Valorisation of sulphonated lignin as a dye for the sustainable colouration of wool fabric using sustainable mordanting agents: enhanced colour yield, colourfastness, and functional properties†
Received
3rd November 2023
, Accepted 18th January 2024
First published on 18th January 2024
Abstract
Biodegradable sulphonated lignin (SL) can be used as a natural dye for the sustainable colouration of wool fabrics, producing light to dark brown shades, but the colourfastness to washing is only moderate, and the colour strength is poor. In this work, wool fabrics were dyed with various concentrations of water-soluble sulphonated lignin using several sustainable mordanting agents, such as calcium (Ca), aluminium (Al), iron (Fe) and copper (Cu) salts, to improve the colour yield and also the colourfastness to washing along with introducing new functional properties. The colour yield of wool fabrics dyed with SL using various mordanting agents was measured using a reflectance spectrometer. The Al and Ca mordants produced a brown colour but the Cu and Fe mordants produced dark olive and dark greyish brown colours, respectively. The wool fabrics dyed with SL using the various mordanting agents exhibited considerably higher colour yield and enhanced colourfastness to washing compared to fabrics dyed with SL without using any mordanting agent. The colour yield considerably increased with an increase in the lignin concentration. Of the mordants studied, Cu and Fe mordanting agents provided the best results. Wool fabric treated with 1% the weight of fibre (owf) SL using Cu mordant, produced better colour yield compared to the fabric treated with 5% (owf) SL without using any mordant. The highest colour strength (4.21) was produced by wool fabric treated with 5% (owf) SL using Cu mordant. The colourfastness increased to grade 4–5 for the fabric dyed with SL using Cu mordant with 35% the weight of SL compared to grade 3 achieved for the fabric dyed with SL without using any mordant. The results suggest that the developed method can be used for the sustainable dyeing of wool fabrics in the textile industry with high colour yield and colourfastness to washing, with a variety of colours.
Sustainability spotlight
Wool fibres are usually dyed with the acid class of dyes, which generates effluent containing left-over toxic and non-biodegradable dyes. The application of lignin as an acid dye substitute will not only valorise lignin and make dyeing sustainable but also solve the disposal issues of lignin, which has very limited use. The work described in this article addresses the United Nation’s Sustainable Development Goals 3, 12, and 14, as the use of modified lignin as a natural dye for the colouration of wool fabrics will solve the effluent problem as lignin is biodegradable and non-toxic ensuring no harmful effect on human health and ensuring the sustainable and responsible production of textiles and discharged effluent is safe for underwater organisms.
|
Introduction
The textile industry is known as one of the major industrial polluters. Effluent discharged from textile dyehouses contains dyes, salts, surfactants, textile auxiliaries, antimicrobial agents, and other finishing agents. Some are toxic and harmful to the environment.1 Wool fibres are popular for various textile applications because of their many beneficial attributes, such as high warmth, fire retardancy, and stain resistance.2 They are usually dyed with synthetic acid and reactive dyes in an aqueous medium, which produces effluent that needs treatment before discharging to the environment. Most of these dyes are recalcitrant and therefore they bioaccumulate causing environmental damage and affecting human health through ingestion of contaminated water, fish and plants.3 Not only is the produced effluent a problem, but when textiles dyed with many of these toxic dyes encounter human skin and become wet with sweating, they may release these toxic dyes to the skin, causing harmful effects including allergic reactions.4,5 Therefore, it is necessary to develop alternative dyes that pose no harmful effect on the environment and human health. Recently, natural dyes derived from plants and fruits have drawn renewed attention for dyeing textiles as they are envisaged as non-toxic, safe, biocompatible, and biodegradable, making them ideal and sustainable alternatives to toxic synthetic dyes.
Natural dyes derived from plants are not a new class of dyes as there is evidence to suggest that dyeing of textiles with natural dyes was practised as early as the Neolithic period. They were the only dyes used for textile dyeing until synthetic dyes were developed. Natural dyes are extracted from the bark, roots, stems, and leaves of plants, vegetables, fruits, fruit skins, seeds, insects, etc. Natural dyes are flavonoids, anthocyanidins, carotenoids, quinonoids, benzoquinone, naphthoquinone and anthraquinoids. Tannins are flavonoids extracted from the bark of various plants including Biancaea sappan,6 cinnamon,7Ziziphus,8 and Dalbergia sissoo,9 leaves of Berberis thunbergia,10 and pomegranate,11 flowers of Hibiscus sabdariffa,12Hibiscus rosasinensis,13Crocus sativus,14 and skins/peel of Citrus sinensis L.15 The natural dyes extracted from fruits studied for wool fibre dyeing may include myrobalan,16 chamomile,17 peanut shell,18 and anthocyanin pigments extracted from the peel/skins of various fruits, including red cabbage,19 and dragon-berries.20 Tannins and other flavonoids are advantageous as some of them have antioxidant and antibacterial properties that make the treated fabric multifunctional.21 Tannins mainly produce a dull brown colour with tonal changes when they are applied to wool fabrics but anthocyanin extracted from various fruit skins produces a variety of colours. The colourfastness of the fabrics dyed with natural dyes is quite poor. Still, many textile products dyed with natural dyes are available on shop floors because of the increase in consumer demand for natural materials. Although natural dyes are procured from cheap biomass, their cost is still very high because of their very low yield, and complicated extraction processes. They are not only more expensive than synthetic dyes, but are not abundantly available at an industrial scale and their dyeing performance is inferior to synthetic dyes. In this respect, lignin is an attractive alternative because of its low cost and abundant availability compared to other natural dyes.
Lignin is a plant-derived biopolymer with a complex chemical structure, and it is the second-most abundantly available natural polymer after cellulose. Kraft lignin is a byproduct of the pulp industry. The huge production of lignin (which is expected to reach 225 million tons per annum by 2030) make its disposal a problem because of its limited use.22 Currently, lignin is mainly used for the generation of heat and energy by combustion.23 It was studied as a source of carbon fibre,24,25 graphene,26 and porous carbon materials,27 as a feedstock with limited success. Published literature shows that lignin works as a UV-blocking and fire retarding agent when added to thermoplastic composites.28,29 Kraft lignin has high colour intensity but because of its water-insolubility, high molecular weight, and low substantivity toward textile fibres, it has rarely been studied for the colouration of textiles. Sulphonated lignin is produced by reacting kraft lignin with sulphuric acid or using bisulphite treatment that introduces sulphonate moieties in lignin to make it water-soluble, but the former produces a sulphonated lignin with a higher anionic charge than the latter.
In our previous work, we reported the colour yield and colourfastness to washing of wool fabric dyed with various concentrations of low-molecular-weight sulphonated lignin (SL) without and with hydrogen peroxide.30 The colourfastness to washing was reasonably good, but the colour strength produced by the dyed fabric was poor and produced only a brown colour shade with tonal changes. These properties of the SL-dyed fabric need further improvement for industrial application. Like textiles dyed with natural dyes, SL-dyed fabrics also show only moderate colourfastness to washing. Therefore, textiles dyed with natural dyes undergo post or pre-mordanting treatment with heavy metal salts and tannins to form a dye–metal complex to reduce the water-solubility of the applied natural dyes and also to bind them to fibres enhancing their colourfastness to washing.31–34 Chromium salts are popular mordanting agents, but they are highly toxic to the environment, and hexavalent chromium is a possible carcinogen.35,36 In this article, for the first time, we are reporting the improvement of colour yields, shades produced, and colourfastness to washing of wool fabrics dyed with SL using various sustainable mordanting agents in a single step. The treated fabric also exhibited high protection against the harmful effects of solar irradiation.
Experimental
Materials
The knitted wool fabric of 177.8 g m−2 used in this work had 20 courses per cm and 18 wales per cm made from merino wool fibres with an average diameter of 19 μm. The fabric was supplied by Levana Textiles (Levin, New Zealand). SL of average molecular weight of 18
000 (C content = 33.7%, and S content = 8.8%) was purchased from Sigma-Aldrich Chemicals (USA) and its chemical structure is presented in Fig. 1. Copper sulphate [Cu(SO4)2], aluminium sulphate [Al2(SO4)3], calcium chloride (CaCl2), ferric sulphate [Fe2(SO4)3], and acetic acid were purchased from Sigma-Aldrich Chemicals (USA). Sandozin MRN (wetting agent) and Sandoclean PC (detergent) were procured from Arkema Chemicals (Switzerland). The phosphate-free standard detergent used for the assessment of colourfastness to washing was supplied by the Society of Dyers and Colourists, UK.
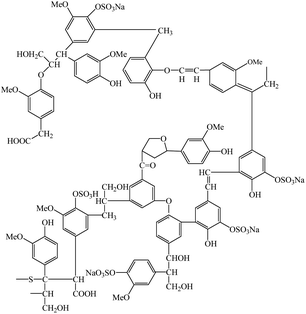 |
| Fig. 1 Specimen chemical structure of sulphonated lignin. | |
Mordant dyeing of wool fabrics with SL
The dirt, spinning oil, and other contaminants present in the wool fabric were removed by washing with 2 g l−1 Sandoclean PC and 0.2 g l−1 Sandozin MRN at 50 °C for 20 min. The fabric samples were washed with hot water and then with cold water to ensure that the detergent was fully removed from the fabric. SL was partially oxidised with peroxide at 90 °C and pH 4 to decrease its molecular weight to ease absorption into wool fibres. The dyeing of wool fabric with SL and post-mordanting treatment with various mordants were carried out using a Roaches laboratory dyeing machine (model: Roaches Pyrotec, Roaches International, UK) using a materials to liquor ratio of 1
:
20. The required quantity of aqueous SL solution was taken in a dyeing pot, and 0.2 g l−1 Sandozin MRN was added to it. After which, the fabric samples were introduced, and dyeing continued for 10 min. Then the dye bath was set at the required pH with sodium acetate/acetic acid or sodium carbonate. The temperature was raised to 98 °C at 2 °C min−1 and held for 60 min. After the completion of dyeing, the temperature was lowered to 70 °C, pre-dissolved mordanting agents were added, the pH was set at 5.0 and held for 30 min. After completion of the mordanting treatment, the bath was cooled to 45 °C, and the fabrics were washed with 0.5 g l−1 Sandoclean PC at 45 °C for 10 min. The fabric samples were then rinsed with cold water and dried.
Measurement of colour yield and colourfastness to washing
The colour strength (K/S) values of fabrics dyed with SL with different mordants at various conditions were measured at the wavelength of maximum absorption using a Datacolor reflectance spectrophotometer (model: DC 550, Datacolor International, Switzerland). All the measurements were carried out under illuminant D65, using a 10° standard observer with the UV component and specular included. Each sample was folded four times, and one measurement was made at five different positions. The CIE L*a* b* values of dyed wool fabrics were measured under illuminant D65, using a 10° standard observer by an X-Rite hand-held spectrophotometer (model 45/0, X-Rite, Incorporated, USA). The colourfastness to washing of wool fabrics dyed with SL was measured according to the ISO test method 105-C03 1987: textiles – tests for colourfastness – part C03: colourfastness to washing: test 3 by washing in a Gyrowash (model 415/8, James Heal, Halifax, England) using the phosphate-free standard detergent. The colour of the fabrics before and after dyeing was compared to the 3 M grey scale to determine the colourfastness grades.
Scanning electron microscopy
To examine whether the applied SL was absorbed into wool fibres or deposited on surfaces of wool fibres, the fabrics dyed with various concentrations of SL using different mordanting agents were examined by scanning electron microscopy. The fabric surface was scanned on a Thermo Scientific scanning electron microscope (model: Phenom Pure G6, Thermo Fisher Scientific, Inc., USA) at an accelerated voltage of 15 kV without any conductive coating.
Fourier transform infrared spectroscopy
To examine the interactions between the wool fibre and SL, the wool fabrics dyed with SL using various mordants were characterised by a Fourier transform infrared (FTIR) spectroscope equipped with an attenuated total reflectance (ATR) attachment (model: Nicolet Summit Pro, ThermoFisher Scientific, USA) at a resolution of 4 cm−1 using a diamond crystal and 64 scans, which were signal-averaged.
Assessment of UV radiation transmission through the fabric
To assess the treated fabrics’ UV protection ability, UV radiation transmission through the fabric was measured. The diffuse transmittance of UV light through the various treated wool fabrics was measured from the wavelength 200 to 380 nm using a Thermo Fisher UV-vis spectrometer (model: Evolution 220, Thermo Fisher Scientific Inc., Waltham, USA) fitted with an integrating sphere reflectance accessory (ISA-220).
Results and discussion
Colour produced on wool fabrics
The UV-visible spectrum of the aqueous lignin solution is provided in Fig. S1 (ESI).† No absorption peak is visible in the visible region of light but researchers found its absorption peak in the UV region.37 Lignin has quinone and conjugated carbonyl chromophore groups providing its colour.38Fig. 2 shows the optical images of control wool fabric dyed with 5% (owf) SL with any mordanting agent and also wool fabrics dyed with various concentrations of SL using Al, Ca, Cu, and Fe mordanting agents at 25% on the weight of SL (ows). The fabric dyed with 5% (owf) SL without using any mordant was a light brown colour, lighter than the fabric dyed with 1% owf SL using mordanting agents. The depth of shade increased with an increase in the concentration of SL. 1% owf SL produced quite a light shade, but the depth of colour dramatically increased when the applied dosage of SL was increased to 5% owf. For 1% (owf) SL, Al and Ca both mordanting agents produced very similar brown shades, but the depth of shade produced by Ca was marginally weaker compared to the shade produced by Al for all concentrations of SL. The colour of SL is brown, and Ca and Al salts are colourless, therefore the colour produced by these two mordanting agents is brown. On the other hand, the Cu mordant produced an olive colour shade as the colour of CuSO4 is blue, which after mixing with brown-coloured SL produced olive shades. The Fe mordant produced a greyish brown colour shade as the colour of ferric sulphate is greyish brown. The Ca mordant produced the lightest shade and the Cu mordant produced the darkest shade. The Fe mordant produced the second darkest colour but was considerably lighter compared to the shade produced by the Cu mordant.
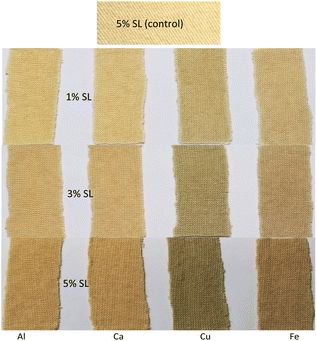 |
| Fig. 2 Optical images of control fabric (dyed without using mordant) and also fabrics dyed with 1, 3, and 5% owf SL using various mordanting agents. | |
The colour of fabrics became lighter to darker with an increase in the SL dosage. However, for 5% (owf) SL, a huge increase in the depth of shade and colour intensity was achieved. For Al and Ca mordanting agents, the depth of shade considerably increased with the increase in SL dosage and the shade turned to reddish-brown, but for Cu and Fe mordants, the shade turned to darker olive and darker greyish brown, respectively.
Fig. S2 (ESI†) shows the effect of Cu and Ca mordant concentration on the shade produced. 25% (ows) Cu mordant produced an olive shade, which became darker with an increase in the concentration of Cu. For Ca mordant, at the applied dosage of 25% (ows) a brown shade is produced, which became only marginally darker with an increase in the mordanting agent concentration. The results suggest that the selection of mordanting agents determines the colour produced on the treated fabrics. Not only SL concentration but also the concentration of mordanting agents influenced the depth of shade produced.
Colour yield and CIE L*a*b* values
We studied the effect of SL concentration and type of mordanting agents on the CIE L*a*b* values and colour strength of wool fabrics dyed with various concentrations of SL, and mordanting agents.
Effect of SL concentration on colour yield.
Depending on the type of mordanting agents and SL concentrations used, light to dark olive, greyish brown, and brown shades were produced on wool fabrics dyed with SL at pH 3. The dyeing was carried out at pH 3 as our previous work showed that the maximum absorption of SL was achieved at that pH.30Fig. 3 shows the effect of SL concentration on the colour strength of wool fabric using a mordanting agent concentration of 25% (ows). SL in combination with a mordanting agent quite considerably increased the colour strength, which increased with an increase in SL concentration. For all concentrations of SL, Ca provided the lowest, and Cu provided the highest, colour yield. For 1% (owf) SL, the colour yield achieved with Cu mordant was 1.7, equal to the wool fabric treated with 8% SL without using any mordanting agent, as reported in our previous article.30 All other mordants produced similar colours except the Cu and Fe mordants, which provided considerably higher colour strength compared to the fabric dyed with other mordants. When the SL dosage was increased to 3% (owf), the colour yield for the Cu mordant increased to 3.13. Even for the Ca mordant, the colour strength increased to 2.20. The highest colour strength, 4.21, was achieved for the wool fabric treated with 5% (owf) SL using the Cu mordant. The second highest colour strength, 2.43, was achieved for the wool fabric treated with 5% (owf) SL using the Fe mordant. The Cu mordanting agent was the best performer, but Fe also showed effectiveness as a mordanting agent, although the colour strength produced was considerably lower compared to the fabric dyed with SL using the Cu mordant.
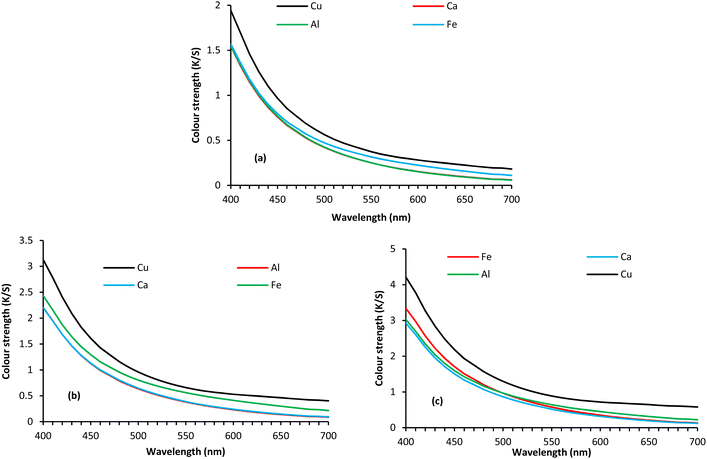 |
| Fig. 3 Colour strength for wool fabric dyed with 1 (a), 3 (b), and 5% (c), SL using various metals at 25% ows. | |
Table 1 shows the effect of SL concentration and the type of mordanting agents studied, on the CIE L*a*b* values of the dyed wool fabrics. The values of L*, a*, and b* denote lightness or darkness, yellowness or greenness, and redness or blueness of the shade produced. The value of L* decreased with an increase in the SL concentrations for all the mordanting agents, i.e., the samples became darker with an increase in the concentration of SL. The control fabric dyed with 5% SL without using any mordanting agent, produced the lightest colour as it showed the highest L* value (87.70). Of the mordanting agents studied, Cu provided the lowest L* value suggesting producing the darkest shade. On the other hand, Al and Ca provided similar L* values, indicating producing a similar depth of shade. The fabric treated with SL using the Fe mordant provided a lower L* value compared to Cu and Al, but was considerably higher than the L* value produced by the fabric treated with SL using the Cu mordant. For Al, Ca, and Fe mordants, the yellowness of the sample increased with an increase in the concentration of SL but for Cu mordant, the yellowness of the sample increased with an increase in SL concentration up to 3%, after which the yellowness of the fabric decreased with a further increase in the SL concentration. On the other hand, the redness of the fabric increased with an increase in the concentration of SL for the Al, Ca, and Fe mordanting agents, but the opposite occurred for the Cu mordant, for which the redness decreased with an increase in the SL concentration. The colour difference compared to the undyed fabric also increased with an increase in the lignin concentration and Cu provided the highest colour difference.
Table 1 CIE L*a*b* values and colour difference compared to the undyed control of wool fabrics dyed with various concentrations of SL using various mordanting agents at 25% ows
SL dosage (% owf) |
Mordanting agents |
CIE L*a*b* values |
ΔE |
Colour strength (K/S) |
L* |
a* |
b* |
Control |
— |
87.70 ± 0.21 |
4.75 ± 0.11 |
22.70 ± 0.13 |
12.65 |
1.19 |
1 |
Al |
75.82 ± 0.17 |
5.08 ± 0.08 |
20.83 ± 0.05 |
15.99 |
1.54 |
|
Ca |
76.34 ± 0.11 |
4.85 ± 0.05 |
21.43 ± 0.02 |
16.01 |
1.54 |
|
Cu |
71.44 ± 0.15 |
2.95 ± 0.03 |
20.03 ± 0.07 |
20.15 |
1.94 |
|
Fe |
73.08 ± 0.11 |
3.66 ± 0.05 |
18.39 ± 0.05 |
17.87 |
1.57 |
3 |
Al |
71.34 ± 0.15 |
6.08 ± 0.05 |
23.62 ± 0.07 |
21.72 |
2.20 |
|
Ca |
71.54 ± 0.15 |
5.82 ± 0.03 |
23.21 ± 0.09 |
21.79 |
2.20 |
|
Cu |
63.94 ± 0.10 |
2.05 ± 0.03 |
20.55 ± 0.05 |
26.82 |
3.13 |
|
Fe |
67.09 ± 0.13 |
3.85 ± 0.02 |
18.96 ± 0.07 |
24.14 |
2.43 |
5 |
Al |
68.71 ± 0.14 |
6.75 ± 0.03 |
24.74 ± 0.06 |
26.31 |
3.02 |
|
Ca |
68.85 ± 0.16 |
7.17 ± 0.05 |
25.36 ± 0.03 |
25.5 |
2.93 |
|
Cu |
59.72 ± 0.11 |
2.73 ± 0.02 |
21.32 ± 0.03 |
31.17 |
4.21 |
|
Fe |
64.51 ± 0.13 |
4.99 ± 0.02 |
20.61 ± 0.04 |
25.85 |
3.34 |
Effect of mordanting agent concentration on the colour strength of the fabric.
Fig. 4 shows the effect of Ca and Cu mordanting agent concentrations on the shade produced by the wool fabric dyed with 3% (owf) SL. The depth of shade increased with an increase in the mordanting agent concentration. In the case of Ca, the reddish tone of shade increased with an increase in the mordanting agent concentration, but for Cu, the greenish tone increased with an increase in Cu concentration. The colour strength of the dyed fabrics increased with an increase in the mordanting agent concentration for Al, Ca, and Fe, but for the Cu mordant, the colour strength increased with an increase in the concentration of Cu until 35% ows, after which the colour strength started decreasing with an increase in Cu concentration.
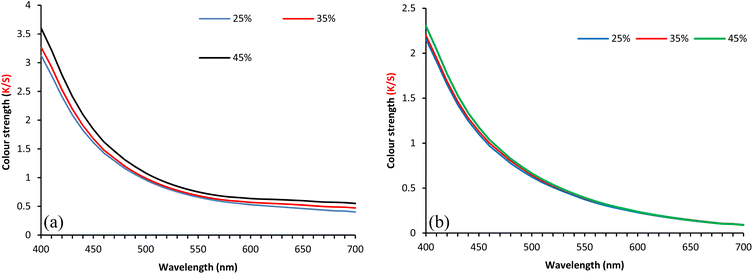 |
| Fig. 4 Effect of Cu (a) and Ca (b), mordanting agent concentration (% ows) on the colour strength of the fabric dyed with 3% owf SL. | |
Table S1 (ESI†) shows the effect of mordanting agent concentration (Ca and Cu) on the CIE L*a*b* values of wool fabrics dyed with SL. The L* value decreased with an increase in the concentration of mordanting agents, but the effect was more pronounced in the case of Cu instead of Ca, for which the effect was only marginal. For Ca, the yellowness and redness of the dyed fabrics increased with an increase in the concentration of the mordanting agent, but for Cu, the yellowness decreased, and the redness increased with an increase in mordanting agent concentration up to 35%, after which it was reversed, i.e., yellowness increased, and redness decreased with a further increase in the mordanting agent concentration. The colour difference compared to the undyed wool fabric also increased with an increase in the concentration of mordanting agents (Al, Ca, and Fe), but for Cu, the colour difference increased up to 35% (ows) Cu concentration. After which the colour difference decreased with further increase in Cu concentration. Therefore, for Cu, 35% (ows) is the optimum mordanting agent concentration, but for others, 45% (ows) is the optimum concentration of mordanting agent for dyeing wool fabrics with SL.
Colourfastness to washing
Table 2 shows the effect of SL concentration and the various mordanting agents studied, on the colourfastness to washing of the fabrics dyed with SL. Except for Ca, all other mordanting agents provided very good colourfastness to washing as the fastness grade was 3–4, much better than the colourfastness to washing of wool fabrics dyed with SL without using any mordanting agent.30 The colourfastness to washing increased by one grade compared to the wool fabric samples dyed with SL alone. The colourfastness to staining for different types of fibres was also quite good except against nylon fabric, which is also a polyamide fibre like wool fibre. Of the mordanting agents studied in this work, except for Ca, all mordanting agents provided better colourfastness to washing as other mordanting agents are trivalent compared to Ca, which is divalent. Therefore, they provided more anchoring sites compared to Ca, which increased the binding of SL to wool compared to Ca.
Table 2 Colourfastness to washing of wool fabrics treated with SL at various conditions using different mordanting agents
SL (% owf) |
Colour change |
Cellulose diacetate |
Bleached cotton |
Polyamide |
Polyester |
Acrylic |
Silk |
Control |
3 |
3–4 |
3–4 |
3–4 |
4 |
4 |
3–4 |
|
Cu
|
1 |
4 |
4 |
4 |
4 |
4 |
4 |
4 |
3 |
4 |
4 |
4 |
4 |
4 |
4 |
4 |
5 |
4 |
4 |
4 |
4 |
4 |
4 |
4 |
|
Fe
|
1 |
4 |
4 |
4 |
3–4 |
4–5 |
4 |
4–5 |
3 |
4 |
4 |
4 |
3–4 |
4–5 |
4 |
4–5 |
5 |
4 |
4 |
4 |
3–4 |
4–5 |
4 |
4–5 |
|
Al
|
1 |
3–4 |
4 |
4 |
3–4 |
4–5 |
4 |
4–5 |
3 |
4 |
4 |
4 |
3–4 |
4–5 |
4 |
4–5 |
5 |
4 |
4 |
4 |
3–4 |
4–5 |
4 |
4–5 |
|
Ca
|
1 |
3–4 |
4 |
4 |
3–4 |
4–5 |
4 |
4–5 |
3 |
3–4 |
4 |
4 |
3–4 |
4–5 |
4 |
4–5 |
5 |
3–4 |
4 |
4 |
3–4 |
4–5 |
4 |
4–5 |
Table S2 (ESI†) shows the effect of concentrations of Ca and Cu mordanting agents on the colourfastness to washing. Cu at 35% ows provided excellent colourfastness to washing as the colourfastness grade increased to 4–5. On the other hand, Ca provided poor colourfastness to washing, which suggests the importance of the selection of the right mordanting agents and their concentrations.
Mechanisms of dyeing
The mordant dyeing of wool fabric with SL is quite complex. SL is moderately anionic due to the presence of many hydroxyl groups and a few carboxyl groups. The isoelectric point of wool in aqueous solutions is 4.5, below which the wool fibre is cationic and above, the fibre is anionic. The various mechanisms of wool fabric dyeing with SL using a Cu mordanting agent are presented in Fig. 5. The other metallic ions (Fe, Ca, and Al) also form similar types of bonding. During dyeing in acidic conditions below pH 4.5, anionic SL ionically binds with the cationic amino groups of wool fibres as well as by forming hydrogen bonding between OH groups of SL and amino/carboxyl groups of wool fibres. During mordanting treatment with metallic salts, the cations of these salts form a metal–SL complex with sulphonate and carboxyl groups of SL. On the other hand, cationic metal ions can also work as a bridge between carboxyl groups of wool fibre and sulphonate/carboxyl groups of SL. Due to these three mechanisms, dyeing wool fibre with SL using mordanting agents provided higher colourfastness to washing compared to dyeing with SL alone. However, the metal ion chelating power of SL is poor compared to natural tannins, and therefore tannins mordanting treatment of SL-treated wool fabric is less effective compared to the mordanting treatment of wool fabrics treated with tannin due to a smaller number of polyphenolic groups in SL compared to tannins.
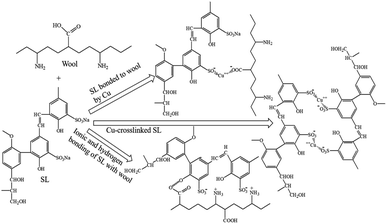 |
| Fig. 5 Mechanisms of dyeing wool fabric with SL using Cu mordanting agent. | |
Elemental analysis
Fig. 6 shows the analysis of C, N, O, S, Al, Ca, Fe, and Cu elements of wool fabric surfaces treated with 5% owf SL using various mordanting agents. The elemental composition of C, N, O, and S of untreated wool fabric was 50.18, 20.68, 26.24, and 2.90%, respectively, which is consistent with published results.38 Obviously, the control fabric did not show the presence of any heavy metal. For the wool fabric treated with SL, the elemental composition changed: the elemental analysis of wool fabric dyed with SL with various metal ions shows the presence of those metals in the respective samples. For the treated fabric samples, the O and S content increased due to the presence of polyphenolic and sulphonate groups in SL. The presence of Ca was the lowest, and Cu was the highest. The order of elemental contents of various mordants of the treated fabrics is consistent with the colour yield data.
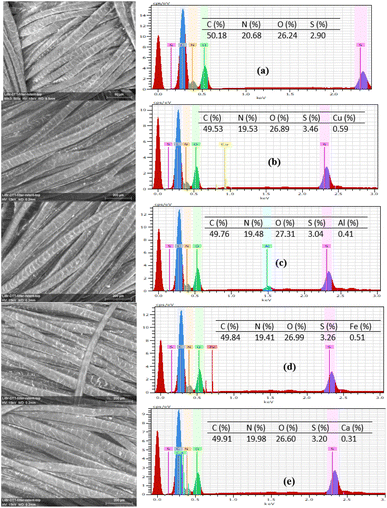 |
| Fig. 6 EDX spectra of wool fabrics treated with 5% owf SL using no mordant (a) and Cu (b), Al (c), Fe (d), and Ca (e), mordanting agents. | |
Fig. S3 (ESI†) shows the distribution of elements on the surfaces of the wool fabrics. It shows that the elements are quite uniformly distributed on the treated fabric surfaces showing the uniformity of the dyeing treatment.
UV radiation absorption
According to the energy level, solar UV radiation is divided into three regions: UV-A (315–400 nm), UV-B (280–315 nm), and UV-C (100–280 nm). Among them, UV-C has the highest energy and therefore is the most harmful for human skin but fortunately, UV-C and most UV-B are blocked by the ozone layer of the Earth’s atmosphere. Only UV-A and partially UV-B reach Earth. The UV transmission through the fabric at 290 (UV-B) and 340 nm (UV-A) is the determining factor for wearer protection from solar UV radiation exposure.37Fig. 7 shows the UV transmission curves of wool fabric treated with 1, 3, and 5% owf SL using Cu mordant compared to the wool fabric dyed with 10% (owf) SL without any mordanting agent. UV radiation transmission through the untreated fabric was quite high as the UV transmission at 290 and 340 nm was 3.05 and 9.73%, respectively, which reduced to 2.02 and 4.53%, respectively, for the fabric treated with 1% owf SL. The best UV protection performance was exhibited by the wool fabric treated with 5% owf SL, for which the UV transmission through the fabric at 290 and 340 nm was reduced to 2.79 and 1.46% respectively, considerably lower compared to the UV light transmitted through the fabric dyed with 10% (owf) SL without any mordanting agent. The wool fabric treated with 5% (owf) lignin using Cu mordant showed UV radiation absorption comparable to the wool fabric treated with tannic acid and various polyphenols extracted from mango seed kernel and feijoa fruit skin,21 but was not as good as the UV protection offered by wool fabrics treated with Ag nanoparticles.39 The treatment of wool fabric with SL at various dosages provided excellent UV absorption ability owing to its aromatic structure and the presence of numerous phenolic, ketone, and sulphonate groups that considerably enhanced its UV protection capability.40 SL has high UV radiation-blocking capability due to its intramolecular hydrogen bonds.41 The UV protection capability achieved for the wool fabric dyed with SL is quite satisfactory.
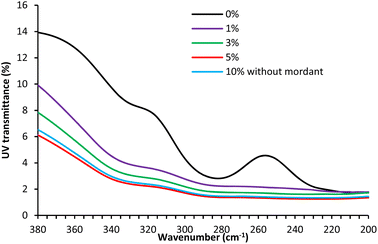 |
| Fig. 7 The effect of SL concentration on the UV transmission through the wool fabric samples treated with SL using Cu as a mordanting agent. | |
Surface morphologies
Fig. 8 shows the SEM micrographs of wool fabric surfaces treated with 5% SL using various mordanting agents. The surface of untreated fabric shows the presence of subdued scales, as the wool fabrics used in this work were made from shrink-resistant-treated wool fibres. The characteristic wool fibre scale edges are etched by the shrink-resist treatment, and fibre surfaces are thinly coated with a polymer resin. For all the treated fabric samples, some deposition of SL is visible on the treated wool fabric surface, suggesting most of the applied SL was absorbed into wool fibres providing good colourfastness to washing. The surfaces of the treated fibres using various mordants, look quite similar except for the wool fabric treated with SL using the Fe mordant, which shows non-uniform coating with SL. In the case of the Fe mordant, some irregular deposition of SL is visible on the treated wool fabric surface.
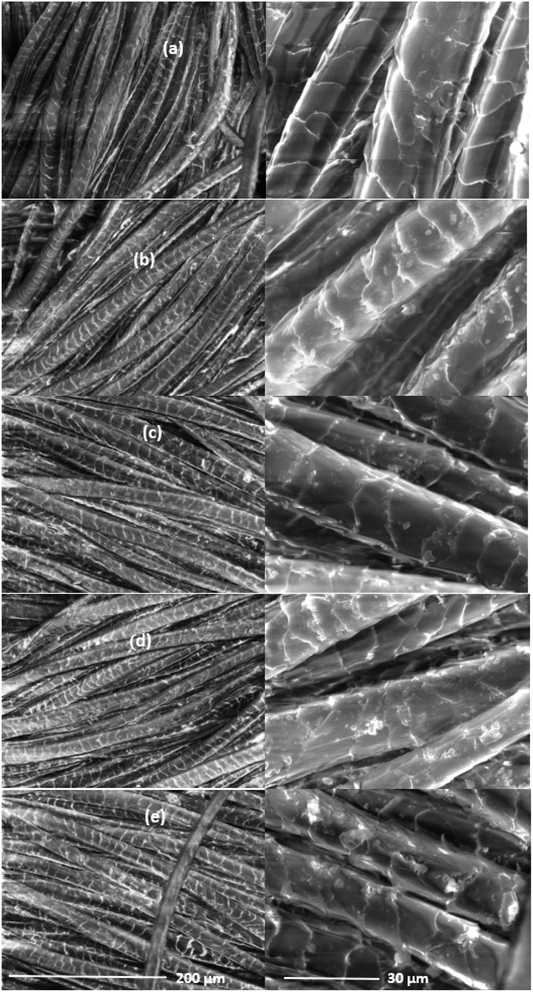 |
| Fig. 8 SEM micrographs of surfaces of the control wool fabric (a), and also wool fabric samples treated with 5% owf SL using 25% ows Al (b), Ca (c), Cu (d), and Fe (e). | |
ATR-FTIR spectra
The FTIR spectral analysis of SL-dyed wool fabrics was carried out to determine the interactions between SL and wool fibre. Fig. S4 (ESI†) shows the FTIR spectra of the control wool fabric as well as wool fabrics treated with SL using the various mordanting agents. The spectrum of the control wool fabric shows typical wool keratin protein-associated IR bands at 1350, 1550, and 1650 cm−1 related to amide(III), amide(II), and amide(I), respectively.42 It also shows a broad peak at around 3300 cm−1, which is related to hydroxyl groups of wool keratin. The wool fabric treated with SL with various mordants shows a new IR band at around 1040 cm−1, which is associated with the sulphonate groups of SL,43,44 and its intensity is associated with the SL contents of the fabric. The presence of this IR band confirms the presence of SL in the treated fabrics. The results suggest that the presence of SL was the highest for the fabric dyed using the Cu mordant and the lowest for the fabric dyed using the Ca mordant, which is consistent with the colour yields, CIE L*a*b* values, and UV radiation transmission through the fabric data.
Sustainability aspects of mordant dyeing of wool with SL
SL is known to depolymerize under composting conditions by thermophilic microfungi and actinomycetes at 40–50 °C but is not fully mineralised.45 However, SL should readily biodegrade after depolymerisation to smaller macromolecules because of its increased water-solubility. Therefore, dyeing with SL should not negatively affect the biodegradability of wool fibres as SL is not difficult to manage like many synthetic dyes used in the textile industry.46 The mordants used in this work, Ca, Fe, and Al, are non-toxic except Cu, which has a low level of toxicity, but it is not a potential carcinogen like chromium (Cr) and cadmium (Cd). The US Environmental Protection Agency has determined that copper levels in drinking water up to 1300 μg l−1 do not have any effect on human health where the safe levels for Cr, Cd, and Ni are 100, 0.5, and 100 μg l−1, respectively.47 The developed process does not reduce water and energy usage compared to the dyeing of wool fabrics with synthetic acid dyes but produces non-toxic effluent, unlike dyeing with acid dyes, enhancing the sustainability of the process.
Conclusions
This work demonstrates that various mordanting agents can be successfully used to produce different colours and also to enhance the colour strength and the colourfastness to washing of wool fabrics dyed with SL. The colour strength considerably increased for all the mordanting agents studied in this work, but the best results were achieved for the Cu and Fe mordanting agents. Al and Ca produced very similar colours with tonal change, but Cu and Fe produced olive and greyish brown coloured shades on wool fabric. The colourfastness to washing achieved in this work is quite impressive as the colourfastness to washing improved to grade 4–5 for the Cu mordant when applied at 35% ows, which is considerably higher than the colourfastness to washing achieved for the wool fabric dyed with SL without using any mordanting agent. The developed method can be used in the textile industry for the sustainable colouration of wool and other natural and synthetic polyamide fibres with SL.
Conflicts of interest
There are no conflicts to declare.
Notes and references
- M. M. Hassan and C. J. Hawkyard, Ozone: Sci. Eng., 2002, 24, 261–270 CrossRef CAS.
- M. M. Hassan and C. M. Carr, J. Adv. Res., 2019, 18, 39–60 CrossRef CAS PubMed.
- B. Lellis, C. Z. Favaro-Polonio, J. A. Pamphile and J. C. Polonio, Biotechnol. Res. Innov., 2019, 3, 275–290 CrossRef.
- F. Iadaresta, M. D. Manniello, C. Östman, C. Crescenzi, J. Holmbäck and P. Russo, Environ. Sci. Pollut. Res., 2018, 25, 24629–24638 CrossRef CAS PubMed.
- M. Meinke, M. F. Abdollahnia Gähr, T. Platzek, W. Sterry and J. Lademann, Exp. Dermatol., 2009, 18, 789–792 CrossRef CAS PubMed.
- M. N. Bukhari, M. A. Wani, M. Fatima, J. S. S. Bukhari, M. Shabbir, L. J. Rather and F. Mohammad, J. Nat. Fibers, 2023, 20, 2208890 CrossRef.
- S. Adeel, N. Habib, F. Batool, N. Amin, T. Ahmad, S. Arif and M. Hussaan, Environ. Prog. Sustainable Energy, 2022, 41, e13794 CAS.
- S. Mirnezhad, M. Sadeghi-Kiakhani and E. Hashemi, Environ. Sci. Pollut. Res., 2023, 30, 51504–51517 CrossRef CAS PubMed.
- K. Iqbal, H. Afzal, M. O. R. Siddiqui, U. Bashir, K. Jan, A. Abbas and H. A. Abid, Sustainable Chem. Pharm., 2023, 33, 101094 CrossRef CAS.
- A. Haji and M. Rahimi, J. Nat. Fibers, 2022, 19, 2785–2798 CrossRef CAS.
- A. Haji, F. Shahmoradi Ghaheh and L. Indrie, Rev. Prog. Color. Relat. Top., 2023, 139, 165–170 CrossRef CAS.
- Z. Omerogullari Basyigit, C. Eyupoglu, S. Eyupoglu and N. Merdan, Rev. Prog. Color. Relat. Top., 2023, 139, 441–453 CrossRef CAS.
- S. Adeel, M. Salman, M. Usama, F.-U. Rehman, T. Ahmad and N. Amin, J. Nat. Fibers, 2022, 19, 6089–6103 CrossRef CAS.
- K. Lachguer, M. El Ouali, I. Essaket, S. El Merzougui, O. Cherkaoui and M. A. Serghini, Fibers Polym., 2021, 22, 3368–3377 CrossRef CAS.
- Z. Romdhani, N. Sakji and M. Hamdaoui, Fibers Polym., 2022, 23, 1621–1630 CrossRef CAS.
- M. Hosseinnezhad, K. Gharanjig, H. Imani and N. Razani, J. Nat. Fibers, 2022, 19, 3893–3915 CrossRef CAS.
- M. A. B. Menegazzo, F. Giacomini and M. A. S. D. D. Barros, J. Nat. Fibers, 2020, 17, 271–283 CrossRef CAS.
- B. Dulo, T. De Somer, K. Phan, M. Roosen, J. Githaiga, K. Raes and S. De Meester, Sustainable Mater. Technol., 2022, 34, e00518 CrossRef CAS.
- H. Barani and H. Maleki, Pigm. Resin Technol., 2020, 49, 229–238 CrossRef CAS.
- N. Baaka, M. Ben Ticha and A. Guesmi, Fibers Polym., 2019, 20, 2522–2528 CrossRef CAS.
- M. M. Hassan, RSC Adv., 2021, 11, 1482–1492 RSC.
- D. S. Bajwa, G. Pourhashem, A. H. Ullah and S. G. Bajwa, Ind. Crops Prod., 2019, 139, 111526 CrossRef CAS.
- A. J. Ragauskas, G. T. Beckham, M. J. Biddy, R. Chandra, F. Chan, M. F. Davis, B. H. Davison, R. A. Dixon, P. Gilna and M. Keller, Science, 2014, 344, 1246843 CrossRef PubMed.
- W. J. Sagues, A. Jain, D. Brown, S. Aggarwal, A. Suarez, M. Kollman, S. Park and D. S. Argyropoulos, Green Chem., 2019, 21, 4253–4265 RSC.
- J. Bai, S. Wang, Y. Li, Z. Wang and J. Tang, Int. J. Biol. Macromol., 2021, 187, 594–602 CrossRef CAS PubMed.
- Y. Liang, Y. Zhou, X. Liu and X. Qi, Int. J. Biol. Macromol., 2023, 230, 123247 CrossRef CAS PubMed.
- F. J. García-Mateos, J. M. Rosas, R. Ruiz-Rosas, J. Rodríguez-Mirasol and T. Cordero, Carbon, 2022, 200, 134–148 CrossRef.
- Y. Wan, J. He, Y. Zhang and E. Y. X. Chen, Angew. Chem., Int. Ed., 2022, 61, e202114946 CrossRef CAS PubMed.
- H. Yang, B. Shi, Y. Xue, Z. Ma, L. Liu, L. Liu, Y. Yu, Z. Zhang, P. K. Annamalai and P. Song, Biomacromolecules, 2021, 22, 1432–1444 CrossRef CAS PubMed.
- M. M. Hassan, ACS Sustainable Chem. Eng., 2023, 11, 13787–13797 CrossRef CAS.
- R. Räisänen, A. Primetta, P. Toukola, S. Fager and J. Ylänen, Ind. Crops Prod., 2023, 198, 116748 CrossRef.
- M. Thehrani, F. S. Ghaheh, Z. T. Beni and M. Rahimi, Environ. Sci. Pollut. Res., 2023, 30, 68625–68635 CrossRef PubMed.
- M. Umesh, S. Suresh, A. S. Santosh, S. Prasad, A. Chinna-thambi, S. Al Obaid, G. K. Jhanani and S. Shanmugam, Environ. Res., 2023, 229, 115973 CrossRef CAS PubMed.
- H. Imani, K. Gharanjig and Z. Ahmadi, Pigm. Resin Technol., 2023, 52, 321–330 CrossRef CAS.
- K. Amutha, A. S. Grace and N. Sudhapriya, Ind. Crops Prod., 2020, 148, 112303 CrossRef CAS.
- A. Zhitkovich, Chem. Res. Toxicol., 2011, 24, 1617–1629 Search PubMed.
- O. A. Abdelaziz and C. P. Hulteberg, Waste Biomass Valorization, 2017, 8, 859–869 Search PubMed.
- S. Sandoval-Torres, W. Jomaa, F. Marc and J.-R. Puiggali, For. Stud. China, 2010, 12, 167–175 Search PubMed.
- P. S. Sobolewski, J. W. Krzyścin, J. Jarosławski, J. Wink, A. Lesiak and J. Narbutt, J. Photochem. Photobiol., B, 2014, 140, 105–110 CrossRef CAS PubMed.
- O. Gordobil, P. Olaizola, J. M. Banales and J. Labidi, Molecules, 2020, 25, 1131 CrossRef CAS PubMed.
- M. M. Hassan, Colloids Surf., A, 2019, 581, 123819 CrossRef CAS.
- M. H. Tran, D.-P. Phan and E. Y. Lee, Green Chem., 2021, 23, 4633–4646 RSC.
- M. M. Hassan and S. J. Leighs, Appl. Surf. Sci., 2017, 419, 348–356 CrossRef CAS.
- M. M. Hassan and J. R. McLaughlin, New J. Chem., 2018, 42, 18919–18927 RSC.
- M. Tuomela, M. Vikman, A. Hatakka and M. Itävaara, Bioresour. Technol., 2000, 72, 169–183 CrossRef CAS.
- M. M. Hassan and C. M. Carr, Chemosphere, 2018, 209, 201–219 CrossRef CAS PubMed.
- A. Jamshidi, M. Morovati, M. M. Golbini Mofrad, M. Panahandeh, H. Soleimani and H. Abdolahpour Alamdari, J. Environ. Health Sci. Eng., 2021, 19, 1117–1131 CrossRef CAS PubMed.
Footnote |
† Electronic supplementary information (ESI) available: Effect of mordant dosage, elemental distribution on fabric surface, ATR-FTIR spectra, and CIE L*a*b* values and colour difference, and colourfastness data. See DOI: https://doi.org/10.1039/d3su00402c |
|
This journal is © The Royal Society of Chemistry 2024 |
Click here to see how this site uses Cookies. View our privacy policy here.