DOI:
10.1039/D1NA00734C
(Paper)
Nanoscale Adv., 2022,
4, 1345-1350
Ligand-assisted deposition of ultra-small Au nanodots on Fe2O3/reduced graphene oxide for flexible gas sensors†
Received
9th October 2021
, Accepted 17th January 2022
First published on 2nd February 2022
Abstract
The development of flexible room-temperature gas sensors is important in environmental monitoring and protection. In this contribution, by using 1-octadecanethiol (ODT) as a surface ligand, Au nanodots (NDs) with ultra-small size of ∼1.7 nm were deposited on the surface of α-Fe2O3/reduced graphene oxide (rGO). The Au ND–ODT/α-Fe2O3/rGO composite was fabricated into flexible gas sensors, which could detect NO2 gas down to 200 ppb at room temperature. Compared with α-Fe2O3/rGO, Au ND–ODT/α-Fe2O3/rGO showed enhanced sensing performance because of the beneficial effects of Au NDs, including facilitating the adsorption of NO2 molecules and forming ohmic-like contact with rGO and α-Fe2O3. In addition, the sensing performance of the composite was also influenced by the surface ligands of the Au NDs. Ligands with less polar terminal groups were found to be beneficial to charge transfer in the sensing film. Moreover, Au ND–ODT/α-Fe2O3/rGO-based flexible sensors showed negligible performance deterioration under moderately bent conditions, suggesting their potential to be used in portable and wearable devices.
1. Introduction
The fast technological and industrial development has led to increasingly serious air pollution. Among the several gaseous pollutants in air, nitrogen dioxide (NO2), which is usually produced by fuel burning and vehicle exhausts,1 can cause several pulmonary diseases such as pulmonary edema, tracheitis and pneumothorax, and is also the main cause for acid rain. Therefore, the development of highly sensitive and selective NO2 gas sensors is important to environmental monitoring and protection.2,3 In addition, making gas sensors flexible can enable their integration into portable and wearable devices.4,5
Metal oxides (MOXs), such as ZnO,6–8 NiO,9–11 Fe2O3,12–14 and In2O3 (ref. 15–17) have been widely used for detection of hazardous gases over the past few decades. For example, alpha-iron oxide (α-Fe2O3) is a commonly used sensing material for detection of acetone,18 H2S19 and NO2 (ref. 14) because of its low cost and simple production.20 However, gas sensors based on MOXs normally require high operating temperatures due to their poor conductivity and moderate surface activity at room temperature (RT), making it difficult to fabricate RT gas sensors with simple configurations towards flexible devices.
Hybridization of MOXs with conductive materials such as graphene derivatives21,22 and carbon nanotubes23,24 can improve their gas sensing performances. For instance, reduced graphene oxide (rGO), which possesses excellent electrical conductivity, large specific surface area, and good surface activity, has been wildly utilized to composite with MOXs for gas sensing.25–27 Examples of MOX/rGO-based sensing materials include ZnO/rGO,28 Fe2O3/rGO,29 and CuO/rGO30 for enhanced H2S, NO2, and acetone detection, respectively. Introducing noble metal nanostructures in sensing materials is another strategy to improve the gas sensing performance of MOX-based gas sensors. This is because, in addition to their good conductivity, noble metal nanomaterials can provide lower energy required for adsorption of gas molecules based on both experimental and theoretical investigations.31 For example, noble metals such as platinum (Pt),32 gold (Au),33 silver (Ag)34 and palladium (Pd)35 have been used to improve the gas sensing response of MOX-based sensors. Besides, previous reports have suggested that the type of surface ligands can influence the surface activity of noble metal nanostructures.2,36 However, few studies have investigated the ligand effects of metal nanomaterials in gas sensing.
In this work, a composite material, i.e. Au ND–ODT/α-Fe2O3/rGO, containing ultra-small Au nanodots (NDs) functionalized with 1-octadecanethiol (ODT), α-Fe2O3 and rGO was prepared and applied in NO2 gas sensing at RT, showing enhanced performance as compared with α-Fe2O3/rGO-based sensor. The improved sensing performance was attributed to the Au NDs, which facilitated the adsorption of NO2 gas and formed the ohmic-like contact with rGO and α-Fe2O3. The surface ligands of Au NDs were also found to influence the sensing performance. Flexible gas sensors based on Au ND–ODT/α-Fe2O3/rGO exhibited well-maintained responses under bent conditions due to the good mechanical strength, flexibility and film-forming ability of rGO.
2. Materials and methods
2.1. Materials
Graphene oxide (GO) aqueous solution (0.5 g L−1) was commercially purchased from Shanghai Carbon Source Huigu New Material Technology Co., Ltd, China. FeCl3·6H2O was purchased from Shanghai Adamas Reagents Co., Ltd, China. HAuCl4·H2O was purchased from Beijing Huawei Ruike Chemical Co., Ltd, China. 1-Octadecanethiol (ODT) and 16-mercaptohexadecanoic acid (MHA) were purchased from Shanghai Aladdin Biochemical Technology Co., Ltd, China. Ethanol (99.7%) was purchased from Sinopharm Chemical Reagent Co., Ltd, China. Printable Ag ink was purchased from Shanghai Mifang Electronic Technology Co., Ltd, China. All chemicals were used without further purification.
2.2. Preparation of α-Fe2O3/rGO hybrids
Typically, 0.25 mmol FeCl3·6H2O was mixed with 40 mL GO aqueous solution (0.5 g L−1) under stirring for 10 min. This mixture was further ultra-sonicated for 20 min before being added into a 50 mL Teflon-lined stainless-steel autoclave and then heated at 160 °C for 18 h. After being naturally cooled to room temperature (RT), the solution was centrifuged and washed with deionized water for 3 times and re-dispersed in 10 mL ethanol for further use.
2.3. Preparation of Au/α-Fe2O3/rGO hybrids
To decorate Au nanodots (NDs) on α-Fe2O3/rGO, 2 mL of the above-mentioned α-Fe2O3/rGO dispersion, 1 mL HAuCl4·ethanol solution (1 mg mL−1), 2 mL ODT (or MHA) ethanolic solution (1 mg mL−1) and 8 mL ethanol were mixed in a 20 mL glass bottle, which was irradiated with a 150 W xenon lamp for 2 min. The solution was then centrifuged at 7000 rpm and washed twice with ethanol. Depending on the ligand used, the products were named as Au ND–ODT/α-Fe2O3/rGO hybrids or Au ND–MHA/α-Fe2O3/rGO hybrids.
2.4. Materials characterization
Transmission electron microscopy (TEM, JEOL, 2100Plus and 2100F, Japan) was used to investigate the morphologies and microstructures of the samples. X-ray diffraction (XRD, Rigaku, XtaLAB mini II, Japan) was performed with Cu Kα radiation (λ = 1.54 Å). An X-ray photoelectron spectrometer (XPS, VersaProbe, PHI 5000, Japan) was utilized to analyze the oxidation state of the GO, and all the binding energies were calibrated to the C 1s band at 284.6 eV. An ultraviolet photoelectron spectrometer (UPS, VersaProbe, PHI 5000, Japan) coupled with an ultraviolet and visible spectrophotometer (UV, Shimadzu, UV-1780, Japan) was used to measure the electronic work functions and band levels of different materials.
2.5. Fabrication of flexible gas sensors and gas sensing tests
By employing a microelectronic printer (Shanghai Mifang Electronic Technology Co., Ltd, Scientific 3, China) with commercial Ag ink, arrays of interdigitated Ag electrodes were printed on polyethylene terephthalate (PET) substrates. To fabricate the flexible gas sensors, 20 μL of the sensing material solution was spin-coated on the as-prepared interdigitated Ag electrodes and then dried at RT for 2–3 h.
The gas sensing tests were conducted at RT in a sealed chamber. Constant currents were applied to the sensor electrodes and the variation of resistance was recorded using a data acquisition system (34972A, Agilent). The response of the sensor was defined as ΔR/R0 (%) (ΔR = Rg − R0, in which R0 and Rg are the resistances of the sample in simulated air environment (20.9% O2, 79.1% N2, and 19% RH) and the target gas, respectively). The sensor response and recovery times refer to the times when the sensor reaches 90% of the total resistance change during the response and recovery process, respectively.
3. Results and discussion
The preparation process of Au nanodot (ND)–1-octadecanethiol (ODT)/α-Fe2O3/reduced graphene oxide (rGO) hybrid is schematically illustrated in Fig. 1a. Typically, α-Fe2O3 nanoparticles (NPs) with a size of 30–40 nm were first deposited on GO nanosheets via a hydrothermal reaction, during which GO was also reduced to rGO because of the reducibility of H2O under high temperature and pressure29,37 (see Fig. S1 and S2 in the ESI†). After that, by using ODT as a surface ligand, Au NDs were decorated on the as-prepared composite through a photochemical reaction.38 As shown in Fig. 1b and S3a (see in the ESI†), Au NDs with an average size of ∼1.7 nm were well dispersed on the surface of α-Fe2O3/rGO. The ultra-small size of the Au NDs was achieved due to the strong binding of the ODT molecules to Au surfaces, which prevented the Au nanoparticles from growing large. Energy dispersive X-ray (EDX) mapping of a typical composite reveals the distribution of Au, Fe and C elements (Fig. 1c). The structure properties of Au ND–ODT/α-Fe2O3/rGO were investigated with X-ray diffraction (XRD), high resolution transmission electron microscope (HRTEM) analysis and selected area electron diffraction (SAED). The XRD pattern of the composite (see Fig. S3b in the ESI†) is similar to that of α-Fe2O3/rGO without showing the characteristic peaks for Au, which is due to the ultra-small size of the Au NDs based on Scherrer's theory.39,40 As shown in the HRTEM image in Fig. 1d, lattice spacings of 0.17 and 0.23 nm can be observed, which can be assigned to the (116) planes of α-Fe2O3 and (111) planes of Au, respectively. Besides, the SAED pattern of the product also reveals rings for rGO and α-Fe2O3 (Fig. 1e).
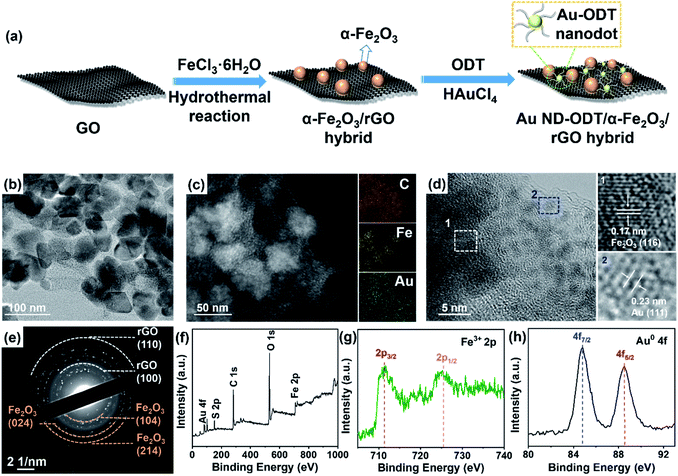 |
| Fig. 1 (a) Schematic illustration of the preparation of Au ND–ODT/α-Fe2O3/rGO hybrids. (b) TEM image, (c) STEM image and EDX mapping, (d) HRTEM image, (e) SAED pattern, (f) XPS full scan spectrum, (g) high-resolution Fe 2p spectrum and (h) Au 4f spectrum of the Au ND–ODT/α-Fe2O3/rGO composite. | |
The oxidation states of the as-prepared Au ND–ODT/α-Fe2O3/rGO were investigated by X-ray photoelectron spectroscopy (XPS). The survey spectrum of the sample shows the presence of Au, Fe and C elements (Fig. 1f). The high-resolution Fe 2p spectrum shows a doublet at 711.7 and 725.6 eV, corresponding to the 2p3/2 and 2p1/2 bands of Fe3+, respectively (Fig. 1g).41 Besides, in the Au 4f spectrum, two peaks at binding energies of 84.8 and 88.5 eV can be assigned to the Au 4f7/2 and 4f5/2 bands of Au0, respectively (Fig. 1h), indicating the successful photochemical reduction of Au3+.42
The as-prepared composites, namely, α-Fe2O3/rGO and Au ND–ODT/α-Fe2O3/rGO were spin-coated onto interdigitated Ag electrodes which were inkjet-printed on flexible polyethylene terephthalate (PET) substrates (Fig. 2a) to prepare flexible gas sensors. The response–recovery curves of these gas sensors toward NO2 were studied at RT in simulated air (20.9% O2, 79.1% N2, and 19% RH) with target gas concentrations increasing from 200 to 1000 ppb (Fig. 2b). All of the sensors showed decreased resistance upon NO2 exposure, and the reduction in resistance (ΔR) increased with increasing NO2 concentrations (Fig. 2b). The α-Fe2O3/rGO and Au ND–ODT/α-Fe2O3/rGO sensors both exhibited fast response times (e.g., about tens of seconds to 800 ppb NO2) but slow recovery times (e.g., more than 20 minutes to 800 ppb NO2) (see Fig. S4 in the ESI†). This points to the strong interaction between the NO2 molecules and the sensing material, leading to a slow desorption process.43–45 In our sensing materials, the rGO nanosheets and α-Fe2O3 showed p-type and n-type semiconducting properties, respectively, based on their ultraviolet photoelectron spectroscopy (UPS) and ultraviolet-visible (UV-vis) spectroscopy analysis results (see Fig. S5 and S6 in the ESI†). Generally, NO2, as an oxidizing gas, could extract electrons from sensing materials. This increased the concentration of holes in the p-type rGO, which was the main conducting matrix in the hybrid sensing material. The n-type α-Fe2O3 also lost electrons to NO2, and because of its lower Fermi level than that of rGO (Fig. 3), its electron vacancies were compensated by extracting electrons from rGO. This further increased the hole concentration in rGO, thus decreasing the resistance of the sensing film.46 Moreover, with the work functions, bandgaps and band level positions determined with UPS and UV-vis spectrometers (see Fig. S5 and S6 in the ESI†), we also studied the band alignment in the composite material as shown in Fig. 3. It can be seen that a p–n junction might form between rGO and α-Fe2O3, resulting in a charge neutral interface (the depletion layer). The adsorption of NO2 molecules could narrow the width of the depletion layer and facilitate the charge transfer at the heterojunction, thus resulting in further decreased resistance of the sensing film.47–50
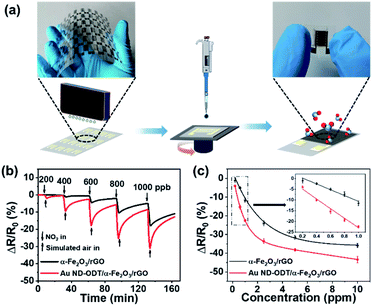 |
| Fig. 2 (a) Schematic illustration of the preparation of the flexible NO2 sensor, with photographs of the printed Ag electrode array and flexible gas sensor coated with Au ND–ODT/α-Fe2O3/rGO. (b) Dynamic response–recovery curves of α-Fe2O3/rGO and Au ND–ODT/α-Fe2O3/rGO in response to NO2 gas with different concentrations at RT. (c) Responses of α-Fe2O3/rGO and Au ND–ODT/α-Fe2O3/rGO sensors for NO2 with different concentrations. | |
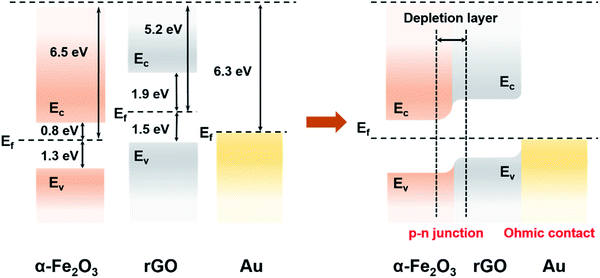 |
| Fig. 3 Schematic of the band level diagram of the Au ND–ODT/α-Fe2O3/rGO composite. | |
The Au ND–ODT/α-Fe2O3/rGO-based sensor showed an enhanced sensing performance as compared with the α-Fe2O3/rGO sensor, for example, with at least three times higher response at 200 ppb (Fig. 2c). Such an improvement might be attributed, in part, to the increased gas adsorption sites on the ultra-small Au NDs. Besides, due to the lower work function of Au NDs as compared to that of rGO, an ohmic contact might be established between them (Fig. 3), which favoured the charge transfer from rGO to Au NDs and finally to the NO2 molecules, thus improving the sensitivity of the hybrid sensing material.51,52 Moreover, ohmic like contact might also form between α-Fe2O3 and Au NDs (see Fig. S7 in the ESI†), which enabled facile electron transfer across the Au/α-Fe2O3 interface, leading to the formation of additional electron vacancies in α-Fe2O3 and thus an enhanced sensitivity. In addition, our Au ND–ODT/α-Fe2O3/rGO-based sensor exhibits performance comparable to that of many previously reported RT NO2 gas sensors (see Table S1 in the ESI†)53–61 and outperforms the recently reported rGO nanofiber,54 Au–CuO59 and MoS2 (ref. 60) based sensors.
Since ODT molecules were used as the capping agent to prepare the ultra-small Au NDs, we also investigated the effect of surface ligands on the gas sensing performance by using another type of thiol, i.e. 16-mercaptohexadecanoic acid (MHA), to prepare Au NDs (see Fig. S8 and S9 in the ESI†), and the resulting material was denoted as Au ND–MHA/α-Fe2O3/rGO. Our results showed that the Au ND–ODT/α-Fe2O3/rGO-based sensor outperformed the Au ND–MHA/α-Fe2O3/rGO sensor (see Fig. S10 in the ESI†). This was mainly attributed to the different terminal groups of the two types of thiols (i.e. carboxylic acid groups in MHA and methyl groups in ODT), considering their similar alkane chain lengths. Compared to the less polar methyl groups of ODT molecules, the polar carboxylic acid groups of MHA possess higher electron withdrawing ability which could extract electrons from Au NDs,62 and hinder the charge transfer in the sensing film (Fig. 4). This was proved by the lower baseline resistance of the Au ND–ODT/α-Fe2O3/rGO sensor compared to that of the Au ND–MHA/α-Fe2O3/rGO sensor (see Fig. S10 in the ESI†).
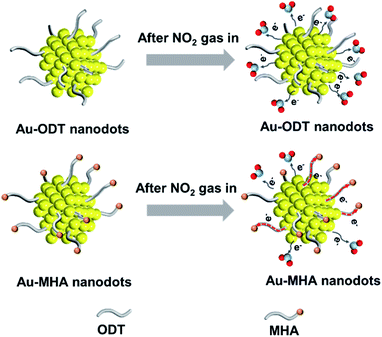 |
| Fig. 4 Schematic illustration of the effect of surface ligands of Au NDs on gas sensing. | |
The selectivity of Au ND–ODT/α-Fe2O3/rGO-based sensors was studied by comparing their responses to NO2 with other gases including NH3, SO2, acetone, formaldehyde and methylbenzene. The responses to the other gases were at least 8 times lower than that to NO2, indicating the good selectivity of the hybrid sensing material (Fig. 5a). Lastly, we demonstrated that our sensors on flexible substrates can work under bent conditions. As shown in Fig. 5b, a typical gas sensor showed similar sensing responses under the flat and bent conditions at bending angles of 15° and 30°, and negligible performance change even after the device was bent 300 times (see Fig. S11 in the ESI†). This can be due to the good mechanical strength, flexibility and film-forming ability of rGO sheets, which could help to avoid the loss of contact points under moderately bent conditions. However, at larger bending angles, e.g. 45° and 60°, the loss of contact points in the sensing film might occur, causing performance deterioration (see Fig. S12 in the ESI†).
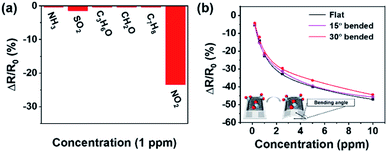 |
| Fig. 5 (a) Responses of the Au ND–ODT/α-Fe2O3/rGO sensor to 1 ppm of NH3, SO2, C3H6O, CH2O, C7H8 and NO2. (b) Comparison of the responses of a typical Au ND–ODT/α-Fe2O3/rGO sensor to NO2 under flat and different bent conditions. | |
4. Conclusion
In summary, the Au ND–ODT/α-Fe2O3/rGO composite was successfully prepared, which was utilized for NO2 sensing. The sensor could detect NO2 with concentrations down to 200 ppb at RT in simulated air, and showed improved sensing performance as compared with α-Fe2O3/rGO because of the advantageous effects of Au NDs. Besides, the surface ligands on Au NDs also influenced the sensing performance, that is, less polar terminal groups of the ligands favored charge transfer in the sensing film. Flexible gas sensors based on Au ND–ODT/α-Fe2O3/rGO exhibited well-maintained sensing responses under moderately bent conditions, indicating their potential applications in portable and wearable electronic devices.
Conflicts of interest
The authors declare no competing interests.
Acknowledgements
This work was supported by the National Natural Science Foundation of China (grant no.: 51832001), the Fundamental Research Funds for the Central Universities of China, the Young 1000 Talents Global Recruitment Program of China, the Joint Research Funds of Department of Science & Technology of Shaanxi Province and Northwestern Polytechnical University (grant no.: 2020GXLH-Z-026 and 2020GXLH-Z-027), and the China Postdoctoral Science Foundation (grant no.: 2021M692618).
References
- W. Huang, X. Zhuang, F. S. Melkonyan, B. Wang, L. Zeng, G. Wang, S. Han, M. J. Bedzyk, J. Yu, T. J. Marks and A. Facchetti, Adv. Mater., 2017, 29, 1701706 CrossRef PubMed.
- Q. Sun, J. Wang, X. Wang, J. Dai, X. Wang, H. Fan, Z. Wang, H. Li, X. Huang and W. Huang, Nanoscale, 2020, 12, 16987–16994 RSC.
- H. Wang, W. P. Lustig and J. Li, Chem. Soc. Rev., 2018, 47, 4729–4756 RSC.
- J. Dai, O. Ogbeide, N. Macadam, Q. Sun, W. Yu, Y. Li, B. L. Su, T. Hasan, X. Huang and W. Huang, Chem. Soc. Rev., 2020, 49, 1756–1789 RSC.
- S. Ota, A. Ando and D. Chiba, Nat. Electron., 2018, 1, 124–129 CrossRef.
- H. Kim, Y. Pak, Y. Jeong, W. Kim, J. Kim and G. Y. Jung, Sens. Actuators, B, 2018, 262, 460–468 CrossRef CAS.
- G. Namgung, Q. T. H. Ta, W. Yang and J. S. Noh, ACS Appl. Mater. Interfaces, 2019, 11, 1411–1419 CrossRef CAS PubMed.
- H. Yuan, S. Aljneibi, J. Yuan, Y. Wang, H. Liu, J. Fang, C. Tang, X. Yan, H. Cai, Y. Gu, S. J. Pennycook, J. Tao and D. Zhao, Adv. Mater., 2019, 31, e1807161 CrossRef PubMed.
- P. Li, C. Cao, Q. Shen, B. Bai, H. Jin, J. Yu, W. Chen and W. Song, Sens. Actuators, B, 2021, 339, 129886 CrossRef CAS.
- S. Y. Yi, Y. G. Song, J. Y. Park, J. M. Suh, G. S. Kim, Y. S. Shim, J. M. Yuk, S. Kim, H. W. Jang, B. K. Ju and C. Y. Kang, ACS Appl. Mater. Interfaces, 2019, 11, 7529–7538 CrossRef CAS PubMed.
- L. Sui, T. Yu, D. Zhao, X. Cheng, X. Zhang, P. Wang, Y. Xu, S. Gao, H. Zhao, Y. Gao and L. Huo, J. Hazard. Mater., 2020, 385, 121570 CrossRef CAS PubMed.
- H. Fu, Q. Wang, J. Ding, Y. Zhu, M. Zhang, C. Yang and S. Wang, Sens. Actuators, B, 2020, 303, 127186 CrossRef CAS.
- R. Ahmad, M. S. Ahn and Y. B. Hahn, Adv. Mater. Interfaces, 2017, 4, 1700691 CrossRef.
- C. Hua, Y. Shang, Y. Wang, J. Xu, Y. Zhang, X. Li and A. Cao, Appl. Surf. Sci., 2017, 405, 405–411 CrossRef CAS.
- Z. Wang, C. Hou, Q. De, F. Gu and D. Han, ACS Sens., 2018, 3, 468–475 CrossRef CAS PubMed.
- L. Jun, Q. Chen, W. Fu, Y. Yang, W. Zhu and J. Zhang, ACS Appl. Mater. Interfaces, 2020, 12, 38425–38434 CrossRef PubMed.
- X. Liu, K. Zhao, X. Sun, C. Zhang, X. Duan, P. Hou, G. Zhao, S. Zhang, H. Yang, R. Cao and X. Xu, Sens. Actuators, B, 2019, 285, 1–10 CrossRef CAS.
- S. Zhang, M. Yang, K. Liang, A. Turak, B. Zhang, D. Meng, C. Wang, F. Qu, W. Cheng and M. Yang, Sens. Actuators, B, 2019, 290, 59–67 CrossRef CAS.
- Y. Guo, X. Tian, X. Wang and J. Sun, Sens. Actuators, B, 2019, 293, 136–143 CrossRef CAS.
- B. Zhang, J. Liu, X. Cui, Y. Wang, Y. Gao, P. Sun, F. Liu, K. Shimanoe, N. Yamazoe and G. Lu, Sens. Actuators, B, 2017, 241, 904–914 CrossRef CAS.
- G. Bae, I. S. Jeon, M. Jang, W. Song, S. Myung, J. Lim, S. S. Lee, H. K. Jung, C. Y. Park and K. S. An, ACS Appl. Mater. Interfaces, 2019, 11, 16830–16837 CrossRef CAS PubMed.
- S. S. Niavol, M. Budde, A. Papadogianni, M. Heilmann, H. M. Moghaddam, C. M. Aldao, G. Ligorio, E. J. W. List Kratochvil, J. M. J. Lopes, N. Barsan, O. Bierwagen and F. Schipani, Sens. Actuators, B, 2020, 325, 128797 CrossRef CAS.
- M. Sinha, S. Neogi, R. Mahapatra, S. Krishnamurthy and R. Ghosh, Sens. Actuators, B, 2021, 336, 129729 CrossRef CAS.
- V. S. Bhati, M. Kumar and R. Banerjee, J. Mater. Chem. C, 2021, 9, 8776–8808 RSC.
- O. C. Compton and S. T. Nguyen, Small, 2010, 6, 711–723 CrossRef CAS PubMed.
- C. Chang, W. Chen, Y. Chen, Y. Chen, Y. Chen, F. Ding, C. Fan, H. Jin Fan, Z. Fan, C. Gong, Y. Gong, Q. He, X. Hong, S. Hu, W. Hu, W. Huang, Y. Huang, W. Ji, D. Li, L.-J. Li, Q. Li, L. Lin, C. Ling, M. Liu, N. Liu, Z. Liu, K. Ping Loh, J. Ma, F. Miao, H. Peng, M. Shao, L. Song, S. Su, S. Sun, C. Tan, Z. Tang, D. Wang, H. Wang, J. Wang, X. Wang, X. Wang, A. T. S. Wee, Z. Wei, Y. Wu, Z.-S. Wu, J. Xiong, Q. Xiong, W. Xu, P. Yin, H. Zeng, Z. Zeng, T. Zhai, H. Zhang, H. Zhang, Q. Zhang, T. Zhang, X. Zhang, L.-D. Zhao, M. Zhao, W. Zhao, Y. Zhao, K.-G. Zhou, X. Zhou, Y. Zhou, H. Zhu, H. Zhang and Z. Liu, Acta Phys.-Chim. Sin., 2021, 37, 2108017 Search PubMed.
- K. Yang, X. Wang, H. Li, B. Chen, X. Zhang, S. Li, N. Wang, H. Zhang, X. Huang and W. Huang, Nanoscale, 2017, 9, 5102–5109 RSC.
- T. K. Dang, N. T. Son, N. T. Lanh, P. H. Phuoc, N. N. Viet, L. V. Thong, C. M. Hung, N. V. Duy, N. D. Hoa and N. V. Hieu, J. Alloys Compd., 2021, 879, 160457 CrossRef CAS.
- H. Zhang, L. Yu, Q. Li, Y. Du and S. Ruan, Sens. Actuators, B, 2017, 241, 109–115 CrossRef CAS.
- M. Liu, Z. Wang, P. Song, Z. Yang and Q. Wang, Sens. Actuators, B, 2021, 340, 129946 CrossRef CAS.
- V. Montes Garcia, M. A. Squillaci, M. Diez Castellnou, Q. K. Ong, F. Stellacci and P. Samori, Chem. Soc. Rev., 2021, 50, 1269–1304 RSC.
- R. Jolly Bose, N. Illyasukutty, K. S. Tan, R. S. Rawat, M. Vadakke Matham, H. Kohler and V. P. Mahadevan Pillai, Appl. Surf. Sci., 2018, 440, 320–330 CrossRef CAS.
- J. Ma, X. Xiao, Y. Zou, Y. Ren, X. Zhou, X. Yang, X. Cheng and Y. Deng, Small, 2019, 15, e1904240 CrossRef PubMed.
- Q. A. Drmosh, Y. A. Al Wajih, I. O. Alade, A. K. Mohamedkhair, M. Qamar, A. S. Hakeem and Z. H. Yamani, Sens. Actuators, B, 2021, 338, 129851 CrossRef CAS.
- Y. Wang, X. Meng, M. Yao, G. Sun and Z. Zhang, Ceram. Int., 2019, 45, 13150–13157 CrossRef CAS.
- J. S. Kim, H. W. Yoo, H. O. Choi and H. T. Jung, Nano Lett., 2014, 14, 5941–5947 CrossRef CAS PubMed.
- Y. Zhou, Q. Bao, L. A. L. Tang, Y. Zhong and K. P. Loh, Chem. Mater., 2009, 21, 2950–2956 CrossRef CAS.
- X. Huang, X. Zhou, S. Wu, Y. Wei, X. Qi, J. Zhang, F. Boey and H. Zhang, Small, 2010, 6, 513–516 CrossRef CAS PubMed.
- K. O'Connell and J. R. Regalbuto, Catal. Lett., 2015, 145, 777–783 CrossRef.
- A. Weibel, R. Bouchet, F. Boulc and P. Knauth, Chem. Mater., 2005, 17, 2378–2385 CrossRef CAS.
- F. Qu, X. Zhou, B. Zhang, S. Zhang, C. Jiang, S. Ruan and M. Yang, J. Alloys Compd., 2019, 782, 672–678 CrossRef CAS.
- P. Li, H. Zhan, S. Tian, J. Wang, X. Wang, Z. Zhu, J. Dai, Y. Dai, Z. Wang, C. Zhang, X. Huang and W. Huang, ACS Appl. Mater. Interfaces, 2019, 11, 13624–13631 CrossRef CAS PubMed.
- H. Y. Lee, Y. C. Heish and C. T. Lee, J. Alloys Compd., 2019, 773, 950–954 CrossRef CAS.
- J. Hu, C. Zou, Y. Su, M. Li, X. Ye, B. Cai, E. S. W. Kong, Z. Yang and Y. Zhang, Sens. Actuators, B, 2018, 270, 119–129 CrossRef CAS.
- B. I. Adamu, A. Falak, Y. Tian, X. Tan, X. Meng, P. Chen, H. Wang and W. Chu, ACS Appl. Mater. Interfaces, 2020, 12, 8411–8421 CrossRef CAS PubMed.
- B. Zhang, G. Liu, M. Cheng, Y. Gao, L. Zhao, S. Li, F. Liu, X. Yan, T. Zhang, P. Sun and G. Lu, Sens. Actuators, B, 2018, 261, 252–263 CrossRef CAS.
- S. Zhao, Y. Shen, F. Hao, C. Kang, B. Cui, D. Wei and F. Meng, Appl. Surf. Sci., 2021, 538, 148140 CrossRef CAS.
- M. Shafiei, J. Bradford, H. Khan, C. Piloto, W. Wlodarski, Y. Li and N. Motta, Appl. Surf. Sci., 2018, 462, 330–336 CrossRef CAS.
- X. Jiang, H. Tai, Z. Ye, Z. Yuan, C. Liu, Y. Su and Y. Jiang, Mater. Lett., 2017, 186, 49–52 CrossRef CAS.
- X. Wang, Y. Liu, J. Dai, Q. Chen, X. Huang and W. Huang, Chem.–Eur. J., 2020, 26, 3870–3876 CrossRef CAS PubMed.
- X. Wang, Z. Wang, J. Zhang, X. Wang, Z. Zhang, J. Wang, Z. Zhu, Z. Li, Y. Liu, X. Hu, J. Qiu, G. Hu, B. Chen, N. Wang, Q. He, J. Chen, J. Yan, W. Zhang, T. Hasan, S. Li, H. Li, H. Zhang, Q. Wang, X. Huang and W. Huang, Nat. Commun., 2018, 9, 3611 CrossRef PubMed.
- J. Bao, S. Zeng, J. Dai, X. Wang, Q. Liu, H. Li, X. Huang and W. Huang, Chem. Commun., 2021, 57, 5590–5593 RSC.
- H. J. Park, W. J. Kim, H. K. Lee, D. S. Lee, J. H. Shin, Y. Jun and Y. J. Yun, Sens. Actuators, B, 2018, 257, 846–852 CrossRef CAS.
- J. Zha, Z. Yuan, Z. Zhou, Y. Li, J. Zhao, Z. Zeng, L. Zhen, H. Tai, C. Tan and H. Zhang, Small Struct., 2021, 2, 2100067 CrossRef.
- Jyoti and G. D. Varma, J. Alloys Compd., 2019, 806, 1469–1480 CrossRef CAS.
- S. Li, Z. Wang, X. Wang, F. Sun, K. Gao, N. Hao, Z. Zhang, Z. Ma, H. Li, X. Huang and W. Huang, Nano Res., 2017, 10, 1710–1719 CrossRef CAS.
- M. Reddeppa, N. T. KimPhung, G. Murali, K. S. Pasupuleti, B. G. Park, I. In and M. D. Kim, Sens. Actuators, B, 2021, 329, 129175 CrossRef CAS.
- M. S. Choi, H. G. Na, J. H. Bang, A. Mirzaei, S. Han, H. Y. Lee, S. S. Kim, H. W. Kim and C. Jin, Sens. Actuators, B, 2021, 326, 128801 CrossRef CAS.
- X. Chen, S. Zhao, P. Zhou, B. Cui, W. Liu, D. Wei and Y. Shen, Sens. Actuators, B, 2021, 328, 129070 CrossRef CAS.
- R. Kumar, N. Goel and M. Kumar, ACS Sens., 2017, 2, 1744–1752 CrossRef CAS PubMed.
- B. Liu, X. Liu, Z. Yuan, Y. Jiang, Y. Su, J. Ma and H. Tai, Sens. Actuators, B, 2019, 295, 86–92 CrossRef CAS.
- N. D. K. Tu, J. Choi, C. R. Park and H. Kim, Chem. Mater., 2015, 27, 7362–7369 CrossRef.
Footnote |
† Electronic supplementary information (ESI) available: Fig. S1–S12. See DOI: 10.1039/d1na00734c |
|
This journal is © The Royal Society of Chemistry 2022 |
Click here to see how this site uses Cookies. View our privacy policy here.