–179 CrossRef CAS.
- B. Ni, M. Liu and S. Lü, Chem. Eng. J., 2009, 155, 892–898 CrossRef CAS.
- B. Ni, M. Liu and S. Lü, Chem. Eng. J., 2009, 155, 892–898 CrossRef CAS.
- J. Chen, S. Lü, Z. Zhang, X. Zhao, X. Li, P. Ning and M. Liu, Sci. Total Environ., 2018, 613, 829–839 CrossRef PubMed.
-
M. E. Trenkel, Controlled-release and stabilized fertilizers in agriculture, International Fertilizer Industry Association, Paris, 1997 Search PubMed.
- A. Shaviv, Adv. Agron., 2000, 71, 79 Search PubMed.
- Association of American Plant Food Control Officials (AAPFCO), Official Publication, 1995, No. 48.
- A. Pourjavadi, M. Doulabi, R. Soleyman, S. Sharif and S. A. Eghtesadi, React. Funct. Polym., 2012, 72, 667–672 CrossRef CAS.
- S. Jin, Y. Wang, J. He, Y. Yang, X. Yu and G. Yue, J. Appl. Polym. Sci., 2013, 128, 407–415 CrossRef CAS.
- E. I. Pereira, F. B. Minussi, C. C. T. D. Cruz, A. C. C. Bernardi and C. Ribeiro, J. Agric. Food Chem., 2012, 60, 5267–5272 CrossRef CAS PubMed.
- R. Liang, H. Yuan, G. Xi and Q. Zhou, Carbohydr. Polym., 2009, 77, 181–187 CrossRef CAS.
- R. Liang, H. Yuan, G. Xi and Q. Zhou, Carbohydr. Polym., 2009, 1–7, DOI:10.1016/j.carbpol.2008.12.018.
- Saruchi, B. S. Kaith, R. Jindal, G. Kapur and V. Kumar, J. Chin. Adv. Mater. Soc., 2014, 2, 40–52 CrossRef.
- A. I. Raafat, M. Eid and M. B. El-Arnaouty, Nucl. Instrum. Methods Phys. Res., Sect. B, 2012, 283, 71–76 CrossRef CAS.
- H. A. A. El-Rehim, E.-S. A. Hegazy and H. L. A. El-Mohdy, J. Appl. Polym. Sci., 2004, 93, 1360–1371 CrossRef.
- L. Wu, M. Liu and R. Liang, Bioresour. Technol., 2008, 99, 547–554 CrossRef CAS PubMed.
- K. Zhong, Z.-T. Lin, X.-L. Zheng, G.-B. Jiang, Y.-S. Fang, X.-Y. Mao and Z.-W. Liao, Carbohydr. Polym., 2013, 92, 1367–1376 CrossRef CAS PubMed.
- R. Liang and M. Liu, J. Appl. Polym. Sci., 2007, 106, 3007–3015 CrossRef CAS.
- L. Chen, Z. Xie, X. Zhuang, X. Chen and X. Jing, Carbohydr. Polym., 2008, 72, 342–348 CrossRef CAS.
- J. Gao, Q. Yang, F. Ran, G. Ma and Z. Lei, Appl. Clay Sci., 2016, 132, 739–747 CrossRef.
- S. Zhang, W. Wang, H. Wang, W. Qi, L. Yue and Q. Ye, Carbohydr. Polym., 2014, 101, 798–803 CrossRef CAS PubMed.
- H. Ge and S. Wang, Carbohydr. Polym., 2014, 113, 296–303 CrossRef CAS PubMed.
- T. Fekete, J. Borsa, E. Takács and L. Wojnárovits, Radiat. Phys. Chem., 2016, 118, 114–119 CrossRef CAS.
-
N. E. Rabat, S. Hashim and R. A. Majid, Adv. Mater. Res., 2014, 98018–22 Search PubMed.
- X. Yan, R. Ye and Y. Chen, Food Chem., 2015, 180, 106–115 CrossRef CAS PubMed.
- R. Liang, M. Liu and L. Wu, React. Funct. Polym., 2007, 67, 769–779 CrossRef CAS.
- A. Jarosiewicz and M. Tomaszewska, J. Agric. Food Chem., 2003, 51, 413–417 CrossRef CAS PubMed.
- C. Bai, S. Zhang, L. Huang, H. Wang, W. Wang and Q. Ye, Carbohydr. Polym., 2015, 125, 376–383 CrossRef CAS PubMed.
- J. Zhang, L. Wang and A. Wang, Ind. Eng. Chem. Res., 2007, 46, 2497–2502 CrossRef CAS.
- N. Roy, N. Saha, T. Kitano and P. Saha, Carbohydr. Polym., 2012, 89, 346–353 CrossRef CAS PubMed.
- W. Laftah and S. Hashim, Chem. Pap., 2014, 68, 798–808 CAS.
- X. Li, Q. Li, X. Xu, Y. Su, Q. Yue and B. Gao, J. Taiwan Inst. Chem. Eng., 2016, 60, 564–572 CrossRef CAS.
- L. Xie, S. Lü, M. Liu, C. Gao, X. Wang and L. Wu, J. Agric. Food Chem., 2013, 61, 3382–3388 CrossRef CAS PubMed.
-
W. A. Laftah, Preparation and Characterization of Biodegradable Polyacrylic Acid Based Hydrogel for Agricultural Application, Doctoral dissertation, Universiti Teknologi Malaysia, 2013.
- D. Klemm, B. Heublein, H. P. Fink and A. Bohn, Angew. Chem., Int. Ed., 2005, 44, 3358–3393 CrossRef CAS PubMed.
- B. Cheng, B. Pei, Z. Wang and Q. Hu, RSC Adv., 2017, 7, 42036–42046 RSC.
- M. Rinaudo, Prog. Polym. Sci., 2006, 31, 603–632 CrossRef CAS.
- H. Ismail, M. Irani and Z. Ahmad, Int. J. Polym. Mater. Polym. Biomater., 2013, 62, 411–420 CrossRef CAS.
- D. Qiao, H. Liu, L. Yu, X. Bao, G. P. Simon, E. Petinakis and L. Chen, Carbohydr. Polym., 2016, 147, 146–154 CrossRef CAS PubMed.
- M. R. Guilherme, F. A. Aouada, A. R. Fajardo, A. F. Martins, A. T. Paulino, M. F. Davi, A. F. Rubira and E. C. Muniz, Eur. Polym. J., 2015, 72, 365–385 CrossRef CAS.
- O. León, A. Muñoz-Bonilla, D. Soto, J. Ramirez, Y. Marquez, M. Colina and M. Fernández-García, J. Polym. Environ., 2018, 26, 728–739 CrossRef.
- A. M. Senna and V. R. Botaro, J. Controlled Release, 2017, 260, 194–201 CrossRef CAS PubMed.
- R. C. Sabadini, V. C. Martins and A. Pawlicka, Cellulose, 2015, 22, 2045–2054 CrossRef CAS.
- T. Zheng, Y. Liang, S. Ye and Z. He, Biosyst. Eng., 2009, 102, 44–50 CrossRef.
- M. Liu, R. Liang, F. Zhan, Z. Liu and A. Niu, Polym. Int., 2007, 56, 729–737 CrossRef CAS.
- M. Teodorescu, A. Lungu and P. O. Stanescu, Ind. Eng. Chem. Res., 2009, 48, 6527–6534 CrossRef CAS.
-
B. Tyliszczak, J. Polaczek, J. Pielichowski and K. Pielichowski, Macromol. Symp., 2009, 2791, 236–242 Search PubMed.
- F. Helaly, H. Essawy, D. El-Nashar and N. Maziad, Polym.-Plast. Technol. Eng., 2005, 44, 253–263 CrossRef CAS.
- M. Likhitha, R. Sailaja, V. Priyambika and M. Ravibabu, Int. J. Biol. Macromol., 2014, 65, 500–508 CrossRef CAS PubMed.
- H. Gharekhani, A. Olad, A. Mirmohseni and A. Bybordi, Carbohydr. Polym., 2017, 168, 1–13 CrossRef CAS PubMed.
- Y. Xiang, X. Ru, J. Shi, J. Song, H. Zhao, Y. Liu, D. Guo and X. Lu, J. Agric. Food Chem., 2017, 65, 10851–10858 CrossRef CAS PubMed.
- A. Bortolin, F. A. Aouada, L. H. Mattoso and C. Ribeiro, J. Agric. Food Chem., 2013, 61, 7431–7439 CrossRef CAS PubMed.
- D. J. Sarkar, A. Singh, P. Mandal, A. Kumar and B. Parmar, Polym.-Plast. Technol. Eng., 2015, 54, 357–367 CrossRef CAS.
- A. Rashidzadeh, A. Olad, D. Salari and A. Reyhanitabar, J. Polym. Res., 2014, 21, 344 CrossRef.
- A. Rashidzadeh and A. Olad, Carbohydr. Polym., 2014, 114, 269–278 CrossRef CAS PubMed.
- F. Wu, Y. Zhang, L. Liu and J. Yao, Carbohydr. Polym., 2012, 87, 2519–2525 CrossRef CAS.
- X. Li, L. G. Tabil and S. Panighrahi, J. Polym. Environ., 2007, 15, 25–33 CrossRef.
-
P. Calvert, Hydrogels for Soft Machines, D. o. M. a. Textiles, University of Massachusetts Dartmouth, Dartmouth, USA, 2009 Search PubMed.
- M. R. Guilhermea, G. M. Campesea, E. Radovanovica, A. F. Rubiraa, E. C. M. Judith and P. A. Feitosab, Polymer, 2005, 46, 7867–7873 CrossRef.
- K. Alharbi, A. Ghoneim, A. Ebid, H. El-Hamshary and M. H. El-Newehy, Int. J. Biol. Macromol., 2018, 116, 224–231 CrossRef CAS PubMed.
- A. Pourjavadi, M. Doulabi, R. Soleyman, S. Sharif and S. A. Eghtesadi, React. Funct. Polym., 2012, 72, 667–672 CrossRef CAS.
- H. A. Essawy, M. B. Ghazy, F. A. El-Hai and M. F. Mohamed, Int. J. Biol. Macromol., 2016, 89, 144–151 CrossRef CAS PubMed.
- R. L. Mikkelsen, Fert. Res., 1994, 38, 53–59 CrossRef CAS.
- G. D. Kang, S. H. Cheon, G. Khang and S.-C. Song, Eur. J. Pharm. Biopharm., 2006, 63, 340–346 CrossRef CAS PubMed.
- R. Censi, T. Vermonden, M. J. van Steenbergen, H. Deschout, K. Braeckmans, S. C. De Smedt, C. F. van Nostrum, P. di Martino and W. E. Hennink, J. Controlled Release, 2009, 140(3), 230–236 CrossRef CAS PubMed.
- J. L. H. West and A. Jeffrey, React. Polym., 1995, 25, 139–147 CrossRef CAS.
- H. Liu, C. Wang, Q. Gao, X. Liu and Z. Tong, Acta Biomater., 2010, 6(1), 275–281 CrossRef CAS PubMed.
- J. Zeng, K. Shi, Y. Zhang, X. Sun, L. Deng, X. Guo, Z. Du and B. Zhang, J. Colloid Interface Sci., 2008, 322, 654–659 CrossRef CAS PubMed.
- H. Wack and M. Ulbricht, Polymer, 2009, 50, 2075–2080 CrossRef CAS.
- Y. Yue, X. Sheng and P. Wang, Eur. Polym. J., 2009, 45, 309–315 CrossRef CAS.
- M. Teodorescu, A. Lungu, P. O. Stanescu and C. Neamt, Ind. Eng. Chem. Res., 2009, 48, 6527–6534 CrossRef CAS.
- M. Guo, M. Liu, Z. Hu, F. Zhan and L. Wu, J. Appl. Polym. Sci., 2005, 96, 2132–2138 CrossRef CAS.
-
D. Hillel, Introduction to Environmental Soil Physics, Elsevier Academic Press, Massachusetts, 2004 Search PubMed.
- H. Abd El-Rehim, E. S. A. Hegazy and H. Abd El-Mohdy, J. Appl. Polym. Sci., 2006, 101, 3955–3962 CrossRef CAS.
- J. H. Ward and N. A. Peppas, J. Controlled Release, 2001, 71, 183–192 CrossRef CAS PubMed.
- R. L. Mikkelsen, Journal, 2007, 91, 6–7 Search PubMed.
- S. Al-Zahrani, Ind. Eng. Chem. Res., 2000, 39, 367–371 CrossRef CAS.
- R. Liang and M. Liu, J. Agric. Food Chem., 2006, 54, 1392–1398 CrossRef CAS.
- S. Noppakundilograt, N. Pheatcharat and S. Kiatkamjornwong, J. Appl. Polym. Sci., 2015, 132, 41249 CrossRef.
-
N. E. Rabat, Synthesis and Characterization of Oil Palm Empty Fruit Bunch Grafted Polymer Hydrogels for Slow Release Fertilizer, Doctoral dissertation, Universiti Teknologi Malaysia, 2014.
-
N. E. Rabat, S. Hashim and R. A. Majid, Effect of oil palm empty fruit bunch-grafted-poly (acrylic acid-co-acrylamide) hydrogel preparations on plant growth performance, Trans Tech Publ, 2014 Search PubMed.
- Y. Zhang, X. Liang, X. Yang, H. Liu and J. Yao, ACS Sustainable Chem. Eng., 2014, 2, 1871–1878 CrossRef CAS.
- M. Hanafi, S. Eltaib and M. Ahmad, Eur. Polym. J., 2000, 36, 2081–2088 CrossRef CAS.
- B. Azeem, K. KuShaari, Z. B. Man, A. Basit and T. H. Thanh, J. Controlled Release, 2014, 181, 11–21 CrossRef CAS.
- K. R. M. Ibrahim, F. E. Babadi and R. Yunus, Particuology, 2014, 17, 165–172 CrossRef.
- A. Ammala, S. Bateman, K. Dean, E. Petinakis, P. Sangwan, S. Wong, Q. Yuan, L. Yu, C. Patrick and K. Leong, Prog. Polym. Sci., 2011, 36, 1015–1049 CrossRef CAS.
- L. Wu and M. Liu, Carbohydr. Polym., 2008, 72, 240–247 CrossRef CAS.
- L. Xie, M. Liu, B. Ni, X. Zhang and Y. Wang, Chem. Eng. J., 2011, 167, 342–348 CrossRef CAS.
- G. Z. Zhao, Y. Q. Liu, Y. Tian, Y. Y. Sun and Y. Cao, J. Polym. Res., 2010, 17, 119–125 CrossRef CAS.
- M. R. Islam, S. Mao, X. Xue, A. E. Eneji, X. Zhao and Y. Hu, J. Sci. Food Agric., 2011, 91, 1990–1997 CrossRef CAS.
- W. A. Laftah and S. Hashim, Int. J. Plast. Technol., 2012, 16, 166–181 CrossRef CAS.
- W. A. Laftah and S. Hashim, Adv. Mater. Res., 2013, 626, 6–10 Search PubMed.
- W. Kong, Q. Li, X. Li, Y. Su, Q. Yue and B. Gao, J. Environ. Manage., 2019, 230, 190–198 CrossRef CAS PubMed.
- A. Olad, H. Zebhi, D. Salari, A. Mirmohseni and A. R. Tabar, New J. Chem., 2018, 42, 2758–2766 RSC.
- D. Cheng, Y. Liu, G. Yang and A. Zhang, J. Agric. Food Chem., 2018, 66, 5762–5769 CrossRef CAS PubMed.
- A. Olad, H. Gharekhani, A. Mirmohseni and A. Bybordi, Adv. Polym. Technol., 2018, 37, 1682–1694 CrossRef CAS.
- H. Gharekhani, A. Olad and F. Hosseinzadeh, New J. Chem., 2018, 42, 13899–13914 RSC.
- F. F. Montesano, A. Parente, P. Santamaria, A. Sannino and F. Serio, Agric. Agric. Sci. Procedia, 2015, 4, 451–458 Search PubMed.
-
W. B. Wang and A. Q. Wang, Adv. Mater. Res., 2010, 96, 177–182 Search PubMed.
- V. Kumar, H. Mittal and S. M. Alhassan, Int. J. Biol. Macromol., 2019, 132, 1252–1261 CrossRef PubMed.
- M. S. Johnson, J. Sci. Food Agric., 1984, 35, 1196–1200 CrossRef CAS.
- M. Bakass, A. Mokhlisse and M. Lallemant, J. Appl. Polym. Sci., 2002, 83, 234–243 CrossRef CAS.
- A. Olad, H. Zebhi, D. Salari, A. Mirmohseni and A. R. Tabar, Mater. Sci. Eng., C, 2018, 90, 333–340 CrossRef CAS PubMed.
-
A. L. Andrady, in Physical Properties of Polymers Handbook, ed. A. L. Andrady, Engineering & Technology Dirsian, RTI International, Research Triangle Park, 2007, ch. 56, pp. 951–961 Search PubMed.
- V. X. Truong, M. L. Hun, F. Li, A. P. Chidgey and J. S. Forsythe, Biomater. Sci., 2016, 4, 1123–1131 RSC.
- V. B. Bueno, R. Bentini, L. H. Catalani and D. F. S. Petri, Carbohydr. Polym., 2013, 92, 1091–1099 CrossRef CAS PubMed.
- Y. Li, J. Rodrigues and H. Tomas, Chem. Soc. Rev., 2012, 41, 2193–2221 RSC.
- P. Rizzarelli, C. Puglisi and G. Montaudo, Polym. Degrad. Stab., 2004, 85, 855–863 CrossRef CAS.
- T. Kijchavengkul, R. Auras, M. Rubino, E. Alvarado, J. R. C. Montero and J. M. Rosales, Polym. Degrad. Stab., 2010, 95, 99–107 CrossRef CAS.
- R. Shogren, W. Doane, D. Garlotta, J. Lawton and J. Willett, Polym. Degrad. Stab., 2003, 79, 405–411 CrossRef CAS.
- D. Wang, Z. Q. Song and S. B. Shang, J. Appl. Polym. Sci., 2008, 107, 4116–4120 CrossRef CAS.
- B. Kaith, R. Jindal, M. Kumari and M. Kaur, React. Funct. Polym., 2017, 120, 1–13 CrossRef.
- A. Huettermann, L. J. Orikiriza and H. Agaba, Clean: Soil, Air, Water, 2009, 37, 517–526 CAS.
- K. Sharma, V. Kumar, B. Kaith, V. Kumar, S. Som, S. Kalia and H. Swart, RSC Adv., 2014, 4, 25637–25649 RSC.
- S. Shinoj, R. Visvanathan and S. Panigrahi, Biosyst. Eng., 2010, 106, 378–388 CrossRef.
- B. Ni, M. Liu, S. Lü, L. Xie and Y. Wang, J. Agric. Food Chem., 2010, 58, 12373–12378 CrossRef CAS PubMed.
- A. M. Elbarbary and M. M. Ghobashy, Radiochim. Acta, 2017, 105, 865–876 CAS.
- P. Wen, Z. Wu, Y. He, B.-C. Ye, Y. Han, J. Wang and X. Guan, ACS Sustainable Chem. Eng., 2016, 4, 6572–6579 CrossRef CAS.
- P. Wen, Y. Han, Z. Wu, Y. He, B.-C. Ye and J. Wang, Arabian J. Chem., 2017, 10, 922–934 CrossRef CAS.
- A. M. Elbarbary, H. A. A. El-Rehim, N. M. El-Sawy, E.-S. A. Hegazy and E.-S. A. Soliman, Carbohydr. Polym., 2017, 176, 19–28 CrossRef CAS PubMed.
- H. A. Abd El-Rehim, J. Appl. Polym. Sci., 2006, 101, 3572–3580 CrossRef CAS.
- L. Yang, Y. Yang, Z. Chen, C. Guo and S. Li, Ecol. Eng., 2014, 62, 27–32 CrossRef.
- Y. Zhang, R. Huang, S. Peng and Z. Ma, J. Chem., 2015, 2015 DOI:10.1155/2015/413497.
- H. Zhang, Q. Luan, Q. Huang, H. Tang, F. Huang, W. Li, C. Wan, C. Liu, J. Xu and P. Guo, Carbohydr. Polym., 2017, 157, 1830–1836 CrossRef CAS PubMed.
- A. Zaharia, A.-L. Radu, S. Iancu, A.-M. Florea, T. Sandu, I. Minca, V. Fruth-Oprisan, M. Teodorescu, A. Sarbu and T.-V. Iordache, RSC Adv., 2018, 8, 17635–17644 RSC.
- X. Xiao, L. Yu, F. Xie, X. Bao, H. Liu, Z. Ji and L. Chen, Chem. Eng. J., 2017, 309, 607–616 CrossRef CAS.
- S. Ghazali, S. Jamari, N. Noordin and K. Tan, Int. J. Chem. Eng. Appl., 2017, 8, 141 CAS.
- A. Olad, H. Gharekhani, A. Mirmohseni and A. Bybordi, Polym. Bull., 2017, 74, 3353–3377 CrossRef CAS.
- T. Zhou, Y. Wang, S. Huang and Y. Zhao, Sci. Total Environ., 2018, 615, 422–430 CrossRef CAS PubMed.
- T. Jamnongkan and S. Kaewpirom, J. Polym. Environ., 2010, 18, 413–421 CrossRef CAS.
|
This journal is © The Royal Society of Chemistry 2019 |
Click here to see how this site uses Cookies. View our privacy policy here.