DOI:
10.1039/C6SC00715E
(Edge Article)
Chem. Sci., 2016,
7, 5537-5546
Photoelectrochemical hydrogen production in water using a layer-by-layer assembly of a Ru dye and Ni catalyst on NiO†
Received
16th February 2016
, Accepted 7th May 2016
First published on 9th May 2016
Abstract
Capture and conversion of sunlight into the storable energy carrier H2 can be achieved through photoelectrochemical water splitting using light-absorbing cathodes and anodes bearing H2 and O2 evolving catalysts. Here, we report on the development of a dye-sensitised p-type nickel oxide (NiO) photocathode with a hexaphosphonated Ru(2,2′-bipyridine)3 based dye (RuP3) and a tetraphosphonated molecular [Ni(P2N2)2]2+ type proton reduction catalyst (NiP) for the photoreduction of aqueous protons to H2. A layer-by-layer deposition approach was employed, using Zr4+ ions to link the phosphonate units in RuP3 and NiP in a supramolecular assembly on the NiO photocathode. This approach keeps the dye in close proximity to the catalyst and semiconductor surface, but spatially separates NiP from NiO for advantageous electron transfer dynamics. The NiO|RuP3–Zr4+–NiP electrodes generate higher photocurrents and are more stable than photocathodes with RuP3 and NiP co-immobilised on the NiO surface in the absence of Zr4+ cations linking dye and catalyst. The generation of H2 with the NiO|RuP3–Zr4+–NiP hybrid electrode in pH 3 aqueous electrolyte solution during irradiation with a UV-filtered solar light simulator (λ > 400 nm, 100 mW cm−2, AM1.5G) has been confirmed by gas chromatography at an underpotential of 300 mV (Eappl = +0.3 V vs. RHE), demonstrating the potential of these electrodes to store solar energy in the chemical bond of H2.
Introduction
Photovoltaic technology, such as dye-sensitised solar cells, enables the conversion of solar energy into electricity and is commercially available.1 Solar fuel devices allow for the storage of solar energy in a chemical energy carrier, but are only in an early stage of development and have not yet reached the required efficiencies and stabilities at low cost suitable for application.2 Splitting of water into its elements in a photoelectrochemical (PEC) cell is a potentially sustainable means of generating renewable H2.3 However, a lack of novel strategies to electronically couple a light-harvesting unit to a stable proton reduction catalyst is currently holding back advances in the development of high-performance PEC devices.4 Molecular dyes and catalysts offer several advantages over heterogeneous alternatives as their composition and activity can be more easily synthetically controlled and fine-tuned.5 They provide an excellent platform to develop rational strategies such as layer-by-layer deposition6 to integrate dyes and catalysts on electrode materials and enable detailed mechanistic studies to improve our understanding of photoelectrode assemblies.7 Ultimately, these insights may contribute to the establishment of advanced approaches to fabricate electrodes in PEC water splitting cells.
We have previously reported on several suspension-based photocatalytic H2-generation systems with molecular catalysts attached to light-absorbing nanoparticles to advance our understanding of efficient combination of dyes and catalysts on semiconducting surfaces.8 However, all of these systems relied on the use of a sacrificial electron donor (SED) to provide the reducing equivalents for fuel formation. SEDs are chemicals of relatively high value and are consumed stoichiometrically during the H2 generation process. They are disadvantageous as half-reaction promoting agents as they often form unknown decomposition products via highly reactive intermediates, which can interfere with the catalytic system, and should ultimately be avoided. One approach to bypass the need for a SED in a H2 evolution system is to immobilise the catalyst onto a photocathode material that can be incorporated into a PEC cell. The redox cycle can then be closed by use of a suitable (photo)anode for water/substrate oxidation.3b,c One of the main challenges for the assembly of molecule-based PEC devices is the design and effective integration of H2 evolving electrocatalysts and dyes onto the electrodes, which should ultimately allow for efficient solar light absorption, charge separation and chemical catalysis.
Photocathode materials that have been studied for solar H2 generation include p-silicon,9 p-GaP10 and p-NiO.11 Of these, p-type NiO offers the possibility to produce nanostructured high-surface area electrodes without the need for specialised techniques. High roughness is a prerequisite for maximising dye and catalyst loading on a given geometric surface area. Dye-sensitised NiO photocathodes in organic or aqueous electrolyte solution have been studied with sacrificial electron acceptors (SEAs),12 [FeFe]-hydrogenase mimics,13 and rhodium and cobaloxime catalysts.11b–e,14 While charge transfer and recombination kinetics of NiO|dye15 and NiO|dye–catalyst13 assemblies have been studied in detail with time-resolved spectroscopy, light-driven H2 production with dye-sensitised NiO photocathodes remains challenging and only cobaloxime-based catalysts have been reported to generate H2 with NiO.11b,d,e The binding of the cobaloxime catalyst in these cases was achieved through a linker tethered to NiO bearing a free pyridine moiety, which coordinates to the axial coordination sphere of the cobaloxime.11c–e Axial pyridine units coordinated to cobaloximes have been shown to be inherently labile during catalytic turnover,5b,10b,16 and therefore H2 evolution catalysts with a stable ligand framework are needed.
Nickel bis(diphosphine) type catalysts, [Ni(P2N2)2]2+, are attractive proton reduction catalysts as they operate in water,8b,17 and display higher activity than cobaloximes in photocatalytic H2 production.17a,18 The [Ni(P2N2)2]2+ complex also provides a stable ligand framework with no coordinating moieties becoming labile during the catalytic cycle,19 and is therefore less susceptible to catalyst dissociation from a surface due to ligand dissociation.20 [Ni(P2N2)2]2+ catalysts have previously been shown to retain high electrocatalytic activity for H2 generation from water when immobilised on multi-walled carbon nanotubes (CNTs) via covalent linking20 or π–π interactions of pyrene moieties,21 and when immobilised via phosphonate groups on mesostructured TiO2 electrodes.22 The phosphonated catalyst, NiP (Fig. 1), was also used as catalyst on TiO2 nanoparticles sensitised with a phosphonated ruthenium-based dye (RuP, Fig. 1) in photocatalytic H2 generation with a SED.17a A [Ni(P2N2)2]2+ and a [Ni(PNP)2]2+ type catalyst have previously been immobilised on p-Si,9c,23 but photocatalytic H2 generation was only shown for the latter assembly in acetonitrile with trifluoroacetic acid as proton source. Thus, previous work on H2 generation with [Ni(P2N2)2]2+ catalysts relied on the use of a SED, an applied electrochemical overpotential or non-aqueous conditions to generate H2.
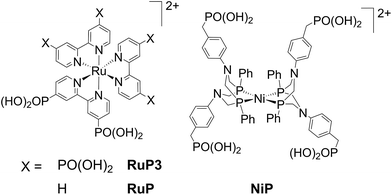 |
| Fig. 1 Structures of the dyes (RuP and RuP3) and proton reduction catalyst (NiP) used in this study. Chloride (RuP3) and bromide (RuP, NiP) counter-ions are omitted for clarity. | |
In this study, PEC H2 evolution was investigated on a p-type NiO photocathode sensitised with a hexaphosphonated ruthenium tris(bipyridine) based dye (RuP3, Fig. 1)24 and NiP. A rational and simple procedure of sequential immersion of NiO films into solutions of RuP3, ZrOCl2 and NiP was employed to produce electrodes of the type NiO|RuP3–Zr4+–NiP (Fig. 2),25 where the catalyst is spatially separated from the semiconductor electrode to reduce inefficiencies from charge-recombination.13 Our study shows that increasing the distance of the catalyst from the NiO surface results in substantially enhanced PEC performance in terms of photocurrent and stability when compared to NiO|RuP3–NiP, where the dye and catalyst are co-immobilised on NiO. We demonstrate a dye-sensitised NiO hybrid electrode with an adsorbed Ni catalyst, which has the potential to store solar energy in the bond of H2 without the decomposition of valuable sacrificial agents or an applied overpotential. Rational layer-by-layer assembly of dye and catalyst on a semiconductor electrode is therefore established as a route to produce functional PEC H2 production systems.
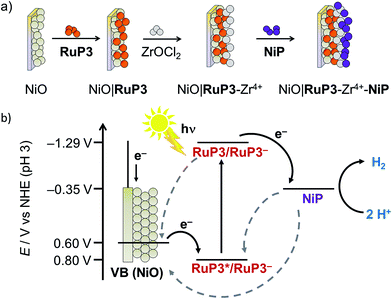 |
| Fig. 2 (a) Supramolecular dye–catalyst assembly on photocathode: layer-by-layer deposition of RuP3, Zr4+ and NiP on p-type NiO photocathode (see text for details). (b) Energy diagram of the NiO photocathode assembly showing the proposed electron transfer mechanisms (reductive quenching) as black solid arrows and possible recombination pathways as grey dashed arrows between p-NiO, RuP3 and NiP. | |
Results and discussion
Assembly and pre-catalysis characterisation
Mesoporous NiO was grown on tin-doped indium oxide (ITO)-coated glass electrodes by a previously reported hydrothermal method26 from a solution containing Ni(NO3)2·6H2O and hexamethylenetetramine (0.25 M each). NiO electrodes were sensitised by immersion in a RuP3 solution (1 mM in H2O) overnight to give NiO|RuP3 for PEC experiments. Immobilisation of monolayers of molecular compounds via phosphonic acids on metal oxide surfaces is a well-established tool for surface modification.25aNiP was immobilised on the NiO|RuP3 photocathodes in a layered assembly using Zr4+ to link the phosphonates of dye and catalyst (Fig. 2; see below for more details). Zr4+ ions bind strongly to phosphonic acid moieties and were previously used for creating multi-layered Zr4+-phosphonate structures.25,27 Zr4+ was bound by dipping NiO|RuP3 electrodes into a solution of ZrOCl2 (5 mM in EtOH/H2O, 60/40 v/v) for 2 h, rinsing with H2O and EtOH and drying under a stream of N2. The NiO|RuP3–Zr4+ electrodes were subsequently submerged in a solution of NiP (0.5 mM in MeOH) for at least 2 h to obtain the supramolecular NiO|RuP3–Zr4+–NiP electrode assembly with one layer of dye and one layer of catalyst linked by Zr4+. All immobilisation steps were carried out at room temperature.
In previously reported homogeneous, SED-promoted photocatalytic H2 generation systems, the ratio between the dye and the catalyst was found to strongly influence the overall performance.17a,28 We have therefore varied the ratio of co-immobilised RuP3 and NiP on the p-NiO photocathodes. The layer-by-layer deposition approach allowed the RuP3 and NiP loading on the metal oxide surface to be controlled more precisely, creating Zr4+-linked dye/catalyst layers by repeated immobilisation cycles.25c Repeated deposition of Zr4+ and either RuP3 dye or NiP catalyst gave electrodes of the structure NiO|(RuP3–Zr4+)2–NiP (containing two layers of RuP3–Zr4+) or NiO|RuP3–(Zr4+–NiP)2 (containing two layers of Zr4+–NiP). For control experiments, NiO|RuP3 electrodes were submerged directly in NiP solution without prior immobilisation of Zr4+ ions, and the so-obtained NiO|RuP3–NiP electrodes were also studied. Additionally, RuP3 was replaced with the diphosphonated dye RuP (Fig. 1), which only allows binding to NiO and does not offer any phosphonic acid moieties to generate Zr4+-linked phosphonate networks.
The photocurrent response of NiO|RuP3 electrodes with different NiO film thickness was recorded in a PEC experiment in aqueous electrolyte solution (0.1 M Na2SO4, pH 3) in the presence of the SEA 4,4′-dithiodipyridine (DTDP, 1 mM; Fig. 3 and S1†) at room temperature. DTDP is reduced in two irreversible steps, with the first reduction occurring at Ep = −0.06 V vs. the reversible hydrogen electrode (RHE). Thickness, morphology and crystallinity of the NiO films was studied by varying the reaction conditions (see Table S1 and Fig. S2 and S3† for powder X-ray diffraction pattern and scanning electron microscopy images). The optimised films have an average pore size (measured as distance between sheets) of 290 ± 81 nm and a film thickness of 2 μm (Fig. 3). The flatband potential of this NiO electrode was determined via electrochemical impedance spectroscopy at 0.75 V vs. RHE from Mott–Schottky analysis (Fig. S4†) and shows Nernstian pH dependence (one electron/one proton couple) in aqueous electrolyte solution, which is in agreement with previous reports on NiO electrodes.29
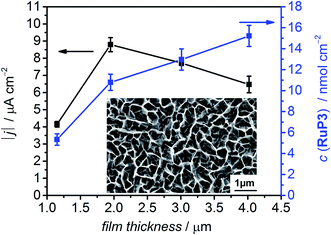 |
| Fig. 3 Photocurrent response of NiO|RuP3 under visible light irradiation (λ > 400 nm, AM1.5G filter, 100 mW cm−2) after 100 s at Eappl = 0.3 V vs. RHE in Na2SO4 (0.1 M, pH 3) in the presence of 4,4′-dithiodipyridine (DTDP, 1 mM) as SEA and dye loading (no applied potential; cm−2 refers to the geometrical surface area of the NiO electrode) with varying thicknesses of the NiO films. Inset: SEM image of optimised p-type NiO electrode (2 μm film thickness). | |
The photocurrent response of NiO|RuP3 and the loading capacity for RuP3 on NiO films with different film thickness was studied by PEC methods and desorption of the attached dye with 0.1 M NaOH and monitoring the UV-vis absorption at λ = 295 nm in solution (Table S1†). The dye loading capacity increased as expected with increasing film thickness, but the highest photocurrent density was achieved with a 2 μm thick NiO film, despite the higher dye loadings for thicker films (Fig. 3, Table S1†). This observation is consistent with the known limitation of hole mobility and lifetime in NiO,30 which suggests that the photocurrent generated with RuP3-sensitised NiO photocathodes is a balance between limiting charge transport in thick films and dye loading on thin films.
We subsequently investigated the interface between molecular components and the p-type NiO surface of the NiO|RuP3–Zr4+–NiP electrodes by UV-vis (Fig. S5†), attenuated total reflection infrared (ATR-IR; Fig. S6†), X-ray photoelectron (XPS; Fig. S7†) and inductively coupled plasma-optical emission spectroscopies (ICP-OES). The UV-vis spectrum of a bare NiO thin film shows the typical strong absorption at λ < 380 nm, and also a broad indirect transition at λ < 550 nm.29 All RuP3-sensitised NiO electrodes exhibit the typical MLCT absorption band for Ru(bpy)3-based dyes around λ = 465 nm and strong π-π* absorption in the UV region.24 When NiP is present on the electrodes a small shoulder at λ = 520 nm could be observed, which is typical for the d–d transition in NiP as also observed in solution spectra (Fig. S5†).
The ATR-IR spectra of the NiO|RuP3 electrodes at ν = 800 to 1250 cm−1 in the presence and absence of Zr4+ and NiP are shown in Fig. S6.† This region is characteristic for P
O and P–O–R vibrations, which are also observed in the spectra of powdered RuP3, RuP and NiP.31 NiO|RuP3 electrodes show a broad band at ν ∼ 1100 cm−1 attributed to P
O vibrations in RuP3, which is absent in a bare NiO film. In a NiO|RuP3–Zr4+ electrode, a small additional IR band at ν ∼ 983 cm−1 appears when compared to NiO|RuP3, and the signal increases and shifts to slightly higher wavenumbers for NiO|RuP3–Zr4+–NiP (ν ∼ 986 cm−1) and NiO|RuP3–(Zr4+–NiP)2 (ν ∼ 992 cm−1). This shift is in good accordance with previously reported values for Zr4+ bound to phosphonic acid groups.25b
XPS analysis was used to further characterise the modified NiO surface, and the presence of Ru and Zr on NiO after each layering step was confirmed (Fig. S7†). The signal for NiP could not be distinguished from the NiO background signal. Instead, mesoporous indium-tin oxide (ITO, 3.3 μm thickness) electrodes were prepared according to a previously reported procedure32 and used here as a scaffold. The XPS signals of ITO|RuP3–NiP, ITO|RuP3–Zr4+ and ITO|RuP3–Zr4+–NiP electrodes (prepared analogously to the related NiO hybrids) were analysed. In the presence of NiP, peaks at 855.0 and 872.5 eV were observed and were assigned to the Ni 2p3/2 and Ni 2p1/2 of the molecular NiP, respectively.17c,33 The P 2p signal for ITO|RuP3–NiP and ITO|RuP3–Zr4+–NiP electrodes is broad (133.0–131.0 eV) and consists of signals for the phosphonic acid bound to ITO34 and for the phosphine ligand.33 In contrast, ITO|RuP3–Zr4+ showed only a sharp XPS peak at 133.5 eV, which is assigned to the –PO(OH)2 groups.34 As the RuP3–Zr4+–NiP was assembled in identical manner on ITO and NiO, the presence of intact NiP on ITO supports its integrity on NiO prior to catalysis.
Finally, we quantified the immobilised dye and catalyst on NiO by UV-vis spectroscopy and ICP-OES analysis after desorption in aqueous NaOH (0.1 M). The overlap of RuP3 and NiP in the electronic absorption spectra prevented the simultaneous determination of dye and catalyst loading on the electrodes and ICP-OES measurements were used instead. Quantification of NiP on NiO was challenging due to the high nickel background from the electrode. Mesoporous ITO electrodes were used again as a scaffold and analysis of ITO|RuP3, ITO|RuP3–NiP, ITO|RuP3–Zr4+ and ITO|RuP3–Zr4+–NiP electrodes was carried out. The quantity of NiP on NiO was estimated from the Ru
:
Ni ratio found on the ITO electrodes (Table 1). The ICP-OES data for the amount of RuP3 immobilised on bare NiO (10.7 ± 0.3 nmol cm−2) correlates well with quantification by UV-vis spectroscopy after dye desorption (10.8 ± 0.8 nmol cm−2). Analysis of ITO|RuP3–NiP electrodes revealed a Ru
:
Ni ratio of 2.6 ± 0.04
:
1 and this ratio decreases only slightly to ∼2.2 ± 1.5
:
1 on ITO|RuP3–Zr4+–NiP, indicating that a similar amount of NiP is immobilised in the presence and absence of Zr4+. This ratio allows us to estimate a NiP loading of 4.98 ± 3.54 nmol cm−2 for NiO|RuP3–Zr4+–NiP, which is comparable to the loading of a cobaloxime catalyst on CdSe-sensitised NiO (∼3 nmol cm−2 for a 5.6 μm thick NiO film).11b
Table 1 Quantification of RuP3 and NiP on the NiO electrodes (determined by ICP-OES) and photocurrents (AM1.5G filter, 100 mW cm−2 and λ > 400 nm) of the respective electrodes after 100 s CPPE at Eappl = 0.3 V vs. RHE at room temperature. RuP3 and NiP loading on ITO is also shown. Loading concentrations are reported for the geometrical surface area of the electrodes.a
Composition |
RuP3/nmol cm−2 |
NiP/nmol cm−2 |
|j|/μA cm−2(a) |
|j|/μA cm−2(b) |
Measured in (a)the absence and (b)presence of DTDP as SEA. (c)Calculated value from RuP3 : NiP ratio on ITO. (d)Not determined.
|
NiO|RuP3 |
10.7 ± 0.3 |
— |
0.51 |
3.0 |
NiO|RuP3–NiP |
9.4 ± 1.6 |
3.57 ± 0.61(c) |
0.94 |
n.d.(d) |
NiO|RuP3–Zr4+ |
6.3 ± 2.2 |
— |
0.76 |
7.62 |
NiO|RuP3–Zr4+–NiP |
6.3 ± 3.1 |
4.98 ± 3.54(c) |
6.40 |
14.0 |
NiO|RuP3–(Zr4+–NiP)2 |
n.d. |
n.d. |
8.82 |
n.d. |
NiO|(RuP3–Zr4+)2–NiP |
n.d. |
n.d. |
2.18 |
n.d. |
ITO|RuP3–NiP |
37.6 ± 0.2 |
14.3 ± 0.2 |
— |
— |
ITO|RuP3–Zr4+ |
53.2 ± 20.5 |
— |
— |
— |
ITO|RuP3–Zr4+–NiP |
41.3 ± 20.3 |
19.2 ± 9.9 |
— |
— |
Photoelectrochemical experiments
The photocathodes were studied in PEC experiments in aqueous electrolyte solution (0.1 M Na2SO4, pH 3) in a three-electrode setup with a Ag/AgCl reference and a Pt counter electrode at room temperature. Linear sweep voltammetry (LSV) scans were recorded between E = +0.6 V and −0.15 V vs. RHE at a scan rate of 5 mV s−1 in the dark and under chopped and UV filtered irradiation with simulated solar light (λ > 400 nm, 100 mW cm−2, AM1.5G; Fig. 4a). All NiO electrodes (irrespective of being loaded with molecules or not) displayed a partially reversible oxidation wave between E = 0.42 and 0.48 V vs. RHE, which is assigned to the Ni3+/Ni2+ redox couple (Fig. S8†).29,30b In the absence of dye, only marginal photocurrent densities (reported per geometrical surface area) were observed in the studied potential range. Transient and small cathodic photocurrents were observed upon irradiating NiO|RuP3 (|j| ∼ 1.4 μA cm−2 at 0.5 V vs. RHE) and NiO|RuP3–Zr4+ (|j| ∼1.2 μA cm−2 at 0.5 V vs. RHE) electrodes, indicating hole injection of the excited dye, RuP3*, into the valence band of NiO (Fig. 2, for details see Mechanistic interpretation below). Quenching of RuP3* by NiO results in the formation of a reduced dye, RuP3−, which is then likely to undergo rapid charge recombination with the holes generated in NiO in absence of a suitable electron acceptor.13,15b A comparable photoresponse was observed between NiO|RuP3 and NiO|RuP3–NiP, indicating that direct binding of the NiP to NiO results in an unproductive assembly with negligible electron accumulation at NiP. When a NiO|RuP3–Zr4+–NiP electrode was used, however, an initial photocurrent density up to |j| ∼ 5.56 μA cm−2 was achieved under the same experimental conditions (Fig. 4a).
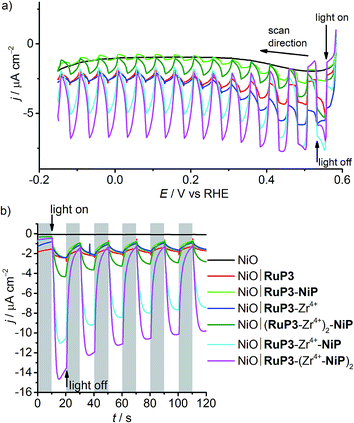 |
| Fig. 4 (a) LSV scans of NiO electrodes at a scan rate of 5 mV s−1 under chopped light irradiation (λ > 400 nm, AM1.5G filter, 100 mW cm−2). (b) Chronoamperometry of NiO working electrodes under chopped light irradiation (10 s on/off cycles) at Eappl = 0.3 V vs. RHE. All experiments were performed in a 3-electrode setup with a Ag/AgCl/KCl(sat.) reference and a Pt mesh counter electrode under N2 in a custom-made one-compartment PEC cell at room temperature. | |
Subsequently, the importance of the phosphonic acid moieties in the assembly of functional electrodes was investigated (Fig. S9†). When the diphosphonated dye RuP (Fig. 1)35 is immobilised on NiO instead of RuP3, no phosphonic acid binding sites are available for Zr4+. A comparable photocurrent was observed for a NiO|RuP–Zr4+–NiP and NiO|RuP–NiP electrode, which confirms that Zr4+ binding to the electrode assembly occurs via the free phosphonic acid groups of RuP3 and not via intercalation in the mesoporous NiO scaffold or precipitation as ZrO2 during the deposition procedure. The results from LSV confirm that the presence of RuP3, NiP and Zr4+ in the layered assembly is essential for the functional hybrid photoelectrode.
Chronoamperograms for all photoelectrodes were recorded at an applied potential, Eappl, of 0.3 V vs. RHE (Table 1 and Fig. 4b) and at Eappl = 0.5 V vs. RHE (Fig. S10†) under chopped light irradiation and confirmed the trends observed by LSV. Cathodic photocurrents for NiO|RuP3 (|j| ∼ 0.5 μA cm−2) and for NiO|RuP3–Zr4+ (|j| ∼ 0.76 μA cm−2) were small at Eappl = 0.3 V vs. RHE. The photocurrent of a NiO|RuP3–NiP electrode (|j| = 0.94 μA cm−2) at Eappl = 0.3 V vs. RHE was more than six times smaller than the photocurrent achieved with a NiO|RuP3–Zr4+–NiP electrode (initial photocurrent |j| = 9.97 μA cm−2 stabilised to 6.40 μA cm−2 after 100 s).
The photoelectrodes were also investigated in the presence of DTDP as SEA. A UV-vis spectrum of NiP in solution in the presence and absence of DTDP (1 mM) shows no differences, confirming the stability of the catalyst in the presence of DTDP (Fig. S11†). As expected, the presence of a soluble SEA in the electrolyte solution enhanced the photocurrents observed for the NiO|RuP3 (|j| = 3.0 μA cm−2) and NiO|RuP3–Zr4+ electrodes (|j| = 7.6 μA cm−2) at Eappl = 0.3 V vs. RHE (Fig. S12†). A significant increase in photocurrent was also found for a NiO∣RuP3–Zr4+–NiP electrode in the presence of DTDP in solution (|j| = 14.0 μA cm−2) compared to a SEA-free system (|j| = 6.4 μA cm−2). This suggests that surface-bound NiP is efficiently reduced by the generated photoelectrons and electron transfer from the reduced catalyst to the dissolved SEA in the electrolyte solution is faster than competing charge recombination. An increased photocurrent in the presence of DTDP suggests that the reduction of the SEA is faster than NiP-promoted catalysis.
The effect of the ratio of dye and catalyst was also studied by preparing electrodes with either two layers of dye, NiO|(RuP3–Zr4+)2–NiP, or two layers of catalyst, NiO|RuP3–(Zr4+–NiP)2. The photocurrent generated by a NiO|(RuP3–Zr4+)2–NiP electrode after 100 s chronoamperometry at Eappl = 0.3 V vs. RHE (|j| = 2.18 μA cm−2) was almost three times lower than the photocurrent of a NiO|RuP3–Zr4+–NiP electrode (Table 1). In contrast, approximately 40% increase in photocurrent was observed for a NiO|RuP3–(Zr4+–NiP)2 electrode (|j| = 8.82 μA cm−2). These experiments confirmed that there is a significant dependence of the number of layers on the photocurrent response and show that transient photocurrents generated by dye-sensitised NiO electrodes are dependent on the strategy used to co-immobilise dye and catalyst on the surface. This layer-by-layer approach has previously been successful for dye-sensitised photoanodes for water oxidation,36 but has not yet been explored for fuel-forming photocathodes.
The formation of H2 at the NiO|RuP3–Zr4+–NiP electrode was then studied by controlled potential photoelectrolysis (CPPE; Fig. 5). Irradiation of the NiO|RuP3–Zr4+–NiP and NiO|RuP3–(Zr4+–NiP)2 electrodes at Eappl = 0.3 V vs. RHE in a two-compartment PEC cell generated 6.11 ± 0.68 and 6.8 ± 0.9 nmol H2 in the headspace (analysed by gas chromatography with N2 carrier gas) with a faradaic efficiency of 8.6 ± 2.3% and 10.1 ± 1.8%, respectively (Table S2†). Increasing the light intensity to 200 mW cm−2 or using an Eappl = 0.5 V vs. RHE did not alter the H2 production rate nor improve the faradaic efficiency for NiO|RuP3–Zr4+–NiP. In the absence of NiP or in the dark, no H2 generation was observed. NiO|RuP3–NiP and NiO|(RuP3–Zr4+)2–NiP electrodes produced only traces of H2 below the limit of quantification (LOQ) of the thermal conductivity detector. The low activity of the NiO|RuP3–Zr4+–NiP electrode is likely due to inefficient charge transfer dynamics at the NiO|RuP3 interface and between reduced NiP and oxidised RuP3 or NiO (Fig. 2b). Nevertheless, confirmation of H2 evolution at the photocathode is an important step towards the goal of implementing dye-sensitised NiO photocathodes in full water splitting PEC cells.11c,13
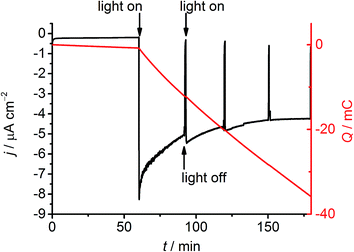 |
| Fig. 5 CPPE of a NiO|RuP3–Zr4+–NiP photoelectrode (1 cm2) at Eappl = 0.3 V vs. RHE in Na2SO4 (0.5 M, pH 3) at room temperature. Electrolysis was performed in a 2-compartment PEC cell with the working and counter compartment separated by a Nafion membrane. The working electrode was held in the dark for 1 h, followed by irradiation for 2 h using a solar light simulator (100 mW cm−2, AM1.5G filter, λ > 400 nm). | |
Post-catalysis characterisation
The electrode stability was further examined by ICP-OES analysis of the Ru content in both electrolyte solution and on the electrodes following 2 h CPPE at Eappl = 0.3 V vs. RHE. For NiO|RuP3–Zr4+–NiP a substantial amount of the initially loaded Ru (6.3 ± 3.1 nmol cm−2) was recovered from the used electrodes (3.4–7.4 nmol Ru cm−2) upon desorption in aqueous NaOH (0.1 M). Almost no Ru leaked into the electrolyte solution of the working or counter compartments (<0.2 nmol total Ru content). The opposite was observed for the NiO|RuP3–NiP electrodes after 2 h CPPE and 4.9–5.3 nmol total Ru content were found in the electrolyte solution of the working compartment and very little Ru (0.39–0.74 nmol cm−2) was recovered from the used working electrode. The Zr4+ interlayer might contribute to stabilising RuP3 on the surface of NiO electrodes under CPPE conditions. The stability of the NiO|RuP3–Zr4+–NiP working electrodes against material degradation was also confirmed by the lack of observable changes in the cyclic voltammograms before and after CPPE (Fig. S13†) and a significant alteration for NiO|RuP3–Zr4+ electrodes after CPPE at 0 V vs. RHE (Fig. S14†), indicating material instability of the latter.
The XPS spectra of a NiO|RuP3–Zr4+–NiP electrode were recorded and confirmed the presence of both RuP3 (281 eV, Ru 3d5/2) and Zr4+ (182.6 and 185 eV for Zr 3d5/2 and Zr 3d3/2, respectively) before and after 2 h CPPE at Eappl = 0.3 V vs. RHE (Fig. S7†). No new peaks in the Ru 3d5/2 region were observed after CPPE to indicate formation of Ru/RuOx particles. The presence and integrity of NiP on the NiO|RuP3–Zr4+–NiP electrode after CPPE could not unambiguously be confirmed by XPS due to the presence of the NiO. However, the stability of NiP on the electrode surface of a mesostructured TiO2 electrode under reducing conditions (Eappl = −0.25 V vs. RHE) in the dark in otherwise identical aqueous electrolyte solution (0.1 M Na2SO4, pH 3) has previously been confirmed.22
Mechanistic interpretation
Visible light irradiation of RuP3 generates RuP3*, which can in principle be quenched by two different mechanisms in the NiO|RuP3–Zr4+–NiP assembly: (a) oxidative quenching of RuP3* (E(RuP3+/RuP3*) ∼ −0.78 V vs. the normal hydrogen electrode (NHE), HOMO–LUMO gap EH–L(RuP3) = 2.19 eV, λem = 567 nm, Fig. S15†)37 by NiP, followed by hole injection from the oxidised RuP3+ (E(RuP3+/RuP3) ∼ 1.41 V vs. NHE, Fig. S16†) into NiO (EVB(NiO) = 0.57 V vs. NHE at pH 3);38 or (b) reductive quenching of RuP3* by fast electron transfer from NiO into the HOMO of the dye to form the reduced species RuP3− (E(RuP3*/RuP3−) ∼ 0.80 V vs. NHE, Fig. 2b).39RuP3− has a sufficiently negative ground state reduction potential (E(RuP3/RuP3−) ∼ −1.29 V vs. NHE)39 to provide driving force for reduction of NiP (E(NiII/I) = −0.35 V vs. NHE at pH 4.5).17a The reductive quenching mechanism for the NiO|RuP3–Zr4+–NiP assembly is much more likely since hole injection from a dye into NiO happens on very fast timescales of hundreds of femto- to picoseconds.13,15a Additionally, spectroscopic studies of a homogenous RuP–NiP system for photocatalytic H2 generation have shown previously that RuP* does not directly inject electrons into NiP in solution or when both molecules are anchored on ZrO2 as a non-injecting matrix. Reductive quenching by a SED or p-NiO yields RuP−, which was shown to efficiently reduce NiP.17a Reductive quenching of the NiO|RuP3–Zr4+–NiP system would provide the catalyst with an overpotential of ∼0.9 V (Fig. 2b).
Our results also suggest an important contribution of the Zr4+ interlayer to the efficiency of electron transfer away from the electrode surface to the associated catalyst. As Zr4+ is inert against reduction, it is unlikely that the Zr4+ coordinated to RuP3 and NiP is acting as an electron relay similar to TiO2 in H2 evolving dye–TiO2–catalyst suspension systems.18 It is more likely that the Zr4+ layer prevents NiP from binding directly on the NiO surface in close proximity to NiO|RuP3, and that spatial separation of the reduced catalyst from the generated holes in NiO is beneficial to avoid charge recombination which is fast when dye and catalyst are in close proximity.13 Reports on the catalytic activity of photoanodes for water oxidation showed that stability was enhanced when the catalyst was spatially separated from the dye-sensitised electrode.25d,36a,40 Spectroscopic studies of a TiO2|RuP3–Zr4+–catalyst photoanode demonstrated that electron back transfer was slowed down significantly compared to a TiO2|catalyst electrode,25b which was assigned to increased spatial separation. Similar effects were also found for electron transfer between photoexcited TiO2 and cobaloxime catalysts with different linker lengths.41 These experiments show the high potential of using rationally designed dye–catalyst assemblies on photocathodes.
Conclusions
A dye-sensitised photocathode with a co-immobilised nickel catalyst for light driven H2 generation in water has been reported. Co-deposition of the Ru dye RuP3 and Ni catalyst NiP on the p-type semiconductor NiO in a supramolecular assembly of Zr4+-phosphonates provided us with a tool to control spatial arrangement of individual species without the need for elaborate chemical synthesis of dye–linker–catalyst dyads. This layer-by-layer approach keeps the catalyst in close proximity to the dye, but increases the distance to the semiconductor electrode. Our PEC experiments confirm that directed forward electron transfer from the excited dye to the catalyst is efficient and recombination kinetics are slowed down. The catalyst was therefore able to turn over and the hybrid electrode able to photo-generate H2 at an electrochemical underpotential, thereby demonstrating the potential of this system to store light in the chemical bonds of H2. Layer-by-layer assembly of dye and catalyst is therefore established as a novel strategy to produce molecule-based photocathodes for H2 evolution.
The efficiency of the presented system can be improved in the future by optimising the NiO|dye interface such as developing phosphonated push–pull dyes optimised for p-NiO,12 and fine-tuning of the H2 evolution catalyst. Further work will also include the synthesis and investigation of dyes, which are better suited to inject holes into the NiO valence band. Optimised molecule-containing photocathodes might ultimately become an attractive component for use in PEC cells for full water splitting.11d,22
Experimental section
Materials and methods
NiP,17aRuP,35 and RuP3
24 (Fig. 1) were synthesised and characterised as previously reported. Chemicals for analytical measurements were purchased in the highest available purity and used without further purification. Ni(NO3)2·6H2O (Fisher Scientific, extra pure, 250 g) and hexamethylenetetramine (Sigma Aldrich, ReagentPlus, 99%) were used for the preparation of NiO electrodes. ITO nanopowder (Sigma Aldrich, particle size below 50 nm) was used for the preparation of mesostructured ITO electrodes. All electrochemical and analytical measurements were performed using Milli-Q® H2O (R > 18 MΩ cm). ITO-covered glass sheets (Vision Tek Systems Ltd., R = 12 Ω cm−2, thickness 1.1 mm) were cut into 3 × 1 cm2 slides for preparation of working electrodes.
Physical characterisation
An FEI Phillips XL30 SFEG SEM was used in the Electron Microscopy Suite in the Cavendish Laboratory, University of Cambridge. Powder X-ray diffraction (XRD) analysis was performed using a PANalytical BV X'Pert Pro X-ray diffractometer in the Department of Chemistry, University of Cambridge. XPS analysis was performed at the NEXUS XPS facility at Newcastle University. XPS spectra were calibrated to the C 1s signal at 284.8 eV. Quantification of Ni and Ru on the electrodes via ICP-OES (PerkinElmer Optima 2100 DV spectrometer) was carried out at the Department of Geography, University of Cambridge. High-resolution ATR-IR spectra were recorded on a Thermo Scientific Nicolet iS 50 FT-IR spectrometer with an ATR unit. UV-vis absorption spectra of electrodes were recorded in transmission mode in air, and UV-vis solution spectra were recorded in a quartz glass cuvette (1 cm path length) with a Varian Cary 50 UV-vis spectrophotometer. Fluorescence emission spectra of RuP3 in Na2SO4 (0.1 M, pH 3) were measured with an Edinburgh Instruments FS5 spectrofluorometer.
Electrochemical impedance spectroscopy
Electrochemical impedance spectroscopy (EIS) was performed on an IviumStat potentiostat in the frequency range of 100 kHz to 0.1 Hz in aqueous Na2SO4 solution (0.1 M, pH 3, 5 and 7). An equivalent circuit (inset Fig. S4†) consisting of electrolyte solution resistance (Rs), constant phase element (CPE), and interfacial charge transfer resistance (RCT) was fitted to Nyquist plots obtained at different potentials in ZView® (Scribner Associates Inc.) to retrieve CSC values required to form a Mott–Schottky plot. The Mott–Schottky equation,
, where CSC is the interfacial capacitance, A is the interfacial area, N the density of acceptors, V the applied potential, Vfb the flatband potential, kB the Boltzmann constant, T the absolute temperature, and e the electronic charge, was used to calculate the flatband potential of NiO. 1/CSC2 plotted against applied potential results in a straight line with the intercept being equal to Vfb + kBT/e. The negative slope is indicative of the p-type character of the NiO electrodes.
Preparation of nanostructured NiO electrodes26b
ITO covered glass slides (3 × 1 cm2) were cleaned by successive sonication in ethanol and acetone for 10 min, respectively. After drying in air, the conductive surface was confined to ca. 1 × 1.5 cm2 with electrical tape. The ITO glass slides were placed at approximately 45° with the conductive side facing down into separate vials and a solution of Ni(NiO3)2·6H2O and hexamethylenetetramine (250 mM each, 6 mL) was added to each vial. For hydrothermal growth of the films, the vials were placed into an oven (Thermo Scientific Heratherm) for 15, 30, 45 or 60 min at 90 °C and the reaction was stopped by the immediate addition of distilled water. The slides were rinsed with water, dried in air and the tape removed before the slides were annealed in a furnace (Carbolite) at 450 °C in air for 30 min (heating rate 20 °C min−1), and left to cool to room temperature in the furnace chamber.
Preparation of mesostructured ITO electrodes32
ITO covered glass slides (3 × 1 cm2) were cleaned by heating them in a mixture of NH3(conc.)/H2O/H2O2(30%) (1
:
5
:
1) at 70 °C for 30 min. The slides were rinsed with distilled water and dried in an oven at 180 °C for 1 h. The surface of the conductive side was confined with Scotch tape to circular 0.28 cm2. ITO nanopowder (20% w/w) was sonicated in EtOH (5 M acetic acid) for 1 hour and then doctor bladed on the ITO support. After drying in air, the tape was removed and the electrodes were annealed in a furnace (Carbolite) at 400 °C in air for 1 h (4 °C min−1 heating rate) and left to cool to room temperature in the oven chamber.
Assembly of molecular photocathodes
The layer-by-layer deposition of dye (RuP3 or RuP) and catalyst (NiP) was achieved by sequential immersion of the electrodes in solutions containing the molecular compounds at room temperature. NiO electrodes were submerged in solutions of RuP3 or RuP (1 mM in H2O, overnight, washed with H2O and EtOH), ZrOCl2 (5 mM in EtOH (60% v/v in H2O), 2 h, washed with H2O and EtOH) and NiP (0.5 mM in MeOH, 2–3 h, washed with MeOH) to build up the supramolecular layered assemblies. The electrodes were dried in a stream of N2 after each immobilisation step. Multiple (n) catalyst and dye layers were assembled by repeating the immobilisation cycles n times. RuP3 sensitised mesostructured ITO electrodes (ITO|RuP3) for controls were prepared according to the same procedure. The electrodes were stored in the dark prior use.
Quantification of immobilised compounds on NiO
(A) Quantification of RuP3 by UV-vis spectrophotometry.
A NiO|RuP3 electrode was immersed in aqueous NaOH (0.1 M, 1.0 mL) for 5 min to desorb the phosphonated species. The absorbance of the resulting solution at λ = 467 and 297 nm was used to determine the amount of RuP3 detached from the surface (assuming quantitative detachment of phosphonic acids in pH 13 solution).
(B) Quantification of Ru, and Ni via ICP-OES.
Surface-bound species were detached by immersing the electrodes in aqueous NaOH (0.1 M, 1.0 mL) for 5 min. The electrodes were rinsed with 10 mL H2O and then HNO3 (2% v/v) was added to a final volume of 25 mL. Samples were prepared and analysed from at least two individual electrodes for each condition and the averages are reported. Errors are given as maximum deviation from the average.
Determination of RuP3 oxidation potential
E(RuP3+/RuP3) was determined by recording a CV of RuP3 in Na2SO4 (0.1 M, pH 3) with a boron doped diamond working, Ag/AgCl/KCl(sat.) reference and Pt mesh counter electrode. The HOMO–LUMO gap EH–L(RuP3) was determined as the intersection of the normalised absorption and emission spectra of RuP3 in Na2SO4 (0.1 M, pH 3).24E(RuP3+/RuP3*) was estimated by E(RuP3+/RuP3*) = E(RuP3+/RuP3) − EH–L(RuP3).
Photoelectrochemistry
Electrochemical measurements were performed on an Ivium CompactStat potentiostat using a three-electrode configuration in a custom-made cell with a flat borosilicate window for PEC experiments. The prepared dye-sensitised NiO slides (1 cm2 geometrical surface area confined with electrical tape) were studied as working electrodes. A Pt mesh counter electrode, and a Ag/AgCl/KCl(sat.) reference electrode were used in aqueous electrolyte solution (0.1 M Na2SO4, pH 3). Prior to any measurements, all solutions were purged for at least 10 min with N2 to remove O2. PEC experiments were performed under irradiation from the back-side of the electrodes with visible light (λ > 400 nm, UQG Optics filter) using a solar light simulator (Newport Oriel, 150 W, 100 mW cm−2) equipped with an AM1.5G and IR water filter.
CPPE was carried out in a custom-made 2-compartment PEC cell separated by a Nafion membrane (quartz glass window, 1.5 cm diameter). In the working compartment, 14.5 mL of electrolyte solution were used, leaving a gas headspace of 4.9 mL. In the counter compartment, 4.5 mL of electrolyte solution were used, leaving a gas headspace of 3.1 mL. Both compartments were purged prior to electrolysis with N2 containing CH4 (2%) as internal standard for gas chromatography measurements. The electrolyte solution (0.5 M Na2SO4, pH 3) in both compartments was stirred during the experiments. The amount of H2 in the headspace of the electrolysis cell was quantified by an Agilent 7890A Series gas chromatograph equipped with a 5 Å molecular sieve column. The GC oven temperature was kept constant at 45 °C, N2 was used as a carrier gas at an approximate flow rate of 3 mL min−1 and a thermal conductivity detector was used. In a standard experiment, the working electrode was held at the respective potential (Eappl) in the dark for the first h, and after confirming the absence of headspace H2, it was exposed to visible light (λ > 400 nm, 100 or 200 mW cm−2) for 2 h at Eappl. All CPPE experiments were carried out at least three times, unless noted otherwise. The mean values of the measurements are reported along with their standard errors.17a
Acknowledgements
We gratefully acknowledge financial support by the Christian Doppler Research Association (Austrian Federal Ministry of Science, Research, and Economy and the National Foundation for Research, Technology, and Development), the OMV Group (E.R. and M.A.G.), the EPSRC NanoDTC in Cambridge (EP/L015978/1; E.R. and C.E.C.), and the World Premier International Research Center Initiative (WPI), MEXT, Japan (K.L.O.). XPS spectra were measured at the National EPSRC XPS User's Service (NEXUS) research facility at Newcastle University, UK. Thanks also to Mr Benjamin Martindale for help with the XPS data analysis and helpful discussions and Mr Chris Rolfe at the Department of Geography at the University of Cambridge for help with the ICP measurements. We appreciate the help of Ms Janina Willkomm in optimising the synthesis of NiO electrodes and Dr Julien Warnan for helpful suggestions and comments on the manuscript.
References
- S. Mathew, A. Yella, P. Gao, R. Humphry-Baker, B. F. E. Curchod, N. Ashari-Astani, I. Tavernelli, U. Rothlisberger, M. K. Nazeeruddin and M. Grätzel, Nat. Chem., 2014, 6, 242–247 CrossRef CAS PubMed
.
-
(a) C.-Y. Lin, Y.-H. Lai, D. Mersch and E. Reisner, Chem. Sci., 2012, 3, 3482–3487 RSC
;
(b) M. S. Prévot and K. Sivula, J. Phys. Chem. C, 2013, 117, 17879–17893 CrossRef
.
-
(a) T. R. Cook, D. K. Dogutan, S. Y. Reece, Y. Surendranath, T. S. Teets and D. G. Nocera, Chem. Rev., 2010, 110, 6474–6502 CrossRef CAS PubMed
;
(b) M. G. Walter, E. L. Warren, J. R. McKone, S. W. Boettcher, Q. Mi, E. A. Santori and N. S. Lewis, Chem. Rev., 2010, 110, 6446–6473 CrossRef CAS PubMed
;
(c) Y.-H. Lai, D. W. Palm and E. Reisner, Adv. Energy Mater., 2015, 5, 1501668 Search PubMed
;
(d) F. F. Abdi, L. Han, A. H. M. Smets, M. Zeman, B. Dam and R. van de Krol, Nat. Commun., 2013, 4, 2195 Search PubMed
.
- Z. Yu, F. Li and L. Sun, Energy Environ. Sci., 2015, 8, 760–775 CAS
.
-
(a) M. P. Stewart, M.-H. Ho, S. Wiese, M. L. Lindstrom, C. E. Thogerson, S. Raugei, R. M. Bullock and M. L. Helm, J. Am. Chem. Soc., 2013, 135, 6033–6046 CrossRef CAS PubMed
;
(b) J. Willkomm, N. M. Muresan and E. Reisner, Chem. Sci., 2015, 6, 2727–2736 RSC
.
- R. Bhosale, J. Mišek, N. Sakai and S. Matile, Chem. Soc. Rev., 2010, 39, 138–149 RSC
.
- A. Reynal, F. Lakadamyali, M. A. Gross, E. Reisner and J. R. Durrant, Energy Environ. Sci., 2013, 6, 3291–3300 CAS
.
-
(a) F. Lakadamyali and E. Reisner, Chem. Commun., 2011, 47, 1695–1697 RSC
;
(b) C. A. Caputo, M. A. Gross, V. W. Lau, C. Cavazza, B. V. Lotsch and E. Reisner, Angew. Chem., Int. Ed., 2014, 53, 11538–11542 CrossRef CAS PubMed
;
(c) B. C. M. Martindale, G. A. M. Hutton, C. A. Caputo and E. Reisner, J. Am. Chem. Soc., 2015, 137, 6018–6025 CrossRef CAS PubMed
;
(d) J. Willkomm, K. L. Orchard, A. Reynal, E. Pastor, J. R. Durrant and E. Reisner, Chem. Soc. Rev., 2016, 45, 9–23 RSC
.
-
(a) B. Kumar, M. Beyler, C. P. Kubiak and S. Ott, Chem.–Eur. J., 2012, 18, 1295–1298 CrossRef CAS PubMed
;
(b) R. N. Dominey, N. S. Lewis, J. A. Bruce, D. C. Bookbinder and M. S. Wrighton, J. Am. Chem. Soc., 1982, 104, 467–482 CrossRef CAS
;
(c) J. Seo, R. T. Pekarek and M. J. Rose, Chem. Commun., 2015, 51, 13264–13267 RSC
;
(d) J. R. McKone, E. L. Warren, M. J. Bierman, S. W. Boettcher, B. S. Brunschwig, N. S. Lewis and H. B. Gray, Energy Environ. Sci., 2011, 4, 3573–3583 RSC
;
(e) Y.-H. Lai, H. S. Park, J. Z. Zhang, P. D. Matthews, D. S. Wright and E. Reisner, Chem.–Eur. J., 2015, 21, 3919–3923 CrossRef CAS PubMed
.
-
(a) D. Cedeno, A. Krawicz, P. Doak, M. Yu, J. B. Neaton and G. F. Moore, J. Phys. Chem. Lett., 2014, 5, 3222–3226 CrossRef CAS PubMed
;
(b) A. Krawicz, J. Yang, E. Anzenberg, J. Yano, I. D. Sharp and G. F. Moore, J. Am. Chem. Soc., 2013, 135, 11861–11868 CrossRef CAS PubMed
.
-
(a) C. E. Castillo, M. Gennari, T. Stoll, J. Fortage, A. Deronzier, M.-N. Collomb, M. Sandroni, F. Légalité, E. Blart, Y. Pellegrin, C. Delacote, M. Boujtita, F. Odobel, P. Rannou and S. Sadki, J. Phys. Chem. C, 2015, 119, 5806–5818 CrossRef CAS
;
(b) P. Meng, M. Wang, Y. Yang, S. Zhang and L. Sun, J. Mater. Chem. A, 2015, 3, 18852–18859 RSC
;
(c) K. Fan, F. Li, L. Wang, Q. Daniel, E. Gabrielsson and L. Sun, Phys. Chem. Chem. Phys., 2014, 16, 25234–25240 RSC
;
(d) F. Li, K. Fan, B. Xu, E. Gabrielsson, Q. Daniel, L. Li and L. Sun, J. Am. Chem. Soc., 2015, 137, 9153–9159 CrossRef CAS PubMed
;
(e) Z. Ji, M. He, Z. Huang, U. Ozkan and Y. Wu, J. Am. Chem. Soc., 2013, 135, 11696–11699 CrossRef CAS PubMed
;
(f) K. A. Click, D. R. Beauchamp, Z. Huang, W. Chen and Y. Wu, J. Am. Chem. Soc., 2016, 138, 1174–1179 CrossRef CAS PubMed
.
- J. Massin, M. Bräutigam, N. Kaeffer, N. Queyriaux, M. J. Field, F. H. Schacher, J. Popp, M. Chavarot-Kerlidou, B. Dietzek and V. Artero, Interface Focus, 2015, 5, 20140083 CrossRef PubMed
.
- J. M. Gardner, M. Beyler, M. Karnahl, S. Tschierlei, S. Ott and L. Hammarström, J. Am. Chem. Soc., 2012, 134, 19322–19325 CrossRef CAS PubMed
.
- L. Li, L. Duan, F. Wen, C. Li, M. Wang, A. Hagfeldt and L. Sun, Chem. Commun., 2012, 48, 988–990 RSC
.
-
(a) A. Morandeira, G. Boschloo, A. Hagfeldt and L. Hammarström, J. Phys. Chem. C, 2008, 112, 9530–9537 CrossRef CAS
;
(b) A. Morandeira, G. Boschloo, A. Hagfeldt and L. Hammarström, J. Phys. Chem. B, 2005, 109, 19403–19410 CrossRef CAS PubMed
;
(c) E. A. Gibson, A. L. Smeigh, L. Le Pleux, J. Fortage, G. Boschloo, E. Blart, Y. Pellegrin, F. Odobel, A. Hagfeldt and L. Hammarström, Angew. Chem., Int. Ed., 2009, 48, 4402–4405 CrossRef CAS PubMed
.
-
(a) T. M. McCormick, Z. Han, D. J. Weinberg, W. W. Brennessel, P. L. Holland and R. Eisenberg, Inorg. Chem., 2011, 50, 10660–10666 CrossRef CAS PubMed
;
(b) B. S. Veldkamp, W.-S. Han, S. M. Dyar, S. W. Eaton, M. A. Ratner and M. R. Wasielewski, Energy Environ. Sci., 2013, 6, 1917–1928 RSC
.
-
(a) M. A. Gross, A. Reynal, J. R. Durrant and E. Reisner, J. Am. Chem. Soc., 2014, 136, 356–366 CrossRef CAS PubMed
;
(b) D. W. Wakerley, M. A. Gross and E. Reisner, Chem. Commun., 2014, 50, 15995–15998 RSC
;
(c) P. Rodriguez-Maciá, A. Dutta, W. Lubitz, W. J. Shaw and O. Rüdiger, Angew. Chem., Int. Ed., 2015, 54, 12303–12307 CrossRef PubMed
;
(d) A. Dutta, S. Lense, J. Hou, M. H. Engelhard, J. A. S. Roberts and W. J. Shaw, J. Am. Chem. Soc., 2013, 135, 18490–18496 CrossRef CAS PubMed
.
- F. Lakadamyali, A. Reynal, M. Kato, J. R. Durrant and E. Reisner, Chem.–Eur. J., 2012, 18, 15464–15475 CrossRef CAS PubMed
.
- S. Horvath, L. E. Fernandez, A. V. Soudackov and S. Hammes-Schiffer, Proc. Natl. Acad. Sci. U. S. A., 2012, 109, 15663–15998 CrossRef CAS PubMed
.
- A. Le Goff, V. Artero, B. Jousselme, P. D. Tran, N. Guillet, R. Métayé, A. Fihri, S. Palacin and M. Fontecave, Science, 2009, 326, 1384–1387 CrossRef CAS PubMed
.
- P. D. Tran, A. Le Goff, J. Heidkamp, B. Jousselme, N. Guillet, S. Palacin, H. Dau, M. Fontecave and V. Artero, Angew. Chem., Int. Ed., 2011, 50, 1371–1374 CrossRef CAS PubMed
.
- T. E. Rosser, M. A. Gross, Y.-H. Lai and E. Reisner, Chem. Sci., 2016 10.1039/c1035sc04863j
, in press.
- G. F. Moore and I. D. Sharp, J. Phys. Chem. Lett., 2013, 4, 568–572 CrossRef CAS PubMed
.
- H. Park, E. Bae, J.-J. Lee, J. Park and W. Choi, J. Phys. Chem. B, 2006, 110, 8740–8749 CrossRef CAS PubMed
.
-
(a) C. Queffélec, M. Petit, P. Janvier, D. A. Knight and B. Bujoli, Chem. Rev., 2012, 112, 3777–3807 CrossRef PubMed
;
(b) K. Hanson, D. A. Torelli, A. K. Vannucci, M. K. Brennaman, H. Luo, L. Alibabaei, W. Song, D. L. Ashford, M. R. Norris, C. R. K. Glasson, J. J. Concepcion and T. J. Meyer, Angew. Chem., Int. Ed., 2012, 51, 12782–12785 CrossRef CAS PubMed
;
(c) K. Kanaizuka, S. Kato, H. Moriyama and C. Pac, Res. Chem. Intermed., 2007, 33, 91–100 CrossRef CAS
;
(d) X. Ding, Y. Gao, L. Zhang, Z. Yu, J. Liu and L. Sun, ACS Catal., 2014, 4, 2347–2350 CrossRef CAS
.
-
(a) A. Xiao, S. Zhou, C. Zuo, Y. Zhuan and X. Ding, Mater. Res. Bull., 2015, 61, 54–57 CrossRef CAS
;
(b) Y. Y. Xi, D. Li, A. B. Djurišić, M. H. Xie, K. Y. K. Man and W. K. Chan, Electrochem. Solid-State Lett., 2008, 11, D56–D59 CrossRef CAS
;
(c) L. Lepleux, B. Chavillon, Y. Pellegrin, E. Blart, L. Cario, S. Jobic and F. Odobel, Inorg. Chem., 2009, 48, 8245–8250 CrossRef CAS PubMed
.
-
A. Clearfield and K. Demadis, Metal Phosphonate Chemistry: From Synthesis to Applications, RSC, Cambridge, 2011 Search PubMed
.
-
(a) M. Natali, A. Luisa, E. Iengo and F. Scandola, Chem. Commun., 2014, 50, 1842–1844 RSC
;
(b) Y. Sun, J. Sun, J. R. Long, P. Yang and C. J. Chang, Chem. Sci., 2013, 4, 118–124 RSC
;
(c) M. P. McLaughlin, T. M. McCormick, R. Eisenberg and P. L. Holland, Chem. Commun., 2011, 47, 7989–7991 RSC
;
(d) P. Du, J. Schneider, G. Luo, W. W. Brennessel and R. Eisenberg, Inorg. Chem., 2009, 48, 4952–4962 CrossRef CAS PubMed
.
- G. Boschloo and A. Hagfeldt, J. Phys. Chem. B, 2001, 105, 3039–3044 CrossRef CAS
.
-
(a) F. Odobel, Y. Pellegrin, E. A. Gibson, A. Hagfeldt, A. L. Smeigh and L. Hammarström, Coord. Chem. Rev., 2012, 256, 2414–2423 CrossRef CAS
;
(b) D. Dini, Y. Halpin, J. G. Vos and E. A. Gibson, Coord. Chem. Rev., 2015, 304–305, 179–201 CrossRef CAS
;
(c) G. Natu, Z. Huang, Z. Ji and Y. Wu, Langmuir, 2012, 28, 950–956 CrossRef CAS PubMed
.
-
(a) F. Odobel, B. Bujoli and D. Massiot, Chem. Mater., 2001, 13, 163–173 CrossRef CAS
;
(b) J. D. Wang, A. Clearfield and G.-Z. Peng, Mater. Chem. Phys., 1993, 35, 208–216 CrossRef CAS
.
- N. M. Muresan, J. Willkomm, D. Mersch, Y. Vaynzof and E. Reisner, Angew. Chem., Int. Ed., 2012, 51, 12749–12753 CrossRef CAS PubMed
.
- A. K. Das, M. H. Engelhard, R. M. Bullock and J. A. S. Roberts, Inorg. Chem., 2014, 53, 6875–6885 CrossRef CAS PubMed
.
- S. A. Paniagua, P. J. Hotchkiss, S. C. Jones, S. R. Marder, A. Mudalige, F. S. Marrikar, J. E. Pemberton and N. R. Armstrong, J. Phys. Chem. C, 2008, 112, 7809–7817 CAS
.
- I. Gillaizeau-Gauthier, F. Odobel, M. Alebbi, R. Argazzi, E. Costa, C. A. Bignozzi, P. Qu and G. J. Meyer, Inorg. Chem., 2001, 40, 6073–6079 CrossRef CAS PubMed
.
-
(a) A. M. Lapides, B. D. Sherman, M. K. Brennaman, C. J. Dares, K. R. Skinner, J. L. Templeton and T. J. Meyer, Chem. Sci., 2015, 6, 6398–6406 RSC
;
(b) X. Ding, Y. Gao, L. Ye, L. Zhang and L. Sun, ChemSusChem, 2015, 8, 3992–3995 CrossRef CAS PubMed
.
- This work, estimated by the intersection point of the normalised absorption and emission spectra of RuP3 in Na2SO4 (0.1 M, pH 3).
- This work, measured by electrochemical impedance spectroscopy of optimised NiO films in aqueous electrolyte solution.
- D. L. Ashford, M. K. Brennaman, R. J. Brown, S. Keinan, J. J. Concepcion, J. M. Papanikolas, J. L. Templeton and T. J. Meyer, Inorg. Chem., 2015, 54, 460–469 CrossRef CAS PubMed
.
-
(a) H.-J. Son, C. Prasittichai, J. E. Mondloch, L. Luo, J. Wu, D. W. Kim, O. K. Farha and J. T. Hupp, J. Am. Chem. Soc., 2013, 135, 11529–11532 CrossRef CAS PubMed
;
(b) K.-R. Wee, M. K. Brennaman, L. Alibabaei, B. H. Farnum, B. Sherman, A. M. Lapides and T. J. Meyer, J. Am. Chem. Soc., 2014, 136, 13514–13517 CrossRef CAS PubMed
.
- A. Reynal, J. Willkomm, N. M. Muresan, F. Lakadamyali, M. Planells, E. Reisner and J. R. Durrant, Chem. Commun., 2014, 50, 12768–12771 RSC
.
Footnote |
† Electronic supplementary information (ESI) available. See DOI: 10.1039/c6sc00715e. Additional data related to this publication are available at the University of Cambridge data repository (https://www.repository.cam.ac.uk/handle/1810/255990). |
|
This journal is © The Royal Society of Chemistry 2016 |
Click here to see how this site uses Cookies. View our privacy policy here.