DOI:
10.1039/C6RA11541A
(Paper)
RSC Adv., 2016,
6, 74493-74499
Effect of oxygen plasma immersion ion implantation on the formation of nanostructures over Ni–Ti alloy
Received
4th May 2016
, Accepted 29th July 2016
First published on 29th July 2016
Abstract
Ni–Ti alloy has been implanted with oxygen ions by plasma immersion ion implantation (PIII-O). Ni–Ti–O nanotubes are formed by anodic oxidation of PIII-O Ni–Ti alloy. The surface of the modified alloy samples has been characterized by X-ray diffraction (XRD), field emission scanning electron microscopy (FESEM), energy dispersive spectroscopy (EDS) and X-ray photoelectron spectroscopy (XPS). The corrosion behaviors of the Ni–Ti substrate, PIII-O and anodized PIII-O samples have been investigated through electrochemical impedance spectroscopy (EIS) and potentiodynamic polarization studies in simulated body fluid (Hanks' solution). It has been observed that oxygen ion implantation leads to the formation of a thin oxide layer on the Ni–Ti alloy. Anodization of the implanted alloy results in Ni–Ti–O nanotubes. Corrosion resistance of the PIII-O and anodized PIII-O samples shows better corrosion resistance compared to that of untreated alloy.
1. Introduction
Nickel–titanium (Ni–Ti) alloy has been used in aerospace, biomedical and automotive industries because of its unique properties such as super elasticity and shape memory effect. Ni–Ti alloy is an important material for biomedical devices due to its specific properties, especially good biocompatibility and high corrosion resistance. Ni–Ti alloy has shown a wide range of biomedical applications including cardiovascular, dental arch wires for orthodontics and orthopedic implants.1–5 However, Ni–Ti alloy releases harmful Ni ions from the implants into living tissues that can be toxic and allergic to the cell, tissue and organs when its concentration exceeds a certain level.1,6,7 Therefore, it is essential to have a barrier layer to impede the diffusion of Ni ions from implants. In order to decrease Ni ion release, various surface modification techniques have been reported including physical and chemical or electrochemical processes,8,9 heat-treatment,9 sol–gel deposition,10 ion implantation11 and plasma immersion ion implantation.12–16 Corrosion resistance and biocompatibility of Ni–Ti alloy can be dependent on the native oxide layer on its surface. However, the oxide layer is very thin (<10 nm) and cannot be re-passivated once oxide layer is damaged.17
Recently, TiO2 nanotubes (NTs) which can be fabricated by electrochemical anodization have attracted much attention in biomedical fields.18–21 Zhang and coworkers have reported growth of TiO2 nanotubes on both sides of Ti foil and nonplanar Ti electrodes by anodization.22–24 Unlike the anodization of other Ti alloys, anodization of Ni–Ti alloys in traditional electrolytes usually cannot yield nanotubes arrays as precise structure control of Ni–Ti–O NTs is quite difficult due to large Ni content.25–27 To date, few works have been reported on anodic fabrication of Ni–Ti–O nanotubes arrays on Ni–Ti alloy.26,28–30 Hang and coworkers have fabricated Ni2O3 doped TiO2 nanotubes on Ni–Ti alloy by electrochemical anodization and studied their corrosion, bioactivity and wettability.25 Authors have also demonstrated that the diameter and length of Ni–Ti–O nanotubes can be tailored in a controlled manner by varying different parameters such as anodization voltage, temperature and NH4F concentration.29 However, in all cases, Ni–Ti alloy has been used as flat substrate. In addition, studies on anodization of oxygen plasma immersion ion implantation treated Ni–Ti alloy at low temperature lacks in the literature. In this work, we report self organized Ni–Ti–O nanotubes fabricated on Ni–Ti alloy through oxygen plasma immersion ion implantation (PIII-O) followed by electrochemical anodization. The nanotubes are characterized for their nanoscale features, corrosion behavior by electrochemical impedance spectroscopy (EIS) and potentiodynamic polarization in simulated body fluid (Hanks' solution).
2. Materials and methods
2.1. Preparation of the samples
Ni–Ti alloy in the form of wire (50 at% Ni) with a diameter of 0.88 mm was procured from Johnson Matthey Noble Metals. Samples of 5 cm length were ultrasonically cleaned with acetone and dried. Prior to anodization, Ni–Ti alloy was implanted with oxygen using plasma immersion ion implantation (PIII-O).
2.2. Plasma immersion ion implantation
Oxygen implantation of Ni–Ti alloy was carried out in a custom designed chamber made by stainless steel (SS304). The chamber was pumped to 2.4 × 10−6 mbar pressure by a diffusion pump backed by a rotary pump. Oxygen flow was controlled by mass flow controller (MKS) and implantation was carried out at 1.4 × 10−4 mbar pressure. Plasma was generated using inductive coupling of 50 W RF (13.56 MHz) power and the samples were biased with negative pulse bias voltage of 10 kV for 40 min. After implantation the samples were cooled down to room temperature under vacuum.
2.3. Fabrication of Ni–Ti–O nanotubes
After oxygen implantation (PIII-O) of Ni–Ti alloy, samples were electrochemically anodized using a two electrode electrochemical anodization cell with a platinum foil as cathode and Ni–Ti wire as anode to fabricate the nanotubes arrays (anodized PIII-O). The electrode separation distance was also kept constant at 2 cm. The electrolyte was ethylene glycol supplemented with 0.25 wt% of NH4F and 0.5 mL of H2O. Anodization was carried out at 20 V with a DC power supply for 15–30 min. The anodic current density was recorded throughout the experiments. The electrolyte volume was held constant at 100 mL and continuously stirred using a magnetic stirrer. The electrolyte temperature was maintained at 30 °C using temperature controller.
2.4. Electrochemical measurements
Electrochemical studies of the alloy, PIII-O and anodized PIII-O samples were conducted using CH 604D electrochemical workstation supplied by CH Instruments, USA. The conventional three electrode glass cell was used to carry out the electrochemical studies. The tests were conducted in 200 mL of Hanks' solution which is a simulated body fluid (SBF) at room temperature. The sample was kept as a working electrode; Pt foil and saturated calomel electrode (SCE) were used as counter and reference electrodes, respectively. The reference electrode was kept very close to the surface of the working electrode. The sample was immersed in Hanks' solution for 1 h in order to establish the open circuit potential (EOCP). EIS measurements were carried out in the frequency range of 10 mHz to 100 kHz. The applied alternating sinusoidal potential was 10 mV on the EOCP. After each experiment, the impedance data were displayed as Bode plots. The Bode plot is a plot of log|Z| vs. log
f and log
f vs. −phase angle (θ), where |Z| is the absolute impedance and f is the frequency. The acquired data were curve-fitted and analyzed using ZSimpwin program (Princeton Applied Research, USA) to get suitable equivalent circuit parameters. The quality of the fit was checked by the χ2 value. After EIS measurements, potentiodynamic polarization studies were carried out in a potential range of 200 mV below and above the OCP value with a scan rate of 1 mV s−1. The measured current–voltage data were plotted as Tafel plots in the form of log
i vs. potential plot. The corrosion current (icorr) and corrosion potential (Ecorr) were deduced from the Tafel plots. The corrosion current was obtained using the cathodic part of the polarization curve since the anodic part lacks necessary Tafel region.31
2.5. Characterization
The structure of surface modified Ni–Ti alloys was determined by XRD employing a PANalytical X'Pert PRO X-ray diffractometer operated with CuKα radiation of 1.5418 Å wavelength at 40 kV and 30 mA in the 2θ range 20–80°. The surface morphologies of surface modified Ni–Ti alloy samples were examined by Carl Zeiss Supra 40 VP FESEM equipped with Inca Penta Fetx3 (Oxford Instruments) EDS analyzer for elemental analysis. XPS were obtained in a SPECS spectrometer (SPECS Surface Nano Analysis GmbH, Germany) equipped with a twin anode X-ray source and a hemispherical analyzer having a single channel detector. The spectra were recorded with non-monochromatic AlKα radiation (1486.6 eV) operated at 150 W. The binding energies reported here were referenced with C1s peak at 284.6 eV. Core level spectra of Ni2p, Ti2p and O1s were obtained at a pass energy of 40 eV and curve-fitted with Gaussian–Lorentzian peaks to identify various species after a Shirley background subtraction using CasaXPS program.
3. Results and discussion
3.1. XRD studies
XRD patterns of the Ni–Ti alloy, PIII-O and anodized PIII-O samples are shown in Fig. 1. It can be seen from XRD patterns that untreated and treated Ni–Ti alloys show two prominent diffraction peaks between 20° and 80°. The prominent peaks at 42.3° (110) and 77.5° (211) belong to austenite Ni–Ti phase (B2).25,32 After oxygen implantation (PIII-O) and anodization a stable characteristic peak of rutile TiO2 phase at 27.8° is observed to appear which is clearly seen their diffraction patterns given in the inset of the figure.25 These results show formation of TiO2 layer on the Ni–Ti surface after oxygen plasma immersion ion implantation and anodization.
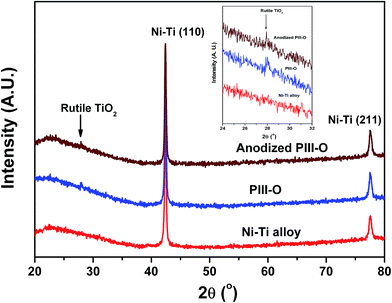 |
| Fig. 1 XRD patterns of Ni–Ti alloy, PIII-O and anodized PIII-O samples. | |
3.2. FESEM studies
Fig. 2(a–f) shows the FESEM images of the samples anodized for different time. It can be seen from the images that the anodization duration significantly affects the surface features of the nanotubes. In Fig. 2(a) sample anodized with 15 min shows “grass-bundle like” morphology with compact oxide layer on top that agrees well with the literature for TiO2 nanotubes.33 Fig. 2(b) shows irregular nanotubes formed with small diameter under compact oxide layer. When anodization time is increased to 20 min, evenly distributed planar nano tubular structure and “mud crack like” micro cracks are obtained on surfaces as presented in Fig. 2(c and d). Sample with 30 min anodization time (Fig. 2(e and f)) shows self organized Ni–Ti–O nanotube arrays formed with average tube length, tube diameter and wall thickness of ∼350, ∼65, and ∼18 nm, respectively. The chemical compositions of Ni–Ti alloy, PIII-O and anodized PIII-O samples obtained from EDS are given in Table 1. As can be seen from the table after PIII-O, increase in oxygen at% is seen which implies the formation of compact oxide on the Ni–Ti alloy due to oxygen implantation. After anodization, gradual increase in oxygen content with increase in anodization time confirms the formation of thick anodic oxide layer (nanostructured oxide layer). This is further substantiated by the results of XPS to be discussed below. Detailed XPS, EIS and corrosion studies have been carried out on Ni–Ti alloy, PIII-O and 30 min anodized PIII-O samples and are discussed in the following subsections.
 |
| Fig. 2 Surface morphologies of as-formed Ni–Ti–O nanotubes on Ni–Ti alloy with different anodization times: (a) and (b) 15 min (inset at higher magnification), (c) 20 min (inset at lower magnification) and (d) cross sectional view as formed nanotubes at 20 min, (e) 30 min and (f) cross sectional view as formed nanotubes at 30 min. | |
Table 1 Chemical compositions obtained from EDS of Ni–Ti alloy, PIII-O and anodized PIII-O samples
Elements |
Ni–Ti alloy (at%) |
PIII-O (at%) |
Anodized PIII-O (at%) |
15 min |
20 min |
30 min |
O |
— |
18.4 |
41.3 |
53.9 |
55.8 |
Ti |
51.3 |
44.3 |
34.2 |
33.4 |
27.0 |
Ni |
48.7 |
37.3 |
24.5 |
12.7 |
17.2 |
3.3. XPS studies
Fig. 3 shows Ni2p, Ti2p and O1s core level spectra of the Ni–Ti alloy, PIII-O and anodized PIII-O samples in the as-received condition. Ni2p3/2 core level spectra have been curve-fitted with Gaussian–Lorentzian components to identify the various components of Ni. Curve-fitting of Ni2p3/2 core level spectra results in three different nickel species (Ni0, NiO and Ni2O3) in alloy and PIII-O samples and four species (Ni0, NiO, Ni2O3 and Ni(OH)2) in anodized PIII-O sample. Table 2 lists the binding energies and relative concentrations of nickel species in different compounds. Ni2p3/2 peak found at 852.7 eV is attributed to Ni0 present in Ni–Ti alloy.25 According to the literature, Ni2p binding energies of Ni2O3 and Ni(OH)2 are close and values are reported in a wide range.25,34–37 Therefore, observed peak at 855.9 eV in the alloy corresponds to Ni2O3.25,34–36 Mainly oxidized Ni species (NiO and Ni2O3) are seen in PIII-O sample and amount of metallic Ni decreases as shown in the figure and table. Again, electrolyte for anodization contains water. Therefore, there is a possibility of formation of Ni(OH)2 in the sample after anodization. Moreover, Ni2p spectral envelope of anodized sample is broader than alloy and PIII-O samples. In this sense, a hump at 856.8 eV in anodized sample is related to Ni(OH)2.34–37 These results confirm that after implantation of oxygen into Ni–Ti substrate compact oxide layer has been formed. As can be seen from the figure and table, Ni2O3 and Ni(OH)2 species are mostly present in the anodized PIII-O sample. This can be due to the formation of Ni2O3 and Ni(OH)2 after anodization. An intense Ti2p3/2 peak at 458.8 eV in Ni–Ti alloy spectrum in Fig. 3 is associated with TiO2.31 A small hump at 454.2 eV in the spectrum indicates the presence of trace amount of metallic Ti. After oxygen implantation, the alloy surface is completely covered with TiO2 and the spectrum has no trace of metallic Ti peak. This shows the formation of compact oxide layer after the oxygen implantation process. After anodization of PIII-O sample, the surface is also covered by oxides (TiO2, NiO and Ni2O3) as can be seen from spectra in Fig. 3. O1s core level spectra from the alloy, PIII-O and anodized PIII-O samples presented in Fig. 3 are broad and are curve-fitted with three Gaussian–Lorentzian peaks corresponding to oxygen in metal oxide at 530.0 eV, oxygen bonded as in hydroxide (OH−) at 531.6 eV and oxygen in adsorbed water at 533.4 eV.38–40 The relative surface compositions of various elements in Ni–Ti alloy, PIII-O and anodized PIII-O samples are given in Table 3. The relative amounts of oxygen in metal oxide, OH− and H2O are also given in Table 3. In case of PIII-O and anodized PIII-O samples, oxygen is bonded mostly as metal oxide form. As can be seen from the table after oxygen implantation and anodization oxygen concentration has increased confirming the formation of oxide layers.
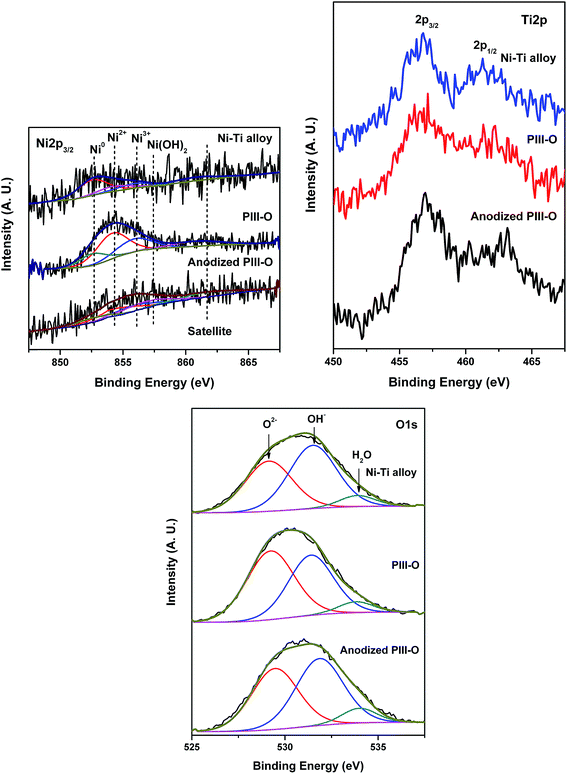 |
| Fig. 3 XPS of Ni2p, Ti2p and O1s core level spectra of Ni–Ti alloy, PIII-O and anodized PIII-O samples. | |
Table 2 Binding energies and relative peak areas of different Ni species in Ni–Ti alloy, PIII-O and anodized PIII-O samples as determined by XPS
Samples |
Ni species |
Binding energy of Ni2p3/2 (eV) |
Relative peak area (%) |
Ni–Ti alloy |
Ni0 |
852.7 |
61.5 |
NiO |
854.1 |
21.1 |
Ni2O3 |
855.9 |
17.4 |
PIII-O |
Ni0 |
852.6 |
19.4 |
NiO |
854.1 |
51.1 |
Ni2O3 |
855.9 |
29.5 |
Anodized PIII-O |
Ni0 |
852.6 |
15.7 |
NiO |
854.5 |
29.8 |
Ni2O3 |
855.9 |
22.9 |
Ni(OH)2 |
856.8 |
31.6 |
Table 3 Relative surface compositions of Ni, Ti and O in Ni–Ti alloy, PIII-O and anodized PIII-O samples evaluated from XPS studies
Samples |
Ni (at%) |
Ti (at%) |
O (at%) |
Oxygen bonded as |
O2− (%) |
OH− (%) |
H2O (%) |
Ni–Ti alloy |
10.3 |
13.8 |
75.9 |
41 |
51.6 |
7.4 |
PIII-O |
5.6 |
3.9 |
90.5 |
51.4 |
42.6 |
6.0 |
Anodized PIII-O |
3.3 |
2.4 |
94.3 |
52.2 |
39.6 |
8.2 |
3.4. Electrochemical studies
Potentiodynamic polarization curves of the Ni–Ti alloy, PIII-O and anodized PIII-O samples in freshly prepared Hanks' solution (simulated body fluid) are shown in Fig. 4. The corrosion current (icorr) has been obtained by extrapolation of the cathodic polarization curve to the corrosion potential. Table 4 shows the polarization resistance, corrosion potential and corrosion current density of the alloy and surface modified samples. The corrosion current density of the substrate is 0.0028 μA cm−2 and that of oxygen implanted sample is 0.0015 μA cm−2. Thus, oxygen implantation has marginal effect on the corrosion resistance. After anodization of PIII-O sample the corrosion resistance is closer to that of alloy. It can be observed from the Fig. 4 that the current is nearly constant in the passivation region and lower than the alloy by an order of magnitude which exemplifies that the stability of passive layer on oxygen implanted sample is better than that of alloy. In case of anodized sample, the corrosion current remains same as that of alloy. The Ecorr values for PIII-O and anodized PIII-O samples have shifted to nobler values (−0.278 and −0.193 V) compared to the alloy one (−0.325 V). These results indicate that the PIII-O and anodized PIII-O samples have better passivation characteristics in comparison with the alloy. As compared to the alloy, the surface area of anodized PIII-O sample is much higher owing to the nanotube morphology. The increased corrosion current can be due to the increased area because of this nanostructure of the Ni–Ti alloy. Therefore, the actual corrosion resistance can be very high.41
 |
| Fig. 4 Tafel plots: (a) Ni–Ti alloy, (b) PIII-O (c) anodized PIII-O samples. | |
Table 4 Potentiodynamic polarization data of Ni–Ti alloy, PIII-O and anodized PIII-O samples
Samples |
Ecorr (V) |
icorr (μA cm−2) |
Ni–Ti alloy |
−0.325 |
0.0028 |
PIII-O |
−0.278 |
0.0015 |
Anodized PIII-O |
−0.193 |
0.0028 |
In Fig. 5, results of electrochemical impedance test in Hanks' solution are shown in the form of Bode plots. In Fig. 5(a), the phase angle changes from −0° to −20° in the high frequency range (10 to 100 kHz) for alloy. In the case of alloy, in the frequency range from 0.01 Hz to 100 Hz, the phase angle remains nearly constant (−82°) which is less than ideal capacitor (−90°). In the same frequency range, a linear relationship between log|Z| and log
f is observed with a slope close to one. In the case of PIII-O sample (Fig. 5(b)), the phase angle in the same frequency range is also lower than −90° and decreases towards −75° in 0.01 to 0.1 Hz frequency range. Phase angle in the same frequency range is observed to be lower than −90° in the case of anodized PIII-O sample and decreases towards −65° in 0.01 to 10 Hz frequency range (Fig. 5(c)).
 |
| Fig. 5 Bode plots obtained in Hanks' solution for (a) Ni–Ti alloy, (b) PIII-O and (c) anodized PIII-O samples; |Z| measured; |Z| calculated; angle measured; angle calculated. | |
The equivalent circuit used for fitting the EIS data of the alloy, PIII-O and anodized PIII-O samples is shown in Fig. 6. Table 5 shows the values of the fitted parameters. The non-ideal capacitive response of the oxide films has been entailed by using a constant phase element (CPE) instead of a pure capacitance in the fitting procedure. This CPE can be due to difference in the relaxation times as a result of different degrees of surface in-homogeneity. The impedance with the capacitance can be defined as ZCPE = [Q(jωn)]−1,42 where Q, j, ω and n are the pseudo capacitance, imaginary function (√−1), angular frequency and the deviation from the ideal behavior of a pure capacitor, respectively. When n = 1, the system behaves like a pure capacitor and Q = C where C is capacitance. In Fig. 6, Rs corresponds to the resistance of the solution, R1 to the resistance of the outer porous layer, R2 to the resistance of the barrier layer, Q1 to the capacitance of the porous layer and Q2 to the capacitance of the barrier layer. The parameters, R1 and Q1 represent the properties of the porous film/solution interface i.e. the charge transfer resistance and double layer capacitance. According to the model used for fitting EIS data of the alloy, the resistance (R1) associated with the outer porous layer is significantly lower than the value of the resistance (R2) of inner barrier layer that is close to the alloy. This indicates that the protection provided by the passive layer is predominately due to the inner barrier layer. The fitting parameters for PIII-O sample in Table 5 show that the resistance (R1) of the outer layer is about 55 Ω cm2 and that of the inner barrier layer (R2) is about 4.6 × 107 Ω cm2. Q1 for the PIII-O sample is 4.3 × 10−7 S sn cm−2 and for Q2 of that is 1.6 × 10−6 S sn cm−2. The non ideal value for the constant phase element representing the outer layer is 0.91 for the alloy and 0.87 for the PIII-O sample. The non ideal value for the constant phase element representing the inner layer is 0.93 for the alloy sample and 0.92 in the case of PIII-O. These results show that implantation replaces the native oxide layer consisting outer porous layer structure by a denser oxide layer. This new oxide layer is responsible for the better passivation and electrochemical behavior of the implanted sample. The outer layer in the case of implanted sample is due to roughness induced by the implantation process during which both sputtering and implantation take place. According to the model used for fitting EIS data of the anodized PIII-O, the resistance (R1) associated with the porous layer is significantly lower than the value of the resistance (R2) of inner barrier layer (bottom of the nanotube) that is close to the alloy. The fitting parameters for anodized PIII-O samples in Table 5 show that the resistance R1 of the outer layer is about 36 Ω cm2 and that of the inner layer is about 6.5 × 106 Ω cm2. This indicates that the protection provided by the passive layer is predominately because of the inner barrier layer. Potentiodynamic polarization results of both PIII-O and anodized PIII-O samples also support this finding.
 |
| Fig. 6 Equivalent circuit (EC) diagram used for fitting EIS data of the Ni–Ti alloy, PIII-O and anodized PIII-O samples. | |
Table 5 Electrochemical impedance parameters obtained by fitting equivalent circuit model for Ni–Ti alloy, PIII-O and anodized PIII-O samples
Samples |
Rs (Ω cm2) |
Q1 (S sn cm−2) |
n1 |
R1 (Ω cm2) |
Q2 (S sn cm−2) |
n2 |
R2 (Ω cm2) |
χ2 |
Ni–Ti alloy |
6 |
1.6 × 10−7 |
0.91 |
17 |
4.5 × 10−6 |
0.93 |
1.5 × 107 |
5.8 × 10−4 |
PIII-O |
22 |
4.3 × 10−7 |
0.87 |
55 |
1.6 × 10−6 |
0.92 |
4.6 × 107 |
3.2 × 10−3 |
Anodized PIII-O |
15 |
2.6 × 10−6 |
0.72 |
36 |
4.0 × 10−6 |
0.94 |
6.5 × 106 |
2.4 × 10−3 |
The better passivation behavior and near ideal capacitor behavior of the PIII-O sample up to low frequency range in electrochemical studies show that the oxide formed by oxygen implantation is compact. This compact oxide helps in preventing release of metal ions from the substrate into the body fluid. Similarly, in the case of anodized PIII-O sample shows better passivation behavior and near ideal capacitor behavior. However, there is a deviation from near ideal capacitor behavior in very low frequency range (0.01 to 0.1 Hz) as phase angle is ∼−65°. Also, the impedance is lower in this frequency regime. This may be due to the defects in the oxide caused during implantation.
4. Conclusions
Ni–Ti–O nanotubes have been fabricated by anodization of oxygen ion implanted Ni–Ti alloy with average tube length, tube diameter and wall thickness of ∼350, ∼65, and ∼18 nm, respectively. XPS studies have demonstrated that mainly oxidized Ni and Ti are formed in PIII-O and anodized PIII-O samples. Surface modified Ni–Ti alloy samples exhibit better corrosion resistance compared to untreated one. Oxygen ion implantation replaces the native oxide layer of Ni–Ti alloy by a compact oxide layer. Most importantly, the new oxide layer is capable of forming Ni–Ti–O nanotubes on the Ni–Ti surface.
Acknowledgements
The work was carried out under the CSIR network project ESC-01-03. Authors would like to thank the Director, CSIR-National Aerospace Laboratories, Bangalore for giving permission to publish the work. The authors would like to thank Mr Siju for FESEM and EDS studies and Dr Shivakumara, Indian Institute of Science, Bangalore for XRD studies.
References
- S. Shabalovskaya, J. Anderegg and J. Van Humbeeck, Acta Biomater., 2008, 4, 447 CrossRef CAS PubMed.
- N. B. Morgan, Mater. Sci. Eng., A, 2004, 378, 16 CrossRef.
- T. Duerig, A. Pelton and D. Stöckel, Mater. Sci. Eng., A, 1999, 273, 149 CrossRef.
- N. Pandis and C. P. Bourauel, Semin Orthod, 2010, 16, 249 CrossRef.
- M. Tomita, K. Yokoyama and J. Sakai, Corros. Sci., 2008, 50, 2061 CrossRef CAS.
- W. Chrzanowski, E. A. A. Neel, D. A. Armitage and J. C. Knowles, Acta Biomater., 2008, 4, 1969 CrossRef CAS PubMed.
- M. Lamberti, B. Perfetto, T. Costabile, N. Canozo, A. Baroni, F. Liotti, N. Sannolo and M. Giuliano, Toxicol. Appl. Pharmacol., 2004, 195, 321 CrossRef CAS PubMed.
- M.-H. Wong, F.-T. Cheng and H.-C. Man, J. Am. Ceram. Soc., 2008, 91, 414 CrossRef CAS.
- S. A. Shabalovskaya, J. Anderegg, F. Laab, P. Thiel and G. J. Rondelli, J. Biomed. Mater. Res., Part B, 2003, 65, 193 CrossRef CAS PubMed.
- J.-X. Liu, D.-Z. Yang, F. Shi and Y.-J. Cai, Thin Solid Films, 2003, 429, 225 CrossRef CAS.
- A. I. Lotkov, L. Meisner and V. N. Grishkov, Phys. Met. Metallogr., 2005, 99, 508 Search PubMed.
- P. K. Chu, J. Vac. Sci. Technol., B: Microelectron. Nanometer Struct.--Process., Meas., Phenom., 2004, 22, 289 CrossRef CAS.
- R. W. Y. Poon, J. P. Y. Ho, X. Liu, C. Y. Chung, P. K. Chu, K. W. K. Yeung, W. W. Lu and K. M. C. Cheung, Nucl. Instrum. Methods Phys. Res., Sect. B, 2005, 237, 411 CrossRef CAS.
- S. Mändl, D. Krause, G. Thorwarth, R. Sader, F. Zeilhofer, H. H. Horch and B. Rauschenbach, Surf. Coat. Technol., 2001, 142–144, 1046 CrossRef.
- L. Tan, R. A. Dodd and W. C. Crone, Biomaterials, 2003, 24, 3931 CrossRef CAS PubMed.
- P. K. Chu, S. Qin, C. Chan, N. W. Cheung and L. A. Larson, Mater. Sci. Eng., R, 1996, 17, 207 CrossRef.
- S. A. Shabalovskaya, G. C. Rondelli, A. L. Undisz, J. W. Anderegg, T. D. Burleigh and M. E. Rettenmayr, Biomaterials, 2009, 30, 3662 CrossRef CAS PubMed.
- D. Gong, C. A. Grimes, O. K. Varghese, W. Hu, R. S. Singh, Z. Chen and E. C. Dickey, J. Mater. Res., 2001, 16, 3331 CrossRef CAS.
- L. Mohan, C. Anandan and N. Rajendran, Electrochim. Acta, 2015, 155, 411 CrossRef CAS.
- L. Mohan, C. Anandan and N. Rajendran, Mater. Sci. Eng., C, 2015, 50, 394 CrossRef CAS PubMed.
- L. Mohan, S. Viswanathan, C. Anandan and N. Rajendran, RSC Adv., 2015, 5, 93131 RSC.
- L. Sun, S. Zhang, X. W. Sun, X. Wang and Y. Cai, Langmuir, 2010, 26, 18424 CrossRef CAS PubMed.
- L. Sun, X. Wang, M. Li, S. Zhang and Q. Wang, Langmuir, 2014, 30, 2835 CrossRef CAS PubMed.
- L. Sun, S. Zhang and Q. Wang, J. Nanosci. Nanotechnol., 2014, 14, 2050 CrossRef CAS PubMed.
- R. Hang, X. Huang, L. Tian, Z. He and B. Tang, Electrochim. Acta, 2012, 70, 382 CrossRef CAS.
- R. Qin, D. Y. Ding, C. Q. Ning, H. G. Liu, B. S. Zhu, M. Li and D. L. Mao, Appl. Surf. Sci., 2011, 257, 6308 CrossRef CAS.
- Z. Huan, L. E. Fratila-Apachitei, I. Apachitei and J. Duszczyk, Nanotechnology, 2014, 25, 055602 CrossRef CAS PubMed.
- R. Hang, Y. Liu, A. Gao, L. Bai, X. Huang, X. Zhang, N. Lin, B. Tang and P. K. Chu, Mater. Sci. Eng., C, 2015, 51, 37 CrossRef CAS PubMed.
- R. Hang, Y. Liu, L. Zhao, A. Gao, L. Bai, X. Huang, X. Zhang, B. Tang and P. K. Chu, Sci. Rep., 2014, 4, 7547 CrossRef CAS PubMed.
- Q. Liu, D. Ding and C. Ning, Materials, 2014, 7, 3262 CrossRef.
- C. Anandan, L. Mohan and P. D. Babu, Appl. Surf. Sci., 2014, 296, 86 CrossRef CAS.
- S. Mändl, J. W. Gerlach and B. Rauschenbach, Surf. Coat. Technol., 2005, 196, 293 CrossRef.
- L. Sun, S. Zhang, X. Wang, X. W. Sun, D. Y. Ong, X. Wang and D. Zhao, ChemPhysChem, 2011, 12, 3634 CrossRef CAS PubMed.
- R. B. Diegle, N. R. Sorensen, C. R. Clayton, M. A. Helfand and Y. C. Yu, J. Electrochem. Soc., 1988, 135, 1085 CrossRef CAS.
- S. K. Kim and N. Winograd, Surf. Sci., 1974, 43, 625 CrossRef.
- A. Davidson, J. F. Tempere, M. Che, H. Roulet and G. Dufour, J. Phys. Chem., 1996, 100, 4919 CrossRef CAS.
- H. W. Nesbitt, D. Legrand and G. M. Bancroft, Phys. Chem. Miner., 2000, 27, 357 CrossRef CAS.
- M. A. Baker, S. L. Assis, O. Z. Higa and I. Costa, Acta Biomater., 2009, 5, 63 CrossRef CAS PubMed.
- H. Takadama, H.-M. Kim, T. Kokubo and T. Nakamura, Sci. Technol. Adv. Mater., 2001, 2, 389 CrossRef CAS.
- B.-H. Lee, Y. D. Kim and K. H. Lee, Biomaterials, 2003, 24, 2257 CrossRef CAS PubMed.
- L. Mohan, C. Anandan and N. Rajendran, RSC Adv., 2015, 5, 41763 RSC.
- L. Mohan, C. Anandan and V. K. W. Grips, J. Mater. Sci.: Mater. Med., 2013, 24, 623 CrossRef CAS PubMed.
|
This journal is © The Royal Society of Chemistry 2016 |
Click here to see how this site uses Cookies. View our privacy policy here.