DOI:
10.1039/D4SU00635F
(Perspective)
RSC Sustainability, 2025,
3, 781-803
Sustainable by (crystal) design: novel materials for agriculture via active ingredient cocrystallization
Received
9th October 2024
, Accepted 16th December 2024
First published on 19th December 2024
Abstract
Novel material design for sustainable development of agriculture is of key importance. In this regard, cocrystallization emerged as an effective laboratory synthesis as well as large-scale agricultural material production technique to enhance the efficiency of active ingredients by forming cocrystals with agriculturally compatible molecules and thereby improving their properties, such as moisture resistance, enzyme inhibition or nitrogen efficiency. This review provides a state of the art of this quickly developing area from the material design perspective and examines cocrystallized products for emerging applications in sustainable agriculture, such as novel fertilizer formulations that incorporate essential nutrients, as well as cocrystals for other applications, such as pest control. The chemical and crystal structures, bonding mechanisms, and the resulting properties of these cocrystals are discussed. Special attention is given to urea-based cocrystals. By integrating macro- (e.g., N, P, K, Ca, Mg and S) and micro-nutrients (e.g., Fe, Mn, Cu, Zn, B, Mo, Cl and Ni), these cocrystals provide novel nutrient delivery and management strategies. We then explore existing cocrystals that assist sustainable agriculture beyond nutrient delivery, e.g. herbicides, insecticides and fungicides. Finally, we discuss the potential routes to enhance agricultural cocrystal sustainability, such as novel methods of their synthesis, including mechanochemical processes.
Sustainability spotlight
From pesticides to fertilizers chemicals used in agriculture have had a significant impact on overall sustainability. Increasing population and intensifying farming practices combined with little to no new arable land increase the need for excessive use of synthetic fertilizers and pesticides, undermining soil health while contributing reactive and greenhouse gases to the environment after the application. The intrinsic diverse chemical and molecular properties of agricultural materials make them a major environmental concern. In particular, nitrogen fertilizers are soluble and volatile, while pesticides and other organic bio-active molecules have low solubility in water and are typically overapplied. Cocrystallization is only now finding its way into agriculture. Here, we provide a perspective on the present status and future opportunities of cocrystallization for more sustainable agriculture.
|
1. Introduction
New developments in sustainable agriculture, including controlled-release fertilizer and plant growth stimulant discovery and synthesis, can provide enhanced nutrient uptake and contribute to soil health.1 Making agriculture fully sustainable will require a fundamental shift in global food production methods.2 To bridge the gap between the desired increase in food demand and its supply under the constraints imposed by climate change, new materials need to be designed to possess tailored properties to address specific agricultural challenges.3 Nutrient management and delivery can be considered one such global challenge. Conventional nitrogen fertilizers are produced at ∼120 million metric tons per year and contribute to the release of reactive nitrogen compounds.4 These conventional N-based fertilizers are susceptible to nutrient loss, which is a cause of their low efficiency.5 N-loss has direct negative effects as it leads to crop yield reduction and economic losses, as well as nutrition insecurity. This is in addition to its negative footprint on the environment due to the reactive and greenhouse gas emissions, eutrophication, and water pollution.6
When conventional fertilizers release nutrients beyond the immediate plants' needs, the excess will not be absorbed by the plant. For example, after applying urea to the soil, it is hydrolyzed to form ammonium ions.7 Moreover, the excess ammonium ions further transform in the soil to nitrite followed by nitrate.6 The runoff of highly soluble nitrates into water bodies will lead to more algae growth and consequently deplete oxygen in the water and therefore cause eutrophication. Increasing harmful algal blooms in Lake Erie, a growing dead zone in the Gulf of Mexico, and hypoxia in the Chesapeake Bay continue to plague the U.S. and demonstrate the growing public concern about the harmful effects of excess nutrients.8 Moreover, nitrate in groundwater leads to the contamination of drinking water supplies. In this regard, from 1991 to 2003, over 4% of 5101 tested wells in the USA exceeded the EPA nitrate limit of 10 mg L−1, while in California's San Joaquin Valley, over 75% of samples surpassed the World Health Organization (WHO) permissible limit, affecting more than 275
000 people.9
Similarly, plant protection from pests and pathogens needs to be ensured10 by designing more efficient pesticides that can avoid negative effects on the environment and human health.11 Excessive use of pesticides and bioactive agrochemicals in general leads to short-term and acute adverse health effects on humans, and modulating their release properties via cocrystallization can control their environmental risks. The overuse of pesticides is due to their low solubility, which leads to the application of excessive amounts.12 Cocrystallization, in general, is well explored in the pharmaceutical industry as a promising strategy to improve the solubility of poorly soluble materials (based on the suitable coformer) but is yet to be fully employed in the agricultural sector, where it can help enhance pesticide bioavailability and reduce the need for over-application.13 Therefore, cocrystals formulated for agrochemical purposes can create a balanced release profile.14 The nutrient release can potentially be sustained and slowed while allowing for the enhanced release of pesticides or other agrochemicals in the structure. This controlled behavior ensures that nutrients remain available to plants over extended periods while reducing nutrient leaching into the environment while simultaneously maintaining effective pest control. Thus, cocrystallization can lead to a more sustainable agricultural approach by providing a relationship between the molecules that form cocrystals, which allows for efficient resource use and minimized environmental impact.
This review underscores the potential and significant advancements in crystal engineering that allow for the sustainable release of nutrients, which offer solutions to agricultural challenges and contribute to environmental sustainability, as shown in Fig. 1. That ensures better crop yields and mitigates environmental impact, which opens the door for a more sustainable future in agriculture.
 |
| Fig. 1 Material design via cocrystallization provides new functional materials for sustainable agriculture. In particular, nutrient-carrying cocrystals, those of active insecticide, herbicide and fungicide ingredients, are already available for large-scale testing. | |
2. Nutrient-containing agricultural cocrystals for sustainable plant nutrition
Plants need nutrients for growth and these are classified depending on the required quantity.15 As illustrated in Fig. 2, the macronutrients are N, Mg, P, S, K, and Ca, while the micronutrients are B, Cl, Cu, Fe, Mn, Mo, Co, and Zn.
 |
| Fig. 2 Classification of nutrients with primary and secondary macronutrients and micronutrients.15 The nutrients with dashed lines have recently been cocrystallized with urea for agricultural applications. | |
By far the largest opportunity to innovate in sustainable agriculture via cocrystallization emerges via the utility of nitrogen-carrying fertilizer urea as a complex molecule. Urea is a white crystalline material widely used in agriculture and it has a critical role in boosting crop yields.16 However, this essential fertilizer exhibits environmental stability challenges, such as absorbing moisture under humid conditions, which can lead to prompt hydrolysis and transformation from dry powder into particles.17 This affects the effectiveness of urea usage and leads to wasted fertilizer.
The traditional solution involves manufacturing complex slow-release coated materials based on sulfur or polymer-encapsulated urea granules or incorporating urease inhibitors into fertilizer formulations.18 These inhibitors delay the enzymatic conversion of urea to ammonia, but their effectiveness diminishes over time, and they add complexity and cost to the fertilizer production process. In this regard, cocrystallization is a promising strategy to address these limitations.19,20 This technique involves the careful selection and combination of urea with other compatible molecules to create a new crystalline material with tailored properties. This cocrystal offers the potential to overcome the stability challenges associated with pure urea.21 By strategically selecting a suitable cocrystal forming molecule, designed urea cocrystals can form that exhibit superior moisture resistance or urease inhibition properties. Additionally, the cocrystallization process could lead to enhanced thermal stability, hindering the decomposition of urea and subsequent ammonia gas release. This translates to a more reliable and environmentally friendly fertilizer with improved storage and handling characteristics.
Fundamentally, the possibility of urea being bonded with other molecules is due to the two lone pairs on the oxygen atom of the carbonyl group or the four protons of the N–H bonds.22 An H-bond acceptor can be an effective cocrystal partner by engaging with the two N–H groups of urea through a split hydrogen bond as shown in Fig. 3a, or through two separate interactions as in Fig. 3b. In addition, an H-bond acceptor can interact with the NH functional group as demonstrated in Fig. 3c. A ditopic donor–acceptor moiety can form an H-bond with oxygen in C
O and hydrogen in NH as shown in Fig. 3d. Furthermore, one or two lone pairs in the oxygen of the carbonyl group can interact with an H-donor through a single or two points as shown in Fig. 3e.22
 |
| Fig. 3 Five potential molecular interactions (a–e) within urea cocrystals resulting in novel nutrient-containing formulations.22 | |
Urea cocrystallization exhibits a range of advantages that enhance the performance and sustainability of urea fertilizers, as shown in Fig. 4. One of the most significant benefits is enhanced cocrystal stability, which achieves improved resistance to both moisture and heat.23 Cocrystallization reduces the tendency of urea to clump and dissolve prematurely, which means more efficient nutrient delivery to plants.22 Additionally, cocrystallized urea exhibits better thermal stability, which leads to the prevention of decomposition at higher temperatures and the maintenance of consistent performance under varying environmental conditions.24 Moreover, urea cocrystallization improves efficiency by addressing common issues associated with conventional urea fertilizers. For instance, it reduces the release of ammonia gas, a major source of nitrogen loss in agriculture, thus enhancing nitrogen use efficiency and minimizing environmental impact.21,25 Furthermore, cocrystals can be engineered to provide a balanced supply of essential macronutrients and micronutrients in a single product, promoting optimal plant growth and health. These advantages will lead to another significant advantage of urea cocrystallization, which is the ability to sustain nutrient release over time. By designing cocrystals for controlled nutrient release, farmers can ensure a steady supply of nutrients to crops, reducing the need for frequent fertilizer applications and improving overall efficiency. Additionally, some urea-based cocrystals can also function as pesticides, which can offer the dual benefits of nutrient supply and pest management in a single application (will be discussed in a separate section).
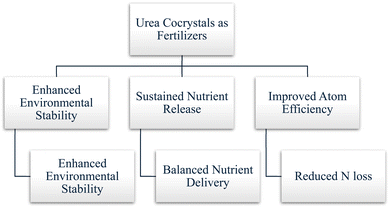 |
| Fig. 4 The potential of urea-based cocrystallized materials in agriculture. | |
2.1. Macronutrient (N, P, K, Ca, Mg and S) salt–urea-cocrystals
2.1.1. N-containing urea cocrystals.
Urea nitrate is a cocrystal that is formed from urea and nitric acid. The crystal consists of layered flat groups and features uronium ions (protonated urea) connected to nitrate ions by hydrogen bonds. These units connect to form chains through additional hydrogen bonds between oxygen and hydrogen atoms. Compared to regular urea, the carbon–oxygen bond in the uronium ion stretches slightly, while the carbon–nitrogen bond shortens. Further, the oxygen atom involved in the strongest hydrogen bond exhibits a longer nitrogen–oxygen distance compared to the others, which leads to a stretching effect.26 D. Joshua et al. prepared urea nitrate by dissolving urea in water under stirring. Then nitric acid was added dropwise to the solution while stirring, and the mixture was cooled using an ice bath to keep the temperature below 40 °C.27 While possessing high nitrogen content in two forms of high usability in agriculture, this cocrystal has a crucial limitation, which is its propensity to explode, thus limiting its applicability compared to solution-based alternatives, such as urea ammonium nitrate (UAN).27
2.1.2. P-containing urea cocrystals.
Urea–phosphoric acid or urea–phosphate is a commercial fertilizer compound that is cocrystallized urea with phosphoric acid. This compound delivers both nitrogen and phosphorus while minimizing nutrient loss. The reason can be due to the proximity between urea and phosphoric acid. This can slow the breakdown of urea by soil enzymes and reduce the amount of ammonia released into the atmosphere.28 This compound crystallizes in an orthorhombic crystal system. There are eight groups of two molecules (dimer units) packed within this unit cell.29 Hydrogen bonds in general arise due to electrostatic attractions between a hydrogen atom on one molecule and an electronegative atom on another. There is a relatively weak hydrogen bond established between NH in the urea molecule and an oxygen atom in the phosphoric acid molecule. There is another shorter hydrogen bond between the oxygen atom in urea and OH in phosphoric acid and this shorter length indicates a stronger bonding.29
In a solid form, it is a 17-44-0 fertilizer that is produced by several manufacturers, including Lifosa, Lithuania, and Haifa Group. It has the advantage of retarding the soil urease ability for enzymatic hydrolysis due to the existence of phosphoric acid leading to a reduction in ammonia gas emissions.30 Furthermore, replacing urea fertilizers with urea phosphate in Nile Delta soil (pH 7.4, 1.9% CaCO3) exhibited several improvements according to Moawad et al. In particular, urea phosphate slowed down the breakdown of urea and its conversion to nitrate, which prevented nitrite accumulation and minimized nitrogen loss through gas emissions. This resulted in a greater recovery of useable nitrogen throughout the experiment, which suggests that it can significantly enhance fertilizer efficiency compared to conventional pure urea.31
2.1.3. K-containing urea cocrystals.
Potassium has been virtually absent from the urea cocrystal landscape since it is difficult to polarize and form coordination bonds. One recently reported instance of a cocrystal involves urea, zinc (Zn), and potassium (K) in the form of ZnCl2–KCl–urea (ZnKU), which has two packing forms. The structure of this type of cocrystal will be discussed further in the Zn section, but it should be mentioned that ZnKU works as a nutrient provider and urease inhibitor.32 The work by Casali et al. proved the JBU residual activity in the presence of ZnKU, which rapidly decreased by increasing the concentration of the cocrystal. In the absence of the cocrystal, the activity was around 10 0%, then 70% at 2 μM, and 10% at 8 μM.32 Therefore, it has higher urease inhibition that leads to the reduction of the ammonia release. This could lead to more sustainable agricultural practices by promoting better crop yields with less environmental impact.
2.1.4. S-containing urea cocrystals.
The reaction between urea and sulfuric acid can lead to the formation of urea sulfate, which is also known as monocarbamide dihydrogen sulfate or 1-aminomethanamide dihydrogen tetraoxosulfate.33 This compound is usually used as an herbicide (or with other herbicides) and desiccant, but it is dangerous due to its caustic and corrosive behavior.34 However, it can be broken down quickly after being applied as a fertilizer, converting into urea and sulfate ions, which are safe compounds. It can be applied through irrigation or foliar methods and is also used to convert low-solubility minerals containing calcium and magnesium into more efficient nitrogen-based fertilizers.35 This means that urea sulfate can contribute to sustainability by enhancing fertilizer efficiency, improving nutrient availability in soils, and minimizing environmental impact. Moreover, its multifunctionality as an herbicide and fertilizer can reduce chemical inputs and promote more sustainable agricultural practices while protecting ecosystem health.
2.1.5. Mg-containing urea cocrystals.
2.1.5.1. MgSO4, Mg(H2PO4)2 and Mg(NO3)2–urea cocrystals.
The combination of nutrients in a single cocrystal is advantageous in sustainable agriculture. High urea-content cocrystals, such as MgSO4·6urea·0.5H2O, have been synthesized and exhibited vastly different thermal properties from pure urea. It showed no melting peak at 132 °C, typical for urea. Instead, they show new melting peaks at higher temperatures of around 210 °C, which means the higher stability of the cocrystallized urea over the conventional one.36 Similarly, Mg(H2PO4)2·4urea has a lack of a well-defined urea melting peak at 132 °C but displays apparent new peaks at 195 °C, likely resulting from the melting of the corresponding urea phosphate fragments.36 On the other hand, there was an endothermal peak observed at 135 °C for Mg(NO3)2·4urea·xH2O. This peak corresponds to the melting of crystalline water and the absence of a strong endothermal transition at 132 °C indicates that urea is incorporated into the new crystal structure, consequently resulting in stronger bonding.36 The use of these high-stability urea cocrystals, such as MgSO4·6urea·0.5H2O, Mg(H2PO4)2·4urea, and Mg(NO3)2·4urea·xH2O, has significant sustainability implications. The enhanced thermal stability of these cocrystals means that they can maintain their structure and function under a wider range of environmental conditions. This can lead to more efficient and prolonged nutrient release. This controlled release mechanism reduces the rapid volatilization and leaching of nitrogen, which are common with traditional urea fertilizers. By minimizing nitrogen loss, these cocrystals enhance nitrogen use efficiency, decreasing the environmental impact associated with nitrogen runoff and greenhouse gas emissions. Furthermore, the incorporation of additional nutrients like Mg and P in these cocrystals supports plant growth and soil health and therefore promotes more sustainable agricultural practices.
2.1.6. Ca-containing urea cocrystals.
2.1.6.1. CaSO4–urea cocrystals.
A recent excellent summary of utilizing gypsum with urea cocrystals for sustained-release fertilizers has been published.37 CaSO4·4urea is the most extensively studied urea cocrystal, primarily due to the widespread availability of gypsum and gypsum-derived waste, as shown in Fig. 5.38 Unlike pure urea, which exhibits a melting peak at 132 °C, CaSO4·4urea shows a melting point peak at approximately 210 °C.36 This shift is a direct indication of the stabilization of urea molecules in CaSO4·4urea crystals, which potentially reduces their environmental reactivity.39 Barčauskaitė et al. synthesized a CaSO4·4urea cocrystal using a 4
:
1 molar ratio of urea to calcium sulfate dihydrate.40 They utilized gypsum drywall powder and demonstrated that other gypsum sources could also be used.
 |
| Fig. 5 The process of using industrial by-product waste to produce CaSO4·4urea.38,40 | |
Brekalo et al. investigated the role of water in synthesizing CaSO4·4urea via ball milling through the two approaches of neat grinding (NG) and liquid-assisted grinding (LAG).41 NG experiments using hydrated calcium sulfate forms (hemihydrate and dihydrate) achieved approximately complete CaSO4·4urea conversion at both room temperature and 70 °C after 1 hour of milling, while anhydrous calcium sulfate showed minimal conversion. This highlights the essential role of water, further demonstrated by LAG experiments, where adding water to anhydrous mixtures resulted in low conversion regardless of water content.42 Comparing this to another study where added water accelerated a similar synthesis, the authors concluded that water directly present in the calcium sulfate structure, as opposed to externally added, proves more effective for CaSO4·4urea formation. However, water has a central role in CaSO4·4urea synthesis via ball milling, but not through the expected neutralization reaction. Instead, water pre-existing within the crystal structure of hydrated calcium sulfates (dihydrate and hemihydrate) acts as a catalyst. Compared to externally added water, this originally existing water in the structure offers unique advantages such as direct coordination to calcium (dihydrate) and mechanical disruption (hemihydrate). This might lead to the creation of internal stress during release, enhancing reactivity.
CaSO4·4urea exhibits lower solubility, slower dissolution, and higher nitrogen retention as represented in Fig. 6 (a–c). While urea releases 70% of its nitrogen as NH3 within 20 days, CaSO4·4urea barely releases any even after 90 days, which means a significant improvement in stability and potential for more sustainable and controlled nitrogen release in agricultural applications.42
 |
| Fig. 6 (a) NH3 emissions from urea and CaSO4·4urea (abbreviated as URCASU) until 50 hours from ref. 36, which was measured in silt loam soil. The measurements were taken over 48 hours under static conditions, with the chamber maintained at 23 °C and a relative humidity level of 50–60%.36 (b) NH3 emissions from the same compounds according to previous work41 but until 75 days. The measurement was done in soil, with either urea or CaSO4·4urea, which was added to a flask containing a thick layer of soil. The relative humidity was approximately 90% and the NH3 released was consistently captured in a 0.2 N H2SO4 solution and quantified using a methyl red indicator. Moreover, mini prills of urea served as the reference, while the urea cocrystal prepared mechanochemically was tested in its powdered form. However, the experiment was designed to compare the NH3 emissions from these two nitrogen sources under controlled conditions.41 (c) The kinetic dissolution of urea.41 The samples of urea and its cocrystal were formed into pellets using a hydraulic press. For the static dissolution test, a single pellet was placed in an Erlenmeyer flask containing distilled water and maintained at room temperature for 120 hours. A urea pellet served as the control. Dissolution rates were measured by taking 0.5 mL samples from the solution at regular intervals.41 | |
2.1.6.2. Ca(H2PO4)2 and Ca(NO3)2–urea cocrystals.
Ca(H2PO4)2·4urea also shows the same behavior as magnesium dihydrogen phosphate, which lacks a well-defined urea melting peak at 132 °C and instead, it has a new melting peak at around 197 °C, due to the existence of urea phosphates.36 Ca(NO3)2·urea thermally has a higher melting point compared to pure urea, around 155 °C, due to the boiling of liquid calcium nitrate. In Honer et al. accelerated experiments, they exposed Ca(H2PO4)2·4urea and Ca(NO3)2·4urea to 100% relative humidity (approximately 21 mm Hg) at 23 °C.35 Time-resolved images revealed that urea deliquesced rapidly, absorbing moisture and forming liquid droplets. Furthermore, Ca(NO3)2·4urea also deliquesced after one day. In contrast, Ca(H2PO4)2·4urea showed only minor moisture formation, which remained mostly surface-bound, not reaching a state similar to urea after one day of exposure. These compounds took until the third day of exposure to achieve comparable moisture absorption under 100% relative humidity. The authors concluded that this indicates that ionic cocrystal materials may inherit the stability properties of their inorganic parent compounds, stabilizing urea from hydrolysis and potentially reducing NH3 losses. This, in turn, promotes sustainability due to the lower negative effects on the environment.
2.2. Micronutrient (Fe, Mn, Cu, Zn, and Ni) salt–urea cocrystals
2.2.1. Fe–urea cocrystals.
An iron chloride complex with urea was synthesized by Ibrahim et al. by mixing solutions of the corresponding metal salts with urea in methanol. This colored solid was then isolated using filtration and dried and the resulting Fe-related compound was FeCl2·6U·3H2O.43 The thermal analysis of the Fe–urea complex showed a loss of water molecules in the thermal region of 42–159 °C as a stage. Further, in another stage from 159 to 290 °C, more water molecules were lost, accompanied by ammonium chloride, ammonia, hydrazine and nitrogen molecules. The first stage showed a 4.14% loss, while the second stage demonstrated a 45.38% loss due to the high quantity of released molecules from the structure. Furthermore, a third stage showed around 32% mass loss and the loss might belong to cyanuric acid and CO2 molecules in the range of 290–397 °C. The last stage, which can be ascribed to CO molecules, was at 397–642 °C with 3.60% mass loss.43
Iron is also a crucial element in the competition between plants and pathogens. By withholding iron, plants can limit pathogen growth. Additionally, iron aids in activating the plant immune system to resist infections.44 Thus, iron is indispensable for plant health and can be strategically utilized to combat bacterial and fungal infections. Guha et al. showed that incorporating iron with urea even in nanocomposites can enhance nutrient utilization and potentially increase plant resistance to pathogens.44 The antibacterial activity of the FeCl2–urea complex is evaluated and reaches around 18 and 14 mm mg−1 against Staphylococcus aureus bacteria and Candida albicans fungi.43 In general, iron is an essential micronutrient vital for various metabolic processes, such as chlorophyll synthesis and enzyme functions. It is important for photosynthesis, which leads to enabling plants to convert sunlight into energy. Iron deficiency can cause chlorosis (yellowing of leaves) and stunted growth.45
2.2.2. Mn–urea cocrystals.
Mn is involved in several physiological processes, such as photosynthesis, nitrogen metabolism, and enzyme synthesis.46 It is crucial for chloroplast formation and the production of specific enzymes. It can support plant defense against pathogens by aiding in the synthesis of lignin, which serves as a physical barrier, and boosting the activity of defense-related enzymes like peroxidases.47,48 Additionally, Mn might have urease inhibition properties, which could further influence nitrogen metabolism and utilization in plants.47
Manganese was complexed with urea in the work of Aghabozorg et al. to prepare manganese(II) hexakis (urea) perchlorate, [Mn(urea)6]·(ClO4)2.49 Ibrahim et al. prepared MnCl2·3urea·3H2O and MnCl2·6urea and examined the thermal decomposition. They revealed that MnCl2·3urea·3H2O had a three-stage decomposition behavior. The compound lost 3 water molecules, 1 urea molecule, 1 ammonium chloride molecule, and half a chlorine molecule, along with some cyanide at temperatures ranging from 156 to 624 °C. On the other hand, MnCl2·6U showed only two-stage decomposition and released 7 ammonia molecules, 3 carbon dioxide molecules, and 1 nitrogen molecule around 260 °C, followed by the loss of a molecule with the formula C2H3N3O3 at a higher temperature (around 466 °C).43
2.2.3. Cu–urea cocrystals.
Prior et al. prepared Cu(urea)2(H2O)3(NO3)·(urea)(NO3) complexes by dissolving copper nitrate trihydrate with urea in 70% aqueous ethanol. Then the solution is warmed and then evaporated at room temperature.50 The resulting cocrystal had a 1
:
4 metal to urea ratio. In this configuration, the copper ion has a distorted octahedral geometry with six ligands and four planar oxygen donors. There are two urea molecules and two water molecules arranged opposite each other, contributing to these four primary bonds. In addition, the remaining two coordination sites involve a loosely bound water molecule (Cu–O distance of 2.441 Å) and a monodentate nitrate anion (Cu–O distance of 2.577 Å).50 Moreover, Eisa et al. successfully obtained CuSO4·3CO(NH2)2·H2O from mechanosynthesis between urea and Cu2(CO3)(OH)2, as listed in Table 1.14 The results showed a delay in releasing nutrients coupled with efficient nitrogen delivery and reduced losses. This cocrystal achieved approximately 24% nitrogen content and reduced nitrogen volatilization emissions from the soil by over 40% after 27 days compared to pure urea, which indicates the improvement of nitrogen retention and availability in the soil. That is an indication of the potential of CuSO4·3CO(NH2)2·H2O for sustainable agricultural applications.14
Table 1 Overview of cocrystal fertilizers from 1933 solution synthesis methods to 2024 mechanochemistry
Coformers |
Cocrystal |
Detected properties |
Method |
Publication year |
Ref. |
CaSO4·2H2O |
CaSO4·4CO(NH2)2 |
Less hygroscopic than urea |
Coprecipitation |
1933 |
56
|
Ca(H2PO4)2·H2O |
Ca(H2PO4)2·4CO(NH2)2 |
Non-hygroscopic |
Coprecipitation |
1967 |
57
|
CaSO4·2H2O |
CaSO4·4CO(NH2)2 |
N–S–Ca fertilizer |
Ball milling |
1998 |
58
|
High hardness |
2007 |
59
|
Slow releaser |
Granulation and drying |
2012 |
60
|
CaSO4·2H2O |
CaSO4·4CO(NH2)2 |
Slow releasers |
Ball milling |
2017 |
36
|
Ca(H2PO4)2 |
Ca(H2PO4)2·4CO(NH2)2 |
Ca(NO3)2·4H2O |
Ca(NO3)2·4CO(NH2)2 |
MgSO4·H2O |
MgSO4·6CO(NH2)2·0.5H2O |
Mg(H2PO4)2·2H2O |
Mg(H2PO4)2·4CO(NH2)2 |
KCl |
CO(NH2)2·ZnCl2·KCl |
Urease inhibitor |
2018 |
32
|
ZnCl2 |
SC(NH2)2 |
ZnCl2·SC(NH2)2 |
Urease inhibitor |
2019 |
51
|
ZnCl2 |
ZnCl2·CO(NH2)2 |
|
ZnCl2·SC(NH2)2·CO(NH2)2 |
CaSO4·2H2O |
CaSO4·4CO(NH2)2 |
Lower probability of reacting with water than urea |
2020 |
40
|
CaSO4·2H2O |
CaSO4·4CO(NH2)2 |
Slow N release |
2022 |
41
|
Cu2(CO3)(OH)2 |
CuSO4·3CO(NH2)2·H2O |
2024 |
14
|
(ZnCO3)2·(Zn(OH)2)3 |
ZnSO4·CO(NH2)2·2H2O |
2.2.4. Zn–urea cocrystals.
ZnKU (Zinc–KCl–urea) ionic cocrystals exist in two polymorphic modifications, as obtained by Casali et al.32 The main difference between both forms belongs to the arrangements of atoms within the crystal lattice. In addition, in both forms, there is a hydrogen bonding network involving urea N–H donors and chloride acceptor ions. Further, there is bifurcated bonding between the urea O atom and both Zn and K.32 The structure of ZnU, ZnT, and ZnTU involves H bonds between NH2 groups and Cl, as shown in Fig. 7. In ZnU, there is another H-bond formed between NH2 groups and O, and in ZnT, there is one between NH2 groups and S. However, in ZnTU, only O and Cl participate in H bonds, and there are no NH2–S bonds.51
 |
| Fig. 7 Cocrystallization products between ZnCl2 and urea/thiourea, where (a) ZnT, (b) ZnU, (c) ZnTU, (d) ZnT with H-bonds, (e) ZnU with H-bonds, and (f) ZnTU with H-bonds.51 | |
Urea has a melting point of about 136 °C, while thiourea has a melting point of about 178 °C. The addition of ZnCl2 to ZnU lowered the melting point to 124 °C, whereas ZnT has a melting point of 157 °C. The combination of the three compounds as a single cocrystal significantly reduced the melting point to 100 °C.51 Form 1 of ZnKU showed a monoclinic system with a P21/m space group, while ZnKU in form 2 is in the space group of P21/n.32 The addition of ZnCl2 and KCl to urea to obtain a ZnKU cocrystal led to a reduction in the melting point to around 135 °C for form 1 and a slight increase to around 142 °C for form 2.32 The solubility of urea decreases by a third when it forms a cocrystal with ZnCl2. The cocrystal of ZnTU dissolves 37% and the rest remains as ZnT and ZnTU.51
The ionic cocrystal of ZnKU provides a sustainable approach to nutrient delivery in agriculture by releasing essential elements such as K and Zn. In addition to supplying key nutrients, ZnKU significantly inhibits urease activity and consequently reduces nitrogen loss and lowers the ammonia emissions into the atmosphere, which leads to higher nitrogen use efficiency (NUE).32 This reduction in ammonia release not only enhances nitrogen cycle management but also can aim to avoid environmental pollution and the negative impact of greenhouse gases. Furthermore, the synthesis of ZnKU is environmentally friendly because it depends on utilizing simple, scalable, and solvent-free methods that align with sustainable agricultural practices and promote eco-efficient fertilizer production on a large scale. Prior et al. synthesized a Zn(urea)4(H2O)2·2(NO3) cocrystal via a chemical method by dissolving urea and zinc nitrate hexahydrate in water. Then the solution is warmed and evaporated similar to copper urea cocrystal preparation with also a 1
:
4 metal-to-urea ratio.50
2.2.5. Ni–urea cocrystals.
Krawczuk et al. reported a complexation between urea and Ni(II) in the form of (Ni(urea)4·(H2O)2)·(NO3)2.52 They prepared this compound by dissolving nickel(II) nitrate hexahydrate in hot isopropyl alcohol (propan-2-ol) using reflux. Then they added urea to the nickel compound with a molar ratio of 1
:
4. The mixture was filtered and slowly evaporated at room temperature, with the product obtained after a few weeks. The resulting combination of Ni and urea compound has a central Ni atom surrounded by four oxygen atoms from urea molecules, arranged in a flat plane around the nickel. In addition, there are two water molecules positioned opposite each other (in trans-positions).52 The existence of the Ni cocrystal with urea is significant, as it is involved in various physiological processes in plants. It plays a role in nitrogen metabolism during the reproductive phase of growth, contributes to phytoalexin synthesis, and participates in the photosynthesis process.53
2.2.6. Outlook for nutrient–urea cocrystal fertilizers.
Important work on the synthesis of nutrient–urea cocrystal materials is shown in Table 1. Initial attempts were focused on coprecipitation, while the recent use of mechanochemical techniques allowed for a more diverse range of nutrients to be incorporated. Yet, the highest emphasis was given to major nutrients using widely available salts, such as CaSO4·2H2O. Recent attempts have been focused on developing new, multicomponent, and multifunctional formulations incorporating other functionalities, such as urease inhibition, into a cocrystal lattice to obtain molecularly uniform fertilizers.14,35,36,39–42,51,54 This trend could be of major importance in creating other fertilizer formulations that can fix nitrogen directly in legumes with the help of certain micronutrients, such as B and Fe.55
Moreover, some significant results can be highlighted such as the finding that chlorophyll a + b content was around 0.8 mg per g FW (fresh weight) after 18 days when no nitrogen was added, 1.3 mg per g FW with urea, 1.2 mg per g FW with CuSO4·3urea·H2O, 1.6 mg per g FW with ZnSO4·urea·2H2O.14 In addition, the decrease in solubility (increase in sustained release) reached 99% for the urea·4HBA cocrystal compared to pure urea.21 A notable observation is a significant reduction in NH3 emissions when compared to urea by more than 50% when using CaSO4·4CO(NH2)2.36 The urease inhibition increased by 80% for ZnKU compared to pure urea.32 Additionally, the reduction in ammonification reached approximately 80% for ZnTU.51 CaSO4·4urea exhibited 91% enhancement in grain yield (g per pot) and 145% for NUE (mg per g biomass).39 The same cocrystal of CaSO4·4urea showed approximately 14% improvement in the amount of protein compared to pure urea when applied.40 Collectively, these show the complex and beneficial behavior of cocrystallized nitrogen fertilizer materials that do not rely on the conventional practices of adding exogenous soil microbiota inhibitors.
3. Carbon-containing compound-urea cocrystals
3.1. Carboxylic acid urea cocrystals
3.1.1. Urea–hydroxybenzoic acid.
Low-molecular-weight phenolic compounds, including hydroxybenzoic acid (HBA), are common components of essential oils with antimicrobial properties.61 Depending on their structure and concentration, they can either promote or inhibit microbial growth. Furthermore, phenolic compounds like HBA are broken down into simpler substances, eventually leading to their mineralization and integration into soil organic matter.62 This biodegradation process helps reduce the persistence of these compounds in the environment, contributing to their safe use in agricultural applications.
Urea–HBA acid cocrystals can also provide a sustainable, slow-release nitrogen source.21 Rajbongshi et al. employed a LAG approach to prepare urea and hydroxybenzoic acids (HBAs).21 This involved grinding stoichiometric amounts of urea and respective co-formers in a mortar and pestle with acetonitrile. Urea formed 0.5
:
1 adducts with 4HBA and 24DHBA (2,4-dihydroxybenzoic acid), each containing one molecule of the respective HBA per half molecule of urea in the asymmetric unit. Both structures shared an infinite urea chain motif, where the p-hydroxy group of the HBA acted as both a hydrogen bond donor and acceptor through synthons II and IV.22 In contrast, urea formed a 1
:
1 cocrystal with 25DHBA, with one molecule of each component in the asymmetric unit, crystallizing in the chiral monoclinic P21 space group (see Fig. 8).21 This diverse range of stoichiometries and crystal structures highlights the intricate interplay between urea and HBAs in cocrystallization, influencing both composition and packing arrangements.
 |
| Fig. 8 Urea and hydroxybenzoic acid cocrystals formed via three different arrangements.21 (a) 4HBA, (b) 24DHBA, (c) 25DHBA, (d) urea·4HBA, (e) urea·24DHBA, and (f) urea·25DHBA. | |
TGA data revealed the material thermal stability up to approximately 180 °C. While pure urea boasts high water solubility, its cocrystals with HBA exhibit lower values. This reduction is attributable to multiple factors such as the existence of less soluble co-formers which drag down the overall solubility. In addition, cocrystals exhibit fewer solvent-exposed facets due to their anisotropic morphology compared to pure urea multi-faceted structures, limiting solvation sites. Furthermore, hydrophobic benzene C–H groups from the co-formers and stronger hydrogen bonding within the crystals further reduce solvation energy. The solubility of urea is around 1000 mg mL−1, while for the urea·4HBA cocrystal it was 9.2 mg mL−1, representing a 99% reduction.21 Moreover, the urea release profile showed that urea was more sustainable in the cocrystal form than in its pure form. The maximum average release was reached after 6 days for pure urea, while sustained until 26 days for the cocrystal form. This is an indication of its ability to be used in the agriculture field.
3.1.2. Urea–glutaric acid (UGA).
Glutaric acid in combination with copper has been proposed as an efficient agricultural fungicide.63 Kumari et al. reported that they prepared UGA from a mixture of 2
:
1 of urea and glutaric acid.64 After 30 days, a crystal was formed within the solution. This experiment demonstrated a straightforward method for crystallizing UGA, potentially leading to further study of its properties and potential applications.64 TGA and DSC analysis showed the promising thermal stability of the UGA crystal. It remained stable up to 137.69 °C, indicated by minimal weight loss. At this point, a major decomposition event occurred, releasing water as evidenced by the weight loss and a sharp peak in the analysis. This indicates a slight increase in thermal stability compared to pure urea.
3.1.3. Urea–adipic acid cocrystal (UAA).
Adipic acid has many applications in the food industry and hence is compatible with a food production chain. It is used as an antimicrobial agent, among other uses.65 Parakatawella et al. synthesized needle-like single crystals of a 2
:
1 urea–adipic acid cocrystal by mixing nitromethane and acetonitrile in equal proportions for crystallization.67 In addition, Shanthi et al. obtained high-purity urea and adipic acid and mixed them in a 1
:
1 ratio.66 The UAA salt was gradually added until a small precipitate formed at the bottom. Conversely, another structural form of the same cocrystal crystallized through slow evaporation of a saturated aqueous solution with a pH of 3.11.67 The crystal structure revealed pairs of urea molecules (centrosymmetric amide dimers) interacting with halves of adipic acid molecules in both polymorphic forms.
The urea release profile of the urea·adipic acid cocrystal is a key feature of its use as a sustained-release nitrogen fertilizer. The 2
:
1 urea·adipic acid cocrystal, particularly form II, revealed significantly reduced solubility and more efficient nitrogen release over time compared to commercial urea. In soil samples, over 60% of commercial urea leached out within two days, while the urea·adipic acid form II cocrystal released only about 40%, indicating a slower and more controlled release.67 These properties help mitigate issues of runoff and eutrophication associated with urea usage in soil, which makes it an environmentally friendly option. However, while these methods have successfully produced the desired cocrystals, their sustainability should be considered. The use of methanol, which is a volatile organic compound, can raise environmental and safety concerns. Furthermore, although effective, the slow evaporation method may not be energy-efficient for large-scale production. Future research should explore more sustainable and energy-efficient crystallization methods to align with green chemistry principles.
3.1.4. Galic acid–urea (GAU) cocrystal.
Gallic acid is an important phenolic compound found in various plants, fruits, and teas. It is known for its antioxidant properties, which help in protecting cells from oxidative damage.68 Additionally, gallic acid exhibits anti-inflammatory, antimicrobial, and anticancer activities, and therefore it is valuable in pharmaceutical and nutraceutical applications.69 Its presence in natural products also contributes to their health benefits, enhancing overall wellness.
Jyothi et al. prepared gallic acid–urea using a mechanochemical grinding method.70 Each gallic acid molecule forms five-membered rings due to hydrogen bonds within itself (intramolecular interactions). In addition, amide and carboxylic acid groups of gallic acid and urea molecules connect through N–H⋯O and O–H⋯O hydrogen bonds, forming “acid-amide supramolecular heterosynthons.” These heterosynthons form 1D chains linked by further N–H⋯O bonds, creating an X-shaped pattern. Chains are further connected by ring motifs OH in GA and NH2 in urea. Further, there is a lone pair interaction that exists between the urea carbonyl and the GA centroid molecule. GA molecules also stack on top of each other through π–π interactions.70
TGA of the cocrystal of GAU showed that it melts at 180 °C and decomposes at 350 °C, leaving a 13% residue. For the GA-propionamide monohydrate cocrystal (for comparison), a weight loss of 4.18% at 100 °C indicates the presence of one water molecule. Additional weight loss occurs at 230 °C and 350 °C due to melting and decomposition. The GA-propionamide leaves 15% of its mass as residue, confirming the presence of one water molecule in the cocrystal. However, this indicates that both cocrystals with GA exhibit a higher melting point than pure urea, which means more thermal stability.70
3.1.5.
DL-Malic acid–urea cocrystal.
DL-Malic acid, or simply malic acid, is a dicarboxylic acid. It is found naturally in various fruits, including apples, and is often used as a food additive to add a tart taste.71–74DL-Malic acid has two stereoisomeric forms: L-malic acid and D-malic acid, which are mirror images of each other. The DL prefix indicates that the compound is a racemic mixture of both L and D forms.75 Malic acid is used in various industries, including food and beverage, pharmaceuticals, and cosmetics, due to its acidity and ability to enhance flavors. It is also a component of the citric acid cycle, an important metabolic pathway in organisms.
Krawczuk et al. prepared cocrystals of urea and L-malic acid (ULMA) by dissolving both components in water at a 1
:
1 molar ratio. The resulting solution was left undisturbed under ambient conditions for slow evaporation of the solvent and controlled crystallization of ULMA.76 Moreover, Kanagathara et al. dissolved DL-malic acid (a 1
:
1 mixture of D and L forms) in a suitable solvent. Urea was then added to the solution in a 1
:
1 molar ratio.77 The mixture was heated until it became clear, which usually means a complete dissolution. Then, the solution is cooled to room temperature for crystallization over several days. Finally, colorless crystals of a urea–DL-malic acid (UDLMA) cocrystal were then filtered and dried under ambient conditions.
The chemical stability of the UDLMA cocrystal is thoroughly examined using computational and experimental approaches. These calculations indicate a stable molecule with a substantial HOMO–LUMO energy gap of 7.152 eV, which suggests potential bioactive properties and feasible charge transfer within the cocrystal.77 Natural Bonding Orbital (NBO) analysis shows significant stabilization energy from intramolecular interactions, supporting the cocrystal stability. Global chemical reactivity descriptors, including chemical hardness (3.576 eV) and electronegativity (4.091 eV), indicate UDLMA chemical stability and its strong electron-attracting ability. Molecular electrostatic potential analysis reveals distinct regions of negative and positive potential, corresponding to hydrogen bond acceptors and donors, respectively, further enhancing the cocrystal stability.77 These results collectively confirm the UDLMA cocrystal chemical stability, which might be potential for various agricultural applications.
3.1.6. Urea–succinic acid cocrystal.
In conventional pharmaceuticals, succinic acid cocrystals might have a crucial role in enhancing drug performance by altering the properties of active pharmaceutical ingredients, such as solubility and stability.78 This enhanced stability and solubility can be beneficial in agricultural applications. Additionally, succinic acid, a component of U–SA cocrystals, is important for energy production in cells, being a key intermediate in the Krebs cycle.79 Its antioxidant properties are utilized to repair cellular damage and protect against environmental stressors.80 Furthermore, succinic acid serves as an acidity regulator and flavor enhancer in food and beverage products, contributing to improved taste and pH balance.
A vapor-phase approach was adopted for cocrystal synthesis by Zhang et al. using a custom-designed apparatus.81 There is a horizontal glass reactor that comprised three distinct zones that are a 300 mm heating zone, a 100 mm crystal growth zone, and a connecting section. In the design, all zones are maintained at a constant diameter of 32.7 mm. Precise temperature control (±1 °C) was achieved within the heating zone using a resistance furnace. However, crystallization occurred in the growth zone, where temperature was controlled by a thermostatic water bath. Nitrogen gas served as the carrier, flowing over the samples in the heating zone and transporting the sublimed material vapors toward the growth zone. This gas-phase approach offers several advantages over traditional solution-based methods, including reducing solvent dependency and accessing metastable phases.81
The thermal behavior showed that the prepared 2
:
1 urea–succinic acid cocrystal exhibited a unique melting point at 120 °C, with transformations detected around 142 and 160 °C.81 B. K. Singh et al. cultivated a urea–succinic acid cocrystal by a slow evaporation technique at 35 °C. They dissolved 25 grams each of high-purity urea and succinic acid (2
:
1 ratio) in water, adding a small amount (1 mol%) of maleic acid. After stirring for 4 hours at 35 °C, the solution was left undisturbed for 4 days in a constant temperature bath.82 Alhlaweh et al. prepared urea–succinic acid via spray drying of 2-propanol solutions and obtained pure bulk 1
:
1 cocrystals. A 2
:
1 cocrystal readily formed via simple solvent evaporation from a 2-propanol solution at room temperature.83
The thermal stability of the urea–succinic acid cocrystal is higher than that of pure urea, reaching around 140 and 150 °C for 1
:
1 and 2
:
1 U–SA cocrystals, respectively. This enhanced stability allows it to handle higher temperatures, which could be significant for agricultural applications. The improved stability and reduced environmental impact of these cocrystals suggest that they could be useful in developing more sustainable agricultural practices. Future research should explore their potential for enhancing nutrient delivery and minimizing environmental degradation in agricultural settings.
3.2. Other-organic carbon urea cocrystals
3.2.1. Citric acid–urea.
Citric acid–urea (CAU) might be used in agriculture for seed protection, antimicrobial activity, and enhancing soil disease resistance. As a seed coating, CA provides a protective barrier against pathogens and metal ions, promoting successful germination. Its antimicrobial properties inhibit bacterial and fungal growth, reducing the need for chemical pesticides.84 When added to soil, citric acid–urea might improve nutrient availability and plant immunity, fostering robust growth and resilience against diseases. These attributes make citric acid–urea a good additive for sustainable and effective agricultural practices. The cocrystal structure shows two synthons between C
O of urea and O–H acid, besides N–H of urea with C
O of acid. Further, the V synthon is between C
O of urea and H–O of the acid.22
3.2.2. Fluconazole–urea.
Fluconazole is an antifungal medication widely used to treat various fungal infections.85 It belongs to the triazole class of antifungals and works by inhibiting the synthesis of ergosterol.86 This disruption weakens the cell membrane, leading to the death of fungal cells. Fluconazole is effective against a broad spectrum of fungal species.
A 1
:
1 molar ratio of fluconazole (FLZ) and urea was dissolved in ethanol by Adewale et al. to form a solution and initiate a cocrystallization process (to form a FLZU cocrystal).87 This solution was left to slowly evaporate over 9 days, leading to the formation of fine white block crystals.87
3.2.3. Trospium chloride–urea.
Trospium chloride (TCl) is an anticholinergic medication used to treat incontinence and overactive bladder syndrome.88 Skořepová et al. fabricated trospium chloride–urea (TClU) cocrystals, shown in Fig. 9, via solution crystallization. The investigation into its thermal stability exhibited initial water evaporation, followed by multiple urea decomposition stages around 190 and 240 °C overlapping with its melting point at 133 °C.88 That means that no distinct melting point for the cocrystal was observed, which might indicate decomposition before melting.
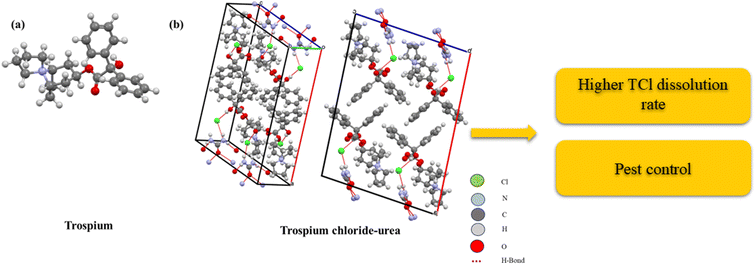 |
| Fig. 9 Trospium and different views for the trospium chloride–urea cocrystal and the measured higher TCl dissolution rate with its suggested application as pest control, where (a) tropsium and (b) tropsium chloride-urea structure.88 | |
The cocrystallization of TCl with urea significantly enhances its intrinsic dissolution rate, which might make it beneficial for agricultural applications.88 This increased dissolution rate of TCl ensures the absorption of the active ingredients when applied to plants, leading to faster and more effective pest control and nutrient delivery. Additionally, the cocrystallized formulation potentially improves TCl permeability through plant cuticles, overcoming its natural low permeability. Urea, as a common fertilizer, adds dual functionality to the formulation, providing both pest control and essential nutrients, thereby promoting overall crop health and productivity. This approach also supports sustainable agriculture by ensuring efficient use of active ingredients, minimizing environmental impact, and offering stable, effective formulations suitable for varied environmental conditions.
3.2.4. Catechin–urea.
Catechin is a natural flavonoid compound found in various foods such as tea, cocoa, fruits, and red wine.89 It is a potent antioxidant known for its health benefits. Catechin has been studied for its role in reducing the risk of cardiovascular diseases, improving cognitive function, and even potentially lowering the risk of certain types of cancer.90 It is also known for its anti-inflammatory and antimicrobial properties, making it a valuable compound in traditional medicine and cosmetic products.91 Catechin ability to scavenge free radicals and reduce oxidative stress in the body contributes to its wide range of health-promoting effects. In general, urea is regarded as a cost-effective and sustainable coformer for enhancing the physical properties of various substances, even those not currently used in agriculture. Through cocrystallization, urea can enhance the stability of active pharmaceutical ingredients (APIs), such as catechin, under conditions of high humidity or elevated temperatures.92
Leng et al. obtained urea–catechin (UC) via dry grinding of a 1
:
1 molar ratio of urea and catechin.93 Regarding thermal stability, compared to pure urea and moisture-sensitive amorphous catechin, the UC cocrystal displays higher stability. While urea degrades rapidly after melting, the cocrystal boasts a significantly higher melting point and resists moisture for weeks at high humidity. The melting point of the cocrystal starts at around 176 °C, which is higher than that of pure urea. Further, amorphous catechin readily absorbs moisture, resulting in the formation of unstable catechin hydrate that loses its improved properties upon dehydration.93 Cocrystallization of catechin with urea enhances its physical stability compared to amorphous catechin. UC remains stable under high humidity (75% relative humidity) at 25 °C for two weeks, while amorphous catechin transforms into catechin hydrate under the same conditions. Additionally, UC shows a melting temperature of 176 °C with a corresponding heat of fusion of 162.78 J g−1, indicating that it is less sensitive to moisture and temperature compared to catechin hydrate.
The cocrystallization of catechin with urea (UC), which enhances catechin stability and storage under high humidity conditions, can be useful in agriculture. UC improved stability compared to amorphous catechin and catechin hydrate makes it ideal for agricultural formulations that require resistance to environmental factors. UC antioxidant and antimicrobial properties can protect plants from oxidative stress and diseases, potentially enhancing plant health and productivity. Additionally, UC stability allows for sustained release formulations, providing long-lasting effects with reduced environmental impact. Therefore, cocrystallization with urea offers a promising strategy for creating a more robust and shelf-stable form of catechin for various applications.
3.2.5. Nitrofurantoin–urea.
Nitrofurantoin (NF) is an antibiotic medication used to treat urinary tract infections, and it inhibits various bacterial enzyme systems and exhibits broad antibacterial activity against both Gram-positive and Gram-negative organisms.94 However, its effectiveness is limited by its poor water solubility, which reduces its significance and requires the development of alternative solid forms.95
The cocrystallization was done via coprecipitation. Khan et al. obtained yellow needle-shaped crystals of a 1
:
1 nitrofurantoin–urea (NFU) cocrystal by dissolving 2 mmol of NF (β-form) and an equal amount (2 mmol) of urea in 160 mL of methanol at 70 °C. The solution was then allowed to evaporate at room temperature for two days.96 Further, Cherukuvada et al. mixed 0.2 mmol of NF powder (46.8 mg) and the same amount of urea powder (12 mg) and then ground them together using a mortar and pestle. This mixture was then dissolved in 4 mL of a hot solvent mixture composed of equal parts DMF and dioxane. The solution was left undisturbed at room temperature to slowly evaporate over several days. Eventually, yellow crystals formed from the solution.97 This structure started to decompose at 160 °C with no definite melting point.
The cocrystallization of NF with urea can make some advancements in utilizing its antibiotic properties for agricultural purposes. NF–urea cocrystals might exhibit enhanced water solubility and stability, which is crucial for effective delivery and prolonged action against bacterial infections in plants. With NF broad-spectrum antibacterial activity, including efficacy against both Gram-positive and Gram-negative organisms, these cocrystals offer a potent and environmentally sustainable alternative to synthetic pesticides. By targeting bacterial pathogens, NF–urea cocrystals can help manage crop diseases, improve plant health, and reduce the need for chemical interventions, thus promoting sustainable agricultural practices.
3.2.6. Outlook for organic compound-urea cocrystals.
Several observations emerge. First, the synthesis of these urea cocrystals has low sustainability due to the high use of solvents, solution handling and solution crystallization, as shown in Table 2. Only a few cocrystals are available in the literature that used mechanochemical methods. Second, there is a lack of information on the properties of the resulting material. The current state of the art is described in Section 4 of this review.
Table 2 A summary of carbon-containing urea cocrystals including preparation methods
Coformers |
Cocrystal |
Properties |
Preparation method |
Ref. |
4HBA |
Urea·4HBA |
Sustainable N release |
LAG mechanochemistry |
21
|
24DHBA |
Urea·24DHBA |
25DHBA |
Urea·25DHBA |
Glutaric acid |
UGA |
More thermally stable than pure urea |
Coprecipitation |
64
|
Adipic acid |
UAA |
Reduced solubility and efficient N releaser |
Coprecipitation |
67
|
Gallic acid |
GAU |
Higher thermal stability and antimicrobial |
Mechanochemical grinding |
70
|
DL-Malic acid |
ULMA |
Chemically stable |
Coprecipitation |
76
|
Succinic acid |
U–SA |
Higher thermal stability |
Gas-phase approach and spray drying |
81 and 83 |
Citric acid |
Citric acid–urea |
Antimicrobial activity |
LAG mechanochemistry |
84
|
Fluconazole |
FLZU |
Antifungal behavior |
Coprecipitation |
87
|
Trospium chloride |
TCLU |
The increasing dissolution rate of TCL |
Coprecipitation |
88
|
Catechin |
UC |
Higher thermal stability and moisture resistance |
Dry grinding |
93
|
Nitrofurantoin |
NFU |
Antimicrobial activity |
Coprecipitation |
97
|
4. Applications in sustainable agriculture and environmental management
4.1. Solubility or urease/nitrification inhibition combined with urea as the nitrogen source
Casali et al. showed that ZnKU has urease inhibition abilities and measured jack bean urease activity (JBU) with varying urea concentrations. Using a fixed, high urea concentration (64 mM), they then tested how different ZnKU concentrations affected enzyme activity. ZnKU significantly shows inhibition in urease, even at low concentrations (2 mM). At the highest tested concentration (8 mM), ZnKU achieved nearly 90% inhibition.32 Casali et al. also reported that the cocrystal, which is composed of urea and CAT in a 1
:
1 stoichiometry, can inhibit urease.54 The choice of catechol as a coformer stemmed from its ability to inhibit soil urease. The resulting urea·CAT cocrystal exhibited comparable inhibition of JBU activity when compared to catechol alone. In addition, after an incubation period of 20 minutes, the cocrystal led to a complete loss of urease activity. Furthermore, the urea·catechol cocrystal demonstrated reduced water absorption capacity, lower solubility (approximately 15% reduction compared to pure urea), and improved moisture stability. These properties position the cocrystal as an excellent alternative to urea for use as a sustained-release fertilizer.54 Further, Silva et al. researched the impact of humic material in stabilizing urea hydrolysis under controlled relative humidity.98 Humic materials play a significant role in the global nitrogen cycle through the incorporation of ammonium produced from urea breakdown and inhibiting the activity of urease, which is the responsible enzyme for converting urea to NH3.23,98 In their study, they used salicylic acid (a model humic material) to form a cocrystal with urea via mechanical milling. The resulting urea·salicylic acid cocrystal exhibited stability and had several noteworthy effects, such as antibacterial properties for plants and a secondary urea stabilization pathway.98 The antibacterial properties are extremely important for protecting plants against harmful microorganisms, and the secondary urea stabilization pathway, which reduces NH3 emissions, can contribute to more efficient nitrogen utilization in soil–plant systems. Moreover, Rajbongshi et al. tested the nitrogen release behavior of urea–hydroxybenzoic acid.21 The fast N release of pure urea, which reached around 65% in its first two days, decreased to around 15% in the same period for urea-24DHBA. This cocrystal achieved 65% N release after two weeks, which indicates the slow-release behavior of the urea cocrystals.
Among the tested fertilizers, CaSO4·4urea boosted both NUE and total nitrogen uptake in plants. This success is likely due to the reduction of nitrogen loss via volatilization, which is evidenced by significantly lower N2O emissions compared to urea alone. The CaSO4·4urea cocrystal revealed multiple peaks in daily nitrous oxide measurements, which means slowing down urea dissolution and nitrogen release. This prevents the rapid loss of N and optimizes plant uptake. This translates to higher NUE and minimal post-harvest soil nitrogen, indicating an efficient utilization and minimal environmental impact.39 Another study by Swify et al. showed that a CaSO4·4urea cocrystal at a high rate of 200 kg N per ha significantly boosted the corn crop nitrogen uptake in both grains and stems, compared to regular urea or no fertilizer. It exhibited around 250 kg kg−1 compared to 125 and 190 kg kg−1 for no fertilizer and pure urea. This led to the enhancement of the NUE reaching a value of around 30% for the cocrystal, compared to around 5% for pure urea.25 Furthermore, Barčauskaitė et al. showed that the behavior of pure urea involves a high rate of N dissolution on the first day, where the dissolved N value reaches 4.2% and the resulting N loss reaches 8.7% after 7 days. On the other hand, the CaSO4·4urea cocrystal has a dissolved N value of around 3.7 after the first day, leading to 0.6% N loss after 7 days.40 Honer et al. investigated the reduction of nitrogen loss from soil. They found that the CaSO4·4urea cocrystal significantly decreased ammonia emissions (4 times less after 30 hours) compared to urea. This effect is hypothesized to be due to various factors, including differences in particle size and solubility, potential enzyme inhibition, and formation of secondary salts.36
4.2. Cocrystallization of pesticides and their application
Pesticides encompass a range of substances that contribute to augmenting food production by safeguarding crops against pests, diseases, and weeds, consequently boosting productivity per unit of land.99 Nevertheless, pesticides with a high solubility can leach, decreasing their effectiveness.100 Consequently, significant quantities of pesticides are often required to manage hazardous organisms, leading to economic and environmental penalties.101 Hence, the development of environmentally friendly strategies is imperative to formulate new pesticides with minimal environmental and economic impacts and recent developments have been summarized in Fig. 10.
 |
| Fig. 10 A summary of enhanced properties of the agricultural cocrystals for agricultural management (herbicides, insecticides, fungicides, and urease inhibition). | |
Over the past few decades, cocrystals have emerged as a highly successful avenue in pesticide applications due to their simple process, low cost, and eco-friendliness, developed using incorporation of a conformer into the crystal lattice, resulting in non-covalent molecular self-assembly.102,103 As a result, the physicochemical properties of pesticides, such as melting point, solubility, chemical stability, physical stability, and dissolution rate, can be significantly enhanced.104
4.2.1. MET.
For instance, Xiao et al. found that the cocrystallization of metamitron (MET), a herbicide that is used for controlling grass and broadleaf weeds in sugar beet fields, and using naringenin (NA) dramatically decreased the dissolution rate by 98.30% compared to pure MET at 45 °C.105 Additionally, thermal gravimetric analysis (TGA) results revealed that the inclusion of NA enhances the thermal stability of MET by up to 30%.
4.2.2. CYC-SM and CYC-TS.
Likewise, Li et al. employed a cocrystallization strategy utilizing succinimide (SM) and trifluoromethanesulfonamide (TS) to enhance the physical and chemical properties of the cycloxaprid (CYC) pesticide. Their work showed a significant 4.7-fold increase in the solubility of the cycloxaprid-succinimide cocrystal compared to CYC in ethyl acetate, clearly. Additionally, CYC-SM exhibited better physical stability in comparison to both CYC and CYC-TS.106
4.2.3. PYR-TM@TA–Cu.
Qu et al. developed a novel cocrystal abbreviated as PYR-TM@TA–Cu (pyraclostrobin-thiophanate-methyl@tannic acid–copper), in which the pyraclostrobin-thiophanate-methyl (PYR-TM) was prepared by a sustainable mechanochemical method and incorporated into metal–phenolic networks in water. Their objective was to enhance the physicochemical properties of PYR, a broad-spectrum fungicide, particularly its photo sensitivity and control efficacy. The results indicate a significant enhancement in the photostability of PYR, with thiophanate-methyl (TM) boosting it by 75.7-fold through competitive energy absorption of photons and modulation of molecular conformation.107 Additionally, the metal–phenolic network coating reduces both the washing persistence and leaching potential of pesticides.
Qu et al. have recently expanded the application of pyrimethanil (PYR), a widely used fungicide, to combat B. cinerea infestations by utilizing nano-crystallization in water using indole-3-acetic acid (3IA), fumaric acid (FMA), 2,6-dimethoxybenzoic acid (26DBA), chrysanthemum acid (CHA), and 4-biphenylcarboxylic acid (4BIP) as co-formers for a total of five cocrystals. This method aims to enhance several properties of PYR, including photostability, volatilization rate, antimicrobial activity, and wettability.108 These improvements not only enhance the efficacy of PYR but also contribute to reducing its environmental impact. The results obtained show that the cocrystals PYR-3IA and PYR-FMA have the highest stability. The melting point of PYR was increased from 96.19 °C to 206 °C. Besides, the photostability and volatility were improved by 3.85-fold and 297-fold, respectively.
4.2.4. EUG–CAR–THY–PHE–HMT.
Mazzeo et al. proposed the cocrystallization of natural oils with antibacterial, antifungal, and insecticidal properties, such as eugenol (EUG), carvacrol (CAR), and thymol (THY), using phenazine (PHE) and hexamethylenetetramine (HMT) as co-formers. These materials were prepared using a solvent-free mechanochemical protocol to reduce costs and avoid contamination from disposed solvents. The results indicate that crystallization enhances the release profile of natural oils, both in terms of acute and prolonged release over 14 days compared to pure oils.109
4.2.5. URCAT.
Casali et al. conducted a synthesis of a novel compound termed urea–catechol (URCAT) through a mechanochemical reaction involving urea and catechol, aimed at mitigating nitrogen losses from soils. Their findings showed that the URCAT cocrystal exhibits dual functionality, where it can act both as a urease inhibitor and a soil fertilizer.54 Furthermore, a significant discrepancy in water vapor absorption was observed between urea and URCAT, with the latter adsorbing 3.5 times less water than urea, thus demonstrating enhanced stability compared to urea.
4.2.6. Based on PMZ-HBA.
Wu et al. developed novel multicomponent cocrystals aimed at bolstering the solubility and humidity resistance of pymetrozine (PMZ). They employed different coformers including p-hydroxybenzoic acid (pHBA), 2,3-dihydroxybenzoic acid (2,3HBA), 2,4-dihydroxybenzoic acid (2,4HBA), 2,5-dihydroxybenzoic acid (2,5HBA), 2,6-dihydroxybenzoic acid (2,6HBA), and 3,5-dihydroxybenzoic acid (3,5HBA). Their results indicated that PMZ-OXA, PMZ-pHBA, PMZ-2,3HBA, PMZ-2,4HBA, and PMZ-2,5HBA experienced negligible mass changes, remaining under 1.5%, across a relative humidity range of 0% to 95%.110 Conversely, the mass of PMZ significantly increased to 17.7% between 70% and 95% relative humidity, stabilizing thereafter during the desorption phase. These results underscored the stability of all newly formed multicomponent cocrystals against humidity.
4.2.7. Based on 2,4-D.
Li et al. successfully synthesized six new multicomponent crystals using 2,4-dichlorophenoxyacetic acid (2,4-D), a widely used herbicide and plant growth regulator in crop production. By combining virtual and experimental co-former screening, they aimed to enhance the aqueous stability and solubility of 2,4-D. The co-formers employed to obtain the crystals included piperazine (PZ), 2-benzimidazole (BZ), 3-aminobenzoic acid (ABA), p-phenylenediamine (PPD), and o-phenylenediamine (OPD), while 2-ethoxybenzamide (EB) was used to create a cocrystal. All salts were obtained through solvent evaporation and slurry suspension, where proton transfer occurred from the carboxyl group of 2,4-D to the nitrogen atom of the co-formers. The results indicate that 2,4-D-EB has the lowest solubility compared to all other salts, showing a 44.9% reduction in solubility compared to 2,4-D alone. This reduction is attributed to the ionization during salt formation. Generally, compounds with higher melting points are more stable and, consequently, have lower solubility.13
Likewise, Fang et al. investigated the factors that affect the formation of multicomponent crystals using a 2,4-dichlorophenoxyacetic acid (2,4-D) molecule and 10 N-heterocyclic compounds including pyrazine (PYE), 4-iodopyridine (IP), triethylene diamine (DABCO), 2,2′-bipyridine (TBP), 1,2-bis(4-pyridyl)ethane (BPA), trans-1,2-bis(4-pyridyl)ethylene (BPE), 1,2-bis(4-pyridyl)ethyne (BPAC), 1,3-bis(4-pyridyl)-propane (BPP), (E)-4,4′-azobispyridine (AP), and 4-(4-pyridinyldisulfanyl)pyridine (DPDS) as co-formers. Their findings revealed that BPP was unable to form multicomponent crystals with 2,4-D. BPAC combined with 2,4-D to create a channel cocrystal solvate, while PYE and 2,4-D formed a cocrystal hydrate. DABCO and BPE each formed salts with 2,4-D. The remaining multicomponent solids of 2,4-D were cocrystals. Among the cocrystals obtained, the 2,4-D-PYE-water cocrystal requires the bridging effect of water molecules. Its crystal structure crystallizes in the triclinic space group P
, with Z = 4, where the water molecules connect 2,4-D molecules through strong O–H⋯O hydrogen-bonding interactions, significantly contributing to the stability of the structure. According to the results, the molecular electrostatic potential (MEP) surface and interaction site-pairing energy differences (ΔEsite-pair) are the main factors for the formation of multicomponent crystals of 2,4-D.111
4.2.8. AMT-FUM.
Carvalho et al. studied a crystal engineering approach for enhancing the solubility of the herbicide ametryn (AMT) using fumaric acid (FUM) and maleic acid (MAL) as co-formers, as shown in Table 3. The results obtained revealed that the solubility of cocrystals AMT-FUM (1.89 ± 0.05 mg mL−1) and AMT-MAL (4.67 ± 0.06 mg mL−1) was about 9 and 20 times higher compared to that of neutral AMT (0.209 ± 0.02 mg mL−1). Moreover, higher decomposition temperatures and thermal stability were achieved for AMT-FUM and AMT-MAL cocrystals suggesting a potential reduction of the overall impact of AMT.112
Table 3 A summary of cocrystals that might be used as pesticides with their properties after cocrystallization
Cocrystals |
Coformers |
Properties |
Ref. |
MET-NA |
NA |
Dissolution rate decreased by 98.30% at 45 °C; enhanced thermal stability by 30% |
105
|
CYC-SM and CYC-TS |
SM and TS |
Solubility increased 4.7-fold (CYC-SM); improved physical stability compared to CYC and CYC-TS |
106
|
PYR-TM@TA–Cu |
TM, TA, and Cu |
Enhanced photostability (75.7-fold); reduced washing persistence and leaching potential |
108
|
PYR-3IA, PYR-FMA, PYR-26DBA, PYR-CHA, PYR-4BIP |
3IA, FMA, 26DBA, CHA, and 4BIP |
Melting point increased from 96.19 °C to 206 °C; photostability and volatility improved by 3.85-fold and 297-fold, respectively |
107
|
EUG–PHE, CAR–PHE, THY–PHE, EUG–HMT, CAR–HMT, THY–HMT |
EUG, CAR, THY, PHE, and HMT |
Enhanced release profile of natural oils for both acute and prolonged release over 14 days |
109
|
URCAT |
Urea and catechol |
Dual function as a urease inhibitor and soil fertilizer; absorbed 3.5 times less water compared to urea |
54
|
PMZ-pHBA, PMZ-2,3HBA, PMZ-2,4HBA, PMZ-2,5HBA |
pHBA, 2,3HBA, 2,4HBA, 2,5HBA |
Negligible mass changes (<1.5%) under 0–95% relative humidity; significantly improved humidity resistance compared to pure PMZ |
110
|
2,4-D-PZ, 2,4-D-BZ, 2,4-D-ABA, 2,4-D-PPD, 2,4-D-OPD, 2,4-D-EB, 2,4-D-PYE-Water |
PZ, BZ, ABA, PPD, OPD, EB, PYE, and water |
Enhanced aqueous stability; reduced solubility for 2,4-D-EB by 44.9%; improved structural stability through strong hydrogen-bonding interactions |
13
|
AMT-FUM and AMT-MAL |
FUM and MAL |
Solubility increased by 9 times (AMT-FUM) and 20 times (AMT-MAL) compared to pure AMT; improved decomposition temperature and thermal stability |
112
|
5. Opportunities in sustainable agricultural cocrystal synthesis and measurement techniques
5.1. Synthesis
Cocrystals of urea can be synthesized through both solution-phase and mechanochemical methods, each with distinct characteristics and environmental implications. Solution-phase synthesis involves dissolving reactants in a solvent and then evaporating the solvent, slowly cooling the reaction mixture, or reducing solubility through antisolvent to reach supersaturation and then cocrystallization.113 This means that choosing the solvent is a critical stage in addition to carefully controlling temperature and solubility. Furthermore, multiple additional steps can be added such as washing, drying and filtration and all of these stages contribute to chemical waste and energy consumption. The complexity of solution-phase methods is further heightened by the need for precise control over reaction conditions and the potential for solvent-related safety and environmental hazards.
In contrast, mechanochemical synthesis offers a more straightforward and environmentally friendly approach, as illustrated in Fig. 11. In mechanochemistry, reactants can cocrystallize directly due to the mechanical forces without intermediate stages. Cocrystals which are synthesized through mechanochemical methods have more advantages in green engineering technology for environmentally friendly fertilizers. Its solvent-free nature and scalability make it an attractive approach. By eliminating the need for solution handling and evaporation, solvent-free mechanochemical synthesis enhances process sustainability.23 This leads to a decrease in chemical waste and energy consumption in addition to being independent of the relative solubilities of reactants, thereby enabling reactions between poorly soluble materials, which is not available with solution-based methods. Moreover, the mechanochemical procedure has been used for many years in large-scale industrial production due to its relative simplicity and cost-effectiveness. For instance, recent work by Brekalo et al. showed that the energy consumption of synthesizing CaSO4·4urea cocrystals during the milling reactions varied depending on the synthesis method and scale. For a mixer mill operating at 70 °C, the energy requirement was 7.6 W h g−1, while larger-scale production using a planetary mill required 3.0 W h g−1 at a 50 g scale and 4.0 W h g−1 at a 100 g scale. Additionally, twin-screw extrusion at both room temperature and 70 °C exhibited an energy consumption of 4.0 W h g−1.41 In the mineral industry, the typical reported energy for producing urea is around 0.92 W h g−1 for using 0.46 g nutrient per g product (the report was in tonnes but converted to grams for a better comparison). Furthermore, both monoammonium phosphate and diammonium phosphate exhibited an energy requirement of approximately 0.1 W h g−1, but diammonium phosphate showed higher efficiency with 0.18 g nutrient per g product, compared to 0.11 g g−1 for the monoammonium phosphate compound. Moreover, the triple super-phosphate showed 0.55 W h g−1 with 0.46 g g−1, while the single super-phosphate was 0.39 and 0.2 g g−1. It must be mentioned that these numbers are obtained from the tonnes scale, which reaches 65 tonnes for urea production.114
 |
| Fig. 11 The typical route for both solution and mechanochemical-based methods. It can be seen that solution-based reactions involve a dissolution step, which typically needs a magnetic stirrer. Then, the evaporation stage can occur on a heat plate to provide sufficient thermal energy. In addition, drying needs a drying furnace and all of these devices have high energy consumption when compared to the milling device. In mechanochemistry, all electricity consumption-related steps are bypassed, and the electricity depends only on the power of the milling instrument and the milling time of the reaction. | |
An important example of mechanochemical synthesis in this field is the recent developments using low-solubility minerals as reactants. Mechanochemistry provides a good route to obtain fertilizers with unique properties using low soluble metal oxides, carbonates, and hydroxides. It was found that combining urea with low-solubility compounds, such as metal carbonates or sulfates, could produce highly stable urea cocrystals. These cocrystals inherit stability properties from the inorganic parent molecules. As a result, the obtained ionic urea cocrystals possess a lower deliquescence tendency compared to pure urea, which can be highly beneficial for nitrogen management by decreasing its hydrolysis rate. Additionally, crystallizing urea with minerals such as zinc, magnesium, phosphorus, and calcium can provide additional nutrients alongside nitrogen. Calcium carbonate was combined with urea phosphate to produce Ca(H2PO4)2·4CO(NH2)2 using a single-step technique, yielding ionic urea cocrystals from low-solubility minerals. Urea phosphate is produced commercially as a (N
:
P) nutrient source in the liquid phase. However, via a mechanochemistry approach, it could be an excellent precursor for creating more stable urea phosphate-based cocrystals for improved nitrogen management, as shown in Fig. 12. The very recent approach of utilizing Cu- and Zn-containing minerals was reported by Eisa et al.,14 whereby basic Zn and Cu carbonates were reacted with solid commercially available urea–sulfuric acid cocrystals to form CuSO4·3CO(NH2)2·H2O and ZnSO4·CO(NH2)2·2H2O cocrystals. These constituted novel multi-nutrient fertilizer materials with enhanced nitrogen efficiency.
 |
| Fig. 12 The ability to produce improved nitrogen cocrystals based on urea with insoluble minerals.35 | |
The development of cocrystals in agriculture is crucial for decreasing nitrogen leaching and its dangerous consequences on farming or the environment. Using cocrystals can affect farming practices, which is aligned with the agenda of the United Nations for Sustainable Development Goals (SDGs). In this regard, there are three main visions related to agriculture, which are SDG 2 (Zero Hunger), SDG 12 (Responsible Consumption and Production), and SDG 15 (Life on Land). Cocrystallization with urea can be considered as an organo-mineral fertilizer route. This can lead to higher productivity with more nutrients and more controllable fertilizers, in addition to enhancing soil health with lower environmental concerns. Cocrystals based on urea can significantly contribute to climate action by enhancing the efficiency of nitrogen utilization in agriculture, thereby reducing the emission of greenhouse gases such as nitrous oxide. These cocrystals offer a more controlled release of nitrogen, which means that crops receive nutrients more effectively and reduce the need for excessive fertilizer application. This optimized nutrient delivery minimizes the environmental impact of traditional fertilizers. Moreover, the solvent-free mechanochemical synthesis of urea cocrystals reduces energy consumption and eliminates the need for harmful solvents, aligning with sustainable production practices.
5.2. Measurement techniques to assess nitrogen release
Evaluating the release rate and solubility behavior of nutrients is an important aspect of understanding the performance of agrochemical systems. Various methods have been employed in the literature to obtain numerical values, each with its strengths and limitations. Therefore, the most commonly used experimental techniques to assess the cocrystallization ability of fertilizers or their potential to improve NUE will be reviewed in this section with emphasis on mobile nitrogen gases.
One of the most common experiments is the equilibrium solubility study, which is based on determining the maximum amount of a material that dissolves in a specific medium under equilibrium conditions. This method is used to predict the behavior of materials in different environments, such as soil moisture or aquatic systems. The results depend on ionic strength, temperature, and pH. For experimenting, there are three major steps: saturated solution preparation, filtration and drying, and mass measurement. In this regard, Eisa et al. used this method to study the solubility of urea and its cocrystals. They weighed the samples with 4.5 g of the cocrystal and dissolved in a fixed volume of distilled water (5 mL) in a sealed 25 mL beaker. The solution was agitated in a water bath to maintain a consistent temperature for 24 hours. This ensured that the system reached equilibrium, where the solution became saturated, and no further dissolution occurred. After equilibration, undissolved solids were separated from the saturated solution by filtration. Then residual solids were dried overnight at 80 °C to remove water content. The difference between initial mass and residual mass per 5 mL was calculated to obtain the average solubility.14
The nitrogen-release soil experiment is one of the experiments that is designed to study the release (or volatilization) of ammonia from soil after applying nitrogen-containing compounds. The major aim of this experiment is to investigate the loss of nitrogen from the soil in the form of NH3 during a period of incubation. The amount of volatilized ammonia indicates the efficiency of nitrogen use in soil and the impact of different nitrogen sources on the environment. Govoni et al. conducted this experiment by using Oxisol collected from the surface layer (30–40 cm) of an agricultural area in São Carlos, São Paulo State, Brazil.115 The soil had the following characteristics: 608 g per kg sand, 367 g per kg clay, and 25 g per kg silt, based on textural analysis using the pipetting method. It had a water holding capacity (WHC) of 200 g kg−1, a pH of 5.2 (measured with a glass electrode), 8 g kg−1 organic carbon content (measured by the Walkley–Black method), a cation exchange capacity (CEC) of 45 cmolc kg−1, and 4 mg per kg phosphorus content. The cocrystal powders were incubated with 10 g of soil and by using nitrogen application rates between 0.9 and 1.1 g-N per kg of soil in 125 mL polyethylene bottles. The powders were applied to the soil surface, and the soil moisture content was adjusted to 80% of its water-holding capacity by adding 1.6 mL of deionized water per 10 g of soil. A 5 mL acid trap containing 4% boric acid was attached to each bottle to capture volatilized ammonia during the incubation. The samples were incubated for 3, 7, and 14 days in a temperature-controlled room set at 25 °C. The volatilized NH3 was then determined by titrating the boric acid with 0.01 mol L−1 HCl. For inorganic nitrogen extraction, the soil samples were shaken for 1 hour with 100 mL of 1 mol per L KCl, containing 5 mg per L phenylmercuric acetate as a urease inhibitor. The resulting suspensions were filtered using a slow filter (diameter 12.5 cm), and the filtrates were stored in 100 mL polyethylene bottles at 5 °C. Furthermore, the ammonium ion content in the extracts was determined using a colorimetric method. Finally, the nitrogen content of each fraction was expressed as a percentage of the applied nitrogen.115 Eisa et al. assessed volatilized nitrogen loss from cocrystals under elevated relative humidity using a flow-through column setup with four independent channels. An air pump circulates approximately 1.5 L min−1 of air, saturated to ∼90% relative humidity, through each channel. The humidified air was passed through a 250 mL soil chamber containing 130 g of soil with 0.3 g of nitrogen from the cocrystals. The outlet air stream was directed through a sulfuric acid scrubber (0.2 N) to capture volatilized ammonia. Ammonium nitrogen content was measured by periodic alkaline titration.14 A static chamber was used by Honer et al. in batch mode. A total of 90 g of silt loam soil was used, and nitrogen was applied in the form of urea or the cocrystal with 0.09 g of nitrogen per 1 g of soil (equivalent to 1 mg of nitrogen per gram of soil). For the experiment, 0.1929 g of urea and 0.3022 g of CaSO4·4CO(NH2)2 were spread on the soil surface in separate trials. NH3 emissions were measured over 48 hours using an NH3 single gas detector that was placed inside the reaction chamber. This experiment was conducted under static conditions within a sealed chamber at 23 °C and 50–60% relative humidity.36
While nitrogen gas release measurements are routine in the laboratory, nitrogen balance measurements in the field present certain challenges yet are necessary to assess the suitability of cocrystals in affecting the overall nitrogen and fertilizer production energy balance. Hence, opportunities lie in the measurements that can provide the data for environmental impact assessment using the life cycle approach. In particular, while NH3 is a common product of urea volatilization, nitrification into NO3− and its denitrification are responsible for N2 and N2O emissions as well as leaching of reactive nitrogen species into solution. The development of measurement systems that account for all the volatile and mobile nitrogen species with high accuracy is necessary.
6. Conclusions and future perspectives
This review underscores the transformative potential of diverse agrochemical purpose molecule cocrystallization in advancing agricultural sustainability by addressing the inherent challenges of traditional fertilizers, such as moisture absorption, thermal decomposition, and ammonia gas release. The significance of cocrystallization can be demonstrated, as it can significantly enhance the stability, efficacy, and environmental friendliness of urea. Cocrystallization can also be used to incorporate essential macronutrients and micronutrients into urea cocrystals to provide nutrient-balanced materials with multifunctional properties. This leads to providing a strong nutrient delivery system that promotes balanced nitrogen uptake and acts as a urease inhibitor, further mitigating environmental impact. The need and the opportunity lie in nutrient management technologies that can be afforded by the cocrystallization of nutrient-containing molecules:
• Major nutrient-containing cocrystals are prone to nutrient loss due to the propensity to react and undergo transformations in moist soil. This category includes macronutrients that are based on nitrogen, which has been the focus of most research to date. Much less is known about potassium-containing cocrystals since only a few examples of them exist in the modern literature. This is related to the low polarizability of potassium ions and novel formulations are needed that include secondary salts to delocalize outer electrons;
• Nutrient-balanced fertilizer materials that incorporate a few or many nutrients, such as N, P, K, Ca, S, and Mg, which are required in large quantities, and micronutrients, such as Fe, Mn, Cu, and Zn, which are required in smaller quantities. A related challenge is ensuring that formulations adhere to the fundamental nutrient ratios necessary for plants;
• Soil health is heavily dependent on the presence of an organic carbon pool. For example, the co-localization of organic carbon with nitrogen can facilitate microbial assimilation for the production of large biomolecules with beneficial effects on soil. The utility of cocrystallization here lies in combining renewably sourced carbon molecules, such as carboxylic acids. Carbon–urea cocrystals that are derived from natural organic matter are a few examples where large-scale formulation can be useful in fostering soil health.
• Finally, technological advancements are mainly based on mechanochemical approaches. The methods based on mechanochemical approaches are green engineering approaches that facilitate the production of urea cocrystals in a sustainable and scalable manner. This solvent-free technique aligns with environmental sustainability principles, which makes it an attractive option for future fertilizer production. In a practical context, for farmers and the agricultural industry, urea cocrystals give practical benefits such as ease of storage, handling, and application. These tailored fertilizers can lead to more efficient nutrient use, reducing the need for frequent applications and lowering operational costs.
The overuse of conventional pesticides and fungicides in agriculture has led to widespread issues such as pest and fungal resistance. Cocrystallization offers a solution by enabling slow-release formulations that deliver only the right/sufficient amount of protection while preventing excessive application. To maximize effectiveness, these formulations must be carefully studied and optimized to achieve the ideal release rate to ensure efficient protection without overuse. In addition, cocrystallizing urea with essential macronutrients and micronutrients can balance and gradually control the nutrient delivery in soil. This might aim to maintain soil fertility over time by reducing the need for excessive chemicals. This can occur because the slow-release cocrystals will provide nutrients over a longer period, which might also help in salinization. Moreover, cocrystals can decrease the chances of nutrient run-off and pesticide leaching due to their controlled-sustained release. Therefore, strategic cocrystallization of urea with compatible molecules can represent a significant advancement in crystal engineering. Future research can be directed into the path of experimenting with the currently used materials in agriculture with urea at different molar ratios to estimate the appropriate ratio for co-crystallization. In particular, expanding the available list of utility chemical compounds that can be cocrystallized with urea would enable the creation of targeted crystalline materials for precision delivery of specific functionality. Opportunities exist in the data-driven discovery of such materials given the large array of organic materials available for agricultural practices but their utility is limited in their pure form.
Data availability
No primary research results, software or code have been included and no new data were generated or analysed as part of this review.
Conflicts of interest
There are no conflicts to declare.
Acknowledgements
This work was supported by the Engineering for Agricultural Production Systems program grant no. 2020-67022-31144 from the USDA National Institute of Food and Agriculture.
References
- J. Baltrusaitis, B. Bakashi, K. Chojnacka, C. Chuck, M. O. Coppens and J. S. Edge,
et al., IOP journal sustainability science and technology (sus sci tech) in 2024 and beyond: equitable publishing aligned with United Nations’ sustainable development goals (SDGs), Sustain. Sci. Tecnolog., 2024, 1, 010201 CrossRef.
- G. Pe'er, A. Bonn, H. Bruelheide, P. Dieker, N. Eisenhauer and P. H. Feindt,
et al., Action needed for the EU Common Agricultural Policy to address sustainability challenges, People Nat., 2020, 2(2), 305–316 CrossRef PubMed.
- M. Lykogianni, E. Bempelou, F. Karamaouna and K. A. Aliferis, Do pesticides promote or hinder sustainability in agriculture? The challenge of sustainable use of pesticides in modern agriculture, Sci. Total Environ., 2021, 795, 148625 CrossRef CAS PubMed.
-
Statista. Statista, Production of Fertilizers Worldwide from 2005 to 2022, by Nutrient, 2024 Search PubMed.
- P. S. Bindraban, C. O. Dimkpa, J. C. White, F. A. Franklin, A. Melse-Boonstra and N. Koele,
et al., Safeguarding human and planetary health demands a fertilizer sector transformation, Plants People Planet, 2020, 2(4), 302–309 CrossRef.
- C. O. Dimkpa, J. Fugice, U. Singh and T. D. Lewis, Development of fertilizers for enhanced nitrogen use efficiency – Trends and perspectives, Sci. Total Environ., 2020, 731, 139113 CrossRef CAS PubMed . https://www.sciencedirect.com/science/article/pii/S0048969720326309.
- M. Klimczyk, A. Siczek and L. Schimmelpfennig, Improving the efficiency of urea-based fertilization leading to reduction in ammonia emission, Sci. Total Environ., 2021, 771, 145483 CrossRef CAS PubMed . https://www.sciencedirect.com/science/article/pii/S0048969721005519.
- J. W. Oh, S. S. C. Pushparaj, M. Muthu and J. Gopal, Review of Harmful Algal Blooms (HABs) Causing Marine Fish Kills: Toxicity and Mitigation, Plants, 2023, 12(23), 3936 CrossRef CAS PubMed.
- S. Singh, A. G. Anil, V. Kumar, D. Kapoor, S. Subramanian and J. Singh,
et al., Nitrates in the environment: A critical review of their distribution, sensing techniques, ecological effects and remediation, Chemosphere, 2022, 287, 131996 CrossRef CAS PubMed . https://www.sciencedirect.com/science/article/pii/S0045653521024681.
-
A. Dubey and D. R. Mailapalli, Nanofertilisers, nanopesticides, nanosensors of pest and nanotoxicity in agriculture, Sustainable Agriculture Reviews: Volume 19. 2016, pp. 307–330 Search PubMed.
- A. E. Larsen, M. Patton and E. A. Martin, High highs and low lows: Elucidating striking seasonal variability in pesticide use and its environmental implications, Sci. Total Environ., 2019, 651, 828–837 CrossRef CAS PubMed.
- L. Fang, Y. Xiao, C. Zhang, Z. Gao, S. Wu and J. Gong,
et al., Intermolecular interactions and solubility behavior of multicomponent crystal forms of 2, 4-D: design, structure analysis, and solid-state characterization, CrystEngComm, 2021, 23(43), 7615–7627 RSC.
- J. Li, C. Li, X. Ji, Q. Sun, Z. Li and H. Liu,
et al., Combined virtual and experimental screening of multicomponent crystals of 2, 4-dichlorophenoxyacetic acid, New J. Chem., 2022, 46(18), 8708–8719 RSC.
- M. Eisa, J. G. Farias, M. Ammar, R. Bortoletto-Santos, C. Ribeiro and C. Williams,
et al., Mechanochemical Synthesis of Nitrogen-Efficient Zn-and Cu-Sulfate Urea Cocrystals from Carbonate Minerals, ACS Sustainable Resour. Manage., 2024, 1(7), 1363–1376 CrossRef CAS.
- G. I. Ågren, Stoichiometry and nutrition of plant growth in natural communities, Annu. Rev. Ecol. Evol. Syst., 2008, 39, 153–170 CrossRef.
- B. E. Channab, C. E. Elhassani, Y. Essamlali, S. E. Marrane, A. Chakir and M. Zahouily, Urea-loaded hydroxyapatite–carboxylated cellulose composites as slow-release N fertilizer pellets for efficient delivery of nitrogen, Ind. Eng. Chem. Res., 2023, 62(37), 14853–14865 CrossRef CAS.
- H. Jariwala, R. M. Santos, J. D. Lauzon, A. Dutta and Y. Wai Chiang, Controlled release fertilizers (CRFs) for climate-smart agriculture practices: a comprehensive review on release mechanism, materials, methods of preparation, and effect on environmental parameters, Environ. Sci. Pollut. Res., 2022, 29(36), 53967–53995 CrossRef CAS PubMed.
- A. B. da Fonseca, C. Santos, A. P. P. Nunes, D. P. Oliveira, M. E. A. de Melo and T. Takayama,
et al., Urease inhibitors technologies as strategy to mitigate agricultural ammonia emissions and enhance the use efficiency of urea-based fertilizers, Sci. Rep., 2023, 13(1), 22739 CrossRef CAS PubMed.
-
L. Casali, Crystal Engineering Strategies for a Healthier Environment: Solid-State Syntheses and Characterization of Organic/inorganic Co-crystals and Host-Guest Systems with Improved Stability and Performance Activities, PhD Thesis, 2021 DOI:10.48676/unibo/amsdottorato/9804.
- Y. Xiao, C. Wu, P. Cui, L. Zhou and Q. Yin, Pursuing Green and Efficient Agriculture from Molecular Assembly: A Review of Solid-State Forms on Agrochemicals, J. Agric. Food Chem., 2023, 71(28), 10500–10524 CrossRef CAS PubMed.
- T. Rajbongshi, S. Parakatawella, D. Gogoi, P. Deka, N. M. Adassooriya and R. Thakuria, Mechanosynthesis of urea–hydroxybenzoic acid cocrystals as sustained-release nitrogen fertilizer, RSC Sustainability, 2023, 1(6), 1416–1422 RSC.
- B. Sandhu, A. S. Sinha, J. Desper and C. B. Aakeröy, Modulating the physical properties of solid forms of urea using co-crystallization technology, Chem. Commun., 2018, 54(37), 4657–4660, 10.1039/C8CC01144C.
- N. M. Adassooriya, S. P. Mahanta and R. Thakuria, Mechanochemistry as an emerging tool for the preparation of sustained release urea cocrystals as a nitrogen source, CrystEngComm, 2022, 24(9), 1679–1689, 10.1039/D1CE01713F.
- C. Lee, A. Y. Cho, W. Yoon, H. Yun, J. W. Kang and J. Lee, Cocrystal formation via resorcinol–urea interactions: Naringenin and carbamazepine, Cryst. Growth Des., 2019, 19(7), 3807–3814 CrossRef CAS.
- S. Swify, D. Avizienyte, R. Mazeika and Z. Braziene, Influence of modified urea compounds to improve nitrogen use efficiency under corn growth system, Sustainability, 2022, 14(21), 14166 CrossRef CAS.
- S. Harkema and D. Feil, The crystal structure of urea nitrate, Acta Crystallogr. B, 1969, 25(3), 589–591 CrossRef CAS.
- A. D. Joshua, D. DeTata, R. Fillingham, R. Dunsmore and S. W. Lewis, Synthesis and characterisation of homemade urea nitrate explosive from commercial sources of urea, J. Forensic Chem., 2021, 26, 100369 CrossRef.
- C. Navizaga, J. Boecker, A. M. Sviklas, J. Galeckiene, J. Baltrusaitis and N. Adjustable, P2O5 ratio urea phosphate fertilizers for sustainable phosphorus and nitrogen use: Liquid phase equilibria via solubility measurements and raman Spectroscopy, ACS Sustain. Chem. Eng., 2017, 5(2), 1747–1754 CrossRef CAS.
- C. A. Morrison, M. M. Siddick, P. J. Camp and C. C. Wilson, Toward Understanding Mobile Proton Behavior from First Principles Calculation: The Short Hydrogen Bond in Crystalline Urea–Phosphoric Acid, J. Am. Chem. Soc., 2005, 127(11), 4042–4048 CrossRef CAS PubMed.
- J. M. Bremner and L. A. Douglas, Decomposition of Urea Phosphate in Soils, Soil Sci. Soc. Am. J., 1971, 35(4), 575–578, DOI:10.2136/sssaj1971.03615995003500040028x.
- H. Moawad, M. H. Enany, S. M. S. B. El-Din, S. A. Z. Mahmoud and R. F. Gamal, Transformations and effects of urea derivatives in soil, Z. für Pflanzenernährung Bodenkunde, 1984, 147(6), 785–792 CrossRef CAS.
- L. Casali, L. Mazzei, O. Shemchuk, K. Honer, F. Grepioni and S. Ciurli,
et al., Smart urea ionic co-crystals with enhanced urease inhibition activity for improved nitrogen cycle management, Chem. Commun., 2018, 54(55), 7637–7640 RSC.
-
R. Zollinger, K. Howatt, M. Bernards, D. Peterson and B. Young, Efficacy of acidic ammonium sulfate replacement adjuvants, in Pesticide Formulation and Delivery Systems: 32nd Volume, Innovating Legacy Products for New Uses, ASTM International, 2013, pp. 183–195 Search PubMed.
- D. L. Shaner, P. Westra and S. Nissen, AMADS Increases the Efficacy of Glyphosate Formulations on Corn, Weed Technol., 2006, 20(1), 179–183 CrossRef CAS . https://www.cambridge.org/core/product/38FA074E56CE557D22517D92E864124C.
- K. Honer, C. Pico and J. Baltrusaitis, Reactive mechanosynthesis of urea ionic cocrystal fertilizer materials from abundant low solubility magnesium-and calcium-containing minerals, ACS Sustain. Chem. Eng., 2018, 6(4), 4680–4687 CrossRef CAS.
- K. Honer, E. Kalfaoglu, C. Pico, J. McCann and J. Baltrusaitis, Mechanosynthesis of magnesium and calcium salt–urea ionic cocrystal fertilizer materials for improved nitrogen management, ACS Sustain. Chem. Eng., 2017, 5(10), 8546–8550 CrossRef CAS.
- J. Zhao, C. Jia, X. Fang, A. Xiao and H. Zhang, Utilization of industrial by-product gypsum to prepare urea gypsum cocrystals as a sustained release fertilizer: A review, Asia-Pac. J. Chem. Eng., 2024, 19(4), e3066, DOI:10.1002/apj.3066.
- J. Zhao, C. Jia, X. Fang, A. Xiao and H. Zhang, Utilization of industrial by-product gypsum to prepare urea gypsum cocrystals as a sustained release fertilizer: A review, Asia Pac. J. Chem. Eng., 2024, e3066 CrossRef CAS.
- P. Bista, M. Eisa, D. Ragauskaitė, S. Sapkota, J. Baltrusaitis and R. Ghimire, Effect of Urea-Calcium Sulfate Cocrystal Nitrogen Fertilizer on Sorghum Productivity and Soil N2O Emissions, Sustainability, 2023, 15(10), 8010 CrossRef CAS.
- K. Barčauskaitė, Z. Brazienė, D. Avižienytė, M. Silva, D. Drapanauskaite and K. Honer,
et al., Mechanochemically synthesized gypsum and gypsum drywall waste cocrystals with urea for enhanced environmental sustainability fertilizers, J. Environ. Chem. Eng., 2020, 8(4), 103965 CrossRef.
- I. Brekalo, V. Martinez, B. Karadeniz, P. Orešković, D. Drapanauskaite and H. Vriesema,
et al., Scale-up of agrochemical urea-gypsum cocrystal synthesis using thermally controlled mechanochemistry, ACS Sustain. Chem. Eng., 2022, 10(20), 6743–6754 CrossRef CAS.
- P. A. Julien, L. S. Germann, H. M. Titi, M. Etter, R. E. Dinnebier and L. Sharma,
et al., In situ monitoring of mechanochemical synthesis of calcium urea phosphate fertilizer cocrystal reveals highly effective water-based autocatalysis, Chem. Sci., 2020, 11(9), 2350–2355 RSC.
- O. B. Ibrahim, Complexes of urea with Mn(II), Fe(III), Co(II), and Cu(II) metal ions, Adv. Appl. Sci. Res., 2012, 3(6), 18 Search PubMed.
- T. Guha, G. Gopal, A. Mukherjee and R. Kundu, Fe3O4-urea nanocomposites as a novel nitrogen fertilizer for improving nutrient utilization efficiency and reducing environmental pollution, Environ. Pollut., 2022, 292, 118301 CrossRef CAS PubMed.
- M. Y. A. Zuluaga, M. Cardarelli, Y. Rouphael, S. Cesco, Y. Pii and G. Colla, Iron nutrition in agriculture: From synthetic chelates to biochelates, Sci. Hortic., 2023, 312, 111833 CrossRef CAS.
- R. Hänsch and R. R. Mendel, Physiological functions of mineral micronutrients (cu, Zn, Mn, Fe, Ni, Mo, B, cl), Curr. Opin. Plant Biol., 2009, 12(3), 259–266 CrossRef PubMed.
- R. Rajpoot, A. Rani, R. K. Srivastava, P. Pandey and R. S. Dubey, Protective role of Mentha arvensis aqueous extract against manganese induced toxicity by reducing Mn translocation and promoting antioxidative defense in growing Indica rice seedlings, J. Crop Sci. Biotechnol., 2018, 21, 353–366 CrossRef.
- M. M. Khan, M. H. Harunsani, A. L. Tan, M. Hojamberdiev, S. Azamay and N. Ahmad, Antibacterial activities of zinc oxide and Mn-doped zinc oxide synthesized using Melastoma malabathricum (L.) leaf extract, Bioprocess Biosyst. Eng., 2020, 43, 1499–1508 CrossRef CAS PubMed.
- H. Aghabozorg, G. J. Palenik, R. C. Stoufer and J. Summers, Dynamic Jahn-Teller effect in a manganese (III) complex. Synthesis and structure of hexakis (urea) manganese (III) perchlorate, Inorg. Chem., 1982, 21(11), 3903–3907 CrossRef CAS.
- T. J. Prior and R. L. Kift, Synthesis and crystal structures of two metal urea nitrates, J. Chem. Crystallogr., 2009, 39, 558–563 CrossRef CAS.
- L. Mazzei, V. Broll, L. Casali, M. Silva, D. Braga and F. Grepioni,
et al., Multifunctional urea cocrystal with combined ureolysis and nitrification inhibiting capabilities for enhanced nitrogen management, ACS Sustain. Chem. Eng., 2019, 7(15), 13369–13378 CrossRef CAS.
- A. Krawczuk and K. Stadnicka, Hydrogen bonding in diaquatetrakis (urea-κO) MII dinitrates, with M= Ni and Co, Acta Crystallogr. C, 2007, 63(10), m448–m450 CrossRef CAS PubMed.
- D. J. Dahiya, J. P. Singh and V. Kumar, Nitrogen uptake in wheat as influenced by the presence of nickel, Arid Land Res. Manag., 1994, 8(1), 51–58 CrossRef CAS.
- L. Casali, L. Mazzei, O. Shemchuk, L. Sharma, K. Honer and F. Grepioni,
et al., Novel dual-action plant fertilizer and urease inhibitor: urea·Catechol cocrystal. Characterization and environmental reactivity, ACS Sustain. Chem. Eng., 2018, 7(2), 2852–2859 CrossRef.
- E. M. Brear, D. A. Day and P. M. C. Smith, Iron: an essential micronutrient for the legume-rhizobium symbiosis, Front. Plant Sci., 2013, 4, 359 Search PubMed.
- C. W. Whittaker, F. O. Lundstrom and S. B. Hendricks, Reaction between Urea and Gypsum, Ind. Eng. Chem., 1933, 25(11), 1280–1282, DOI:10.1021/ie50287a022.
- A. W. Frazier, J. R. Lehr and J. P. Smith, Urea-monocalcium phosphate, a component of mixed fertilizers, J. Agric. Food Chem., 1967, 15(2), 345–347, DOI:10.1021/jf60150a025.
-
E. Kotuła and R. Nowak, Czteromocznikan siarczanu wapnia-nawóz azotowo-siarkowo-wapniowy jako alternatywa utylizacji fosfogipsu, Prace Naukowe Politechniki Szczecińskiej Instytut Technologii Nieorganicznej, 1998, pp. 91–96 Search PubMed.
- P. Malinowski, A. Biskupski and J. Głowiński, Preparation methods of calcium sulphate and urea adduct, Pol. J. Chem. Technol., 2007, 9(4), 111–114 CrossRef CAS.
- M. Borowik, P. Malinowski, A. Biskupski, M. Dawidowicz, S. Schab and P. Rusek,
et al., Production technology of nitrogen-sulphur-calcium fertilizers on the base of urea and phosphogypsum, Chemik, 2012, 66(5), 525–534 CAS.
- M. Gutiérrez-Larraínzar, J. Rúa, I. Caro, C. de Castro, D. de Arriaga and M. R. García-Armesto,
et al., Evaluation of antimicrobial and antioxidant activities of natural phenolic compounds against foodborne pathogens and spoilage bacteria, Food Control, 2012, 26(2), 555–563 CrossRef.
- Y. Chen, Y. Peng, C. C. Dai and Q. Ju, Biodegradation of 4-hydroxybenzoic acid by Phomopsis liquidambari, Appl. Soil Ecol., 2011, 51, 102–110 CrossRef.
-
T. W. Z. Luhui, Method for Preparing Agricultural Fungicide Glutaric Acid Copper, 2016 Search PubMed.
- C. R. T. Kumari, S. Sudha, G. Vinitha, M. Nageshwari, M. L. Caroline and G. Mathubala,
et al., Synthesis and characterization analysis of unique organic crystal–Urea Glutaric acid, an optimistic candidate for optical device applications, Phys. B Condens. Matter, 2020, 577, 411804 CrossRef.
- M. Carocho, P. Morales and I. C. F. R. Ferreira, Antioxidants: Reviewing the chemistry, food applications, legislation and role as preservatives, Trends Food Sci. Technol., 2018, 71, 107–120 CrossRef CAS.
- A. Shanthi, C. Krishnan and P. Selvarajan, Growth and characterization of a single crystal of Urea Adipic acid (UAA)–A third order nonlinear optical material, Spectrochim. Acta, Part A, 2014, 122, 521–528 CrossRef CAS PubMed.
- S. Parakatawella, D. Gogoi, P. Deka, Y. Xu, C. Sandaruwan and A. C. A. Jayasundera,
et al., Mechanochemical Synthesis of Polymorphic Urea·Adipic Acid Cocrystal as a Sustained-Release Nitrogen Source, ChemSusChem, 2022, 15(3), e202102445 CrossRef CAS PubMed.
- A. Moradi, M. Abolfathi, M. Javadian, E. Heidarian, H. Roshanmehr and M. Khaledi,
et al., Gallic acid exerts nephroprotective, anti-oxidative stress, and anti-inflammatory effects against diclofenac-induced renal injury in malerats, Arch. Med. Res., 2021, 52(4), 380–388 CrossRef CAS PubMed.
- A. Nouri, F. Heibati and E. Heidarian, Gallic acid exerts anti-inflammatory, anti-oxidative stress, and nephroprotective effects against paraquat-induced renal injury in male rats, Naunyn-Schmiedebergs Arch. Naunyn-Schmiedebergs Arch. Pharmakol., 2021, 394, 1–9 CrossRef CAS PubMed.
- K. L. Jyothi, R. Gautam, D. Swain, T. N. Guru Row and N. K. Lokanath, Cocrystals of gallic acid with urea and propionamide: supramolecular structures, Hirshfeld surface analysis, and DFT studies, Cryst. Res. Technol., 2019, 54(8), 1900016 CrossRef.
- C. Marques, A. R. Sotiles, F. O. Farias, G. Oliveira, M. L. Mitterer-Daltoe and M. L. Masson, Full physicochemical characterization of malic acid: Emphasis in the potential as food ingredient and application in pectin gels, Arab. J. Chem., 2020, 13(12), 9118–9129 CrossRef CAS.
- Y. S. Do, H. J. Whang, J. E. Ku and K. R. Yoon, Organic acids content of the selected Korean apple cultivars, J. Food Sci. Technol., 2005, 37(6), 922–927 Search PubMed.
- J. W. Daniel, The metabolism of L-and DL-malic acids by rats, Food Cosmet. Toxicol., 1969, 7, 103–106 CrossRef CAS PubMed.
- T. L. Chang, R. P. Streicher, H. Zimmer and J. W. Munch, The Intehaction of Aqueous Solutions of Chlorine with Malic Acid, Tartaric Acid, and Various Fruit Juices: A Source of Mutagens, Anal. Lett., 1988, 21(11), 2049–2067 CrossRef CAS.
-
V. Schneider and S. Troxell, Acidity Management in Musts & Wines: Acidification, Deacidification, and Crystal Stabilization, Board and Bench Publishing, 2018 Search PubMed.
- A. Krawczuk, M. Gryl, M. B. Pitak and K. Stadnicka, Electron density distribution of urea in co-crystals with rigid and flexible dicarboxylic acids, Cryst. Growth Des., 2015, 15(11), 5578–5592 CrossRef CAS.
- N. Kanagathara, R. Bhavani, A. Y. Lo, M. K. Marchewka and J. Janczak, Structural, vibrational characterization and DFT calculations of urea: DL-malic acid (1: 1)–co-crystal, J. Mol. Struct., 2022, 1270, 133930 CrossRef CAS.
- E. Zaini, F. L. Afriyani, F. Ismed, A. Horikawa and H. Uekusa, Improved solubility and dissolution rates in novel multicomponent crystals of piperine with succinic acid, Sci. Pharm., 2020, 88(2), 21 CrossRef CAS.
- R. J. Mailloux, Still at the center of it all; novel functions of the oxidative Krebs cycle, Bioenergetics, 2015, 4(1), 1–14 Search PubMed.
- I. V. Zarubina, M. V. Lukk and P. D. Shabanov, Antihypoxic and antioxidant effects of exogenous succinic acid and aminothiol succinate-containing antihypoxants, Bull. Exp. Biol. Med., 2012, 153, 336–339 CrossRef CAS PubMed.
- T. Zhang, Q. Yu, X. Li and X. Ma, Preparation of 2: 1 urea-succinic acid cocrystals by sublimation, J. Cryst. Growth, 2017, 469, 114–118 CrossRef CAS.
- B. K. Singh, N. Sinha, N. Singh, K. Kumar, M. K. Gupta and B. Kumar, Structural, dielectric, optical and ferroelectric property of urea succinic acid crystals grown in aqueous solution containing maleic acid, J. Phys. Chem. Solids, 2010, 71(12), 1774–1779 CrossRef CAS.
- A. Alhalaweh, S. George, D. Boström and S. P. Velaga, 1: 1 and 2: 1 Urea–succinic acid cocrystals: structural diversity, solution chemistry, and thermodynamic stability, Cryst. Growth Des., 2010, 10(11), 4847–4855 CrossRef CAS.
- N. Keshavarzi, S. Cao and M. Antonietti, A new conducting polymer with exceptional visible-light photocatalytic activity derived from barbituric acid polycondensation, Adv. Mater., 2020, 32(16), 1907702 CrossRef CAS PubMed.
- Y. Feng, H. Lu, M. Whiteway and Y. Jiang, Understanding fluconazole tolerance in Candida albicans: Implications for effective treatment of candidiasis and combating invasive fungal infections, J. Global Antimicrob. Resist., 2023, 314–321 CrossRef CAS PubMed.
- M. Janowski, O. M. Demchuk and M. Wujec, Fluconazole Analogs and Derivatives: An Overview of Synthesis, Chemical Transformations, and Biological Activity, Molecules, 2024, 29(12), 2855 Search PubMed.
- T. S. Adewale and O. O. Abosede, Synthesis and Spectroscopic Characterization of Co-Crystals of Fluconazole with Succinic Acid and Urea as Coformer, Mediterr. J. Basic Appl. Sci., 2022, 6(1), 1–6 Search PubMed.
- E. Skořepová, M. Hušák, J. Čejka, P. Zámostný and B. Kratochvíl, Increasing dissolution of trospium chloride by co-crystallization with urea, J. Cryst. Growth, 2014, 399, 19–26 CrossRef.
-
S. Devi, in A Centum of Valuable Plant Bioactives, Catechins, Elsevier, 2021, pp. 525–544 Search PubMed.
- L. Ciumărnean, M. V. Milaciu, O. Runcan, C. Vesa Ştefan, A. L. Răchişan and V. Negrean,
et al., The effects of flavonoids in cardiovascular diseases, Molecules, 2020, 25(18), 4320 CrossRef PubMed.
- J. Bae, N. Kim, Y. Shin, S. Y. Kim and Y. J. Kim, Activity of catechins and their applications, Biomed. Dermatol., 2020, 4, 1–10 CrossRef.
- V. Nagaraju, C. Jange, C. Wassgren and K. Ambrose, Understanding Urea Polymorphism and Cocrystallization to Develop Enhanced Fertilizers: A Review, J. Environ. Chem. Eng., 2024, 114308 Search PubMed.
- F. Leng, K. Robeyns and T. Leyssens, Urea as a cocrystal former—Study of 3 urea based pharmaceutical cocrystals, Pharmaceutics, 2021, 13(5), 671 CrossRef CAS PubMed.
- D. K. Maity, R. K. Paul and G. R. Desiraju, Drug–drug binary solids of nitrofurantoin and trimethoprim: crystal engineering and pharmaceutical properties, Mol. Pharm., 2020, 17(12), 4435–4442 CrossRef CAS PubMed.
- X. Y. Teoh, F. N. bt Mahyuddin, W. Ahmad and S. Y. Chan, Formulation strategy of nitrofurantoin: co-crystal or solid dispersion?, Pharm. Dev. Technol., 2020, 25(2), 245–251 CrossRef CAS PubMed.
- E. Khan, A. Shukla, M. A. S. Al-Hanafi, P. Tandon and V. R. Vangala, Structural insights, spectral and H-bond analyses, of nitrofurantoin-phenazine cocrystal and comparison of its chemical reactivity with other nitrofurantoin cocrystals, J. Mol. Struct., 2022, 1247, 131387 CrossRef CAS.
- S. Cherukuvada, N. J. Babu and A. Nangia, Nitrofurantoin–p-aminobenzoic acid cocrystal: Hydration stability and dissolution rate studies, J. Pharm. Sci., 2011, 100(8), 3233–3244 CrossRef CAS PubMed.
- M. Silva, K. Barcauskaite, D. Drapanauskaite, H. Tian, T. Bučko and J. Baltrusaitis, Relative humidity facilitated urea particle reaction with salicylic acid: a combined in situ spectroscopy and DFT study, ACS Earth Space Chem., 2020, 4(7), 1018–1028 CrossRef CAS.
- E. D. Clarke and J. S. Delaney, Physical and molecular properties of agrochemicals: an analysis of screen inputs, hits, leads, and products, Chimia, 2003, 57(11), 731 CrossRef CAS.
- J. C. Anderson, C. Dubetz and V. P. Palace, Neonicotinoids in the Canadian aquatic environment: a literature review on current use products with a focus on fate, exposure, and biological effects, Sci. Total Environ., 2015, 505, 409–422 CrossRef CAS PubMed.
- D. Wang, N. B. Saleh, A. Byro, R. Zepp, E. Sahle-Demessie and T. P. Luxton,
et al., Nano-enabled pesticides for sustainable agriculture and global food security, Nat. Nanotechnol., 2022, 17(4), 347–360 CrossRef CAS PubMed.
- B. S. Sekhon, Co-crystals of agrochemical actives, Int. J. Agric. Sci., 2015, 5(3), 472–475 Search PubMed.
- O. Chovnik, S. R. Cohen, I. Pinkas, L. Houben, T. E. Gorelik and Y. Feldman,
et al., Noncovalent Bonding Caught in Action: From Amorphous to Cocrystalline Molecular Thin Films, ACS Nano, 2021, 15(9), 14643–14652 CrossRef CAS PubMed.
- P. C. Vioglio, M. R. Chierotti and R. Gobetto, Pharmaceutical aspects of salt and cocrystal forms of APIs and characterization challenges, Adv. Drug Deliv. Rev., 2017, 117, 86–110 CrossRef PubMed.
- Y. Xiao, C. Wu, L. Zhou, Q. Yin and J. Yang, Cocrystal engineering strategy for sustained release and leaching reduction of herbicides: a case study of metamitron, Green Chem., 2022, 24(20), 8088–8099 RSC.
- M. Li, J. Wang, X. Xu, G. Ren, B. Zhu and M. Hong,
et al., Study of cycloxaprid co-crystals: characterization, theory calculation, solubility, and stability, Cryst. Growth Des., 2022, 22(7), 4437–4452 CrossRef CAS.
- H. Qu, S. Wu and J. Gong, A sustainable and smart fungicide release platform through cocrystal nanocapsules for improved utilization rate and environmental safety, Chem. Eng. J., 2023, 473, 145284 CrossRef CAS.
- H. Qu, Y. Gao, L. Zhou, S. Wu and J. Gong, Construction of fungicide nano delivery platform through crystal engineering for sustainable fungal control, Chem. Eng. J., 2024, 490, 151902 CrossRef CAS.
- P. P. Mazzeo, C. Carraro, A. Monica, D. Capucci, P. Pelagatti and F. Bianchi,
et al., Designing a palette of cocrystals based on essential oil constituents for agricultural applications, ACS Sustain. Chem. Eng., 2019, 7(21), 17929–17940 CrossRef CAS.
- D. Wu, J. Li, Y. Xiao, X. Ji, C. Li and B. Zhang,
et al., New salts and cocrystals of pymetrozine with improvements on solubility and humidity stability: Experimental and theoretical study, Cryst. Growth Des., 2021, 21(4), 2371–2388 CrossRef CAS.
- L. Fang, Y. Ma, Y. Xiao, Z. Li, Z. Gao and S. Wu,
et al., Theoretical and Structural Understanding of the Different Factors Influencing the Formation of Multicomponent Crystals of 2, 4-Dichlorophenoxyacetic Acid with N-heterocyclic Compounds, Cryst. Growth Des., 2022, 22(3), 1707–1719 CrossRef CAS.
- P. S. Carvalho, G. G. F. Guimarães, L. F. Diniz, J. Ellena and C. Ribeiro, Highly water soluble agrichemicals by using engineered organic salts for reducing adverse environmental impacts, Green Chem., 2019, 21(23), 6419–6429 RSC.
- N. Pawar, A. Saha, N. Nandan and J. V. Parambil, Solution cocrystallization: A scalable approach for cocrystal production, Crystals, 2021, 11(3), 303 CrossRef CAS.
- D. A. Daramola and M. C. Hatzell, Energy demand of nitrogen and phosphorus based fertilizers and approaches to circularity, ACS Energy Lett., 2023, 8(3), 1493–1501 CrossRef CAS.
- B. M. Govoni, R. Bortoletto-Santos, J. G. Farias, C. S. Farinas, M. Ammar and C. Ribeiro,
et al., Mechanochemically Synthesized Nitrogen-Efficient Mg-and Zn-Ammonium Carbonate Fertilizers, ACS Sustain. Chem. Eng., 2024, 12(16), 6182–6193 CrossRef.
|
This journal is © The Royal Society of Chemistry 2025 |
Click here to see how this site uses Cookies. View our privacy policy here.